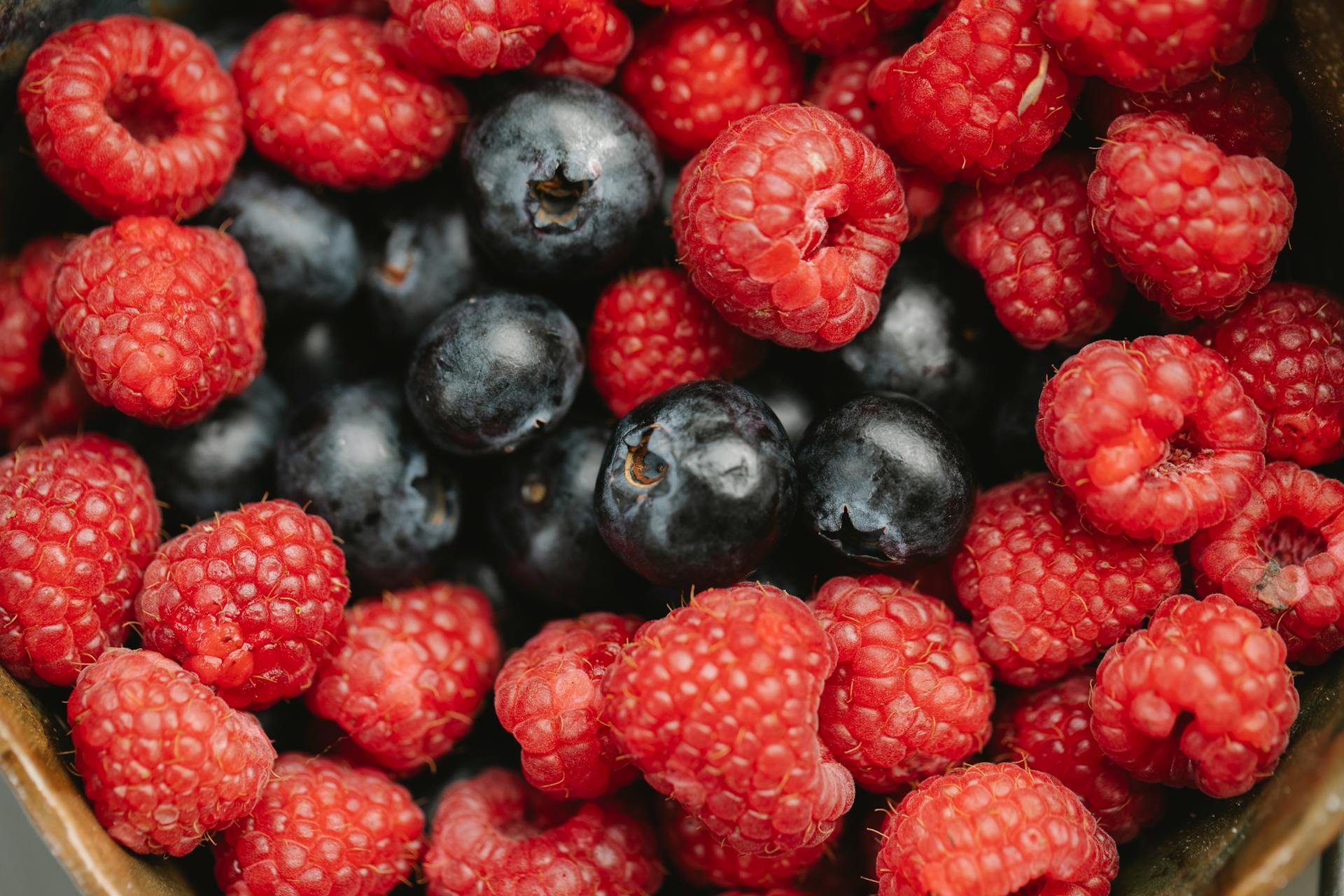
Effective pick and pack fulfillment solutions are crucial for eCommerce businesses, as they directly impact customer satisfaction and loyalty. According to a recent study, 85% of customers are more likely to shop with a company again if they have a positive delivery experience.
Inefficient pick and pack processes can lead to delays, errors, and increased costs. A well-designed pick and pack system can help streamline operations, reducing errors by up to 90%.
What Is Fulfilment?
Fulfilment is the process of getting products from a warehouse to customers. It involves several steps to ensure timely and accurate delivery.
The pick and pack process is a key part of fulfilment, where items are selected from inventory and placed in a box for shipping. This process involves four main steps.
Items are picked from inventory, which is the storage of goods in a warehouse. The picked items are then packed in a box for shipping.
For more insights, see: Pick Pack and Ship Warehouse
Warehouse Setup
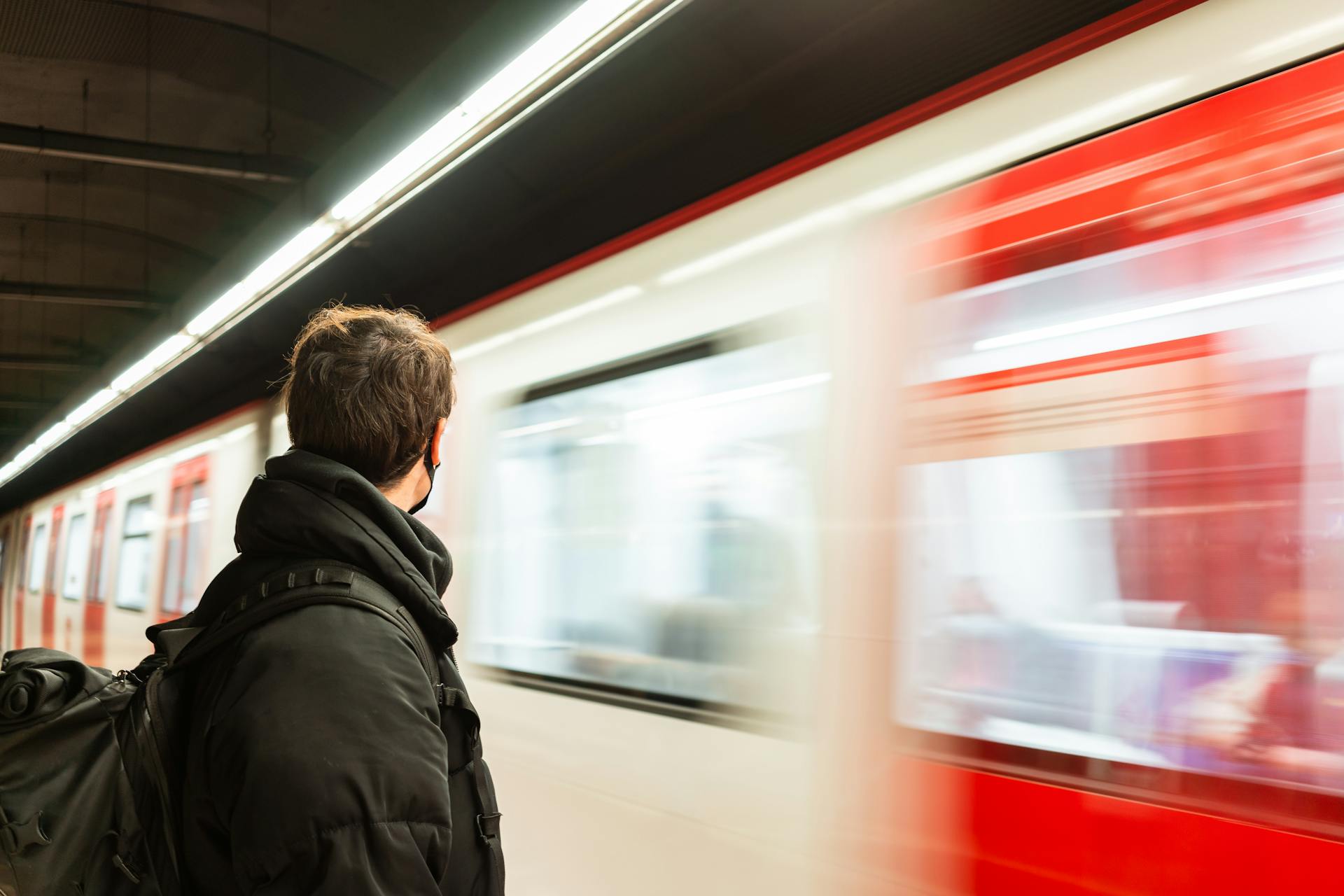
Organizing a warehouse is crucial for efficient pick and pack fulfillment. This is called "slotting", a warehouse operations strategy that minimizes warehouse travel and search time.
To avoid traffic jams, popular items should be placed strategically, not too close together. This helps speed up the pick and pack process.
Efficient path instructions can also reduce errors, making order fulfillment more accurate and timely.
A fresh viewpoint: Warehouse Pick Pack Work
Kitting
Kitting is a specialized kind of pick and pack service that involves assembling various SKUs into a single SKU to create a subscription pack or promotional bundle.
Your warehouse will need to adjust its packing techniques monthly or as new promotions arise to accommodate kitting operations.
This can be a challenge, but with the right systems and processes in place, you can efficiently create and ship these customized bundles.
For example, your warehouse may need to pack a different combination of products each month to reflect changing promotions or seasonal offerings.
Consider reading: Warehouse Pick and Pack
Receiving
Receiving is a crucial step in the warehouse setup process.
A warehouse fulfillment software creates a packing slip when an order is placed online, thanks to the integration with ecommerce sales channels and warehouse systems.
This automated process ensures that the right information is available for picking and packing, making it easier to manage inventory and fulfill orders efficiently.
The packing slip includes all the necessary details, such as the order number, items to be shipped, and shipping address.
Fulfilment Methods
As your ecommerce business grows, you may need to evolve your warehouse picking and packing methods to meet demand. Startups and early-stage companies may get away with picking items one at a time.
Your pick and pack system should match your inventory and order complexity. Advanced warehouse picking methods can create speed when you sell more.
There are various pick and pack processes to consider, but it's essential to find the one that works best for your business.
On a similar theme: Order Picking Methods
Waveicking
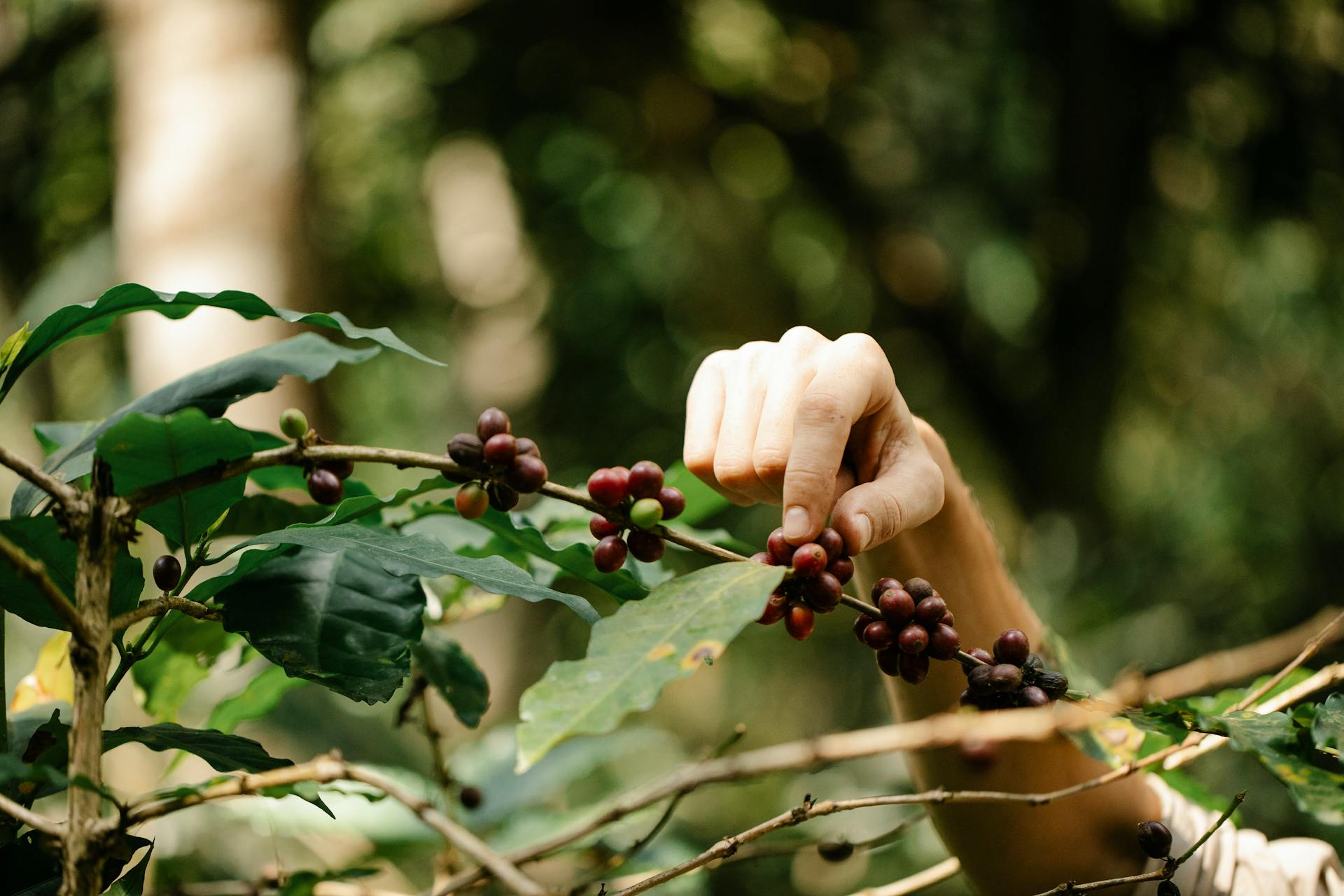
Wave picking is a complex method that combines batch and zone picking, allowing warehouses to move batches across zones for greater efficiency and cost savings.
This method is best suited for high-performing businesses with thousands of monthly orders and high SKU volumes, as seen in Example 4.
Wave picking streamlines the picking process by allowing employees to stay within a zone but pick more than one order at a time, making it a great option for businesses with high order volumes.
According to Example 4, wave picking is the most complex method, but it can save money over time due to its efficiency.
Here's a comparison of the different picking methods:
By implementing wave picking, businesses can improve their picking efficiency and reduce costs, making it a great option for high-performing businesses with high order volumes.
Protect with Infill
Protecting your items during shipping is crucial, and infill plays a significant role in this process.
Infill materials like shredded cardboard and packing peanuts provide the necessary cushioning to prevent items from shifting in boxes during shipping.
For larger items, you may need custom infill, including molded inserts or a mix of infill types.
This ensures that your items arrive safely and in the same condition they were sent in.
Branded infill can also complement branded packaging, creating a cohesive and professional look.
Effective eCommerce Solution
Our pick and pack fulfillment solution is available 9 am to 6 pm at our well-equipped facility, where experts handle all picking, packing, and shipping.
We prioritize precision and accuracy in every step of the pick and pack process, from inventory management to quality control, ensuring your orders are handled with care.
Customized solutions are available, tailored to your unique requirements, whether you're a small startup or an established enterprise.
Our streamlined processes and cutting-edge technology ensure that orders are picked, packed, and shipped with speed and efficiency, reducing lead times and improving customer satisfaction.
You can reduce overhead costs associated with warehousing and labor by outsourcing your pick and pack operations to us, allowing you to focus on growing your business.
We offer advanced reporting and analytics tools to gain insights into your inventory and order fulfillment performance, making informed decisions to optimize your supply chain further.
Here are some key benefits of our pick and pack fulfillment services:
- Precision and accuracy in every step of the process
- Customized solutions tailored to your unique requirements
- Scalability to adapt to your changing business needs
- Speed and efficiency in picking, packing, and shipping
- Cost-effectiveness through reduced overhead costs
- Advanced reporting and analytics tools for supply chain optimization
Our team aims for 100% accuracy, providing a high level of care and expertise that has led hundreds of ecommerce clients to switch to our services.
Best Practices
Having the right processes in place is crucial for pick and pack order fulfillment to drive customer satisfaction. Accuracy at this stage may help reduce the risk of returns, which incur reverse logistics and restocking costs and may disappoint customers.
This is a last chance for warehouse packing teams to check picking accuracy, making sure the right quantities of the right items go in the box before it’s sealed and shipped.
Broaden your view: Order Picking Accuracy
Staying Ahead of the Competition
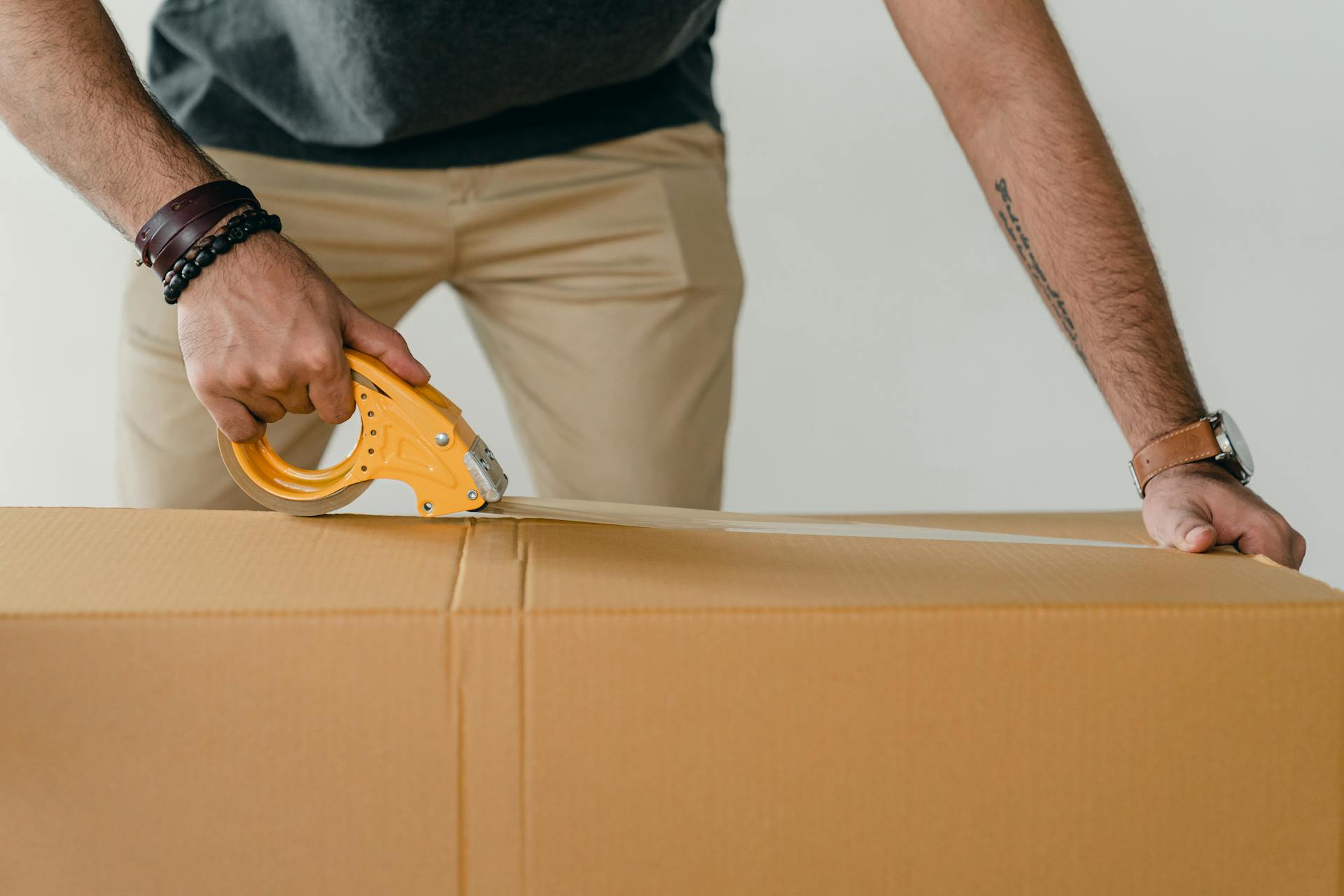
To stay ahead of the competition, it's essential to scale up your resources to match the expectations set by big box retailers and marketplaces like Amazon. A 3PL can help you achieve this by providing the necessary support to handle same-day and next-day delivery on millions of items.
Technological advancements in 3PL services, such as real-time tracking and good inventory management systems, offer increased visibility and control, making outsourcing to a 3PL a practical solution. This means you can focus on other areas of your business while your 3PL partner handles the logistics.
Fluctuating order volumes can be a challenge, but a 3PL can offer flexibility to accommodate these changes. This allows your business to scale its operations up or down based on demand, making it easier to handle small and large orders.
During peak seasons or promotional periods, this adaptability is particularly valuable. By partnering with a 3PL, you can efficiently handle increased order volumes and maintain a competitive edge.
Check this out: 3pl Order Fulfillment
Cost-Effectiveness
By streamlining operations and optimizing resources, businesses can achieve cost savings through pick and pack fulfillment. This process eliminates the need to collect items from different storage facilities and send them elsewhere for packing and labeling.
Reducing costs is a significant benefit of pick and pack fulfillment. It helps businesses save money by minimizing unnecessary steps in the order fulfillment process.
By optimizing picking and packing methods, businesses can further reduce costs and improve efficiency.
Intriguing read: Ecommerce Order Fulfillment Process Steps
Improved Accuracy
Having the right processes in place is crucial for ensuring order accuracy. This is especially true for warehouse packing teams, who have a last chance to check picking accuracy before sealing and shipping the order.
With dedicated staff members responsible for picking and packing individual orders, errors and mix-ups are significantly reduced. This leads to improved order accuracy.
Accuracy at the packing stage can help reduce the risk of returns, which incur reverse logistics and restocking costs. Disappointed customers are also minimized.
Having the right quantities of the right items in the box before shipping is essential for order accuracy. This helps prevent shipping mistakes, incorrect items, or missing components.
Fulfilment Software
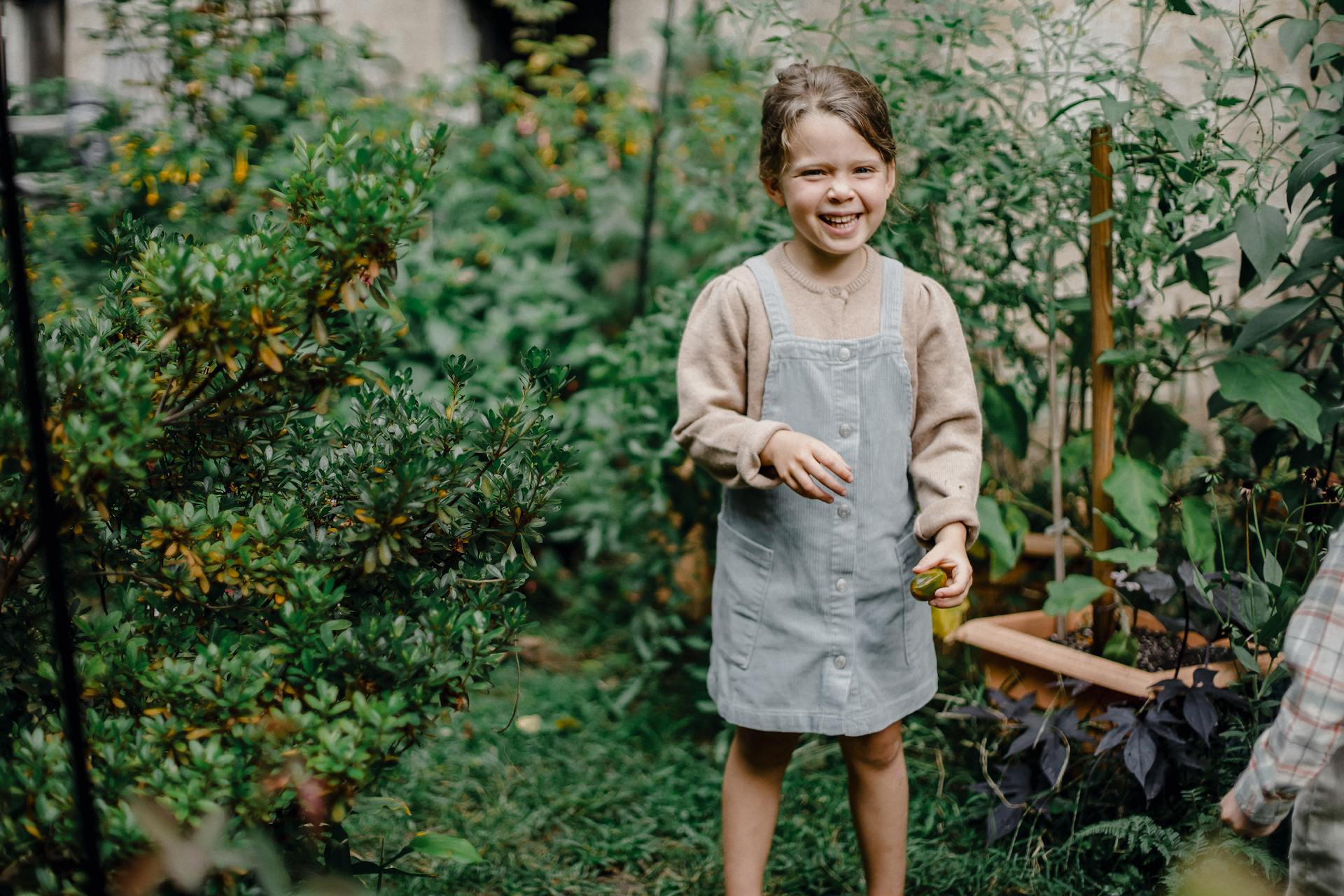
Fulfilment software plays a crucial role in ensuring a smooth pick and pack process. It ties together various information, including overall workflows, fulfillment status, and productivity, giving ecommerce store owners and leadership visibility into pick and pack services.
Inventory and warehouse software solutions, including your warehouse management system, are essential for connecting this information. This is especially important when starting a partnership with a 3PL, as their warehouse management software may determine the complexity of your setup and integrations.
Here are some key features to look for in a fulfilment software:
- Order integration: Connects to sales channels and receives new orders.
- Picking: Assigns picking lists and optimized paths to staff on mobile devices.
- Packing: Assigns packing tasks based on weight, size, and order requirements.
- Shipping: Generates shipping labels with accurate weight and address information.
These features help automate certain tasks, like picking assignments, order status, and other aspects of communication, supporting effective supply chain management.
How Software Works
Fulfilment software connects to sales channels and receives new orders, making it a crucial part of the pick and pack process.
This integration allows the software to provide staff with optimized picking paths on mobile devices, showing them item details, locations, and quantities in real-time. This helps team members monitor pick completion progress and identify potential bottlenecks.
Discover more: Software Order Fulfillment
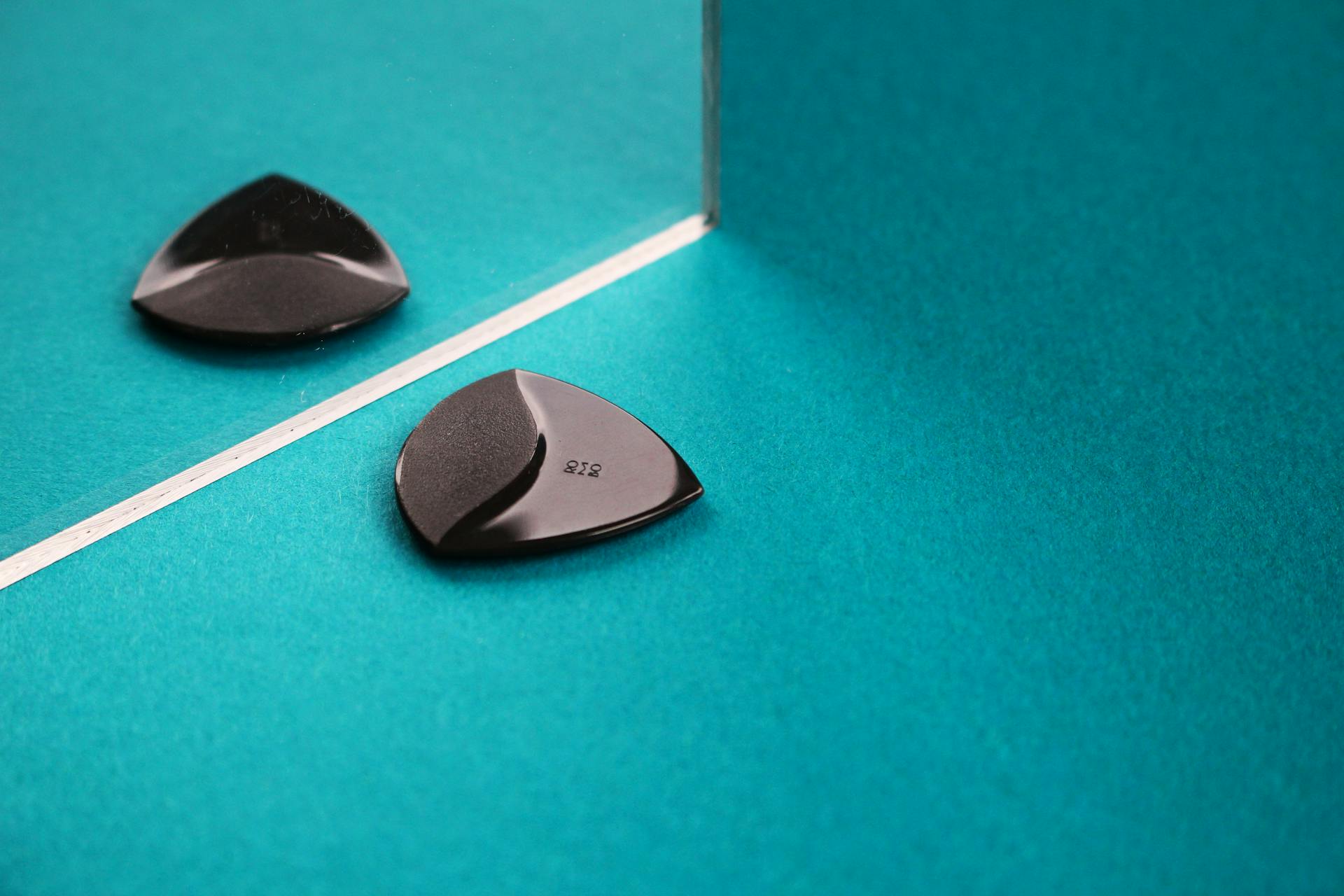
Picked items are scanned, and packing tasks are assigned based on weight, size, and order requirements. Packers receive alerts for missing or incorrect items, enabling them to intervene and correct errors right away.
The software generates shipping labels with accurate weight and address information, streamlining the dispatch process. This helps teams track shipped orders in real-time, providing updates to customers and improving communication.
Here's a breakdown of the key steps in the pick and pack process:
- Order integration: Software connects to sales channels and receives new orders.
- Picking: Staff receive optimized picking lists and paths on mobile devices.
- Packing: Picked items are scanned, and packing tasks are assigned based on order requirements.
- Shipping: The software generates shipping labels with accurate weight and address information.
Integrating Process Data
Data silos can occur when systems don't connect, making it difficult to analyze operations in context.
Having real-time inventory visibility is crucial to prevent stockouts and overstocking, ensuring products are readily available for pick and pack fulfillment without wasted capital.
Real-time order tracking allows for communication of potential delays or issues, helping to manage customer expectations effectively.
Integrated data can inform targeted promotions and upselling opportunities, enhancing customer engagement and satisfaction.
You can readily adapt to fluctuating order volumes and product offerings with integrated data systems, ensuring smooth operations during growth phases.
Take a look at this: Order Picking Systems
Tracking key metrics lets you identify areas for improvement and optimize the picking and packing process and other warehouse operations.
Here are some key benefits of integrating process data:
Outsourcing
Outsourcing can be a game-changer for businesses with fluctuating order volumes, as it allows for scalable and cost-effective solutions. This flexibility is especially beneficial during seasonal or market trend fluctuations.
Outsourcing pick and pack operations to a 3PL can enhance order accuracy, reduce errors, and streamline the order fulfillment process.
By partnering with a 3PL, businesses can eliminate the need for substantial upfront investments in pick and pack warehouse space and other resources, shifting to variable costs that provide financial flexibility.
Cost considerations play a crucial role in the decision-making process, and a 3PL may offer a favorable pick and pack fee based on order fulfillment and SKU volumes.
Outsourcing to a 3PL can also provide a range of benefits, including:
- Reducing labor costs
- Streamlining shipping and logistics
- Improving inventory management
- Enhancing customer satisfaction
By outsourcing pick and pack operations, businesses can focus on more productive tasks, such as growing their business and improving customer satisfaction.
Warehouse Operations
Organizing your warehouse is crucial for efficient pick and pack fulfillment, and it's called "slotting." This strategy helps minimize warehouse travel and search time by identifying the most efficient route through the warehouse.
Popular items shouldn't be placed too close together to avoid traffic jams in the warehouse. By separating visually similar items, you can also reduce picking errors.
Efficient path instructions can help reduce errors, leading to accurate and timely order fulfillment. This is especially important in a warehouse where pickers need to move quickly.
Keeping your inventory updated and in stock is essential for efficient order fulfillment. An inventory management app can help with real-time tracking, keeping tabs on current inventory and notifying you when stock runs low.
Inventory must be accurately identified and stored to ensure pickers can find what they need quickly.
Benefits of Fulfilment
Pick and pack fulfillment can significantly impact a business's efficiency and success. By outsourcing these services, you can save time, money, and efforts.

You don't have to rent space to stock inventory, which can be a significant cost savings. This allows you to focus on more productive tasks.
By partnering with a 3PL, you can track inventory levels without stocking the product or employing a person to track it. This is a huge relief for businesses with limited resources.
You don't have to fulfill tasks such as boxing, labeling, or finding the shipping carrier, which can be time-consuming and labor-intensive. This frees up your team to focus on more important tasks.
By optimizing your profits and boosting customer satisfaction, you can take your business to the next level.
Improving Warehouse Processes
Optimizing picking and packing methods is essential to streamlining order fulfillment.
Becoming familiar with the basics of pick and pack is the first step to improving the order fulfillment process at your warehouse.
Optimizing the pick packing process is crucial to streamlining order fulfillment.
Learning how to improve the order fulfillment process at your warehouses is a vital step in the pick and pack fulfillment process.
By optimizing picking and packing methods, businesses can significantly reduce errors and improve overall efficiency.
3PL Services
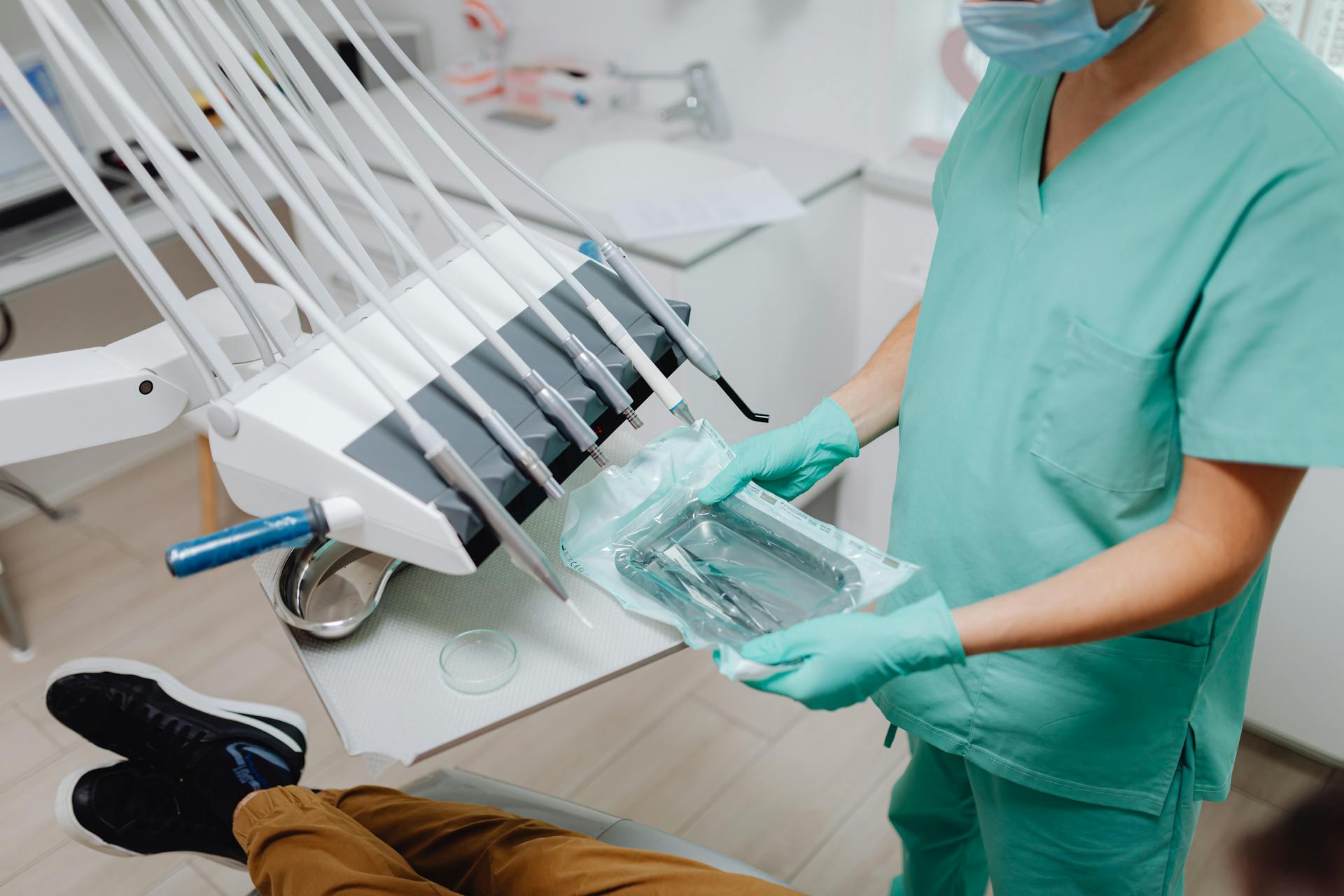
3PL Services help businesses streamline their pick and pack fulfillment process, allowing them to focus on growth.
We employ a range of picking strategies to fulfill orders, including Piece Picking, Batch Picking, and Zone Picking.
Our pick-and-pack fulfillment services have been widely used by clients due to various reasons, including the ability to pack products in the right boxes to ensure their visual appeal and safety.
We can pack products with air pillows or other liners to protect the product stored inside, if required.
We use warehouse management and order fulfillment software to batch orders, print labels, and track inventory in a warehouse.
This software can be integrated with sales channels for effective results, making it easier to manage orders and inventory.
Custom pick and pack services are also available, specially customized to meet your order fulfillment requirements.
Broaden your view: Order Picking Software
Frequently Asked Questions
What does a pick and packer do?
A Pick and Packer selects items from a warehouse and packs them into orders for shipping, ensuring accurate and efficient order fulfillment. They play a crucial role in getting products from storage to customers quickly and reliably.
Is being a picker packer hard?
Being a picker packer can be physically demanding, requiring long hours on your feet and some heavy lifting. It's suitable for those who enjoy routine work and can handle physical activity all day.
What does your order is in fulfillment mean?
Your order is in fulfillment when it's being processed in our warehouse, getting ready for shipping. This is the first step before it's labeled and sent on its way to you
Featured Images: pexels.com