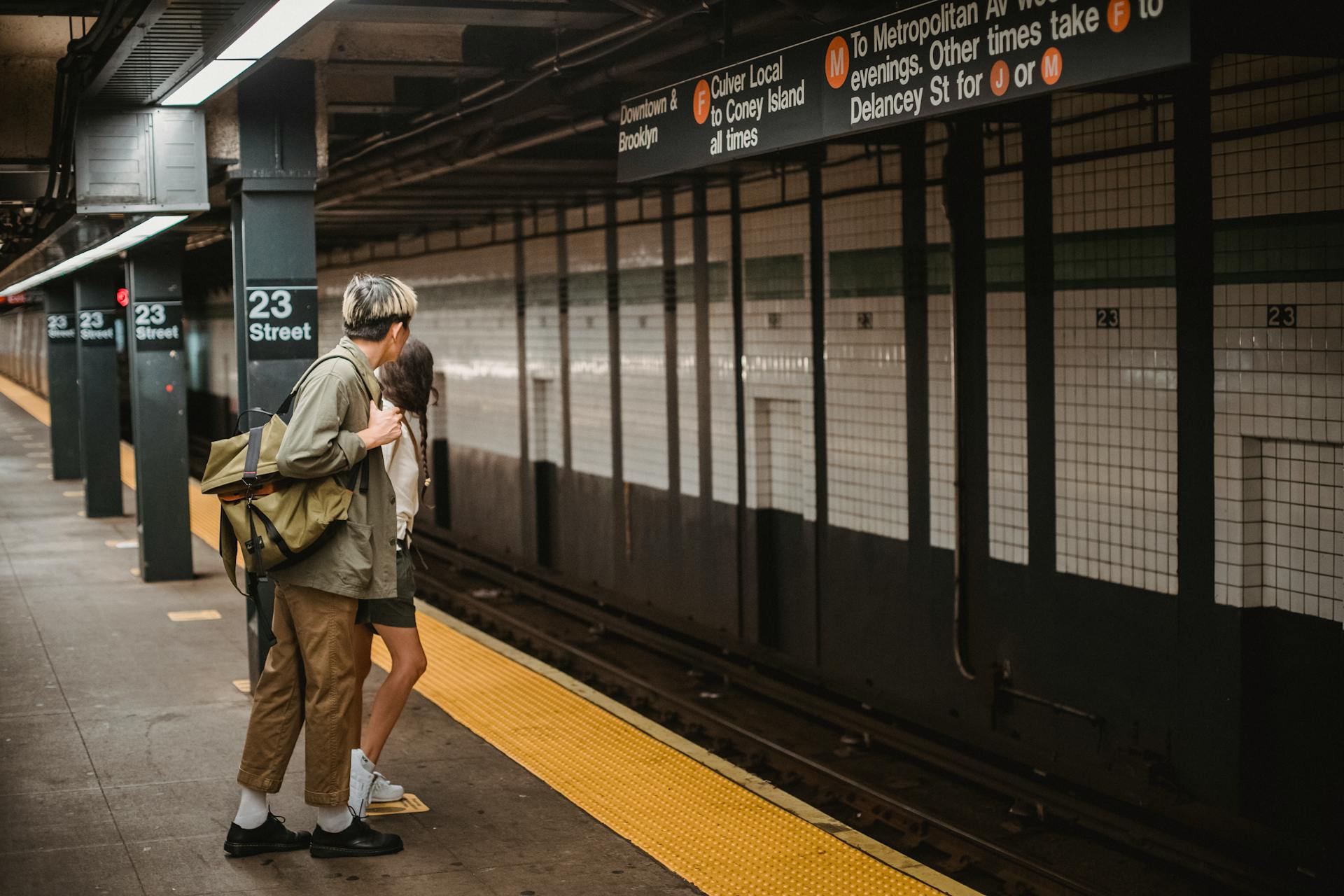
The pick and pack system is a crucial component of efficient warehousing. A well-implemented pick and pack system can reduce labor costs and increase order fulfillment accuracy.
In a typical pick and pack operation, orders are received and processed quickly, with the system able to handle a high volume of orders per hour. This is made possible by the use of efficient picking and packing procedures, such as batch picking and zone picking.
With the pick and pack system, products are stored in a way that allows for easy retrieval, reducing the time it takes to pick and pack orders. This is achieved through the use of a warehouse management system (WMS) that optimizes storage and retrieval processes.
By streamlining the picking and packing process, the pick and pack system helps to minimize errors and reduce the risk of stockouts or overstocking.
What Is a Pick and Pack System?
A pick and pack system is the heart of efficient order fulfillment. It's a process where items are selected from inventory and then placed in a box for shipping.
At its core, a pick and pack system involves four main steps: picking items from inventory, packing them into boxes, and shipping them to customers. These steps can be optimized for faster and more accurate fulfillment.
A pick and pack system provides numerous benefits for businesses, including streamlined order processing, improved inventory management, and enhanced customer satisfaction. It centralizes order-related information, facilitating real-time tracking and visibility across the entire order lifecycle.
Pick and pack software is a specialized tool designed to streamline the order fulfillment process in warehouses, distribution centers, and eCommerce operations. It guides workers through efficient picking paths and suggests optimal packing methods and materials.
By optimizing workflows, reducing errors, and improving overall productivity, a pick and pack system ensures the efficient picking, packing, and shipping of customer orders. This leads to increased operational efficiency and cost savings for businesses.
Broaden your view: Order Fulfillment System
Types of Pick and Pack Systems
There are several types of pick and pack systems, each with its own unique characteristics and benefits.
Automated pick and pack systems use conveyor belts, robots, and other machinery to streamline the picking and packing process, increasing efficiency and reducing labor costs.
Manual pick and pack systems, on the other hand, rely on human labor to pick and pack items, making them more suitable for smaller operations or those with complex or irregular items.
Mobile Shelf-Based
Mobile Shelf-Based systems are a type of pick and pack system that use robots to bring shelves to the picker.
In these systems, robots bring shelves to the picker and then return them to the warehouse floor, making it easier and faster for pickers to retrieve items.
This approach can be particularly useful in warehouses with high storage density, where shelves are packed tightly together and robots can navigate through narrow aisles.
MSOP systems are designed to increase efficiency and reduce labor costs by minimizing the time pickers spend walking and searching for items.
Kitting
Kitting is a specialized kind of pick and pack service that involves assembling various SKUs into a single SKU to create a subscription pack or promotional bundle.
This requires adjusting warehouse packing techniques, often on a monthly basis or as new promotions arise.
Integrated data can inform targeted promotions and upselling opportunities, enhancing customer engagement and satisfaction.
Kitting allows businesses to create unique bundles that cater to specific customer needs, increasing customer satisfaction and loyalty.
Setting Up a Pick and Pack System
Setting up a pick and pack system is crucial for efficient order fulfillment. You'll want to choose a layout that minimizes warehouse travel and search time, which can be achieved through efficient path instructions.
A well-organized warehouse is essential for a successful pick and pack system. This means storing inventory items in a way that makes it easy for pickers to find what they need.
Consider using a warehouse management system (WMS) to guide nearly every aspect of warehouse operations. A WMS can help you receive, process, and store inventory, provide real-time visibility into inventory, and support picking and packing technologies.
Discover more: Warehouse Pick Pack Work
Popular items should be stored in a way that minimizes congestion and reduces errors. This can be achieved by storing similar items together, but not too close together.
The way you organize your inventory will affect picking speed and accuracy. You can use methods like "like with like", "chaotic", "volume", or "class-based" to allocate SKUs to different areas of your facility.
Here are some common warehouse layout approaches to consider:
You can also consider bringing in experts to analyze your warehouse data and offer solutions. By understanding your business's specific needs and product characteristics, you can select and implement the most effective layout for your pick and pack system.
Best Practices for Pick and Pack
Having the right processes in place can make a huge difference in your pick and pack order fulfillment. This is a last chance for warehouse packing teams to check picking accuracy, ensuring the right quantities of the right items go in the box before it's sealed and shipped.
Accuracy at this stage can help reduce the risk of returns, which incur reverse logistics and restocking costs and may disappoint customers. To optimize your pick and pack service, consider using pack strategies that streamline your fulfillment process and reduce costs.
Here are some key strategies to keep in mind:
* Faster fulfillment: Use an Order Management System (OMS) to analyze inventory locations and determine the quickest route for shipping.Decreased labor costs: Automate tasks and reduce labor hours devoted to order fulfillment.Decreased shipping costs: Distribute from the closest locations to reduce shipping costs.Reduce excess inventory: Use an OMS to significantly reduce the need for excess inventory.Less redundant data entry: Use a single system for all stages of the order management process to reduce errors.Increased visibility: Use an OMS to track order status and provide visibility to customers and staff.Data analysis: Use an OMS to analyze data and identify areas for improvement.
By implementing these strategies, you can create a more efficient and effective pick and pack process that benefits your business and customers alike.
Take a look at this: In a Just in Time Inventory System Suppliers
Methods
As your ecommerce business grows, you may need to adapt your warehouse picking and packing methods to meet demand. Startups and early-stage companies can often get away with picking items one at a time, but as sales increase, advanced methods create speed.
Your pick and pack system should match your inventory and order complexity. The optimal pick method depends on the number of orders you receive daily.
In fact, the picking and packing process works best when things are organized and coordinated. Every detail matters!
Suggestion: Order Picking Methods
Best Practices
Having the right processes in place is crucial for ensuring pick and pack order fulfillment drives customer satisfaction. Accuracy at this stage can help reduce the risk of returns, which incur reverse logistics and restocking costs and may disappoint customers.
Your warehouse packing teams should check picking accuracy to ensure the right quantities of the right items go in the box before it's sealed and shipped. This is a last chance to catch any mistakes.
Additional reading: Order Picking Accuracy
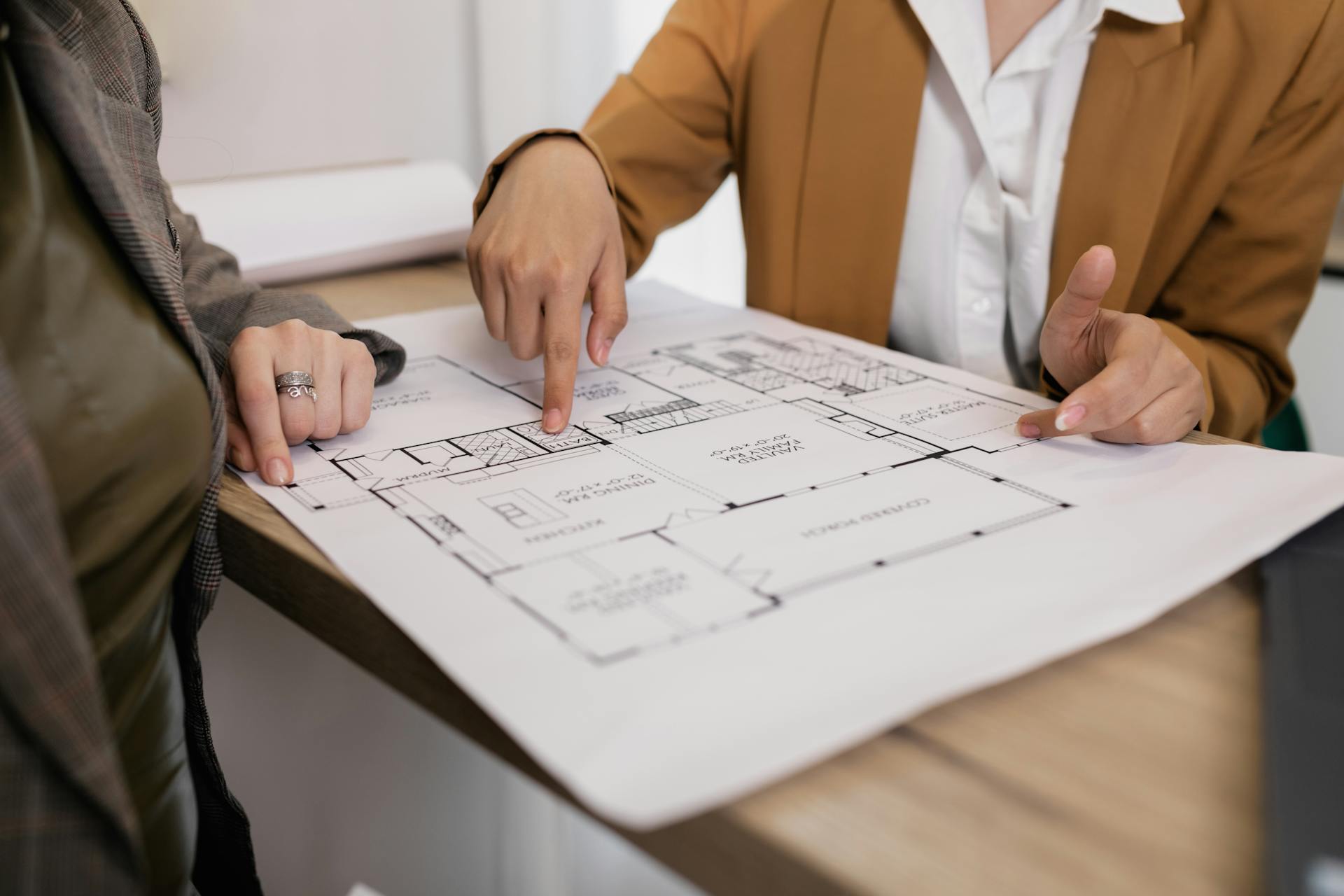
To optimize your pick and pack service, use pack strategies that streamline your fulfillment process and reduce costs. Consider implementing a pick and pack system that automates tasks and reduces labor hours.
Incorporating real-time inventory visibility into your supply chain management is essential. This prevents stockouts and overstocking, ensuring products are readily available for pick and pack fulfillment without wasted capital.
Integrating data systems can help adapt to fluctuating order volumes and product offerings, ensuring smooth operations during growth phases. Tracking key metrics lets you identify areas for improvement and optimize the picking and packing process.
By using a pick and pack system and Order Management System (OMS), you can experience significant advantages, including faster fulfillment, decreased labor costs, decreased shipping costs, reduced excess inventory, less redundant data entry, increased visibility, and data analysis.
Here are some benefits of using a pick and pack system and OMS:
- Faster fulfillment: Analyze your inventory locations and determine the quickest route for shipping orders.
- Decreased labor costs: Automate tasks and reduce labor hours previously devoted to order fulfillment.
- Decreased shipping costs: Distribute from the closest locations to reduce shipping costs.
- Reduced excess inventory: Automatically find the most cost-effective and fastest method for getting orders to customers.
- Less redundant data entry: Use the same information across all stages of the order management process.
- Increased visibility: Track order status and provide visibility to customers and staff.
- Data analysis: Analyze data to determine how to improve operations, identify sales patterns, track KPIs, and forecast sales and inventory levels.
The optimal pick method depends on the number of orders you receive daily. Consider using piece, batch, zone, or wave picking methods, depending on your business needs and order volume.
Benefits and Optimization
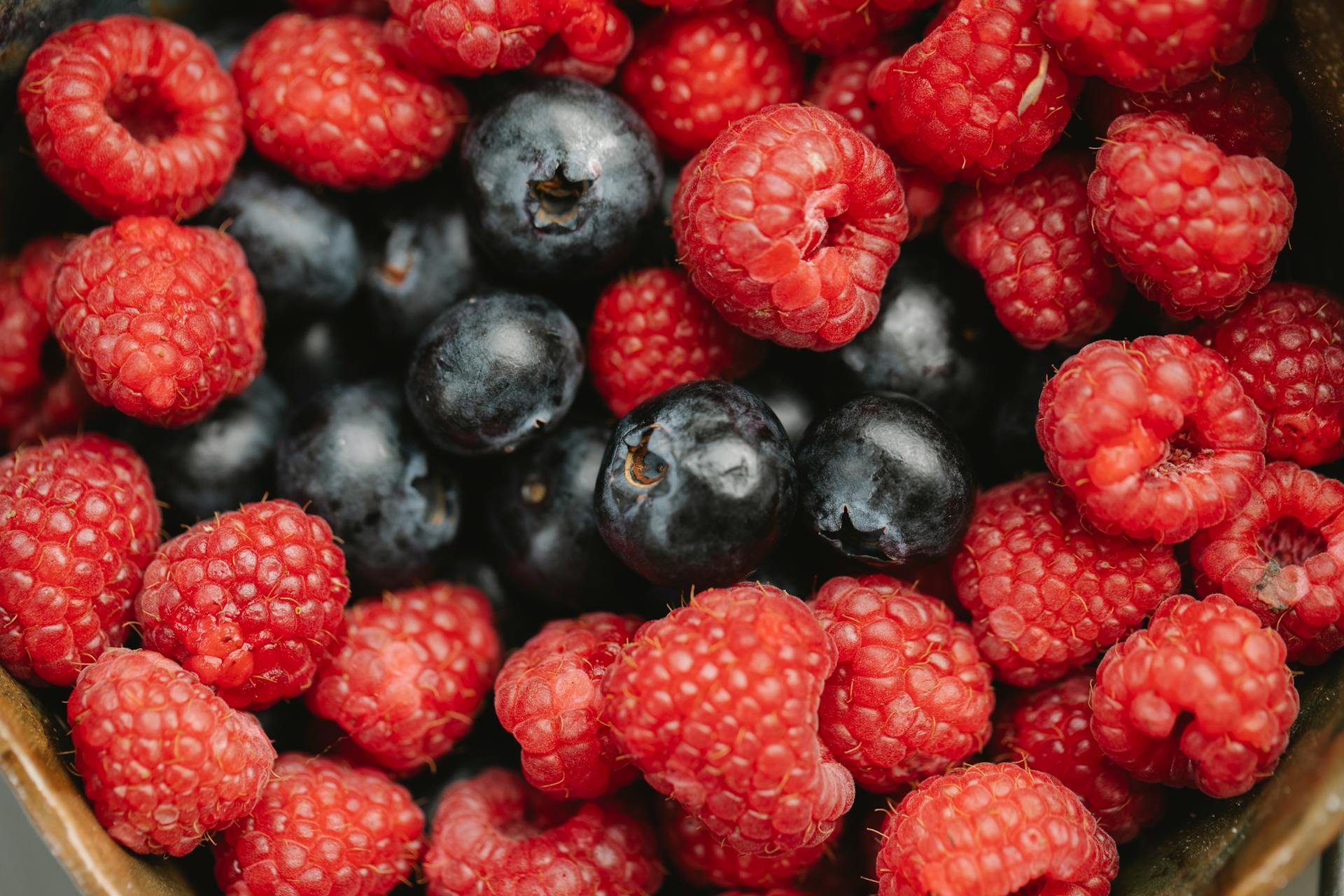
A pick and pack system offers numerous benefits, including faster fulfillment, decreased labor costs, and reduced shipping costs. With an Order Management System (OMS), you can analyze your inventory locations and determine the quickest route to ship an order from the closest warehouse.
Using a pick and pack system can also reduce excess inventory, as an OMS will automatically find the most cost-effective and fastest method for getting your orders to your customers. This means you can avoid keeping too much stock on hand and reduce the risk of missed sales opportunities.
Some key features of a pick and pack system include picking optimization, which guides workers through the most efficient path to pick items in the warehouse. This can be achieved through various picking methods, such as batch picking, zone picking, or wave picking.
Here are some of the benefits of an effective pick and pack system:
- Faster order fulfillment
- Improved accuracy
- Cost savings
- Scalability
- Enhanced customer experience
These benefits can lead to increased customer satisfaction, brand loyalty, and customer retention. By optimizing your warehouse pick-pack-ship management, you can free up staff to handle tasks that generate additional revenue for your business.
Optimize for Dimensional Weight
Some products have different shipping price structures, and if you ship large or heavy items, you may be subject to dimensional weight pricing.
This measures the size of a package to calculate a weight equivalency, which can affect your pick and pack fee.
Compact packaging can reduce your pick and pack fee based on packaging materials and your dimensional weight, leading to cost savings on shipping.
Here are some ways to optimize for dimensional weight:
By implementing these strategies, you can reduce your dimensional weight and save on shipping costs.
Benefits of Pick and Revised
Using a pick and pack system and an Order Management System (OMS) can bring significant benefits to your business. Faster fulfillment is one of the key advantages, as an OMS can analyze your inventory locations and determine the quickest route to ship an order from the closest warehouse.
Automating tasks and reducing labor hours devoted to order fulfillment can also lead to decreased labor costs. An effective system will optimize your warehouse pick-pack-ship management, saving you time and money.
You might enjoy: Shore to Ship Power Systems
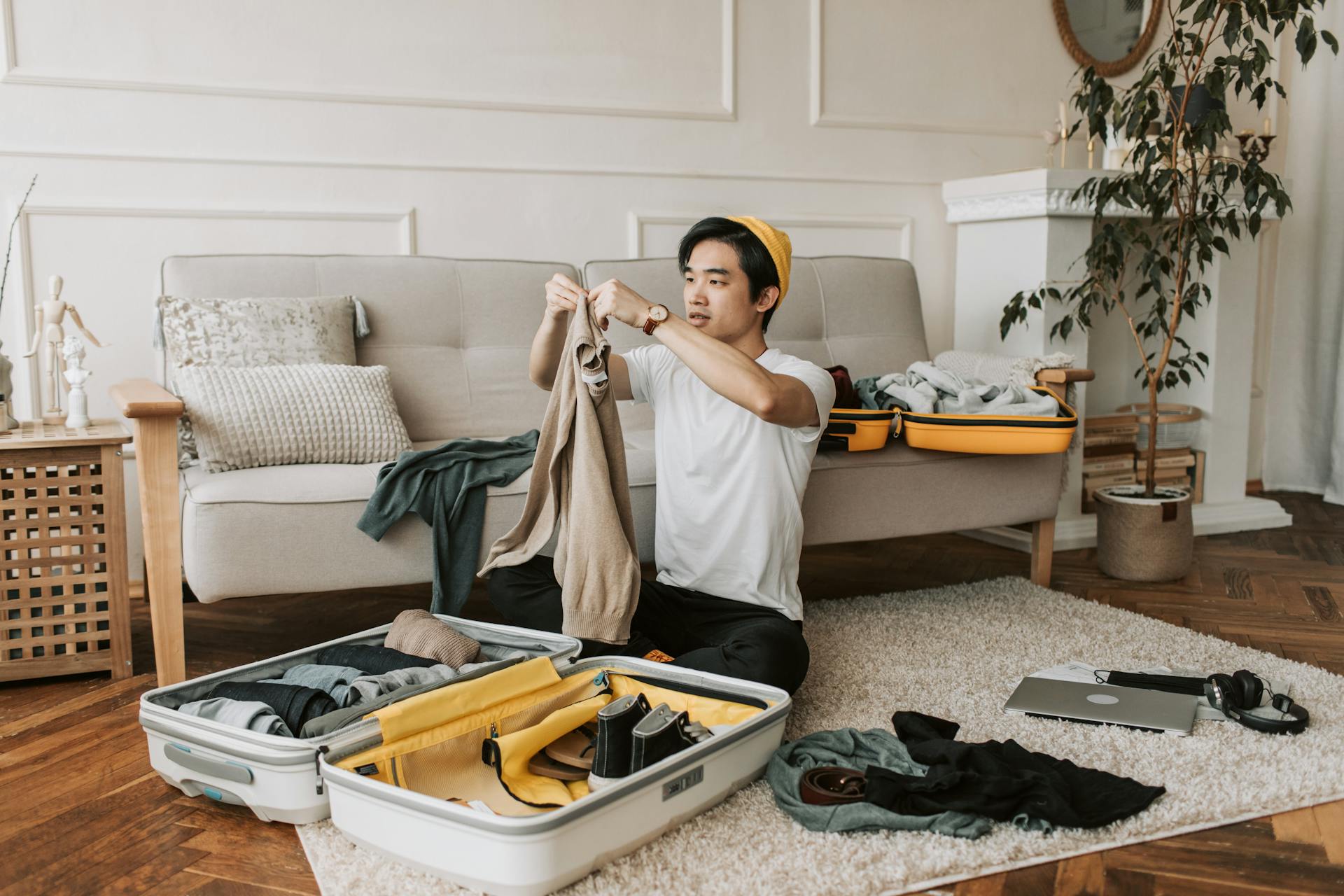
Reducing shipping costs is another benefit of using a pick and pack system and OMS. By distributing from the closest locations, you can reduce your shipping costs and find the most cost-effective method for getting orders to customers.
Excess inventory can also be reduced with an OMS, which will help you monitor your inventory levels and avoid keeping too much stock on hand. This will reduce the need for excess inventory and help you avoid missed sales opportunities.
The same information is used across all stages of the order management process with an OMS, reducing the need for redundant data entry and minimizing the possibility of errors.
A pick and pack system and OMS also provide increased visibility into order status, allowing customers to track their own orders and staff to help with any issues that arise.
Here are some specific benefits of using a pick and pack system and OMS:
- Faster fulfillment
- Decreased labor costs
- Decreased shipping costs
- Reduce excess inventory
- Less redundant data entry
- Increased visibility
- Data analysis
Benefits of Fulfillment
Using a pick and pack system can significantly improve your warehouse operations. It can help you fulfill orders faster by analyzing your inventory locations and determining the quickest route.
An organized warehouse is essential for efficient picking and packing. A clutter-free environment reduces distractions for warehouse staff, allowing them to focus on their tasks and safely complete them.
A robust inventory management system enables accurate monitoring of stock levels, reducing the likelihood of stockouts. This ensures that packing personnel can easily locate and pick the required items.
Using an Order Management System (OMS) can help you reduce excess inventory, saving you money and reducing the risk of missed sales opportunities. An OMS can also analyze your data to determine how to improve your operations and identify sales patterns.
Here are some of the key benefits of using a pick and pack system:
- Faster fulfillment
- Decreased labor costs
- Decreased shipping costs
- Reduce excess inventory
- Less redundant data entry
- Increased visibility
- Data analysis
By implementing a pick and pack system and an OMS, you can improve your warehouse operations, increase efficiency, and reduce costs. This will enable you to focus on growing your business and providing a better customer experience.
Greater Efficiency
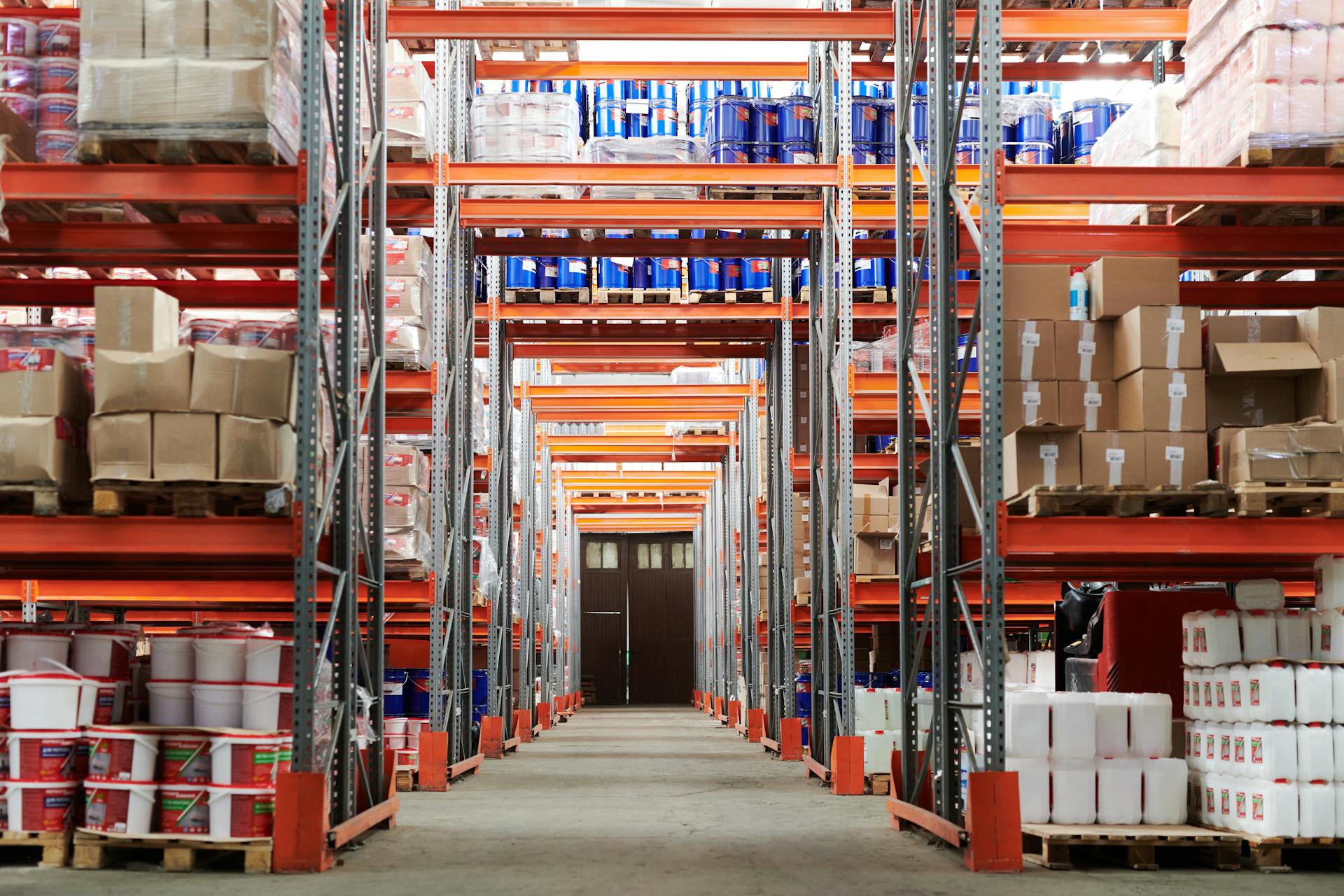
Using a pick and pack system can significantly reduce labor costs by automating tasks and increasing efficiency. An effective system will optimize your warehouse pick-pack-ship management, saving you time and money.
According to Example 9, the more often your warehouse team uses the pick and pack system, the more comfortable they'll become with this technique, leading to greater efficiency. This is especially true when combined with improved speed, resulting in high-quality results with every order.
A pick and pack warehouse setup, as described in Example 7, involves organizing your warehouse to minimize travel and search time. This can be achieved by identifying the most efficient route through the warehouse and implementing tactics like separating popular items to avoid traffic jams.
Here are some benefits of using a pick and pack system:
- Faster order fulfillment: Optimizes workflows to ensure orders are picked, packed, and shipped quickly.
- Cost savings: Reduces labor costs by increasing efficiency and avoiding overuse of packing materials.
- Scalability: Supports growing operations by handling increased order volumes seamlessly.
These benefits are outlined in Example 5, which highlights the importance of using a pick and pack system for high-volume warehouses. By implementing a pick and pack system, you can improve accuracy, reduce labor costs, and increase customer satisfaction.
Choosing and Implementing a System
Choosing and implementing a pick and pack system can be a straightforward process, but it requires careful consideration of the variables that impact efficiency.
The overall concept of pick and pack is simple, but optimizing it for your business is a different story.
You may start with a simpler pick and pack system and transition to different methods as your business grows and expands its omnichannel fulfillment efforts.
The optimal pick method depends on the number of orders you receive daily.
To ensure efficient operations, it's essential to consider the number of orders you receive daily when selecting a pick method.
Recommended read: Business Packing List
System Components and Integration
A pick and pack system is only as good as its components and integrations. Integrating pick and pack process data is crucial for effective supply chain management, preventing data silos that lose their analytical value.
Real-time inventory visibility is key to preventing stockouts and overstocking, ensuring products are readily available for pick and pack fulfillment. Real-time order tracking allows for communication of potential delays or issues, helping to manage customer expectations effectively.
You might enjoy: Packing List for Moving Out for the First Time
To optimize efficiency, consider the variables that impact your pick and pack system, such as order volumes and product offerings. You may start with a simpler system and transition to different methods as your business grows and expands its omnichannel fulfillment efforts.
Here are some key integrations to consider for your pick and pack software:
- Sales Platforms: Sync orders from Shopify, Amazon, or other platforms directly into the system.
- Shipping Carriers: Access real-time shipping rates and automated label printing.
- Accounting Software: Simplify invoicing and financial tracking.
- Customer Relationship Management (CRM): Enhance customer service by keeping order details at your team’s fingertips.
System Components
A well-designed pick and pack system is crucial for efficient order fulfillment.
The overall concept of pick and pack is simple, but there are variables to consider for optimization.
You may start with a simpler pick and pack system and transition to different methods as your business grows and expands its omnichannel fulfillment efforts.
A key aspect of a pick and pack system is its ability to reduce mistakes and conserve resources.
Elements of a pick and pack system include optimizing efficiency through variables such as different methods and techniques.
On a similar theme: Pick and Pack Company
Integration
Integration is key to a smooth pick and pack process. Integrating pick and pack process data is crucial for effective supply chain management.
Data silos can form when certain systems don't connect, losing their analytical value. This can lead to stockouts and overstocking, wasting capital and impacting customer satisfaction.
Real-time inventory visibility is a game-changer, preventing stockouts and overstocking by ensuring products are readily available for pick and pack fulfillment. This also helps prevent wasted capital.
Some key integrations to consider include sales platforms, shipping carriers, accounting software, and customer relationship management (CRM) systems. These integrations can simplify order fulfillment, invoicing, and financial tracking, while also enhancing customer service.
Here are some specific integrations to look for:
- Sales Platforms: Sync orders from Shopify, Amazon, or other platforms directly into the system.
- Shipping Carriers: Access real-time shipping rates and automated label printing.
- Accounting Software: Simplify invoicing and financial tracking.
- Customer Relationship Management (CRM): Enhance customer service by keeping order details at your team’s fingertips.
By integrating these systems, you can ensure seamless and efficient order fulfillment, adapt to fluctuating order volumes and product offerings, and identify areas for improvement in the picking and packing process.
Automation
Automation is a game-changer for pick and pack processes. It can significantly enhance efficiency, accuracy, and speed of order fulfillment. Integrating automation technologies with your Warehouse Management System (WMS) can reduce labor costs and improve overall warehouse operations.
Suggestion: Warehouse Pick and Pack
Conveyor systems, robotic pickers, and automated sorting machines are examples of automation technologies that can enhance efficiency. These technologies can be combined with your WMS to improve accuracy and speed up order fulfillment.
Goods-to-person technologies, such as automated storage and retrieval systems (AS/RS), use vehicles, cranes, and carousels to transport goods to workers for picking and packing. This can save time and reduce labor costs.
Automatic guided vehicles (AGVs) use sensors to navigate through warehouses, transporting inventory to more accessible locations for picking. Autonomous mobile robots (AMRs) can also navigate through warehouses without physical guides or markers.
Pick-to-light systems use bar codes and LED lights to help pickers locate goods. Voice picking technology tells workers what to pick through headsets, giving them a hands-free and paperless way of receiving instructions.
Here are some automation technologies to consider:
- Goods-to-person technologies: AS/RS, conveyor systems
- Automatic guided vehicles (AGVs)
- Autonomous mobile robots (AMRs)
- Pick-to-light systems
- Voice picking technology
- Sortation systems
As your warehouse becomes more streamlined, the cost to store and ship goods will go down, and customer satisfaction with the delivery process will increase.
Frequently Asked Questions
What is the average pick and pack fee?
The average pick and pack fee ranges from $0.20 to $5.00 per item, depending on the fulfillment center. Fees can add up quickly for multiple item orders.
Sources
- https://redstagfulfillment.com/ultimate-guide-pick-and-pack-methods/
- https://cart.com/blog/what-is-pick-pack-and-ship
- https://www.easypost.com/blog/2024-02-26-how-to-build-a-great-pick-and-pack-process-for-your-business
- https://made4net.com/knowledge-center/the-best-pick-and-pack-software-have-these-6-features/
- https://www.extensiv.com/glossary/pick-and-pack
Featured Images: pexels.com