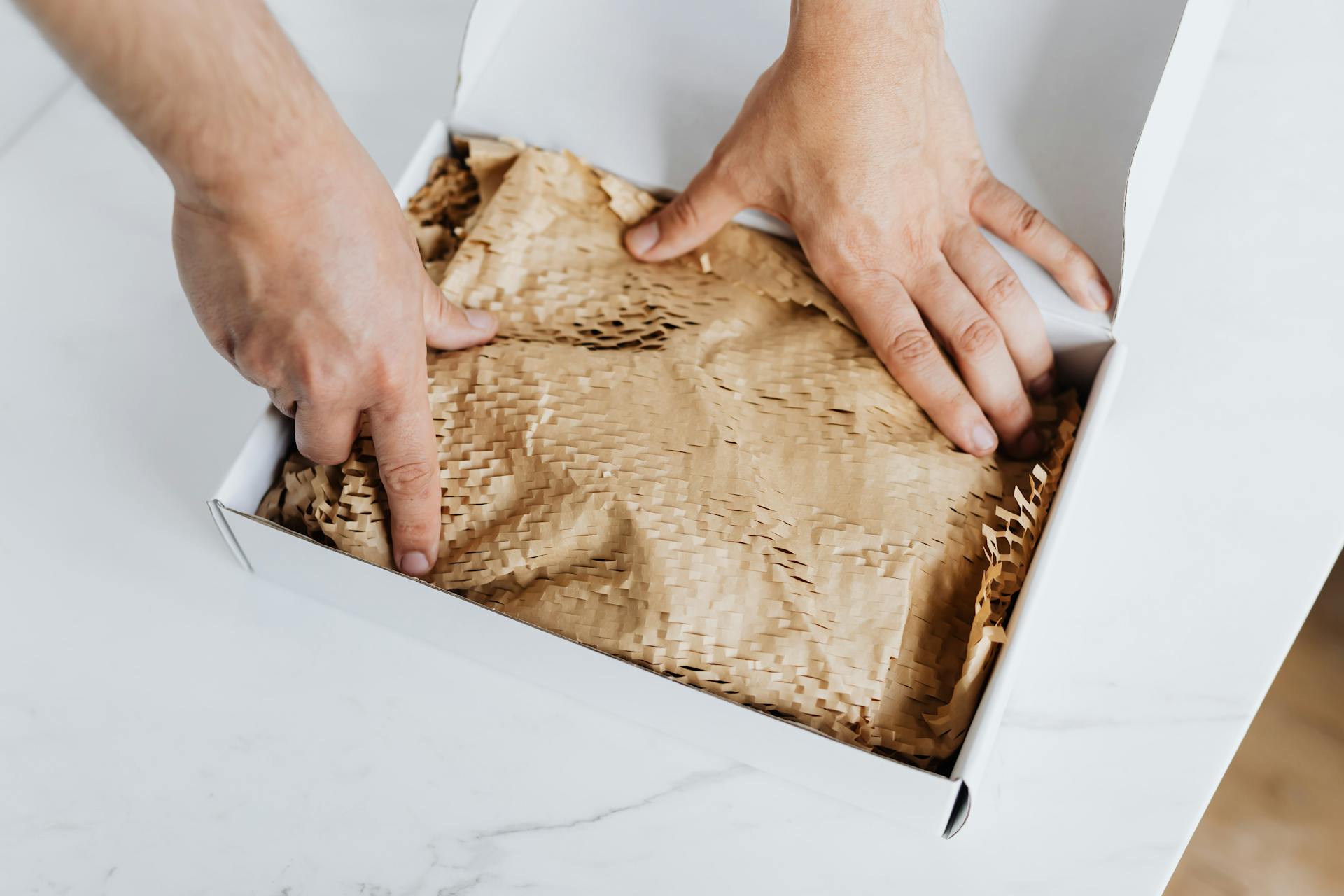
Order picking systems are a crucial component of efficient warehouse operations. They enable warehouses to pick and pack orders quickly and accurately, improving customer satisfaction and reducing costs.
According to a study, warehouses that implement order picking systems experience a 20% reduction in labor costs. This is because order picking systems automate many tasks, freeing up staff to focus on higher-value tasks.
Effective order picking systems require careful planning and implementation. This includes choosing the right equipment, such as conveyor belts and automated storage and retrieval systems (AS/RS), and training staff on how to use it.
A well-designed order picking system can increase picking speeds by up to 30%. This is because it streamlines the picking process, reducing the time it takes to locate and pick items.
Order Picking Systems
Order picking systems are designed to streamline the process of selecting and collecting items from a warehouse or storage facility.
Pick to light systems, for example, facilitate the creation of personalized systems adaptable to all kinds of picking, sorting, and assembly operations.
Pick indicator systems help operators quickly and accurately locate required items, directing them to a specific location and providing information for the task to be completed.
Automated solutions like the Order Picking System (OPR) based on gantry robots can also be used to optimize the picking process.
Technologies like automated picking systems (robots), vertical carousel warehouses, and automated sequencing and buffering systems (SQS, FSS, etc.) are becoming increasingly common in picking system solutions.
Bar code scanning and radio frequency identification (RFID) are also used in AICD systems to validate and capture information about items, which can then be used to trigger pick indicator systems.
Here are some common technologies used in AICD systems:
- Bar Code Scanning: uses barcode labels that can be scanned by handheld or fixed-location radio frequency (RF) scanners or camera-based imagers.
- Radio Frequency Identification (RFID): uses a small tag or label with an integrated circuit and antenna to capture data, which can be transferred to a host data system without line-of-sight.
Automated Warehouse Systems
Automated warehouse order picking systems are a game-changer for modern warehouses. They work best with the right technology.
Goods-to-Person Systems are highly efficient and flexible, designed to keep operations ahead of the industry. Hai Robotics creates these solutions.
By integrating with a Warehouse Management System (WMS), operations are monitored in real-time, offering a view of order status and inventory. This helps maximize efficiency.
Modula Picking Solutions have been implemented in various case studies, resulting in impressive performance. Subaru of New England, for example, can process up to 60 orders at a time with picking rates of over 1,600 lines per day.
Expand your knowledge: Time between Order and Delivery
Maximize Efficiency
Automated warehouse systems are designed to maximize efficiency by reducing manual labor and minimizing errors.
Batch picking optimizes picking activities by retrieving SKUs in bulk to fulfill multiple orders at a time. This minimizes travel time and speeds up fulfillment operations, especially for warehouses that receive multiple orders containing the same SKUs.
With the multi-batch order picking system, workers can pick items for multiple orders simultaneously, reducing picking times and minimizing overall travel time.
Wave picking is a variation of batch and zone picking that is particularly useful for large warehouses that regularly receive multiple high-volume orders. Orders are grouped into sets or waves according to factors like customer location, order frequency, order type, picking zones, delivery date, etc.
By using a put-to-light batch picking system, Subaru of New England can process up to 60 orders at a time, with picking rates of over 1,600 lines per day.
Zone picking significantly reduces travel time through fulfillment centers since workers stay within their assigned zones when picking items.
Automated Warehouse Types
Automated warehouse order picking systems work best for modern warehouses with the right technology.
There are several types of automated warehouse systems, including automated warehouse order picking systems, which work best for modern warehouses with the right technology.
These systems can be implemented in various ways, such as using automated picking systems that can handle a high volume of orders efficiently.
Some warehouses use automated storage and retrieval systems (AS/RS) to store and retrieve inventory, which can improve picking accuracy and reduce labor costs.
Automated picking systems can be designed to handle specific types of inventory, such as small or large items, and can be integrated with other warehouse systems for a seamless operation.
Broaden your view: Types of Conveyor Systems
Pick-to-Light Systems
Pick-to-Light Systems are one of the most productive order fulfillment solutions, increasing productivity and accuracy while reducing costs throughout all the stages of the order filling process.
The technology has a very low learning curve, so productivity gains are quick, even with new and seasonal employees.
Pick-to-Light Systems require the installation of pick-to-light LEDs and barcode scanners on racks and shelves throughout the warehouse.
These systems allow workers to follow LED lights to retrieve SKUs on their pick list, making the picking process more efficient.
The Modula Picking Station is ideal for operations with predetermined put positions, and can be paired with Put to Light Systems for increased efficiency.
Facilitated by Pick to Light systems, personalised systems can be created to adapt to all kinds of picking, sorting and assembly operations.
Each time an item is slotted into the correct position, the user presses a confirmation button to indicate the task is complete, making the process more streamlined.
The use of Pick-to-Light Systems can be taken on the go with the Modula Picking Cart, a Put to Light station on wheels that allows for easy movement of retrievals to different locations.
Voice and Mobile Scanner-Based Systems
Voice and Mobile Scanner-Based Systems are designed to streamline order picking processes, allowing employees to quickly and accurately scan items as they pick them.
These systems often utilize voice commands, enabling employees to receive instructions and confirm picks without needing to physically interact with a screen.
Research has shown that voice-based systems can increase picking accuracy by up to 20%.
Mobile scanners, on the other hand, provide employees with a handheld device that allows them to scan items and receive real-time updates on their picking progress.
Studies have demonstrated that mobile scanner-based systems can reduce picking times by up to 30%.
Collaborative Mobile Robots and Technology
Collaborative mobile robots are changing the game in warehouse order picking by automating the movement of items and assisting human operators. They can minimize walking through real-time route optimization and can be programmed to follow discrete, batch, zone and cluster picking methods.
These robots leverage artificial intelligence and machine learning to optimize picking routes and tasks in real-time, making them a valuable asset to any warehouse. They can also be programmed to work in collaborative human-machine environments, making them a great option for companies looking to streamline their order fulfillment operations.
Companies can use collaborative mobile robots in conjunction with other technologies, such as automated picking systems and pick to light systems, to create a comprehensive order picking system. By choosing the right combination of technologies, companies can achieve their order fulfillment goals with the minimum resources, effort, and errors.
If this caught your attention, see: Machine Conveyor Systems
Collaborative Mobile Robots
Collaborative mobile robots are changing the way we pick orders in warehouses. They can help human operators by automating the movement of items throughout the warehouse.
These robots assist in order picking activities by handling the manual task of moving products around. They can be programmed to follow discrete, batch, zone, and cluster picking methods.
Collaborative mobile robots can minimize walking through real-time route optimization. This can help reduce fatigue and increase productivity for warehouse workers.
They also leverage artificial intelligence and machine learning to optimize picking routes and tasks in real-time. This means they can adapt to changing circumstances and make adjustments on the fly.
Collaborative mobile robots can be used in conjunction with other picking systems, such as automated picking systems and pick to light systems.
Smart Carts
Collaborative mobile robots can work with smart order picking carts to streamline the order picking process. These carts can be integrated with industry-standard warehouse carts and iPads to provide a cost-effective solution.
A different take: Picking Carts for Order Pickers
Recent years have seen increased use of robots in order picking activities, and smart carts are a key part of this trend. Collaborative mobile robots can assist in order picking activities by handling the manual task of moving products around.
Smart order picking carts can work in conjunction with DCX Software to completely streamline the order picking process. By leveraging artificial intelligence and machine learning, these robots can optimize picking routes and tasks in real-time.
Mobility and flexibility in the picking process are key benefits of smart carts. With smart carts, workers can retrieve items from their storage location and place them in a bin/container on the robot, minimizing walking and optimizing routes.
By choosing the right picking system, companies can increase efficiency, speed, and accuracy of picking activities. The goal is to choose a picking system that helps achieve order fulfillment goals with the minimum resources, effort, and errors.
Storage and Transport
Storage and transport are crucial components of an order picking system. They ensure that products are moved efficiently and effectively throughout the warehouse.
Pallet Jacks, Hand Trucks and Carts, and Lift Trucks are commonly used manually operated or powered vehicles to move inventory within the warehouse.
Lift Trucks are classified into seven separate categories by OSHA and are often used to load and unload vehicles, stock storage locations, and retrieve pallet loads for replenishment. They're powered by batteries, fuel cells, liquified petroleum gas, gasoline, or diesel.
Fixed Transport Systems, like conveyors, can be oriented horizontally, vertically, or on an incline, moving loads ranging from individual products to cases to full pallet loads from one area to another within an operation.
Automatic Guided Vehicles (AGVs) and Autonomous Mobile Robots (AMRs) are computer-controlled load carriers that navigate loads throughout a facility autonomously.
Explore further: Sea Transport Systems
Storage
Storage is a crucial aspect of any warehouse or distribution center, and there are many different systems to choose from. From static shelving to automated storage and retrieval systems (ASRS), each has its own unique benefits and applications.
Static shelving is a convenient and cost-effective option, often used for storing smaller, lightweight items in cartons or reusable plastic parts bins.
Pallet rack systems, on the other hand, are designed for storing palletized loads or cartons and are typically accessed with forklifts. They can be sub-divided with roller track to create flow-rack for picking of smaller items.
A-frames are self-contained and automated, with vertical storage channels dispensing small items at high speeds to totes or containers passing underneath via conveyor.
Here are some common types of ASRS:
- Horizontal Carousel Modules: save up to 60% of floor space compared to standard shelving and rack
- Vertical Carousel Modules: save up to 75% of floor space compared to static shelving and rack
- Vertical Lift Modules (VLMs): save up to 85% of floor space compared to static shelving and rack
- Unit-Load ASRS: automatically store and retrieve pallet loads from long, narrow aisles of storage rack
- Mini- and Micro-Load ASRS: handle smaller, lighter loads, typically held in trays, reusable totes or cartons
- Robotic Shuttles: handle cases, totes or trays with independently moving robotic shuttles
- Robotic Cube Storage: uses smart robots to shuffle, sort and retrieve bins and deliver them to a workstation
- Vertical Buffer Modules: a bin handling system designed for smaller applications with enclosed shelving and a movable mast
Transport
Transport can be a crucial part of your warehouse operations, and it's essential to choose the right equipment for the job. Manual options like pallet jacks and hand trucks are great for smaller loads and can be used to move non-palletized items around the warehouse.
Pallet jacks are manually operated forked vehicles that can move a single pallet load stored at floor-level. Hand trucks and carts are also useful for moving non-palletized loads, and some carts even have shelves to hold pick destinations.
Check this out: Pallet Roller Conveyor
Lift trucks, on the other hand, are powered industrial trucks that can move palletized loads. They come in various configurations and can be used for a range of indoor and outdoor load handling applications.
Fixed transport systems like conveyors can be oriented horizontally, vertically, or on an incline and are great for moving loads from one area to another within an operation. They can be used for tasks like transferring pick totes between pick zones or transporting completed picks to consolidation and packaging.
Automatic guided vehicles (AGVs) and autonomous mobile robots (AMRs) are also worth considering. AGVs are computer-controlled, wheeled load carriers that can navigate loads throughout a facility autonomously. They can be used to follow a picker who places picks onto a pallet transported by the AGV.
AMRs are smaller than AGVs and can transport smaller loads throughout a facility autonomously. They can be used to transport static shelving holding inventory from storage locations to pickers, or to transport picked items from one location to another.
Here are some common transportation equipment options:
- Pallet jacks: manually operated forked vehicles for moving single pallet loads
- Hand trucks and carts: manually pushed or towed units for moving non-palletized loads
- Lift trucks: powered industrial trucks for moving palletized loads
- Conveyors: fixed transport systems for moving loads from one area to another
- AGVs: computer-controlled, wheeled load carriers for navigating loads throughout a facility
- AMRs: computer-controlled, smaller load carriers for transporting smaller loads
Pick Indicators and Process Creation
Pick indicators are a crucial part of creating an efficient order picking system. They help operators quickly and accurately locate required items, directing them to a specific location and providing information for the task to be completed.
By using paperless pick indicator systems, operators can work hands-free, resulting in extremely high accuracy rates. This is especially beneficial for tasks that require a lot of concentration and precision.
Pick indicator systems can be combined with other elements to create a customised picking system that meets the specific needs of your operation. This can include elements like pick to light, which facilitates the creation of personalised systems adaptable to all kinds of picking, sorting and assembly operations.
Create Your Process
Creating a process that works for your business can be a challenge, but it's a crucial step in streamlining your operations.
Combining different elements is key to creating an order picking system that runs smoothly. This involves making sure each component works together seamlessly.
A-Frame picking systems are a great example of how different elements can come together to create an efficient process. They combine storage, automated picking, and conveying in one machine.
Personalised systems can be created using pick to light technology, which is adaptable to various picking, sorting, and assembly operations. This means you can tailor your system to meet your specific needs.
Continuous tweaking is essential to maintaining efficiency in your order picking system. This involves regularly reviewing and adjusting your process to ensure it's still working effectively.
Pick Indicator
Pick indicators are a crucial part of efficient warehouse operations. They help operators quickly and accurately locate required items, directing them to a specific location and providing information for the task to be completed.
Pick indicators are paperless and allow operators to work hands-free, resulting in extremely high accuracy rates. This leads to reduced training time and faster picking speeds.
There are several types of pick indicator systems, including Light Directed, Voice Directed, and Vision Directed with AR Glasses. These systems use various technologies to guide operators through the picking process.
Light Directed systems use a series of modules with colored lights and alphanumeric displays to direct operators to a storage location. They can also be used to direct put tasks, creating a Put to Light system.
Voice Directed systems consist of a wearable headset that tells the operator what item to pick and how many. The operator confirms the pick by speaking back into the headset.
Vision Directed systems use wearable smart glasses to guide operators through the picking process, displaying information such as production location, pick quantity, and put placement.
Here are some key benefits of using pick-to-light systems:
- Increases productivity and accuracy
- Reduces costs throughout all stages of the order filling process
- Has a very low learning curve, making it easy for new and seasonal employees to learn
Pick-to-light systems are one of the most productive order fulfillment solutions, making them a popular choice for modern warehouses.
Frequently Asked Questions
What are the different types of order pickers?
Order pickers are also known as cherry pickers, stock pickers, order selectors, or warehouse selectors. These versatile machines help workers reach high shelves with ease.
Is order picking a hard job?
Order picking can be physically demanding due to the need to move around a warehouse and lift items. It requires operating equipment safely and efficiently, which can be challenging.
What are automated picking systems?
Automated picking systems use voice, light, or person-to-goods technologies to streamline order picking and reduce errors. These efficient solutions can be easily integrated with existing material handling equipment.
Sources
- https://6river.com/types-of-warehouse-order-picking-systems/
- https://modula.us/solutions/picking-solutions/
- https://www.mmci-automation.com/order-picking.html
- https://www.ulmahandling.com/en/automated-intralogistics/solution-picking-system
- https://us.blog.kardex-remstar.com/order-picking-system-technologies
Featured Images: pexels.com