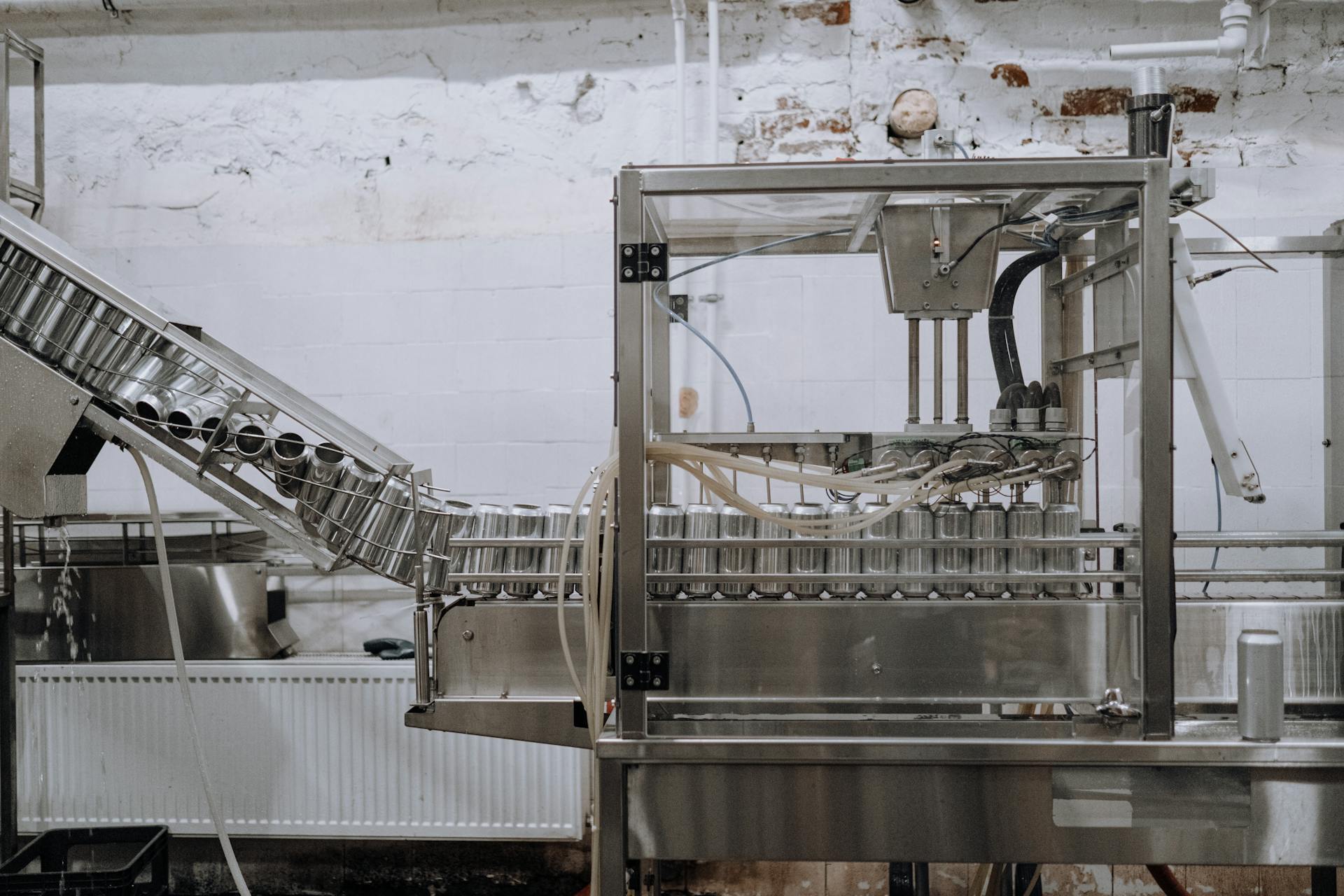
Just in Time manufacturing is a production strategy that aims to produce and deliver products just in time to meet customer demand. This approach eliminates the need for large inventories and reduces waste.
By adopting a Just in Time approach, businesses can significantly reduce their inventory levels, with some companies reporting a decrease of up to 80%. This is achieved by having suppliers deliver materials and components directly to the production line, reducing storage needs.
Just in Time manufacturing relies heavily on efficient supply chain management, which involves coordinating with suppliers to ensure timely delivery of materials. This requires strong relationships with suppliers and a high level of communication.
The benefits of Just in Time manufacturing are numerous, including reduced costs, improved quality, and increased flexibility. Businesses can respond quickly to changes in demand and production can be adjusted accordingly.
What Is Just-In-Time Manufacturing?
Just-in-Time manufacturing, also known as JIT, is a production strategy that produces goods based on customer orders. This approach minimizes inventory and increases efficiency within a company's supply chain.
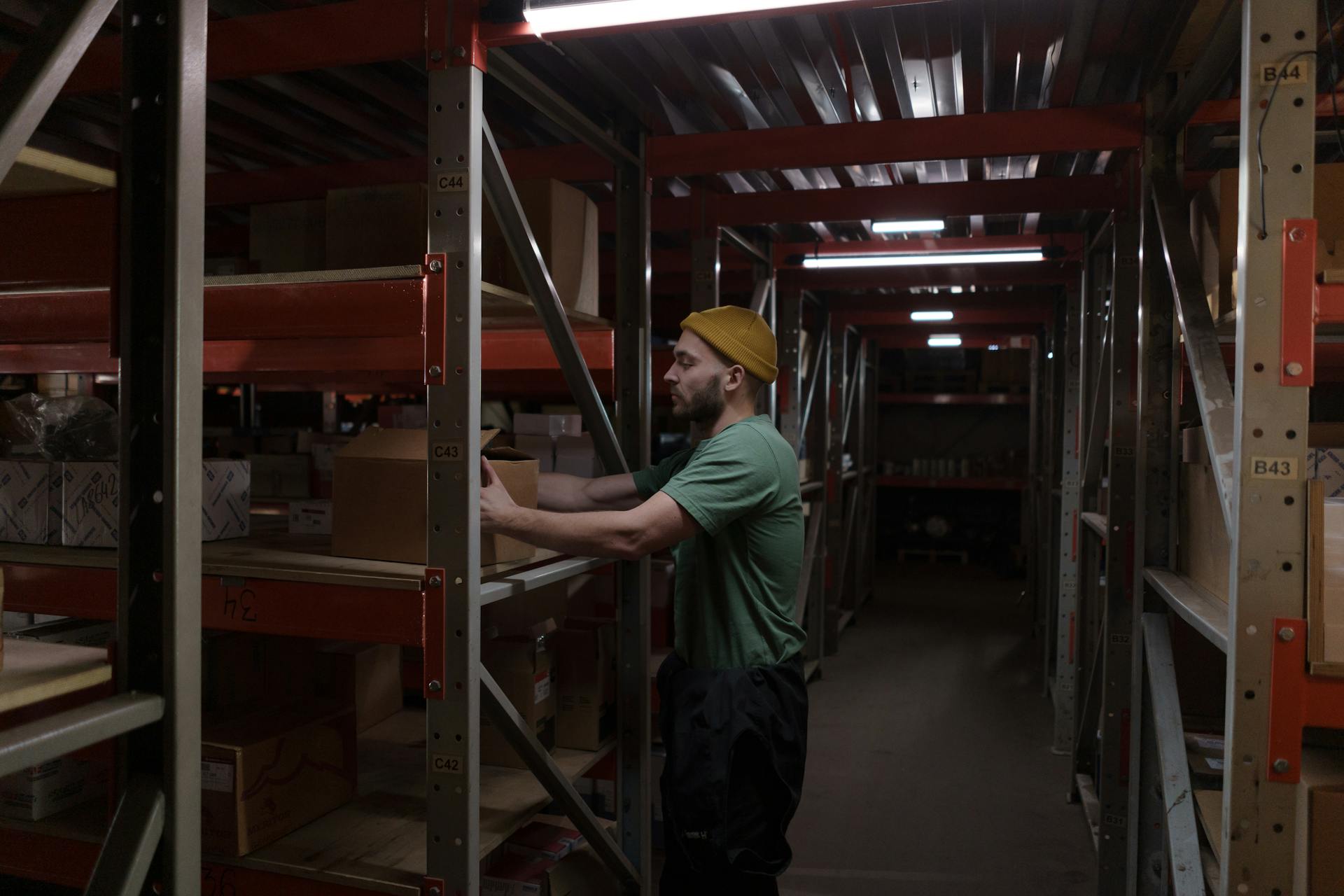
By closely coordinating the flow of materials, information, and equipment, JIT manufacturing ensures that customer orders are produced and delivered within specific time windows. This strategy is used to minimize inventory and increase efficiency.
JIT manufacturing borrows heavily from the "lean manufacturing" philosophy, which focuses on reducing waste and maximizing efficiency in all production areas. By implementing JIT manufacturing and lean principles, companies reduce production costs and improve competitiveness.
Companies that adopt JIT manufacturing can expect to see a reduction in production costs and an improvement in competitiveness. This is because JIT manufacturing eliminates waste and maximizes efficiency.
Explore further: Just in Time Lean Management
Benefits and Advantages
Just in time manufacturing offers several benefits and advantages that can improve a company's efficiency and bottom line.
With JIT, production runs are short, allowing manufacturers to quickly move from one product to another. This flexibility is a major advantage over traditional manufacturing methods.
Reduced storage costs are another benefit of JIT, as companies don't need to maintain large warehouses to store excess inventory. This can lead to significant cost savings.
See what others are reading: Protien Bar Manufacturing and Packaging Companies

Companies that implement JIT also experience less waste and no overproduction. This is because they only produce what's needed, when it's needed.
Here are some of the key benefits of JIT in a concise list:
- Reduced storage costs
- Less waste
- No overproduction
- Resource-efficient (both in material, people and capital)
- Better cash flow
- Shortened throughput time
By implementing JIT, companies can improve their resource efficiency and cash flow, leading to a more sustainable and profitable business model.
Advantages and Disadvantages
JIT inventory systems have several advantages over traditional models. Production runs are short, which means that manufacturers can quickly move from one product to another.
Companies that use JIT inventory systems can reduce costs by minimizing warehouse needs. This is because they only need to store the raw materials required for the products they're currently producing.
Reduced storage costs are a significant benefit of JIT inventory systems. This is because companies don't need to spend money on storing large quantities of inventory.
One of the disadvantages of JIT inventory systems is the potential for supply chain disruptions. If a raw-materials supplier has a breakdown and cannot deliver the goods promptly, it could stall the entire production line.
A different take: Best Home Time Trucking Companies
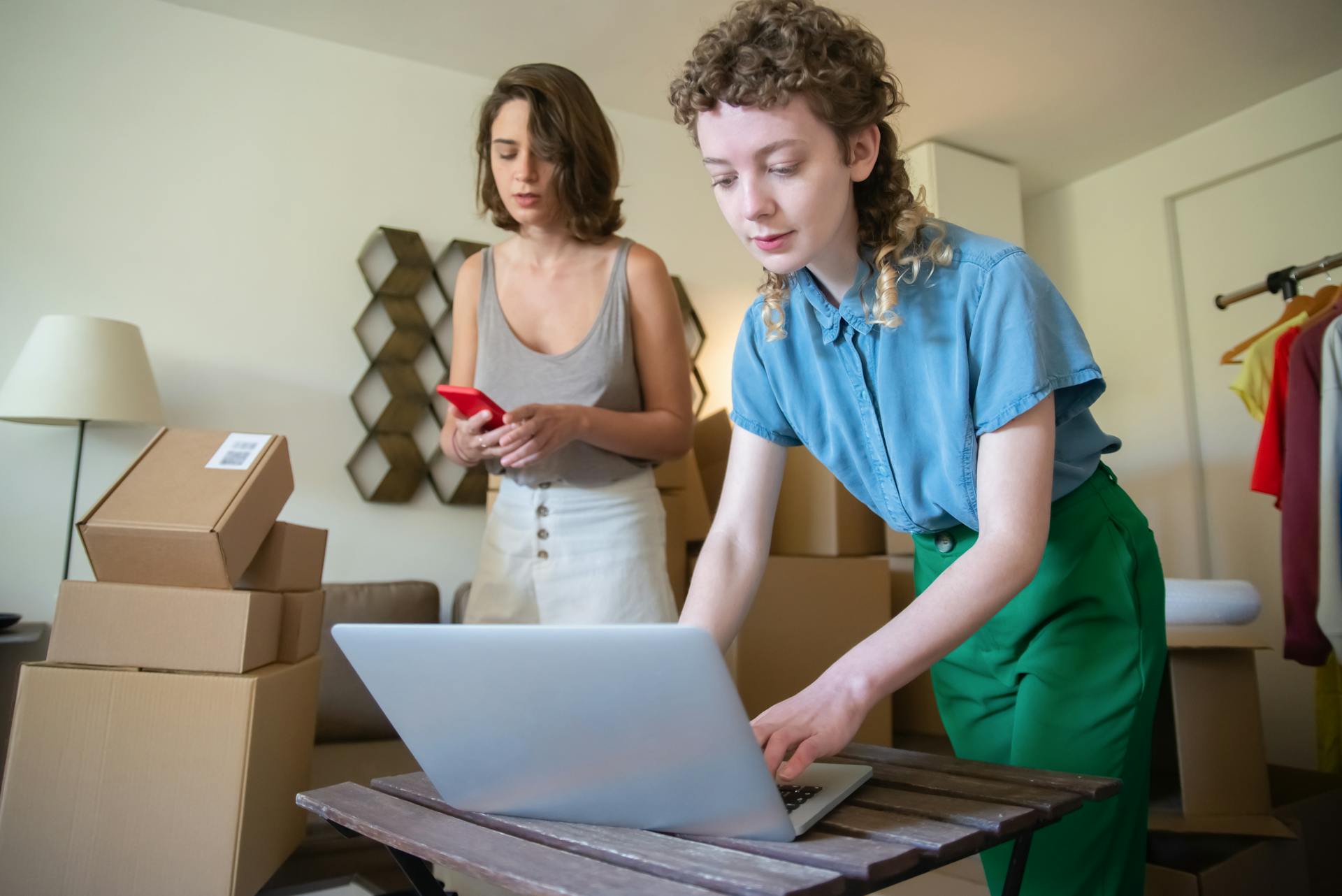
Here are some of the key advantages of JIT inventory systems:
- Reduced storage costs
- Less waste
- No overproduction
- Resource-efficient (both in material, people and capital)
- Better cash flow
- Shortened throughput time
These benefits can have a significant impact on a company's bottom line. By reducing waste and overproduction, companies can save money and improve their efficiency.
Companies Benefiting Most
Companies that operate with high volumes of orders and frequent inventory turnover can greatly benefit from JIT manufacturing. These companies can reduce the cost of storing and maintaining excess inventory while improving the overall efficiency of the production process.
Retailers are a great example of companies that benefit from JIT. They have a high volume of orders and need to respond quickly to changes in market trends.
Automotive and electronics manufacturers also benefit from JIT due to their high demand for products. They need to be able to respond quickly to changes in market trends and can't afford to have excess inventory taking up valuable space.
Companies like on-demand publishing and tech manufacturing can also benefit from JIT. They have unique production needs that require them to produce products quickly and in small batches.
Explore further: Just in Time Stock Control
Inventory Management
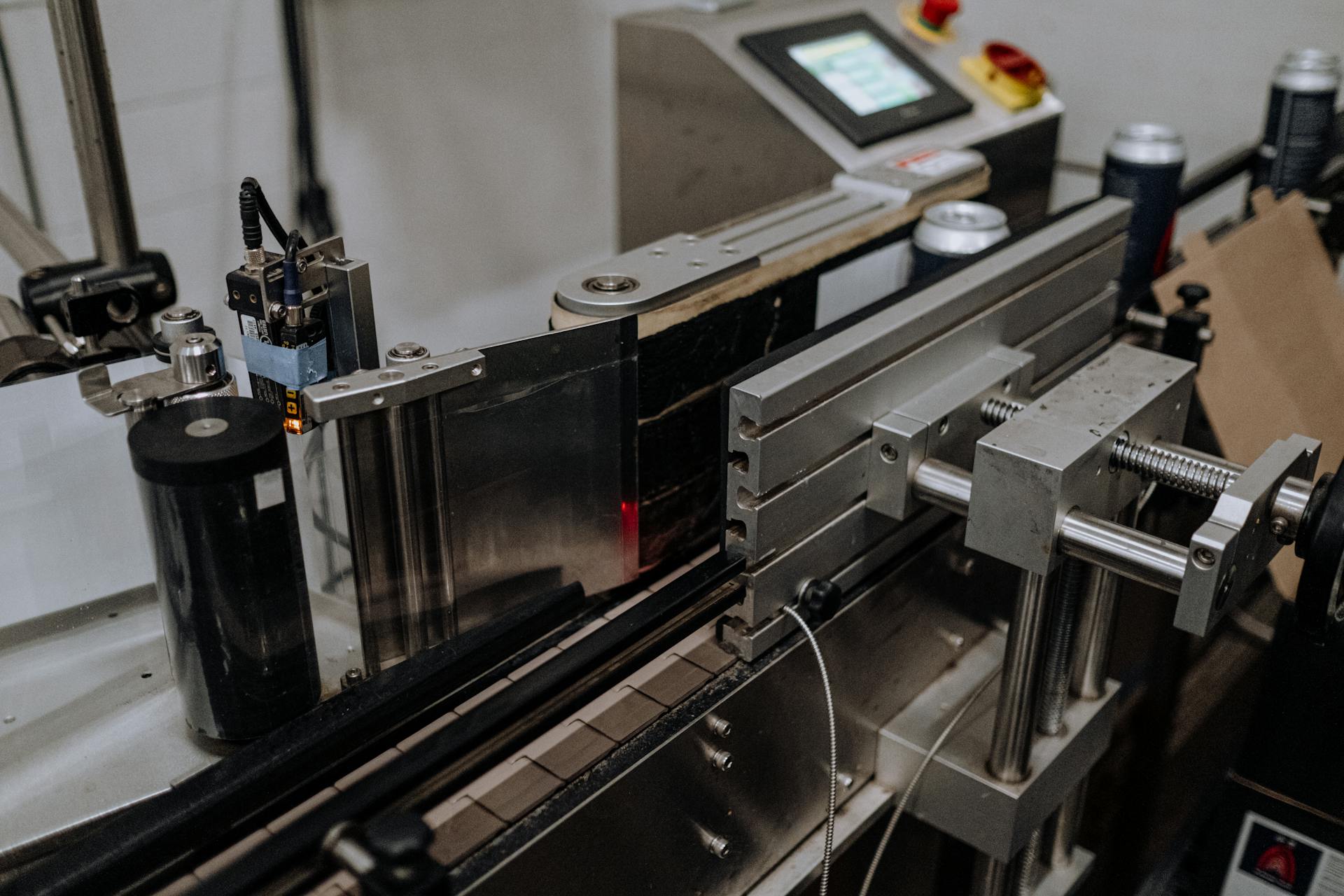
Inventory management is a crucial aspect of just-in-time manufacturing. It's all about minimizing inventory levels by only ordering products as needed for production or sale.
To achieve this, companies must closely coordinate their production schedule with the delivery schedule of suppliers and the projected buying patterns of customers. This is done by using techniques like kanban cards or signals to authorize and control the flow of inventory movement and replenishment.
Accurate demand forecasting and production scheduling are critical for JIT inventory control. Companies like Dell Computer use a just-in-time inventory system, where they wait until they receive an order for their computers and only order the components and parts needed for that specific order.
The goal of JIT inventory management is to have zero inventory at the end of the process. This is achieved by minimizing excess inventory and its associated costs, such as inventory holding costs and storage costs.
Check this out: Order Fulfillment Cycle Time
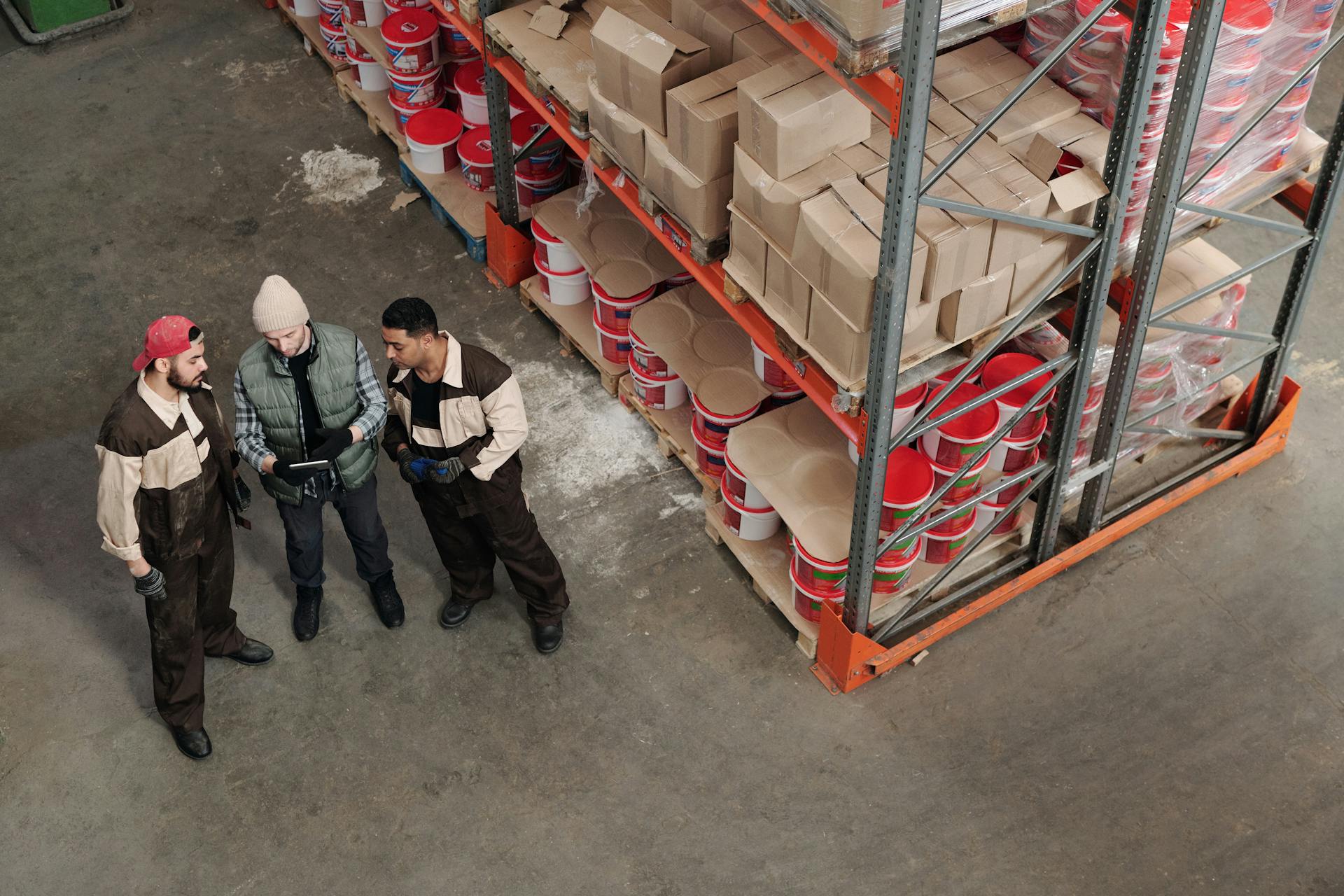
Raw materials and components are delivered by suppliers just as they are needed for production, rather than being stockpiled. This stockless production approach minimizes excess inventory and its associated costs.
Here are the key principles of JIT inventory management:
- Minimal inventory levels
- Highly coordinated pull production
- Closely coordinated production schedule with suppliers and customers
- Accurate demand forecasting and production scheduling
- Use of techniques like kanban cards or signals for inventory control
- Zero inventory at the end of the process
Traditional Methods vs. JIT
Backward scheduling is a traditional method that involves working backwards from the customer's due date to determine when each step must be completed to meet that deadline.
This approach helps minimize delays and stockouts, ensuring everything is in place when needed. By doing so, companies can quickly identify potential problems or delays and address them in advance.
JIT (just-in-time) manufacturing, on the other hand, only stores materials needed to meet an order, reducing costs but also increasing reliance on a smooth supply chain.
JIC (just-in-case) is a similar concept, but it keeps an inventory of raw materials and completed end-products to prepare for supply chain disruptions or sudden spikes in demand.
Manufacturing with a JIC system is more costly, but it provides a buffer against unexpected events and can meet sudden demand instantly.
Traditional Methods
Traditional Methods can be quite rigid and hard to adjust, making it difficult to respond to changes in demand. This is because goods are produced in advance and stored in inventory.
One of the main drawbacks of Traditional Methods is that it can lead to a buildup of inventory, which can take up valuable space and tie up resources.
In contrast to JIT manufacturing, Traditional Methods don't have the same level of flexibility to analyze production processes and improve product quality frequently.
Types of Companies Using
Retailers have benefited from the just-in-time inventory system, allowing them to minimize storage costs and maximize shelf space.
Restaurants are another example of an industry that has successfully implemented JIT, reducing food waste and minimizing inventory holding costs.
On-demand publishing companies have also adopted JIT to quickly respond to changing market demands and reduce inventory levels.
Tech manufacturing companies use JIT to produce and deliver products in a timely manner, meeting the high demand for innovative gadgets and electronics.
Automobile manufacturing is another industry that has benefited from JIT, allowing them to reduce inventory levels and minimize waste in production.
Scheduling

Scheduling is a critical aspect of both traditional methods and JIT. Backward scheduling is a technique where you start with the customer's due date and work backward to determine when each step must be completed to meet that deadline. This ensures everything is in place when needed and helps minimize delays and stockouts.
By working backward, you can quickly identify potential problems or delays and address them in advance. This helps maintain a continuous flow of manufacturing that runs smoothly and efficiently. Companies can meet customer demand on time and at the right quality.
Production scheduling also involves leveling, which is essential for JIT. Heijunka, or production leveling, establishes a smooth production sequence and consistent demand rate by avoiding batching.
Versus
JIT versus JIC manufacturing: which one is right for you?
JIT (just-in-time) manufacturing relies on a smooth supply chain to function, but this can be a risk.
JIC (just-in-case) is a similar concept, but it keeps an inventory of raw materials and completed end-products to prepare for supply chain disruptions or sudden spikes in demand.
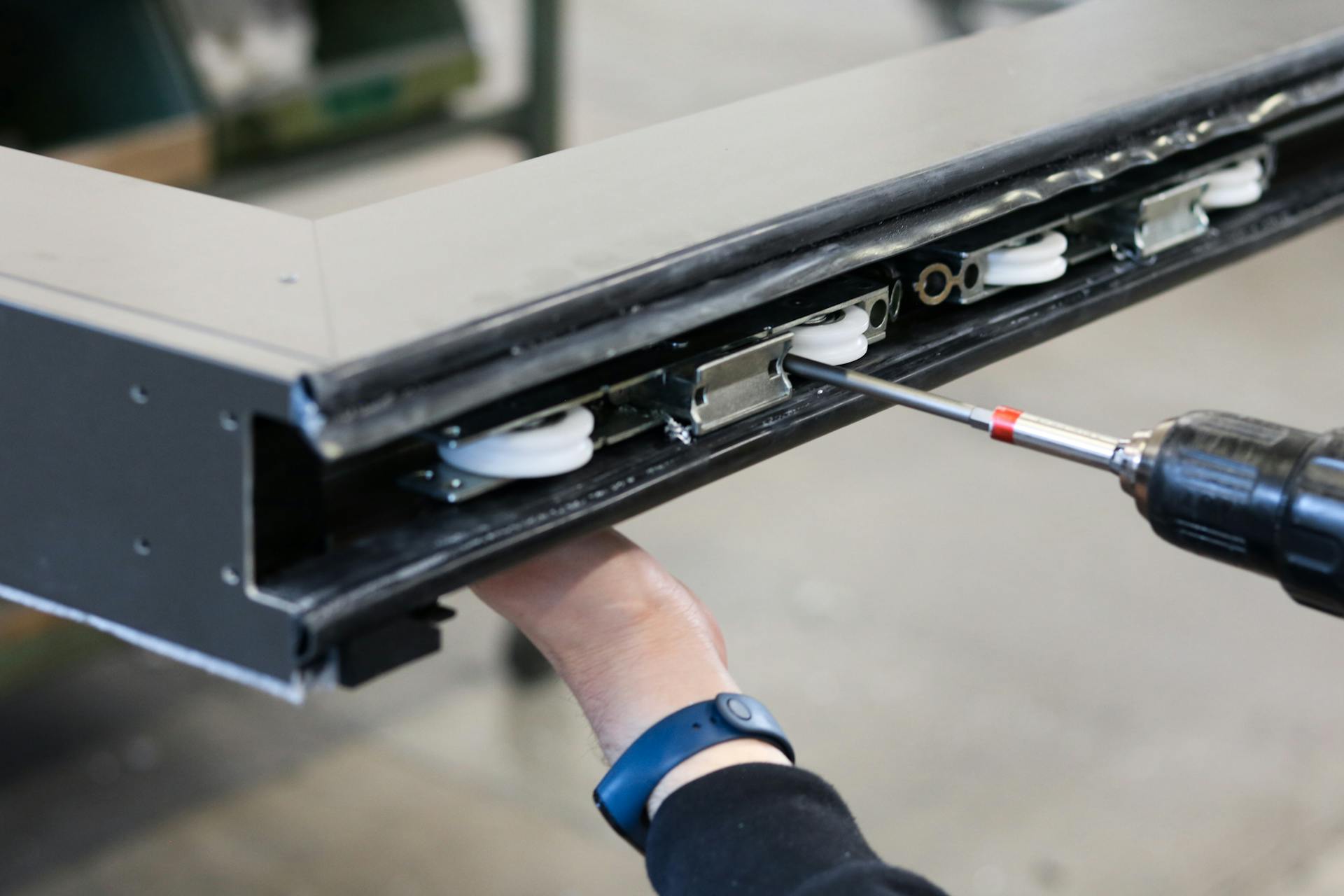
Manufacturing with a JIC system is more costly, but it's better prepared for unexpected events.
A factory with a JIC system can meet sudden demand instantly, which was a major advantage during the COVID-19 pandemic.
The best practice is to find a balance between JIT and JIC, eliminating wasteful practices and being somewhat prepared for unforeseen circumstances.
If this caught your attention, see: In a Just in Time Inventory System Suppliers
Key Components of JIT
The just-in-time manufacturing system is built on a few key principles that make it so effective. One of the core elements is the use of kanban, a scheduling system that helps avoid overcapacity of work-in-process.
Kanban is often used in conjunction with JIT to ensure a smooth flow of production. It's a crucial component of the system, as it helps prevent waste and inefficiency.
The success of JIT production relies on several factors, including steady production, high-quality workmanship, no machine breakdowns, and reliable suppliers. This requires a high level of coordination and communication between suppliers, manufacturers, and buyers.
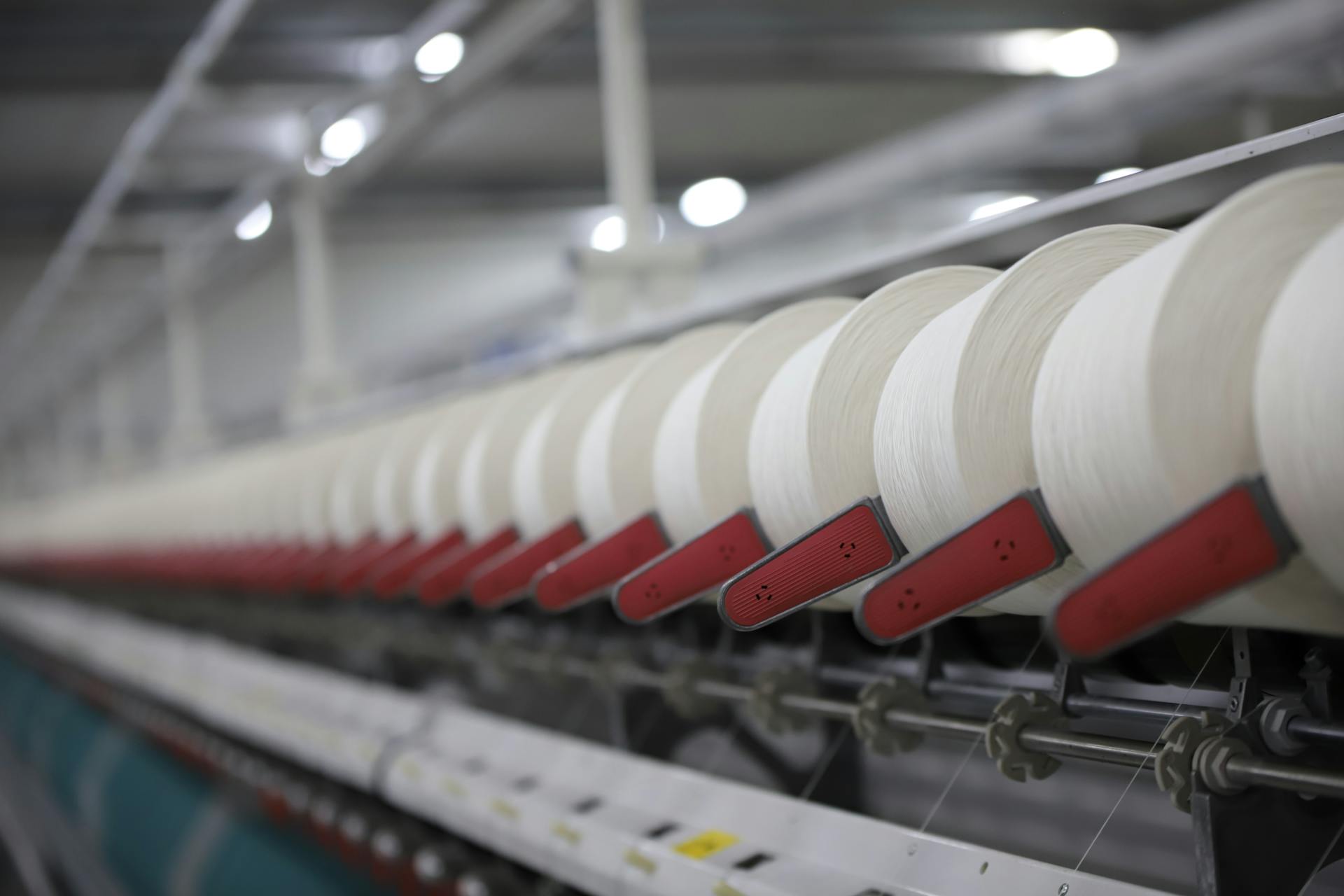
Here are some key components of the JIT system:
- Kanban: a scheduling system used to avoid overcapacity of work-in-process
- Smooth movement: a key gear in the JIT system, ensuring a continuous flow of production
- Demand-driven output: JIT production is built around reacting to real customer orders, rather than producing inventory for stock
- Strategic timings: JIT production relies on carefully timed production and delivery to meet customer needs
- Savvy inventory governance: JIT production requires careful management of inventory to minimize waste and maximize efficiency
- Stringent quality standards: high-quality workmanship is essential for JIT production
By mastering these key components, manufacturers can achieve the benefits of JIT production, including reduced waste, increased efficiency, and improved customer satisfaction.
Implementation and Challenges
Implementing a just-in-time production system requires careful planning and execution across the entire organization. It involves overhauling manufacturing processes, supplier relationships, quality control methods, and even company culture.
Implementing a just-in-time production system requires careful planning and execution across the entire organization. Some key challenges in JIT implementation include overhauling manufacturing processes, supplier relationships, quality control methods, and even company culture.
Implementation and Challenges
Implementing a just-in-time production system requires careful planning and execution across the entire organization. This involves overhauling manufacturing processes, supplier relationships, quality control methods, and even company culture.
One of the key challenges in JIT implementation is the need for suppliers to adapt to frequent and short-notice delivery schedules. This requires them to have a good track record of timely delivery, consistent quality, and the ability to respond quickly to changes in demand.
For another approach, see: Tubular Mesh Bag Machine Manufacturer High Quality
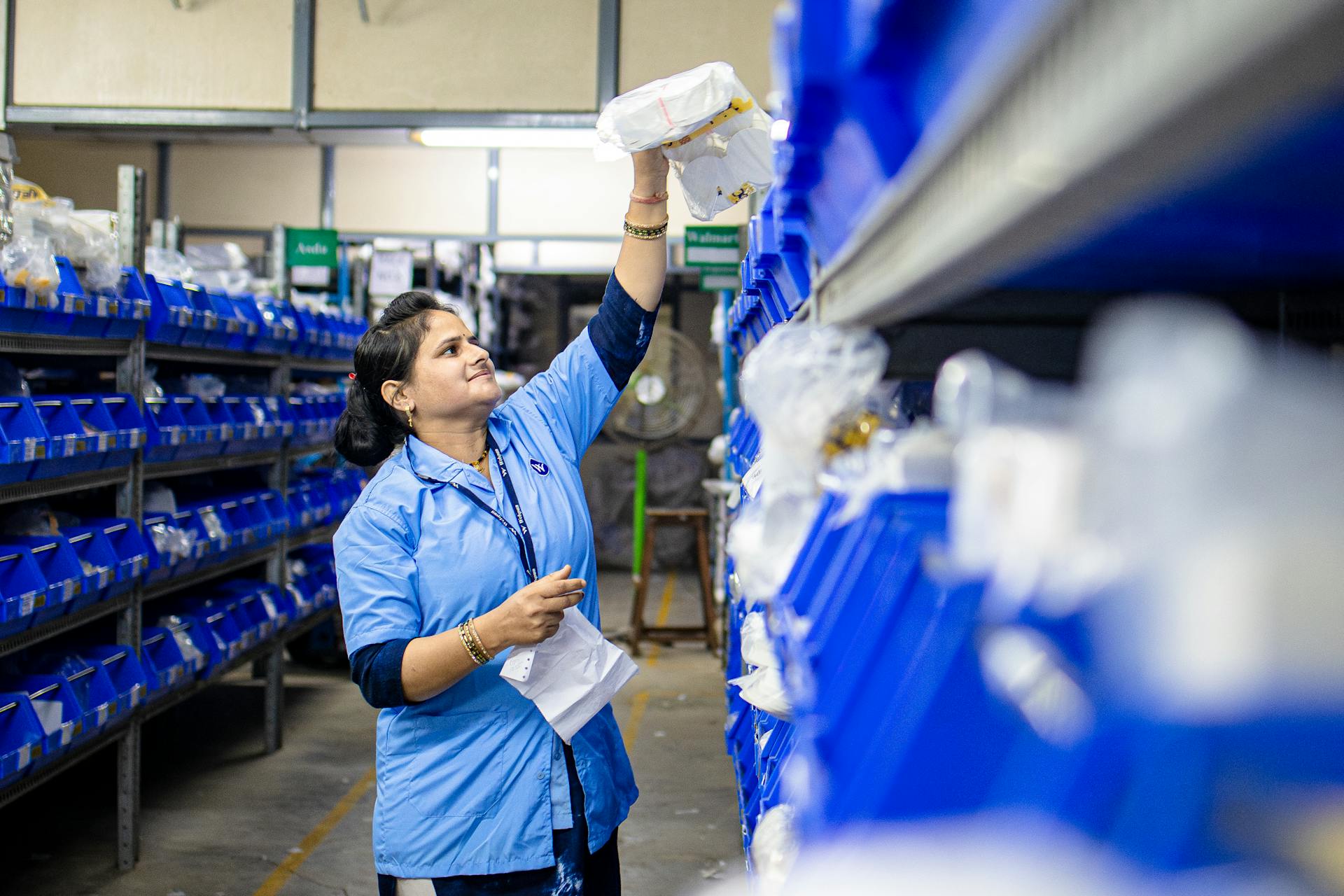
Tight integration and coordination with suppliers is essential for JIT production. Manufacturers develop close supplier partnerships with frequent deliveries of small lot sizes to minimize incoming inventory.
Building close partnerships with key suppliers is crucial for JIT. This involves sharing production schedules and ensuring they have the capacity and systems in place for frequent deliveries.
A reliable supply chain is critical for JIT production. Suppliers must be able to deliver small batches of raw materials/components exactly when needed.
Employee Training & Mindset Shift
Implementing a Just-In-Time (JIT) system requires a major cultural shift for manufacturers. This involves a significant change from traditional batch production.
Employees at all levels need training on lean manufacturing principles. This training is essential to ensure a smooth transition to JIT.
Kanban systems are a key component of JIT, and employees must understand how they work. Quick changeovers are also crucial, as they enable manufacturers to respond quickly to changes in demand.
Problem-solving techniques like Kaizen are vital for identifying and addressing issues in real-time. This mindset shift is critical for the success of a JIT system.
Moving to a JIT system is a major undertaking, and employees must be equipped with the necessary skills and knowledge to make it work.
Material Handling
Material handling is a crucial aspect of implementing changes in a factory. Reducing waste through continuous flow often requires changing the factory layout to a cellular manufacturing model that minimizes material handling and transportation waste between processes.
This approach can significantly decrease the time and resources spent on moving materials around the factory. By grouping similar processes together, manufacturers can reduce the amount of walking and transportation needed, making the production process more efficient.
Changing the factory layout can be a complex task, but it's a necessary step towards reducing waste and improving productivity. Manufacturers can start by analyzing their current processes and identifying areas where material handling can be improved.
By implementing a cellular manufacturing model, manufacturers can reduce waste, increase productivity, and improve overall efficiency. This can lead to cost savings and a more competitive edge in the market.
Efficiency and Productivity
In just in time manufacturing, workflow efficiency is key to meeting customer needs on time. This is achieved by streamlining operations to minimize delays and ensure timely delivery.

Good communication and coordination between the supplier and the manufacturer are crucial for workflow efficiency. Automation tools and process improvement methodologies like Lean or Six Sigma can be used to optimize the workflow.
Minimizing setup times for changeovers between product runs is essential for small lot production and one-piece flow. Techniques like quick die changes, standardized work, and SMED can be used to reduce setup times.
By implementing these strategies, manufacturers can improve their efficiency and productivity, leading to better customer satisfaction and reduced costs.
For another approach, see: Canada Us Border Crossing Wait Times
Quality Control
Quality control is a critical component of just-in-time (JIT) manufacturing. It's essential to producing only the necessary quantities when needed, so any defects or quality issues can quickly disrupt the entire production flow.
JIT places a strong emphasis on quality control and continuous improvement processes. This is because quality is a critical component of the JIT production system.
Zero defects and inventory buffers are key to JIT's success. To achieve this, quality must be built into each process through techniques like Jidoka (automation with human intelligence), poka-yoke (mistake-proofing), and rigorous statistical process control methods.
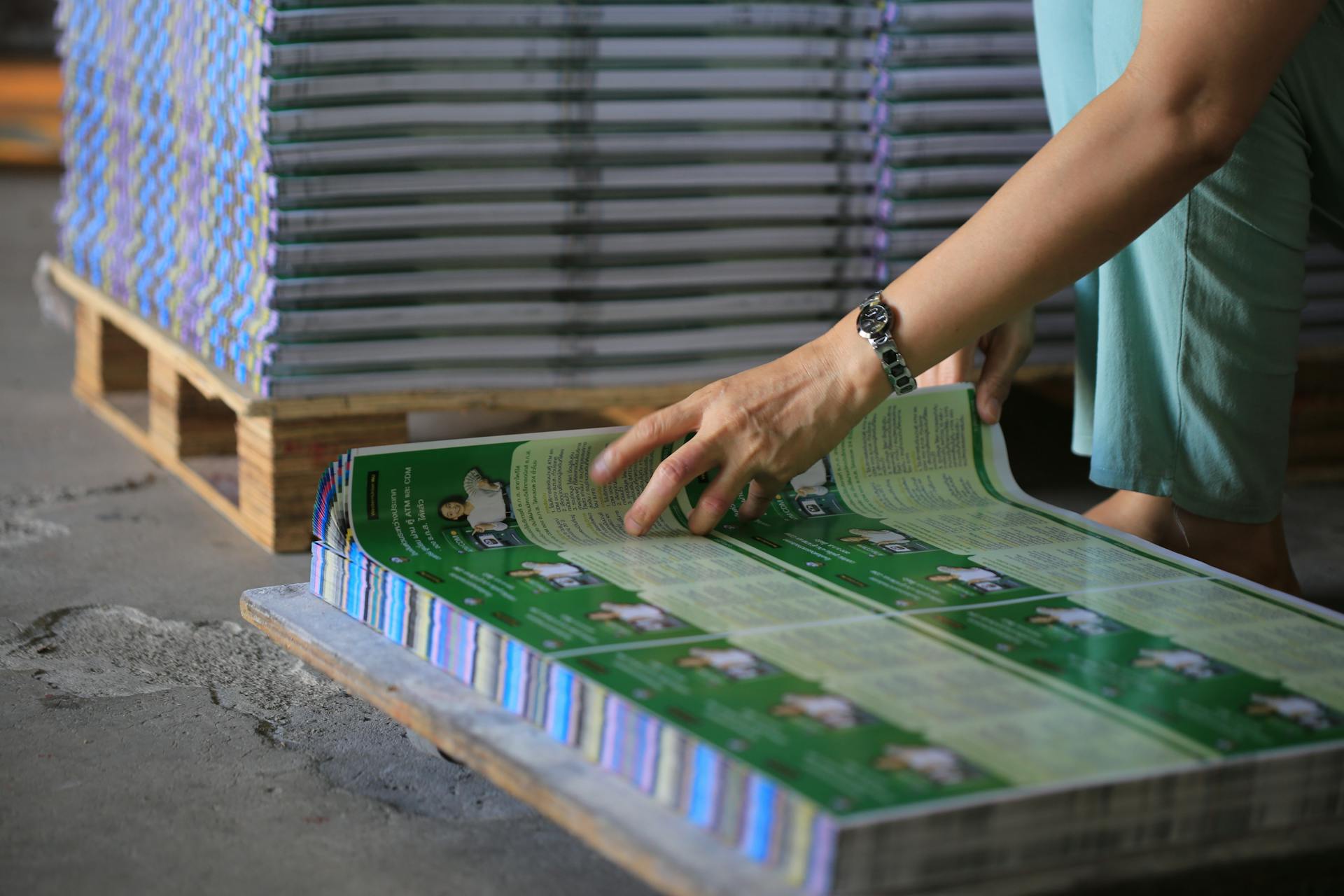
Total quality management (TQM) is adopted by JIT manufacturing to ensure quality at every step. This involves every employee taking responsibility for quality, with processes in place for continuous monitoring and improvement.
Continuous improvement is a core tenet of the JIT philosophy, known as Kaizen. Kaizen encourages employees at all levels to continuously look for opportunities to improve processes and eliminate waste (muda).
Jidoka, or "automation with a human touch", is a core JIT principle that allows processes to stop automatically when defects are detected. This prevents defects from getting passed down the line.
Delivery of personalized materials and components by suppliers also helps improve the process. By working together, companies can achieve continuous improvement and stay competitive in the market.
History and Background
Just in Time manufacturing, or JIT, has a fascinating history that dates back to the early 1970s in Japan. JIT is attributed to the Japanese automaker Toyota Motor Corporation, where executives realized that keeping minimal inventory allowed them to adapt quickly to changes in trends or demands.
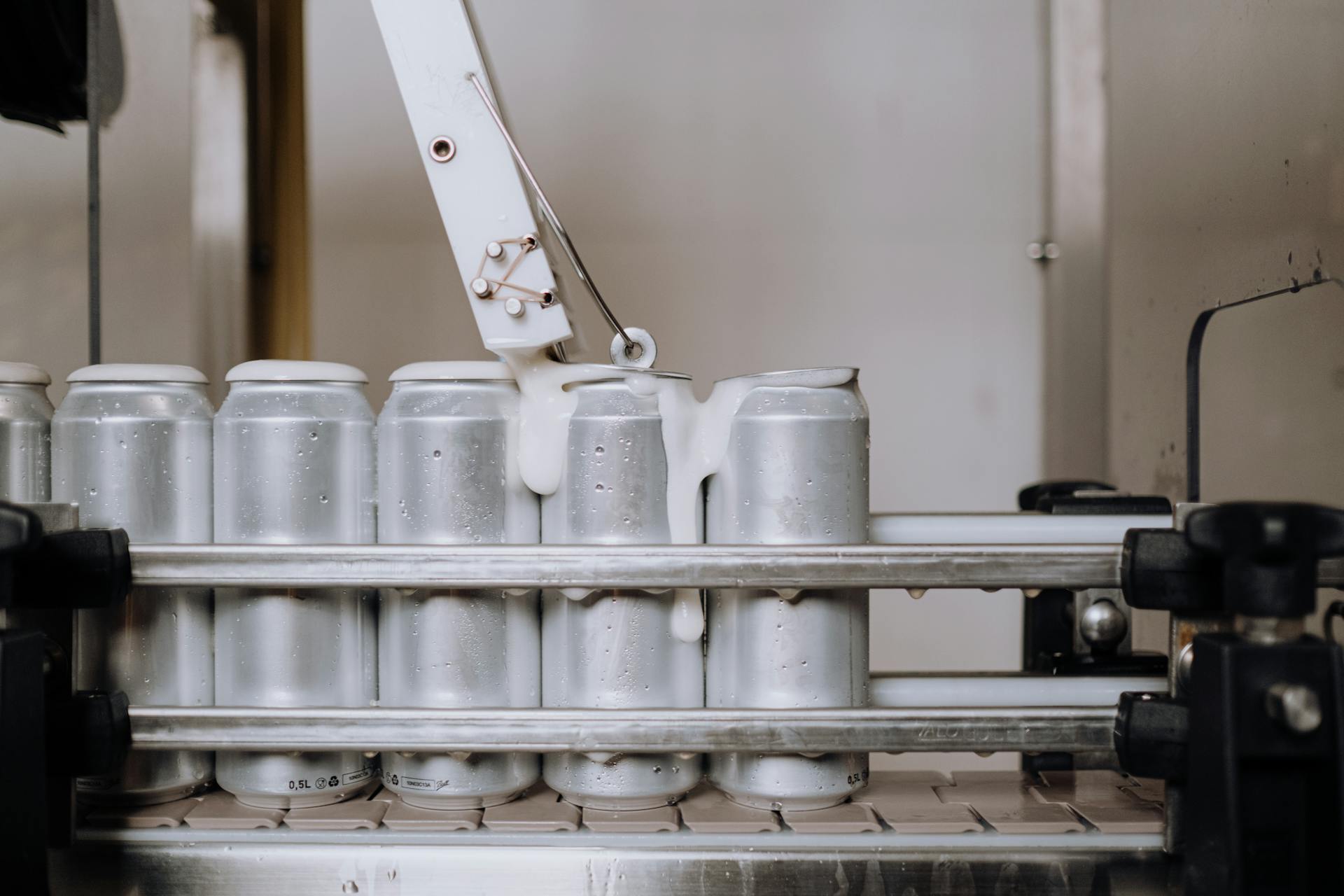
Taiichi Ohno, often referred to as the father of JIT, developed and perfected the concept within Toyota's manufacturing plants. He observed that traditional mass-production methods resulted in waste, including excess inventory, overproduction, and defects. Ohno believed that by eliminating these types of waste, companies could improve efficiency and profitability.
Ohno's approach involved the pull system and kaizen techniques, which focused on customer demand-driven production and employee involvement in identifying and solving problems. This approach was a key factor in JIT's popularity in Japan during the 1970s and 1980s.
The Japanese work ethic played a significant role in the emergence of JIT, with concepts such as constant improvement, group effort, and prioritizing work over leisure contributing to the philosophy's success. These cultural aspects allowed for employee loyalty, low turnover costs, and fulfillment of company goals.
- Key concepts of the Japanese work ethic:
- Constant improvement
- Group effort
- Work prioritized over leisure
- Employee loyalty
What Do You Mean by
Just-in-time inventory systems are all about receiving goods as close as possible to when they're actually needed. This means a company doesn't keep a stock of airbags on its shelves, but rather receives them as cars come onto the assembly line.

Manufacturers using JIT inventory systems minimize inventory and increase efficiency by receiving materials and parts as needed for production. They don't have to pay storage costs, and they're not left with unwanted inventory if an order is canceled.
Companies that operate with low inventory levels heavily rely on their supply chain to deliver the parts they require to build cars on an as-needed basis. This is a key characteristic of a JIT inventory system.
To succeed with JIT manufacturing, companies must have steady production, high-quality workmanship, and reliable suppliers.
History of Inventory Management
The history of inventory management is a fascinating topic. JIT inventory management was first attributed to Toyota Motor Corporation in the 1970s. Executives at Toyota reasoned that the company could adapt more quickly to changes in trends or demands if it didn't keep any more inventory than was immediately needed.
JIT is a Japanese management philosophy that was first developed and perfected within Toyota manufacturing plants by Taiichi Ohno. Ohno is frequently referred to as the father of JIT.
Taiichi Ohno worked for Toyota in a time when Japan suffered from a shortage of capital, storage space, and natural resources. Ohno dealt with these circumstances by designing a highly organized and efficient low-cost production process.
Ohno's approach was based on the concept of constant improvement, where workers are motivated to seek higher standards even when high standards are currently being met. This approach, combined with a focus on group effort and the prioritization of work over leisure, allowed Toyota to meet customer demands with minimum delays.
The benefits of Ohno's approach include employee loyalty, low turnover costs, and the fulfillment of company goals. This is achieved through the opportunity for employees to hone their skills and abilities at a constant rate.
Here are some key cultural aspects associated with the emergence of JIT in Japan:
- Workers are highly motivated to seek constant improvement.
- Companies focus on group effort, combining talents and sharing knowledge.
- Work takes precedence over leisure, with employees often working 14-hour days.
- Employees tend to remain with one company throughout their career span.
These cultural aspects played a significant role in the success of JIT manufacturing in Japan. Just In Time manufacturing gained popularity in Japan in the 1970s and 1980s, and it is a widely used strategy in various industries.
Comparison and Conclusion
Just in time manufacturing reduces inventory costs by 30-50% compared to traditional manufacturing methods.
This significant cost savings is a major advantage of just in time manufacturing, allowing companies to allocate resources more efficiently.
In a study of a Japanese auto manufacturer, production was reduced by 25% through the implementation of just in time manufacturing.
Companies that adopt just in time manufacturing often see a corresponding increase in productivity, as they can focus on producing high-quality products in smaller batches.
A key benefit of just in time manufacturing is that it allows companies to respond quickly to changes in demand, reducing the risk of overproduction and waste.
The reduced production lead times also enable companies to offer faster delivery times to customers, giving them a competitive edge in the market.
Overall, just in time manufacturing is a flexible and efficient approach to production that can have a significant impact on a company's bottom line.
A unique perspective: Auspost Delivery Times
Frequently Asked Questions
Does McDonald's use JIT?
Yes, McDonald's uses Just-In-Time (JIT) methodology to minimize inventory and maximize efficiency. This means they typically only prepare food items after receiving a customer's order.
Is JIT the same as lean manufacturing?
No, JIT and Lean manufacturing are not the same, although they share some similarities and tools. Lean manufacturing is a broader approach that focuses on operations management, while JIT is a specific inventory management strategy that can be achieved through Lean tools.
What companies use just-in-time manufacturing?
Apple and McDonald's are two well-known companies that utilize just-in-time (JIT) manufacturing to streamline their production and delivery processes. By implementing JIT, these companies aim to reduce waste, increase efficiency, and provide customers with fresh products.
Does Nike use JIT production?
Yes, Nike uses a just-in-time (JIT) inventory system to produce and deliver goods on demand. This approach helps Nike meet customer requests efficiently and minimize excess inventory.
What is an example of a just in time JIT?
A just-in-time (JIT) example is a car assembly plant receiving airbags as cars come onto the assembly line, eliminating the need for pre-stocked inventory. This strategy ensures timely delivery of goods exactly when needed.
Sources
- https://www.investopedia.com/terms/j/jit.asp
- https://www.ifm.eng.cam.ac.uk/research/dstools/jit-just-in-time-manufacturing/
- https://www.inboundlogistics.com/articles/just-in-time-manufacturing/
- https://www.6sigma.us/manufacturing/just-in-time-production-system-jit/
- https://4industry.com/manufacturing-glossary/just-in-time/
Featured Images: pexels.com