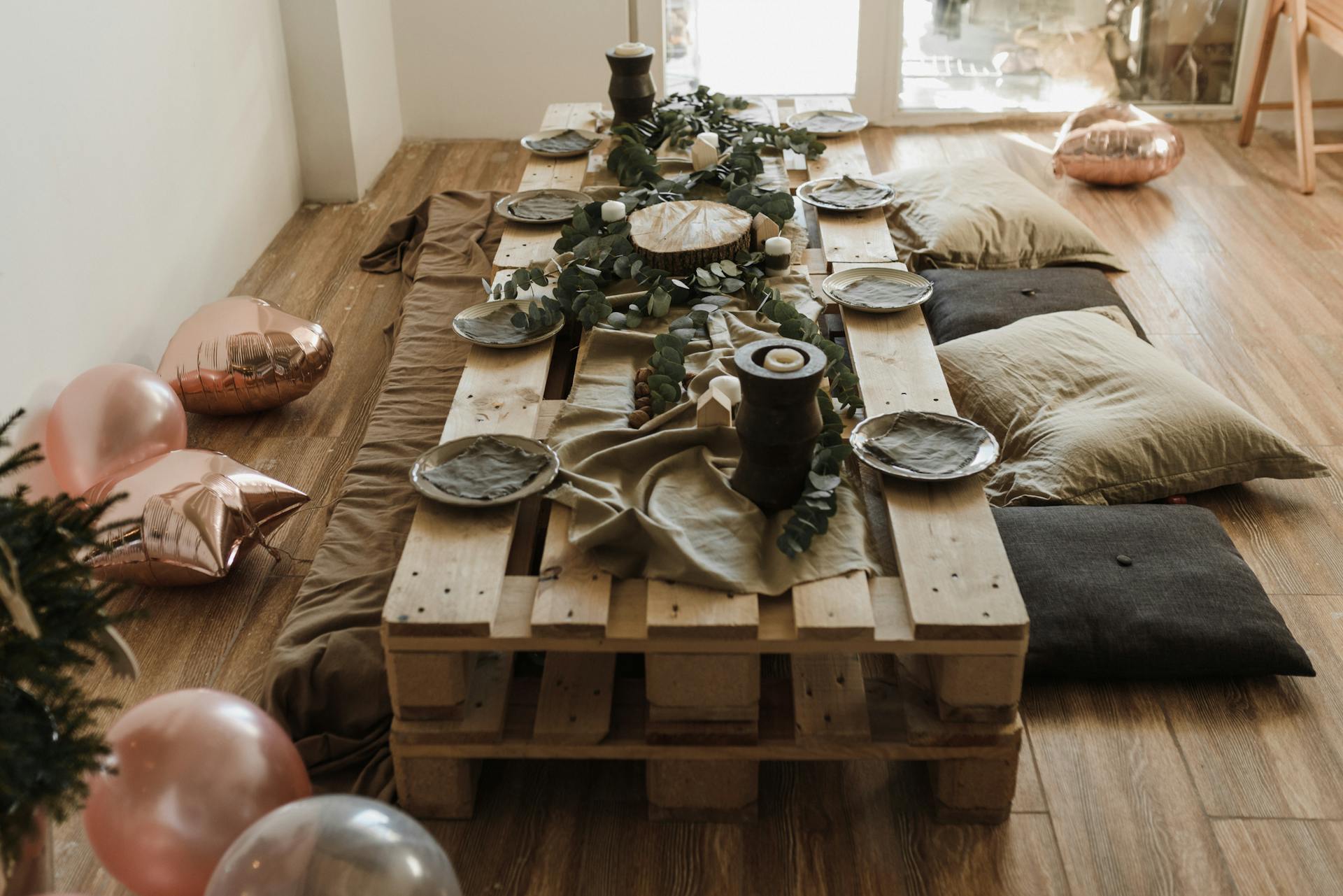
Wrapping pallets correctly and safely is crucial to prevent damage and ensure secure transportation. According to the article, the best wrapping material for pallets is stretch wrap, as it provides a tight and secure hold.
To start wrapping your pallet, you'll want to begin at the bottom and work your way up. This helps prevent air bubbles from forming and makes the wrapping process more efficient.
A typical pallet wrap job requires 2-4 wraps, depending on the size of the pallet and the weight of the load. This is because each wrap provides additional support and stability to the load.
By following these simple steps, you can ensure your pallets are wrapped correctly and safely, reducing the risk of damage and accidents during transportation.
Pallet Wrapping Basics
Good stacking is the foundation of good pallet wrapping. Stack inventory without gaps as much as possible and use slip sheets between layers to help prevent shifting.
Start with larger and heavier items on the bottom, and use a column-style stacking pattern where possible. Finish with lighter boxes at the top.
To ensure a stable load, confirm your pallet load weight is within the pallet specifications.
Here's a quick checklist to keep in mind:
- Stack inventory without gaps
- Use slip sheets between layers
- Start with larger items on the bottom
- Finish with lighter boxes at the top
- Confirm pallet load weight is within specifications
By following these simple steps, you'll be well on your way to creating a stable and secure pallet load.
Pallet Basics
Good stacking is key to a well-wrapped pallet. Start with larger and heavier items on the bottom, and use a column-style stacking pattern where possible.
Use slip sheets between layers to help prevent shifting. This will ensure a stable load and prevent damage during transit.
The weight of the pallet load should be confirmed to be within the pallet specifications. This is crucial to prevent damage to the pallet and the items being transported.
Hazards in the work area should be checked and cleared before wrapping a pallet. This includes any obstacles that could impede safe worker movement.
Here's a quick checklist to ensure you're starting with a solid foundation:
- Larger and heavier items on the bottom
- Use slip sheets between layers
- Confirm pallet load weight is within specifications
- Clear hazards in the work area
Blown vs Cast
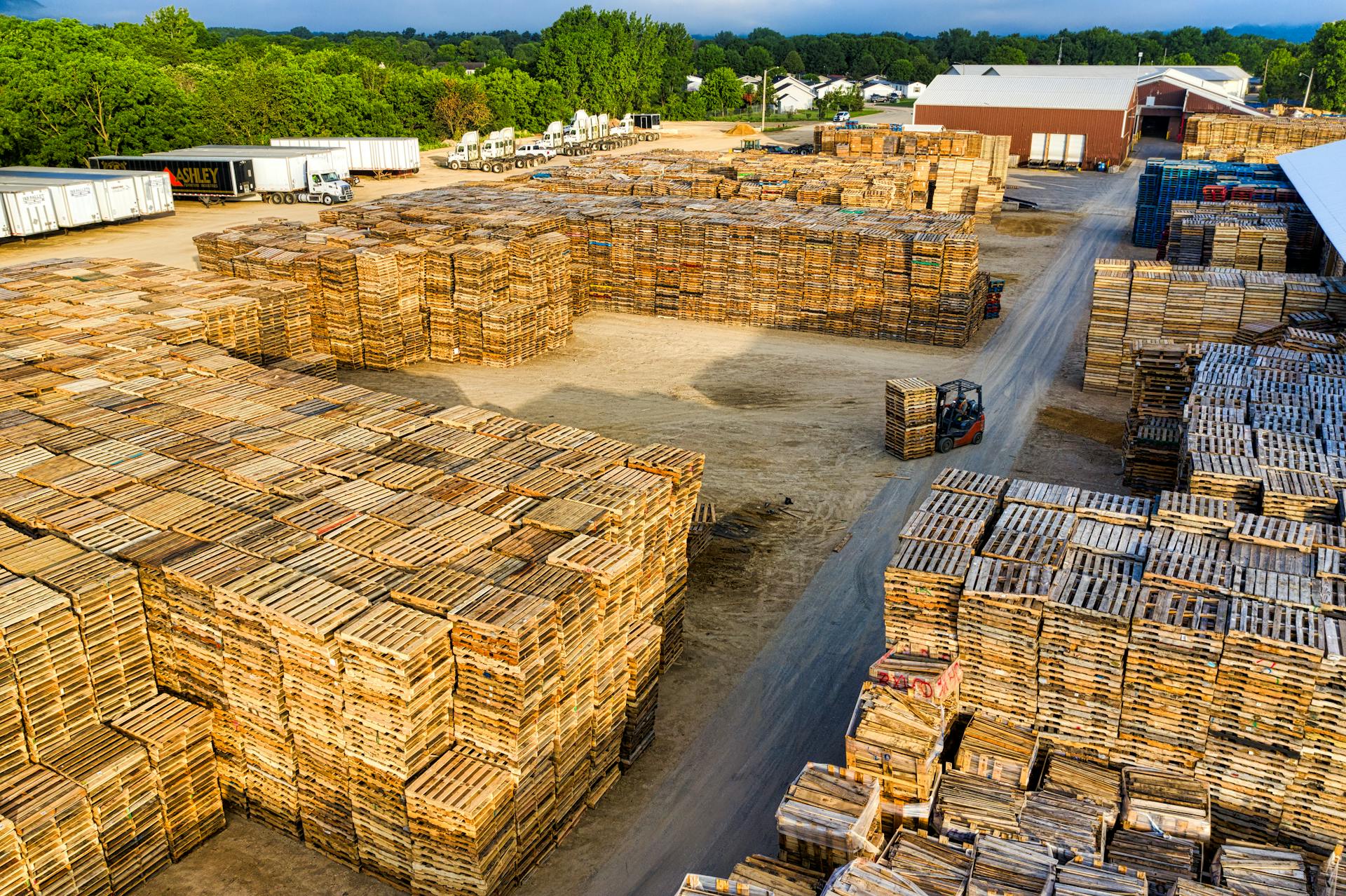
Blown vs Cast stretch wrap are two main types of stretch wrap materials used for industrial applications. Each type has its own unique characteristics.
Cast stretch wrap is known for its clarity, making it easy to scan barcodes and labels on products. This type of stretch wrap is considered less durable and is best suited for light- or medium-duty applications.
Blown stretch wrap, on the other hand, is less clear but offers a high stretch capacity and durability. It's ideal for heavy-duty wrapping applications and provides extra protection during transit and storage.
The choice between cast and blown stretch wrap ultimately depends on the specific needs of your application. If you need to scan barcodes frequently, cast stretch wrap may be the better choice. If you're wrapping items with sharp edges or irregular shapes, blown stretch wrap is likely a better option.
Here's a quick comparison of the two types of stretch wrap:
UVI
UVI stretch wrap is a specialty wrap that includes light-discouraging additives to protect pallets from ultraviolet radiation. This can cause yellowing or discoloration of products or packaging over time.
The slow degradation rate of UVI stretch wrap is one of its key benefits. This means it lasts longer and provides better protection for your products.
You can use UVI stretch wrap for outdoor use, where it's exposed to the elements. This makes it an ideal choice for businesses that ship products outside.
UVI stretch wrap comes in two varieties: clear and opaque. This gives you the flexibility to choose the right type for your needs.
Here are some key characteristics of UVI stretch wrap:
- Treated with ultraviolet additives
- Slow degradation rate
- Ideal for outdoor use
- Can be clear or opaque
Pre
Pre-stretch wrap is a game-changer for businesses looking to reduce their packaging expenses. It uses nearly half as less film as other pallet wraps, making it a cost-effective solution.
This lightweight wrap also offers improved cost savings, which can be a huge relief for small businesses or those on a tight budget. By reducing the amount of film used, you can save money on materials and reduce waste.
You might like: Cling Film Wrapper
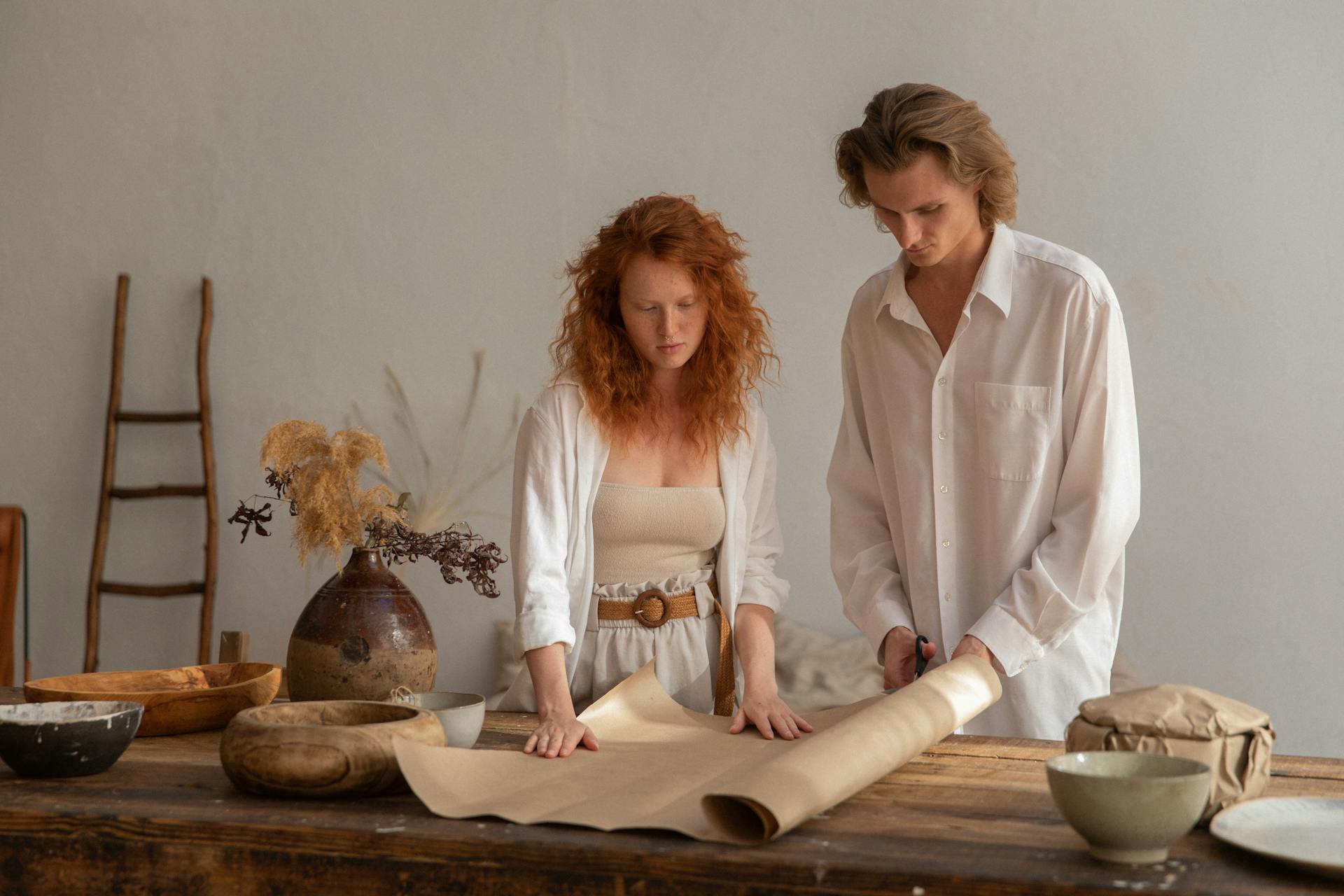
One of the key benefits of pre-stretch wrap is its increased holding force, which means it can keep your pallets secure without breaking the bank. This is especially important for businesses that ship fragile or heavy items.
Here are some key characteristics of pre-stretch wrap:
- Lightweight and durable
- Improved cost savings
- Increased holding force
- Less environmental waste
Vented
Vented pallet wrapping is a game-changer for certain types of products. It's designed to allow air to circulate around the pallet, which is perfect for wrapping wood, landscaping products, hot and cold foods, and produce.
This design feature helps prevent moisture buildup and mold growth, ensuring that your products arrive at their destination in top condition. I've seen firsthand how vented stretch wrap can make a big difference in preserving the quality of perishable goods.
One of the key characteristics of vented stretch wrap is its reinforced fiber. This adds strength and durability to the wrap, making it less likely to tear or break during shipping.
Here are some key benefits of vented stretch wrap:
- Vented design
- Slows foods from rotting
- Prevents mold growth
Gauge
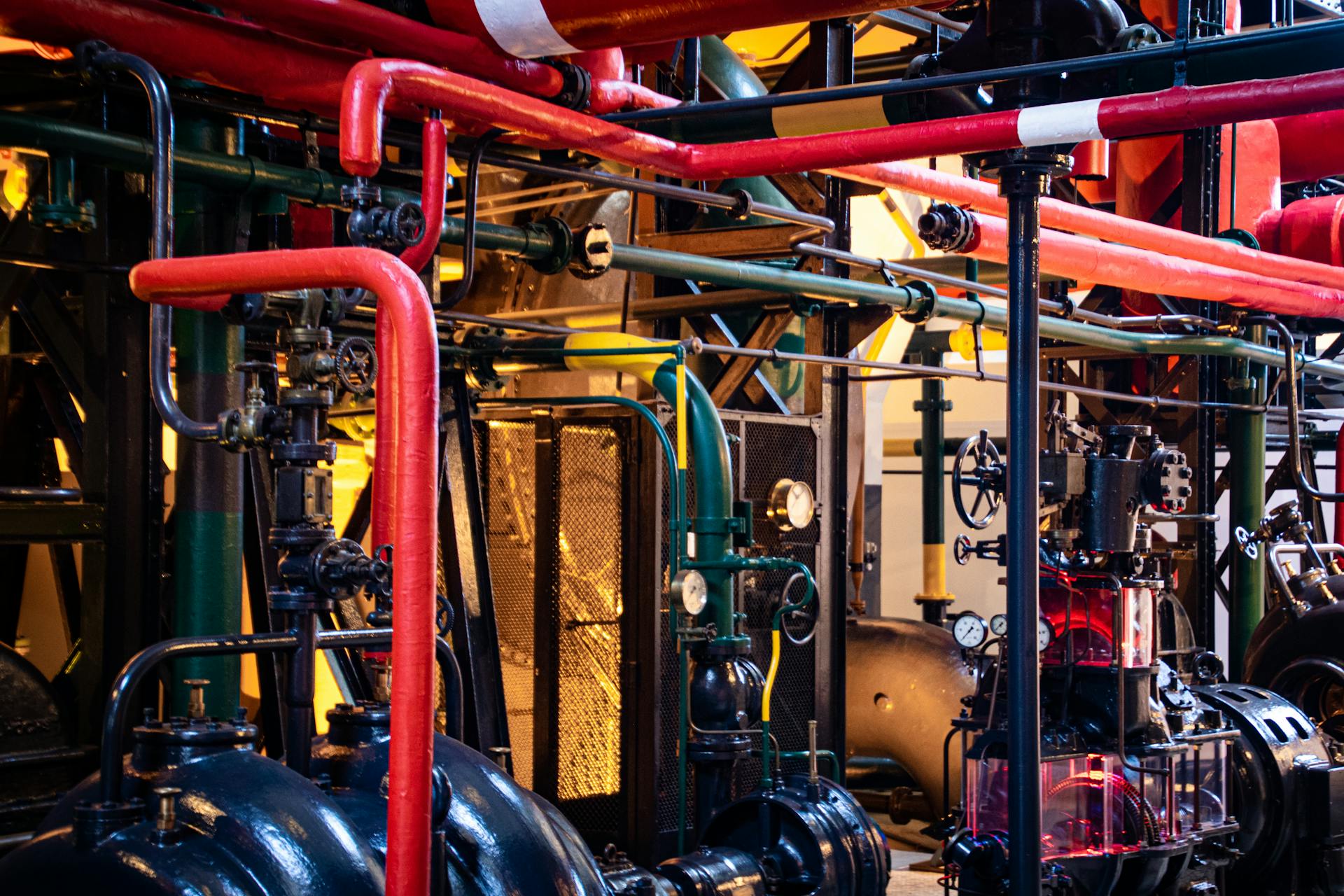
Gauge is a crucial factor to consider when it comes to pallet wrapping. It represents how thick a stretch wrap is, and the higher the gauge, the more durable your stretch wrap will be.
A 37 gauge is typically found in pre-stretched wraps, while a 47 gauge is a hybrid gauge that can be used for heavier products. However, it's not suitable for products with sharp edges or abnormal shapes.
60 gauge stretch wraps feature increased puncture resistance and can be used for heavier objects. This gauge is a great middle ground for many applications.
70 gauge stretch wraps offer increased durability and can be used to wrap heavy pallets or products with mildly sharp edges. They're a popular choice for many industries.
The most common gauge for stretch wraps is 80 gauge, known for its versatility and wide range of wrapping applications. It's a great all-around choice for many users.
Readers also liked: Stretch Wrap Gauge
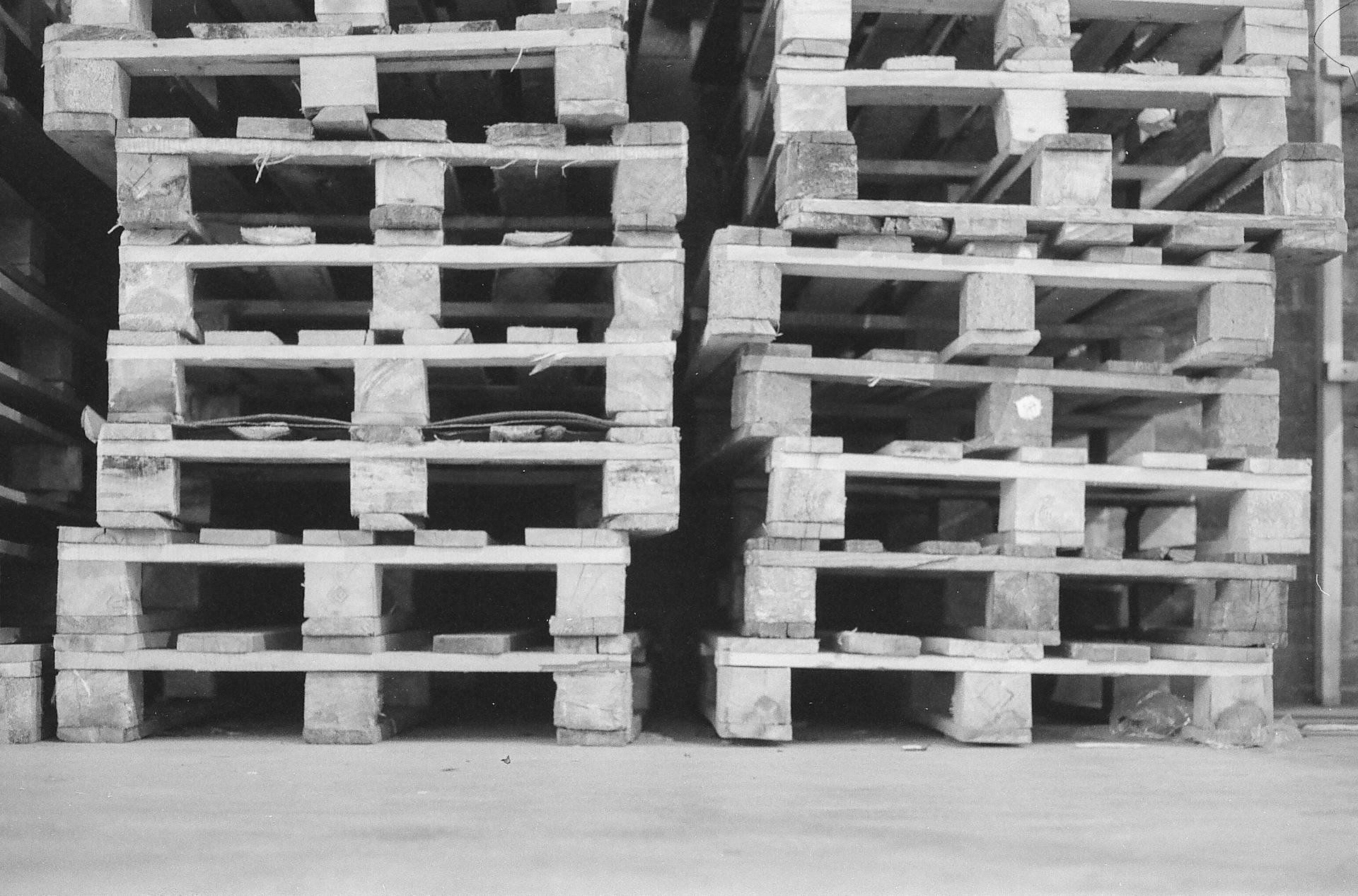
For heavier-duty loads, consider using 90 gauge or 100 gauge stretch wraps. These gauges offer enhanced durability and are ideal for wrapping heavy pallets.
If you need the most strength and puncture resistance, look for a 115 gauge or 150 gauge stretch wrap. These gauges are perfect for wrapping heavy-duty pallets and objects with irregular shapes or sharp edges.
Here's a quick reference guide to help you choose the right gauge:
Cores
When it comes to wrapping your pallets, you'll need to choose the right core for the job. There are three main types of stretch wrap cores: standard, one-sided extended, and two-sided extended.
A standard core is ideal for use with machines or dispensers, fitting perfectly onto the spindle of a stretch wrap machine and being compatible with most stretch wrap dispensers.
One-sided extended cores are a great option for businesses that want to wrap pallets by hand, allowing for quick and efficient use without the added expense of a dispenser.
Recommended read: Which End of Pallet Industry Standard for Lifting Pallets
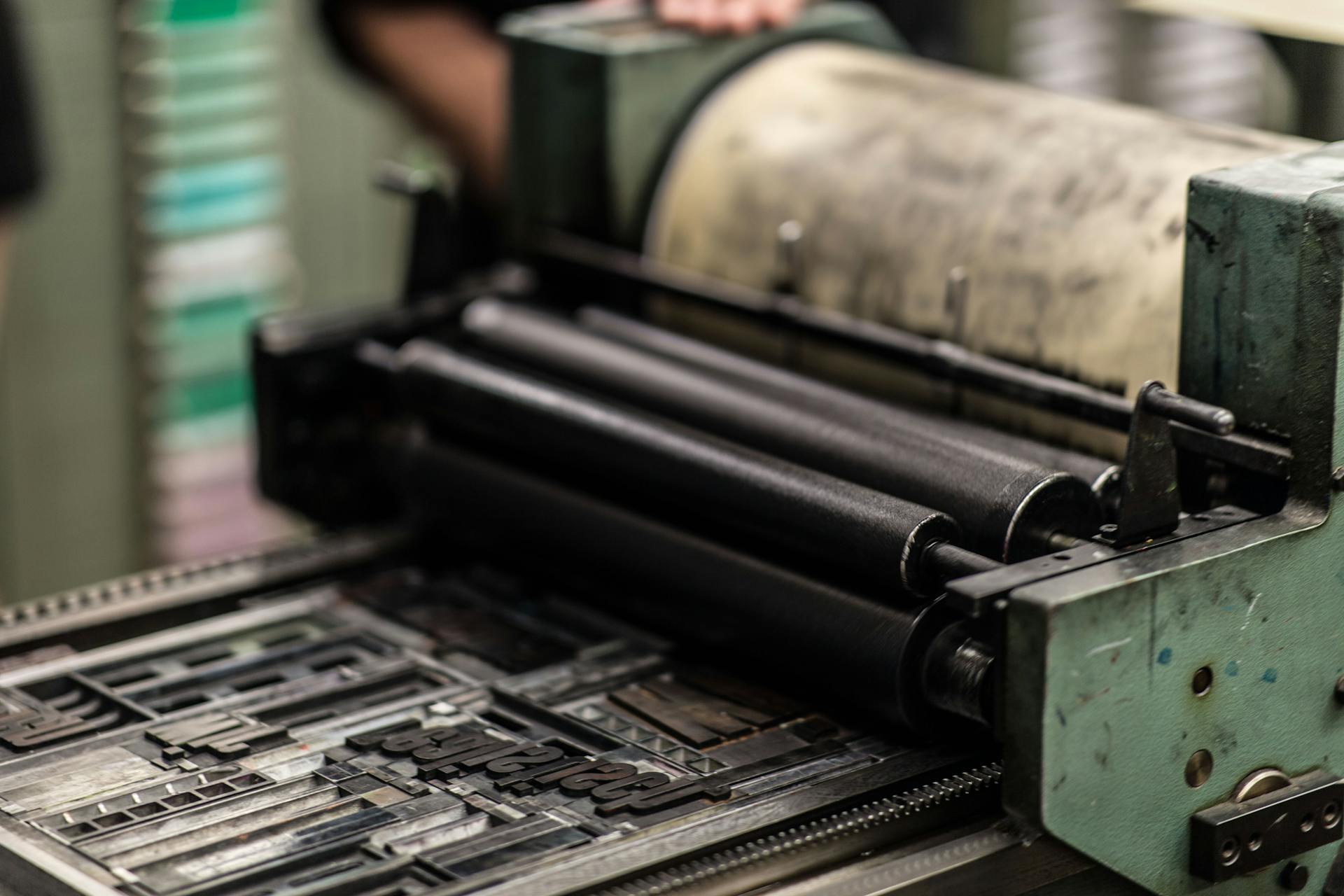
Two-sided extended cores are ideal for businesses that need to wrap pallets quickly and efficiently, with an extended length on both sides.
Here's a quick rundown of the different types of cores:
Wrapping Machines
Wrapping machines come in different types, including semi-automatic and fully automatic models. These machines can wrap pallets at varying speeds, ranging from 12 rpm to 65 rpm.
Semi-automatic machines are a great option for those who want to reduce manual labor. They can wrap pallets at speeds of up to 30 pallets per hour and often come with features like cut & clamp units and touch screens.
Fully automatic machines, on the other hand, can wrap pallets at much higher speeds. Some models can even reach speeds of up to 65 rpm and wrap up to 130 pallets per hour.
There are several types of wrapping machines, including turntable stretch wrappers, rotary arm stretch wrappers, and horizontal stretch wrappers. Each type is designed for specific applications and can handle different types of pallets.
A fresh viewpoint: Stretch Wrap Equipment
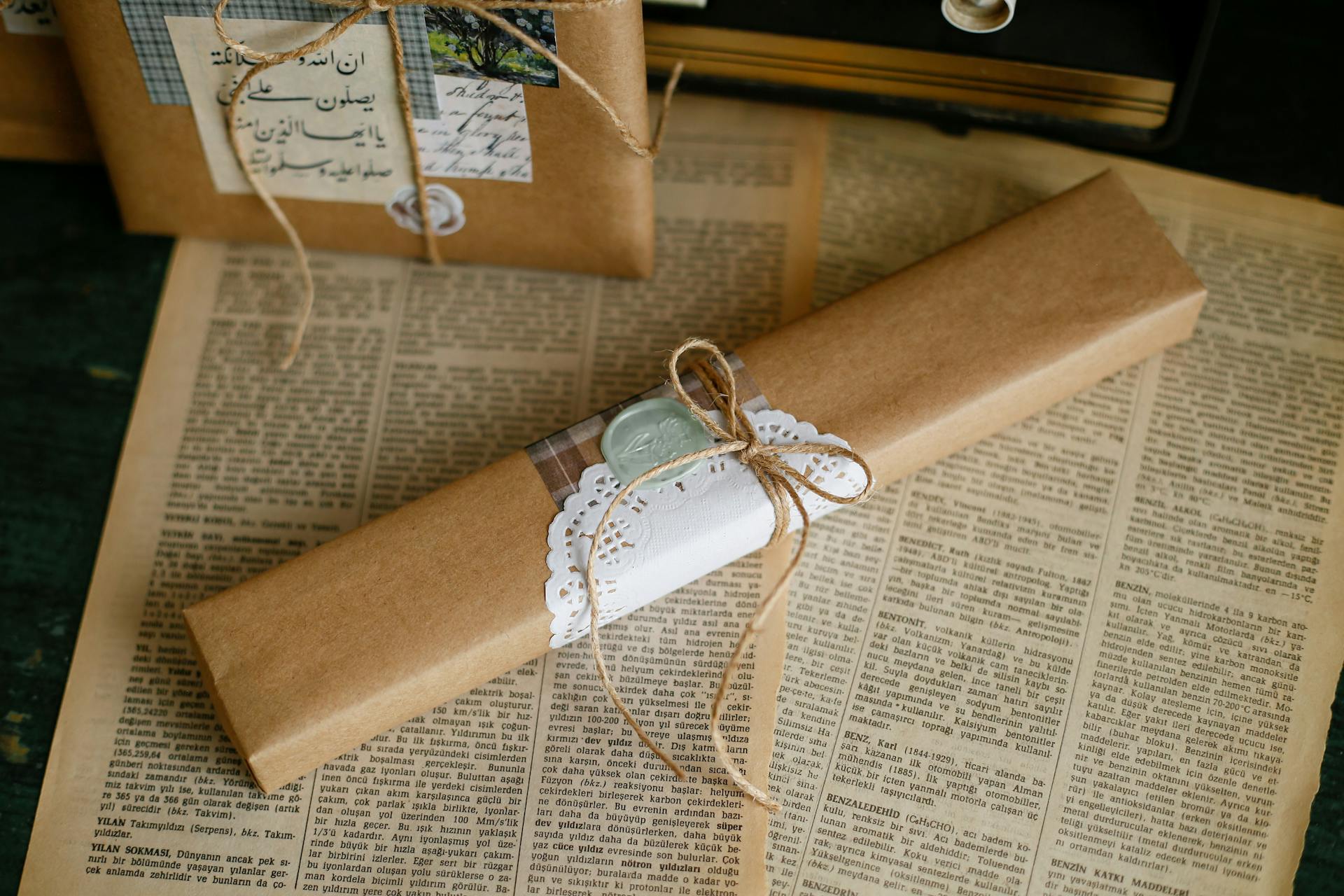
Here are some common features found in wrapping machines:
- Turntable stretch wrappers: ideal for most commercial wrapping applications
- Rotary arm stretch wrappers: useful for light loads or heavy loads
- Horizontal stretch wrappers: ideal for wrapping lengthy items
Some wrapping machines also come with pre-stretch systems that can stretch the wrapping film to the desired pre-stretch percentage. This feature can help reduce waste and improve the overall wrapping process.
Fully automatic pallet wrapping machines can process up to 150 pallets per hour and often come with multiple wrapping programs to choose from. These machines can also select the right wrapping pattern for each load, making the process even more efficient.
Safety and Regulations
Pallet wrapping is a year-round activity in warehouse facilities, and it's a critical component of warehouse safety. It secures loose items onto a pallet to protect the inventory from damage and workers from injuries.
Load stability and uniform weight distribution across the pallet are crucial elements of safe palletizing and wrapping. This ensures forklift operators can safely secure the pallet onto the forks, lift it, and place it into a pallet rack system or truck.
Back injuries are a common workplace injury associated with pallet wrapping, sustained from bending and pulling the wrap using the required force. You can mitigate these concerns with an ergonomically supportive wrap dispenser.
OSHA has identified several workplace injuries common to pallet wrapping, including back injuries. Implementing safe procedures and protective equipment can save workers from painful injuries and operations from downtime and worker's compensation costs.
Pallet Wrapping Techniques
Pallet wrapping techniques are crucial for ensuring your goods arrive safely at their destination.
There are several techniques to choose from, including hand wrapping, machine wrapping, and shrink wrapping.
Hand wrapping is a simple and cost-effective method, but it can be time-consuming and may not provide the same level of protection as other methods.
Machine wrapping is a more efficient option, but it requires a significant upfront investment and may not be feasible for small businesses or one-time shipments.
Shrink wrapping is a popular choice for fragile or irregularly shaped items, as it provides a tight seal and can be easily customized to fit unique shapes.
Check this out: Shrink Wrapping Film
Correct Handing Technique
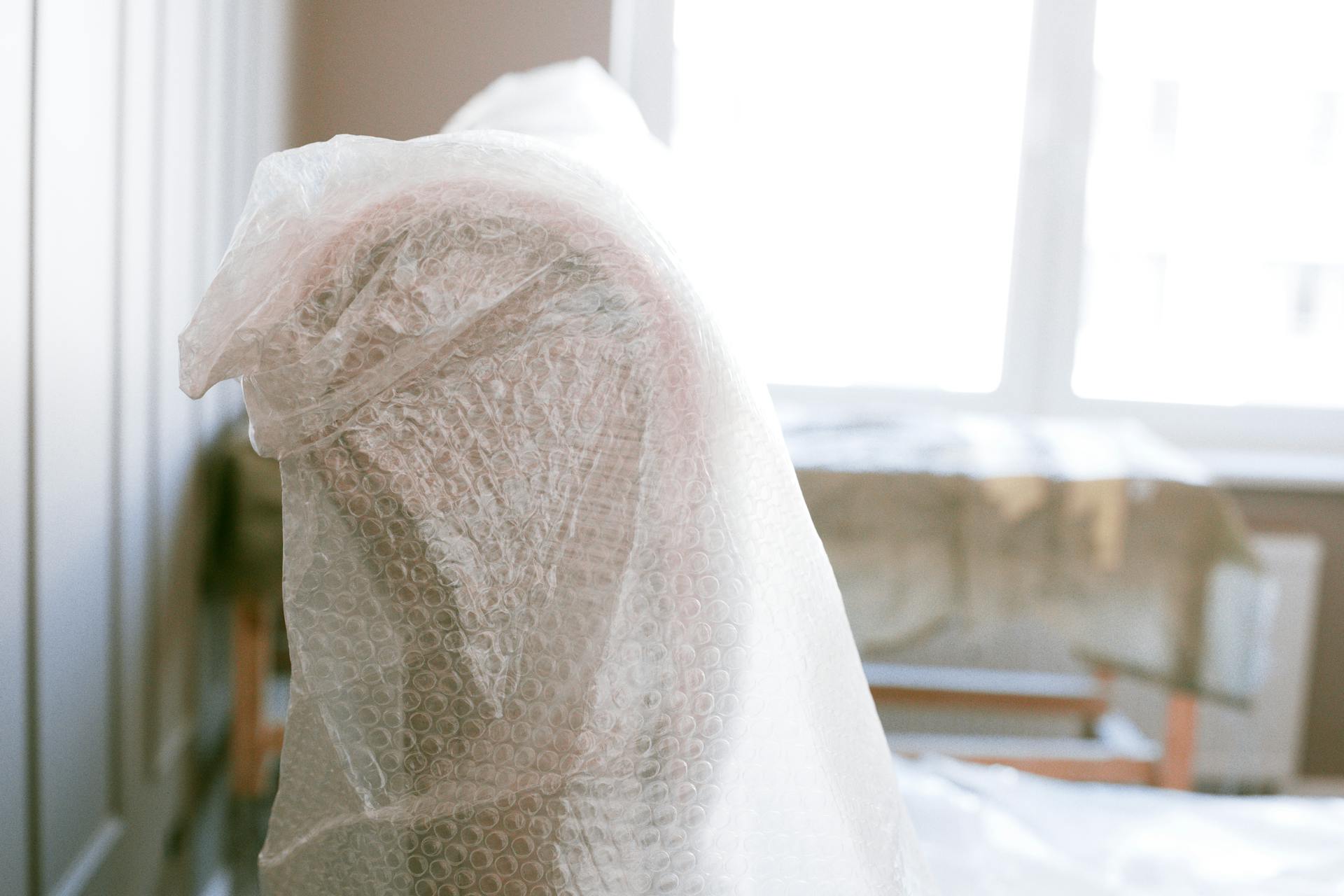
Correct Handing Technique is crucial for efficient pallet wrapping. A well-handled pallet is easier to wrap and reduces the risk of damage.
Start by positioning the pallet on a stable surface, with the opening facing you. This ensures a smooth wrapping process.
Next, ensure the pallet is level and secure to prevent it from shifting during wrapping. A stable pallet is essential for consistent wrapping results.
Hold the film at a 45-degree angle, with the edge of the film aligned with the edge of the pallet. This angle allows for even tension and prevents wrinkles.
To maintain even tension, apply gentle to moderate pressure as you wrap the film around the pallet. Avoid applying too much pressure, which can cause the film to buckle.
As you wrap, keep the film taut but not too tight, allowing for a small amount of give. This ensures a snug fit without compromising the structural integrity of the pallet.
When Manual Isn't Enough
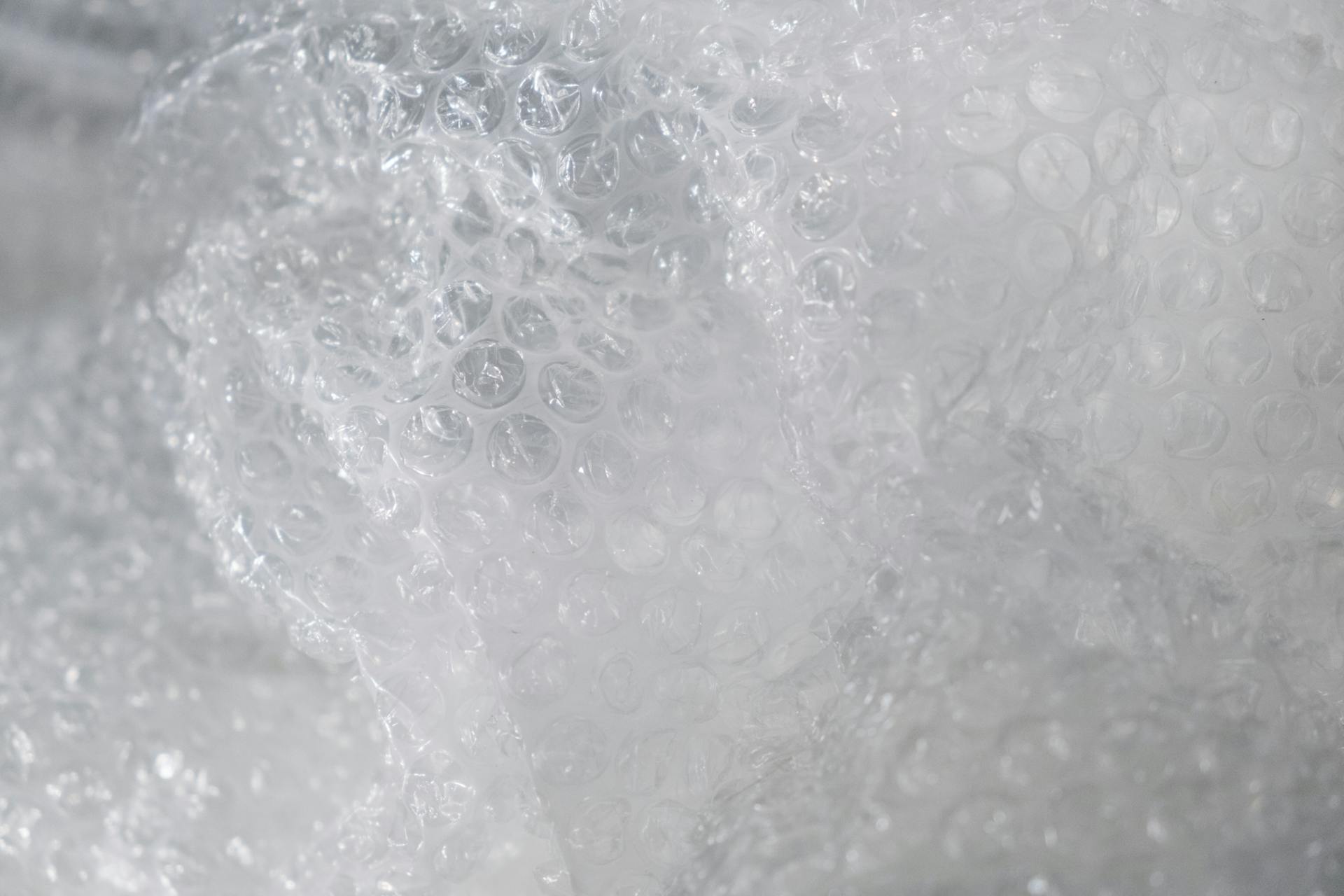
Manual wrapping can only handle a few pallets per hour, making it impractical for high-capacity operations.
If you've outgrown manual wrapping, semi-automatic or fully automatic pallet wrapping machines can increase your efficiency.
These machines are provided by companies like Matco International, which offers a wide range of options to choose from.
A semi-automatic pallet wrapping machine can help you keep up with demand, while a fully automatic machine can take it to the next level.
The choice between a semi-automatic and fully automatic machine ultimately depends on your specific needs and preferences.
Pallet Wrapping Accessories
Pallet wrapping accessories can make a big difference in the efficiency of your staff. A stretch wrap machine is a great option for businesses of all sizes, allowing you to automate the pallet wrapping process and save time and effort.
A stretch wrap dispenser is a must-have for hand-wrapping pallets, making the process more efficient and convenient. They come in several forms and can be used for light-, standard-, and heavy-duty wrapping applications.
Using a film cutter is a safer and more efficient way to slice through stretch wrap film for precise cuts. This is especially useful when cutting through thicker films.
Accessories
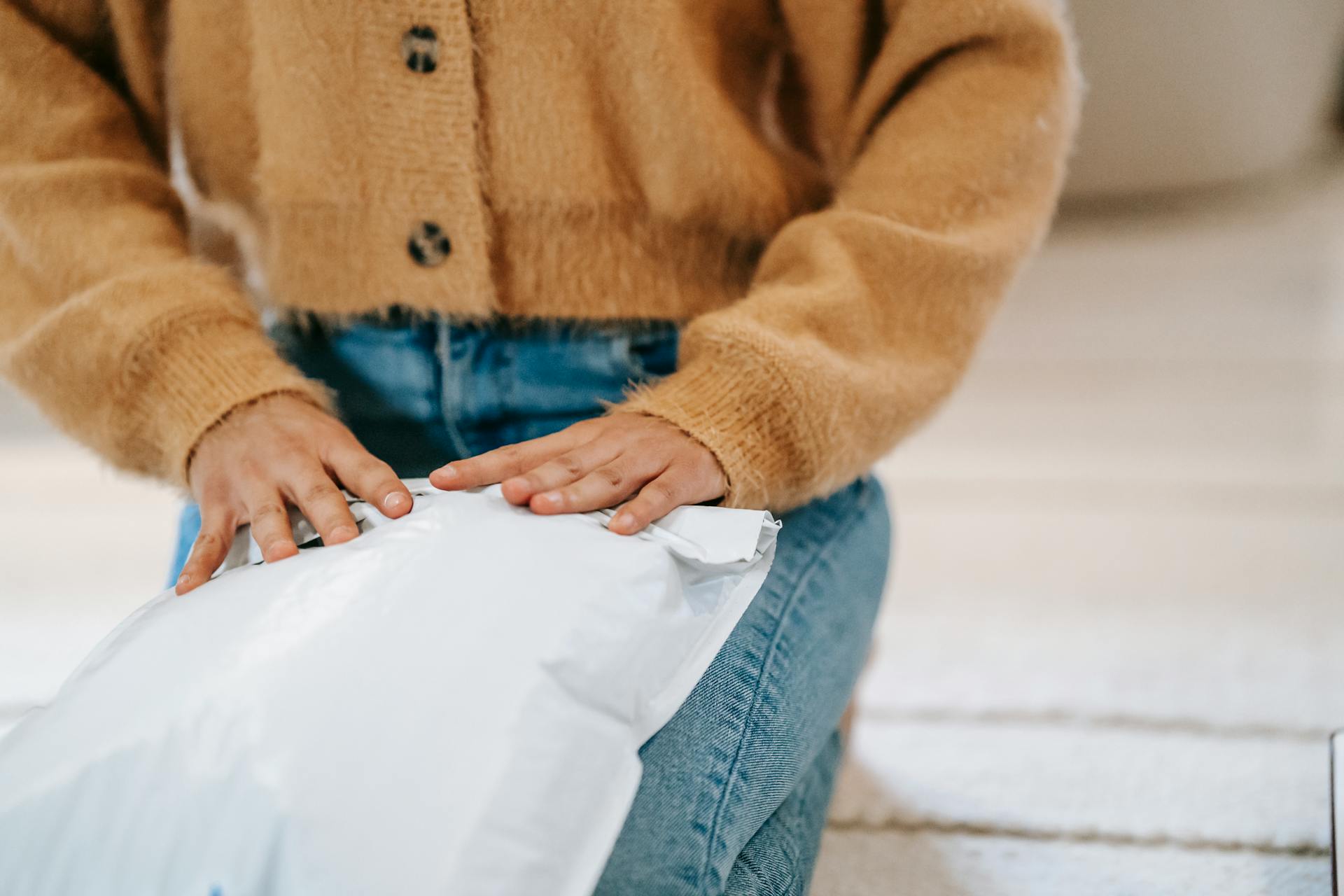
Stretch wrap machines can be adjusted for size and scale, making them a great option for businesses of all sizes.
Automating the pallet wrapping process with a stretch wrap machine can save you a significant amount of time and effort.
A stretch wrap dispenser can make wrapping pallets by hand more efficient, and they come in several forms for light-, standard-, and heavy-duty wrapping applications.
These dispensers can be used to improve accuracy and ensure the entire pallet is secure.
A film cutter offers a safer and more efficient way to slice through stretch wrap film for precise cuts.
Using a film cutter can eliminate the frustration and time-consuming process of cutting stretch wrap film with scissors.
Here are the four main types of stretch wrap dispensers:
These types of dispensers can help you optimize the wrapping process and improve efficiency in your warehouse.
Color
Color can play a significant role in pallet wrapping, especially when it comes to color stretch wrap.
Assigning different colors of stretch wrap to pallets makes it easy to identify products or shipments. This is particularly useful in warehouses where products or shipments need to be tracked.
Color stretch wrap is also used to track the production date of products, allowing warehouse managers to quickly identify the oldest items.
Color stretch wrap is commonly used in international transportation, as it helps meet specific regulations about packaging products for importation and exportation.
Here are some key characteristics of color stretch wrap:
- Easy to identify
- Tamper-proof
- Improved appearance
- Puncture-resistant
The Advantages of
Wrapping pallets is a simple yet effective way to protect your products during shipping and storage. A solid, complete, and inexpensive packaging is one of the key advantages of pallet wrapping.
Protection against dirt and damage is also a major benefit. This is especially important for fragile products that need extra care.
One of the easiest ways to apply pallet wrapping is to use a machine that can stretch and wrap the film around the pallet quickly and efficiently. This makes the process faster and more cost-effective.
For more insights, see: Glad Wrap Products
Pallet wrapping is suitable for a wide range of products, from boxes to doors. This versatility makes it a great option for businesses that need to ship a variety of items.
By wrapping pallets with a coloured film, you can make the product more recognisable, which can be helpful for inventory tracking and theft prevention.
Pallet Wrapping Videos
You can find plenty of pallet wrapping videos online to learn the basics and get tips from experienced wrappers.
The right wrapping technique is crucial to prevent damage and make the pallet more secure.
A well-wrapped pallet can save you time and money in the long run by reducing damage and losses.
Watch videos that demonstrate the use of different types of wrapping materials, such as stretch wrap and shrink wrap.
Stretch wrap is a popular choice for pallet wrapping because it's easy to use and provides good protection.
Shrink wrap, on the other hand, is more durable and provides better protection for fragile items.
Some videos show how to wrap pallets with a forklift or a wrapping machine for faster and more efficient wrapping.
These machines can increase productivity and make wrapping pallets a breeze.
Broaden your view: How to Use Pallet Truck
Frequently Asked Questions
How much does it cost to wrap a pallet?
Wrapping a standard pallet costs between $1.50 to $2.00, depending on the wrapping machine used. Learn more about pallet wrapping costs and options.
How many times should you wrap a pallet?
For a standard pallet under 2,000 pounds, aim for 3 revolutions of wrap on top and bottom for secure loading. However, be cautious not to overwrap, as it can waste time and resources without added benefit.
Sources
- https://www.webstaurantstore.com/article/811/how-to-wrap-a-pallet.html
- https://www.apexwarehousesystems.com/pallet-wrapping-101-pallet-packing-osha-safety-more-apex-safety-spotlight/
- https://www.webstaurantstore.com/guide/1048/types-of-pallet-wrap.html
- https://matco-international.com/pallet-wrapping/
- https://omnigroup.com.au/blogs/correct-way-to-hand-stretch-wrap-pallet
Featured Images: pexels.com