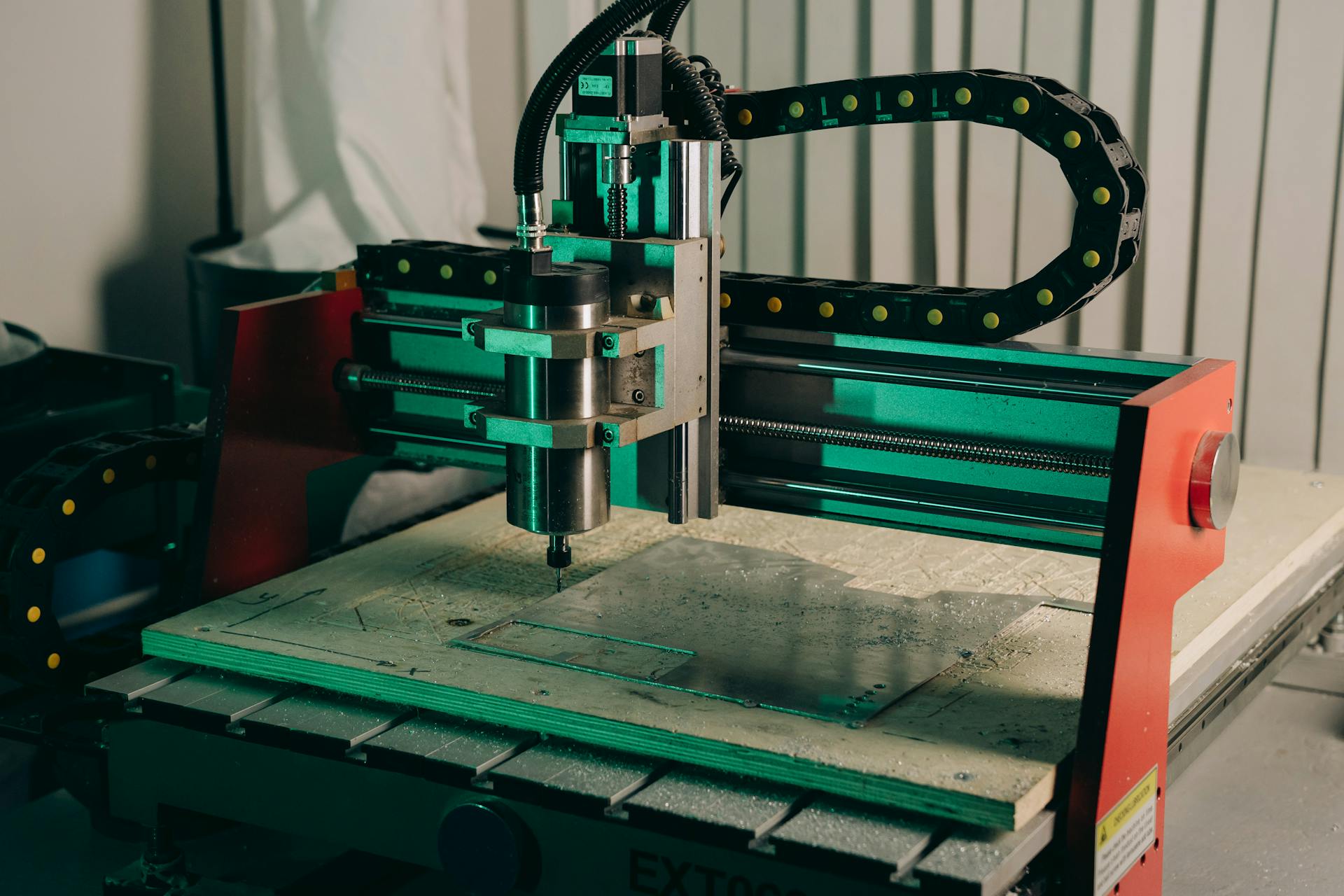
Vacuform machines are incredibly versatile and can produce a wide range of products, from simple plastic containers to complex medical devices.
Thermoforming is a process that involves heating a plastic sheet to a pliable state, allowing it to be molded into the desired shape. This process is often used in conjunction with vacuform machines to create custom products.
The benefits of using vacuform machines are numerous, including the ability to produce high-quality products quickly and efficiently. With the right equipment and training, anyone can learn to operate a vacuform machine and start producing their own products.
Types of Vacuform Machines
There are several types of vacuform machines, each designed for specific applications and production scales.
Formech's automatic range includes semi and fully automatic vacuum forming machines, such as the HD and TF series, which are ideal for industrial and manufacturing applications.
The HD Series operates semi-autonomously using sheet materials and is the most advanced Formech series, established in 2002.
Semi-Automatic Machines
Semi-automatic machines are a step up from desktop models and floor-standing machines, offering more advanced features and capabilities. They're perfect for industrial and manufacturing applications where high production volumes are required.
The HD and TF series of semi-automatic machines from Formech are designed to handle demanding applications, with features like pneumatic heater drive, pneumatic clamps, and a safety light curtain. These machines are also compact, making them ideal for spaces with limited room.
The HD Series, introduced in 2002, established a new price-performance ratio for semi-automatic production class machines. It's efficient, easy to use, and has a compact footprint.
The TF Series is specifically designed for reel feed packaging and decorative film applications, such as chocolate trays and inserts. It can process reel materials up to 0.07" (1.8mm) and sheet materials up to 0.25" (6mm).
Here's a comparison of the key features of the HD and TF series:
The TF Series machines are highly versatile and represent a cost-effective and compact alternative to high-speed in-line machines.
Large Format Machines
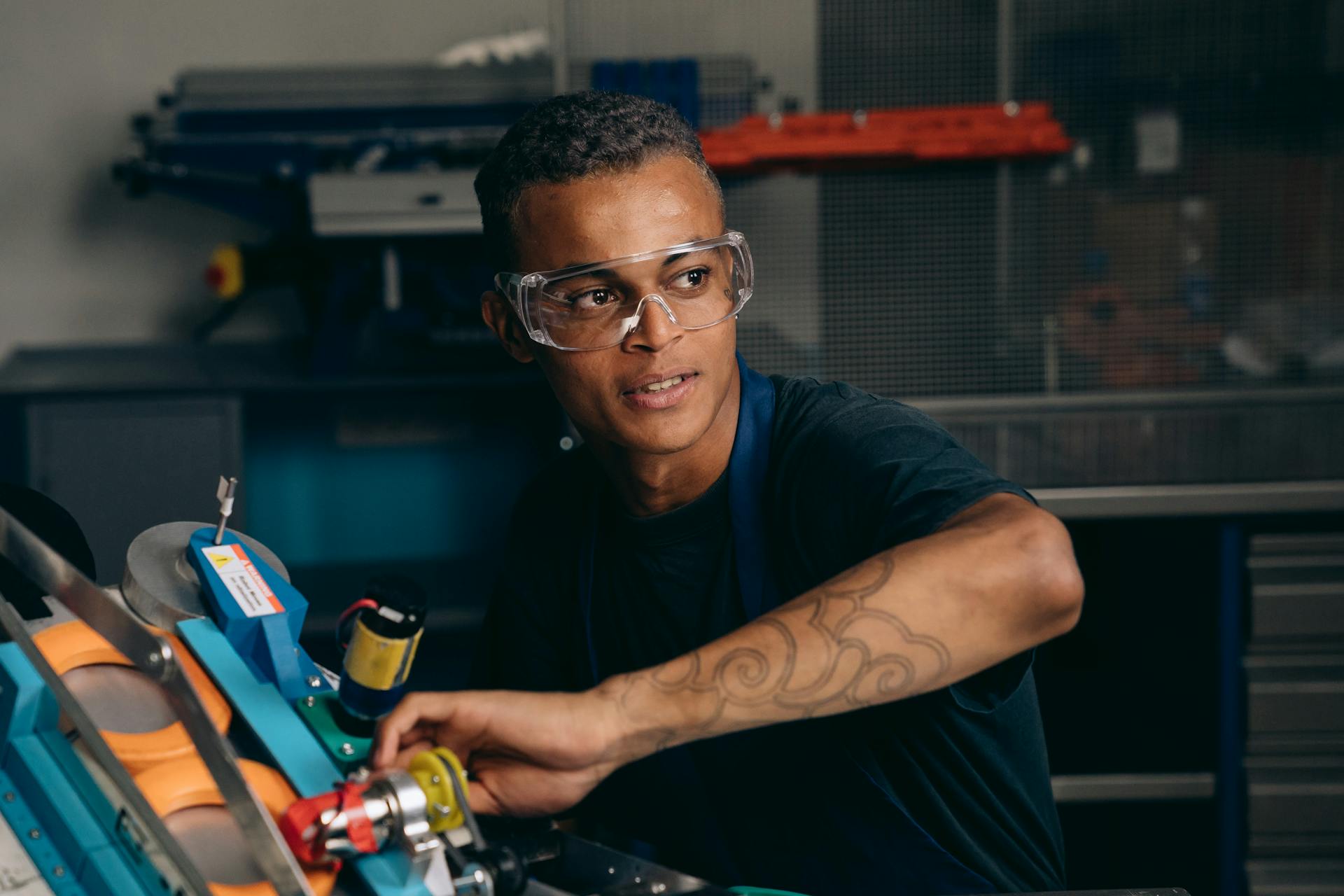
Large Format Machines are perfect for demanding applications, offering a forming area of 1220 x 1220mm.
They combine larger forming areas with semi-automatic capabilities, giving operators more control over the process.
The high-resolution touchscreen with Formech Cycle View (FCV) allows for easy access to machine settings, enabling real-time adjustments during forming.
Multi-user PIN access control is also available, allowing supervisors to adapt accessibility to match the operator's skill level.
Diverse Options
Desktop vacuum forming machines are perfect for prototyping, arts & craft projects, pastry and chocolatier moulding, small-product production lines and more. They come in two sizes, 960 x 960mm and 1050 x 1050mm.
A vacuum former is used to create plastic parts, custom molds, and products by shaping thin sheets of plastic into specific forms or shapes using vacuum pressure.
Desktop vacuum forming machines offer convenience and affordability for creating prototypes, personalized items, or small batches of plastic components. They're compact units designed for prototyping, small-scale production, or hobbyist use.
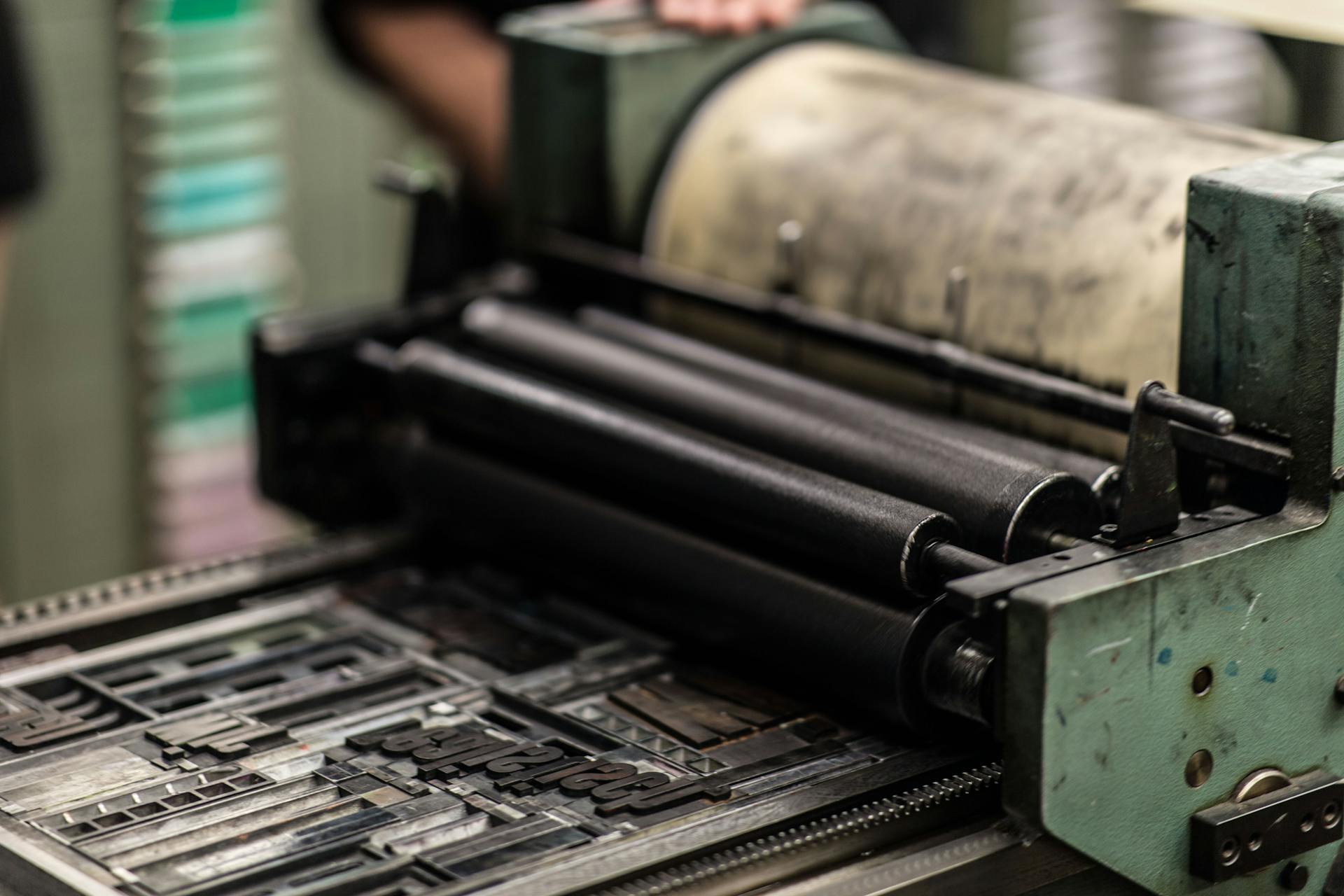
Table top vacuum forming machines are suitable for workshops, small businesses, or enthusiasts looking to experiment with thermoforming processes. They're a step up from desktop machines, but still relatively small.
Large vacuum forming machines cater to industrial-scale production needs. They're equipped with larger work areas, robust heating elements, and powerful vacuum systems to handle larger sheets of plastic and produce a higher volume of formed parts.
Thermo vacuum forming machines specialize in working with specific types of thermoplastics, offering precise temperature control and compatibility with various plastic materials. They're suitable for specific manufacturing applications.
Formers Collections
Formers Collections are a crucial part of Vacuform Machines, allowing for the production of complex and detailed designs.
The most common type of Former used in Vacuform Machines is the Rotomolded Former, which is ideal for producing large, hollow parts with smooth surfaces.
Rotomolded Formers are typically made from steel or aluminum and are designed to withstand high temperatures and pressures.
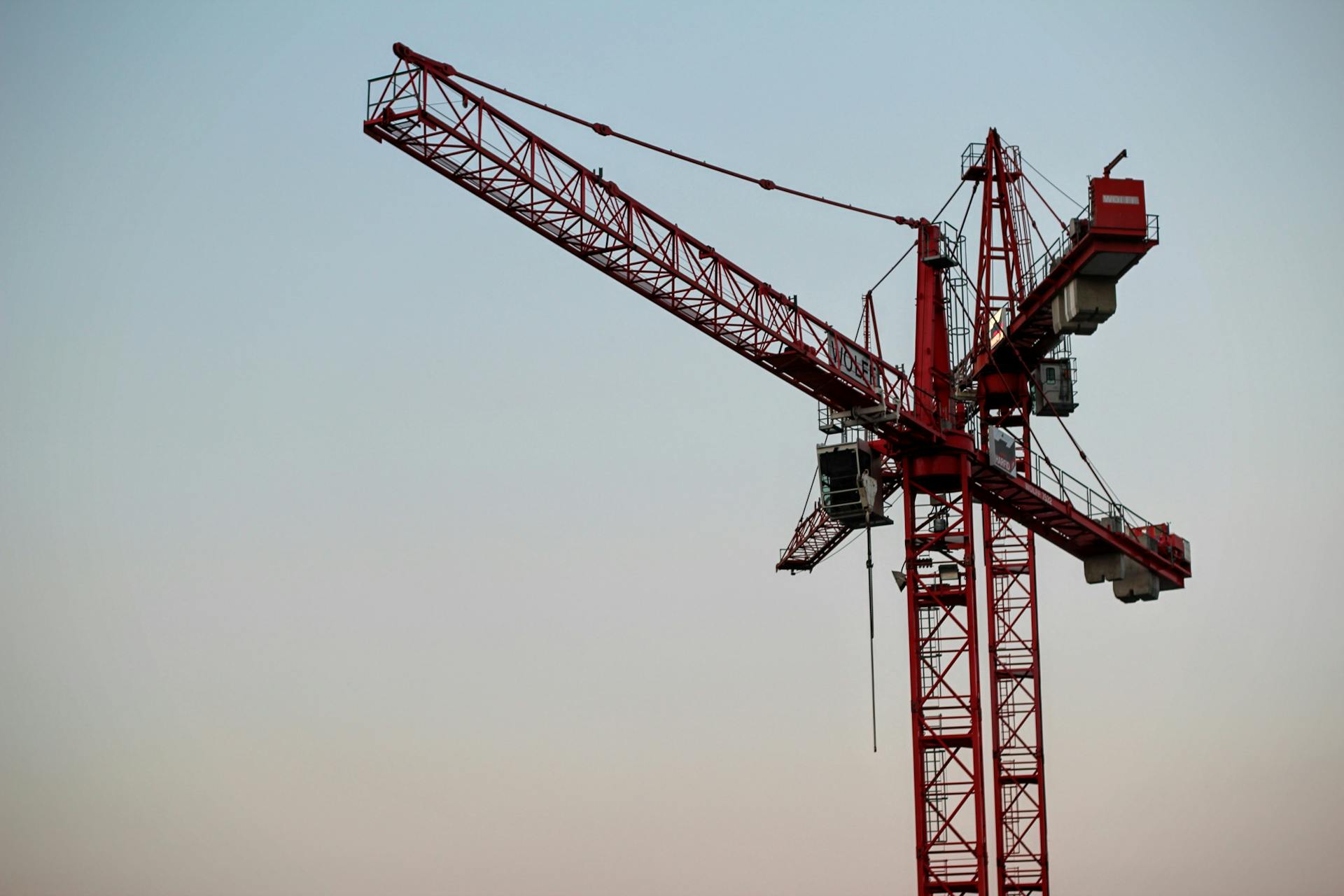
A well-designed Former can significantly improve the efficiency and productivity of a Vacuform Machine, allowing for faster production times and higher quality parts.
The choice of Former depends on the specific application and the type of material being used, with some Formers being better suited for certain materials than others.
In some cases, multiple Formers may be used in combination to produce complex parts with multiple components.
All Formers
Vacuum formers and thermoformers are incredibly versatile machines that can be used in a wide range of industries and applications.
From packaging to custom chocolate making, these machines are capable of producing a variety of products.
Small business applications are also well-suited to vacuum formers and thermoformers, which can help entrepreneurs and small business owners create prototypes and small batches of plastic components.
Automotive parts, aerospace parts, and medical components like prosthetics and dental guards are just a few examples of the many industrial applications of vacuum formers and thermoformers.
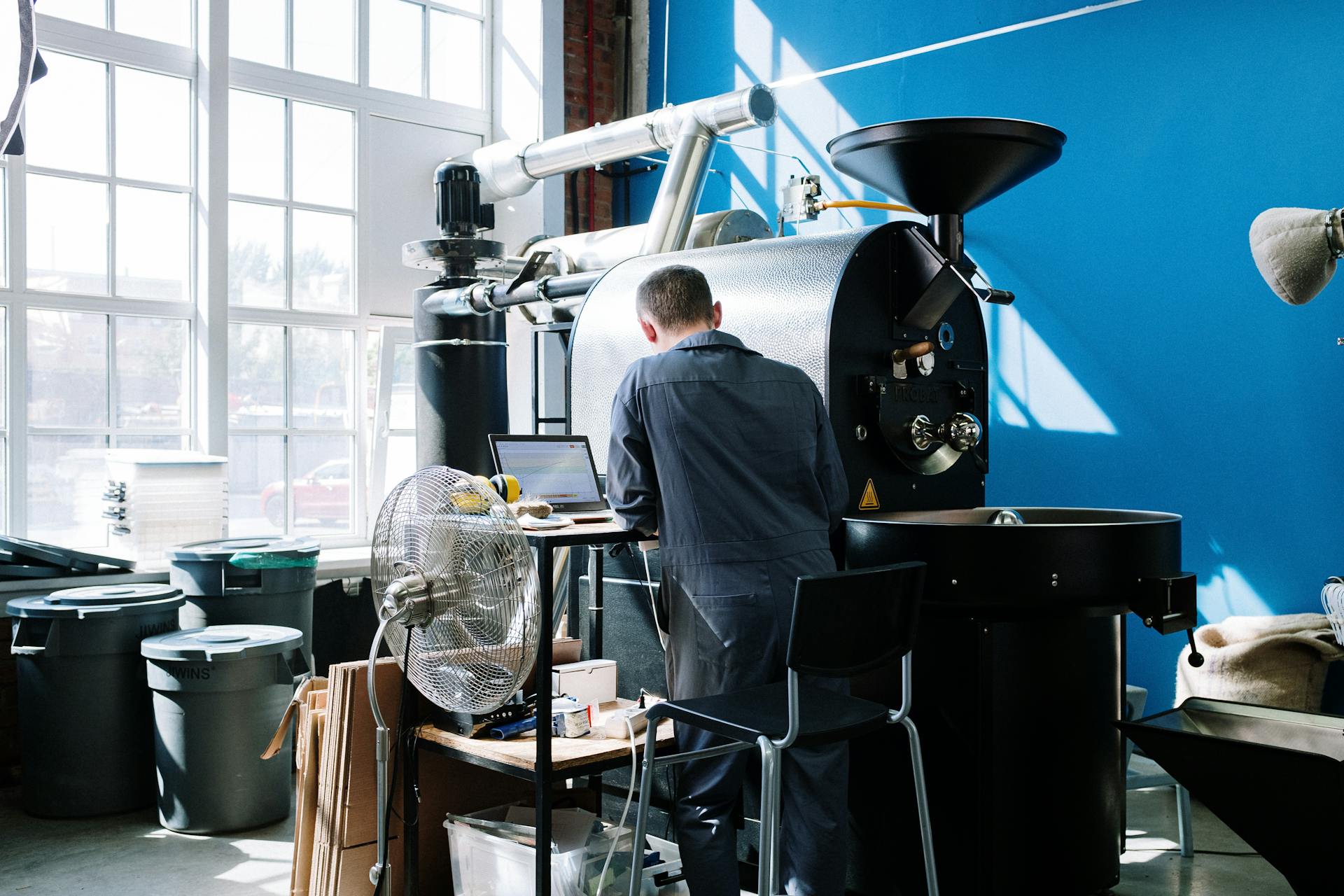
Letters and logos in signage, toys and games, and various industrial applications are also possible with these machines.
Here are some examples of applications for vacuum formers and thermoformers:
- Packaging
- Custom chocolate making
- Small business applications
- Automotive parts
- Aerospace parts
- Medical components like prosthetics and dental guards
- Letters and logos in signage
- Toys and games
- Various industrial applications
Vacuum forming machines, in particular, are known for their ease and affordability in mold production, making them a great option for projects that require high-quality, cost-effective results.
Understanding Vacuform Machines
Vacuform machines are a type of plastic forming machine that uses vacuum pressure to shape thin sheets of plastic into specific forms or shapes.
They come in various types, including semi-automatic and fully automatic machines, with the latter being more efficient and adaptable.
The HD Series, for example, is a semi-automatic machine that operates semi-autonomously using sheet materials, and was first introduced in 2002, establishing a new price-performance ratio for semi-automatic production class machines.
The TF Series, on the other hand, is a fully automatic machine designed for reel feed packaging and decorative film applications, such as chocolate trays and inserts.
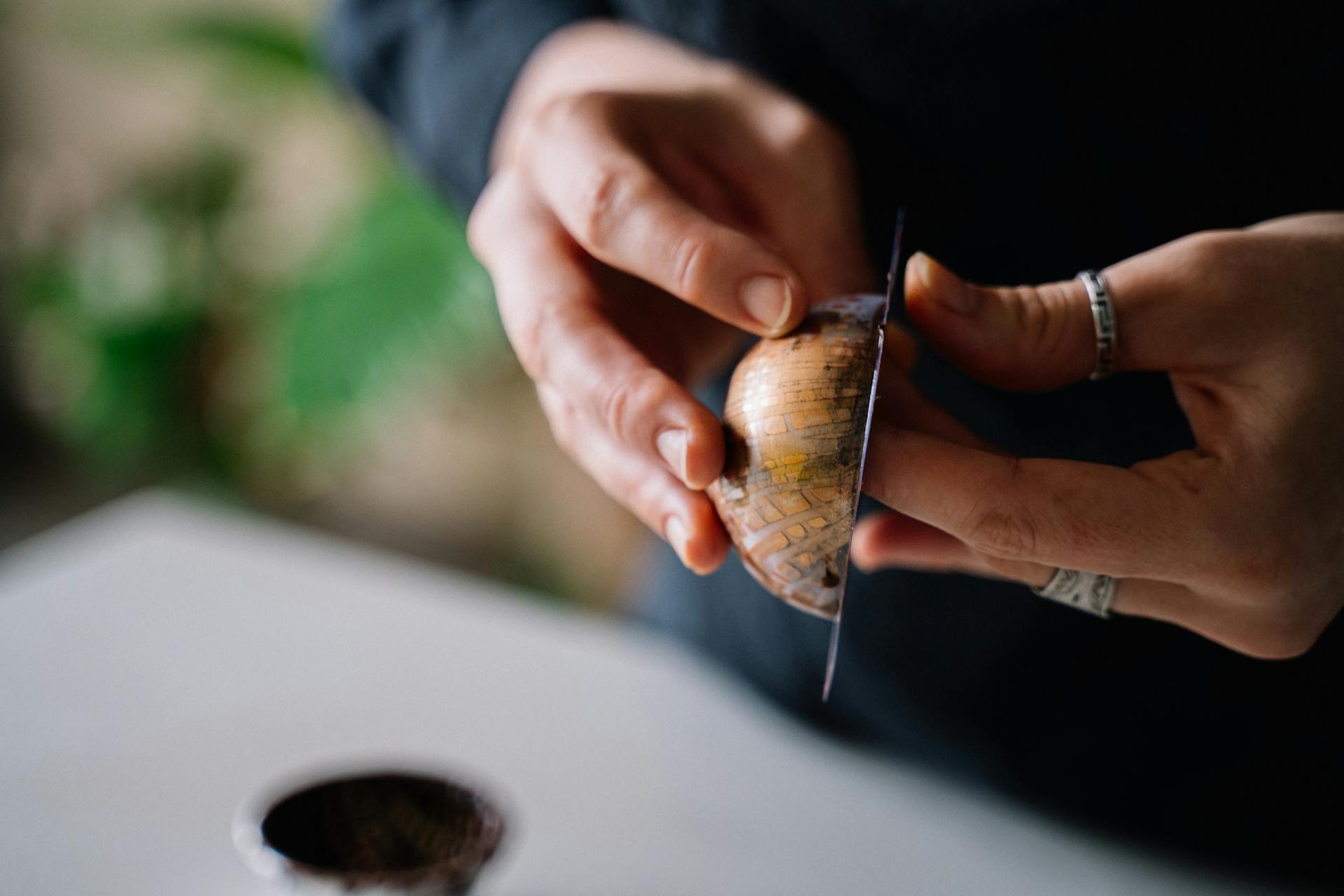
Vacuform machines work by heating the plastic sheet until it becomes soft and pliable, then positioning it over a mold, creating a vacuum to shape it into the desired form, and finally cooling and removing the part.
This process can be done manually or using an automated system, with some machines offering plug assist and being able to process reel materials up to 0.07" (1.8mm) and sheet materials up to 0.25" (6mm).
The vacuum forming process involves several steps, including preparing the mold, heating the plastic sheet, positioning the plastic sheet, creating a vacuum, and cooling and removing the part.
Some vacuform machines are designed specifically for reel feed packaging and decorative film applications, while others are more versatile and can adapt to a diverse number of applications.
Here's a comparison of the HD and TF Series machines:
Overall, vacuform machines are a popular and affordable type of 3D forming technology that can efficiently and affordably create molds, making them a great option for various projects and applications.
Vacuform Machine Basics
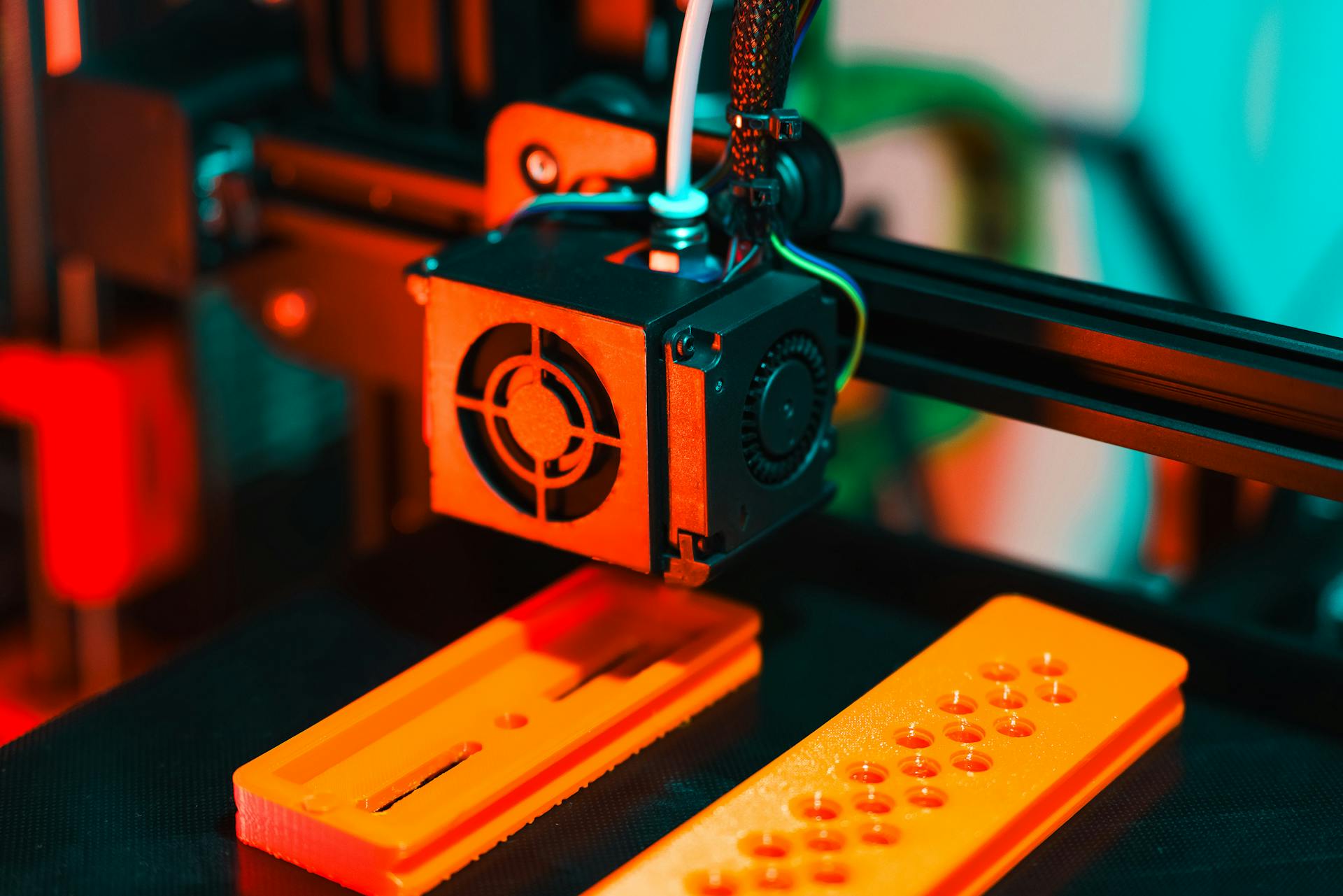
A vacuum form machine, also known as a vacuum former or thermoformer, is a device that uses vacuum pressure to shape thin sheets of plastic into specific forms or shapes.
The heating element or oven in the plastic vacuum forming machine plays a pivotal role in the thermoforming process, heating the plastic sheet to a specific temperature, usually just below its melting point.
A vacuum former is used to create plastic parts, custom molds, and products by shaping thin sheets of plastic into specific forms or shapes using vacuum pressure. It is commonly used in various manufacturing and fabrication processes, including food packaging, decorative items, and custom product manufacturing.
The vacuum system is a crucial component that removes air from between the softened plastic sheet and the mold, creating atmospheric pressure that forces the pliable plastic to conform precisely to the contours of the mold.
Here are the main components of a vacuum forming machine:
- Heating element or oven
- Frame or platform that holds the mold
- Vacuum system
- Molds (made from materials like aluminum, wood, or composite materials)
- Cutting tools or trimming mechanisms (optional)
Main Components
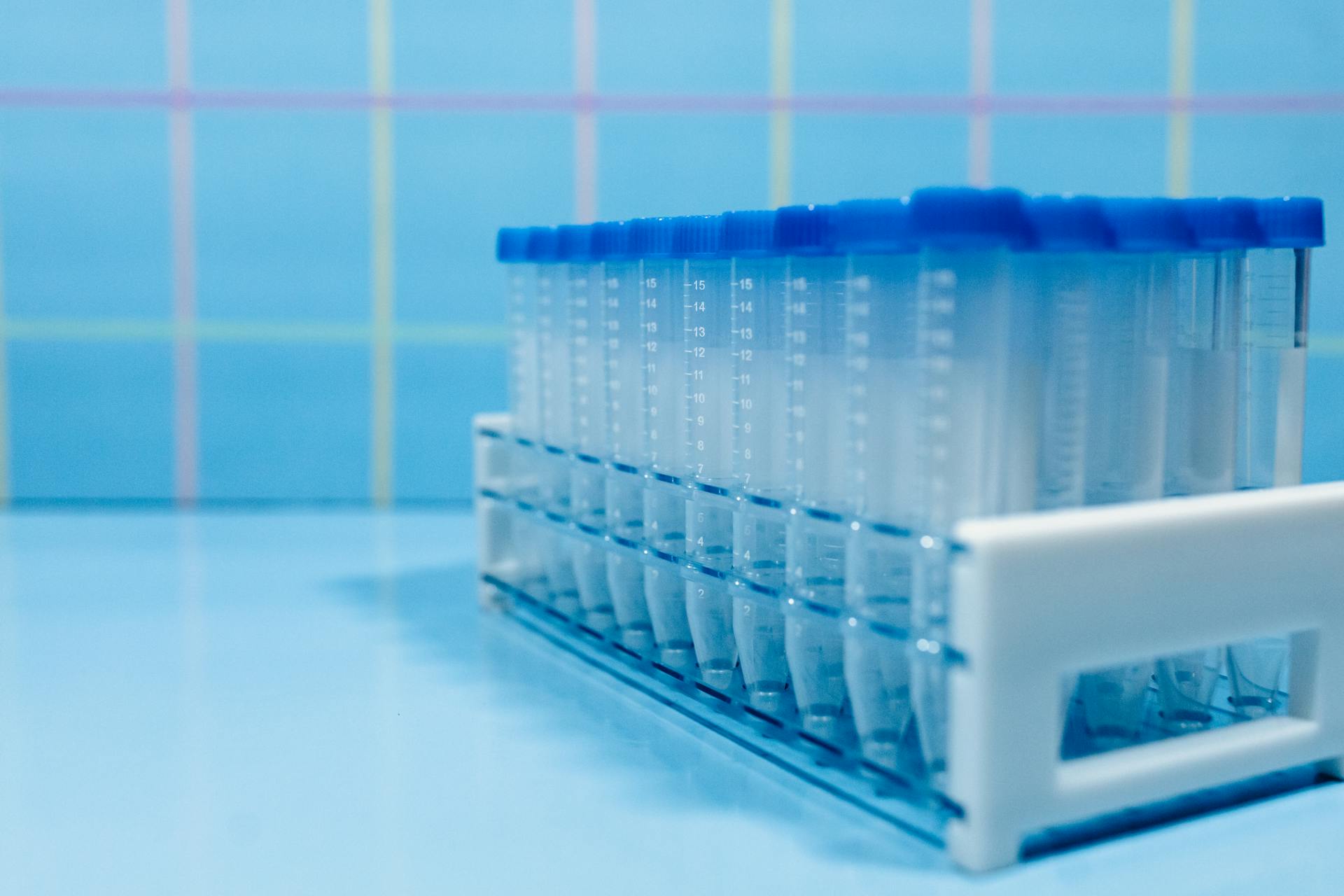
The main components of a vacuum forming machine are crucial to its functionality.
The heating element or oven is a pivotal part, heating the plastic sheet to a specific temperature just below its melting point, making it pliable and easily moldable.
The frame or platform that holds the mold is the base for the forming process, securing the mold in place and providing stability for the plastic sheet during forming.
Molds are typically made from aluminum, wood, or composite materials, and are custom-designed to replicate the desired shape or pattern for the final plastic product.
The vacuum system removes air from between the softened plastic sheet and the mold, creating atmospheric pressure that forces the pliable plastic to conform precisely to the contours of the mold.
A strong vacuum ensures an even and accurate forming process, resulting in high-quality finished products.
Thermoforming Basics
A vacuum former and thermoformer are both machines used to create plastic parts, custom molds, or products. They share some similarities, but also have key differences.
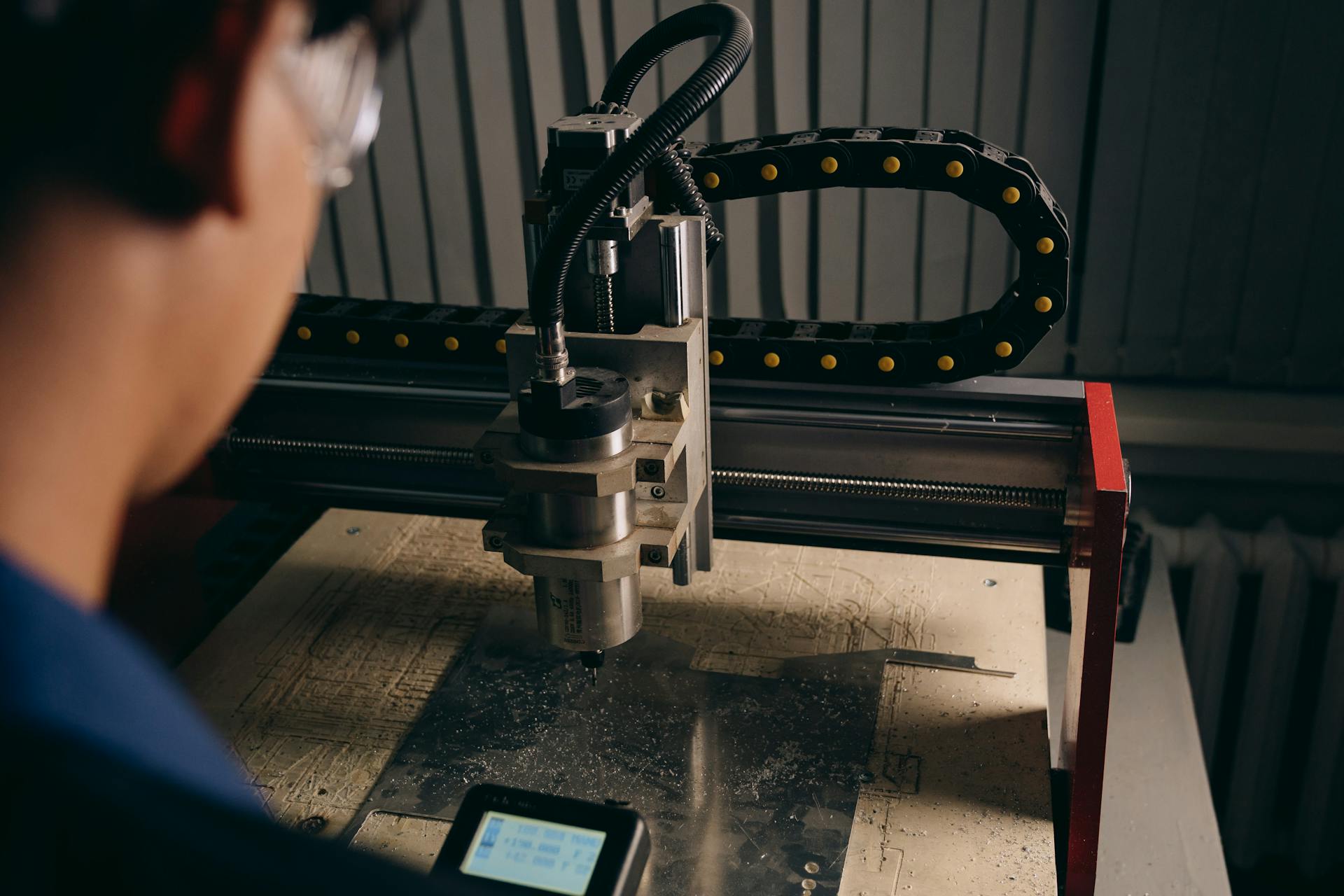
A vacuum former uses vacuum pressure to shape thin sheets of plastic into a specific form or shape. It heats the plastic sheet until it becomes soft and pliable, and then uses a vacuum pump to remove the air from the space between the plastic and the mold, creating a tight fit that conforms to the shape of the mold.
The heating element or oven in the plastic vacuum forming machine plays a pivotal role in the thermoforming process. It heats the plastic sheet to a specific temperature, usually just below its melting point, making it pliable and easily moldable.
The vacuum system is a crucial component that removes air from between the softened plastic sheet and the mold. This process creates atmospheric pressure, forcing the pliable plastic to conform precisely to the contours of the mold, capturing its shape and details.
A vacuum former is used to create plastic parts, custom molds, and products by shaping thin sheets of plastic into specific forms or shapes using vacuum pressure. It is commonly used in various manufacturing and fabrication processes, including mold production and product fabrication.
Vacuum forming is a popular and affordable type of 3D forming technology. This type of plastic forming machine is renowned for its ability to efficiently and affordably create molds.
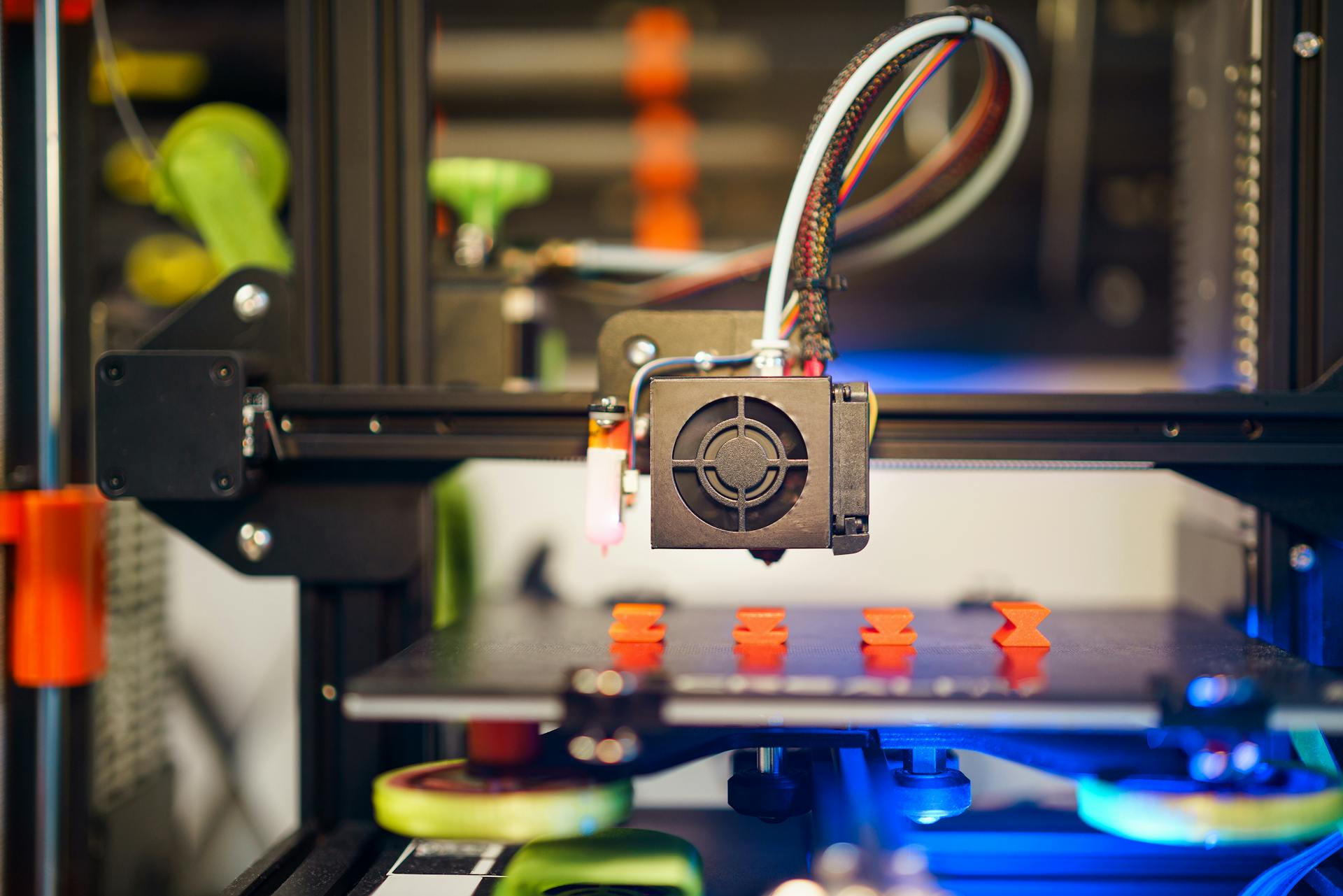
Here are the main components of a vacuum forming machine:
- Heating element or oven
- Frame or platform
- Molds (made from aluminum, wood, or composite materials)
- Vacuum system
- Cutting tools or trimming mechanisms (in advanced machines)
The vacuum forming process involves five basic steps:
1. Preparing the mold
2. Heating the plastic sheet
3. Positioning the plastic sheet
4. Creating a vacuum
5. Cooling and removing the part
Vacuform Machine Comparison
A small, tabletop vacuum former can cost a few hundred dollars, while a large industrial-grade machine can cost tens of thousands of dollars or more.
Desktop vacuum formers are typically the least expensive type and can cost anywhere from a few hundred dollars to a few thousand dollars. They are designed for hobbyists or small-scale production and can be used to create small parts or prototypes.
Mid-size vacuum formers are larger and more powerful than tabletop vacuum formers and can cost anywhere from several thousand to tens of thousands of dollars. They are typically used for more advanced prototyping or small-scale production.
Here's a comparison of the different types of vacuum formers:
Large industrial-grade vacuum formers are the most expensive type and can cost tens of thousands of dollars or more. They are designed for high-volume production of large parts or products and may require specialized training or expertise to operate.
Thermoforming vs Injection Molding
Thermoforming is ideal for larger items and shorter runs due to lower tooling costs, which makes it perfect for projects that require a lot of plastic.
Thermoforming shapes plastic by heating and molding sheets, a process that's ideal for larger items.
One of the main advantages of thermoforming is that it's more cost-effective, especially for smaller production runs.
Lower tooling costs mean that you can produce larger items without breaking the bank, making it a great option for projects with bigger budgets.
Injection molding, on the other hand, is better suited to high-volume production, which makes it perfect for projects that require a lot of smaller, more complex parts.
Injection molding involves injecting molten plastic into molds for consistent precision, which is essential for high-volume production.
In contrast, thermoforming is more flexible and can produce a wide range of items, from simple packaging to complex medical devices.
Overall, the choice between thermoforming and injection molding depends on your specific project needs and goals.
Pressure Forming Comparison
Pressure forming is a plastic thermoforming process that applies additional force with air pressure for sharper detail, resulting in parts that are closer in quality to injection molding.
This method is ideal for intricate, high-quality parts that require a high level of precision. Vacuum forming, on the other hand, is cost-effective and suited for simpler designs.
Pressure forming can produce parts with a higher level of detail, making it a better choice for projects that require complex shapes or designs.
Vacuform Machine Costs and Materials
Vacuform machine costs can vary widely, depending on factors such as machine size, features, and manufacturer. A small, tabletop vacuum former can cost a few hundred dollars, while a large industrial-grade machine can cost tens of thousands of dollars or more.
Desktop vacuum formers are typically the least expensive option, costing anywhere from a few hundred dollars to a few thousand dollars. They're ideal for hobbyists or small-scale production.
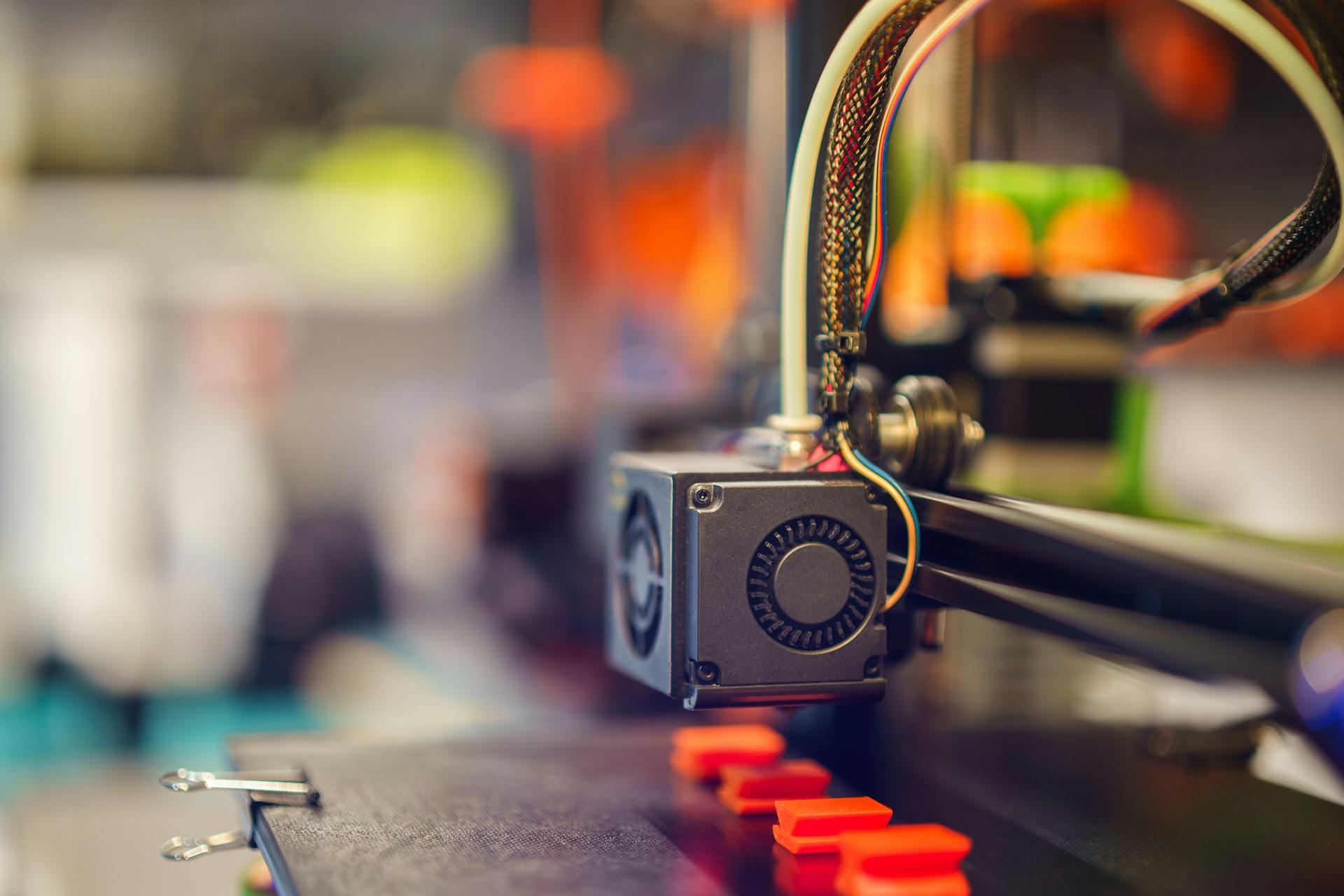
Mid-size vacuum formers are larger and more powerful, costing several thousand to tens of thousands of dollars. They're suitable for more advanced prototyping or small-scale production.
Large industrial-grade vacuum formers are the most expensive option, costing tens of thousands of dollars or more. They require specialized training or expertise to operate and are designed for high-volume production.
Vacuform machines can accommodate a range of durable materials, including ABS, polycarbonate, HDPE, and PETG. These materials cater to different application requirements and offer various benefits such as impact resistance, clarity, toughness, and ease of recycling.
Here are some common materials used in vacuum forming:
- ABS for impact resistance
- Polycarbonate for clarity and strength
- HDPE for toughness
- PETG for versatility and ease of recycling
Thermoformer Cost
A vacuum former can cost anywhere from a few hundred dollars to tens of thousands of dollars or more, depending on the size and features of the machine.
The cost of a vacuum former varies widely, with desktop models being the least expensive, typically costing a few hundred dollars to a few thousand dollars.
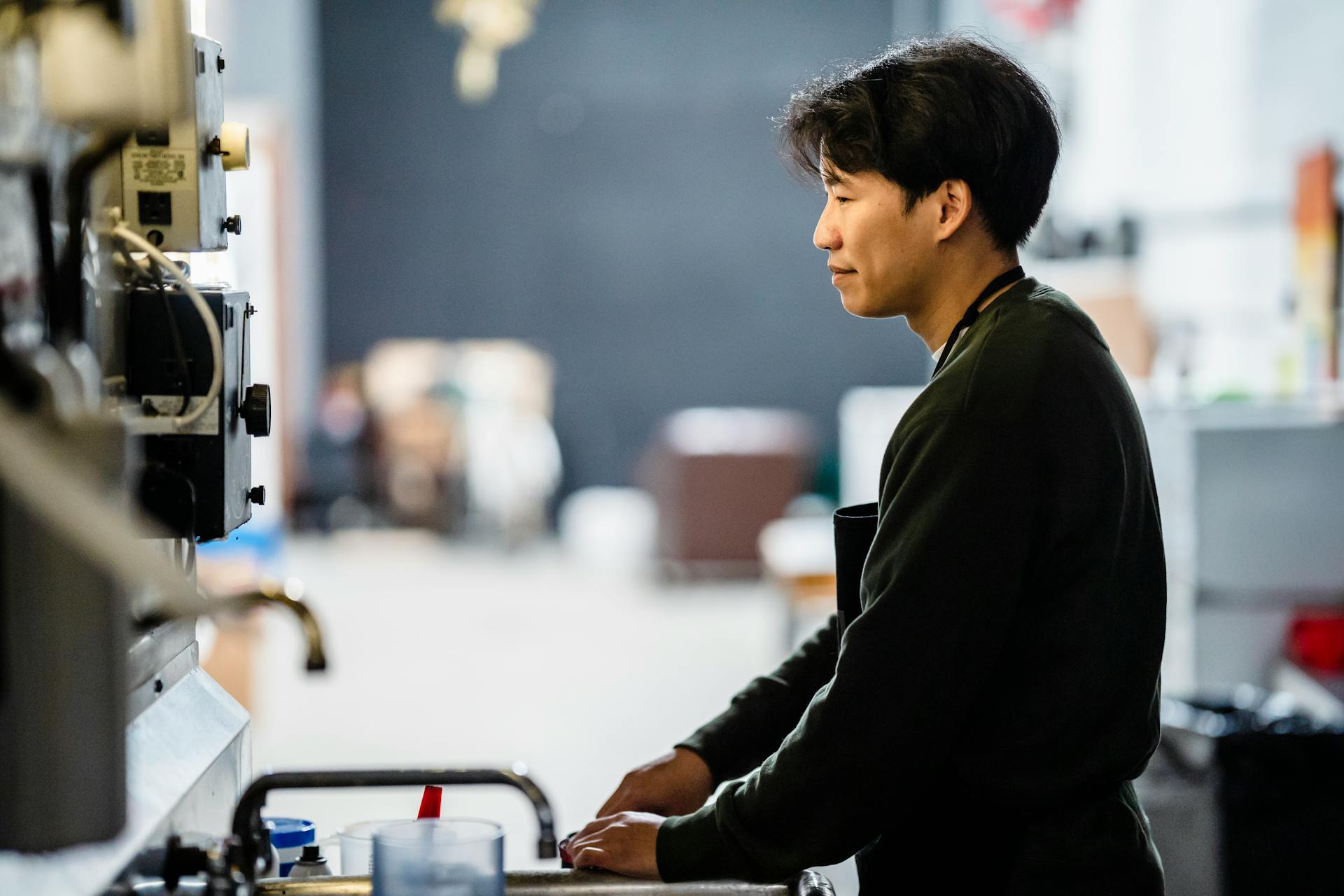
For mid-size vacuum formers, the price range is several thousand to tens of thousands of dollars, depending on the size and features.
Large industrial-grade vacuum formers are the most expensive, costing tens of thousands of dollars or more and requiring specialized training or expertise to operate.
Here's a rough breakdown of the price ranges for different types of vacuum formers:
- Desktop vacuum formers: $100-$3,000
- Mid-size vacuum formers: $3,000-$30,000
- Large industrial-grade vacuum formers: $30,000-$100,000+
Suitable Materials for Pressure
Pressure forming is a versatile manufacturing process that can work with a variety of materials.
ABS is a popular choice for pressure forming due to its impact resistance, making it suitable for applications where durability is key.
Polycarbonate is another option, prized for its clarity and strength, which makes it ideal for applications where transparency is important.
HDPE is also a suitable material for pressure forming, offering toughness and a long lifespan.
PETG is a versatile material that's easy to recycle, making it a great choice for applications where sustainability is a priority.
Sources
- https://www.formech.com/category/vacuum-forming-machines
- https://www.alibaba.com/showroom/vacuum-forming-machine.html
- https://www.matterhackers.com/store/c/desktop-vacuum-formers
- https://www.widgetworksunlimited.com/12_x12_Hobby_Vacuum_Former_p/vf-12x12-vac_former.htm
- https://shop3duniverse.com/collections/3d-forming-machines
Featured Images: pexels.com