
The kraft paper machine is a highly efficient and versatile production line that can produce a wide range of paper products. It's a crucial component in the paper manufacturing process.
The machine's production process involves several key steps, including pulping, screening, and bleaching. The pulping process involves breaking down wood chips or other plant material into a pulp, which is then mixed with water to create a uniform consistency.
The kraft paper machine can produce paper with a wide range of thicknesses, from 50 gsm to 500 gsm. This makes it suitable for various applications, including packaging, printing, and specialty paper products.
One of the machine's key capabilities is its ability to produce paper with high strength and durability. This is due to the use of a strong and flexible wire mesh, which helps to create a smooth and even surface.
Recommended read: Corrugated Paperboard Production Line
Types of Kraft Paper Machines
There are several types of kraft paper making machines, each with its own unique features and applications. One type is the kraft paper plant, which is a large production line used to create industrial-scale quantities of kraft paper from wood and chemical slurry.
The kraft paper plant is ideal for producing strong paper products used mainly for packaging, wrapping, and other heavy-duty applications. Another type is the kraft paper roll machine, which produces paper in roll form and includes automatic paper rewinding and cutting devices for smaller size paper sheets.
Here are the different types of kraft paper making machines:
- Kraft paper plant: Industrial-scale production line for strong paper products
- Kraft paper roll machine: Produces paper in roll form with automatic rewinding and cutting devices
- Kraft paper sheet machine: Creates fixed-sized sheets of paper for customers and retailers
- Kraft paper board machine: Produces thicker and denser paper for solid packaging needs
- Automatic kraft paper machine: Includes automated features like pulp feeding system and finished product stacking facility
Types of
There are several types of kraft paper making machines, each designed to produce specific types of paper products.
A kraft paper plant is a large production line that creates industrial-scale quantities of kraft paper from wood and chemical slurry.
Kraft paper roll machines produce paper in roll form, with automatic paper rewinding and cutting devices for smaller size paper sheets.
These machines are ideal for creating continuous paper in large quantities, and it's easier to divide the paper into smaller parts after it's produced.
A kraft paper sheet machine creates fixed-sized sheets of paper, which are cut sheets instead of continuous rolls.
Discover more: Brown Kraft Paper Roll Wholesale
These sheets are ideal for customers and retailers looking for small-sized paper sheets, and are also used to create boxes and other paper products that require a non-rolled sheet.
A kraft paper board machine creates thicker and denser paper that is ideal for solid packaging needs, and may also include facilities for lamination, coating, and printing of the board.
Automatic kraft paper machines include automated features like a pulp feeding system and a finished product stacking facility, reducing manual input and increasing productivity.
Here are some of the main types of kraft paper machines:
- Kraft paper plant
- Kraft paper roll machine
- Kraft paper sheet machine
- Kraft paper board machine
- Automatic kraft paper machine
Two Fourdrinier Systems
Two Fourdrinier Systems are a significant advancement in kraft paper machine design. They improve the strength and quality of the kraft paper by adding two wire screens.
This design is ideal for producing heavy-duty industrial packing papers that require higher strength. Two Fourdrinier Wire Kraft Paper Systems can produce high-quality kraft paper continuously into a reel.
The fourdrinier system allows for better control of the roll diameter and thickness, as well as the quality of the paper roll. This results in increased production efficiency and quality of kraft paper.
Take a look at this: Packaging Conveyor Systems
Specifications & Maintenance
The specifications of a kraft paper machine are crucial for its overall efficiency and performance. The production capacity, typically measured in tons per day or hours, directly affects the machine's output.
A paper machine's raw material handling system is designed for efficient storage and transportation of raw materials, such as wood chips or recycled paper. This automated feeding system ensures a smooth production process.
The pulping process is a critical step in paper production, and the machine's specifications detail the type of pulp produced and the methods used, such as mechanical or chemical pulping. Digital technology often guides or automates this process for optimal results.
Here are the key specifications and maintenance tips for a kraft paper machine:
- Production capacity: tons per day or hours
- Raw material handling: automated feeding system
- Pulping process: mechanical or chemical pulping
- Sheet formation: wire, felt, and wet pressing
- Dewatering: pressing, suction, or combination of both
- Drying: drying sections and equipment
- Finishing: coating and cutting
- Automation and control systems: digital control system
- Energy efficiency: energy-efficient features
- Safety features: safety features to prevent accidents
Regular maintenance is essential to keep the machine in good shape. Operators should clean the machine parts often to avoid blockages and lubricate movable parts like chains and bearings.
Specifications & Maintenance
The specifications of a kraft paper manufacturing machine are crucial for its efficiency and productivity. The production capacity of the machine affects the overall efficiency of the production process, typically indicated in tons per day or hours.
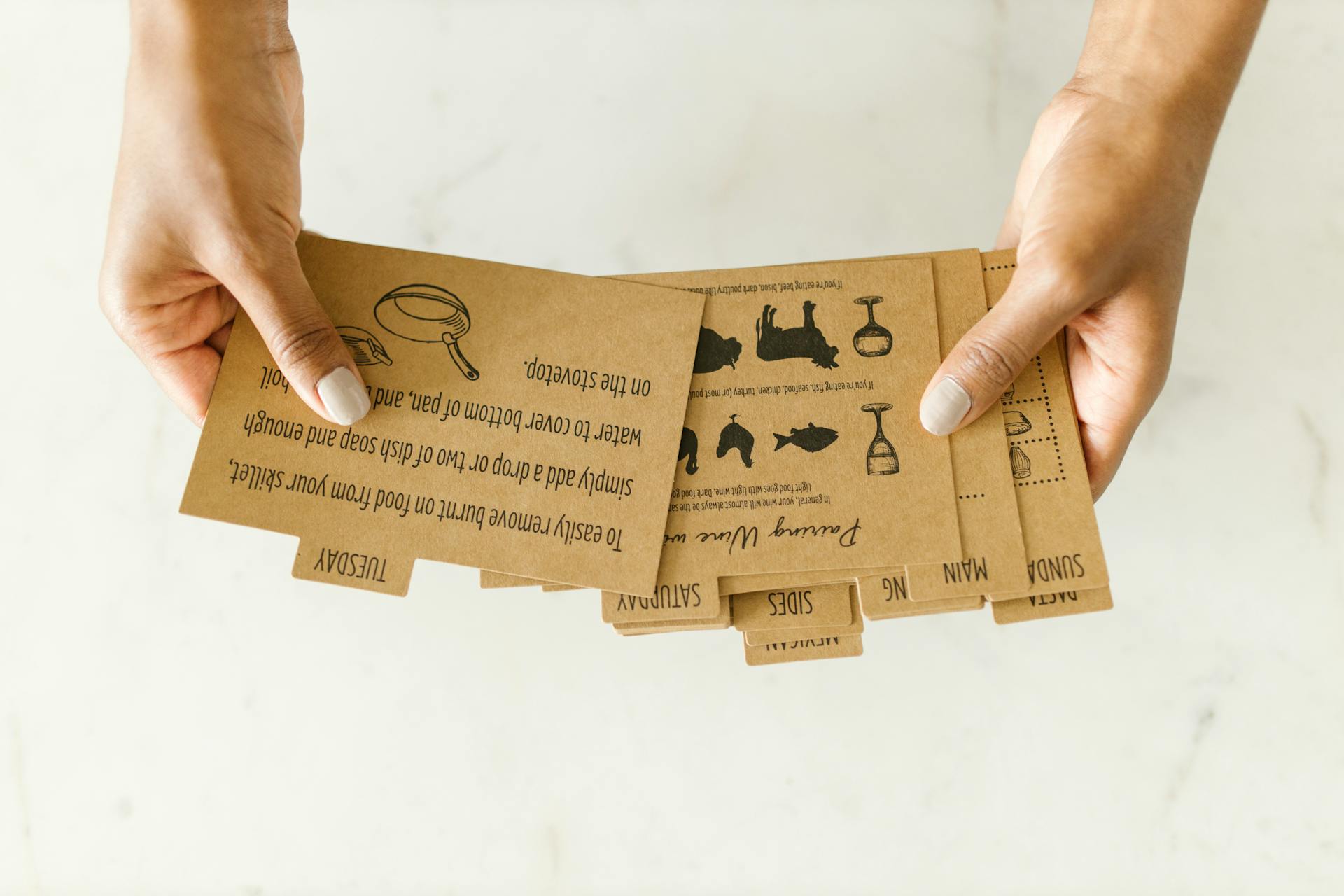
To ensure optimal performance, regular maintenance is essential. Operators should clean the machine parts often to avoid blockages and lubricate movable parts like chains and bearings with acceptable lubricant materials.
A paper machine may have a room to store raw materials, like wood chips or recycled paper, and a transportation system, like conveyor belts, for automated feeding of raw materials into the machine. This allows for efficient production.
The pulping process is another critical aspect of a kraft paper machine, with specifications including details about the type of pulp produced and the methods used, such as mechanical or chemical pulping. Digital technology can guide or automate this process.
The dewatering method affects the moisture content and consistency of the paper sheets, which can be done through pressing, suction, or a combination of both. The machine's design and capacity also influence the energy consumption.
Here are some key specifications to consider:
- Production capacity: tons per day or hours
- Pulping process: mechanical or chemical pulping
- Dewatering method: pressing, suction, or both
- Drying sections and equipment: determine final moisture content
- Automation and control systems: make it easy to monitor and manage production parameters
- Energy efficiency: features that lower the cost of production
- Safety features: prevent accidents and protect users from harm
By understanding and maintaining these specifications, you can ensure your kraft paper machine operates efficiently and safely.
UDTECH Parameters
The UDTECH Kraft Paper Machine is a highly efficient and versatile machine, and understanding its parameters is key to getting the most out of it. The machine can produce a wide range of paper products, including corrugating paper, kraft paper, and specialty papers.
The machine's raw material is recycled paper, such as newspaper and used boxes. This eco-friendly approach not only reduces waste but also saves on raw material costs.
The machine's output paper weight ranges from 110-240 g/m², making it suitable for a variety of applications. The net paper width is a generous 1600 mm, allowing for efficient production.
Here are some key parameters of the UDTECH Kraft Paper Machine:
The machine's production capacity is an impressive 10 tons per day, making it an excellent choice for high-volume production. The working speed is between 70-150 m/min, while the design speed is 200 m/min.
Technical Parameters
The technical parameters of a kraft paper making machine are crucial for understanding its capabilities and maintenance requirements. The machine's output product can range from packing paper to kraft paper, with a gram weight of 90-220g/m².
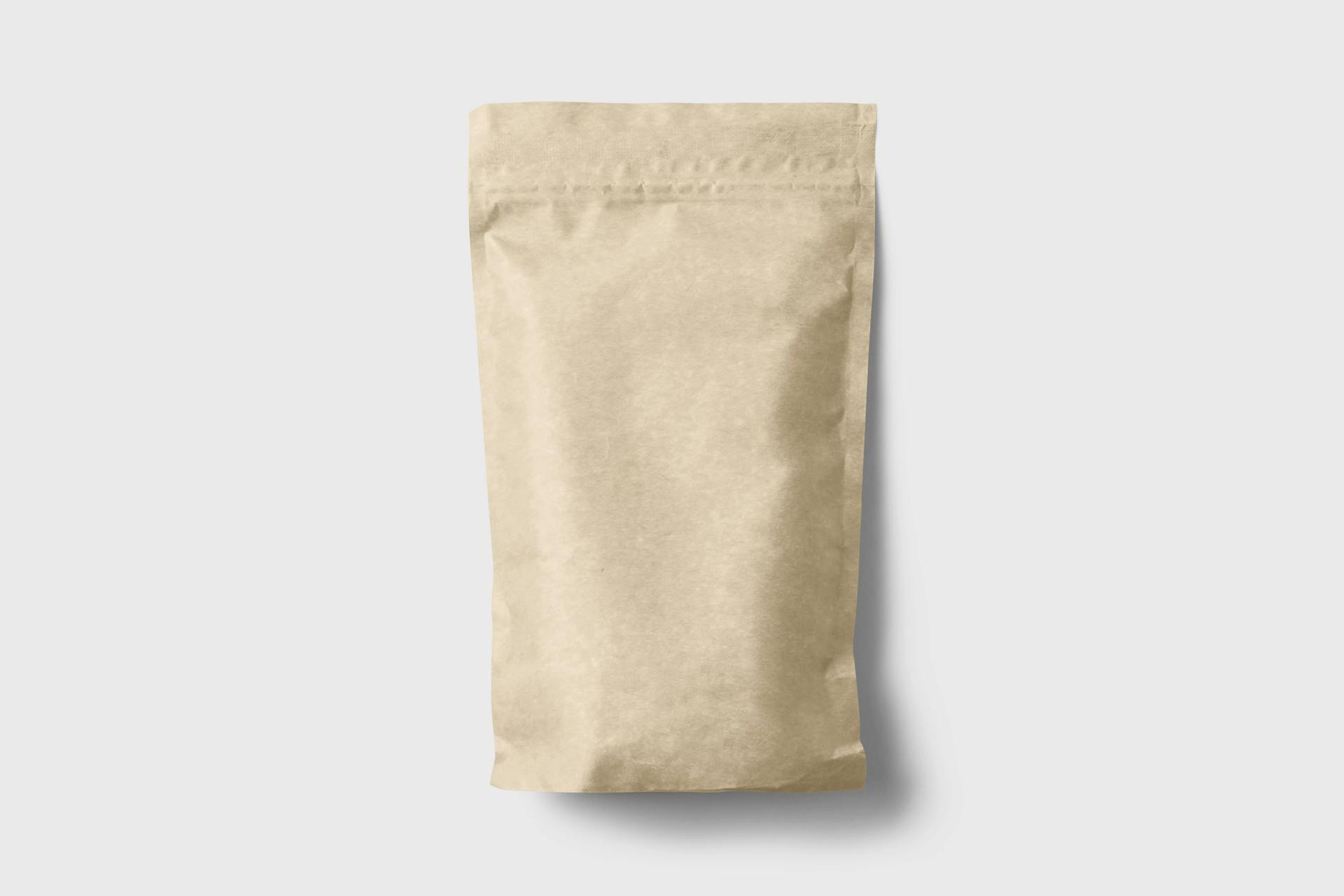
The net paper width is typically 1600mm, which is also the rolled paper width. The wire width, however, can be 1950mm.
The daily capacity of the machine is 10T/D, and it operates at a working speed of 40-80m/min. The design work speed, on the other hand, is 100m/min.
The transmission form is a division of the drive, with AC frequency conversion speed regulation. The gauge of the machine is 2400mm.
Here's a summary of the key technical parameters:
Applications and Uses
Kraft paper machines are used in the papermaking industry to manufacture paper products from wood pulp and natural fibers. These papers are renowned for their strength, sturdiness, and eco-friendliness.
The primary use of kraft paper machines lies in the production of paper, which is then used in various industries and sectors. Kraft paper is made into various types of paperboard and corrugated paper, used as packaging materials for domestic and industrial use.
Suggestion: What Is Card Stock Paper Used for
Fast food chains, food manufacturers, and beverage producers often use kraft paper as food packaging. This is due to its eco-friendly qualities and ability to be composted and recycled.
The textile industry uses kraft paper as an eco-friendly option for clothing labels, tape, and other applications. Kraft paper is also used in the construction industry for temporary protection and masking, as well as a moisture barrier and insulation.
Kraft paper is used in the agriculture industry for plant pots, seedlings, and protective packaging, among other things. Its sustainable qualities make it an attractive option for industries looking to reduce their environmental impact.
Here are some of the industries that utilize the output of paper-making machines:
- Manufacturing: Kraft paper is made into various types of paperboard and corrugated paper.
- Food and Beverage: Kraft paper is used as food packaging.
- Textile: Kraft paper is used as an eco-friendly option for clothing labels, tape, etc.
- Construction: Kraft paper is used for temporary protection and masking, as a moisture barrier, and insulation.
- Agriculture: Kraft paper is used for plant pots, seedlings, and protective packaging.
Choosing the Right Machine
Choosing the right kraft paper machine is crucial to meet your production demands. Assess your production needs, including required output, frequency of usage, and paper specifications, to select a machine that meets your demands.
Business buyers should focus on the level of automation and control system of the machine, choosing machines with an advanced automated system and a user-friendly control interface to improve production efficiency and ease of operation.
To reduce energy costs and environmental impact, consider machines with energy-efficient design and waste recycling and treatment systems. This will help you make a more informed decision.
Here are the key factors to consider when choosing a kraft paper machine:
- Production demand analysis
- Automation and control system
- Energy efficiency and environmental performance
- Machine quality and reliability
- Comprehensive cost analysis
Customizable for Diverse Needs
When choosing the right machine for your needs, one of the most important factors to consider is its ability to adapt to your specific requirements.
Accommodating different paper weights is crucial for many manufacturing processes, and some machines can handle a wide range of weights with ease.
UDTECH's solution, for instance, flexibly adapts to different paper weights, widths, and manufacturing process specifications.
This means you can use the same machine for various tasks, reducing the need for multiple machines and saving you time and resources.
By choosing a machine that can accommodate different paper widths, you can also expand your product offerings and increase your market reach.
UDTECH's solution is designed to be versatile, making it a great option for businesses with diverse needs.
Intriguing read: Paper Stock Weights
How to Choose
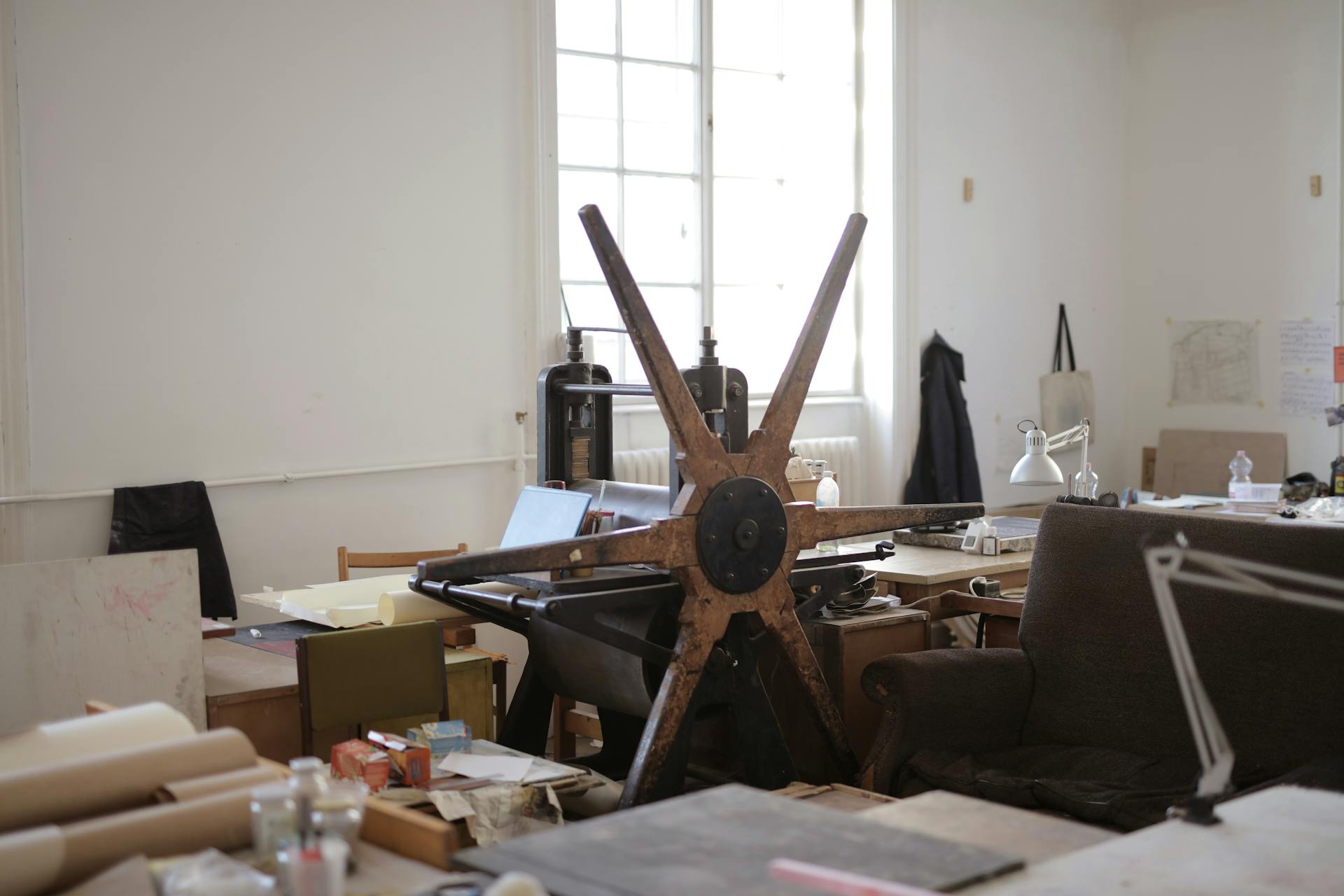
Choosing the right machine requires careful consideration of several key factors. First and foremost, you need to assess your production demands, including required output, frequency of usage, and paper specifications.
This assessment will help you select a machine that meets your production demands in terms of capacity and flexibility. For example, if you need to produce a large quantity of paper, you'll want a machine with a high output capacity.
An advanced automated system and user-friendly control interface are essential for improving production efficiency and ease of operation. Look for machines with these features to streamline your workflow.
Energy costs can be a significant expense, so choose machines with energy-efficient design to reduce your operating costs. Consider the machine's environmental performance as well, such as waste recycling and treatment systems.
It's also crucial to choose a machine from a reputable manufacturer with a proven track record of producing high-quality machines.
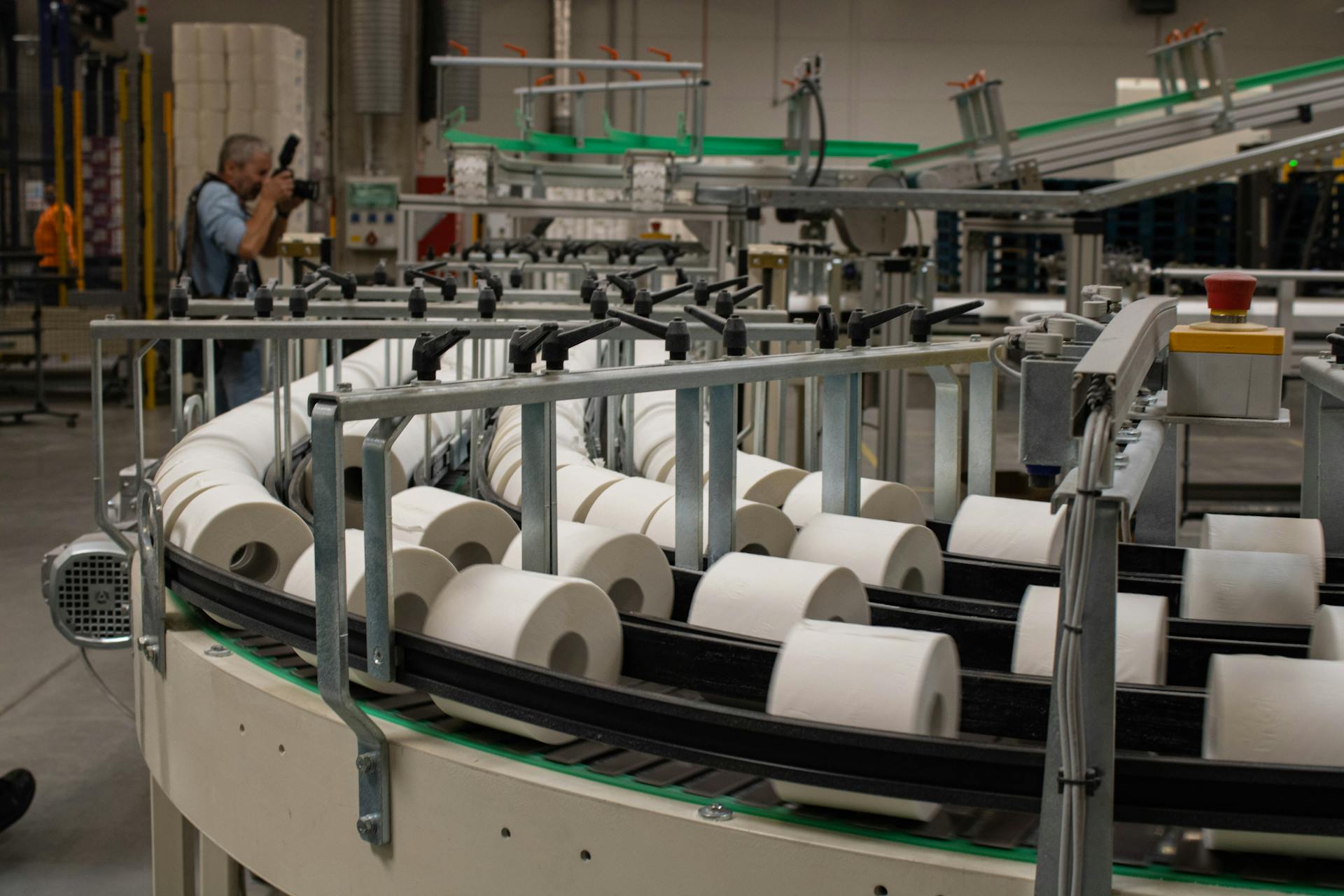
Here are some key considerations to keep in mind when evaluating machine quality and reliability:
- Machine quality: Look for machines produced by manufacturers with good reputations and proven track records.
- Reliability: Choose machines that are designed to minimize downtime and maximize uptime.
Finally, don't forget to conduct a comprehensive cost analysis that takes into account more than just the purchase price. Consider the machine's maintenance cost, energy consumption, and paper raw material utilization to make an informed decision.
Curious to learn more? Check out: Franking Machine Cost
Production Process and Capabilities
The production process of kraft paper involves several key steps. Raw materials, such as waste paper, are first fed into a pulper to break them down into a pulp.
The pulp is then processed through a series of machines, including a vibrating sieve, a pulp tank, a pulp pump, a bleach machine, and a refiner machine, to refine and clean the pulp. This process helps to increase safety and quality within the paper mill.
The refined pulp is then formed into a paper sheet using a paper making machine, which increases production speed and efficiency.
What Is the Manufacturing Process?
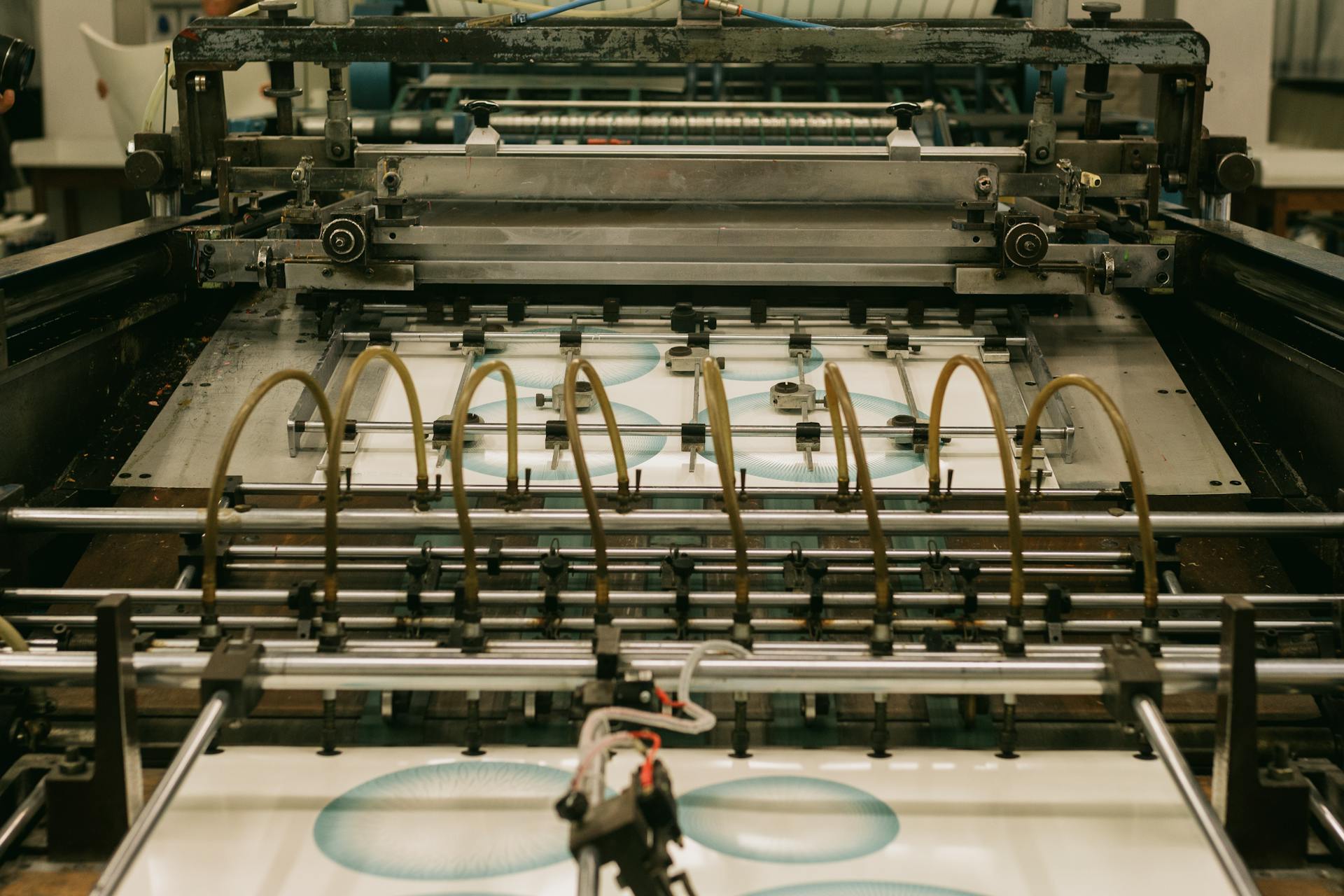
The manufacturing process of kraft paper is quite fascinating. The journey begins with raw material selection, where wood chips or waste paper are gathered to extract fiber pulp. This pulp is then put through a chemical pulping process, which divides the constituents and is critical in achieving the thickness, strength, and eco-friendly nature of kraft paper.
The pulping process is a key step in achieving the desired characteristics of kraft paper. The fibers separated during this process are then formed into a wet paper sheet, which forms the structure and quality of the paper.
The wet paper sheet undergoes drying using the latest drying systems available. This step is crucial in preparing the paper for industrial use. Once dried, the paper is rewound to a predetermined diameter, preparing it for packaging.
The final step in the manufacturing process is packaging, where the rolls of kraft paper are protected during movement and transportation. This ensures the paper arrives at its destination in perfect condition.
See what others are reading: Packaging Corporation of America
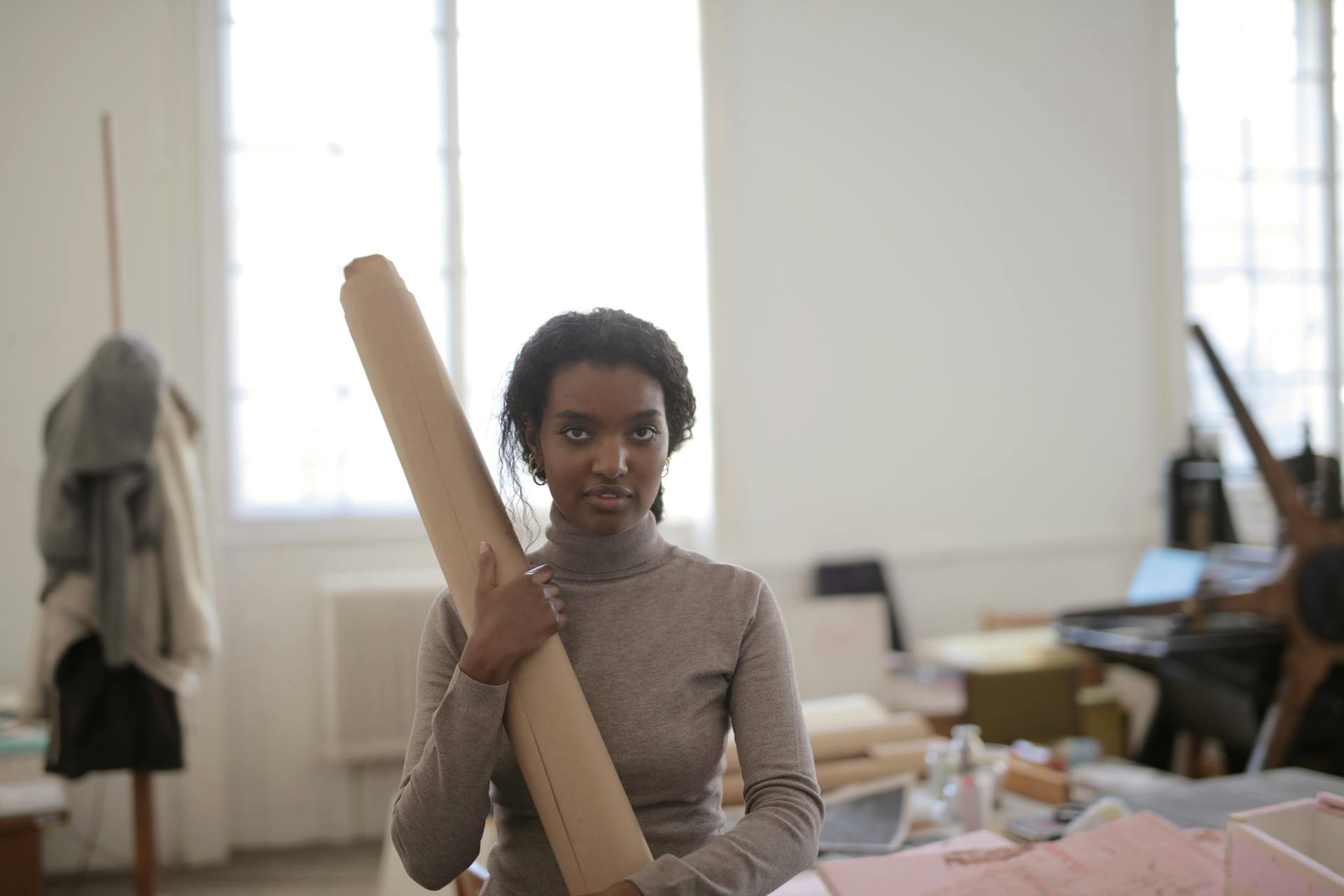
Here's a breakdown of the manufacturing process:
- Raw Material Selection: Wood chips or waste paper are gathered to extract fiber pulp.
- Pulping Process: Chemical pulping process divides the constituents and achieves the desired characteristics.
- Sheet Formation: Fibers are formed into a wet paper sheet.
- Drying Process: Wet paper sheet is dried using the latest drying systems.
- Rewinding: Paper is rewound to a predetermined diameter.
- Packaging: Rolls of kraft paper are protected during movement and transportation.
Production Capabilities
Our Kraft paper machines are designed to produce high-quality paper with efficiency and speed. They are built to handle various types of paper production, from standard rolled kraft paper to heavier and multi-layered kraft paper.
The Fourdrinier Machine is a popular choice for producing standard rolled kraft paper, making it a great option for those who need a reliable and consistent output.
We also offer the Two Fourdrinier Wire Machine, which is capable of producing a wide range of paper grades, including heavier and multi-layered kraft paper.
Here are some key features of our Kraft paper machines:
These machines are designed to work efficiently and produce high-quality paper, making them a great investment for any paper mill.
Quality Control and Assurance
To ensure high-quality kraft paper production, maintaining kraft paper machines is crucial. Periodic cleaning, lubrication, and other routine checks are central to ensuring the operational longevity of Kraft paper machines.
Worth a look: Tubular Mesh Bag Machines

The quality of kraft paper is reliant on the input materials, and choosing high-strength kraft materials can improve the final product's strength and utility. High-grade fibers and other high-strength kraft materials are essential for producing high-quality kraft paper.
Quality control is essential in the manufacturing of kraft papers, with inspections conducted from the pulping stage all the way to the final packing stage. This ensures that every step of the process meets quality standards.
The kraft process utilizes chemical treatment of wood chips to create sturdy paper products, and innovative processes like DDS replacement cooking enhance quality while saving energy. Optimizing the kraft pulping process is key to producing high-quality kraft paper.
To achieve the desired strength, smoothness, and uniformity, controlling pulp ratios, pressing, drying, and air permeability is crucial. This process control is essential for producing high-quality kraft paper.
Here are some key factors to consider for quality control and assurance:
- Maintaining Kraft Paper Machines
- Choosing High-Strength Kraft Materials
- Quality Control
- Optimizing the Kraft Pulping Process
- Enhancing Paper Properties Through Process Control
Raw Materials and Costs
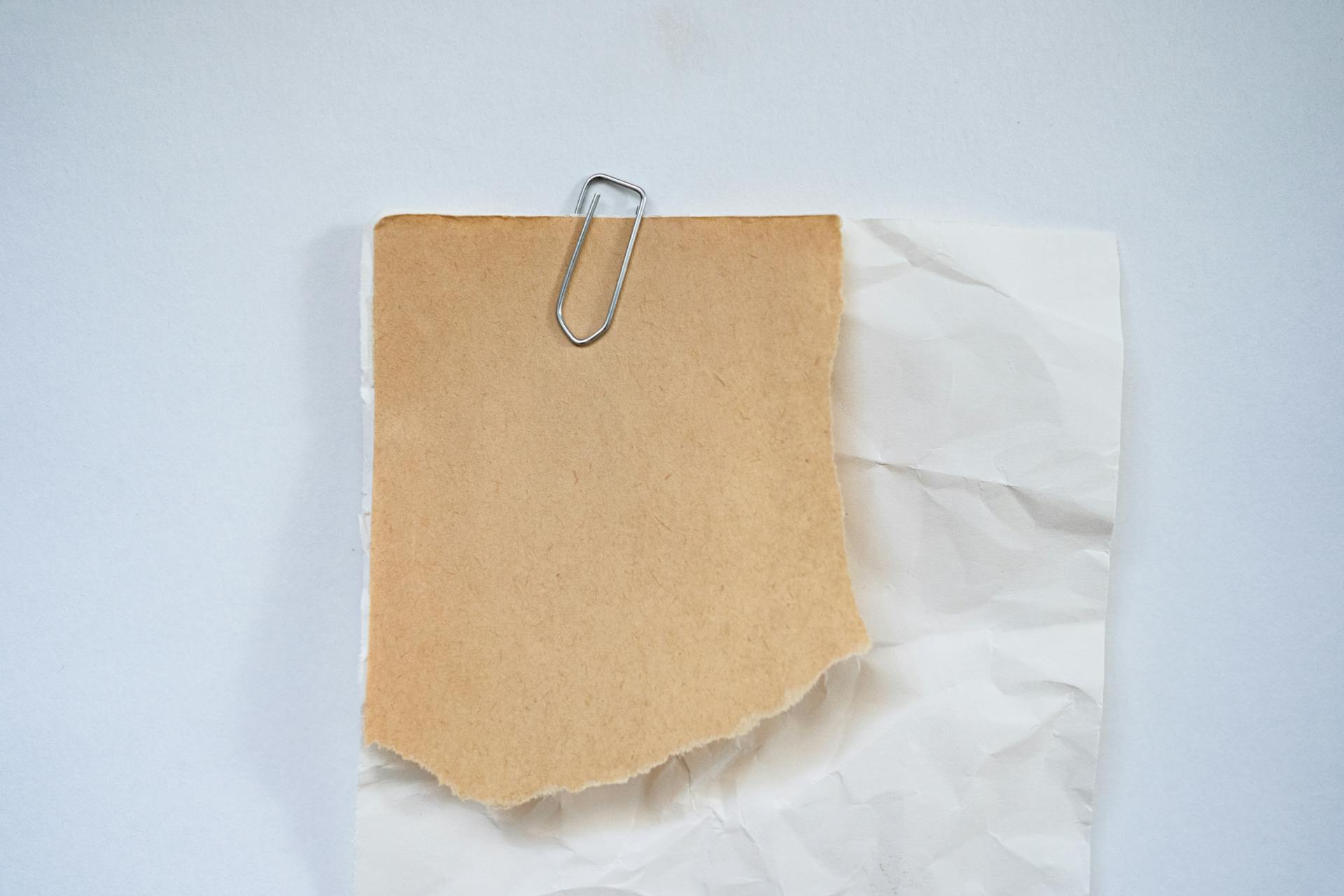
Raw Materials and Costs are a significant consideration when it comes to setting up a kraft paper machine. High-grade materials or specialized systems can increase costs.
Worldwide supply chain difficulties, like the increase in freight charges, pose additional risks to your business. As a result, purchasing machinery that meets the potential workload is crucial to mitigate these risks.
Using recycled materials can help reduce costs and minimize the impact of supply chain difficulties. This approach not only saves money but also contributes to a more sustainable operation.
Here are some key factors to consider when evaluating raw materials and costs:
- Purchasing machinery that meets the potential workload can help mitigate risks associated with supply chain difficulties.
- Using recycled materials can help reduce costs and contribute to a more sustainable operation.
How it Works
The kraft paper machine is a remarkable piece of equipment that plays a crucial role in the production of kraft paper.
The machine works through various steps, starting from pulp preparation to drying and pressing the kraft paper into a continuous roll.
Pulping is the first step in the process, where wood chips or other plant material is converted into a pulp.
You might like: Paper Pulp Molding Machine
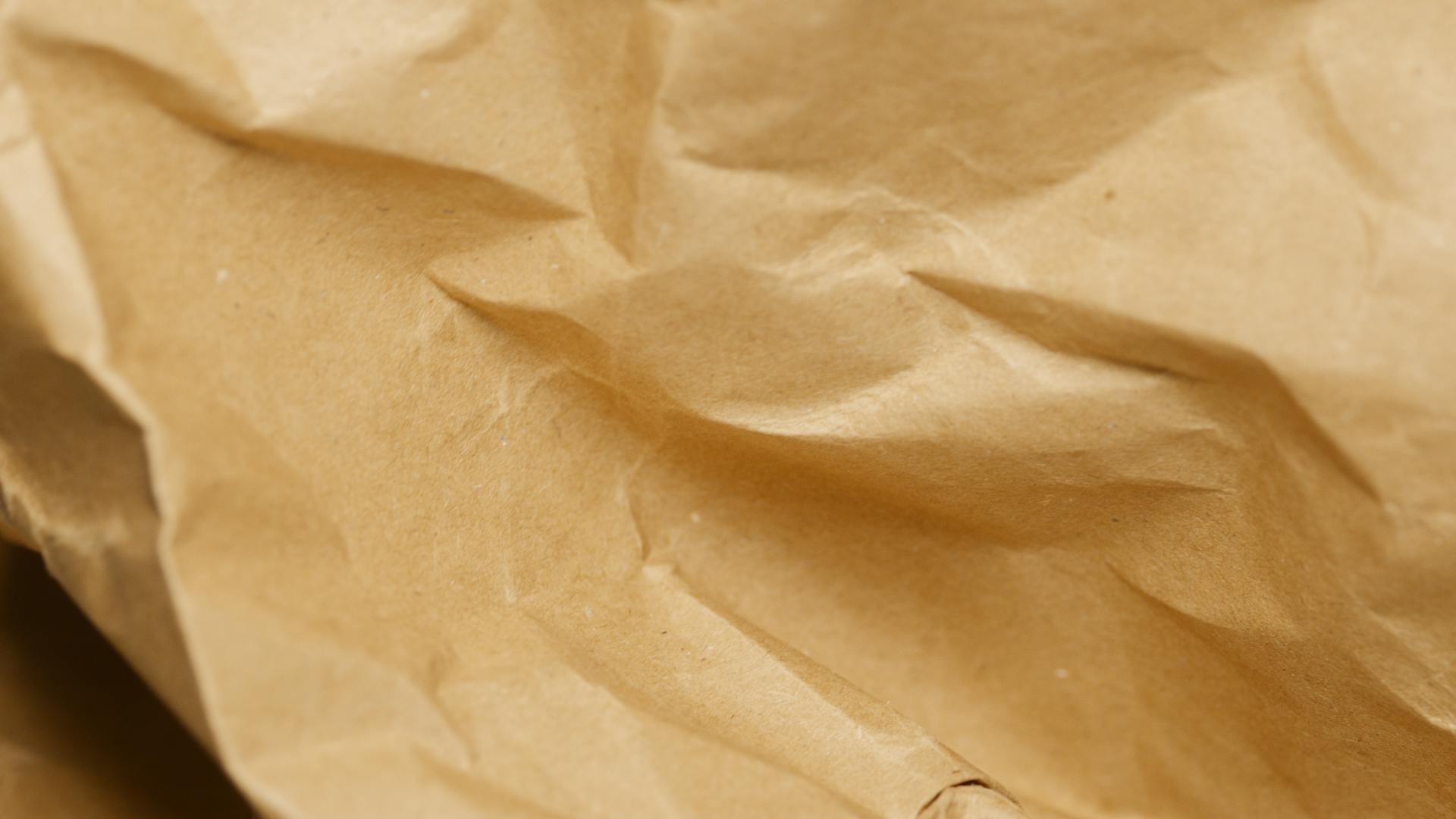
Screening is another important step, where the pulp is cleaned and refined to ensure consistency and quality.
A fourdrinier forming stage is also a key part of the process, allowing for better control of the roll diameter and thickness, as well as the quality of the paper roll.
This fourdrinier system enables the production of paper and board continuously into a reel, increasing production efficiency and quality.
The machine's ability to continuously produce kraft paper into a reel is a significant advantage, allowing for faster and more efficient production.
You might enjoy: Roll Stock Paper
Importance and Benefits
Kraft paper is a game-changer for the environment. It's both bio-degradable and compostable, making it a crucial component in the circular economy.
Recycled kraft paper is non-toxic and biodegradable, which is why it's commonly used in printing, packaging, food, and sanitary materials. This versatility makes it a top choice for various industries.
Its exceptional strength and tear resistance make it perfect for packaging, transportation, and industrial use. This is especially true for applications where durability is key.
Discover more: Packaging with Kraft Paper
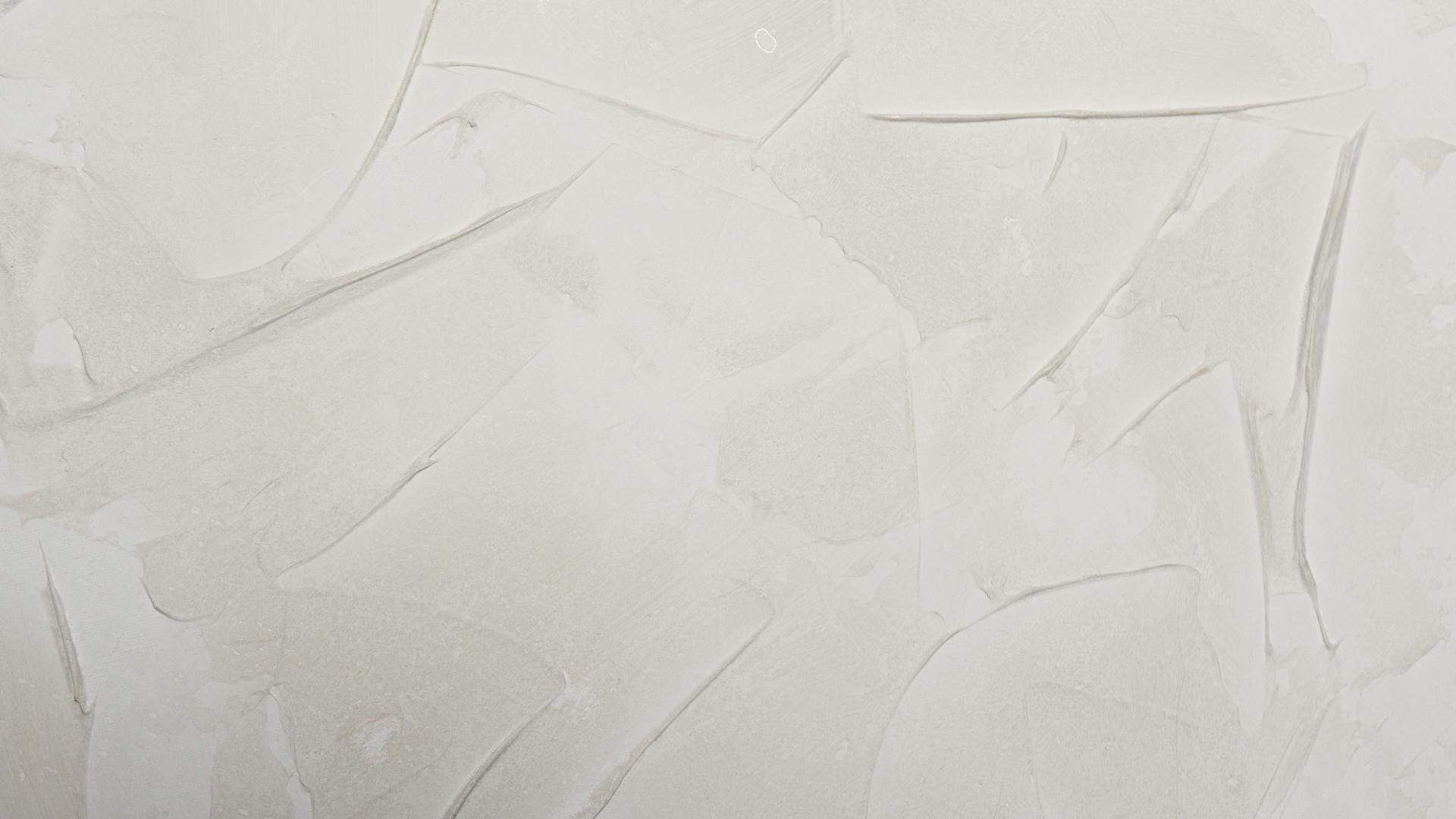
By utilizing post-consumer waste paper, manufacturers can lower their carbon emissions. Recycling paper reduces CO2 emissions by approximately 20% compared to incineration.
The fourdrinier wire kraft paper making machine increases production efficiency and quality of kraft paper. This machine allows for continuous production, better control of roll diameter and thickness, and improved paper roll quality.
Recycling paper into kraft paper reduces the cost of raw materials and enhances the circular economy. It also creates jobs in the recycling and manufacturing sectors, stimulating the local economy.
Recommended read: Kraft Paper Roll Wall Mount
Utech's Solution and Capabilities
UDTECH's Kraft Paper Machine Solution is designed to provide high-quality, reliable, and efficient production of paper, with a focus on automation and increasing productivity.
The Fourdrinier Machine from UDTECH is most efficiently and consistently suited for producing standard rolled kraft paper.
Kraft paper-making machines like the ones from UDTECH and YG Machinery are popular choices for kraft paper processing, offering advantages in raw material selection and increased production with reduced loss of paper.
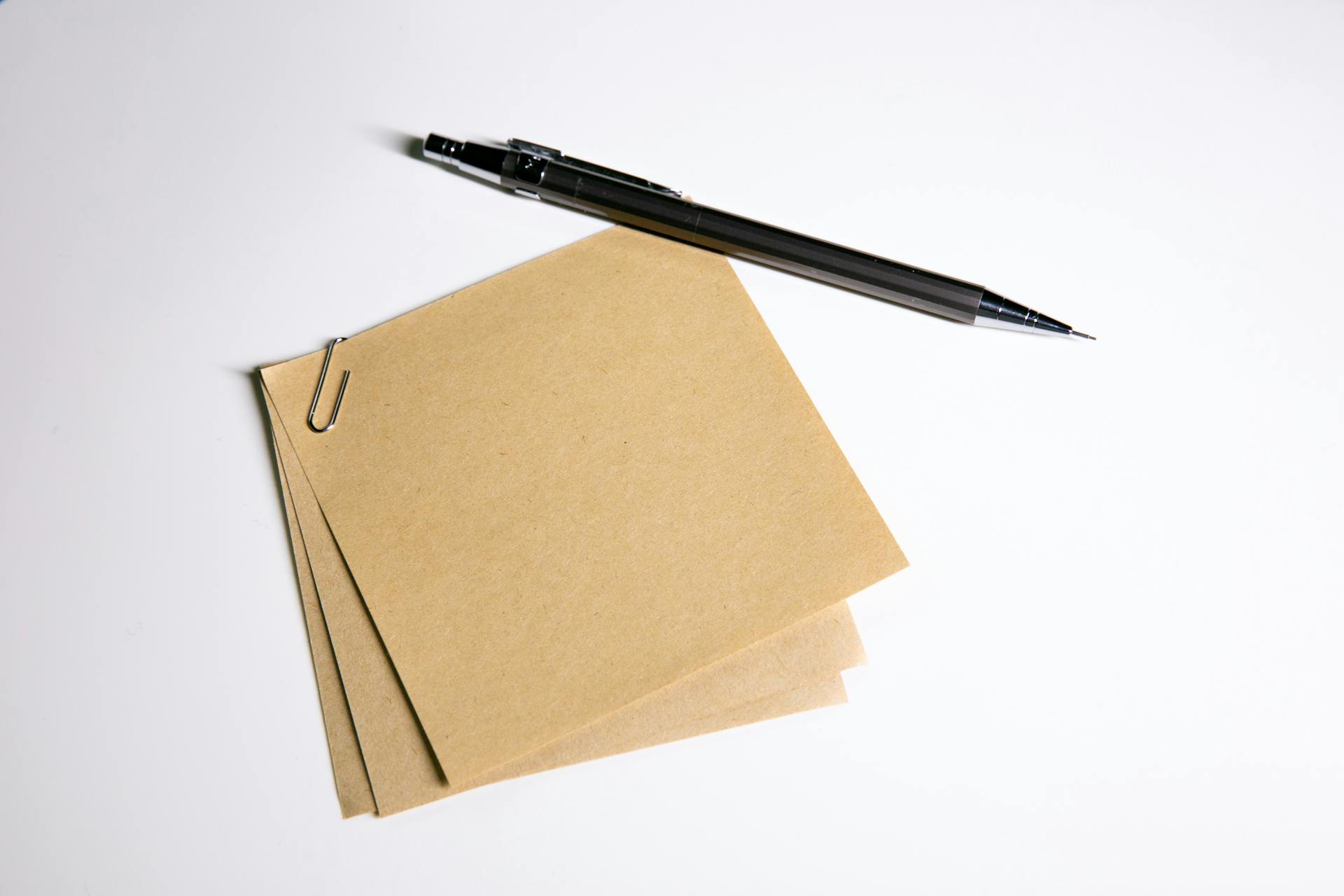
UDTECH's Kraft Paper Machine Solution can produce standard rolled kraft paper efficiently, and YG Machinery offers a range of paper-making machines, including kraft paper-making machines, tissue-making machines, and more.
Here is a list of some of the paper-making machines offered by YG Machinery:
- Kraft paper-making machine
- Tissue-making machine
- A4 paper-making machine
- Corrugated paper machine
- Slitting machine
- Rewinder machine
- Egg tray-making machine
- Paper bag-making machine
- Garbage bag-making machine
- Woven bag-making machine
- Nonwoven bag-making machine
- Disposable cup-making machine
- Paper bowl-making machine
- Paper dish-making machine
- Paper straw-making machine
- Wet tissue machine
Professional Manufacturer
As a professional manufacturer, Utech offers a wide range of paper-making machines, including kraft paper-making machines, which are one of the most commonly used types of equipment in the industry.
Our kraft paper-making machines have advantages in terms of raw material choices and production efficiency, allowing businesses to increase production and reduce losses.
We also have other specialized machines, such as tissue-making machines and A4 paper-making machines, that cater to specific needs and applications.
In addition to paper-making machines, we also manufacture equipment for making other products, like egg trays, paper bags, and disposable cups.
Our machines are designed to be efficient and reliable, helping businesses streamline their operations and improve productivity.
Related reading: Paper Sack Making Machine

We have a variety of machines to choose from, including corrugated paper machines, slitting machines, rewinder machines, and more.
If you're interested in learning more about our machines or would like to get in touch, you can contact us via WhatsApp, WeChat, phone, or Skype at +86 136 1385 6800.
Utech's Solution
Utech's Kraft Paper Machine Solution guarantees high-quality production of paper with reliable and efficient performance.
Its design focuses on automation, which increases productivity.
This solution meets your performance requirements.
10 Tpd and Plant
For a kraft paper machine, you have two options when it comes to production capacity: 10 TPD or 5 Ton. The 10 TPD machine is an automatic, made of MS, with a speed of 70-80 MPM and a normal production basis of 10 MTPD saleable on 120 GSM at 85% machine efficiency.
The 10 TPD machine is designed to produce 10 tons of paper per day, with a felt length of approximately 23,000mm and a shrinkage of 2%. It can be powered by waste paper as the furnish.
Here are the key specifications of both machines:
- 10 TPD Machine:
- Capacity: 10 ton/day
- Automation Grade: Automatic
- Body Material: MS
- Felt Length: 23,000mm (Approx)
- Shrinkage: 2%
- Furnish: Waste Paper
10 Tpd
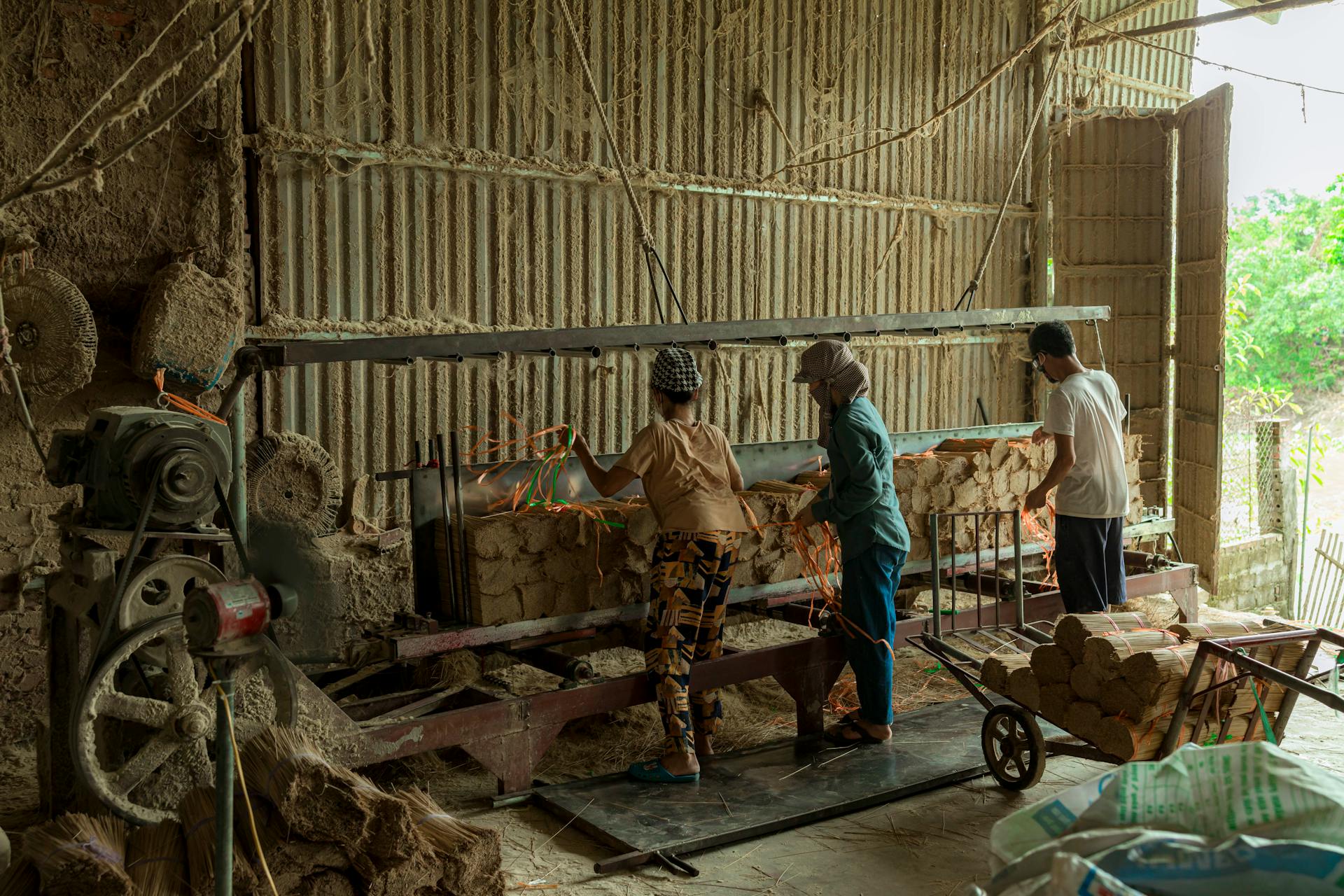
The 10 Tpd machine is a significant part of any paper production plant. It has a production capacity of 10 TPD.
The automation grade of the 10 Tpd machine is automatic, which means it can operate with minimal human intervention. This level of automation ensures efficiency and consistency in production.
The machine's body is made of MS, a material commonly used in industrial equipment. Its speed is impressive, ranging from 70-80 MPM.
The 10 Tpd machine is designed to produce 10 MTPD of saleable paper at 120 GSM, with a machine efficiency of 85%. This is a significant output, and the machine is capable of achieving this level of production.
Here are some key specifications of the 10 Tpd machine:
The 10 Tpd machine is designed to operate efficiently, with a shrinkage rate of 2%. This is a relatively low rate, indicating that the machine can produce high-quality paper with minimal waste.
The machine is suitable for processing waste paper as its furnish.
Plant
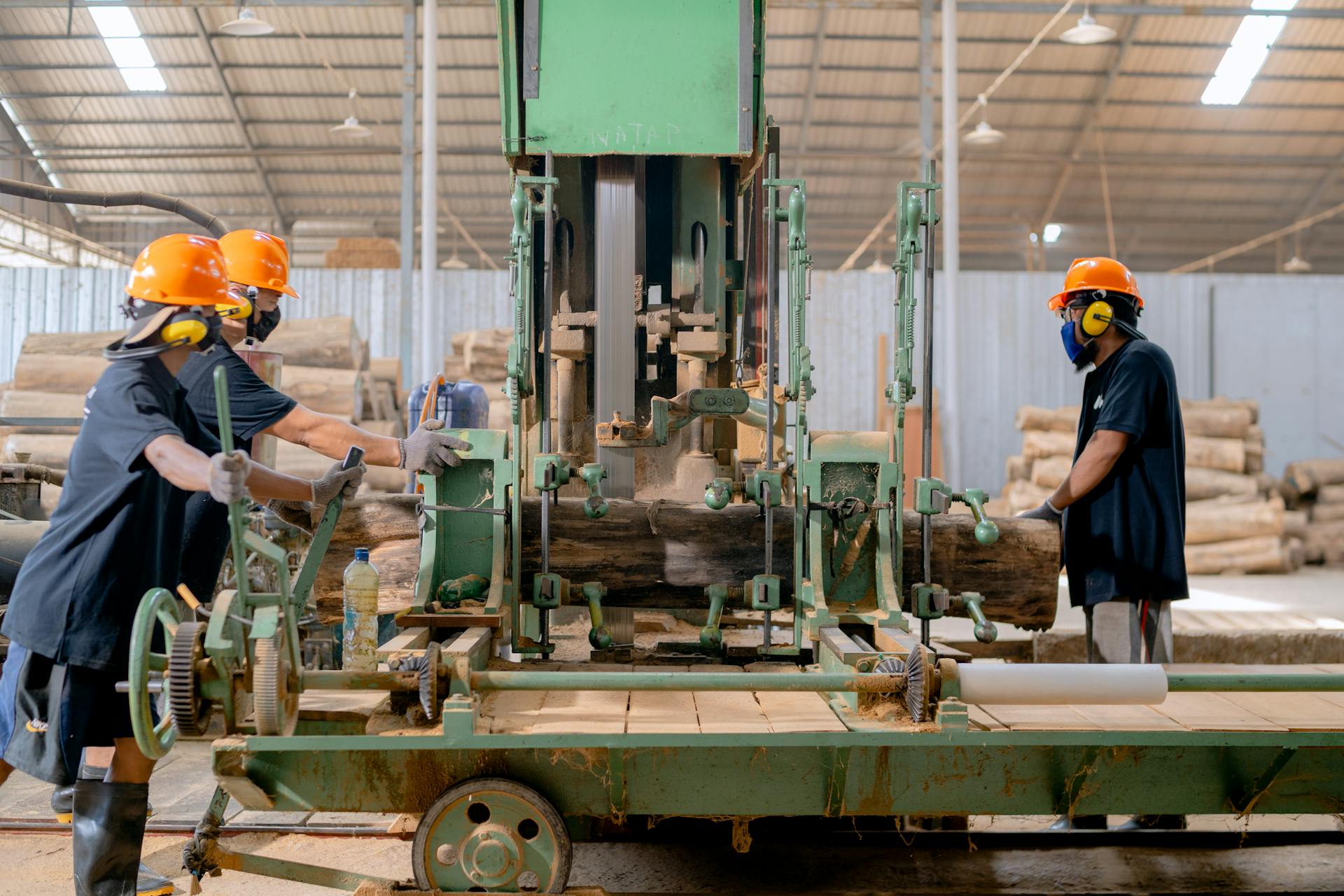
Our 10 Tpd and plant is equipped with a Kraft Paper Making Plant that boasts a production capacity of 5 Ton. This impressive capacity ensures efficient production and meets the demands of the market.
The plant's automation grade is automatic, which means it can operate with minimal human intervention. This level of automation reduces labor costs and increases productivity.
The body material of the plant is made of MS (mild steel), a durable and long-lasting material that can withstand harsh conditions. This ensures the plant's longevity and reduces maintenance costs.
The plant is equipped with AC variable drive, which allows for smooth and efficient operation. This feature also helps to reduce energy consumption and lower operating costs.
The rail gauge of the plant is 4700 mm, which is a standard measurement used in the industry. This ensures compatibility with other equipment and makes transportation and storage easier.
The plant uses a variety of raw materials, including wood pulp, waste paper, straw, bamboo, and bagasse. These materials are readily available and can be sourced locally, reducing transportation costs and environmental impact.
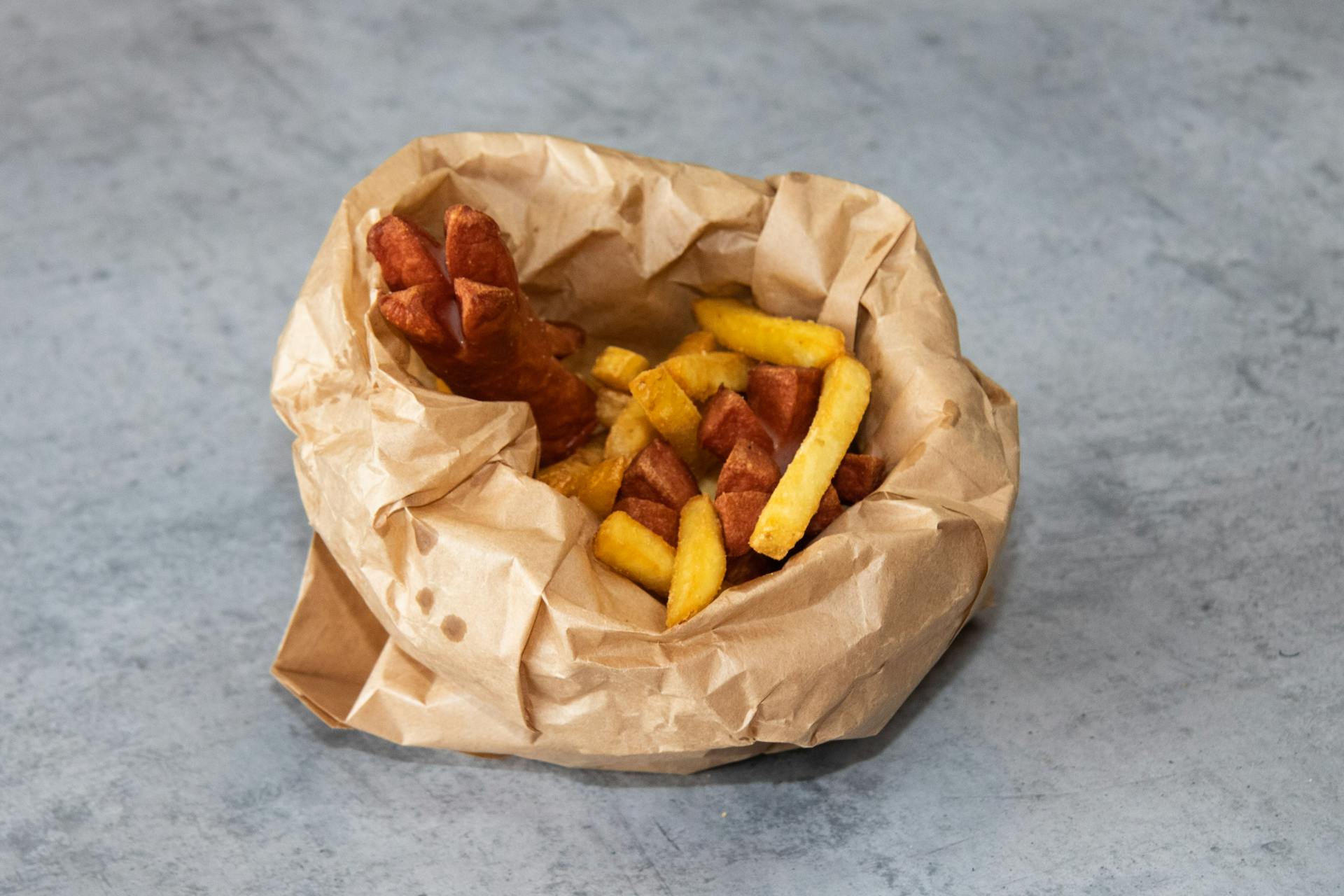
The plant's production range is 90-150 GSM (grams per square meter), which is suitable for various applications, including packaging, printing, and crafts.
The plant is made in India, which ensures compliance with local regulations and standards. This also supports the local economy and promotes domestic manufacturing.
The plant's HS Code is 8439200000, which is a unique identifier used for customs and trade purposes. This helps to facilitate international trade and ensures accurate classification and taxation.
Here's a summary of the plant's key features:
Sources
- https://www.alibaba.com/showroom/kraft-paper-making-machine-price.html
- https://www.mohseenengineeringworks.in/kraft-paper-mill-machine.html
- https://ud-machine.com/paper-making-machine/kraft-paper-machine/
- https://www.yugongmachinery.com/kraft-paper-making-machine/
- https://www.ygpapermachinery.com/kraft-paper-making-machine/
Featured Images: pexels.com