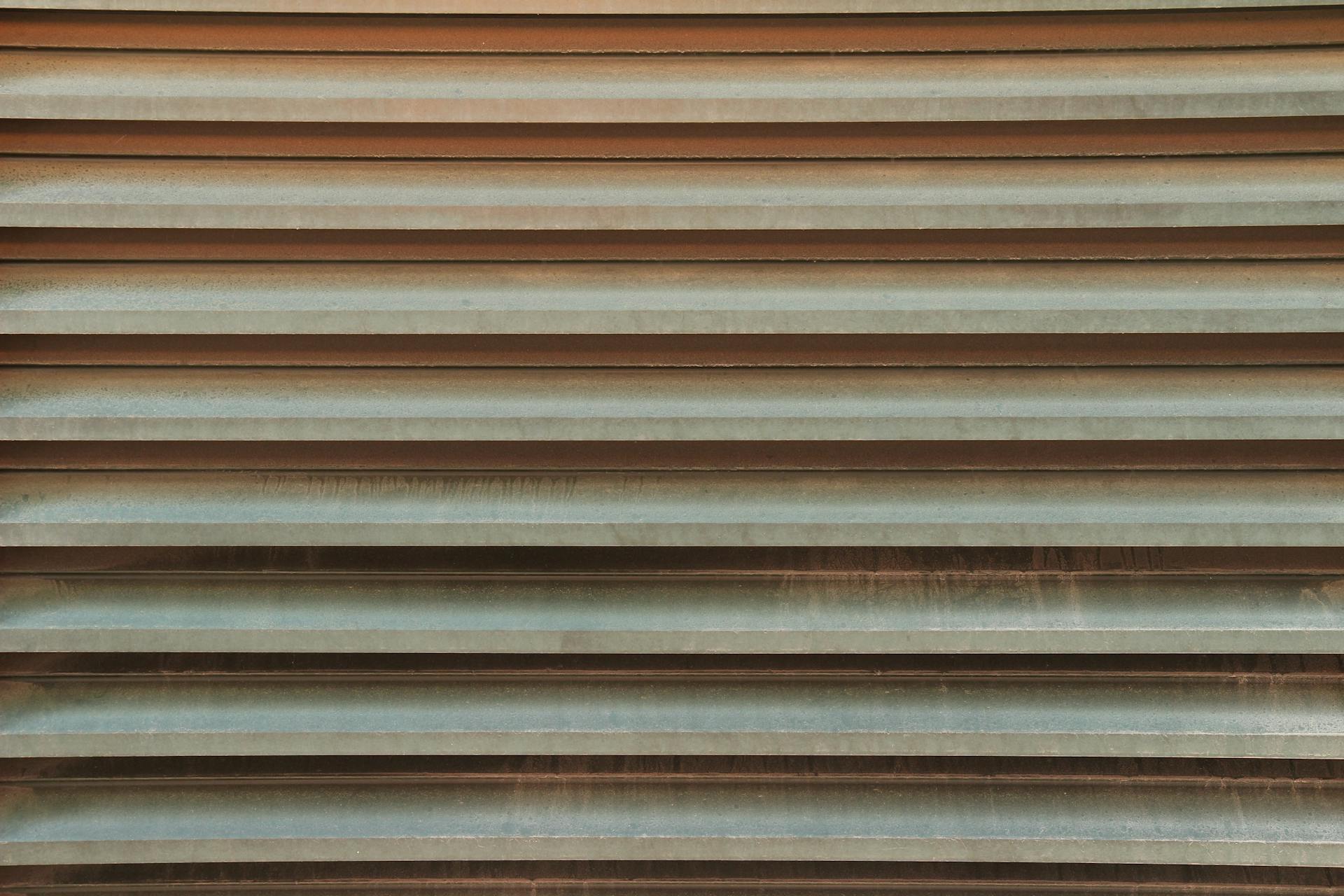
Let's start with the basics of corrugated board production. Corrugated board is made from a combination of paper pulp and fluff pulp, which are mixed together with water and other chemicals to create a pulp mixture.
The pulp mixture is then formed into a sheet using a machine called a fourdrinier. This machine uses a series of rollers to remove excess water from the pulp and flatten it out into a thin sheet.
Corrugated board production involves several stages, including pulping, forming, and cutting. The entire process is designed to be efficient and cost-effective, with the goal of producing high-quality corrugated board for a variety of applications.
The corrugating process involves passing the sheet through a series of rollers, which folds the paper into a wavy pattern. This wavy pattern is what gives corrugated board its strength and durability.
Curious to learn more? Check out: Paper Pulp Molding Machine
Introduction
Corrugated board production is a fascinating process that involves creating a sturdy and versatile material used in packaging, shipping, and construction.
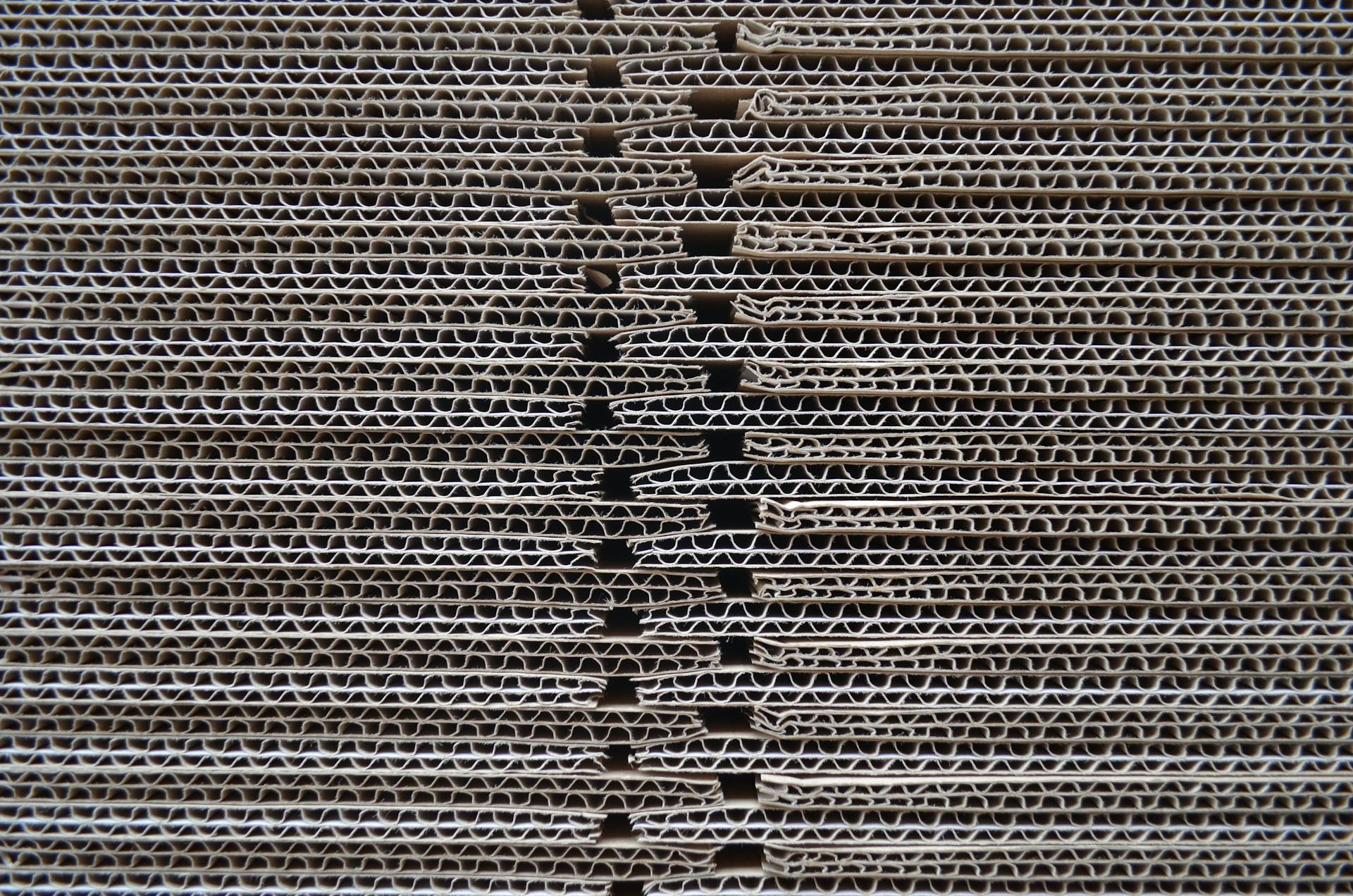
The process begins with the production of corrugated medium, which is made by passing paper pulp through a machine that creates a wavy pattern, also known as the flute.
This flute is what gives corrugated board its strength and rigidity.
The corrugated medium is then sandwiched between two layers of linerboard, which provides additional strength and protection.
In 1871, Oliver Long, an English merchant, invented the first corrugated board by gluing a wavy sheet of paper to a flat sheet of paper.
This innovation revolutionized the packaging industry and paved the way for modern corrugated board production.
Intriguing read: Ldpe Foam Sheet
Production Line Overview
A corrugated board production line is made up of several machines that work together to produce high-quality corrugated boards. These machines include a reel rack, a one-side corrugated board-forming machine, and a rotating cutting unit.
The production line can produce more than 3 layers of corrugated board simultaneously with the glue machine or veneer. This process is crucial for creating a strong and durable corrugated board.
Here's a breakdown of the key components of a 5 ply corrugated cardboard production line:
- Maximum mechanical speed: 300m/min
- Production line width: 1400~2800mm
- Positive pressure cassette type quick roll change single face corrugator
- Double motor upper and lower independent drive double-sided machine
- Equipment high stability, low noise, long life
- High physical index and high speed of cardboard
- Energy saving of equipment, reducing unit energy consumption
- Easy to operate and maintain
What is a Production Line?
A production line is a series of connected machines and processes that work together to manufacture a product, like corrugated board.
It can be divided into separate parts, such as wet and dry processes, each with its own equipment. The wet process equipment includes a roller rack, auto feed machine, pre-heater, bridge, glue, double-sided machine, etc.
These machines are used to process the corrugated board into layers, specifically 3, 5, and 7 layers. The drying equipment, on the other hand, consists of a CNC cutter, groove press, and stacking machine.
These machines help cut, indent, cross-cut, and stack the corrugated board as needed. The production line also includes ink printing rollers to apply customer graphics and die-cutting machines to remove debris.
Crease units are used to facilitate later bending and folding. The final step involves stacking and gluing the plates together to make a compact transportation unit.
Cardboard Line
A cardboard line, also known as a corrugated board production line, is a complex system that produces corrugated cardboard from raw materials. This line is composed of two separate parts: the wet and the dry process equipment.
The wet process equipment includes a roller rack, auto feed machine, pre-heater, bridge, glue, double-sided machine, and more, which work together to process the cardboard into 3, 5, and 7 layers. The drying equipment, on the other hand, includes a CNC cutter, groove press, and stacking machine, which are used for cutting, indentation, cross-cutting, and stacking the cardboard as required.
The corrugated board production line can produce various types of cardboard, including single-side and double-side corrugated board. A single-side corrugated production line typically consists of a reel rack, a one-side corrugated board-forming machine, and a rotating cutting unit. The paper is continuously manufactured and cut to the required size with a roll material and a potato or cornstarch binder.
Here's an interesting read: Single Wall Corrugated Board
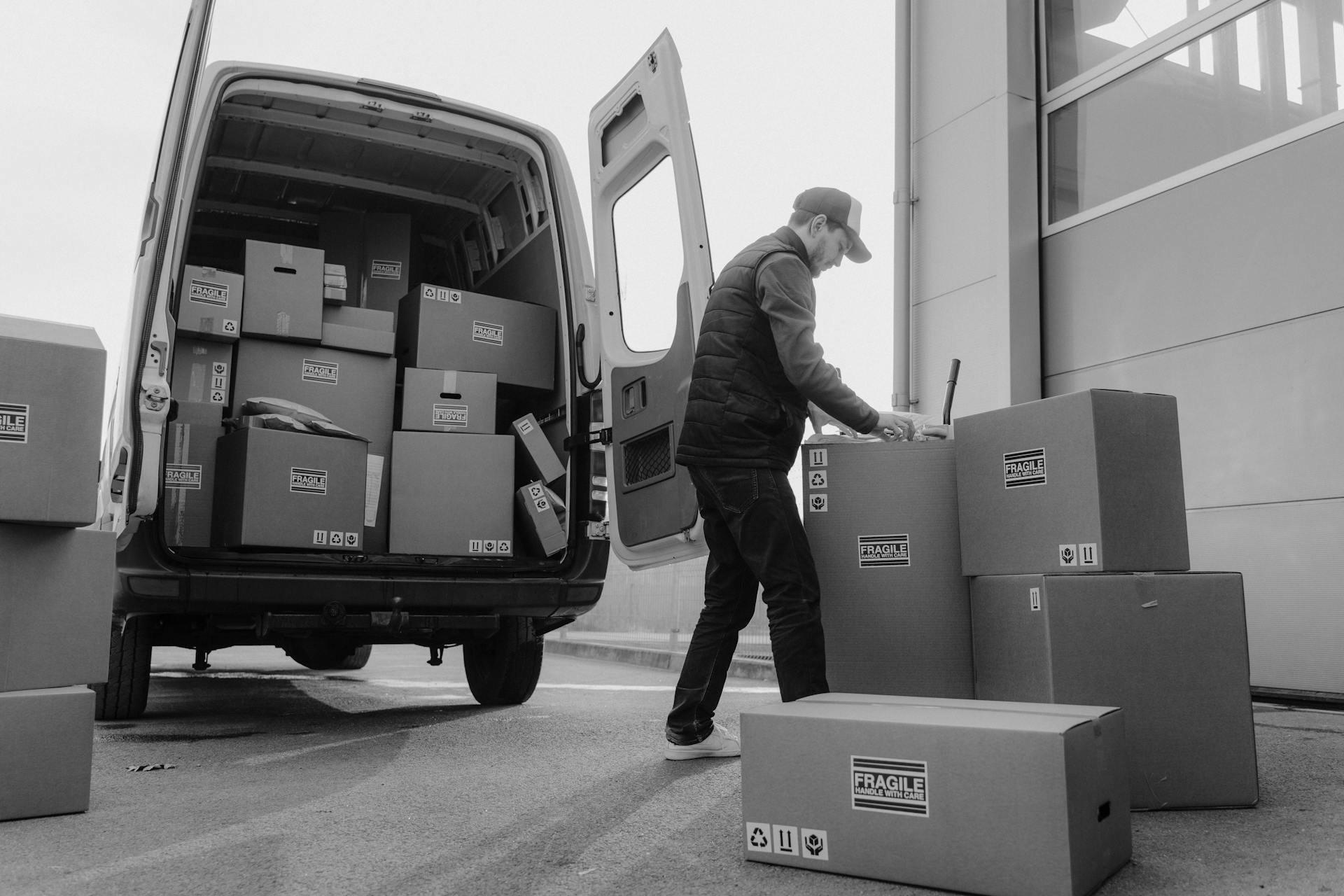
Here are some key features of a 5 Ply Corrugated Cardboard Production Line:
A corrugated board production line can produce cardboard with various layers, including 2, 3, 5, 7, and 9 ply. The line can also be equipped with various machines, such as die-cutting machines, crease units, and ink printing rollers, to produce cardboard with specific designs and features.
Curious to learn more? Check out: Corrugated Paperboard Production Line
Production Line Components
A production line for corrugated board production typically consists of several key components. These include the paper machine, the corrugator, and the finishing line.
The paper machine produces the base paper that will be used to make the corrugated board. This machine can produce up to 2,000 metric tons of paper per day.
The corrugator is responsible for fluting the paper to create the corrugated layer. The corrugator can produce up to 1,000 tons of corrugated board per day.
The finishing line is where the corrugated board is cut to size and prepared for packaging. This line can produce up to 5,000 boxes per hour.
Base Papers
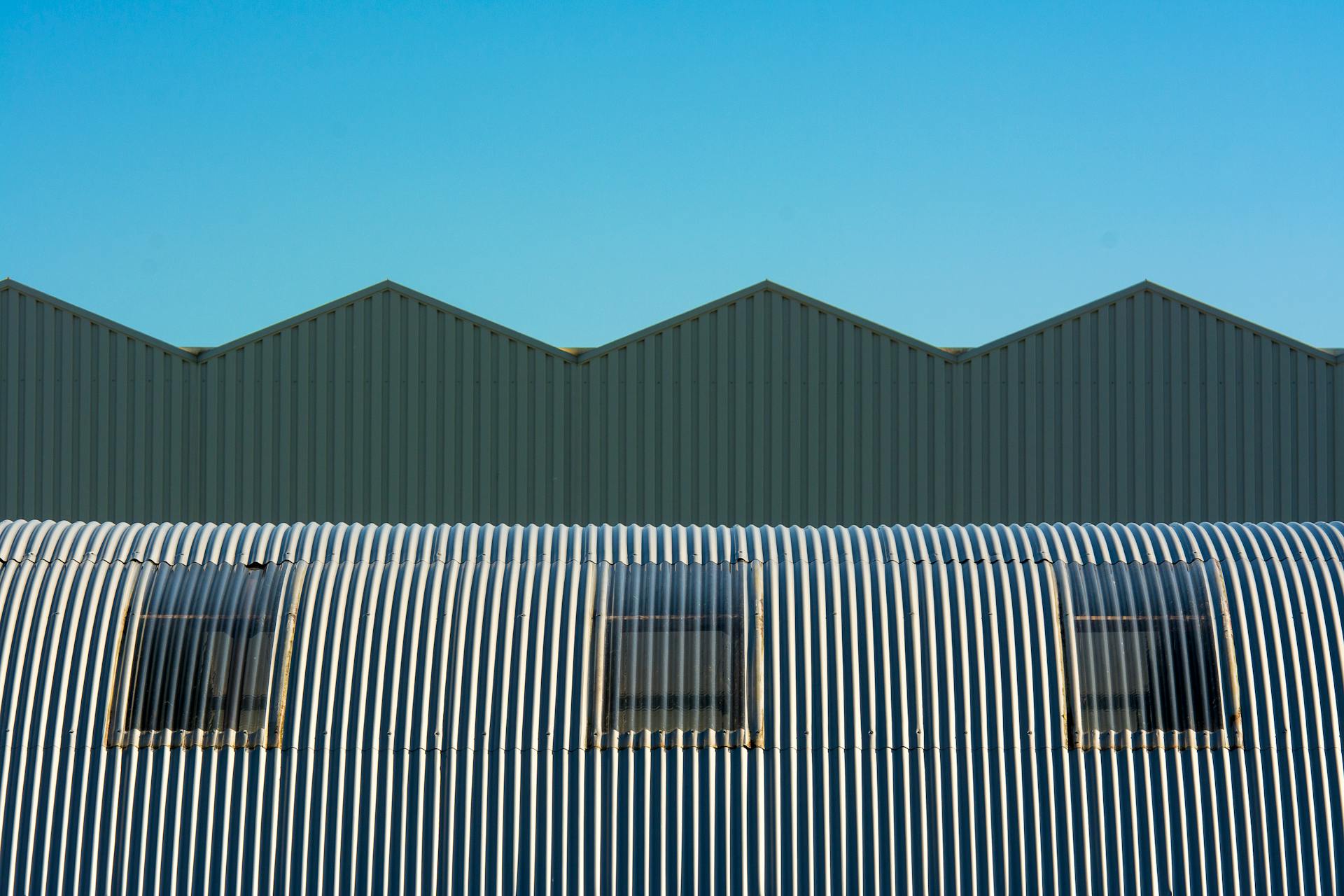
Base Papers are a crucial component in the production line, serving as the foundation for various products such as paper bags, packaging materials, and even banknotes.
These papers are made from wood pulp or recycled fibers, with the wood pulp being sourced from sustainably managed forests or plantations.
The production process involves refining the wood pulp to create a pulp, which is then mixed with water and other chemicals to create a uniform consistency.
The pulp is then formed into a paper sheet using a machine called a fourdrinier, which uses a series of rollers to flatten and dry the paper.
The type of pulp used can affect the final product's strength, durability, and even its ability to withstand moisture.
For example, a paper bag made from a high-strength pulp can hold more weight than one made from a weaker pulp.
Equipment on the Line
A corrugated board production line typically consists of a reel rack, a one-side corrugated board-forming machine, and a rotating cutting unit. This setup allows for continuous manufacturing and cutting of paper to the required size.
For another approach, see: Corrugated Board Cutting
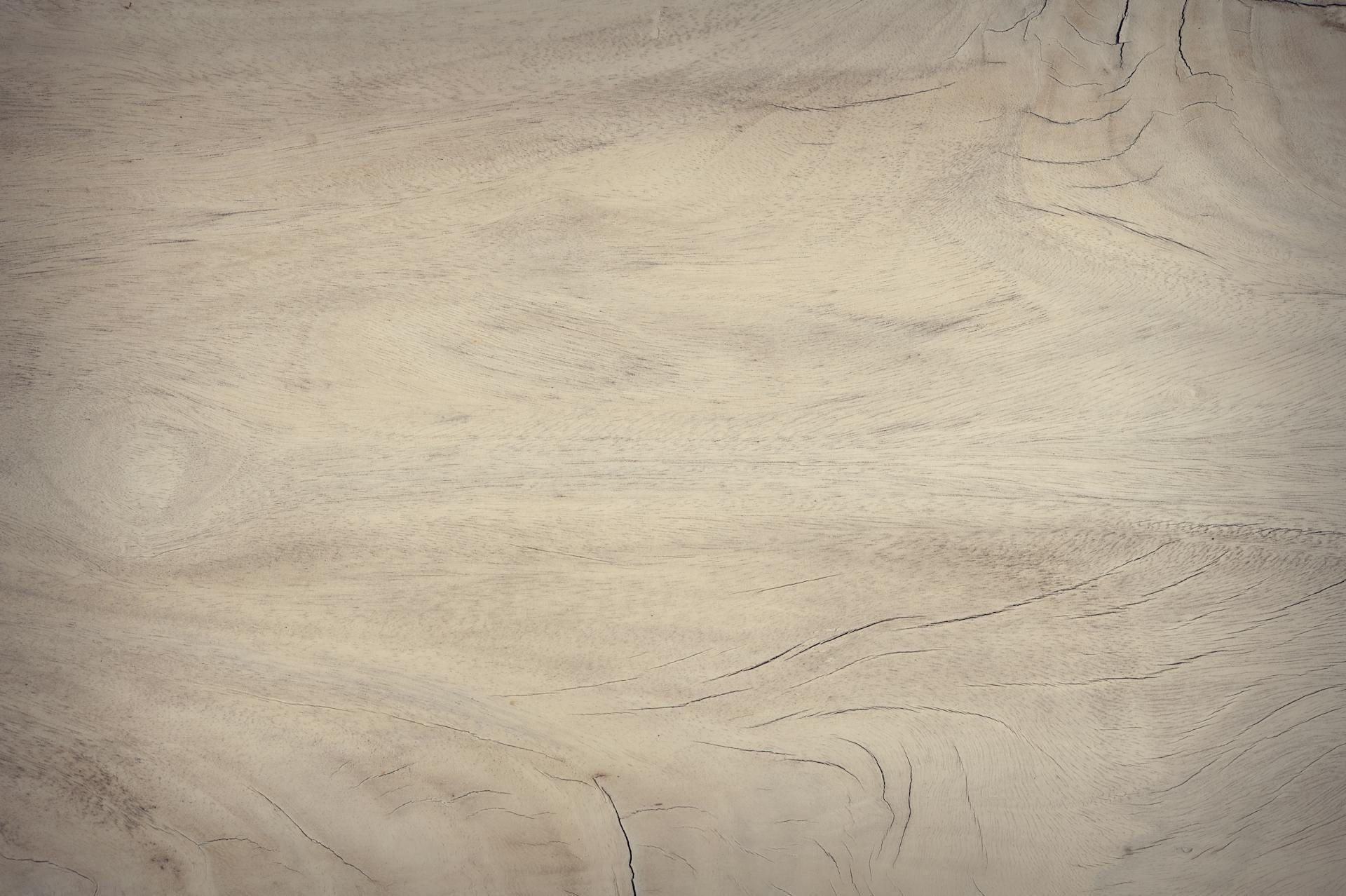
The production line width can vary, ranging from 1400 to 2800mm, depending on the specific machine configuration. This flexibility is beneficial for producing corrugated boards of different sizes.
The maximum mechanical speed of a complete corrugating board production line can reach up to 300m/min. This high speed enables efficient production and meets the demands of modern manufacturing.
A 5-Ply Corrugated Cardboard Production Line includes various machines, such as a positive pressure cassette type quick roll change single face corrugator and a double motor upper and lower independent drive double-sided machine. These machines work together to produce high-quality corrugated boards.
The equipment on a corrugated board production line is designed with energy efficiency in mind, reducing unit energy consumption and minimizing environmental impact.
Here are some of the key machines found on a 5-Ply Corrugated Cardboard Production Line:
Wet Device Configuration
The wet device configuration is a crucial part of the corrugated board production line, responsible for processing the base paper, glue, and steam to produce high-quality corrugated board.
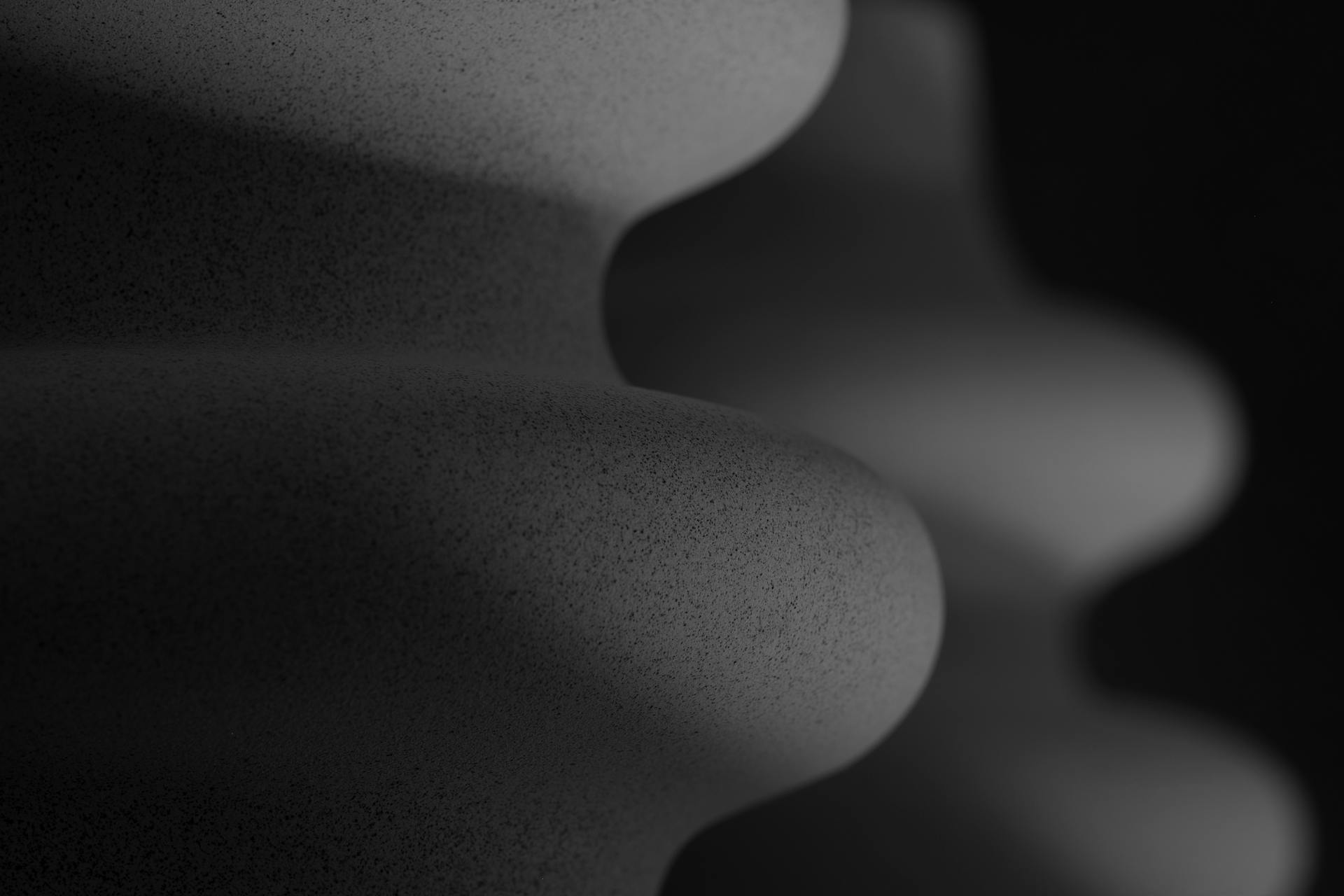
The wet process equipment is the most important part of the production line, as it directly affects the quality of the base paper, glue, and steam used.
A castle single-side machine, the key equipment of the wet part, must use advanced technology equipment, such as a positive pressure card single-side machine.
This advanced technology allows for adjustable gaps and precise control over the amount of glue used, ensuring optimal results.
The wet process equipment consists of a roller rack, auto feed machine, pre-heater, bridge, glue, double-sided machine, etc.
These machines work together to process the corrugated board into 3, 5, and 7 layers of corrugated board, making it essential for the production line to function smoothly.
The quality of the paper board is greatly influenced by the wet process equipment, making it a critical component of the production line.
Worth a look: Single Face Corrugated Board
Line Working and Precautions
A corrugated board production line may be made up of various machines, including a reel rack, a one-side corrugated board-forming machine, and a rotating cutting unit. These machines work together to continuously manufacture and cut paper to the required size with a roll material and a potato or cornstarch binder.
The line's output includes corrugated board, which is cardboard made without sun or sun drying. Simultaneously, the glue machine or veneer produces more than 3 layers of corrugated board.
Some precautions to take when working with a corrugated board production line include making sure the power supply is good and the connection is in accordance with the specification and request of equipment. The electricity has to be shut down for all tests and repairs.
Here are some additional precautions to keep in mind:
- Unable to move locked device parts.
- Make sure that there is no foreign matter in the chain and belt before starting the machine.
- Regular inspection of drive components, fasteners, and adjustment of fastening in time.
- Periodically oil the drive part to make sure the device has a good transmission performance.
Line Working Principle
A corrugated board production line is quite complex, but I'll break it down for you. The working principle of a corrugated board production line involves corrugating, bonding, separating, pressing, cutting into board size, and stacking output.
The line typically consists of a reel rack, a one-side corrugated board-forming machine, and a rotating cutting unit. This setup allows for continuous paper manufacturing and cutting to the required size with a roll material and a potato or cornstarch binder.
The paper is cut to the required size, and the corrugated board is made without sun or sun drying.
Line Precautions
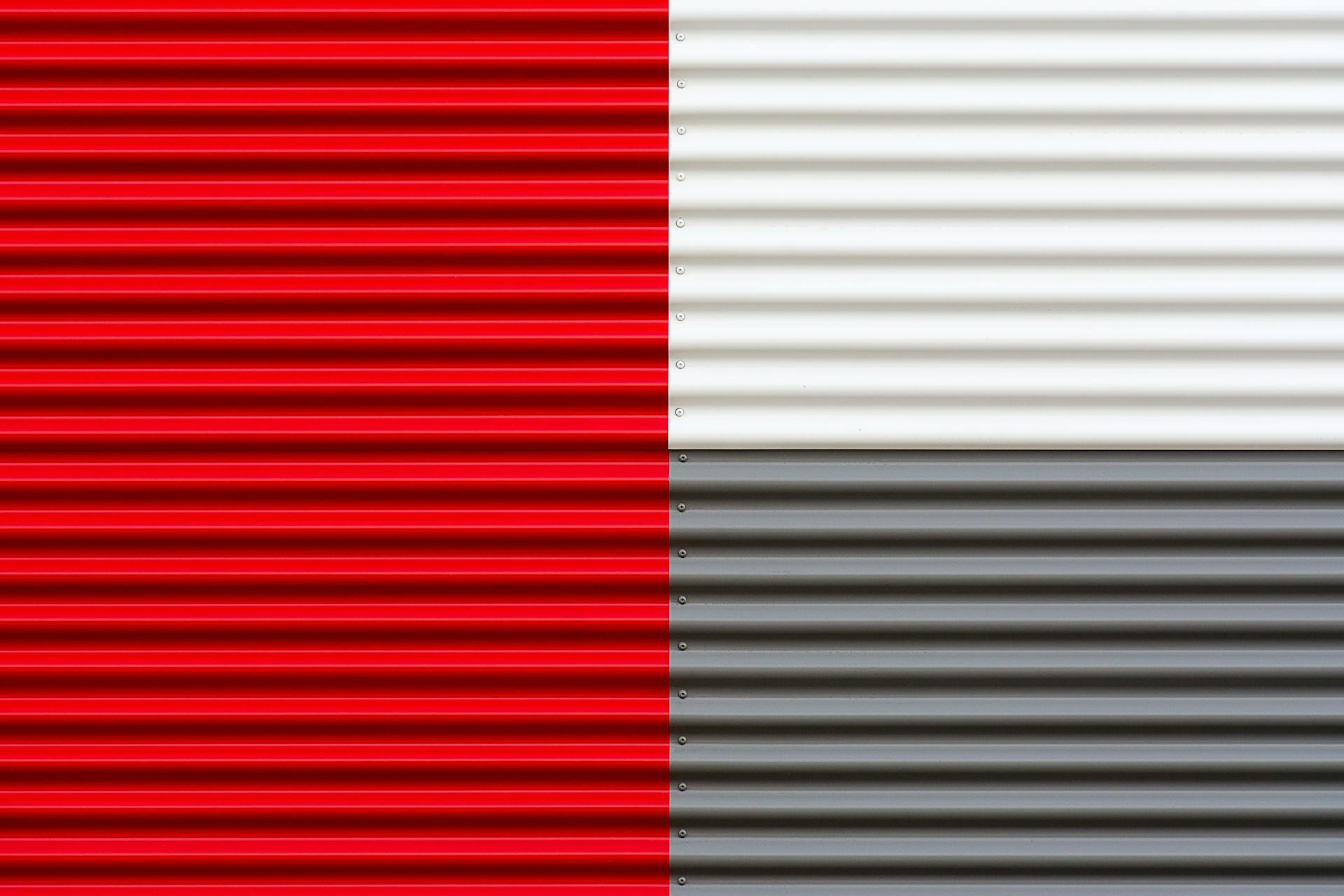
Working on a production line requires attention to detail and a commitment to safety. Make sure the power supply is good and the connection is in accordance with the specification and request of equipment.
It's essential to shut down the electricity for all tests and repairs to prevent accidents. This is a crucial step that should never be skipped.
When working on the line, be aware of locked device parts and do not attempt to move them. This can cause damage to the equipment and put you at risk.
Before starting the machine, inspect the chain and belt for any foreign matter. This will ensure the function works normally and prevent damage to the machine.
To minimize transmission damage, it's recommended to open the machine as little as possible. This will also help prevent electrical shock and damage to parts.
Regular inspection of drive components, fasteners, and adjustment of fastening in time is crucial. This will help prevent breakdowns and ensure the line runs smoothly.
Here are some essential precautions to keep in mind:
- Regularly oil the drive part to ensure good transmission performance.
- Do not wash the belt with solvent to prevent corrosion.
- Avoid dry glue after work to prevent interfering with the following work.
- Only allow professional personnel to open the distribution box and replace the cables.
Three Temperatures: Steam, Moisture, Speed Control
Temperature control is a delicate balance in corrugated cardboard production. If the corrugator roll temperature falls below 150°C, flute formation and bonding will suffer.
Maintaining a steam temperature of at least 150°C is crucial for proper bonding and production speed. If the hot plate temperature is too low, high-speed production becomes impossible.
Moisture and humidity control are just as important as steam temperature. If the pre-heater temperature is too high, the paper will lose excessive moisture, causing the board to crack or burst.
To achieve the right moisture levels, the pre-heater temperature must be carefully controlled. This ensures the paper maintains its moisture throughout the production process.
Faster production speeds demand higher heat levels. If production is running too fast without enough heat, the glue won’t activate properly, leading to weak bonding.
Here's a summary of the temperature control factors to keep in mind:
- Steam temperature: at least 150°C for proper bonding and production speed
- Pre-heater temperature: carefully controlled to maintain moisture levels
- Production speed: adjusted to match available heat for optimal bonding
Control and Optimization
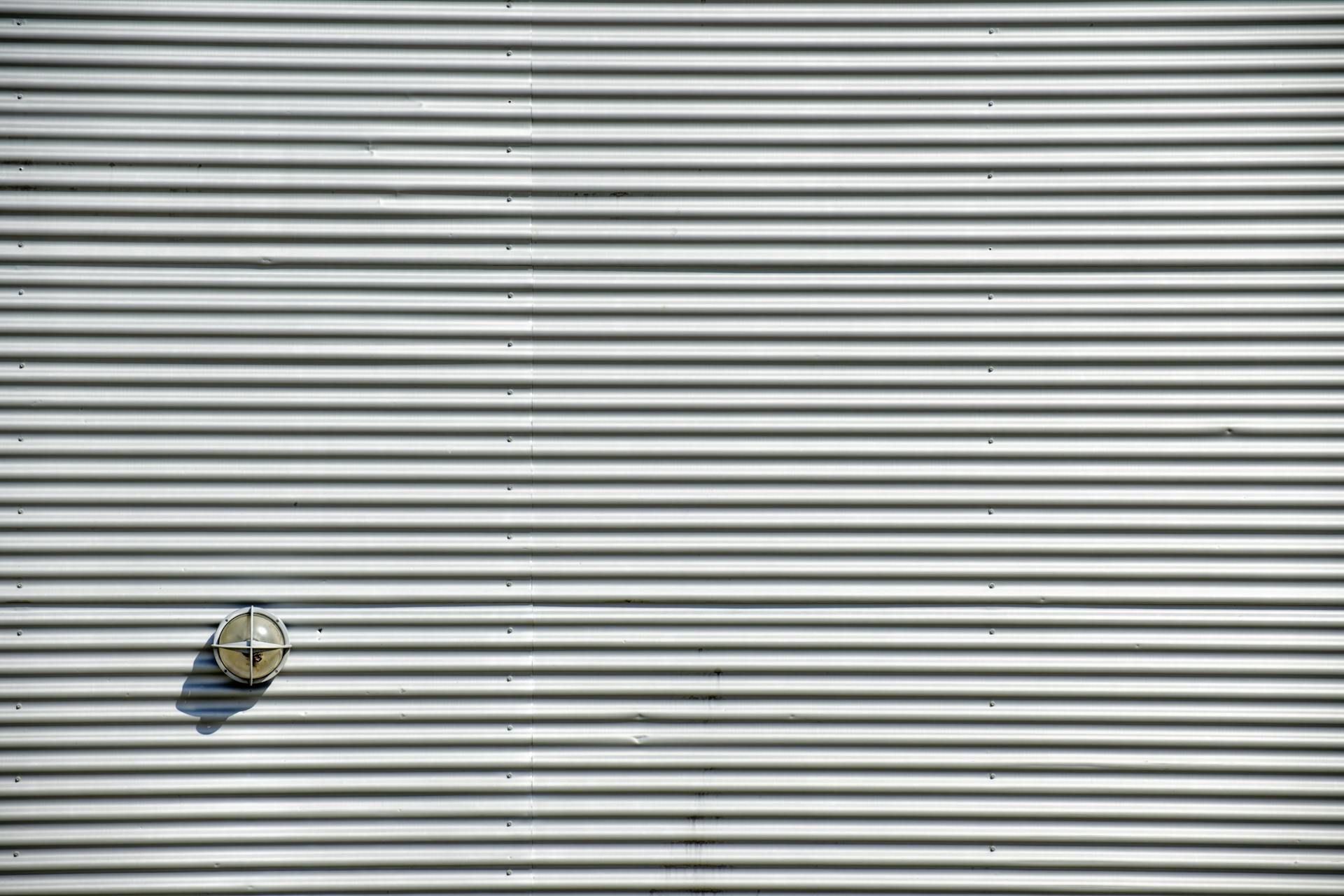
Controlling tension and temperature is crucial in corrugated board production. Improper tension can lead to warping and defects, while inconsistent temperature can affect bonding and production speed.
A properly balanced tension system ensures the paper enters the next stage of production smoothly, improving overall stability and quality. This involves adjusting brake tension and using tension rollers and correction systems.
Tension rollers can significantly affect the cardboard's physical properties, so ensuring that roller gaps and alignment are properly set is essential. Excessive pressure can flatten the board, reducing its edge crush and box compression strength.
Steam temperature is critical in bonding the layers of the corrugated cardboard. A properly regulated steam temperature directly impacts cardboard adhesion and production speed. If the corrugator roll temperature falls below 150°C, flute formation and bonding will suffer.
The pre-heater temperature must be carefully controlled to maintain appropriate moisture levels in the paper. If it's too high, the paper will lose excessive moisture, causing the board to crack or burst.
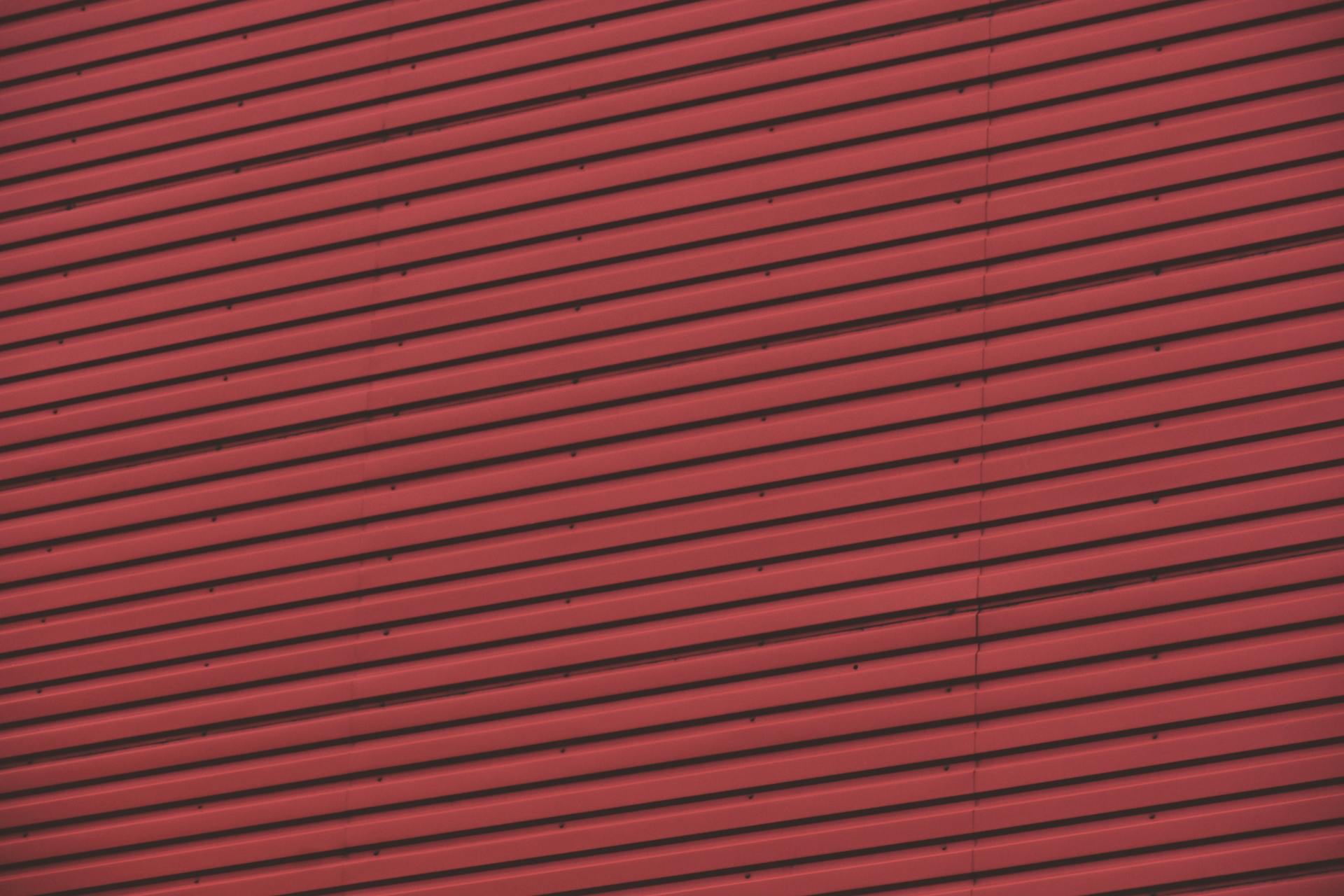
Faster production speeds demand higher heat levels. If production is running too fast without enough heat, the glue won’t activate properly, leading to weak bonding. To maintain product quality, it may be necessary to reduce the production speed.
Here are some key temperature and tension control factors to consider:
Inconsistent tension can lead to poor flute formation and warping, while excessive pressure can flatten the board. By optimizing tension and temperature control, manufacturers can improve overall stability and quality in corrugated board production.
Improvement and Cost Reduction
Controlling glue viscosity is essential for improving quality and reducing costs in corrugated cardboard production.
Proper management of glue viscosity ensures that the board produced will meet the highest standards.
Mastering One Glue allows for a more cost-effective and streamlined production process.
Controlling tension throughout the production line is also crucial for improving quality and reducing costs.
Tension adjustments can significantly impact the quality of the board produced.
Proper heat management is also vital for reducing costs and improving quality.
By mastering Three Temperatures, you can create a more efficient production process.
Machine optimization, such as using a robot arm palletizer, can also help streamline production and reduce costs.
Proper management of the entire production line, from flexo printer to strapper, is necessary for achieving optimal results.
Frequently Asked Questions
What is the raw material of corrugated board?
Corrugated board is made from corrugated cardboard base paper, primarily sourced from recycled paper in Germany, with some fresh fibers and starch glue added. This raw material is then processed in a corrugator to produce the final product.
What is the corrugation process step by step?
The corrugation process involves making paper, creating fluting, combining layers, cutting and folding, and printing and labeling. This multi-step process transforms raw materials into sturdy, versatile corrugated boxes.
Sources
- https://www.fefco.org/lca/dscription-of-production-system/corrugated-board-production
- https://www.aopackmachine.com/corrugated-cardboard-production-line-faq-guide/
- https://www.linkedin.com/pulse/mastering-corrugated-cardboard-production-key-points-moss-s9boc
- https://bioresources.cnr.ncsu.edu/resources/revolutionizing-corrugated-board-production-and-optimization-with-artificial-intelligence/
- https://www.llypack.com/corrugated-line/61588843.html
Featured Images: pexels.com