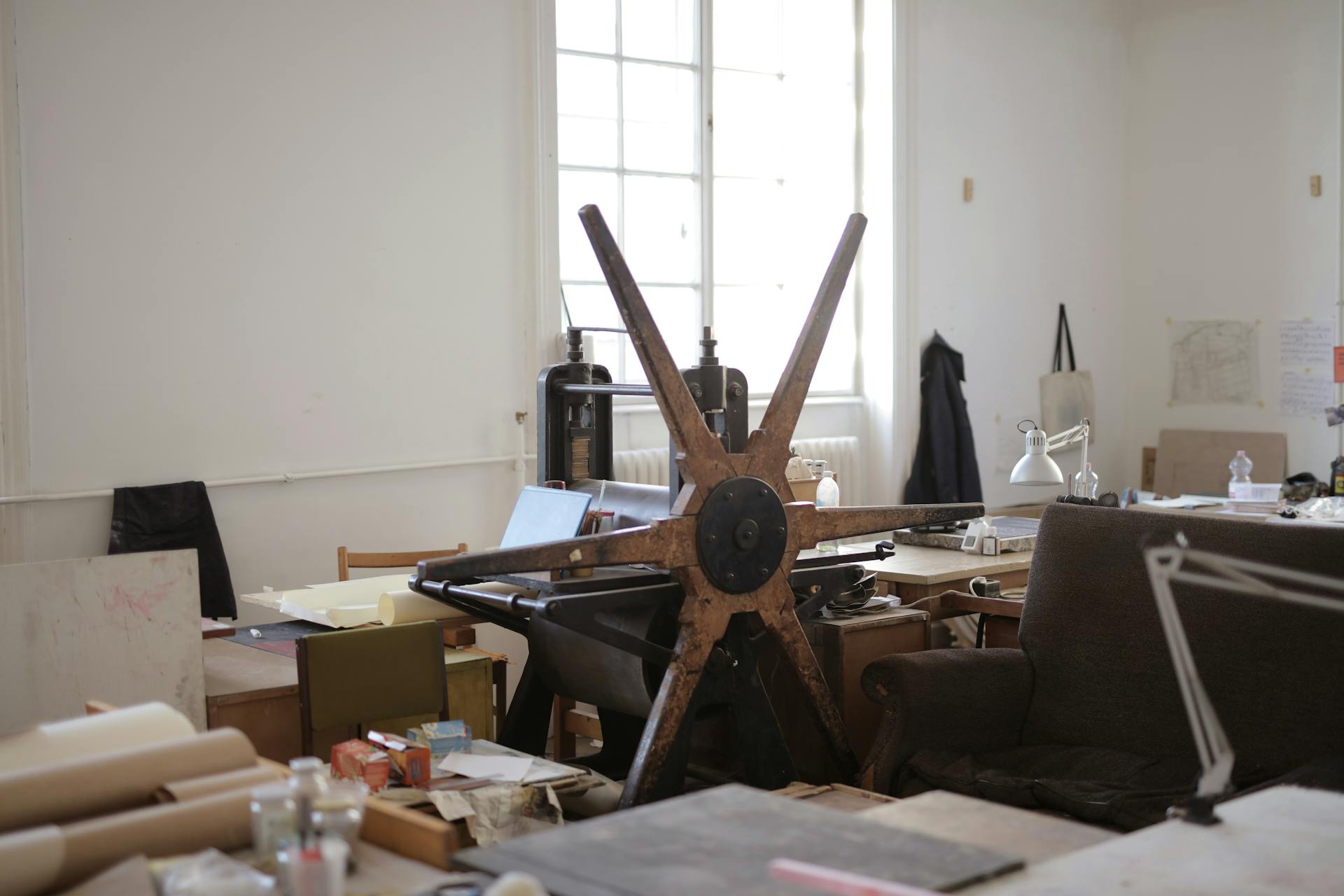
Paper pulp molding machines are versatile and widely used in various industries for packaging and beyond. They can produce a wide range of products, from cups and bowls to trays and containers.
These machines work by processing paper pulp into a moldable material that can be shaped into various forms. The pulp is mixed with water and other additives to create a consistent texture and strength.
One of the key benefits of paper pulp molding machines is their eco-friendliness. They use recycled paper as the primary material, making them a more sustainable option compared to traditional manufacturing methods.
Paper pulp molding machines are also highly customizable, allowing manufacturers to create products with specific dimensions, shapes, and designs. This flexibility makes them ideal for a wide range of applications.
Consider reading: Packing Material for Glass
Types of Machines
There are three main types of paper pulp molding machines, each with its own unique capabilities. These machines can process various raw materials.
Type 1 machines can utilize waste paper like cartons, wrapping paper, books, and notebooks, as well as pulp. They're ideal for producing agricultural product packaging, such as egg trays and fruit trays.
Type 2 machines also work with waste paper, creating industrial product packaging like coffee cup holders and seedling nursery holders. Type 3 machines, on the other hand, use fiber biomass and produce tableware trays, including food boxes and cup lids.
Here are the three types of machines in a concise table:
Type 1: Tableware
Type 1 pulp molding machinery is used to make a variety of tableware products. The raw material for this type of machine is fibrous biomass.
The tableware products made by Type 1 machines include food boxes, food plates, food bowls, food containers, fruit plates, and cup lids. These machines can be semi-automatic or fully automatic.
The semi-automatic tableware machine, model BCB-950, has a capacity of 0.4-0.6T and an equipment size of 4100*1200*2800. The fully automatic tableware machine, model BCB-950s, has a capacity of 0.8-1T and an equipment size of 5400*2500*2800.
Here's a list of the specifications for the semi-automatic and fully automatic tableware machines:
Type 3: Machine-Powered Industrial Packaging
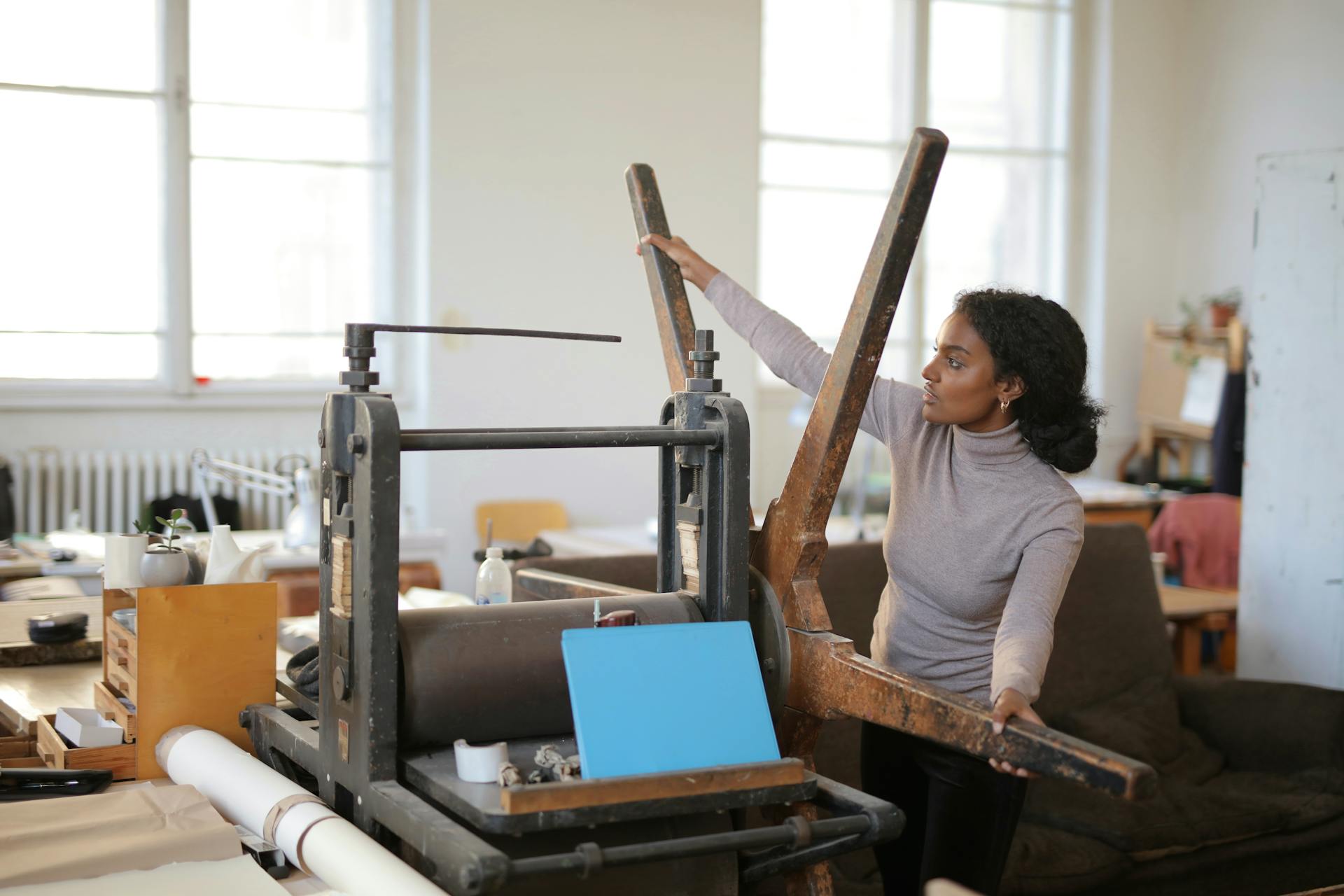
Type 3 pulp molding machinery is used to produce industrial product packaging, including single-station and double-station types. This equipment is versatile and can create a wide range of packaging types.
Beston Group offers custom molds for customers, allowing them to send product pictures and specific data for tailored mold design. The parameters of this machine are also available for reference.
The production process for industrial product packaging is similar to that of making agricultural packaging, with the equipment capable of producing a variety of packaging types.
This type of equipment is often used to produce packaging for industrial products such as auto parts, precision instruments, and computer accessories. Pulp-molded packaging provides good cushioning and fixing effects, effectively preventing damage to products during transportation.
The BGB-2 and BGB-1 models of Type 3 pulp molding machinery have a capacity of 14400 and 7200 Mould Template stations per 24 hours, respectively. The equipment size and weight for these models are 2800*2200*3800 and 1.8T, with a final trays height of 75mm and a power consumption of 500w.
Here is a comparison of the BGB-2 and BGB-1 models:
Product Applications
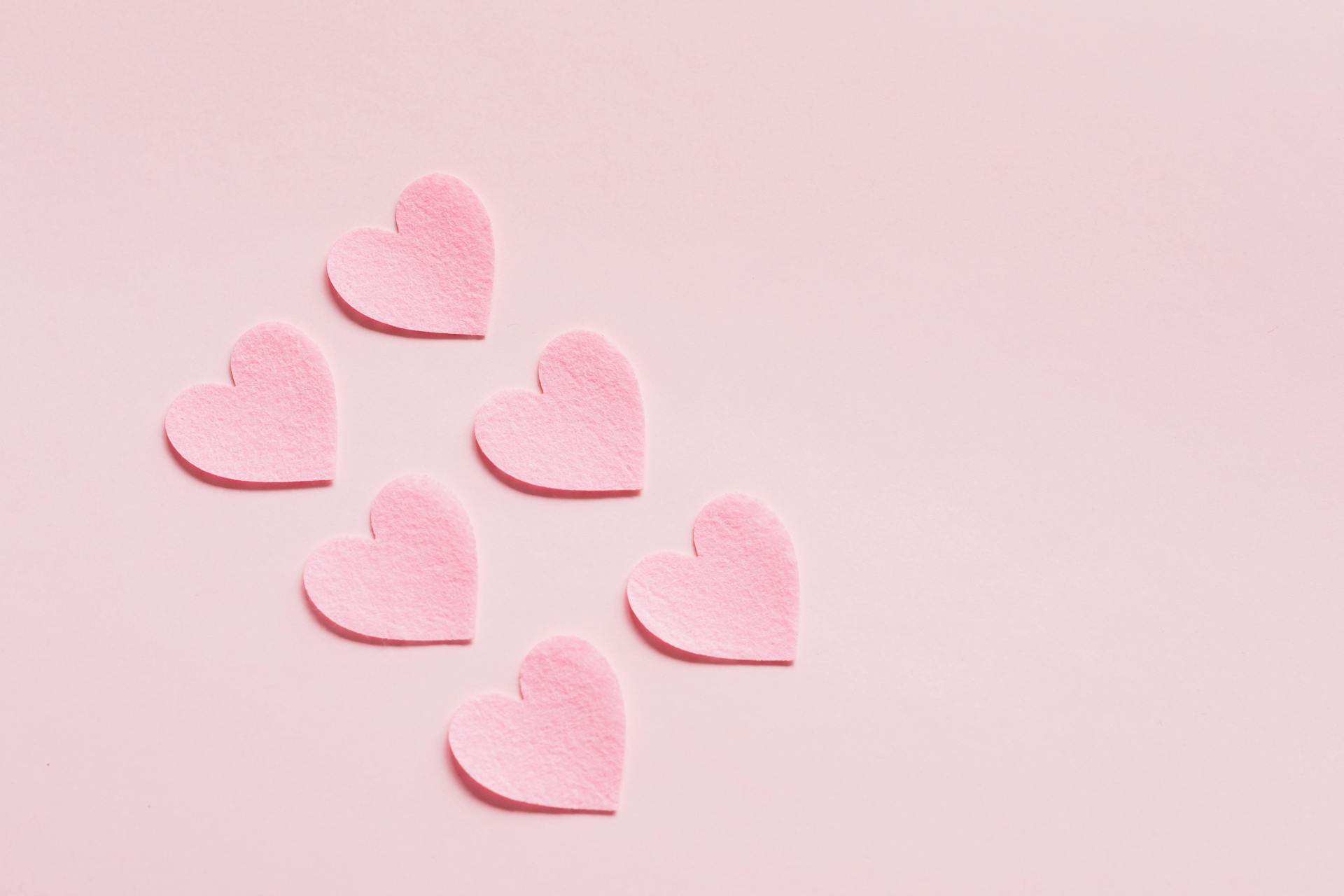
Paper pulp molding machines are incredibly versatile and can be used to produce a wide range of products. The machines can make various types of egg trays, with five different models available, including the BTF1-3, BTF1-4, BTF3-4, BTF4-4, and BTF4-8.
The BTF1-3 model, for example, can produce 800-1000 egg trays per hour. This is just one of the many models available, and customers can choose customized molds to produce paper trays that better suit their products.
One of the key benefits of paper pulp molding machines is their ability to produce large quantities of products quickly. The BTF5-8 model, for instance, can produce 5000-5500 egg trays per hour, making it an ideal choice for large-scale production.
To give you a better idea of the different models available, here's a comparison of some of the key specifications:
Overall, paper pulp molding machines are a great choice for anyone looking to produce high-quality products quickly and efficiently.
World Cases and Solutions
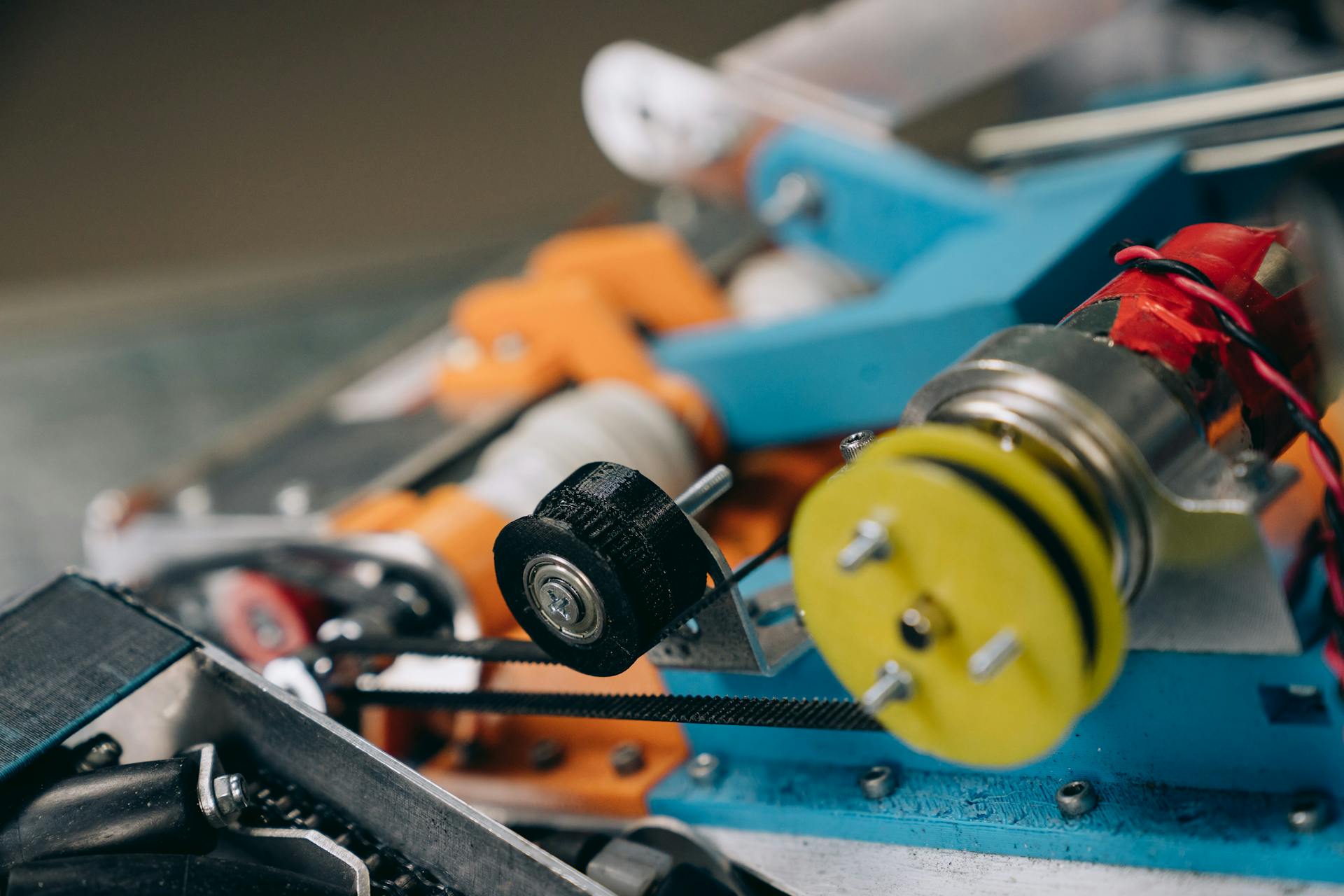
We've shipped paper pulp molding machines to countries such as Indonesia and Thailand. These machines are primarily used for making coffee trays and industrial packaging.
Our team conducted a trial run at the factory before shipping a machine to Indonesia. The trial run went smoothly, ensuring the quality of the equipment.
Beston Group welcomes customers to visit the factory and view the equipment if they're interested.
For another approach, see: Food Packaging Equipment Manufacturers
Machine Specifications
The machine specifications for paper pulp molding machines are quite varied, but I'll break down the key details for you.
The machine types available range from the compact FM-135 to the larger MT-150, with outputs ranging from 40 kg/h to 220 kg/h. You can also choose between a batch dryer or a tunnel dryer, depending on your production needs.
Here are some key specifications to consider:
Each machine type has its own unique features and capabilities, so it's essential to choose the right one for your specific needs.
MT-40: 40 kg

The MT-40 pulp moulding machine is a compact powerhouse that's ideal for small-scale production sites. It has an output of 40 kilograms per hour.
This machine is designed to process (recycled) paper and various (virgin) fibres, making it a versatile option for various applications. It features water and heat recovery, which is a highly sustainable and energy-efficient approach.
One of the unique features of the MT-40 is its ability to be tailored to meet specific requirements. This includes individual vacuum port configuration for simultaneous production of multiple products.
Here are some key specifications of the MT-40:
The MT-40 also features a hand-fed dryer, which allows for smooth operation and quick tool change for flexible production planning.
MT-150: 150-220 kg
The MT-150 is a pulp moulding machine that can produce up to 220 kg of output per hour.
This machine is highly flexible, with various dies that can be applied to meet specific production needs.
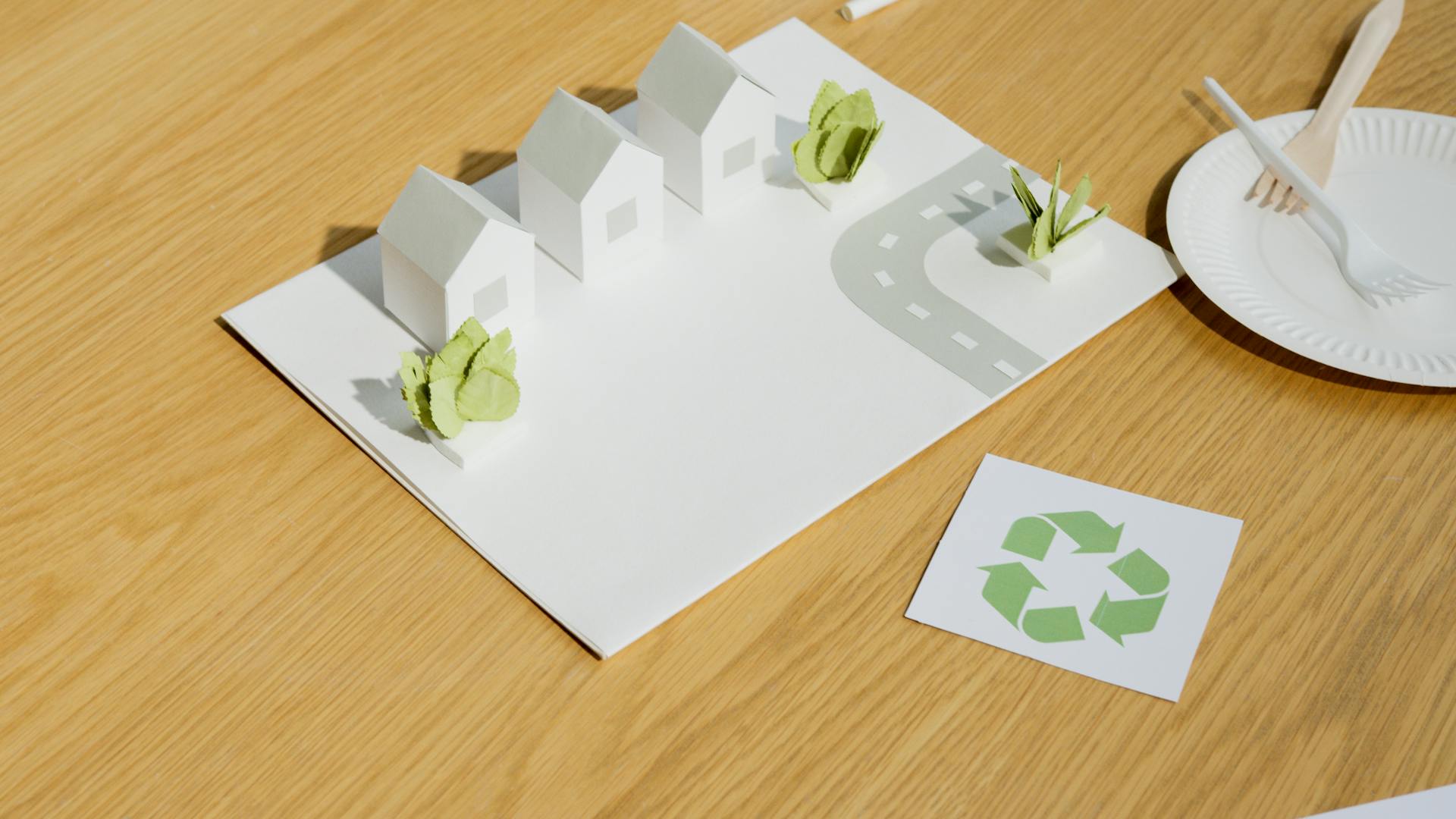
Its output ranges from 150 to 200 kilograms per hour, depending on the height, design, and product wall-thickness.
The MT-150 can process (recycled) paper and various (virgin) fibres, making it a versatile option for manufacturers.
Here are some key features of the MT-150:
- Output 150 – 200 kilograms per hour
- With two, four, or six vacuum ports
- Processes (recycled) paper and various (virgin) fibres
- Teflon conveyor belt in drying tunnel
- Water and heat recovery
- CE-certified
This machine is designed to meet individual requirements, with tailored configurations available for simultaneous production of multiple products.
The MT-150 features a smooth operation and quick tool change, making it ideal for flexible production planning.
The Teflon conveyor belt is easy to clean, and the 'endless' conveyor belt in the drying tunnel dries vast numbers in one batch.
Here are some key specifications of the MT-150:
MT-375: 375 kg Output
The MT-375 pulp moulding machine is a beast of a machine, capable of producing an impressive 375 kilograms per hour. This is a significant output, making it suitable for large production sites.
Here are some key specs to keep in mind:
The MT-375 is designed to handle various types of fibres, including recycled paper and virgin fibres. It's also equipped with a Teflon conveyor belt in the drying tunnel, which is a clever touch.
Machine Types and Configurations
There are three types of pulp molding machinery: Type 1, Type 2, and Type 3. Each type has its own unique characteristics and applications.
Type 1 and Type 2 use waste paper as their raw material, including cartons, wrapping paper, books, and pulp, to produce agricultural and industrial product packaging, respectively. Type 3, on the other hand, uses fiber biomass as its raw material to make tableware trays.
Here are the specific types of pulp molding machines mentioned in the article:
The pulp molding machines come in semi-automatic and fully automatic types, with the semi-automatic type having a capacity of 0.4-0.6T and the fully automatic type having a capacity of 0.8-1T.
Curious to learn more? Check out: Auto Strapping Machine
Automatic
Automatic machines are a game-changer in the pulp molding industry, offering high production rates and flexibility.
AGICO's Automatic Pulp Molding Machine can produce up to 6000-7000 pieces per hour, making it ideal for large-scale productions.
One of the key benefits of automatic machines is their ability to be easily integrated with ancillary equipment, such as afterpress machinery, which allows for embossing, printing, or coating of the pulp molded products.
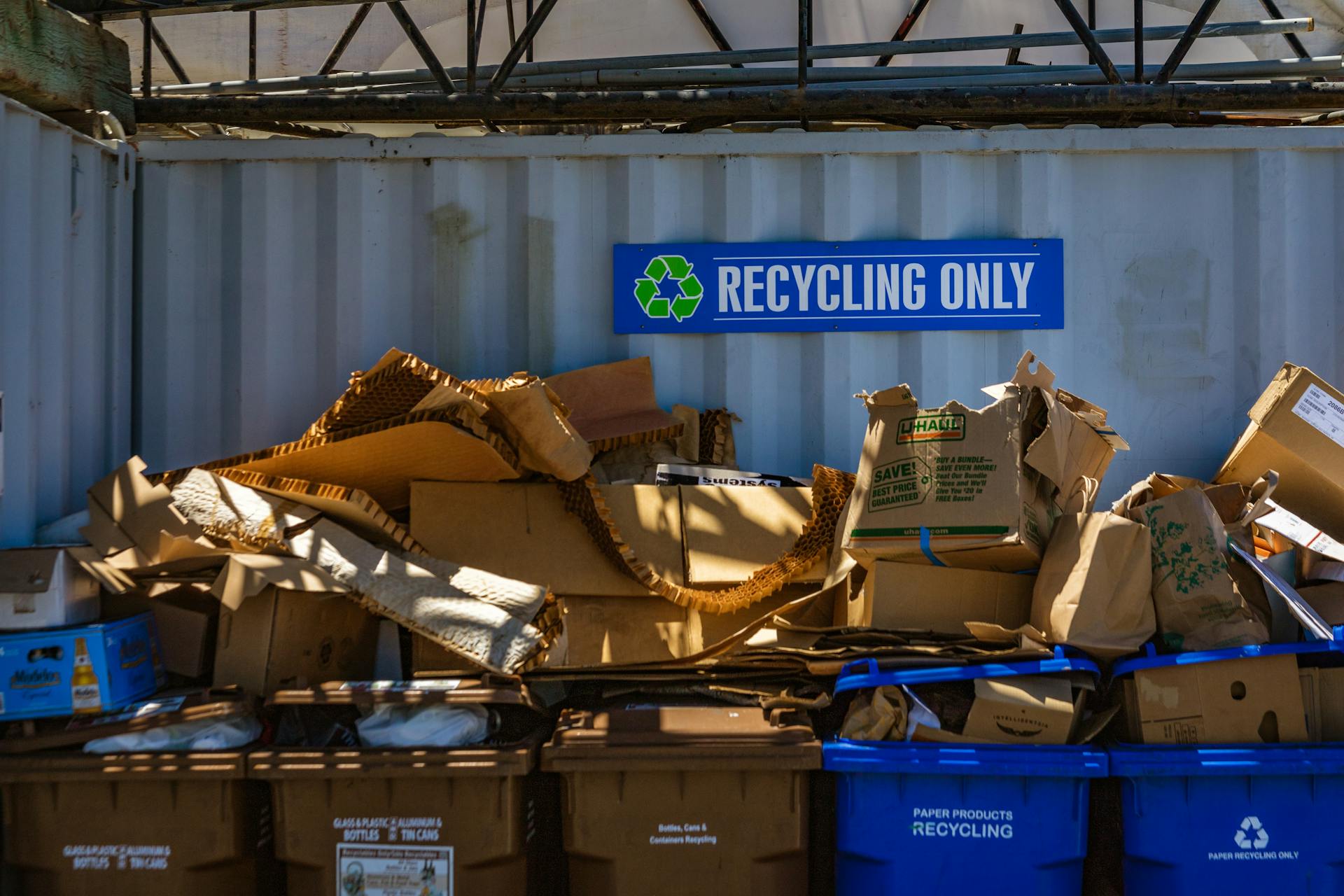
This integration makes it possible to add a finishing touch to the products, increasing their quality and value.
The molds used in automatic pulp molding machines are commonly made of plastic, aluminum, or a combination of both, and can last for more than 2-3 years with proper maintenance.
AGICO offers a one-year warranty on their molds, giving you peace of mind and protecting your investment.
If you're looking to customize your mold, AGICO offers a range of options, including mold customization services, where you can send them a sample or provide specific mold dimensions data or CAD/PDF drawings.
Here's a list of some of the customized mold options available:
- Egg tray molds
- Fruit tray molds
- Bottle tray molds
- Egg carton molds
- Cup tray molds
- Seedling tray molds
- Electronic product packaging molds
- Lunch box molds
- Coffee cup carrier molds
- Paper urinal molds
- Paper mask molds
Packaging Industry: 3. Equipment Configuration
In the packaging industry, equipment configuration plays a crucial role in determining the quality and production efficiency of your products. A well-configured pulping system, for example, can significantly impact the quality of the pulp.
The type and number of molding systems you choose will also affect the shape and precision of your product. This is especially important if you're producing complex or customized products.
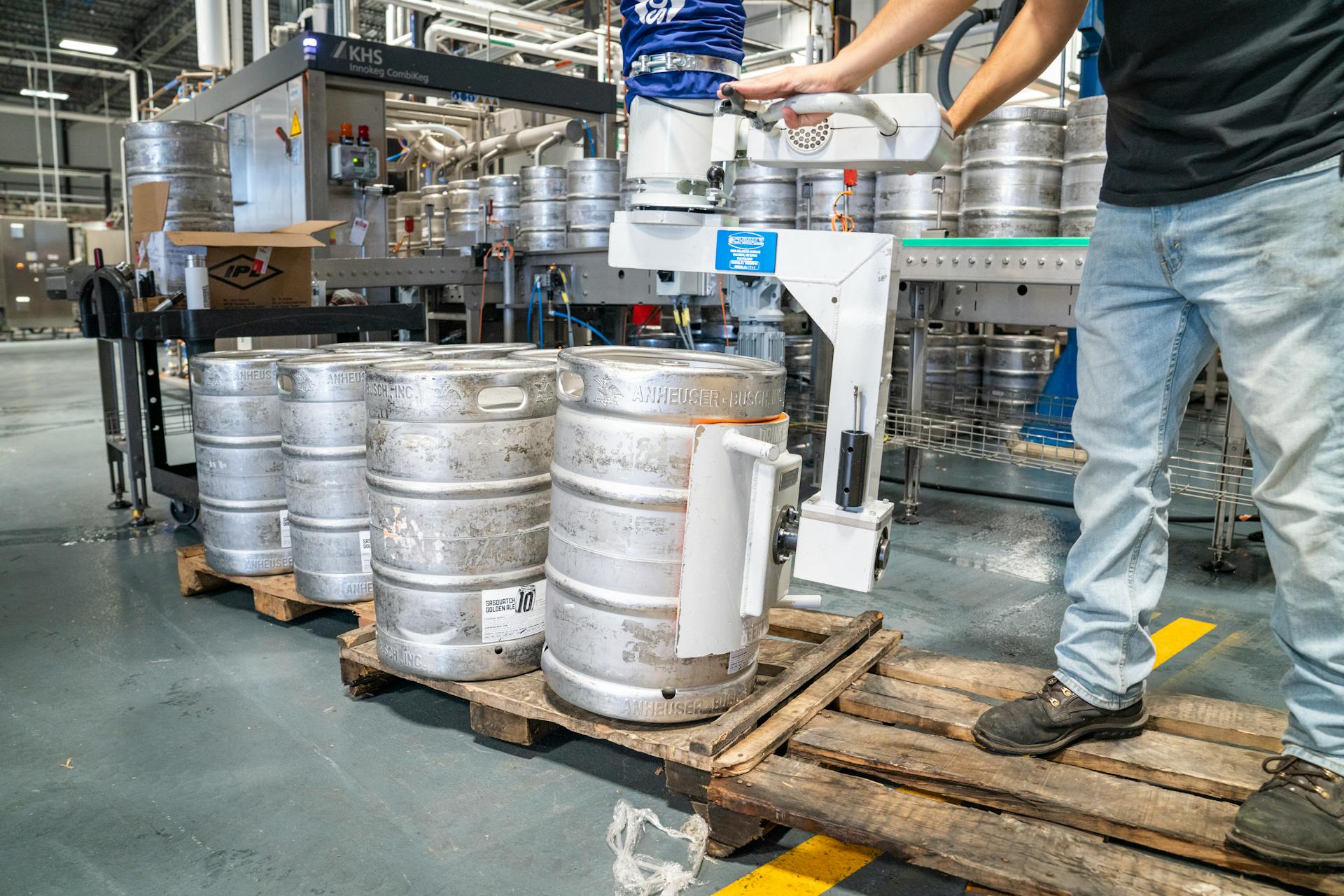
The choice of drying method can greatly impact the drying speed and quality of your product. Some drying methods, like heat drying, can be faster but may compromise on product quality.
A higher degree of automation can increase production efficiency, but it also comes with a higher cost. This is something to consider when deciding on the level of automation for your equipment.
Here are some key factors to consider when configuring your equipment:
- Pulping system: affects the quality and production efficiency of the pulp
- Molding system: affects the shape and precision of the product
- Drying system: affects the drying speed and quality of the product
- Automation degree: affects production efficiency and cost
Machine Parameters
The paper pulp molding machine is a remarkable piece of equipment, and understanding its parameters is crucial for optimizing its performance.
The capacity of these machines varies significantly, with the YG-1*3 model producing 1000 pieces per hour, while the YG-6*8 model can produce a staggering 7000 pieces per hour.
The forming mould quantity also differs across models, ranging from 3 moulds in the YG-1*3 model to 48 moulds in the YG-6*8 model.
Here's a breakdown of the machine parameters for each model:
Manual
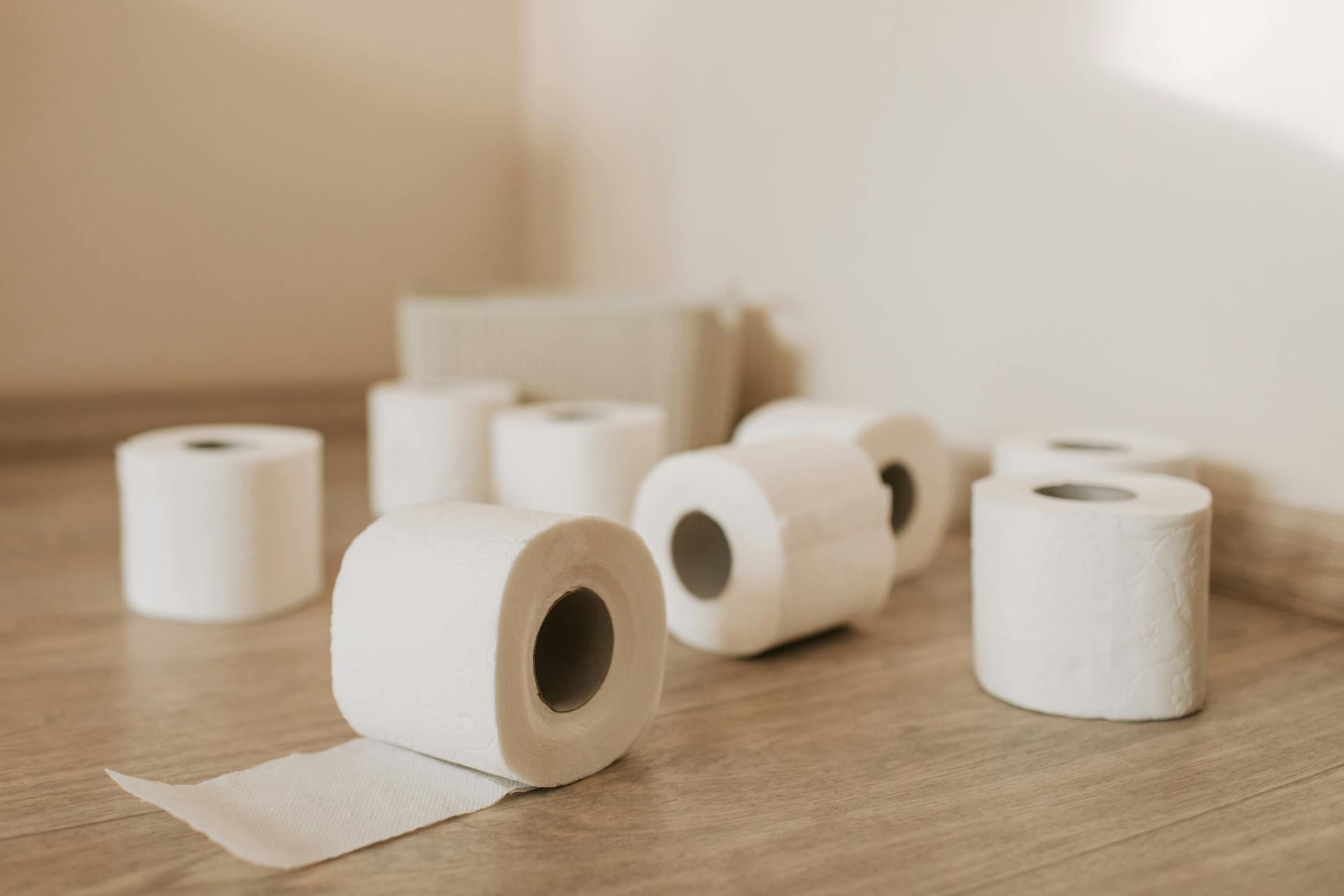
Manual machines are capable of producing a range of output speeds.
The Manual Pulp Molding Machine can produce up to 1000 pieces per hour, making it suitable for smaller-scale production.
Some Manual machines can reach output speeds of 1500 pieces per hour, which is a noticeable increase from the 1000 piece per hour mark.
Higher-end Manual machines can produce 1800-2300 pieces per hour, offering a significant boost in productivity.
The top-of-the-line Manual machines can crank out 2200-2500 pieces per hour, making them ideal for high-volume production.
Here's an interesting read: Paper Sack Making Machine
Parameter
Machine parameters are a crucial aspect of any machine, including the Paper Pulp Molding Machine. The capacity of these machines can vary greatly, with some models producing up to 7000 pieces per hour.
The YG-6*8 model, for instance, has a capacity of 7000 pieces per hour. This is significantly higher than the YG-1*3 model, which has a capacity of 1000 pieces per hour.
The number of forming molds also varies across different machine models. The YG-4*4 model, for example, has 16 forming molds, while the YG-1*3 model has only 3.
Here's a breakdown of the total power consumption for each machine model:
The electricity consumption also varies across different machine models. The YG-6*8 model, for instance, consumes up to 130 kilowatt-hours of electricity per hour.
Packaging Industry
The packaging industry is a vital sector where paper pulp molding machines play a significant role. Pulp-molded packaging has good cushioning properties and can effectively protect products.
Egg trays are a common example of pulp-molded packaging, with production capacities ranging from 800 to 9000 pieces per hour, depending on the machine model. For instance, the BTF1-3 model produces 800-1000 egg trays per hour.
Food packaging is another area where pulp-molded packaging excels, providing effective protection for products like fruit and fast food. The machine parameters for different models are outlined in the article, showcasing their varying capacities and power consumption.
Electronic product packaging also benefits from pulp-molded packaging, which offers good cushioning and fixing effects for products like mobile phones and computer accessories. The machine parameters for different models, such as the BGB-2 and BGB-1, show their capacities and power consumption.
Industrial product packaging is where pulp-molded packaging truly shines, providing effective protection for auto parts and precision instruments during transportation. The machine parameters for different models, such as the BTF5-8 and BTF6-8, show their capacities and power consumption.
Here are some key benefits of pulp-molded packaging:
* BenefitsDescriptionGood cushioning propertiesProtects products from damage during transportationEffective protectionPrevents damage to products during transportationGood fixing effectsSecures products in place during transportation
For more insights, see: Egg Crate Foam Packing
Machine Models
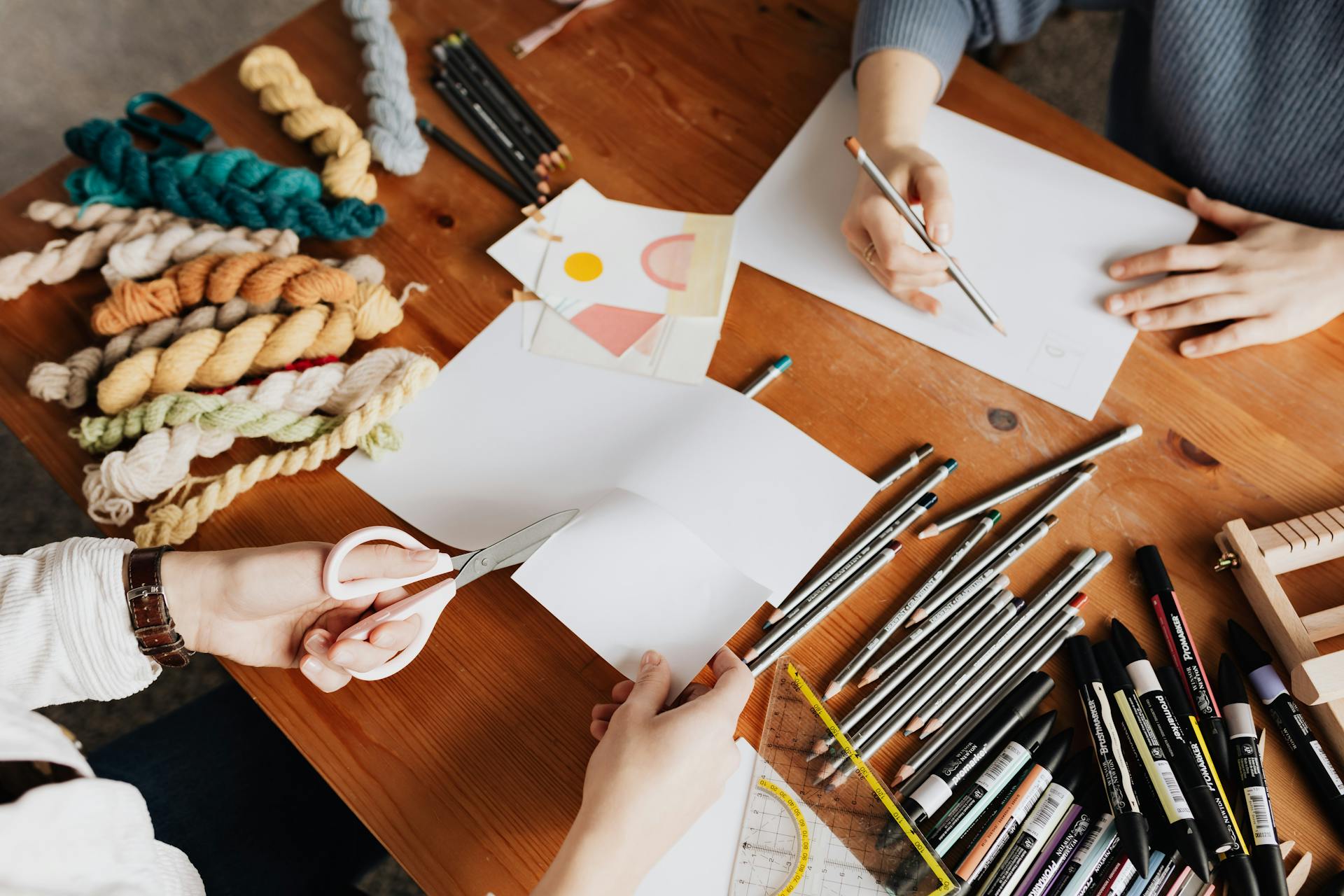
The MT-250 pulp casting machine has an average production of approximately 275 kilograms, with an output of 250-300 kilograms per hour.
The machine is designed for flexible manufacturing, with relatively straightforward tool changes. It's also CE-certified for safety and efficiency.
Here are some key specifications of the MT-250 machine:
AGICO offers paper pulp molding machines with different models, including one with an impressive output of 10,000 pieces per hour.
MT-250:
The MT-250 is a pulp casting machine with a middle-range output. It produces approximately 275 kilograms of pulp per hour.
This machine is relatively flexible, with straightforward tool changes that allow for easy adjustments to production. The exact output depends on the dies used.
The MT-250 can be equipped with two, four, or six vacuum ports. This feature allows for efficient processing of various fibers, including recycled paper and virgin fibers.
A Teflon conveyor belt is used in the drying tunnel, which helps to recover water and heat. This eco-friendly design is CE-certified, ensuring compliance with safety regulations.
You might enjoy: Molded Pulp Packaging Market
Here's a quick overview of the MT-250's key features:
- Output: 250 – 300 kilograms per hour
- Vacuum ports: 2-4-6
- Processes: Recycled paper and various (virgin) fibers
- Drying: Teflon conveyor belt in drying tunnel
- Energy recovery: Water and heat recovery
- Certification: CE-certified
The MT-250 can produce up to 5 shots per minute, making it a reliable choice for pulp casting needs.
AGICO Hot-Sales
AGICO Hot-Sales offers a range of paper pulp molding machines that cater to different production needs. Their machines can produce up to 10000 pcs/h.
AGICO's machines are available in various models, allowing customers to choose the most suitable equipment for their specific needs. Customers can select from different output levels, drying methods, and paper consumption rates.
AGICO's paper pulp molding machines can be customized based on factors like output, drying method, paper consumption, occupied area, and investment funds. This flexibility makes it easier for customers to find the perfect machine for their production requirements.
Here are some key features of AGICO's paper pulp molding machines:
- Output: 10000 pcs/h
Benefits and Features
The paper pulp molding machine is a game-changer for production. It's tailored to meet your specific requirements, making it a versatile and effective solution.
One of the key benefits of this machine is that it eliminates the need for transfer, resulting in fewer mold costs. This not only saves you money but also reduces waste.
Smooth operation is guaranteed, thanks to the machine's ability to perform quick tool changes. This flexibility is perfect for production planning, allowing you to adapt to changing demands quickly.
The Teflon conveyor belt is incredibly easy to clean, making maintenance a breeze. This reduces downtime and keeps your production running smoothly.
The drying tunnel is another innovative feature, featuring an 'endless' conveyor belt that can dry large numbers of products in one batch. This increases efficiency and reduces the need for multiple drying cycles.
For your interest: One Sided Corrugated Cardboard
Machine Pricing and Business
Purchasing a paper pulp molding machine can be a significant investment, and understanding the factors that affect its price is crucial. The configuration of the machine is a major factor, with different types of configurations resulting in varying prices.
A higher-leveled configuration usually comes at a higher price, and the price will be higher for machines with high output and capacity. For example, a plastic forming mold has a lower price than a metal mold.
The cost of labor, land, electricity, and water also play a significant role in determining the final price of the machine. You'll need to consider these costs when creating a business plan for your pulp molding business.
If you're looking to start a pulp molding business, the moderate cost and high quality of the machines make it an attractive option. The large market for the final products also means a high and fast return on investment.
This machine is also an eco-friendly way to turn waste paper into valuable resources, which is an important consideration for many businesses.
On a similar theme: Kraft Paper Business Cards
Molds and Packaging
Molds are a crucial component of paper pulp molding machines, and they can be customized to produce a wide range of products. Beton Group supplies plastic and aluminum molds for their machines, which can be used to make various types of egg trays.
The molds can be designed to produce different types of packaging, such as food packaging, electronic product packaging, and industrial product packaging. For example, pulp-molded packaging can provide good cushioning and fixing effects for electronic products, such as mobile phones and computer accessories.
AGICO offers custom molds for their pulp molding machines, which can be designed according to customers' specific needs and requirements. They have a range of molds available, including paper egg carton molds, seed tray molds, and shoe tray molds.
Here's a list of some of the molds and packaging options available:
- Food packaging: egg trays, fruit trays, fast food boxes
- Electronic product packaging: inner packaging of mobile phones, computer accessories
- Industrial product packaging: inner packaging of auto parts, precision instruments
By changing the molds on a pulp molding machine, customers can produce a variety of different products, making the machine a versatile and cost-effective option.
Barrier Coating Options
Barrier Coating Options can be a game-changer for food packaging materials. Sometimes, a coating is necessary to provide humidity control, make them airtight, or seal them off.
Our pulp moulding machines can accommodate a wide array of barrier linings upon request. This is a process step that can be added to our machines to enable the addition of these coatings.
Take a look at this: Paper Coating Machine
Food packaging materials often require a coating to maintain freshness and prevent spoilage. This is especially true for products that are sensitive to moisture or air exposure.
We can customize our pulp moulding machines to include a barrier coating option that meets the specific needs of your product. This ensures that your packaging is both effective and efficient.
Custom-Made
You can choose customized molds to produce paper trays that better suit your products. Beton Group supplies plastic and aluminum molds for pulp molding machines.
Customization options are vast, allowing you to create molds for various products, such as paper egg carton molds, seed tray molds, shoe tray molds, and egg tray molds.
AGICO has its own design department, model workshop, casting workshop, CNC machining workshop, and fitter assembly workshop, enabling them to design and manufacture molds in-house.
Their molds are designed by computer and processed using CNC machining, resulting in high-precision and good effect.
Discover more: Kraft Paper with Design
AGICO can customize special pulp molds according to customers’ design and style.
By choosing custom-made molds, you can produce a wide range of pulp molding products, from egg trays to fruit trays.
AGICO's pulp molding machines can be used for various applications, including egg tray equipment, fruit tray, and seedling tray making machines.
Here are some of the main pulp molding machines offered by AGICO:
Frequently Asked Questions
What is the process of molding paper pulp?
The process of molding paper pulp involves depositing a water suspension of fibers onto a mold and applying a vacuum to create a strong fiber-mat. Water is then removed using pressure from a matched mold, allowing the pulp to take shape.
What is the technology of pulp molding?
The technology of pulp molding uses "cure-in-the-mold" technology to produce smooth-surfaced products. This process involves heating and pressing molded pulp to create products with a plastic-like appearance.
Featured Images: pexels.com