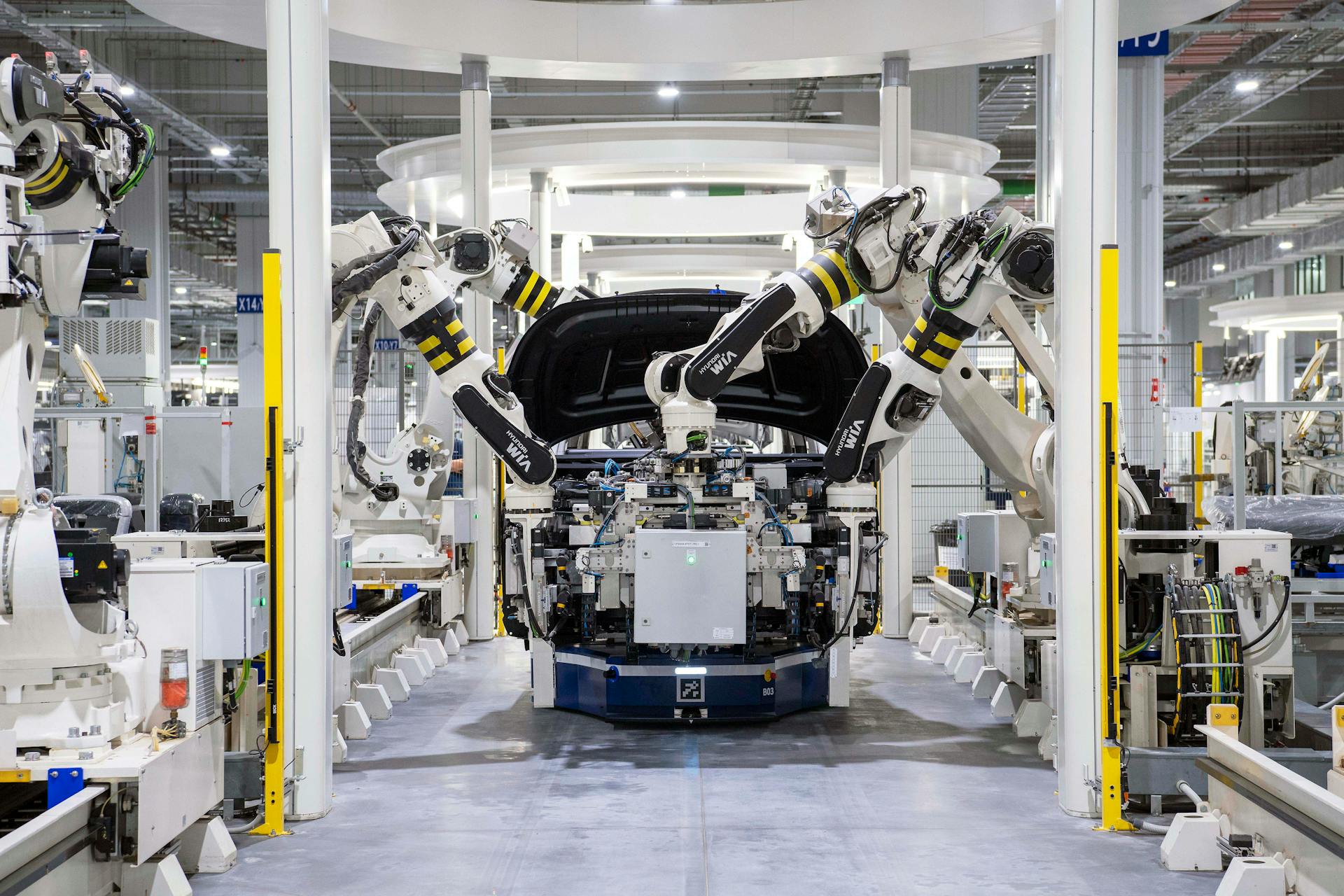
Just in time lean management can be a game-changer for businesses looking to boost efficiency and productivity. By focusing on continuous improvement and eliminating waste, companies can achieve significant cost savings and improve customer satisfaction.
The key to successful implementation lies in understanding the principles of just in time lean management. This involves recognizing and eliminating non-value added activities, streamlining processes, and improving flow.
A well-executed just in time lean management system can lead to substantial reductions in inventory levels, resulting in significant cost savings.
What Is Just-In-Time Lean Management?
Just-in-time (JIT) lean management is a materials management strategy that aligns the construction schedule with the inventory transportation schedule to ensure that workers receive materials only when they are needed, reducing waste in the process.
This approach aims to minimize inventory, reduce waste, and boost efficiency by receiving goods only as they are needed in the production process. By understanding JIT's core principles, businesses can enhance their production workflows, improve product quality, and respond more swiftly to shifts in consumer demand.
Broaden your view: Transportation Management System
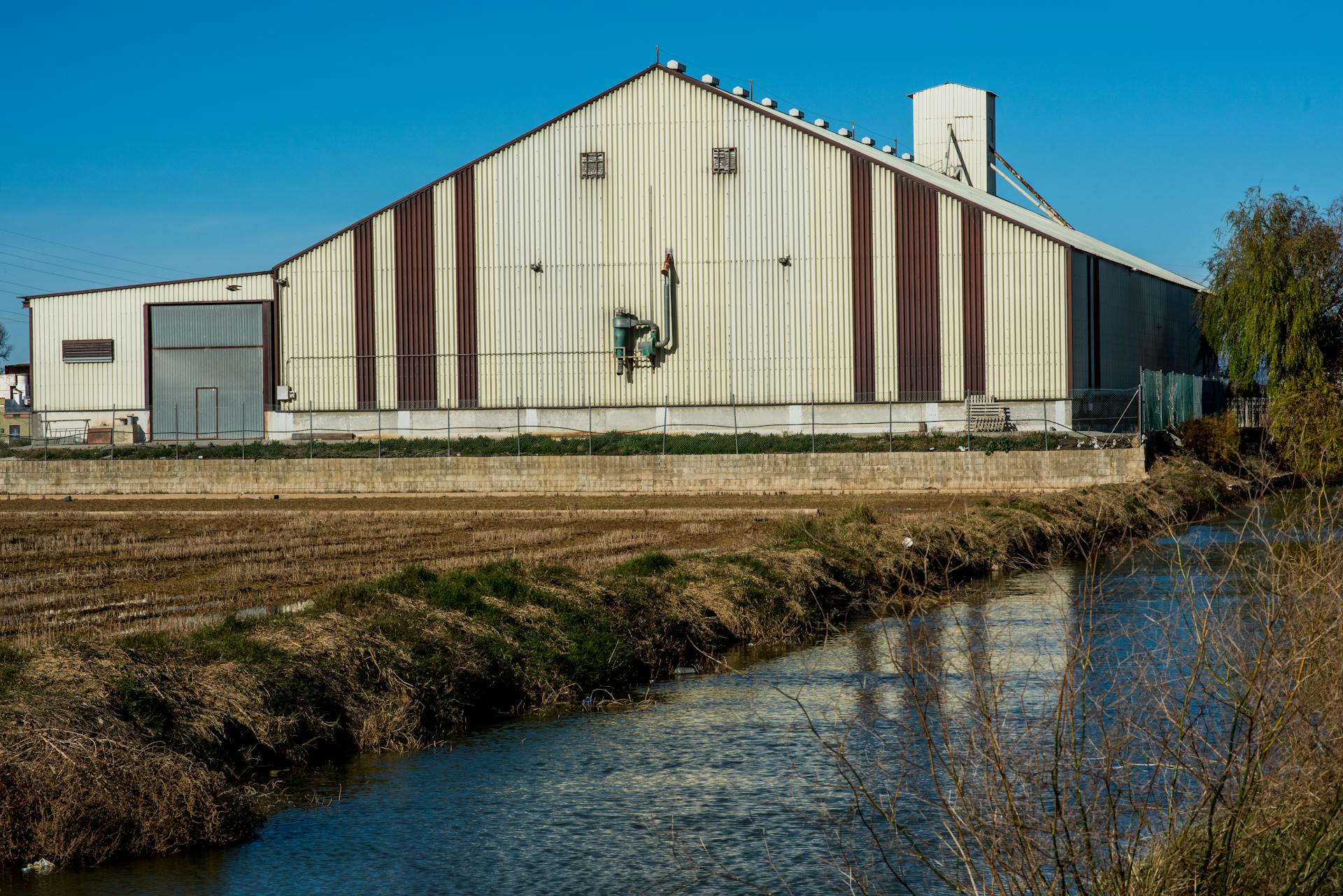
Just-in-time lean management targets removing wasted efforts and expenses from making methods by crafting the right part, in the right spot, at precisely the right moment. This contrasts traditional approaches that often hold lots of raw materials, work underway, and finished products waiting idly.
The core elements of JIT production system involve pull-driven output, smooth streaming, takt timings, and kanban signals. These concepts help JIT dump waste, minimize what sits waiting, and improve overall efficiency for elongated savings and stronger client loyalty.
Here are the 8 types of waste that occur in construction projects, as identified by the Lean Construction Institute:
- Unnecessary Transportation
- Overproduction
- Waiting Time
- Transportation
- Inventory
- Overprocessing
- Defects
- Skills Wastefulness
Just-in-time lean management aims to solve the problem of unnecessary transportation by helping teams better organize their material management and transportation logistics.
Method and Approach
Just-in-time lean management is all about producing and delivering products just in time to meet customer demand. This approach minimizes inventory, reduces waste, and boosts efficiency.
Explore further: Dutch Harbor Alaska Time
Load leveling is a key technique in JIT production, where organizations determine the right quantities and types of products needed each day to meet customer orders. This involves creating a daily schedule to produce products with various customer specifications in a smooth sequence.
Takt time is critical in leveled production, as it represents the rate at which each product must be completed to meet customer needs, expressed in time per part. By calculating takt time, organizations can ensure they're producing products at the right pace.
Kanban is a vital technique in JIT production, often referred to as the "nervous system" of lean production. It determines production quantities and facilitates JIT production and ordering systems by creating a "pull" system, where products are produced only when ordered.
Here are the four important "rules" for implementing a kanban system:
- Kanban works from upstream to downstream in the production process, starting with the customer order.
- Upstream processes only produce what has been withdrawn, following the sequence and quantity indicated on the kanban.
- Only 100% defect-free products continue through the production line, with each step uncovering and correcting defects.
- The number of kanban should be decreased over time to uncover areas of needed improvement.
By following these rules, organizations can effectively implement a kanban system and achieve the benefits of JIT production.
Benefits and Advantages
Just-in-time lean management offers numerous benefits and advantages that can transform your business. One of the most significant advantages is the reduction of inventory, as seen in the case study of Daman Products in 1999, where inventory was reduced from 4 to 8 weeks to 5 to 10 days.
Reduced inventory levels also lead to a decrease in storage space, with some companies achieving a reduction of up to 50%. For example, Hewlett-Packard's Greeley division reduced its storage space by 50%.
Another key benefit of just-in-time lean management is the reduction of lead times. The case study of NCR in 1998 shows that lead times were reduced from 15 days to 2 days by implementing just-in-time purchasing.
Here are some specific benefits of just-in-time lean management:
These statistics demonstrate the potential for significant improvements in inventory management, labor costs, and storage space with just-in-time lean management. By reducing inventory and lead times, companies can also reduce the amount of energy used for heating, air conditioning, and lighting, as well as the resource consumption and waste associated with maintaining unneeded space.
Potential Challenges and Shortcomings
Implementing a just-in-time (JIT) production system can be challenging, especially when it comes to reducing overproduction and associated waste. Large and unpredictable market fluctuations can make it difficult to succeed in this area.
JIT can result in more frequent "milk runs" for parts and material inputs, leading to increased traffic congestion, fuel use, and vehicle emissions. However, efficient load planning can significantly reduce or eliminate these environmental impacts.
Implementing JIT throughout the supply chain is crucial, as it can push inventory carrying activities up the supply chain if not done properly, resulting in increased environmental impacts from overproduction, damaged goods, and inventory storage.
Here are some key challenges to consider when implementing a JIT production system:
- Milk runs can contribute to traffic congestion and environmental impacts.
- Large and unpredictable market fluctuations can make it difficult to reduce overproduction and associated waste.
- JIT can push inventory carrying activities up the supply chain if not implemented throughout the supply chain.
Potential Shortcomings
Implementing a just-in-time production system can be a game-changer for businesses, but it's not without its challenges. One of the main potential shortcomings is the increased frequency of "milk runs" for parts and material inputs, leading to more transport trips and associated environmental impacts.
This can be particularly problematic if not managed properly, resulting in increased fuel use and vehicle emissions. However, efficient load planning can help mitigate these effects.
Another potential issue is that JIT/kanban may not be effective in reducing overproduction and waste if products have large and unpredictable market fluctuations. This can make it difficult to accurately forecast demand and adjust production accordingly.
If a JIT system is not implemented throughout the supply chain, it can simply push inventory carrying activities up the supply chain, leading to increased environmental impacts from overproduction, damaged goods, and more.
Implementation and Challenges
Implementing a just-in-time production system requires careful planning and execution across the entire organization. This involves overhauling manufacturing processes, supplier relationships, quality control methods, and even company culture.
Some key challenges in JIT implementation include careful planning and execution, which can be daunting for many organizations. Overhauling multiple aspects of the business can be overwhelming.
To overcome these challenges, organizations should develop their own Lean plan as developed by the "Lean Leadership". This enables Lean teams to provide suggestions for their managers who then make the actual decisions about what to implement.
Coaching is recommended when an organization starts off with Lean to impart knowledge and skills to shop-floor staff. Improvement metrics are required for informed decision-making.
The solution to a specific problem for a specific company may not have generalized application. The solution must fit the problem. This requires understanding the true problem by consulting shop floor personnel.
Value-stream mapping (VSM) and 5S are the most common approaches companies take on their first steps to Lean. Front-line workers should be involved in VSM activities.
Implementation and Steps
To implement Lean effectively, it's essential to have a Lean plan developed by Lean Leadership, which enables Lean teams to provide suggestions for their managers. This plan should be tailored to the specific needs of the organization.
Coaching is a crucial step in the Lean implementation process, as it helps impart knowledge and skills to shop-floor staff. This is especially important when an organization is starting off with Lean.
Management should not decide on solutions without understanding the true problem by consulting shop-floor personnel. This ensures that the solution fits the problem.
Value-stream mapping (VSM) and 5S are commonly used approaches in the first steps to Lean. Front-line workers should be involved in VSM activities to ensure their input and expertise are considered.
Implementing a series of small improvements incrementally along the supply chain can bring forth enhanced productivity. This approach helps to minimize waste and maximize efficiency.
To implement Just-in-Time (JIT) manufacturing, decisive planning and adherence to lean principles are necessary.
Key Principles and Tools
The core elements of just-in-time production systems focus on minimizing inventory and reducing waste to boost efficiency.
Just-in-time production revolves around a few key principles and practices that allow manufacturers to achieve this goal.
A key principle of just-in-time production is the use of lean operations, which can be refined with a Next Plus MES platform that seamlessly aligns with lean manufacturing frameworks.
Next Plus' MES platform has been engineered to harmonize with JIT production, featuring workflow optimization tools that auto-tune manufacturing sequences in real-time.
Data is king in JIT systems, and Next Plus' real-time data collection capability captures every detail required to streamline operations.
The platform's real-time data collection capability includes detailed sensor data and equipment performance, providing a comprehensive view of the manufacturing process.
Traceability and compliance are non-negotiable in today's manufacturing landscape, especially in JIT environments where each part's history is essential for quality control.
The Kanban system uses visual signals like cards or markers to signal when more material or product is needed, providing a simple pull mechanism to move items through the just-in-time system.
Customization is a critical aspect of JIT, as no two manufacturing setups are identical, and Next Plus' customizable forms and documentation offer the flexibility to structure workflow documentation to meet specific operational needs.
Supplier Relationships and Inventory Management
JIT production systems require very tight integration and coordination with suppliers. This involves frequent deliveries of small lot sizes to minimize incoming inventory.
Close supplier relationships are essential for JIT. Manufacturers develop partnerships with suppliers to ensure timely deliveries and minimize inventory holding costs.
Accurate demand forecasting and production scheduling are critical for JIT inventory control. This helps determine precisely how much inventory is needed and when based on the production schedule and lead times.
To enable lean inventory management, JIT manufacturing requires highly reliable vendors who can provide frequent deliveries of small lot sizes on a just-in-time basis. Techniques like kanban cards or signals are used to authorize and control the inventory movement and replenishment.
Strong relationships with reliable suppliers are the backbone of JIT. Cultivate partnerships based on timely delivery and quality materials, ensuring a synchronized supply chain.
Sourcing materials locally will enable you greater control over the shipping schedule of materials and allow you to make on-the-fly changes with minimal consequence. This is a great opportunity to begin sourcing your materials locally, whether that means receiving materials from a nearby manufacturer or manufacturing materials on your own.
Employee Training and Mindset Shift
Implementing a Just-In-Time (JIT) system requires a significant cultural shift for manufacturers accustomed to traditional batch production. Employees at all levels need training on lean manufacturing principles.
This training should cover key areas such as kanban systems, quality at the source, quick changeovers, and problem-solving techniques like Kaizen. Employees must be equipped to adapt to a more agile and responsive production environment.
Involving employees in the process is crucial for a successful JIT implementation. By instilling a culture of continuous improvement, every member can be proactive about identifying inefficiencies.
Employee Training and Mindset Shift
Implementing a Just-In-Time (JIT) system requires a significant cultural shift for manufacturers accustomed to traditional batch production. This means employees at all levels need training on lean manufacturing principles.
To achieve this, employees must be trained on kanban systems, which are a key component of JIT. This involves understanding how to manage inventory levels and production flow.
Quick changeovers are another critical aspect of JIT, and employees need to learn how to perform them efficiently. This involves minimizing downtime and maximizing productivity.
Involving employees in the training process is crucial for a successful JIT implementation. This means instilling a culture of continuous improvement where every member is proactive about identifying inefficiencies.
Cross-training employees across multiple disciplines is also essential for JIT flexibility. This allows employees to adapt quickly to changing production needs and ensures that the workforce is versatile and well-trained.
Rebranding
Rebranding as "lean" is a significant step towards transforming your organization. John Krafcik coined the term Lean in his 1988 article, which marked the beginning of a new era in manufacturing.
Implementing Lean manufacturing can have a significant impact on productivity and quality. According to Krafcik, Lean manufacturing plants have higher levels of productivity and quality than non-Lean plants.
However, implementing Lean is not without its challenges. Krafcik noted that the level of plant technology seems to have little effect on operating performance. This means that investing in the latest technology may not necessarily lead to better results.
To mitigate the risks associated with implementing Lean, it's essential to develop a well-trained, flexible workforce. This can be achieved by providing ongoing training and development opportunities to employees.
Product designs that are easy to build with high quality are also crucial for successful Lean implementation. This means that organizations need to focus on designing products that are simple, efficient, and easy to manufacture.
A supportive, high-performance supplier network is also essential for Lean success. This can be achieved by building strong relationships with suppliers and ensuring that they meet the organization's quality and delivery standards.
Continuous Improvement
Continuous Improvement is key to a successful JIT process. Regularly analyzing performance metrics is essential to make informed decisions.
Foster an environment of constant evaluation and refinement, just like the article suggests. This mindset allows you to identify areas for improvement and make necessary adjustments.
Continuous Improvement involves making iterative changes to continually enhance the JIT process. This means being open to new ideas and willing to adapt to changing circumstances.

By regularly evaluating and refining your JIT process, you can ensure it remains responsive, cost-effective, and efficient. This is the essence of lean manufacturing, where every step is optimized for maximum impact.
Maintaining a culture of Continuous Improvement helps you stay ahead of the curve and respond to market conditions and technological advancements. This is crucial for effective JIT implementation and long-term success.
History
Just in time lean management has a rich history that spans several decades. Frederick Taylor and Henry Ford documented their observations on the subject, laying the groundwork for future innovations.
Frederick Taylor and Henry Ford's work was later built upon by Shigeo Shingo and Taiichi Ohno at Toyota in the late 1940s. They applied their enhanced thoughts on the subject, resulting in the development of new methods.
Shigeo Shingo and Taiichi Ohno's work was researched and defined in the mid-20th century. John Krafcik coined the term "Lean" in 1988, marking a significant milestone in the evolution of just in time lean management.
The concepts of Lean were further detailed in two influential books: "The Machine that Changed the World" and "Lean Thinking", both written by James Womack and Daniel Jones.
Frequently Asked Questions
What is JIT vs lean management?
JIT (Just-In-Time) management focuses on timely inventory delivery, while Lean management targets efficiency across all processes to eliminate waste and maximize value
Sources
- https://www.epa.gov/sustainability/lean-thinking-and-methods-jitkanban
- https://leanconstruction.org/lean-topics/just-in-time/
- https://www.6sigma.us/manufacturing/just-in-time-production-system-jit/
- https://en.wikipedia.org/wiki/Lean_manufacturing
- https://nextplus.io/lean-manufacturing/how-to-implement-just-in-time-jit-production-a-beginners-guide/
Featured Images: pexels.com