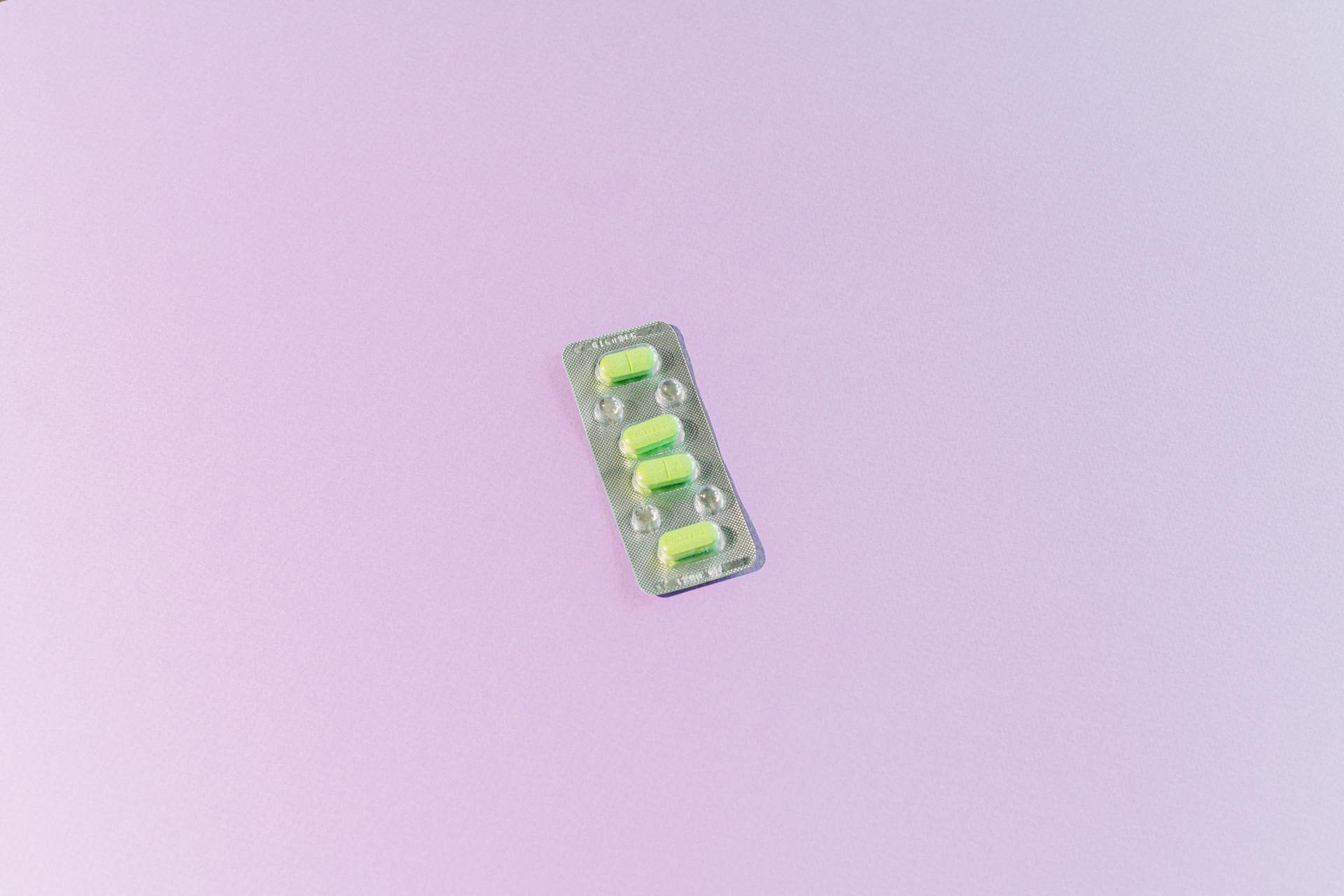
Blister pack sealers are a crucial investment for any business that uses these types of packaging. They ensure your products are securely sealed and ready for distribution.
There are various types of blister pack sealers available, ranging from manual to automatic machines. Manual machines are ideal for small-scale production, while automatic machines are better suited for high-volume production.
The choice of blisters pack sealer depends on your production needs and budget. If you're just starting out, a manual machine is a cost-effective option.
Blister pack sealers can be powered by electricity or air, with electric machines being more common. Electric machines are generally easier to use and maintain.
See what others are reading: Automatic Strapping Machine
Types of Sealing
There are several types of blister pack sealing machines, each with its own unique features and benefits.
Cold-Seal Blister Pack Sealing Machines are great for packaging heat-sensitive products, as they don't require heat to seal the package. They work by using adhesive that reacts to pressure to create a seal.
Check this out: Blister Card Sealing Machine
High-Pressure Hydroforming Blister Pack Sealing Machines are extremely versatile and can be used to package a wide range of items, from pills to food items to electronics parts. They're also very efficient and produce strong and exact blister packs at quick speeds.
Rotary Blister Pack Sealing Machines work fast and are quite efficient, making them great for high-volume productions. However, their speed does drop when sealing varying product sizes.
Forms-Fill-Seal Blister Pack Sealing Machines are automated and great for packaging individual servings of items like yogurt or ketchup. They form, fill, and seal the product in one machine.
Here are the main types of blister pack sealing machines:
- Cold-Seal Blister Pack Sealing Machine
- High-Pressure Hydroforming Blister Pack Sealing Machine
- Rotary Blister Pack Sealing Machine
- Forms-Fill-Seal Blister Pack Sealing Machine
Choosing the Right Sealer
Choosing the right blister pack sealer requires careful consideration of several factors. The type of blister sealing machine you need depends on your production volume, packaging requirements, and budget.
To determine the right machine for you, evaluate its features and specifications, including sealing accuracy, temperature control, pressure adjustment, and tooling options. You should also look for advanced features like data logging, digital controls, and automatic emergency shut-off.
Suggestion: Vertical Form Fill and Seal Packaging Machines
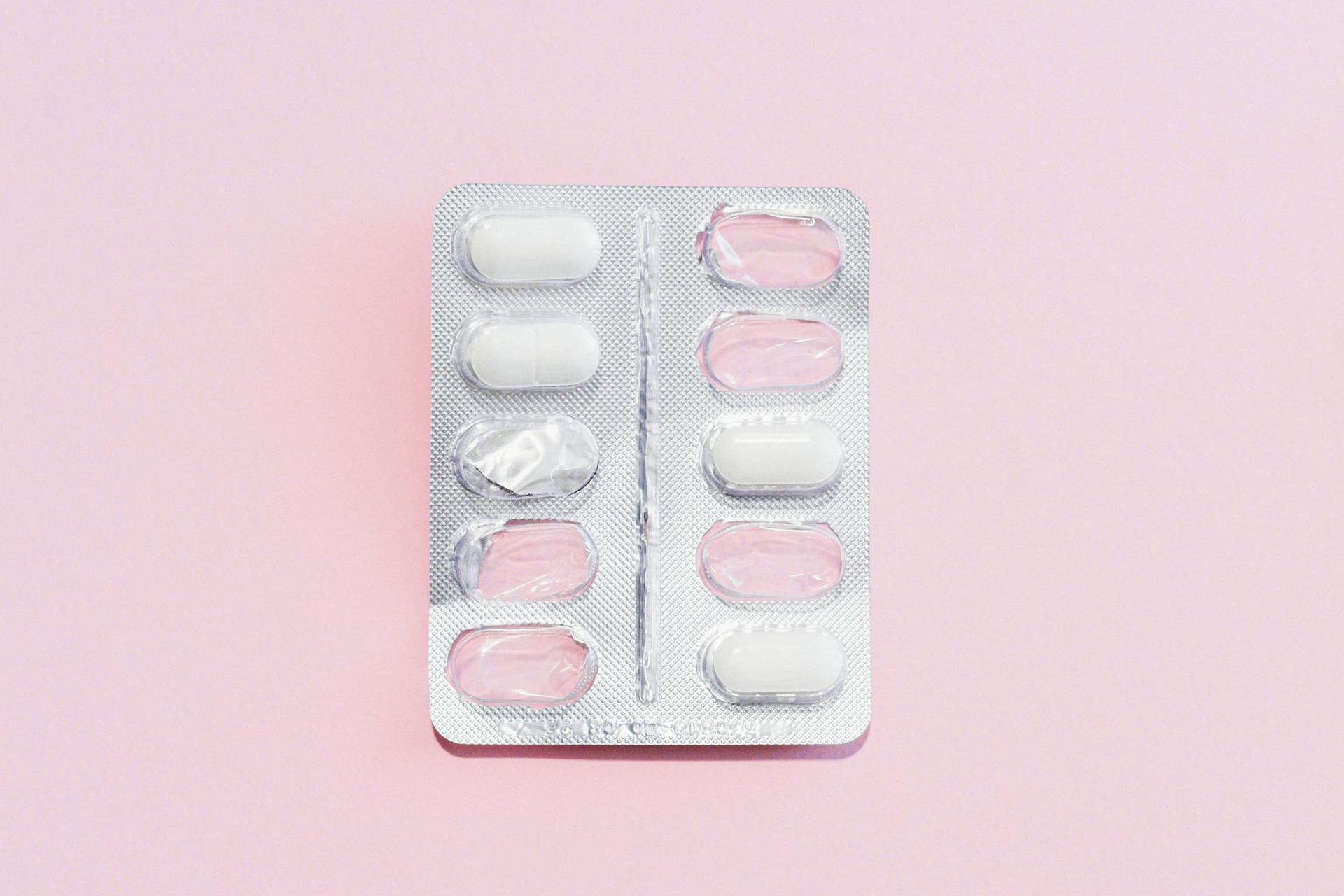
Consider the machine's size and weight in relation to your available production floor space. Ensure that the machine fits within your existing production layout and workflow.
A blister pack sealing machine can be used in various industries, including pharmaceuticals, food, electronics, and cosmetics. Here are some common areas where this machine is used for blister packing:
How to Choose
Choosing the right sealer for your business requires careful consideration of several key factors.
First, you need to determine the type of sealer that matches your specific needs, taking into account production volume, packaging requirements, and budget.
The type of sealer you choose will have a significant impact on your operations. Consider a machine that can handle your expected production volume.
To evaluate features and specifications, look for sealing accuracy, temperature control, pressure adjustment, and tooling options.
Some sealers come with advanced features like data logging, digital controls, and automatic emergency shut-off, which can enhance efficiency and safety.
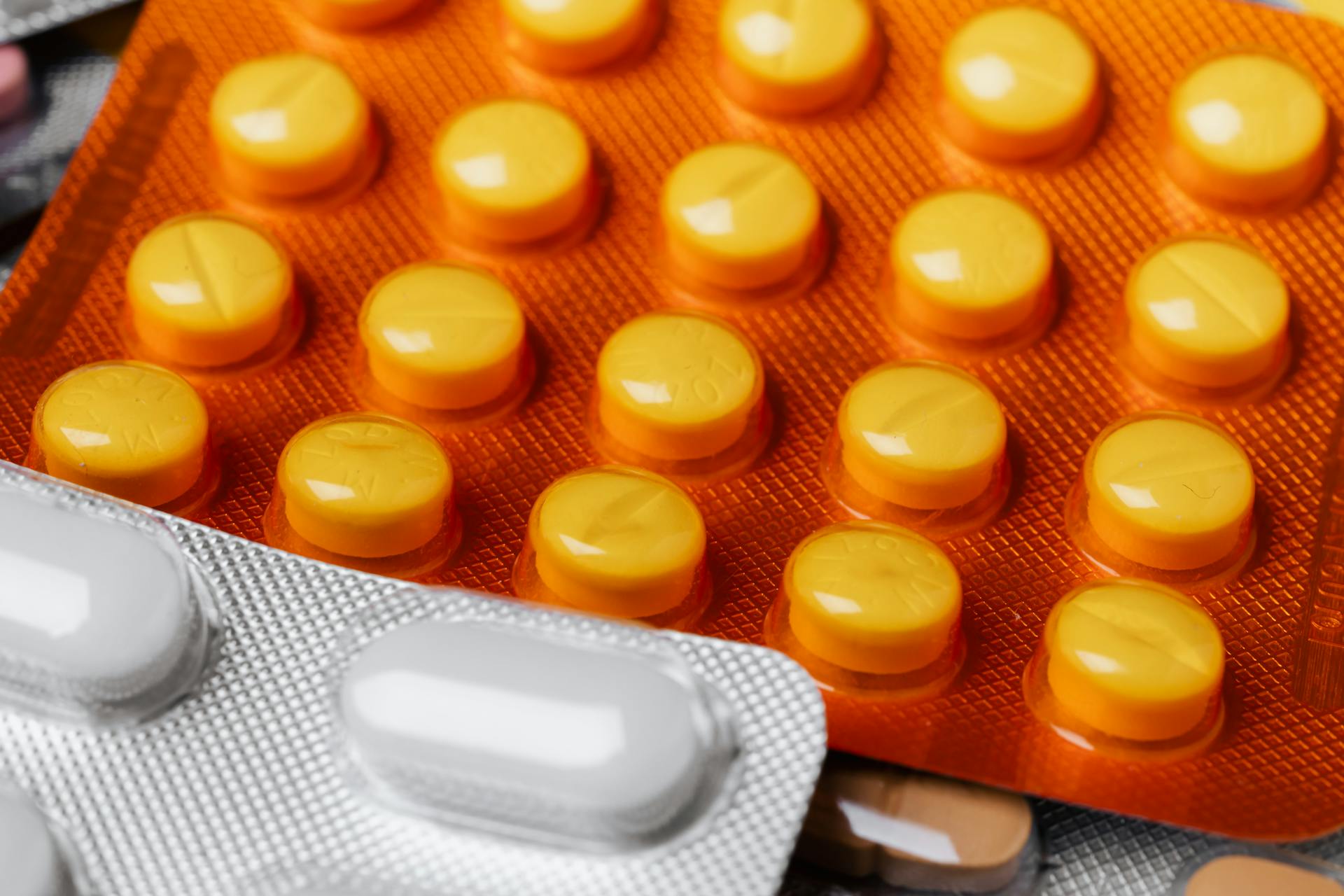
When choosing a sealer, don't forget to consider the space it will occupy on your production floor. Ensure the machine fits within your existing layout and workflow.
Maintenance requirements and support from the manufacturer are also crucial factors to consider. Look for a sealer with easy maintenance and a reliable supplier of spare parts.
Finally, your budget will play a significant role in determining the type of sealer you can afford. Try to find a machine that provides good value for the investment and has a strong resale market.
Here are some key factors to consider when choosing a sealer:
- Blister pack sealing machine type
- Features and specifications
- Floor space
- Maintenance and support
- Budget
#1 Match Materials
Matching materials is crucial when it comes to achieving a strong and reliable blister seal. You'll want to choose materials that are compatible with each other to guarantee seal integrity.
Material selection is a combination of cost and the level of barrier protection needed to ensure product stability and shelf life. Your supplier can advise on the best combination.
Any lidding foil that's compatible with PVC won't be a match with PET. This is a general rule of thumb to keep in mind when selecting materials.
You'll need a speciality coating or PVC layer to ensure a strong bond with the lidding material when working with PCTFE (Aclar).
Check this out: White Foam Packing Material
Scenarios
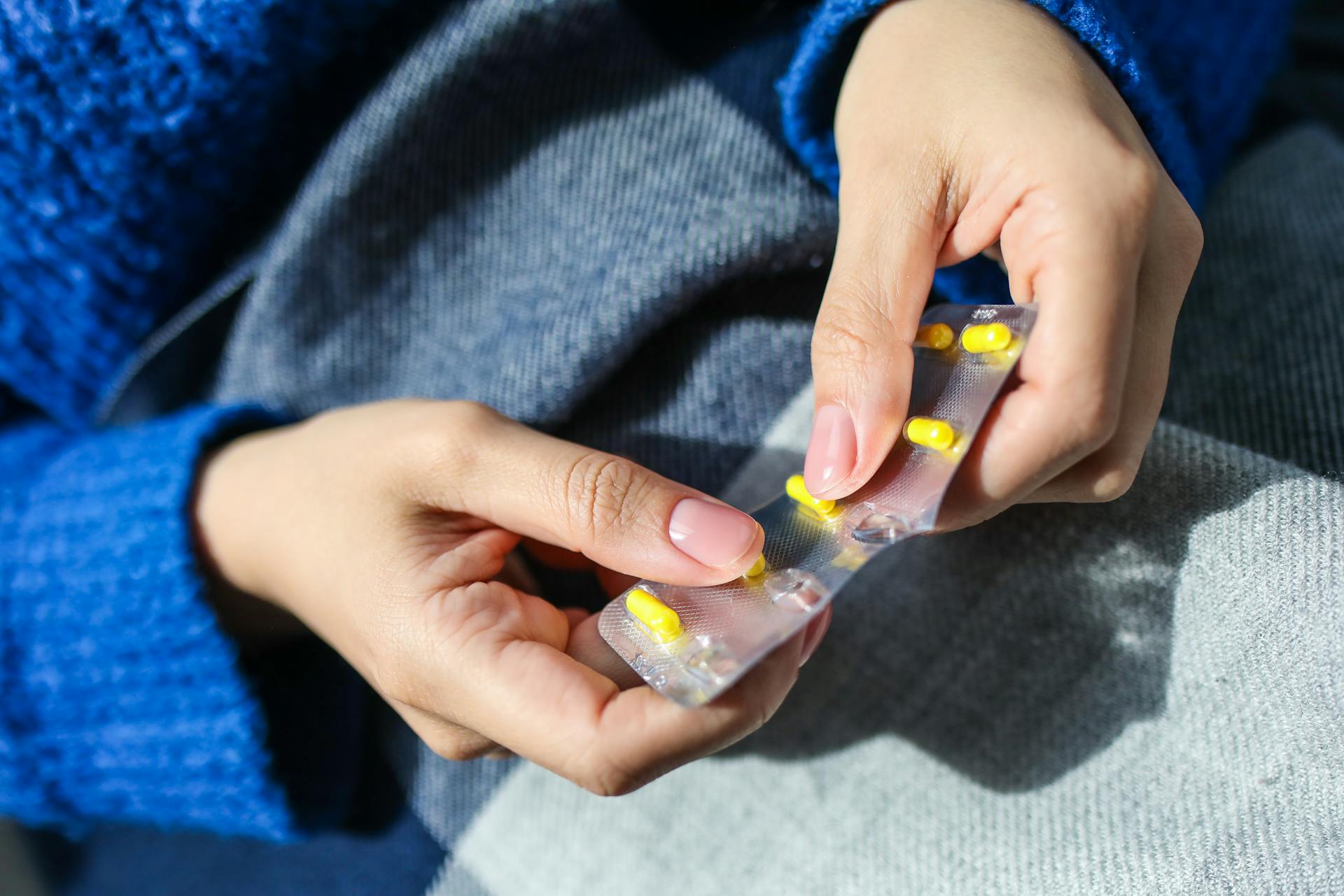
In the pharmaceutical industry, blister pack sealing machines play a crucial role in forming medicine packs that are easy to consume, carry, and protect from damage.
These packs meet the requirements of both patients and doctors, making them a vital component in the industry.
Blister pack sealing machines are also used in the food industry to keep food fresh for a long time and seal in its freshness.
Packs made by this tool are practical and meet the needs of convenient food packaging.
In the electronics industry, blister pack sealing machines are used to securely display and protect gadgets like headphones, remote controls, and smartphone accessories.
Some products that benefit from blister pack sealing include batteries, tools, and electronics, which can be displayed and protected through the unique see-through marketing offered by these packs.
Here are some examples of products that can be packaged using a blister pack sealing machine:
- Medicines
- Food
- Batteries
- Tools
- Electronics
- Headphones
- Remote controls
- Smartphone accessories
Sealer Features and Benefits
A cold-seal blister pack sealing machine uses adhesive to seal the package, requiring little to no heat, making them great for packaging heat-sensitive products.
Recommended read: Vacuum Heat Sealing Machine
Some sealing machines can produce strong and exact blister packs at quick speeds, while others may have slower speeds when sealing varying product sizes.
A rotary machine works by placing the product on the turntable of the machine, which then seals the product while rotating. This is great for high-volume productions.
Here are some key features and benefits of different blisters pack sealing machines:
Features
Compact machine bodies are a common feature among blister packing machines, making them suitable for small spaces.
The DPP-88 blister packing machine has a compact machine body, which makes it ideal for hospital dosage rooms and small pharmacy factories.
Some blister machines, like the DPP-260, have advanced functions that make them suitable for large and medium-sized pharmaceutical companies.
The DPH260H highly intelligent high-speed roller blister packaging machine is equipped with positive pressure forming and rolling heat sealing, resulting in crisp blisters and flat plates.
Blister machines like the DPP-260 and DPH320H II are designed to meet the requirements of the pharmaceutical industry's (GMP) standards.
For another approach, see: Small Blister Pack Machine
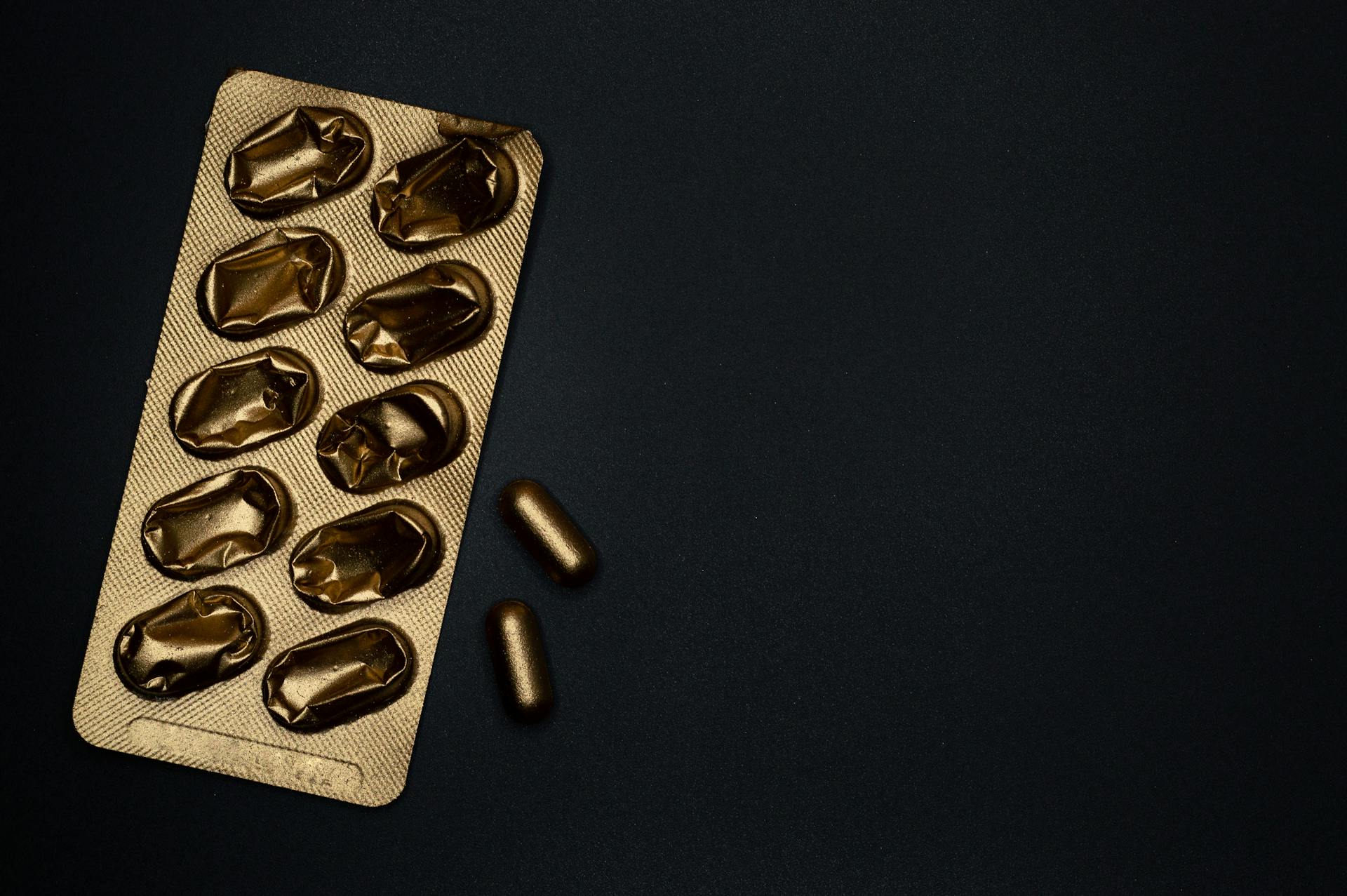
These machines have high production efficiency, making them ideal for large and medium-sized pharmaceutical companies, healthcare products, and the food industry.
The DPP-260 automatic blister packaging machine has variable frequency speed regulation and integrates mechanical, electrical, optical, and pneumatic control technology.
Blister machines like the DPH320H and DPH320H II are used for pharmaceutical packing, food packing, cosmetic packing, medical device packing, and more.
These machines can seal various types of products, including pharmaceuticals (tablets, capsules, ampoules), food, cosmetics, and more.
The DPH320H II is a full servo blister machine that uses the continuous drum sealing principle.
Some blister machines, like the QPB-01, can seal about 5000 times when fully charged.
Recommended read: Blister Packaging Machine Pharmaceutical Industry
DPP-140
The DPP-140 is a versatile blister packaging machine that integrates multiple functions, including PVC feeding, heating and forming, PTP feeding, sealing, batch number printing, creasing line making, and more.
It's designed to handle a wide range of products, from capsules to ampoules, making it a great option for pharmaceutical companies.
The DPP-140 is particularly suitable for packaging medicines such as capsules, tablets, sugar-coated tablets, honey pills, injections, and ampoules.
A unique perspective: Paper Sack Making Machine
Easy to Operate
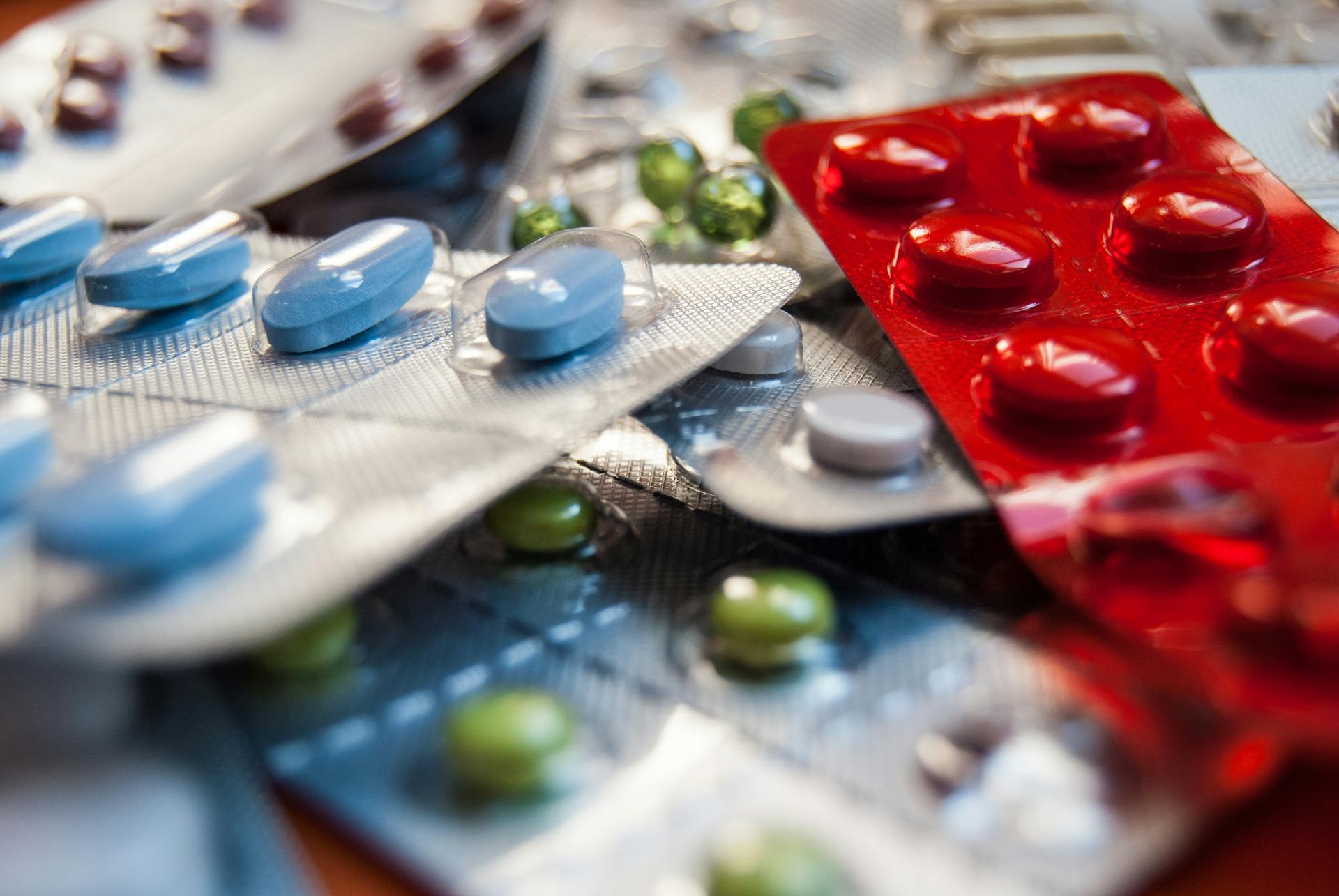
Operating a sealer is a breeze. Just grip the handpiece for a few seconds and release to weld. This simple process makes it easy to use, even for those with limited experience.
The sealer doesn't use consumables like needles, which means you don't have to worry about foreign matter entering the package. This feature also provides an attractive packing appearance.
This design makes it perfect for use in various settings, such as hospitals and pharmacies, where ease of operation is crucial.
Maximise Seal Area
A strong seal is crucial for maintaining the integrity of your blister pack. To achieve this, maximising the seal area is essential.
Designing your packs with a minimum of 5mm between each cavity is a good starting point. This allows for a secure seal and minimises the risk of weak points.
Sealing across a larger area and then cutting off the excess is also a recommended practice. This helps to ensure that the seal is uniform and effective.
Sealer Maintenance and Testing
To achieve a brilliant blister seal, you need to pay attention to sealer maintenance and testing. Anodised aluminium plates will need to be stripped and re-anodised from time to time to maintain sealing performance.
Regular maintenance is crucial, especially when running printed materials, as the build-up of ink can distort the knurl pattern and lead to areas of weakness across the seal and micro-channeling. This can be prevented by re-anodising the plates as needed.
Performing pack integrity testing is also essential to verify the strength of the seal and check for capillaries in the seal. The traditional blue dye test is widely adopted, but it's messy, subjective, and wasteful, making camera-based integrity testing a more efficient option.
Specification and Maintenance
Proper maintenance is essential to ensure the longevity and effectiveness of your sealer. Regular checks and maintenance can help prevent costly repairs and downtime.
Anodised aluminium plates will need to be stripped and re-anodised from time to time to maintain sealing performance. This is particularly true for blister packaging machines running printed materials, as the build-up of ink can distort the knurl pattern and prevent the upper and lower sealing tools from interlocking properly.
Regular cleaning of the sealer's components is also crucial to prevent the buildup of debris and contaminants. This includes the sealing plates, as well as other moving parts.
The build-up of ink on blister packaging machines can distort the knurl pattern, leading to areas of weakness across the seal and micro-channeling. This can compromise the integrity of the seal and affect the overall performance of the sealer.
By following a regular maintenance schedule, you can help ensure that your sealer continues to run smoothly and efficiently. This includes tasks such as cleaning and inspecting the sealing plates, as well as checking for any signs of wear or damage.
Integrity Testing
Integrity testing is a crucial step in ensuring the quality of your seals. It verifies the strength of the seal, checks for capillaries in the seal, and looks for defects in the material caused by the packaging process.
Pack integrity testing involves various methods, including destructive and non-destructive tests. These tests vary in sensitivity, technology, and cost.
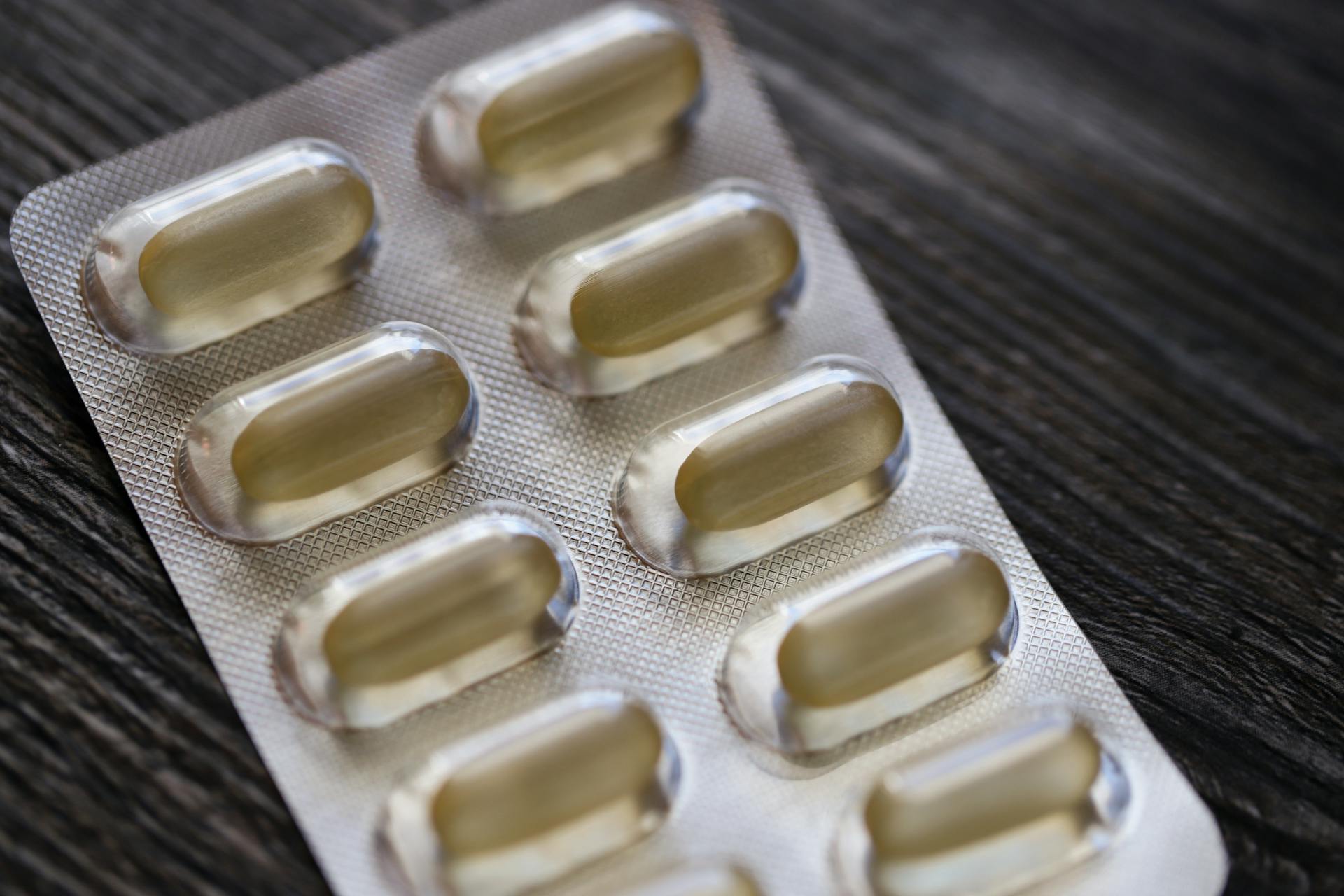
The blue dye test is the most widely adopted method in the pharmaceutical industry due to its low cost and ease of implementation. However, it's messy, subjective, and wasteful.
Camera-based integrity testing offers increased efficiencies by utilizing non-destructive techniques as part of the process. This method is more technologically advanced and efficient than traditional methods.
Market and Purchase Information
The blister pack sealer market is growing rapidly, with a projected CAGR of 10.75% from 2023 to 2030, reaching USD 568.91 million.
This growth is driven by increasing demand for efficient packaging solutions across various sectors, particularly in the pharmaceuticals and consumer goods industries.
The market size grew from USD 278.23 million in 2023 to USD 307.01 million in 2024.
Businesses are adopting these machines to enhance productivity and reduce operational costs, making them a valuable investment for companies looking to stay competitive.
Intriguing read: Ampoules Blister Packaging Market
Market Dynamics
The blister pack sealing machine market is growing rapidly, with a projected CAGR of 10.75% expected to reach USD 568.91 million by 2030. This growth is driven by increasing demand for efficient packaging solutions across various sectors.
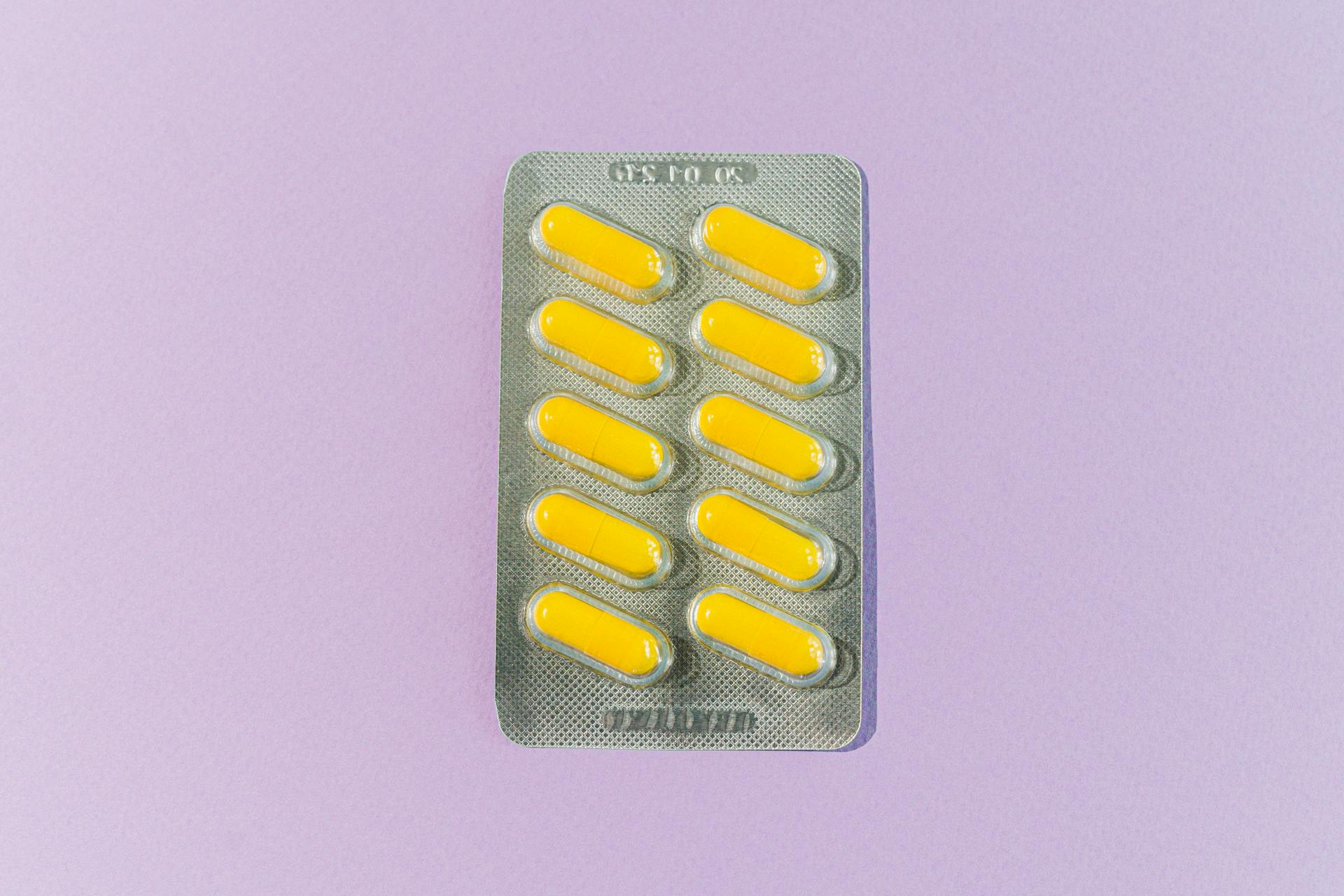
The market has already shown significant growth, from USD 278.23 million in 2023 to USD 307.01 million in 2024. This is a notable increase in just one year.
The surge in e-commerce has created a huge demand for durable, protective packaging in industries such as pharmaceuticals and consumer goods. This has led to a significant boost in the adoption of blister pack sealing machines.
Automation and the integration of advanced technologies in packaging processes are also contributing to market expansion. Businesses are seeking to enhance productivity and reduce operational costs by investing in these machines.
The Asia-Pacific region is poised for growth, particularly in countries like China, which is witnessing rapid industrialization and an expanding manufacturing base. This growth is expected to drive the demand for blister pack sealing machines in the region.
Consumer preferences are also evolving, with a greater emphasis on convenience and safety in product packaging. As a result, key players in the blister pack sealing machine market are investing in research and development to meet these changing consumer behaviors and maintain competitive advantage.
Where to Purchase
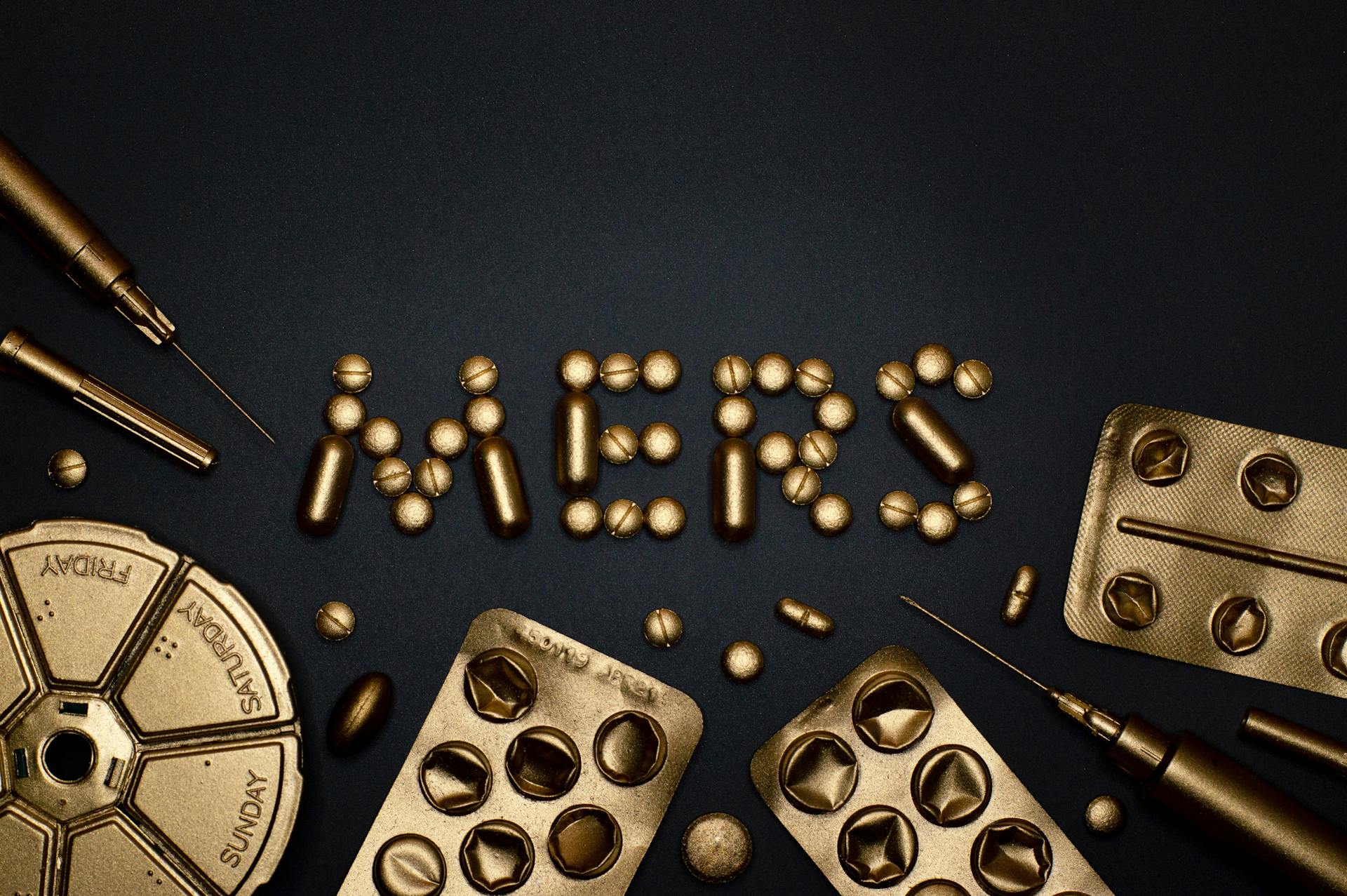
If you're in the market for a blister packaging machine, consider contacting 3KRF, a division of MARKPERI International, Inc.
They have decades of experience manufacturing heat sealing technology, including radio-frequency sealing equipment and HF welding machines for packaging.
Their reputation in the fields of RF welding machines and HF welding machines is unmatched.
They offer both brand-new, state-of-the-art custom-designed heat-sealing machines and high-quality used heat-sealing equipment.
Their used heat-sealing equipment is highly effective at generating superior packaging seals at a lower cost.
Frequently Asked Questions
How to seal a blister pack?
To seal a blister pack, place the blister into a sealing machine's specialized jig, add the product and card, and apply pressure with a hot metal plate. This process seals the blister to the card, creating a secure and tamper-evident package.
What adhesive is used in blister packaging?
Polyurethane adhesives are commonly used in blister packaging due to their temperature resistance, strong adhesion, and flexibility. They provide a reliable bond for blister packs, making them ideal for medical applications.
What is the difference between a hot seal and a cold seal for a blister pack?
Cold seal packaging is up to 10 times faster than hot seal methods, reducing production time and workplace risks. This speed and safety advantage makes cold seal a popular choice for high-volume blister pack production.
Sources
- https://www.ipharmachine.com/blister-packaging-machine
- https://www.alibaba.com/showroom/blister-pack-sealing-machine.html
- https://blog.sepha.com/8-top-tips-for-achieving-a-brilliant-blister-seal
- https://asahi-packaging.com/products/qpb-01/
- https://markperi.com/sealing-technologies/captured-blister-sealing-machines/
Featured Images: pexels.com