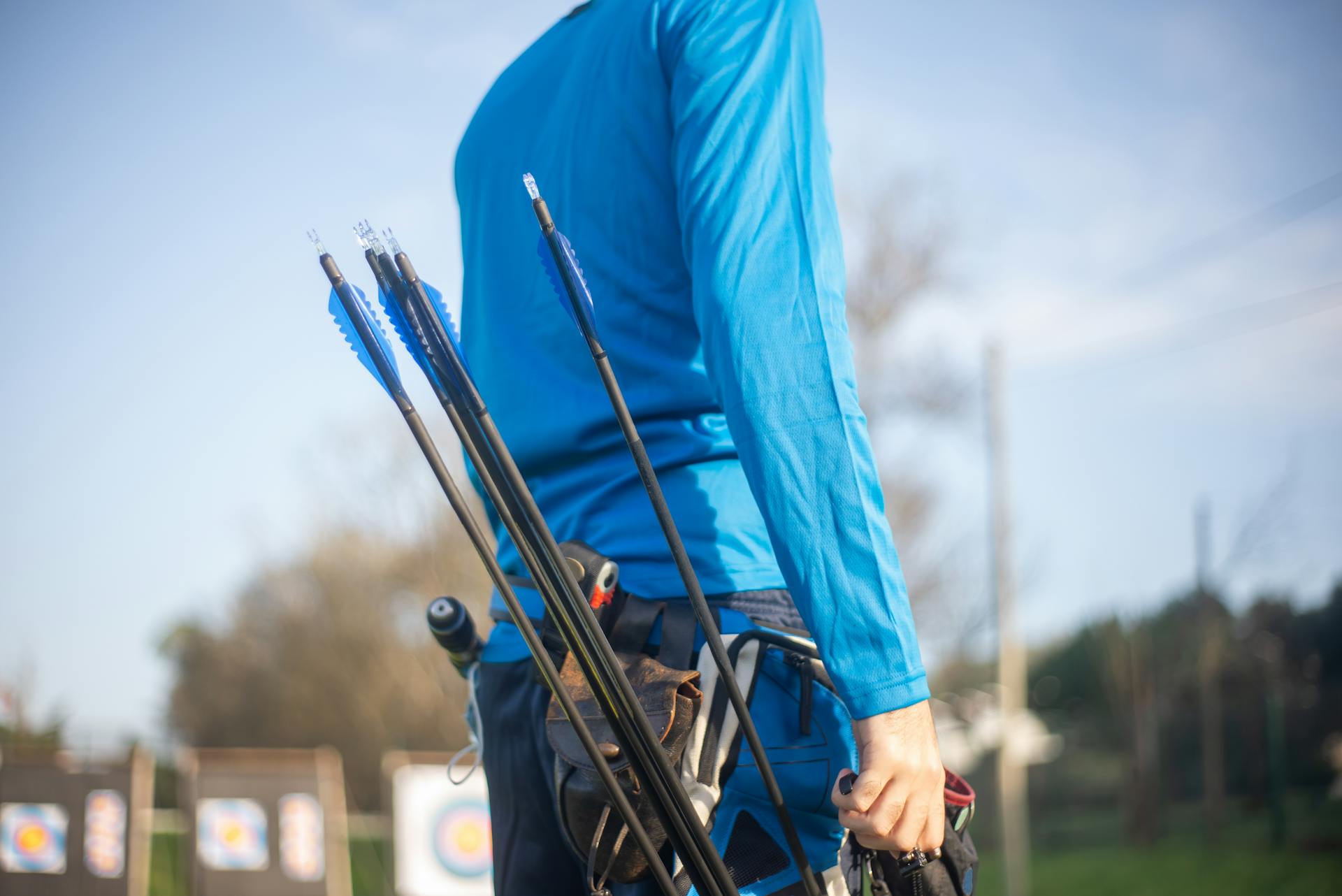
Order picking accuracy is crucial for warehouse efficiency. It directly impacts customer satisfaction, order fulfillment speed, and ultimately, the bottom line.
A single error in order picking can lead to a 30% increase in labor costs and a 20% decrease in productivity.
To achieve high order picking accuracy, it's essential to have a well-designed picking process. This includes clear and concise picking instructions, as well as a system for verifying order accuracy before shipping.
Studies have shown that using a pick-to-light system can improve order picking accuracy by 15% and reduce errors by 12%.
What Is Order Picking Accuracy?
Order picking accuracy refers to the ability of a warehouse or distribution center to accurately select and pick the correct items from inventory to fulfill customer orders.
Accurate order picking is crucial for maintaining customer satisfaction, reducing costs, and increasing efficiency. A single mistake can lead to delayed shipments, lost business, and damaged relationships.
Intriguing read: Customer Order Fulfillment
According to a study, order picking accuracy can range from 90% to 99% in a well-managed warehouse. This means that 1% to 10% of orders may contain errors.
Order picking accuracy is influenced by various factors, including the warehouse's layout, the type of inventory, and the efficiency of the picking process. A warehouse with a well-designed layout can reduce picking errors by up to 30%.
Effective order picking involves a combination of technology, processes, and training. This can include the use of barcode scanners, automated storage and retrieval systems, and regular training for warehouse staff.
A unique perspective: Pick & Pack Warehouse
Importance and Consequences
Order picking accuracy is crucial for meeting customer expectations and retaining hard-won customers. Customers want precisely what they ordered, and if they can't rely on a merchant to deliver the correct items consistently, they may take their business elsewhere.
A single mispick can be enough to lose customers forever, and in a competitive market, one order picking mistake can have severe consequences. Mis-picks during warehouse order picking make it hard to succeed in ecommerce.
Unhappy customers can quickly turn into negative reviews that deter potential buyers, which can harm your brand's reputation. Customer satisfaction is your ultimate guide when navigating ecommerce.
Mis-picks lead to costly returns and drain future revenue, causing lost sales opportunities as customers seek other retailers capable of better order accuracy. The ripple effect of negative reviews and returns creates a cycle that deters new buyers.
Order picking errors and mis-shipments deplete resources, requiring employees to switch to time-consuming corrective processes.
Optimizing Operations
Optimizing operations is key to achieving high order picking accuracy. Improving order picking accuracy doesn't have to be expensive or complicated. Simple strategies like optimizing the picking and packing process can make a big difference.
To optimize the picking and packing process, evaluate areas of improvement across your distribution centers to lower error rates. This can involve getting feedback from your team on what can be improved, optimized, or even automated. Some common areas to focus on include:
- Using the right barcodes
- Picking lists that are descriptive enough
- Picking lists that are digitized and optimized for similar inventory routes
By implementing these strategies, you can improve picking accuracy and functionality, and even reduce costs and increase customer satisfaction.
Operation Setbacks
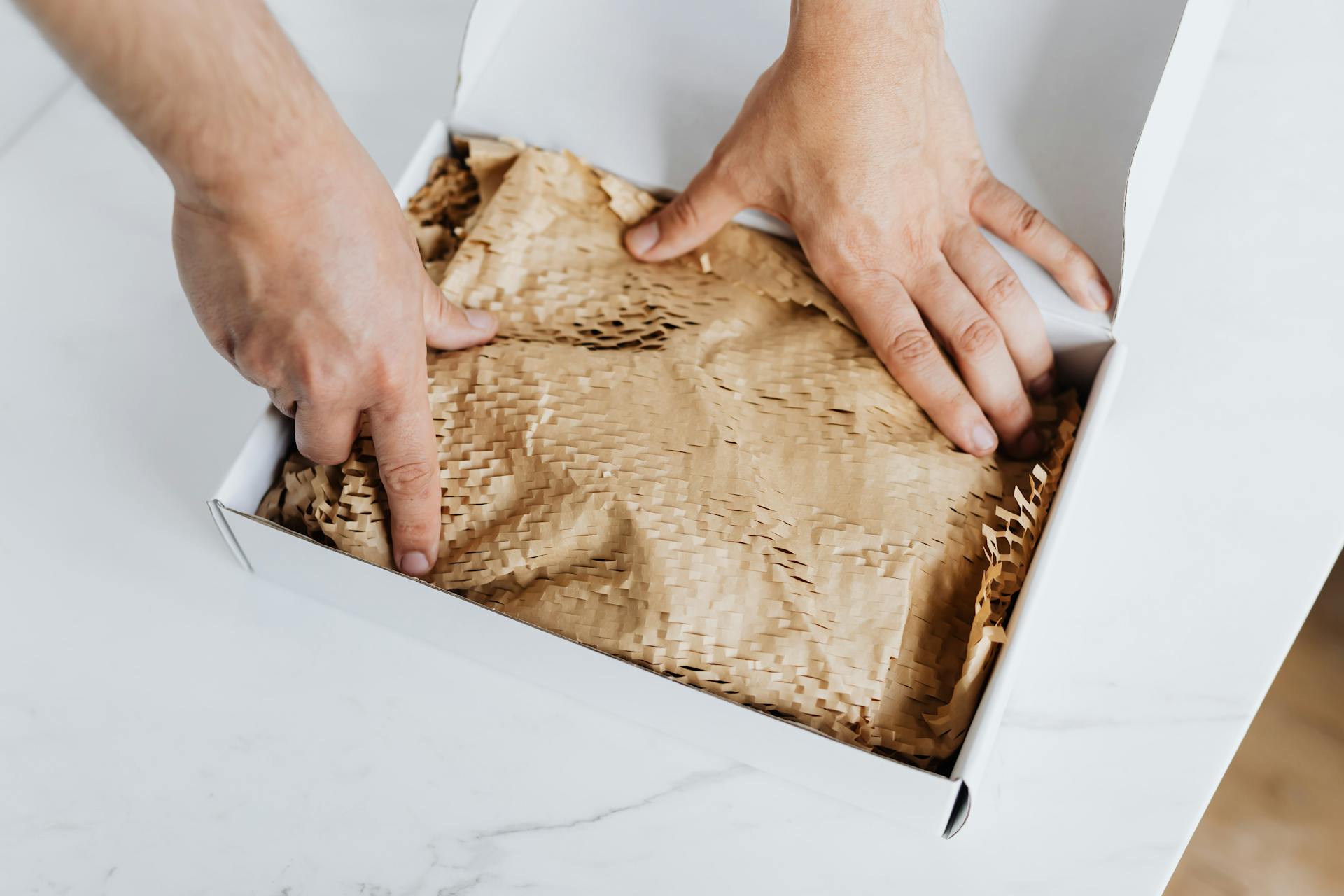
Operation setbacks can be a real challenge. Mis-picks create a cascade of problems that require a lot of resources to correct.
Managing returns, re-shipping orders, and assisting unhappy customers are just the tip of the iceberg. The result of failed order accuracy leads to financial losses, backorders, and chaos in your order fulfillment processes.
Correcting errors requires a great deal of resources. This includes time, money, and personnel to manage the fallout.
Failed order accuracy can lead to a loss of customer trust and loyalty. It's essential to get it right the first time to avoid these setbacks.
Establishing a system to collect and analyze feedback from pickers and other staff can help identify bottlenecks and improvement opportunities. This is a key part of continuous process improvement.
Implementing quality control checkpoints throughout the picking process can catch and correct errors promptly. This helps prevent the cascade of problems that arise from mis-picks.
Explore further: Time between Order and Delivery
Optimize Operations
Improving order picking accuracy doesn't have to be expensive or complicated. Here are some simple strategies for optimizing order picking accuracy.
Optimizing the picking and packing process is crucial to lowering error rates. Most order processing errors occur during this phase, so take the time to evaluate areas of improvement across your distribution centers.
Use the right barcodes to avoid confusion. Make sure picking lists are descriptive enough to prevent mistakes. Digitize and optimize picking lists for similar inventory routes to streamline the process.
Warehouse slotting can simplify the picking and packing stage by storing ecommerce inventory in a logical manner. This eliminates confusion for the picker and allows for faster picking by taking the guesswork out of where certain items are located.
A well-organized warehouse layout is essential for efficient picking. Give each SKU its own location to prevent pickers from having to hunt for the correct item. Clearly label SKUs to avoid confusion.
Partnering with a professional fulfillment provider can help you fulfill and ship orders accurately. They often have strategies in place to ensure high order accuracy rates, such as digitizing and optimizing picking lists.
The right picking strategy can make a big difference in your operations. Depending on your order volume, you may want to experiment with batch picking or zone picking to break down complex orders and speed up fulfillment.
Here are some common picking strategies to consider:
Organize Fulfillment Center
Organizing your fulfillment center is crucial to optimize operations. Chaos can cause a lot of problems, especially in picking. To make your picker's job easier, make sure the layout of your warehouse makes sense and lends itself to efficient picking routes.
Give each SKU its own location so pickers don't have to hunt for the correct item. Always label SKUs clearly. This will help reduce errors and improve picking accuracy.
Here are some tips to help you organize your fulfillment center:
- Store ecommerce inventory in a way that makes sense for the picker, such as by type, size, weight, location, etc.
- Use warehouse slotting to simplify the picking and packing stage.
- Implement a system to collect and analyze feedback from pickers and other staff to identify bottlenecks and improvement opportunities.
By implementing these strategies, you can improve picking accuracy and functionality, eliminate any possible confusion for the picker, and allow for faster picking by taking the guesswork out of where certain items are located.
Improving Efficiency
Having a high order pick rate is crucial for efficient order fulfillment. This rate measures the number of customer orders that can be fulfilled within a specific timeframe.
The order pick rate, also called picks-per-hour, can be improved by implementing efficient labor allocation and identifying training needs. AutoStore's mobile robots can operate simultaneously within the grid, allowing for parallel order processing.
Consider reading: Order Fulfillment Rate
To optimize the picking and packing process, evaluate areas of improvement across your distribution centers to lower error rates. This can be done by getting feedback from your team on what can be improved, optimized, or even automated across fulfillment operations.
- Are you using the right barcodes?
- Are picking lists descriptive enough?
- Are they digitized and optimized for similar inventory routes?
By implementing warehouse slotting, you can simplify the picking and packing stage by storing ecommerce inventory that makes the most sense for the picker. This can improve picking accuracy and functionality by eliminating any possible confusion for the picker.
Factors Affecting Efficiency
Improving efficiency in a warehouse requires a combination of effective strategies and technologies. One key factor is the warehouse layout, which can greatly impact the flow of products and materials. A well-designed warehouse layout can improve visibility, accessibility, and efficiency.
A good warehouse layout is essential for efficient order picking. As James Prior suggests, using a voice picking system or picker bots can improve verification and accuracy. Voice picking allows workers to receive picking instructions through a voice system, enabling hands-free and eyes-free operation.
Check this out: Warehouse Pick Pack Work
The right picking method is also crucial. According to Mohamed Shetta, training for newcomers about the picking method can improve efficiency. This includes recognizing the best picking order with 0 mistakes, which can encourage staff to be more focused.
Technology can also play a significant role in improving efficiency. As Abel Le Rouge points out, using technology such as Pick to Light, Voice-directed Picking, or RFID Picking can enhance accuracy and speed. These methods can help reduce manual scanning and improve the overall picking process.
Here are some common factors that affect efficiency in a warehouse:
- Warehouse layout and design
- Picking method and technology
- Staff training and motivation
- Use of automation and innovation
- Quality control and feedback
How to Improve?
To improve efficiency, it's essential to focus on order accuracy. ShipBob's best-in-class warehouse management system (WMS) can help brands manage inventory in real-time, reducing picking, packing, and shipping errors.
Analyzing order data is a crucial step in identifying trends related to order accuracy and error rates. This allows you to root out the source of issues and prevent future mistakes.
Implementing quality control checkpoints throughout the picking process can catch and correct errors promptly. Mohamed Shetta suggests training newcomers about the picking method and recognizing the best picking order with 0 mistakes to encourage staff to focus.
Optimizing the warehouse layout and design can improve visibility, accessibility, and flow of products and materials. This can be achieved by using a good layout for the warehouse, as suggested by Mohamed Shetta.
To improve picking accuracy, consider using technology such as Pick to Light, Voice-directed Picking, or RFID Picking. These methods can enhance accuracy and speed, as mentioned by Abel Le Rouge.
Regularly reviewing order picking results and conducting frequent audits can help improve accuracy. This can also involve establishing clear and measurable standards, as suggested by James Prior.
Here are some strategies to improve order accuracy:
- Implement a warehouse management system (WMS) to track and monitor inventory and order status.
- Use technology such as Pick to Light, Voice-directed Picking, or RFID Picking to enhance accuracy and speed.
- Train and motivate picking staff with regular training and coaching.
- Regularly review order picking results and conduct frequent audits.
- Establish clear and measurable standards for picking accuracy.
By implementing these strategies, you can improve order accuracy and efficiency, leading to increased customer satisfaction and loyalty.
Technology and Automation
Technology and Automation plays a crucial role in achieving high order picking accuracy. Leveraging technology can significantly reduce human error during the picking process.
Barcode scanning technology can verify items during picking, confirming location, quantity, batch/lot numbers, and serials. This feature is available on Propel Apps' platform, making it an efficient solution.
Automated picking solutions can increase speed and accuracy, especially in high-volume environments. Consider using robotic systems to streamline your picking process.
Voice picking technology allows for hands-free operation, reducing errors and increasing productivity. By implementing voice-directed picking systems, you can optimize your picking routes and improve overall efficiency.
A fresh viewpoint: Order to Delivery Process
Training and Management
Continuous training is key to improving order picking accuracy. Regular training sessions should cover best practices, new technologies, and error prevention techniques to help staff stay up-to-date.
Monitoring individual picker performance is also crucial. This involves tracking metrics such as order accuracy rates and efficiency statistics to identify areas where staff may need additional training.
Regular audits and checks of fulfillment accuracy rates are essential to maintaining high standards. This includes evaluating inventory accuracy, workforce performance, and efficiency statistics to ensure everything is running smoothly.
Regular Audits
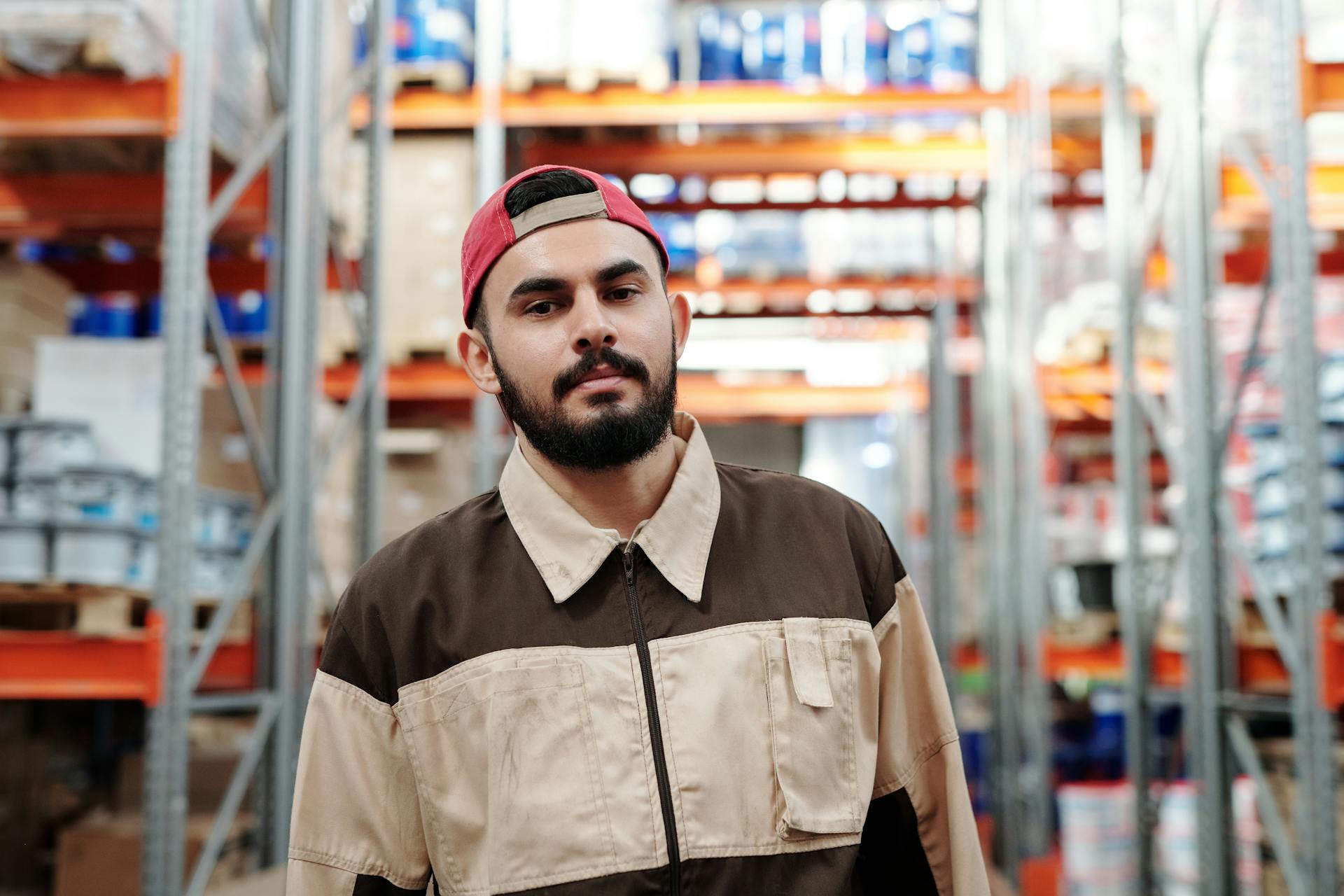
Regular Audits are a crucial part of ensuring your operations are running smoothly. Conducting regular audits allows you to evaluate inventory accuracy, which is essential for maintaining order accuracy.
Audits can also help you identify areas where your workforce performance can be improved. Regular checks of workforce performance can help you pinpoint problem areas and make necessary adjustments.
Conducting audits and checks of your fulfillment accuracy rates often is essential for maintaining high standards. Evaluating efficiency statistics can also help you optimize your operations and reduce waste.
Regular audits can help you stay on top of your operations and make data-driven decisions. By regularly evaluating your inventory accuracy, workforce performance, and efficiency statistics, you can maintain a high level of order accuracy and keep your operations running smoothly.
Training and Workforce Management
Providing regular training to staff is crucial in order picking, as it helps them stay up-to-date on best practices and new technologies. This can be done through continuous training sessions, which should be a regular part of your workflow.
Monitoring individual picker performance is also essential, as it allows you to identify areas for improvement and provide targeted training to those who need it. By doing so, you can optimize your order picking process and reduce errors.
Continuous training sessions can help prevent errors and improve efficiency in order picking.
Measuring and Benchmarking
Measuring and benchmarking order picking accuracy is crucial for warehouses to improve their performance.
To effectively manage order picking accuracy, warehouses must implement a robust system for tracking and improving it. This includes defining what constitutes accurate picking, which includes correct item, quantity, and condition.
Order picking accuracy can be calculated using the formula: (Number of Accurately Picked Orders / Total Number of Orders Picked) × 100%. Regular assessment of this KPI provides valuable insights into picking performance and areas for enhancement.
Benchmarking order picking accuracy can be done by comparing it with industry standards and best practices, as well as with competitors and peers. This can help identify gaps and opportunities for improvement, and set realistic goals and targets.
In fact, Mohamed Shetta suggests measuring order picking accuracy on a daily basis using the KPI "% of accuracy for orders", which is the number of wrong order pickings divided by total picking orders.
For more insights, see: Postal Orders of the United Kingdom
Conclusion and Future
Order picking accuracy is a crucial aspect of warehouse operations, and with the right strategies, it can be significantly improved. By implementing a zone picking system, warehouses can reduce picking errors by up to 25%.
Using a barcode scanner to verify each item can increase accuracy by 15%. This simple technology can make a huge difference in the efficiency of the picking process.
Automating the picking process using robots can increase accuracy by up to 99%. This is especially useful for high-value or high-priority items where accuracy is paramount.
The key to improving order picking accuracy is to identify and address the root causes of errors. By analyzing data and implementing targeted solutions, warehouses can reduce errors and improve efficiency.
Implementing a cycle counting program can help identify and correct errors before they become major issues. This can be especially effective for high-value or high-priority items.
By combining these strategies, warehouses can achieve order picking accuracy rates of over 99%. This is a significant improvement over the 90% accuracy rate that is typical for manual picking systems.
Explore further: Order Fulfillment Strategies
Frequently Asked Questions
How do you calculate order accuracy?
To calculate order accuracy, divide the number of perfect orders by the total number of orders and multiply by 100. A perfect order meets all requirements, including correct items, quantities, documentation, and delivery specifications.
What is a good order of accuracy?
A good order accuracy rate is typically above 99%, which is considered excellent and a goal for companies aiming to provide exceptional customer service. Achieving this rate requires a high level of order processing efficiency and attention to detail.
Sources
- https://www.shipbob.com/blog/order-accuracy/
- https://www.elementlogic.net/uk/insights/warehouse-picking-kpis/
- https://www.linkedin.com/advice/0/how-can-you-measure-warehouse-order-picking-nwvhf
- https://www.logiwa.com/blog/precision-order-picking-how-online-retailers-can-avoid-mis-picks
- https://www.propelapps.com/blog/enhancing-order-picking-accuracy-in-warehouse-operations
Featured Images: pexels.com