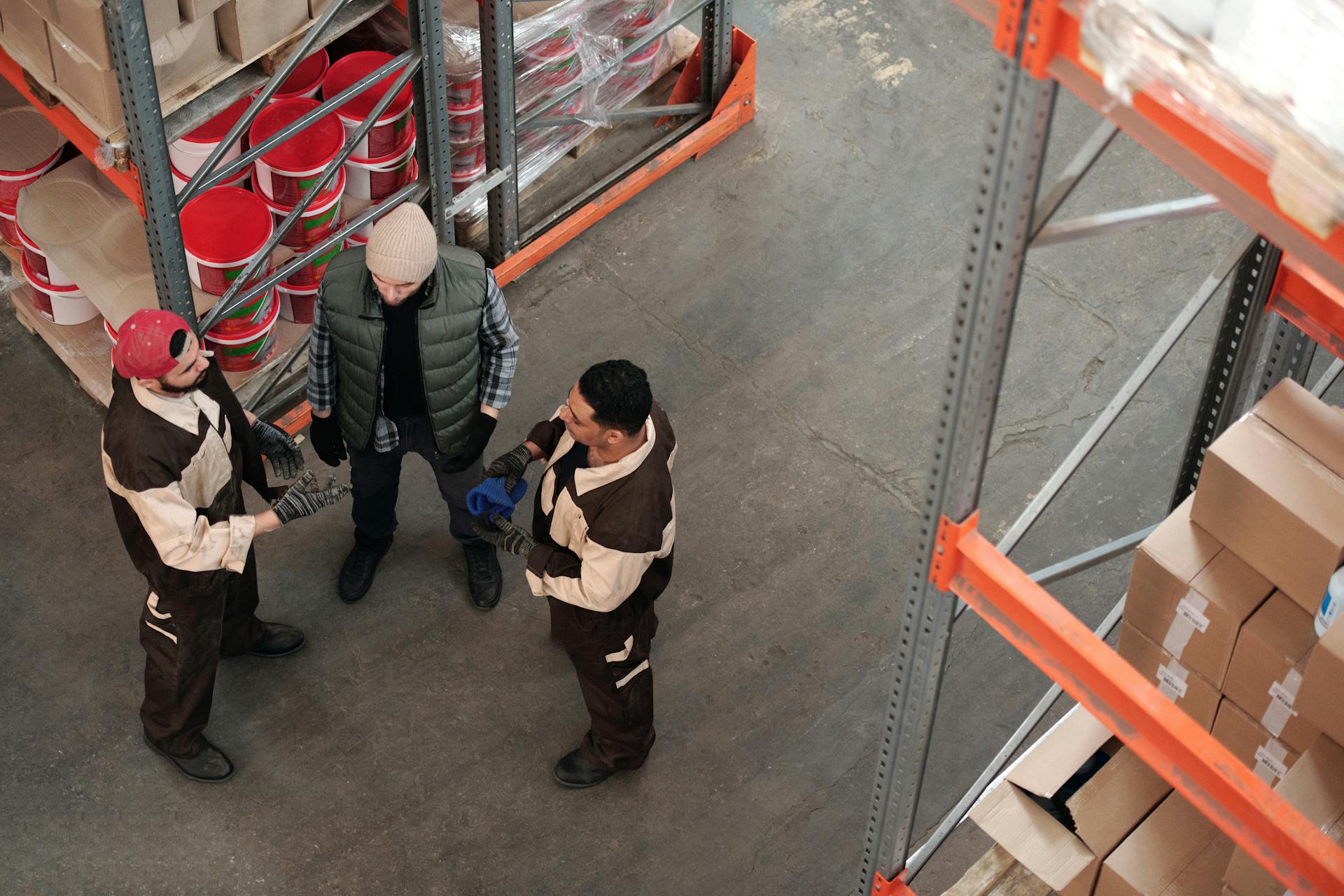
On time cross docking is a game-changer for businesses looking to optimize their supply chain operations. By implementing this strategy, companies can reduce transit times, decrease inventory costs, and improve customer satisfaction.
In a typical cross docking operation, goods are received and then immediately reloaded onto outbound trucks or trains, eliminating the need for intermediate storage. This can result in significant time and cost savings.
For example, a study found that cross docking can reduce transit times by up to 50% compared to traditional warehouse-based distribution methods. This can be a huge advantage for businesses operating in fast-paced industries.
By streamlining their supply chain with on time cross docking, companies can gain a competitive edge in the market and improve their bottom line.
Consider reading: Cross Border Moving Companies
What is Cross-Docking?
Cross-docking is the process of directly transferring goods from inbound to outbound transport, minimizing the need for storage and handling costs. This process typically takes place within 24 hours.
Ideal shipments are already palletized or in smaller packages, making them easy to transfer and reducing handling time. This efficiency is especially important for perishable goods like food, where speed preserves freshness.
Cross-docking is often used in industries such as FMCG, where quick turnover and minimal storage time are crucial for maintaining product quality. Retailers, e-commerce companies, and manufacturers also use cross-docking to optimize inventory and speed up deliveries.
Benefits and Advantages
On-time cross docking offers numerous benefits, including reduced costs by lowering warehouse storage costs, labor costs, and other expenses associated with inventory storage.
It can speed up package handling by bypassing pick and pack fulfillment during the shipping process, and improve shipping times by removing the need for warehouse storage, allowing products to be unloaded, repacked, and shipped on the same day.
By optimizing your supply chain and simplifying inventory management, you can reduce the number of touchpoints your products experience during shipping, which can lead to reduced costs, increased efficiency, and improved product quality.
Intriguing read: Storage Unit with Loading Dock
Here are some of the key advantages of on-time cross docking:
Reducing cross docking times offers several benefits, including faster order fulfillment, lower handling costs, improved inventory management, and enhanced customer satisfaction.
By meeting delivery timelines and providing fresher products, businesses can lead to higher customer satisfaction and loyalty.
In scenarios where demand is stable, high-volume products are moving quickly, perishable goods need to reach their destination quickly, or promotional items need to be delivered promptly, cross docking is particularly effective.
By understanding when and how to use cross docking, businesses can optimize their supply chains, reduce costs, and improve delivery times, ultimately enhancing customer satisfaction.
Types and Strategies
Companies can use traditional warehousing in combination with cross-docking operations to move outbound shipments quickly. This approach can be particularly effective in fulfillment warehouses and distribution centers.
A dedicated cross-docking facility is laid out to efficiently move inbound pallets directly from the receiving dock to outbound trucks. This layout is designed to minimize handling and storage time.
Walmart uses the lean supply chain approach, which involves transferring goods immediately from inbound to outbound shipments with minimal handling. This strategy minimizes storage time, reduces handling costs, and speeds up delivery.
Check this out: Inbound Cross Dock
Types of
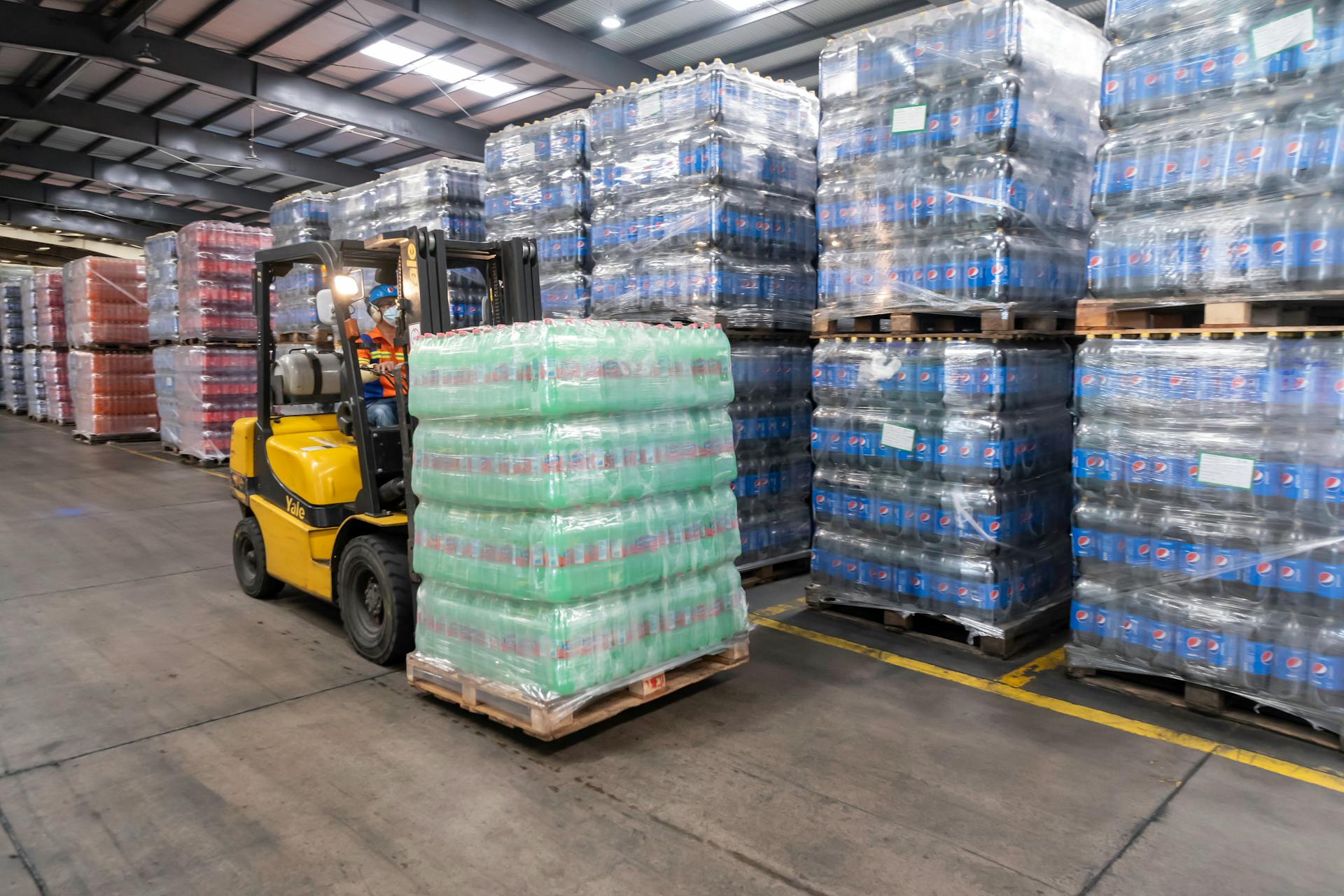
Companies can utilize cross-docking operations effectively in combination with other inventory management and storage strategies in traditional warehousing.
Cross-docking facilities are laid out to efficiently move inbound pallets directly from the receiving dock to outbound trucks.
A dedicated cross-docking facility can be used as a distribution method, specifically pre-distribution or post-distribution.
Strategies
Cross-docking strategies can be employed to maximize the benefits of this efficient method.
Different strategies can be employed to maximize the benefits of cross-docking. One key method is the lean supply chain approach. Walmart uses this method extensively.
In the lean supply chain approach, goods are transferred immediately from inbound to outbound shipments with minimal handling. This minimizes storage time, reduces handling costs, and speeds up delivery.
Expand your knowledge: Just in Time and Lean Operations
Typical Times
Cross-docking times can vary widely due to numerous factors, making it challenging to provide a one-size-fits-all answer.
In some cases, a cross-docking operation may take just a few hours, particularly for simple, well-planned shipments of non-perishable goods.
More complex operations or those involving high volumes of products might extend to several hours or even a full day.
Many businesses aim to continually improve their cross-docking processes to reduce processing times, which often results in shorter cross-docking durations.
Challenges
Cross-docking can be a complex process, and it's essential to be aware of the challenges that come with it. Demands on warehousing for increased docking space and layout changes to create clear cross-dock pathways can be a significant burden.
One of the main challenges of cross-docking is the need for precise timing and coordination among various stakeholders, which can lead to high complexity. This is especially true for items with quick turnover, as cross-docking works best for these products.
Cross-docking requires specialized facilities designed for rapid product flow, which can involve significant upfront costs. These costs can be a barrier for some companies, especially those with limited budgets.
The risk of disruptions due to low inventory and reliance on transportation is higher in cross-docking operations. This is because cross-docking relies on a just-in-time approach, which can leave companies vulnerable to delays or cancellations.
Here are some of the key challenges of cross-docking compared to traditional warehousing:
Implementation and Optimization
To achieve on-time cross docking, it's essential to implement a well-designed plan for receiving, sorting, and shipping. Effective planning and scheduling can optimize cross-docking operations.
Facilities that have a well-designed plan in place can minimize delays. This plan should include coordination with suppliers and carriers to ensure timely arrivals.
At Transload Services USA, prompt processing of freight inbound and outbound is a key aspect of their cross docking optimization services. This ensures that products can arrive and leave quickly, reducing storage time in the warehouse.
Businesses that use cross docking need to be dedicated to shipping at a fast pace to keep everything moving to fulfill orders promptly. This means that time is of the essence in cross docking operations.
Here are some key services that make Transload Services USA a premier option for retailers seeking to outsource their cross docking operations:
- Prompt processing of your freight inbound and outbound
- Quicker delivery time to customers
- Less storage time in the warehouse
- Consolidation of inventory
- Cost savings
By partnering with a team that knows the industry, businesses can elevate their supply chain efficiency and reduce costs. At Transload Services USA, they pride themselves on being industry leaders in cross docking optimization.
Facility and Operations
To achieve on-time cross docking, it's essential to have a well-designed facility. A facility with efficient flow patterns and ample space for sorting and loading can significantly expedite the process.
Regular reviews of operations are also crucial. This can help identify areas of improvement and ensure that operations stay streamlined and efficient. Key performance metrics to review include processing time, error rates, and shipment delays.
To further optimize operations, companies can gather feedback from various groups, such as employees, drivers, suppliers, and customers. This can provide valuable insights into what parts of the cross docking procedures need to be improved.
Improved Product Quality
Cross-docking is a game-changer for businesses that want to maintain the quality of their products. Fewer handling stages mean less chance for products to get damaged.
Perishable goods like food and beverages benefit greatly from cross-docking, which reduces the likelihood of spoilage. This is because these items are not stored for long periods, ensuring they reach customers in optimal condition.
Here are the benefits of cross-docking for product quality:
- Minimizes damage through fewer handling stages.
- Reduces the risk of spoilage, especially for perishable goods.
By implementing cross-docking, businesses can ensure their products reach customers in the best possible condition.
Training & Workforce
Training & Workforce is crucial for a successful cross docking operation. Ensuring employees are knowledgeable and working in harmony can significantly boost efficiency and accuracy.
Providing skill development is essential for employees to handle goods swiftly and correctly. This includes training on safety protocols to prevent injury from handling heavy and dangerous goods.
Effective workforce management means having the right number of employees during peak times and avoiding overstaffing during lulls. This can be achieved through efficient shift scheduling.
Regular team building activities foster teamwork, ensuring staff communicate well and collaborate effectively to move shipments smoothly. A well-trained and effectively managed workforce is key to a successful cross docking operation.
Here are some ways retailers can help their employees perform this operation:
- Skill development
- Safety protocols
- Efficient shift scheduling
- Team building activities
Facility Design and Layout
Facility design and layout can make a huge difference in how efficiently your operations run. A well-designed facility can help streamline processes and reduce delays.
Facilities with efficient flow patterns can expedite the processing time, making it easier to get goods in and out.
Crowded or poorly organized facilities, on the other hand, may experience delays, which can impact your bottom line.
A facility designed with ample space for sorting and loading can help keep things moving smoothly.
Transportation
Transportation is a critical aspect of facility and operations, and it's essential to understand the factors that affect it.
The time it takes to move goods from one location to another can vary significantly, depending on the distance between the supplier or manufacturer and the cross-docking facility.
Products arriving from nearby suppliers or manufacturers will have a shorter transportation time, making it easier to manage inventory and meet customer demand.
Conversely, products arriving from distant locations will require more time in transit, which can impact the overall efficiency of the facility.
Product Specifics
Simple, uniform items that require minimal handling and sorting will move through the cross-docking process quickly.
However, cross-docking complex products like fragile glassware, which requires extra care in handling, can extend the process time.
Perishable goods require faster cross-docking to maintain their quality, often leading to quicker processing times.
Products with strict delivery windows, such as perishable goods, need to be prioritized to meet customer expectations.
Cross-docking electronic components, on the other hand, may be faster than cross-docking fragile glassware, highlighting the impact of product specifics on cross-docking time.
Ecommerce Fulfillment
Ecommerce fulfillment is a key area where cross-docking can shine. In an order fulfillment warehouse, cross-docking is often used opportunistically, as needed, to fill orders quickly.
By implementing cross-docking, businesses can reduce costs and improve efficiency, which is especially important in the fast-paced world of ecommerce. Fewer handling stages mean less chance for products to get damaged, ensuring that items reach customers in optimal condition.
Consolidation and deconsolidation strategies allow businesses to optimize the size and number of shipments, making the entire process more efficient. This can be especially beneficial for perishable goods like food and beverages, which benefit greatly from cross-docking.
Here are some key benefits of using cross-docking in ecommerce fulfillment:
- Reduced Costs: Cuts down on storage and handling expenses.
- Improved Efficiency: Speeds up delivery times and streamlines operations.
- Improved Product Quality: Minimizes damage and spoilage through fewer handling stages.
Regular review of operations is also crucial in ecommerce fulfillment, as it allows businesses to continually adapt and improve their cross-docking processes. By reviewing metrics such as processing time, error rates, and shipment delays, businesses can identify areas for improvement and make data-driven decisions.
Manufacturing
In manufacturing, cross-docking makes material handling more efficient by sorting materials and components into sets before sending them to the factory.
This process, also known as a post-distribution consolidation arrangement, allows distributors to deliver exactly what each factory needs to complete the manufacturing process.
Cross-docking in manufacturing works similarly to retail distribution, streamlining the flow of materials and reducing waste.
By consolidating materials, factories receive only what they need, minimizing excess inventory and saving space.
A different take: Just in Time Manufacturing
Retail Distribution
In retail distribution centers, cross-docking is a common practice where trucks loaded with goods from manufacturers come in and trucks carrying assortments of goods for retail locations go out.
Products are re-sorted for outbound transportation shortly after they arrive in the warehouse, making it a good fit for JIT inventory management.
Cross-docking facilities reorganize the products, consolidating inventory from multiple manufacturers into mixed deliveries for furniture showrooms.
Three trucks arriving at a retail distribution center might bring in sofas, tables, and lamps from different manufacturers, which are then reorganized into mixed deliveries for furniture showrooms.
This process is efficient and helps reduce storage needs, allowing for faster delivery of products to customers.
Recommended read: Best Semi Trucks of All Time
Real-World Applications
Walmart minimizes storage costs by transferring goods directly from inbound to outbound trucks, reducing costs and improving efficiency.
Amazon uses cross-docking in its fulfillment centers to speed up order processing, ensuring fast deliveries and higher customer satisfaction.
Traditional warehousing is preferred by most furniture retailers and seasonal brands, who need large storage spaces, especially during peak seasons.
This approach helps them manage inventory efficiently and meet changing demand without the immediate pressures of cross-docking.
Cross-docking is particularly beneficial for businesses that need to maintain competitive pricing, like Walmart, which uses it to stay ahead.
Here's an interesting read: Cross Docking in Walmart
Frequently Asked Questions
How long does cross-docking take?
Cross-docking typically takes a few hours for simple shipments, but can extend to several hours or a full day for more complex operations or high-volume shipments. The duration depends on the complexity and volume of the products involved.
When to use cross-docking?
Use cross-docking when you need to quickly fulfill orders, reduce inventory costs, and meet customer demand for fast delivery. This efficient logistics strategy is ideal for businesses looking to streamline their supply chain and boost operational efficiency.
Sources
- https://redstagfulfillment.com/what-is-cross-docking/
- https://transloadservicesusa.com/blog/cross-docking-optimization/
- https://mymilehighdelivery.com/how-long-does-cross-docking-take/
- https://flexlogistics.com/news/cross-docking-explained-streamlining-your-supply-chain
- https://fareye.com/what-is-cross-docking
Featured Images: pexels.com