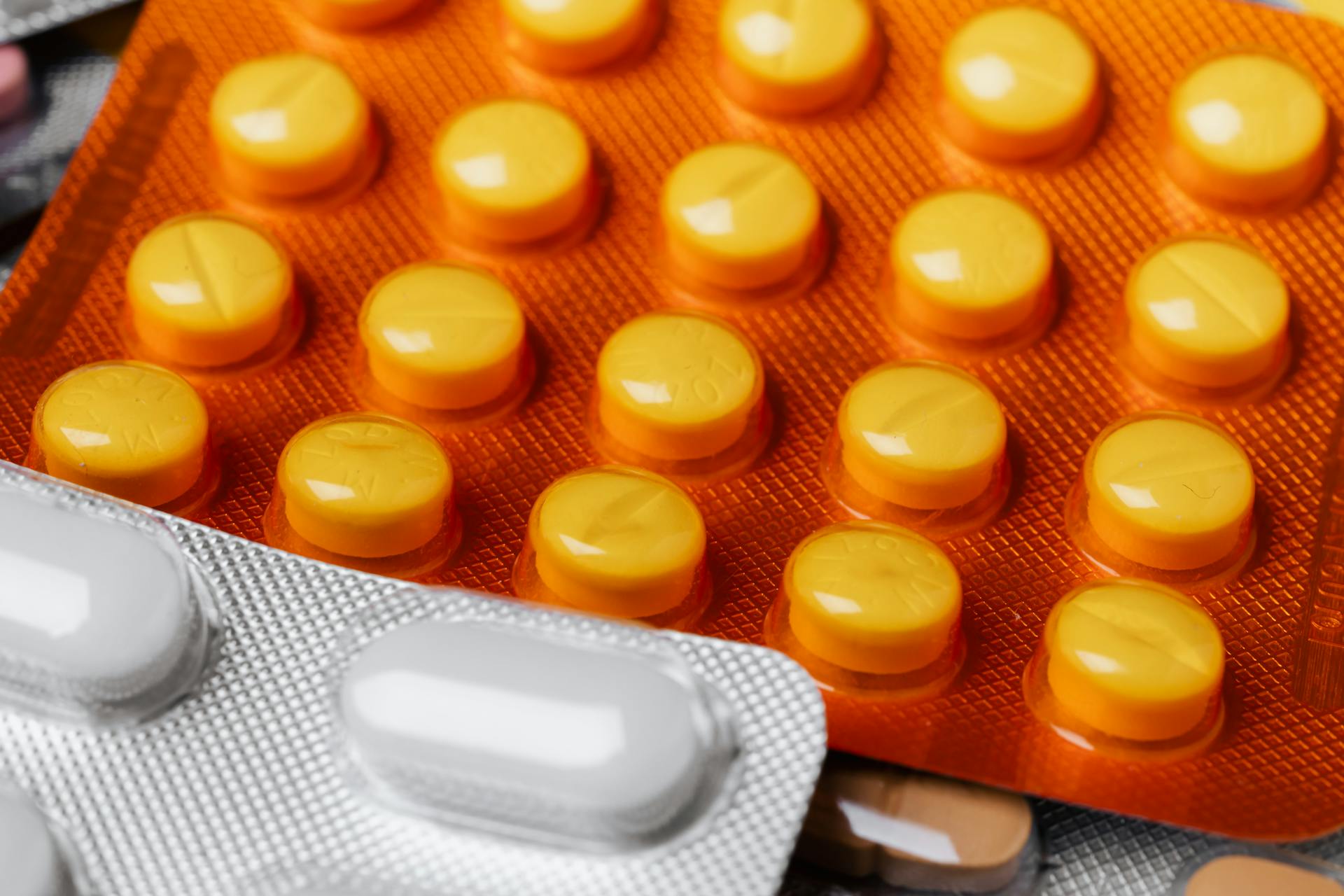
Blister packs are a popular packaging solution for a wide range of products, including pharmaceuticals, cosmetics, and electronics. They offer excellent protection and visibility for products.
Blister packs are made from a plastic tray and a clear plastic cover, which can be made from PVC or PET. The tray is molded to fit the product perfectly, and the cover is pressed onto the tray to create a secure seal.
The benefits of blister packs include their ability to display products clearly, making them ideal for retail and point-of-sale displays. They also provide excellent product protection, keeping items safe from damage and tampering.
Blister packs are commonly used for products that require a high level of protection, such as fragile electronics or sensitive medications.
Suggestion: Ifco Tray
What Is Blister Pack?
Blister packaging is a type of packaging that involves placing a product in a molded cavity covered with a transparent plastic film or aluminum foil.
This style of packaging is most frequently used for products that require visibility and protection, such as tablets, capsules, and electronics.
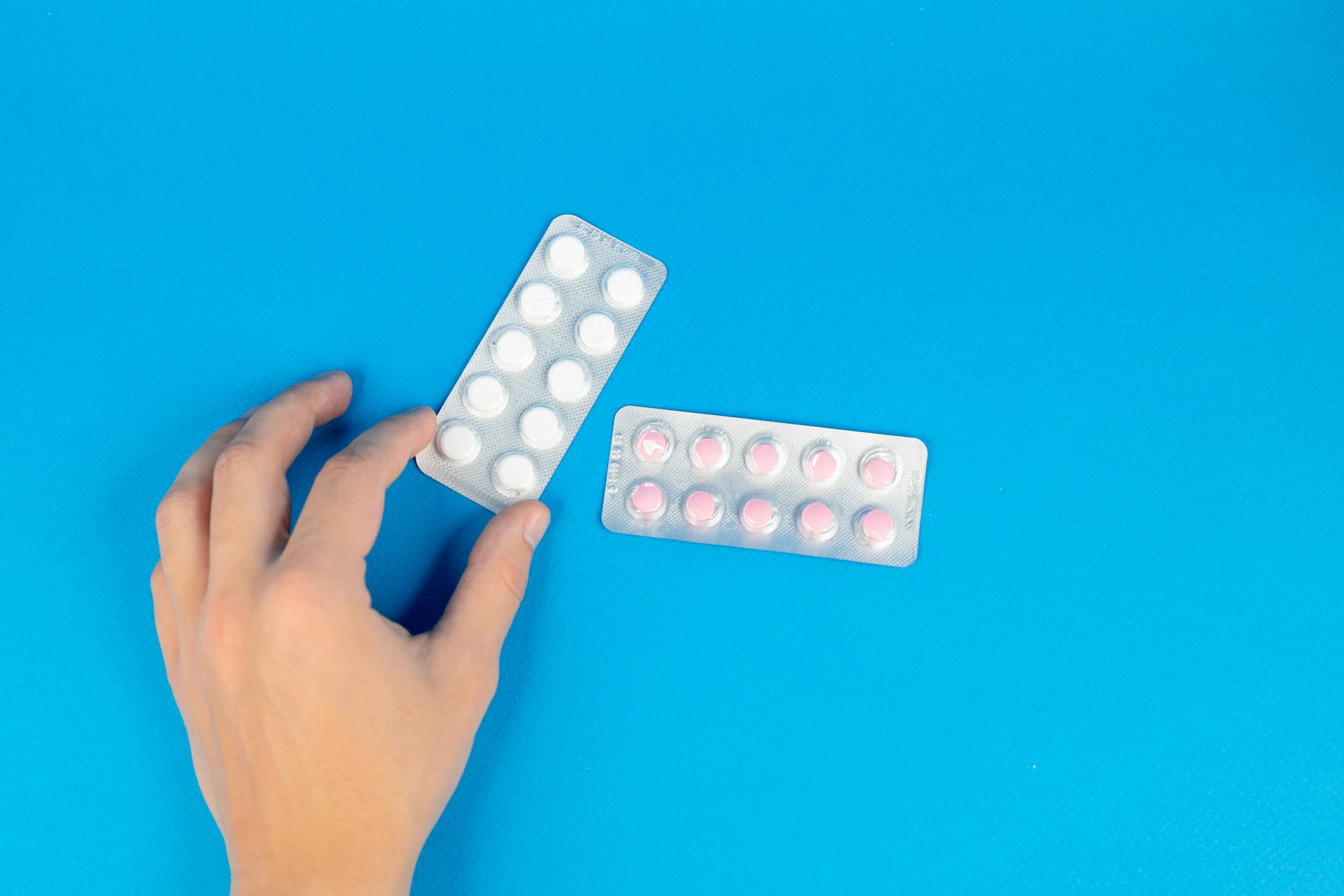
A depression is formed in the blister pack to encompass the product, which is then covered with a lidding material like plastic film, aluminum foil, or both.
Blister packaging provides a barrier against moisture, contaminants, and shock, in addition to offering an aesthetical appeal to the product.
Manufacturing processes of blister packaging include forming, filling, sealing, and cutting.
Types of Blister Pack
There are several types of blister packaging, each with its unique qualities and price points. Face Seal, Full-Face Seal, Trap, and Slide are some of the most common types.
The selection of materials for blister packaging machines is determined by the specific requirements of different industries and type of blister packaging desired. PVC (Polyvinyl Chloride) is the most preferred material for blister packaging due to its outstanding transparency and excellent barrier qualities.
The most popular and frequently used materials in blister packaging include PVC, PET (Polyethylene Terephthalate), Aluminum Foil, and PVDC coatings. Each material has its pros and cons, such as PVC's limited environmental sustainability and PET's less effective barrier compared to PVC.
Unit Dose
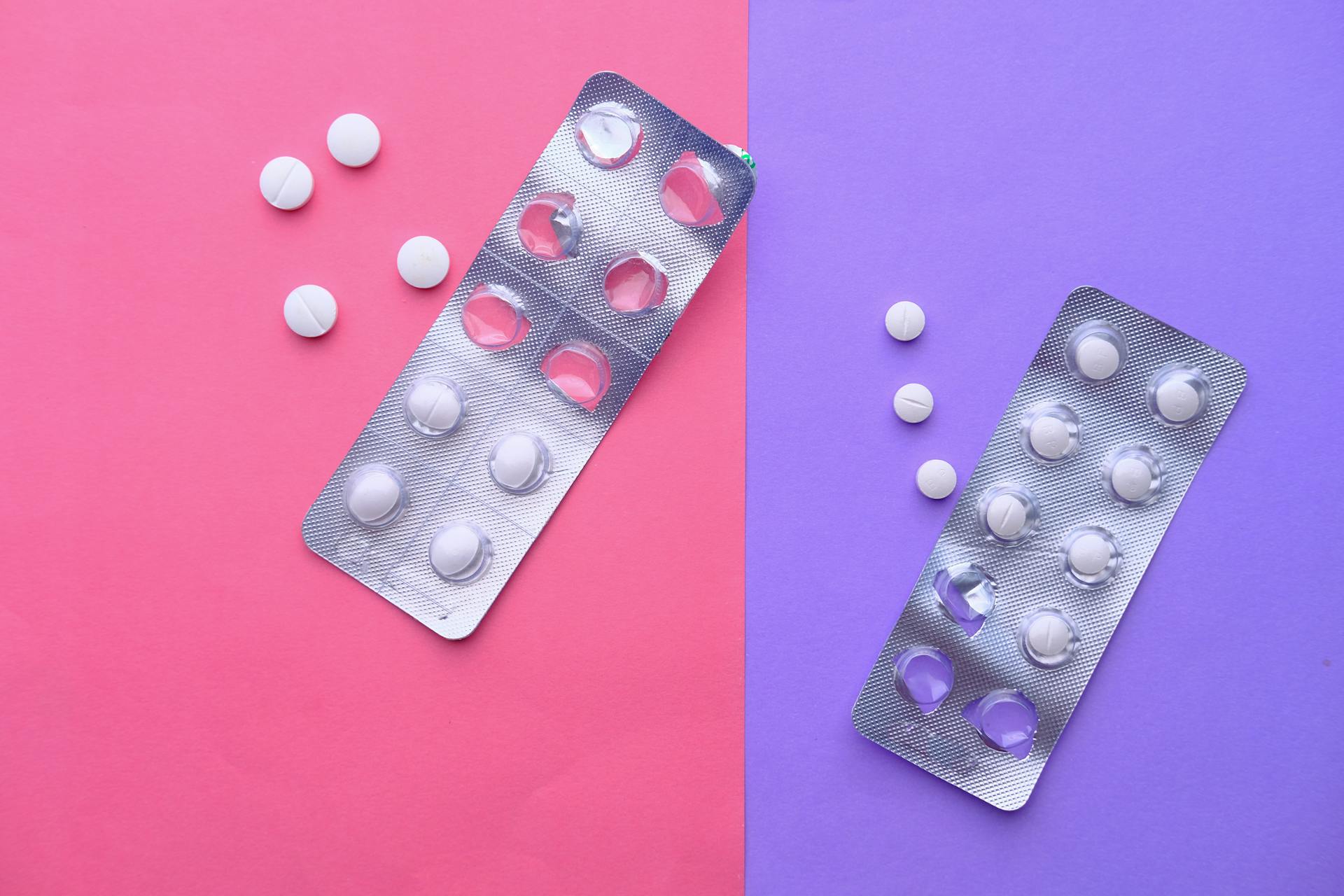
Unit Dose blister packs are commonly used for pharmaceutical tablets, capsules, or lozenges. They provide barrier protection for shelf life requirements and a degree of tamper resistance.
In the US, Unit Dose blister packs are mainly used for packing physician samples of drug products or for over-the-counter (OTC) products in the pharmacy. Pharmacy dispensing and re-packaging are not common in the US.
A series of blister cavities is sometimes called a blister card or blister strip as well as blister pack. The difference between a strip pack and blister pack is that a strip pack does not have thermo-formed or cold formed cavities.
The main advantages of Unit Dose blister packs include the assurance of product/packaging integrity, including shelf-life, of each individual dose. This ensures that each dose is safe and effective.
Blister packs are created by means of a form-fill-seal process at the pharmaceutical company or designated contract packer. This process involves creating the blister pack from rolls of flat sheet or film, filling it with the pharmaceutical product, and closing it (sealing) on the same equipment.
Explore further: Shelf Life
Clamshell
A clamshell is a type of blister pack that's folded over onto itself and sometimes fused at the edges. They're often used for small high-value items like consumer electronics.
Clamshells can be securely heat sealed, making them difficult to open by hand, which can deter tampering. A pair of scissors or a sharp knife is often required to open them.
Trauma shears are also effective at opening clamshell packaging. Care must be used to safely open these packages, as opening them without care can result in injury.
Around 6,000 Americans are sent to the emergency room each year for injuries suffered while opening clamshell packages.
A fresh viewpoint: How to Open Blister Packaging
Slide
Slide blisters have three wrap around edges and the header card slides into the open end, securing the contents. Staples or tape are often applied, but no heat or glue sealing process is required.
Slide blisters are a cost-effective option, making them suitable for entry-level packaging solutions.
Intriguing read: Slide Blister Pack
Bubble or Cavity
To design a bubble or cavity, you can send in a sample of the product to be packaged or a drawing of the design.
A mold is engineered based on the sample or drawing, which will produce a clear, plastic bubble.
The type of blister package chosen affects the cavity design, including the type of material, such as PVC or PET plastic.
VisiPak customers can provide a sample or drawing to get started on designing their bubble or cavity.
Additional reading: Bubble Pack
Manufacturing Process
The manufacturing process of blister packs involves several key steps.
The first step is to create the blister, which is typically made from a type of plastic called PVC. The PVC is molded into a sheet and then cut to size.
The next step is to apply the backing material, usually a paper or foil sheet, to the back of the PVC sheet. This provides a smooth surface for the product to be applied to.
The product is then carefully placed onto the blister, which is held in place by the backing material.
The finished blister pack is then sealed by applying heat and pressure, which causes the PVC to melt and bond with the backing material.
On a similar theme: Foam Pouches for Packing
Trays
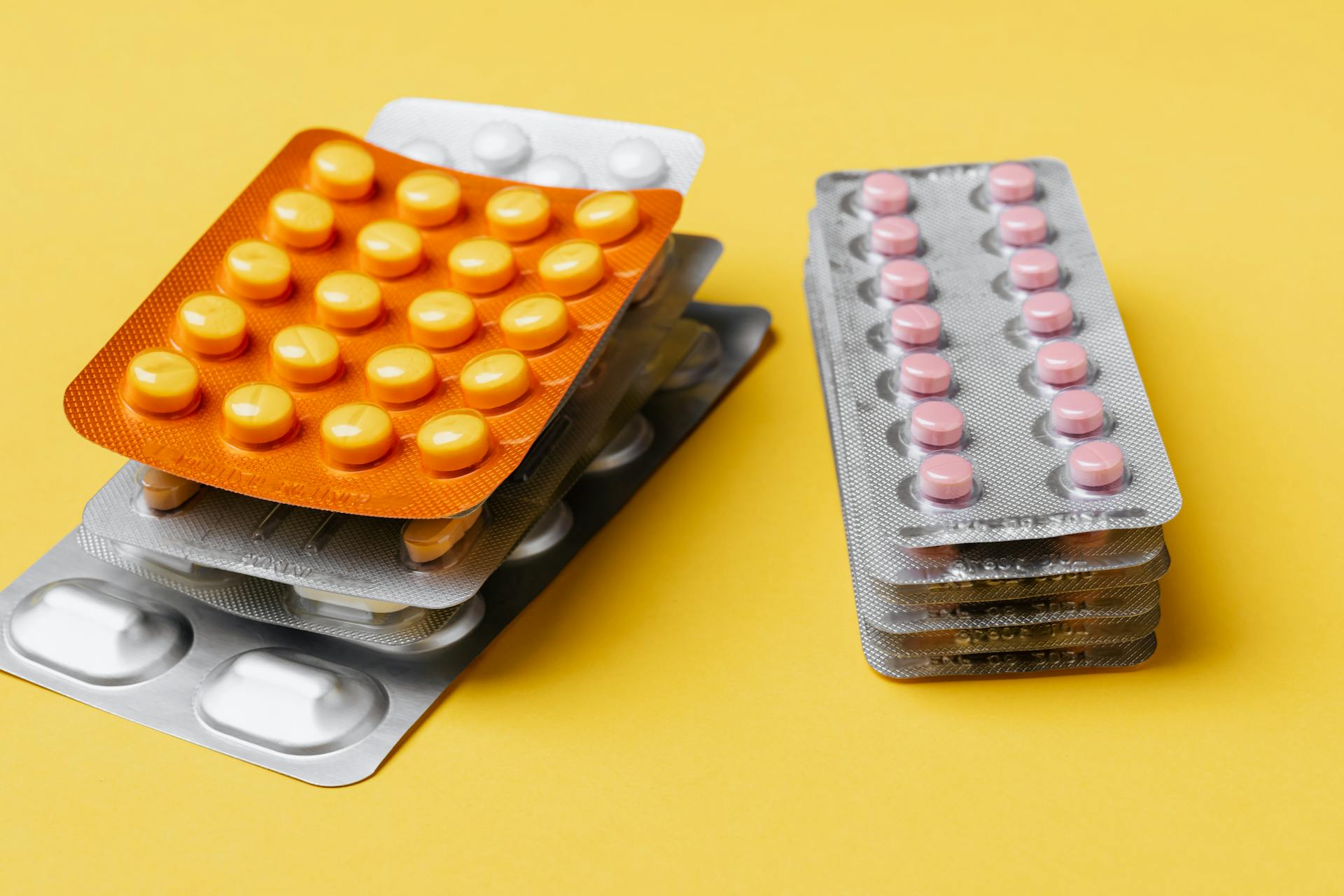
Trays are a type of packaging that can be made using the same machines and plastics as blister packs.
Medical blister trays are made with a thicker plastic sheet, typically between 500 and 1,000 μg, which cannot be collapsed, forming a solid tray.
They are used for sterile medical devices in hospitals, where the lidding film is porous to allow sterilization.
Blister trays are essentially the same as blister packs, made on the same machines with the same types of plastics.
They can be sealed to a paperboard card or hung on a merchandising wall, making them suitable for various applications.
Blister trays can be lidded with foil, film, or a thermoformed plastic lid, and may function as packaging insert trays or shipping trays.
A fresh viewpoint: What Are Styrofoam Peanuts Made of
Heating and Forming
The heating and forming process is a critical step in manufacturing high-quality pharmaceutical packaging.
The plastic film or sheet, typically made of materials like PVC or PET, is heated until it reaches the required temperature. This is often achieved through a pre-heating station on the blister line.
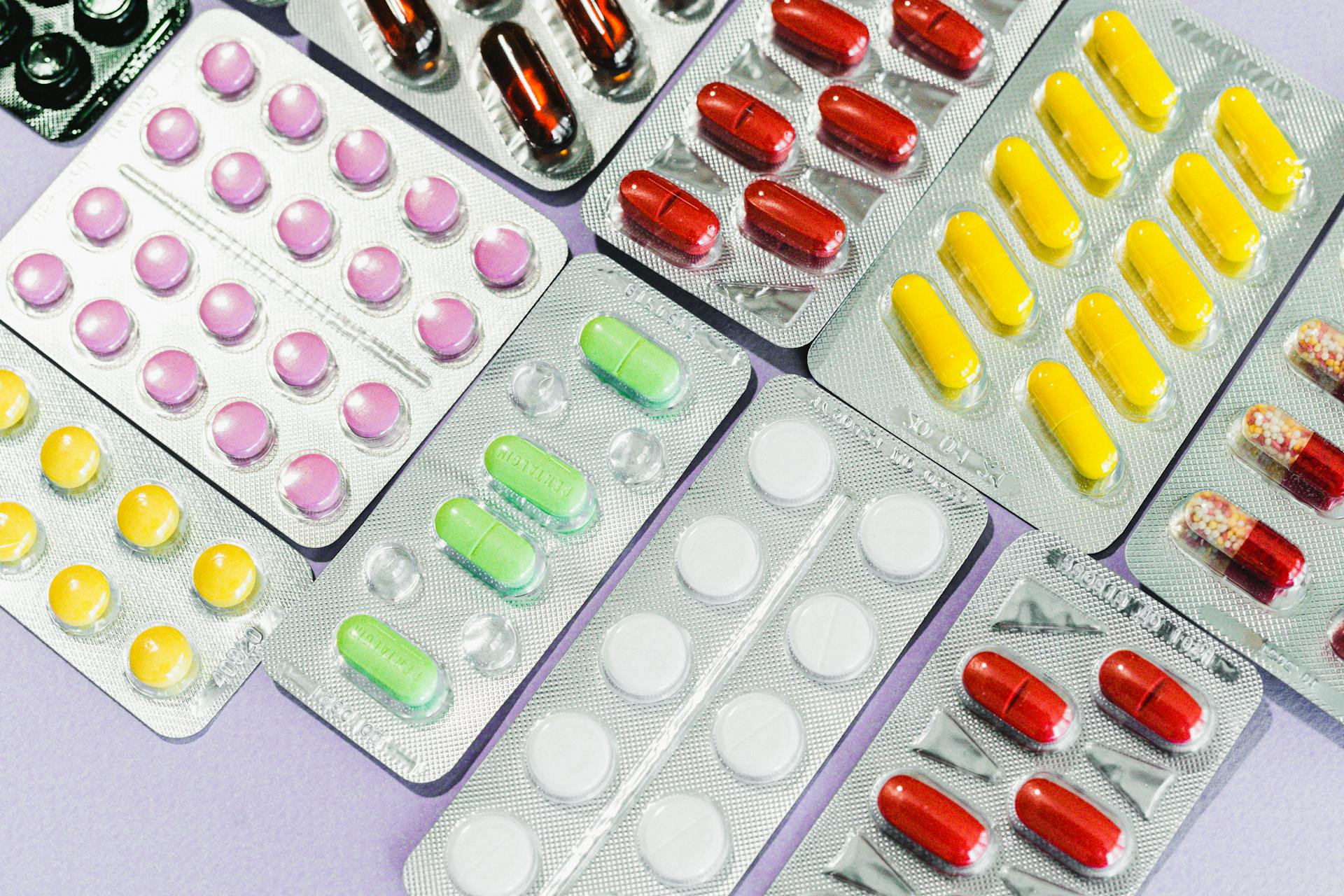
The heated material is then shaped into cavities through vacuum or pressure forming, allowing each compartment to be individually shaped.
A critical aspect of this stage is constructing the ‘blister’ shape that will securely hold the product. PVDC or other polymers are often added to some machines to enhance the water vapor barrier properties.
This heating and forming process allows for a secure and protective fit for the packaged items.
Cold Forming
Cold forming is a manufacturing process that involves pressing an aluminum-based laminate film into a mold using a stamp.
The aluminum will be elongated and maintain the formed shape, resulting in a product known as cold form foil (CFF) blisters.
Cold form foil blisters have a near complete barrier for water and oxygen, allowing an extended product expiry date.
This is a significant advantage of cold form foil blisters, making them a popular choice in the industry.
However, cold form foil blisters also have some disadvantages, including a slower speed of production compared to thermoforming.
The lack of transparency of the package is another disadvantage, which can be a problem for therapy compliance.
The larger size of the blister card is also a drawback, as aluminum can't be formed with near 90-degree angles.
Cutting and Finishing
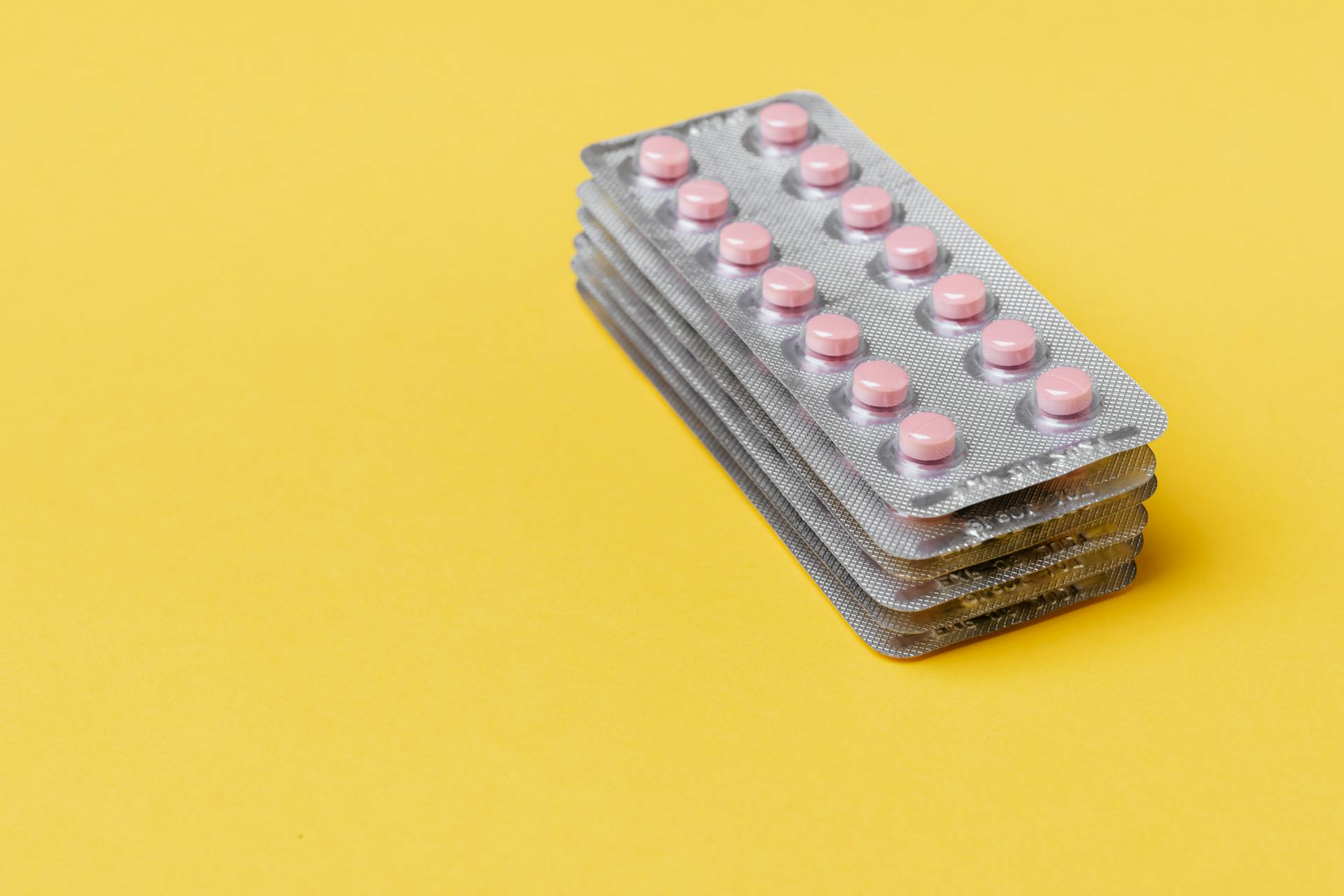
The cutting and finishing process is a crucial stage in the manufacturing process, where completed and sealed blister packs are divided into individual units or sheets.
Some equipment is capable of flexible deployment parameters, allowing for the production of different sizes and configurations of packages, such as blister cards for medicines or clamshells for electronics.
Clean edges are produced on the surface during the cutting and finishing processes, making it easy to use and store the finished blister packs.
After this stage, the blister packs are prepared for shipments and sales, which are long-lasting, protective, and attractive to consumers.
Part Production & Fulfillment
In the part production and fulfillment process, a product is scheduled for production usually within 1 to 2 weeks after First Article approval is provided.
This allows for a smooth transition from design to production, ensuring that the product meets the required specifications.
Here are the typical business day lead times after a Purchase Order (PO) and all relevant information has been submitted and acknowledged:
- Product is shipped to the customer in blisters.
Materials and Advantages
Blister packaging uses various materials to ensure product protection and visibility. PVC (Polyvinyl Chloride) is the most preferred material due to its outstanding transparency and excellent barrier qualities.
PVC offers adequate protection from moisture, humidity, and contaminants, making it suitable for pharmaceutical and consumer packaging. It's also low-cost and economically effective, ideal for mass production.
PET (Polyethylene Terephthalate) is another popular material, offering reusability and sustainability. However, it may lack some barrier strengths compared to PVC.
Here's a comparison of common blister packaging materials:
Aluminum foil provides high protection levels and excellent barrier properties, making it ideal for sensitive products like tablets and capsules.
Pctfe
PCTFE is a popular choice for blister packaging due to its exceptional moisture barrier properties. Typical constructions used for pharmaceutical products are 250μ PVC film laminated to 15μ-150μ PCTFE film.
PCTFE films have the lowest water vapor permeation compared to all other plastic films used in blister packaging. They also have thermoforming properties similar to plain PVC, although they are the most expensive option.
For your interest: Machine Stretch Wrap Film
A duplex structure of PVC/PCTFE is commonly used for pharmaceutical products, and triplex laminates such as PVC/PE/PCTFE can be used to form deeper cavities. These constructions offer improved moisture protection and flexibility.
Typical Water Vapor Transmission Rate (WVTR) values for PCTFE films are 0.06–0.40 g/m per day. This is significantly lower than the WVTR values for PVC films, which are around 3.0 g/m per day.
PCTFE is also a more environmentally friendly option than PVC, as it does not suffer from the environmental liability of discharging hydrochloric acid during incineration.
Lidding Foils
Lidding foils are a crucial component of pharmaceutical blister packs, and they come in different types. The most common type is 20 μm hard tamper aluminum, which is pinhole-free.
This type of lidding foil is often coated with a heat-seal lacquer on the inside and a print primer on the outside. The heat-seal lacquer helps to create a strong seal when the foil is pushed through or peeled open.
A different take: Security Seal
Types of Material
When selecting a material for blister packaging, it's essential to consider the specific requirements of your industry and the type of packaging you need. PVC (Polyvinyl Chloride) is a popular choice due to its outstanding transparency and excellent barrier qualities, making it suitable for both pharmaceutical and consumer packaging.
Rigid PVC is the most preferred material for blister packaging, offering adequate protection from outside interference such as moisture, humidity, and contaminants. This material is also low cost and economically effective, making it an ideal choice for mass production of packages.
PET (Polyethylene Terephthalate) boasts a reusability that makes it a sustainable solution for blister packaging. Its environmentally friendly attributes have made PET and polypropylene more popular in industries with a focus on eco-friendliness.
Aluminum Foil is ideal for packaging items that require high levels of protection, such as medicines. It has excellent barrier properties and forms a tight seal that protects against moisture, air, and light.
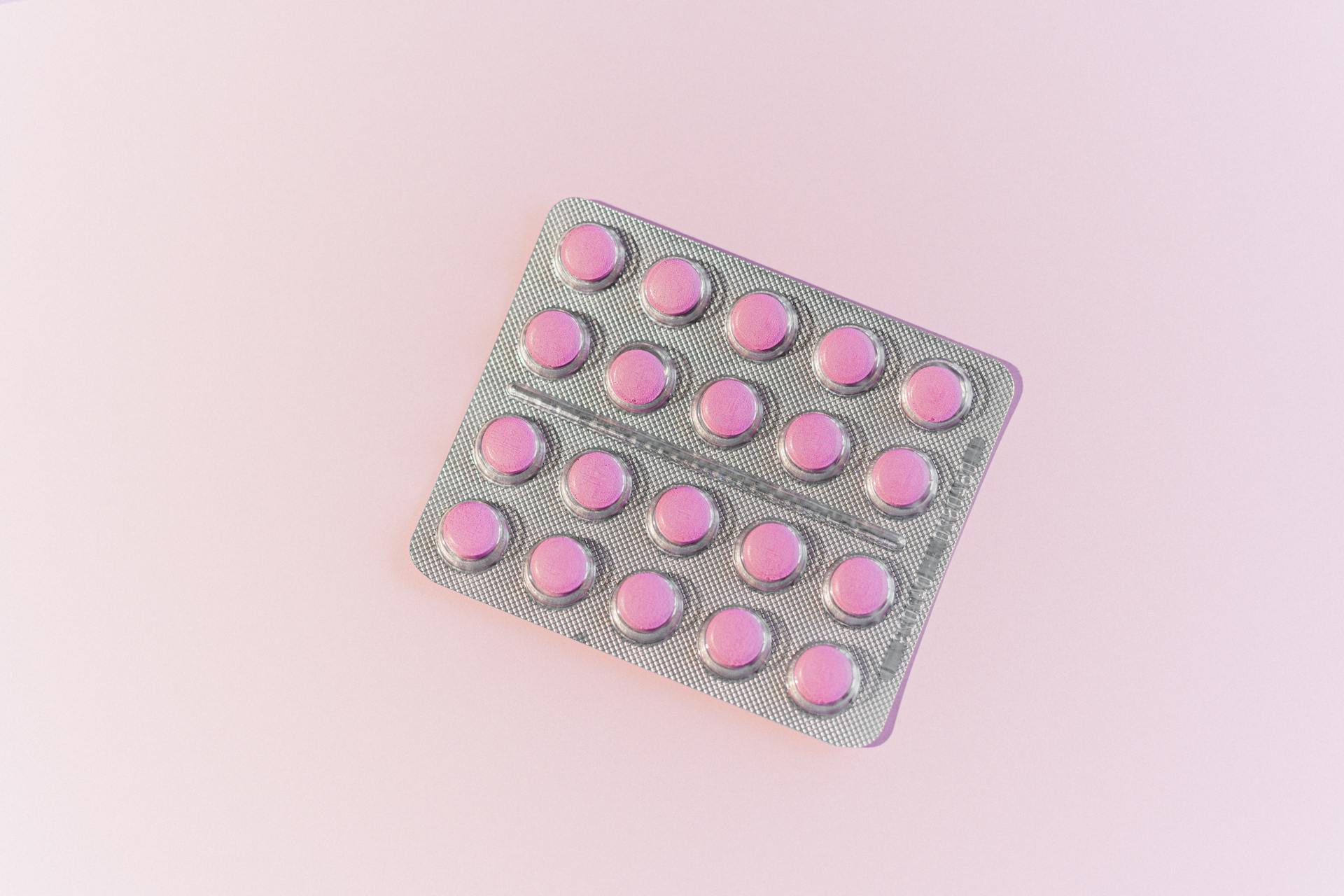
PVDC coatings are applied to plastic films, such as PVC and other materials without chlorine, to enhance their barrier properties. This material is ideal for packaging products vulnerable to moisture and oxygen.
Advantages
Blister packaging offers optimum protection to products, especially those prone to defects like moisture, light, and contamination.
The barrier created by blister packs made from aluminum foil and PVC materials enhances the shelf life of products, making them ideal for medicines, small consumer goods, and other perishables.
Blister packaging machines are fast and economical to use, reducing the need for additional protective materials and lowering packaging costs effectively.
This contributes to lower price points for the end products, making them competitive in the market.
Related reading: China Packing Materials
Applications and Industries
Blister pack is widely used in various industries, including club stores, major retail chains, and home improvement, hardware, and tools. These industries rely on blister pack for its convenience and durability.
Blister pack is particularly popular in the pharmaceutical industry, where it's used to pack tablets, capsules, and syringes. This is because blister pack is safe, resistant to tampering, and ensures patient safety and adherence to medication schedules.
In pharmacies and other health structures, blister pack is essential for guaranteeing patient safety and meeting legal standards. Blister pack's safety features make it a reliable choice for medication packaging.
Blister pack is used in the following markets and product categories:
- Club Stores
- Major Retail Chains
- Home Improvement, Hardware, Tools
Machine Operation and Selection
Choosing the right blister packaging machine requires careful consideration of the product's characteristics. For food products like candies or chewing gums, speed of filling is critical.
Speed is essential for these types of products to maintain freshness and prevent damage. This is especially true for products that have a short shelf life.
The materials used for the machine are also crucial, as they can affect the overall quality of the packaging.
Face Seal
Face Seal packaging is a popular choice for small lightweight items like lip balms and sewing notions. A sealing process is applied to secure the contents.
Plastic blisters lay on top of a portion of the header card for this type of packaging. This design is often used for products like pens and markers.
Face Seal blisters require a sealing process to secure the contents, which is essential for keeping the items inside fresh and protected.
What Is Machine Operation?
Machine operation is essentially the process of running a machine to perform a specific task. This can involve controlling the machine's movements, speed, and power to achieve the desired outcome.
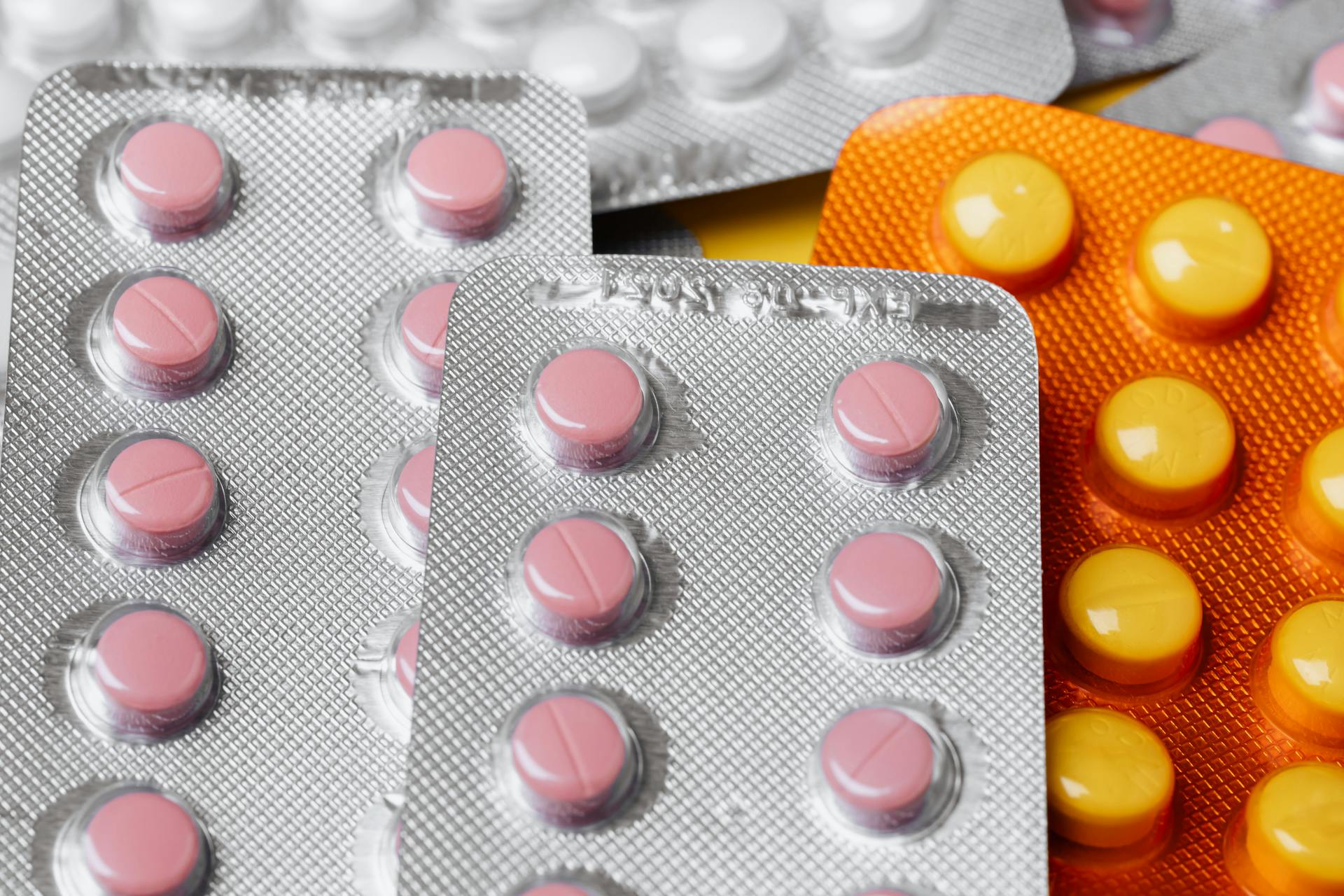
A machine's operation is determined by its design, which includes factors like its type, size, and purpose. For example, a drill press is designed to drill precise holes, while a milling machine is designed to remove material from a workpiece.
Machine operation requires a good understanding of the machine's capabilities and limitations. Operators need to know how to adjust the machine's settings to achieve the desired results, such as adjusting the drill press's speed to avoid damaging the workpiece.
The type of machine operation can vary greatly, from simple tasks like drilling or cutting to more complex tasks like assembly or welding.
Selecting Ideal Machines for Applications
Selecting ideal machines for applications is crucial to ensure the quality and safety of products. This involves considering the characteristics of the product, as well as the application requirements of the machine.
For pharmaceutical products, precise dosing and tamper-evident sealing are key requirements. This ensures that patients receive the correct dosage and prevents unauthorized access to the product.
You might like: Amazon Polybag Requirements
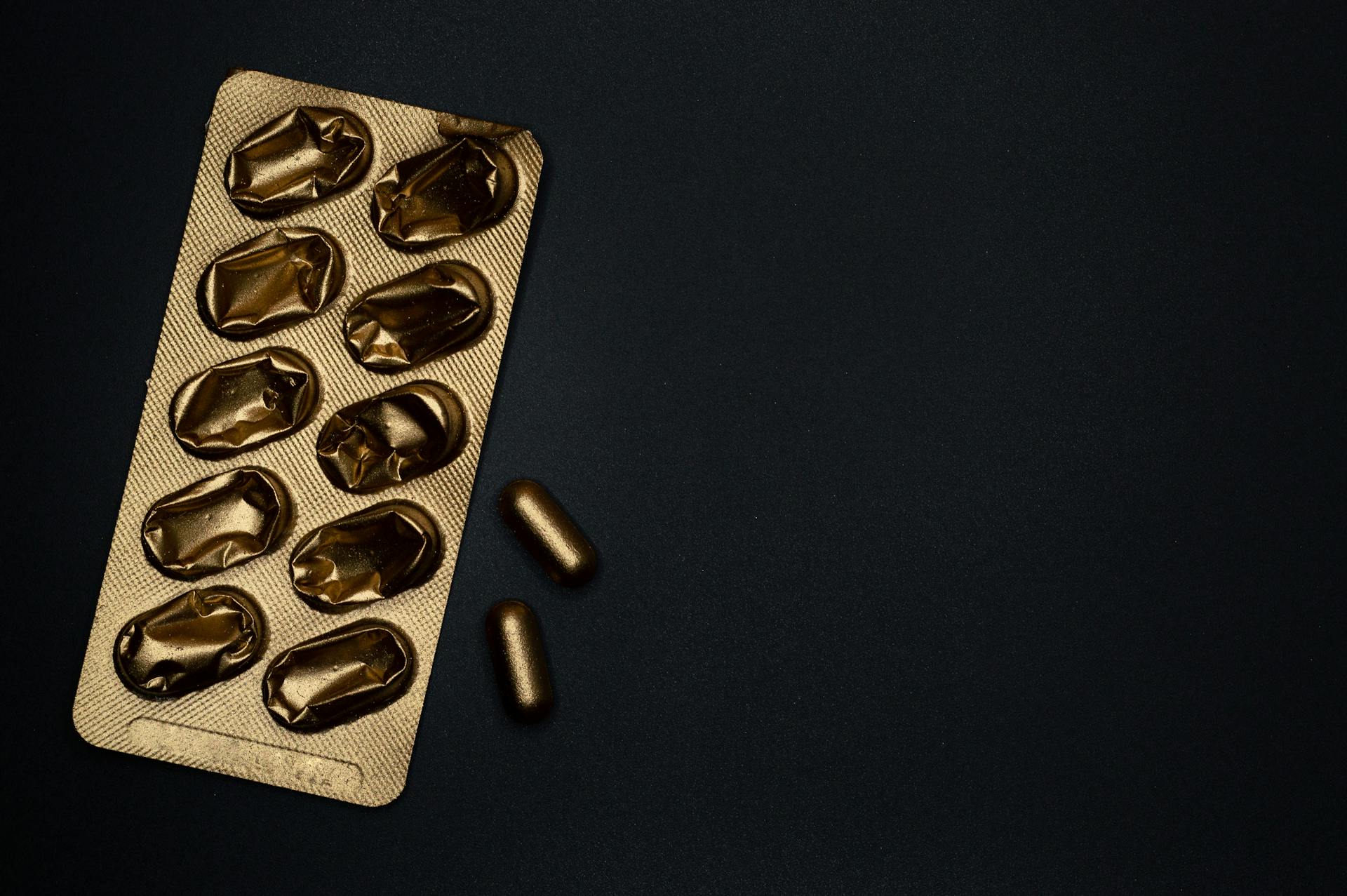
High-Precision Automated Blister Packaging Machines are recommended for pharmaceutical applications, as they provide high-speed and high-accuracy production lines that guarantee the safety and wholeness of the products.
In contrast, electronics and small tools require strong and difficult-to-open packaging, often achieved with clamshell or rigid blister packs. These packs provide impact resistance and high transparency, allowing consumers to see the product while ensuring its safety during transportation.
Rigid Blister Packaging Machines or Heat-Seal Blister Machines are suitable for electronics and small tools, offering long-lasting and secure packaging solutions with good visibility.
For high-turnover production lines, High-Speed Blister Packaging Machines are ideal, as they provide efficient packaging with moisture and oxygen protection, utilizing aluminum foil or PVDC-coated films to enhance shelf life.
In some industries, such as cosmetics or auto spare parts, packaging may need to be unique, requiring flexibility and multi-functionality. In these cases, Multi-Functional Blister Packaging Machines are suitable, as they can accommodate packaging of different sizes, shapes, and materials.
Here are some key considerations for selecting ideal machines for applications:
Hanging Element
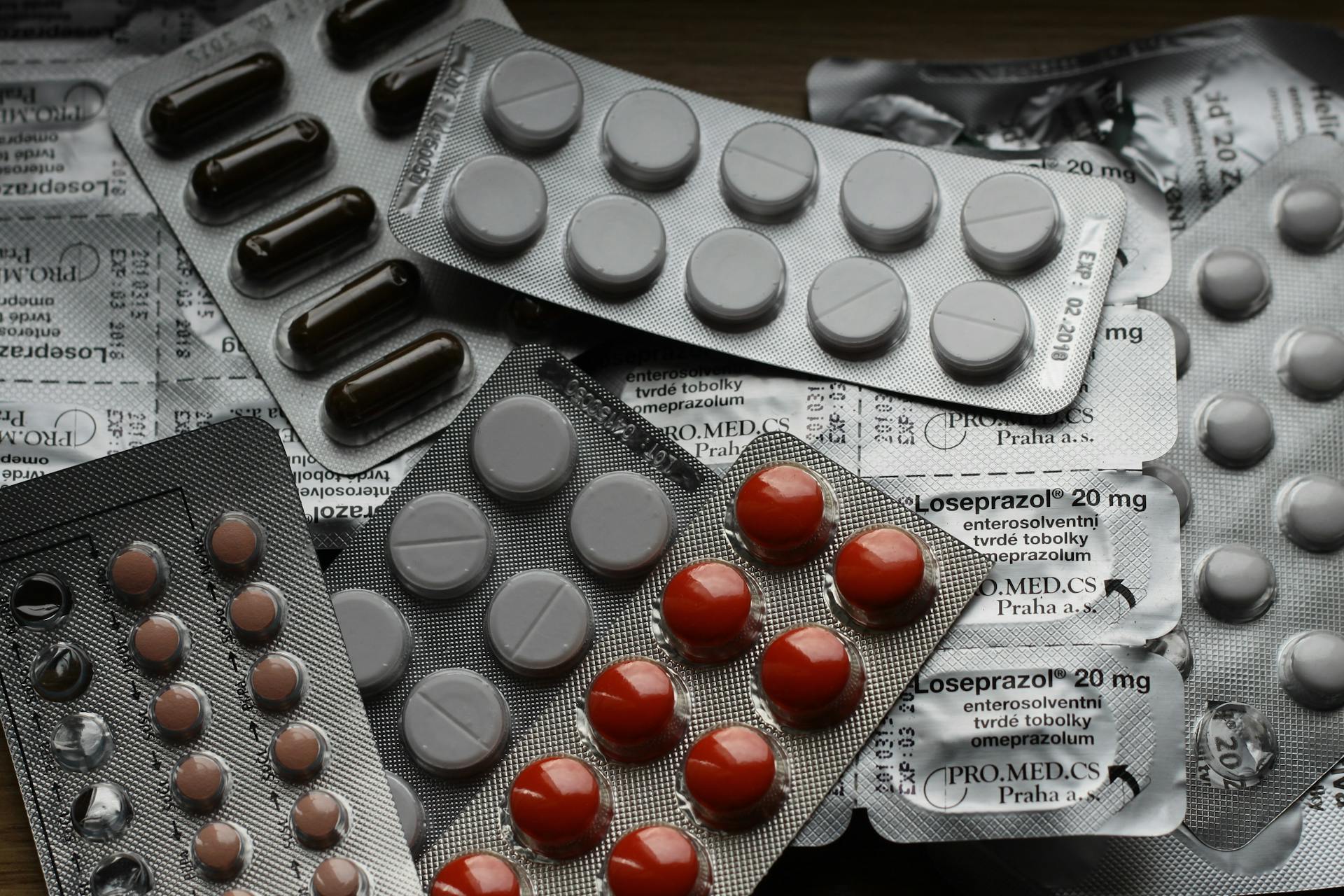
When designing a blister pack, it's essential to consider how it will be displayed on a merchandising wall. Most blister packs are designed to hang, so they feature a hanging element.
Given that paperboard can rip more easily than plastic, many blister packaging designs feature hang holes integrated into the plastic blister. This is a crucial consideration for packaging designers.
Multiple hanging hole styles are available, allowing designers to choose the best option for their product.
3. Romaco
Romaco is an internationally recognized supplier of blister packaging machines, particularly for small to medium runs.
Their Noack blister packaging machines are valued for short cycle time retooling, high dependability, and compactness. This makes them ideal for contract packaging firms and generics producers.
The Unity series blister machines from Romaco are designed to meet various production requirements. These machines are part of their range of key products.
Customized packaging solutions and rapid retooling support are among the key services offered by Romaco. They also provide technical support and process optimization to their clients.
Custom Package Development
Custom package development allows for the creation of unique blister packs that meet specific product requirements.
Blister packs can be designed to hold a wide range of products, from small electronics to pharmaceuticals.
Custom package development enables businesses to differentiate their products from competitors and create a memorable brand image.
The blister pack's compact size and portability make it an ideal packaging solution for travel-sized products, as seen in the example of travel-sized toiletries.
Take a look at this: Custom Cd Packaging
Steps to Develop a Custom Package
Developing a custom package involves several key steps. Prototyping is a crucial part of this process.
To establish a customer's credit, they submit a purchase order for a prototype. This is the first step in creating a custom package.
A Ren board mold is created in-house and blister samples are produced. This allows for testing and evaluation of the package's form, fit, and function.
We design and test the customer sample to ensure it meets their requirements. This includes testing for any issues that may arise during production.
A fresh viewpoint: Product Packaging Testing
The blister samples are then shipped to the client for approval. This is an important step, as it allows the client to review the package and make any necessary revisions.
If the client approves the blister, the process is complete. However, if revisions are needed, we make one revision at no additional charge.
Card or Backboard
A blister card or paperboard is often included in blister packages to provide space for graphics and product information.
This extra layer of information can help grab the buyer's attention and inform them about the product.
Cost and Product Display
Blister packaging is a cost-effective way to showcase a product, making it a great option for businesses.
More than half of shoppers believe it's essential to see a product through its packaging, which is exactly what blister packaging provides.
Blister packs are one of the most cost-effective methods for packaging a product, with both paperboard and plastic blisters being inexpensive options.
Numerous companies make equipment to automate the packing and sealing processes, making it easy to get started with blister packaging.
Most consumers believe it's crucial to see the actual product before making a purchase, and blister packaging allows shoppers to view the product and see a well-protected product.
Broaden your view: Cost of Shrink Wrapping Boat
Product Display
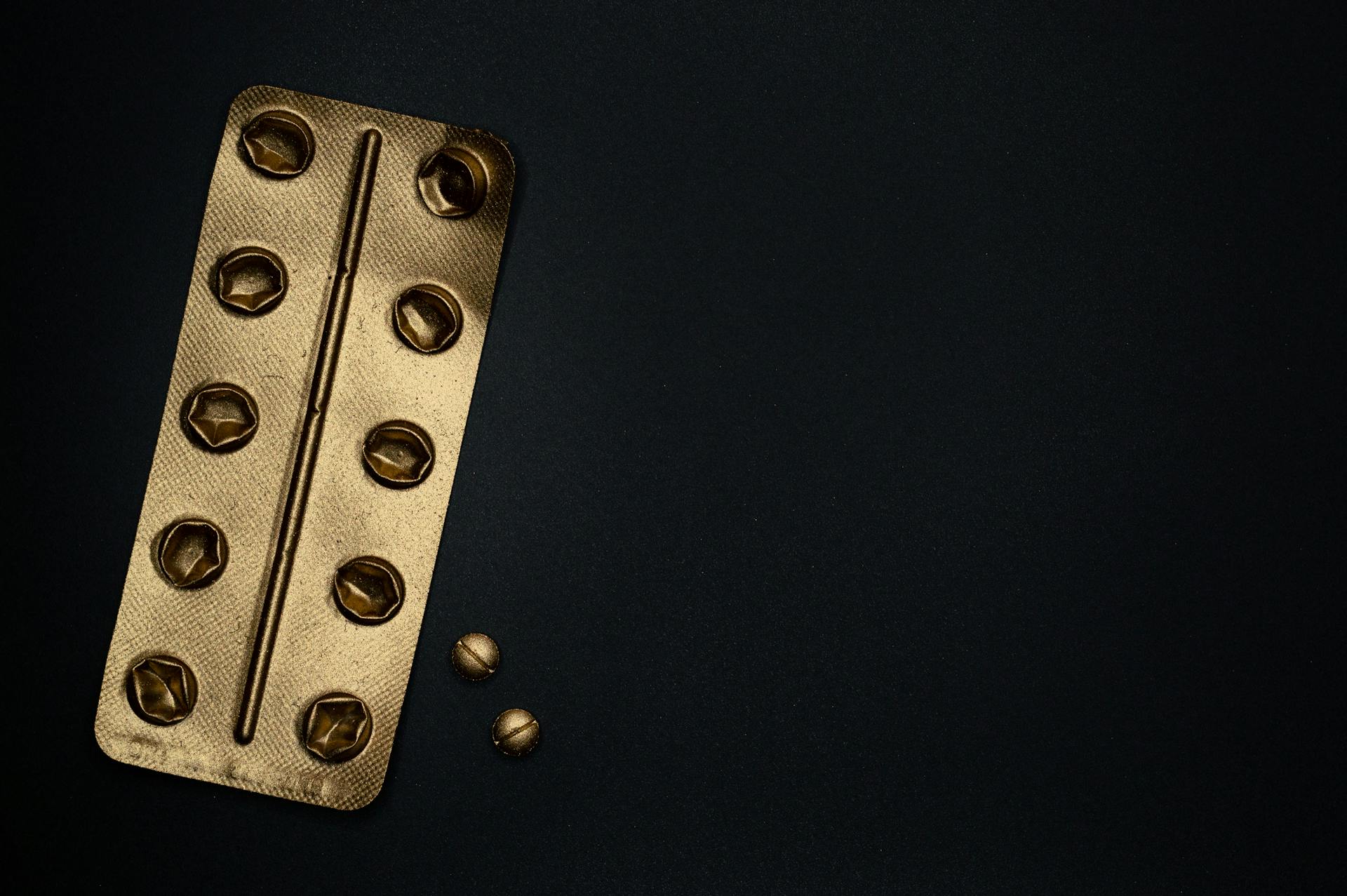
More than half of shoppers believe it is important to see a product through its packaging, making clear product display crucial for making a purchase decision.
Blister packaging helps shoppers see the product, making it easier to decide whether to buy. This is especially true for small lightweight items like lip balms and pens.
A clear display of the product is essential for consumers, with most believing it's important to see the actual product before making a purchase. This is where blister packaging shines, allowing shoppers to view the product and see it's well-protected.
Face Seal Blisters are a popular choice for small items like lip balms and pens, where the plastic blister lays on top of a portion of the header card.
A unique perspective: Clear Plastic Box with Hinged Lid
Cost Savings
Blister packaging is a cost-effective way to showcase a product.
Blister packs are one of the most cost-effective methods for packaging a product, making them an attractive option for businesses.
For another approach, see: Cost of Sustainable Packaging
Both the paperboard and plastic blister are inexpensive materials that can be used for blister packaging.
Numerous companies make equipment to automate the packing and sealing processes, making it easier and more efficient to use blister packaging.
The different types of blister packaging, such as Face Seal, Trap, Mock, Slide, and Interactive, offer varying price points, from entry level to high end.
Choosing the right type of blister packaging can help businesses save money without sacrificing product display.
Retail and Packaging
Retail and Packaging is a crucial aspect of blister packs. There are several types of retail packaging blisters, including Face Seal, Full-Face Seal, Trap, and Slide. Each one has its unique qualities and price points, from entry level to high end.
Face Seal blisters are a popular choice for many companies. They are relatively inexpensive and easy to use. Full-Face Seal blisters offer an extra layer of protection and are more secure than Face Seal blisters. Trap blisters are designed to keep products secure by trapping them between two plastic pieces. Slide blisters are similar to Trap blisters but are easier to open and close.
Pharmaceutical Equipment and Manufacturers
Pharmaceutical equipment manufacturers like Sedpharma and Pharmaworks specialize in producing high-quality blister packaging solutions for the pharmaceutical industry.
Sedpharma, founded in 2012, focuses on blister packaging machinery specifically for pharmaceutical applications, with a 5,500 m² factory and over 100 R&D and office personnel.
Their machines, like the SED-GP Series, support high-speed blister packaging for ALU-PVC and ALU-ALU materials, with production speeds reaching up to 14,400 plates per hour.
Pharmaworks, a North American company, offers a wide choice of blister packaging equipment, including semi-automatic machines for small-scale production and high-speed ones with production rates of up to 300 blisters per minute.
Both Sedpharma and Pharmaworks have gained recognition for their quality equipment, with Sedpharma holding ISO9001 and CE certifications, and Pharmaworks providing custom tooling design and technical consulting services.
Additional reading: Blister Packaging Machine Pharmaceutical Industry
Pharmaceutical Packs
Pharmaceutical blister packs are a type of packaging specifically designed for pills and tablets, typically consisting of a thin blister tray lidded with a foil barrier.
These packs provide tamper evidence, protect against external factors like humidity and contamination, and can safeguard light-sensitive products from UV rays.
The lidding material allows medication or supplements to be pushed through, making it easy to access the product while maintaining product integrity.
Pharmaceutical blister packs are primarily used in the pharmaceutical industry for packing tablets, capsules, and syringes.
Pharmaworks is a leading manufacturer of pharmaceutical blister machines, offering semi-automatic and high-speed machines with production rates of up to 300 blisters per minute.
Blister packs are essential in pharmacies and other health structures because they guarantee patient safety and meet legal standards.
Custom tooling design, technical consulting, and after-sales support are key services offered by Pharmaworks to cater to their clients' needs.
Pharmaceutical blister packs are designed to maintain adherence to medication schedules, often marked with the days of the week, making it easier for patients to stay on track with their medication.
These packs are safe, resistant to tampering, and provide a secure way to store and dispense medication.
A fresh viewpoint: Pill Blister Packaging
Leading Pharmaceutical Equipment Manufacturer
Sedpharma is a leading pharmaceutical equipment manufacturer, delivering high-quality solutions worldwide from its 5,500 m² factory.
With a dedicated team of over 100 R&D and office personnel, Sedpharma is well-equipped to meet the needs of the pharmaceutical market.
Their key products include blister packaging machines for pharmaceuticals, customizable blister packaging solutions for tablets and capsules, and medical device blister packaging equipment.
Sedpharma was founded in 2012 and has since focused on blister packaging machinery specifically for pharmaceutical applications.
Their machines, like the SED-GP Series, support high-speed blister packaging for ALU-PVC and ALU-ALU materials, with production speeds reaching up to 14,400 plates per hour.
Sedpharma's equipment meets industry standards for dosing precision and contamination control.
With ISO9001 and CE certifications, and a focus on meeting FDA regulatory requirements, Sedpharma is a reliable choice for quality blister packaging solutions in the pharmaceutical sector.
Broaden your view: Contract Pharmaceutical Packaging Companies
Frequently Asked Questions
Do pharmacies still do blister packs?
Yes, pharmacies still offer blister packs for convenient medication organisation. Just let the pharmacy team know and they'll arrange it for you.
What is the difference between a blister card and a blister pack?
A blister card is a flat, pre-formed plastic or paper sheet with cavities, while a blister pack is a 3D container with a cavity or pocket made from thermoformed plastic, often used to hold pharmaceuticals. The main difference lies in their shape and structure, with blister packs being more compact and convenient.
What is the difference between a blister pack and a pill pack?
A blister pack has a calendar-like layout, making it easy to identify missed doses at a glance, whereas a pill pack requires reading the day/date on each pouch to determine if a dose has been missed. This design difference affects how users manage their medication.
What is the problem with blister packaging?
Blister packaging can be prone to issues such as adhesive build-up, thermal expansion, and clean-up problems. Proper press maintenance is key to minimizing these challenges and ensuring a smooth packaging process.
Featured Images: pexels.com