
Having a well-organized warehouse can save you up to 20% on labor costs, according to a study cited in our previous section on "Warehouse Layout and Design".
A key factor in achieving this efficiency is implementing a first-in-first-out (FIFO) inventory management system. This ensures that older stock is sold or used before it expires or becomes obsolete.
By streamlining your warehouse operations, you can also reduce errors and increase customer satisfaction. In fact, a study found that 75% of customers are more likely to shop with a company that has a seamless and efficient online shopping experience.
Effective warehouse management also requires investing in technology, such as automated storage and retrieval systems (AS/RS) and warehouse management software (WMS).
What Is Pick Pack and Ship Warehouse?
A pick pack and ship warehouse is a distribution center where businesses store and manage their inventory. It's where the pick pack and ship process takes place.
Pick pack and ship operations are usually conducted in these warehouses, which may involve shipping orders through multiple sales channels. This can include handling a high volume of orders and ensuring accurate and timely order fulfillment.
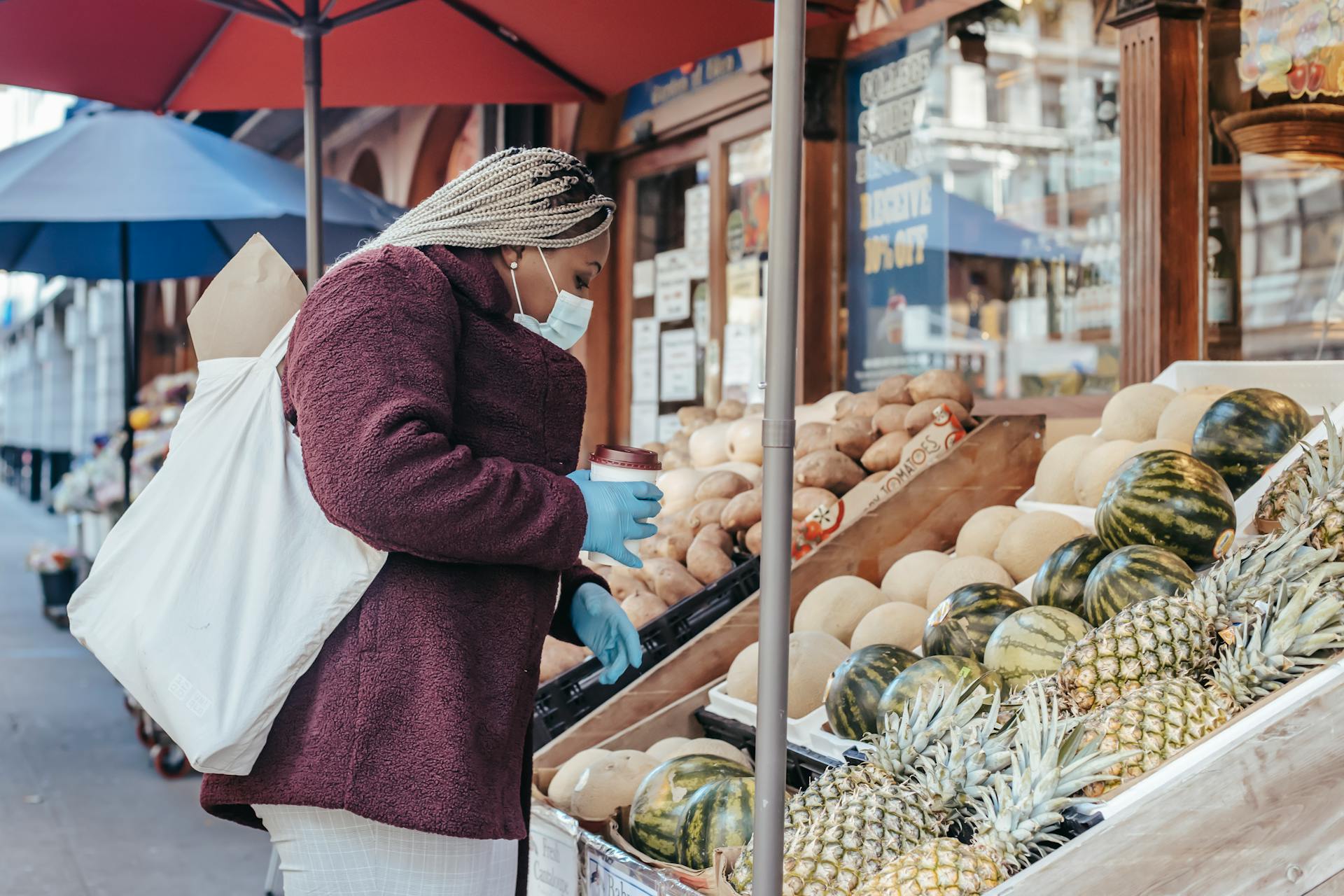
E-commerce businesses often use pick and pack warehouses to fulfill sales orders. These warehouses are equipped with warehouse systems software, such as Shipstation and Magento, to manage inventory and track the pick pack and ship process.
The pick pack and ship process is a three-stage process: pick, pack, and ship. It involves selecting the right items, packing them safely, and dispatching them to customers.
Save on Your Bottom Line
Reducing shipping costs is a major advantage of an efficient pick pack and ship system. By optimizing package size and using the right packing materials, businesses can save big on shipping charges.
Properly managing the packing process can lead to substantial savings, especially for high-volume shippers. In fact, by streamlining operations and reducing waste, businesses can save on their bottom line.
A well-coordinated pick pack and ship system can help businesses scale smoothly and manage higher order volumes without a hitch. This means they can focus on growing their business without breaking the bank.
Curious to learn more? Check out: Packing List for Alaska
Here are some ways to save on shipping costs:
- Use appropriate packing materials to minimize waste and damage.
- Optimize package size to reduce shipping charges.
- Automate the picking and packing process to reduce labor costs.
By implementing these strategies, businesses can reduce their shipping costs and improve their bottom line. In fact, efficient pick pack and ship processes are more than just operational necessities – they're strategic advantages.
Challenges and Disadvantages
The pick, pack, and ship process can be a challenge to manage, especially as order volume and inventory increase.
Poorly planned fulfillment operations can lead to costly mistakes or long lead times.
Today's online brands expect packages to ship within 24 hours, and failing to meet this expectation can reduce customer satisfaction and damage the brand's reputation.
Insufficient operational structure can't handle increasing order volume or unit count, making it difficult to keep up with demand.
Challenges arise when the operational structure is insufficient to handle the increasing order volume or unit count.
Inventory Management
Inventory management is crucial to the smooth functioning of a pick, pack, and ship operation. A robust inventory management system helps track inventory levels in real time, anticipate stockouts, and prevent overstocking.
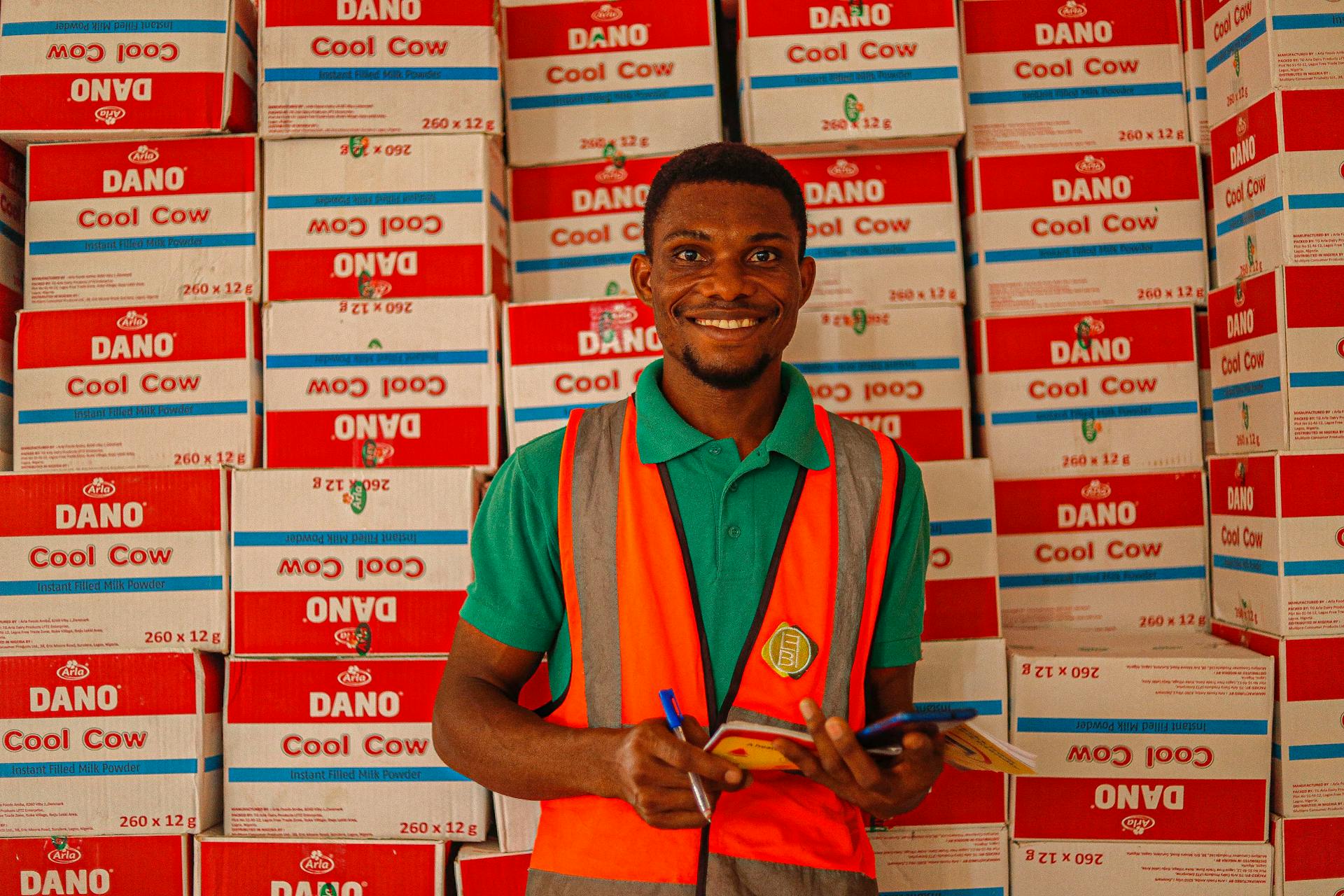
The number one challenge of any pick pack and ship operation is properly managing inventory, especially in a fulfillment warehouse with a large number of products. A well-managed pick, pack, and ship system can limit excess inventory by ensuring the right products are always available for fulfillment.
Implementing a WMS (inventory management software) is one of the main ways to improve the pick pack ship process and inventory management process. Volume inventory management, where SKUs with high turnover are stored closest to the packing station, minimizes the steps staff take when order picking.
Revised Heading: Return Only the Core Meaning
A well-managed pick, pack, and ship system can limit excess inventory by ensuring the right products are available for fulfillment.
Limiting excess inventory is key to avoiding overstocking and tying up capital in unnecessary inventory.
Automating the pick and pack process with software can increase order picking accuracy and efficiency.
This can be achieved by deploying software that streamlines the order picking process and reduces errors and delays.
As your ecommerce business grows, you may need to evolve your warehouse picking and packing methods to meet demand.
Startups and early-stage companies may get away with picking items one at a time, but advanced warehouse picking methods are necessary for speed and efficiency.
Your pick and pack system should match your inventory and order complexity to ensure smooth operations.
The Puzzle—Damaged Goods
Damaged Goods can be a real puzzle to solve. Incorrect packing materials and processes can lead to damaged goods.
Choosing the right packing materials for each item is crucial. This helps prevent damage during shipping.
Incorrect packing materials can increase shipping costs. This is a problem for both the business and the customer.
Streamlining packing processes is essential for efficiency. This helps prevent damage and reduces costs.
Incorrect packing processes can lead to dissatisfied customers. This can harm a business's reputation and relationships with customers.
Here's an interesting read: Packing Box for Wine Glasses
Inventory Control
A well-managed pick, pack, and ship system can limit excess inventory. By ensuring that the right products are always available for fulfillment, you can avoid overstocking and tying up capital in excess inventory.
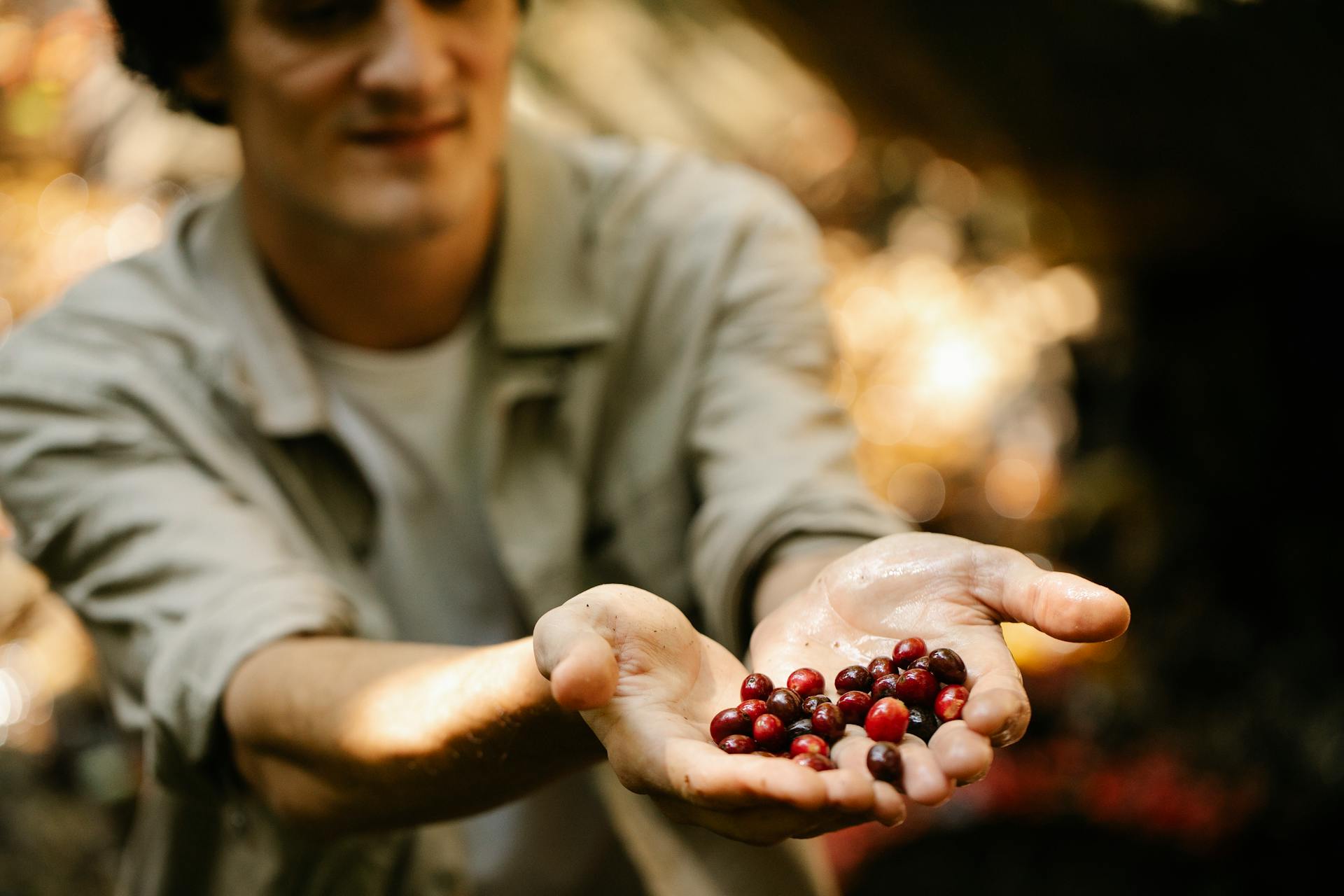
Excess inventory can lead to wasted resources and lost opportunities. It's essential to strike a balance between having enough stock to meet demand and avoiding overstocking.
Inventory management software can help you track inventory levels in real-time, anticipate stockouts, and prevent overstocking. This is especially crucial for 3PL or fulfillment companies serving multiple clients.
Grouping items by shared traits, such as turnover or packing methods, is a key strategy in inventory management. For example, grouping products that all need bubble wrap or large items that don't require an additional box can simplify the pick and pack process.
Automation can greatly improve the pick and pack process, increasing order picking accuracy and efficiency while reducing errors and minimizing delays.
Optimization and Efficiency
An efficient pick pack and ship process can significantly enhance your business's operational efficiency, expediting the order fulfillment process and providing opportunities for reducing labor costs, minimizing errors, and ensuring customer satisfaction.
A streamlined pick pack and ship operation is crucial for growth, customer satisfaction, warehouse efficiency, and overall success. It's a strategic tool that can give your business a competitive edge in today's dynamic e-commerce landscape.
Properly managing the pick pack and ship process can reduce labor costs by implementing efficient picking strategies, allowing workers to fulfill more orders in less time. This increased productivity can reduce the need for additional staff and overtime hours.
Automated packing systems can adjust on the fly to different product sizes and pack them uniformly, reducing material waste and human error. One case involved a client who adopted automated packing lines and saw a 40% increase in packing speed and a reduction in material usage by 15%.
A well-organized warehouse layout can also save vast amounts of time and increase efficiency. For example, if your most popular product is located in the back of the warehouse, altering the warehouse layout to move this material closer to the fulfillment area could save time and increase efficiency.
To optimize your pick pack and ship process, you must identify and reduce unnecessary steps or distance as much as possible. This can be achieved by implementing a zone picking, wave picking, or piece picking strategy, depending on your customers' needs and inventory type.
Check this out: Alaska Packing List Pdf
Here are some key benefits of efficient pick pack and ship processes:
- Streamlining operations helps businesses scale smoothly and manage higher order volumes without a hitch.
- Reducing costs through optimized workflows means less waste, fewer errors, and better use of resources.
- Improving customer satisfaction by ensuring quick, accurate deliveries – because nothing builds loyalty like a package that arrives on time and in perfect condition.
By implementing efficient pick pack and ship processes, you can unlock the secrets of optimizing your logistics operations and see how solutions like SkuNexus can transform your warehouse operations.
Solutions and Strategies
Investing in comprehensive software solutions can greatly simplify the pick, pack, and ship process. Warehouse management software can help manage warehouse operations efficiently by providing the most efficient route for picking and suggesting the appropriate packing materials for each order.
A proper Warehouse Management System (WMS) will also help direct your pick pack ship process by choosing the right picking strategy for your particular type of inventory and inventory management process. This involves selecting the best type of picking, such as zone picking, wave picking, or piece picking, that is best suited for your customers and inventory type.
The best pick pack and ship operations feature seamless integration, efficient automation, and customizable workflows. SkuNexus excels at providing these features, which can transform your logistics operations.
Subpar Strategies
Subpar Strategies can really hinder your pick, pack, and ship process. Employing inappropriate picking methods given your order volume, warehouse size, and product range can lead to wasted time and increased labor costs.
Failing to optimize your picking strategies can be a major obstacle. Not all products require a zone picking strategy, some may suit better for a wave picking, or even piece picking strategy.
Choosing the wrong picking strategy can be costly. Inventory software can help direct your pick pack ship process, but only if it's used correctly.
Inadequate picking strategies can lead to inefficiencies. A proper Warehouse Management System (WMS) will help you choose the right picking strategy for your particular type of inventory and inventory management process.
In the end, it's all about finding the right fit for your business. Not all products are created equal, and neither are all picking strategies.
Optimized Strategy
Having a subpar picking strategy can lead to wasted time and increased labor costs, so it's essential to optimize your approach.
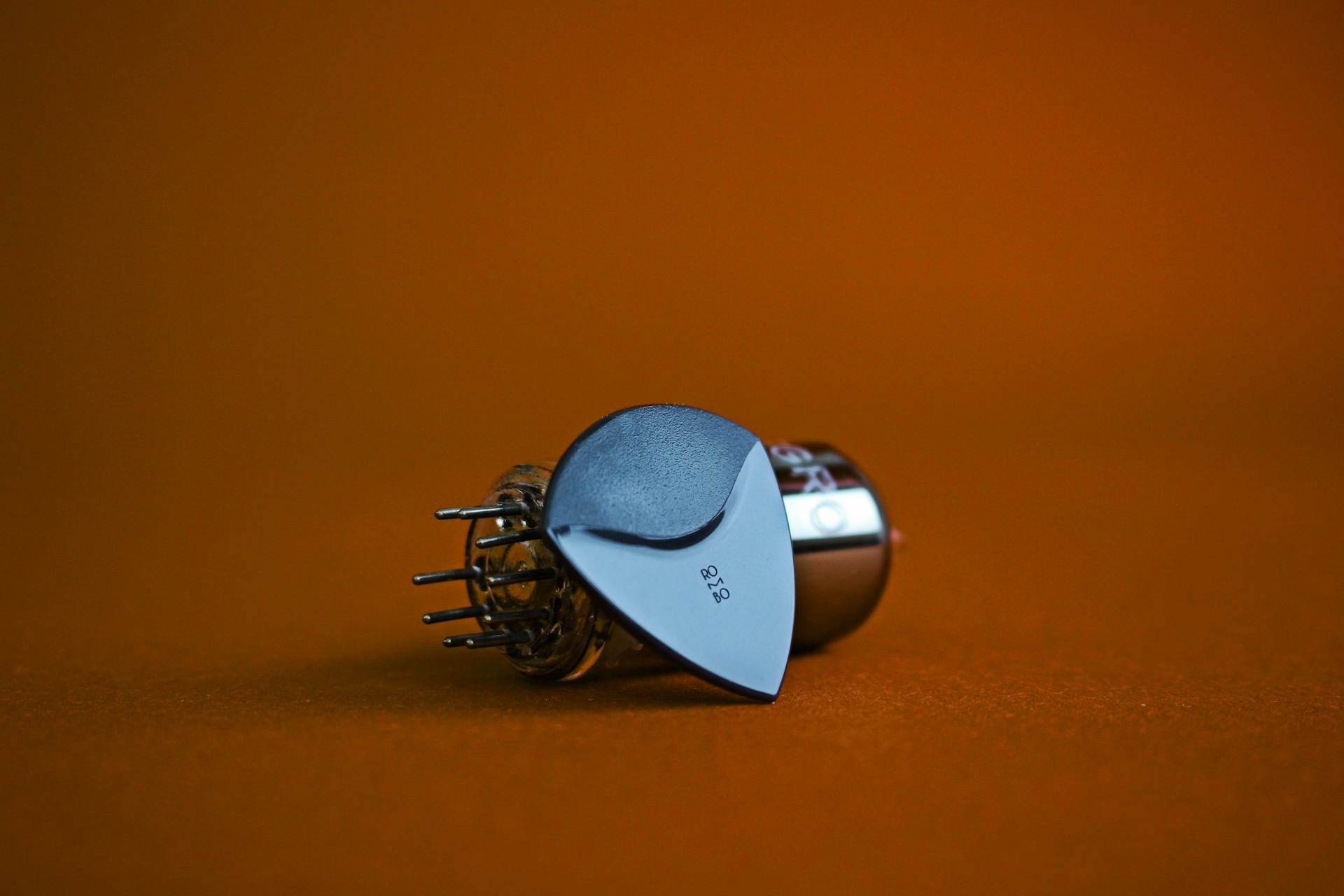
Investing in comprehensive software solutions can greatly simplify the pick, pack, and ship process by providing the most efficient route for picking and suggesting the right packing materials.
Not all products require a zone picking strategy, some may suit better for a wave picking, or even piece picking strategy, so choose the type of picking that is best suited for your customers and inventory type.
The best pick pack and ship operations feature seamless integration, efficient automation, and customizable workflows, all of which can be achieved with the right software solution.
To determine the best pick and pack fulfillment method, you need to consider what your customers want, such as fast shipping or free shipping, and what kind of packing or packing materials they prefer.
Whether you use piece picking, batch picking, zone picking, or wave picking, make sure your operations are as streamlined as possible by identifying and reducing unnecessary steps or distance in your pick pack and ship process.
By optimizing your picking strategy and using the right software solution, you can save time and increase efficiency, just like altering the warehouse layout to move popular products closer to the fulfillment area can save vast amounts of time and increase efficiency.
Outsourcing and In-House Fulfillment
Outsourcing pick and pack operations to a 3PL can provide scalable and cost-effective solutions, especially for businesses with fluctuating order volumes. A 3PL's flexibility allows for adjustments to meet changing demand.
Cost considerations play a crucial role in the decision-making process, too. A 3PL may be able to provide a favorable pick and pack fee based on order fulfillment and SKU volumes.
Outsourcing eliminates the need for substantial upfront investments in pick and pack warehouse space and other resources, providing financial flexibility.
Outsourcing
Outsourcing can be a game-changer for businesses with fluctuating order volumes. If your order quantities vary seasonally or due to market trends, a 3PL's flexibility can provide scalable and cost-effective solutions.
Outsourcing to a 3PL can eliminate the need for substantial upfront investments in pick and pack warehouse space and other resources. This shift to variable costs provides financial flexibility and allows businesses to allocate resources strategically.
A 3PL can help with the picking and packing process, labor costs, shipping, and other supply chain considerations. They can also enhance order accuracy, reduce errors, and streamline the order fulfillment process.
Outsourcing can renew your company focus and multiply your success in other areas. By partnering with a 3PL, you can save time, money, and efforts, and focus on more productive tasks.
You don't have to rent space to stock inventory or fulfill boxing, labelling, or finding the shipping carrier. A 3PL can store, pick, pack, and ship products on your behalf.
Outsourcing can provide a favorable pick and pack fee based on order fulfillment and SKU volumes. This can be a cost-effective solution for businesses with varying order quantities.
Deciding on In-House Fulfillment
Involving your leadership team in the decision-making process is crucial when considering in-house order fulfillment.
Examine areas such as quality control, inventory storage, warehouse managers, and supply chain managers to gather all the necessary information.
Make sure to leave no stone unturned in this process, as companies often make poor decisions due to incomplete analysis.
A solid understanding of the pick pack ship process, including packing, shipping, inventory management, and packing materials, is essential for a successful in-house operation.
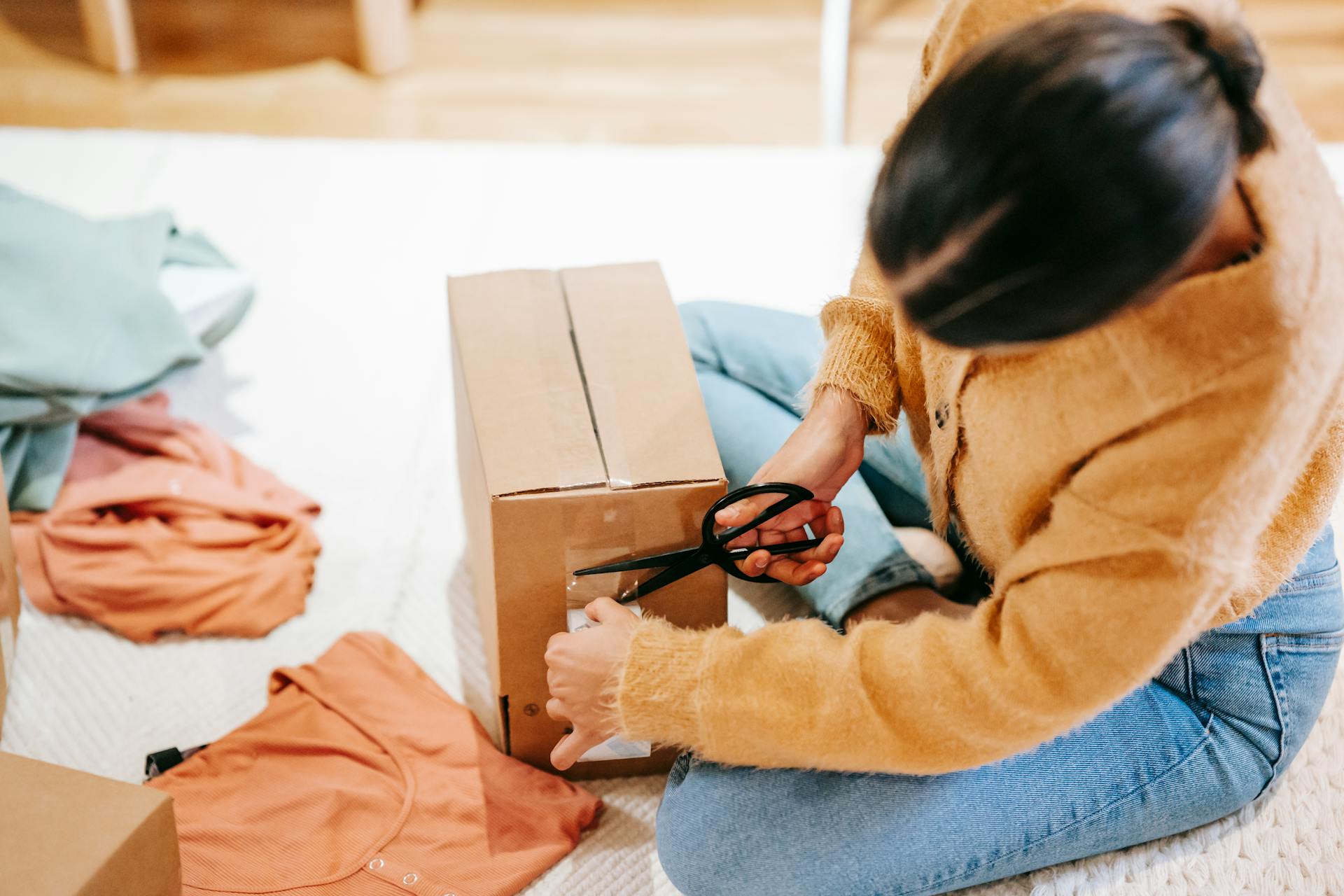
You should also consider how you will measure success in areas such as customer satisfaction, shipping times, and inventory levels.
Involving managers from all areas of your company will help you make a decision with all the information at hand.
Developing an in-house picking, packing, and shipping service can provide tighter control and more profitability potential.
Automation and Technology
Automation and technology have revolutionized the pick pack and ship process, making it faster, more efficient, and cost-effective. Automation in packing, for instance, can adjust on the fly to different product sizes and pack them uniformly, reducing material waste and human error.
With the right automation and technology, you can increase your packing speed by 40%, like a client who adopted automated packing lines. They also reduced material usage by 15%, showing that automation can pay off in efficiency and cost savings.
Automated guided vehicles (AGVs) can transport products between zones without human intervention, while robotic arms can handle repetitive tasks, reducing strain on human workers and speeding up the packing process. A major e-commerce retailer implemented robotic sorting arms in their distribution centers, increasing their package processing speed by 200%.
What Is Software?
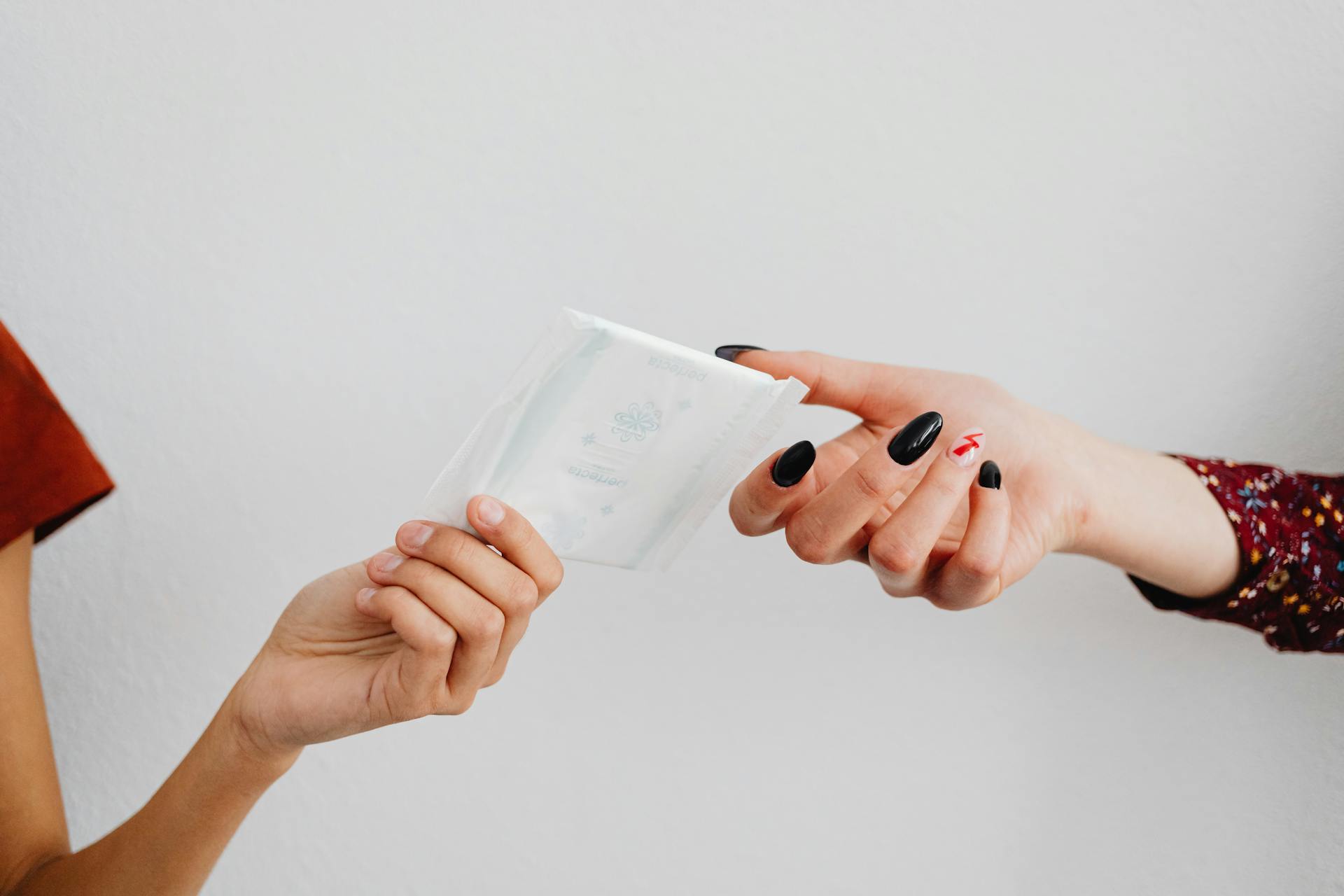
Software plays a crucial role in automation and technology, and one key area where it shines is in pick and pack fulfillment. Software for pick and pack fulfillment is designed to help businesses streamline their order fulfillment process.
It provides a range of features and capabilities, including order management, inventory tracking, and packing slip and shipping label generation.
Automation can increase the accuracy and efficiency of pick and pack processes by automating tasks.
Some software solutions are capable of managing the full set of warehouse systems, while others are purpose-built just for deploying the various pick and pack processes.
By automating these processes, businesses can better manage their inventory and reduce errors.
Advanced Technologies in Ops
Automation and technology are revolutionizing the way we work, and warehouse operations are no exception. By leveraging advanced technologies, businesses can streamline their pick, pack, and ship processes, reducing errors and increasing efficiency.
One key area of focus is automation in packing, which can adjust on the fly to different product sizes and pack them uniformly, reducing material waste and human error. This can lead to significant cost savings, as seen in one case where a client saw a 40% increase in packing speed and a reduction in material usage by 15%.
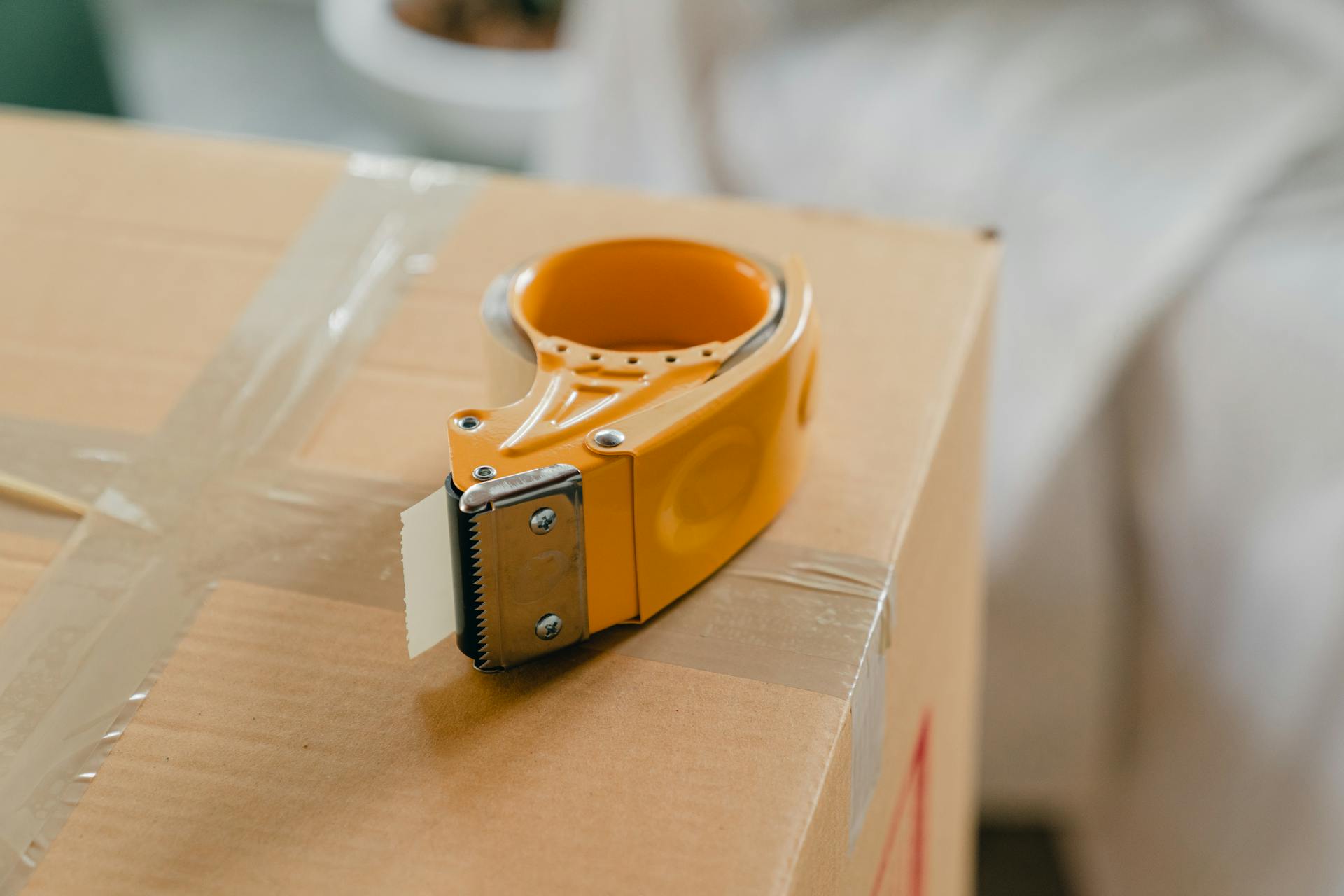
Robotics in warehouses is also becoming increasingly prevalent, with automated guided vehicles (AGVs) transporting products between zones without human intervention. This can speed up the packing process and reduce strain on human workers, as seen in a major e-commerce retailer that implemented robotic sorting arms in their distribution centers, increasing their package processing speed by 200%.
AI and machine learning are also playing a crucial role in optimizing warehouse operations, predicting order trends and optimizing routing and sorting processes. This can lead to faster picking and error-free packing, as seen in an example where AI algorithms dynamically assigned picking tasks based on worker location and inventory status, slashing time spent on each order.
By embracing these advanced technologies, businesses can transform their logistics operations and achieve greater efficiency and accuracy.
Logistics
Logistics can be a major bottleneck in your warehouse operations, but it doesn't have to be. Integrating with shipping carriers can make a huge difference, allowing you to automate carrier selection and dispatch.
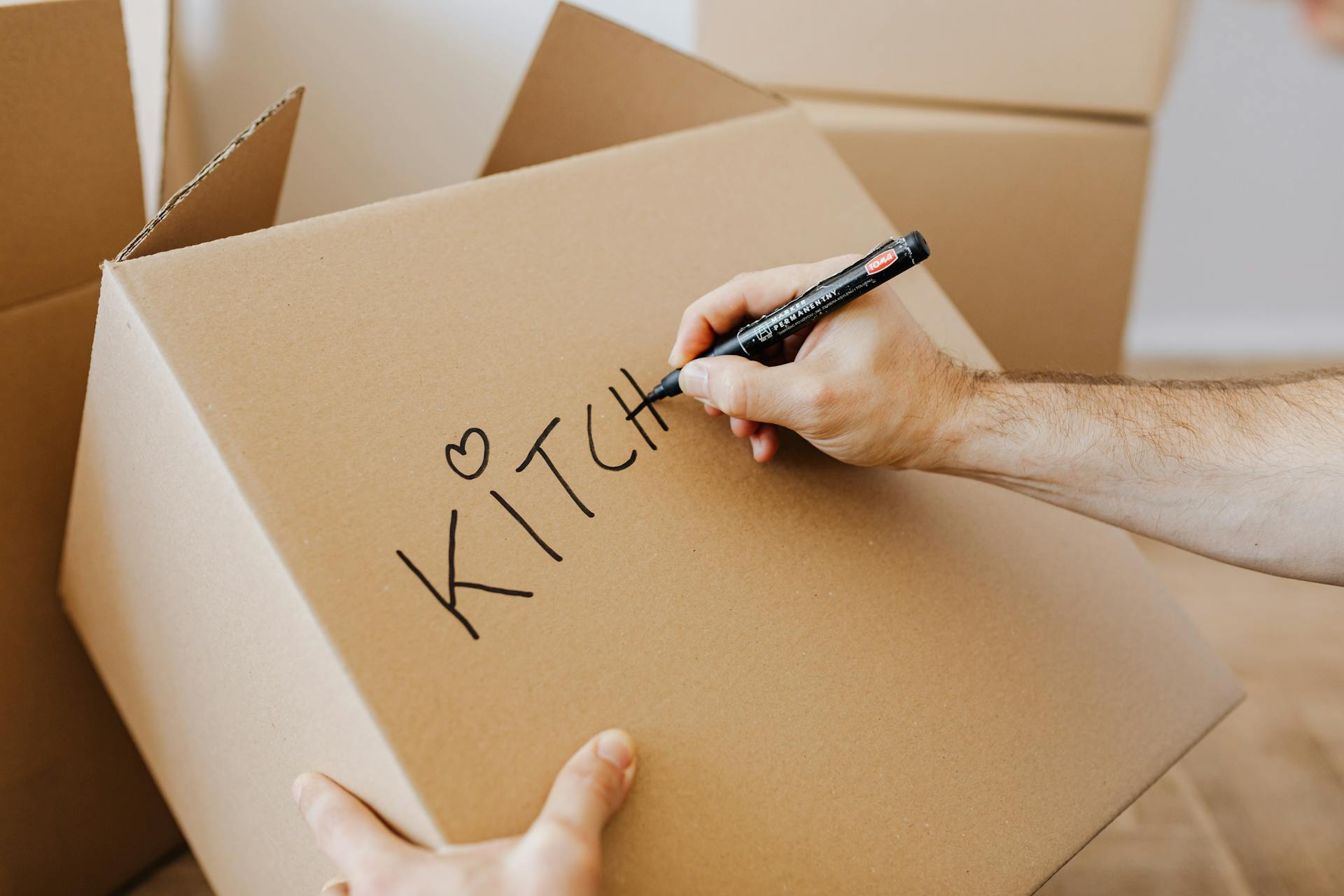
At SkuNexus, we've seen clients reduce their manual processing time by up to 50% by integrating their systems with carriers. This means you can free up half your time for more strategic tasks.
A seamless flow from your warehouse to the customer's doorstep is key, and a robust integration system can help achieve this. This can reduce delays and errors, making your logistics chain more efficient.
Consider upgrading to a more sophisticated system that automates carrier selection and dispatch, and evaluate your current integration setup to see where gaps or disconnects might be causing delays or data errors.
Data Analytics
Data analytics is a game-changer for pick, pack, and ship warehouses. It helps track and tweak every detail of operations, from warehouse layout efficiency to optimal shipping methods.
By leveraging data analytics, businesses can improve current processes and gain actionable insights for future improvements. This can lead to significant gains, such as a 30% improvement in picking efficiency.
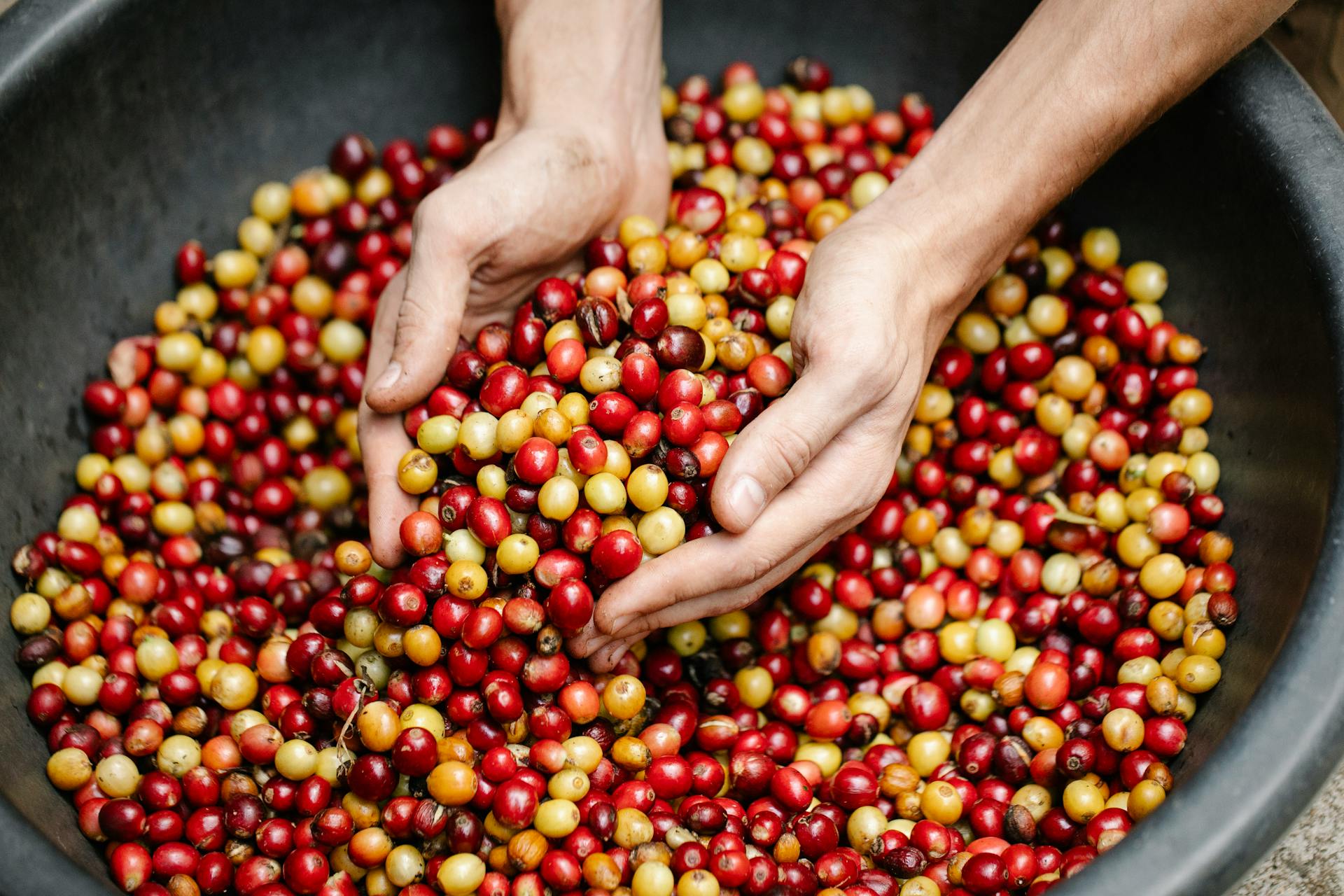
Data analytics allows businesses to monitor key metrics, identify areas for improvement, and optimize the picking and packing process. This includes tracking inventory turnover, delivery times, and error rates.
Real-time inventory visibility prevents stockouts and overstocking, ensuring products are readily available for pick and pack fulfillment. This helps businesses avoid wasted capital and ensures products are readily available for customers.
With data analytics, businesses can also inform targeted promotions and upselling opportunities, enhancing customer engagement and satisfaction. This is made possible by integrated data systems that provide real-time order tracking and allow for communication of potential delays or issues.
Future of Fulfillment
The Future of Fulfillment is here, and it's all about efficiency. Gone are the days of manual logs and chaotic storage spaces, replaced by sophisticated hubs utilizing cutting-edge tech like robotics and AI.
Our pick, pack, and ship warehouse services are designed to keep everything flowing smoothly to customers. Between 9 am and 6 pm, our experts perform all picking, packing, and shipping in-house at our well-equipped facility.

Robotics in warehouses isn't about replacing humans; it's about augmenting human capabilities and increasing efficiency. Automated guided vehicles can transport products between zones without human intervention.
A major e-commerce retailer implemented robotic sorting arms in their distribution centers, increasing their package processing speed by 200%. This is a real-world example of how robotics can make a significant impact.
By exploring which repetitive tasks in your warehouse could be handled by robots, you can start small with a single automated solution and pave the way for more extensive robotic integration. This can help reduce strain on human workers and speed up the packing process.
Frequently Asked Questions
Is pick packing stressful?
Pick packing can be a stressful job due to fast-paced and physically demanding work settings. However, with the right skills and mindset, you can thrive in this role and complete tasks efficiently.
How do companies pick pack ship in PRD?
Companies pick items from larger containers, pack them into smaller boxes for delivery, and then ship them to customers via services like FedEx or UPS. This process ensures efficient and secure delivery of products to end-users.
Featured Images: pexels.com