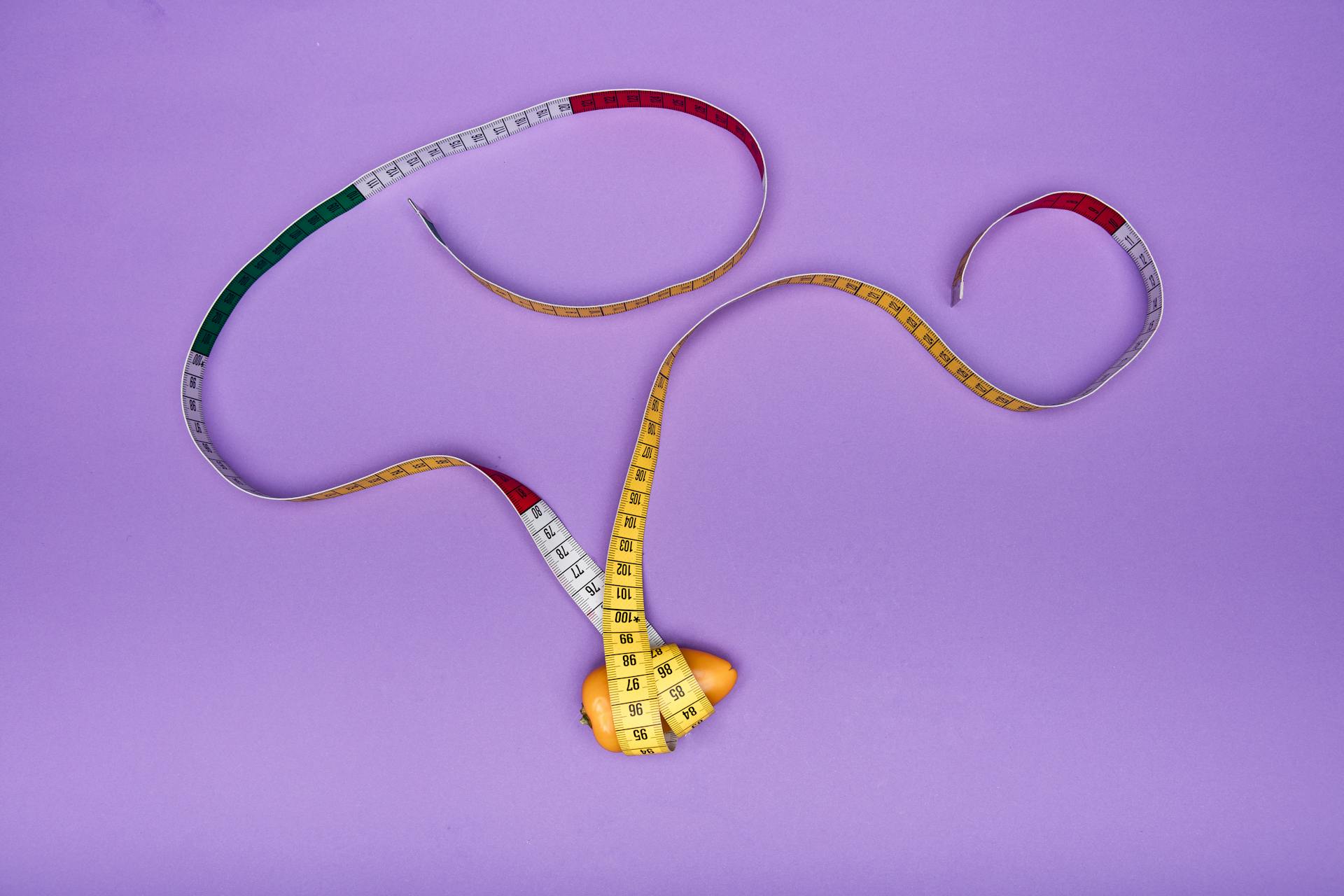
Stretch wrap gauge options can be overwhelming, but understanding the specifications can make all the difference. There are three main types of stretch wrap gauges: manual, digital, and automatic.
Manual stretch wrap gauges are the most basic and affordable option, typically priced between $50 to $200. They're often used for small-scale operations.
Digital stretch wrap gauges offer more accuracy and can be calibrated to precise measurements. Some digital gauges can even store data for future reference.
Automatic stretch wrap gauges take precision to the next level, with some models capable of wrapping up to 100% of the load's surface area.
What Is?
Stretch wrap gauge is a measure of a stretch wrap's thickness. The gauge of stretch wrap film typically ranges from 40 gauge to 150 gauge, with the number indicating the thickness of the film in micrometers.
A higher gauge number means the film is thicker and more resistant to punctures and tears. For example, a 40 gauge film is very light and might be used for uniform and not very heavy loads, while a 150 gauge film would be robust enough to secure a pallet of bricks or metal parts.
On a similar theme: Stretch Wrap Gauge Chart
The choice of stretch film gauge depends on the load's weight, shape, and the likelihood of protrusions that could stress the film. General purpose 80-gauge wrap is the industry standard and can secure loads up to 2,400 lbs.
Here's a conversion chart to help you understand the different gauge numbers:
Types of Stretch Wrap Gauge
There are several types of stretch wrap gauge to choose from, each with its own strengths and weaknesses. The 37 Gauge is suitable for light, uniform loads of up to 800 lbs.
The 60 Gauge is a light true-gauged film that can handle light to medium loads of up to 1,600 pounds. This gauge is a good choice for loads that require a bit more protection.
The 80 Gauge is a versatile film that can handle loads of up to 2,400 pounds and is often considered the most common stretch film thickness.
Blown versus Cast
Cast extrusion stretch film is less expensive than blown stretch wrap, but it has less memory and tear resistance.
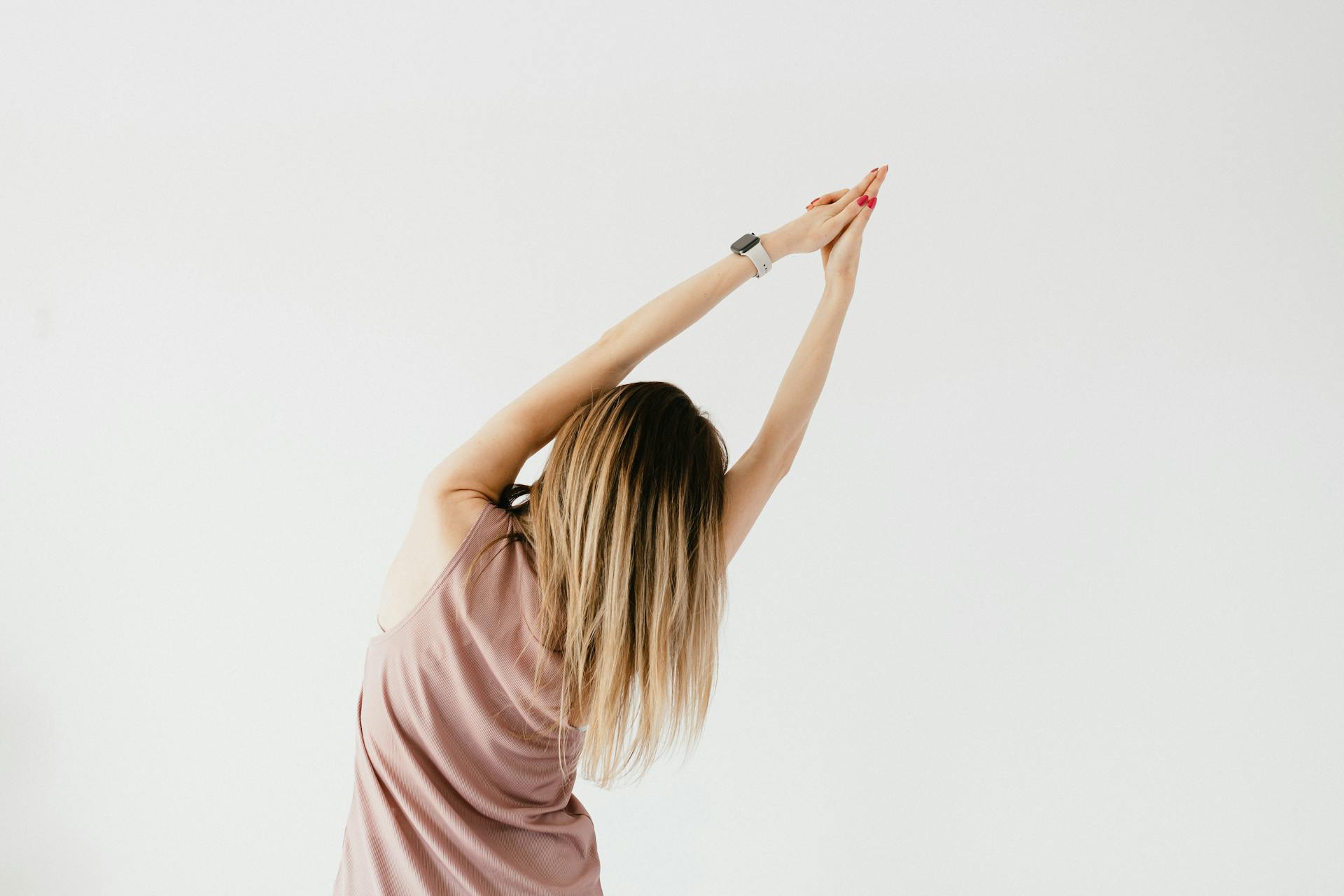
Cast extrusion cools film resins with chilled rollers, allowing the film to have better clarity and requiring less force to stretch.
Cast stretch film unwinds quietly from pallet wrapping machines and offers a superior cling, making it a popular choice for wrapping products.
However, its lack of memory and tear resistance means it may not be the best option for products that need to withstand rough handling or extreme temperatures.
If this caught your attention, see: Glad Wrap Products
Machine
Machine stretch wrap excels in uniformity and efficiency, particularly for medium to high-volume operations.
Machines are designed to stretch wrap to its optimal tension, maximizing the film's strength and efficacy.
Machine stretch wraps often use thinner gauges, ranging from 50 to 80, because the machine can apply the wrap with consistent tightness, minimizing waste and maximizing load security.
The cost-effectiveness of machine stretch wraps escalates with volume, making it a great option for businesses that need to wrap a large number of items.
A device can stretch a high-performance 60 gauge stretch film roll (15 Micron) to the equivalent of a manually applied 80 gauge stretch film roll (20 Micron), providing similar load stability with less material.
For example, a stretch wrap machine can provide substantial long-term savings in labor costs and material usage.
The initial investment in a stretch wrap machine may be significant, but the savings can be substantial, making it a worthwhile investment for businesses that need to wrap a lot of items.
Additional reading: Shrink Wrapping Roll
Hybrid or Equivalent
Hybrid or Equivalent Stretch Films are thinner than true-gauge equivalents, but offer similar holding power.
They can be used for light to medium loads, with the 60 Gauge being a good example of a light true-gauged film that can handle loads up to 1,600 pounds.
For loads that are heavy, irregular, or have many sharp points or corners, you'll want to consider a heavier-duty film like the 100 Gauge, which can hold loads up to 3,000 pounds.
Hybrid or Equivalent Stretch Films, like the 60 Gauge, are a great option for those who want a thinner film that still provides reliable holding power.
Common
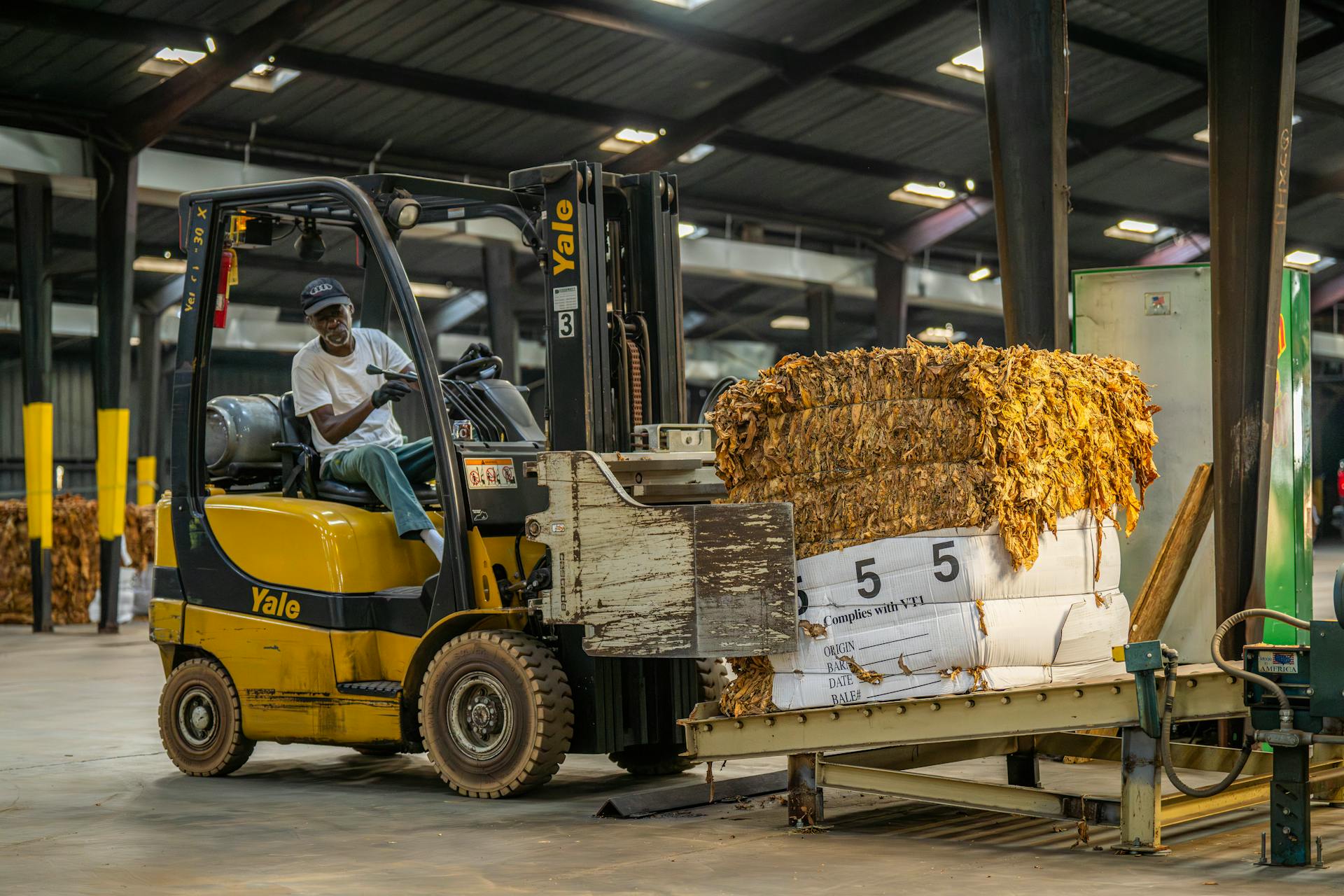
Common stretch film gauges range from 37 to 150 gauge, with different gauges suited for various load weights and types.
The 37 gauge is suitable for light, uniform loads of up to 800 lbs, making it a great option for small, delicate items.
For light to medium loads up to 1,600 pounds, a 60 gauge stretch film is a good choice, providing a balance between strength and flexibility.
80 gauge is the most common stretch film thickness, suitable for loads up to 2,400 pounds, and is often used for a wide range of applications.
A 100 gauge stretch film can hold loads up to 3,000 pounds, making it ideal for heavy, irregular objects like steel beams or 55-gallon drums.
For extremely heavy loads, loads with many sharp points or corners, and heavy irregular objects that may shift during transit, a 150 gauge stretch film is the way to go, requiring machine application for proper tension.
The 90 gauge, 100 gauge, and 115 gauge stretch films are more resistant to punctures and stronger than thinner films, with the 90 gauge rated for loads of up to 2,600 lbs.
Choosing the Right Gauge
Choosing the right stretch wrap gauge is crucial for securing your loads safely and efficiently. The weight of the load is a key factor in determining the gauge you need, as heavier loads require stronger wraps.
A simple chart can serve as a reference point for load weight and recommended gauge: Load WeightRecommended GaugeUp to 800 lbs (Up to 362 kgs)60 - 70 Gauge (15 - 18 Micron)800 - 1200 lbs (362 - 544 kgs)70 - 80 Gauge (18 - 20 Micron)1200 - 1600 lbs (544 - 725 kgs)80 - 90 Gauge (20 - 23 Micron)1600 - 2000 lbs (725 - 907 kgs)90 - 120 Gauge (23 - 30 Micron)Over 2000 lbs (Over 907 kgs)120+ Gauge (30+ Micron)
The shape and size of the load also play a significant role in determining the gauge you need, as irregular loads require more robust wraps to prevent tears and punctures.
Recommended read: 18 Stretch Wrap
Choosing the Right
The weight of the load is a crucial factor to consider when choosing the right gauge. Heavier loads require stronger stretch wrap gauges, with industry-standard 80-gauge wrap capable of securing loads of up to 2,400 lbs.
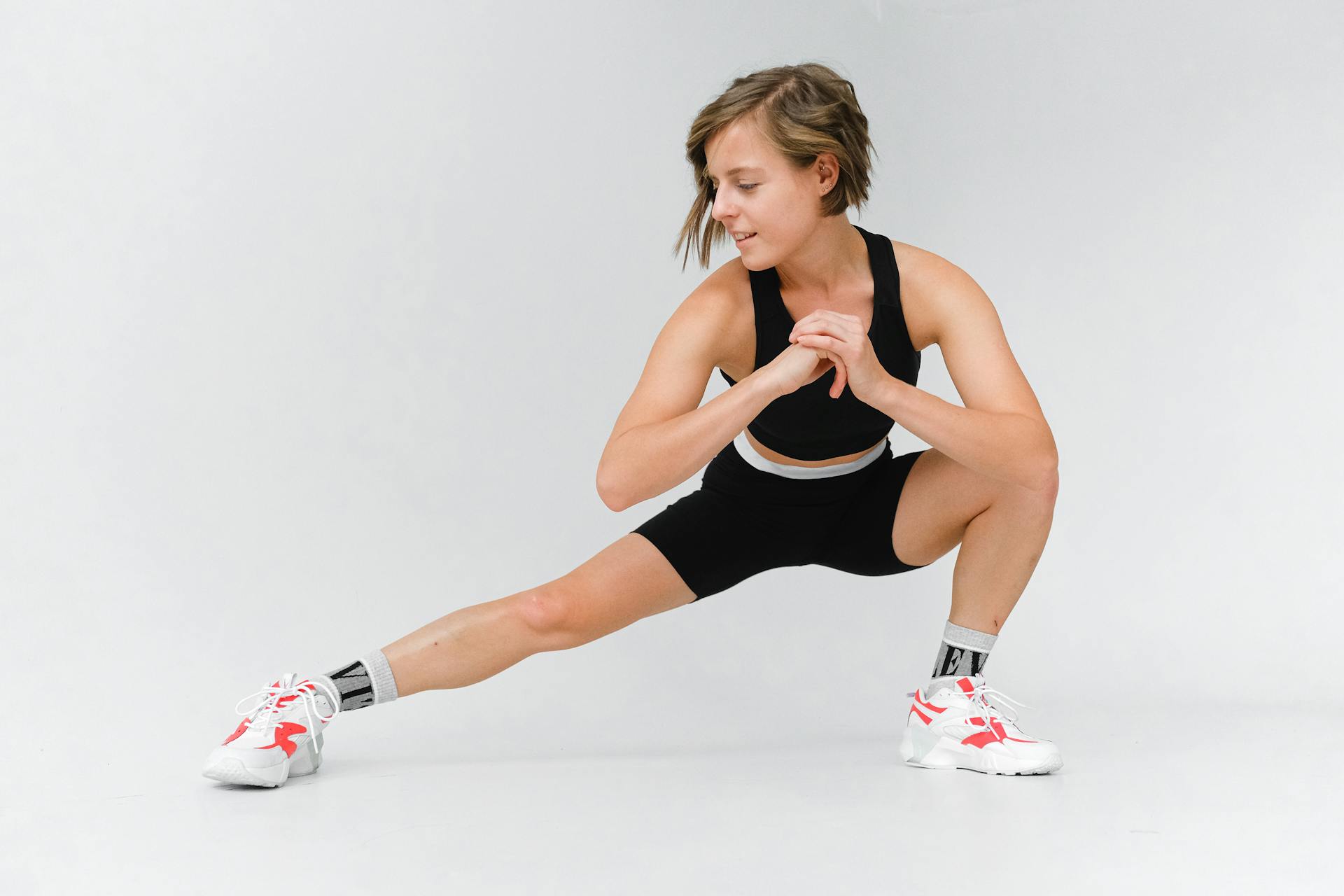
The shape of the load also plays a significant role in gauge selection. Uniform loads, such as pallets of same-size boxes, require less holding power and durability than highly irregular or unstable loads with lots of sharp corners and edges.
A chart can serve as a reference point for load weight and recommended gauge:
The application method also plays a role in gauge selection. Hand stretch wrapping, typically utilized for low-volume operations, accommodates lighter gauges such as 60-90 due to the manual ability to control the tension and wrap force.
High stretch wrap gauges, while more expensive, offer the pinnacle of protection with superior strength and resilience, which is essential for heavy or hazardous materials.
True
True-gauged stretch film is the standard option. It has not been pre-stretched, making it a straightforward choice for many users.
A true-gauged film is just that - unaltered and uncomplicated.
Performance Factors and Considerations
Load shape and size are key factors in determining the required gauge for stretch wrap rolls. The more irregular the load, the thicker the gauge needed to prevent tears and punctures.
A simple chart can serve as a reference point for load weight and recommended gauge: Load WeightRecommended GaugeUp to 800 lbs (Up to 362 kgs)60 - 70 Gauge (15 - 18 Micron)800 - 1200 lbs (362 - 544 kgs)70 - 80 Gauge (18 - 20 Micron)1200 - 1600 lbs (544 - 725 kgs)80 - 90 Gauge (20 - 23 Micron)1600 - 2000 lbs (725 - 907 kgs)90 - 120 Gauge (23 - 30 Micron)Over 2000 lbs (Over 907 kgs)120+ Gauge (30+ Micron)
The nature of the items being wrapped also impacts the choice of gauge, with heavier gauge wraps required for lighter but bulkier items prone to shifting during transit.
Performance Factors
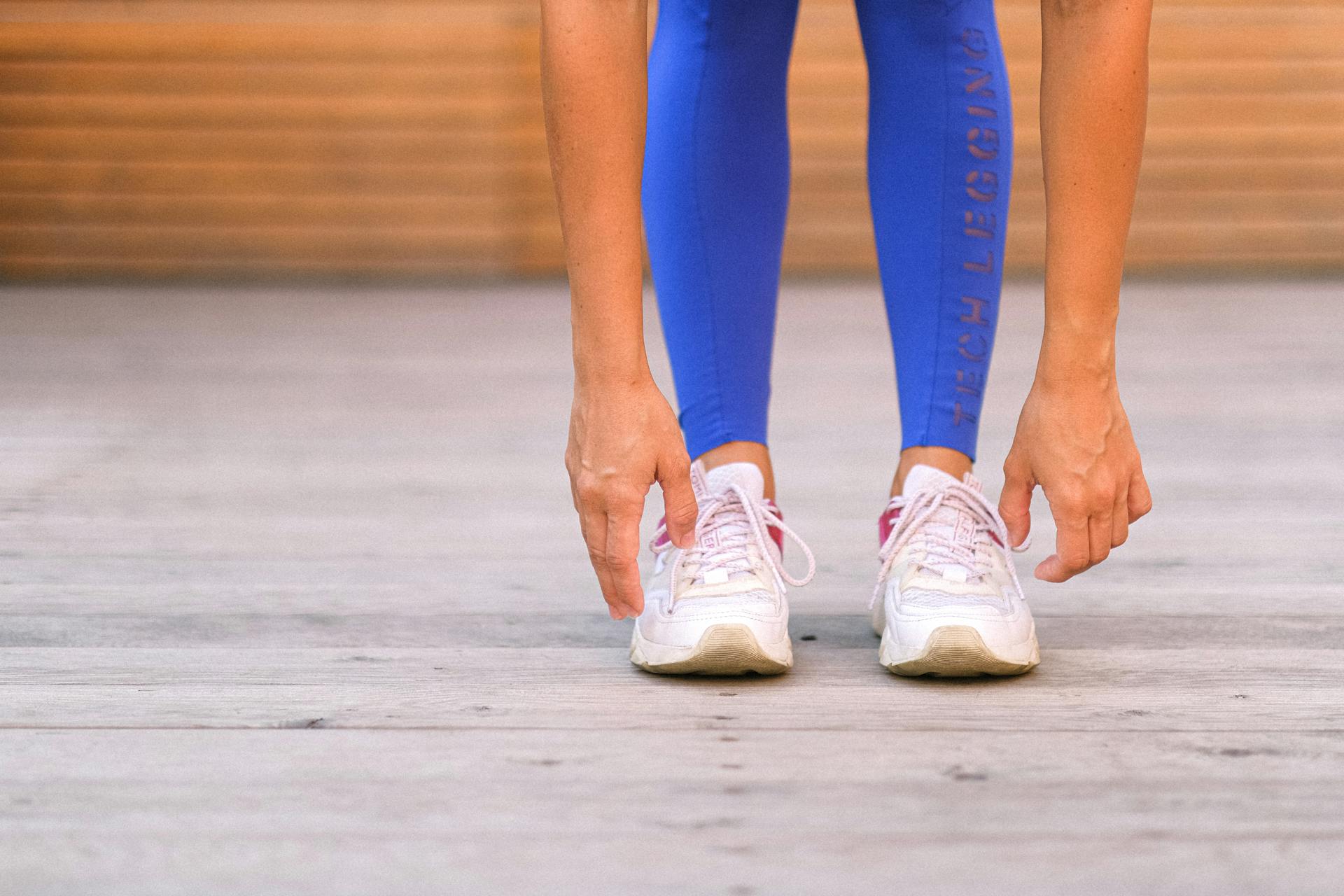
Performance Factors can be a complex mix of physical and mental aspects, but understanding them can help you perform at your best.
Core temperature affects athletic performance, with research showing that a core temperature of around 38°C can lead to significant declines in performance.
Adequate hydration is also crucial, with studies indicating that even mild dehydration can impair performance by up to 12%.
Proper nutrition can also play a significant role in performance, as a diet lacking essential vitamins and minerals can lead to fatigue and decreased endurance.
Sleep deprivation can have a significant impact on performance, with research showing that even one night of poor sleep can affect cognitive function and reaction time.
Stress management is also an important factor, with chronic stress leading to decreased performance and increased risk of injury.
Load Considerations
Load Considerations are crucial in determining the right stretch wrap gauge for your shipping needs. The shape and size of the load dictate the thickness of the film required.
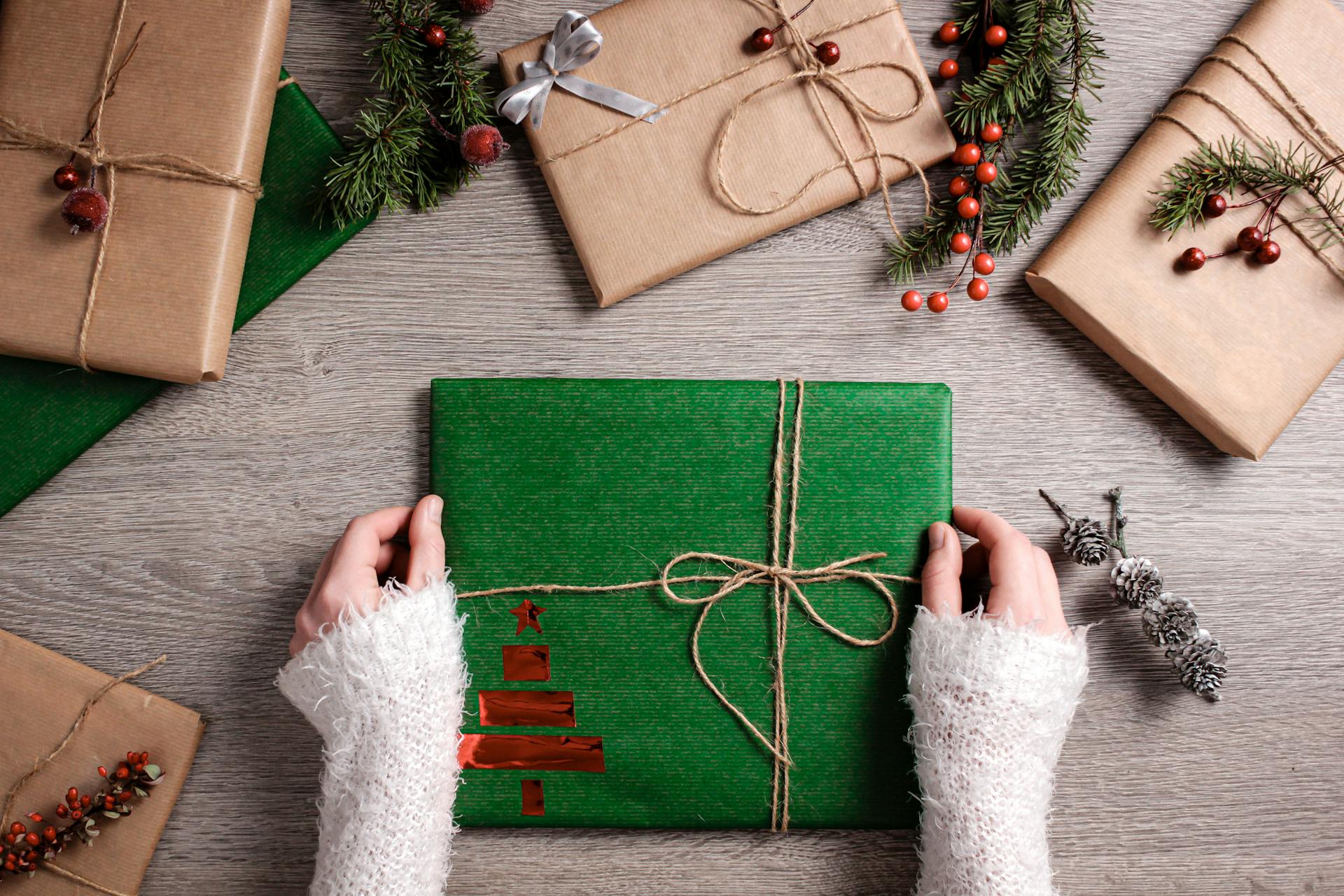
A lighter gauge can often do the job effectively for uniform loads with flat surfaces and right angles. This is because the uniformity of the load allows for an even distribution of tension, reducing the risk of tears.
However, as loads become more irregular, a thicker gauge becomes imperative. This is especially true for loads with sharp edges or uneven weight distribution, which demand more from the stretch wrap.
The weight of the load must also be factored into the equation. For example, a pallet of machinery parts with sharp metal edges necessitates a heavier gauge to prevent punctures.
Here's a helpful chart to reference:
The nature of the items being wrapped also impacts the choice of gauge. For example, a heavier gauge wrap might be required for lighter but bulkier items if they are prone to shifting during transit.
Gauge Options and Specifications
The starting point for heavy-gauge stretch wrap is 90 gauge, which is more resistant to punctures and stronger.
Typically, 90-gauge film is rated for loads up to 2,600 lbs.
For heavier loads, you can also find 100- and 115-gauge films that are suitable for use when shipping loads up to 3,000 lbs. or more.
These thicker films are even more resistant to damage and can handle heavier loads with ease.
Cast Extrusion
Cast extrusion is a process that cools film resins with chilled rollers, allowing cast stretch film to have better clarity.
This process also requires less force to stretch, increasing tear resistance and making it unwind quietly from pallet wrapping machines.
Cast extrusion stretch film offers a superior cling, making it a popular choice for wrapping products.
One of the advantages of cast stretch films is that it is less expensive than other options.
However, cast stretch film has less memory and tear resistance than blown stretch wrap.
90, 100, 115
The 90, 100, and 115 gauge stretch wrap options are a great place to start when looking for the right material for your shipping needs. 90 gauge is considered the starting point for heavy-gauge stretch wrap.
This film is more resistant to punctures and stronger, rated for loads up to 2,600 lbs. Thicker films of 100 and 115 gauge can handle even more, up to 3,000 lbs or higher.
For loads that require a bit more support, 100 and 115 gauge films are suitable options.
Gauge Measurements and Conversions
The thickness of stretch film is called its gauge, and it can be measured in microns or mils. Simply put, the higher the gauge micron or mil, the thicker the plastic.
A mil is equivalent to 0.001 inches, and 25.4 microns equal 1 mil. This is a key conversion to keep in mind when working with stretch film gauge.
Here's a quick reference guide to gauge measurements:
Micron Conversion Chart
A micron is a unit of measurement for the thickness of stretch film, and it's essential to understand how it relates to gauge.
One mil is equal to 0.001 inches. This is a crucial conversion to keep in mind when working with stretch film.
Here's a key conversion fact: 25.4 microns equal one mil. This is a fundamental relationship to grasp when measuring gauge.
Now, let's take a look at the micron conversion chart:
70 to 80
70 to 80 gauge stretch wrap is a common range for industry standard film. Eighty-gauge film is typically considered the industry standard.
Both 70-gauge and 80-gauge film can provide similar strength and protection. 70-gauge film can handle loads of up to 2,200 lbs.
Eighty-gauge film is rated for loads of up to 2,400 lbs. This makes it suitable for heavier loads.
The difference in weight capacity between 70-gauge and 80-gauge film is relatively small. However, 80-gauge film can handle slightly heavier loads.
A true 80 gauge stretch wrap can be stretched up to 200% of its original length. However, this can vary depending on the type of extrusion process used.
Case Studies and Applications
In a real-world example, a beverage distribution company switched from a standard 70 gauge film to an 80 gauge film, resulting in a 15% reduction in film usage.
This change also led to a significant decrease in breakage rates during transit. Businesses can make informed decisions by analyzing performance factors.
A slight increase in gauge can lead to substantial savings and efficiency gains, as seen in the beverage distribution company's experience.
The decision on gauge selection is not taken lightly, as it impacts the protection of goods and the bottom line.
Advanced Considerations and Innovations
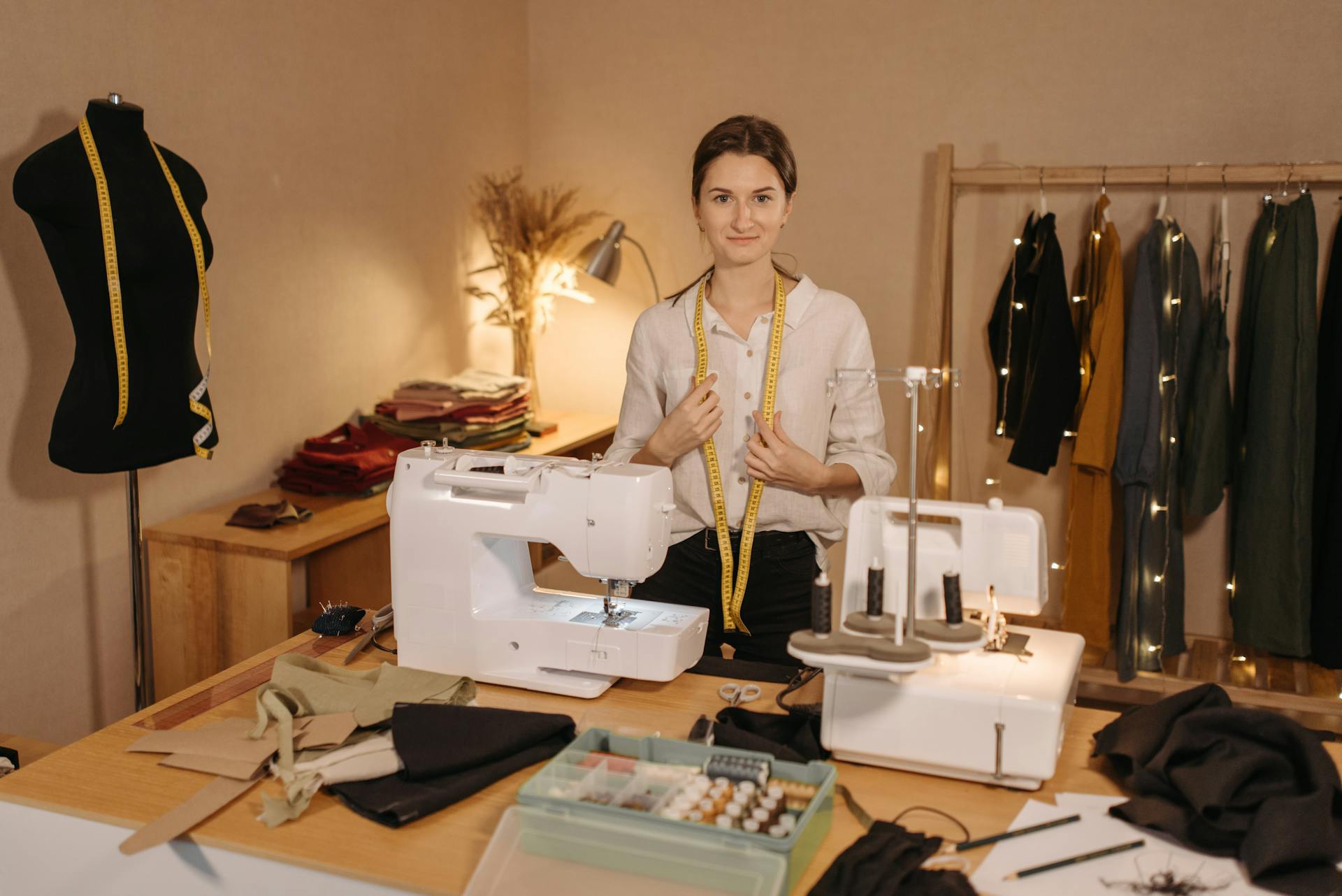
The stretch wrap industry has shifted towards more environmentally friendly options, such as biodegradable and recycled-content stretch wraps.
These products are engineered to provide robust load stability while addressing ecological concerns.
In colder climates, wraps must withstand a higher degree of brittleness, prompting a choice for films with better cold resistance.
High humidity can affect the film's cling and load-holding ability, necessitating wraps with specific additives for better performance under such conditions.
Selecting the correct gauge becomes even more nuanced with these materials, as their mechanical properties can differ from traditional films.
Blow Extrusion
Blow extrusion is a process that cools film resin with air, making stretch film tougher and more resilient than cast film. This process also allows for a higher load and stretch capacity, with a higher tear resistance.
Blown stretch wrap is more expensive than cast film, and it can be noisy when unwound from rolls. It also has poor clarity.
The thickness of blown stretch film can be measured using a micrometer to check the film thickness.
Suggestion: Blown Stretch Wrap
Human vs. Machine Application
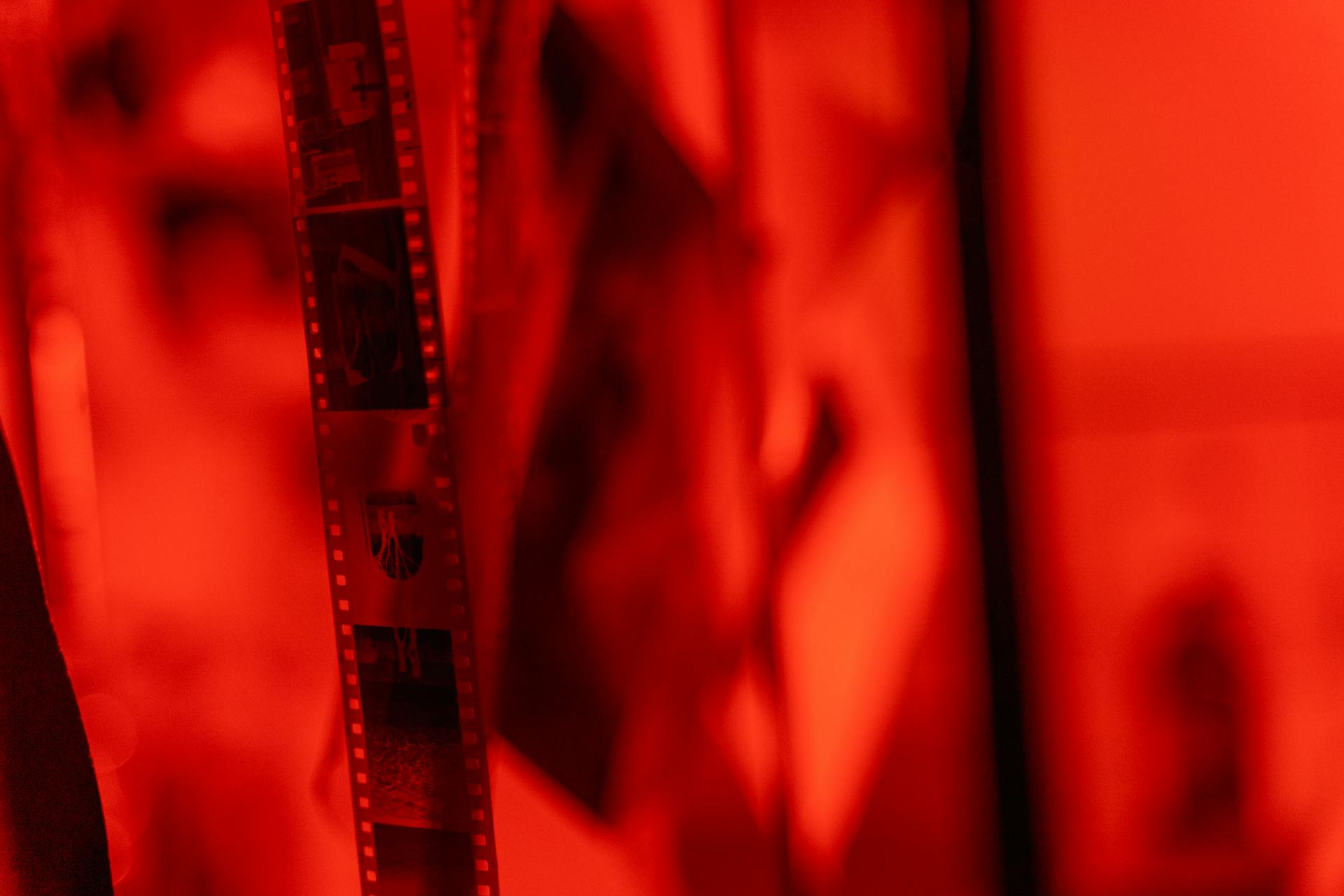
Human vs. Machine Application is a crucial area of consideration in the realm of advanced technologies.
Machine learning algorithms have been shown to outperform humans in tasks such as image recognition and natural language processing.
However, humans possess unique abilities like creativity and empathy that machines have yet to replicate.
In tasks that require complex decision-making, humans can often outperform machines due to their ability to consider multiple factors and nuances.
Machines, on the other hand, can process vast amounts of data in a fraction of the time it takes humans, making them ideal for tasks like data analysis and pattern recognition.
Ultimately, the choice between human and machine application depends on the specific needs and goals of the project.
For more insights, see: Stretch Wrap Equipment
Advanced Considerations and Innovations
In colder climates, the stretch wrap must withstand a higher degree of brittleness, making films with better cold resistance a necessary choice.
Temperature and humidity significantly influence gauge selection, affecting the film's performance and load-holding ability.
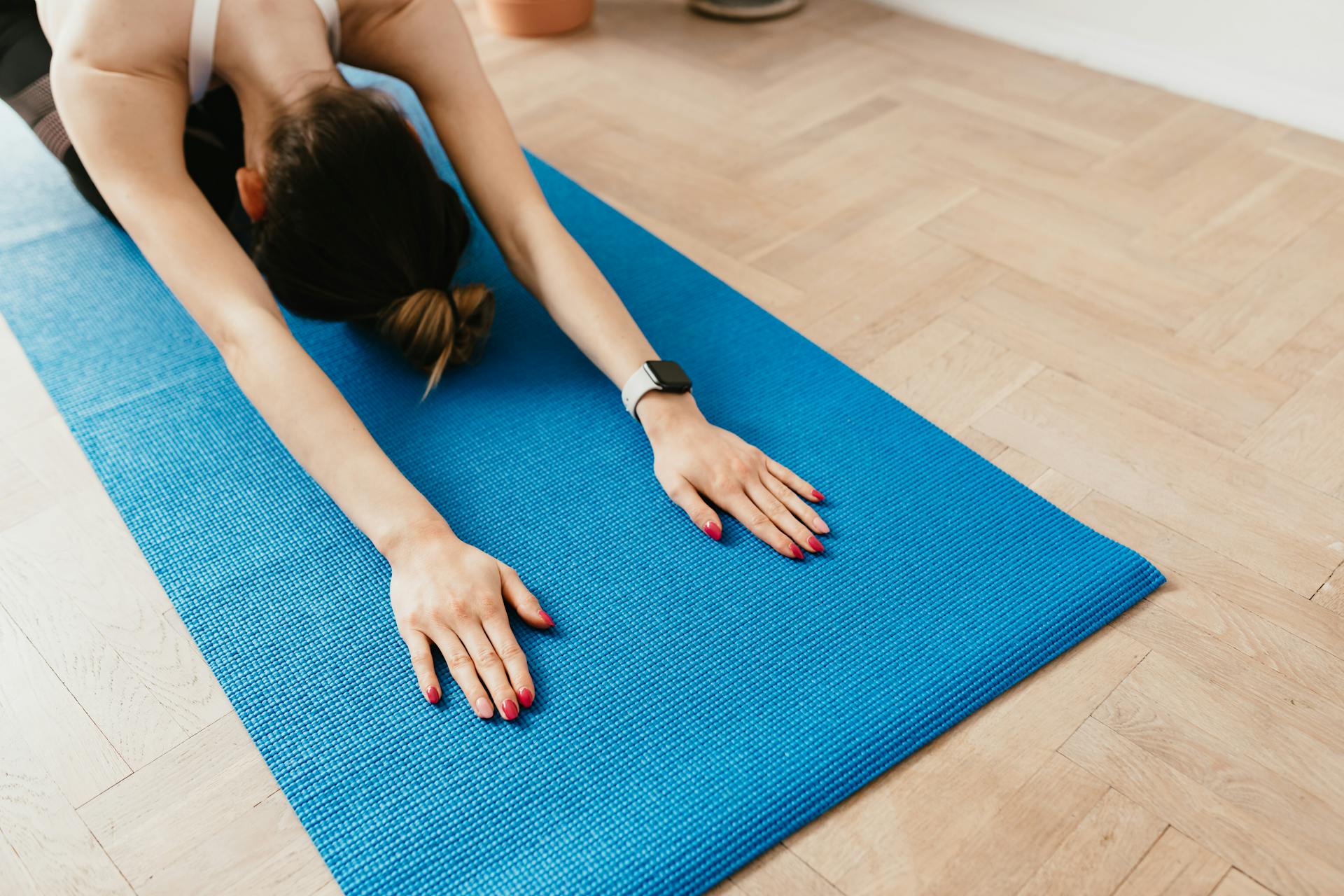
High humidity can compromise the cling and load-holding ability of traditional films, necessitating wraps with specific additives for better performance.
The stretch wrap industry has shifted towards more environmentally friendly options, such as biodegradable and recycled-content stretch wraps.
These products are engineered to provide robust load stability while addressing ecological concerns.
Selecting the correct gauge becomes even more nuanced with these materials, as their mechanical properties can differ from traditional films.
Businesses must now balance operational needs with sustainable practices when choosing a gauge that ensures load safety.
Frequently Asked Questions
What's thicker, 60 gauge or 80 gauge?
80 gauge is thicker than 60 gauge, making it a better choice for heavier loads.
How thick is stretch wrap film?
Stretch wrap film thickness ranges from 12 to 30 microns, with higher micron values indicating thicker film. Standard thicknesses are suitable for various applications, from light to heavy-duty use.
Sources
- https://mrshrinkwrap.com/blog/choosing-the-right-stretch-wrap.html
- https://www.aaapolymer.com/choosing-the-right-stretch-wrap-gauge-or-thickness/
- https://www.keeptoppackaging.com/blog/selecting-right-stretch-wrap-film-gauge/
- https://www.aaapolymer.com/stretch-film-micron-vs-gauge/
- https://www.thongguan.com/80-gauge-stretch-wrap/
Featured Images: pexels.com