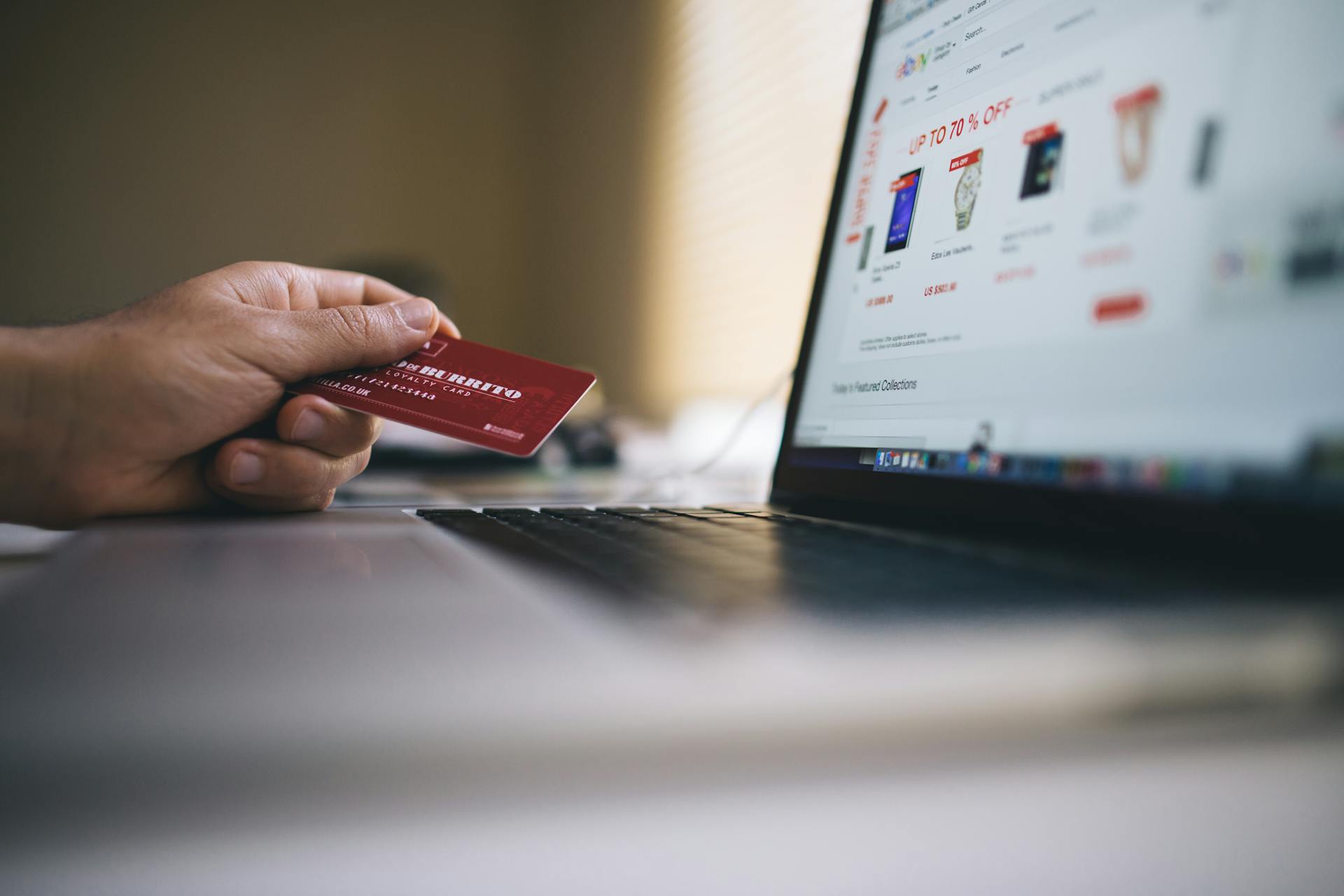
To achieve ecommerce pick and pack success, you need to optimize your warehouse operations. A well-designed pick and pack system can significantly improve order fulfillment efficiency.
A key strategy is to implement a zone picking system, which involves dividing the warehouse into separate zones for different product categories. This approach can reduce travel time and increase productivity by up to 30%.
By streamlining your pick and pack process, you can also reduce errors and improve customer satisfaction. According to a study, a 1% reduction in error rates can lead to a 10% increase in customer satisfaction.
Investing in the right technology, such as automated storage and retrieval systems, can also help optimize your pick and pack operations. These systems can reduce manual labor and increase accuracy by up to 99%.
If this caught your attention, see: Order Picking Systems
Ecommerce Pick and Pack Strategies
Ecommerce Pick and Pack Strategies can be streamlined to reduce costs. A key part of this is reducing the labor required for picking the right products for an order.
To achieve this, warehouses use various pick methods such as piece picking, batch picking, zone picking, and wave picking. These methods help minimize labor costs and increase efficiency.
The optimal pick method depends on the number of orders received daily. This means that different businesses may need to try out different methods to find what works best for them.
A simple pick and pack system can be implemented initially, but as the business grows, it's essential to consider variables to optimize efficiency. This can help reduce mistakes and conserve resources.
Suggestion: Order Picking Methods
Order Management
Order Management is crucial for ecommerce pick and pack operations. An Order Management System (OMS) is the central hub that handles orders from all sales channels, including websites, marketplaces, and social media platforms.
An OMS helps organize, automate, and optimize the purchase to fulfillment workflow, ensuring that orders are processed efficiently. It finds the best way to pick, pack, and ship orders and provides real-time tracking and visibility across the entire order lifecycle.
By integrating with various channels, an OMS ensures consistency in order fulfillment, reducing errors and minimizing delays. It also empowers businesses to make data-driven decisions, optimize inventory levels, and adapt to changing market demands.
Here are some key benefits of using an OMS:
- Streamlined order processing
- Improved inventory management
- Enhanced customer satisfaction
- Increased operational efficiency
Orders
Orders are the lifeblood of any business, and managing them efficiently is crucial for success. An Order Management System (OMS) is the heart of an efficient pick-pack-ship process, serving as a centralized hub to handle orders from all sales channels.
There are various picking methods, including piece picking, batch picking, zone order picking, and wave picking. Each method has its own advantages and disadvantages, and the right one for your business will depend on your specific needs and operations.
Piece picking is a common method where employees hand-pick each product for an entire order as they come in. This method can be time-consuming, but it's often used for small orders or when products are stored in a small area.
Worth a look: Small Blister Pack Machine
Batch picking is similar to piece picking, but orders are done in batches all at once. This method can be more efficient than piece picking, but it requires a larger storage area and more complex inventory management.
Zone order picking is another method where employees are assigned to a specific area of the warehouse and only pick one order at a time within that area. If an order needs products from more than one zone, it's handed off via conveyor belt.
Wave picking is a combination of batch and zone picking, where employees stay within a zone but pick more than one order at a time. This method is often used for high-volume orders and can be more efficient than batch picking.
To reduce shipping costs and maintain order accuracy, packing should keep an order within the smallest number of boxes and use the right type of packing material(s) for each product.
Here are some common picking methods:
An OMS platform can help you find the best way to pick, pack, and ship your orders, giving you insight into every step of the process. By integrating with various channels, an OMS ensures consistency in order fulfillment, reducing errors and minimizing delays.
Batch
Batch picking is an order fulfillment strategy where multiple orders are picked together in a single trip through a warehouse or fulfillment center. This method improves efficiency by reducing travel time and maximizing productivity.
Warehouse workers gather items for several orders simultaneously, organizing them into batches. Batch picking is widely used in ecommerce and distribution centers.
Fulfillment software (WMS/OMS) is essential if you're using this method. It helps streamline the picking process and enhance overall order fulfillment speed and accuracy.
For another approach, see: Pick Pack and Ship Warehouse
Warehouse Services
Warehouse services play a crucial role in the ecommerce pick and pack process. They help streamline operations, ensuring that products are delivered to customers efficiently.
You can outsource your warehouse services to a 3PL provider, which will store, pick, pack, and ship products on your behalf. This can save you time, money, and efforts.
A dedicated fulfillment site takeover can help you optimize your profits and boost customer satisfaction. This involves partnering with a 3PL provider that has the technology and expertise to grow your business.
A unique perspective: Warehouse Pick Pack Work
The pick and pack workflow is a fundamental process within the logistics and ecommerce ecosystem. It includes the following steps: Receive order, Pick order, Pack order, and Ship order.
Here's a breakdown of the pick and pack workflow:
- Receive order: A packing slip is automatically generated in the warehouse when a customer places an order.
- Pick order: A picker sources the product from the warehouse using the packing slip.
- Pack order: The packer sorts items into orders, packs them into the appropriate packing material, and labels them for shipping.
- Ship order: Your packages will be picked up by the carrier and tracked until they reach your customers.
By outsourcing your warehouse services and implementing a efficient pick and pack workflow, you can improve your ecommerce operations and deliver better customer experiences.
Packaging and Shipping
You can keep your branded packaging, and we'll use it to create a seamless unboxing experience for your customers.
We'll store your inventory for you, so you don't need to rent space to stock it.
You'll be able to track your inventory levels in real-time, without having to employ someone to do it for you.
We'll handle boxing, labeling, and finding the shipping carrier, so you can focus on other tasks.
By partnering with us, you'll gain access to the technology and expertise needed to grow your business.
Benefits and Best Practices
Ecommerce pick and pack can be a game-changer for businesses looking to streamline their order fulfillment process. By adopting pick and pack fulfillment, you can expect to see greater efficiency in your operations.
Pick and pack is a flexible and scalable fulfillment method that can meet seasonal demands and support promotional campaigns. This is because it optimizes efficiency, reducing handling times and enabling faster order processing and delivery.
One of the key benefits of pick and pack is that it focuses on carefully retrieving and packaging individual orders, which reduces the risk of errors. This is achieved through barcode scanning and other technology that verifies item accuracy.
Pick and pack also offers real-time visibility into available inventory, allowing for accurate tracking of stock levels and enabling businesses to maintain optimal inventory levels. This is made possible by updating inventory management systems as items are picked for orders.
By adopting pick and pack, businesses can reduce the risk of costly returns, lower their carrying costs, and improve resource utilization. This is achieved through operational efficiency enhancements, such as systematically organizing products and optimizing warehouse layout.
Pick and pack fulfillment also provides customization options, such as adding special designs or details to packages to enhance brand recognition. This can be achieved through customized packaging services offered by third-party logistics companies.
Here are some key benefits of ecommerce pick and pack:
- Greater efficiency
- Fewer errors
- Optimized inventory
- Cost-savings
- Customization options
Shipping Process
The shipping process is a crucial step in the ecommerce pick and pack workflow. It's where the packages are handed over to the shipping carrier for delivery to the customer.
Warehouse staff typically use handheld scanners or picking carts to efficiently gather the required items. This is done during the Order Retrieval (Pick) step of the Pick and Pack process.
Once the packages are properly labeled and documented, they are handed over to the shipping carrier for delivery to the customer. This step may also involve updating the order status and providing tracking information to the customer.
The shipping carrier will take care of the rest, but it's essential to make sure the packages are accurately labeled and documented. This includes printing shipping labels with the customer's address and order details.
Here's a breakdown of the shipping process steps:
- Shipping and Dispatch: The final step in the Pick and Pack process involves shipping and dispatching the packages to their respective destinations.
- Documentation and Labeling: As part of the Pick and Pack process, appropriate documentation and labeling are generated for each package.
Accurate labeling is important for making sure that packages are delivered to the correct recipients and that all necessary information is provided to the shipping carrier. This helps ensure a smooth delivery process and prevents any potential issues.
Scaling and Outsourcing
Scaling your ecommerce business can be a daunting task, especially when it comes to pick and pack services. Outsourcing to a 3PL (third-party logistics) provider can save you time, money, and efforts.
You don't have to rent space to stock inventory, which can be a huge cost savings. By partnering with a 3PL, you can focus on more productive tasks.
Streamlining your order fulfillment and inventory management processes is crucial for providing a great customer experience. Omnichannel fulfillment is often one of the biggest challenges that brands must handle.
Automating and increasing the efficiency of your fulfillment process can be achieved by using a pick and pack system. This will give you the transparency, reliability, and speed required to get packages to your customers swiftly and accurately.
Outsourcing your pick and pack services can provide you with access to a range of pick-and-pack fulfillment strategies, including piece picking, batch picking, and zone picking.
Worth a look: Pick up Pack and Ship Services
Understanding Ecommerce Services
Ecommerce fulfillment services are crucial for efficiently delivering products to customers. Our pick and pack services have been widely used by clients due to various reasons.
We employ a range of pick-and-pack fulfillment strategies to fulfill orders, including piece picking, batch picking, and zone picking. Picking strategies help us efficiently pick and pack orders.
We can pack products in the right boxes to ensure their visual appeal and safety. If required, we can line the boxes with air pillows or other liners to protect the product stored inside.
By partnering with a 3PL provider, you can save time, money, and efforts, and focus on more productive tasks. You don't have to rent space to stock inventory or track inventory levels.
We can provide custom pick and pack services specially customized to meet your order fulfillment requirements. Our warehouse management and order fulfillment software can be integrated with sales channels for effective results.
Take a look at this: Pick and Pack Fulfillment Center
Frequently Asked Questions
What is the average pick and pack fee?
The average pick and pack fee is around $2.50, but can range from $0.20 to $5.00 depending on the fulfillment center. This fee can add up quickly when shipping multiple items in one order.
What is pick and pack at Amazon?
At Amazon, "pick and pack" refers to the process of retrieving and packaging products from our fulfillment centers for shipping. This fee covers the costs of locating, retrieving, and preparing your items for delivery.
What does eCommerce packaging mean?
eCommerce packaging refers to specially designed packaging for shipping goods to individual consumers, typically more attractive and durable than retail packaging. It's designed to withstand the delivery process and make a great first impression on customers.
Featured Images: pexels.com