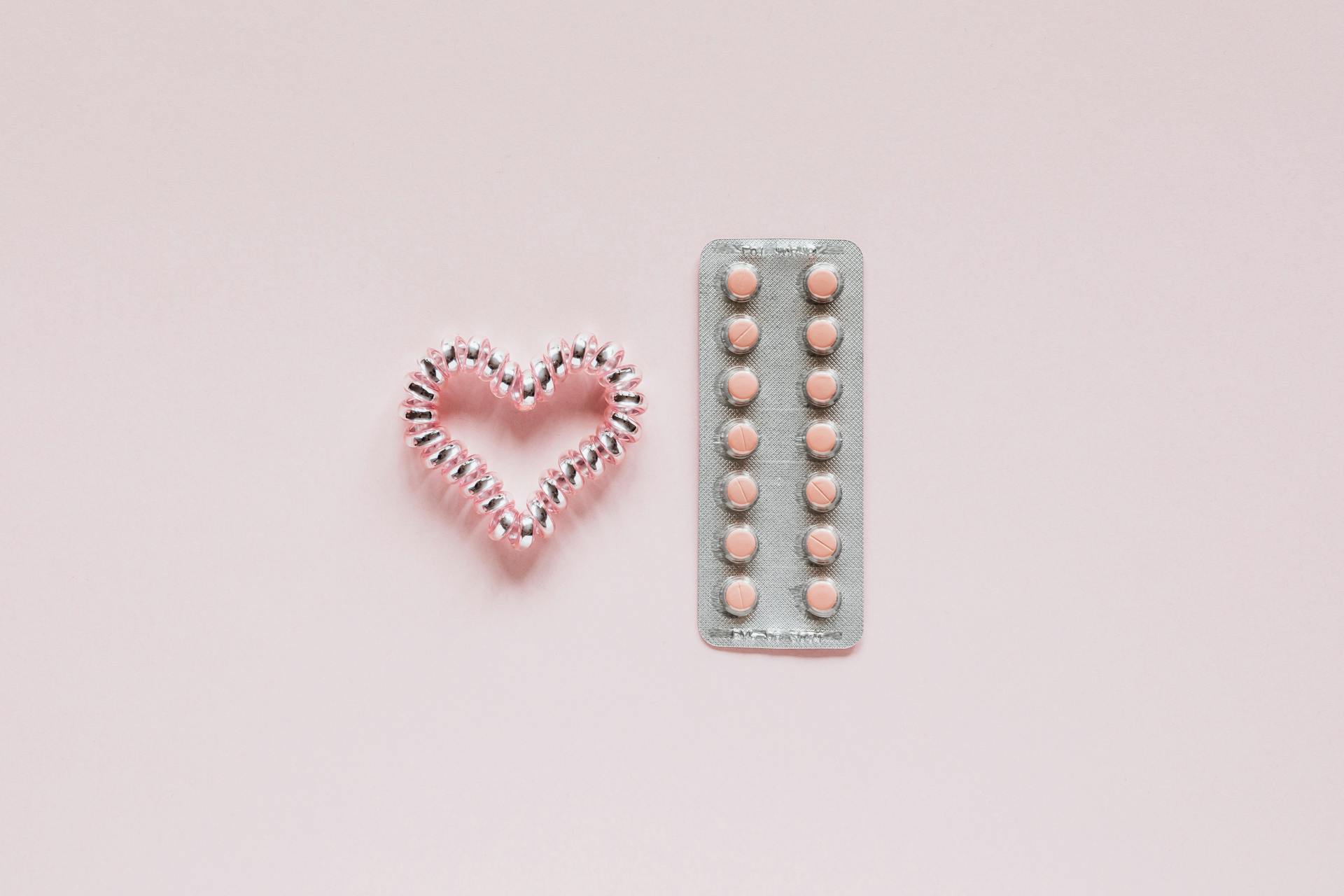
Slide blister packs offer several benefits, including reduced packaging waste and improved product visibility. They can be designed to accommodate a wide range of product sizes and shapes.
One of the key benefits of slide blister packs is their ability to reduce packaging waste by minimizing the amount of material used. This is especially important for companies looking to reduce their environmental impact.
Slide blister packs can be customized to fit specific product needs, including the size and shape of the product, as well as the type of packaging material used. This flexibility makes them a popular choice for many industries.
Expand your knowledge: Packing Foam Material
What Is a Slide Blister Pack?
A slide blister pack is a type of packaging that allows for easy opening and closing during packing of the product. This is achieved through the sliding of the blister on the cardboard.
The slide blister pack is an efficient and visually appealing packaging solution, especially for displaying and protecting small products. It combines a thermoformed blister tray with a paper card, providing a convenient way to protect products while showcasing product information.

The sliding blister packaging consists of two parts: a plastic blister and a paper card. The plastic blister needs to fold the three sides of the blister to the back with a folding machine.
This type of packaging provides strong protection against product damage during transit and is easy to access. The transparent plastic section allows consumers to clearly see the product, while the printed paper card provides additional product information and brand promotion.
Here are some benefits of slide blister packaging:
- Strong Protection: The durable plastic blister tray effectively prevents product damage during transit.
- Easy Access: The sliding design makes it simple and quick for users to retrieve the product, enhancing the user experience.
- Excellent Display: The transparent plastic section allows consumers to clearly see the product, while the printed paper card provides additional product information and brand promotion.
- Eco-Friendly Materials: Can be made from recyclable plastic materials (such as PET and RPET), meeting environmental standards.
- Flexible Customization: Customizable in terms of size, shape, and printing design to meet various market needs.
Types and Comparisons
Slide blister packaging offers several types to choose from, including flange or flanged folded blister packaging, which is a popular option.
You can also consider flange blister packaging, edge blister packaging, or sliding or slide on blister packaging, each with its own unique characteristics.
A cost-effective way to package products is with a slide blister, and it's relatively cheaper to thermoform than a normal blister.
What Types Compare
Slide blister packaging is a cost-effective way to package products in most industries, making it a popular choice for many companies.
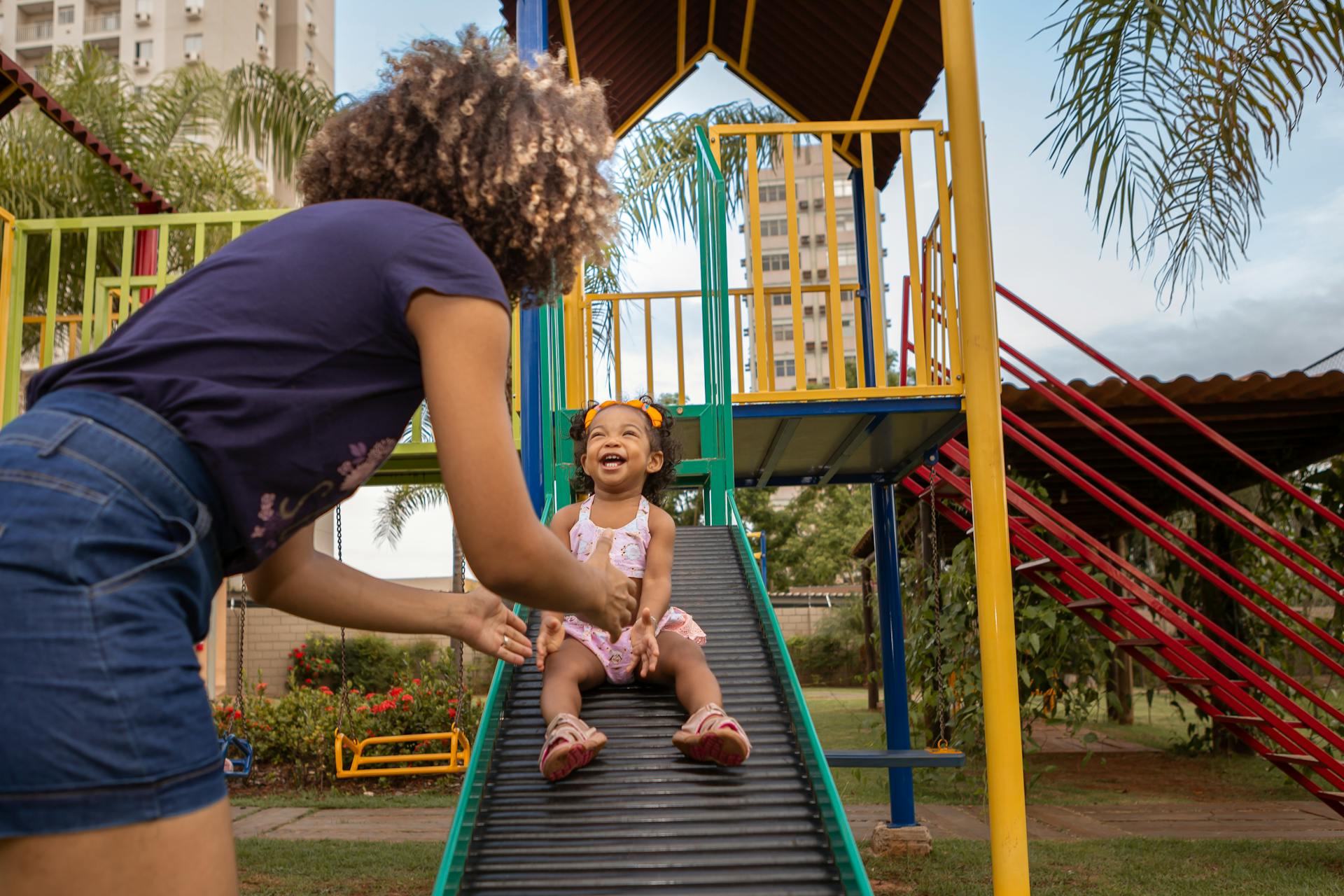
It's easier to thermoform a slide blister than a normal blister, which is a significant advantage in the manufacturing process.
In fact, slide blister packaging is relatively cheaper than normal blister packaging, which can be a major factor in business decisions.
There are several types of blister packaging to consider, including flange blister packaging, edge blister packaging, and sliding or slide on blister packaging.
Here are some of the main types of blister packaging:
- Flange blister packaging
- Flange or flanged folded blister packaging
- Edge blister packaging
- Sliding or slide on blister packaging
- Folded flange blister packaging
- Bent blister packaging
Difference Between Heat Seal Clamshell
Heat seal clamshell packaging has hinges on the sides, which is a key difference from slide blister packaging.
The hinges on heat seal clamshell packaging provide flexibility and make it easier to open and close the packaging.
In contrast, slide blister packaging lacks hinges, making it a more rigid and less flexible option.
Take a look at this: Clamshell Blister Pack
Difference Between Strip and
Strip packaging involves packing a product between two layers of sealable heat foil, such as aluminum-poly and paper-poly.
The sealable heat foil used in strip packaging provides a secure and tamper-evident seal.
On a similar theme: How to Pack a Wound with Packing Strip
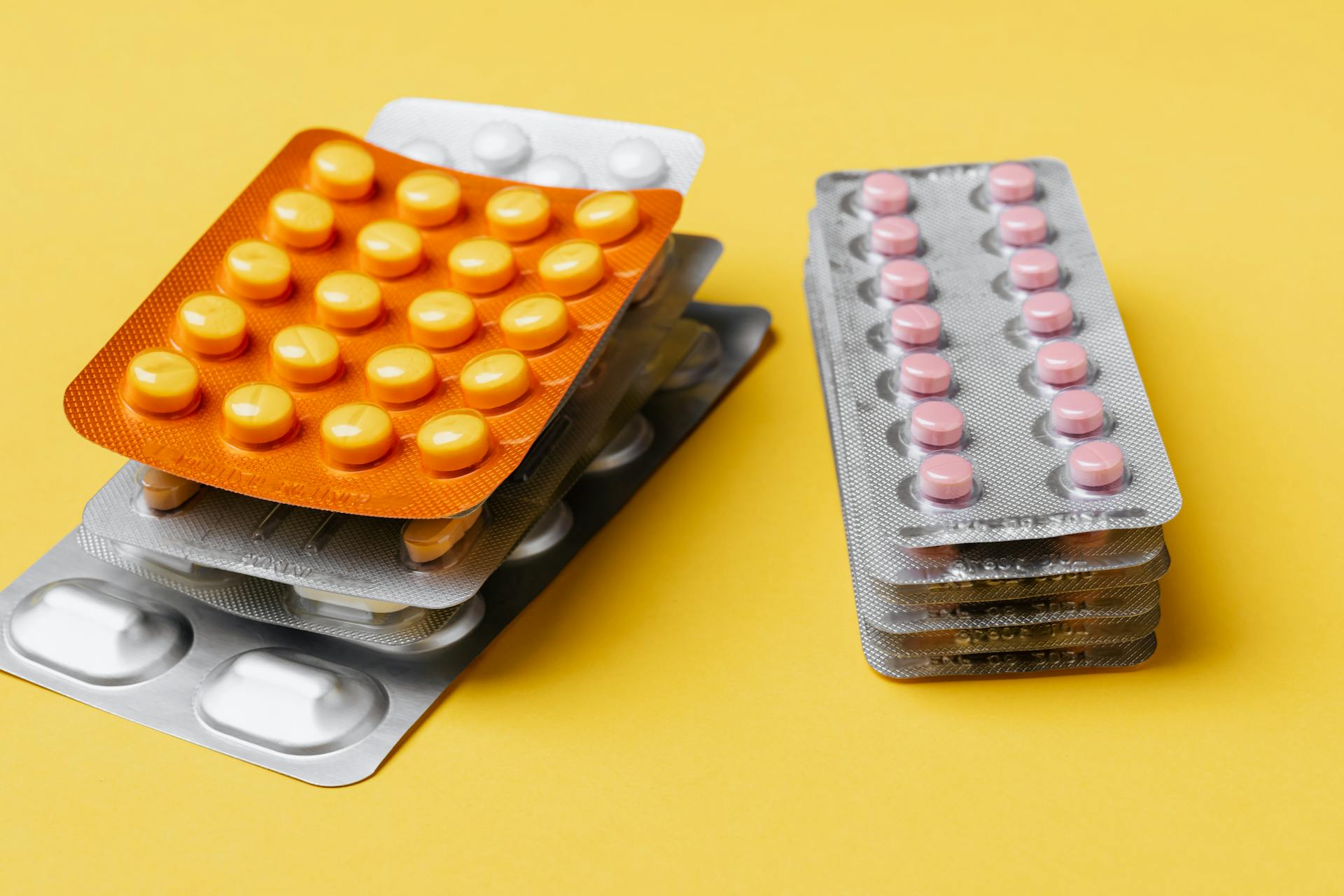
One notable difference between strip and slide blister packaging is the way the product is exposed. In strip packaging, the product is completely hidden between the two layers of foil, whereas in slide blister packaging, the product is partially exposed.
Slide blister packaging uses a type of blister that easily opens and closes by a sliding mechanism, making it convenient for consumers to access the product.
This sliding mechanism allows consumers to easily open and close the blister pack, which can be a major advantage for certain types of products.
Design and Manufacturing
You can customize slide blister designs with Elsepack, bringing your design in advance with all specifications. This allows for competitive prices and an in-house pattern and mould design capability.
Elsepack has an in-house tooling design capacity for slide blisters, but you'll need to incur all the charges. This cost-effective solution is suitable for branding and marketing needs.
The materials used in manufacturing blister packs include Polyvinyl Chloride (PVC), Polyvinylidene Chloride (PVDC), Polychlorotrifluoroethylene (PCTFE), Polypropylene (PP), Polyethylene (PET), Cyclic Olefin Copolymers (COC), and Laminated Aluminum Foil.
Here's an interesting read: Cosmetic Packaging Design Companies
Mold and Manufacturing Co-Location

Having the mold and manufacturing process under one roof can be a game-changer for businesses.
Flexible and fast design changes are possible when the mold and manufacturing process are co-located, allowing for quick adjustments to be made as needed.
This approach also enables low R&D and cost manufacturing, which can be a significant advantage for businesses looking to streamline their operations.
You can also quickly fix unexpected mold failure in mass production, minimizing downtime and lost productivity.
Here are some key benefits of co-locating mold and manufacturing:
- Flexible and fast design changes
- Low R&D and cost manufacturing
- Quick fix for unexpected mold failure in mass production
- Green packaging design and manufacture mold under the same roof
Mold Selection
Mold selection is a crucial step in the design and manufacturing process of slide blister packaging. It's essential to choose the right mold to ensure high-quality packaging.
There are several types of molds to choose from, including plaster, copper, and aluminum molds. Plaster molds are easy to make and cost-effective, but they may not produce the most transparent blisters.
Copper molds, on the other hand, are more durable and produce high-quality blisters with good transparency. They are also relatively affordable and are often used for mass production.
Curious to learn more? Check out: Custom Quality Control Stickers
Aluminum molds are the most precise and produce blisters with beautiful contours and angles. However, they are the most expensive option and require a 3D design or product sample to create.
Here's a brief comparison of the different types of molds:
Ultimately, the choice of mold will depend on your specific application requirements and budget.
Thermoforming Process
Thermoforming is a straightforward process used in blister packaging manufacturing. It's a technique that involves heating a plastic sheet.
The first step in thermoforming is heating the plastic sheet. This process is crucial in shaping the plastic into the desired form.
Next, the heated plastic sheet is molded to form the shape of the slide blister. This step requires precision to ensure the final product meets the desired standards.
The molded plastic sheet is then trimmed to have the desired slide blister product. Trimming is an essential step to achieve the perfect shape and size.
Explore further: Plastic Blister Pack
After trimming, the final slide blister is cooled. Cooling is a critical step to ensure the plastic is stable and ready for inspection.
Finally, the quality of the final thermoformed slide blister is inspected. This step ensures that the product meets the required standards and is ready for packaging.
Here's a summary of the thermoforming process:
- Heating of a plastic sheet
- Molding of the heated plastic sheet
- Trimming to achieve the desired shape and size
- Cooling of the final product
- Inspecting quality of the final product
Elsepack Tooling Design Capability
Elsepack's tooling design capability is a significant advantage for buyers. They can custom thermoform slide blisters to your unique specification.
Elsepack has an in-house pattern and mould design capability, which allows for flexible and fast design changes. This means you can easily adjust your design without incurring additional costs.
You can also take advantage of Elsepack's in-house tooling design capacity for your slide blister. However, be aware that you will need to cover all the charges incurred while using this facility.
Elsepack's manufacturing process has several benefits, including low R&D and cost manufacturing. This is because they can self-develop and manufacture molds in-house.
Here are some of the key benefits of Elsepack's mold and sliding blister packaging manufacturing in the same factory:
- Flexible and fast design changes
- Low R&D and cost manufacturing
- Quick fix for unexpected mold failure in mass production
- Green packaging design and manufacture mold under the same roof
Enhanced Product Visibility
Blister packaging is transparent, which allows customers to clearly see the product before they buy. This level of visibility can be particularly effective for products like mascara, eyeliner, and promotional lipstick in cosmetics, where appearance is key.
The transparent nature of blister packaging also allows for attractive and eye-catching packaging designs, such as bright colors, that can grab customers' attention and make a product stand out on store shelves.
You might enjoy: Transparent Tetra Pack
Minimal Movement
In blister packaging, the products inside are likely to stay secure, minimizing potential accidental damage and deterioration.
This design ensures that products are well-protected during transportation and storage, which is especially important for fragile items.
Minimal movement in the packaging also reduces the risk of products getting scratched or damaged, which can be a major concern for manufacturers.
By keeping products stable and secure, blister packaging helps to maintain their quality and appearance.
Materials and Manufacturing
Slide blister packs can be made from a variety of materials, each with its own unique properties and benefits. Polyvinyl Chloride (PVC) offers structural rigidity and protection for pharmaceutical items.
For certain products, a laminated barrier made from Polyvinylidene Chloride (PVDC) can prevent exposure to moisture and oxygen. This is particularly useful for products that require a high level of protection.
Polypropylene (PP) is another popular material, offering a barrier that protects the product and is eco-friendly due to its recyclability. The material thickness of a slide blister pack will depend on the weight of the product being packed, with heavier products requiring thicker materials.
Here are some common materials used in slide blister pack manufacturing:
Material Thickness and Size
Material thickness and size of slide blister packs are crucial factors to consider, especially for small products that require secure packaging.
Slide blister packs are commonly used for small products, which means they come in small sizes. You can discuss specific size requirements with the manufacturer.
The material thickness of a slide blister pack depends on the weight of the product being packed. Heavier products require relatively thick material to ensure stability.
In most cases, the material thickness will be adjusted accordingly to accommodate the product's weight. This ensures the product remains secure during packing.
Materials for Manufacturing
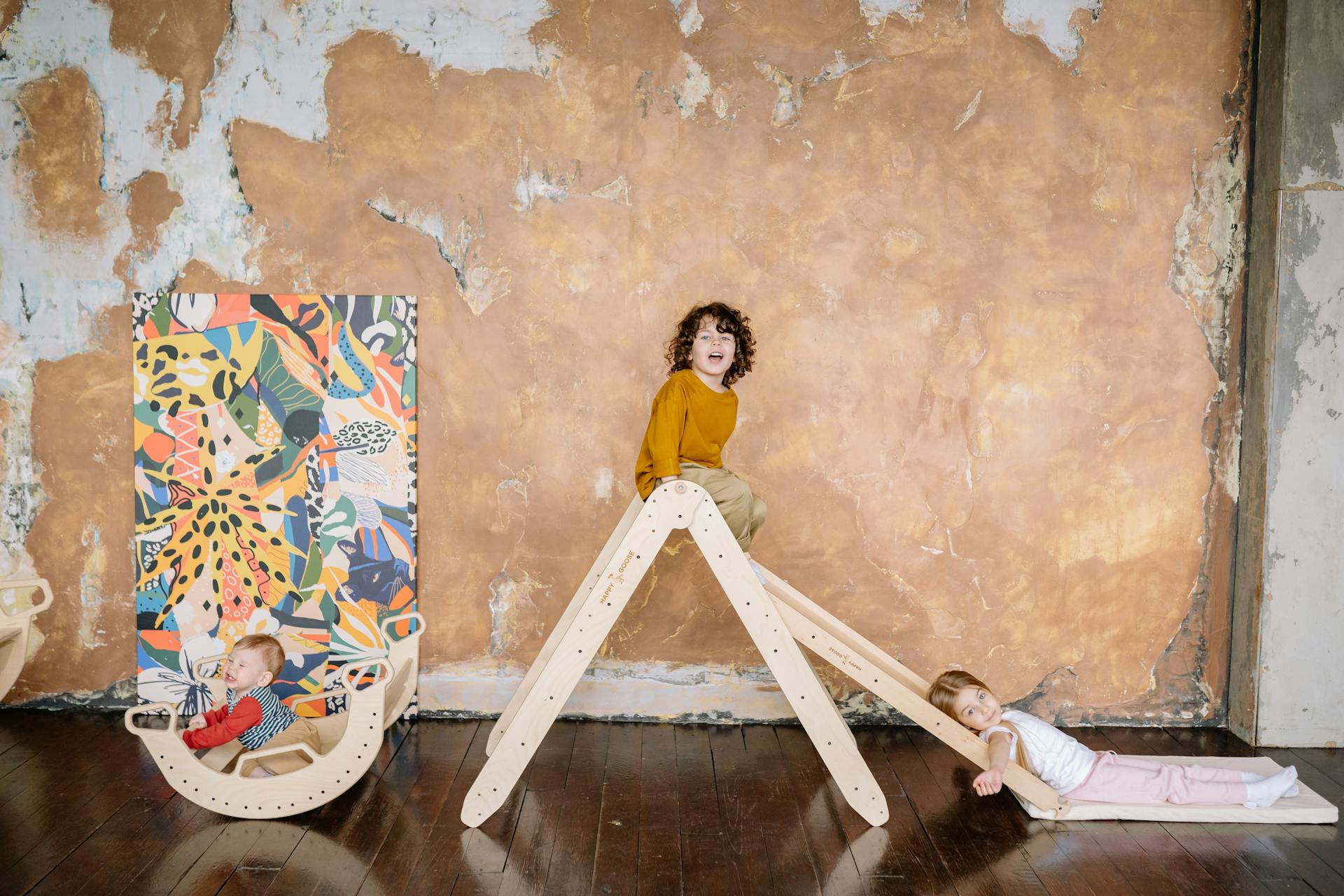
Polyvinyl Chloride (PVC) is a popular choice for blister packs due to its structural rigidity and ability to protect pharmaceutical items.
Polyvinylidene Chloride (PVDC) is used as a laminated barrier to prevent moisture and oxygen from affecting the product.
Polychlorotrifluoroethylene (PCTFE) is used as a coating to protect chemical formulations, adding an extra layer of protection to blister packs.
Polypropylene (PP) offers a barrier that protects the product and is eco-friendly because it's easy to recycle.
Polyethylene (PET) is easy to mold into the correct shape of the item, making it a practical choice for blister packaging.
Cyclic Olefin Copolymers (COC) provides protection and prevents damage to consumer goods and pharmaceutical products, easily adapting to the shape of the product.
Laminated Aluminum Foil helps maintain the quality and standards of the product by providing a secure and protective barrier.
Expand your knowledge: Contract Pharmaceutical Packaging Companies
Thermoforming Machine Working Principle
Thermoforming is a thermal processing method used in sliding blister packaging manufacturing. It involves heating and softening a thermoplastic sheet.
The thermoplastic sheet is cut into a certain size before the process begins. Heating and softening the plastic sheet is a crucial step in the thermoforming process.
A difference in atmospheric air pressure and mechanical pressure is used to make the sheet deformation. This deformation is what allows the sheet to take on the shape of the mold.
The sheet is then covered on the surface of a specific mold. After cooling, the deformation is set, and the sheet is trimmed to complete the process.
Here are the key steps involved in the thermoforming process:
- Heating of a plastic sheet
- Molding of the heated plastic sheet
- Trimming to have the desired shape
- Cooling of the final product
- Inspecting quality of the final product
Key Advantages and Benefits
Slide blister packaging offers several advantages and benefits that make it a popular choice for packaging small products. One of the key benefits is its low mold development cost, typically around $100.
The development cycle is also relatively short, taking only 5-7 days, which is a significant time-saving compared to other packaging methods. This is because advanced thermoforming equipment can produce high volumes quickly.
A single thermoforming machine can have a daily capacity of over 50K, making it an efficient way to produce large quantities of packaging. This efficiency is further enhanced by the use of fully automatic slide blister packaging machines, which can produce up to 20K units per day.
Slide blister packaging also offers a clean and neat presentation, with accurate sizing and minimal waste. This makes it an attractive option for companies looking to present their products in a professional and visually appealing way.
Some of the key features to consider when selecting a slide blister pack include water-resistance, UV protection, and oxygen and moisture barrier features. These features can help ensure that the product remains fresh and protected during storage and transportation.
Here are some of the key features to look for in a slide blister pack:
- Water-resistance features
- Slide blister pack color
- Thickness of the slide blister pack
- UV protection features
- Designs and size of slide blister pack
- Tamper evident features
- Material type for the slide blister
- Product visibility features
- Oxygen and moisture barrier features
Product Suitability and Requirements
For sliding plastic packaging, a product's volume and weight should be relatively small, and its appearance should be bright and attention-grabbing. This type of packaging is suitable for products like mascara, eyeliner, and promotional lipstick in cosmetics.
The quality of sliding blister packaging is crucial, and there are two key things to look out for. The first is whether the paper card and the sliding blister match, with a supplier of good quality control adjusting the position of the blister card printing and the blister hanging hole for a good look.
A smooth sliding blister track is also essential, typically formed by three flaps to the back edge that hold the blister card in place.
A unique perspective: Blister Card Packaging Machine
Is Your Product Suitable for Plastic?
If your product has a relatively small volume and weight, it's likely suitable for sliding plastic packaging. This type of packaging is great for products that need to stand out, like bright-colored cosmetics.
For instance, mascara, eyeliner, and promotional lipstick are all good examples of products that can benefit from sliding blister packaging. The back of the package can even have a strong paper card for printing advertisements or instructions.
Requirements for Suppliers
When selecting a supplier for high-quality sliding blister packaging, there are certain requirements to look out for. A good supplier will pay attention to the alignment of the paper card and the sliding blister, ensuring they match perfectly.
The quality of the paper card and the sliding blister is crucial. A supplier with good quality control will adjust the position of the blister card printing and the blister hanging hole to ensure a visually appealing package.
To gauge a supplier's production experience, examine the size and smoothness of the sliding blister track. Typically, this track is formed by three flaps to the back edge of the package, holding the blister card in place.
A well-manufactured sliding blister pack should have a smooth and even track. This attention to detail is a testament to the supplier's expertise in producing high-quality packaging.
Suggestion: High End Packaging Companies
Application Examples
Slide blister packaging is a versatile and effective way to showcase products. The high-transparency PVC/PET material used in this type of packaging allows customers to see the inside products.
If you have colorful or beautifully designed products, consider using clear blister packaging. The transparent material will let the products shine.
The shape of the blister can be customized to fit your product's design. You can choose a shape that matches your product's shape or create a larger cavity to hold all the products.
You can choose between two styles of blister cavities: one that matches the product shape and another that's big enough to hold all the products.
Frequently Asked Questions
What is the difference between a blister pack and a bubble pack?
Blister packs and bubble packs differ in size, with bubble packs being a larger, customized version. Bubble packs offer more space for products, making them ideal for larger items or multiple items.
Sources
Featured Images: pexels.com