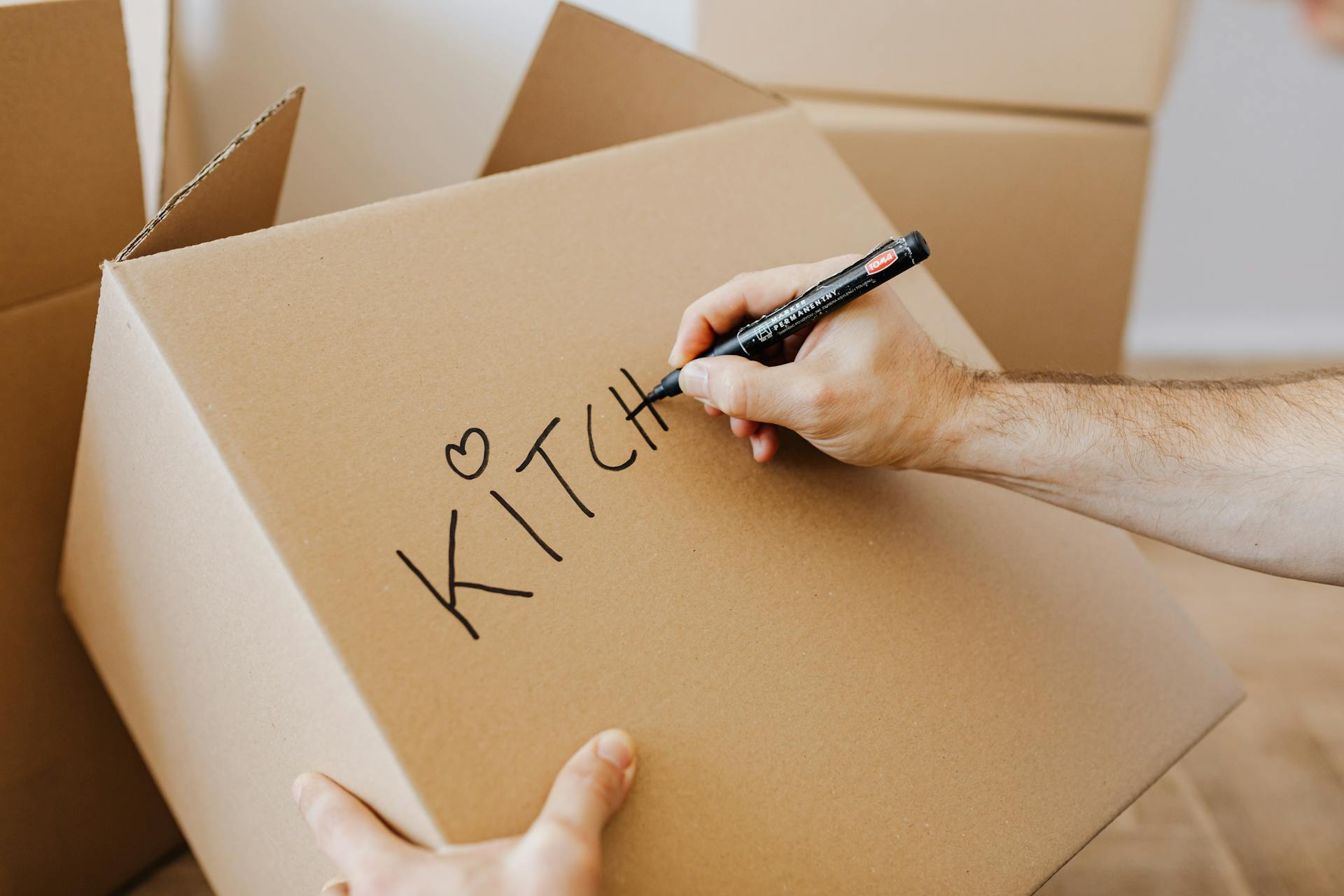
Streamlining order fulfillment is crucial for businesses to remain competitive in today's fast-paced market. Efficient pick and pack processes can make all the difference.
A well-designed warehouse layout can reduce pick times by up to 30%. This is achieved by minimizing travel distances and optimizing storage locations.
Effective labeling and signage are essential for accurate picking. Labels should be clear, easy to read, and placed in a consistent location on each item.
Accurate inventory management is critical for efficient pick and pack operations. A discrepancy of just 1% in inventory accuracy can result in over 100 incorrect orders per day.
Order Management
Order Management is a crucial aspect of a streamlined pick and pack process. By optimizing order management, you can minimize errors and ensure customer satisfaction.
Volume inventory storage places the SKUs with the highest turnover closest to the packing station, minimizing the steps staff take when order picking. This helps to reduce errors and increase efficiency.
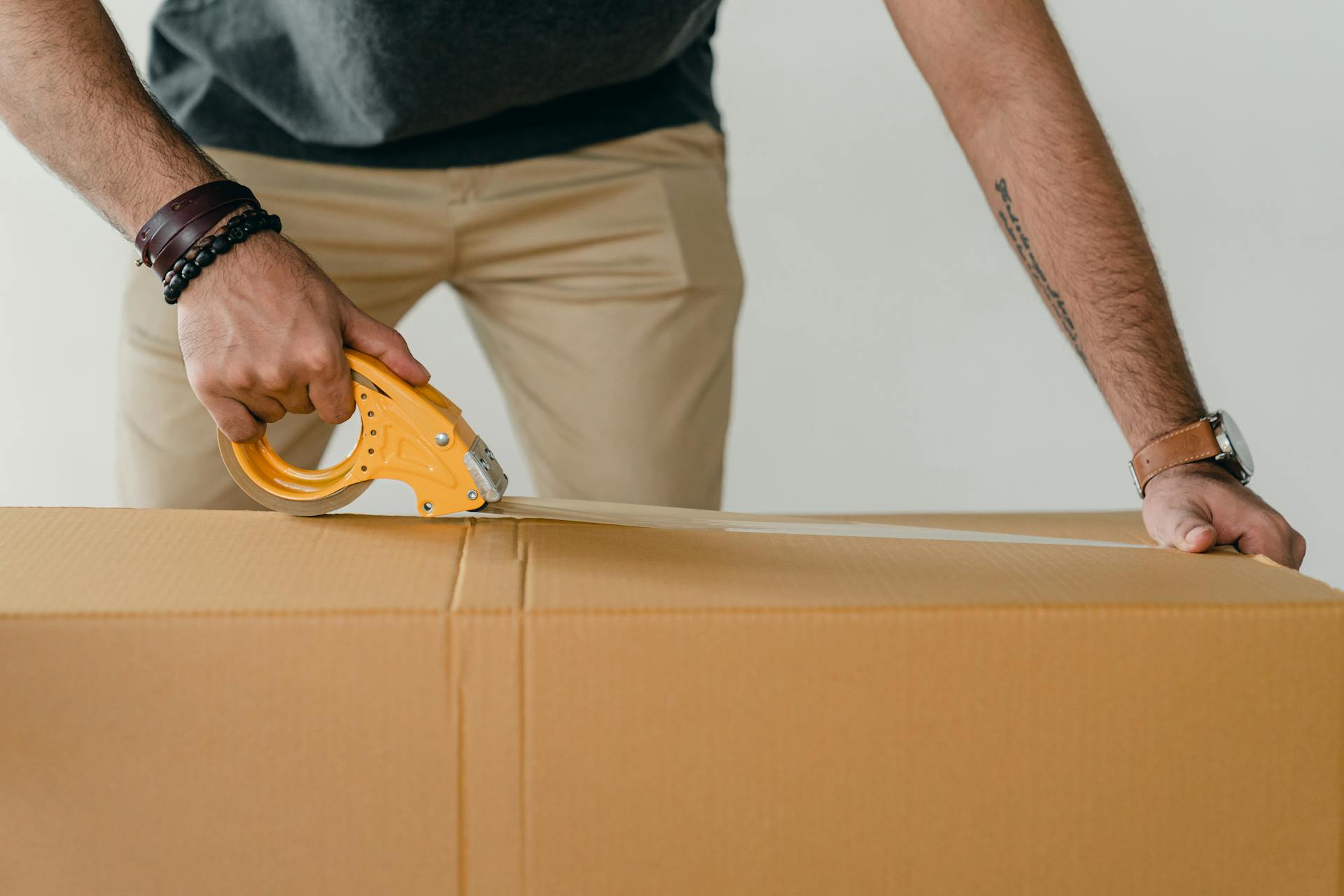
To ensure accuracy, it's essential to have the right processes in place during the packing stage. This is the last chance for warehouse packing teams to check picking accuracy, making sure the right quantities of the right items go in the box before it's sealed and shipped.
Picking orders can be done in various ways, including piece picking, batch picking, zone order picking, and wave picking. Each method has its own advantages, but the key is to find the one that works best for your operation.
Here are some common picking methods:
By implementing the right order management strategies and technologies, you can optimize your pick and pack process, reduce errors, and improve customer satisfaction.
Orders
Orders are a crucial part of the order management process, and there are several picking strategies that can help streamline fulfillment. Piece picking is one such strategy where an employee handpicks each product for an entire order as they come in.
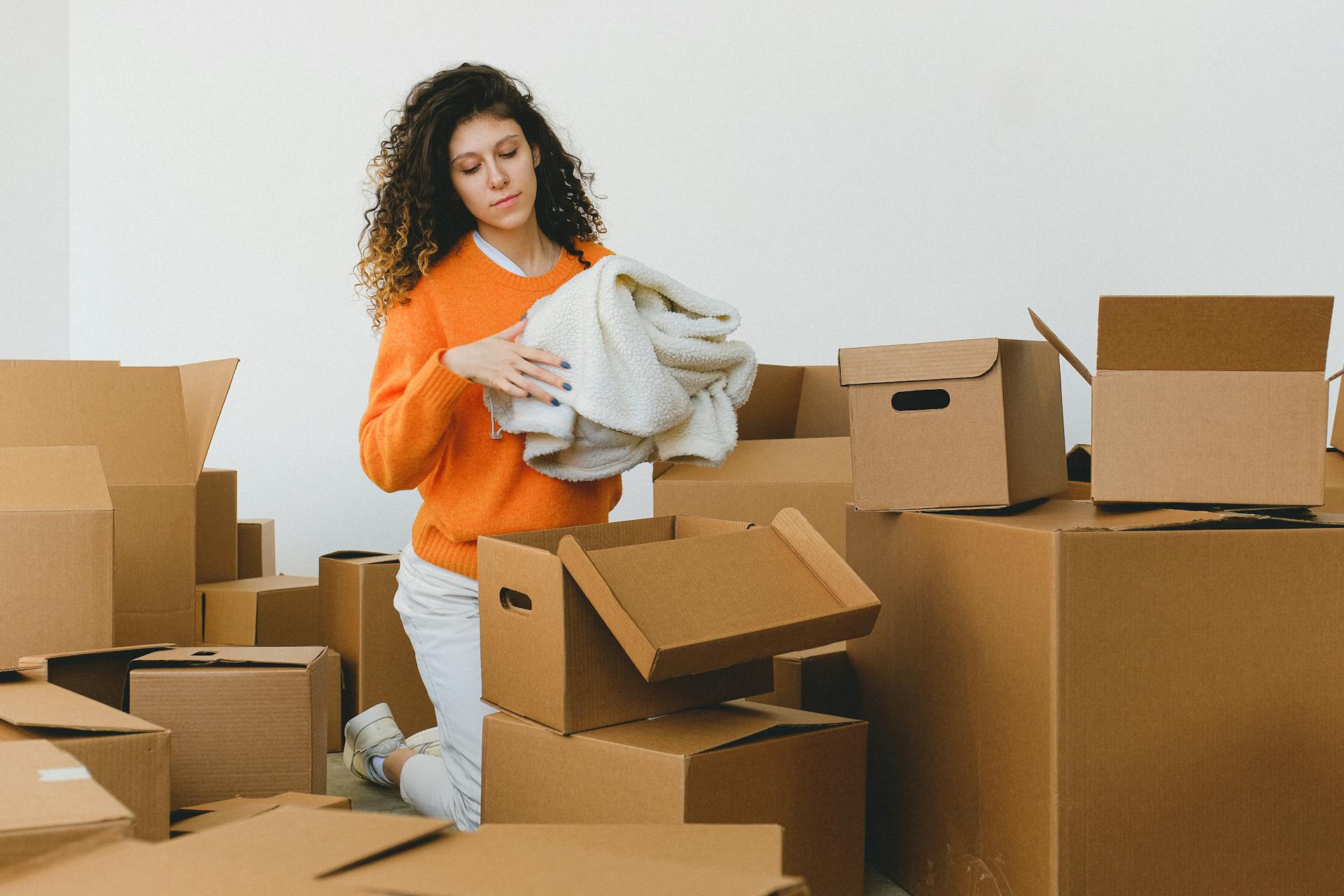
Batch picking is similar to piece picking, but orders are done in batches all at once instead of one at a time. This can help increase efficiency, but it requires careful planning to ensure accuracy.
Zone order picking is another strategy where employees are assigned to a specific area of the warehouse and only pick one order at a time within that area. If an order needs products from more than one zone, it is handed off via conveyor belt.
Wave picking is a combination of batch and zone picking, where employees stay within a zone but pick more than one order at a time. This can be a good option for warehouses with a high volume of orders.
Here are some picking strategies at a glance:
Order Management Systems
Adopting an order management system is crucial for efficient order fulfillment. It tracks inventory and communicates information in real-time, ensuring accuracy and preventing stockouts.
The right order management system can improve order fulfillment efficiency by planning routes and tracking inventory. This can be achieved through the integration of warehouse management technology.
Inventory software can manage stock across multiple locations, making it easier to maintain accuracy. A single source of truth for managing stock, sales, and other business data is essential for a holistic view of operations.
Finding a platform that integrates with your existing technology suite is key to implementing an effective order management system. This ensures seamless communication and data synchronization.
Inventory Management
Inventory management is crucial for efficient pick and pack operations. A well-implemented inventory management system can make or break your warehouse's productivity.
Consider implementing volume inventory management, where products with the highest turnover are stored closest to the packing station, reducing time spent picking. This strategy minimizes steps staff take when order picking.
Class-based inventory management can also be effective, grouping items by shared traits like turnover or packing methods. For example, grouping products that need bubble wrap or large items that don't require an additional box.
A picking list is the information sent to warehouse pickers after a customer has made an order, including products to pick, their locations, the picking route, and shipping data.
Curious to learn more? Check out: Wine Glass Moving Box
Volume Inventory Management
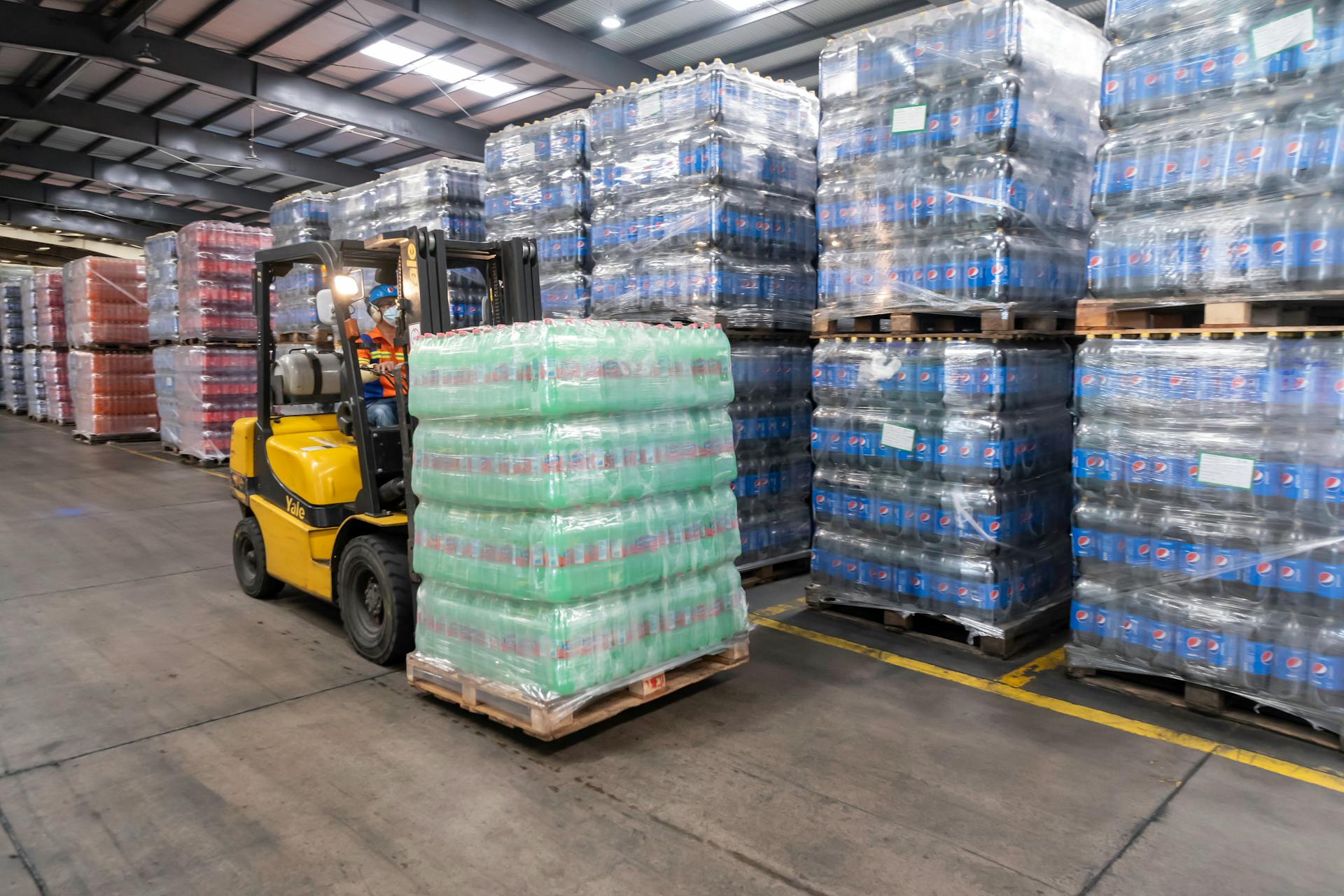
Volume inventory management is a game-changer for warehouses. It involves storing SKUs with the highest turnover closest to the packing station, while slower-selling products are stored farther away. This simple yet effective strategy minimizes the steps staff take when order picking.
By placing fast-moving products near the packing station, pickers can quickly grab what they need and move on to the next task. This reduces the time spent on picking and packing, making the entire process more efficient.
In fact, volume inventory management can cut down on the steps staff take by a significant amount. This not only saves time but also reduces the risk of errors and improves overall productivity.
To implement volume inventory management, you can group your products by their turnover rates and store them accordingly. This might involve rearranging your shelves or using a combination of storage solutions to keep your most popular products within easy reach.
With the right system in place, you can enjoy faster picking and packing times, reduced labor costs, and improved customer satisfaction. It's a win-win for everyone involved!
Intriguing read: Packing List Alaska
What Is a List?
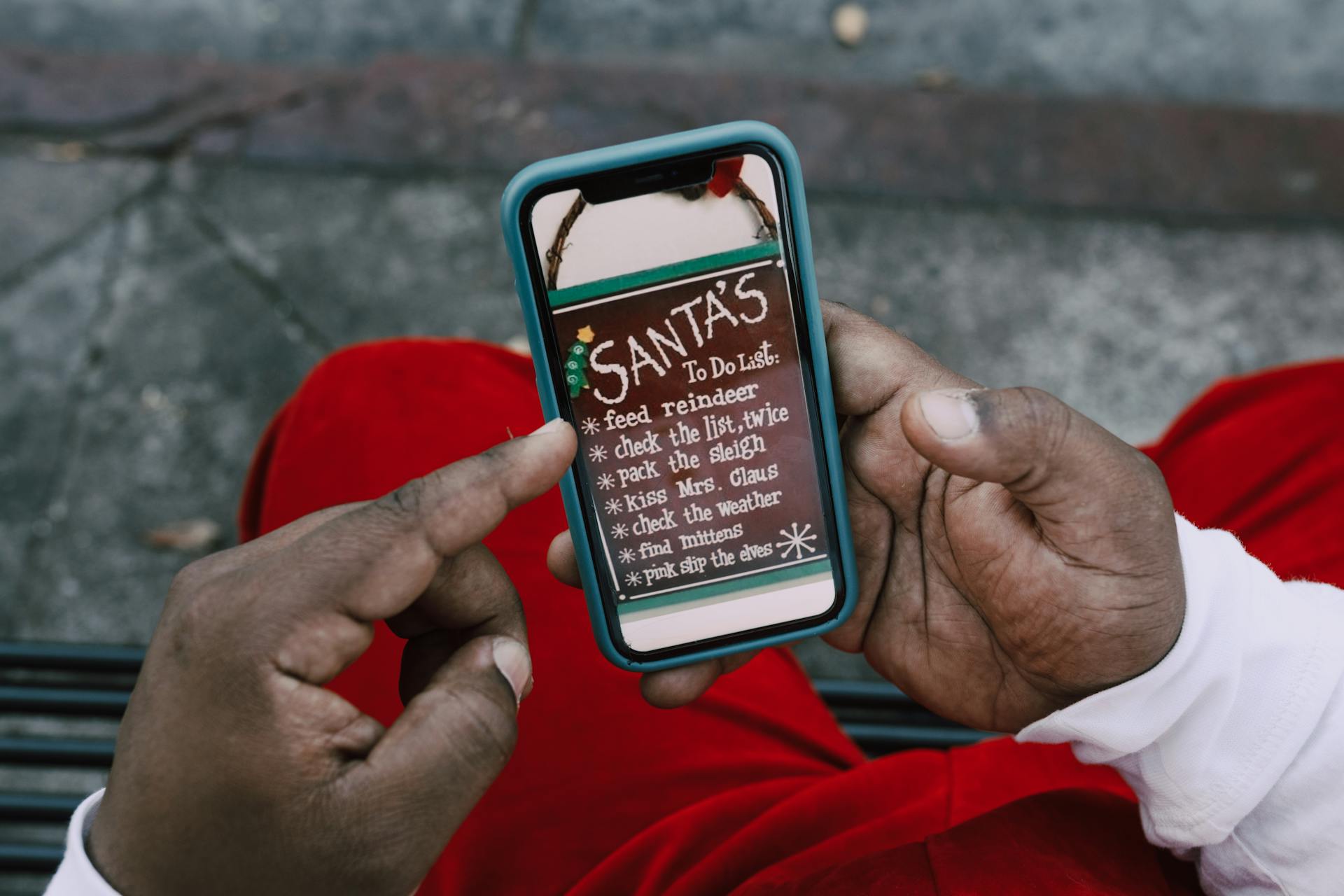
A list is a crucial component of inventory management, and it's used to keep track of the products and items you need to pick and ship to customers. It's essentially a document that outlines what needs to be picked and where it's located in the warehouse.
A picking list, for example, is sent to warehouse pickers after a customer has made an order, and it includes the list of products and items that need to be picked, along with their location and shipping data.
Having accurate and up-to-date lists is essential to ensure that the right products are picked and shipped to the right customers on time. This helps to prevent errors and delays, and it also helps to improve customer satisfaction.
A picking list typically includes the picking route, which is the sequence in which the products are to be picked from the warehouse. This helps the pickers to efficiently navigate the warehouse and pick the products in the correct order.
Expand your knowledge: Alaska Packing List Pdf
Picking and Packing Methods
Picking and packing methods are crucial for efficient order fulfillment. As your ecommerce business grows, you may need to evolve your warehouse picking and packing methods to meet demand.
Startups and early-stage companies may get away with picking items one at a time, but as you sell more, advanced warehouse picking methods can create speed. Your pick and pack system should match your inventory and order complexity.
Here are four common warehouse picking and packing methods to consider: Piece picking, where an employee handpicks each product for an entire order as they come in.Batch picking, where orders are done in batches all at once.Zone order picking, where employees are assigned to a specific area of the warehouse and only pick one order at a time.Wave picking, a combination of batch and zone picking, where employees stay within a zone but pick more than one order at a time.
What Is the Process?
The picking and packing process can be complex, but it starts with receiving an order. The warehouse management technology, or WMS, tells your team which items to pick, where they are, and in what order to pick them.
Inventory software manages stock across multiple locations, keeping everything accurate and preventing stock outs. This is especially helpful when items are stored in different places.
An efficient pick and pack approach speeds up order fulfillment activities and enables goods to be inventoried, stored, picked, and packed in one location. This shortens the process of assembling products from various storage facilities and sending them to another location for packing and labeling.
The WMS acts as a single source of truth for managing stock, sales, and other business data, offering a holistic view of your operations.
Mobile Shelf-Based Order Systems
Mobile Shelf-Based Order Systems can be a game-changer for warehouses looking to boost efficiency. Mobile shelf-based order pick (MSOP) systems, as mentioned in Example 3, bring shelves to the picker and then return them to the warehouse floor. This innovative approach can help reduce travel time and increase picking speed.
To implement a mobile shelf-based order system, consider the following benefits:
- Reduced travel time, which can account for up to 55% of order-picking time (Example 16)
- Increased picking speed, allowing for faster order fulfillment
- Improved picker productivity, as they can focus on picking items without having to travel long distances
However, it's essential to weigh the costs and benefits of implementing a mobile shelf-based order system. This may require significant investment in technology and infrastructure, but the long-term gains in efficiency and productivity can be substantial.
Protect with Infill
Protecting your items with infill is a great way to prevent them from shifting in boxes during shipping.
Infill, like shredded cardboard and packing peanuts, provides a much-needed cushioning effect.
For larger items, you may need custom infill, including molded inserts or a mix of infill types.
Using branded infill can complement branded packaging and add a professional touch to your shipping.
Effective Inventory Storage Strategy
Implementing an effective inventory storage strategy is crucial for improving picking and packing speed. This involves considering how you store inventory across the warehouse.
Store high-volume items in easily accessible locations to save time and make picking easier for staff. By doing so, you can reduce the time spent picking.
Consider using volume inventory management, where products with the highest turnover are stored nearest to the packing station. This helps to reduce time spent picking.
Extending shelves upward organizes items while maximizing your warehouse's carrying capacity. Just make sure to implement safety requirements to help staff reach items easily.
An inventory management system is often used by warehouses to help further improve the picking and packing workflow.
Efficiency and Optimization
Efficiency and Optimization is crucial for a smooth pick and pack process. A streamlined workflow helps complete orders with minimal errors, ensuring customers receive items on time.
Picking and packing software can make or break your process, improving order fulfillment efficiency by tracking inventory, planning routes, and communicating information every minute. This technology can also manage stock across multiple locations, maintaining accuracy and preventing stock outs.
To boost efficiency, plan optimal picking routes to reduce traveling time and use automation and technology to reduce mispicks. Store inventory strategically so that popular items are placed near the packing station, minimizing the steps staff take when order picking.
Here are some key benefits of implementing a Warehouse Management System (WMS) or picking and packing software:
- Automated workflows
- Optimized stock control
- Advanced location management
- Reduced costs and mispicks
Maximize Efficiency with Management Tech
A warehouse management system (WMS) is strongly recommended for a warehouse to perform at its best. By using cloud-based warehouse management software, warehouses can benefit from automated workflows, optimised stock control and advanced location management.
Automated workflows and streamlined processes can reduce order completion time and keep customers happy. Picking and packing software supports businesses the most during the pick and pack process.
The right WMS can help warehouses as they grow and scale, ensuring a growing volume of sales and increasingly complex orders are processed with ease. This is crucial when trying to keep up with competitors.
Here are some key benefits of adopting warehouse management tech:
- Improved order fulfillment efficiency by tracking inventory, planning routes, and communicating information every minute.
- Inventory software manages stock across multiple locations, maintaining accuracy and preventing stock outs.
- Automated workflows and streamlined processes reduce order completion time and keep customers happy.
Optimize for Dimensional Weight
Optimizing for dimensional weight can make a significant difference in your shipping costs. This pricing structure measures the size of a package to calculate a weight equivalency, which can be costly for large or heavy items.
Some products, like shipping large or heavy items, are subject to dimensional weight pricing. This can lead to increased shipping costs.
Compact packaging can help reduce your pick and pack fee based on packaging materials and your dimensional weight. By optimizing your packaging, you can save on shipping costs.
Software and Technology
Software and Technology plays a crucial role in the efficiency and accuracy of warehousing pick and pack operations.
To ensure smooth pick and pack processes, each step must happen in coordination with the others, requiring a clear understanding of who is handling which orders and when items are ready to flow to the next stage.
Inventory and warehouse software solutions, including the warehouse management system, tie this information together.
Pick and pack software connects warehouse activity and communication, automating certain tasks and providing real-time updates.
Here's an overview of how pick and pack software works:
- Order integration: Software connects to sales channels and receives new orders.
- Picking: Staff receive picking lists and optimized paths on mobile devices, allowing them to see item details, locations, and quantities.
- Packing: Picked items are scanned, and packing tasks are assigned based on weight, size, and order requirements.
- Shipping: The software generates shipping labels with accurate weight and address information, streamlining the dispatch process.
By leveraging automation, picking and packing software optimizes tasks like generating packing lists, locating items, and integrating with other systems in the warehouse.
This ensures accurate reporting and allows for the tracking of metrics such as pack accuracy and stock levels.
Operations and Logistics
Optimizing your warehouse operations is crucial for efficient pick and pack processes. Streamlining warehouse operations can lift your business to new heights, but you need an all-in-one solution like Fishbowl to achieve that level of synergy.
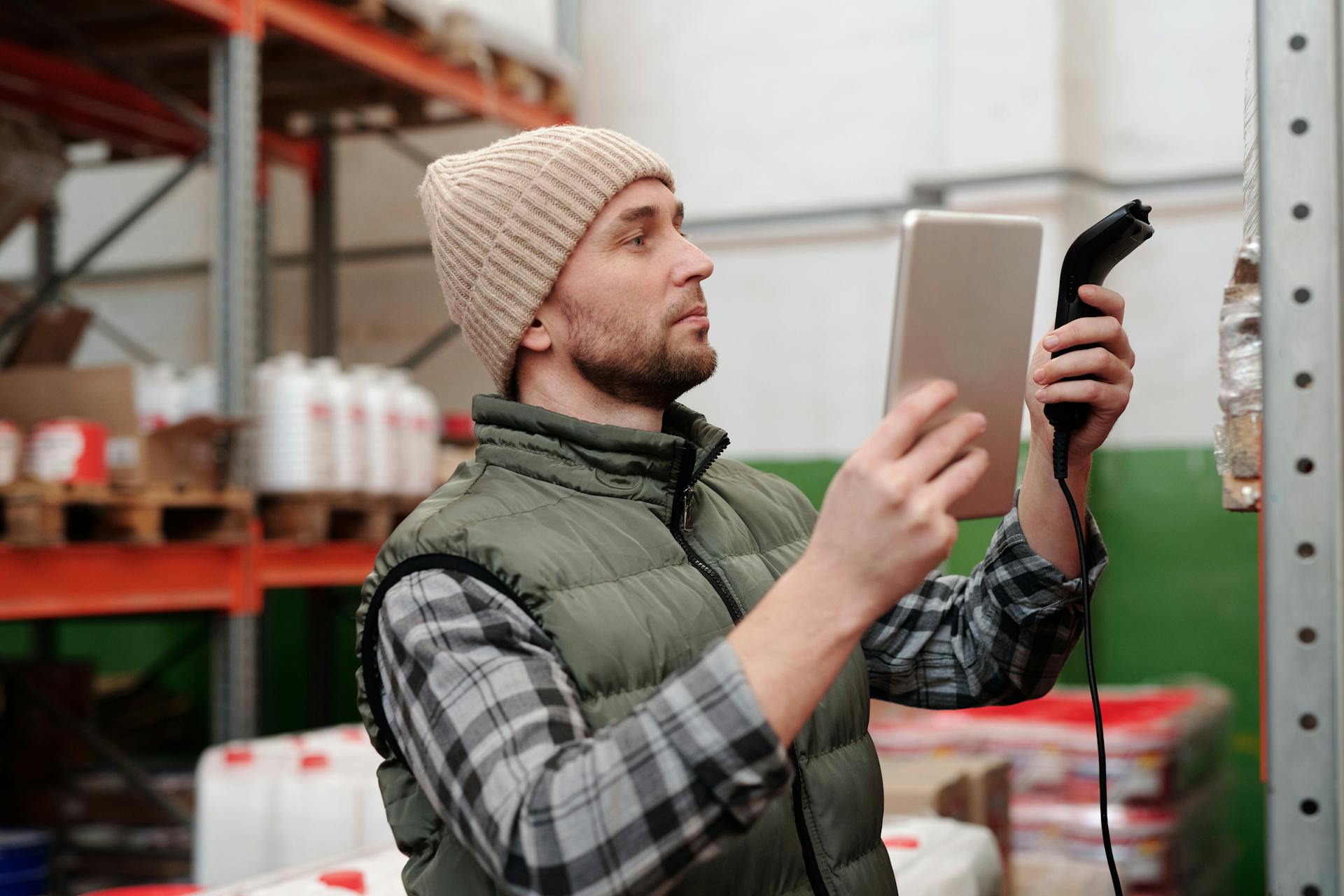
Warehouse picking and packing are key processes that impact the time an order spends in a warehouse, accounting for about 55% of warehouse operating costs. Researchers and warehouse operators have been working on improving order picking for a long time.
Volume inventory management is a strategy where SKUs with the highest turnover are stored closest to the packing station, minimizing the steps staff take when order picking. This approach can significantly improve efficiency.
The right warehouse management technology can make or break your picking and packing process, improving order fulfillment efficiency by tracking inventory, planning routes, and communicating information every minute. A WMS acts as a single source of truth for managing stock, sales, and other business data.
Here are some key warehouse management metrics to track:
- Order fulfillment rate
- Inventory turnover rate
- Picking accuracy rate
- Warehouse stock levels
- Shipping and delivery times
Adopting warehouse management tech is essential for maximizing efficiency, and finding a platform that integrates with your existing technology suite is crucial. This way, your WMS offers a holistic view of your operations.
Returns and Errors
Returns can be a significant issue in warehousing pick and pack, with up to 20% of orders being returned due to incorrect or missing items.
The key to minimizing returns is to have a clear understanding of what is being picked and packed. This includes accurate labeling and inventory management, as seen in the example of XYZ Corporation's use of barcode scanning to verify inventory levels.
Returns can also be caused by errors in the packing process, such as overstuffing boxes or failing to include essential items. This is why it's essential to follow a standardized packing procedure, such as the one used by ABC Warehouse, which includes double-checking each box before sealing it.
Return
Returns can be a significant challenge for warehouse management. Efficiency in picking is crucial for warehouse management.
A warehouse picker will then pick the correct items from the warehouse shelves using the packing slip. Efficiency here is absolutely crucial for warehouse management.
Different warehouses will use different picking methods, depending on inventory storage, order volume and other factors. This can lead to errors if not managed properly.
Preventing Errors with Barcodes
Barcodes are a simple yet effective way to prevent errors in the pick and pack process. They can significantly improve picking accuracy.
Picking is a labour-intensive process that can often result in mispicks, leading to costly errors and unhappy customers. Mobile barcode scanning software can help reduce errors and costly mistakes.
Barcode scanning software can also help suggest optimal picking routes for each individual warehouse worker. This can help streamline the picking process and reduce errors.
Barcodes can be integrated with WMS technology to facilitate better route planning. This can help warehouses optimize their operations and reduce errors.
Automated warehouse technology, such as barcode scanning, is becoming increasingly common amongst modern warehouses. Warehouses that don't invest in barcode scanning may be left behind by their competitors.
Best Practices and Strategies
Establishing best practices in your warehouse improves efficiency and accuracy. Having the right processes in place can help make sure your pick and pack order fulfillment drives customer satisfaction.
Accuracy at the packing stage is crucial, as it's the last chance to check picking accuracy and ensure the right quantities of the right items go in the box before it's sealed and shipped. This can help reduce the risk of returns, which incur reverse logistics and restocking costs and may disappoint customers.
To optimize your pick and pack service, consider using pack strategies such as piece picking, batch picking, zone picking, and wave picking. These methods can help reduce the labor required to choose the right products for an order, streamlining the fulfillment process and reducing costs.
Choosing an effective inventory storage strategy is essential to improve picking and packing speed. Storing products with the highest turnover nearest to the packing station can help reduce time spent picking.
Warehouse Management Systems
Warehouse Management Systems play a crucial role in maximizing efficiency in your picking and packing process. They track inventory, plan routes, and communicate information in real-time, making them a game-changer for order fulfillment.
A Warehouse Management System (WMS) tells your team which items to pick, where they are, and in what order to pick them, ensuring accuracy and speed.
The right WMS integrates with your existing technology suite, acting as a single source of truth for managing stock, sales, and other business data. This provides a holistic view of your operations and helps maintain accuracy across multiple locations.
Warehouse Management Systems can help you overcome common challenges like stock outs by managing inventory across multiple locations. This is especially important for maintaining accuracy and preventing stock outs.
A good WMS will also help you track key performance indicators (KPIs) that are essential for improved operations, such as inventory levels, order fulfillment rates, and shipping times.
Shipping and Fulfillment
Shipping and Fulfillment is a crucial step in the pick and pack process. ShipBob is a tech-enabled 3PL that offers accurate and speedy shipping services to ecommerce businesses.
The final step in the pick and pack process is shipping, where the team sorts and labels orders for dispatch. You need to work with reliable carriers that balance cost, speed, and reliability.
Shipping involves preparing packages for collection from the carriers, and it's essential to have a system for tracking packages and giving customers updates so they know when their orders will arrive. This limits strain on your customer support from curious buyers.
What Is Fulfillment?
Fulfillment is the process of getting products to customers after they've placed an order. It involves several steps, including warehouse picking and packing.
Warehouse picking is a crucial part of fulfillment, where staff use a picking list to find and retrieve the right quantities of each product from its location in the warehouse.
Picking and packing are often done together, as they're essential steps in preparing orders for shipping.
In a warehouse, picking and packing are the processes that occur after an order is placed from an online store.
Shipping
Shipping is a crucial step in the pick and pack process, and it's essential to work with reliable carriers that balance cost, speed, and reliability.
You need to choose carriers that can deliver packages efficiently and on time. This is vital for maintaining a good reputation and keeping customers happy.
To keep everything organized, you should have a system for tracking packages and giving customers updates on when their orders will arrive. This limits strain on your customer support from curious buyers.
Kitting and Outsourcing
Kitting is a specialized kind of pick and pack service that involves assembling various SKUs into a single SKU to create a subscription pack or promotional bundle.
Packing for kitting may require adjusting warehouse packing techniques monthly or as new promotions arise.
This flexibility is key to keeping up with changing customer demands and promotions.
Kitting
Kitting is a specialized kind of pick and pack service where your warehouse assembles various SKUs into a different, single SKU to create a subscription pack or promotional bundle.
This process may require adjusting warehouse packing techniques monthly or as new promotions arise. Packing for kitting can be a complex task, but integrated data can inform targeted promotions and upselling opportunities.
Outsourcing
Outsourcing can be a game-changer for businesses looking to streamline their pick and pack operations. A 3PL, or third-party logistics provider, can help with labor costs, shipping, and other supply chain considerations.
Fluctuating order volumes are a key indicator for outsourcing. Seasonal or market-driven changes in order quantities can be handled more effectively by a 3PL.
The expertise and infrastructure of a 3PL can enhance order accuracy and reduce errors. This is especially important for businesses with high SKU volumes.
Cost considerations play a crucial role in the decision-making process. A 3PL may offer a more favorable pick and pack fee based on order fulfillment and SKU volumes.
Outsourcing eliminates the need for substantial upfront investments in pick and pack warehouse space and other resources. This shift to variable costs provides financial flexibility and allows businesses to allocate resources strategically.
Sources
- https://redstagfulfillment.com/ultimate-guide-pick-and-pack-methods/
- https://www.shipbob.com/ecommerce-fulfillment/pick-pack-fulfillment/
- https://www.fishbowlinventory.com/blog/warehouse-picking-and-packing-everything-you-need-to-know
- https://www.mintsoft.com/warehouse-management/picking-and-packing/
- https://6river.com/advantages-of-pick-and-pack-order-fulfillment-for-logistics-operators/
Featured Images: pexels.com