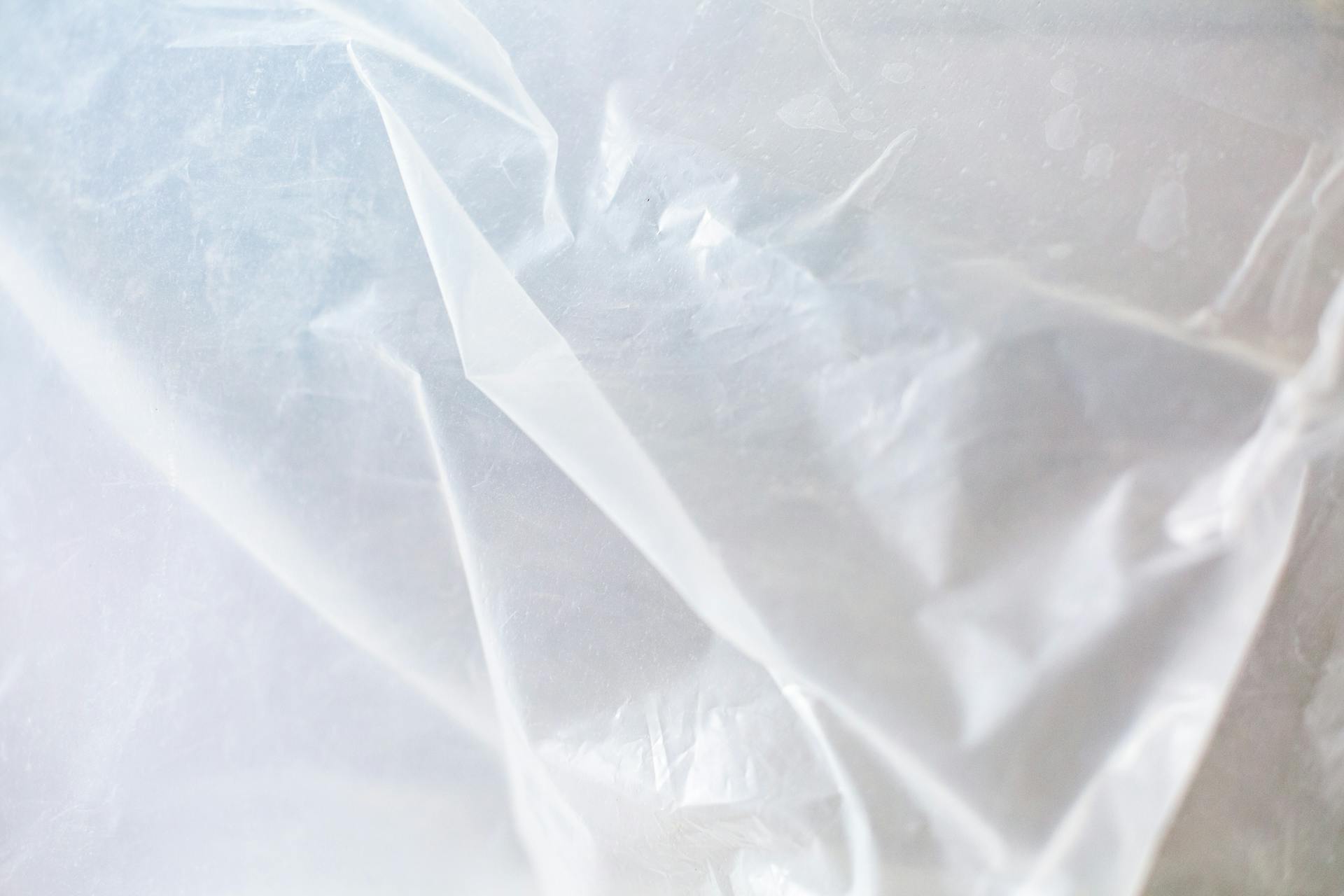
High density polyethylene foam sheets come in various types, each with its unique properties and applications.
There are two main types of high density polyethylene foam sheets: closed-cell and open-cell foam. Closed-cell foam has a higher density and is more durable, while open-cell foam is more flexible and has better sound absorption properties.
High density polyethylene foam sheets are used in a wide range of applications, including packaging, insulation, and cushioning. They are also used in the production of sports equipment, such as helmets and pads.
Their versatility and durability make them a popular choice for industries that require high-quality foam products.
See what others are reading: Green Cell Foam
Types and Characteristics
High density polyethylene foam sheets are closed-cell thermoplastic foams, meaning they have compact cells surrounded by solid walls that prevent the flow of liquids and gases.
Their closed-cell architecture makes them impervious to air, moisture, and chemical penetration, which grants them superior strength, density, and rigidity compared to open-cell foams.
Polyethylene foam sheets are known for their exceptional impact resistance and durability, making them perfect for cushioning purposes. They also exhibit excellent dimensional stability, allowing them to undergo various fabrication techniques.
Their minimal thermal conductivity makes them superior insulating materials, and they feature antimicrobial properties that help inhibit bacteria, mold, and other microorganism growth.
Types of Sheets
Coated Foam Sheets are perfect for outdoor applications due to their durable and resistant nature.
Non-Crosslinked Foam Sheets are ideal for applications that require flexible cushioning, and they maintain their integrity under stress without losing shape.
Crosslinked Foam Sheets are known for their enhanced stability and buoyancy, making them commonly used in heavy-duty applications.
Custom Fabricated Sheets are tailored to specific dimensions and requirements, making them perfect for unique projects that need specialized sizes or profiles.
Here's a breakdown of the different types of sheets:
Chapter 1: Characteristics of Foams
Polyethylene foam is a closed-cell thermoplastic foam substance, crafted from compact cells surrounded by solid walls that efficiently obstruct the flow of liquids and gases.
These closed-cell foams are impervious to air, moisture, and chemical penetration, making them superior to open-cell foams in terms of strength, density, and rigidity.
Their lightweight and pliable qualities are a result of their closed-cell architecture.
Polyethylene foams are known for their exceptional impact resistance and durability, making them perfect for cushioning purposes.
Their minimal thermal conductivity makes them superior insulating materials.
They are characterized by their softness, non-abrasiveness, and resistance to dust, tearing, and decay.
These foams exhibit excellent dimensional stability, allowing them to undergo various fabrication techniques.
They also feature antimicrobial properties that help inhibit bacteria, mold, and other microorganism growth.
Supplies Inc. - Ecomate
The FSI Ecomate Foam Systems from Foam Supplies Inc. are tailored for the production of polyethylene foam.
These systems deliver accurate control over foam density.
They allow for formulation customization, giving manufacturers flexibility in their production process.
Foam Supplies Inc. uses eco-friendly blowing agents to ensure both effective and sustainable foam manufacturing.
Recommended read: Corrugated Board Production
Low-Density and High-Density
Low-density polyethylene foams are softer and have better thermal insulating materials than high-density foams. They're also valued for their buoyancy and water resistance.
Their cellular structure has more voids, which makes their density relatively lower. This is in contrast to high-density foams, which have smaller and thicker cellular walls.
Low-density polyethylene foams are commonly used as a packaging material. They're a great choice for this application because they provide good cushioning and protection for fragile items.
High-density polyethylene foams, on the other hand, are more preferred for heavy-duty applications. They have high compressive and tensile strength, fatigue resistance, and low thermal shrinkage.
Here's a comparison of the two types of foams:
Low-density polyethylene foams have a disadvantage - their thickness decreases due to prolonged exposure to compressive stress. This is something to keep in mind when using them for packaging or other applications where they may be subject to pressure.
Applications
High density polyethylene foam sheets have a wide range of applications, making them a versatile material for various industries.
In the packaging industry, these foam sheets are used to protect fragile items during transportation, providing excellent shock absorption for electronics and heavy machinery.
Their firmness makes them a reliable tool for packaging, ensuring that important items arrive safely at their destination.
For construction projects, high density polyethylene foam sheets are used for insulation and soundproofing, reducing heat loss and improving energy efficiency.
In fact, they're often used in aircraft interiors and automotive parts, taking advantage of their lightweight yet durable nature to enhance performance and safety.
These foam sheets are also used in furniture upholstery, providing cushioning and comfort without compromising support.
Here are some of the key applications of high density polyethylene foam sheets:
- Packaging
- Construction
- Aerospace and Automotive
- Furniture Upholstery
Their chemical and moisture resistance, strong insulation ability, and high shock absorption make them an ideal material for various indoor and outdoor applications.
Features and Advantages
High density polyethylene foam sheets are incredibly durable, resistant to wear and tear, making them suitable for long-term use across various environments.
Their versatility is one of their greatest strengths, available in a range of thicknesses and densities that can be adapted for numerous uses, from industrial applications to consumer products.
One of the key benefits of these foam sheets is their water resistance, thanks to their closed-cell structure that prevents moisture absorption, ensuring they're suitable for both indoor and outdoor applications.
Here are some of the key features and advantages of high density polyethylene foam sheets:
- Durability: resistant to wear and tear
- Versatility: available in various thicknesses and densities
- Water Resistant: closed-cell structure prevents moisture absorption
- Eco-Friendly Options: recyclable polyethylene foam sheets are available
- Ease of Handling: lightweight yet sturdy, easy to cut and shape
Features and Advantages
High density polyethylene foam sheets have some amazing features that make them a great choice for various applications. They are incredibly durable and can withstand wear and tear, making them suitable for long-term use in different environments.
Their versatility is one of their biggest advantages. They come in different thicknesses and densities, allowing them to be used in a wide range of applications, from industrial settings to consumer products.
These foam sheets are also water-resistant, thanks to their closed-cell structure that prevents moisture absorption. This means they can be used both indoors and outdoors without any issues.
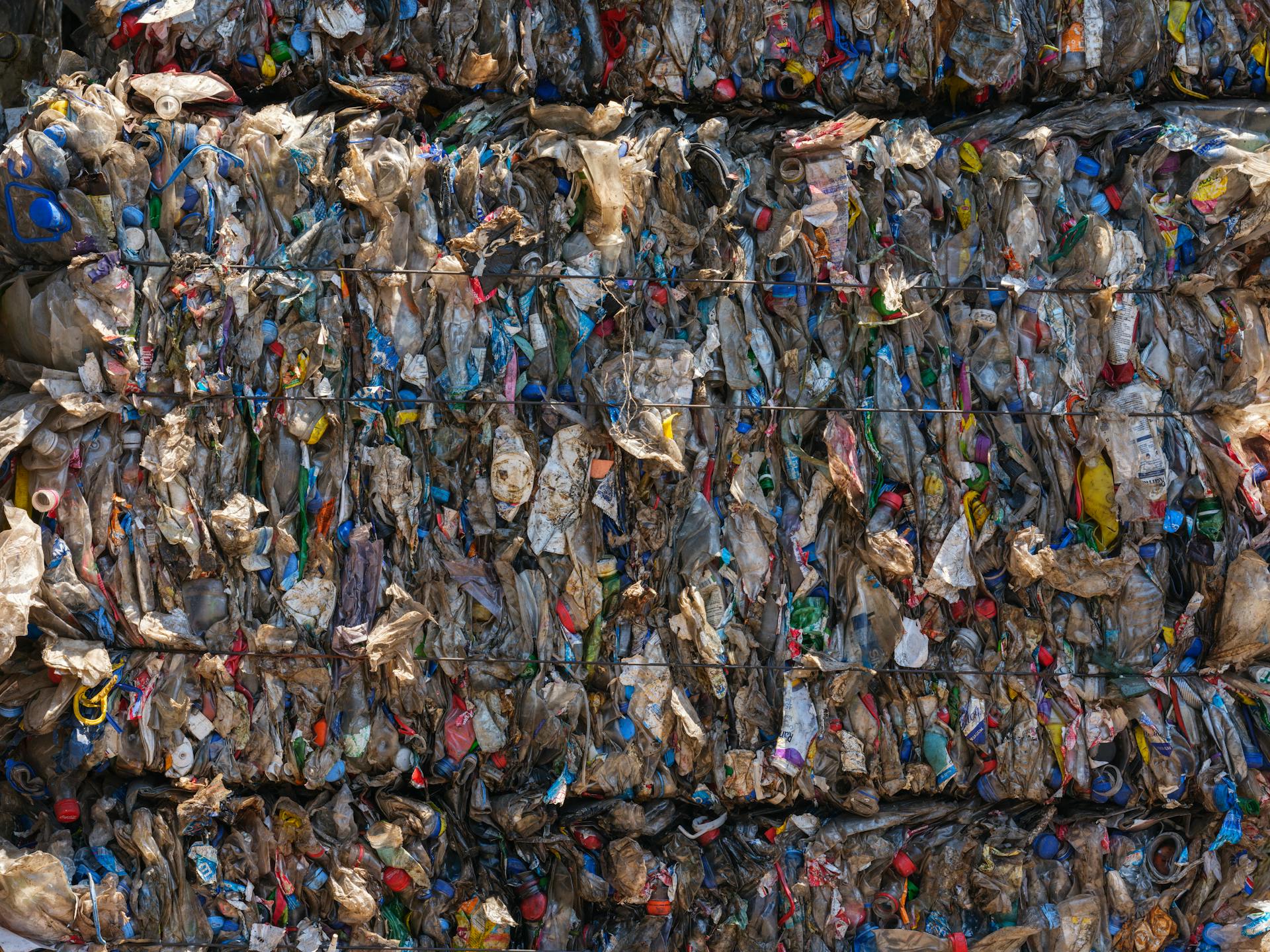
If you're looking for eco-friendly options, you'll be happy to know that many manufacturers now offer recyclable polyethylene foam sheets. This makes them a sustainable choice for consumers who care about the environment.
One of the best things about these foam sheets is how easy they are to handle. They're lightweight yet sturdy, making them a breeze to cut and shape, which in turn makes installation and application a hassle-free process.
Anti-Static
Anti-static materials are a game-changer for protecting electronic devices from damage.
Anti-static polyethylene foams, for instance, prevent the build-up of static electricity on electronic devices, which can cause damage or even destroy them.
These foams are typically pink in color and come in sheet form, making them easy to use in packaging electronic and semiconductor devices.
They provide excellent cushioning and minimize the effects of shock and vibration during transportation and handling, which is especially important for delicate devices.
By protecting devices from moisture, heat, and accidental spills, anti-static polyethylene foams offer a reliable safeguard against damage.
Expand your knowledge: Anti Static Stretch Wrap
Fire Retardant Sheets
Fire Retardant Sheets are a game-changer for safety-conscious builders and DIY enthusiasts.
Polyethylene foams, commonly used in fire retardant sheets, are inherently flammable.
To enhance their fire resistance, antimony oxide is often combined with halogen or phosphorus-based systems, but this raises environmental and health issues due to toxic fumes produced.
New techniques and halogen-free additives are being explored to improve fire resistance, with magnesium hydroxide emerging as a promising alternative.
Advancements in high-temperature melting, chemical cross-linking, and mold processing are also being pursued to create fire-resistant, low-density polyethylene foam.
This innovative approach combines ethylene-vinyl acetate with polyethylene foam to create a safer, more sustainable option.
Manufacturing Process
High density polyethylene foam sheets can be manufactured using two main processes: foam injection molding and temperature-induced batch foaming. These processes allow for the production of foams with complex shapes and precise dimensions.
Foam injection molding involves a large-scale, batch-mode foaming process that uses a barrel with heating zones and a reciprocating screw to mix the resin and blowing agent. The melt is injected with sufficient pressure and speed until it reaches the nozzle, triggering cell nucleation and growth as it fills the mold cavities.
Temperature-induced batch foaming, on the other hand, involves gas saturation in a high-pressure autoclave at lower temperatures, followed by cell nucleation and growth in a hot bath of oil, water, or glycerin.
Expand your knowledge: Paper Pulp Molding Machine
Extrusion
Extrusion is a continuous process used to produce foams with a uniform cross-section, such as sheets, rods, and tubes. It's a key method in foam manufacturing.
In foam extrusion, polyethylene pellets and additives are fed from a hopper into the barrel of a foam extruder, which has multiple heating zones. The blowing agent is introduced into the molten polyethylene either at the hopper or at a specific point in the barrel.
The extruder screw applies high pressure to push the melt through the barrel and out of the extruder die, causing cell nucleation and growth. This process is carefully controlled to achieve optimal results.
Foam extrusion can be classified as either a physical or a chemical foaming process, depending on the type of blowing agent used.
Here are the key differences between physical and chemical extrusion foaming:
- Physical extrusion foaming involves the injection and dissolution of a supercritical fluid, usually carbon dioxide or nitrogen, in the polyethylene melt at a certain point in the barrel.
- Chemical extrusion foaming involves the introduction of a blowing agent in the hopper together with the polyethylene pellets and additives, which thermally decomposes inside the barrel.
The choice of blowing agent and the control of the extrusion process are critical factors in achieving high-quality foam products.
Injection Molding
Injection molding is a large-scale, batch-mode process used to create complex shapes and precise dimensions.
This process involves a machine with a barrel, heating zones, and a reciprocating screw that feeds the resin and blowing agent into the polyethylene melt.
The blowing agent is introduced into the melt at a specific point in the barrel or at the hopper, depending on the type of agent used.
The melt is then injected with pressure and speed until it reaches the nozzle, where it undergoes a sudden pressure drop that triggers cell nucleation and growth.
The foam expands to fit the mold, remains in place for a specified time, and is then removed when the mold halves are opened.
Excess material around the foam product is trimmed off to create a clean and precise finish.
This process is repeated to meet production demands, allowing for the creation of large quantities of foam products.
The cost of tooling and energy can be significant in foam injection molding, but the end result is a product with precise dimensions and complex shapes.
Explore further: Pu Foam Process
Types of Resins and Blowing Agents
High density polyethylene foam sheets rely on two key components: the type of resin used and the blowing agent. The resin is the base material that provides the structure and properties of the foam, while the blowing agent is responsible for creating the cellular structure within the foam.
Polyethylene foams can be categorized into different types, but for high density applications, the type of resin used is crucial. Polyethylene foams are typically made from a type of thermoplastic resin.
The blowing agent used in polyethylene foams can be classified into two categories: chemical and physical blowing agents. Chemical blowing agents are great for creating fine cellular structures and can be further divided into reactive and non-reactive types, with examples including azodicarbonamide and sodium bicarbonate. Physical blowing agents, on the other hand, are in a gaseous form and are introduced directly into the polyethylene melt, with examples including carbon dioxide and nitrogen.
Here's a breakdown of the types of blowing agents:
- Chemical blowing agents: Azodicarbonamide, sodium bicarbonate, zinc carbonate, and acylhydrazide
- Physical blowing agents: Carbon dioxide, nitrogen, argon, water, air, and chlorofluorocarbons
- Expandable beads: Thermoplastic acrylic resin polymer with hollow spherical microparticles
Resins
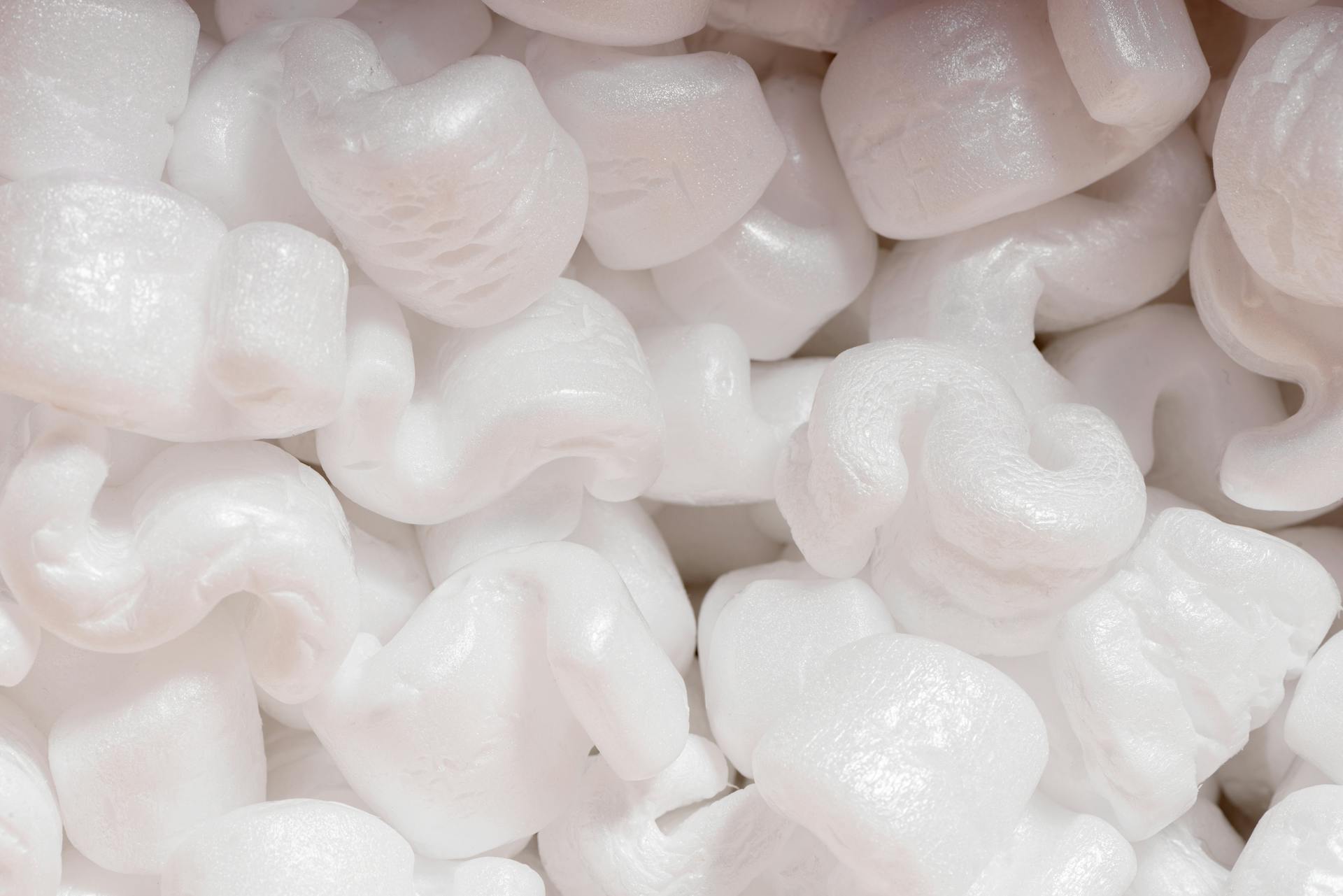
Polyethylene resin is the primary component in the production of polyethylene foams.
Low-density polyethylene (LDPE) and high-density polyethylene (HDPE) resins are the most commonly used types. LDPE foams are known for their lightweight, elasticity, water resistance, and cost-effectiveness.
HDPE foams offer greater strength and durability compared to LDPE foams.
Blowing Agents
Blowing Agents play a crucial role in creating fine cellular structures within the polyethylene matrix.
Chemical blowing agents are classified into two categories: those that liberate gas through thermal decomposition or a chemical reaction, and those that are reactive and produce nitrogen or carbon dioxide gas. Examples of chemical blowing agents include azodicarbonamide, sodium bicarbonate, zinc carbonate, and acylhydrazide.
Physical blowing agents, on the other hand, are in a gaseous form and are introduced directly into the polyethylene melt. Examples of physical blowing agents include carbon dioxide, nitrogen, argon, water, air, and chlorofluorocarbons.
Some chemical blowing agents, like azodicarbonamide, are exothermic, while others, like sodium bicarbonate, are endothermic. This means they either release or absorb heat during the reaction.
Physical blowing agents can be introduced into the polyethylene melt in various ways, depending on the specific application and desired outcome.
Here's a breakdown of the types of chemical blowing agents mentioned in the article:
- Azodicarbonamide: exothermic
- Sodium bicarbonate: endothermic
- Zinc carbonate: endothermic
- Acylhydrazide: thermal decomposition
Customization and Lamination
High density polyethylene foam sheets can be laminated with other materials to create thicker layers, which enhances their mechanical strength, cushioning effect, insulation properties, and overall durability.
This process allows for the creation of thicker, more robust foam sheets that can provide even better comfort and ergonomics. Polyethylene foams can be used as padding and cushioning for various furniture items, such as chairs, couches, and car seats.
Custom-cut cross-poly foam is also available, allowing you to select from various options, including simple square pieces or custom pattern shapes. However, keep in mind that certain shapes, like cylinders and wedges, may have size limitations due to the nature of the foam.
If this caught your attention, see: Custom Pu Foam Blocks
Custom-Cut Cross-Poly
Custom-cutting your cross-poly foam to precise dimensions is possible. You can select from various options, including simple square pieces or custom pattern shapes.
The type of foam makes some limitations unavoidable. Due to its nature, custom sizes can't be cut in all dimensions.
You can cut custom sizes in certain dimensions, but there are some restrictions. For instance, cylinders and wedges can't be cut deeper than 2 inches.
Laminated
Laminated foams can be created by layering polyethylene foam sheets with other materials, resulting in enhanced mechanical strength and insulation properties.
This process can also improve the durability of the foam, making it a great option for furniture that needs to withstand heavy use.
Polyethylene foams can be used as padding and cushioning for various furniture pieces, including chairs, couches, beds, and car seats.
They can even be used to enhance ergonomics in furniture, providing comfort and support to users.
Open-cell foams, on the other hand, are softer and more comfortable than polyethylene foams, making them a great option for applications where comfort is a top priority.
Frequently Asked Questions
What are the disadvantages of polyethylene foam?
Polyethylene foam can be a costly option due to its time-consuming fabrication and processing. It may also be prone to breaking or tearing, depending on its formulation.
Sources
- https://www.alibaba.com/showroom/high-density-polyethylene-foam-sheets.html
- https://www.iqsdirectory.com/articles/foam-fabricating/polyethylene-foam.html
- https://www.foamorder.com/foam/cross-poly-foam
- https://www.foamfabricators.ie/closed-cell-polyethylene-foam
- https://www.olympicoutdoorcenter.com/products/closed-cell-foam-with-adhesive
Featured Images: pexels.com