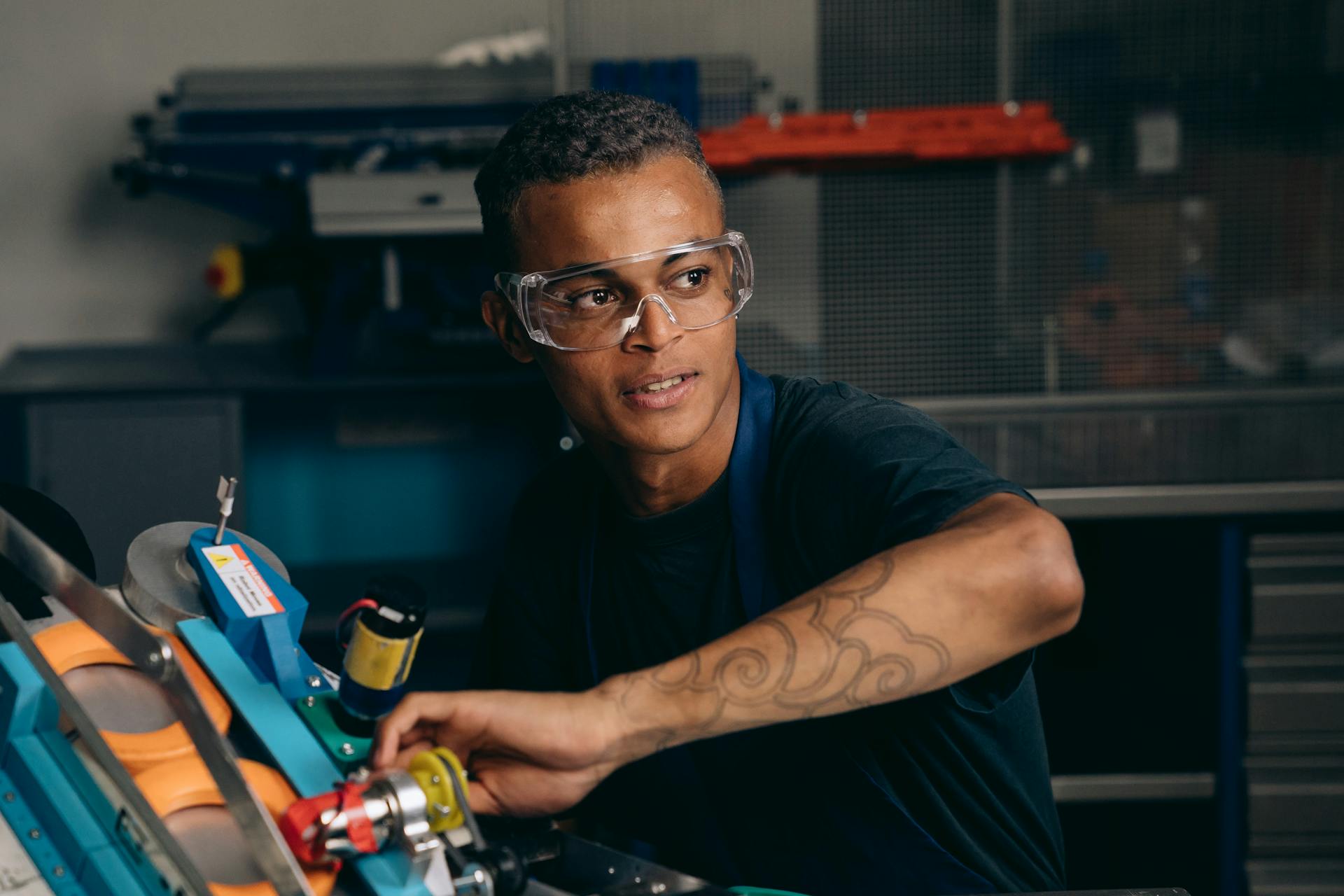
A plastic cup thermoforming machine is a fantastic investment for businesses looking to produce high-quality cups at a rapid pace. These machines can produce up to 1,000 cups per hour.
The fully automatic production process is made possible by the machine's advanced technology, which includes a precise temperature control system and a hydraulic system for forming the cups.
With a plastic cup thermoforming machine, you can produce cups with a thickness of 0.5-1.5mm, making them suitable for hot and cold beverages. This is achieved through the machine's ability to control the temperature and pressure of the forming process.
The machine's efficiency and accuracy make it an ideal choice for businesses that require high-volume production, such as large events or festivals.
Readers also liked: High Density Polyethylene Plastic
What You Need to Know
Plastic cup thermoforming machines can produce up to 1,000 cups per hour, making them a fast and efficient option for high-volume production.
A single machine can be used to produce a variety of cup sizes, from 6 ounces to 64 ounces, depending on the mold used.
These machines are capable of producing cups with walls as thin as 0.5 mm, allowing for a lightweight and shatter-resistant product.
The process of thermoforming involves heating a sheet of plastic to a temperature of around 300°F, at which point it is molded into the desired shape using a metal mold.
The entire process, from heating to molding, typically takes around 10-15 seconds, making it a quick and efficient process.
The cost of a plastic cup thermoforming machine can range from $50,000 to $200,000, depending on the size and complexity of the machine.
Machine Details
Thermoforming machines are used for a variety of products, including food containers, blister packs, and clamshell packaging.
There are two main types of thermoforming machines: vacuum forming machines and pressure forming machines.
Vacuum forming machines use negative pressure to suck the softened sheet of plastic onto the mold, making them faster and able to handle larger sheets of plastic.
Specification and Maintenance
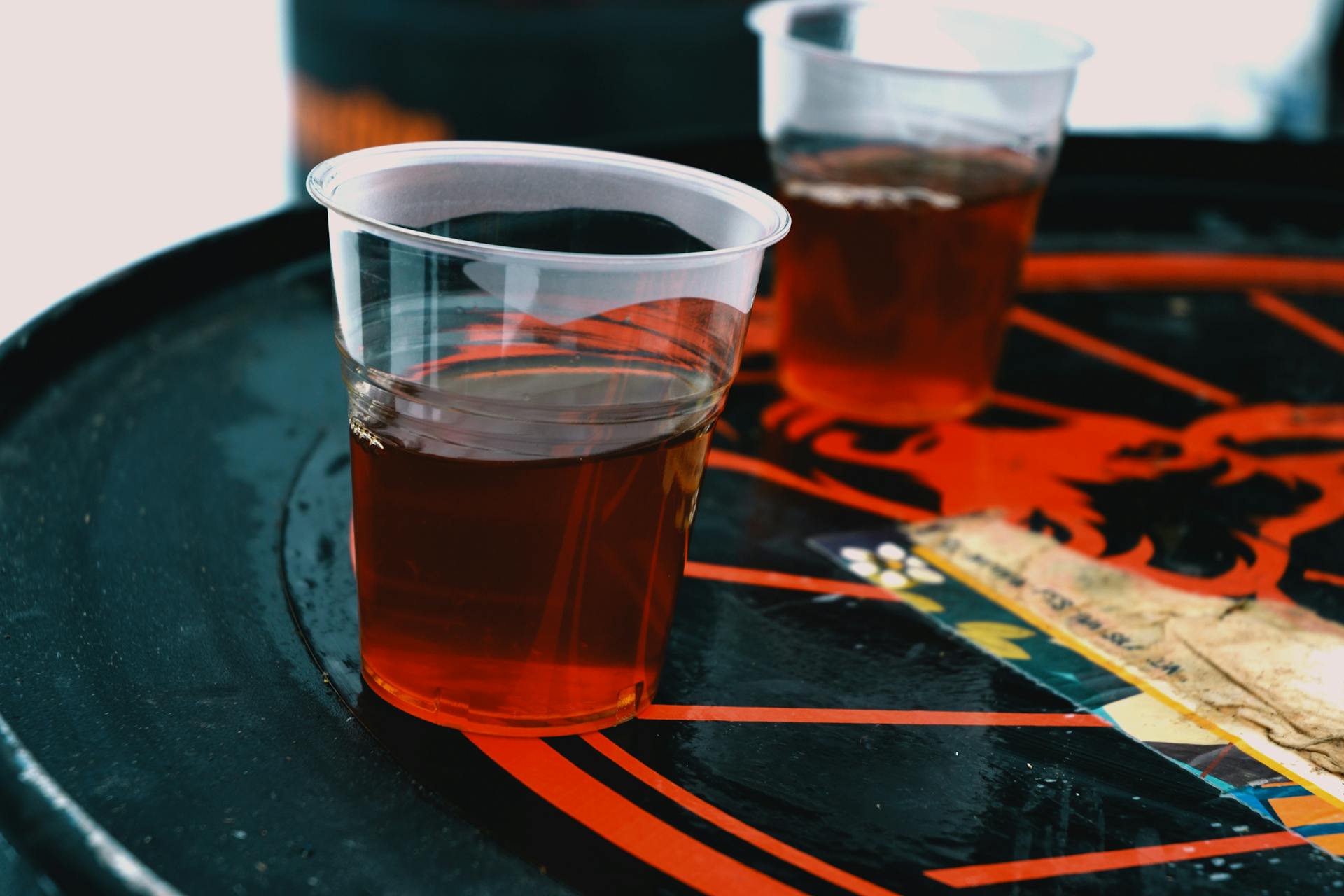
The capacity of a thermoforming machine is a crucial specification to consider, as it determines the volume of plastic material it can handle. Many machines can form sheets that are between 0.5 and 6 mm thick.
The rate of production is another important specification, with some machines able to produce up to 1000 formed cups per hour. This fast production rate is made possible by the automation of feeding and cutting systems for material.
The type of material a machine handles is very important, with some machines working with specific kinds of pre-cut plastic materials like PET. Businesses need to know the kind of material they will be supplying so as to choose a machine that can handle it.
Regular cleaning is a must for maintaining plastic cup thermoforming machines, as the process involves heating plastic and leaving residue on the heating element and other parts. This helps keep the machine in good condition and makes maintenance of spare parts easier.
Lubricating moving parts of the machine periodically is another important maintenance task, as it reduces friction and eases movement.
How It Works
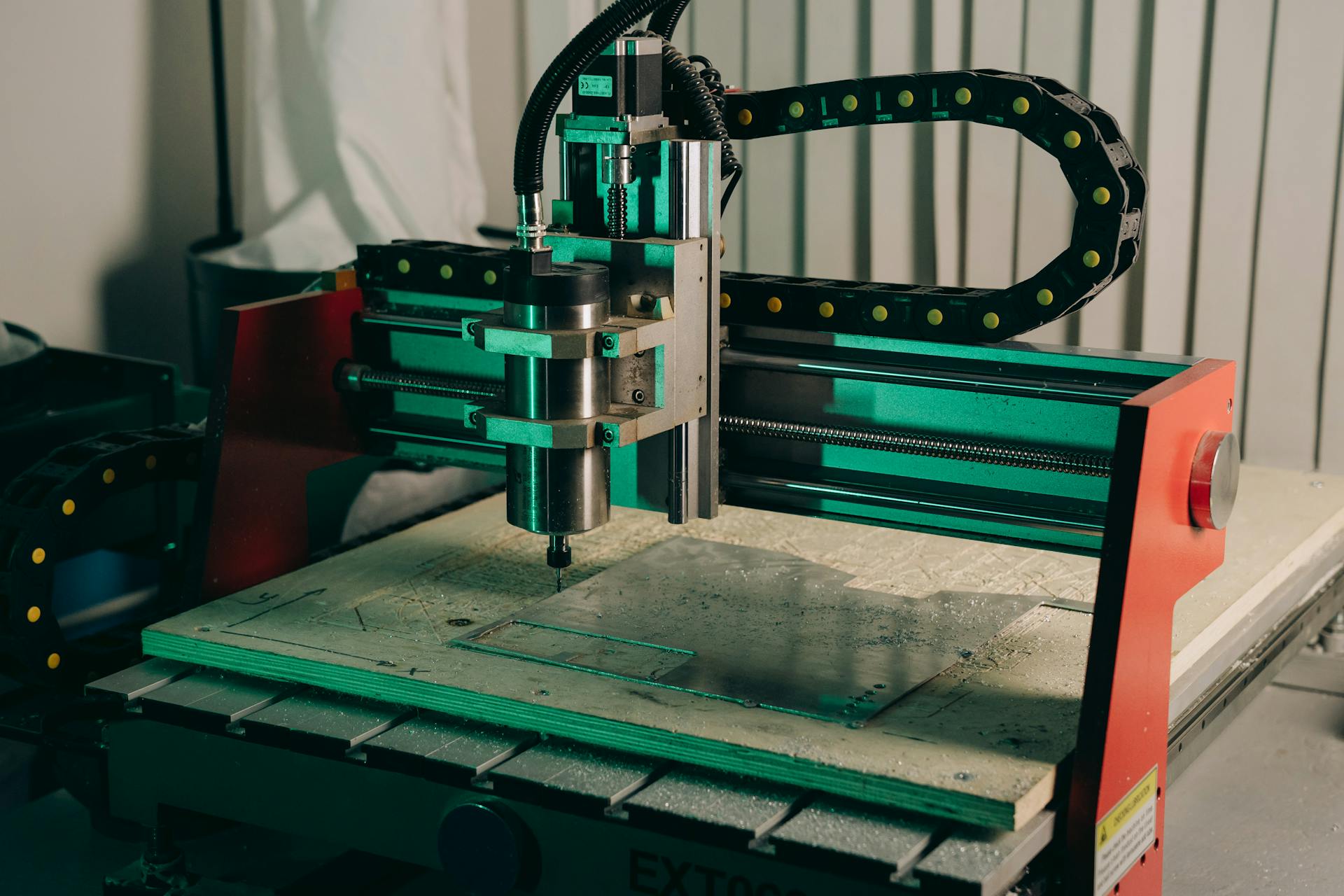
Thermoforming is a process that uses heat and pressure to form a sheet of plastic into a desired shape.
The plastic sheet is first heated until it's soft and pliable, then placed over a mold or die and formed into the desired shape.
Once the plastic cools and hardens, it maintains its new shape.
There are two main types of thermoforming machines: vacuum forming machines and pressure forming machines.
Vacuum forming machines use negative pressure to suck the softened sheet of plastic onto the mold.
Pressure forming machines use positive pressure to push the softened sheet of plastic onto the mold.
Vacuum forming machines are often used for large-scale production runs because they're faster and can handle larger sheets of plastic.
Pressure forming machines, on the other hand, are often used for small-scale production runs or for more delicate applications because they provide more control over the shaping process.
Fully Automatic
The Fully Automatic Plastic Cup Thermoforming Machine is designed for effortless operation, reducing labor costs and maximizing productivity.
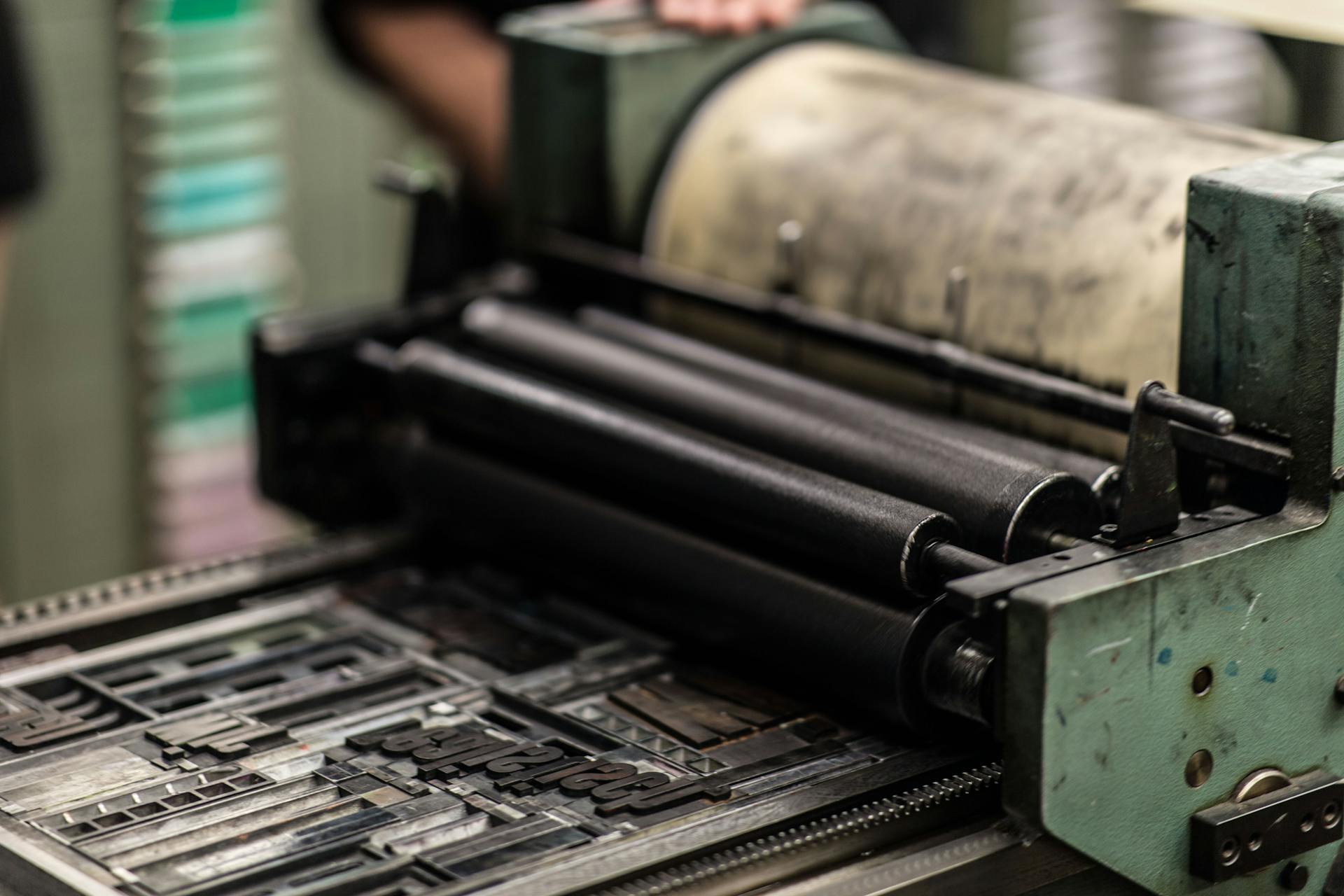
This machine allows for seamless operation and minimal downtime, thanks to its innovative features and cutting-edge technology.
The Fully Automatic Plastic Cup Thermoforming Machine is equipped with a user-friendly interface that ensures ease of use and comprehensive control, enabling operators to monitor and adjust settings effortlessly.
With its fully automatic functionality, manufacturers can produce plastic cups with exceptional accuracy, speed, and consistency, streamlining the production process.
The machine's high-grade materials and components ensure durability, longevity, and uninterrupted performance, reflecting the company's commitment to quality.
Broaden your view: Automatic Strapping Machine
How to Choose
When selecting a plastic cup thermoforming machine, it's essential to consider several factors to ensure optimal performance and compatibility with your production needs. First, assess the production volume and speed requirements. High-speed machines are suitable for large-scale manufacturing, while smaller machines may suffice for limited production runs.
To determine your production needs, consider the complexity of the shapes and designs you aim to produce. Some machines offer enhanced capabilities for intricate detailing, while others may struggle with more complex designs.
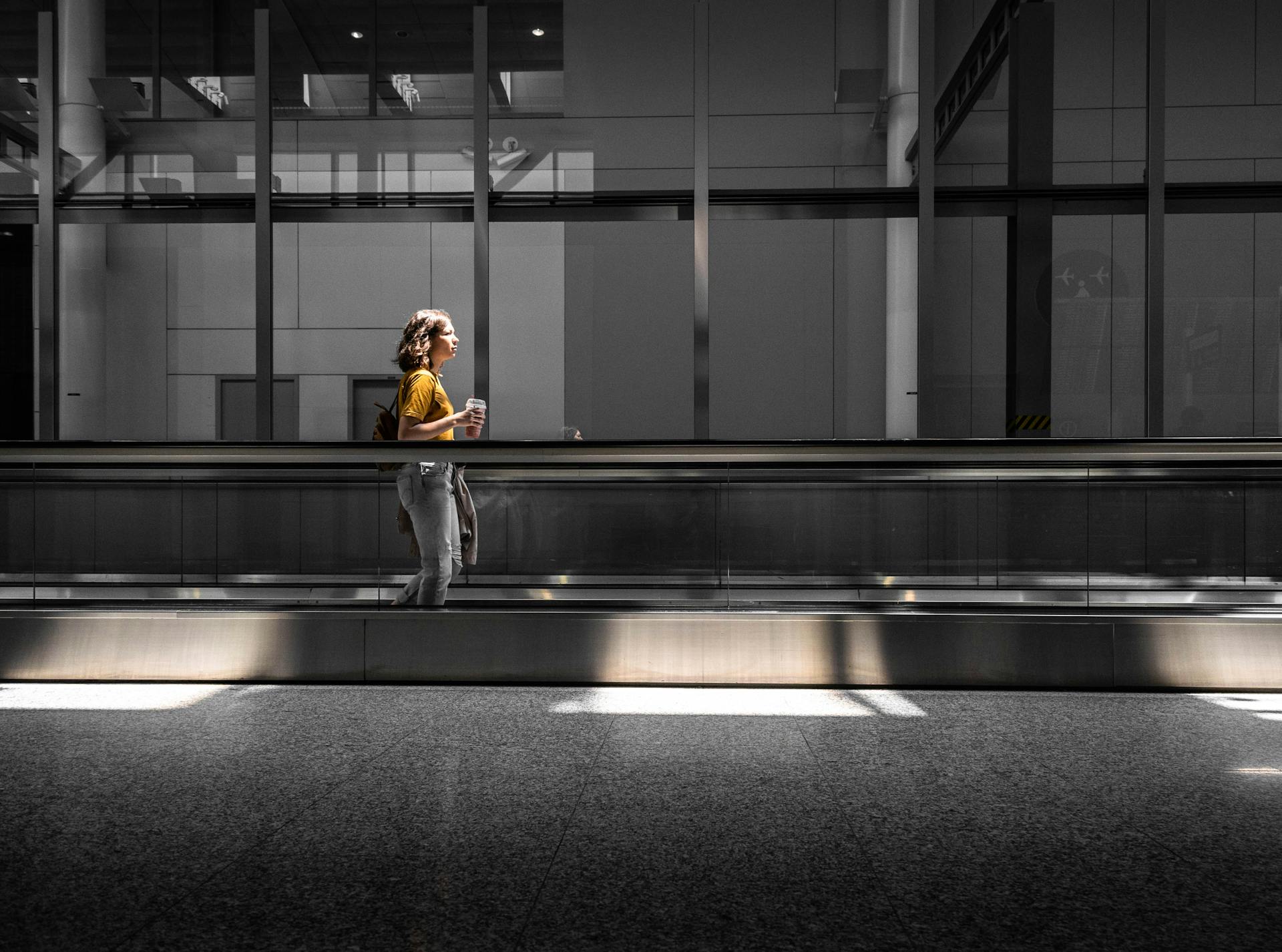
Evaluating the machine's compatibility with different thermoplastic materials is also crucial, as this will impact the range of products you can manufacture. Different machines can handle specific materials and thicknesses, providing flexibility and precision in manufacturing.
Consider the level of automation offered by the plastic cup making mould thermoforming machine. Machines with advanced automation features, such as automatic sheet loading and unloading, can significantly enhance efficiency and reduce labor costs.
Machines with user-friendly controls and automated features can also reduce downtime and improve productivity. Look for a machine that comes with intuitive interfaces and automated features.
Here are some key factors to consider when choosing a plastic cup thermoforming machine:
Finally, consider the cost of the machine in relation to its features and specifications. Set a budget and look for a plastic cup thermoforming machine that offers good value for the investment.
Machine Operation
Regular maintenance and calibration are essential to ensure efficient operation of a plastic cup making mould thermoforming machine. This includes checking the heating elements for consistent temperature distribution.
The molds need to be clean and free of debris to prevent any issues. Operators should be trained to handle the machine correctly.
Implementing a routine inspection schedule can help identify potential issues before they lead to significant downtime. This can save you a lot of time and money in the long run.
Twin sheet thermoforming machines allow for the creation of hollow parts with uniform wall thickness. This makes them ideal for producing items that require additional strength and rigidity.
Moulding and Production
The moulding process is where the magic happens with a plastic cup thermoforming machine. The machine heats a plastic sheet until it becomes pliable, allowing it to be formed into the desired shape.
This process is crucial for creating a wide range of products, including packaging materials, automotive components, and consumer goods. The versatility of plastic cup making mould thermoforming machines makes them a staple in industrial settings.
The machine shapes the plastic sheet over a mould to create the desired shape, resulting in high-quality products at scale. This efficiency is a key benefit of using plastic cup making mould thermoforming machines.
Manufacturers rely on these machines to produce products quickly and effectively. The process is widely used in the plastics production sector, where plastic cup making mould thermoforming machines are integral components.
Broaden your view: Polythene Bag Making Machine
Machine Features and Options
A key feature of plastic cup making mould thermoforming machines is the heating system, which ensures uniform heat distribution across the plastic sheet, allowing for consistent forming.
The forming station is where the magic happens, with options for vacuum, pressure, or mechanical forming methods to shape the sheet over the mold.
Advanced machines may also include automatic sheet loading and unloading, making the process smoother and more efficient.
Programmable control systems allow for easy adjustments and customization of the forming process, reducing downtime and increasing productivity.
Additional reading: Paper Sack Making Machine
Functions and Features
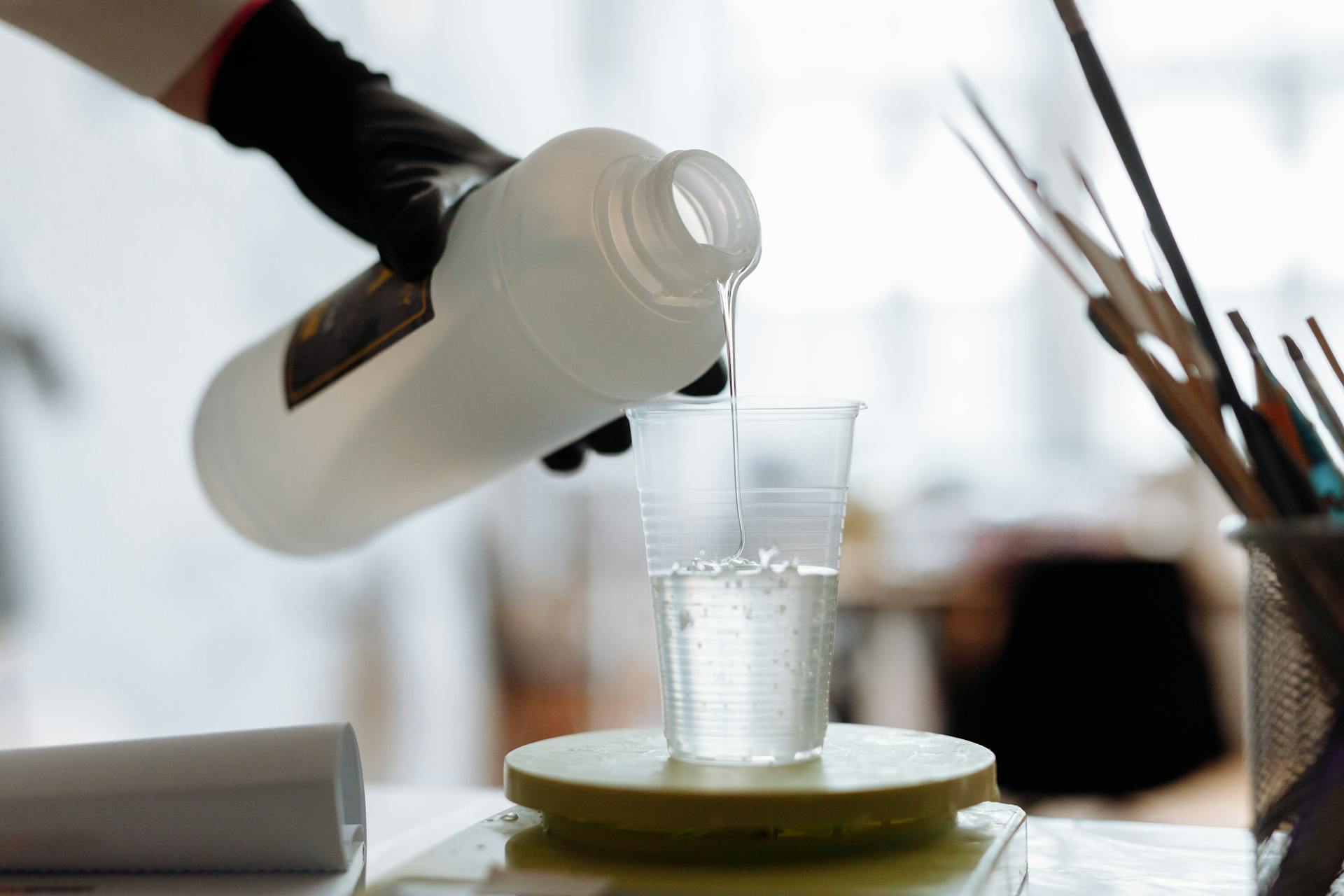
The functions and features of plastic thermoforming machines are designed to make the process as efficient as possible. These machines are equipped with a heating system that ensures uniform heat distribution across the plastic sheet.
The forming station is where the magic happens, allowing the sheet to be shaped over the mold using various methods such as vacuum, pressure, or mechanical forming. The trimming station is responsible for cutting the formed part from the excess material, ensuring clean edges and precise dimensions.
Some advanced machines come with automatic sheet loading and unloading capabilities, making the process even more streamlined. Programmable control systems are also available, allowing for customized settings and increased productivity.
Quick-change mold capabilities are another feature that can be found in some machines, reducing downtime and increasing overall efficiency.
Machine Features and Options
Plastic cup making mould thermoforming machines are incredibly versatile, allowing you to work with a wide range of thermoplastic materials.
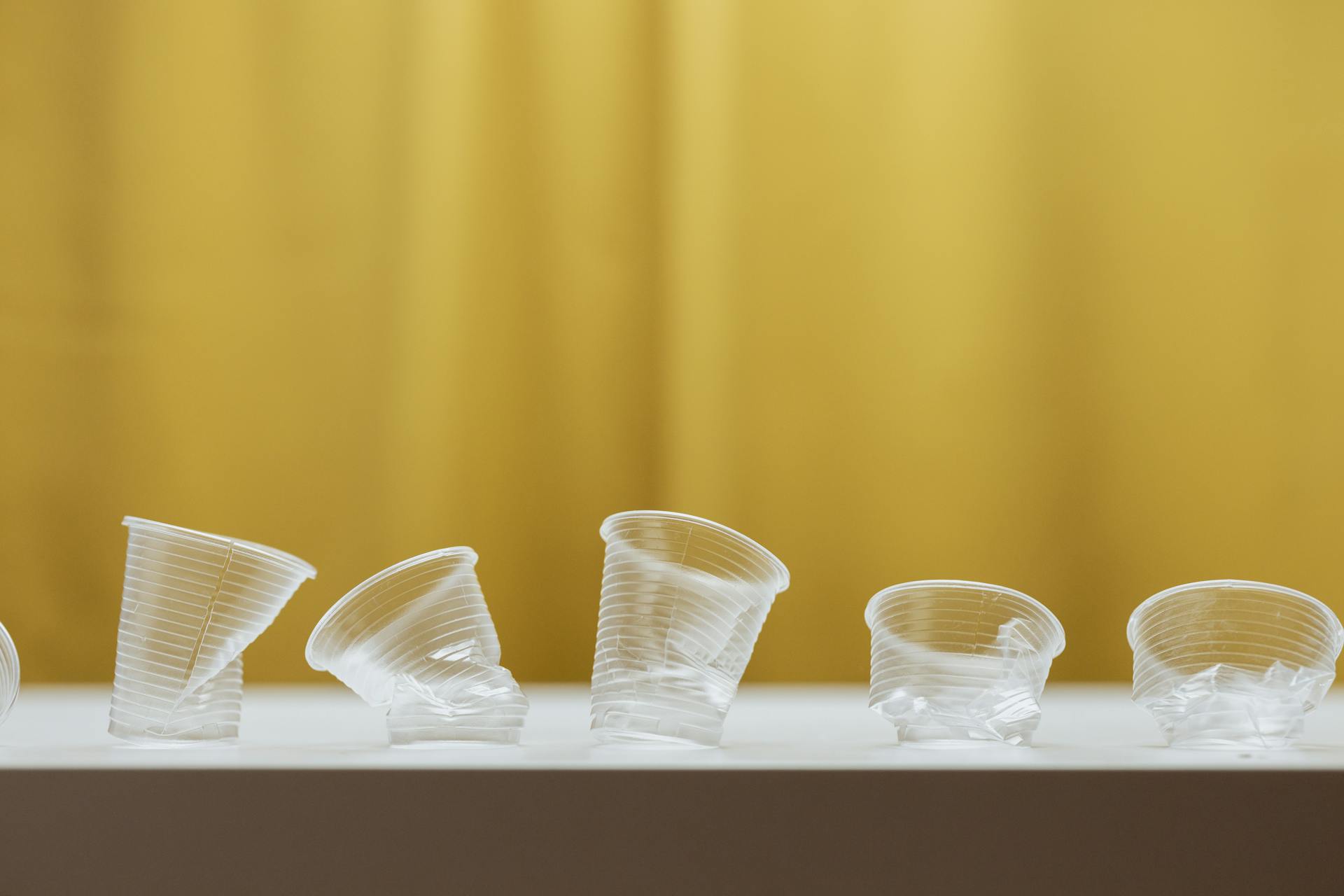
Polyethylene is a popular choice for its durability and resistance to impact, making it suitable for heavy-duty applications. Polypropylene is favored for its chemical resistance and lightweight nature, while polystyrene is often used for products requiring a high level of detail and rigidity. Polycarbonate offers excellent optical clarity and toughness, ideal for applications where transparency and strength are critical.
Energy-efficient machines can minimize power consumption, further contributing to sustainable practices. By selecting sustainable materials and optimizing the manufacturing process, you can utilize plastic cup making mould thermoforming machines for eco-friendly production.
Frequently Asked Questions
What is the cost of plastic cup making machine?
The cost of an Automatic Disposal Plastic Cup Glass Making Machine ranges from approximately ₹450,000 to ₹800,000. For a more detailed quote, please contact us for a custom pricing assessment.
Sources
- https://www.alibaba.com/showroom/plastic-cup-thermoforming-machine.html
- https://www.litai.cc/n-show/1288.html
- https://www.alibaba.com/showroom/plastic-cup-making-mould-thermoforming-machine.html
- https://www.litaimachine.com/latest-news/plastic-cup-thermoforming-machine
- https://www.rmthermoforming.com/fully-automatic-plastic-cup-thermoforming-machine/
Featured Images: pexels.com