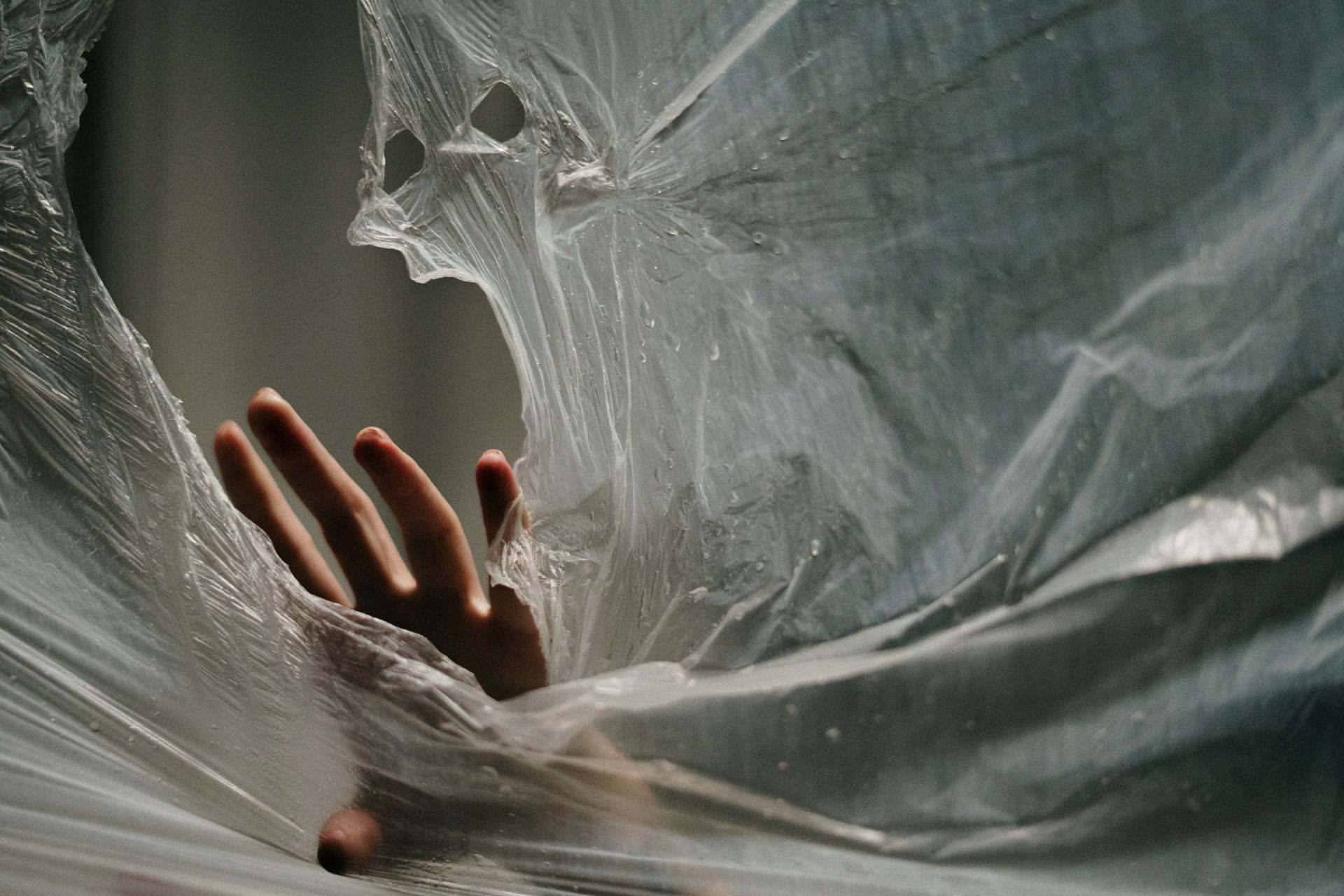
Vacuform plastic sheets are incredibly versatile and can be used in a wide range of applications and industries. They are particularly useful for creating custom parts and products with complex shapes and designs.
From automotive trim and moldings to medical devices and equipment, vacuform plastic sheets are used to create parts that require precision and accuracy. For example, they can be used to make dashboards, door panels, and other interior components for cars.
In the medical field, vacuform plastic sheets are used to create custom trays, containers, and other equipment that require precise dimensions and smooth surfaces. Their durability and resistance to chemicals make them ideal for use in medical settings.
Vacuform plastic sheets can also be used in the construction industry to create custom parts for building and renovation projects, such as window frames and door components.
For your interest: Vacuform Machine
Description and Features
Vacuum Form Plastic Sheets are sheets of plastic that have been heated and flattened under a vacuum. They can be cut into any shape and are typically used in the manufacturing of car parts, packaging for products, and clothing.
Curious to learn more? Check out: Plastic Bags Vacuum Packaging
These sheets are made to be durable and long-lasting, with a maximum width of 2200 mm. They are perfect for industries that require precision and accuracy in their products.
The sheets come in various colors, making them easy to see from across the factory. This feature is especially useful in high-volume production settings where visibility is crucial.
Some sheets are designed to fit around rollers, allowing them to be easily inserted into a vacuum-forming machine. This feature streamlines the manufacturing process and reduces production time.
Thermoformed plastic sheets can have a liner surface to prevent rough edges and improve the overall look of the final product. This is especially important in industries where aesthetics are crucial, such as the food industry.
To ensure high-quality sheets, look for the following characteristics:
- They should withstand a long shelf life (at least one year).
- They should be free of crumbs and dirt, and they should not be brittle or break apart easily.
Advantages and Applications
Vacuum-form plastic sheets have numerous advantages and applications. They are lightweight, strong, and have a smooth surface that resists scratching.
Their durability is impressive, as they can be folded and cut easily without any creases or sharp edges. They also don't contain any harmful substances that might cause damage to your skin.
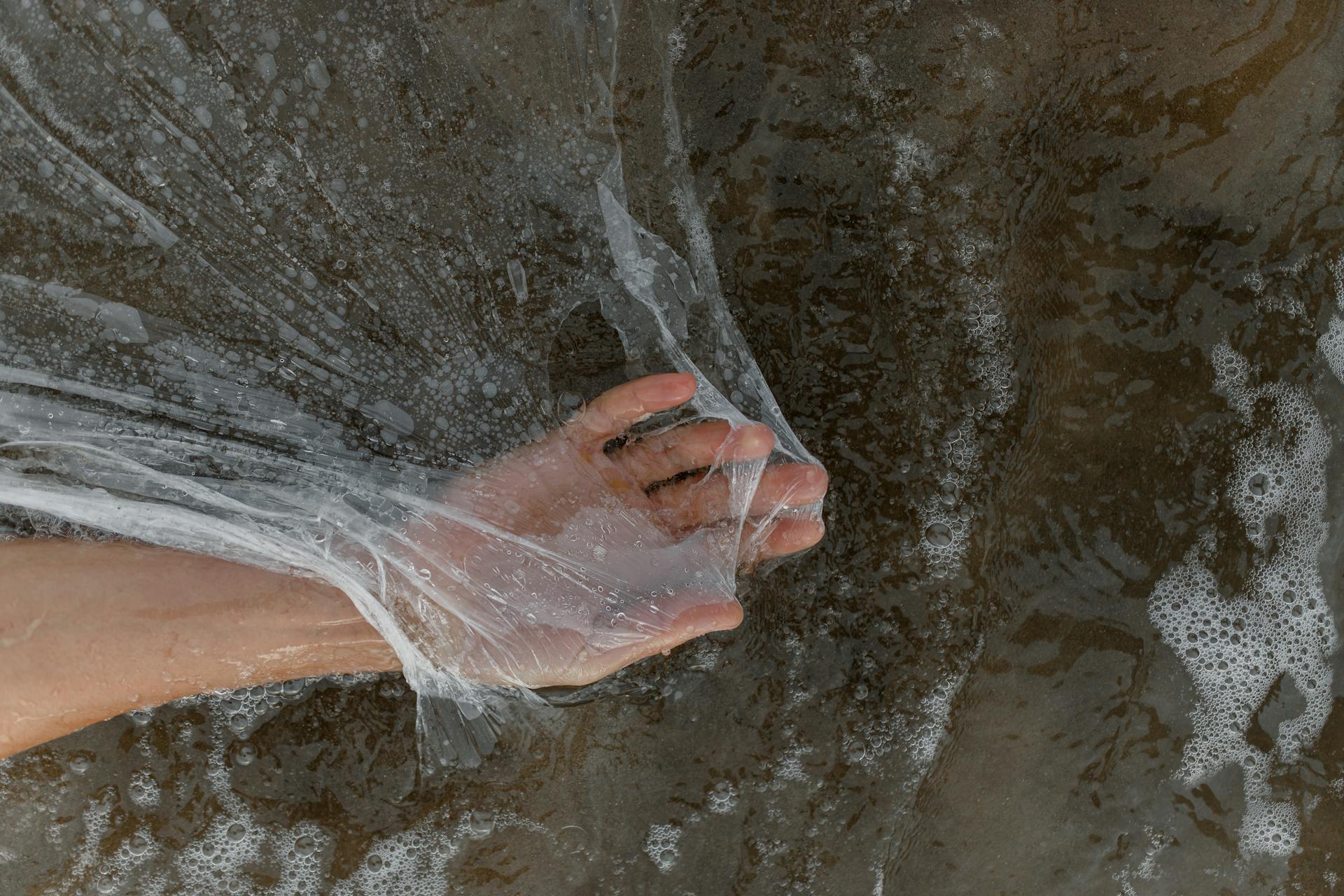
Some of the key applications of vacuum-form plastic sheets include agricultural components, automotive parts, and retail and marketing displays. They are also used for packaging objectives, such as food packaging, and for creating household items like plastic bathtubs and appliances.
Here are some of the key benefits of vacuum-form plastic sheets:
- Lightweight and robust
- Won't easily break or crack
- Easy to fold and cut
- Long-lasting and durable
- Available in a wide range of colors
- Non-stick property
- Relatively lightweight
Advantages
Vacuum Form Plastic Sheets are a great option for many applications, and they have several advantages that make them a popular choice.
They are lightweight, strong, and have a smooth surface that resists scratching. This makes them easy to handle and transport.
One of the key benefits of Vacuum Form Plastic Sheets is their ability to be folded and cut easily, without any creases or sharp edges. This makes them perfect for applications where flexibility is important.
They can be used for a long time without any damage, making them a cost-effective option in the long run.
Here are some of the key advantages of Vacuum Form Plastic Sheets:
- They are lightweight and robust.
- They won't easily break or crack even if you drop them from a great height.
- They can be easily folded and cut because they don't have any creases or sharp edges.
- They can be used for a long time without any damage.
- They are produced in a wide range of colors that you can choose from as per your needs.
- They are pretty light in weight and are available at a very reasonable price.
- They can be easily cut into your desired shape as per your requirements.
Overall, Vacuum Form Plastic Sheets are a versatile and practical option for many applications.
Applications
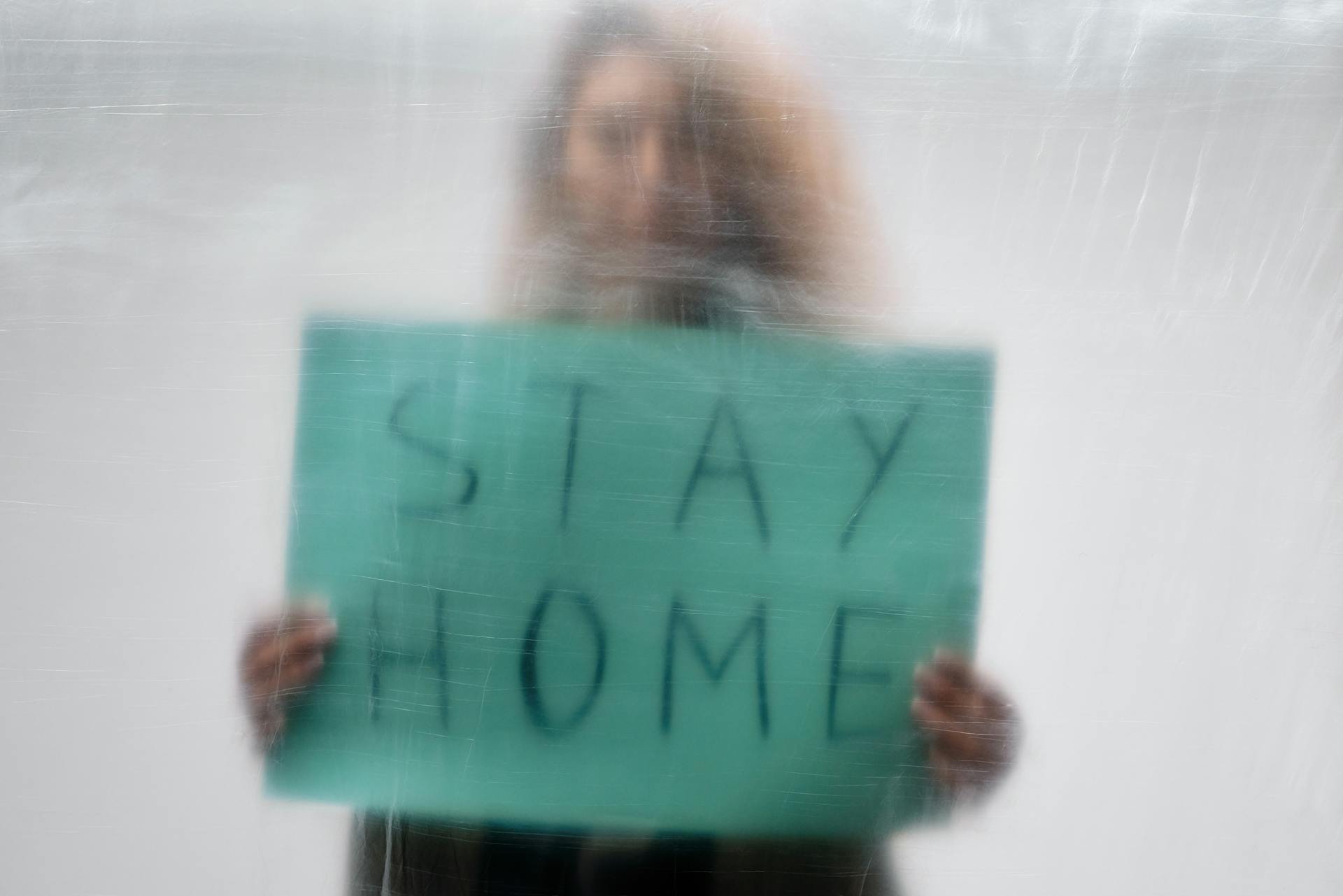
Vacuum forming is a versatile technique that's used in various industries, including automotive and agriculture. It's a fast and cost-effective solution that's perfect for long-term outdoor use.
The automotive industry relies heavily on vacuum-formed plastics for both aesthetic and practical purposes. You'll find vacuum-formed parts in every car, from the dashboard to the door panels.
Vacuum forming is also used to create parts for vans, lorries, buses, boats, and aircraft. These parts are compact and cost-effective, with a wide range of finishes that can be tailored to fit any vehicle's style.
Plastics used in vacuum forming are ideal for packaging due to their affordability, hygiene, and versatility in terms of size and shape. They're perfect for large production lines.
From plastic bathtubs to garden tools, vacuum-forming plastic is used to create household items that are used every day. These products are a testament to the technique's versatility and practicality.
Retailers are now using vacuum forming to create eye-catching promotional displays that catch customers' attention. These displays are a great way to promote a business or event, and can be designed to be truly unique and memorable.
You might enjoy: Cost of Plastic Pallets
Specification
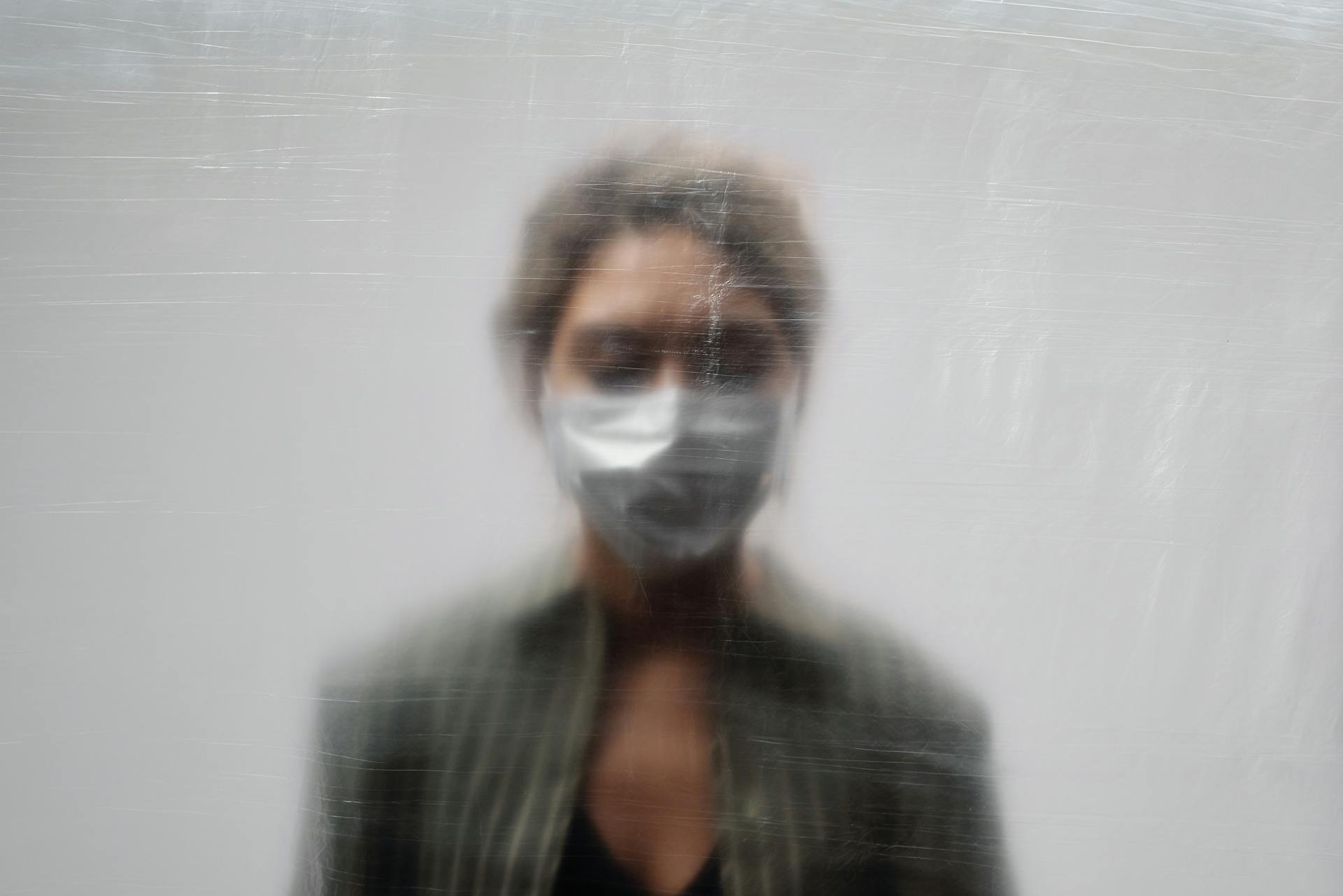
The specification of vacuform plastic sheets is quite impressive. The thickness of these sheets can range from 0.2mm to 9.00mm.
You can choose from various surface finishes, including plain, glossy, matt, and embossed. This flexibility in design makes them suitable for a wide range of applications.
The size of the sheets can be cut to size or provided as rolls, as per the customer's requirements. This ensures that you get the exact size you need for your project.
Here's a summary of the key specifications:
The DESU brand of vacuform plastic sheets has its own set of specifications. They are made in Shanghai, China, and come in a range of widths from 300-1400mm.
Materials
PET plastic sheets are a popular choice for vacuum forming due to their excellent combination of properties. They're made from a type of thermoplastic polymer and are commonly used in various applications.
APET, a type of PET plastic sheet, is hard, has good toughness, and high strength, making it suitable for high-end and environmentally friendly products. However, it's more difficult to heat seal and is more expensive than PVC.
PET plastic sheets are also available in transparent and various colors, and are environmentally friendly and non-toxic.
A different take: Pp vs Pet Plastic
2.0 mm PET Application
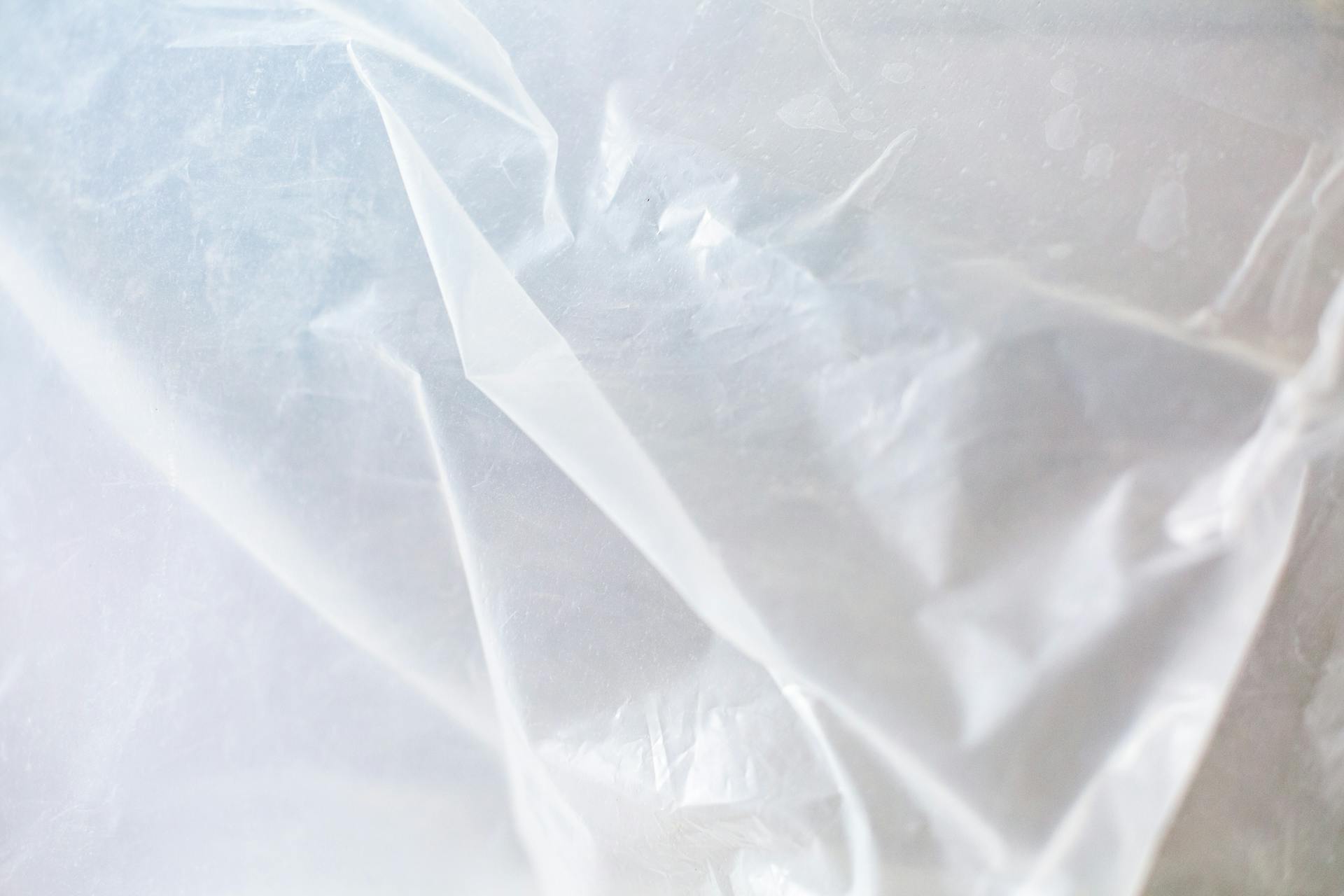
PET plastic sheet is widely used for the external packing of different kinds of products because of its good transparency.
The 2.0 mm PET plastic sheet is a popular choice for vacuum forming due to its versatility.
It can be processed into trays of different shapes by vacuum thermal forming for food packaging, medical packaging, medical instrument packaging, and electronics packaging.
The sheet's ability to be formed into different shapes by molds makes it suitable for creating covers for clothes packing.
The 2.0 mm PET plastic sheet is also used in various industries such as the chemical industry, oil industry, galvanization, water purification equipment, environmental protection equipment, medical appliances, and more.
One of the key advantages of PET plastic sheet is its anti-static, anti-UV, and anti-sticky properties.
Its environmentally friendly and non-toxic nature makes it a popular choice for applications where safety is a concern.
The sheet's good transparency and ability to be formed into various shapes make it an ideal material for packaging and other applications.
Additional reading: Plastic Vacuum Packaging
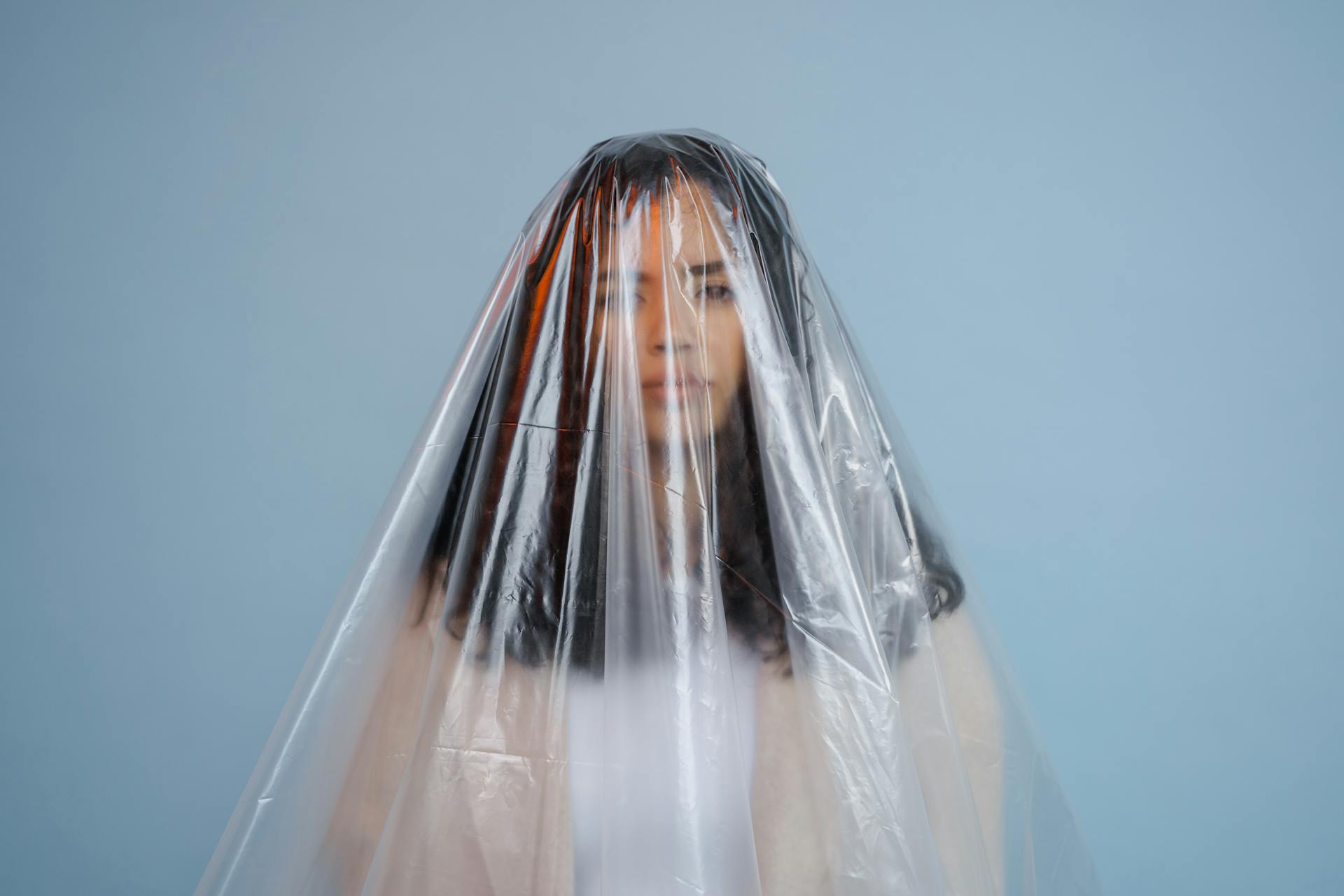
Its high strength and toughness also make it suitable for use in a wide range of industries.
The 2.0 mm PET plastic sheet is a cost-effective and efficient material that can be used for a variety of applications.
Its good plasticity and ability to be formed into different shapes make it a popular choice for manufacturers.
The sheet's poor toughness and tendency to become brittle when exposed to high temperatures are its main drawbacks.
However, its advantages make it a popular choice for many applications.
HDPE
HDPE is a versatile plastic material that offers numerous advantages. HDPE sheet has good heat resistance.
Its cold resistance is also noteworthy, allowing it to perform well in a variety of temperatures. HDPE has high rigidity.
This makes it suitable for applications where durability is essential. HDPE is tough.
Its excellent environmental stress cracking resistance is a significant benefit, reducing the risk of damage from external factors. HDPE is used in 200-liter buckets.
Fuel tanks are another common application for HDPE. Pallets also utilize this material.
HDPE is used in large components, such as those found in yachts. Blister tray tops are another example of its use.
HDPE is even used in special packaging for most auto parts.
ABS
ABS plastic sheet is widely used in various industries due to its excellent properties. It has good impact resistance, heat resistance, low temperature resistance, and chemical resistance. ABS sheet also has excellent electrical properties and is easy to form.
ABS sheet is commonly used in the production of products that require high packaging dimensional accuracy, such as in robot automatic pick-up projects. Its stable product size and good surface gloss make it an ideal choice for these applications.
Pet-G
PET-G plastic sheet is a type of thermoplastic polymer used in various applications.
Its physical properties are similar to A-PET, but it has an added advantage of being able to be heat-sealed with high frequency.
The price of PET-G plastic sheet is 80% more expensive than A-PET, which may be a consideration for some users.
Additional reading: Pet Plastic Tray
Thermoforming
Thermoforming is a process used to create plastic sheets, and there are two main types of plastic sheets for thermoforming: thick-gauge and thin-gauge. Thick-gauge plastic sheets are commonly used for vacuum forming.
Worth a look: Plastic Cup Thermoforming Machine
These sheets are typically made from HDPE, ABS, and ABS+TPU materials. HDPE plastic sheets are known for their durability and resistance to scratches. ABS plastic sheets, on the other hand, offer excellent impact resistance and are often used in applications where strength is essential.
The most common materials used for thick-gauge thermoforming include HDPE, ABS, and ABS+TPU. Here are some key characteristics of these materials:
Form
Thermoforming is a process that involves forming a plastic sheet into a specific shape using heat and pressure. This is done in a vacuum chamber, which helps to remove any air bubbles and create a smooth finish.
The process of forming a plastic sheet into a specific shape is where the magic happens. By applying heat and pressure in a vacuum chamber, a thin film with a particular shape is created.
Vacuum-formed plastic sheets are made by applying heat and pressure in a vacuum chamber. This process is also known as thermoforming.
The shape of the formed plastic sheet can be customized to fit a specific application. This is one of the advantages of thermoforming.
Here are some of the key features of vacuum-formed plastic sheets:
- Thin film with a particular shape
- Customizable shape to fit specific applications
Thermoforming
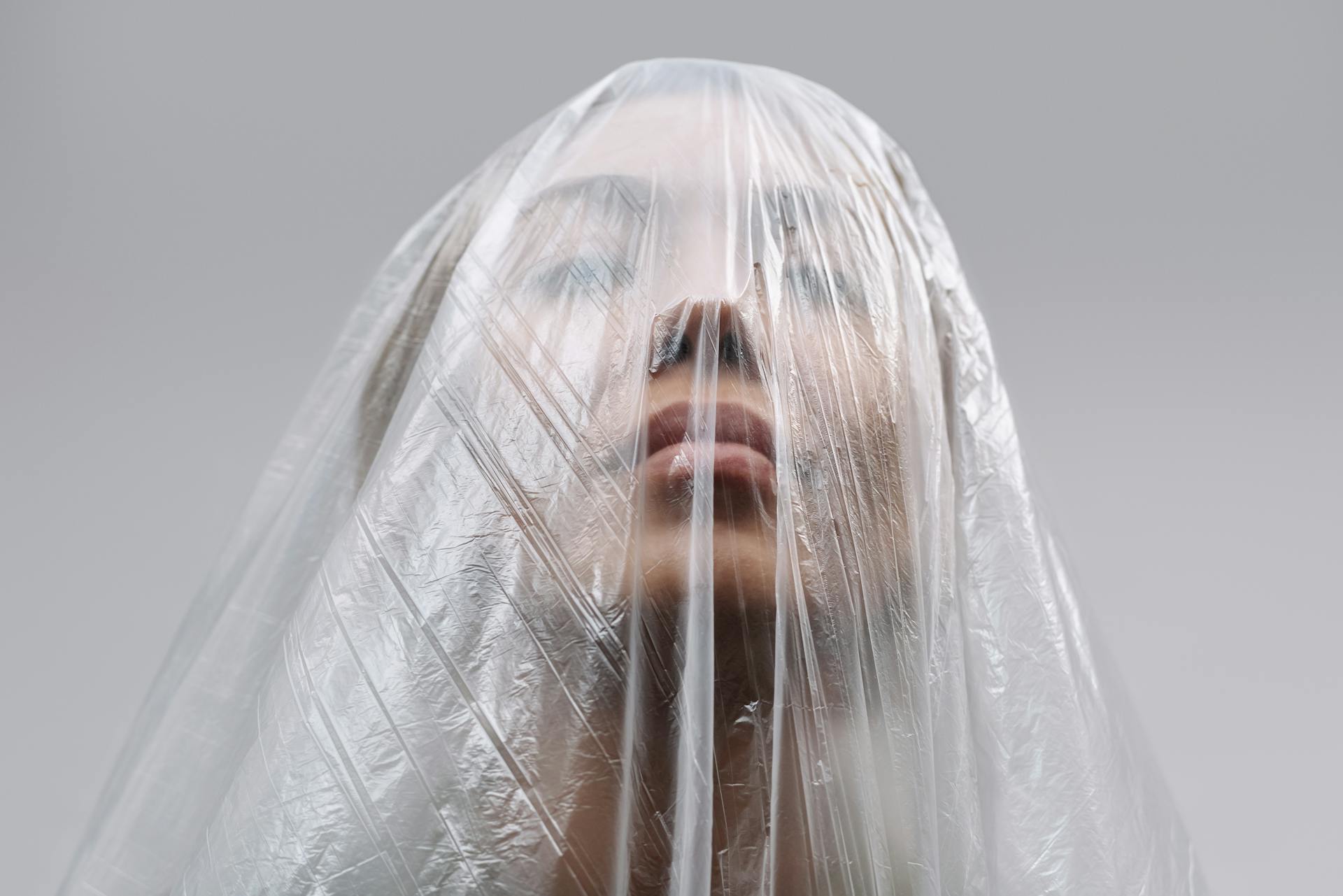
Thermoforming is a process that involves heating a plastic sheet to a pliable state and then shaping it using a mold. This process is commonly used to create custom-shaped products such as containers, trays, and packaging.
There are two main types of plastic sheets used for thermoforming: thick-gauge and thin-gauge. Thick-gauge sheets are typically used for applications that require more rigidity and durability.
HDPE plastic sheet is a popular choice for thick-gauge thermoforming due to its high impact resistance and chemical resistance. ABS plastic sheet is another common option, known for its high impact resistance and heat resistance.
ABS+TPU plastic sheet is also used for thick-gauge thermoforming, offering a unique combination of properties. PVC plastic sheet, PET plastic sheet, PETG plastic sheet, and PS plastic sheet are also used for various applications.
Vacuum-forming is a type of thermoforming that involves applying heat and pressure in a vacuum chamber to form a thin film with a particular shape. This process is often used to create complex shapes and designs.
Take a look at this: High Impact Polystyrene
Some common features of vacuum-formed plastic sheets include:
- High accuracy and precision
- Fast production times
- Low material waste
- Customizable shapes and sizes
The advantages of vacuum-forming include:
- High production efficiency
- Low material costs
- Ability to create complex shapes and designs
Vacuum-formed plastic sheets have a wide range of applications, including:
- Packaging and labeling
- Medical devices and equipment
- Automotive parts and accessories
- Consumer products and household items
Thin-Gauge
PVC is a popular material used for thin-gauge thermoforming.
Thin blister sheets can be made from a variety of materials, including PET and PP.
PS and flocking sheets are also commonly used for thin-gauge applications.
Gold-plated sheets and anti-static sheets are available based on these materials.
These types of sheets are ideal for creating thin, detailed parts that require precision and accuracy.
They are often used in industries such as packaging, electronics, and medical devices.
Suggestion: Packaging Materials Foam Sheets
Frequently Asked Questions
What plastic sheets are best for vacuum forming?
For vacuum forming, consider using clear plastics like PET, polycarbonate, or acrylic for their excellent clarity and toughness. These options provide a strong and transparent finish, ideal for various applications.
Can you vacuum form PVC sheet?
Yes, PVC sheet can be vacuum formed, but it requires specific processing conditions to achieve the desired results. Vacuum forming PVC sheet can produce durable and versatile products, but it's essential to consider the material's properties and limitations.
Can you vacuum form acrylic sheets?
Yes, vacuum forming is a suitable technique for working with acrylic sheets, enabling the creation of large parts with precise details and custom designs.
Sources
- https://www.singhalglobal.com/products/vacuum-form-plastic-sheets
- https://desuplastic.com/2-0-mm-pet-plastic-sheet-for-vacuum-forming/
- https://www.mdeplastics.com/plastic-sheet-for-thermoforming-and-vacuum-forming
- https://www.roechling.com/us/industrial/vacuum-forming
- https://rfpllc.com/capabilties/vacuum-forming/
Featured Images: pexels.com