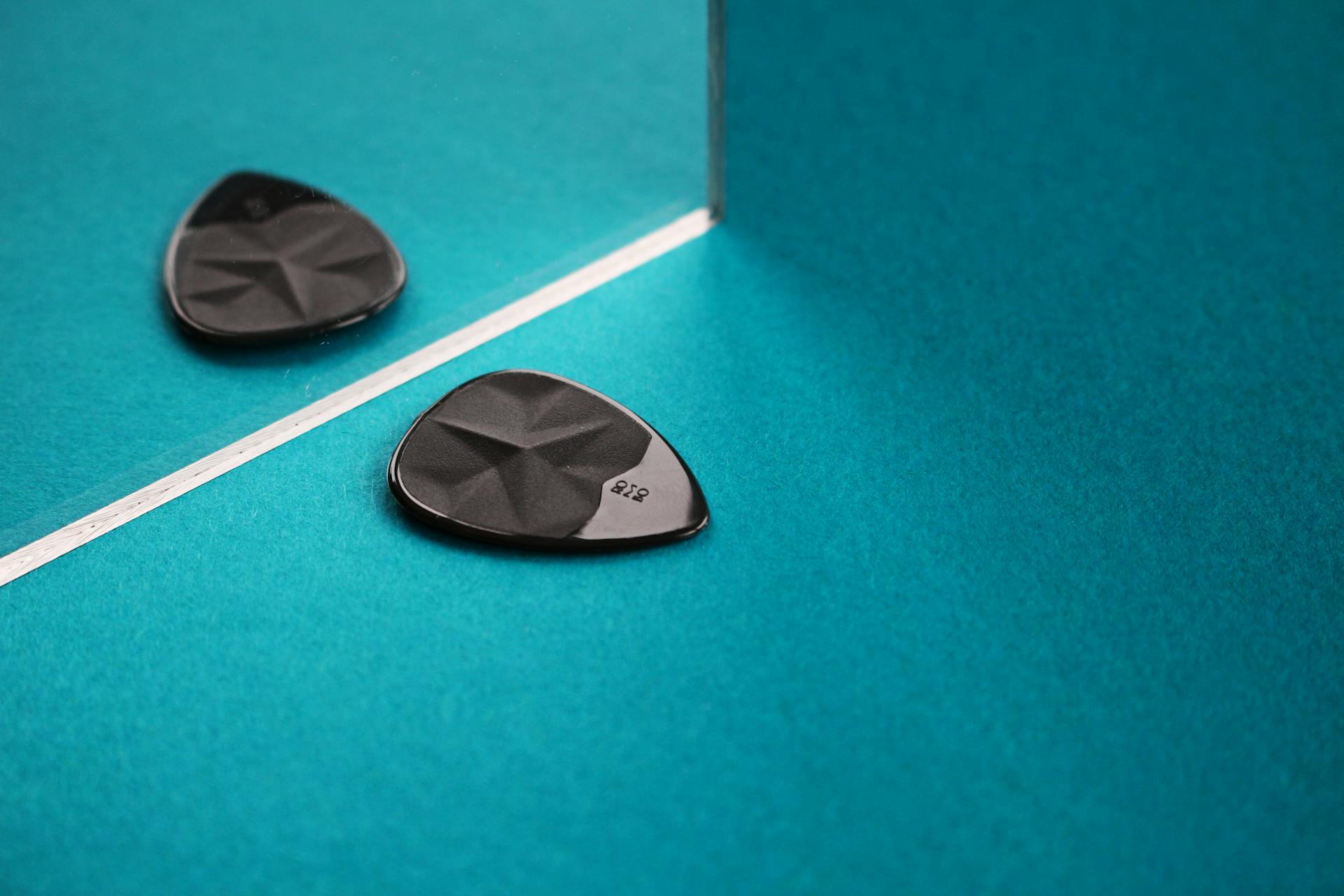
Outsourcing pick and pack services can save you up to 30% of your labor costs.
By partnering with a reputable pick and pack service provider, you can free up valuable resources to focus on core business activities.
Pick and pack services can handle a wide range of products, including small items like jewelry and electronics, as well as larger items like furniture and appliances.
This flexibility makes it an ideal solution for businesses with varying product lines and shipping needs.
Curious to learn more? Check out: Pick up Pack and Ship Services
What Is Pick and Pack?
Pick and pack is a supply chain process where items are picked from storage and combined in a package. A business can store its inventory in a warehouse and integrate its eCommerce channels into the warehouse's systems for inventory management and customer order processing.
The process involves a warehouse picker locating and picking ordered items from their respective locations, which requires detailed organization software and warehouse layouts. This step is crucial for efficient order fulfillment.
Expand your knowledge: Pick and Pack Warehouse

When you order multiple items from a website, like a book, bookmark, and t-shirt, a pick and pack fulfillment provider collects a specified number of certain products from their respective locations to fulfill your order. This process reduces costs by reducing packaging materials and waste.
Pick and pack improves the customer experience by delivering all ordered items in the same package. It also optimizes shipping costs and speeds up delivery.
Order Fulfillment Methods
Order fulfillment methods can be complex, but they're essential for a smooth pick and pack process. Startups and early-stage companies may get away with picking items one at a time, but as your ecommerce business grows, you'll need to evolve your warehouse picking and packing methods to meet demand.
There are several order fulfillment methods to consider, including wave picking, which combines batch and zone picking. Wave picking is ideal for large and complex warehouses, as it offers a balance of efficiency and accuracy.
Related reading: Order Picking Methods
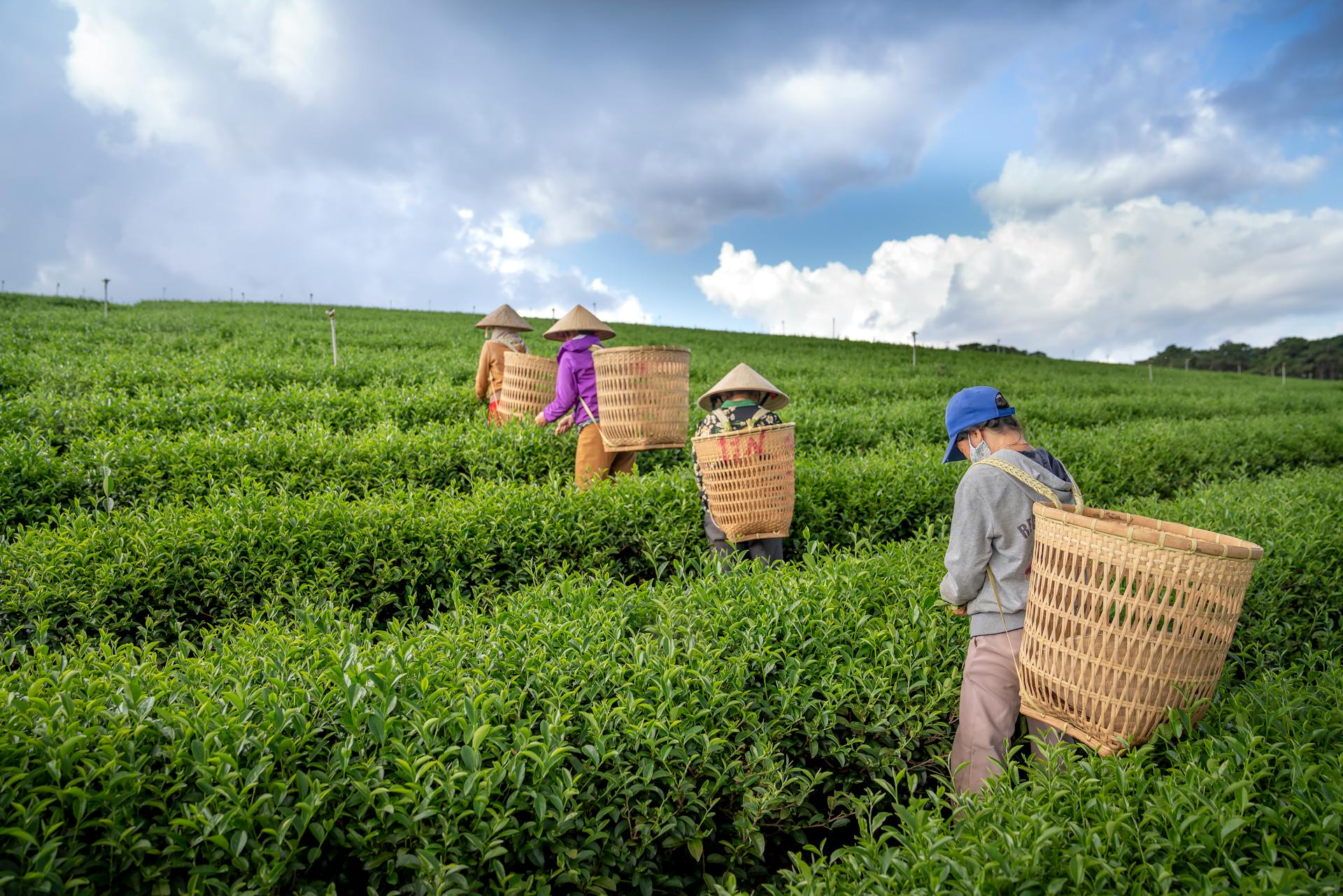
You can also consider using an Order Management System (OMS) to streamline your order fulfillment process. An OMS will help you process orders in a seamless manner, verifying product availability and updating inventory levels in real-time.
Here are four key warehouse picking and packing methods to test in your warehouse to maximize efficiency:
- Wave picking
- Batch picking
- Zone picking
- Batch and zone picking
Methods
As your ecommerce business grows, you may have to evolve your warehouse picking and packing methods to meet demand.
Startups and early-stage companies may get away with picking items one at a time, but as you sell more, advanced warehouse picking methods create speed.
The optimal pick method depends on the number of orders you receive daily, with four common pick methods to consider.
You should match your pick and pack system to your inventory and order complexity, and consider a few pick and pack processes to optimize efficiency.
Four key warehouse picking and packing methods to test in your warehouse are batch picking, zone picking, wave picking, and pick-to-light picking.
Worth a look: Pick Pack and Ship Warehouse
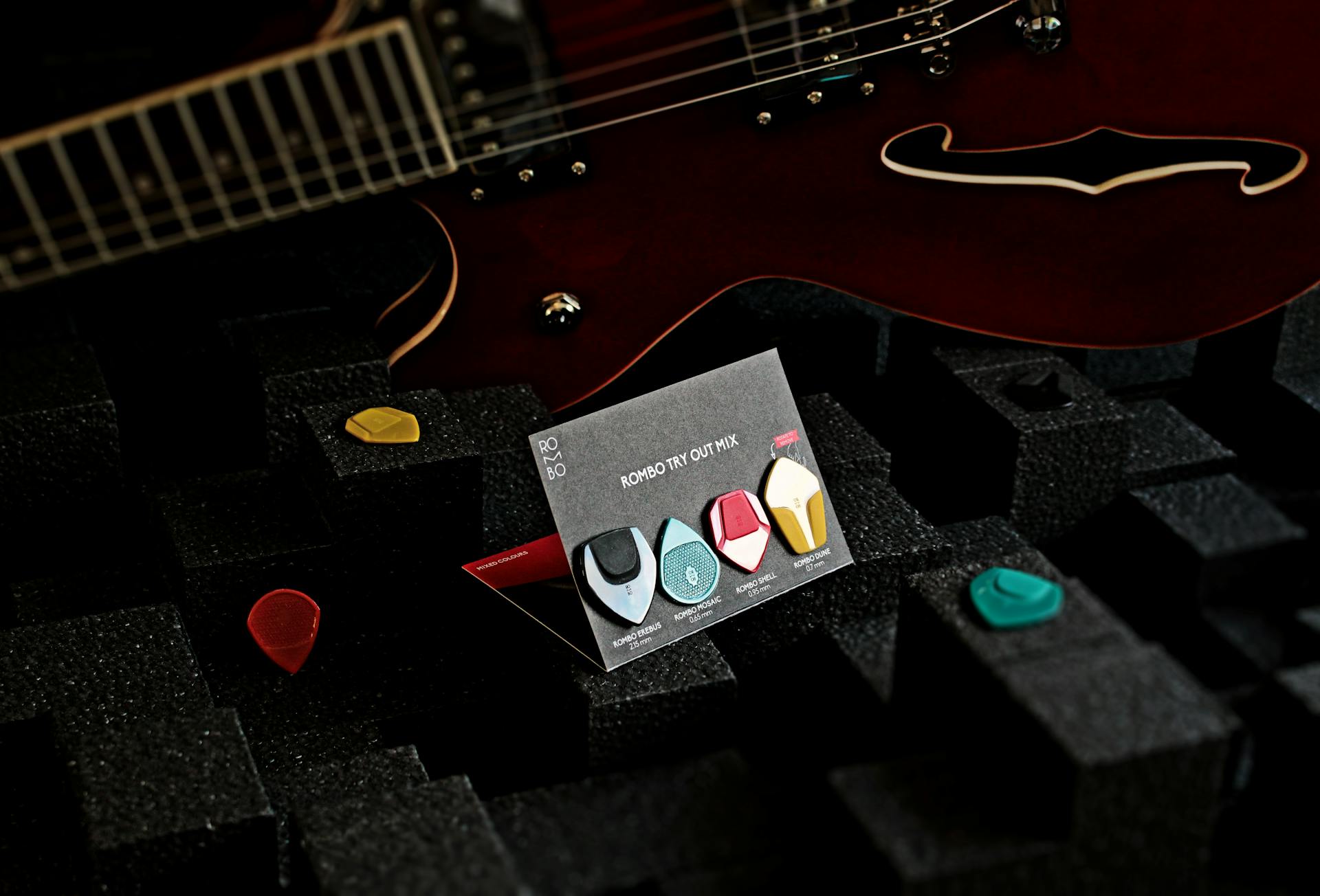
Establishing best practices in your warehouse improves efficiency and accuracy, and four warehouse picking and packing best practices to consider are planning your routes, using a successful Warehouse Management System (WMS), implementing batch picking, and using a pick-to-light system.
Wave picking combines batch and zone picking, with workers organizing orders into zones and picking all items within their zone for multiple orders during each run, reducing unnecessary travel time.
Industry experts play a pivotal role in guiding the decision-making process when businesses select a pick and pack method or kitting approach, and choosing the right pick and pack method can make a significant difference in your business's success.
A different take: Warehouse Pick Pack Work
Wave
Wave picking is a method that combines batch and zone picking to optimize order fulfillment. It's a complex but efficient strategy that can save money over time, especially for high-performing businesses with thousands of monthly orders.
By grouping orders into waves based on common characteristics such as location, product type, or order priority, warehouse workers can pick items for several orders simultaneously, streamlining the picking process and improving efficiency. This approach allows for a more organized and systematic approach to order fulfillment.
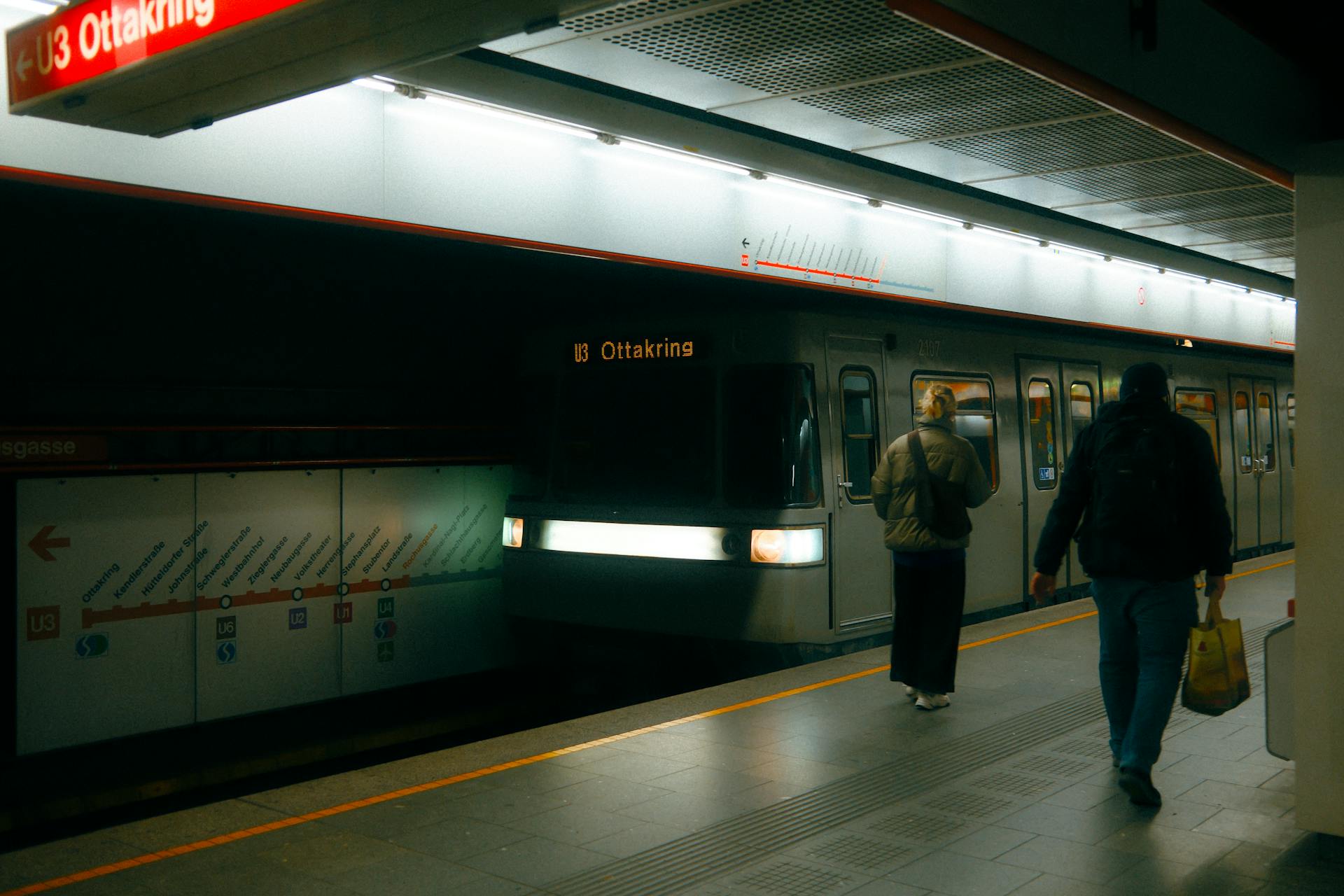
Wave picking is commonly used in distribution centers and ecommerce warehouses to handle high order volumes and diverse product assortments. It's ideal for businesses with complex operations and large SKU volumes.
The largest and most complex warehouses rely on wave picking because it offers the ideal combination of efficiency and accuracy. Workers can focus on their designated zones and complete picking runs in batches to avoid unnecessary travel time.
Here are the key characteristics of wave picking:
Wave picking is a powerful strategy for optimizing order fulfillment, but it requires careful planning and execution to ensure its benefits are fully realized.
The 4-Step Process
The 4-step pick and pack process is a crucial part of order fulfillment. The process begins when you receive an order, which is the first step in the workflow.
Your warehouse management system (WMS) creates a packing slip for each order, giving workers all the information they need to pick and pack accordingly. This includes the number of items, where they are in the warehouse, and any other specifications.
The second step is picking, where workers select the items from the warehouse based on the packing slip. Advanced warehouse picking methods, such as picking items in batches, can create speed and efficiency.
The third step is packing, where workers put the selected items into boxes or bags for shipping. A well-designed pick and pack system should match your inventory and order complexity.
The final step is shipping, where the packed orders are sent to customers. Real-time order tracking allows for communication of potential delays or issues, helping to manage customer expectations effectively.
Here is a summary of the 4-step process:
Inventory Management
Effective inventory management is crucial for a smooth pick and pack process. By grouping items by shared traits, such as turnover or packing methods, you can streamline your operations with class-based inventory management.
You can also store SKUs with the highest turnover closest to the packing station, minimizing the steps staff take when order picking. This is known as volume inventory storage.
To maximize efficiency, consider implementing storage solutions that align with your inventory's size, shape, and turnover rate. This might include storing high-volume items in easily accessible locations to save time and make picking easier for staff.
Check this out: 3pl Transportation Management System
Chaotic Inventory Management
Storing similar items together might seem logical, but it can actually cause slowdowns and errors. This is because it's easy to grab the wrong item when they look alike.
For example, if the medium black dress is next to the large black dress, it's easy to pick up the wrong one. This is especially true in a chaotic inventory management system where items are not organized in a way that promotes picking accuracy.
Piece picking, a method used in order fulfillment, involves selecting individual items one by one, which is ideal for businesses that typically ship a small volume of items. This method is commonly used in ecommerce and retail settings where orders consist of diverse products, sizes or variations.
In a chaotic inventory management system, storing items in a way that minimizes visual similarity can help prevent picking errors. For instance, storing the medium black dress near the gray baseball caps or pink sweaters can make it easier to pick the correct item.
As your ecommerce business grows, you may have to evolve your warehouse picking and packing methods to meet demand. This is because piece picking, which works well for small businesses, can become inefficient as order volume grows.
On a similar theme: Small Cargo Planes
Class-Based Inventory Management
Class-Based Inventory Management is a smart way to organize your inventory. By grouping items with shared traits, like turnover or packing methods, you can streamline your picking process and reduce errors.
You can group products that all need bubble wrap or large items that don’t require an additional box. This makes it easier to pick and pack orders efficiently.
With class-based inventory management, you can also identify slow-moving items and store them in less accessible locations, minimizing the steps staff take when order picking.
A different take: Transportation Management System Providers
Zone
Zone picking is an efficient way to manage inventory, especially in large warehouses with diverse products. This method reduces travel time and increases overall efficiency in fulfilling customer orders.
Zone picking divides the warehouse into distinct zones and assigns pickers to specific zones. Each picker focuses on their designated area, making the picking process more streamlined.
In a high-volume business, zone picking is particularly effective as it helps with speed. Pickers work specific warehouse zones, moving items across them all so items can be organized by order ahead of delivery to a packing station.
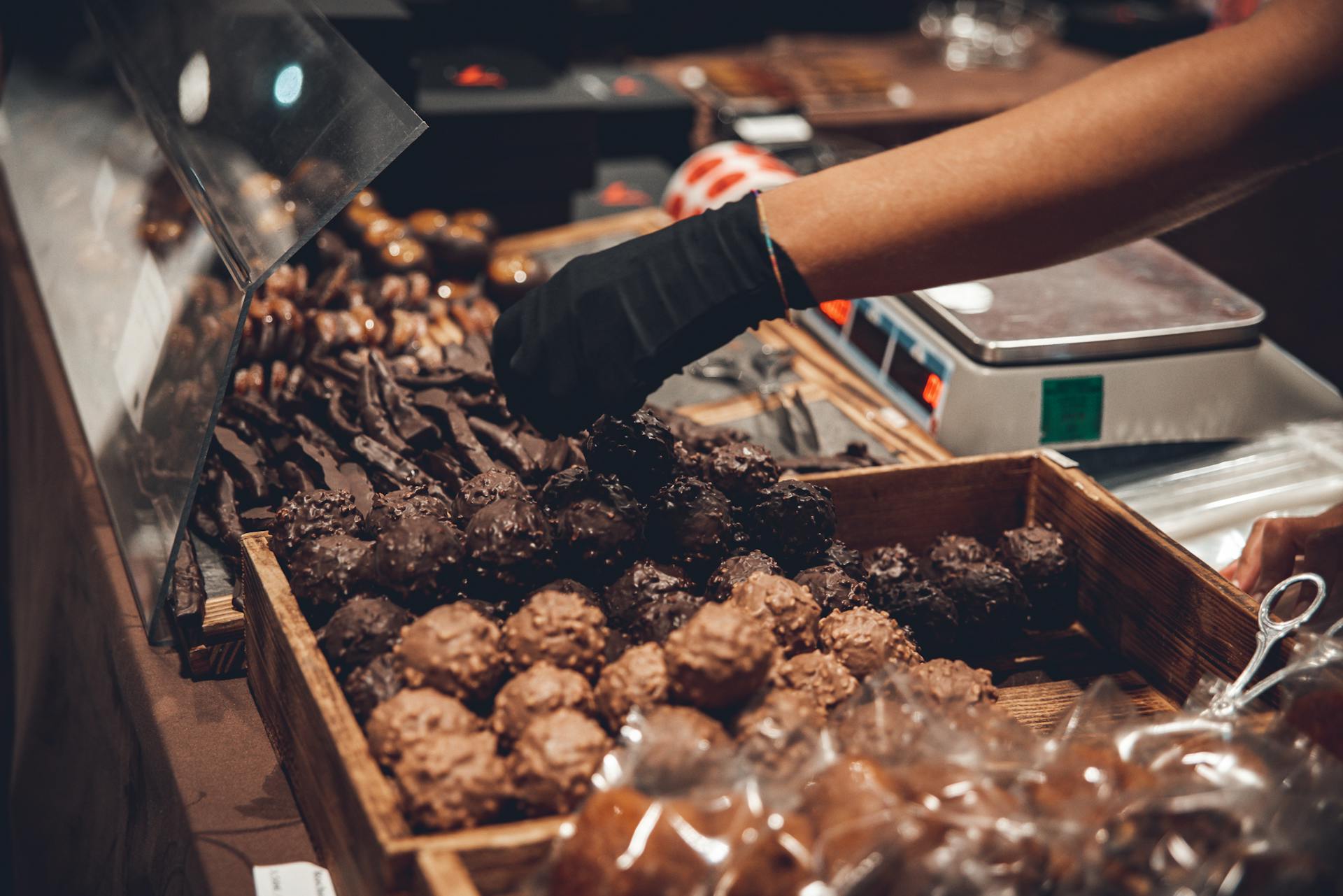
To implement zone picking, you divide the warehouse into as few or as many zones as necessary to promote efficiency. Designating each aisle as a separate zone can be a good approach in exceptionally large warehouses.
Using a Warehouse Management System (WMS) helps staff stay coordinated, especially because zone picking paths may change as inventory updates. This system is essential for businesses with a high volume of customer orders and high SKUs per order.
Zone picking optimizes the picking process by reducing travel time and increasing overall efficiency. This method is particularly effective for large warehouses with a diverse range of products.
Worth a look: High Value Cargo Transportation
Protect with Infill
Protecting your inventory with infill is a great way to prevent damage during shipping. Infill materials like shredded cardboard and packing peanuts provide cushioning and help keep items from shifting in boxes.
Shredded cardboard is a great option for smaller items, but for larger items, you may need custom infill, including molded inserts or a mix of infill types. This ensures that your items are well-protected and arrive at their destination in good condition.
Branded infill can complement branded packaging, creating a cohesive look for your shipping and receiving process. This can be especially important if you're shipping high-end or specialty items.
How Software Works
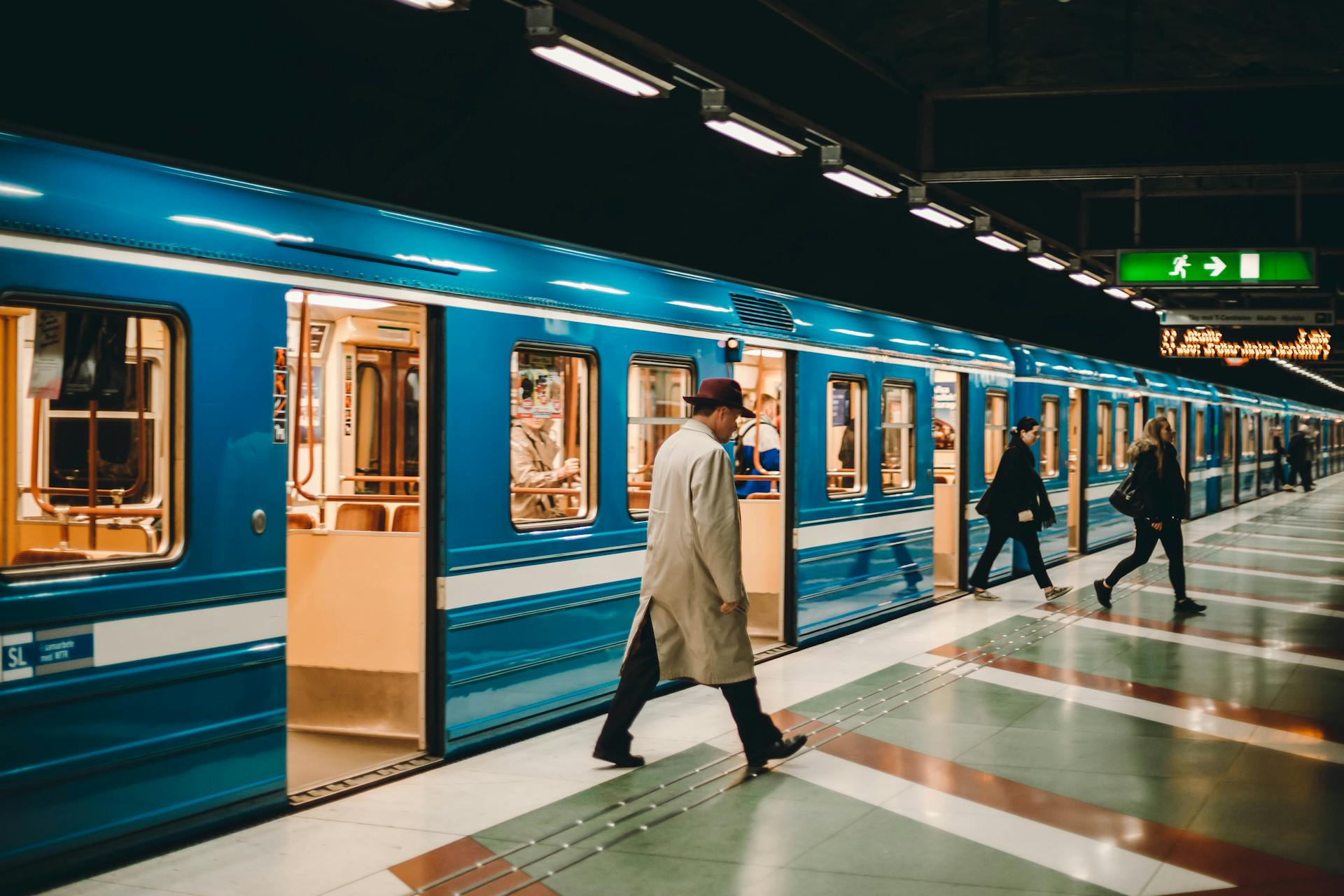
Here's how pick and pack software works its magic. It connects warehouse activity and communication by integrating with sales channels to receive new orders.
The software then assigns picking lists and optimized paths to staff on mobile devices, allowing them to see item details, locations, and quantities in real-time. This helps team members monitor pick completion progress and identify potential bottlenecks to adjust workflows as needed.
Picked items are scanned, and packing tasks are assigned based on weight, size, and order requirements. Packers receive alerts for missing or incorrect items, allowing for immediate intervention and error correction.
Shipping labels are generated with accurate weight and address information, streamlining the dispatch process. Teams can track shipped orders in real-time, providing updates to customers and improving communication.
Here's a breakdown of the pick and pack process:
- Order integration: Software connects to sales channels and receives new orders.
- Picking: Staff receive picking lists and optimized paths on mobile devices.
- Packing: Picked items are scanned, and packing tasks are assigned based on weight, size, and order requirements.
- Shipping: The software generates shipping labels with accurate weight and address information.
This connectivity provided by warehouse management software acts as a source of truth for workflow progress and automates certain tasks, like picking assignments, order status, and other aspects of communication. This helps ensure smooth operations during growth phases, and integrated data systems can readily adapt to fluctuating order volumes and product offerings.
Order Management Process
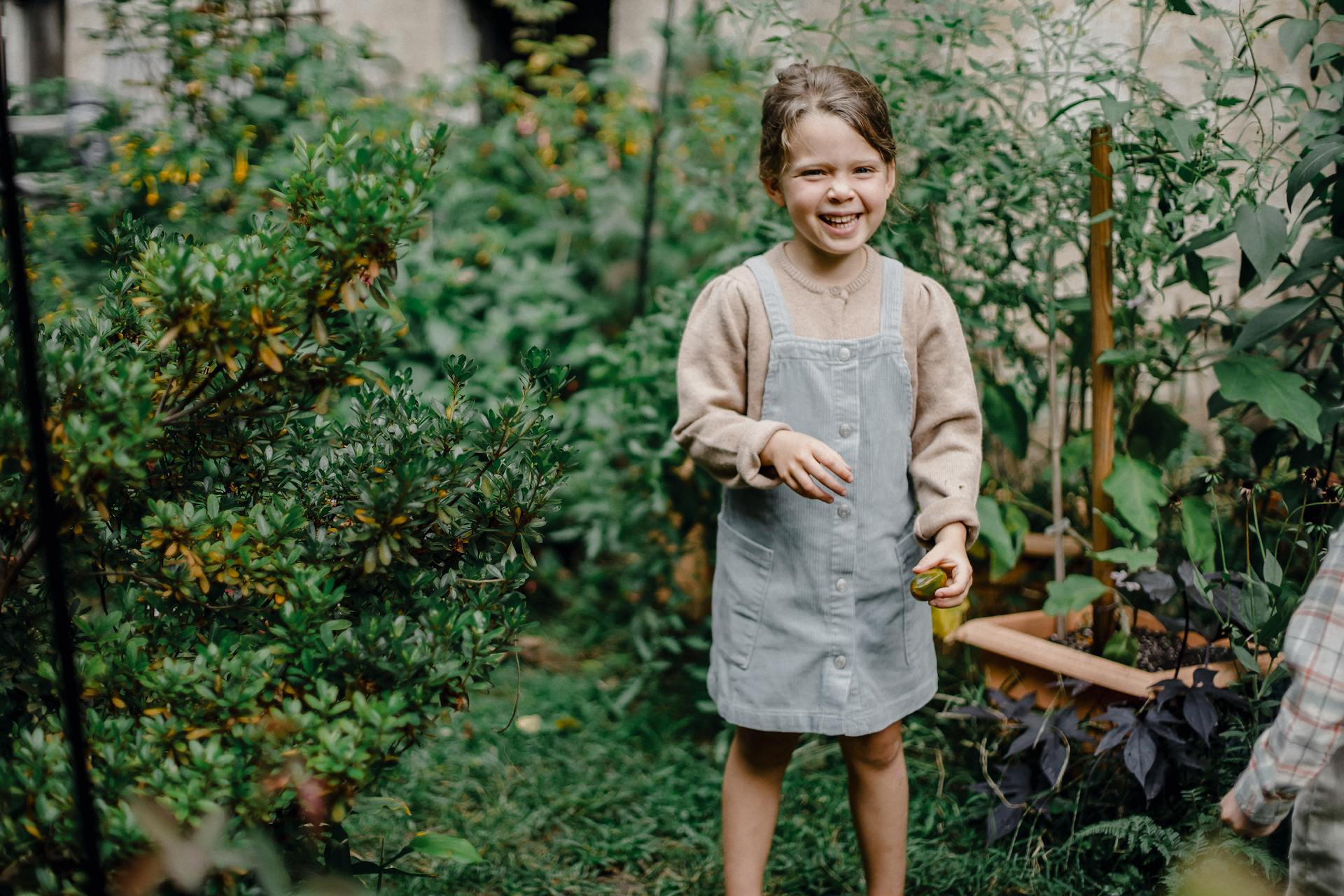
The order management process is a critical component of the pick and pack workflow. It involves receiving, processing, and fulfilling customer orders in a seamless manner.
The Order Management System (OMS) process begins with order creation, where customer requests are captured through various channels. The OMS then orchestrates order processing, verifying product availability, determining optimal fulfillment locations, and updating inventory levels in real-time.
Real-time order tracking allows for communication of potential delays or issues, helping to manage customer expectations effectively. This is especially important for businesses that want to provide a seamless customer experience.
A well-designed OMS can centralize and automate order-related tasks, optimizing the end-to-end order lifecycle, including the returns process. This can help businesses reduce labor costs, decrease shipping costs, and increase visibility throughout the order management process.
Here are some key benefits of using an OMS:
- Faster fulfillment: An OMS can analyze your inventory locations and determine the quickest route for shipping.
- Decreased labor costs: An effective OMS can automate tasks and reduce labor hours previously devoted to order fulfillment.
- Decreased shipping costs: An OMS can help you find the most cost-effective and fastest method for getting your orders to your customers.
- Less redundant data entry: An OMS can reduce the need for duplicate data entry, which can lead to errors.
- Increased visibility: An OMS can provide real-time tracking and updates throughout the order management process.
- Data analysis: An OMS can analyze your data to determine how you can improve your operations and make data-driven decisions.
By implementing an effective OMS, businesses can streamline their order management process, improve customer satisfaction, and increase efficiency throughout their operations.
Benefits and Best Practices
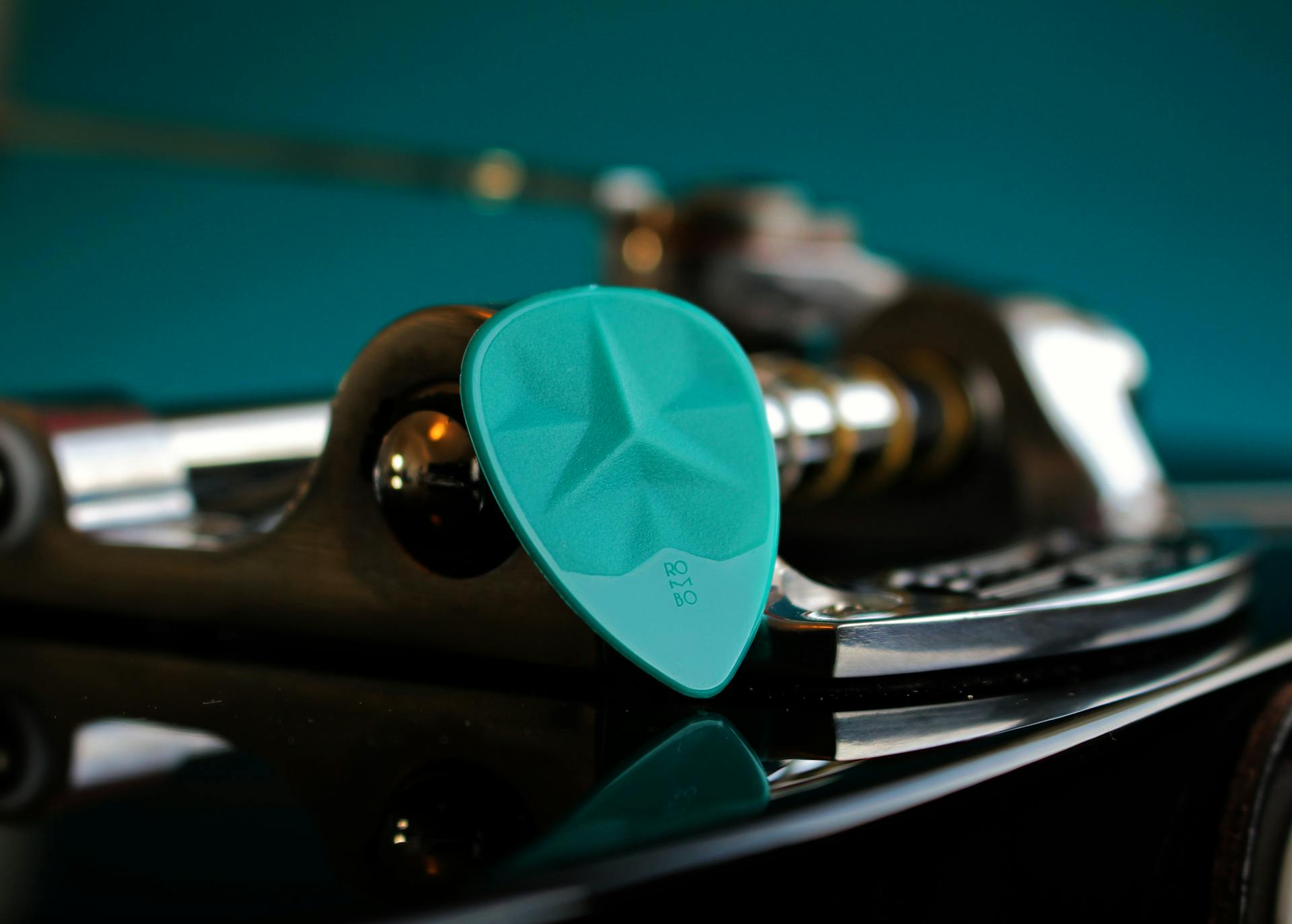
Using a pick and pack system and OMS offers significant advantages, including faster fulfillment, decreased labor costs, and decreased shipping costs.
An effective OMS can analyze your inventory locations and determine the quickest route, automatically shipping an order from the closest warehouse. This can save you time and money by optimizing your warehouse pick-pack-ship management.
Here are some benefits of implementing a pick and pack system:
- Faster fulfillment
- Decreased labor costs
- Decreased shipping costs
- Reduce excess inventory
- Less redundant data entry
- Increased visibility
- Data analysis
Pick and Process Benefits
Using a pick and pack system and OMS offers significant advantages, including faster fulfillment and reduced labor costs. An effective system can automate tasks and reduce labor hours previously devoted to order fulfillment, freeing up staff to handle tasks that generate additional revenue.
Faster fulfillment is achieved through analyzing inventory locations and determining the quickest route to ship an order from the closest warehouse. This can also help identify bottlenecks in the supply chain that may be slowing you down.
Decreased shipping costs are another benefit, as an OMS can automatically find the most cost-effective and fastest method for getting orders to customers. This is achieved by distributing from the closest locations.
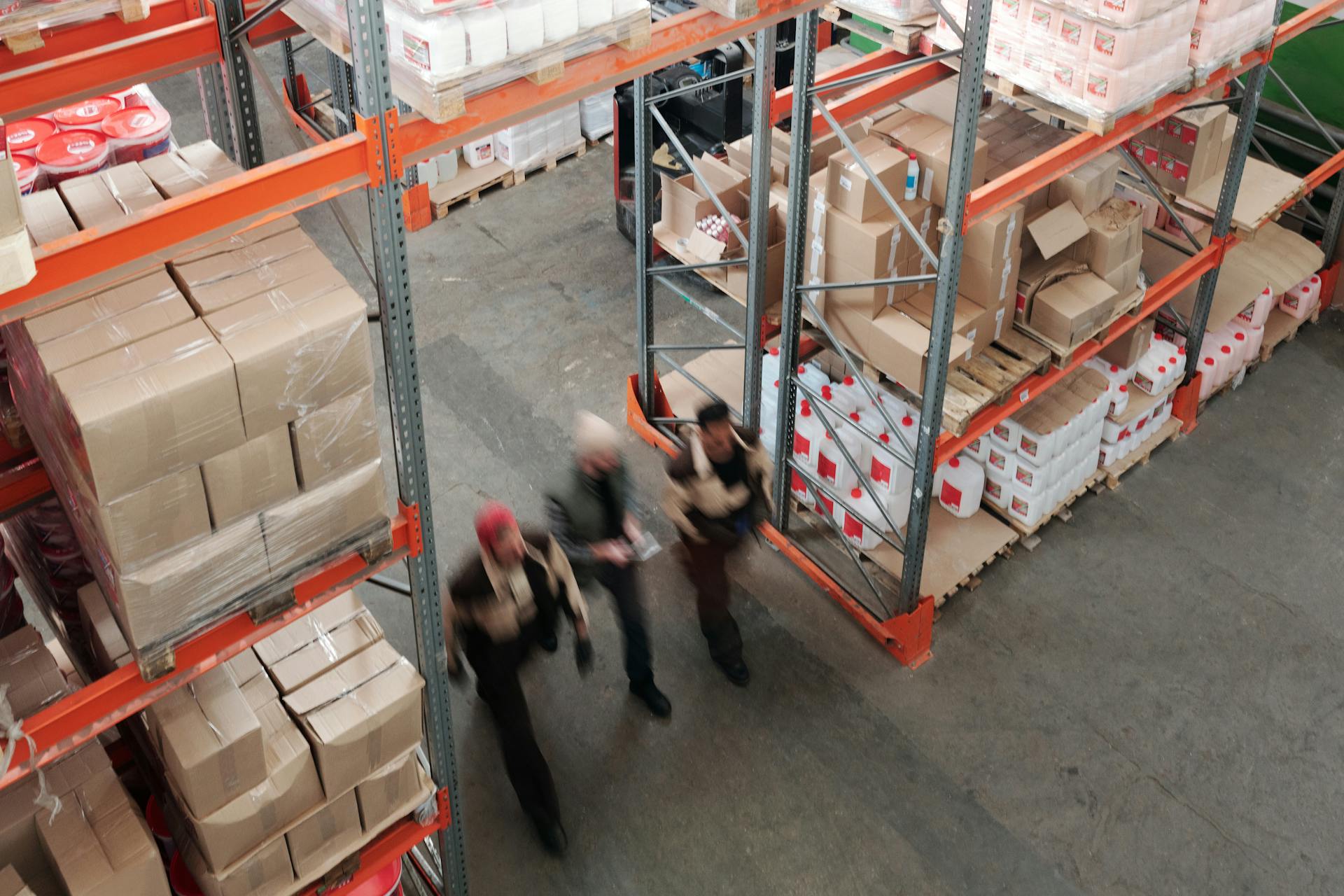
Reducing excess inventory is also possible with an OMS, which can significantly reduce the need for excess stock on hand. This means you can rest easy knowing that orders received from any channel can be fulfilled without keeping too much stock on hand.
Here are some key benefits of using a pick and pack system and OMS:
- Faster fulfillment
- Decreased labor costs
- Decreased shipping costs
- Reduce excess inventory
- Less redundant data entry
- Increased visibility
- Data analysis
Data analysis is also a key benefit, as an OMS can analyze your data to determine how to improve operations. This can include identifying sales patterns, tracking KPIs, and forecasting sales and inventory levels.
Order Best Practices
Having the right processes in place for order packing can make a huge difference in customer satisfaction. This is a last chance for warehouse packing teams to check picking accuracy, ensuring the right quantities of the right items go in the box before it's sealed and shipped.
Accuracy at this stage can help reduce the risk of returns, which can be costly and disappointing for customers. Returns incur reverse logistics and restocking costs, so it's essential to get it right.
Expand your knowledge: Order Picking Accuracy
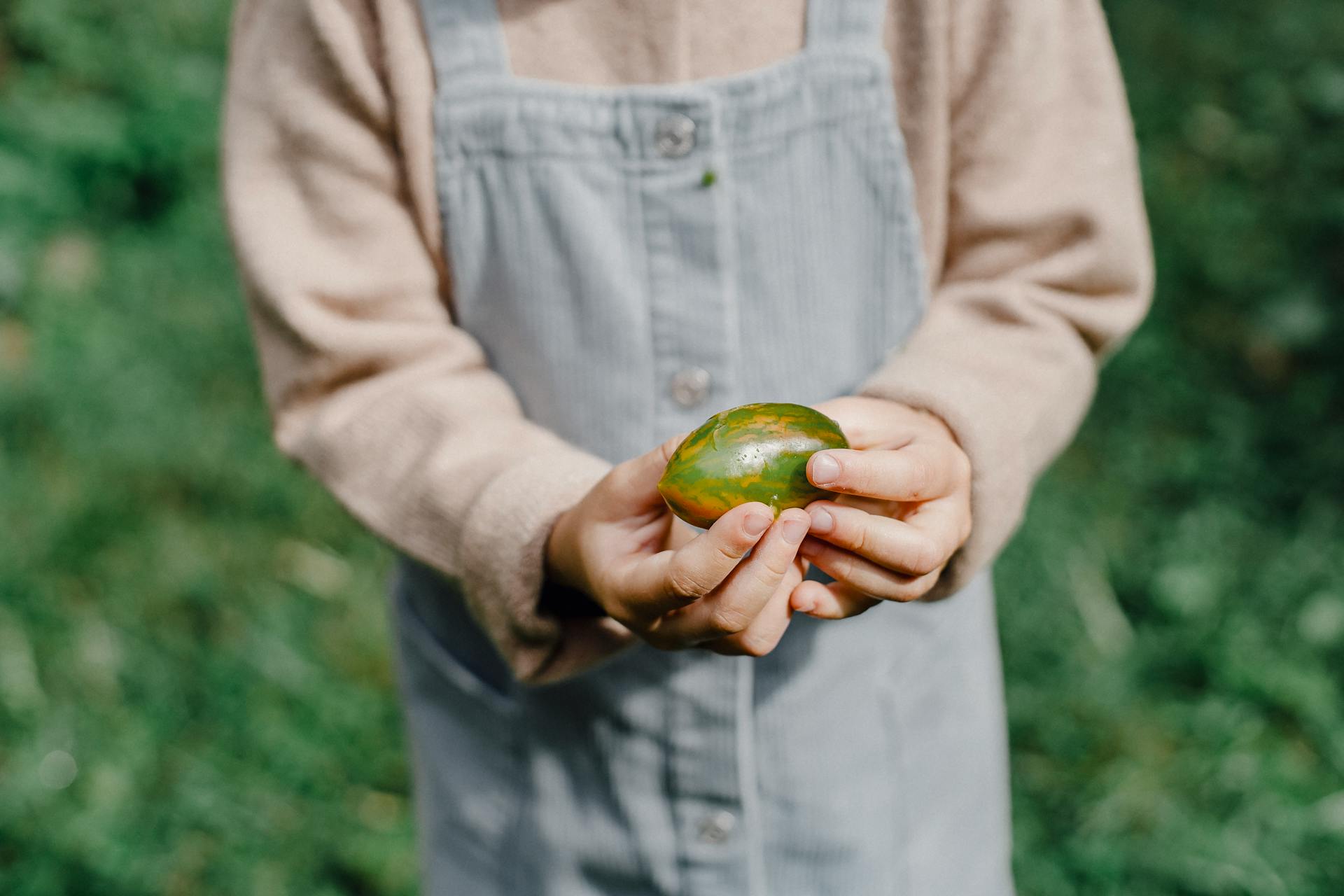
Establishing best practices in your warehouse is crucial for efficiency and accuracy. By implementing strategies like checking picking accuracy, you can optimize your pick and pack service for a streamlined fulfillment process.
Real-time order tracking allows for communication of potential delays or issues, helping to manage customer expectations effectively. This can prevent disappointed customers and maintain a positive brand reputation.
Fulfillment is the backbone of your brand's operations, ensuring that products are delivered to customers efficiently. By prioritizing order packing best practices, you can ensure that your products reach customers quickly and accurately.
Shipping and Logistics
Shipping is the final step in the pick and pack process, where the team sorts and labels orders for dispatch.
It's essential to work with reliable carriers that balance cost, speed, and reliability. This can be a challenge, but it's crucial for meeting customer expectations.
Parcel costs can account for as much as 70% of your total fulfillment costs, so it's vital to manage them closely.
To avoid straining your customer support, make sure you have a system for tracking packages and giving customers updates on when their orders will arrive.
Fulfillment Solutions
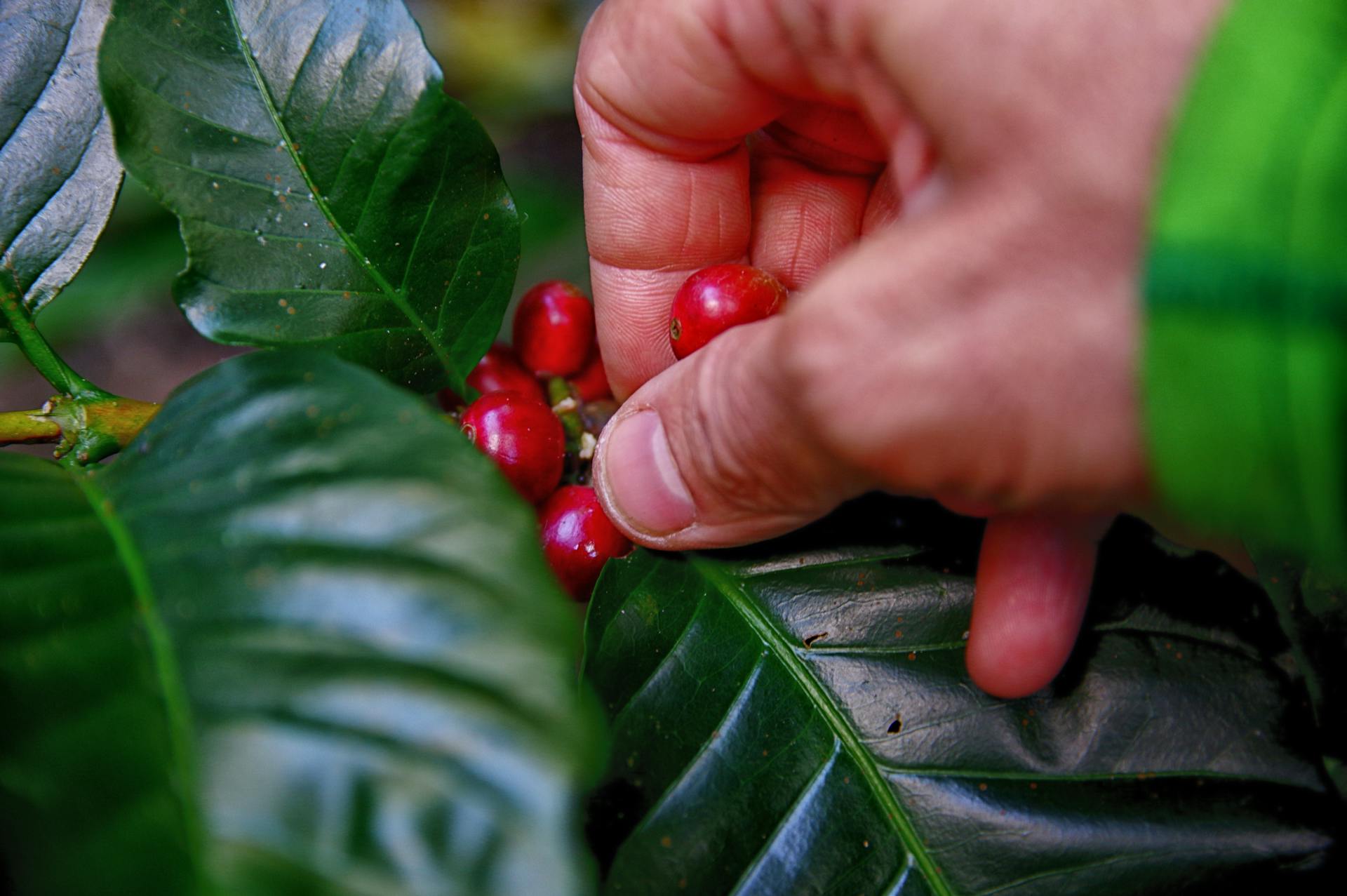
Fulfillment is the backbone of your brand's operations, ensuring that products are delivered to customers efficiently. It's a critical aspect of e-commerce that requires careful planning and execution.
Industry experts agree that finding one fulfillment solution that caters to all of your business's needs is not an easy task, especially if you're a growing business.
A 3PL (third-party logistics) provider can offer several advantages over in-house fulfillment, including expertise, scalability, and cost savings. Partnering with a 3PL can help you streamline your operations and improve customer satisfaction.
There are several options to consider when choosing a fulfillment solution, including pick and pack, kitting, and value-added services. Kitting is particularly useful for businesses that want to customize their customer experience by adding a unique unboxing experience.
Kitting involves packaging multiple items together, and it's perfect for subscription boxes or companies that frequently change their bundles to inspire new sales. This approach can help you stand out in a crowded market and build customer loyalty.
A fresh viewpoint: 3pl Pick and Pack
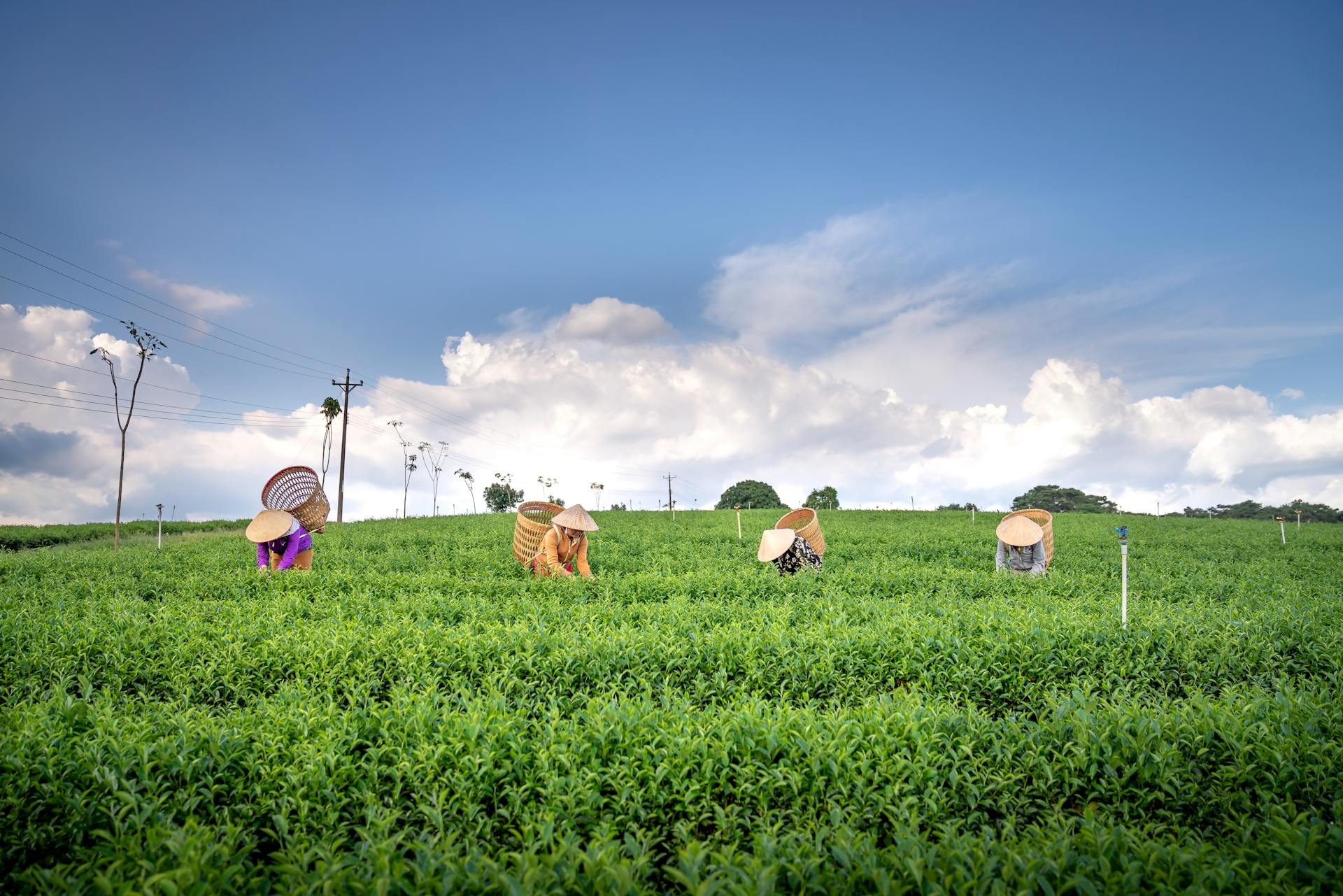
If you're looking to fulfill orders on the East Coast, consider partnering with a provider that has a strong presence in the region. Kanban Logistics, for example, offers pick and pack services from their logistics campuses in Eastern North Carolina.
Here are some key benefits of partnering with a provider like Kanban:
- Process design to minimize labor and per-order fulfillment costs
- Value-added services such as kitting, packaging, and product rework
- Quality checks to ensure accuracy and avoid returns
Ultimately, the right fulfillment solution will depend on your business needs and goals. Be sure to research your options and choose a provider that can help you deliver exceptional customer experiences.
Cost-Efficiency and Scalability
Outsourcing pick and pack services can be a cost-effective solution for businesses of all sizes. This approach allows companies to focus on their core business while leaving the intricacies of order fulfillment to specialists.
Streamlining your order fulfillment and inventory management processes can be achieved by automating and increasing the efficiency of your fulfillment process, which can be done using a pick and pack system.
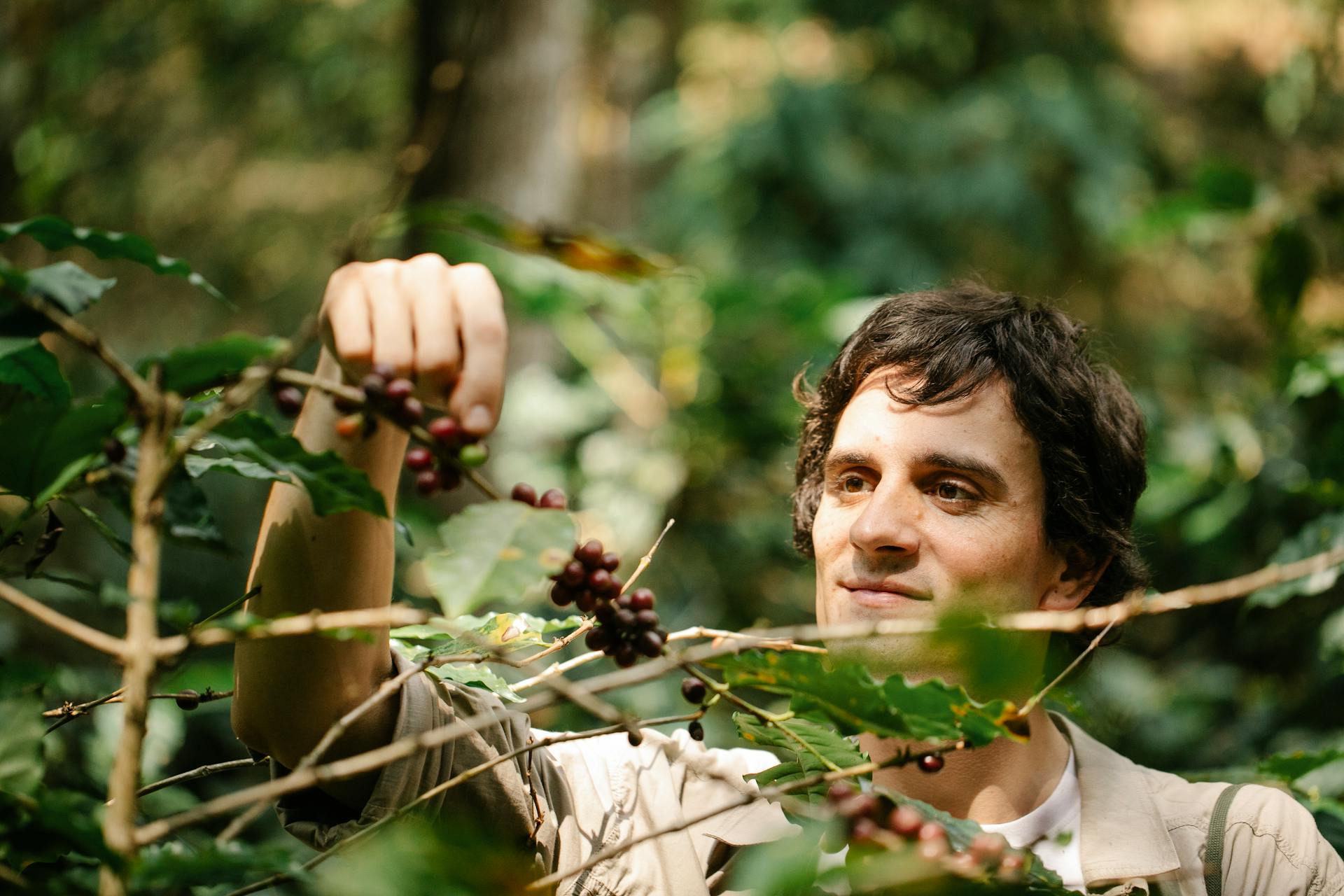
By relying on the expertise of a fulfillment provider, companies can maintain accuracy and guard against stock outs, which is crucial for maintaining a positive customer experience.
Implementing a warehouse management system can improve order fulfillment efficiency by tracking inventory, planning routes, and communicating information every minute. This can help reduce the risk of stock outs and improve customer satisfaction.
Outsourced pick and pack services tend to be very scalable, accommodating fluctuations in demand with ease and then ratcheting back manpower as volume dissipates. This helps your fulfillment costs parallel your revenue stream.
Kitting
Kitting is a specialized kind of pick and pack service that involves assembling various SKUs into a single SKU to create a subscription pack or promotional bundle. This requires adjusting warehouse packing techniques monthly or as new promotions arise.
In a kitting service, multiple different items are combined into a single box to make a unique SKU. This package can be shipped right away or kept as a new SKU for shipment at a later time.
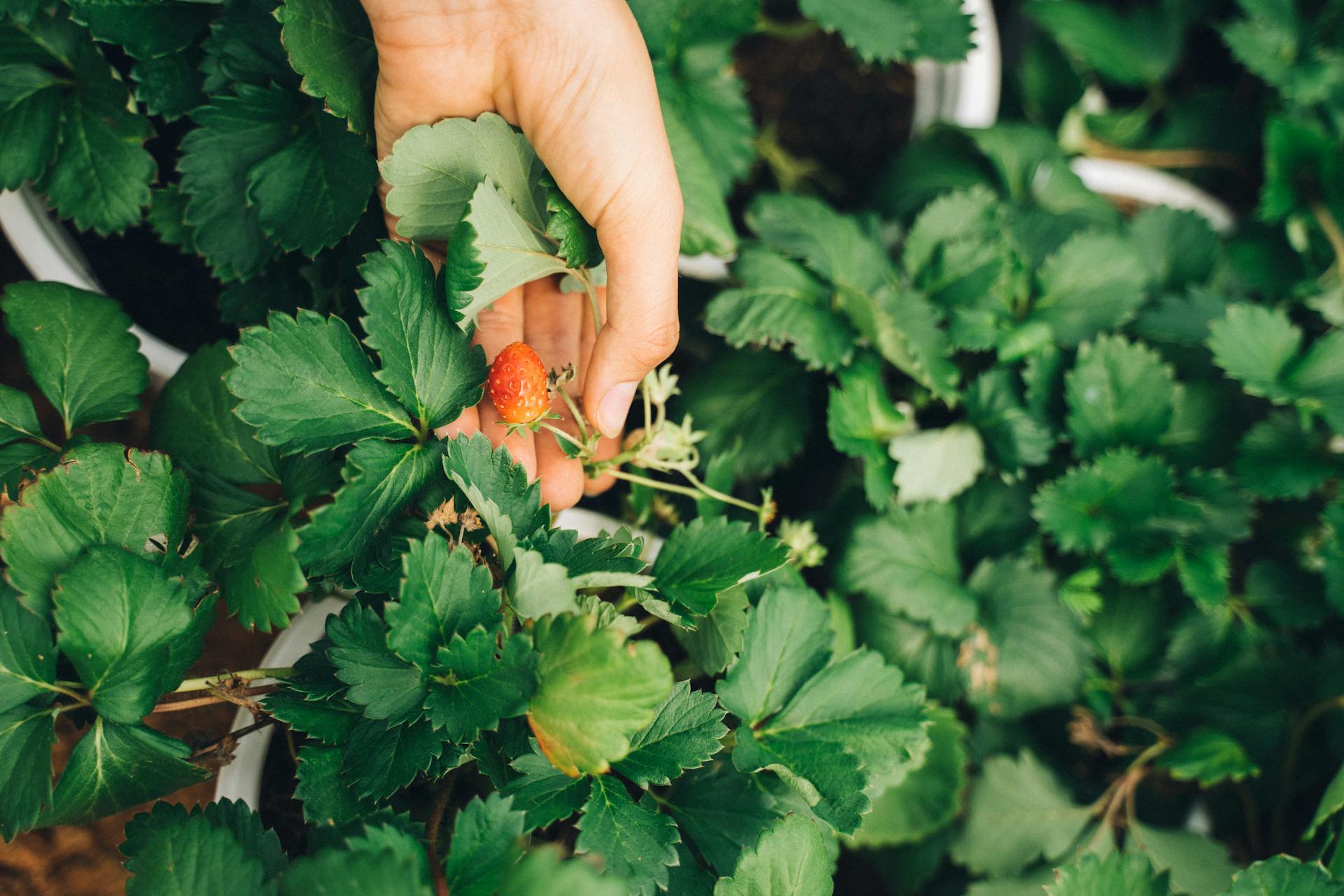
Kitting is often used for marketing or convenience, and package customization and add-ons are popular reasons for companies to turn to kitting services. Many promotional product kits, such as new hire kits, are fulfilled this way.
Some common kit customization capabilities include adding customized thank-you notes with customer's names, custom product labels, and print and pack promotions and coupons.
Frequently Asked Questions
Is pick packer a hard job?
Yes, pick packing can be physically demanding, especially on the back, due to frequent bending and reaching. Consider jobs with OPU trucks or explore other options in your field to minimize the strain.
What is the average pick and pack fee?
The average pick and pack fee is between $0.20 and $5.00 per item, varying by fulfillment center. Understanding these costs can help you optimize your shipping strategy and save on fulfillment expenses.
What does a pick and packer do?
A Pick and Packer selects items from a warehouse and packs them into orders for shipping, ensuring accurate and efficient order fulfillment. Their role is crucial in getting products from storage to customers quickly and reliably.
Sources
- https://redstagfulfillment.com/ultimate-guide-pick-and-pack-methods/
- https://cart.com/blog/what-is-pick-pack-and-ship
- https://www.fishbowlinventory.com/blog/warehouse-picking-and-packing-everything-you-need-to-know
- https://kanbanlogistics.com/blog/what-are-pick-and-pack-services
- https://www.brprinters.com/pick-and-pack-vs-kitting/
Featured Images: pexels.com