
Maximizing efficiency and cost savings in a pick and pack warehouse is crucial for businesses to stay competitive. A well-designed pick and pack process can reduce labor costs by up to 30%.
To achieve this, warehouses can implement a zone picking system, which can increase picker productivity by 25%. This is because pickers only need to travel to specific zones to collect items, reducing walking distances and time.
A study found that implementing a pick-to-light system can reduce picking errors by 90%. This is because pickers are guided by lights that indicate the correct items to pick, minimizing mistakes.
By streamlining their pick and pack operations, warehouses can also reduce inventory holding costs, which can account for up to 20% of total inventory costs.
For more insights, see: Automated Pick and Pack System
What Is
Pick and pack is a fulfillment process where items are selected from inventory and then placed in a box for shipping. It's a straightforward process that involves four main steps.
The first step is picking, where items are chosen from inventory. This is a critical part of the process, as it determines what gets shipped out to customers.
Picking involves selecting the right items, in the right quantities, and getting them ready for packing. This requires a good understanding of inventory management.
The next step is packing, where the picked items are placed in a box or container. This is where the item is prepared for shipping, and it's essential to get it right.
Packing involves carefully placing items in a box, making sure they're secure and won't get damaged during transit. This requires attention to detail and a focus on customer satisfaction.
The four main steps to picking and packing are a key part of a well-run warehouse operation. By following these steps, businesses can ensure their customers receive their orders accurately and on time.
A different take: What's the Right Way to Move Pallets with a Forklift
Warehouse Setup
Organizing your warehouse is crucial for efficient pick and pack fulfillment. It's called "slotting", a warehouse operations strategy that minimizes warehouse travel and search time.
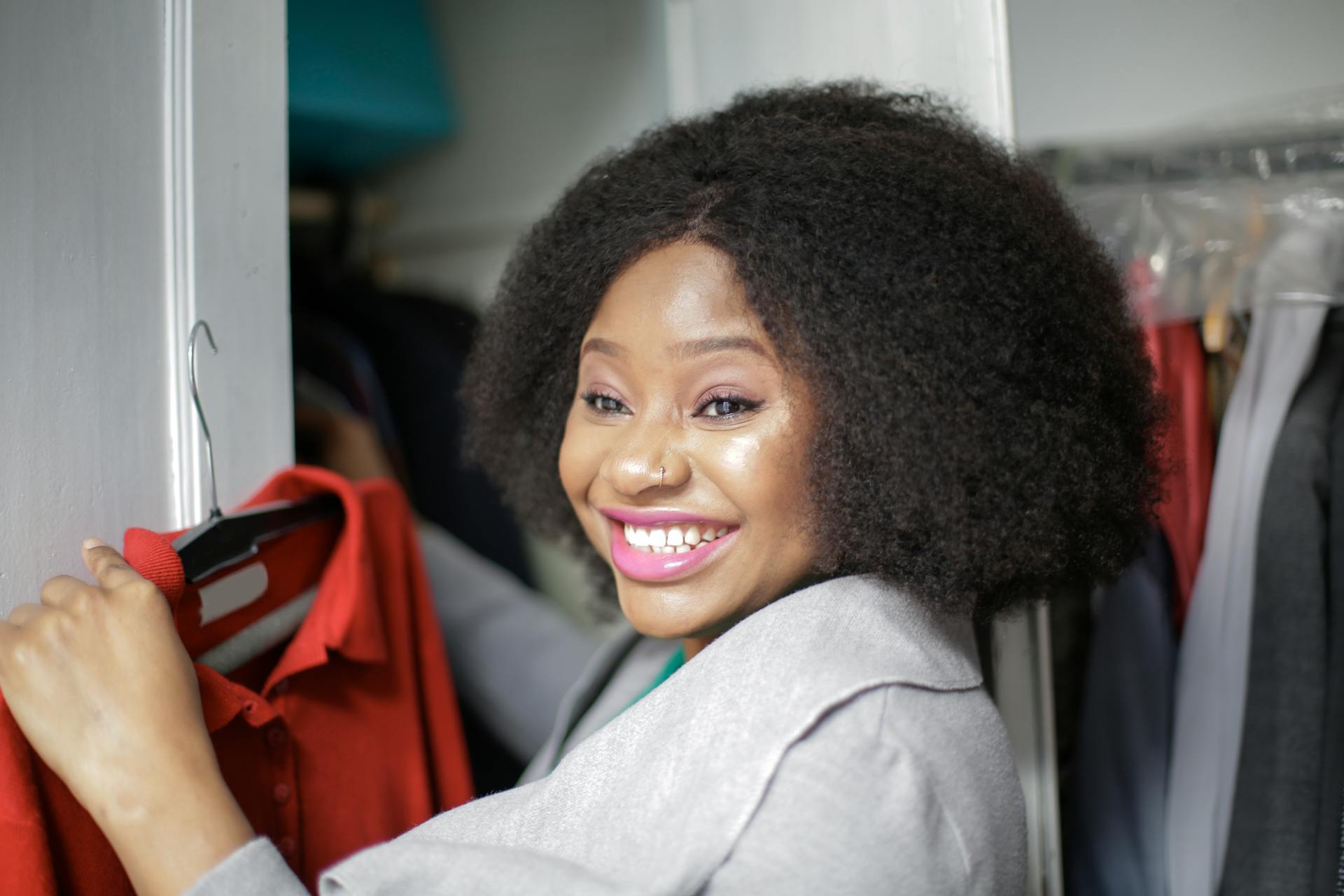
To manage slotting, you need advanced inventory management software to guide pickers to items. This approach is too much for someone to remember, especially with new product introductions updating item slotting and warehouse systems.
Zone picking increases complexity but helps with speed. Pickers work specific warehouse zones, moving items across them all so items can be organized by order ahead of delivery to a packing station.
Warehouse Setup
Organizing your warehouse is crucial to efficient order fulfillment. This is where slotting comes in, a warehouse operations strategy that minimizes warehouse travel and search time.
Slotting involves identifying the most efficient route through a warehouse, which helps speed up the pick and pack fulfillment process. It's not just about placing items in a random order.
Popular items should be placed far apart to avoid traffic jams. Visually similar items should be separated to prevent picking errors.
Zone picking is another approach that increases complexity but helps with speed. In this method, your warehouse is divided into sections or zones, often based on product type or demand frequency.
Recommended read: Pick and Pack Warehouse Services
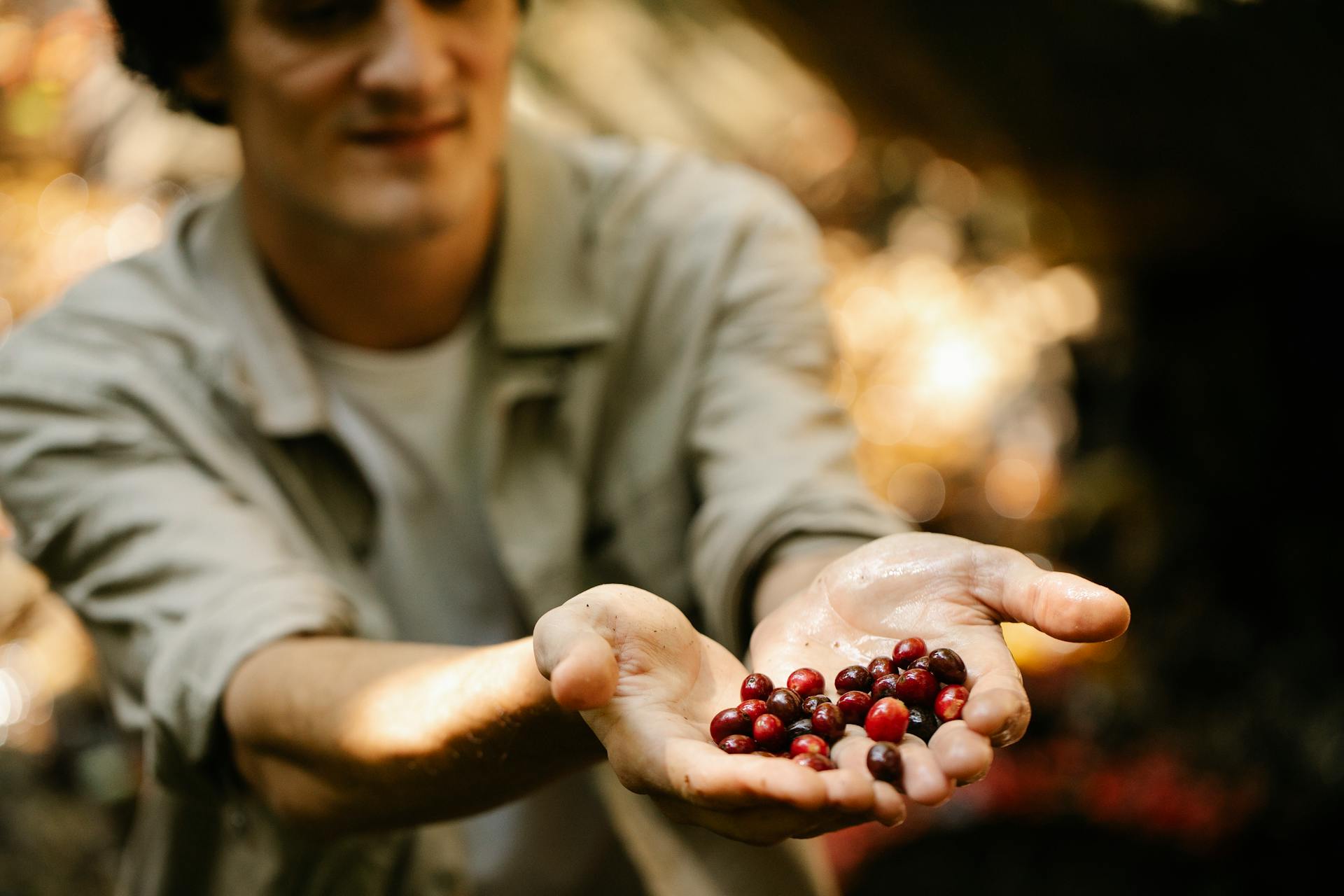
Each picker is assigned a zone and is responsible for picking all items within that area. Orders requiring items from multiple zones are passed sequentially from one zone to the next.
Zone picking is excellent for large warehouses or when specialized handling is needed for certain products. For example, a sports equipment retailer could have one zone for apparel, another for footwear, and a third for equipment to ensure specialists handle fragile items.
A Warehouse Management System (WMS) is essential for coordinating staff in a zone picking setup. The WMS helps staff stay organized, especially when inventory updates require changes to zone picking paths.
Batch
Batch picking is a warehouse strategy that organizes orders into groups based on where items are in the warehouse.
This approach reduces travel time and is effective for businesses dealing with numerous small orders in a large warehouse space.
Batch picking involves collecting items for multiple orders in a single trip through the warehouse by grouping similar orders.
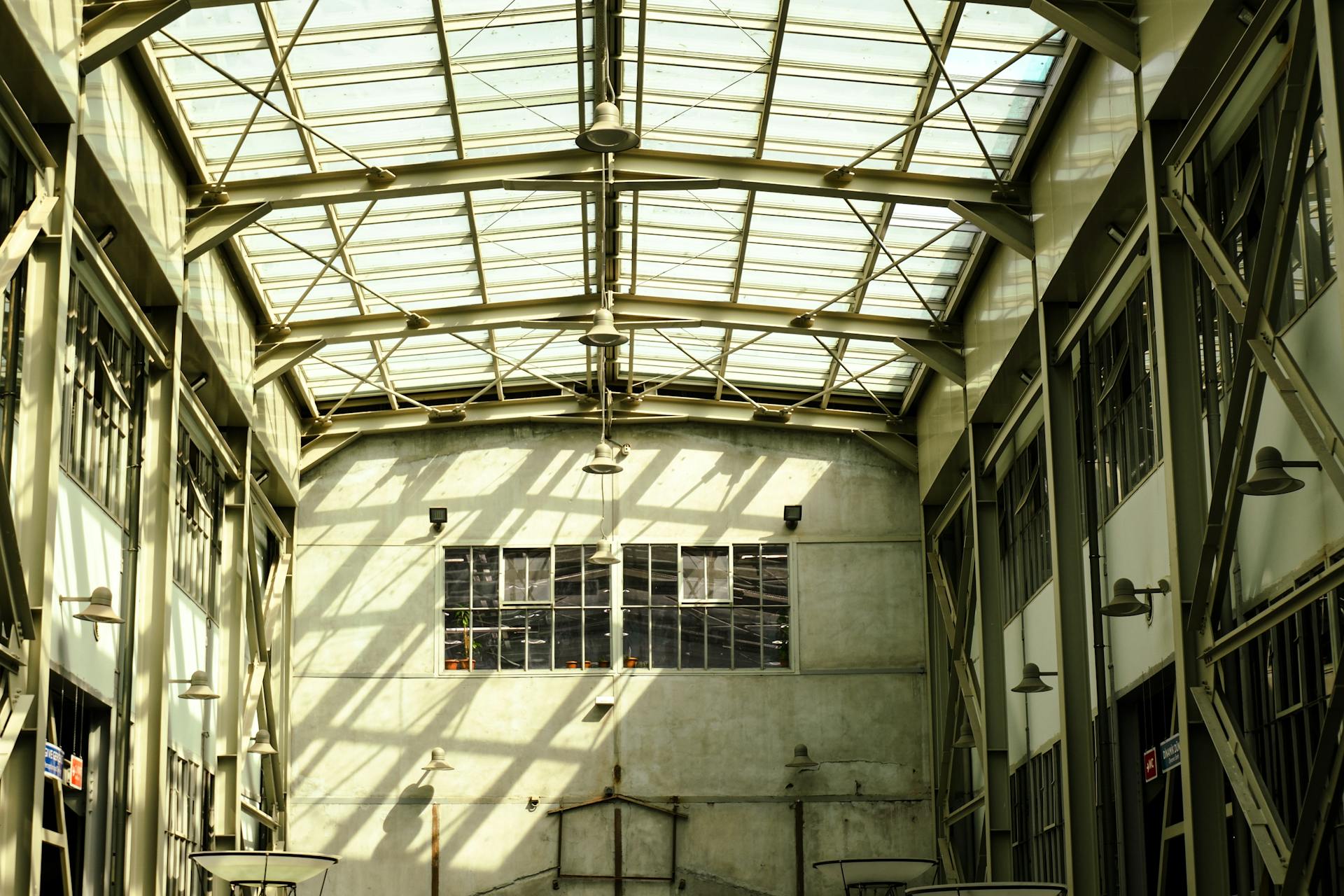
This strategy is typically required by a Warehouse Management System (WMS) to guide staff on when to pick items and from where.
An online beauty retailer, for instance, might batch-pick orders for lipsticks, gathering all “Ruby Red” shades for the day’s orders in one efficient warehouse run.
By grouping similar orders, batch picking reduces travel time and increases efficiency in the pick and pack fulfillment process.
Kitting
Kitting is a specialized kind of pick and pack service where your warehouse assembles various SKUs into a different, single SKU to create a subscription pack or promotional bundle. This often requires adjusting warehouse packing techniques monthly or as new promotions arise.
In a warehouse setup, kitting involves pre-assembling related products into ready-to-ship packages. Workers at packing stations gather items that frequently sell together and package them in advance.
A skin care company might notice that customers often buy the same set of moisturizers, toners, and cleansers, making kitting a convenient option. This way, pickers can grab the pre-made kit instead of individual items.
Kitting is slightly different from bundling, a strategy in which brands specifically market curated collections of products.
Receiving
The receiving process is a crucial step in getting your warehouse up and running. Your Warehouse Management System (WMS) instantly processes the order, converting it into actionable steps for your warehouse staff.
A unique identifier is assigned to each order, allowing your team to track its progress. This identifier is based on factors like shipping method, ensuring timely delivery.
Your WMS also prioritizes orders, so the most critical ones get attention first. This helps prevent delays and keeps customers happy.
The moment an order is placed, a packing slip is generated, detailing everything from item specifics to its location within the warehouse.
Pick and Pack Methods
As your ecommerce business grows, you may need to adapt your warehouse picking and packing methods to meet demand. Startups and early-stage companies may get away with picking items one at a time, but as sales increase, more advanced methods are necessary.
Your pick and pack system should match your inventory and order complexity. Picking and packing methods can be simple or advanced, depending on the size of your business.
You can group items by shared traits, like turnover or packing methods, using class-based inventory management. For example, you may group products that all need bubble wrap or large items that don’t require an additional box.
Expand your knowledge: Do You Need a Certification to Use a Pallet Jack
Class-Based

Class-Based inventory management can be a game-changer for businesses with diverse product offerings.
You group items by shared traits, like turnover or packing methods, to streamline your inventory system. For example, grouping products that all need bubble wrap can simplify the packing process.
Large items that don’t require an additional box can be grouped together, reducing waste and saving resources. This can help reduce packaging costs and minimize environmental impact.
By categorizing items by shared traits, you can create a more efficient inventory system that saves time and money.
If this caught your attention, see: Case Picking System
Methods
As your ecommerce business grows, you may have to evolve your warehouse picking and packing methods to meet demand. Startups and early-stage companies may get away with picking items one at a time.
Advanced warehouse picking methods create speed as you sell more. Your pick and pack system should match your inventory and order complexity.
Here are a few pick and pack processes to consider: picking items one at a time, and more advanced methods that create speed.
Take a look at this: Order Picking Methods
Piece
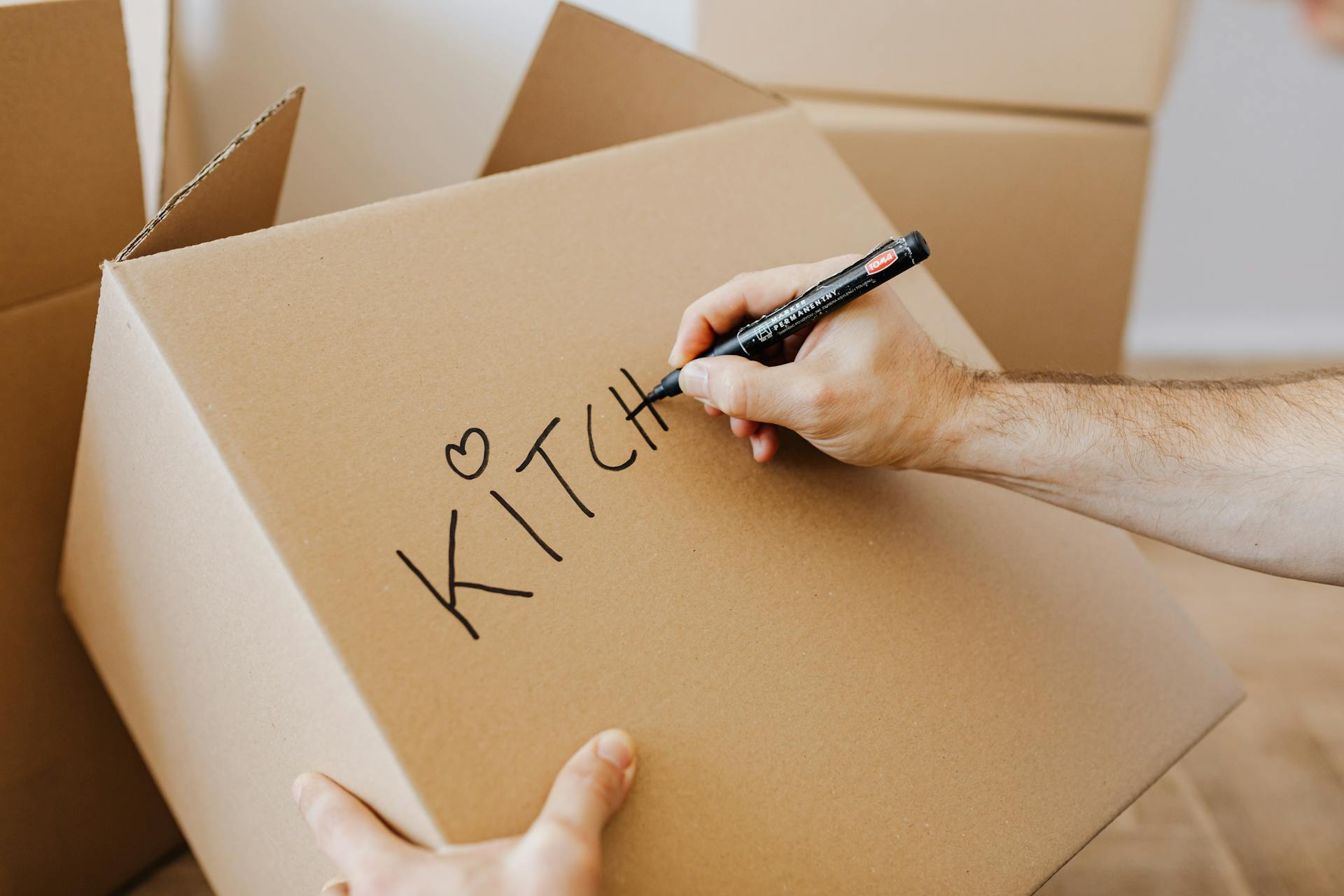
Piece picking is a method where team members pick one order at a time and take the items to a packing station.
This method works well for small businesses with only a few daily order picking requirements.
Piece picking, also known as discrete picking, is the simplest method.
It's ideal for businesses that have low order volumes or deal with large, complex products that require individual attention.
For example, a custom furniture retailer might use piece picking to carefully select and inspect each unique, handcrafted item.
Optimizing Pick and Pack
A well-designed pick and pack warehouse can reduce labor costs by up to 30%.
The key to achieving this is to streamline the picking process, which can be done by implementing a zone picking system. This involves dividing the warehouse into separate areas, each containing a specific range of products.
By doing so, pickers can focus on a single area, reducing travel time and increasing productivity.
Studies have shown that a zone picking system can increase picking speeds by up to 25% and reduce errors by 15%.
Additionally, using a warehouse management system (WMS) can help optimize the picking process by providing real-time inventory updates and automating tasks such as order processing and shipping.
A WMS can also help reduce inventory levels by up to 20%, freeing up valuable warehouse space.
Implementing a pick-to-light system can also improve efficiency by providing pickers with visual instructions and reducing the need for paper-based picking lists.
This can lead to a significant reduction in errors and increased productivity, with some warehouses reporting a 90% reduction in errors.
By implementing these strategies, warehouses can optimize their pick and pack processes, leading to increased efficiency, reduced labor costs, and improved customer satisfaction.
For more insights, see: Pick and Pack System
Software
Pick and pack software is essential for a smooth and efficient warehouse operation. It connects warehouse activity and communication, ensuring that every step happens in coordination with the others.
Order integration is the first step, where software connects to sales channels and receives new orders. This allows for real-time visibility into order status and fulfillment.
Picking is the next step, where staff receive picking lists and optimized paths on mobile devices. This enables them to see item details, locations, and quantities, making it easier to identify potential bottlenecks and adjust workflows as needed.
Packing involves scanning picked items and assigning packing tasks based on weight, size, and order requirements. This ensures that packers receive alerts for missing or incorrect items, allowing for immediate intervention and error correction.
Shipping is the final step, where the software generates shipping labels with accurate weight and address information. This streamlines the dispatch process and allows teams to track shipped orders in real-time, providing updates to customers and improving communication.
Here are some key features of pick and pack software:
- Order integration
- Picking
- Packing
- Shipping
Inventory management software is also crucial for tracking SKUs, their quantities, and storage locations. This ensures that every item is accounted for and easily accessible.
Real-time inventory visibility prevents stockouts and overstocking, ensuring products are readily available for pick and pack fulfillment without wasted capital.
Fulfillment Strategies
To streamline pick and pack fulfillment, warehouses use different picking strategies to reduce labor costs. Piece picking, batch picking, zone picking, and wave picking are the main methods used.
Piece picking involves picking individual items one by one, while batch picking involves picking multiple items at once. Zone picking is a combination of the two, where items are grouped by location. Wave picking is the most complex method, combining batch and zone picking to achieve the greatest efficiency.
Here are the different picking strategies used in warehouses:
- Piece picking
- Batch picking
- Zone picking
- Wave picking
The packing process is also crucial in pick and pack fulfillment, and warehouses use strategies like kitting, cartonization, and branded packaging to improve efficiency and customer experience.
Strategies Explained
Pick and pack fulfillment is a crucial process in ecommerce and retail, and streamlining it can reduce costs and improve customer satisfaction. One way to do this is by implementing efficient picking strategies.
Piece picking, batch picking, zone picking, and wave picking are four different picking strategies that warehouses use to reduce labor required to choose the right products for an order.
Here are some common picking strategies:
The packing process is also crucial, and there are several strategies to consider. Kitting, cartonization, and branded packaging are three ways to improve efficiency and customer satisfaction.
Kitting involves packaging related items together, while cartonization optimizes the use of space in boxes. Branded packaging adds a personal touch to the customer experience.
By implementing these strategies, you can streamline your fulfillment services, reduce shipping costs, and leave a lasting impression on your customers.
Wave
Wave picking is a complex method that combines batch and zone picking to achieve the greatest efficiency. It's ideal for high-performing businesses with thousands of monthly orders and high SKU volumes.
Wave picking involves creating "waves" of orders based on shipping priority, product type, or carrier routes. This allows pickers to work on specific orders by zone or batch.
By prioritizing urgent orders, wave picking ensures that priority orders are picked and shipped first. This is especially useful during peak periods like holiday sales.

Wave picking can save money over time, making it a viable option for high-volume businesses. It's a strategy that leverages batch efficiencies while meeting shipping deadlines.
A major book retailer might use wave picking to create one wave for overnight shipping orders across all zones during a holiday sale. This ensures that priority orders are picked and shipped first, followed by waves for standard shipping.
For your interest: Packing List Shipping
Shipping
Shipping is a crucial part of the fulfillment process, and it's where the order is handed over to the carrier for delivery to the customer.
Bulk shipping discounts can be negotiated with shipping carriers, and these savings can be passed on to the business, as seen with ShipBob, which ships hundreds of thousands of packages daily and passes on the savings.
The packed order is now ready for shipping, with shipping labels generated by the warehouse management system (WMS) that has already calculated the most cost-effective shipping method based on order value, weight, and delivery speed.
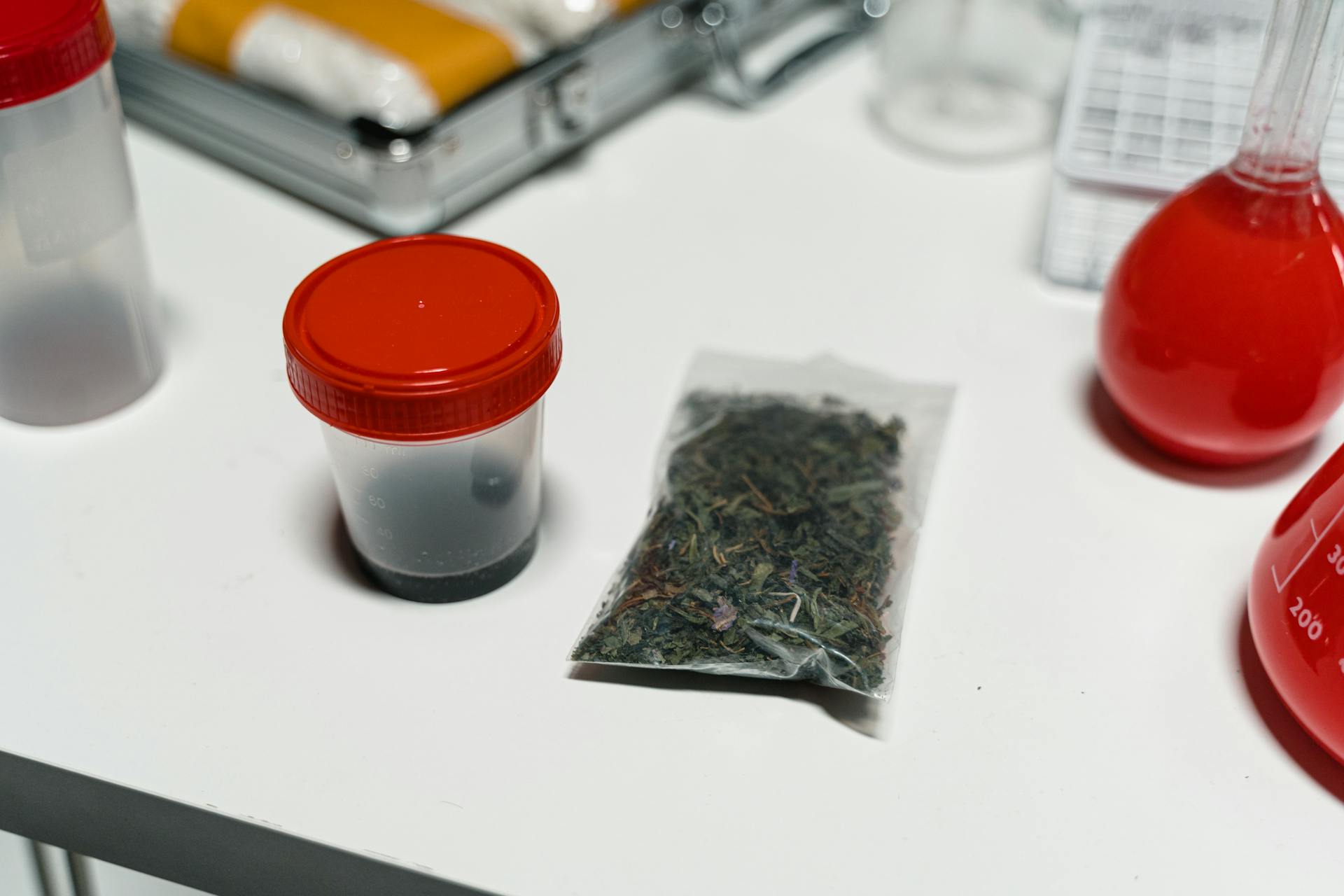
Your WMS tracks every step in the journey, providing real-time updates on order status, ensuring transparency and accountability throughout the shipping process.
Order shipping is a critical phase where the packed order is handed off to the chosen shipping carriers, with the WMS generating shipping labels that are applied by the team.
The shipping team meticulously places the package in the designated area to await the arrival of the carrier truck, ensuring a smooth and efficient handoff.
In-house shipping can be managed using your own facilities and staff, or you can outsource to third-party logistics providers (3PLs) that specialize in order fulfillment and offer expertise, scalability, and cost savings.
Warehouse Operations
In a pick and pack warehouse, warehouse operations play a crucial role in ensuring smooth and efficient order fulfillment.
A well-designed warehouse layout is essential for maximizing storage capacity and reducing travel times for warehouse staff. This can be achieved by implementing a zone picking system.
Effective inventory management is vital in a pick and pack warehouse, as it enables accurate tracking of stock levels and prevents stockouts or overstocking. This can be achieved by implementing a first-in, first-out (FIFO) inventory management system.
Warehouse staff should be trained to efficiently pick and pack orders, with an average pick rate of 150-200 picks per hour. This can be achieved by implementing a standardized picking process and providing regular training to staff.
A pick and pack warehouse can process up to 1,000 orders per day, depending on the size of the warehouse and the number of staff available. This can be achieved by implementing a efficient warehouse management system (WMS) and utilizing automation technologies such as robotic picking arms.
Efficiency and Cost
Deploying handheld barcode scanners can help ensure accuracy in order picking, reducing errors and saving time. Strategically organizing items by placing popular ones in easily accessible locations can also improve efficiency.
To optimize the packing process, select the appropriate sized box and packing materials, balancing protection with cost-effectiveness. Regularly monitoring metrics like order picking accuracy can help refine the pick & pack process for improved efficiency and reduced returns.
Here are some key tips to keep in mind:
- Optimize packing materials to balance protection with cost-effectiveness.
- Monitor order picking accuracy to continually refine the pick & pack process.
- Use bulk shipping discounts to save money on shipping costs.
Cost
Optimizing the packing process is key to cost-effectiveness. By selecting the right sized box and packing materials, you can balance protection with cost.
Regular monitoring of metrics like order picking accuracy is crucial to refining the pick & pack process. This helps reduce returns and improves efficiency.
ShipBob has negotiated bulk shipping discounts with the four major U.S. carriers, passing the savings onto their customers.
Here are some ways to save on shipping costs:
- Optimize the packing process by selecting the right sized box and packing materials.
- Regularly monitor metrics like order picking accuracy to improve efficiency.
Zenventory can help optimize your pick & pack fulfillment, but you'll need to complete their form to learn more.
Final Thoughts
Embracing technologies and best practices in inventory management and order fulfillment is crucial for success in e-commerce.
In today's competitive landscape, leveraging robust warehouse management software like Zenventory is essential for mastering the art of pick & pack.
Tools and Services
In a pick and pack warehouse, technology plays a vital role in streamlining operations.
The Zenventory mobile app is a game-changer, offering real-time stock location tracking and barcode scanning. This means warehouse staff can quickly and easily locate items and pick orders with precision.
Over 50 reports are available to provide valuable insights into warehouse operations, including inventory and shipping. This data can be used to make informed decisions and optimize workflows.
Electronic order picking options, such as web, mobile app, or custom printed pick tickets, cater to different operational preferences. This flexibility ensures that warehouse staff can work efficiently, regardless of their specific needs.
Here are some of the key tools and services that can help you pick, pack, and ship like a pro:
- The Zenventory mobile app offers real-time stock location tracking, paperless order picking, and barcode scanning.
- Over 50 reports provide insights into inventory, shipping, and other aspects of warehouse operations.
- Electronic order picking options include web, mobile app, or custom printed pick tickets.
Tracking and Management
In a pick and pack warehouse, accurate tracking and management are crucial for efficient operations. Inventory management software is essential for tracking SKUs, their quantities, and storage locations, ensuring every item is accounted for and easily accessible.
A Warehouse Management System (WMS) like Zenventory automates inventory tracking, enhances order accuracy, and streamlines warehouse operations. Real-time insights provided by WMS enable you to make informed decisions and optimize your warehouse operations.
Serial numbers are vital for inventory management, and tracking them effectively is essential. Utilizing a WMS can streamline the process of tracking serial numbers, ensuring that every item is accurately accounted for.
Pick & pack fulfillment is a critical process in a warehouse, and it requires precision and speed. Implementing pick & pack software can automate crucial order fulfillment tasks, including inventory level management, shipping label generation, and order tracking.
In a pick and pack warehouse, accuracy is key, and barcode scanning devices play a crucial role in ensuring that each item matches the order. Automated picker assignment technology can pre-assign specific orders to individual pickers based on various criteria, further enhancing the accuracy and reliability of the pick & pack process.
Here are some key features of a WMS that can help streamline inventory management and tracking:
- Automates inventory tracking and enhances order accuracy
- Provides real-time insights into inventory levels and storage locations
- Streamlines warehouse operations and improves efficiency
Frequently Asked Questions
What is a picker packer in a warehouse?
Picker packers, also known as order fulfillment associates, are warehouse workers responsible for picking products from shelves and packing them for shipment to customers. They play a crucial role in today's economy by ensuring timely and accurate order fulfillment.
Is being a picker packer hard?
Being a Picker Packer can be physically demanding, requiring long hours on your feet and some heavy lifting. It's a role that suits those who are comfortable with routine and physical activity.
Sources
- https://redstagfulfillment.com/ultimate-guide-pick-and-pack-methods/
- https://www.shipbob.com/ecommerce-fulfillment/pick-pack-fulfillment/
- https://www.shopify.com/blog/pick-and-pack-fulfillment
- https://www.warehousingandfulfillment.com/services/pick-and-pack-fulfillment-warehouse-services/
- https://www.zenventory.com/blog/understanding-pick-and-pack-how-it-works-in-warehouse-fulfillment
Featured Images: pexels.com