
Just in time delivery is a method that minimizes inventory holding costs by receiving goods just in time to meet customer demand. This approach requires precise planning and coordination to ensure timely delivery.
Companies like Toyota and Dell have successfully implemented just in time delivery, reducing their inventory levels and improving their supply chain efficiency.
By adopting just in time delivery, businesses can save on storage costs, reduce waste, and improve their overall operational efficiency.
For example, Toyota's just in time delivery system allows the company to produce cars with minimal inventory, reducing the need for storage space and minimizing the risk of inventory obsolescence.
For more insights, see: Just-in-time Stock Control
What Is Just-In-Time Delivery?
Just-in-time delivery is a system that offers many benefits for eCommerce businesses. It allows you to control inventory levels in your fulfillment centers, reducing storage costs and increasing order cycles.
Implementing just-in-time delivery requires careful planning and execution. This involves using demand forecasting to estimate inventory requirements and cutting down production to minimum inventory levels based on demand forecast.
For another approach, see: In a Just in Time Inventory System Suppliers
To streamline the process, you can use data analytics, software integration, and automation to optimize warehouse receiving and order fulfillment. This enables faster fulfillment and reduces storage time.
Here are the key steps to implement just-in-time delivery in eCommerce:
- Use demand forecasting to estimate inventory requirements.
- Cut down production to minimum inventory levels based on demand forecast.
- Reduce the time in storage by optimising warehouse receiving and order fulfilment.
- Implement an efficient warehouse management process to enable faster fulfilment.
- Alter the production schedule based on estimated demand and inventory levels in storage.
- Use efficient logistics management to ensure less storage time and a faster delivery rate.
What Is Ecommerce?
Ecommerce is a type of business that sells products or services online. This means that customers can browse and purchase items from a website or mobile app. In an ecommerce business, inventory levels need to be controlled to ensure that products are available when customers want to buy them.
To manage inventory effectively, ecommerce businesses use various strategies such as demand forecasting and efficient logistics management. For example, using data analytics and software integration can help streamline the supply chain process.
Implementing just-in-time delivery in ecommerce can offer many benefits, including reduced storage costs and improved inventory management. By controlling inventory levels, ecommerce businesses can carry out more order cycles using less space.
For more insights, see: Last Mile Delivery Business Model
Here are the key steps to implement just-in-time delivery in ecommerce:
- Use demand forecasting to estimate inventory requirements.
- Cut down production to minimum inventory levels based on demand forecast.
- Reduce the time in storage by optimising warehouse receiving and order fulfilment.
- Implement an efficient warehouse management process to enable faster fulfilment.
- Alter the production schedule based on estimated demand and inventory levels in storage.
- Use efficient logistics management to ensure less storage time and a faster delivery rate.
What Is?
Just-in-time delivery is a philosophy that fills market demand quickly by making goods only when orders come in. This approach helps cut down costs from the production process with careful planning.
The goal of just-in-time delivery is to reduce waste and inefficiencies in the production process. Companies use this strategy to create the highest-quality product while cutting down costs.
Just-in-time inventory systems flag low stock levels, so managers can order more goods to keep stock at optimal levels. This approach ensures that stock-outs don't happen or that excess inventory doesn't result in waste.
Companies employ this inventory strategy to increase efficiency and decrease waste by receiving goods only as they need them for the production process. This method requires producers to forecast demand accurately.
Just-in-time inventory systems keep stock at optimal levels, ensuring that stock-outs don't happen or that excess inventory would result in waste.
If this caught your attention, see: Best Home Time Trucking Companies
Advantages
Just in time delivery is a lean management system that minimizes resource utilization, creating room for efficiency and cost reduction.
By focusing on customer demand, retailers can manage existing resources and inventory to fulfill orders on the same day or immediately.
This approach helps reduce costs by optimizing internal fleet or outsourcing to external fleets, and intelligent handoff systems ensure timely delivery.
Just in time delivery can be offered at checkout without harming profitability, as long as the retailer has the availability to meet a two-hour timeframe.
However, making blanket promises of short delivery windows can lead to scrambling and paying premiums to delivery providers.
In the just in time delivery system, retailers only procure goods based on demand, reducing the risk of wasted inventory and saving money on unused or expired products.
By cutting down on inventory, retailers can also save on warehousing and inventory management costs, including rent, maintenance, staffing, insurance, and more.
On a similar theme: Order and Delivery Management System
Done right, just in time delivery reduces costs across the entire supply chain by utilizing the origin point of inventory in an intelligent way.
The process of forwarding an order request to a store associate and picking inventory should take no more than five to ten minutes to keep the supply chain moving efficiently.
This synchronization is critical in reducing costs by upping efficiency and keeping the supply chain moving without requiring much storage space.
Just in time inventory management methods may differ depending on the type of location, such as using robotics in dark stores or automating processes in warehouses.
Ongoing communication between all parts of the process is essential for continuous improvement and lowering costs by maintaining a constant flow of materials and orders.
Worth a look: Packing List for Moving Out for the First Time
Key Features and Pros and Cons
Just-in-time delivery is a lean management system that focuses on minimizing resource utilization. It's a philosophy that aims to eliminate waste and improve efficiency.
The key characteristics of just-in-time inventory management include elimination of waste, continuous performance evaluation, continuous improvement, customer-driven strategies, and a finely-tuned work environment. This means that every resource, including human resources, is used to its maximum potential.
By adopting a just-in-time delivery system, businesses can reduce costs, improve efficiency, and enhance customer satisfaction. However, there are also potential drawbacks to consider, such as disruptions in the supply chain due to unexpected events or breakdowns.
Here are some of the main pros and cons of just-in-time delivery:
Overall, just-in-time delivery can be a powerful tool for businesses looking to improve their operations and reduce costs. However, it requires careful planning and management to avoid potential pitfalls.
Optimize Storage
Optimizing storage is a crucial aspect of just-in-time delivery. The goal is to minimize inventory storage time.
Goods are brought into the warehouse based on demand and expected delivery lead time, reducing the need for long-term storage. This approach allows for minimal storage space to be used for multiple product rotations.

Keeping inventory levels balanced to the minimum required level is essential in just-in-time inventory management. This helps to avoid unnecessary storage costs.
The just-in-time delivery model relies on products arriving at precise times to avoid unexpected waiting and additional storage costs. Finding the balance in the supply chain is vital to keep just-in-time delivery working properly.
Minimal storage space can be advantageous for omnichannel retail as it allows them to supply products to multiple channels from the same storage space.
Offers Flexibility
The just-in-time inventory system offers flexibility in several ways. It reduces your dependence on stored inventory, which means you can adapt to changes in market trends.
This flexibility allows you to shift various aspects of the supply chain, such as manufacturing or distribution, to accommodate new target markets. For example, in the fashion industry, just-in-time delivery gives you the ability to quickly respond to changing trends.
Retailers, restaurants, and other businesses that use just-in-time inventory management can benefit from this flexibility. They can alter their business practices without being tied to large inventories.
Here are some examples of industries that have benefited from just-in-time inventory management:
- Retailers
- Restaurants
- On-demand publishing
- Tech manufacturing
- Automobile manufacturing
By reducing inventory levels, just-in-time inventory management can help you avoid the costs associated with storing and managing large amounts of inventory. This can be a major competitive advantage in industries where trends change quickly.
Pros and Cons
The just-in-time delivery system has both advantages and disadvantages.
One of the main benefits of JIT delivery is that it eliminates waste, including raw materials, time, and human resources. This approach focuses on minimizing the utilization of resources, creating room for efficiency and cost reduction.
The JIT delivery system also allows for continuous performance evaluation, analyzing everyday tasks based on productivity, and continuous improvement, striving for quality and finding ways to improve efficiency.
Companies that adopt JIT delivery spend less money on raw materials because they buy just enough resources to make the ordered products and no more. This reduces costs by minimizing warehouse needs.
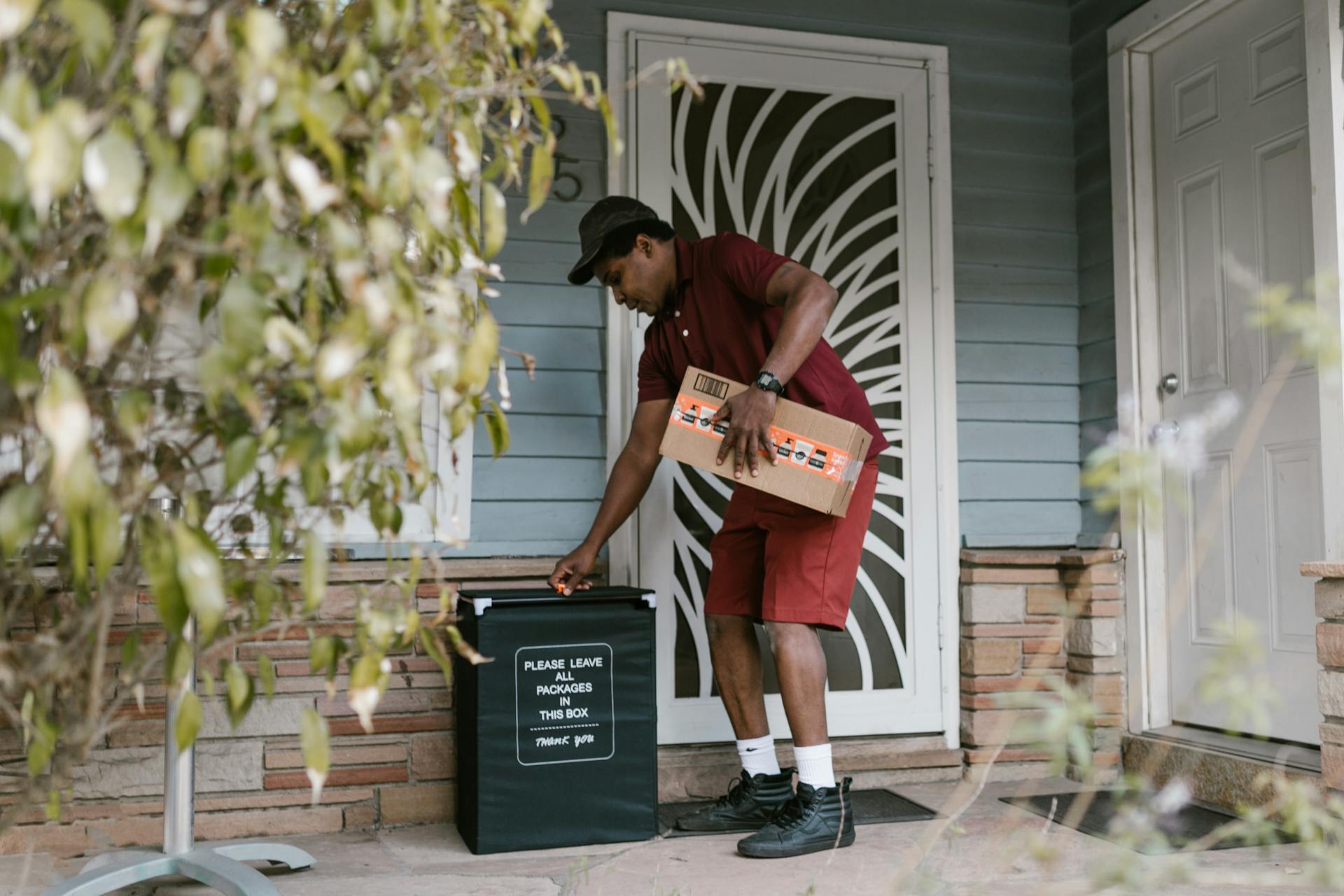
However, the disadvantages of JIT inventory systems involve potential disruptions in the supply chain. If a raw-materials supplier has a breakdown and cannot deliver the goods promptly, this could conceivably stall the entire production line.
A sudden unexpected order for goods may delay the delivery of finished products to end clients. The JIT delivery model relies heavily on the supplier's ability to deliver materials on time.
Here are the key pros and cons of JIT delivery:
Example and Implementation
Just in time delivery is a complex system that requires precise planning and execution. The goal is to reduce the time products spend in storage, which can be achieved by accurately forecasting demand and estimating the time frames for each stage of the supply chain.
To understand how just in time delivery works, let's consider an example from eCommerce. In this example, the demand forecast for 100 products is 20 days, and the estimated time frames for each stage are: 1 day for raw material procurement, 1 day for material processing, 2 days for product manufacturing, 3 days for distribution to a fulfilment centre, 1 day for processing at the warehouse, 2 days for order fulfilment, and 1 day for last mile delivery.
Here are the estimated time frames for each stage of the just in time supply chain:
- Raw Material Procurement: 1 Day
- Material Processing: 1 Day
- Product Manufacturing: 2 Days
- Distribution to Fulfilment Centre: 3 Days
- Processing at Warehouse: 1 Day
- Order Fulfilment: 2 Days
- Last Mile Delivery: 1 Day
Example of eCommerce
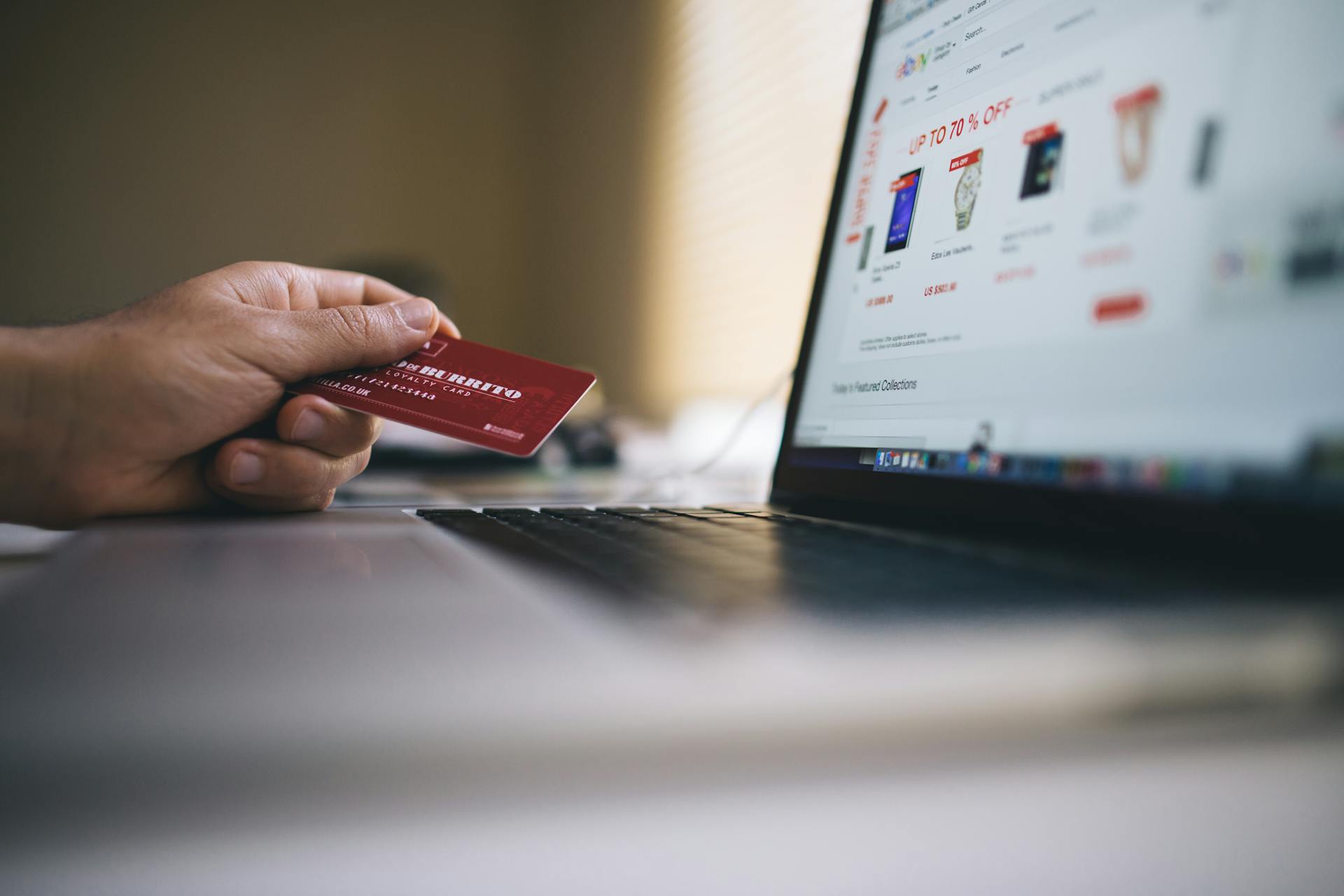
In eCommerce, just in time delivery relies heavily on demand forecasting. Let's say you've estimated a demand for 100 products in 20 days.
The just in time delivery system involves multiple stages, each with its own time frame. Here are some of the key stages and their estimated time frames: Raw Material Procurement: 1 DayMaterial Processing: 1 DayProduct Manufacturing: 2 DaysDistribution to Fulfilment Centre: 3 Days Processing at Warehouse: 1 DayOrder Fulfilment: 2 DaysLast Mile Delivery: 1 Day
You need 11 days to complete the order cycle from just in time manufacturing to order fulfilment. The goal of the JIT delivery model is to reduce the time in storage.
For your interest: Last Day to Order for Christmas Delivery
Example of
The just-in-time delivery model is a game-changer in the world of e-commerce, and it's all about reducing storage time. In e-commerce, the just-in-time delivery system heavily relies on demand forecasting, which helps businesses predict customer demand and plan accordingly.
To give you a better idea, let's take a look at Toyota's approach to just-in-time inventory management. Toyota orders parts only when it receives new car orders, minimizing inventory levels and reducing carrying costs. This approach has been perfected over the years and is now a hallmark of the company's success.
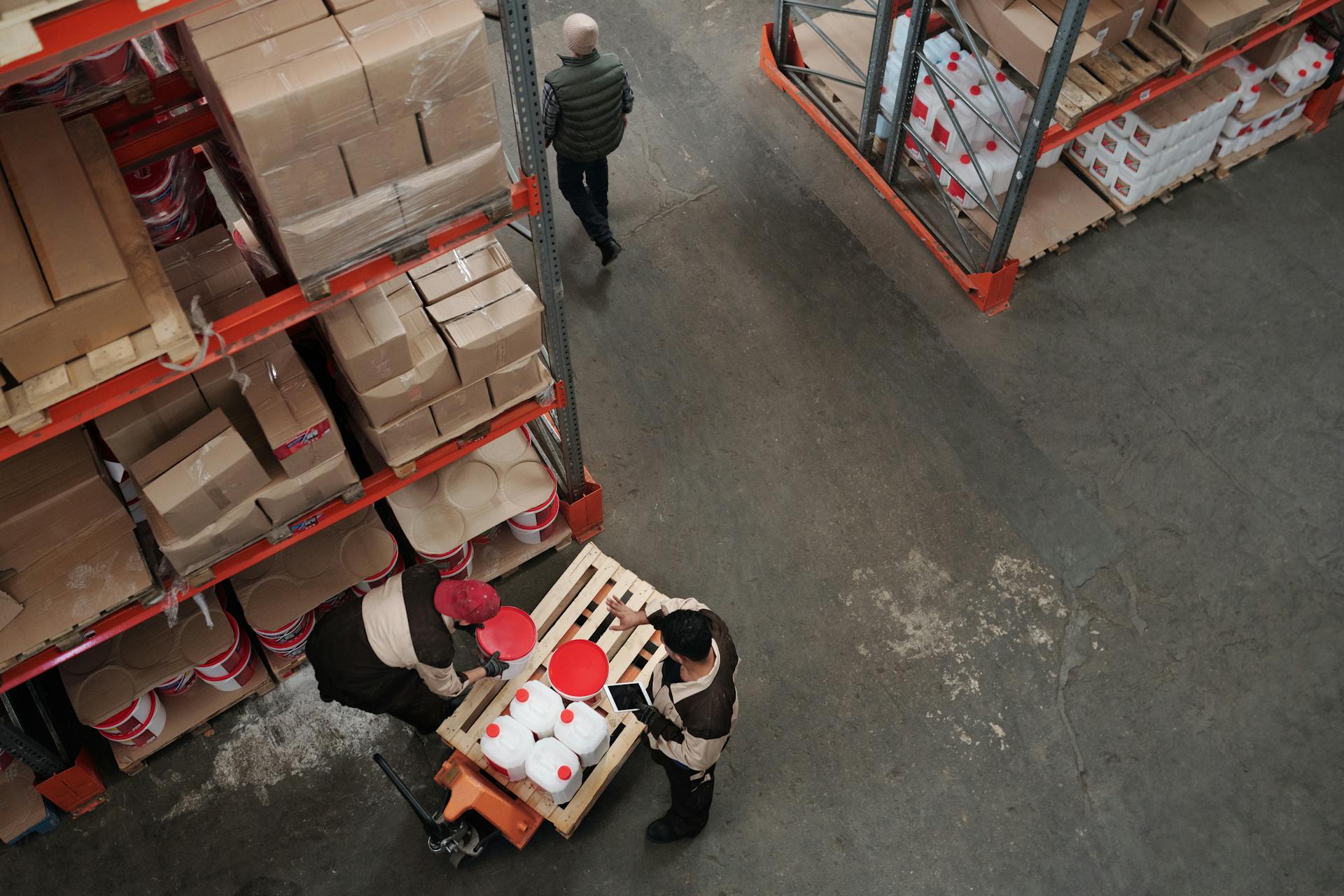
Here's a breakdown of the time frames involved in the just-in-time supply chain:
- Raw Material Procurement: 1 Day
- Material Processing: 1 Day
- Product Manufacturing: 2 Days
- Distribution to Fulfilment Centre: 3 Days
- Processing at Warehouse: 1 Day
- Order Fulfilment: 2 Days
- Last Mile Delivery: 1 Day
These time frames add up to 11 days, which is the total time needed to complete the order cycle from just-in-time manufacturing to order fulfillment. The goal of the JIT delivery model is to reduce the time in storage, making it an attractive option for businesses looking to streamline their operations.
Just-in-time inventory systems can be seen in some of the world's biggest product-led businesses, including Toyota, Apple, and McDonald's. These companies have benefited from the just-in-time inventory system, which helps them adapt quickly to changes in trends or demands.
Challenges and Considerations
Implementing just in time delivery can be challenging, especially when it comes to managing supply chain logistics. Taiichi Ohno's kanban system, which measures lead and cycle times, can help identify problem areas and prevent overcapacity.
Measuring lead and cycle times is crucial to avoiding overcapacity and identifying inefficiencies in the production process. Kanban highlights these areas, making it easier to optimize the system.
Additional reading: Order Fulfillment Cycle Time
Supply chain management is critical for just in time delivery, and finding the balance is vital to keeping the system working properly. Keeping the supply chain moving without holdups is crucial, but with just in time delivery, it's even more pivotal.
Managing inventory costs, storage costs, and raw materials is essential to avoid holdups and excess inventory. This is especially true for just in time delivery, where products need to arrive at precise times to avoid unexpected waiting.
History and Management
The concept of just-in-time delivery has its roots in Japan's post-war economic struggles. Isolated Japan needed to get its economy going ASAP, so pioneers developed ways to lean up their inventory management completely, building smaller factories with only the raw material inventory needed for existing orders.
This approach allowed businesses to be more flexible and reduced capital tied up in inventory. They also adopted best practices from the US, including Ford's moving assembly line. The results spoke for themselves, and people paid attention when Japanese manufacturing started to become competitive in the 1970s.
Companies across the globe have adopted just-in-time inventory management to replicate this success, with investment in technology allowing countries like the US, the UK, and Japan to remain relevant in worldwide manufacturing.
For more insights, see: Just in Time and Lean Operations
The History of
Isolated Japan needed to get its economy going ASAP, so they favored large-scale mass production.
In the 1970s, Japanese manufacturing became competitive, and companies across the globe started to take notice.
Japanese pioneers developed ways to lean up their inventory management completely, building smaller factories that only kept the raw material inventory needed for existing orders.
Less capital tied up with carrying inventory allowed these businesses to be more flexible.
They also adopted best practices from the US, including Ford's moving assembly line.
Fast-forward to 2022, Japan is in the top six countries for manufacturing competitiveness and is projected to stay there in 2023.
Investment in technology has allowed countries like the US, the UK, and Japan to remain relevant in worldwide manufacturing.
Advanced machinery and lean inventory software modernized JIT inventory management, keeping it competitive.
Toyota Motor Corporation reported over $23 billion in net profit in 2021, attributing its success to its commitment to just-in-time manufacturing.
Check this out: Us Postal Service Tracking Delivery Confirmation
Management Guide
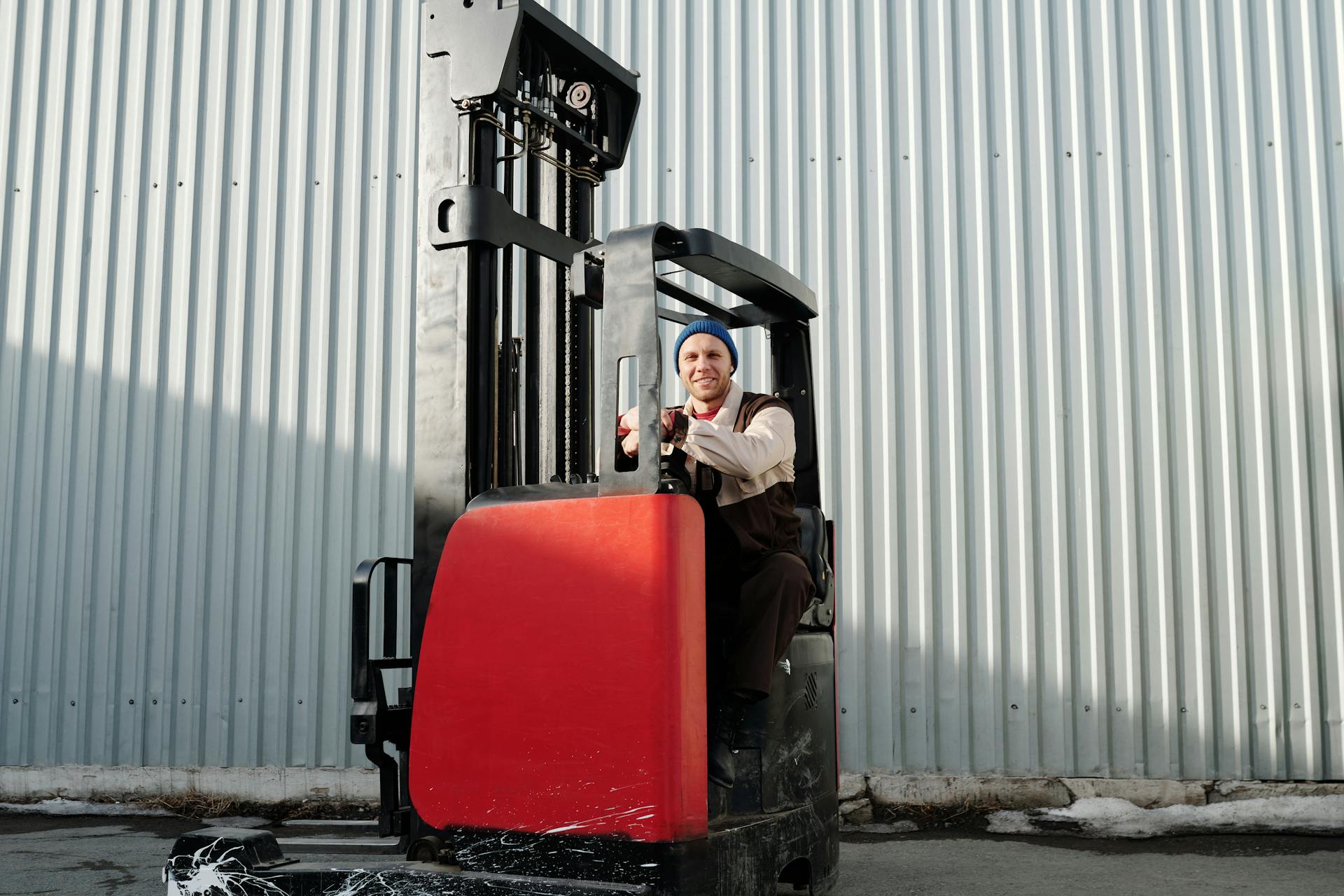
Effective inventory management is a crucial aspect of any business. It's essential to understand the different types of inventory, such as raw material inventory, work-in-process inventory, and finished goods inventory.
Inventory management methods can vary, but some popular ones include ABC inventory, batch tracking, and just-in-time inventory. ABC inventory is a method where items are categorized based on their value and priority.
Inventory control is also vital, and it includes techniques like multilocation inventory management, inventory planning, and safety stock formula. The safety stock formula helps businesses determine the right amount of inventory to hold.
Stock replenishment is another critical aspect of inventory management. It involves restocking inventory when it falls below a certain level, known as the reorder point. The reorder point formula can help businesses determine the optimal time to restock.
Understanding stock keeping units (SKUs) is also essential. SKUs can be generated using a SKU generator, and it's a good idea to rationalize SKUs to simplify inventory management.
Inventory analysis is a regular process that helps businesses evaluate their inventory performance. It includes metrics like inventory turnover ratio, inventory valuation methods, and days inventory outstanding.
Readers also liked: Order to Delivery Process
Management Cost Reduction
Just in time inventory management can significantly reduce management costs. The process involves synchronizing the picking of inventory with the collection process, which helps up efficiency and reduces costs.
The key to just in time delivery is timing, with orders being directed to a location right before the delivery vehicle arrives. This process should take around 5 to 10 minutes to complete.
In a just in time delivery system, you only procure goods based on demand, which means you don't have to worry about wasting inventory. This approach also helps you save money on unused or expired inventory.
Just in time delivery can also help you cut down on warehousing and inventory management costs, such as rent, maintenance, staffing, and insurance. By using the same space to fulfill more orders, you can save a significant amount of money.
In some locations, like dark stores, the supply chain hand-off may not be done by humans, but by robots that perform both the picking and the handing over of goods to the delivery vehicle.
Special Considerations and Risks
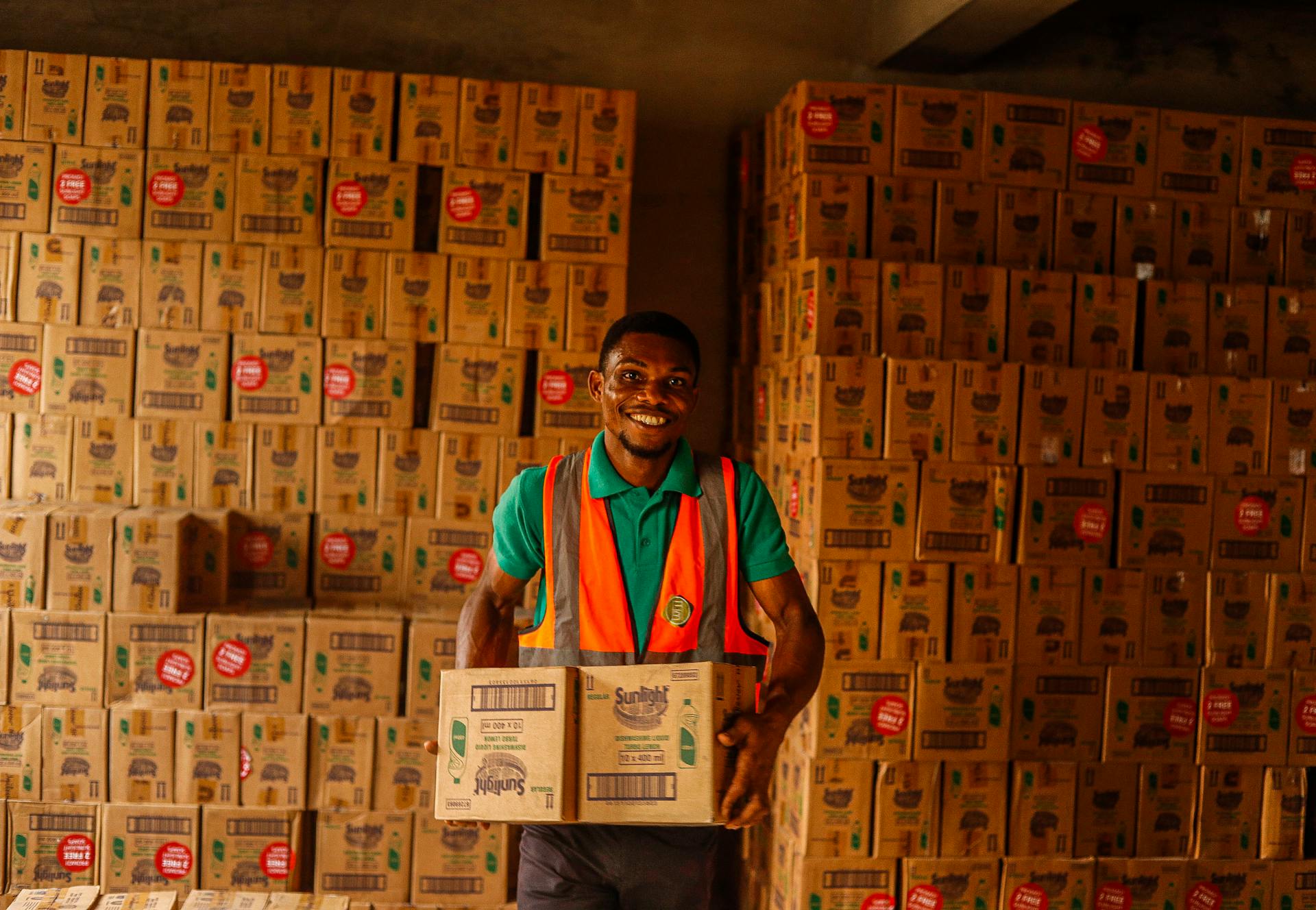
Just-in-time manufacturing can be a double-edged sword, offering both efficiency and cost savings, but also risking disruption in the event of a supply or demand shock.
Taiichi Ohno, an industrial engineer at Toyota, developed kanban, a scheduling system used in conjunction with lean manufacturing and JIT, to improve manufacturing efficiency.
A chief benefit of a JIT system is that it minimizes the need for inventory storage, but this can bring everything to a halt if there's a supply or demand shock, as seen during the 2020 economic crisis when ventilators and surgical masks experienced disruption.
For another approach, see: Just in Time Manufacturing
Is Manufacturing Risky?
Manufacturing can be a high-risk endeavor, especially when it comes to supply chain disruptions. A JIT system can bring everything to a halt if there's a supply or demand shock.
One key example is the 2020 economic crisis, where ventilators and surgical masks experienced disruptions due to delayed inputs from overseas.
Inefficient inventory management can lead to costly stockouts and overstocking, which can be devastating for businesses.
A JIT system minimizes the need for inventory storage, but this also means companies are more exposed to supply chain risks.
This was evident during the 2020 crisis, where companies couldn't meet the surge in demand due to delayed inputs from overseas.
For more insights, see: Walmart Delivery Order Delayed
Special Considerations
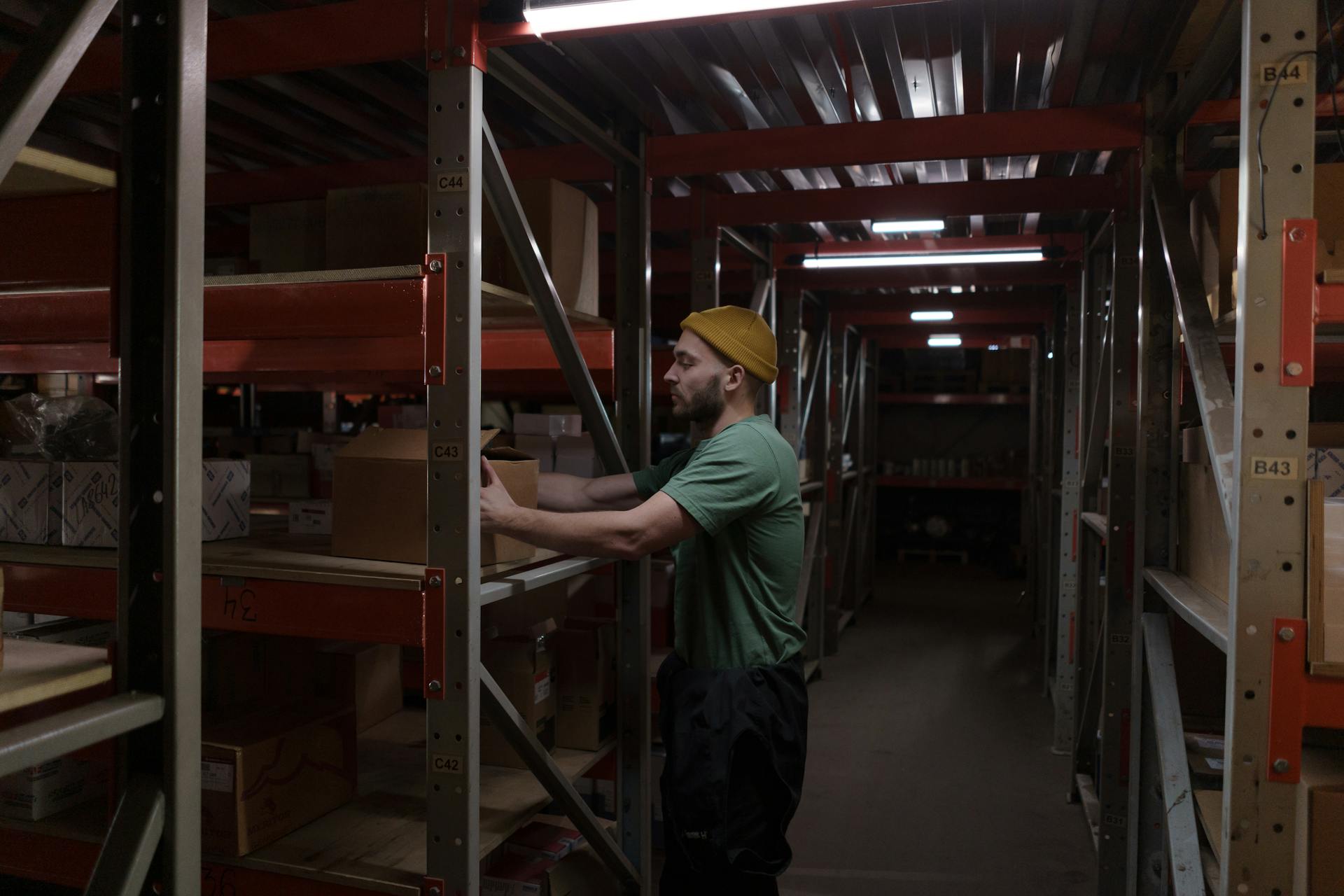
Kanban, a Japanese scheduling system, is often used in conjunction with lean manufacturing and JIT. Taiichi Ohno, an industrial engineer at Toyota, developed kanban to improve manufacturing efficiency.
Kanban measures lead and cycle times across the production process to identify problem areas. This helps to avoid overcapacity by setting upper limits for work-in-process inventory.
The kanban system is designed to highlight problem areas, which is essential for identifying and addressing potential issues before they become major problems.
The Bottom Line
The JIT inventory system is a management strategy that minimizes inventory and increases efficiency. It's popular with small businesses and major corporations alike because it enhances cash flow and reduces the capital needed to run the business.
A disruption in the supply chain can cause the system to fail, resulting in delayed deliveries.
Featured Images: pexels.com