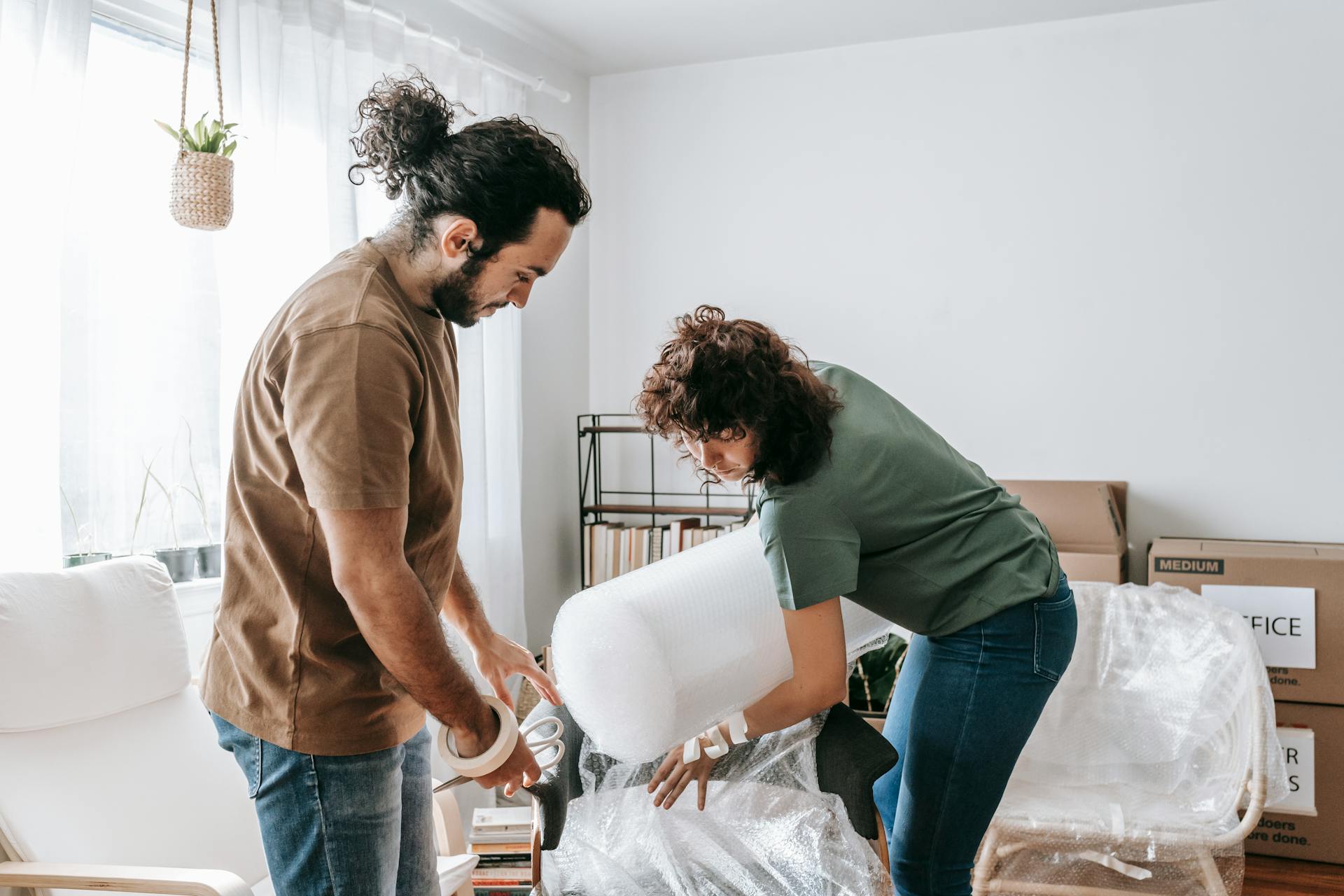
Blown stretch wrap is a type of plastic film used for packaging and protecting products during shipping and storage. It's a popular choice for industries like manufacturing, logistics, and e-commerce.
Blown stretch wrap is made from a type of plastic called polyethylene, which is blown into a thin film using a machine called a blower. This process creates a strong and durable film that can stretch to fit around products of various sizes and shapes.
The film comes in different types, including LDPE (low-density polyethylene) and HDPE (high-density polyethylene), each with its own unique properties and benefits. LDPE is more flexible and suitable for wrapping smaller items, while HDPE is stronger and more suitable for larger items.
The thickness of the film also varies, with common gauges ranging from 10 to 30 microns. Thicker films provide more protection and support, while thinner films are more flexible and easier to use.
Here's an interesting read: Plastic Packaging Films
What It's Made Of
Blown stretch wrap is made from a granular resin, which is a type of plastic material.
This resin is fed into a heated screw barrel, where it's melted to create a liquid state. The melted resin is then blown through a circular die, creating a bubble.
The air blown into the tube stretches it out to the desired width, with the speed of the air determining the thickness of the film. This slow cooling process is also what gives the film its hazy and dull appearance.
Nip rollers can then flatten the material into a tube that can be reeled for creating bags and pouches, or it can be slit and reeled for creating a flat sheet of film.
You might enjoy: Shipping Air Pillow
Benefits and Features
Blown stretch wrap offers a range of benefits, including very high tear and puncture resistance. This makes it an excellent choice for protecting products during shipping and storage.
One of the key benefits is its ability to protect against moisture, gases, and aromas. This is especially important for products that are sensitive to these elements.
A unique perspective: Glad Wrap Products
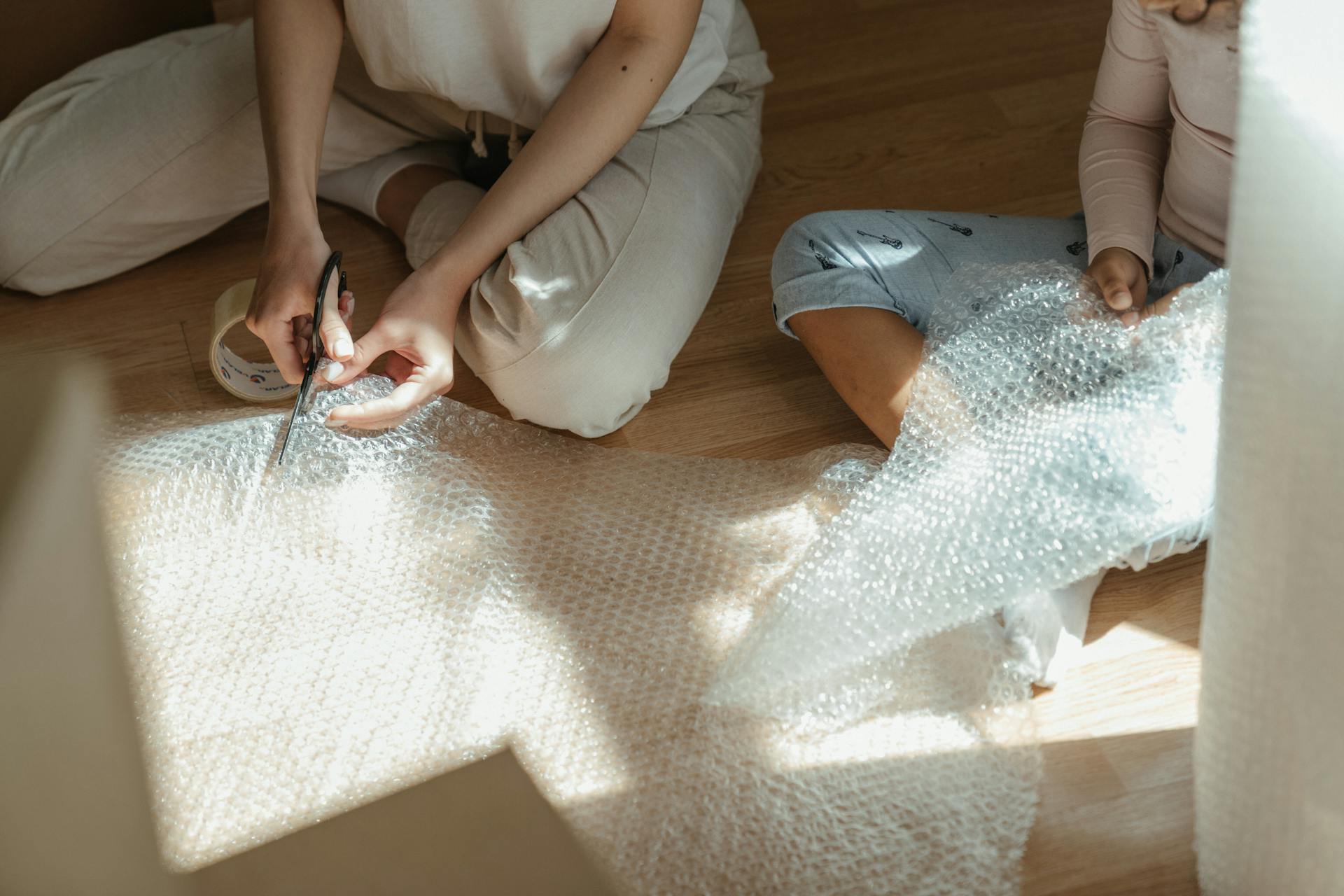
Blown stretch wrap is also very durable and tough, providing increased protection for your products. It produces less manufacturing scrap, which can help reduce waste and save you money.
Here are some key features of blown stretch wrap:
- SOLD AS 4 Rolls Per Case
- Film Color – Clear
- Puncture and tear resistance
- Excellent cling provides great stabilization of loads
- Works well in temperatures down to -5° F
- For use with Dispensers
Benefits of Film
Film plays a crucial role in packaging products, and it's worth exploring its benefits.
Stretch film is incredibly durable and tough, providing increased protection for items. This is especially important when shipping fragile goods.
One of the key advantages of blown stretch film is its high level of tear and puncture resistance. This makes it perfect for protecting items during transit.
Blown stretch film also protects against moisture, gases, and aromas, which is essential for maintaining product quality.
Here are some key benefits of film:
- Very high tear and puncture resistance
- Protects against moisture, gases and aromas
- Very durable and tough for increased protection
- Produces less manufacturing scrap
- High level of cling
Packaging Control Features
Pack Kontrol Blown Hand Stretch Film is sold as 4 rolls per case, making it easy to stock up and keep on hand.
The film is also available in clear color, which is a great option for showcasing products.
Related reading: Hand Stretch Wrap
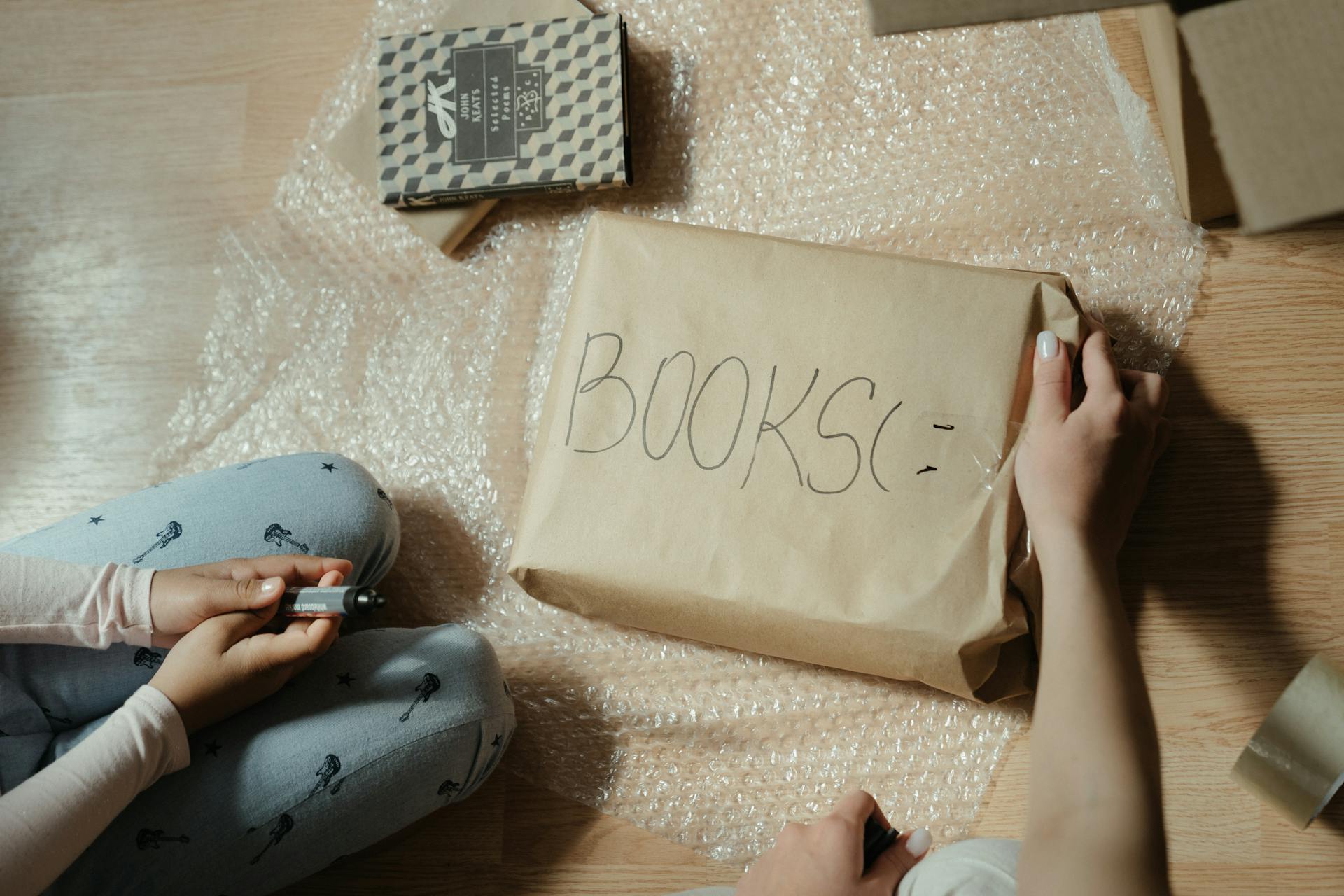
One of the standout features of this film is its puncture and tear resistance, which helps prevent damage to your packages.
Excellent cling is another key benefit, providing great stabilization of loads and keeping items secure.
This film works well in temperatures as low as -5° F, making it suitable for use in cold storage facilities or during winter shipments.
For added convenience, it can be used with dispensers, making it easy to apply the film to your packages.
Types of Blown Stretch Wrap
Blown stretch wrap comes in different types, each with its own advantages. Cast and blown stretch film are two options to consider.
Cast stretch film is made using a different manufacturing process than blown film, which affects its thickness and strength. This results in a more consistent gauge.
Blown stretch film, on the other hand, is made using a process that can produce a wider range of gauges. This flexibility can be beneficial for specific applications.
Related reading: What Are Dissolvable Packing Peanuts Made of
Understanding Film Types
Cast stretch film is a popular choice for its balance of strength and flexibility, but it's worth noting that its thickness and strength can be affected by the manufacturing process.
The type of film you choose should also consider the gauge, or thickness, of the film. True gauge stretch film is designed to maintain its thickness throughout the roll.
Blown stretch film, on the other hand, is made by blowing air into a tube to create the film, resulting in a thinner and more flexible product.
Pre-stretched stretch film is another option, but it's worth noting that its advantages may vary depending on your specific workflow.
Explore further: Stretch Wrap Gauge Chart
Which Has the Least Gloss?
Blown stretch wrap has less gloss than cast stretch wrap. This reduced gloss makes it easier to scan and identify products under warehouse lighting.
The quicker cooling process and types of resin used in cast stretch wrap manufacturing result in higher levels of gloss. This can make it difficult to scan or see through the film with standard warehouse lighting.
Blown stretch wrap's lower gloss levels provide a practical advantage in warehouse operations. It's a small but significant detail that can make a big difference in productivity and efficiency.
Manufacturing and Production
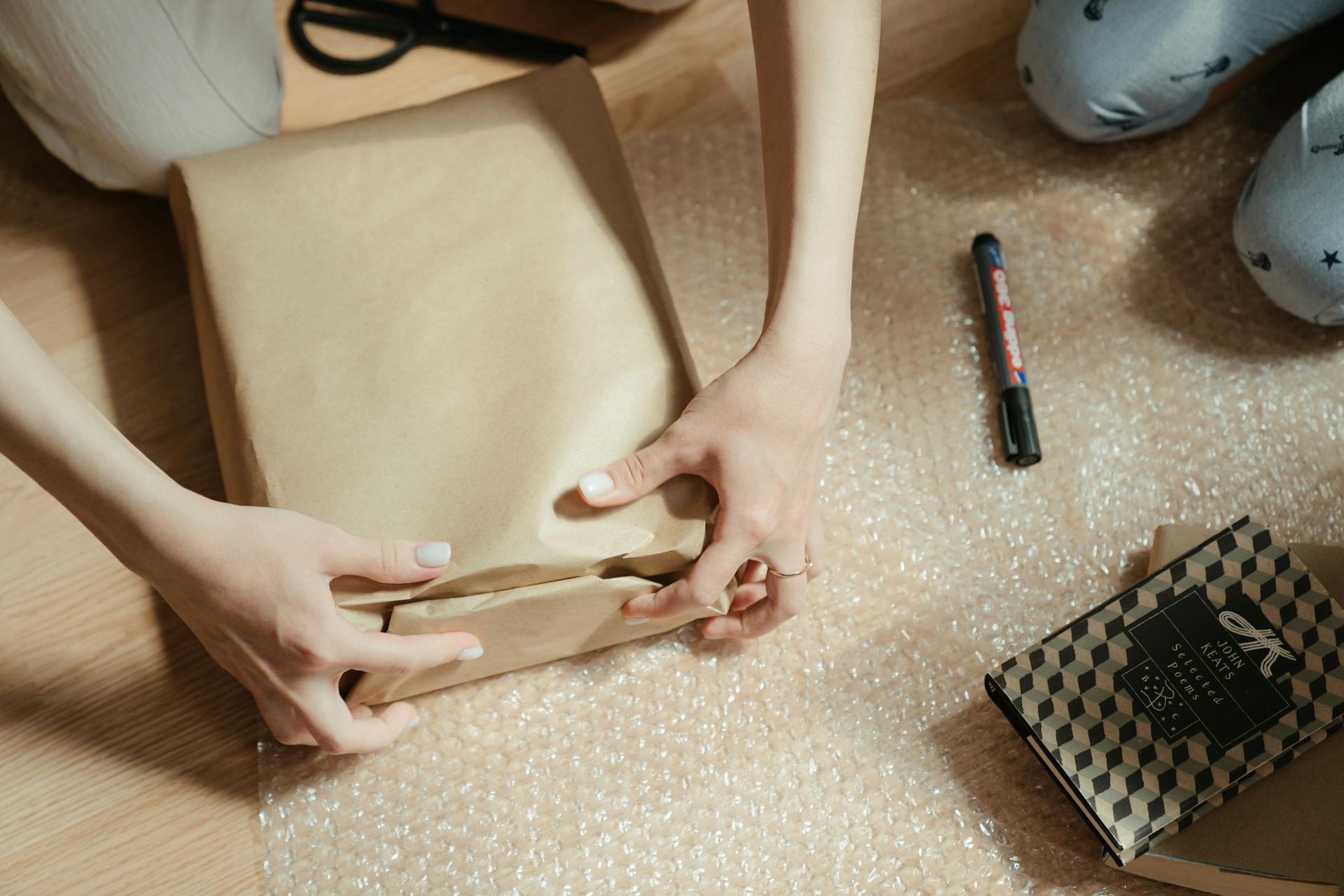
Blown stretch wrap is made through a blown film extrusion manufacturing process, where granular resin and additives are fed into a heated screw barrel.
The resin is then forced into a circular die and vertically blown upward and outward, creating a bubble.
This slow cooling process, where the bubble is cooled by air as it rises up the tower, contributes to the wrap's hazy and dull appearance.
The bubble is then nipped together and drawn down to the winding and slitting stations with guide rollers.
How Is Made?
Blown stretch wrap is made through a blown film extrusion manufacturing process, which begins with granular resin and additives being fed into a heated screw barrel.
The resin is then forced into a circular die, creating a bubble of hot resin that's blown upward and outward.
This slow cooling process, where the bubble is cooled gradually by air as it rises, is one of the reasons blown stretch wrap can look hazy and dull.
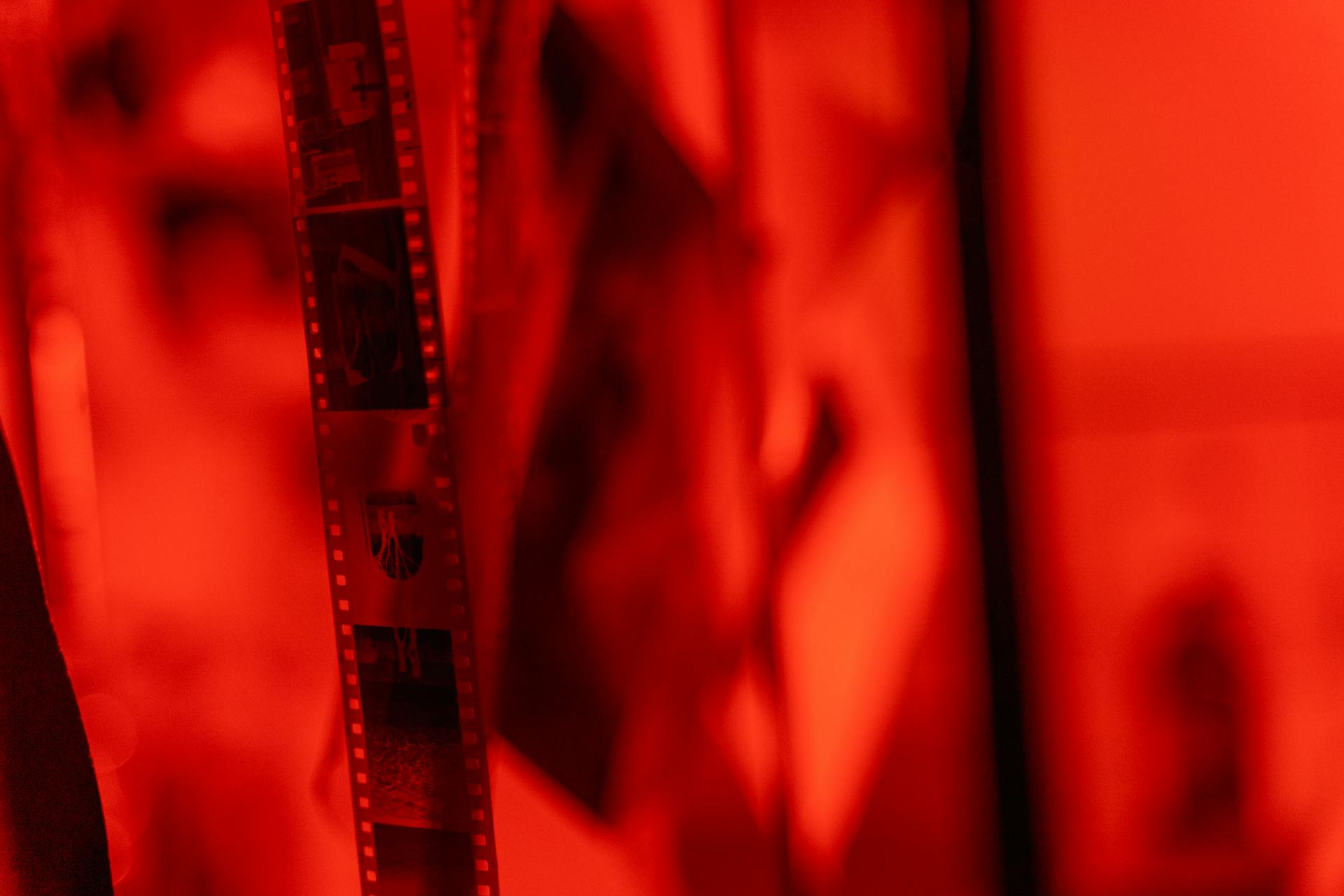
The bubble is then nipped together and drawn down to the winding and slitting stations with guide rollers.
Cast stretch wrap, on the other hand, is extremely clear and produces high levels of clarity, which is achieved through a different manufacturing process.
By casting the molten resin over a frozen roller, crystallization is reduced and clearer film is produced, resulting in a more transparent wrap.
Film Extrusion Advantages
In the manufacturing process, certain methods offer unique benefits that set them apart from others. The blown film extrusion process is one such method that provides superior puncture resistance.
This means that products made using this method are less likely to tear or puncture, making them more durable and long-lasting. I've seen firsthand how this can make a big difference in the performance of a product.
One of the advantages of blown film extrusion is that it produces less manufacturing scrap. This not only saves resources but also reduces waste and the environmental impact of the manufacturing process.
Here are some of the key benefits of blown film extrusion:
- Superior puncture resistance
- Produces less manufacturing scrap
- Durable and provides maximum toughness
- Blown scrap has a high level of cling
Comparing Blown Stretch Wrap
Blown stretch wrap can stretch further than cast stretch wrap, but it requires more force. This makes blown stretch wrap a great option for applications where a little extra stretch is needed.
One of the benefits of blown stretch wrap is that it allows users to down-gauge to a thinner stretch wrap while maintaining load stability on pallets. This can save money and reduce plastic waste.
The mechanical properties of blown stretch wrap also give it a high level of stretch resistance, making it a great choice for applications where a lot of force is applied.
Differences Between Cast &
Cast stretch wrap cools fast, while blown stretch wrap cools slowly. This affects the final product's appearance, with cast stretch wrap being very clear and glossy, and blown stretch wrap being hazy and dull.
Cast stretch wrap has high puncture and tear resistance, but blown stretch wrap has even higher resistance. If you're looking for a product that can withstand rough handling, blown stretch wrap might be the better choice.
Cast stretch wrap has moderate stretch resistance, while blown stretch wrap has high stretch resistance. This means that blown stretch wrap can stretch further, but may require more force.
Here's a comparison of the two:
As you can see, blown stretch wrap has some significant advantages over cast stretch wrap. However, it's worth noting that cast stretch wrap can still be a good choice in certain situations, particularly if you need a product with consistent cling.
Comparing Memory Capacities
Blown stretch wrap has a much higher degree of memory than cast stretch wrap. This is due to the orientation of the molecular chains, which causes it to contract in both the cross direction (CD) and machine direction (MD).
Cast stretch wrap, on the other hand, has a single orientation and softer characteristics, resulting in reduced memory. This difference in memory capacity affects how well the stretch wrap will hold its shape after being stretched.
The higher memory capacity of blown stretch wrap makes it a better choice for applications where a strong, resilient film is needed.
Gauge and Thickness
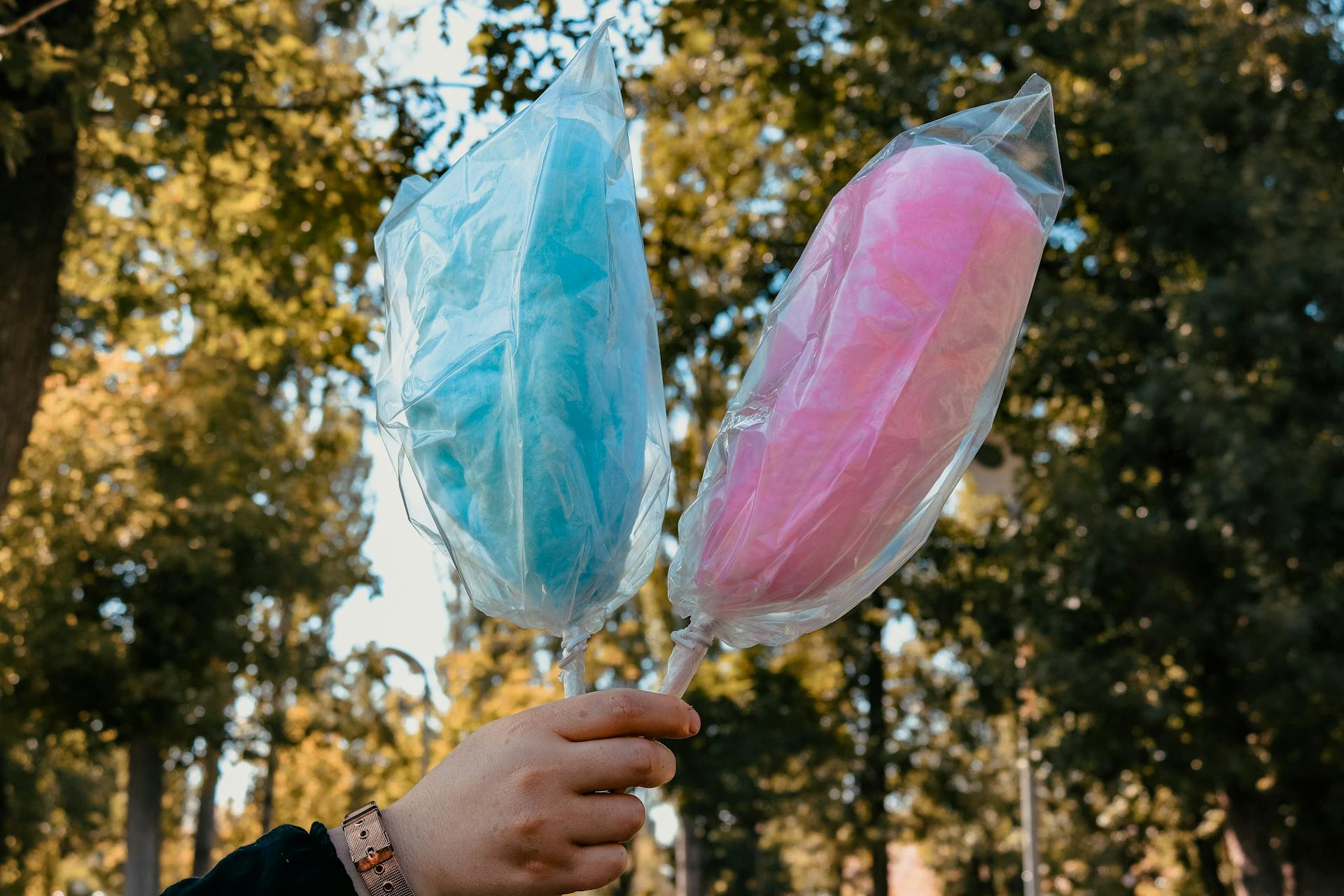
The gauge and thickness of blown stretch wrap are crucial factors to consider when choosing the right product for your business. 70- and 80-gauge wraps can handle loads ranging from 2,200 to 2,400 pounds.
These gauges are popular options due to their efficient wrapping processes, premium stretch capabilities, and ability to help reduce weight. 80-gauge film is the standard for the industry due to its superior versatility.
If you need to handle heavier loads, a 90-gauge film is the way to go. It offers high tension and an excellent stretch rate, making it ideal for pallet loads ranging from 2,400 to 2,600 pounds.
Suggestion: Stretch Wrap Gauge
Which Can Stretch Farther?
Blown stretch wrap can stretch further than cast stretch wrap, but it requires more force. Many tests have concluded that blown stretch wrap will outstretch cast in most cases.
However, in some instances, you may be able to achieve a greater yield or better stretch with cast stretch wrap. This is because the mechanical properties of cast stretch wrap can be beneficial in certain situations.
Using a lower micron blown stretch wrap can counteract the additional stretch of cast stretch wrap. This is an important consideration when choosing between the two.
Down-gauging to a thinner stretch wrap with blown stretch wrap can save money and reduce plastic waste.
70- and 80-Gauge
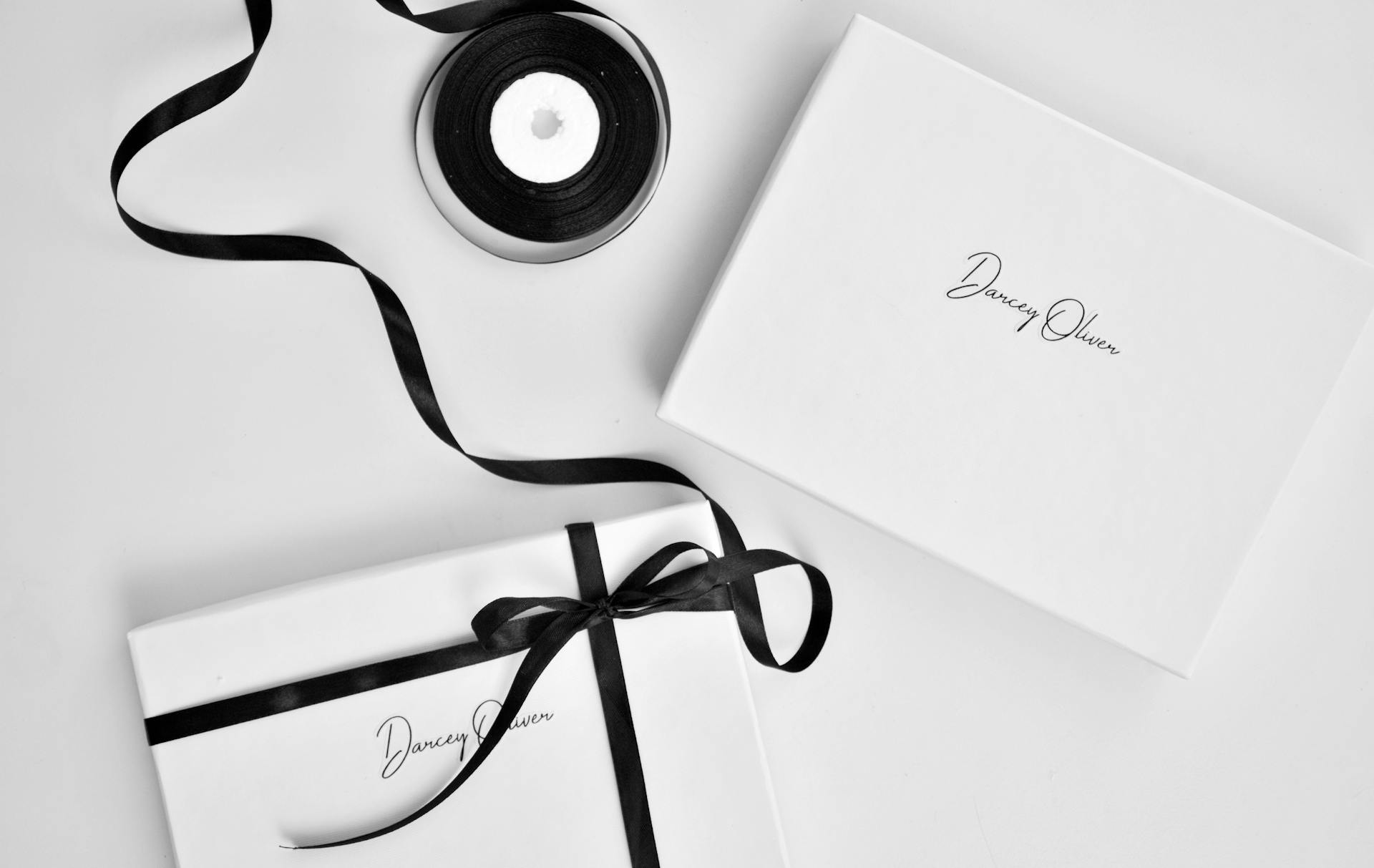
70- and 80-gauge wrap are popular options for their efficient wrapping processes, premium stretch capabilities, and ability to help reduce weight. They can handle loads ranging from 2,200 to 2,400 pounds.
The 80-gauge film is the standard for the industry due to its superior versatility, making it a widely accepted choice.
90-Gauge
The 90-gauge wrap is a heavy-duty option that's perfect for heavy pallet loads. It's ideal for pallet loads ranging from 2,400 to 2,600 pounds.
A 90-gauge film offers high tension and an excellent stretch rate. This makes it a reliable choice for applications that require a strong and flexible wrap.
The 90-gauge wrap is stronger and more resistant to tears, punctures, and other damage compared to lighter gauges.
You might like: Plastic Pallet Specifications
Frequently Asked Questions
Which is better, cast or blown stretch wrap?
For lighter loads, cast stretch film is a better choice, but for heavier loads, blown stretch film offers superior holding power. The right choice depends on the weight and type of load you're securing.
What is the strongest stretch wrap?
The strongest stretch wrap is 150-gauge, a heavy-duty option that requires specialized wrapping equipment for effective use. This thick gauge provides maximum protection for pallet loads.
Sources
- https://www.ipoly.uk.com/news/differences-between-cast-vs-blown-stretch-wrap
- https://www.cabletiesandmore.com/blown-hand-stretch-film
- https://www.aaapolymer.com/cast-vs-blown-stretch-wrap/
- https://primepackaging.com/product-category/stretch-wrap/hand-stretch-wrap/blown-hand-stretch
- https://robopacusa.com/everything-you-need-to-know-about-stretch-wrap-thickness/
Featured Images: pexels.com