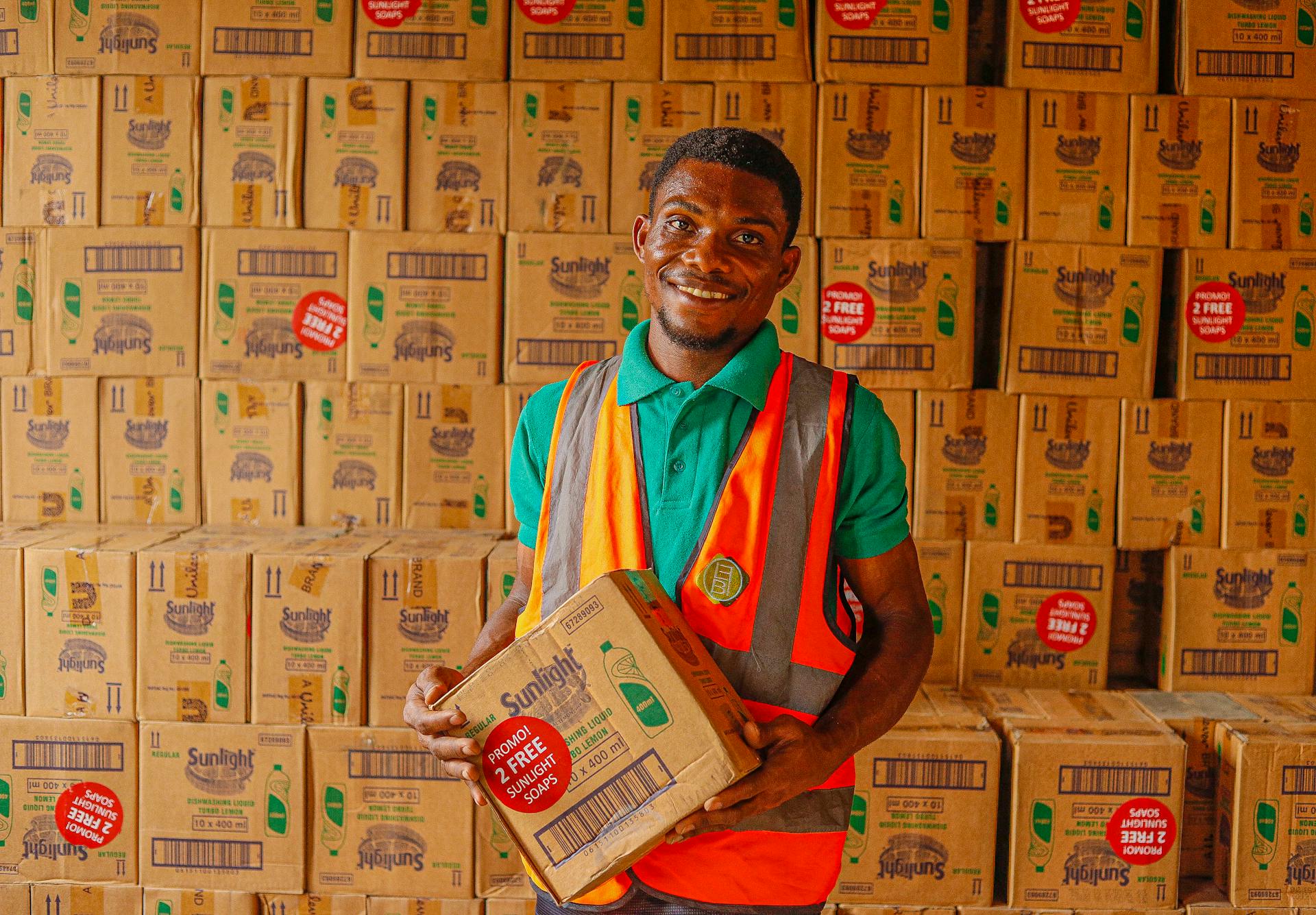
Effective warehousing and order fulfillment are crucial for businesses to stay competitive in today's fast-paced market. A well-designed warehouse can increase efficiency by up to 30% through optimized storage and retrieval systems.
Proper inventory management is key to efficient order fulfillment. This involves accurately tracking stock levels, identifying slow-moving items, and implementing a first-in, first-out (FIFO) system to minimize waste and reduce the risk of expired or damaged products.
A study found that 75% of businesses experience stockouts due to poor inventory management, resulting in lost sales and damaged customer relationships. By prioritizing inventory management, businesses can minimize stockouts and improve customer satisfaction.
Intriguing read: Order Fulfillment in Supply Chain Management
What Is Fulfillment?
A fulfillment warehouse is essentially a fulfillment center, but the terms are often used interchangeably.
A fulfillment center is a facility that specializes in fulfilling customer orders, particularly for online stores or eCommerce companies. They handle every aspect of order fulfillment, including receiving goods from suppliers or from a warehouse, picking and packing orders, and shipping goods to their final destination.
For your interest: Tagg Logistics Order Fulfillment Center
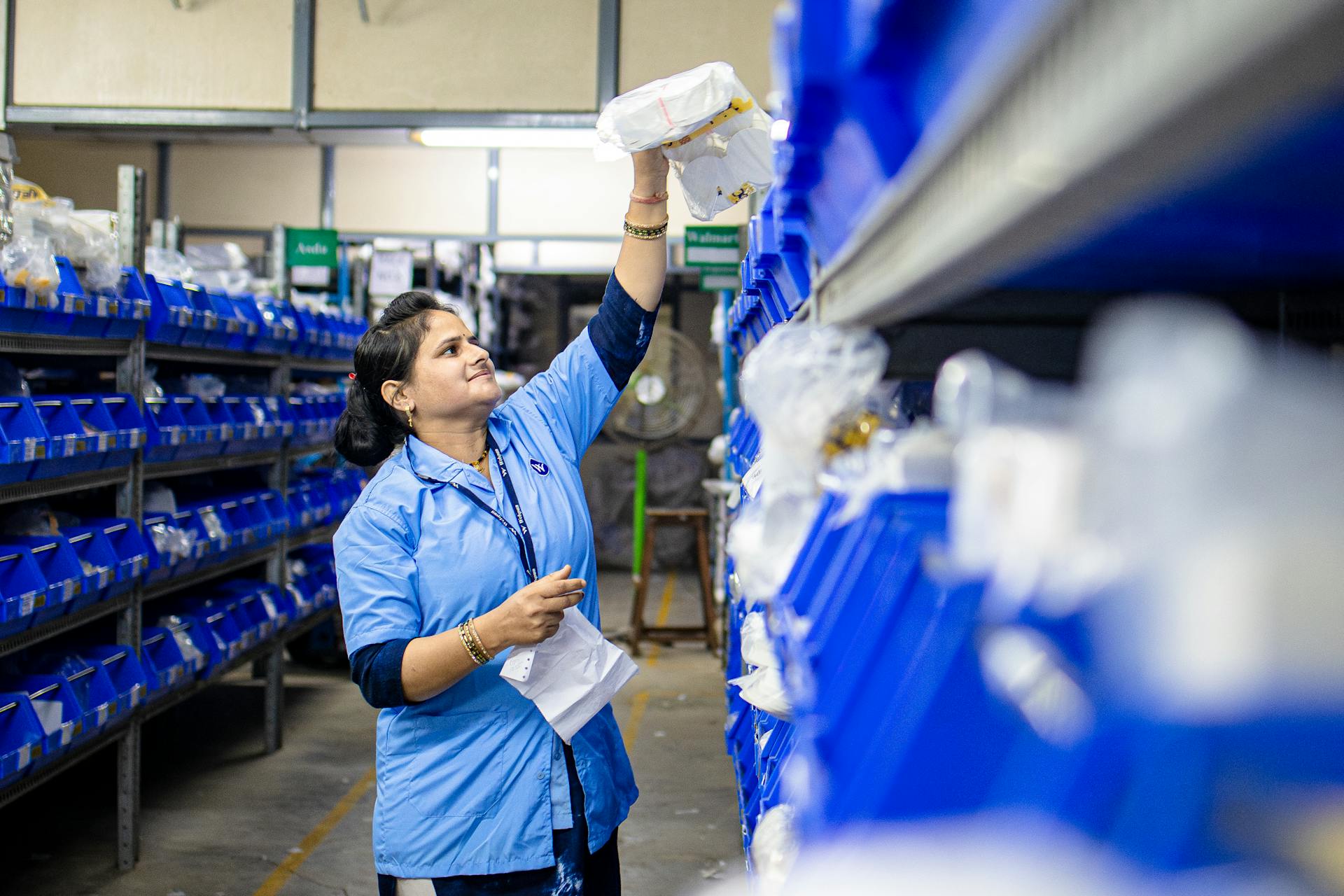
They provide full-service operations, including rapid order processing and expedited shipping times. This means orders can be processed quickly and efficiently, getting products to customers fast.
Many fulfillment centers have eCommerce expertise to help their clientele navigate complex online order processing. This expertise allows them to deliver the scalability to accommodate seasonal demand.
A stand-alone warehouse, on the other hand, is just a place where inventory is stored. It doesn't serve the same purposes as a fulfillment center.
A fresh viewpoint: Order Processing
Benefits and Importance
Having a well-run warehouse and efficient order fulfillment process is crucial for any business. It's the backbone of e-commerce, encompassing everything from receiving customer orders to delivering products.
A streamlined order fulfillment process ensures timely delivery, maintains product quality, and reduces errors, all of which are vital for building customer trust and loyalty. This aspect of the business is critical as it represents the physical connection between the customer and the company.
Here's an interesting read: Customer Order Fulfillment
Delegating supply chain operations to a fulfillment center frees up time and resources to focus on other areas of business growth, such as marketing, accounting, and product research and development. This allows businesses to scale and grow more efficiently.
Fulfillment centers provide brands with flexibility to meet the demands of different sales seasons, as well as a robust network that helps them to reduce shipping costs. A fulfillment center is an important aspect of inventory management, and allows for implementation of a consistent pick, pack, and ship process.
Timely and accurate fulfillment of orders builds trust and reliability in the brand, encouraging repeat business and positive word-of-mouth. In the digital age, where customer reviews can significantly influence purchasing decisions, flawless order fulfillment becomes even more essential.
A well-executed order fulfillment process ensures that customers receive their products promptly and in perfect condition. This is a key differentiator in competitive markets and can be the deciding factor in winning and retaining customers.
Types of Fulfillment
Fulfillment centers come in all shapes and sizes, each designed to suit a particular need. There are many different types of warehouses, including private warehouses, public warehouses, automated warehouses, climate-controlled warehouses, and on-demand warehouses.
Private warehouses are owned and operated by a specific company for their exclusive use, while public warehouses are shared by multiple companies and typically owned and operated by a third-party logistics (3PL) company.
Automated warehouses use mechanized systems to reduce or eliminate manual intervention, while climate-controlled warehouses preserve the quality and integrity of sensitive or perishable goods. On-demand warehouses provide temporary or short-term storage space to businesses, allowing them to adapt to fluctuations in inventory and demand.
Some fulfillment centers specialize in specific types of orders, such as direct-to-consumer (DTC) fulfillment centers that pick, pack, and ship orders directly to end consumers. Others focus on international fulfillment, reverse logistics, or automated fulfillment.
Here are some common types of fulfillment centers:
These types of fulfillment centers can help businesses streamline their operations, reduce costs, and improve customer satisfaction. By choosing the right type of fulfillment center, businesses can optimize their workflow and take their operations to the next level.
Operations and Management
Operations in a fulfillment center are hubs of activity, with a variety of tasks including receiving, checking, and stowing inventory, generating pick lists and picking products, and shipping orders.
Fulfillment centers often store inventory for a minimal amount of time, focused on picking and packing products to fill ecommerce orders, and shipping those orders directly to the customer. This is in contrast to warehouses, which are generally static and have a main activity of receiving inventory or transferring it out.
Inventory ships in and out of a warehouse on a shipping pallet container, and most of the logistics operations at warehouses concern a freight carrier or intermodal provider. Inbound inventory shipments arrive palletized at fulfillment centers, but they ship out as parcel-sized shipments.
Here are some key tasks performed by warehouse managers:
- Inventory management
- Budgeting
- Liaising with stakeholders
- Team management
- Performance reporting
Technological advancements are increasingly shaping modern warehouse operations, with the extensive use of robotics and automation for tasks like sorting and picking, and the implementation of Warehouse Management Systems (WMS) for improved tracking and process control.
In-House vs Outsourcing
In-house order fulfillment allows for complete control over the warehousing, handling, and shipping processes.
Outsourcing, on the other hand, can be cost-effective and scalable, especially for businesses experiencing rapid growth or fluctuating order volumes.
In-house fulfillment involves managing every aspect of fulfillment within the company, from organizing storage areas to processing orders.
Outsourced fulfillment transfers these responsibilities to a third-party provider, which can offer more flexibility and potentially reduce costs.
However, outsourcing may also mean less control over the logistics and fulfillment process.
How Do Operate?
Operating a warehouse or fulfillment center is a complex task that requires careful planning and execution. Effective inventory management is critical for successful order fulfillment, and strategies like just-in-time inventory can help minimize holding costs and maintain optimal stock levels.
Technologies like ERP systems help track inventory in real-time, reducing the chances of stockouts or overstocking. This is especially important in a fulfillment center, where inventory is constantly being received, picked, and shipped out.
For your interest: Temu Order Delivery Time
The fulfillment process begins when products arrive at a warehouse, typically on pallets for organization and efficiency. The warehouse performs critical tasks such as sorting the products, storing them in designated areas, and eventually picking and packing them for delivery.
In a fulfillment center, the main activities include receiving, checking, and stowing inventory, generating pick lists and picking products, kitting and assembling shipments, packing boxes, labeling shipments, shipping orders, and managing returns. A fulfillment partner provides these services, making it easier for ecommerce businesses to manage their inventory and improve customer service.
To manage returns efficiently, warehouses should establish a well-defined process that includes implementing return authorization procedures, inspecting returned items, and determining their disposition. This process can help streamline operations, minimize disruptions, and improve customer trust and loyalty.
Here are some key tasks that warehouse managers are responsible for:
- Inventory management
- Budgeting
- Liaising with stakeholders
- Team management
- Performance reporting
By integrating various management systems, such as WMS, order management systems, and customer relationship management software, warehouses can enhance the efficiency of the fulfillment process. This integration allows for seamless communication between different stages of fulfillment, ensuring consistency and reliability.
Intriguing read: Order Picking Systems
Streamlining
Streamlining is key to efficient warehousing and order fulfillment. It's about using technology to automate processes and reduce errors.
Automated picking systems, robotics, and AI-driven software are increasingly being adopted by warehouses to streamline order processing. This enhances accuracy and speed, allowing for rapid order processing and reduced human error.
Effective inventory management within a warehouse is crucial for successful order fulfillment. This involves more than just keeping track of what's in stock; it's about understanding the flow of goods, predicting demand, and ensuring products are available when needed.
Warehouse automation significantly improves efficiency, safety, and customer satisfaction by streamlining operations and minimizing errors. It includes advanced technologies like AI, robotics, drones, and automated vehicles.
Businesses can maintain control of their warehouse operations while leveling them up using a best-in-class warehouse management system (WMS). ShipBob's WMS capabilities include easy-to-learn tools, prescriptive step-by-step packing flows, and location-specific inventory visibility.
Here are some of the key benefits of using a WMS:
- Improved inventory management
- Reduced errors
- Increased scalability
- Enhanced customer satisfaction
By optimizing inventory management, businesses can ensure that their order fulfillment process is not just efficient but also adaptable to changing market demands. This makes it a critical component of a successful operation.
Storage and Space
A good warehouse layout minimizes travel time and boosts storage capacity, resulting in quicker order fulfillment.
Effective use of storage space is key to streamlining operations, involving strategic placement of goods for easy access.
Organizing pallets and items in a way that maximizes space utilization is crucial, ensuring that the most frequently ordered products are easily reachable.
There are different types of warehouses, each designed to suit a particular need. Here are some common types:
Planned and optimized space and layout are crucial for smooth operations and meeting customer needs.
Pick, Pack, and Ship
The pick, pack, and ship process is a crucial part of order fulfillment. It involves a series of coordinated steps to ensure the right product reaches the right customer at the right time.
Picking is the first step, where items are selected from the warehouse and prepared for packaging. This step is often executed with efficiency in mind, allowing businesses to boost productivity.
A good example of kitting is beauty subscription boxes that bundle related products from different manufacturers into a single package. This process can also be used to trim the overall cost of shipping.
Packing is a vital step in the process, where picked items are placed into appropriate packaging and secured for transport. Efficient packing ensures product safety during transit.
Each order is checked with a packing slip before it's taped up and scheduled for pick-up to ensure accuracy and promote on-time arrival. This consistent, high level of quality is met every time with a well-executed packing process.
A well-executed packing process boosts productivity and ensures customer satisfaction by delivering orders accurately and intact.
Take a look at this: Time between Order and Delivery
Returns and Reporting
Returns are a crucial aspect of warehouse operations, ensuring efficient supply chain management and customer satisfaction. By establishing a well-defined process for handling returns, warehouses can streamline operations and minimize disruptions.
Effective returns management improves inventory accuracy, reduces costs associated with returns, and enhances customer trust and loyalty. This is achieved by implementing efficient return authorization procedures, inspecting returned items for quality and condition, and determining appropriate disposition.
Maintaining accurate inventory records is also essential for reporting purposes, allowing businesses to prevent out-of-stock messages to customers and maintain an accurate sales forecast.
Readers also liked: Order and Delivery Management System
Managing Returns
Managing returns is a significant aspect of warehouse operations that ensures efficient supply chain management and customer satisfaction.
By establishing a well-defined process for handling returns, warehouses can streamline operations and minimize disruptions. This process includes implementing efficient return authorization procedures.
Inspecting returned items for quality and condition is crucial to determine their disposition. Effective returns management improves inventory accuracy.
Reducing costs associated with returns is a key benefit of efficient returns management. It also enhances customer trust and loyalty.
Accessing Reports and Analyzing Data
Accessing reports and analyzing data is crucial for optimizing efficiency in the supply chain. Reports provide insights into warehouse operations, such as inventory levels, order fulfillment rates, and storage utilization.
Data analysis helps identify patterns and trends, enabling better decision-making and increased warehouse efficiency. By making data-driven adjustments and optimizations, processes can be streamlined to meet customer demands effectively.
Optimizing warehouse layout, maintaining cleanliness, ensuring effective lighting, conducting regular maintenance and inspections, securing loading docks, and using stretch wraps and safety straps are crucial for efficient warehouse operations.
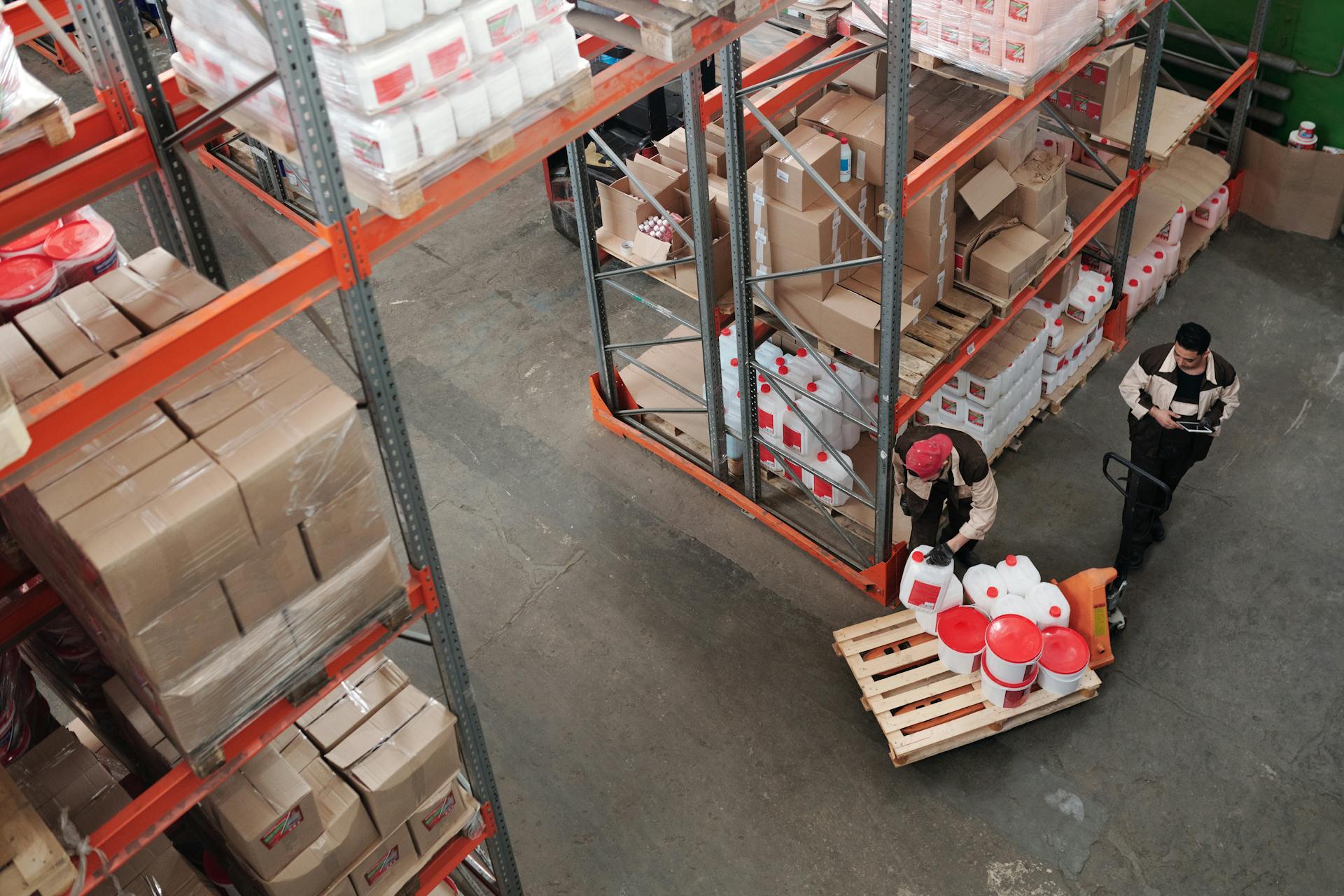
Regular data analysis can help you identify areas for improvement, such as slow-moving inventory or inefficient storage practices. This can lead to cost savings and improved customer satisfaction.
Integrating management systems, such as WMS, order management systems, and customer relationship management software, can enhance the efficiency of the fulfillment process. This integration allows for seamless communication between different stages of fulfillment, ensuring consistency and reliability.
Real-time inventory management and tracking are essential for maintaining a steady cycle of sales and inventory replenishment. This helps prevent stock from going stale on storage shelves and optimizes supply chain costs and efforts.
Software
Software plays a vital role in enhancing warehouse fulfillment. Inventory monitoring with software is a secondary process step that significantly improves efficiency in the supply chain.
By utilizing advanced software systems, warehouses can accurately track and manage their inventory in real-time. This enables automatic data collection, analysis, and reporting, providing valuable insights to make informed decisions and streamline operations.
Warehouse management systems (WMS) are designed to optimize inventory control and logistics. Automation systems improve efficiency and reduce the risk of stockouts or overstocking.
Implementation of software and technology improves logistics, productivity, and customer satisfaction. Careful consideration of pros and cons is important for successful implementation.
Here's an interesting read: Order Picking Software
Future Trends and Growth
The future of order fulfillment is shaped by technological advancements like drone deliveries, automated warehouses, and AI-driven forecasting models.
Drone deliveries are becoming increasingly popular as a way to get packages to customers quickly and efficiently. This trend is expected to continue as companies like Amazon invest heavily in drone technology.
Automated warehouses are also on the rise, using robots and other machines to streamline inventory management and shipping processes. This can help businesses save time and money by reducing labor costs and increasing productivity.
AI-driven forecasting models are another key trend in order fulfillment, helping businesses predict demand and optimize inventory levels. By staying ahead of the curve, companies can avoid stockouts and overstocking, reducing waste and improving customer satisfaction.
Discover more: Best Order Fulfillment Companies
Why Is Essential for Growth
Order fulfillment is essential for business growth because it directly affects customer satisfaction and retention. A well-executed order fulfillment process ensures customers receive their products promptly and in perfect condition.
Timely and accurate fulfillment of orders builds trust and reliability in the brand, encouraging repeat business and positive word-of-mouth. Customer reviews can significantly influence purchasing decisions in the digital age.
Flawless order fulfillment becomes even more essential in competitive markets, and it can be the deciding factor in winning and retaining customers.
Future Trends
The future of order fulfillment is being shaped by technological advancements like drone deliveries, automated warehouses, and AI-driven forecasting models.
Drone deliveries are becoming increasingly popular, offering a faster and more efficient way to get products to customers.
Automated warehouses are also on the rise, streamlining the storage and management of goods.
AI-driven forecasting models are helping businesses predict and prepare for demand, reducing the risk of stockouts and overstocking.
Staying abreast of these trends and innovations is crucial for businesses looking to maintain a competitive edge.
Planning for growth strategically with a fulfillment company like Flowspace ensures you have a vetted source in place and ready to go when the time arises.
A unique perspective: Order Fulfillment Automation
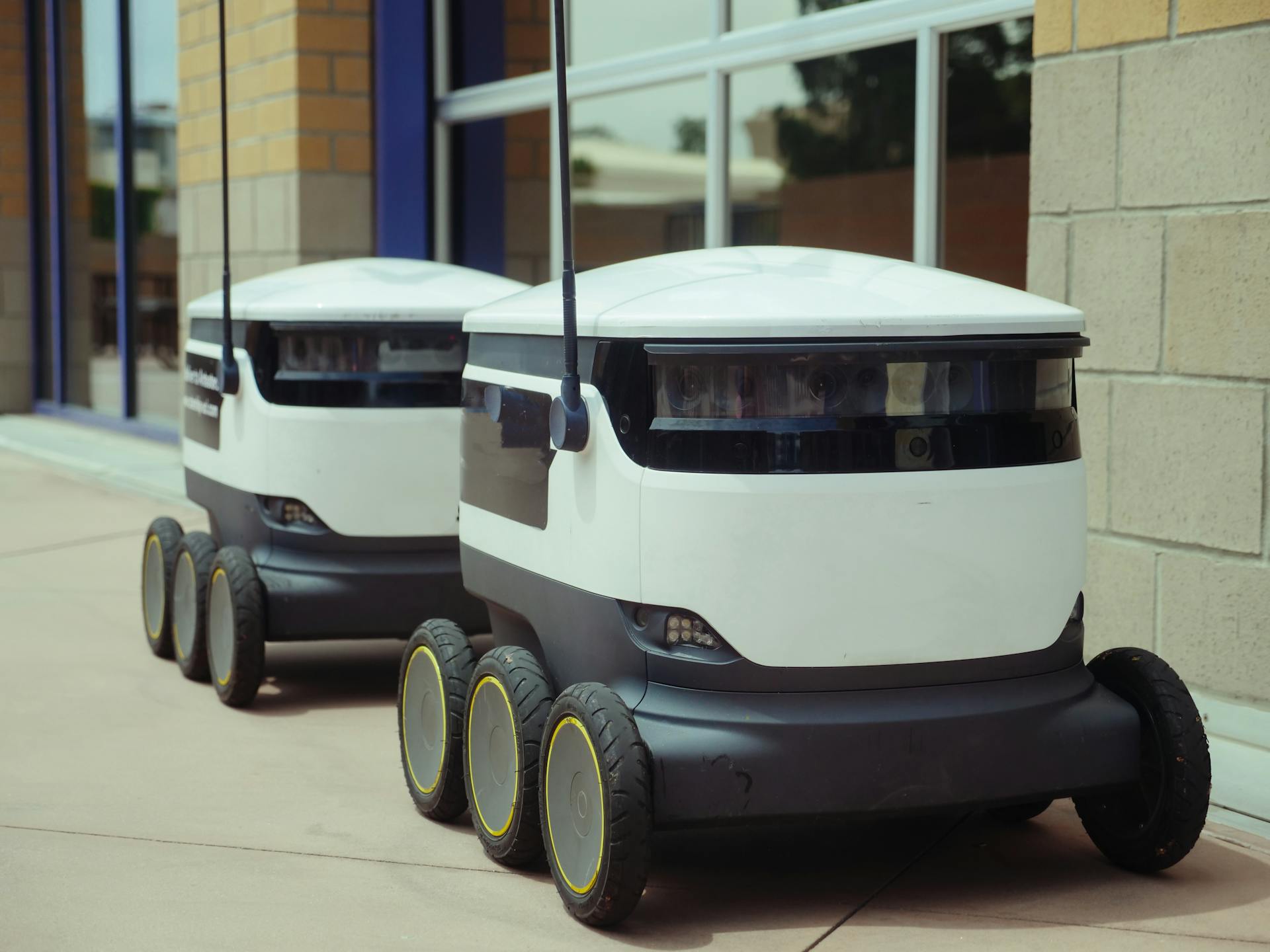
Flowspace can step in and fill the gaps necessary to keep your fulfillment operation running smoothly and reach your business goals, even if you need a solution right away.
The warehousing industry has experienced a significant shift from traditional warehousing to third-party logistics (3PL) warehousing, which offers integrated warehousing and transportation services tailored to global market demands.
Today's 3PL services provide scalable, customized logistics solutions driven by technological and global supply chain complexities.
Curious to learn more? Check out: Warehousing Pick and Pack
Plan Growth with Flowspace
Planning for growth is crucial for e-commerce retailers, and that's where Flowspace comes in. They offer fulfillment services that help brands stay agile as their business grows.
A steady buzz of activity within a fulfillment center allows brands to be agile and adapt to changing demands. This is especially important for e-commerce retailers with a large inventory of products and a growing customer base.
Rather than waiting until the number of orders becomes overwhelming, planning for growth strategically with a fulfillment company like Flowspace ensures you have a vetted source in place and ready to go when the time arises. This approach helps prevent disruptions to your business.
A different take: Small Business Order Fulfillment
If you're in a position where you need a solution right away, Flowspace can step in and fill the gaps necessary to keep your fulfillment operation running smoothly. They're ready to figure out fulfillment solutions with you, no matter what stage of business you're in.
A streamlined order fulfillment process is vital for building customer trust and loyalty, and Flowspace can help you achieve that. By optimizing delivery, enhancing fulfillment, and improving warehouse operations, you can deliver a better customer experience.
Efficient warehouse processes are essential for effective logistics and supply chain management, and Flowspace can help you optimize yours. This leads to reduced costs in storage and transportation, making your business more profitable.
With Flowspace, you can streamline operations, improve accuracy, reduce processing time, and deliver a better customer experience. They offer flexible storage, advanced inventory management, and efficient order fulfillment, making them an ideal partner for e-commerce retailers looking to grow their business.
Choosing the Right Solution
Choosing the right solution for your business needs is crucial for success. You have two options: buy or build your own warehouse, or lease warehouse space from an outside provider.
Larger brands with resources may afford their own warehouse, but for small businesses, leasing is often more cost-effective. This is especially true if they partner with a warehousing provider and rent space in a shared warehouse.
In-house order fulfillment gives you complete control over the warehousing, handling, and shipping processes. However, this can be a complex and time-consuming task, especially for businesses with fluctuating demand.
Outsourced fulfillment transfers these responsibilities to a third-party provider, offering more flexibility and potentially reducing costs. But it may also mean less control over the logistics and fulfillment process.
Unless your goal is simply to store goods for a long period, a fulfillment center is a more valuable solution. Fulfillment centers offer comprehensive services that can help you reach a wider customer base and maintain customer satisfaction.
Companies that choose to operate their own fulfillment centers often limit their capabilities and can't always optimize for fast and/or affordable shipping. This can damage the customer experience and lead to lost business.
A distributed network like Flowspace, which uses a unique Network Optimization algorithm, can provide the flexibility and scalability you need to meet evolving customer expectations. With a distributed network, you can pivot quickly and adjust based on current expectations, delivering fast and affordable shipping without added costs.
3PL Warehouse Solutions can also optimize delivery, enhance fulfillment, and improve warehouse operations. They offer flexible storage, advanced inventory management, and efficient order fulfillment, helping you streamline operations and improve accuracy.
Explore further: Temu Minimum Order for Free Shipping
Warehouse and Distribution
A warehouse is a large storage center or industrial space designed to house inventory in bulk, and a warehousing solution refers to a company that stores products on a business's behalf within their warehouses for an extended period of time.
You have two options when it comes to acquiring warehouse space: buy (or build) your own, or lease warehouse space from an outside warehousing provider. Leasing warehouse space is typically more cost-effective for small businesses, especially if they partner with a warehousing partner and rent space in a warehouse in conjunction with other ecommerce businesses.
Here are some common types of warehouses:
- Private warehouses: A storage facility owned and operated by a specific company for their exclusive use or by a third-party logistics (3PL) company on behalf of a client.
- Public warehouse: A storage facility shared by multiple companies and typically owned and operated by a 3PL company that works with multiple clients.
- Automated warehouse: A facility in which various aspects of storage, retrieval and the movement of goods are mechanized and managed by automated systems.
- Climate-controlled warehouse: A facility equipped with specialized temperature and humidity control systems to preserve the quality and integrity of sensitive or perishable goods.
- On-demand warehouse: A facility that provides storage space to businesses on an as-needs basis, offering temporary or short-term warehousing space.
- Distribution center: A specialized form of warehouse designed to receive, store, process and distribute products to retailers, wholesalers or directly to consumers.
Typical Services
A warehouse solution can refer to a company that stores products on a business's behalf within their warehouses for an extended period of time.
There are different types of warehouses, including private warehouses owned by one organization, public warehouses that are sub-leased to retailers, and automated warehouses that use technology and robotics to automate their processes.
A fulfillment center offers a range of services, including receiving and inventory management, short-term storage, order fulfillment, drop shipping, and last-mile delivery.
Some fulfillment centers also provide value-added services, such as cross-docking, kitting and assembly, specialized handling, labeling and barcoding, subscription box services, custom packaging, promotional inserts, repackaging, returns management, and transportation optimization.
Here are some examples of value-added services offered by fulfillment centers:
- Cross-docking
- Kitting and assembly
- Specialized handling
- Labeling and barcoding
- Subscription box
- Custom packaging
- Promotional inserts
- Repackaging
- Returns management
- Transportation optimization
Warehousing solutions, such as 3PL warehouse solutions, can optimize delivery, enhance fulfillment, and improve warehouse operations by offering flexible storage, advanced inventory management, and efficient order fulfillment.
Warehouse

A warehouse is a large storage center or industrial space designed to house inventory in bulk. Warehouses can be dedicated to storing only certain types of inventory, such as wholesale business inventory.
There are two main options for acquiring warehouse space: buying or building your own, or leasing warehouse space from an outside warehousing provider. Leasing warehouse space is typically more cost-effective for small businesses.
A warehouse process refers to the activities and procedures involved in optimizing the efficiency of a warehouse, ensuring timely delivery of goods to customers. This includes streamlining operations, implementing automated inventory management and order-picking systems, and balancing automation with human labor to maximize productivity.
Types of warehouses include private warehouses, public warehouses, automated warehouses, climate-controlled warehouses, and on-demand warehouses.
Here are some key differences between warehouses and distribution centers:
Warehouse solutions, on the other hand, refer to a company that stores products on a business's behalf within their warehouses for an extended period of time. Warehouse solutions can be a cost-effective option for businesses that don't have the resources to build or maintain their own warehouses.
3PL warehouse solutions optimize delivery, enhance fulfillment, and improve warehouse operations. They offer flexible storage, advanced inventory management, and efficient order fulfillment. With 3PL warehouse solutions, you can streamline operations, improve accuracy, reduce processing time, and deliver a better customer experience.
Check this out: How to Improve Order Fulfillment Process
Legacy and Full Package
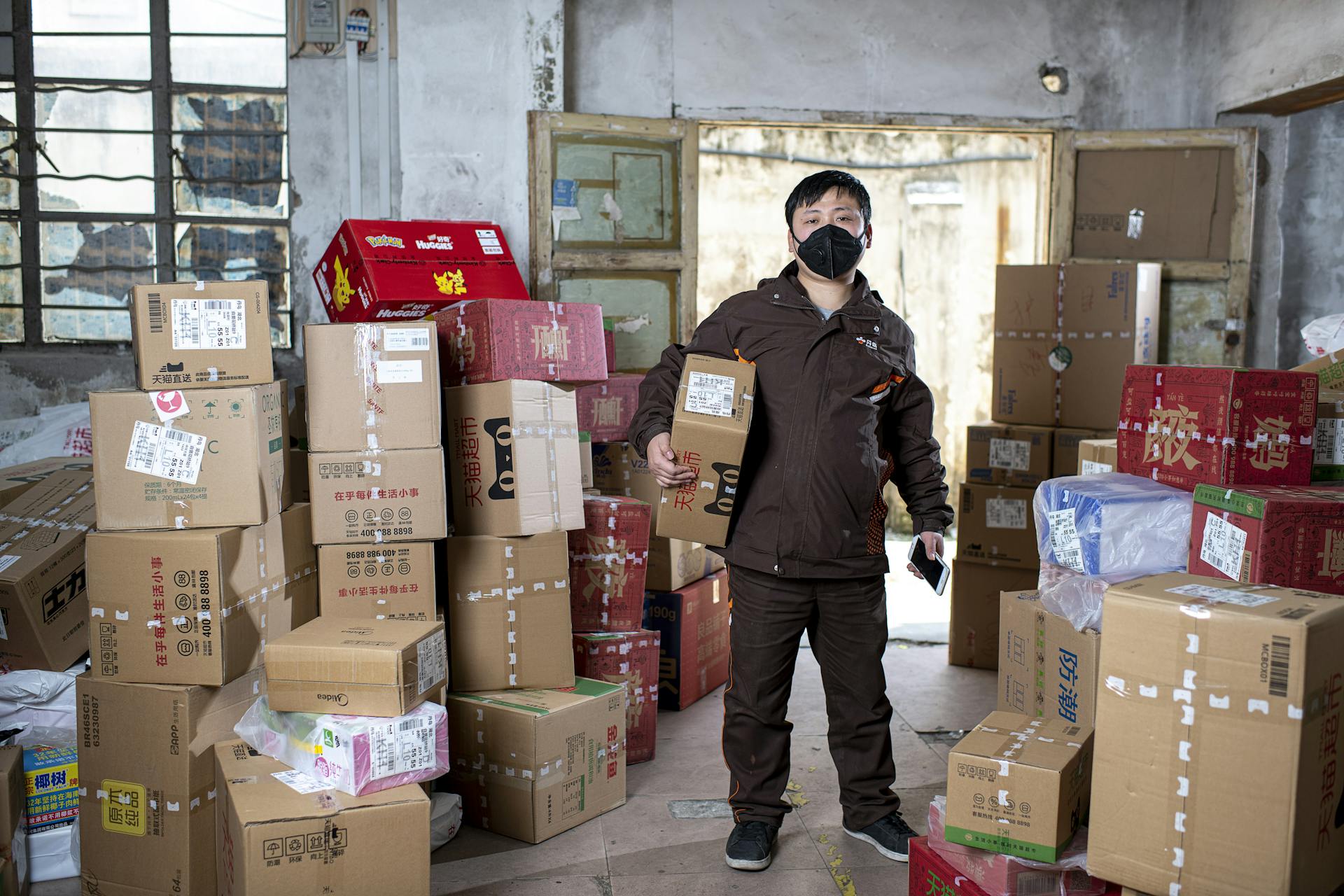
Legacy Supply Chain has over 40 years of experience in providing logistics services, including dedicated contract warehousing and omni-channel distribution.
This extensive experience allows them to deliver world-class customer service and navigate supply chain complexity with ease. Legacy Supply Chain's expertise is built on decades of on-the-job experience.
A streamlined order fulfillment process is crucial for ecommerce, ensuring timely delivery, maintaining product quality, and reducing errors. This is vital for building customer trust and loyalty.
Legacy Supply Chain provides full-service logistics, including warehousing and fulfillment, to help businesses optimize operations and build dependable connections with their customers.
Frequently Asked Questions
What is the difference between warehousing and fulfillment?
A warehouse primarily stores inventory, whereas a fulfillment warehouse handles storage, processing, and shipping of orders, offering a more comprehensive service. This key difference makes fulfillment warehouses more complex and dynamic than traditional warehouses.
What are FCs in supply chain?
Fulfilment centres (FCs) are facilities that store and manage inventory for efficient order processing and shipping. They play a crucial role in the modern supply chain by ensuring timely and accurate delivery of products to customers.
Sources
- https://www.shipbob.com/blog/differences-warehouse-fulfillment-center/
- https://phasev.com/blog/understanding-the-role-of-warehouses-in-the-fulfillment-process/
- https://flow.space/blog/fulfillment-center-vs-warehouse/
- https://www.inboundlogistics.com/articles/warehousing-process/
- https://legacyscs.com/fulfillment-center-vs-warehouse/
Featured Images: pexels.com