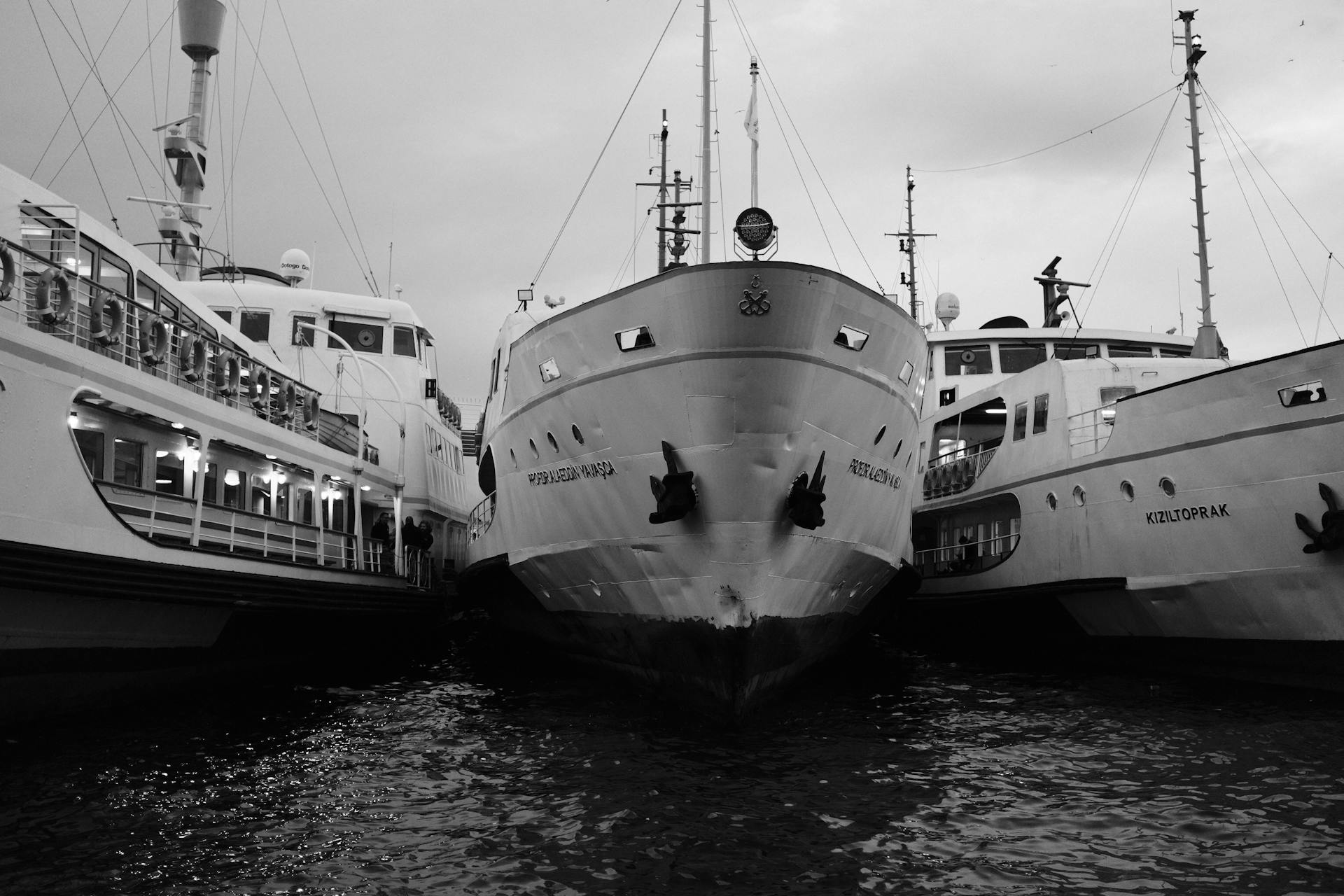
Inbound cross dock is a game-changer for supply chain efficiency. It allows companies to receive, process, and distribute products quickly and effectively, reducing inventory holding costs and improving customer satisfaction.
By implementing an inbound cross dock, businesses can consolidate shipments from multiple suppliers into a single, streamlined process. This reduces the need for multiple handling and storage steps.
Inbound cross dock can be especially beneficial for companies with high-volume, fast-moving products. By reducing transit times and increasing inventory turnover, businesses can free up capital and focus on growth.
This efficient process also enables companies to offer faster delivery times and improved service levels to their customers, giving them a competitive edge in the market.
What is Inbound Cross Dock
Inbound cross dock is a type of cross docking that involves receiving goods from suppliers and transferring them directly to outbound transportation, without storing them in a warehouse. This process is especially useful for high-volume products and perishable goods that must be shipped immediately.
The benefits of inbound cross dock are numerous. Retailers can enjoy increased efficiency and productivity, while suppliers can benefit from reduced time between receiving an order and shipping the product out, resulting in increased revenue and profit margins.
Inbound cross dock takes place in a distribution dock terminal where transport vehicles have dock doors on the sides and minimal storage space. This setup allows for a quick and efficient transfer of goods from one vehicle to another.
Here are the benefits of inbound cross dock for different stakeholders:
- Retailers benefit from increased efficiency, productivity, and lower inventory costs.
- Suppliers benefit from the reduced time between receiving an order and shipping the product out, resulting in increased revenue and profit margins.
- Consumers benefit because they receive products faster than they would have if they were shipped using traditional distribution methods.
Inbound cross dock is a cost-effective way to manage inventory and reduce transportation time. By eliminating unnecessary steps such as unloading and storing items in a warehouse facility, retailers can save on storage and handling costs.
Benefits of Inbound Cross Dock
Inbound cross dock allows for the efficient processing of large volumes of inventory, reducing the need for multiple storage facilities.
By consolidating shipments from multiple vendors into a single location, inbound cross dock streamlines the supply chain and minimizes costs associated with storage and handling.
Inbound cross dock facilities can process up to 80% of inventory within 24 hours, significantly reducing the time it takes to get products to market.
This increased speed and efficiency enables businesses to respond quickly to changes in demand and stay competitive in the market.
With the ability to process high volumes of inventory, inbound cross dock facilities can accommodate a wide range of product types and sizes, making them a versatile solution for companies with diverse product lines.
The streamlined process of inbound cross dock also reduces the risk of damage and loss associated with traditional storage and handling methods.
Broaden your view: Drayage Services Market
Streamlining Logistics
Streamlining Logistics is a crucial aspect of inbound cross dock. By creating a single shipment to the nearest Receive Center, sellers eliminate the need for multiple shipments, making the process much more efficient.
Sellers only need to make one shipment, which reduces logistical complexities and saves time. This streamlined approach also reduces the number of appointments required, as they're only necessary for the Receive Center.
Here are some benefits of this streamlined approach:
- Simplified logistics with a single shipment
- Reduced logistical complexities
- Less need for appointments
By consolidating shipments, businesses can also reduce the risk of damage and loss, as there are fewer transfers involved. This leads to lower storage requirements and reduced storage fees.
Best Practices and Considerations
To set up an effective inbound cross dock system, consider the increasing popularity of cross docking service, which has led to the development of best practices to follow.
Clear communication between the warehouse team and the transportation providers is crucial to ensure smooth operations. This can be achieved by implementing a system to track and manage shipments in real-time.
The warehouse system should be designed to accommodate the flow of goods, with a focus on minimizing delays and maximizing efficiency. This can be done by implementing a layout that allows for easy navigation and minimal congestion.
By following these best practices, you can ensure that your inbound cross dock system runs smoothly and efficiently, allowing you to meet your customers' needs and stay competitive in the market.
Docking Best Practices
To set up a warehouse system for cross docking, consider the best practices such as ensuring an even distribution of dock doors to accommodate all inbound shipments.
The number and placement of dock doors are critical design considerations that determine the efficiency of your cross docking operation.
Aim for an even distribution of dock doors to avoid bottlenecks and slow down your operation.
Too many small or far-apart dock doors can lead to inefficiencies, while too few doors can cause incoming trucks to back up and wait for their turn to unload.
The ideal number, size, and placement of dock doors depend on the size of your warehouse and the volume of shipments you receive.
Handling Complexity
Handling complexity in cross docking can be a significant challenge, as it involves more steps and coordination than traditional warehousing. This extra complexity can lead to a higher risk of error.
Cross docking requires communicating with other warehouses and coordinating their operations, which can complicate the process. Additional staff or new software may be needed to handle the extra work involved in cross docking operations.
The extra steps and coordination involved in cross docking can result in increased costs for a company.
See what others are reading: Loading Dock Stairs
Difference Between IXd and FBA
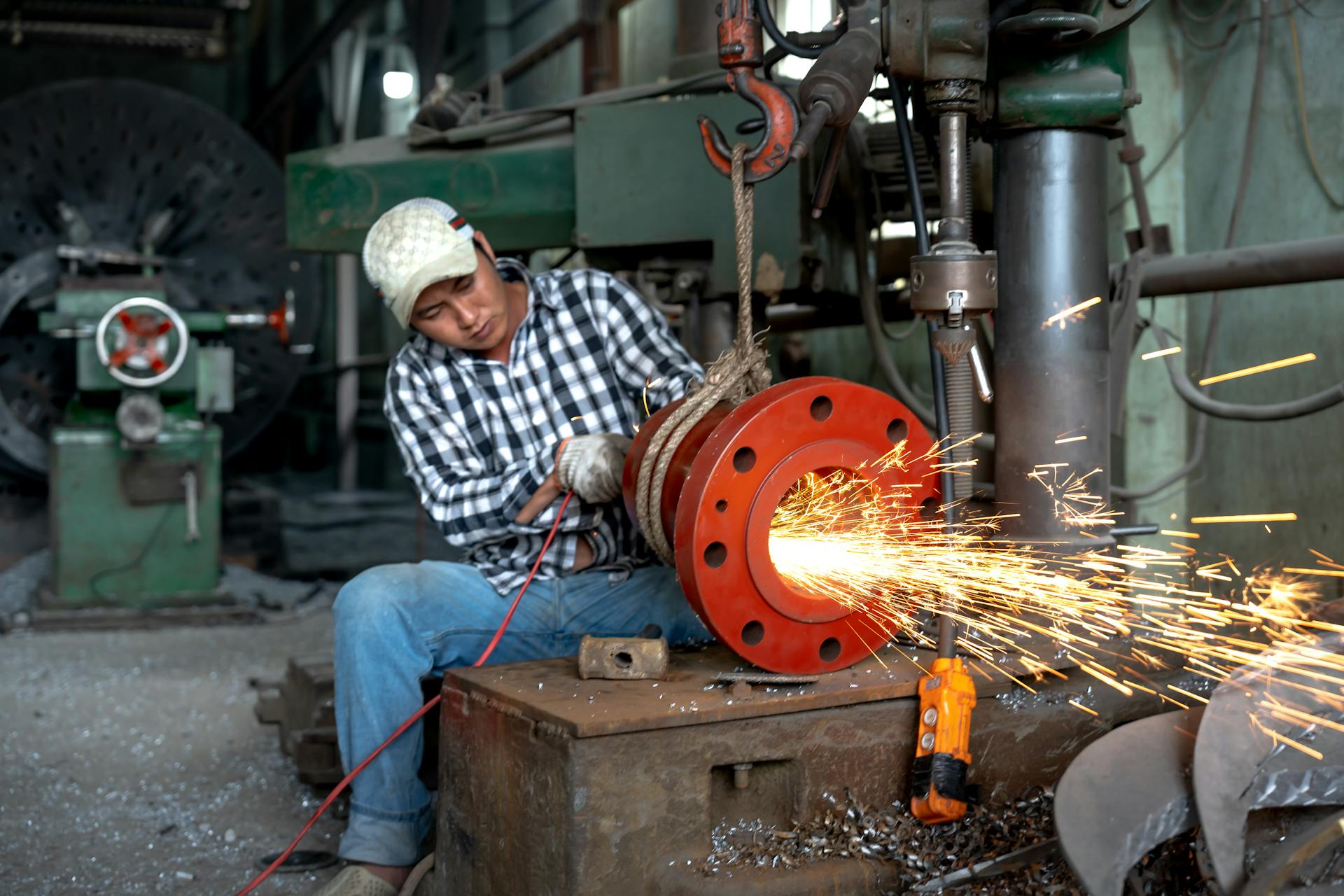
IXD and FBA are two different fulfillment options on Amazon.
The main difference between IXD and Standard FBA lies in the way inventory is handled. Inventory sent to a Receive Center under the IXD program is managed by Amazon, which ensures optimal placement across its network.
This improves delivery times and cost efficiency. Amazon's management also helps in redistributing inventory to ensure it's available to customers quickly.
With Standard FBA, you're responsible for sending your inventory directly to an Amazon fulfillment center. This can be more complicated and may not offer the same level of efficiency as the IXD program.
Industry and Operational Considerations
Industries that use cross-docking services include those that handle high volumes of material on a regular basis, such as companies that need to rapidly sort, store, and distribute these materials.
Cross-docking is particularly beneficial for industries with multiple steps involved before products reach their final destination, allowing companies to move product out the door as soon as possible after it arrives at their warehouses.
This process saves time and money by reducing the time products are exposed to the elements during transportation and minimizing the risk of product damage.
You might enjoy: What Is Cross Docking in Supply Chain
Docking History
Cross docking has a rich history that dates back to the 1930s in the U.S. trucking industry. Companies were looking for ways to improve their supply chain management systems and speed up delivery.
The implementation of cross docking continued to improve in the 1950s, particularly in the retail sector. This led to more efficient delivery systems.
Walmart, one of the world's largest retailers, introduced a cross docking system in the 1980s that gave them a significant competitive advantage. This innovation helped them stay ahead in the market.
Today, companies are still striving to improve the speed and efficiency of delivering goods to customers. They're also looking to keep costs as low as possible.
Related reading: Cross Docking Warehouse Systems
Industries Using Docking
Several industries benefit from cross docking due to their high volume of material and need for rapid sorting, storing, and distributing.
The logistics of these industries often involve multiple steps before products reach their final destination, making cross docking a necessary solution.
Companies in these industries use cross docking to move products out the door as soon as possible after they arrive at warehouses.
This helps them avoid waste or spoilage and ensures they can meet customer demand.
Cross docking saves time and money by reducing the time products are exposed to the elements during transportation.
It also reduces the risk of product damage that might occur if there were a problem with the transport vehicle.
For another approach, see: On Time Cross Docking
Supply Chain Vulnerability
Supply chains become much more vulnerable to disruption with less inventory and shorter lead times.
Traditional warehousing allows for longer lead times, giving companies time to plan for disruptions and set up contingency plans if needed.
With cross docking, everything happens quickly, leaving little time for contingency planning.
Less inventory and shorter lead times can lead to supply chain disruptions, which can have serious consequences for businesses.
Amazon Hiring Fayetteville
Amazon is now hiring for its new Inbound Cross-Dock facility in Fayetteville, with positions posted online each Friday evening after 7:00 p.m.
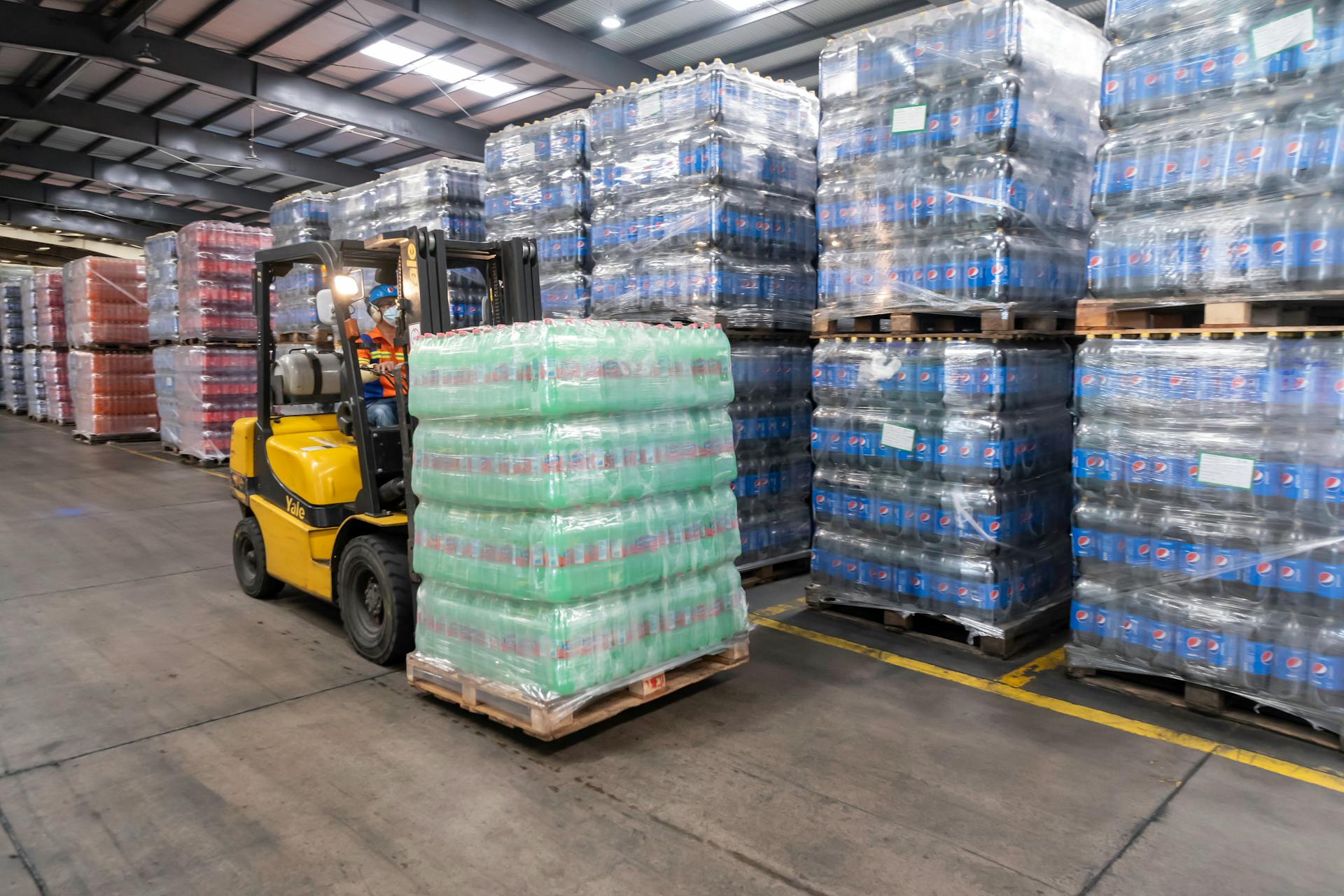
The facility, located in the Military Business Park, will employ over 1,000 workers in full and part-time positions at full operation, which will be a significant economic boost to the area.
Pay for these positions starts at $17.00 per hour, with benefits including medical, dental, and vision effective on the first day of employment.
Applications must be made online and will not be taken on site, but those without internet access can visit any of Cumberland County's eight library locations.
The project is a result of strong collaborative efforts from multiple public and private organizations, including the City of Fayetteville, Cumberland County, and Amazon itself.
This new facility will bring in millions of dollars in wages to the local economy, as well as property tax revenue to the City and County, making Amazon one of the largest private sector employers in Cumberland County.
Automation and Efficiency
Automation is a key feature of inbound cross docking, allowing for faster and more accurate processing of shipments. Inbound cross docking facilities can automate tasks such as scanning and tracking shipments, reducing labor costs and increasing efficiency.
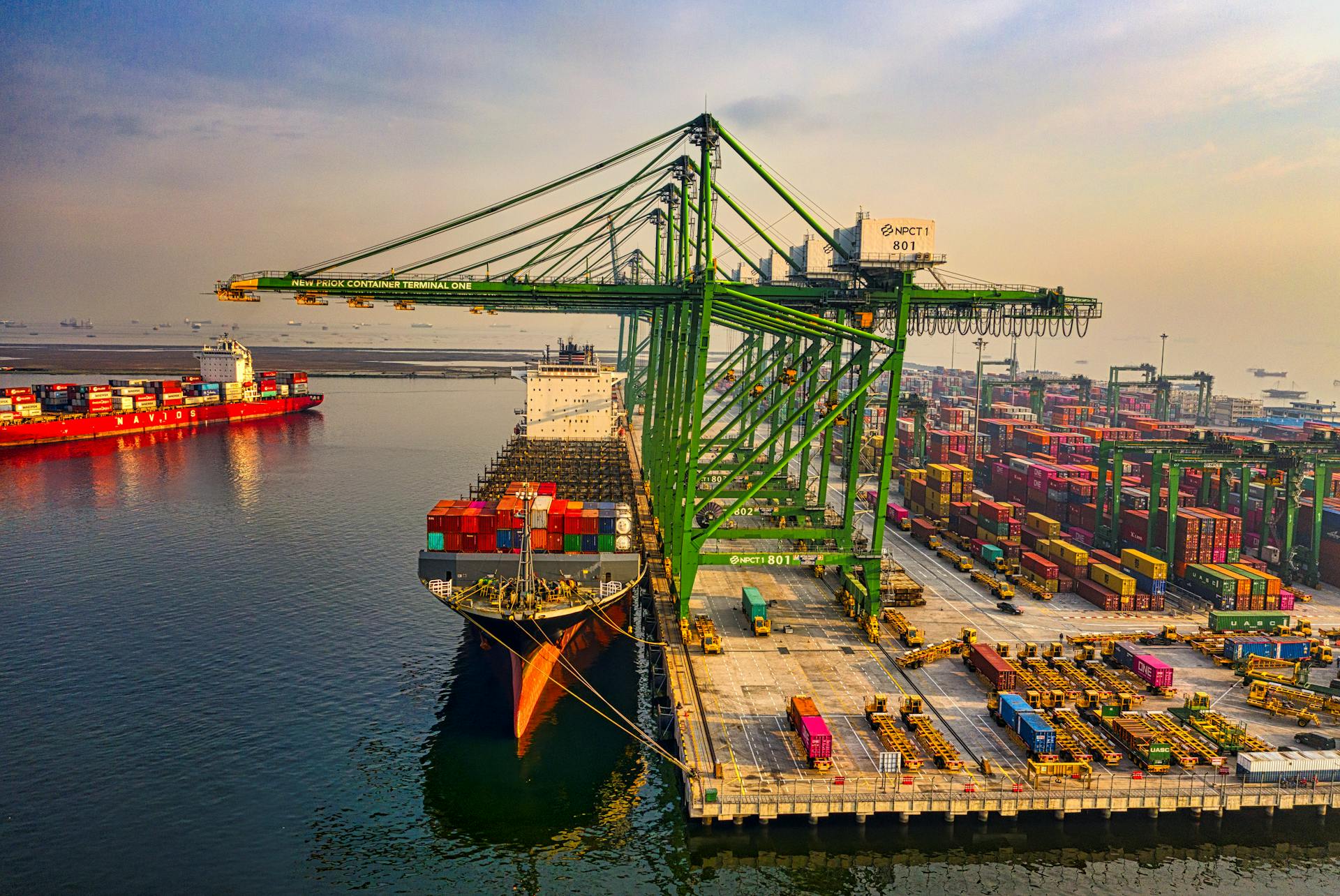
With automation, shipments can be processed in as little as 15 minutes, compared to the 2-3 days it can take for manual processing. This rapid processing time enables cross dockers to handle a higher volume of shipments.
Automated systems can also reduce errors and improve inventory management, as shipments are accurately tracked and updated in real-time. This results in improved customer satisfaction and reduced costs associated with lost or misplaced shipments.
Frequently Asked Questions
What is an inbound dock?
An inbound dock is the area where goods are received from suppliers and manufacturers, marking the beginning of their journey through the warehouse or distribution center. It's a critical checkpoint where items are documented and managed to ensure smooth logistics.
Sources
- https://docs.oracle.com/en/cloud/saas/warehouse-management/22a/owmim/implementationandconfiguration/topics/receiving_and_cross_dock.html
- https://www.inboundlogistics.com/articles/cross-docking/
- https://amancentral.com/amazons-inbound-cross-docking-ixd-program-streamlining-inventory-distribution-for-enhanced-efficiency/
- https://fcedc.com/amazon-now-hiring/
- https://www.inboundlogistics.com/articles/enhancing-cross-docking-efficiency/
Featured Images: pexels.com