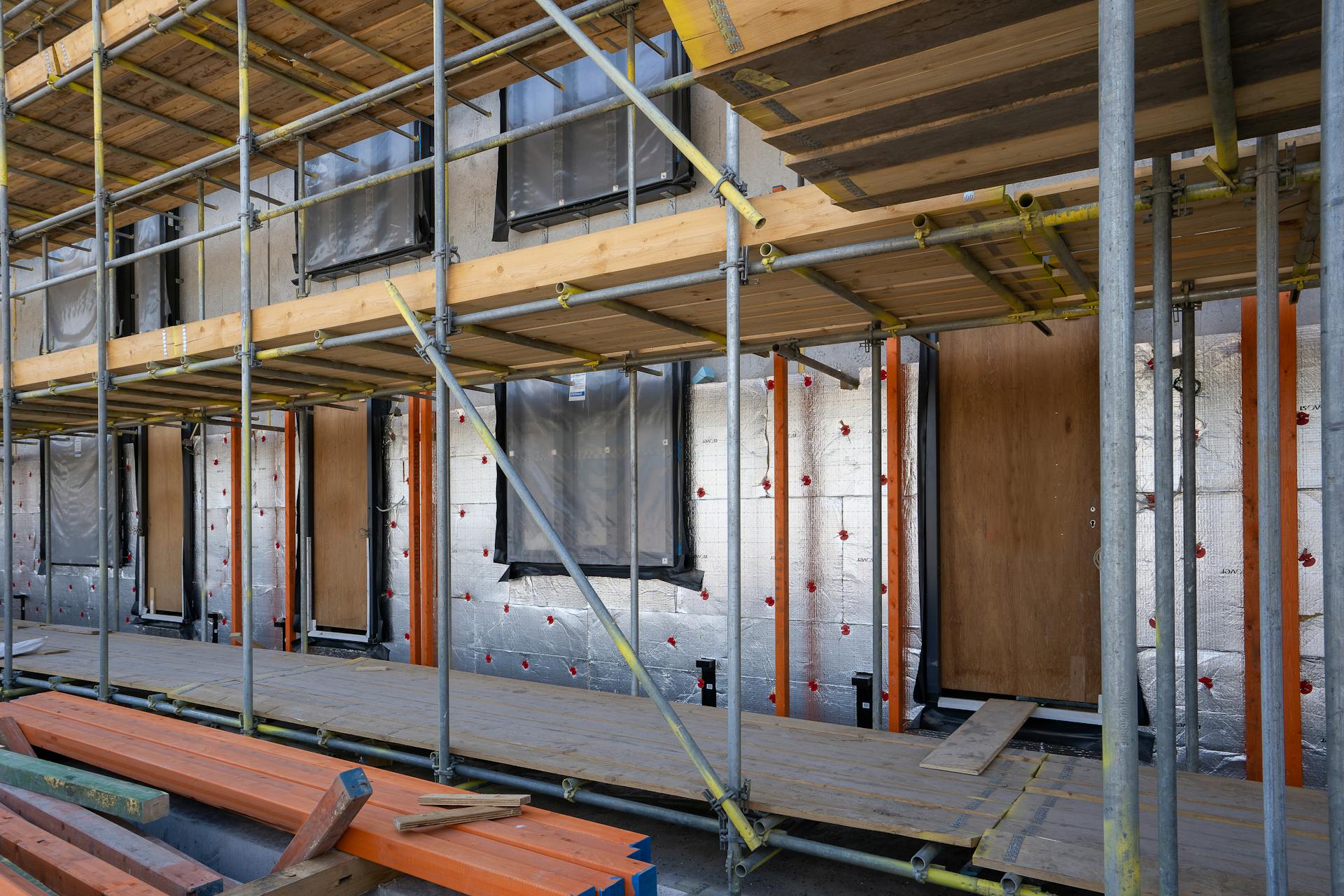
Rigid PU foam sheets are made from a combination of polyol and isocyanate, which are mixed together to form a rigid foam material. This unique composition gives rigid PU foam sheets their excellent insulation properties.
Rigid PU foam sheets have a high R-value, typically ranging from R-5 to R-7 per inch, making them an effective material for reducing heat transfer and energy loss.
One of the key benefits of rigid PU foam sheets is their ability to provide excellent thermal insulation, which can help reduce energy consumption and lower utility bills.
They are also lightweight, easy to cut, and can be easily shaped to fit specific applications, making them a versatile material for various industries.
Additional reading: Pu Foam Machine
Introduction to Rigid PU Foam Sheets
Rigid PU foam sheets are a popular choice for architectural and design model making due to their favourable material properties and ease of machinability.
These sheets can be machined easily, making them ideal for creating complex designs and models. However, it's essential to note that unpainted PUR materials should not be exposed to intense sunlight for long periods, as UV radiation can cause colour changes and decompose the material.
The density of the foam is indicated by a number behind the rigid foam, with smaller numbers representing softer materials. This is crucial to consider when selecting the right sheet for your project.
To ensure the longevity of your model, it's vital to rule out greater temperature fluctuations during transport and storage, as this can cause cracks in the material. This means taking steps to maintain a stable environment, such as avoiding extreme temperatures.
When bonding two blocks together, it's recommended to use two-component adhesives based on epoxy or polyurethane resin. These adhesives are suitable for clean, dry, dust- and grease-free surfaces, and can be cured to a harder state than the board material.
Here's a quick reference guide to help you evaluate the need for rigid PU foam sheets:
- Evaluate the area of application: Determine if the foam is needed for a wall, roof, or floor.
- Consider the R-value: Higher R-value products offer better thermal resistance and are more effective insulators.
- Assess additional features: Products with added functionalities like air barrier properties or attached ply may offer added benefits depending on the project's needs.
Properties and Performance
Rigid PU foam sheets are incredibly versatile and offer a range of impressive properties and performance characteristics.
Density varies greatly, from 35 to 300 Kg/m3, making it suitable for a wide range of applications.
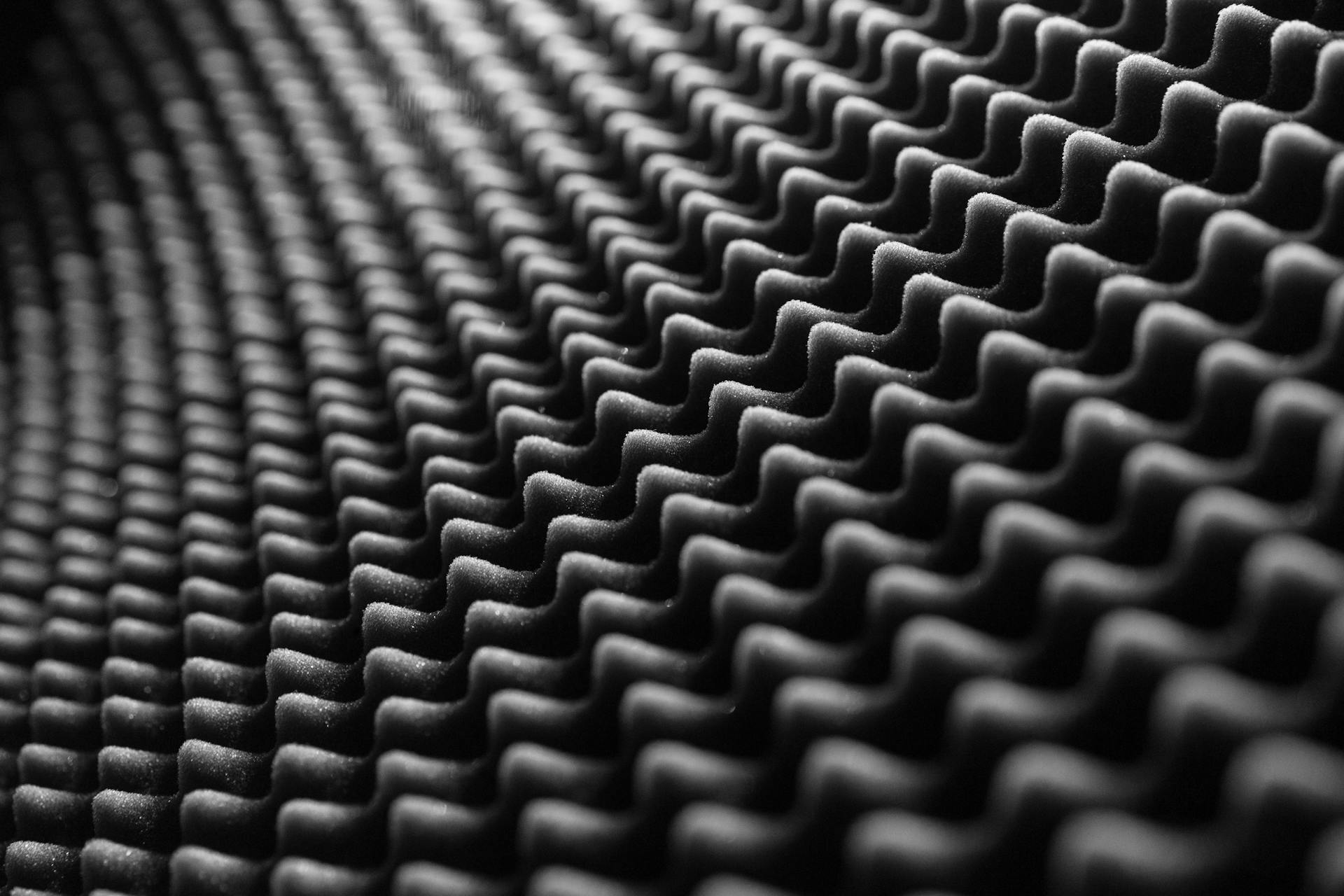
Their compression strength is at least 0.15 Mpa, providing a decent level of resistance to pressure.
Rigid PU foam sheets have a closed cell rate of at least 97%, which contributes to their excellent thermal insulation properties.
Thermal conductivity is relatively low, ranging from 0.017 to 0.022 W/m·K, making them a great choice for energy-efficient applications.
Water absorption is minimal, at less than 0.2%, ensuring that the material remains durable and resistant to moisture.
Operating temperature is limited to 100°C, so it's essential to consider this when selecting a rigid PU foam sheet for a particular application.
Here are some key properties of rigid PU foam sheets at a glance:
Applications and Uses
Rigid PU foam sheets are incredibly versatile and can be used in a variety of applications.
They are widely used in the thermal insulation layer of boxes such as cold storage, refrigerated trucks, RVs, storage tanks, pipes, building walls, and more. Generally, polyurethane rigid foam with lower density is mainly used as thermal insulation material.
Rigid PU foam sheets can also be used to create durable, reusable tools, prototypes, models, and patterns with CNC machines. This is especially useful for reducing residual particles and making cleanup easy.
They have excellent dimensional stability and can maintain tolerances even when exposed to extremes of temperature and humidity. This makes them ideal for applications where precision is crucial.
Some of the specific uses of rigid PU foam sheets include:
- General Thermal Insulation and Refrigeration
- Marine Buoyancy & Void Filling
- Fibreglass Void Forming
- Tooling
These applications are just a few examples of the many uses of rigid PU foam sheets. Their unique properties make them an excellent choice for a wide range of industries and projects.
Processing and Selection
Rigid PU foam sheets are processed using a unique method that involves combining polyol and isocyanate in a specific ratio to create a chemical reaction that produces a rigid foam.
This process is typically done in a controlled environment to ensure the reaction proceeds smoothly and efficiently, resulting in a high-quality foam sheet.
The selection of rigid PU foam sheets depends on the intended application, with different types of foam offering varying levels of density, compressive strength, and thermal insulation.
Broaden your view: Pu Foam Spray Machine
Processing PUR Foam
Before you start processing PUR foam, it's essential to temper the material to room temperature.
You can machine PUR panels and rigid foams with high-quality wood and metalworking tools, such as sawing, drilling, turning, and milling.
In fact, hand tools can also be used for lighter panels up to a density of 200 kg/m³, and surprisingly, they work quite well.
However, thermal cutting is not possible because polyurethane is a duroplast.
To avoid heating up the material and causing distortion, use carbide-tipped saw blades and work at speeds between 3000 and 6000 rpm.
For sawing, blunt saw blades only lead to trouble, so make sure to use the right ones.
The surfaces of all PUR hard foam and model plates can be machined by hand with conventional abrasives, but be prepared to sand and smooth them multiple times to get a lacquerable surface.
For lighter types, you can use higher removal rates, but be gentle with the heavier ones.
Choosing the Right Product
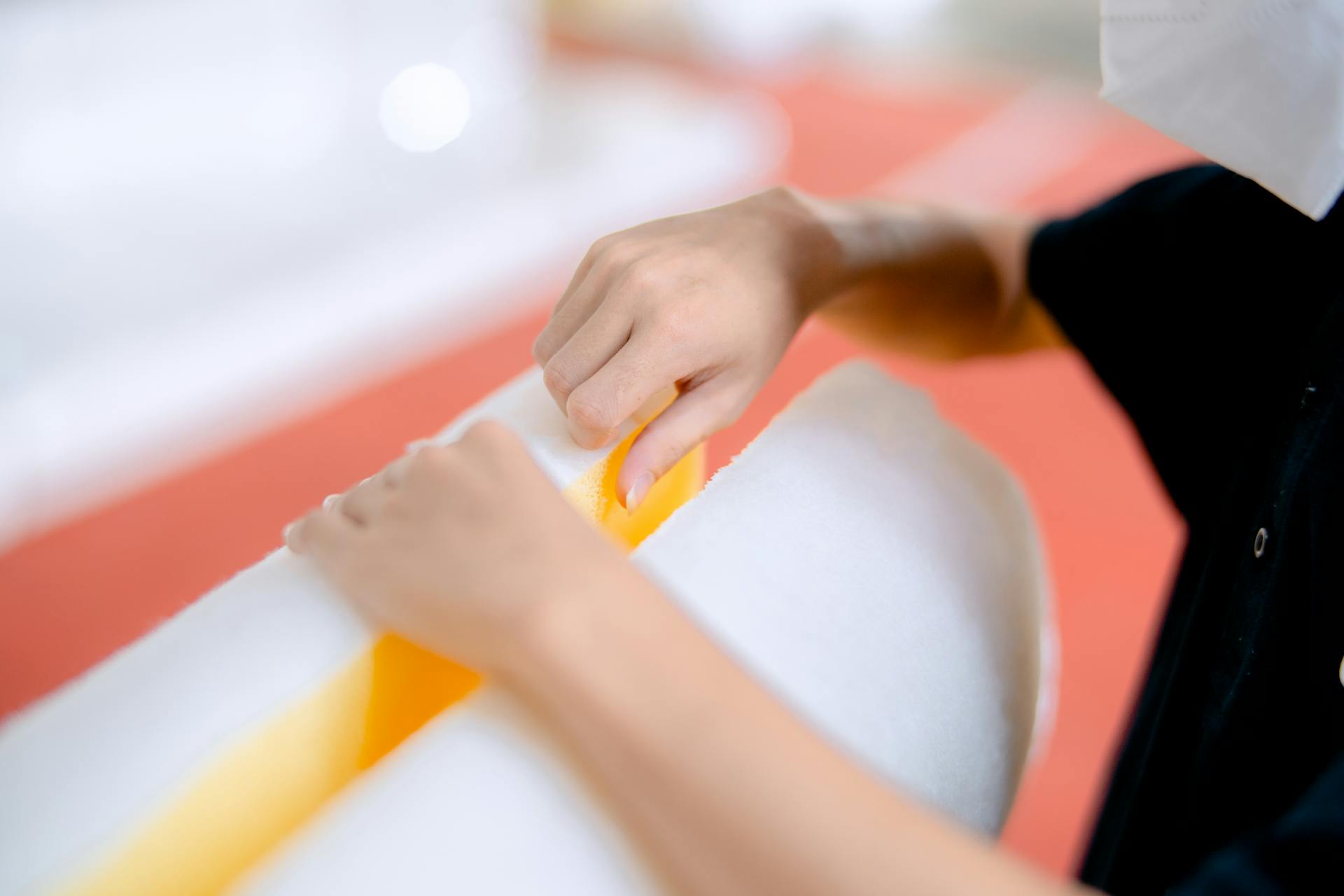
Choosing the Right Product is crucial when it comes to selecting the perfect polyurethane foam sheet for your project. This decision depends on several key factors.
First, evaluate the need for your insulation requirements, determining whether it's for a wall, roof, or floor. This will help you decide which type of foam is best suited for the job.
R-value is another important consideration, with higher R-value products offering better thermal resistance and being more effective insulators. For example, Rigitech Polyurethane Sheet Foam has extremely low thermal conductivity values, making it an optimal choice for applications requiring high performance.
Products with added functionalities, such as air barrier properties or attached ply, can offer added benefits depending on the project's needs. Tricast foam, for instance, is highly versatile and can be used as a core material, shaping media, insulation, or even as a structural part of a composite.
The density of the foam is also a crucial factor to consider, with densities ranging from 32kg/m3 to 96kg/m3 in the Tricast range. Each material density has a range of physical properties, so it's essential to choose the right one for your application.
Here's a brief overview of the Tricast range:
Standard sheet sizes for all materials are 2.44M x 1.22M x thickness to order, with maximum and minimum thickness varying by product density.
Sources
- https://www.modulor.de/en/plates/rigid-foam-sheets/polyurethane-rigid-foam-sheets/
- https://topolocfrt.com/pu-foam/
- https://rigitech.com.au/products/block-sheet-foams
- https://grpukltd.com/product/sheet-foam-1220-x-1220-25mm-tricast-2-32kg-m3-density/
- https://insulation4us.com/collections/polyurethane-foam
Featured Images: pexels.com