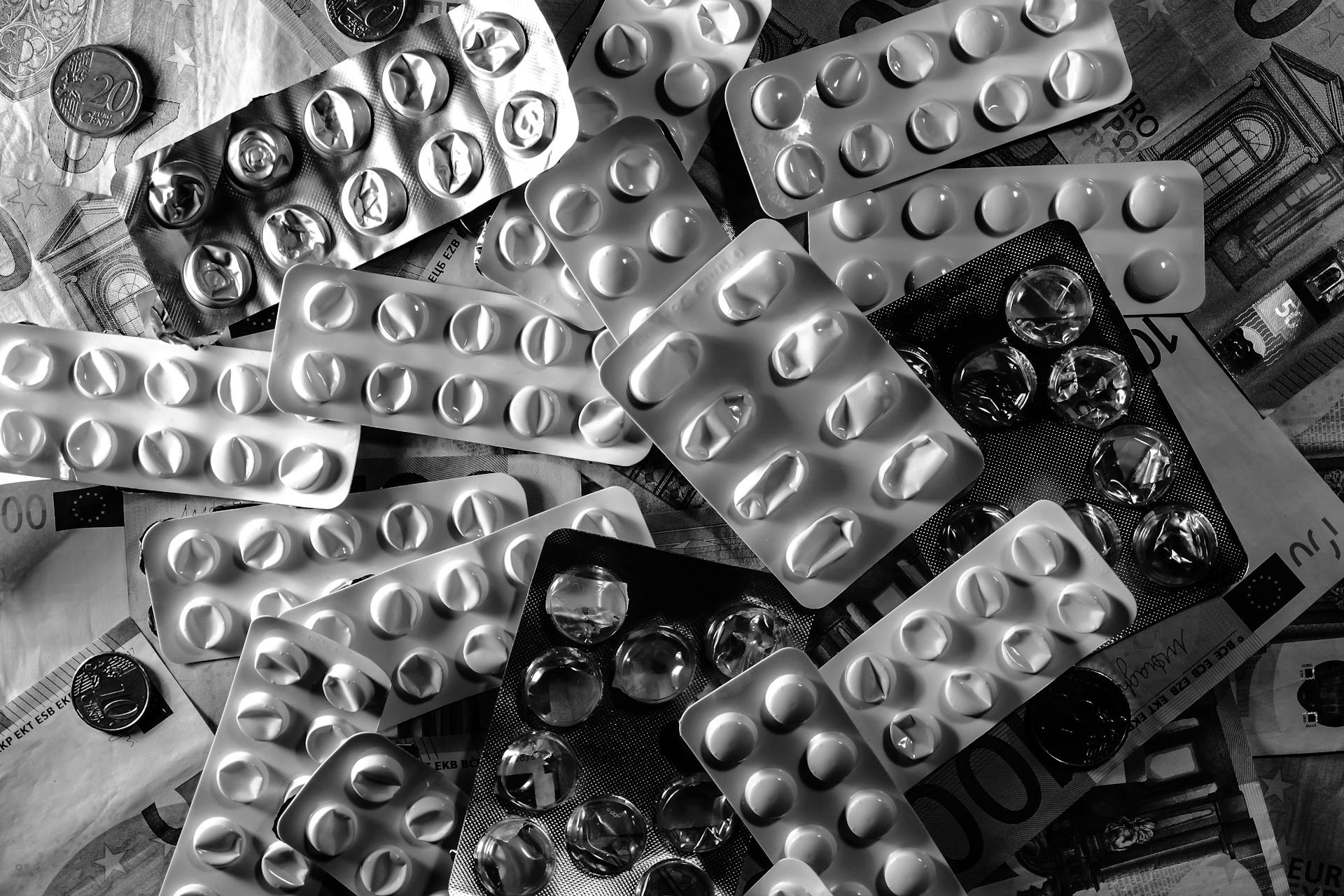
Plastic blister packs are a common sight in stores and online marketplaces, but have you ever stopped to think about what they're made of and how they're used? They're typically made from a combination of plastic and aluminum.
The plastic used in blister packs is usually a type of plastic called polyvinyl chloride, or PVC. This type of plastic is durable and can be molded into various shapes.
Blister packs are designed to protect products from damage during shipping and storage. They're often used to package small electronics, cosmetics, and pharmaceuticals.
A typical blister pack consists of a plastic base, a cavity, and a backing card. The plastic base is usually made from a type of plastic called polystyrene, or PS.
Benefits and Drawbacks
Blister packaging has several benefits that make it a popular choice for packaging products.
It helps catch the consumer's eye easily by letting the product speak for itself, making it stand out in stores.
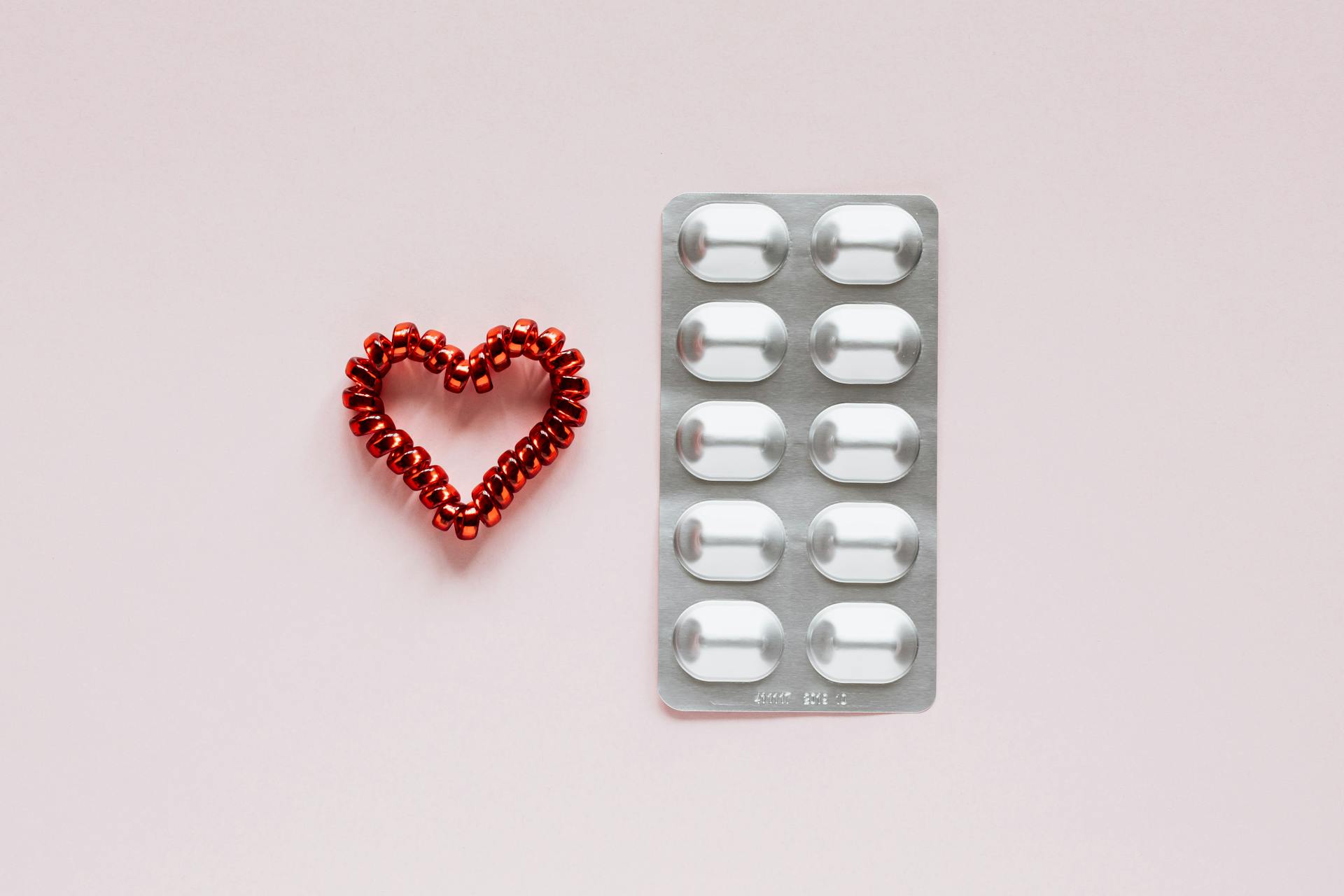
Products in blister packs are shielded from damage and kept clean, and the packaging shows when it has been tampered with.
This makes it harder for shoplifters to conceal, which is a major advantage for supermarkets that struggle with shoplifting.
Blister and clam packaging is also very light, which lowers transport costs.
Clam packaging is simple to recycle as it's made purely of plastic.
The packaging can be marked so each little pocket holding a tablet or pill is numbered or listed by days, helping people monitor their medication routine.
Here are some of the key benefits of plastic blister pack packaging:
- Visual impact
- Protection
- Harder to steal
- Lightweight
- Easily recycled
- Helps with following routines for medication
Applications and Uses
Plastic blister packs are incredibly versatile, used in a wide range of applications, from pharmaceuticals to consumer electronics.
Their tamper-evident nature is a major advantage, providing an added layer of security and peace of mind for consumers.
In pharmaceuticals, blister packs are often used to package tablets, creating a sterile environment that helps maintain the product's effectiveness.
The clear visibility of the product in blister packs also enhances consumer trust and product appeal, making it easier for customers to choose the right product.
Consumer Goods
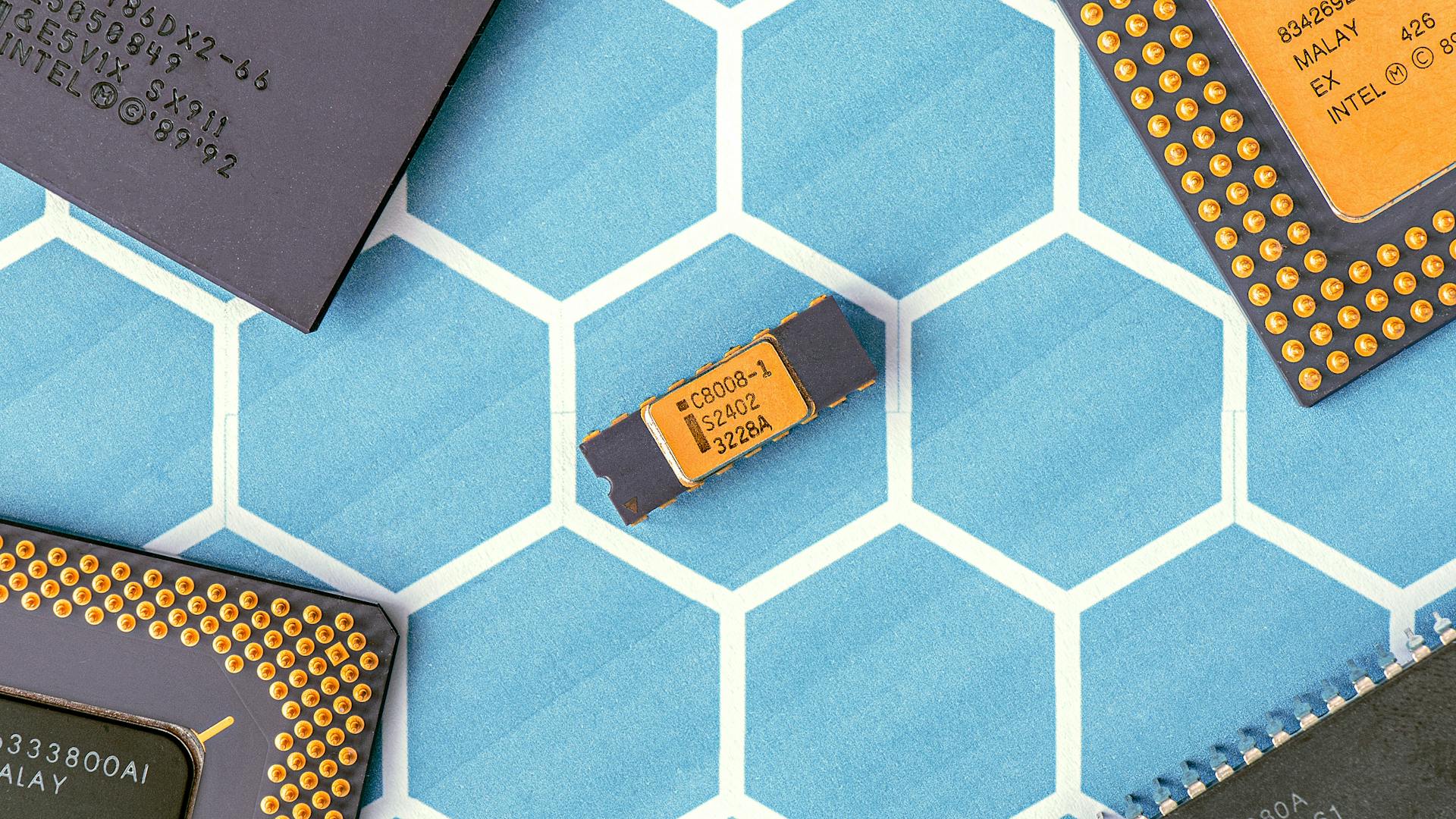
Consumer goods often come in blister packs that contain toys, hardware, and electrical items. These packs are made with a specially designed paperboard card and clear pre-formed plastic, such as PVC.
The transparent plastic allows consumers to visually examine the product, which can enhance consumer trust and product appeal. This is similar to how pharmaceutical blister packs work.
The plastic shell is vacuum-formed around a mold to snugly contain the item inside. The card is colored and designed depending on the item, and the PVC is affixed to the card using heat and pressure.
Sometimes, with large items, the card has a perforated window for easy access. This design allows consumers to easily open the package without damaging the contents.
Related reading: Blister Card Sealing Machine
What Products Suit?
Blister packs are perfect for packaging products that need extra protection. They're especially useful for electronic goods and accessories, like USB drives, cables, and headphones.
If you've ever tried to store small toys, you know how easily they can get damaged. Blister packs can help prevent that by keeping them safe and secure. For example, they're great for packaging toys, stationery, and DIY goods.
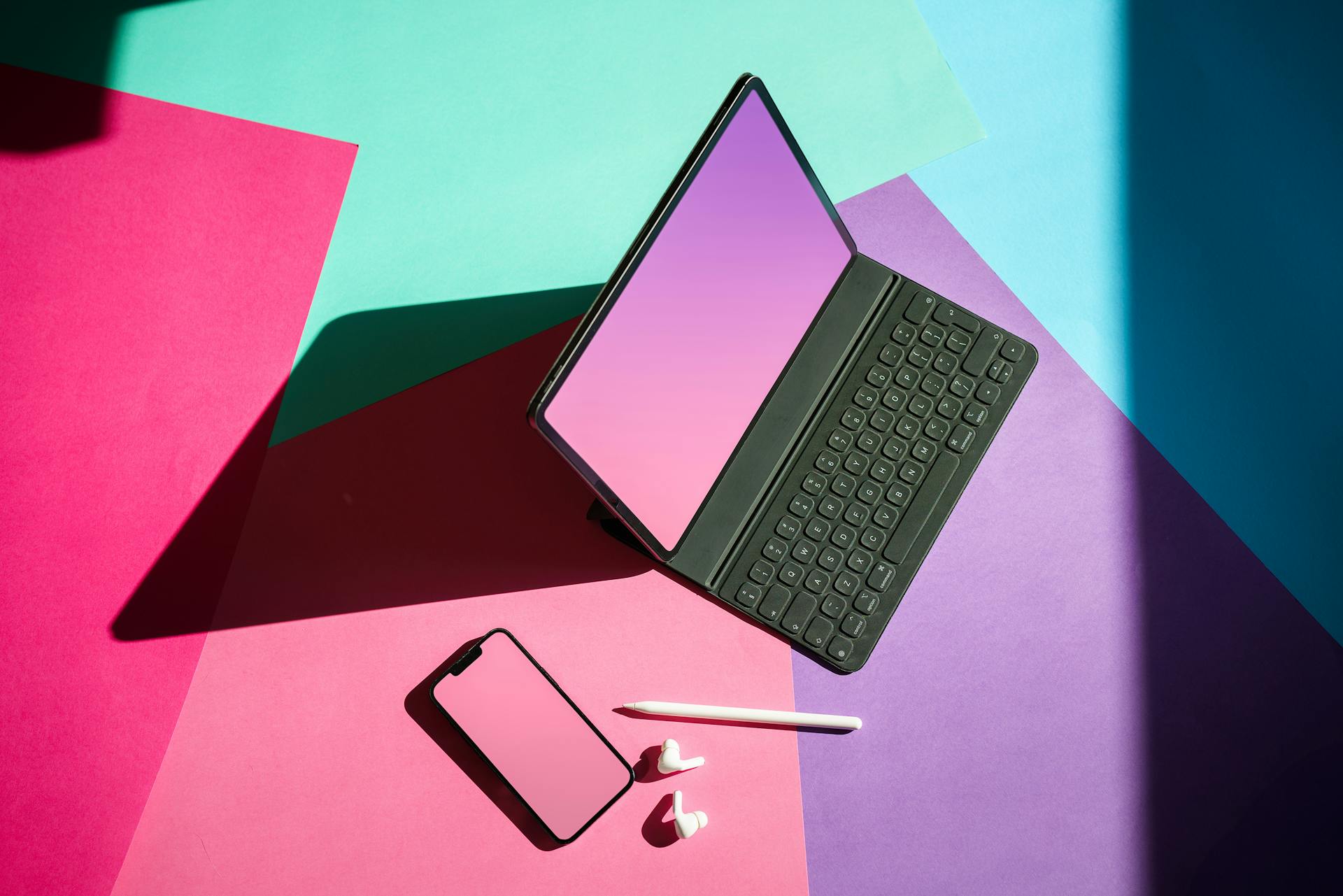
Batteries and toothbrushes also benefit from blister packaging, as they can be easily damaged or contaminated. And if you've ever tried to store printer ink cartridges, you know how delicate they can be - blister packs are a great solution.
Some products, like tablets and capsules, require blister packaging to keep them clean and uncontaminated. And if you're looking for a tamper-proof solution, blister packs are a great option - any tampering will be visible from a break in the packaging.
Here are some examples of products that suit blister packaging:
- Electronic goods and accessories (e.g. USB drives, cables, headphones)
- Toys
- Stationery (e.g. pens, drawing pins, paper clips, superglue)
- Batteries
- Toothbrushes and dental floss
- DIY goods (e.g. screws, nails, nuts and bolts)
- Tablets and capsules
- Products with delicate parts
- Products that are vulnerable to breaking (e.g. printer ink cartridges)
Unit Dose Pharmacy
Blister packs are commonly used as unit-dose packaging for pharmaceutical tablets, capsules, or lozenges.
In the US, blister packs are mainly used for packing physician samples of drug products or for over-the-counter (OTC) products in the pharmacy.
Blister packs can provide barrier protection for shelf life requirements, and a degree of tamper resistance.
The main advantages of unit-dose blister packs are the assurance of product/packaging integrity and the ability to create a compliance pack or calendar pack.
Suggestion: Unit Dose Pack
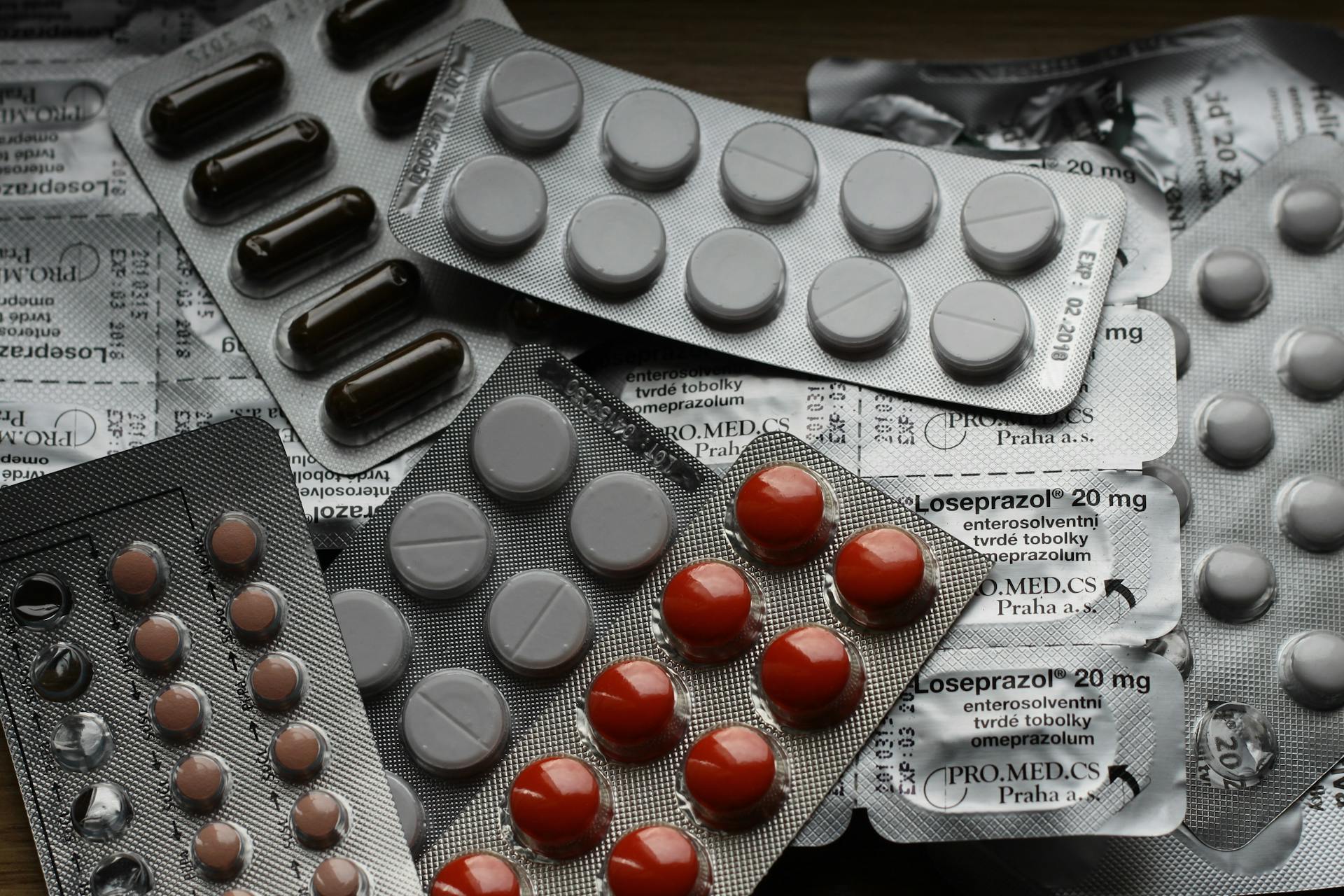
A compliance pack or calendar pack is created by printing the days of the week above each dose.
Blister packs are created by a form-fill-seal process at the pharmaceutical company or designated contract packer.
A form-fill-seal process means the blister pack is created from rolls of flat sheet or film, filled with the pharmaceutical product, and closed (sealed) on the same equipment.
There are two types of blister machine designs: rotary and flat-plate.
The choice of design depends on the mechanism for sealing the lidding foil.
In some parts of the world, the pharmaceutical blister pack is known as a push-through pack (PTP), which is an accurate description of two key properties.
See what others are reading: Blister Packaging Machine Pharmaceutical Industry
Materials and Types
Plastic blister packs are made from a variety of materials, with PET being a popular choice due to its transparency, strength, and ability to hold its shape well.
PET is widely used in blister packaging because it's transparent, strong, and holds its shape well, making it ideal for showcasing products.
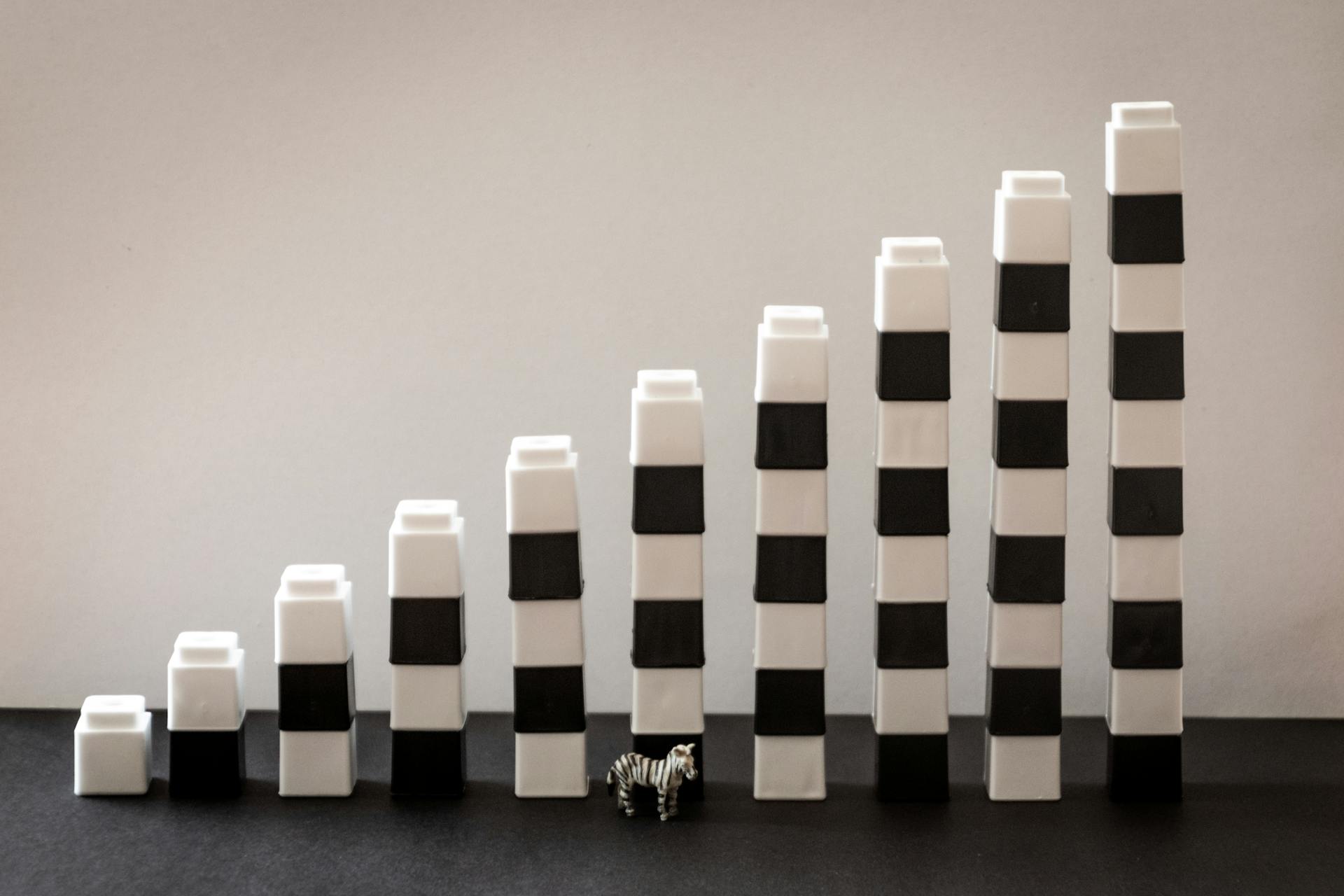
PVC, on the other hand, is also commonly used in blister packaging, particularly in medical applications, due to its low cost and ease of thermoforming.
PVC sheets for pharmaceutical blisters are typically 250 μm (0.25 mm) in thickness and can be coated or laminated to increase their protective properties.
The most common types of blister packaging include plastic blister, full-face seal blister, and trapped blister, each serving a specific purpose and offering unique benefits.
Common Plastic Types
PVC is a common material used in blister packaging due to its low cost and ease of thermoforming.
The principal advantages of PVC are the low cost and the ease of thermoforming. The main disadvantages are the poor barrier against moisture ingress and oxygen ingress.
PVC sheets for pharmaceutical blisters are typically 250 μm (0.25 mm) in thickness.
Most PVC sheets for pharmaceutical blisters are 250 μm (0.25 mm) in thickness. Typical values for the Water Vapor Transmission Rate (WVTR or MVTR) of a 250 μm PVC film are around 3.0 g/m per day measured at 38 °C (100 °F) and 90% RH.
A unique perspective: Contract Pharmaceutical Packaging Companies
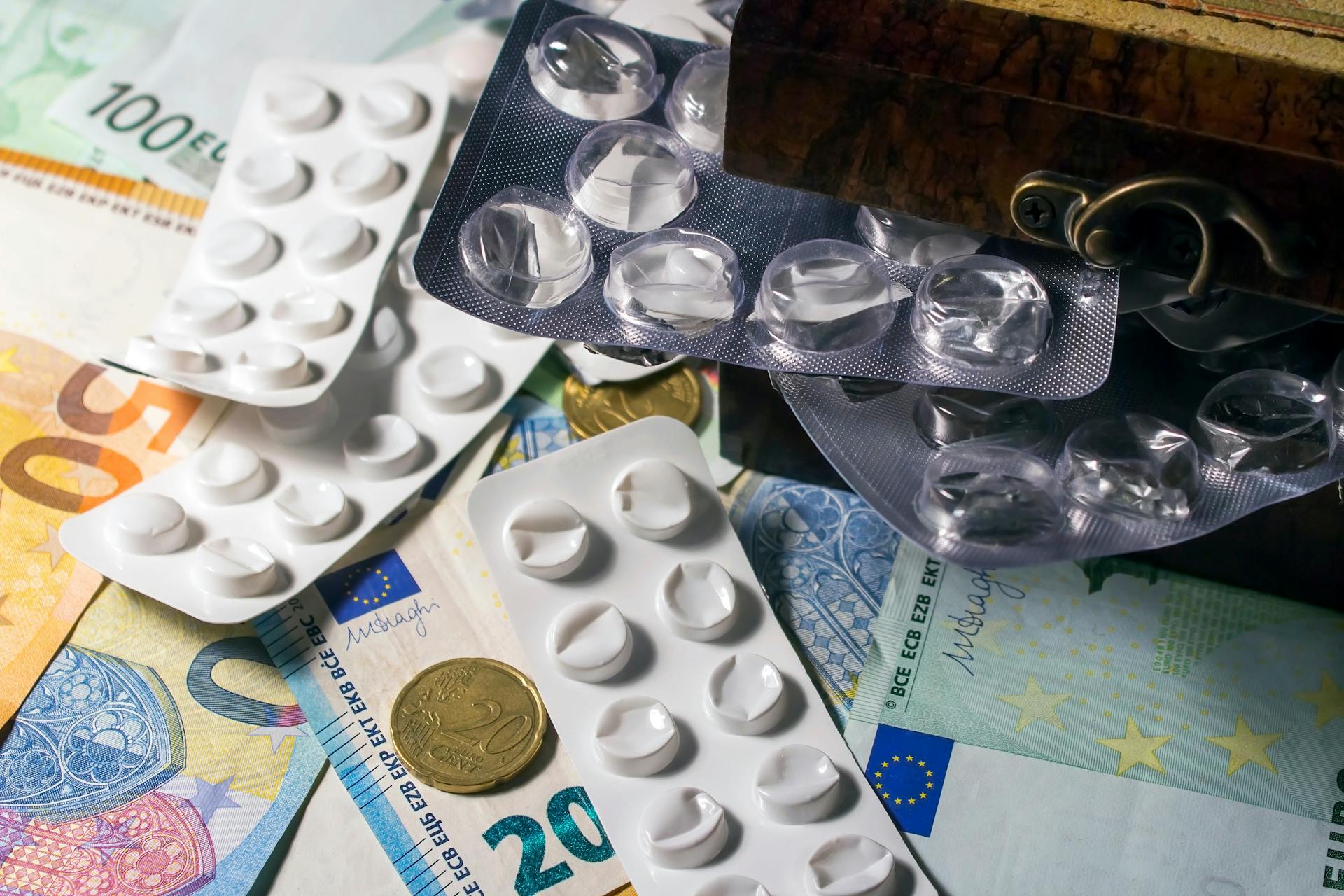
PCTFE can be laminated to PVC to obtain very high moisture barrier.
Typical constructions used for pharmaceutical products are 250μ PVC film laminated to 15μ-150μ PCTFE film. Duplex structures are PVC/PCTFE and triplex laminates are PVC/PE/PCTFE.
PET is a common alternative to PVC, as it's transparent, strong, and holds its shape well.
PVC is slightly less transparent and can sometimes appear a little yellow compared to PET.
A unique perspective: Shrink Film Labels
Clamshell
Clamshell packaging is a type of hinged blister used for various products.
It's often used as a security package to deter package pilferage for small high-value items, like consumer electronics.
Clamshell packaging consists of one sheet folded over onto itself and sometimes fused at the edges.
They can be securely heat sealed, making them difficult to open by hand to deter tampering.
A pair of scissors or a sharp knife is often required to open them, although these are often sold in similar packages.
Trauma shears are also effective at opening packaging of this type.
Care must be used to safely open some of these packages, as opening it without care can result in injury; 6,000 Americans are sent to the emergency room each year by injuries suffered in opening such packages.
Intriguing read: Opening Plastic Blister Pack
Types of Containers
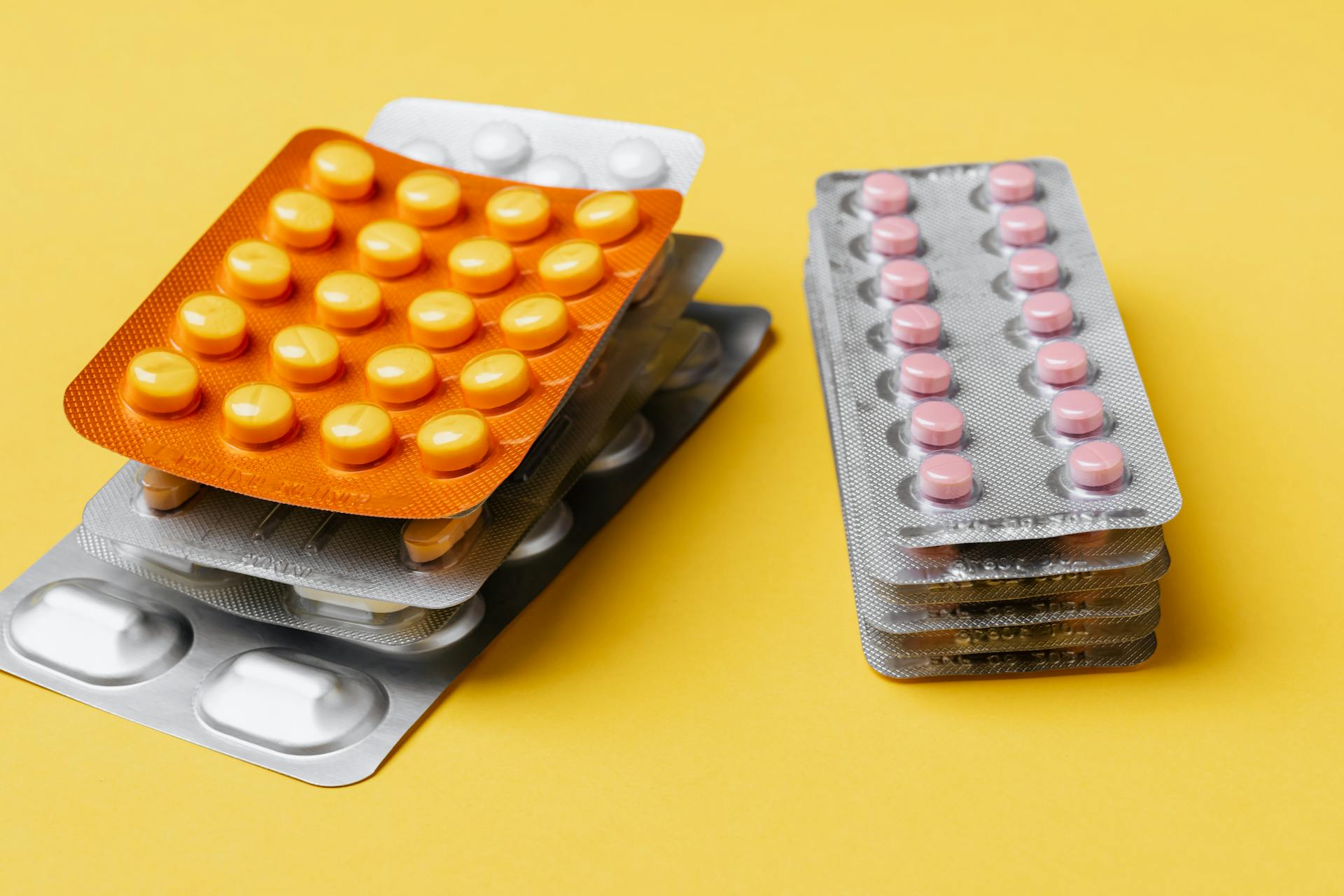
Types of Containers are crucial for packaging products.
The most common type of container is the plastic blister, which is moulded around the product and heat-sealed to a cardboard backing.
This type of container is fairly inexpensive and generally used for products made in large volumes.
For stronger and better-looking packaging, the plastic blister surrounds not only the entire product but the card backing too.
The blister is either heat-sealed to the card or slid through additional plastic pieces on each side.
Another type of container is the full-face seal blister, which covers the full size of the card.
It has flanges that wrap around it, and the card is slid, and sometimes stapled, into place.
A trapped blister is similar to a traditional blister pack, but the plastic part that sticks to the cardboard has another piece of cardboard in front of it that fits around the shape of the blister.
This type of container uses no heat-sealing methods, making it cheaper to produce than traditional methods.
Suggestion: Blister Card Packaging Machine
Thermoforming
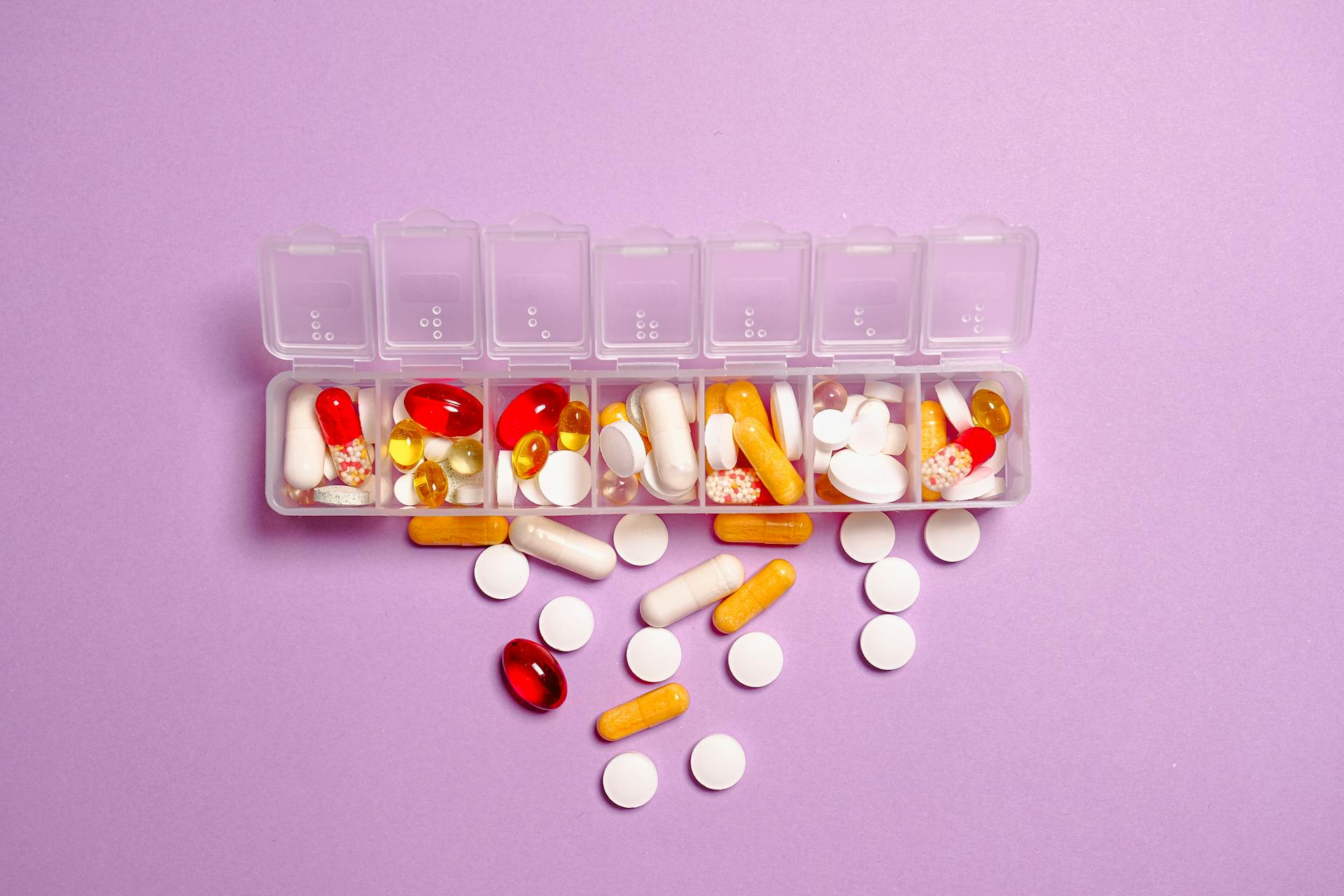
Thermoforming is a process that uses heat to soften plastic, making it pliable and easy to shape. The plastic film or sheet is guided through a pre-heating station on the blister line.
The pre-heating station causes the plastic to soften, allowing it to be formed into a specific shape. This process involves applying a large pressure of 4 to 8 bar, which is equivalent to 58 to 116 psi.
The pressure used in thermoforming is significant, and it's what allows the plastic to take on the shape of the mold. The mold is then cooled, causing the plastic to become rigid again and maintain its shape.
In some cases, a "plug-assist" feature is used to help form difficult shapes. This feature involves physically pushing the warm film down into the cavity, resulting in a blister cavity with a more uniform wall distribution.
You might like: Machine Stretch Wrap Film
Design and Packaging
Plastic blister packs are designed to showcase products in a visually appealing way, often featuring a clear plastic shell that wraps around the product. This design helps attract customers and make a good first impression.
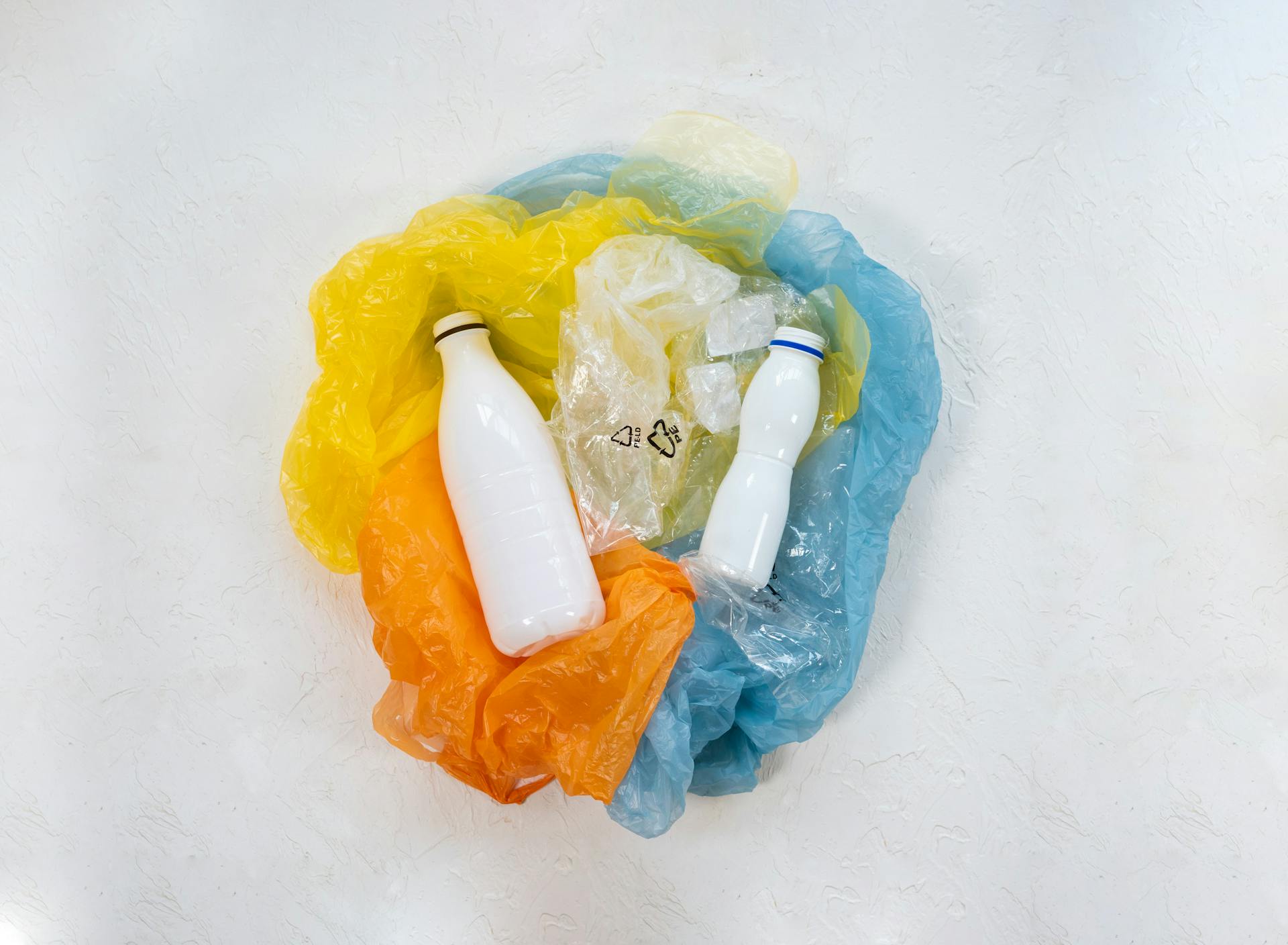
The size and shape of the blister pack are carefully chosen to fit the product snugly, ensuring it is secure and easy to handle. A typical blister pack is 1-2 inches thick and 2-4 inches wide.
The plastic used in blister packs is usually a type of polystyrene or polyvinyl chloride (PVC), which is lightweight and inexpensive. These materials are also easy to mold into the desired shape.
To prevent the product from moving around inside the blister pack, a backing card is often used to keep it in place. This card is usually made of cardboard or paper and is attached to the back of the blister pack.
The blister pack design also includes a perforated line that allows the product to be easily removed and the packaging to be recycled.
Cost and Sustainability
Blister packing is not a low-cost option, especially for small quantities, but the costs can be spread across many products if a large number of units are packed.
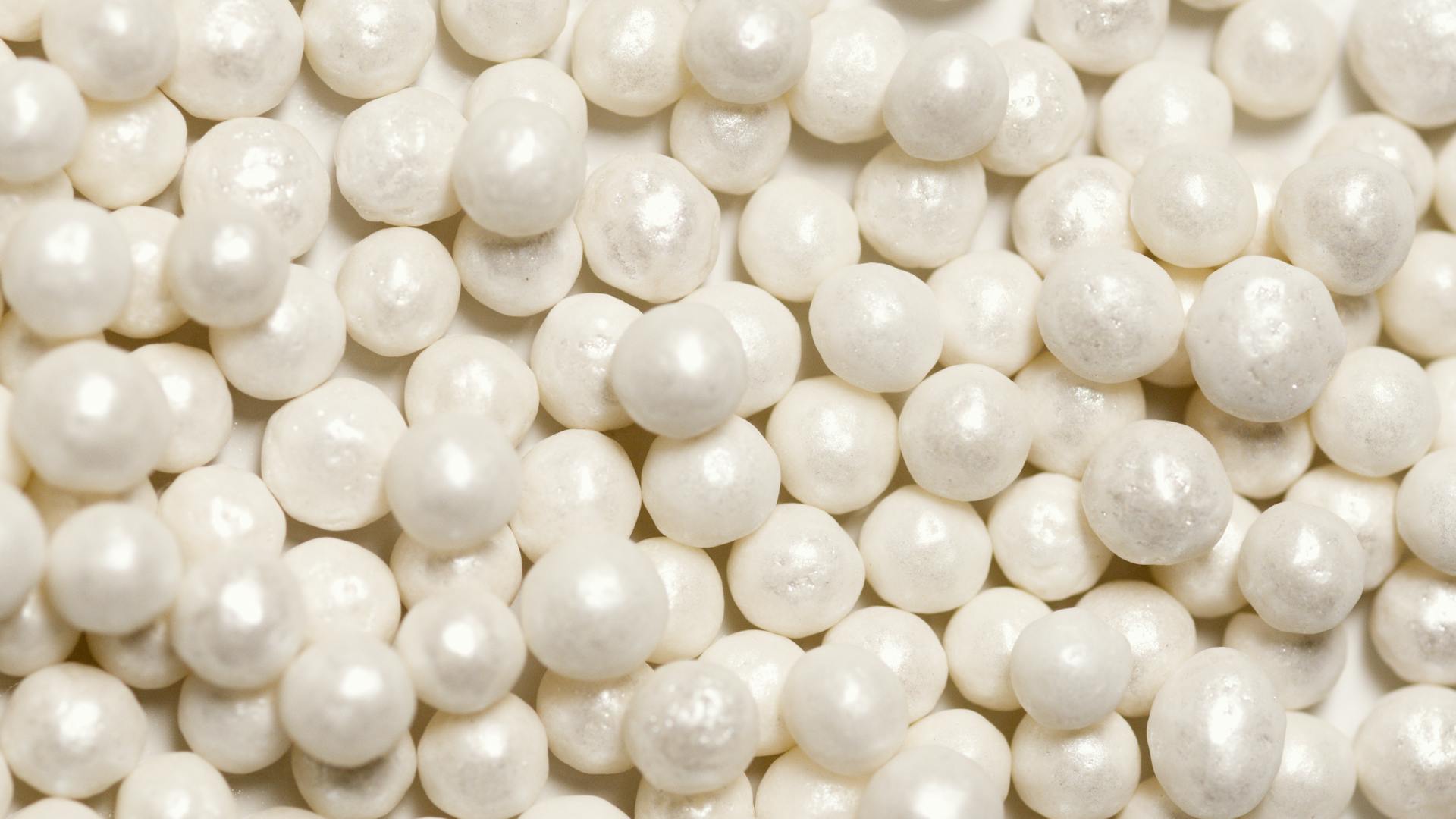
Producing a traditional blister pack is quite expensive to set up compared to a single carton, but clamshell packaging can often be sourced as an “off the shelf” product, saving on set-up costs.
The shift towards sustainability has influenced the blister packaging sector, with an emphasis on creating plastic blister options that can be easily recycled.
Many local councils now recycle blister packs, but it's always worth checking before throwing anything away, as some councils don't recycle them.
Cost and Sustainability
The cost and sustainability of blister packaging is a complex issue.
Blister packs can be more difficult and costly to recycle due to the different materials used, such as PET or PVC and aluminium.
Many local councils now recycle blister packs, but it's always worth checking before throwing anything away.
Empty blister packs for tablets/pills aren't recyclable, so you'll need to dispose of these with your normal rubbish.
The industry is working towards sustainability, with some companies producing plastic-free, environmentally friendly blister packaging options.
The introduction of tablet blister packaging that incorporates eco-friendly materials is a testament to the industry's commitment to reducing its environmental footprint.
You can recycle the cardboard box that the blister packs of tablets came in, which is a small step towards reducing waste.
Consider reading: Packaging Materials Foam Sheets
What's the Cost Comparison?
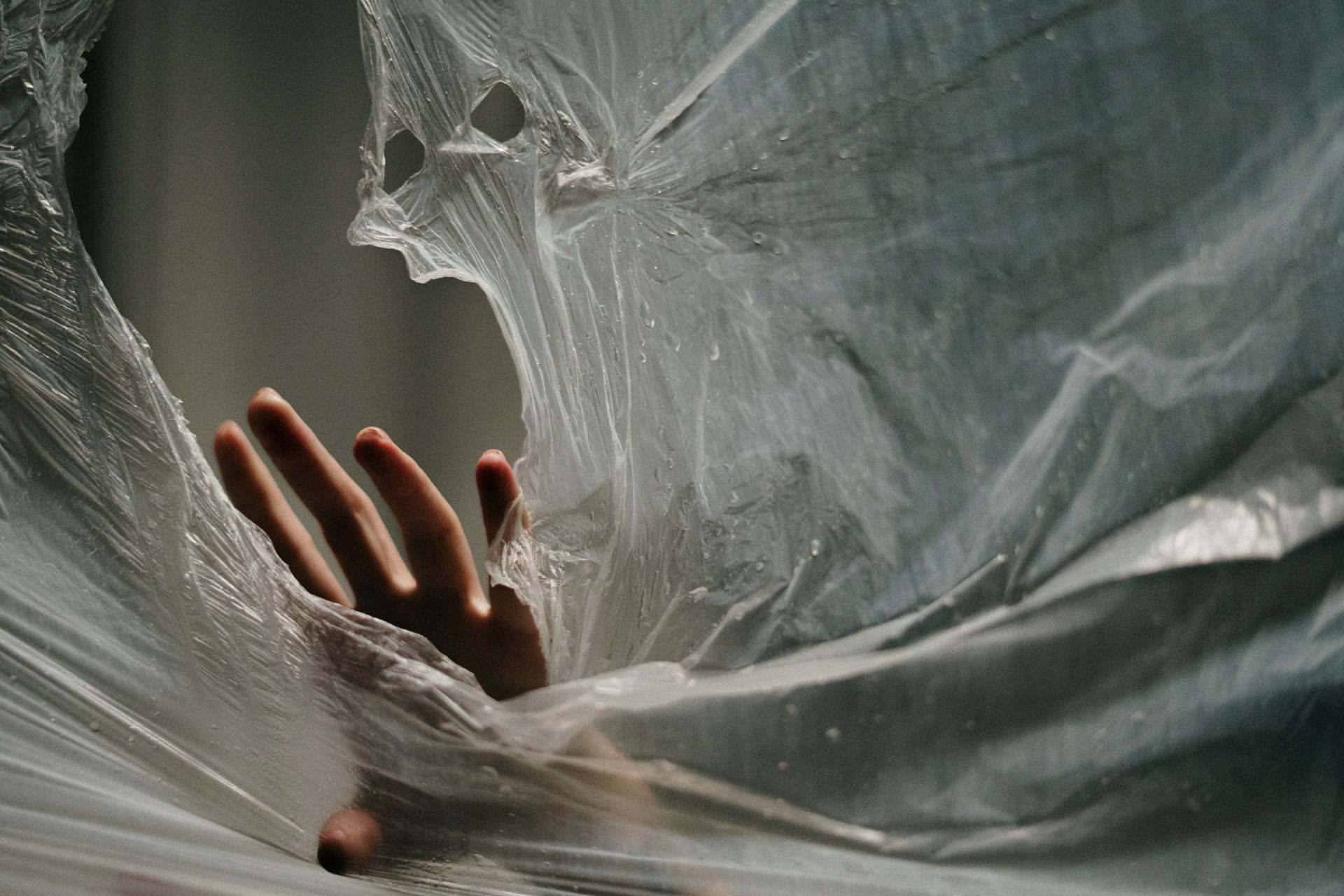
Blister packing isn't the most cost-effective option, especially for small productions. Producing a traditional blister pack can be quite expensive to set up compared to a single carton.
However, if you're packing a large number of units, the costs can be spread across many products, making it more manageable.
Clamshell packaging, on the other hand, can be a very competitive option if used well. It can often be sourced as an "off the shelf" product, saving on set-up costs.
Companies that offer standard sizes and moulds can make clamshell packaging a convenient choice, especially for those who don't need custom designs.
Curious to learn more? Check out: Clamshell Blister Pack
Manufacturing and Machinery
Blister packaging machinery is a specialized piece of equipment designed to form, fill, and seal products in blister packs efficiently.
This machinery can handle various materials, including advanced alu alu blister packaging, which offers superior protection, especially for sensitive products.
The production of blister packaging requires this specialized machinery to ensure high-quality packaging.
Machinery
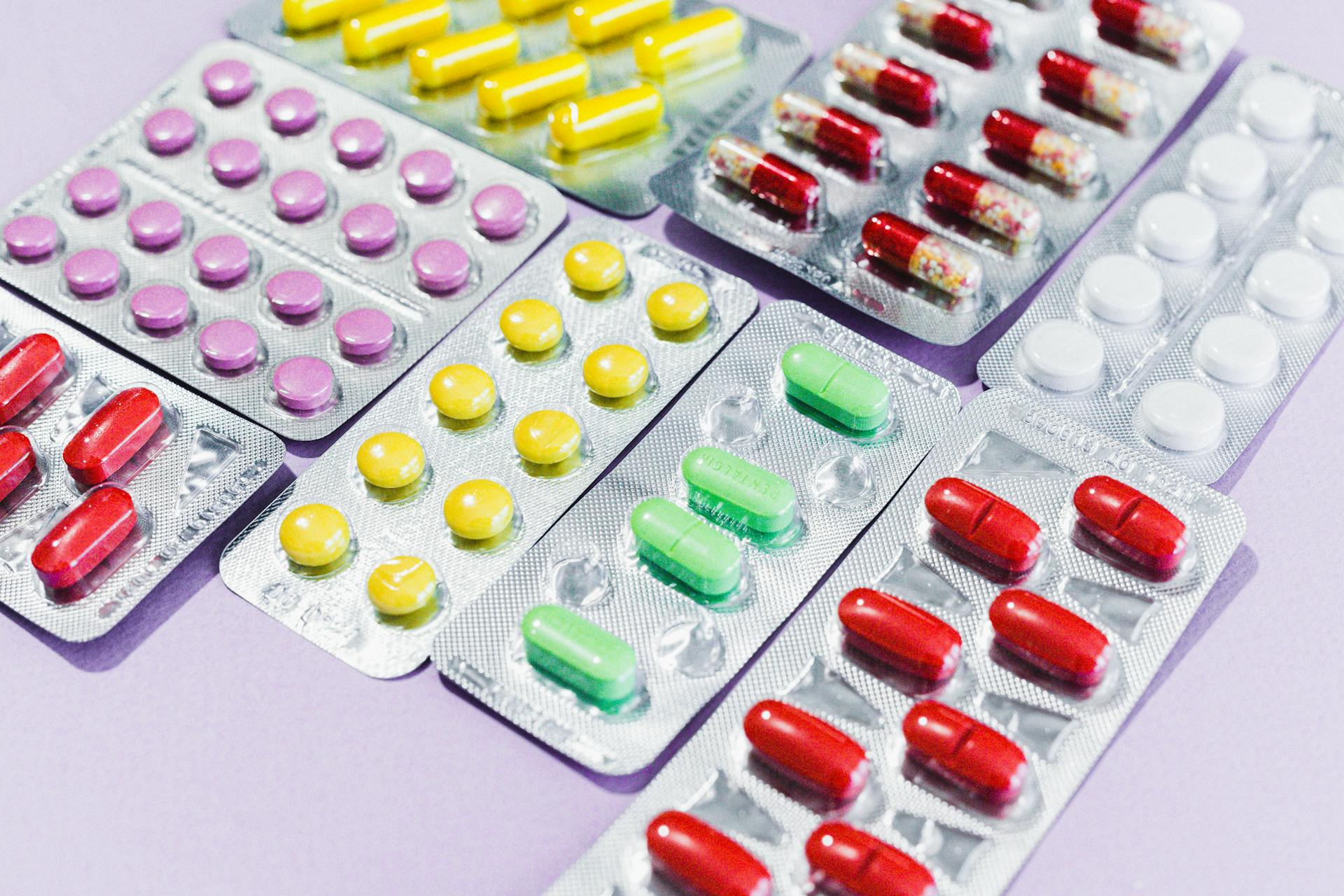
Blister packaging machinery is designed to form, fill, and seal products in blister packs efficiently. This equipment is a crucial investment for any manufacturer looking to produce blister packaging on a large scale.
The machinery can handle various materials, including advanced alu alu blister packaging, which offers superior protection for sensitive products.
The production of blister packaging requires specialized blister packaging machinery, making it an essential component of the manufacturing process.
Here's a breakdown of the different types of blister packaging machinery:
These machines are designed to work together to produce high-quality blister packaging efficiently.
Methods
In a thermo cold forming process, the first packing is done by thermoforming technique, after which the product is repacked with a cold-formed package.
This process is a key step in manufacturing, allowing for the creation of complex shapes and designs.
The thermoforming technique is used to shape the initial packaging, which is then replaced with a cold-formed package for added durability.
Manufacturers often use this method to create custom packaging solutions for various products.
Frequently Asked Questions
Is it worth recycling blister packs?
Yes, recycling blister packs is worth it, as they can be recycled and help reduce the significant amount of plastic waste in the UK. Recycling blister packs is a simple step towards making a positive impact on the environment.
Sources
- https://clamshell-packaging.com/blister-packaging/
- https://en.wikipedia.org/wiki/Blister_pack
- https://www.alibaba.com/showroom/blister-packaging.html
- https://www.we-pack.co.uk/advice-centre/guides/blister-packaging-and-clam-packaging-what-they-are-and-why-your-business-should-be-using-them
- https://dmspack.com/blister-packing/
Featured Images: pexels.com