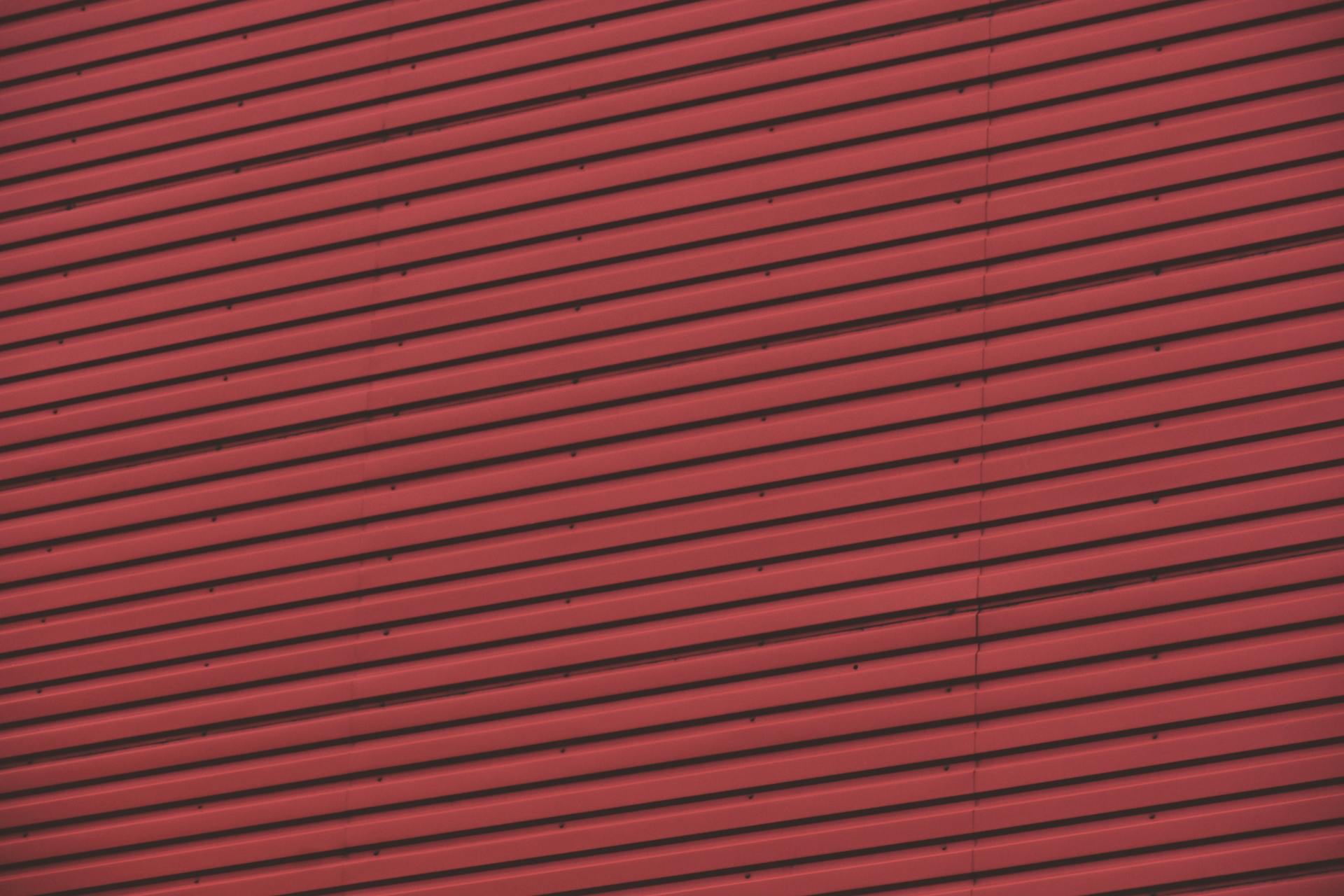
A corrugated board machine is a complex piece of equipment that requires a solid understanding of its features and specifications to operate effectively.
The machine's production capacity ranges from 100 to 200 tons per day, depending on the model and manufacturer.
Corrugated board machines can be categorized into three main types: single-facer, double-facer, and triple-facer.
A single-facer machine produces a single layer of corrugated board, while a double-facer machine produces two layers, and a triple-facer machine produces three layers.
The machine's speed can vary from 100 to 500 meters per minute, depending on the model and production requirements.
Take a look at this: Single Wall Corrugated Board
General Information
The corrugated board machine is a complex piece of equipment, but let's break it down to its basics. The total length of the machine is 68 meters.
This machine is designed for high-speed production, with a total power consumption of 150KW. It's a beast of a machine, but it's also very efficient.
The corrugated board machine has a unique design feature - it uses a shaftless holder with double arms for up and down movement. This allows for smoother and more precise operation.
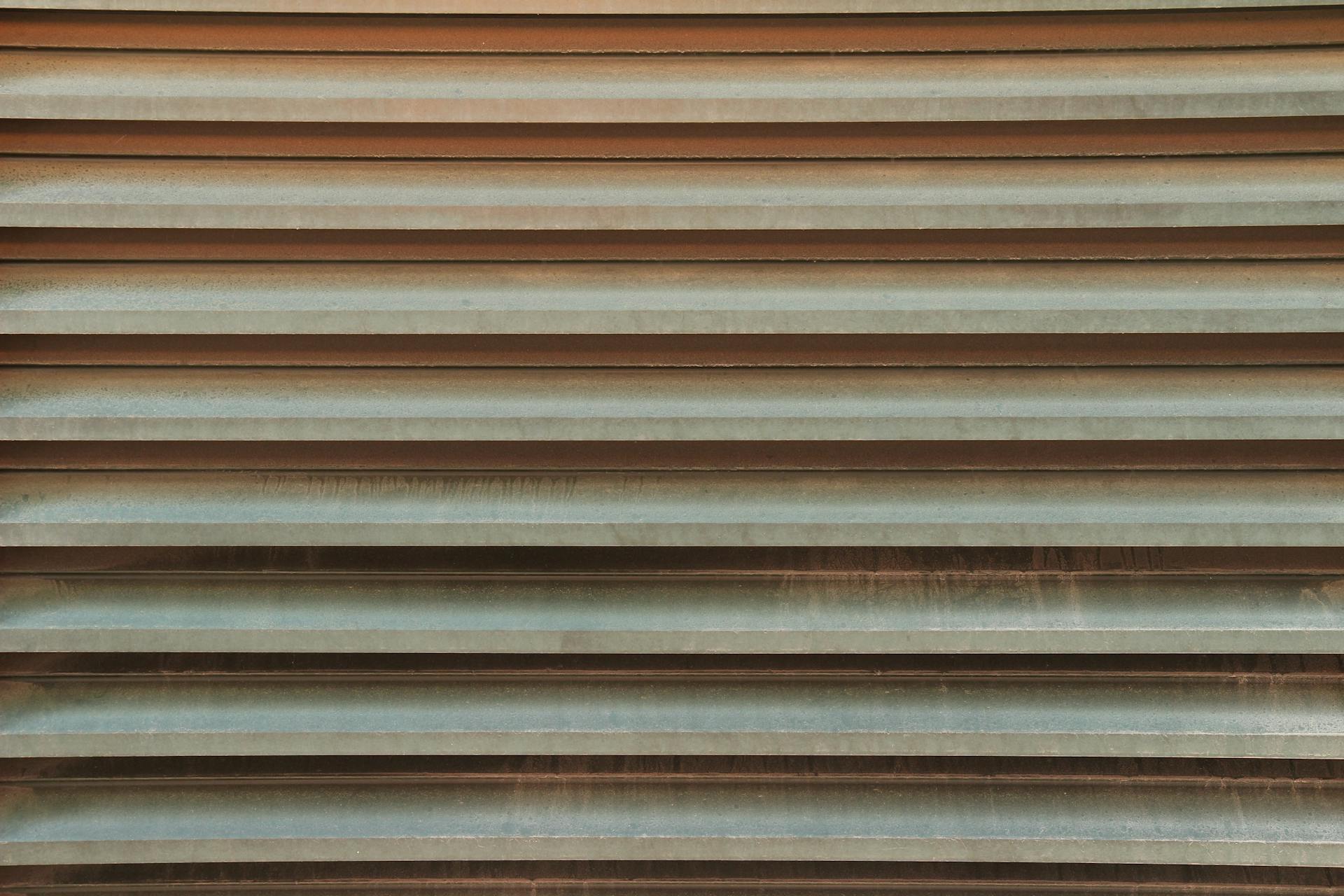
Here are some key specifications of the machine's various components:
- Laminator: uses an electromagnetic adjusting motor
- Two roller gluer: uses glossy paper in the bottom two layers of adhesive roller guide
- Dryer: 10 meters long, with 14 pieces of heating board, and a pneumatic device that separates automatically when power is off
- Molding Part: includes 27 pairs of molding shaft
- Slitter: allows for common knife or thin knife selection, with highly automatic and easy operation
- Cutting machine: computer-controlled, with four optional means for customers to choose
- Boiler: self-contained, with coal consumption of 120 kg/hr
The hydraulic mill roll stand has a double rotary shaft structure with four arms, allowing for simultaneous loading and unloading of paper mill rolls. It's also equipped with twin-stage springiness chucks and a ventilating disc-type pneumatic brake system.
Corrugator Specifications
Corrugator specifications can vary significantly depending on the manufacturer and model. The maximum speed of a corrugator can range from 380m per minute to 450m per minute, as seen in the SH-400 and H-350 models.
The maximum paper width of a corrugator can also vary, with some models capable of handling widths of up to 2,800mm (110.24"). The SH-400 and H-350 models both have a maximum paper width of 2,800mm, while the H-350 can also handle widths of 2,200mm (86.61").
Here are some key specifications for different corrugator models:
Specifications and designs are subject to change without prior notice, so it's essential to verify the specifications with the manufacturer before making a purchase.
Main Specifications
The main specifications of a corrugator are crucial to understand its capabilities and limitations. The maximum machine speed can range from 380m per minute to 450m per minute, depending on the model.
A key consideration is the machine width, which can be 2,500mm or 2,800mm. The standard specifications of a corrugator can vary, but some models come with a preheat drum standard diameter of 910mm or 500mm.
The preheating drum optional diameter can also vary, with some models offering 750mm or 1,100mm options. The overall length of the machinery can range from approximately 115m to 130m.
Here's a summary of the main specifications:
The specifications and designs of these machines are subject to change without prior notice, so it's essential to check with the manufacturer for the most up-to-date information.
63N
The 63N Mill Roll Stand is a game-changer for operators who need to change paper rolls efficiently. It reduces operator work and makes it easier to change paper rolls.
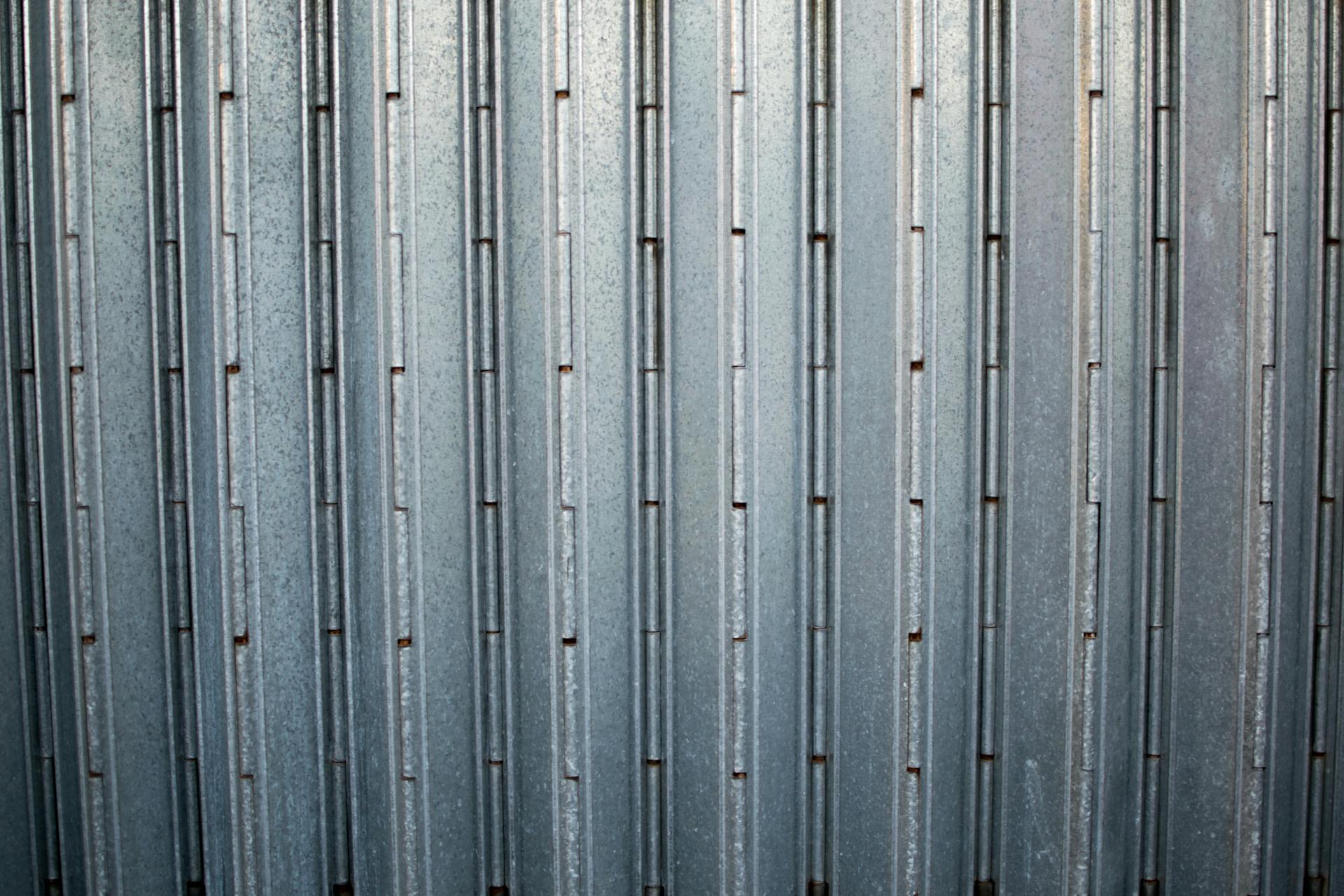
The 63N Mill Roll Stand significantly increases arm opening/closing & lifting speed and shortens the cycle time of paper roll change. This is a huge time-saver for anyone who's had to deal with cumbersome roll changes.
The maximum paper diameter that the 63N Mill Roll Stand can handle is 1,524mm (60.00"). This is impressive, and it means you can work with large paper rolls without any issues.
Here are the standard specifications for the 63N Mill Roll Stand, including its machine width and minimum paper diameter:
Flex
The FLEX Line from BHS Corrugated is the most automated and end-to-end digital corrugator line available. It's perfect for corrugated box plants that need to produce a wide range of products with high quality and consistency.
You can process all customer orders with outstanding quality using the FLEX Line, which supports flutes from G to AAA, corrugated board grammages from 150g/m² to 3,000g/m², and a wide variety of papers from 40g/m² to 440g/m². This flexibility is a huge advantage in today's market.
Take a look at this: Corrugated Paperboard Production Line
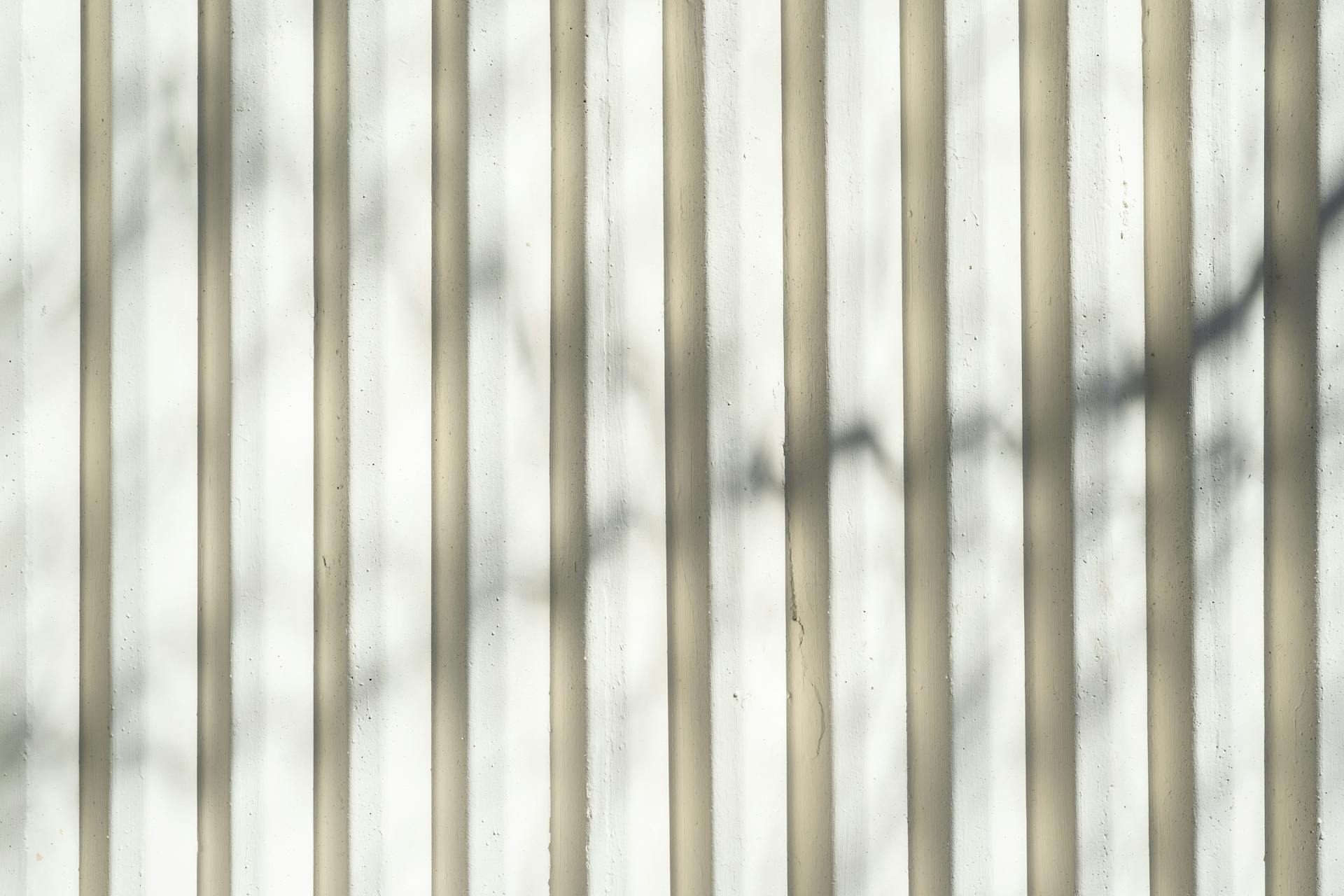
The FLEX Line also allows for smooth integration of BHS Jetliner digital print and autonomous iMotion intralogistics. This means you can streamline your production process, reduce waste, and minimize your carbon footprint.
Here's a quick rundown of the FLEX Line's key features:
The FLEX Line is designed to keep your production always adaptable, whether it's a broad mix of orders, new market trends, or rapid digital transformation.
Value S
The VALUE S Line from BHS Corrugated is a game-changer for corrugated board production. It's designed for customers who receive a lot of short orders, requiring frequent format changes.
This line is perfect for double knife corrugator markets, where short orders are the norm. It's also suitable for customers who want to add corrugated board production to their existing value chain.
One of the key features of the VALUE S Line is its ability to maintain constant speed during frequent format changes. This results in simple operation and consistently high-quality corrugated board.
A fresh viewpoint: Corrugated Board Production
The VALUE S Line is also cost-effective, with lower trim loss and reduced logistics expenses within the factory.
Here are some key specifications of the VALUE S Line:
The VALUE S Line is a reliable solution for single-knife markets, offering high-quality corrugated board production with minimal downtime.
Machine Types
There are several types of corrugated board machines, each designed to produce a specific type of corrugated board.
The most common type is the single-facer, which produces a single layer of corrugated board.
The double-facer, on the other hand, produces a double-layered corrugated board with a liner on both sides.
Worth a look: Single Face Corrugated Board
DE245/DE248
The DE245/DE248 is a Double Down Stacker dedicated for Mitsubishi corrugating machine, supplied in collaboration with NE Engineering, Italy. This machine is designed to provide excellent sheet stack quality.
One of the unique features of the DE245/DE248 is the "PIN head" and "Squaring Plates" design. These features work together to achieve excellent sheet stack quality.
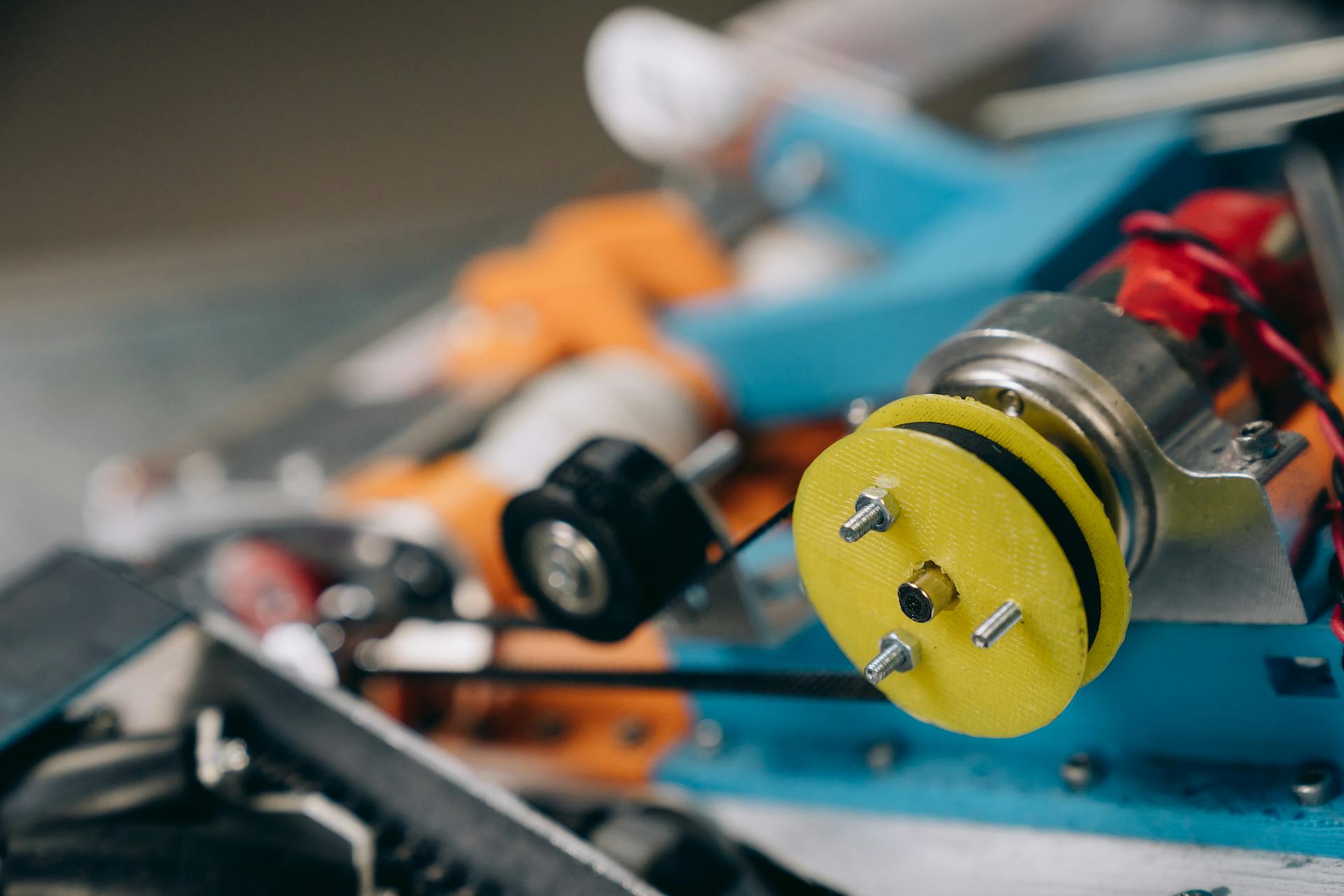
The DE245 and DE248 models have different maximum machine speeds: 400mm per minute for the DE245, and no specified maximum speed for the DE248.
The machine widths for the DE245 and DE248 are 2,500mm (98.43") and 2,800mm (110.24") respectively.
The DE245 and DE248 have different maximum sheet stacking heights: 1,800mm (70.87") for the first bay of the DE245, and 2,200mm (86.61") for the second bay of the DE245.
Here's a summary of the machine specifications for the DE245 and DE248:
Sh-400 (Double Cut-off Type)
The Sh-400 (Double Cut-off Type) is a heavy-duty machine designed for efficient paperboard production. It features a unique double facer design that allows for high-speed production of double-cut paperboard.
The machine's heating board is made of container board, meeting the first-class national pressure vessel standard, and comes with a pressure vessel certificate and inspection certificate. This ensures the board can withstand the high temperatures and pressures involved in the production process.
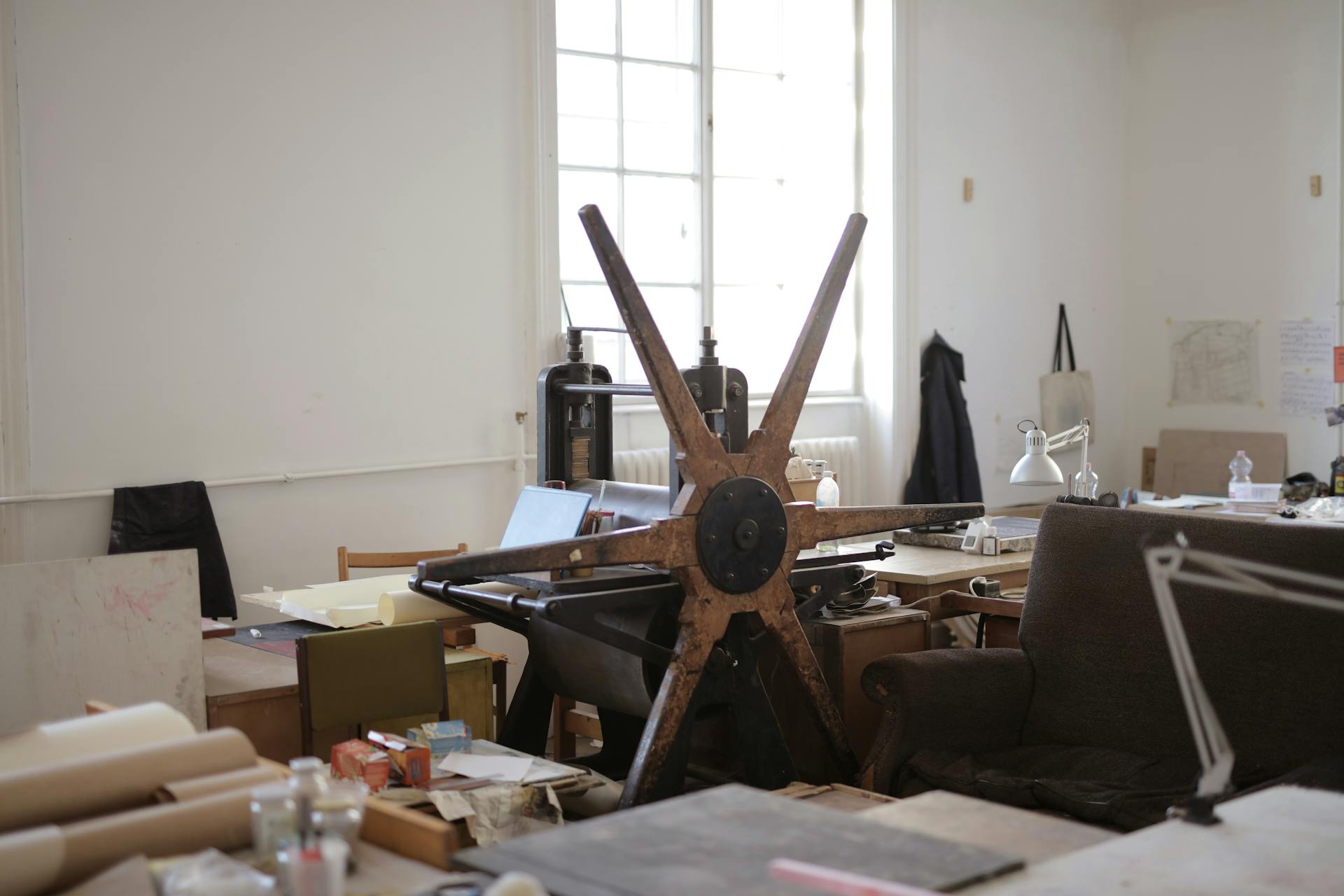
The Sh-400's heating board is equipped with intensive heavy press shoes and pneumatic thermal shoe type pressure rolls. This design allows for precise temperature control and even heat distribution.
The machine's transmission belt system features automatic adjustment for left-right correction, with two sets of tension systems: one manual and one pneumatic. This ensures smooth and consistent production.
The Sh-400's heat-conducting pipes are designed to control temperature in different sections, with digital displays to monitor temperature levels. This allows for precise temperature control and optimization.
Here's a summary of the Sh-400's key features:
The Sh-400's driving parts are designed for high-speed operation, with an independent speed change box and oil-immersed lubrication. The main driving motor is a frequency conversion energy-saving motor, providing low speed and big torque, with a wide speed-adjusting range.
The machine's surface is designed for smooth output, with wear-resisting rubber attached to the driving roll and a herringbone structure to prevent paperboard damage.
Fingerless Single Facer
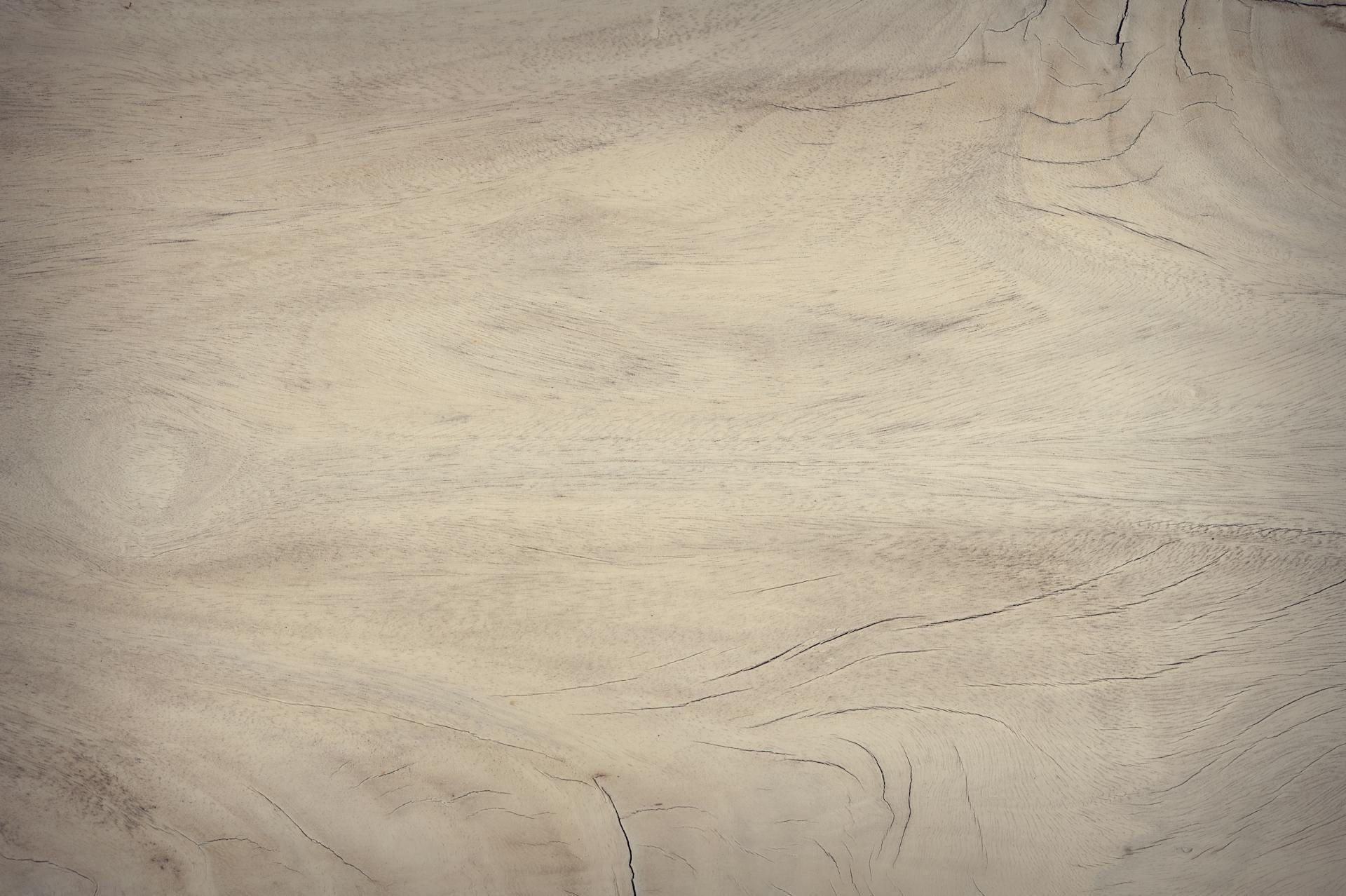
The fingerless single facer is a type of machine used in the paper production process. It's designed to efficiently produce corrugated cardboard.
This machine features a fingerless vacuum suction system, which helps to feed paper into the machine. The system includes a high-pressure draught fan and a silencer to minimize noise.
The engine base and wall plate of the fingerless single facer are made of iron casting, with a wall plate thickness of 150mm. This provides a sturdy foundation for the machine.
The main corrugated roll has a diameter of 320mm and is made of 48CrMo alloy steel. After hardening and tempering, the roll undergoes various processes such as NC grinding and mid-frequency quenching.
Here are the key specifications of the fingerless single facer:
The pressure roll has a diameter of 340mm and is made of 45# medium carbon steel. The glue wall plates adopt a sliding structure, with a diameter of 242mm for the applicator glue roll.
Classic

The CLASSIC Line from BHS Corrugated is designed for optimal local market coverage. It offers a wide variety of packaging solutions, including microflutes and small orders.
This line gives you the flexibility you need to meet any customer's requirements. It's a reliable corrugator line with cutting-edge, intuitive technology.
Components and Features
A corrugated board machine is made up of several key components that work together to produce high-quality corrugated board. The machine consists of a corrugator, which is the heart of the machine, where the paper pulp is converted into corrugated fluting.
The corrugator is equipped with a series of rollers that shape and compress the paper pulp into a wavy pattern. This wavy pattern is what gives corrugated board its strength and durability.
The machine also includes a creaser, which is responsible for creating the folds in the corrugated board. The creaser is typically a heated roller that applies pressure to the board to create a crisp fold.
Suggestion: Paper Pulp Molding Machine
Double Facer
The Double Facer is a crucial component in the paperboard production process. It's designed to apply a layer of heat to the paperboard to improve its smoothness and quality.
The Double Facer's heating board is made of container board, meeting the first-class national pressure vessel standard. It's also equipped with a pressure vessel certificate and inspection certificate for added assurance.
The heating board is divided into 18 PCS, each with a width of 600mm. The length of the cooling case-hardened parts is a significant 6300mm.
The Double Facer features a unique structure of intensive heavy press shoes, which helps to distribute the heat evenly. The up and down pressure rolls are equipped with pneumatic thermal shoe type structure for improved performance.
The machine's temperature control system is precise, with heat-conducting pipes that allow for digital temperature display in different sections. This ensures that the paperboard is heated to the optimal temperature.
Broaden your view: Vacuum Heat Sealing Machine
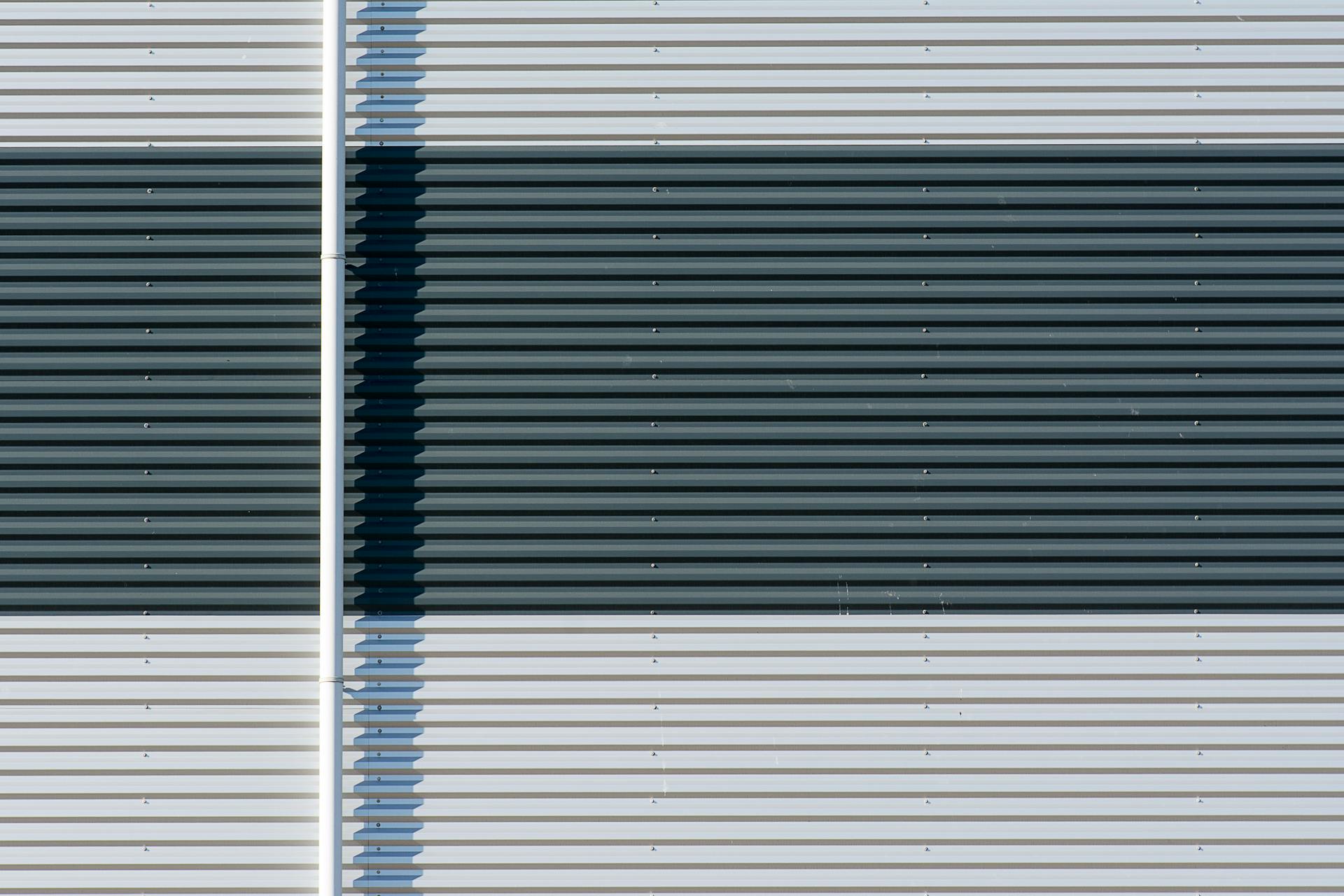
The driving roll is attached with wear-resisting rubber, forming a herringbone structure that helps to output paperboard smoothly. The driving parts are designed for independent speed change, with a wheel gear made of ZG-500# cast steel and oil-immersed lubrication for reduced wear and tear.
The electrical components are sourced from global famous brands, ensuring stable and reliable operation. The main driving motor is a frequency conversion energy-saving motor, which provides low speed and big torque, wide speed-adjusting range, and easy maintenance.
Here's a quick rundown of the Double Facer's key specifications:
The Double Facer is designed to work efficiently, with a temperature range of 160-200 C and steam pressure of 0.8-1.3 Mpa. The pneumatic pressure is between 0.6-0.9 Mpa, ensuring optimal performance.
Overall, the Double Facer is a critical component in the paperboard production process, providing precise heat control and smooth output.
Cardboard Feeding
Cardboard feeding is an essential component of many printing and packaging machines. You can load 20-50 sheets of cardboard at a time, with thicknesses ranging from 2 to 12 mm.
A continuous cardboard feeding system is a game-changer, thanks to its vacuum pump that makes cardboard feeding more accurate.
Slitter Scorer
The slitter scorer is an essential component in the production of corrugated cardboard. It's responsible for cutting and creasing the cardboard to the desired shape and size.
There are several types of slitter scorers, including horizontal slotting and scoring, up and down slitter scorer, and vertical slitting.
Here are some key features of slitter scorers:
- Creasing wheels with a minimum creasing distance of 20mm
- Automatic go up and down slitter scorer with electric adjusting blade distance
- Synchronous belt transmission for high accuracy
- Pneumatic sharpening for automatic and manual sharpening
- Scoring speed of 150m/min
- Max slitting width of 2200mm
- Max slitting thickness of 11mm
The slitter scorer is equipped with various features to ensure efficient and accurate cutting and creasing. For example, the up and down slitter scorer has an electric axial displacement device that allows for effective cooperation of paper offset. The machine also has a transmission system that ensures high accuracy and a pneumatic sharpening system that allows for automatic and manual sharpening.
Here's a summary of the key features of slitter scorers:
Steady S
The Steady S Line is designed for customers who receive very short orders, requiring frequent format changes.
This line is perfect for those with moderate output volumes, as it maintains constant speed despite the frequent changes.
The Steady S Line from BHS Corrugated is built for simplicity and high-quality output.
It's thoroughly simple to operate, which means less stress for you and your team.
Consistently high-quality corrugated board is the result of this line's design.
Printing
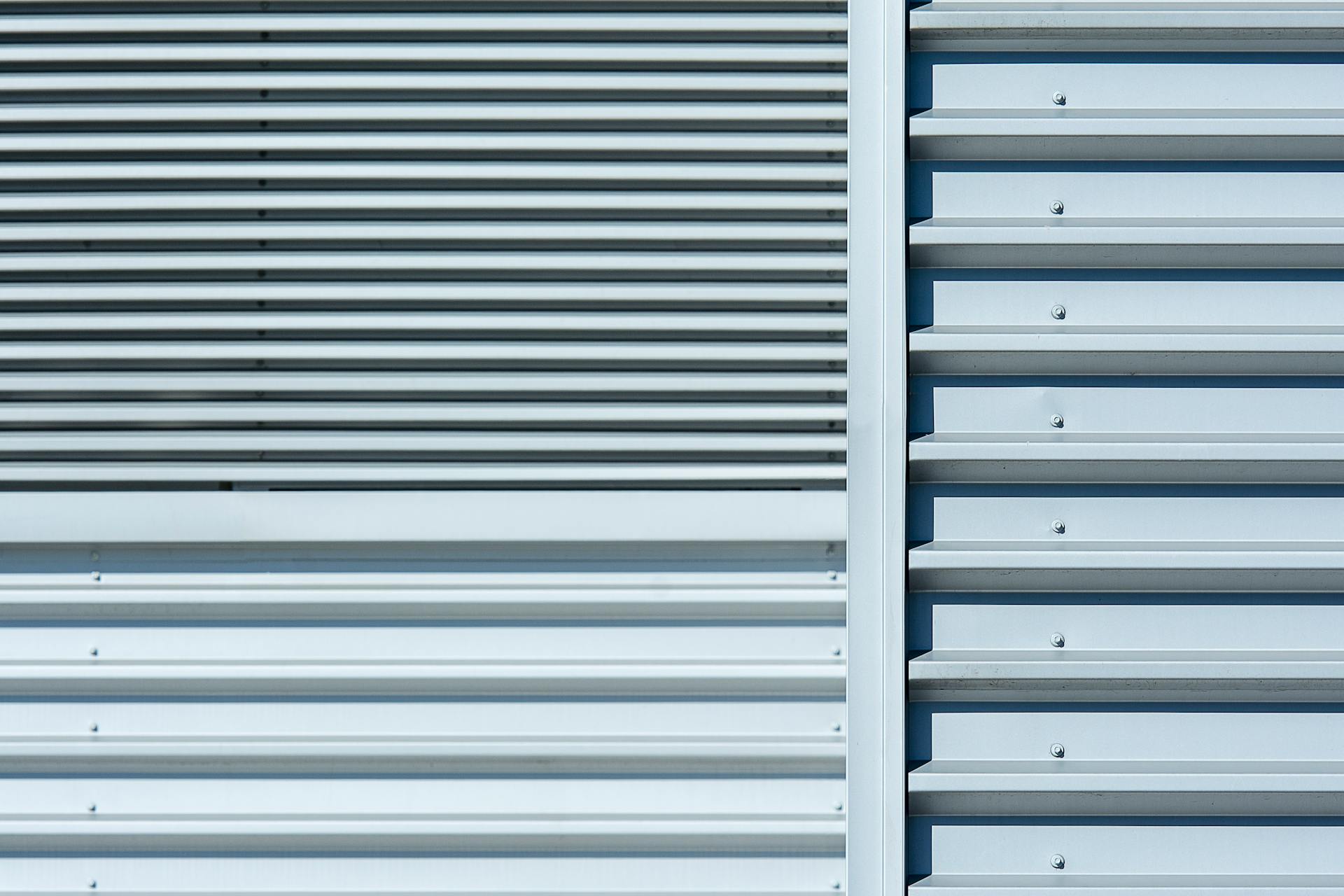
Printing on corrugated sheets is a common practice that allows for various types of packaging to be customized.
The flexographic print process is often used for printing on corrugated, making it a popular choice for many manufacturers.
Printing can be done in-line or off-line, giving businesses flexibility in their production processes.
Digital direct print is also entering the market, offering new possibilities for packaging design and customization.
Broaden your view: Flexographic Printing Press
Die-Cutting, Folding, Gluing
Die-cutting is a process where the board is cut and creased with a specifically designed form to create the unique packaging shape required by the customer.
Most corrugated containers are manufactured on Flexo-Folder-Gluer (FFG) machines, which combine printing, die-cutting, folding, and gluing in one process.
Die-cutting can also be performed on separate machines, allowing for more flexibility in the manufacturing process.
The FFG machines are a common sight in corrugated container manufacturing, making it possible to produce a wide range of packaging shapes and sizes.
Die-cutting is a crucial step in creating the unique shape of a packaging container, and it's often done in combination with folding and gluing to create a finished product.
You might enjoy: Corrugated Board Cutting
Corrugator Solutions
Corrugator Solutions offer a range of options for corrugated board machine manufacturers. They can be tailored to meet specific production needs, with individual machines, complete lines, and connected process and control systems available.
The SPEED Line from BHS Corrugated is designed for high-volume production, capable of achieving production volumes of up to 56,000 m²/hour.
Corrugator Solutions can be categorized into three main types: Individual Machines, Corrugator Lines, and Corrugated 4.0.
Corrugator Solutions
Corrugator Solutions offer a range of options for your corrugator needs. Our Portfolio includes individual machines, complete lines, and connected process and control systems under the topic Corrugated 4.0.
If you're looking for high-volume solutions, the Corrugator SPEED Line is a great option. It features automated end-to-end systems that can achieve production volumes of up to 56,000 m²/hour.
We also offer individual machines, which can be tailored to your specific needs. Corrugator Lines are another option, providing a complete solution for your corrugating needs.
Take a look at this: Machine Conveyor Systems
The SPEED Line is designed for transregional markets, making it a great choice for companies looking to expand their reach. Its high-volume capabilities and automated systems make it an efficient and effective solution.
Here are some key features of our Corrugator Solutions:
BHS and Agfa Enhance BHS Jetliner Series
BHS and Agfa Enhance BHS Jetliner Series by forming a strategic commercial agreement to boost the BHS Jetliner Series.
BHS Corrugated, a leading supplier in the corrugated industry, has partnered with Agfa, a global provider of inkjet solutions.
This partnership will enhance the BHS Jetliner Series, a line of single-pass inkjet print systems.
Agfa's expertise in inkjet technology will likely play a key role in this enhancement.
The BHS Jetliner Series is designed for the corrugated industry.
BHS Corrugated is the OEM of this series, indicating they have a high level of control over its development.
This agreement is a strategic move to improve the BHS Jetliner Series, likely increasing its efficiency and effectiveness.
By working together, BHS and Agfa aim to provide a more comprehensive solution for the corrugated industry.
The partnership is a testament to the growing importance of inkjet technology in the corrugated industry.
Here's an interesting read: Blister Packaging Machine Pharmaceutical Industry
Eco
The ECO Line from BHS Corrugated is a future-proof product designed for emergent markets. It's a high-quality solution for packaging products with a monthly output of 2,500 to 3,000 tons.
Manufacturers previously had limited options, choosing between a ready-made corrugator layout or assembling their own tailored corrugator from individual components. This was a time-consuming process.
The ECO Line offers a perfect blend of adaptability and individual options, making it a unique solution for each manufacturer. It's designed to meet the needs of manufacturers with varying production yields and automation requirements.
This line of corrugator solutions is perfectly adapted to a variety of market requirements, including differing production yields and automation needs. It's a tried and tested solution that saves time.
Converting of Board
The converting of board is a crucial step in creating finished packaging products. It involves transforming flat boards into usable packaging materials.
The converting process includes operations like printing, die-cutting, folding, and gluing (taping or stitching). These operations are carried out according to the customer's specifications and the type of packaging required.
The specific operations performed vary based on the type of packaging. Different types of packaging have unique requirements, and the converting process is tailored to meet these needs.
Additional operations may be performed to meet specific customer requirements.
Machine Configurations
A corrugated board machine's configuration can make or break its efficiency. The machine's configuration typically includes a corrugator, which is responsible for creating the fluted paperboard.
The corrugator is usually a complex machine with multiple components, including rolls, cutters, and glue application systems. The machine can be configured in different ways, such as single-facer or double-facer, depending on the production requirements.
A single-facer corrugator is often used for small to medium-sized production runs, while a double-facer corrugator is better suited for larger production volumes.
Standard Configuration
The standard configuration of a machine is a great place to start when understanding its capabilities. This configuration includes a paper feeding bracket.
The standard configuration typically includes two 350mm slotting knives. These knives are a crucial part of the machine's functionality.
One horizontal scoring beam is also included in the standard configuration. This beam plays a vital role in the machine's performance.
Six vertical creasing wheels are part of the standard configuration. These wheels help to create precise creases in the paper.
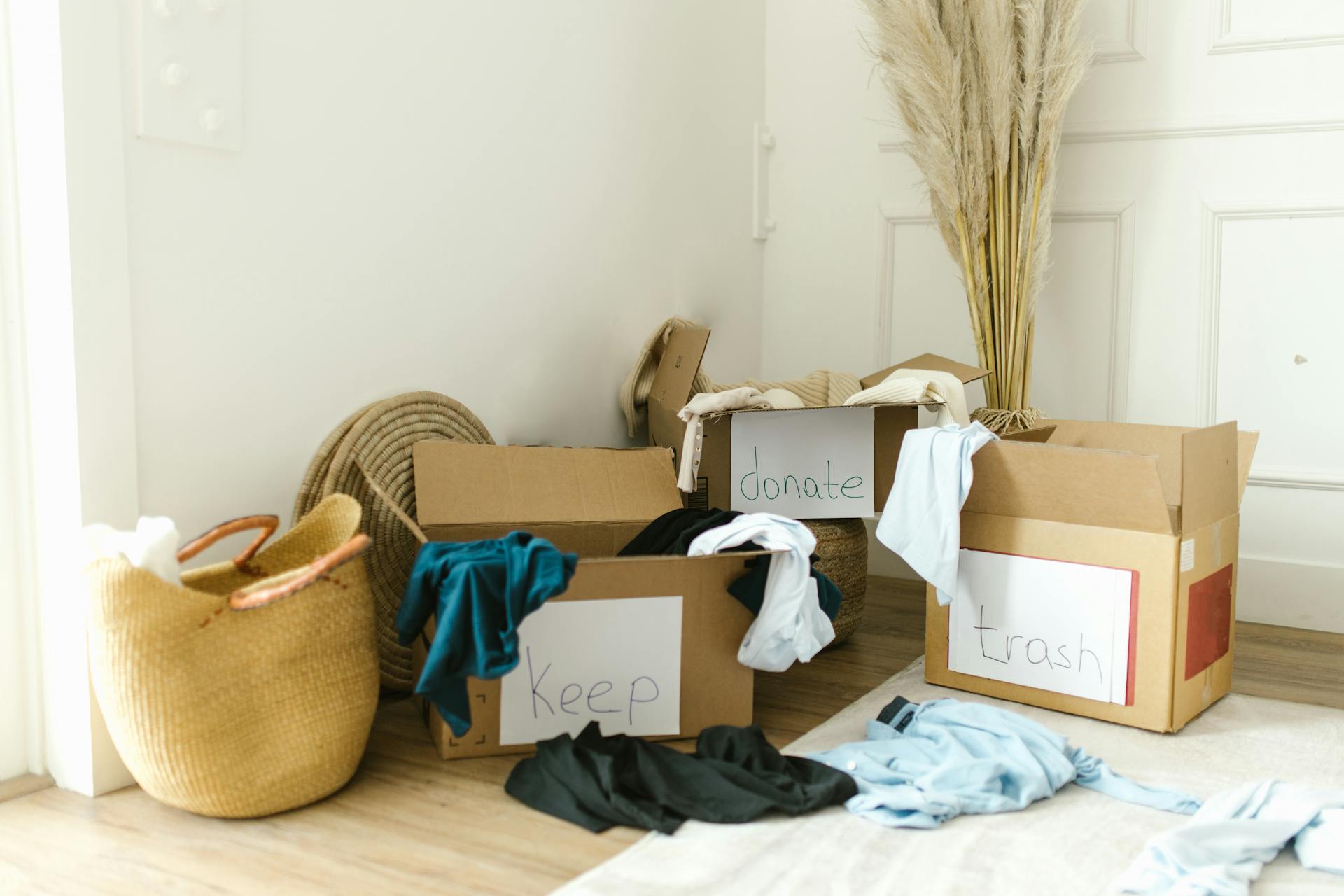
The standard configuration also includes six vertical slitting knives. These knives are used to cut the paper into precise slits.
Finally, one horizontal cutting knife is included in the standard configuration. This knife is used for making straight cuts in the paper.
Here's a quick rundown of the standard configuration:
- 1 pcs paper feeding bracket
- 2 pcs 350mm slotting knives
- 1 pcs horizontal scoring beam
- 6 pcs vertical creasing wheels
- 6 pcs vertical slitting knives
- 1 pcs horizontal cutting knife
Sixty N
The Sixty N machine configuration is a great option for those looking for efficiency and reliability. It features a Belt Press System that has been perfected over 30 years by Mitsubishi.
The Belt Press System eliminates pressure-marks on corrugated boards, ensuring a smooth finish. This is a game-changer for any corrugated board production process.
One of the standout features of the Sixty N is its adaptability. Full and semi-automatic cartridge changes are available as an option, making it easy to switch between different configurations.
Peripherally heated corrugating rolls are equipped as standard on the Sixty N, providing consistent heat and performance.
Speed
The SPEED Line from BHS Corrugated is a high-speed corrugator line that can achieve production volumes of up to 56,000 m²/hour.
Automated end-to-end systems are a key feature of this line, allowing for maximum machine availability and fast service.
This level of automation also enables cost-efficient machine configurations, which is crucial for keeping unit costs to a minimum.
You can depend on the SPEED Line to supply large orders reliably.
Applications and Uses
A corrugated board machine is a versatile tool with a wide range of applications.
The Aopack BM1800-Mini is a super cost-efficient corrugated box machine, perfect for box plants with small quantity orders.
It effectively solves the problem of scattered orders, making it a great solution for businesses with varied packaging needs.
The machine is suitable for a variety of industries, including furniture and e-commerce logistics.
Customized packaging solutions are available for box plants and end-users alike, making it a flexible option for many businesses.
The Aopack BM1800-Mini is available for a wide range of industries, including hardware accessories and more.
Intriguing read: Paper Sack Making Machine
Frequently Asked Questions
What is the cost of 42 inch corrugation machine?
The cost of a 42 inch corrugation machine is ₹ 650,000 per piece. This semi-automatic machine is available in Amritsar.
What is the price of Natraj corrugation machine?
The price of a Natraj Single Face Paper Corrugation Machine is ₹ 450,000 per piece. This is a competitive price for a high-quality corrugation machine.
What is the difference between cardboard and corrugated board?
Corrugated board has multiple layers, while cardboard has only one thin layer. This difference in construction gives corrugated board its unique strength and durability
Sources
- https://www.mhi.com/products/industry/corrugating-machine.html
- https://www.aopackmachine.com/corrugated-box-machine/
- https://www.bhs-world.com/en/corrugators/corrugator-lines
- https://northpack.en.made-in-china.com/product/HXzJQtoKRrYE/China-Automatic-Five-Layer-Corrugated-Cardboard-Sheet-Production-Line-Plant-Machine.html
- https://www.fefco.org/technical-information/production-process
Featured Images: pexels.com