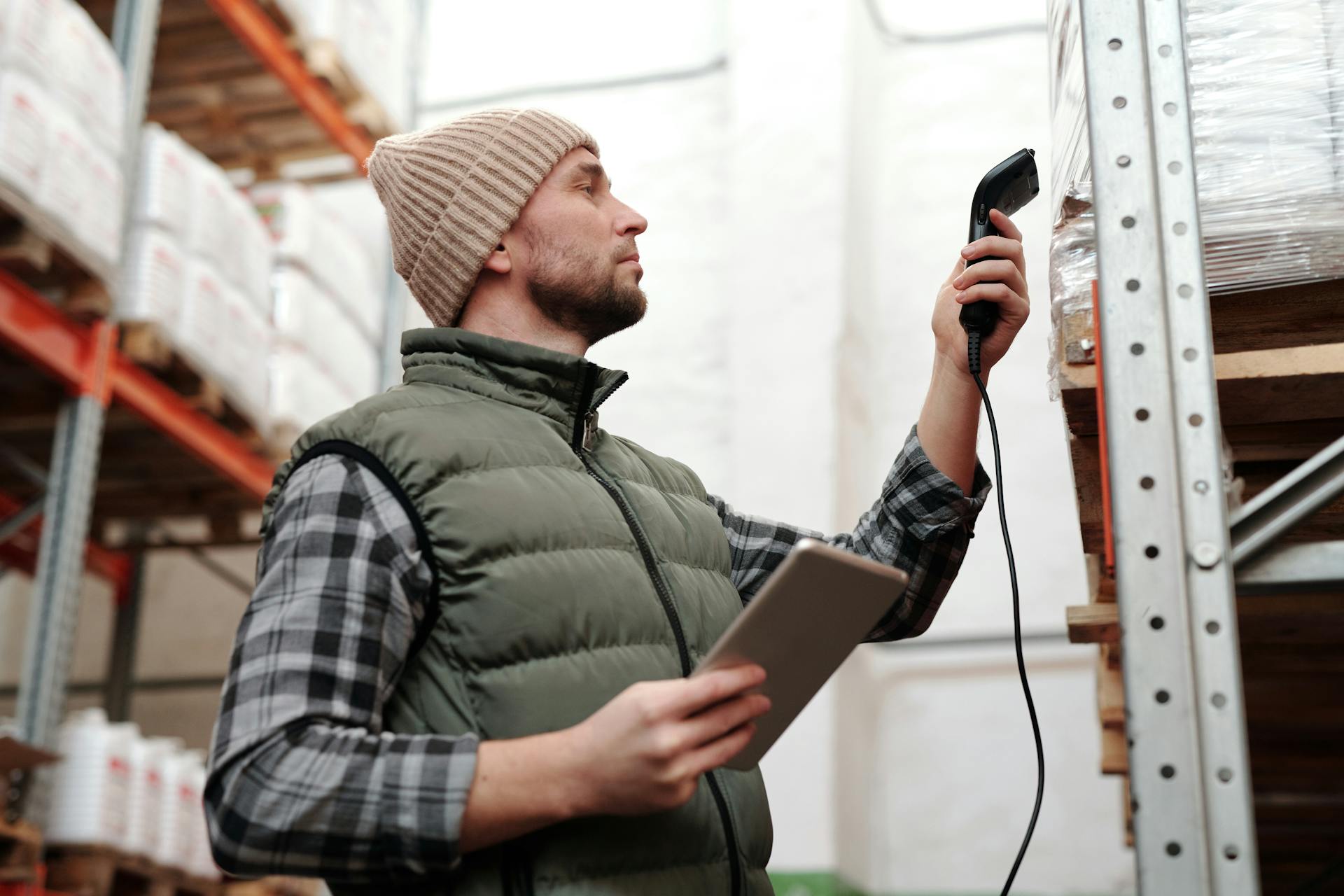
An automated pick and pack system is a game-changer for efficient warehouse operations. By streamlining the picking and packing process, businesses can significantly reduce labor costs and improve order fulfillment rates.
These systems use advanced technology, such as artificial intelligence and machine learning, to optimize picking routes and reduce errors. This results in faster order fulfillment times and increased customer satisfaction.
A well-designed automated pick and pack system can process up to 1,000 orders per hour, making it an ideal solution for high-volume warehouses.
What Is an Automated Pick and Pack System?
An Automated Pick and Pack System is a technology that streamlines order fulfillment by automating the picking and packing process.
It uses a combination of warehouse management software, conveyor systems, and robotic arms to quickly and accurately pick and pack orders.
These systems can process thousands of orders per day, making them ideal for businesses with high volume sales.
They also reduce labor costs and minimize the risk of human error, which can lead to damaged products or incorrect orders.
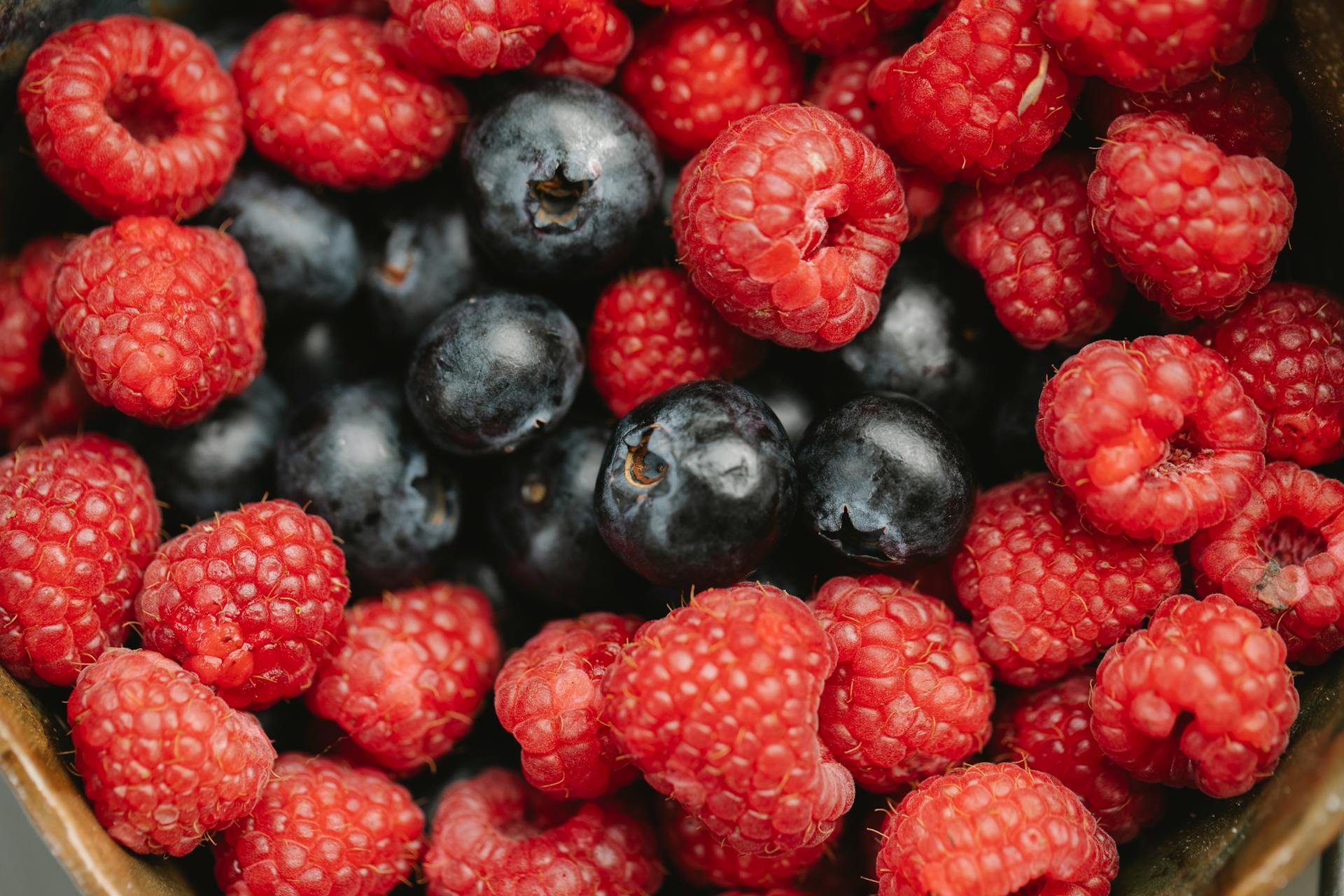
By automating the picking and packing process, businesses can free up staff to focus on other tasks, such as customer service and marketing.
Some Automated Pick and Pack Systems use artificial intelligence to optimize picking routes and reduce travel time for robots and warehouse staff.
These systems can also integrate with existing warehouse management systems, making it easy to implement and manage.
How Automated Pick and Pack Systems Work
An automated pick and pack system is a precise and efficient process that involves several key steps. The system integrates with the warehouse management system (WMS) to gather order details, which is crucial for accurate fulfillment.
The picking process involves robots or guided vehicles retrieving items from warehouse shelves, minimizing the risk of damage, especially for delicate products like pre-rolls.
The packing process not only ensures secure packing but also allows for value-added services like adding distillates or kief before packaging, providing a seamless integration of manufacturing and packing in one automated process.
The final step involves labeling and dispatching the orders, which is handled by the system with ease, ensuring cannabis-specific requirements, such as child-resistant packaging and regulatory compliance, are met.
Here's a breakdown of the key steps in the automated pick and pack process:
- Order Receipt: The system integrates with the WMS to gather order details.
- Picking: Robots or guided vehicles retrieve items from warehouse shelves.
- Packing: Products are automatically packed, and value-added services are integrated.
- Shipping: Orders are labeled and dispatched, ensuring regulatory compliance.
How Work
An automated pick-and-pack system follows a precise and efficient flow. This process involves several key steps that work together to get orders fulfilled quickly and accurately.
The first step is order receipt, where the system logs the order and gathers details from the warehouse management system (WMS) or directly from dispensaries' or retailers' point-of-sale systems in the cannabis sector.
The picking step is where the system uses robots or guided vehicles to retrieve items from the warehouse shelves. This process is critical in the cannabis industry, where delicate products like pre-rolls need to be handled gently to avoid damage.
Packing is the next step, where products are automatically packed and secured. Some systems, like Sorting Robotics' Omni, also integrate with distillate infusion and dusting systems, allowing for value-added services like adding distillates or kief before packaging.
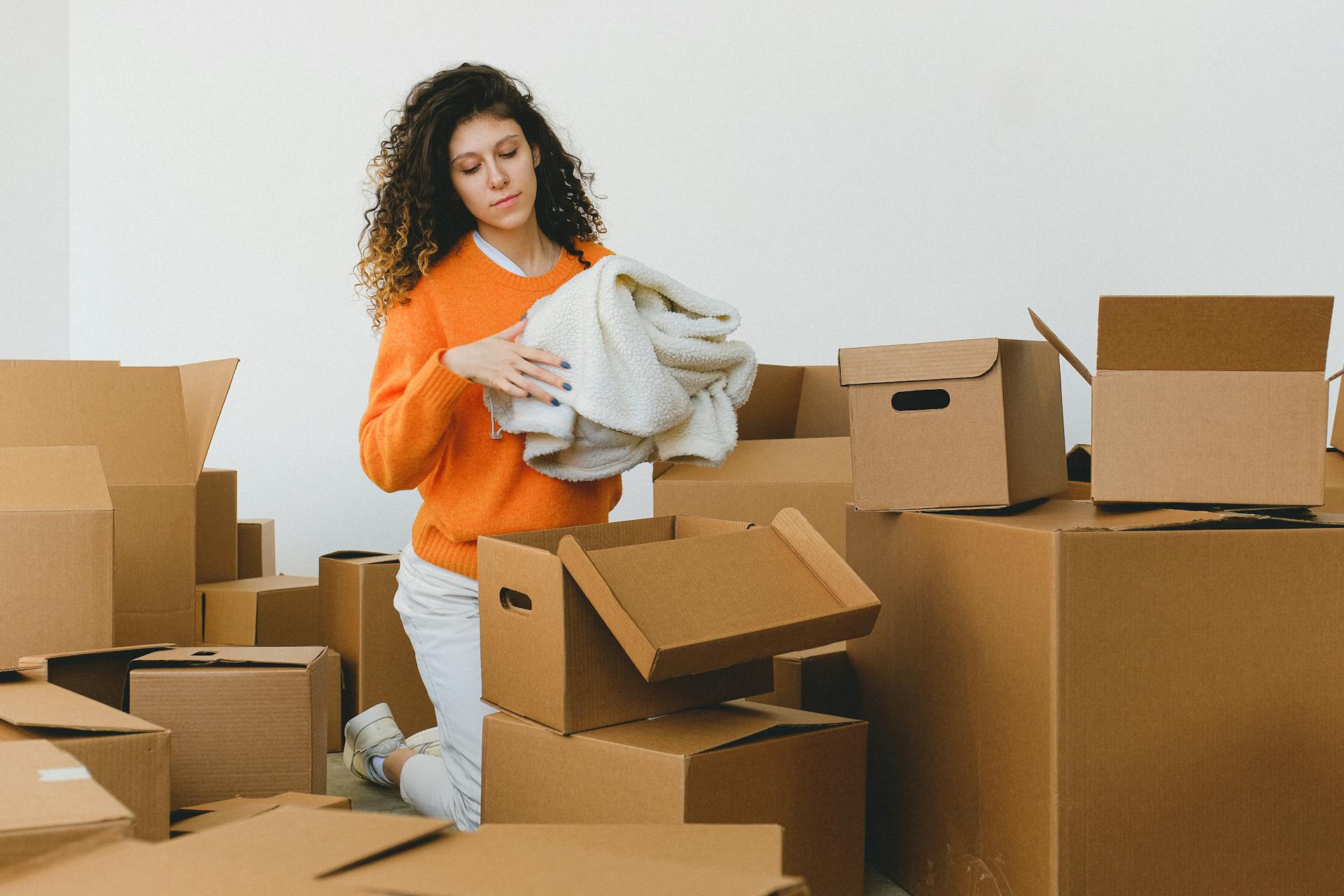
The final step is shipping, where the system labels and dispatches the orders. Sorting Robotics' Stardust system handles this with ease, ensuring cannabis-specific requirements like child-resistant packaging and regulatory compliance are met.
Here's a breakdown of the key steps in the automated pick-and-pack process:
- Order Receipt: The system logs the order and gathers details from the WMS or point-of-sale systems.
- Picking: Robots or guided vehicles retrieve items from the warehouse shelves.
- Packing: Products are automatically packed and secured.
- Shipping: The system labels and dispatches the orders.
Goods-to-Person (GTP)
Goods-to-Person (GTP) picking systems deliver picked items directly to the warehouse worker, reducing the time spent walking and searching for items. This significantly increases efficiency in automated warehouse order picking.
In large warehouses that process large volumes of orders, Goods-to-Person (GTP) picking systems are particularly effective. They include conveyor belts, stacker cranes, and Automated Mobile Robots (AMRs).
These systems bring items to a stationary worker for picking, minimizing the need for workers to navigate through the warehouse aisles. Goods-to-Person (GTP) picking systems are a type of automated picking system that can be used in various warehouse environments.
Here are some benefits of Goods-to-Person (GTP) picking systems:
- Improved efficiency: By bringing items directly to the worker, GTP systems reduce the time spent searching for items.
- Increased accuracy: With items brought directly to the worker, the risk of picking errors is minimized.
- Reduced labor costs: GTP systems can automate the picking process, reducing the need for manual labor.
Benefits of Systems
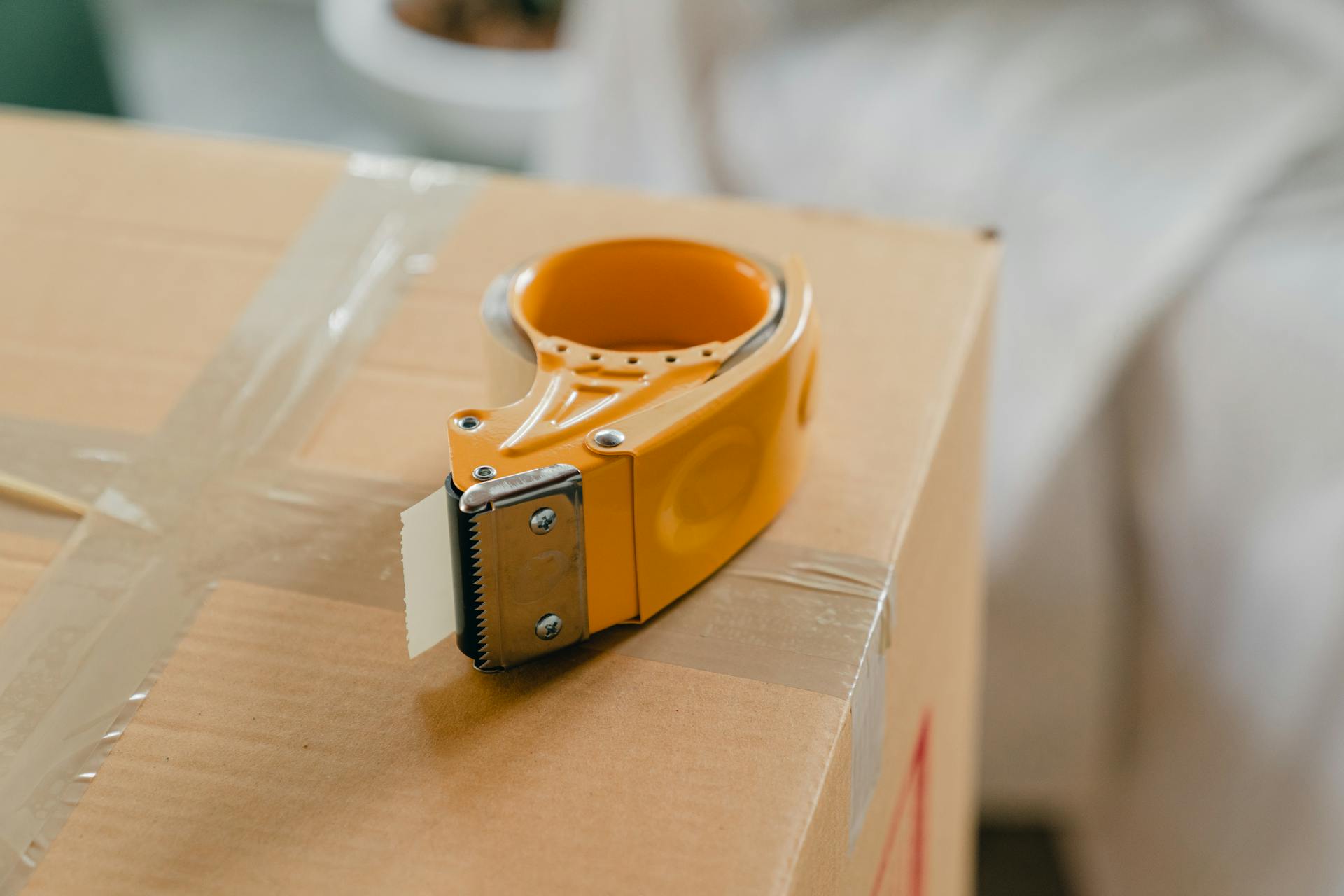
Automated pick and pack systems offer numerous benefits that can transform operations, particularly for cannabis businesses. They improve speed, accuracy, and scalability, helping businesses meet challenges while reducing errors and labor costs.
Using automated pick and pack systems can improve compliance with packaging regulations and maintain product quality. This is especially important for cannabis businesses that face unique challenges in these areas.
Automated warehouse picking can prevent costly product returns and boost picking throughput. This can lead to significant cost savings and increased efficiency.
AMRs can safely navigate warehouses using intelligent sensors and automatically stop if a collision is imminent. This enhances safety and reduces the risk of operator-error incidents.
Companies can optimize transportation by using the safest and most efficient route, reducing the need for forklift drivers. This can lower manual labor costs and help companies meet their goals, even with labor shortages.
Automated pick and pack systems can collect important data about the indoor environment with centimeter-level accuracy. This can improve path planning, robot speed, and navigation software for robots.
AMRs can complete repetitive transportation tasks quickly and consistently without breaks. This results in improved accuracy and productivity, reduced error, and enhanced safety.
Suggestion: Pick Pack and Ship Companies
Efficiency and Productivity
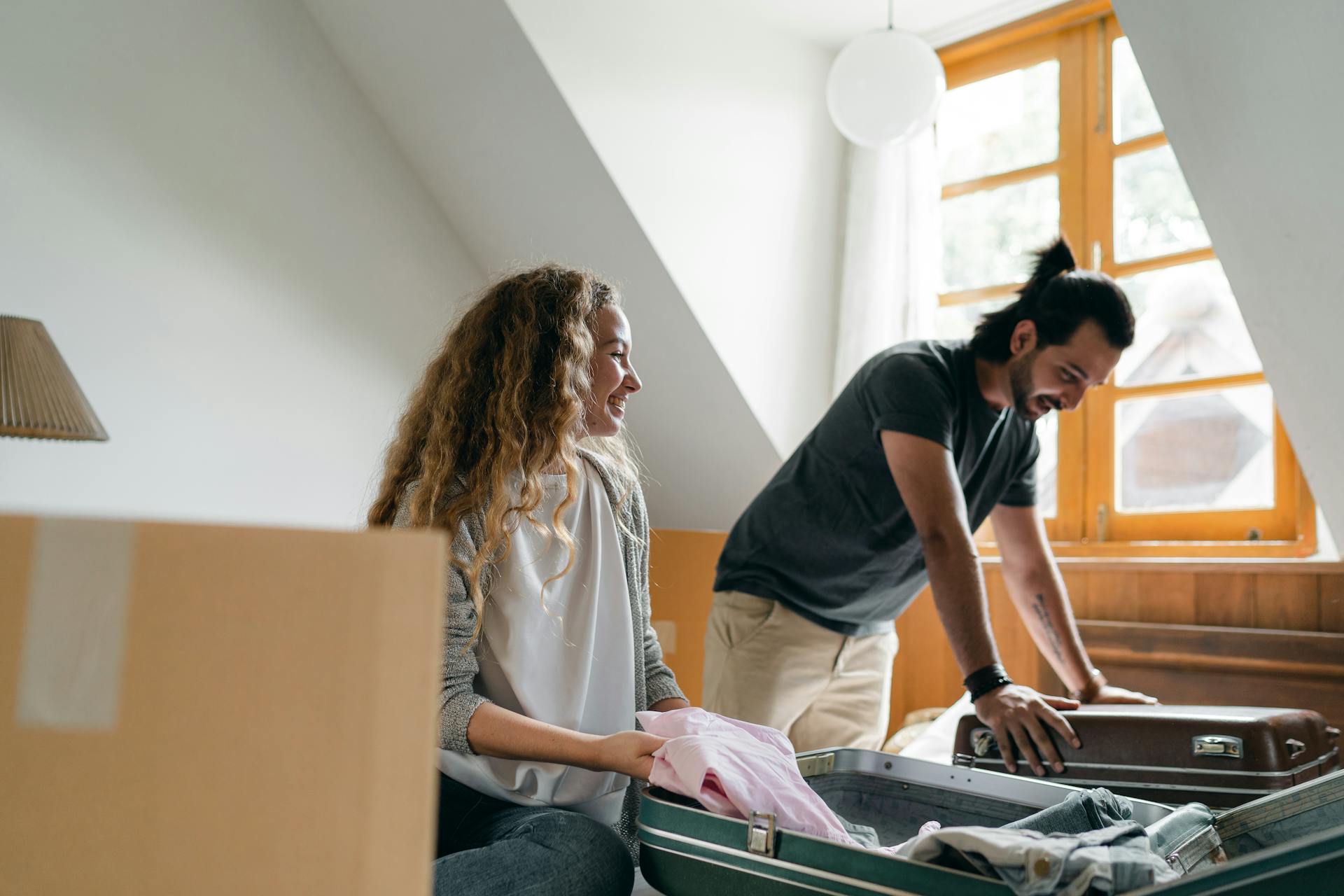
Automated pick and pack systems are a game-changer for businesses, especially in the cannabis industry. By automating repetitive tasks, these systems minimize labor needs and reduce operational costs.
Industry leaders like 6 River Systems have reported a 2-3x increase in picking speed with their collaborative robots. This means that businesses can meet high-volume demand efficiently, especially during peak times like harvest season or holiday sales.
Sorting Robotics' systems, like Jiko for picking and Omni for packing, allow for rapid fulfillment without compromising on the safety and quality of the product. This is especially important for cannabis businesses that need to handle delicate products like pre-rolls and vapes.
Automated systems can operate at high speeds and even work 24/7, significantly increasing the rate of order picking. This increased efficiency allows for faster order processing and delivery times.
Here are some key benefits of automated pick and pack systems:
* 2-3x increase in picking speedRapid fulfillment without compromising on product safety and qualityFaster order processing and delivery timesReduced labor needs and operational costs
By streamlining the entire fulfillment process, automated systems can reduce bottlenecks, ensure accuracy, and accelerate the process to meet customer demands quickly. This is especially important for businesses that need to manage high volumes of orders from various sources, such as retail partners, ecommerce platforms, and direct-to-consumer channels.
Intriguing read: White Glove Last Mile Delivery
Industry-Specific Requirements and Solutions
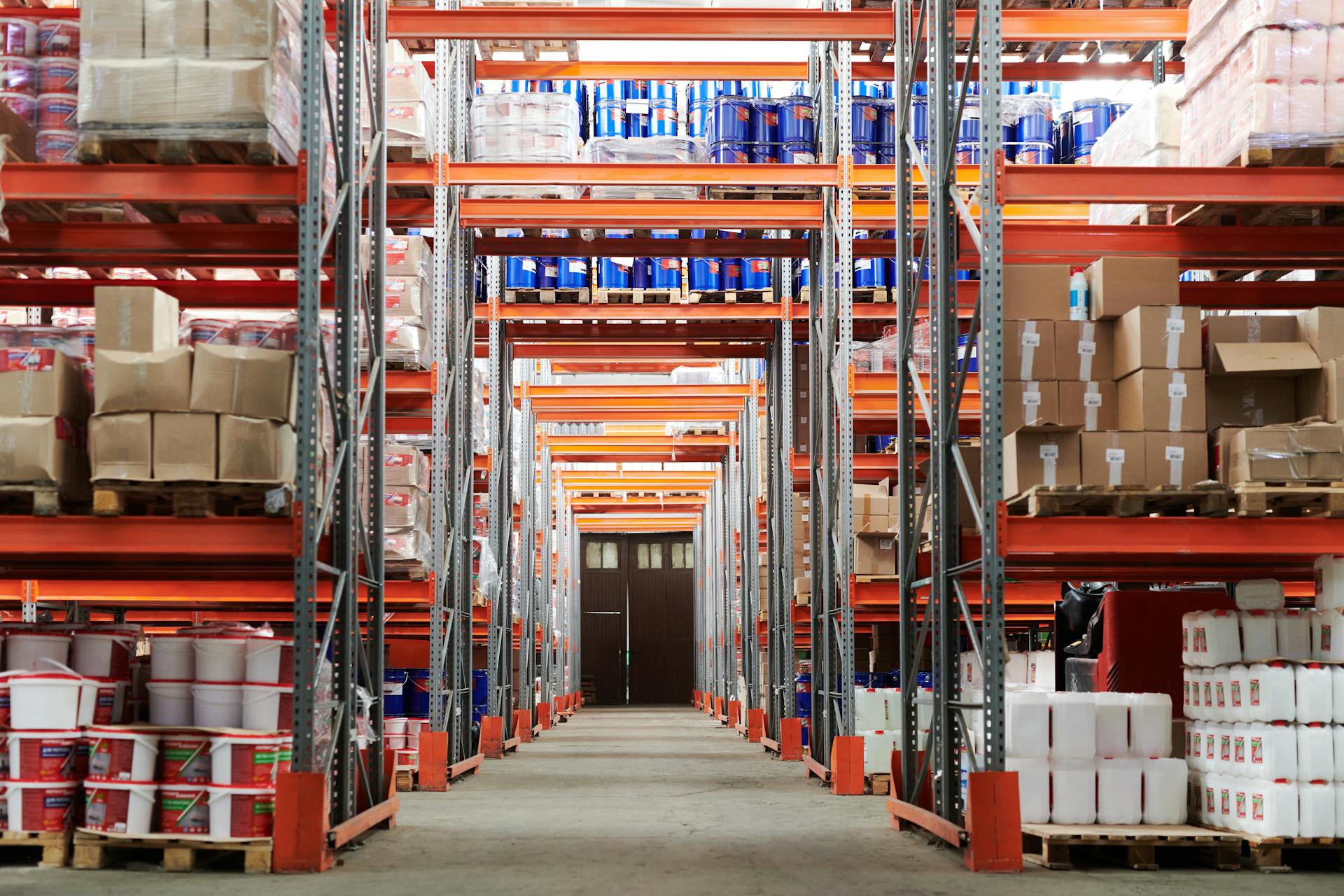
Automated pick-and-pack systems can accommodate specific packaging needs, including child-resistant packaging and compliance labeling, making them a great fit for the cannabis industry. They can handle delicate products like pre-rolls and vapes securely without damage or loss of quality.
The cannabis industry faces unique challenges, and automated pick-and-pack systems are essential for addressing these challenges. They can help reduce labor costs, improve speed and accuracy, and ensure compliance with regulations.
In the cannabis industry, automated pick-and-pack systems use advanced technology, including robots, artificial intelligence, and warehouse management software, to pick products from inventory and pack them for shipping. These systems are designed to meet the specific needs of the cannabis industry, including compliance labeling and child-resistant packaging.
Readers also liked: Packaging Blister Pack
What Is a System in Cannabis?
In the cannabis industry, a system refers to a network of technology and processes that work together to streamline operations. An automated pick-and-pack system is a type of system that uses advanced technology to pick cannabis products from inventory and pack them for shipping.
These systems improve speed, accuracy, and reduce labor costs. They also automate the entire fulfillment process.
Robots, artificial intelligence, and warehouse management software are key components of an automated pick-and-pack system.
Benefits of Cannabis Business Systems

Automated pick-and-pack systems can improve speed and accuracy for cannabis businesses, helping them meet high demand fluctuations.
These systems can handle the delicate nature of products, such as pre-rolls and vapes, ensuring they are packed securely without damage or loss of quality.
By using automated pick-and-pack systems, cannabis businesses can reduce errors and labor costs.
These systems are designed to accommodate the cannabis industry's specific packaging needs, including child-resistant packaging and compliance labeling.
Automated pick-and-pack systems can improve scalability, helping businesses meet the unique challenges of the cannabis industry.
Cannabis Businesses Need Efficient Fulfillment
Cannabis businesses face unique challenges in fulfilling orders efficiently. One major issue is labor costs, which can be significant as the industry grows.
Automated pick-and-pack systems can greatly reduce labor costs by minimizing the need for manual labor and repetitive tasks. According to Example 9, labor costs are a significant burden for cannabis businesses, and automation can help alleviate this issue.
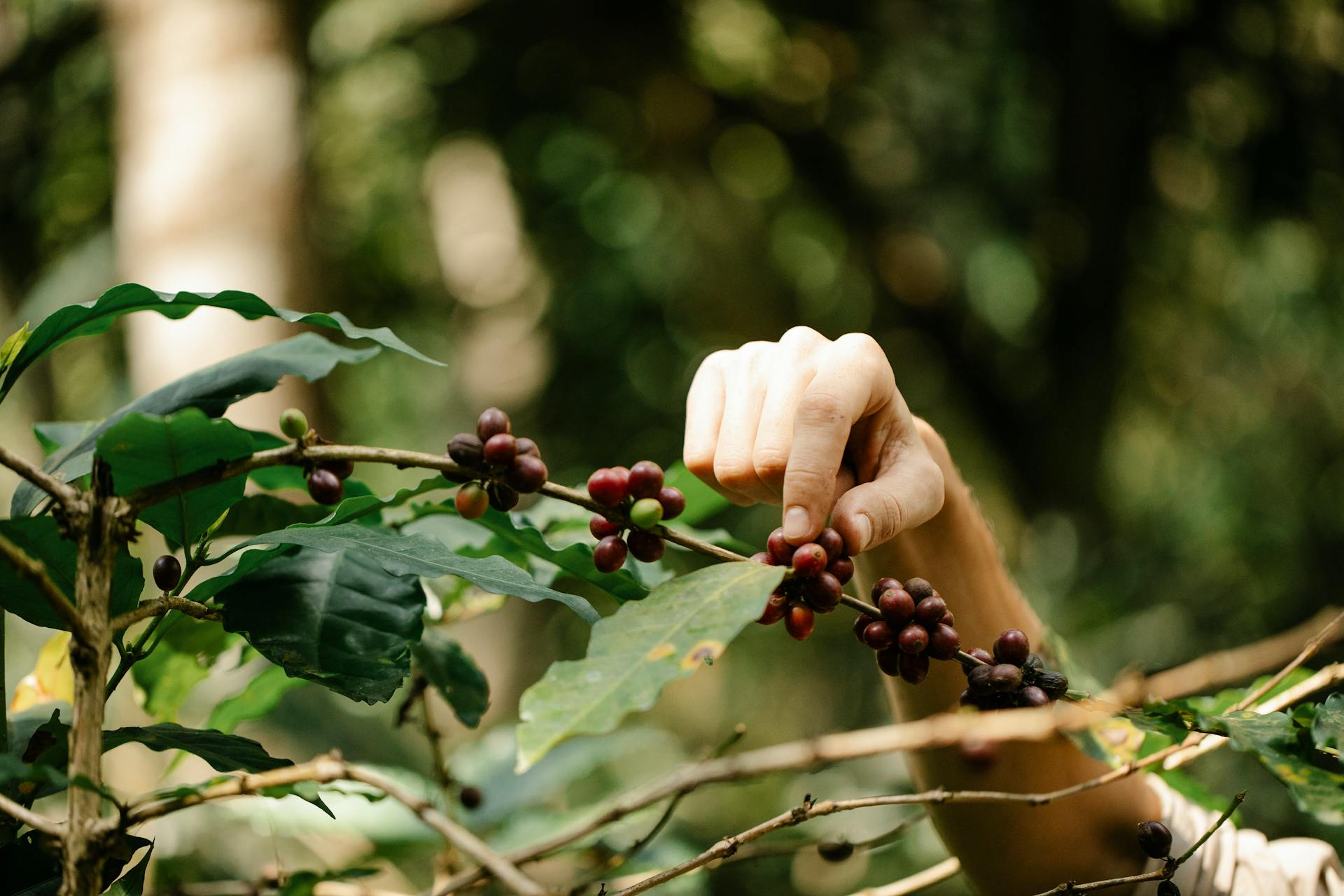
The cannabis industry requires specific packaging requirements, including child-resistant packaging and compliance labeling. Automated pick-and-pack systems, like those designed by Sorting Robotics, can accommodate these needs.
Sorting Robotics' systems, such as Omni, can handle delicate products like pre-rolls and vapes securely without damage or loss of quality. This is particularly important for cannabis businesses that need to maintain product quality and safety.
A 2-3x increase in picking speed has been reported by industry leaders like 6 River Systems, which can be a game-changer for cannabis businesses. This increased speed and efficiency can help businesses meet high-volume demand during peak times like harvest season or holiday sales.
Here are some benefits of implementing automated pick-and-pack systems in the cannabis industry:
- Faster processing times
- Higher accuracy
- Enhanced product quality
- Compliance with industry regulations
- Reduced manual labor and costs
These benefits can help cannabis businesses streamline their operations, improve product quality, and ensure compliance with industry regulations. By investing in automated pick-and-pack systems, businesses can take their fulfillment to the next level and thrive in a competitive market.
Technology and Integration

Automated pick and pack systems rely on a combination of robotics, sensors, and sophisticated software to perform tasks efficiently.
These systems often include Autonomous Mobile Robots (AMRs), robotic arms, and conveyor belts that work together to streamline the picking process. Advanced sensors and cameras enable robots to navigate warehouses, identify items, and transport them to packing areas.
The software component uses algorithms to optimize warehouse picking automation, ensuring the most efficient paths are taken to enhance speed and accuracy.
The integration of these technologies allows warehouses to manage high volumes of orders with minimal errors, leveraging automated picking solutions for maximum efficiency and accuracy.
AI and real-time data integration is also a crucial aspect of automated pick and pack systems. This allows systems to predict demand patterns, optimize inventory, and adjust operations dynamically based on real-time data.
Here are some key benefits of AI integration in automated pick and pack systems:
- Predictive analytics to forecast demand and adjust production
- Optimization of inventory and operations
- Improved accuracy and decision-making
Robotics Integration
Robotics integration is a game-changer for cannabis businesses. Advanced technology, including robots, artificial intelligence, and warehouse management software, can automate the entire fulfillment process, improving speed, accuracy, and reducing labor costs.
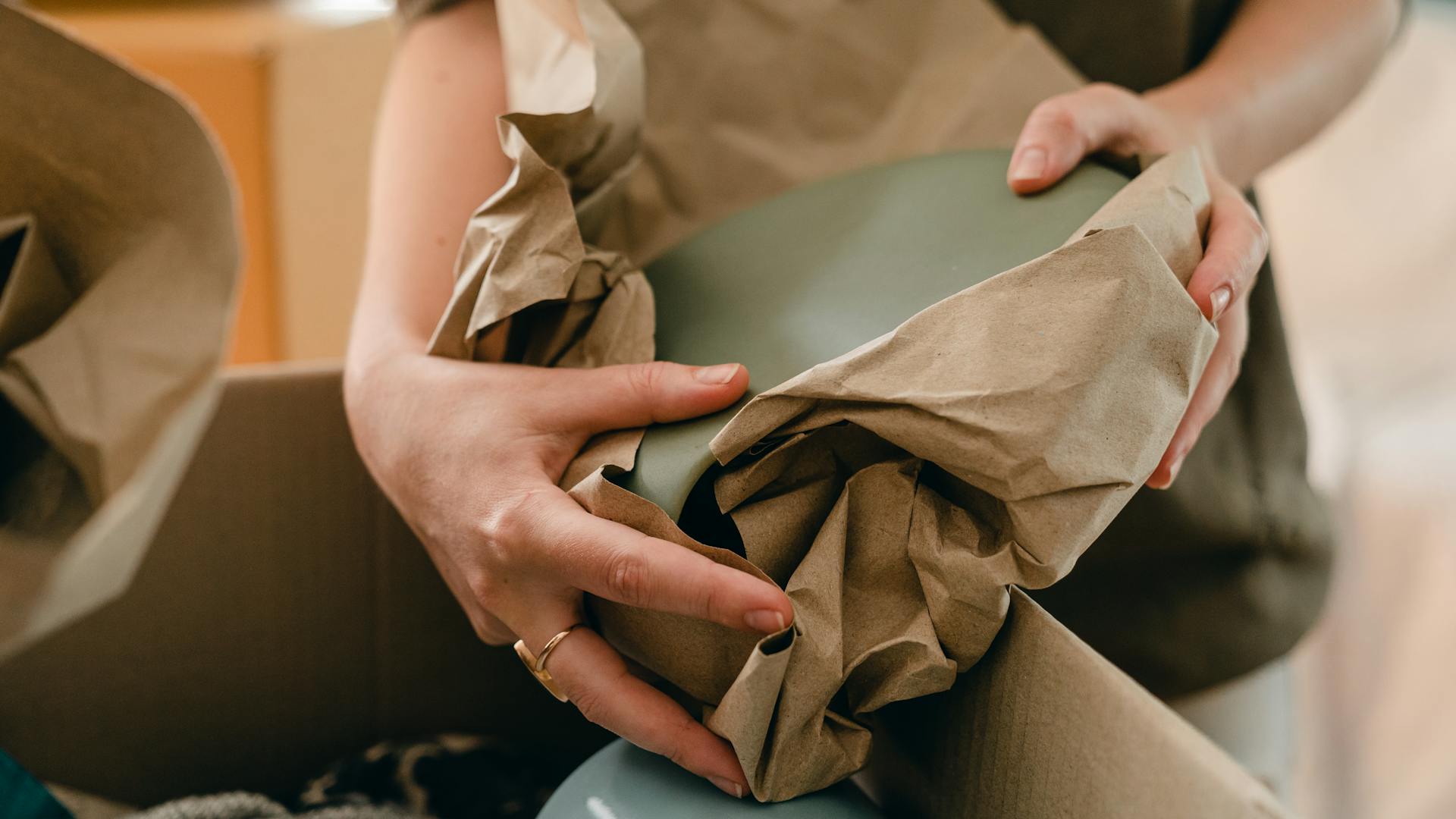
Automated pick-and-pack systems use robots to pick cannabis products from inventory and pack them for shipping. These systems can handle delicate products like pre-rolls and vapes with precision.
Sorting Robotics specializes in cannabis-specific needs, offering automation solutions that integrate product enhancement features, such as distillate infusion and kief dusting. This sets them apart from general logistics providers.
Fully automated picking systems, like robotic arms and AMRs, handle the entire picking process, from locating items to delivering them to the packing area. These systems offer the highest level of automation and efficiency.
Here are some key benefits of robotics integration in cannabis fulfillment:
- Hands-Free Fulfillment: Robotics technology can handle all aspects of order fulfillment, from picking to packing to shipping, with minimal human intervention.
- Increased Efficiency: Automated systems can process high volumes of orders with minimal errors, leveraging robotics integration for maximum efficiency and accuracy.
- Reduced Labor Costs: Automation can reduce labor costs by minimizing the need for manual labor in the fulfillment process.
The technology behind automated picking systems is impressive. It utilizes a combination of robotics, sensors, and sophisticated software to perform its tasks. The robots are equipped with advanced sensors and cameras that enable them to navigate the warehouse, identify items, and transport them to the designated packing areas.
AI & Real-Time Data Processing
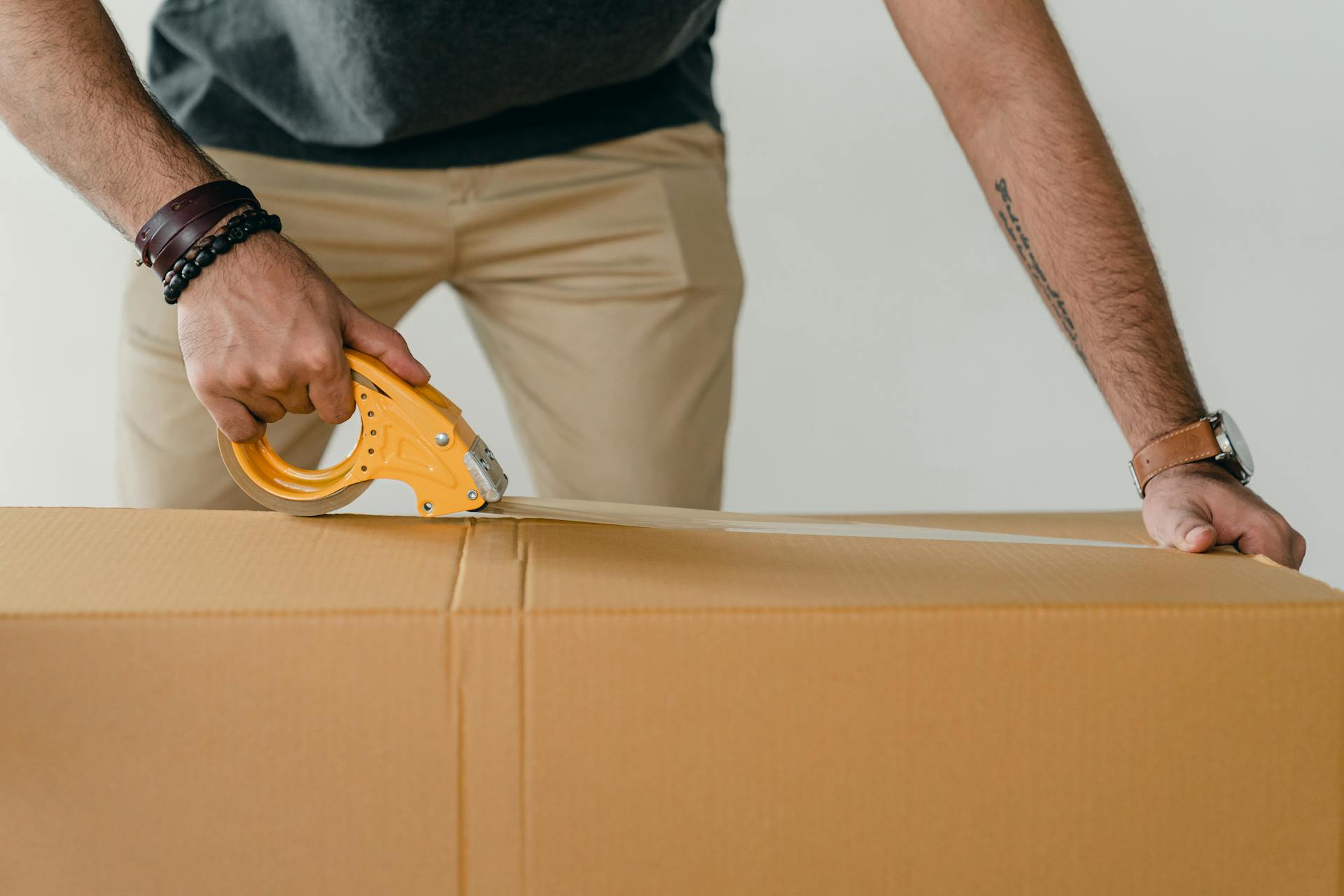
AI & Real-Time Data Processing is a game-changer for businesses, particularly in the cannabis industry. This technology allows systems to predict demand patterns, optimize inventory, and adjust operations dynamically based on real-time data.
With AI integration, businesses can forecast which strains or products will be in demand, enabling them to adjust production and fulfillment proactively. This proactive approach ensures that production aligns perfectly with customer demand.
Predictive analytics is a key component of AI and real-time data processing. This technology uses algorithms to analyze data and make predictions about future demand.
Here are some key benefits of AI and real-time data processing:
- Predictive analytics: Forecasts demand patterns and optimizes inventory
- Dynamic adjustments: Adjusts operations based on real-time data
- Improved accuracy: Ensures production aligns with customer demand
By leveraging AI and real-time data processing, businesses can increase speed and efficiency, while also improving accuracy and decision-making. This technology is already being integrated into automated pick-and-pack systems, transforming operations and setting a new standard for the industry.
Comparisons of System Technologies
When selecting an automated warehouse picking system, it's essential to consider the unique strengths of each technology. Automated warehouse picking systems have distinct advantages, making them suitable for specific warehouse operations.
Conveyor-based picking systems are ideal for high-volume warehouses with a large number of SKUs. These systems can handle a high throughput of orders.
Automated storage and retrieval systems (AS/RS) are perfect for warehouses with a high storage density, as they can optimize storage capacity. They can also reduce labor costs.
Robotic picking systems are suitable for warehouses with a high mix of SKUs, as they can quickly switch between different products. They also provide a high degree of flexibility.
Each of these technologies has its own set of advantages, and selecting the right one depends on the specific needs and constraints of the warehouse operation.
Scalability and Adaptability
Automated pick and pack systems offer scalability to accommodate growing order volumes and adaptability to handle diverse product sizes and variations.
These systems can easily be adjusted to meet changing demands and enable businesses to efficiently manage fluctuating inventory levels.
Sorting Robotics' automated systems are highly scalable, making them suitable for both small and large-scale operations, and can grow with your business as demand fluctuates.
Modula
Modula is a leading provider of automated warehouse solutions, including automated warehouse picking systems, that reimagines warehouses across industries to improve picking speed and accuracy.
Their automated picking systems combine advanced picking aids, easy-to-use technology, and intelligent software to create a seamless and efficient workflow.
Modula's Put to Light System boosts throughput by enabling the simultaneous picking of multiple orders, replacing traditional paper-based methods and reducing errors.
The Put to Light System uses lights and digital displays to guide warehouse operators through the order fulfillment process, directing them to the right area to "put" items using light signals.
Modula's Picking Station is a workstation that can be modified with adjustable shelves to store goods, and each bin or order is linked with a put-to-light display.
The Picking Station can integrate with both manual and automated handling systems, such as belt conveyors, and can be paired with additional modules to install monitors, label printers, or barcode readers.
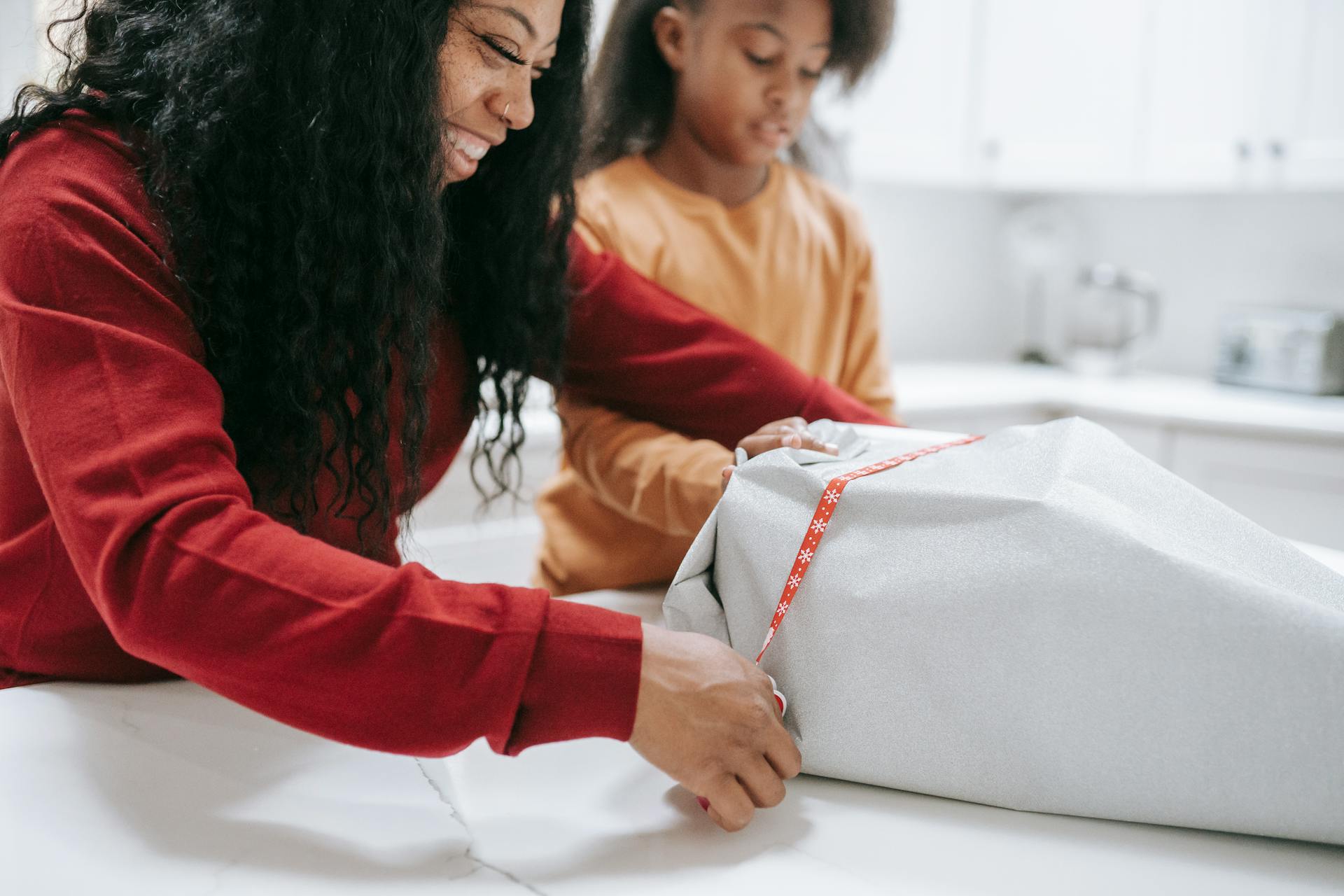
Modula's Picking Cart is a mobile solution for paperless batch or multiple order processes, featuring a put-to-light display to guide operators and a wireless connection to the WMS.
The Picking Cart seamlessly integrates with both manual and automated handling systems, making it suitable for any warehouse operation.
Modula's Picking App is a user-friendly tool that helps operators move around the warehouse while maintaining real-time updates and control of all processes, accessed directly on a smartphone or tablet.
The Picking App includes a built-in barcode reader, allowing inventory to be scanned and monitored directly from the mobile device, eliminating the need for paper.
Modula's solutions are designed to optimize the picking process, reducing time and labor while maximizing accuracy and throughput, making them a scalable and adaptable choice for warehouses.
Can Handle Both Small and Large-Scale Operations?
Automated pick-and-pack systems can handle both small and large-scale operations. Sorting Robotics' automated systems are highly scalable, allowing businesses to grow with their operations.
Whether you're a small cannabis producer or a large-scale distributor, Sorting Robotics' solutions can accommodate your needs. Berkshire Grey's Robotics-as-a-Service (RaaS) model allows businesses to expand fulfillment capabilities without the hefty upfront costs.
Sorting Robotics' modular systems can easily scale up to accommodate demand spikes, such as those experienced during new product launches or increased market interest. This helps reduce labor costs by automating tasks that would typically require multiple manual laborers.
Cannabis producers can experience surges in demand during harvest seasons or product launches, and Sorting Robotics' systems can easily adjust to meet these changing demands. With Sorting Robotics, businesses can efficiently manage fluctuating inventory levels and adapt to diverse product sizes and variations.
You might like: Conveyor Scale Systems
Cost Efficiency and Labor Savings
Automated pick and pack systems can significantly reduce labor costs for cannabis businesses, which often face labor shortages or high operational costs.
Labor costs are a significant burden for cannabis businesses, especially as the industry grows.
Automation reduces the need for manual labor, cutting costs in the long term. By automating repetitive tasks, our systems minimize labor needs and reduce operational costs. Sorting Robotics’ solutions not only save money but also improve profit margins by speeding up the fulfillment process and maintaining efficiency.
Here are some key statistics on labor costs in the cannabis industry:
Sustainability and Compliance
Cannabis businesses have to meet strict regulations, including packaging and labeling requirements, to avoid fines and reputational damage. Errors can be costly, but automated systems like Sorting Robotics help ensure compliance.
Automated systems integrate cannabis-specific features directly into the fulfillment process, reducing human error. This includes ensuring child-resistant packaging and accurate labeling.
Sorting Robotics optimizes packaging size and material usage, reducing waste while maintaining product integrity. This focus on sustainability aligns with growing trends in the industry, where brands are under increasing pressure to meet environmental expectations.
Here's a breakdown of the benefits of automated systems in terms of sustainability and compliance:
Industry Compliance
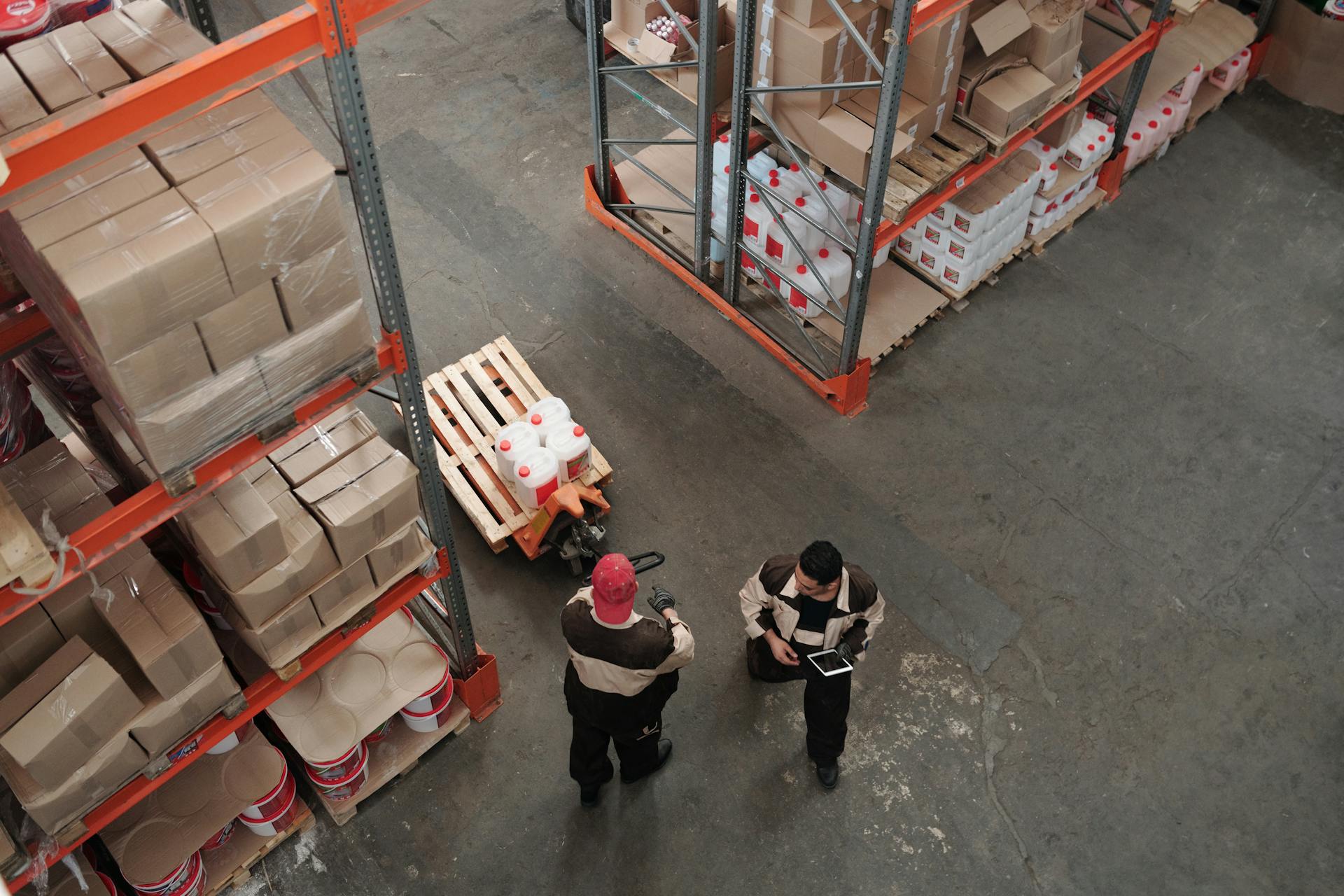
Industry Compliance is a top priority for cannabis businesses. Errors in packaging, labeling, and tracking can lead to fines, recalls, or reputational damage.
Automated systems can help businesses comply with regulations by integrating necessary features directly into the fulfillment process. This reduces human error and ensures products meet regulations.
Child-resistant packaging is a crucial aspect of compliance. Sorting Robotics ensures that products are packaged in a way that meets safety standards.
Accurate labeling is also essential for compliance. Automated systems can help ensure that products are labeled correctly, reducing the risk of errors.
Here are some key aspects of industry compliance:
- Cannabis businesses must adhere to strict regulations.
- Automated systems can help with packaging, labeling, and tracking requirements.
- Errors in these areas can lead to fines, recalls, or reputational damage.
By prioritizing industry compliance, cannabis businesses can protect their reputation and avoid costly mistakes.
Sustainability in Packaging
As the cannabis industry continues to grow, so does its environmental impact. Sustainability in packaging has become a top priority for both customers and regulators.
The industry is under increasing pressure to meet environmental expectations, with brands facing pressure to adopt greener practices. This is driving innovation in sustainable packaging solutions.
Sorting Robotics is committed to sustainability, designing systems that optimize packaging size and material usage to reduce waste. This focus on sustainability aligns with industry trends.
By reducing waste and maintaining product integrity, sustainable packaging solutions like those offered by Sorting Robotics can help cannabis brands meet environmental expectations.
On a similar theme: Pick and Pack Solutions
Logiwa and Support
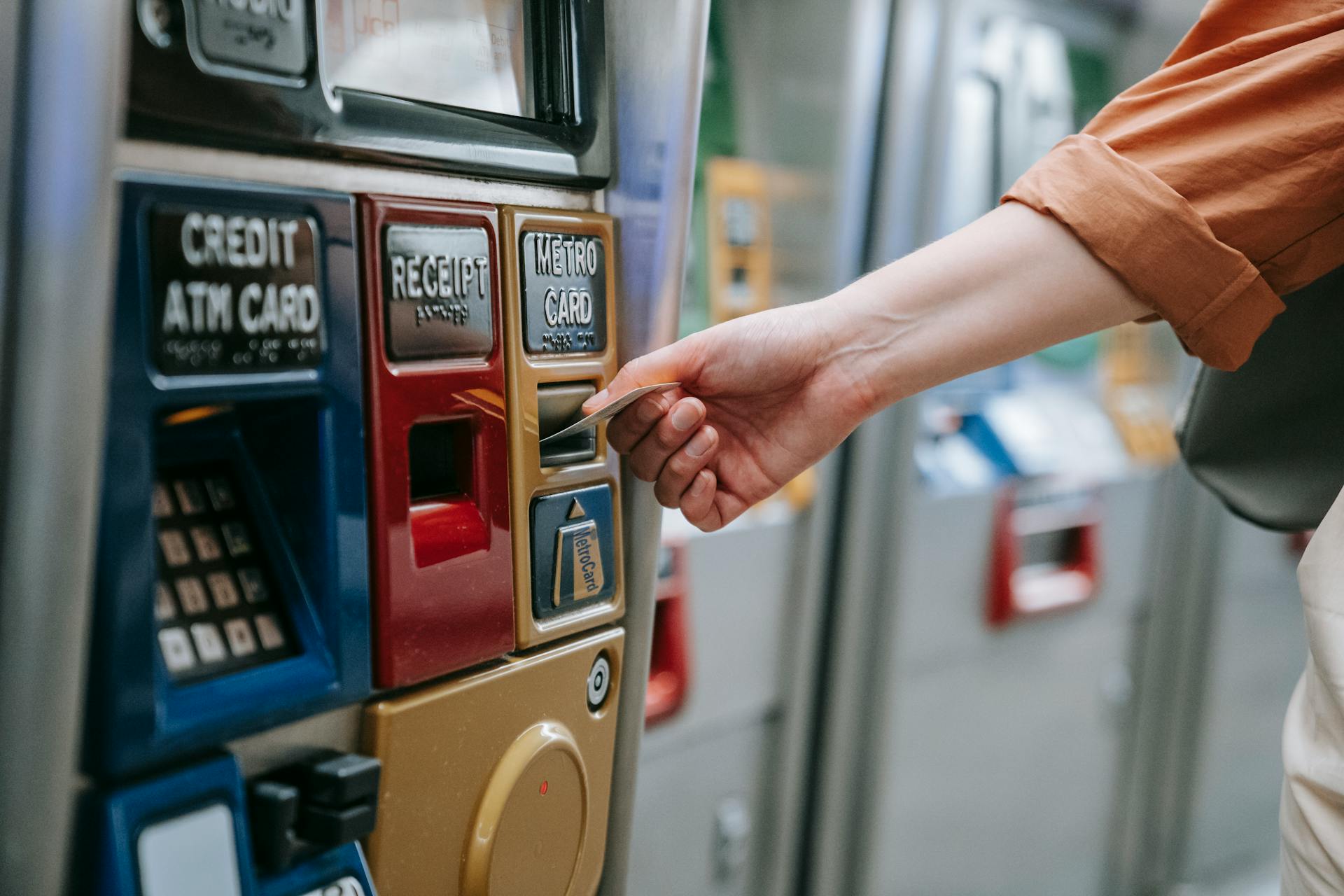
Installing a robotics system is just the first step in automating your warehouse's picking process. You also need a warehouse management system to control and monitor your robots.
Logiwa WMS is an all-in-one solution that can turn your traditional facility into a fully digital warehouse. It can increase your labor efficiency by up to 40%.
The software comes ready to use out of the box with pre-built automation rules to quickly automate and optimize your picking, packing, and shipping processes. This means you can start seeing results faster.
Connecting to your favorite shipping, accounting, robotics, and ecommerce solutions is made seamless through Logiwa's integrations process.
Management and Operations
Automated pick and pack systems can greatly improve efficiency and streamlined operations. Manual pick-and-pack processes can lead to inefficiencies and human error, but our automated systems can reduce bottlenecks and ensure accuracy.
Time-consuming handoffs between departments can slow down operations, but our system integrates all stages of fulfillment into a single automated workflow. This streamlines the entire process from picking to packing to shipping.
To achieve maximum ROI with a modern warehouse management system (WMS), it's essential to select a system that can integrate into existing warehouse processes quickly and seamlessly. A WMS can help improve inventory management and reduce labor costs.
Here are some benefits of automated pick and pack systems:
- Improved speed and accuracy
- Reduced labor costs
- Increased efficiency and streamlined operations
Max ROI with Modern Management System
Managing your warehouse operations effectively is crucial for achieving maximum ROI. Manual pick-and-pack processes can lead to inefficiencies and human error.
In the cannabis industry, automated pick-and-pack systems have become a game-changer. These systems use advanced technology, including robots, artificial intelligence, and warehouse management software, to pick products from inventory and pack them for shipping.
For major brands and high-volume third-party providers (3PL), fulfillment logistics are impossible to effectively manage manually. Orders may come from various sources, such as retail partners, ecommerce platforms, and direct-to-consumer channels.
A modern warehouse management system (WMS) can help streamline operations and reduce labor costs. Automated systems can integrate all stages of fulfillment into a single automated workflow, reducing bottlenecks and ensuring accuracy.
Related reading: What Is a Transportation Management System

Here are some key benefits of a modern WMS:
- Reduces manual errors and inefficiencies
- Improves speed and accuracy
- Reduces labor costs
- Optimizes inventory and adjusts operations dynamically
Predictive analytics can also be integrated into a modern WMS to forecast demand patterns and adjust operations proactively. This allows businesses to adjust production and fulfillment based on real-time data, ensuring that production aligns perfectly with customer demand.
Experience Paperless Process
A modern digital Warehouse Management System (WMS) powers a modern fulfillment experience, making it possible to manage orders from various sources, such as retail partners, ecommerce platforms, and direct-to-consumer channels.
Manual management of logistics is impossible for major brands and high-volume third-party providers, making a trusted WMS essential.
Automated pick-and-pack systems use advanced technology, including robots, artificial intelligence, and warehouse management software, to pick products and pack them for shipping.
These systems automate the entire fulfillment process, improving speed, accuracy, and reducing labor costs, making them particularly beneficial for cannabis businesses.
An automated pick-and-pack system in the cannabis industry uses advanced technology to pick products from inventory and pack them for shipping, improving speed and accuracy.
A unique perspective: Order Picking Accuracy
Management
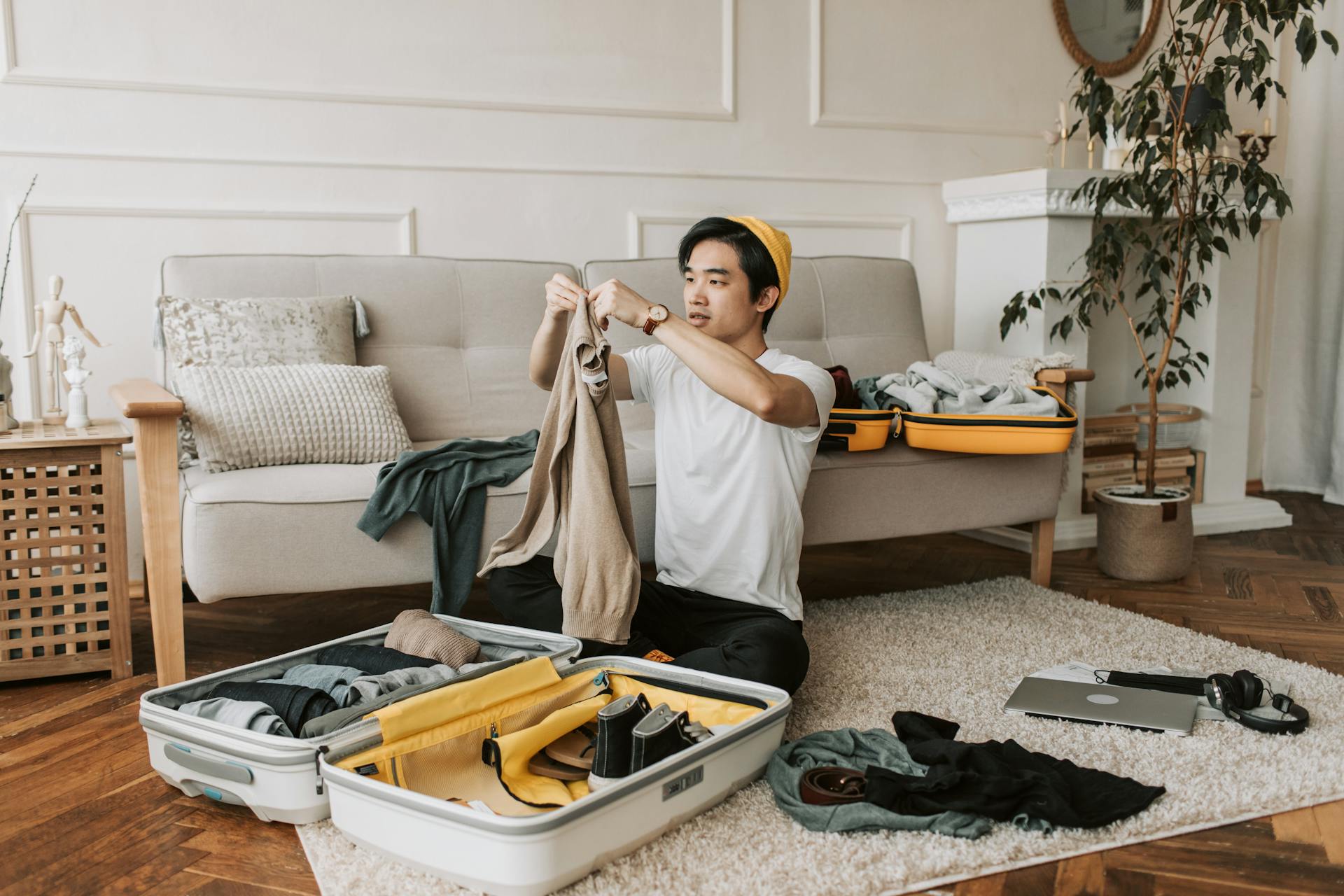
Managing your warehouse and inventory is crucial for efficient operations. You can streamline your warehouse picking by using automated technologies that reduce walking time and optimize picking routes.
Automated warehouse picking solutions can integrate into your existing processes quickly and seamlessly. Look for a solution that keeps human involvement to a minimum and is compatible with your Warehouse Management System (WMS) and preferred order-picking method.
Inventory management is also essential, especially for major brands and high-volume third-party providers. A good inventory management system can help you effectively manage your supply chain.
Warehouse Management Systems (WMS) are designed to power a modern fulfillment experience. They can help you manage your warehouse operations more efficiently.
By using AI and real-time data, you can predict demand patterns and optimize inventory. This can help you adjust production and fulfillment proactively, ensuring that you meet customer demand.
For your interest: Order and Delivery Management System
Traditional and Modern Systems
Traditional pick and pack systems are often manual and prone to errors, whereas modern automated systems can significantly improve efficiency and safety.

Automated pick and pack systems can reduce repetitive motion injuries in workers and keep them out of harm's way, increasing safety and reducing downtime from accidents and injuries.
Modern pick and pack machinery can increase useable floor space and improve ergonomics for employees, allowing for more room, enhanced safety, and smoother operations.
By implementing automated pick and pack systems, labor costs can be lowered by completing repetitive tasks efficiently and protecting products during packaging.
With modern pick and pack systems, labor reduction is achieved through robots working consistently and reliably, reducing dependency on manual labor.
Economic Impact and Benefits
Automated pick and pack systems can significantly reduce labor costs by automating repetitive and labor-intensive tasks. This leads to significant cost savings for businesses.
By streamlining operations and improving efficiency, warehouses can handle higher volumes of orders in less time, increasing overall throughput and operational capacity. Automation enables warehouses to process orders faster with minimal delays.
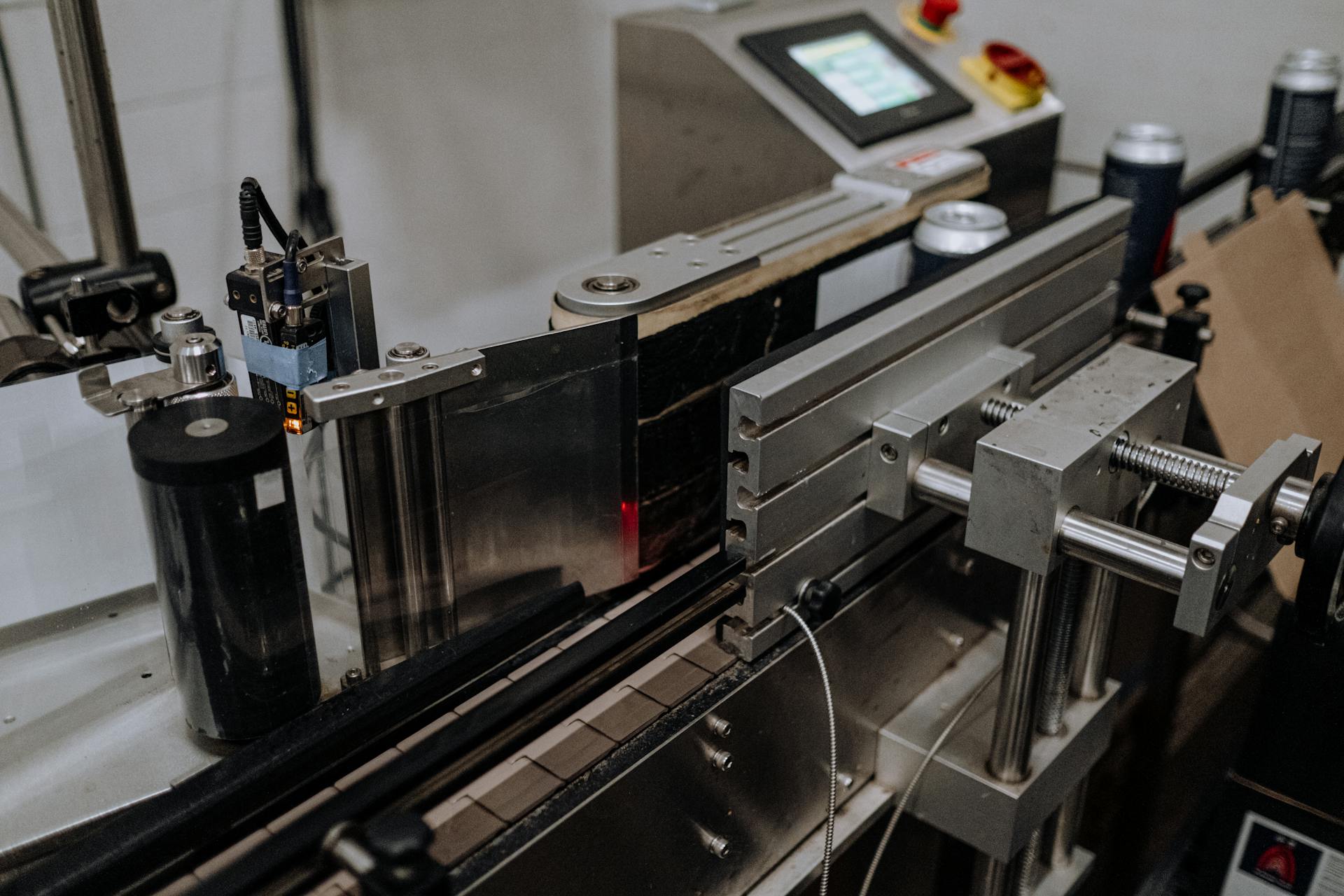
Automated order picking systems reduce picking errors, leading to fewer returns and higher customer satisfaction, ultimately boosting profitability. This is achieved through enhanced order accuracy and consistency.
Automated picking technology can easily adapt to changes in order patterns and inventory, making it easier to scale operations and respond to market demands. This supports agile and dynamic warehousing strategies.
The use of AMRs in combination with pick and pack systems provides enhanced benefits for companies by delivering a fully automated process. This eliminates the need for forklift drivers and reduces manual labor costs.
AMRs can collect important data about the indoor environment with centimeter-level accuracy for path planning, robot speed, and improvements in navigation software for robots. This data can be used to optimize warehouse operations and improve efficiency.
Automated pick and pack systems improve speed, accuracy, and scalability, helping businesses meet the challenges of compliance with packaging regulations, maintaining product quality, and managing high demand fluctuations.
A different take: Automated System for Customs Data
Frequently Asked Questions
What are the three main picking systems?
The three main picking systems used in warehouses are batch picking, zone picking, and wave picking. Each system offers a unique approach to optimizing order fulfillment and efficiency.
Which device do associates use to pick products?
Associates use multi-tiered picking carts to efficiently pick products for multiple orders. This system streamlines their workflow and minimizes travel time within the warehouse.
Sources
- https://www.sortingrobotics.com/the-grind-blog/what-is-an-automated-pick-and-pack-system
- https://www.logiwa.com/blog/automated-warehouse-picking
- https://modula.us/blog/automated-warehouse-picking/
- https://mobile-industrial-robots.com/blog/optimizing-warehouse-efficiency-with-advanced-picking-systems
- https://robex.us/industries/pick-pack/
Featured Images: pexels.com