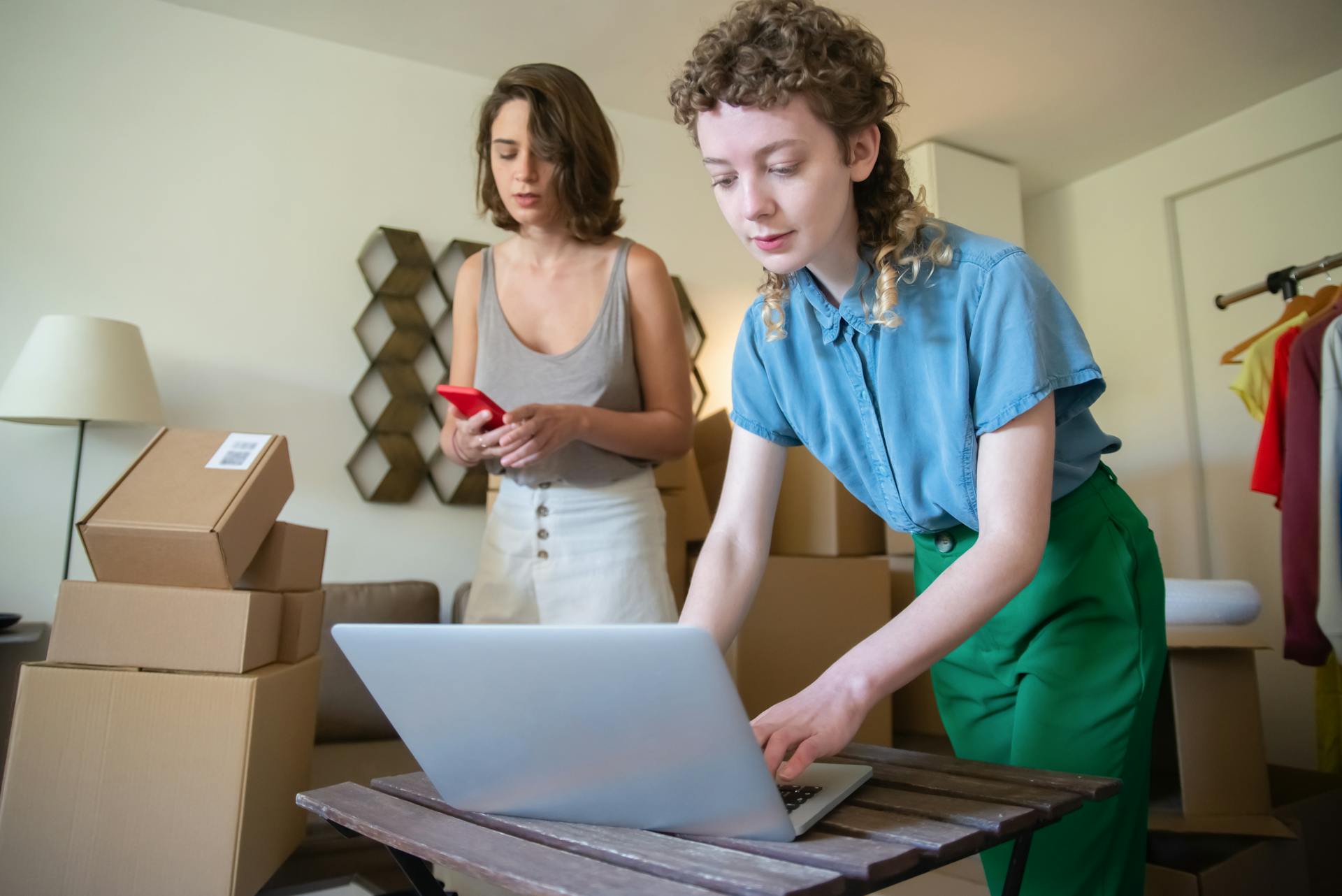
Just in Time inventory strategies can be a game-changer for businesses looking to maximize efficiency. By implementing a just-in-time inventory system, companies can reduce storage costs and minimize waste.
With just-in-time inventory, products are ordered and received just in time to meet customer demand, eliminating the need for large storage spaces. This approach has been adopted by many companies, including Toyota, which has seen significant cost savings as a result.
Just-in-time inventory requires a high level of coordination and communication between suppliers, manufacturers, and customers. This can be achieved through the use of technology, such as inventory management software, to track inventory levels and automate ordering processes.
Intriguing read: Dutch Harbor Alaska Time
What is JIT Inventory?
Just-in-time inventory is a management philosophy that prioritizes minimizing inventory and maximizing efficiency. It was originally referred to as a production system that meets customer demand exactly, in time, quality, and quantity.
The Institute for Manufacturing at the University of Cambridge defines just-in-time as a strategy for forwarding material or explicit labor or qualities at the exact second where it's required, reducing nearby inventories and inefficient worker hours.
This approach is characterized by minimal inventory on hand, reduced holding costs, and a streamlined production process that is highly responsive to market demands. By implementing JIT inventory management, companies can significantly lower their storage costs and reduce waste in the production process.
Here are some key benefits of implementing JIT inventory management:
- Reduced Waste: By only ordering and receiving materials or goods as they are needed for production, excess inventory is minimized.
- Lower Storage Costs: With a smaller inventory on hand, there is less risk of damage or theft, and storage costs are reduced.
- Heightened Operational Efficiency: JIT inventory management streamlines the production process, eliminating bottlenecks that can slow down operations.
What Is?
Just-in-time (JIT) inventory is a philosophy that prioritizes minimizing inventory and maximizing efficiency. It's a management approach that aims to produce goods exactly when and where they're needed, reducing nearby inventories and inefficient worker hours.
JIT inventory management is a strategy that aligns raw materials orders from suppliers directly with production schedules. This approach allows for lower storage costs of parts and products to entice inventory turnover.
By implementing JIT inventory management, companies can significantly lower their storage costs. There's no need to maintain large warehouses to store excess inventory, which can be expensive in terms of rent, utilities, and labor costs.
JIT inventory management helps to streamline the production process and eliminate bottlenecks that can slow down operations. It reduces idle time for workers and machines waiting for materials to arrive.
Here are some key benefits of implementing JIT inventory management:
- Reduced Waste: By only ordering and receiving materials or goods as they're needed for production, companies can minimize overproduction and excess inventory.
- Lower Storage Costs: With JIT inventory management, companies can lower their storage costs by not maintaining large warehouses to store excess inventory.
- Heightened Operational Efficiency: JIT inventory management helps to streamline the production process and eliminate bottlenecks that can slow down operations.
A Brief History of Manufacturing
The concept of just-in-time manufacturing has a rich history that dates back to the early 1970s in Japan, specifically in Toyota's manufacturing organizations.
Taiichi Ohno, an industrial engineer and businessman, is credited with establishing the Toyota Production System (TPS) in the 1940s, which laid the foundation for the just-in-time method.
Ohno's framework for the just-in-time method emphasized producing only what is needed, when it is needed, and in the amount needed, aiming to eliminate all waste.
The TPS was based on two key concepts: "jidoka" (automation with a human touch) and just-in-time production, where each process produces only what is needed for the next process in a continuous flow.
Ohno's successors innovated automation in the textile industry, including a weft-breakage automatic stopping device in 1896 and the world's first automatic loom with non-stop shuttle-change motion in 1924.
These innovations were later applied to Toyota's automotive production lines, where they remain a cornerstone of the company's manufacturing philosophy.
The just-in-time philosophy has since been applied to the supply chains of major auto manufacturers, including household EV manufacturers, in an effort to mitigate battery and chip shortages.
Advantages of JIT Inventory
Implementing a just-in-time (JIT) inventory strategy can bring significant value to your company. Real-time inventory control is the foundation of JIT management, ensuring that materials and products are ordered and produced only when needed.
By using real-time inventory control, businesses can drastically lower holding costs, including storage, insurance, and spoilage expenses. This is because inventory is ordered and stored only as required.
Real-time inventory control also creates transparent supply chain visibility, allowing businesses to have an accurate database to monitor inventory, sales, orders, and deliveries. This reduces the risk of human error, providing a more defined and detailed inventory trail.
The system bolsters efficiency in production and order fulfillment processes, ensuring that resources are allocated justly. This leads to increased efficiency in production and order fulfillment, while reducing costs associated with inventory.
Implementing JIT inventory also enhances a company's flexibility and responsiveness to market changes, thereby improving customer satisfaction. Businesses can meet demand without delay or compromise, resulting in higher customer satisfaction and brand loyalty.
Here are some key benefits of JIT inventory:
- Reduced holding costs
- Transparent supply chain visibility
- Increased efficiency in production and order fulfillment
- Improved customer satisfaction
- Enhanced flexibility and responsiveness to market changes
Disadvantages of JIT Inventory
Just in time inventory systems can be complex to plan, especially when relying on fewer suppliers to cut down on construction overhead. This can lead to potential disruptions in the supply chain.
In construction, just in time inventory practices can increase inventory turnover, hoarding at jobsites, and stockouts if not implemented dynamically. These issues can arise due to the reliance on fewer suppliers and the need for dynamic inventory managers.
Some potential disadvantages of just in time inventory systems include:
- Potential disruptions in the supply chain
- Reliance on fewer suppliers could lead to construction downtime if supplier experiences an unexpected breakdown
- Potential compromise in quality if supply chain issues lead to sourcing materials from non-preferred vendor, while unexpected costs may also be incurred
- Increase of inventory turnover
- Increase in hoarding experienced at various jobsites
- Possible increase in stockouts
Disadvantages of
JIT inventory systems can be complex to plan, requiring dynamic inventory managers to respond to potential supply chain disruptions.
Potential disruptions in the supply chain are a significant disadvantage of JIT inventory systems.
Reliance on fewer suppliers can lead to construction downtime if a supplier experiences an unexpected breakdown.
In construction, JIT inventory practices can lead to an increase in inventory turnover.
Hoarding at various jobsites is another issue that can arise from JIT inventory practices.
Possible increases in stockouts are also a concern in construction projects that adopt JIT inventory systems.
Here are some specific disadvantages of JIT inventory systems in construction:
- Increase of inventory turnover
- Increase in hoarding experienced at various jobsites
- Possible increase in stockouts
Challenges and Solutions
The JIT inventory system can be a game-changer for businesses, but it's not without its challenges.
The primary challenge lies in the need for precise demand forecasting, which can be a daunting task.
Accurate forecasting tools are crucial in this regard, as they help businesses predict demand with greater accuracy.
A misstep in demand forecasting can lead to stockouts and unmet orders, which can have serious consequences for a business's reputation and bottom line.
Forming a reliable partnership with logistics providers is also essential to ensure a seamless supply chain that can support JIT's stringent requirements.
Lean Supply Solutions, for instance, offers the expertise and infrastructure necessary to bolster JIT implementation efforts, ensuring that potential hurdles are effectively addressed.
Who Should Use JIT Inventory?
Established businesses with trusted vendors and a solid understanding of their production and supply chain processes tend to work well with JIT systems. This is because they can form close, mutually beneficial partnerships with their vendors and predict customer demand.
Older businesses are more likely to have the kinks worked out of their production and supply chain processes, making it easier to get replenishment orders when they're needed and reduce inventory costs. They're also more likely to have a better idea of what to expect in terms of seasonality and demand fluctuation.
Companies with quick product turnaround, predictable customer demand, and solid vendor relationships can benefit from JIT inventory management. This includes industries like on-demand publishing, manufacturing, automotive, construction, fast-food franchises, and florists.
Here are some examples of JIT inventory industry applications:
- On-demand publishing: The publishing industry often uses JIT inventory systems to reduce waste by printing and assembling books only when they're sold.
- Manufacturing industry: JIT systems are beneficial for manufacturers that plan for raw materials to be delivered on specific production days.
- Automotive industry: The JIT system originated within the industry when Toyota Motor Company developed it in the 1970s to reduce delays and costs.
- Construction industry: The construction industry relies on quickly moving materials to stock different locations and projects.
- Fast-food franchises: Fast-food chains only make meals when customers place orders, reducing waste and keeping food fresh.
- Florists: Many florists use JIT inventory to maintain a fresh stock of flowers by ordering specific quantities that relate to their typical demand and customer expectations.
Implementing JIT Inventory
To implement a JIT inventory system, you need a solid forecast of customer demand. This is crucial for ordering the correct quantities and avoiding stockouts.
A JIT system works best for established businesses with trusted vendors and a smooth supply chain management. This allows for close, mutually beneficial partnerships with suppliers, which is necessary for JIT success.
You should also have an efficient customer order fulfillment system and inventory control software that can process replenishment orders quickly. This will help reduce inventory costs and make it easier to get replenishment orders when needed.
Here are the key requirements for JIT inventory implementation:
- Forecast vs. demand: You must have a thorough knowledge of typical industry demands and cycles.
- Supplier production times: Understand supplier lead times and work closely with suppliers to understand typical production times.
- Supplier shipment times: Plan for upcoming shipments as accurately as possible and understand supplier shipping timetables.
- Supplier locations: Note physical locations and consider how they could affect success.
External influences, such as global events, can impact JIT inventory management success. It's essential to consider this risk when deciding whether to integrate a JIT model into your company.
Best Practices for JIT Inventory
Just in time inventory systems can be a game-changer for businesses, but they require careful planning and execution to succeed.
Established businesses tend to be the best fit for JIT systems due to their trusted vendors, streamlined production processes, and better understanding of customer demand.
To implement a JIT system, you need reliable suppliers that follow the same production schedules consistently, and a solid forecast of customer demand.
Having a smooth supply chain management system is also crucial, with dependable third-party logistics providers that can get your replenishment orders to you on time.
A JIT system works best when inventory production has short turnaround times, and you have an efficient customer order fulfillment system in place.
To achieve this, you need an inventory control or inventory management software that can process replenishment orders quickly or automatically.
Here are the key criteria to consider when deciding if a JIT system is right for your business:
Higher Efficiency
Just-in-time inventory is all about streamlining production and order distribution. By only processing requested products, employees have less inventory to sort, process, and manage.
With fewer items in stock, it's easier to retrieve items for order fulfillment. Regular inventory management becomes much smoother with a limited and well-coordinated stock.
Partnering with locally-sourced suppliers can be a game-changer. They can deliver products rapidly and ensure a fresh stock, reducing the need for safety inventory.
Having a nearby supplier also reduces the need for excess inventory. You can safely rely on your local partner to resupply your stores, making excess inventory unnecessary.
A just-in-time inventory system can lower storage costs by reducing the amount of inventory that takes up extra space in warehousing.
Reducing Costs with JIT Inventory
Just-in-time inventory is a game-changer when it comes to reducing costs. By requiring very low inventory levels, JIT inventory reduces the working capital required for inventory purchases as well as storage costs.
With a JIT system, you can purchase raw materials only when needed, freeing up available cash for the company to utilize more effectively. This is especially beneficial for established businesses with trusted vendors and smooth supply chain management.
In fact, established businesses are more likely to have the kinks worked out of their production and supply chain processes, making it easier to get replenishment orders when they're needed and reduce inventory costs.
Labor costs are also lower in JIT manufacturing, as fewer factory workers are required compared to full-time production. This is a significant advantage for businesses looking to reduce their operational expenses.
Here are some key benefits of reducing costs with JIT inventory:
- Reduced working capital required for inventory purchases
- Lower storage costs
- Improved cash flow
- Lower labor costs
By implementing a JIT inventory system, businesses can minimize waste, reduce costs, and improve their overall efficiency. It's a strategy that's worth considering for any business looking to streamline its operations and reduce its environmental impact.
Examples and Case Studies
Just-in-time inventory systems have been implemented in various industries, achieving significant results.
Companies like Dell and Toyota have successfully adopted this approach, reducing inventory costs and improving production efficiency.
Dell's just-in-time inventory system allows it to hold only 3-4 days' worth of inventory, compared to the industry average of 30-60 days.
This enables Dell to save around $1 million per year in inventory holding costs.
Toyota, on the other hand, has reduced its inventory levels by 90% since implementing its just-in-time system.
By doing so, Toyota has been able to minimize waste and optimize production processes.
The semiconductor industry has also seen the benefits of just-in-time inventory, with companies like Intel reducing their inventory levels by 50-60%.
This has led to significant cost savings and improved supply chain efficiency.
Frequently Asked Questions
What is the difference between JIT and EOQ?
JIT and EOQ are inventory management methods that differ in their approach to ordering and stocking: JIT orders just-in-time, minimizing inventory, while EOQ calculates optimal quantities to balance costs and demand
What are the 4 steps in JIT process?
The JIT process consists of sourcing, production, delivery, and continuous improvement. These four steps work together to optimize efficiency and minimize waste in manufacturing and logistics.
Sources
- https://www.business.org/finance/inventory-management/what-is-just-in-time-inventory-management/
- https://www.truecommerce.com/blog/what-is-just-in-time-inventory-management/
- https://onekeyresources.milwaukeetool.com/en/what-is-just-in-time-inventory
- https://www.leansupplysolutions.com/blog/just-in-time-management/
- https://www.itconvergence.com/blog/6-key-benefits-of-just-in-time-inventory-management/
Featured Images: pexels.com