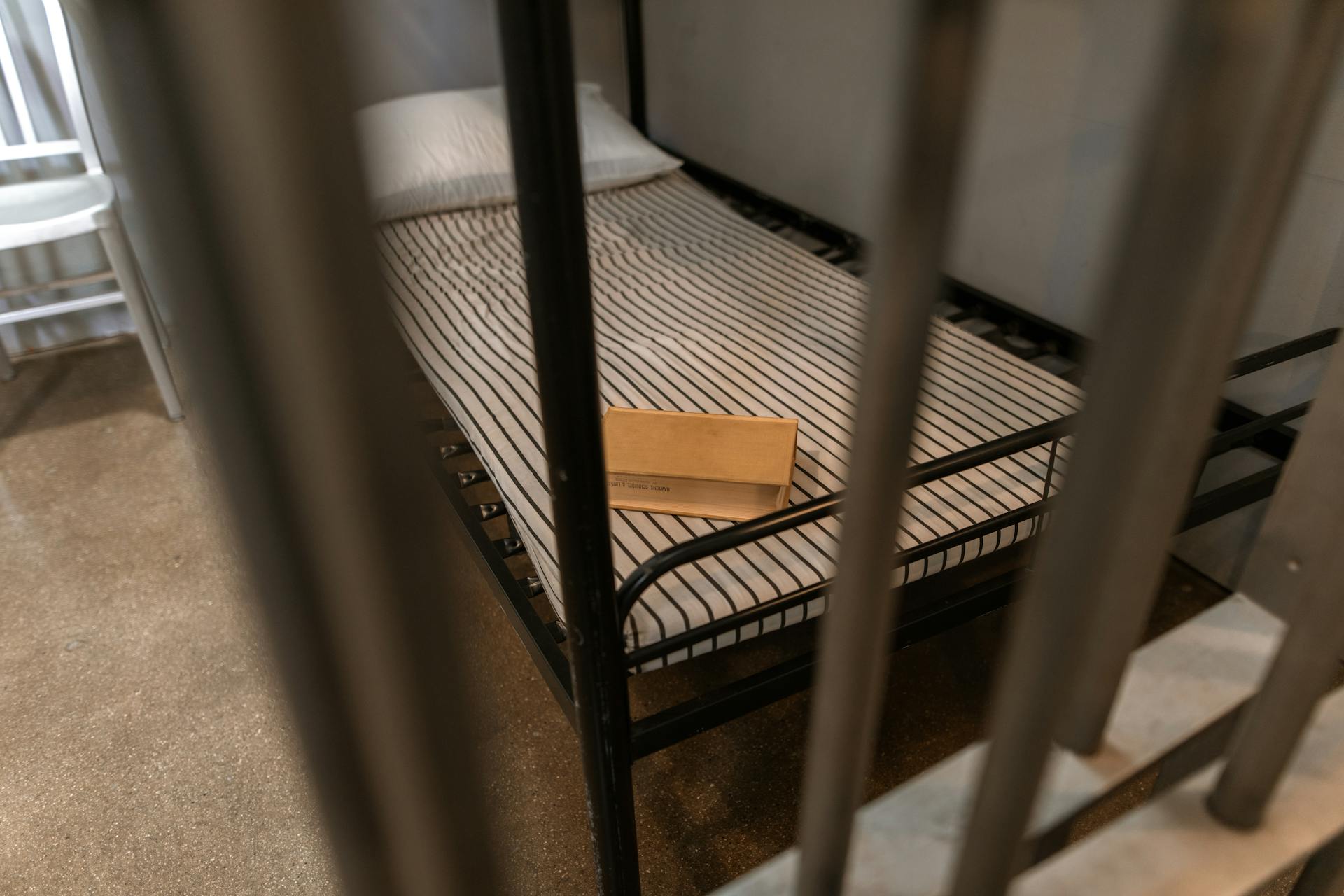
PU foam is a game-changer for sustainable and eco-friendly projects. It's a type of foam made from polyurethane, which is a non-toxic and recyclable material.
PU foam is incredibly versatile and can be molded into various shapes and forms, making it perfect for custom projects. It's also lightweight, yet incredibly durable.
One of the biggest advantages of PU foam is its insulation properties, which can help reduce energy consumption and lower carbon emissions. By using PU foam in building insulation, we can significantly reduce the amount of energy needed to heat and cool buildings.
With its eco-friendly properties and endless design possibilities, it's no wonder PU foam is becoming a go-to material for sustainable projects.
Here's an interesting read: Pu Foam Material
Applications and Uses
Polyurethane foam is a versatile material with a wide range of applications. It's durable and can maintain its form even after repeated impacts.
The packaging industry relies on polyurethane foam's ability to absorb shocks repeatedly while retaining its original cushioning properties. This makes it an ideal material for protecting items during shipping.
A unique perspective: White Foam Packing Material
In addition to packaging, polyurethane foam is also used in the bedding and furniture industry, where its ability to maintain its shape is crucial. Its versatility also makes it suitable for various other uses, including:
- Soft furnishing manufacture
- Medical cushioning & support
- Automotive seating
- Acoustic insulation
- Strips, gaskets & seals
- Pipe lagging
- Packaging protection
- Clothing & textile manufacture
Primary Applications
Polyurethane foam is an incredibly versatile material, and its primary applications reflect its impressive range of uses.
One of its key applications is in the bedding and furniture industry, where it's used to create durable and comfortable products. This is because polyurethane foam can maintain its form and cushioning properties even after repeated impacts.
In the packaging industry, polyurethane foam is used to absorb shocks repeatedly while retaining its original cushioning properties, making it an ideal material for protecting fragile items during shipping.
Polyurethane foam is also used in various construction applications, including filling and insulating gaps between different types of building materials, and bonding embedded electrical fittings such as cable-runs and junction boxes.
Here are some of the primary applications of polyurethane foam:
Sustainable Straw
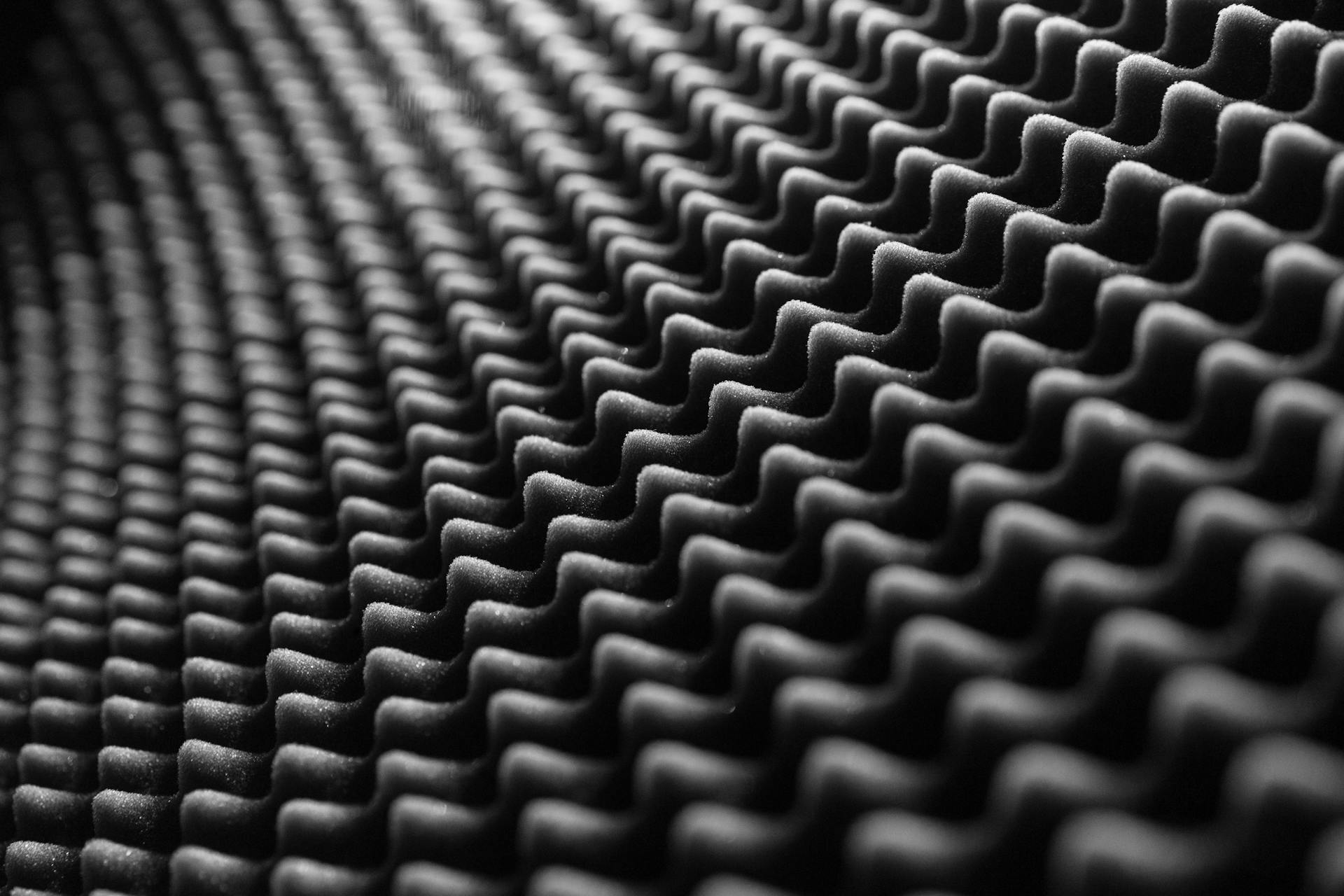
Sustainable Straw is a game-changer for environmentally conscious builders and homeowners. It's a one-component, ready-to-use polyurethane straw foam that contains over 50% of sustainable raw materials.
The foam has good volume expansion for effective filling of holes and gaps, making it perfect for sealing window and door joints. This means you can achieve airtight sealing without worrying about deformation of building elements.
Using a polyurethane foam provides a durable seal that adheres well to most materials like wood, concrete, stone, plaster, metal, PVC, and polystyrene. This versatility is a huge plus for builders and homeowners alike.
The packaging of Sustainable Straw is also eco-friendly, with over 80% of the plastic content being recycled. Even the foam cap and straw are made of 100% recycled plastic.
Here are some key benefits of Sustainable Straw at a glance:
- 50% of the ingredients are based on recycled and biobased materials
- More than 80% of the plastic content in the packaging is recycled
- Foam cap and straw made of 100% recycled plastic
- Produced with 100% green electricity
Gap Filling
Gap filling is a crucial aspect of various applications, including construction, automotive, and manufacturing. It involves filling gaps and holes to prevent air leaks, water intrusion, and thermal bridging.
PU Foam 1000 can be used for manual and gun application, and it's recommended to start filling from the lowest, deepest part of the gap and work upwards. The foam will expand to fill the gap completely.
For larger gaps, it's best to apply multiple layers of PU Foam 1000, waiting for each layer to expand before applying the next one. This ensures a thorough and effective fill.
Low isocyanate monomer straw foam is another option for gap filling, offering higher post-expansion and better gluing properties compared to gun foams. It's suitable for sealing window and door perimeter joints, insulation of various penetrations, and filling of holes and gaps.
Sustainable Straw Foam is a one-component, ready-to-use polyurethane straw foam that contains over 50% sustainable raw materials. It has good volume expansion, low curing pressure, and adheres well to various materials.
Here are some key benefits of using gap filling products:
- Effective filling of holes and gaps
- Good thermal and sound insulation properties
- Low curing pressure to avoid deformation of building elements
- Airtight sealing and gluing properties
Gap filling gun foam is a softer structured foam with very low curing pressure and post expansion, making it suitable for filling of holes, insulation of penetrations, and sealing and connection of joints.
Desert
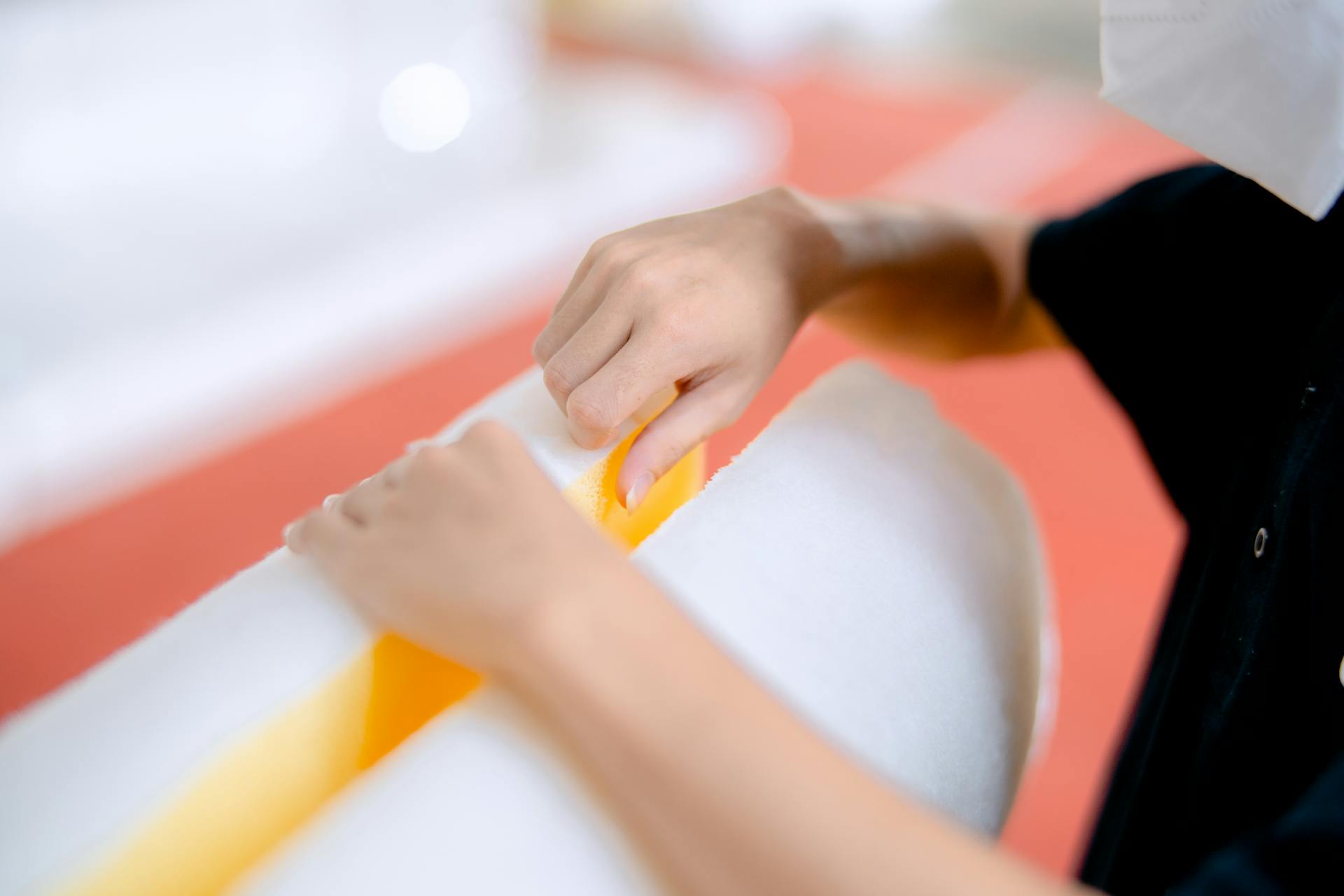
Desert environments can be unforgiving, but with the right tools, you can tackle even the harshest conditions. Desert Gun Foam is a game-changer for hot and dry climates.
This polyurethane gunfoam is specifically designed to thrive in such environments, making it perfect for various building applications. It adheres well to most materials like wood, concrete, stone, plaster, metal, PVC, and polystyrene.
One of the key benefits of Desert Gun Foam is its high yield, allowing you to get more done with less material. This is especially useful when working on larger projects.
Low curing pressure is another advantage, which means it won't bend or warp window frames like other products might. This helps preserve the integrity of your building's structure.
Manufacturing and Composition
Polyurethane foam is made from the reaction of two key chemicals, a polyol and an isocyanate with water. This reaction happens instantly, forming a bubbly froth that hardens into a slabstock bun.
The manufacturing process is similar to bread rising, taking only minutes to complete. The resulting foam can be fabricated into various forms and products.
Flame retardant additives can be introduced during the manufacturing process to meet specific fire code standards.
Related reading: Pu Foam Process
Characteristics
Polyurethane foam, also known as PU, is a highly versatile material with a wide range of applications.
Its compress-ability and cushioning properties make it perfect for use in furniture and packaging.
The open-cell structure of polyurethane foam allows it to absorb energy and reduce vibrations.
This material is also incredibly flexible, with a wide hardness spread selection from 20 Newtons to 295 Newtons.
You can find polyurethane foam in a variety of forms, including sheets, rolls, strips, gaskets, and seals.
Its low thermal conductivity and low water vapor transmission make it an excellent insulator.
Here are some of the key characteristics of polyurethane foam:
- Compress-ability
- Cushioning
- Energy absorption
- Fabrication-ability
- Flexibility
- Insulating
- Light-weight
- Low thermal conductivity
- Low water vapor transmission
- Resiliency
- Sound absorption
- Vibration dampening
Polyurethane foam is also available in polyether and polyester formats, offering a range of options for different applications.
Its average density is around 24 kg/m, making it a lightweight yet durable material.
The open-cell structure of polyurethane foam also makes it highly useful in thermal insulation applications.
In terms of specifications, polyurethane foam is commonly used in cushioning, packaging, and sealing applications.
Its density ranges from 22 to 29 kg/m, and it's available in a variety of colors, including dark grey as standard.
PU
PU foam, or polyurethane foam, is a highly versatile and widely used material in various industries. It's a flexible, open-cell type of foam that exhibits excellent compress-ability, cushioning, energy absorption, and fabricability.
Polyurethane foam can be manufactured to provide varying degrees of comfort, support, and durability, making it an aesthetically pleasing material while still providing adequate protection and support. It's available in different densities, ranging from 1 to 6 pounds per cubic foot (PCF), and various colors, including pink, blue, and charcoal.
The material is highly durable, with excellent tear and abrasion resistance, making it perfect for use in furniture. It also possesses a superior softness and flexibility over other foam products. Polyurethane foam is used in a wide range of applications, including insulation, sealing, packaging, filters, clothing, and medical applications.
Here are the common characteristics of PU foam:
- Compress-ability
- Cushioning
- Energy absorption
- Fabrication-ability
- Flexibility
- Insulating
- Light-weight
- Low thermal conductivity
- Low water vapor transmission
- Resiliency
- Sound absorption
- Vibration dampening
PU foam can be supplied in various forms, including sheets, rolls, strips, gaskets, and seals, and can be produced plain or adhesive-backed for easy installation. It's also available in different hardness levels, ranging from 20 Newtons to 295 Newtons.
Manufacturing
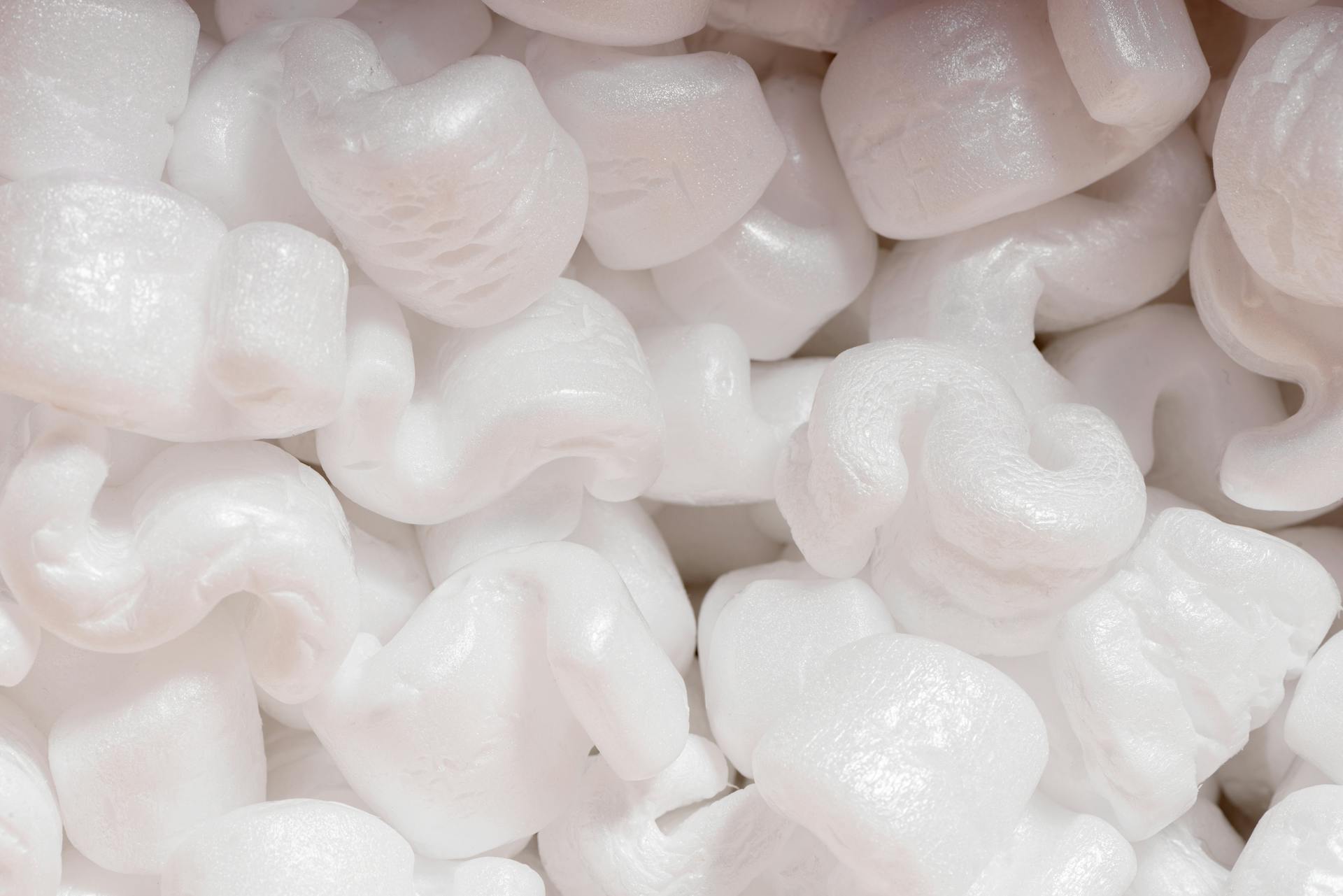
Manufacturing polyurethane foam is a fascinating process. The Polyurethane Foam Association identifies it as the reaction of two key chemicals, a polyol and an isocyanate, with water.
These two compounds are combined with other key ingredients and mixed together with the assistance of a blowing agent. The blowing agent is typically CO2, which blows little air pockets into the PU to form the foam.
The foaming begins instantly with the expanding formation of a bubbly froth. This process is similar to bread rising, and it happens in a matter of minutes.
The froth hardens, resulting in a slabstock bun of polyurethane foam ready for fabrication. During this manufacturing process, flame retardant additives can be introduced to meet various fire code standards.
The polyurethane foam can be produced in a variety of formats, including polyether and polyester. It's a highly versatile, open cell material that's used in a wide range of industries.
The manufacturing process allows for the introduction of various additives, such as anti-microbial, anti-static, conductive, and electrostatic dissipation (ESD) additives. This enables the creation of polyurethane foam with specific properties for different applications.
Polyurethane foam can be produced in a range of densities, with an average density of 24 kg/m. It can also be produced in various hardness levels, from 20 Newtons to 295 Newtons.
Types and Variations
There are several types of pu foam, including open-cell and closed-cell foam.
Open-cell pu foam is more breathable and flexible than closed-cell foam.
Closed-cell pu foam is more rigid and provides better insulation, but it can be more expensive.
Some pu foams are also treated with additives to enhance their performance or appearance.
Check this out: Green Cell Foam
Types of Polyurethane
Polyurethane comes in different types, and it all starts with the type of isocyanate used. TDI (diisocyanate) is used for flexible and semi-rigid foaming, while MDI (diisocyanate) is used for rigid foaming.
Expand your knowledge: Rigid Pu Foam Sheets
The type of isocyanate determines the type of polyurethane. TDI produces a flexible and semi-rigid polyurethane, while MDI produces a rigid one.
Polyurethane can be linear, unbranched, or branched and cross-linked. Linear polyurethane is like a rope, strong but structurally susceptible to bending and reshaping.
The branched and cross-linked polyurethane, on the other hand, is like a ladder, with multiple points of tension that allow for weight distribution and elasticity.
These differences in structure affect the properties of the polyurethane.
Polyester vs. Polyether
Polyester foam has a higher tensile strength than polyether foam, making it a better choice for applications where durability is crucial.
Polyester foam is also more resistant to hydrocarbons and alcohols than polyether foam, which is a significant advantage in certain industries.
In applications where the foam will come into contact with gases, such as oxygen, nitrogen, and/or carbon dioxide, polyurethane foam should be manufactured with polyester-based polyols.
Polyurethane foam that will be exposed to liquid-based solutions, on the other hand, should be made with polyether-based polyols to ensure compatibility.
Low Isocyanate Monomer Straw
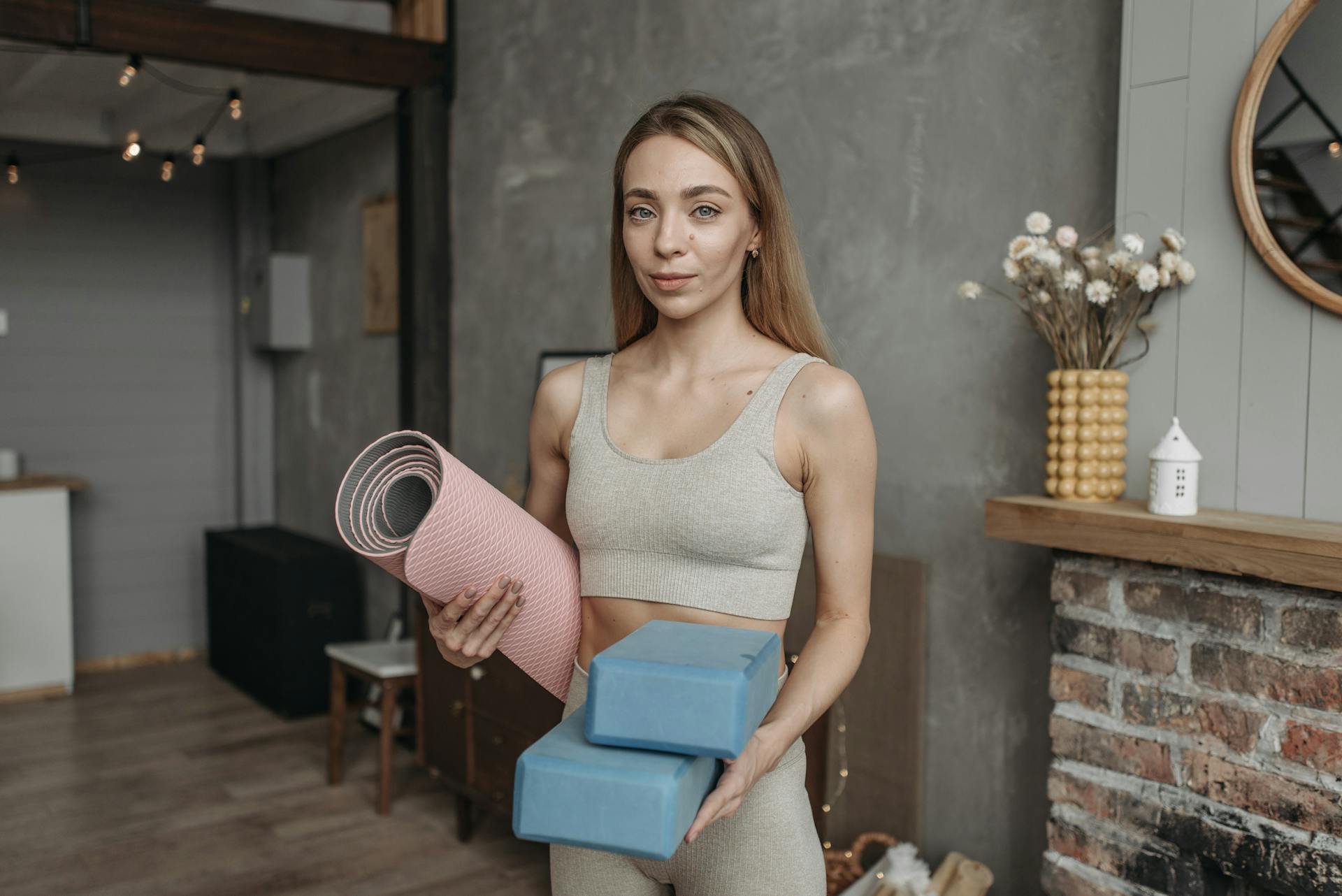
Low Isocyanate Monomer Straw foam is a dense and flexible structured foam with low curing pressure and enhanced UV-resistance.
It contains less than 0.1% free isocyanate monomers, making it an environment-friendly option.
This type of foam is well-suited for sealing of joints and cavities, insulation of penetrations, installation of window and door frames, and sealing of thermal or acoustic insulation boards.
Its higher post expansion compared to gun foams makes it effective for filling works, and its higher foam density gives better gluing properties.
As it can be used with a straw applicator, there is no need to spend additional money on a foam gun.
Consider reading: Spray Foam Insulation Shipping Container
Fast-Curing Adhesive
The Fast-Curing Adhesive is a game-changer in the world of building and construction. It's a single-component, ready-to-use polyurethane foam adhesive that cures rapidly.
This adhesive is strong and can bond different substrates, making it a great alternative to traditional adhesives. It's also incredibly versatile, allowing you to fix boards and panels both indoors and outdoors.
One of its key uses is fixing insulation boards on facades and foundations, which can be a real challenge in construction projects. It's also great for fixing interior design boards, windowsills, wooden, plaster, and decorative panels.
Here are some specific applications where this adhesive shines:
- Fixing of insulation boards on facades and foundations
- Fixing of interior design boards
- Fixing of windowsills
- Fixing of wooden, plaster and decorative panels
- Strengthening screw connections and reducing screw usage
Part III: Additives
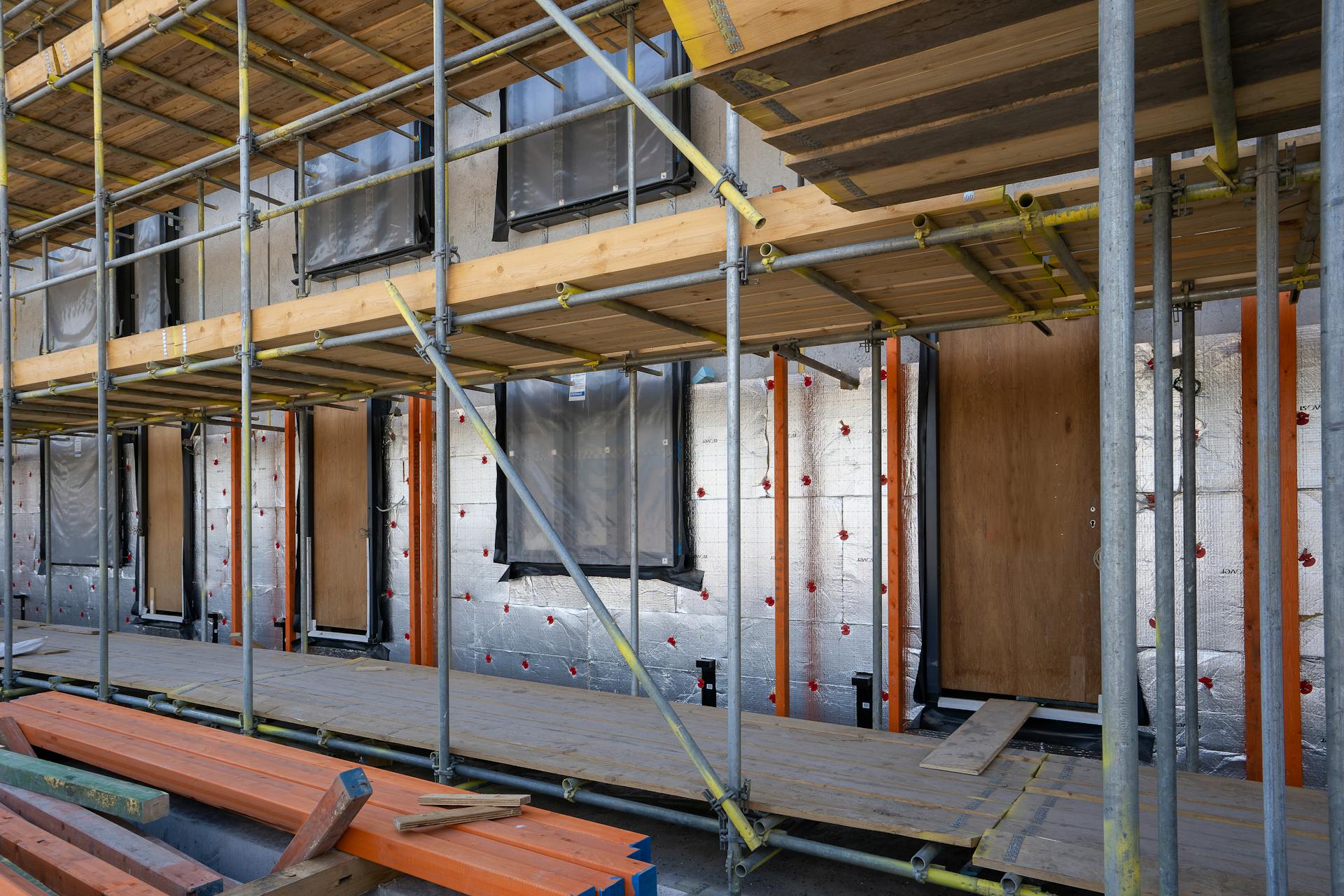
Additives play a crucial role in polyurethane (PU) foaming, and they come in various forms to achieve different effects.
Catalysts speed up the expansion and gelling process, while also cooling the reaction to reduce fire hazards. This is especially important for PU production, as high temperatures can be a major concern.
Surfactants, like emulsifiers, help mix oil and water into a uniform mixture, resulting in a smoother reaction and more even cell sizes.
Physical blowing agents reduce the fire hazard associated with water blowing, which is a common method used in PU foaming. These additives encourage cell expansion without relying on chemical reactions.
Fillers, including particulate and fibrous types, can add physical properties like tensile or compressive strength to foam, while also reducing costs by minimizing the amount of liquid chemicals used.
Flame retardants are another essential additive, but their use is heavily regulated due to concerns over their impact on consumer health. Different countries have varying regulations on flame retardant types and testing methods.
Usage and Application
Polyurethane foam is a versatile material with a wide range of applications, including bedding and furniture, where it's used for its durability and ability to maintain its original cushioning properties.
The packaging industry relies on polyurethane foam for its shock-absorbing capabilities, allowing it to retain its original form even after repeated impacts.
For manual application, you'll need to remove the protective cap and screw the feed tube to the spray nozzle, then hold the can upside down and feed the foam into the area starting from the lowest, deepest part.
To fill larger gaps, it's recommended to apply several layers of product, waiting between each layer until the previous one has expanded before applying the next one.
PU Foam 1000 can be applied using either a manual or gun application method, with the gun application allowing for more control over the amount of foam fed into the area.
The packaging industry uses polyurethane foam for its ability to absorb shocks repeatedly while retaining its original cushioning properties.
Intriguing read: Foam Packaging Materials
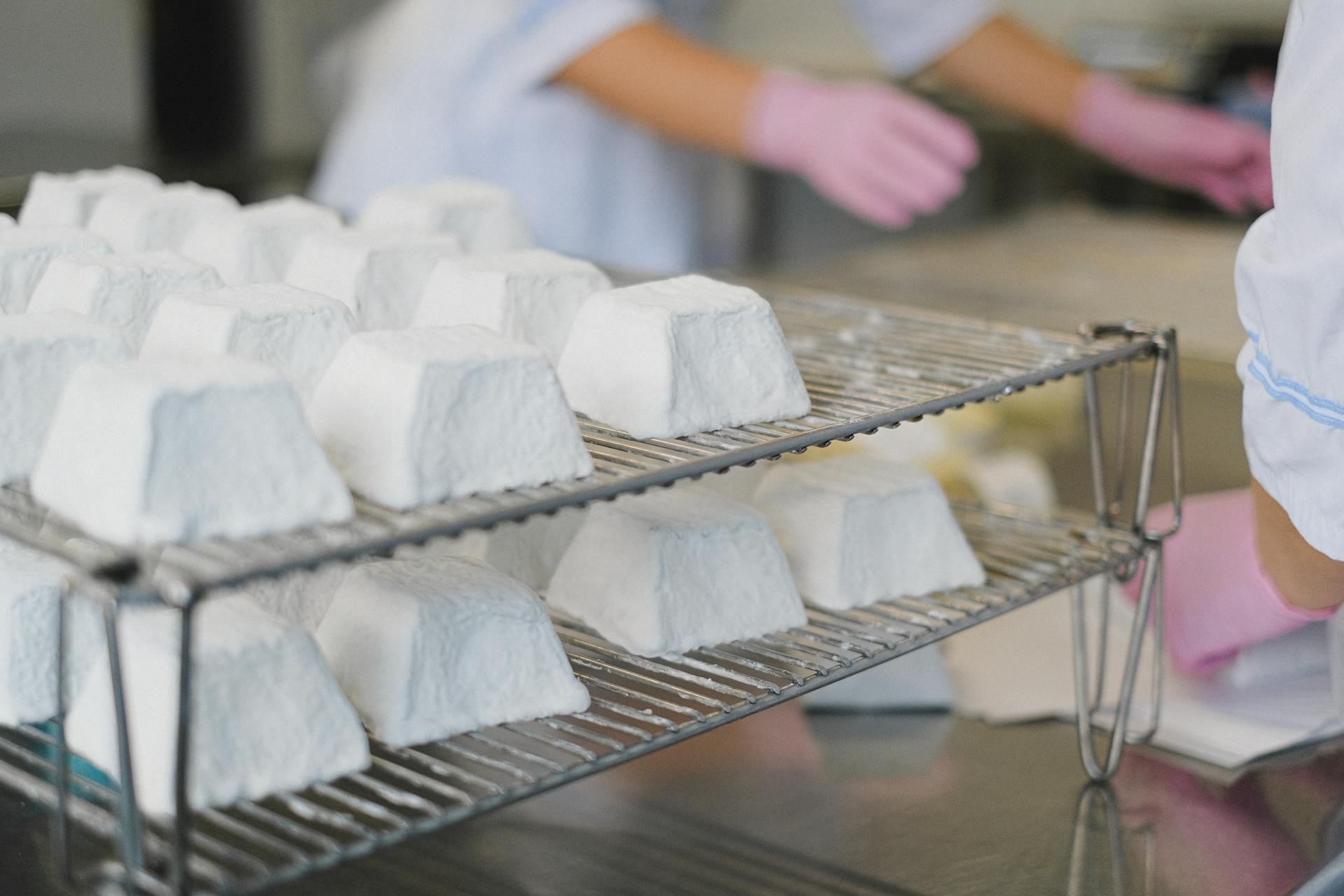
The ideal time to fill a gap with polyurethane foam is when it's around 50-60% of its volume, as this allows the material to expand and fill the space completely.
Here are some potential applications for polyurethane foam:
- Soft furnishing manufacture
- Medical cushioning & support
- Automotive seating
- Acoustic insulation
- Strips, gaskets & seals
- Pipe lagging
- Packaging protection
- Clothing & textile manufacture
Cleaning and Maintenance
To keep your pu foam in good condition, it's essential to clean it regularly.
Regular cleaning helps prevent dirt and debris from accumulating and causing damage to the foam.
You can use a mild soap solution to clean your pu foam, but be sure to rinse it thoroughly to prevent any residue from affecting its performance.
Make sure to avoid using harsh chemicals or abrasive cleaners that can damage the foam.
For more intense cleaning, you can use a mixture of equal parts water and white vinegar to remove stubborn stains and odors.
This solution is gentle yet effective in maintaining the cleanliness and quality of your pu foam.
To prevent damage and extend the lifespan of your pu foam, it's crucial to store it properly when not in use.
This means keeping it away from direct sunlight, moisture, and extreme temperatures.
It's also a good idea to inspect your pu foam regularly for signs of wear and tear, such as cracks, tears, or discoloration.
Addressing any issues promptly can help prevent further damage and maintain the overall quality of the foam.
Frequently Asked Questions
Is PU foam mattress good or bad?
A PU foam mattress is not recommended for regular use due to its poor comfort and short lifespan. It's best to explore other options for a comfortable and long-lasting sleeping surface.
Is PU foam hard or soft?
PU foam can be either hard or soft, depending on its type and density, making it suitable for a range of applications. Understanding the difference between soft and hard PU foam is key to selecting the right type for your needs.
What are the downsides of polyurethane foam?
Polyurethane foam can be expensive and has a significant environmental impact due to its production and disposal. Additionally, it may release toxic fumes during and after installation, posing health risks.
Sources
Featured Images: pexels.com