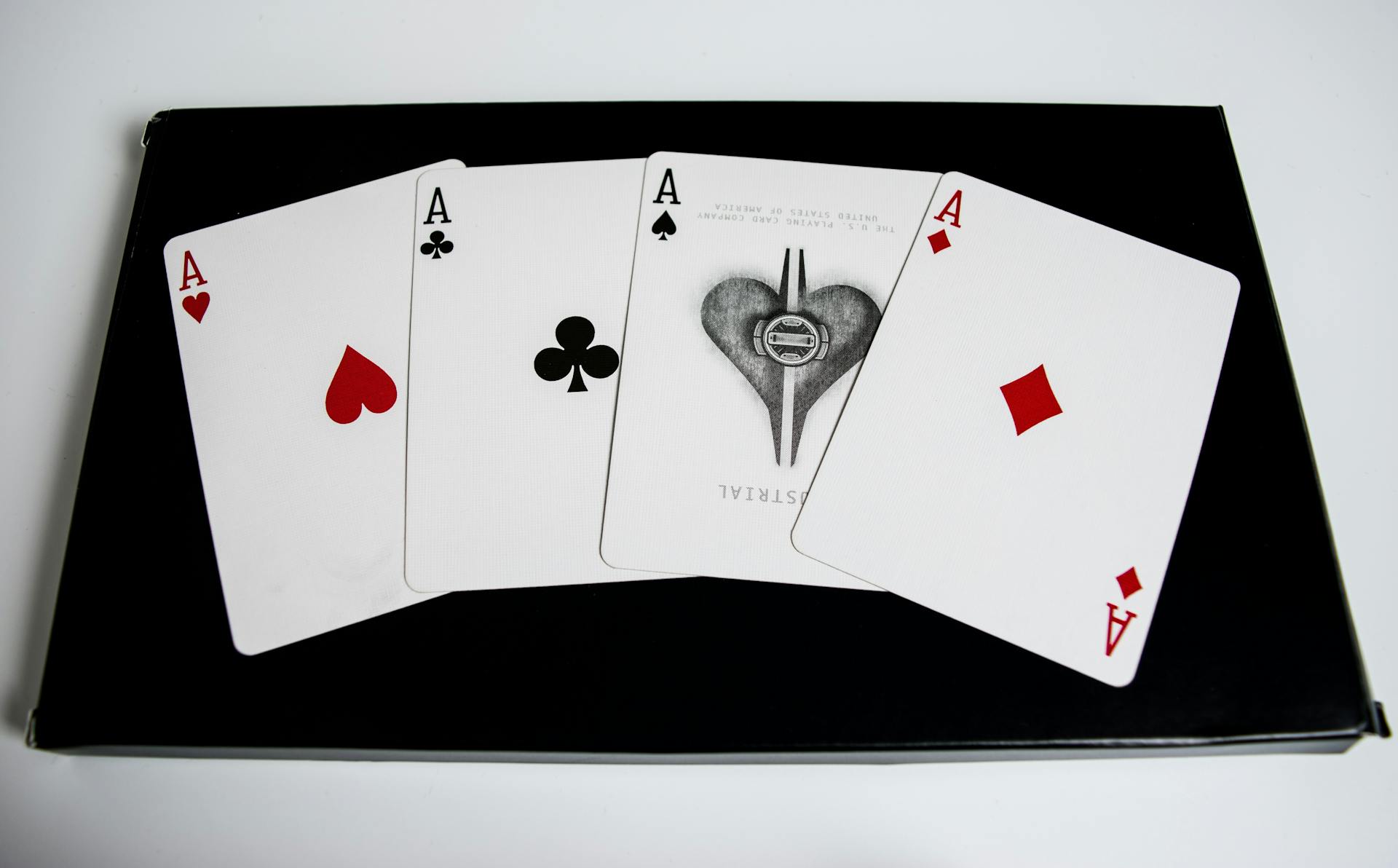
A blister card packaging machine is a versatile tool that can be used in various industries, including pharmaceuticals, cosmetics, and electronics. It's a machine that can handle a wide range of products.
The machine's compact design makes it suitable for use in small to medium-sized production facilities. Its small footprint also allows for easy integration into existing production lines.
Blister card packaging machines are designed to meet the needs of different industries, with features such as adjustable blister size and shape, and the ability to package products of varying weights and sizes. This flexibility makes them a popular choice for companies that need to package a wide range of products.
Broaden your view: Food Packaging Machines for Small Business
What Is It?
Blister card packaging machines are specialized devices used to create blister packs, a common packaging format for various products.
Blister packaging was invented and popularized in Germany in the late 1950s.
The first blister pack sealing machine was used for the packaging of tablets and capsules, providing a convenient alternative to bottled tablets.
A blister pack consists of a product sealed between a transparent plastic sheet and a base plate made of cardboard, plastic film, or aluminum foil.
The blister-packed tablets are squeezed by hand when taking the medicine, allowing the tablets to break through the aluminum foil.
Types of Machinery
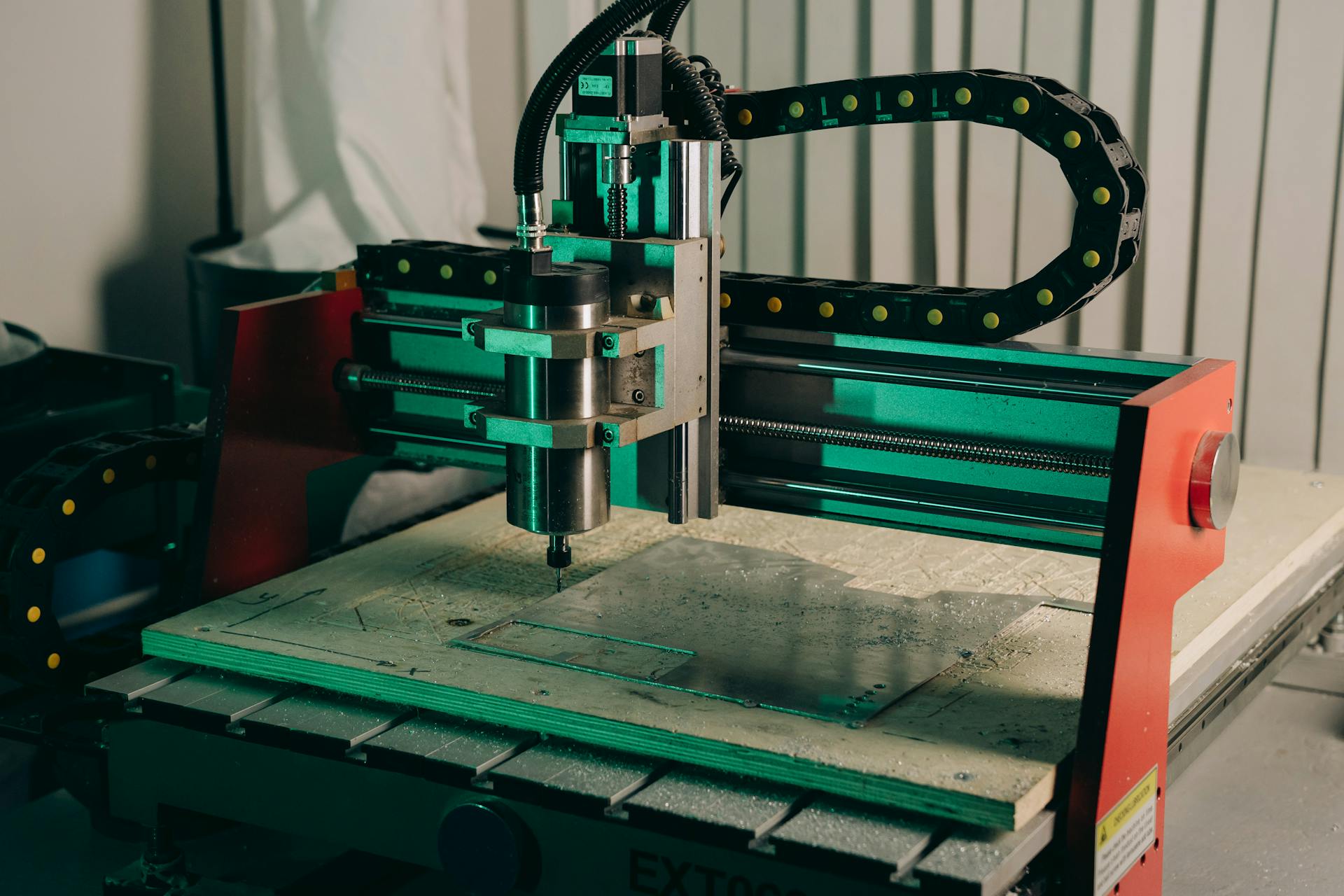
Let's talk about the different types of machinery that can be used for blister card packaging.
There are several types of machinery that can be used for blister card packaging, including automatic and semi-automatic machines.
Automatic machines can produce blister cards at a high speed, often up to 100 cards per minute.
Semi-automatic machines, on the other hand, require manual intervention to load and unload the cards.
These machines are often used in smaller production runs or for testing purposes.
Some machines can also be equipped with additional features such as printing and labeling capabilities.
This can help increase efficiency and reduce labor costs.
Other machines may be designed for specific types of products, such as pharmaceuticals or cosmetics.
These machines are typically designed with safety features to prevent contamination and ensure accurate dosing.
In some cases, machines may also be designed for specific packaging formats, such as clamshell or tray packaging.
This can help reduce waste and improve the overall appearance of the product.
Related reading: Automatic Strapping Machine
How It Works
A blister card packaging machine works by following a systematic process. This process involves four main steps: plastic forming, product loading, sealing, and cutting.
Plastic forming is the first step, where a sheet of plastic is heated and molded into cavities (blisters) using vacuum or pressure forming.
In the product loading step, products are placed into the formed blisters manually or through automated systems.
Sealing is the next step, where a backing card or film is aligned and sealed to the blister using heat, pressure, or adhesives.
The final step is cutting, where the sealed packs are cut into individual units or specific shapes for distribution.
Here's a brief overview of the steps involved in the process:
- Plastic forming: A sheet of plastic is molded into cavities using vacuum or pressure forming.
- Product loading: Products are placed into the formed blisters manually or through automated systems.
- Sealing: A backing card or film is sealed to the blister using heat, pressure, or adhesives.
- Cutting: The sealed packs are cut into individual units or specific shapes.
Key Features and Benefits
A blister card packaging machine is a fantastic investment for any business, and understanding its key features and benefits is crucial.
High-speed operations are one of the standout features of these machines, capable of producing hundreds to thousands of packs per hour. This level of efficiency can significantly boost productivity and meet high demand.
Versatility is another key advantage, as these machines are compatible with various materials, including PVC, PET, and aluminum foils. This adaptability makes them a great choice for companies that work with different materials.
User-friendly controls are designed to make operation a breeze, thanks to programmable logic controllers (PLCs) that allow for precise operation. This ensures that even those without extensive experience can easily navigate the machine.
Customization options are also a major benefit, with adjustable settings that can accommodate different product sizes and shapes. This flexibility is particularly useful for companies that produce a range of products.
Quality assurance is a top priority, and these machines feature sensors to detect misalignment or sealing defects. This helps prevent defective products from entering the market and saves companies from costly rework or recalls.
To give you a better idea of the machine's capabilities, here are some of its key features:
- High-Speed Operations: Produces hundreds to thousands of packs per hour
- Versatility: Compatible with PVC, PET, and aluminum foils
- User-Friendly Controls: Equipped with PLCs for precise operation
- Customization Options: Adjustable settings for different product sizes and shapes
- Quality Assurance: Features sensors to detect misalignment or sealing defects
Automation and Innovation
The Axial BP-290 is a game-changer in blister card packaging, capable of filling blister cards at a rate of 1 per minute, or 55-60 per hour.
This machine is designed to make a significant impact on labor hours, with pharmacies reporting a 60-70% reduction in manual filling labor hours. It's also easy to clean and maintain.
The Axial BP-290 offers customization to match your workflow, making it a versatile solution for pharmacies. With the ability to package unit and multi-dose blister cards at scale, it's clear that this machine is built for efficiency.
Here are some key features of the Axial BP-290:
- Fill blister cards, Lid Sealing and Inspection Assistant, 290 dedicated canisters, 3 universal canisters for changing NDC#’s and a manual fill tray
- Generate Unit and Multi-dose blister cards at scale
- Package 55-60 blister cards per hour
- Customize the system to match your work flow
- Easy to clean and maintain
Fast, Reliable, and Intelligent Automation
The Axial BP-290 is a game-changer in pharmacy automation, capable of generating unit and multi-dose blister cards at scale.
This machine can package 55-60 blister cards per hour, resulting in a significant reduction in manual filling labor hours, with pharmacies reporting a ~60-70% reduction in labor hours required to do packaging.
The Axial BP-290 is designed for speed, with a blister preparation time of just 1 per minute on average.
One of the key benefits of this machine is its ease of use - it requires just a single technician to operate, making it a great option for pharmacies looking to streamline their packaging process.
Here are some of the key features of the Axial BP-290:
- Fill blister cards, Lid Sealing and Inspection Assistant, 290 dedicated canisters, 3 universal canisters for changing NDC#’s and a manual fill tray
- Generate Unit and Multi-dose blister cards at scale
- Package 55-60 blister cards per hour
- Customize the system to match your work flow
- Easy to clean and maintain
The Axial BP-290 is also equipped with an optical sensor that detects anomalies and stores photographs of each blister for review, providing an added layer of quality control and assurance.
Semi-Automatic
In semi-automatic blister packaging, a roll or single plastic sheet is fed into the machine.
The machine operates continuously or intermittently, depending on the production needs.
A semi-automatic machine can have multiple forming molds, which depends on the size and output of the product.
Typically, these machines have multiple columns to accommodate various product sizes.
After forming, the product is manually loaded into the blister covers.
The covers are then sealed with a printed roll or individual shape substrate, and the trimmed edges are heat sealed to complete the packaging.
Expand your knowledge: Semi-automatic Bag in Box Filling Machines
Machine Specifications
The RapidCardRx System is a versatile blister card packaging machine that's designed to handle various packaging needs. Its packager dimensions and weight are substantial, measuring 33 inches wide by 18 inches long by 60 inches high for 20 cartridges, and weighing around 450 pounds for 40 cartridges.
The machine's compact size belies its impressive capabilities, which include a built-in controller, power supplies, and 20, 30, or 40 "smart" universal cartridges. These cartridges are designed to accommodate any size and type of pill, and they come with 20, 30, or 40 built-in vision inspection systems, as well as consumables sensors.
The RapidCardRx System's internal cleanliness is a standout feature, with the manufacturer claiming it's the easiest to clean in the industry.
RapidRx Specifications
The RapidRx System is a powerful tool for managing medication. It's built with a built-in controller and power supplies, making it a self-contained unit.
The packager dimensions are quite large, measuring 33 inches wide, 18 inches long, and 60 inches high for 20 cartridges. For 30 or 40 cartridges, the height increases to 84 inches.
In metric units, the packager dimensions are 84 cm wide, 46 cm long, and 152 cm high for 20 cartridges. For 30 or 40 cartridges, the height is 213 cm.
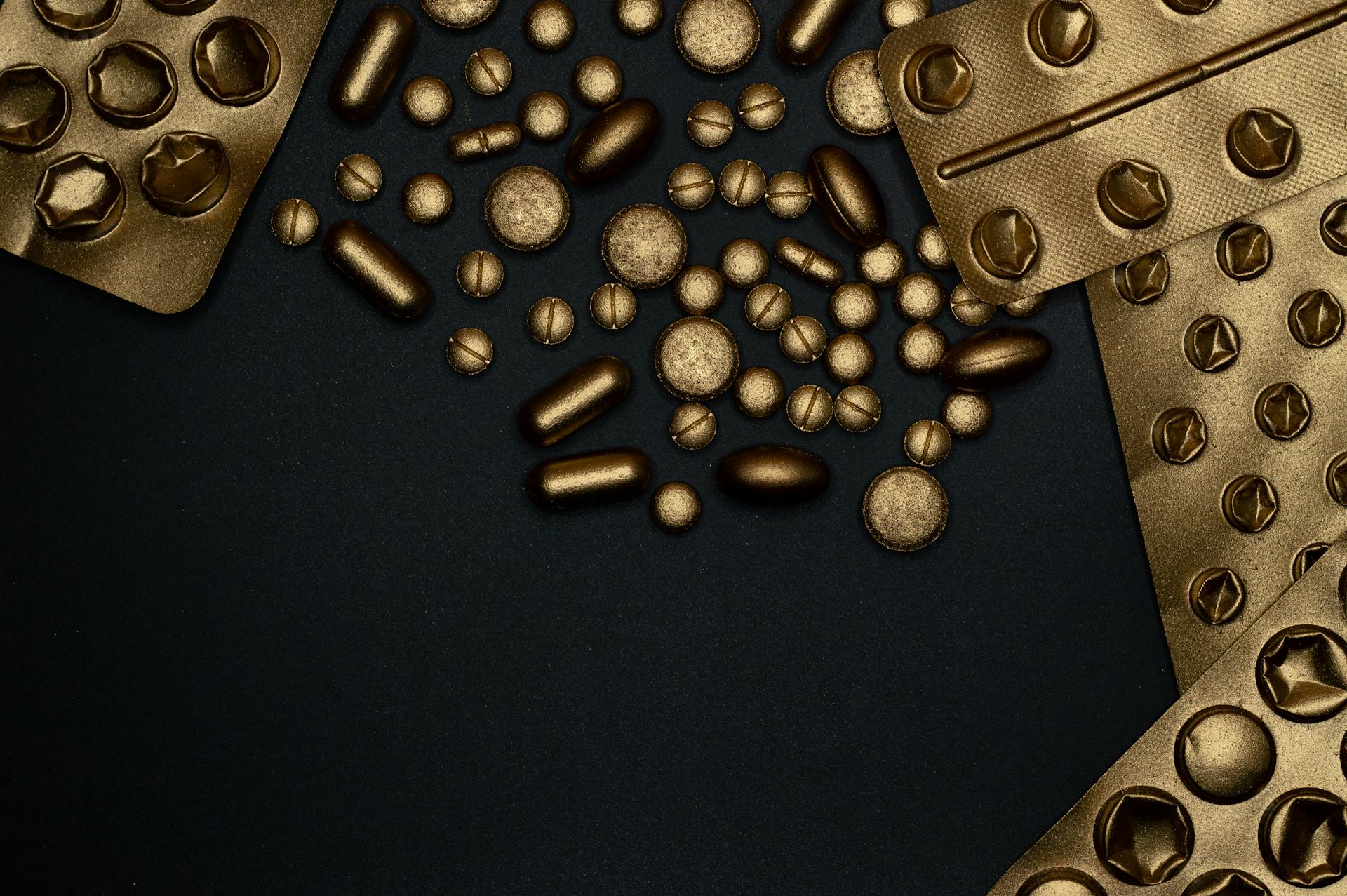
The RapidRx System is designed with 20, 30, or 40 "smart" universal cartridges, which can accommodate any size or type of pill. Each cartridge comes with its own built-in vision inspection system and consumables sensor.
Cleaning the RapidRx System is a breeze, with the manufacturer claiming it has the easiest cleaning process in the industry.
Power Requirements
Power Requirements can be a bit tricky, but don't worry, I've got you covered. To operate the Packager, you'll need a dedicated 110v/20 AMP outlet.
The Inspection Station and Optical Counter, on the other hand, can run on standard 110v power. This is a great feature, as it makes setup and installation a breeze.
Here's a breakdown of the power requirements for each component:
With these power requirements in mind, you'll be able to set up and run your machine with confidence.
Environmental Specifications
The machine can operate in a wide temperature range, from 45 degrees to 90 degrees Fahrenheit, which is equivalent to 7 degrees to 32 degrees Celsius.
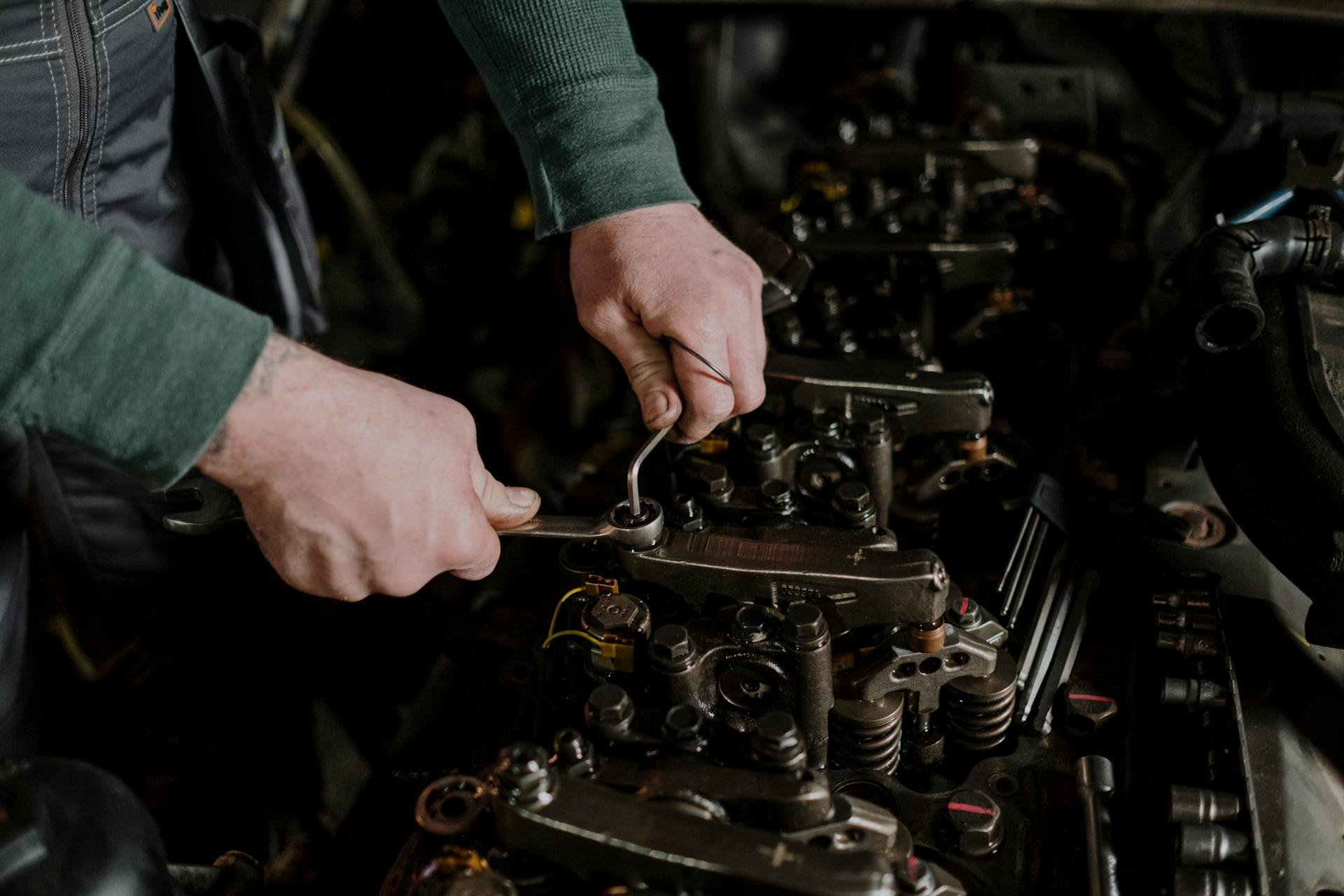
This temperature range is quite broad, and it's something to consider when placing the machine in a specific environment.
To ensure optimal performance, it's essential to maintain a relative humidity level between 10% and 80%. This is a non-condensation range, which means the air can hold moisture without causing any issues.
You'll want to monitor the humidity levels to prevent any potential problems.
Here's a quick summary of the environmental specifications:
Machine Types and Applications
Blister card packaging machines are used to create blister packs for various products. These machines efficiently seal products within a cavity (the blister) covered by a backing card or film, providing protection, visibility, and tamper resistance.
There are different types of blister card packaging machines, each suitable for specific products. For example, pencil, ball pen, marker pen, hardware, and toys can be packaged using these machines.
Some blister card packaging machines are specialized in face seal blister packaging, where the seal is only on the flange while the rest of the card is not sealed.
Here are some examples of products that can be packaged using blister card packaging machines:
- Pencil
- Ball pen
- Marker pen
- Hardware
- Toys
Widely Application
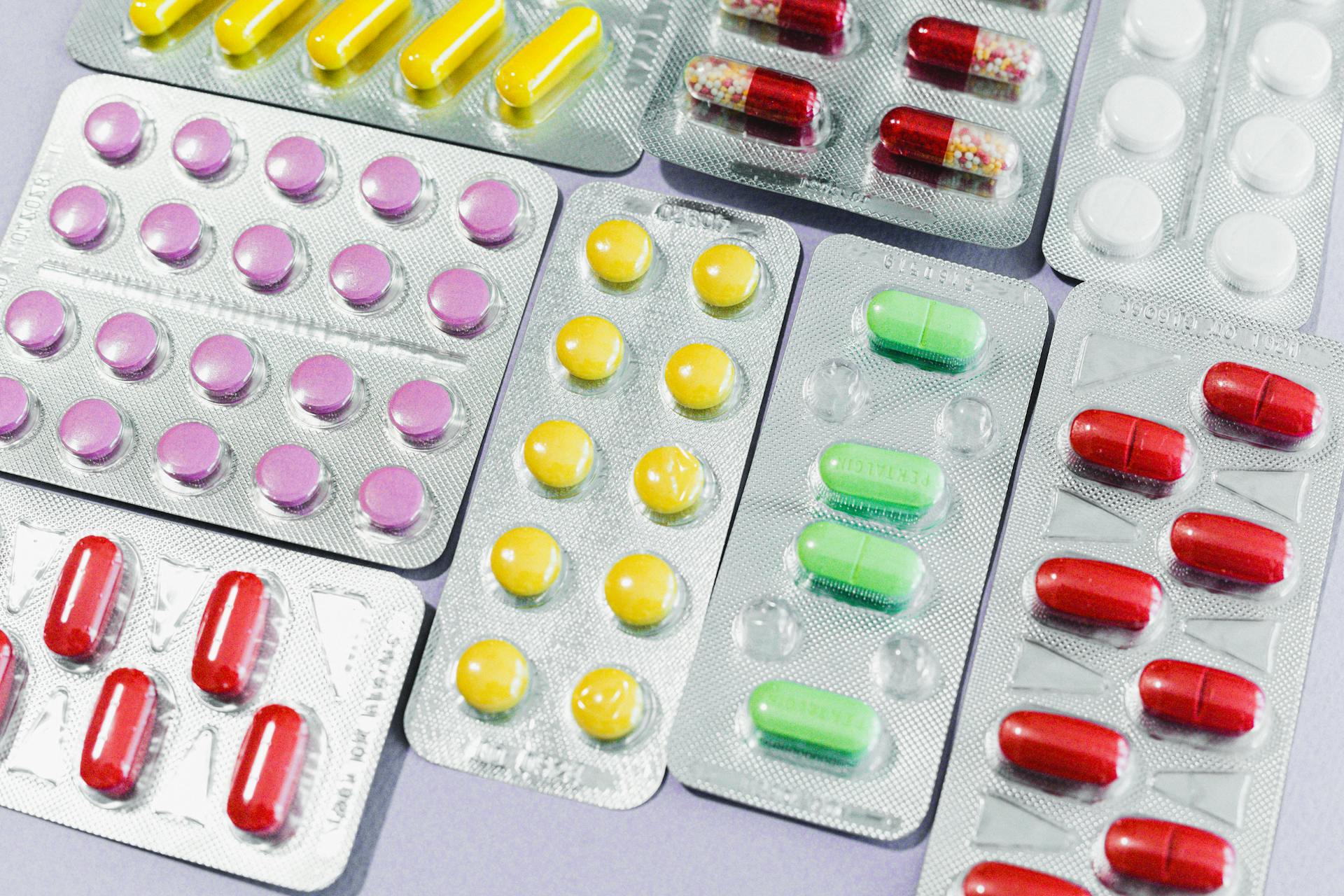
Blister packaging machines have a wide range of applications. They're suitable for packaging many kinds of products, including pencils, ball pens, marker pens, hardware, and toys.
Blister card packaging machines are used to create blister packs for various products. These machines are specialized devices that efficiently seal products within a cavity covered by a backing card or film.
The blister packaging method was invented in Germany in the late 1950s. It was initially used for packaging tablets and capsules.
Here are some examples of products that can be packaged using blister card packaging machines:
- Pencils
- Ball pens
- Marker pens
- Hardware
- Toys
Types of Machinery
There are several types of machinery, each with its own unique characteristics and applications.
Industrial machinery includes everything from manufacturing equipment to construction tools.
Some examples of industrial machinery include lathes, milling machines, and drill presses.
Construction machinery, on the other hand, is designed for building and infrastructure projects.
Examples include cranes, excavators, and bulldozers.
Agricultural machinery is used in farming and includes tractors, plows, and harvesters.
These machines are essential for food production and can be found on farms worldwide.
If this caught your attention, see: Industrial Stretch Wrap
Rotary

Rotary machines are great for high-speed production, and one example is the Rotary Blister Packaging Machines. They feature a rotating table that allows multiple operations to occur simultaneously.
This design makes them ideal for high-speed production of pharmaceuticals and small consumer goods.
Difference Between Strip
The main difference between a strip and a rod is their shape and application. A strip is typically a thin, flat piece of material, often used in applications like cutting and forming.
In contrast, a rod is a long, cylindrical piece of material, commonly used in applications like drilling and machining. Rods are often used for precision work due to their straightness and consistency.
The choice between a strip and a rod depends on the specific requirements of the project. For example, a strip might be preferred for applications that require a lot of flexibility, such as in the manufacture of springs.
In the article, we discussed how rods are often used in applications like drilling and machining, where their straightness and consistency are valuable assets.
Materials and Packaging
We're going to talk about the materials used in blister card packaging, and I'll give you a quick rundown of the most common ones. Plastic films are a popular choice for blister packaging, especially in the pharmaceutical industry.
The choice of plastic film depends on the adaptability of the film and the packaged product. For example, polyvinyl chloride (PVC) is a widely used rigid plastic sheet in pharmaceutical blister packaging.
Here are some common materials used in blister packaging:
- Polyvinyl chloride (PVC)
- Polyvinylidene chloride (PVDC)
- Composite materials like PVC/PVDC/PE, VDC/OPP/PE, and PVC/PE
- Aluminum foil, such as PET/aluminum foil/PP and PET/aluminum foil/PE
These materials are chosen for their barrier properties, such as water vapor, light, and anti-odor resistance, making them suitable for packaging sensitive products like medicines.
What Is Packaging Machinery?
Packaging machinery is a game-changer for businesses of all sizes, allowing for high-speed and automated packaging that's perfect for both small-scale and large-scale manufacturing.
Blister card packaging machines, for example, form plastic blisters, fill them with products, and seal them to backing cards, resulting in a secure and attractive package.
A blister card packaging machine is a device that streamlines the production process, making it suitable for a wide range of industries.
These machines can produce a large quantity of packages in a short amount of time, making them a valuable investment for companies that need to package products quickly and efficiently.
For your interest: Paper Sack Making Machine
Types of
The flatbed blister packaging machine is a type of packaging equipment that allows for efficient and flexible packaging of pharmaceutical products. It has a large filling space, making it ideal for packaging multiple drugs in one plate.
This machine uses a flat heating device to soften the film, which is then blown into a blister by compressed air. The filling device then fills the packaged material into the blister.
The flatbed blister packaging machine can arrange multiple filling machines at the same time, increasing packaging efficiency and expanding the packaging range.
Worth a look: Pill Bottle Filling Machine
Aluminum Plastic
Aluminum plastic blister packaging is a cost-effective option, but its sealing performance is slightly worse than strip packaging.
The choice of composite film for drug packaging depends on the properties of the drug, such as moisture, oxidation, and retention of drug taste.
Ordinary composite film is made of polyester, aluminum foil, and polyethylene (PET/AL/PE), which has good printing adaptability and gas and moisture barrier properties.
This type of film is suitable for packaging medicines that require a good balance of properties.
Medicinal strip-shaped easy-tear composite film is composed of cellophane, polyethylene, and aluminum foil (PT/PE/AL/PE), making it convenient for consumers to take products.
It has good gas and water vapor barrier properties, ensuring a longer shelf life of the contents.
Paper-aluminum-plastic composite film is composed of paper, polyethylene, and aluminum foil (paper/PE/AL/PE), which has good printability and stiffness.
It also has good barrier properties to gas or water, ensuring a long shelf life of medicines.
Here's an interesting read: Shrink Film Machine
Common Materials
Polyvinyl chloride (PVC) is the most widely used material for rigid plastic sheets in pharmaceutical blister packaging.
The polyvinyl chloride sheet used for pharmaceutical packaging has high hygienic requirements for the resin, meaning it must be non-toxic.
Non-toxic polyvinyl chloride resin, a non-toxic modifier, and a non-toxic heat stabilizer are used to ensure the PVC sheet meets these requirements.
Polyvinylidene chloride (PVDC) has strong gas sealing and excellent moisture resistance, making it ideal for packaging that requires barrier properties.
PVDC also has good oil resistance, chemical resistance, and solvent resistance, particularly for oxygen, water vapor, and carbon dioxide gas.
Composite plastic rigid sheets for pharmaceutical blister packaging include PVC/PVDC/PE, VDC/OPP/PE, and PVC/PE.
A composite material of plastic sheet and aluminum foil, such as PET/aluminum foil/PP or PET/aluminum foil/PE, can be used for packaging that requires barrier properties and light-proof properties.
Paper Packing
Paper packing is a crucial step in protecting and showcasing products. It's suitable for a wide range of industries, including hardware, stationery, toys, and cosmetics.
The types of products that can be packed using paper card blister packing machines include razors, batteries, electronics, and small household items. These machines can also be used for blister paper card packaging of hardware, medical equipment, toys, batteries, and electronics.
Curious to learn more? Check out: How to Address Post Card
Paper card blister packing machines can be categorized into different types, including rotary and automatic machines. Rotary machines are suitable for packing battery/pen/stationery, while automatic machines can be used for blister paper card packaging of hardware, cosmetics, and other products.
Some paper card blister packing machines are designed for specific industries, such as the HP-500C Multi-function Intelligent Packaging Machine, which is applicable to all kinds of bank cards, oil cards, gift cards, and commercial consumer cards.
The machines can be used for various packaging forms, including positive/negative pressure forming, aircraft hole punching, cutting, feeding, paper card feeding, thermal sealing, and finished products conveying. They can also be used for packaging products with double blister packages or cardboard with blister packages.
Here are some examples of paper card blister packing machines and their features:
These machines are designed to be easy to operate and maintain, with some models featuring stainless steel covers and simple structures. They are also suitable for industries that require high-quality packaging, such as the pharmaceutical industry.
How It's Made Step by Step
Blister packaging machines can be operated in three main forms: manual, semi-automatic, and fully automatic. The latter two types are the most commonly used in production lines.
Manual operation is the simplest form, but it's not as efficient as the other two. Semi-automatic and fully automatic machines are preferred for their speed and accuracy.
Semi-automatic and fully automatic machines are the most common types used in production lines.
Choosing and Making a Machine
Choosing and making a machine can be a daunting task, especially if you're new to the world of packaging. There are many types of blister card packaging machines available, each with its own unique features and benefits.
Blister card packaging machines come in different sizes and configurations, ranging from small, tabletop models to large, floor-standing machines. These machines can be manual or automated, depending on the level of production required.
Manual blister card packaging machines are often used for small-scale production or for packaging products that require a high level of customization. They typically consist of a blister card, a product, and a backing card, which are assembled together by hand.
Automated blister card packaging machines, on the other hand, are ideal for high-volume production. They can package products quickly and efficiently, with minimal labor required.
You might enjoy: Blister Card Sealing Machine
Sources
- https://rxsafe.com/solutions/rapidcardrx/
- https://www.euclidmedicalproducts.com/axial-bp-290-blister-card-packaging-machine/
- https://www.cn-thermoforming.com/blister-card-packaging-machine/
- https://www.antaipacking.com/paper-card-blister-packing-machine/
- https://sedpharma.com/news-events/knowledge-of-pharmaceutical-blister-packaging-machine/
Featured Images: pexels.com