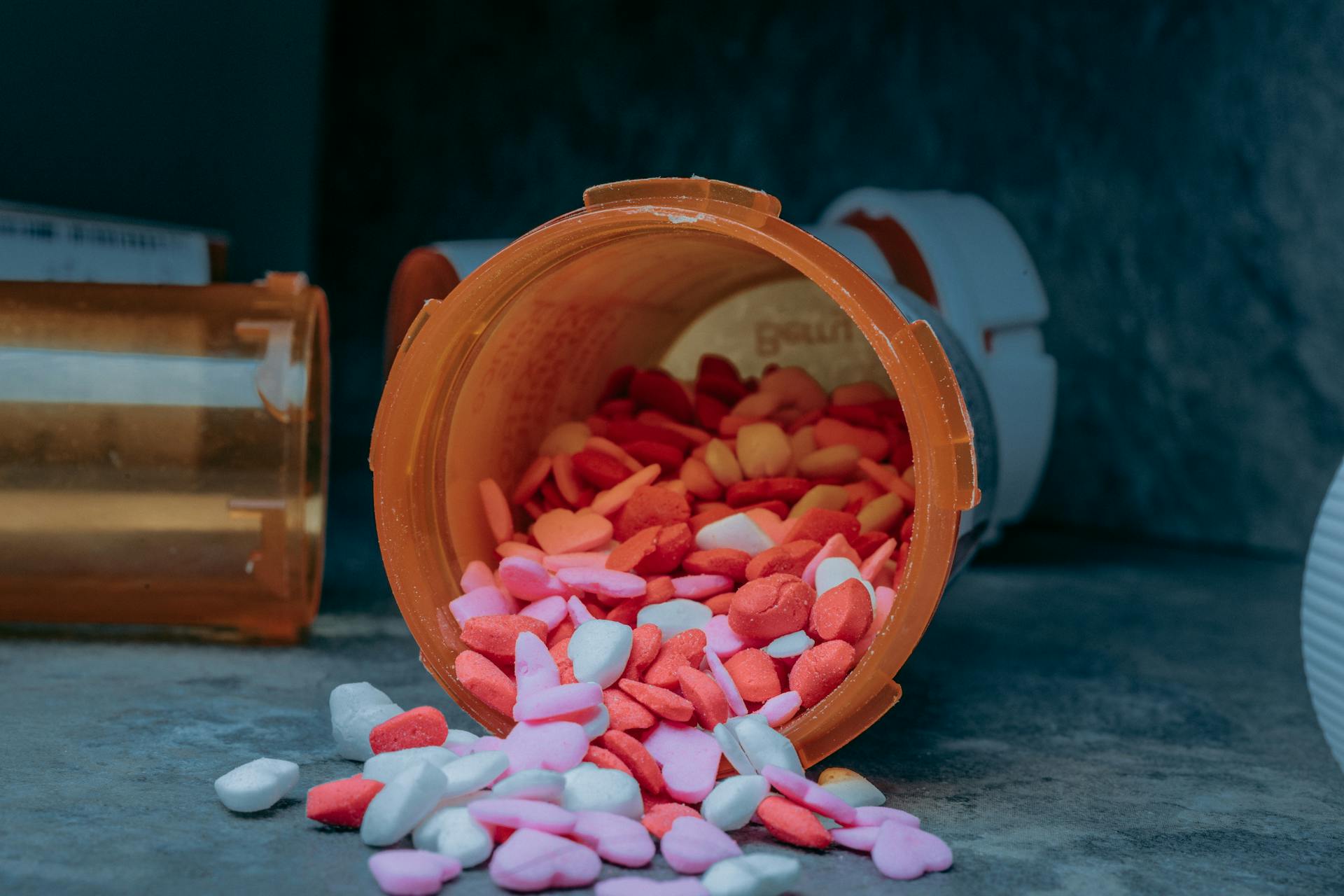
Unit dose packaging machines are designed to streamline your workflow by reducing manual handling and minimizing errors. This can lead to a significant reduction in labor costs, which is a major advantage for businesses.
With the ability to package a single dose of medication or product at a time, unit dose packaging machines can help prevent overfilling or underfilling of containers. This precision is especially important in the pharmaceutical industry.
These machines can also be integrated with existing inventory management systems to ensure that the right products are packaged and shipped to the right locations.
You might enjoy: Unit Dose Pack
Benefits and Features
Investing in a unit dose packaging machine can greatly improve efficiency by reducing manual labor and minimizing packaging errors.
These machines can produce up to 60 packages per minute, making them ideal for high-volume operations in hospitals and large pharmacies.
One of the key features to consider when purchasing a unit dose packaging machine is labeling and barcode printing functionality.
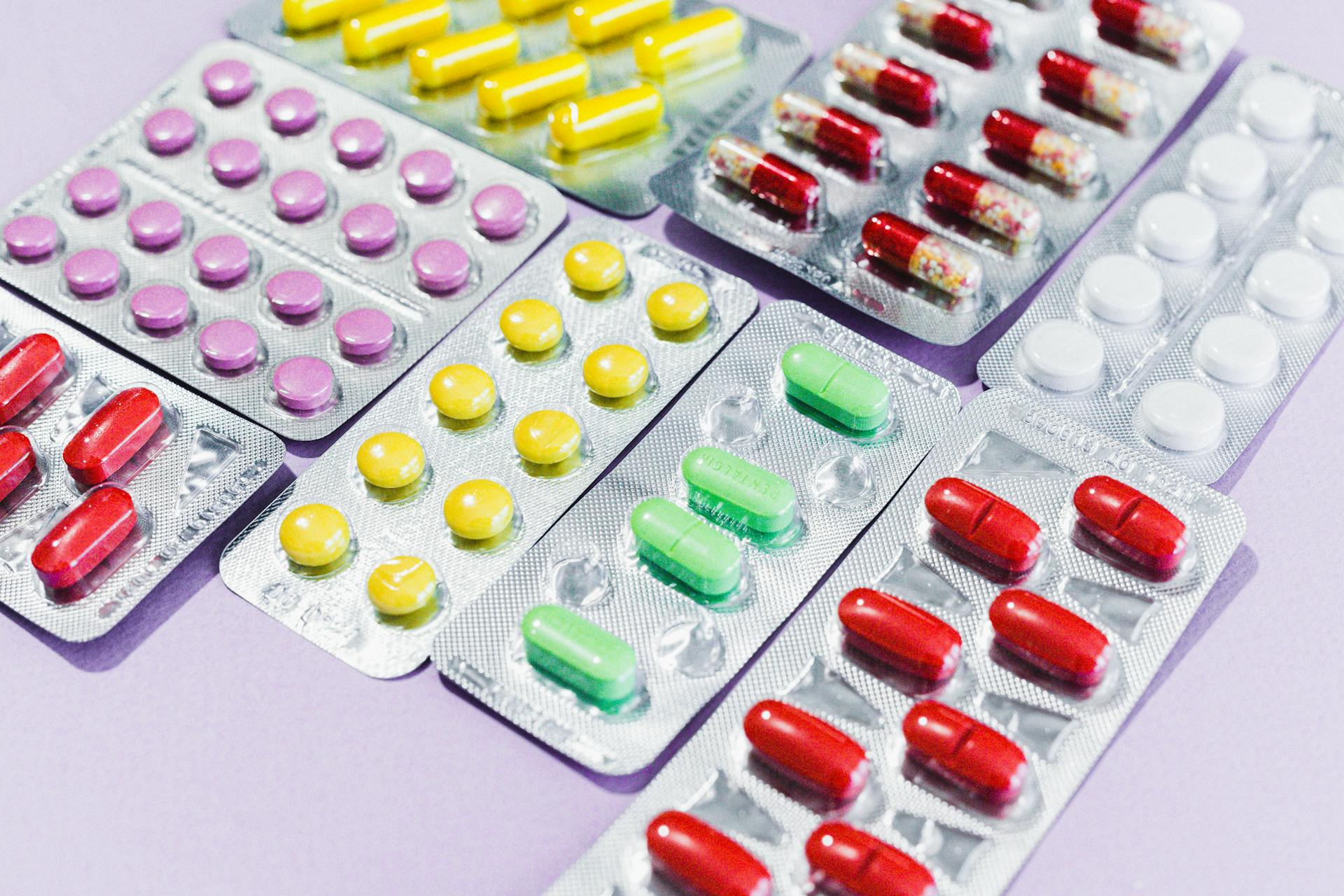
This feature ensures that medication information is clearly printed and scannable barcodes are available for accurate tracking.
Here are some key features to look for in a unit dose packaging machine:
- Labeling and barcode printing functionality
- Adjustable pouch size settings for different medications
- Accuracy and weight control systems to ensure correct dosage
- Automatic sealing to prevent contamination
- Ease of maintenance and availability of customer support
By considering these features, you can ensure that your unit dose packaging machine meets your business needs and provides the best possible results.
Benefits and Advantages
Investing in a unit dose packaging machine can greatly improve efficiency by reducing manual labor and minimizing packaging errors. These machines can produce up to 60 packages per minute, making them ideal for high-volume operations in hospitals and large pharmacies.
One of the key benefits of unit dose packaging machines is their ability to ensure consistent dosing accuracy. This is achieved through accuracy and weight control systems that ensure correct dosage. This means that patients receive the right amount of medication every time.
Automated feeding systems in modern unit dose packaging machines reduce crushed pills and eliminate empty packages between runs. This not only saves time but also reduces waste and increases productivity. With multiple package sizes available, including 2″ x 2″, 2″ x 1.67″, 2″ x 1.43″, and 2″ x 1.25″, businesses can customize their packaging to meet specific medication needs.
Here's an interesting read: Packaging Conveyor Systems
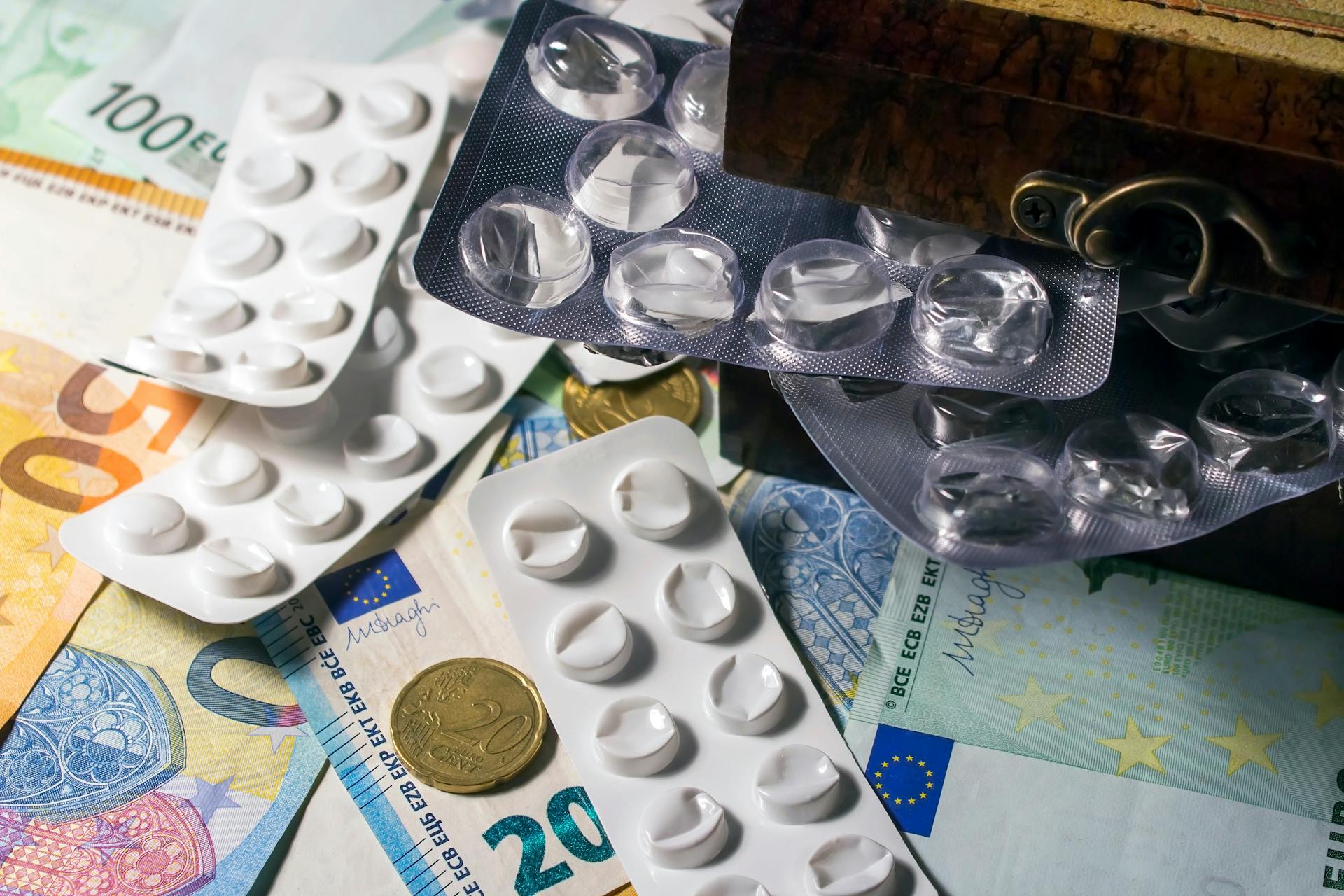
Unit dose packaging machines also enhance product safety and quality control by sealing individual doses securely, protecting them from contamination or tampering. This is especially important in the healthcare industry where patient safety is paramount.
Here are some key features to consider when purchasing a unit dose packaging machine:
- Labeling and barcode printing functionality
- Adjustable pouch size settings for different medications
- A accuracy and weight control systems to ensure correct dosage
- Automatic sealing to prevent contamination
- Ease of maintenance and availability of customer support
Smart Pack Features
Smart Pack offers four package size options, including 2.0" x 1.10", 1.32", 1.65", and 2.2", for versatile medication packaging.
The system verifies each package's scannability and accuracy, ensuring correct information is encoded. This ensures that medication information is accurate and can be easily tracked.
The Smart Pack system can print instructions on medicine packages in any language with easy-to-use software.
Here are some key features of the Smart Pack system:
The Smart Pack system also boasts advanced barcode technology, with clear and legible printing of medication information, and scannable barcodes for accurate tracking.
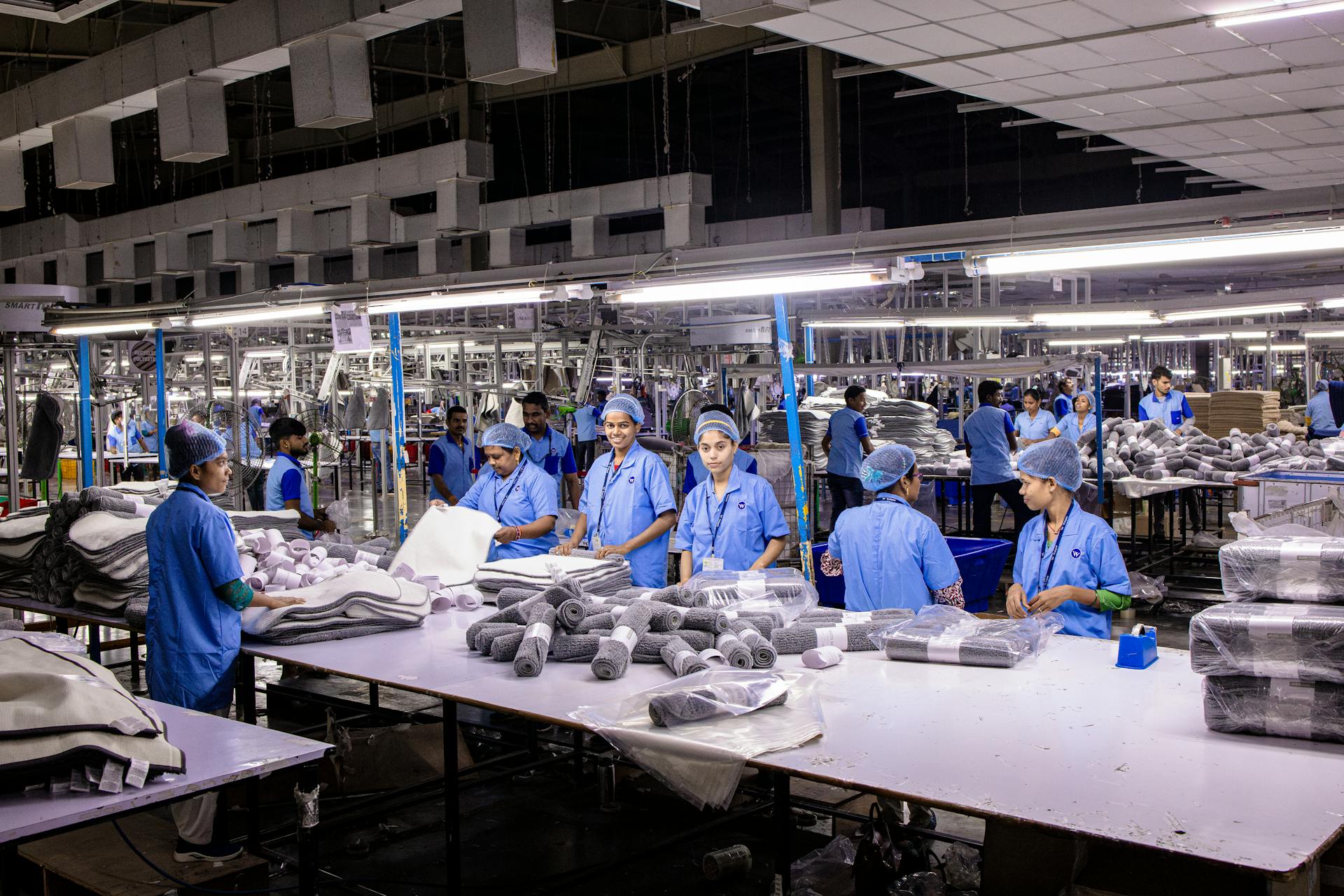
The system is designed to reduce manual labor and increase productivity, making it ideal for high-volume operations in hospitals and large pharmacies.
The Smart Pack system is also compatible with various tablet and capsule sizes, and offers flexible packaging options for different medications.
The system's automated feeding systems, such as the patented pill feeders, reduce crushed pills and eliminate empty packages between runs.
Overall, the Smart Pack system is designed to improve patient safety, streamline dispensing, and enhance inventory control.
Efficiency and Productivity
Unit dose packaging machines can significantly enhance efficiency and output quality by automating the packaging process, reducing labor costs, and improving overall productivity. These machines can package individual doses accurately and swiftly.
With the ability to fill and package multiple powders simultaneously, unit dose packaging machines can reduce the time and cost of production. They can also measure and dispense precise amounts of powder, ensuring that each sachet contains the correct dose of medication.
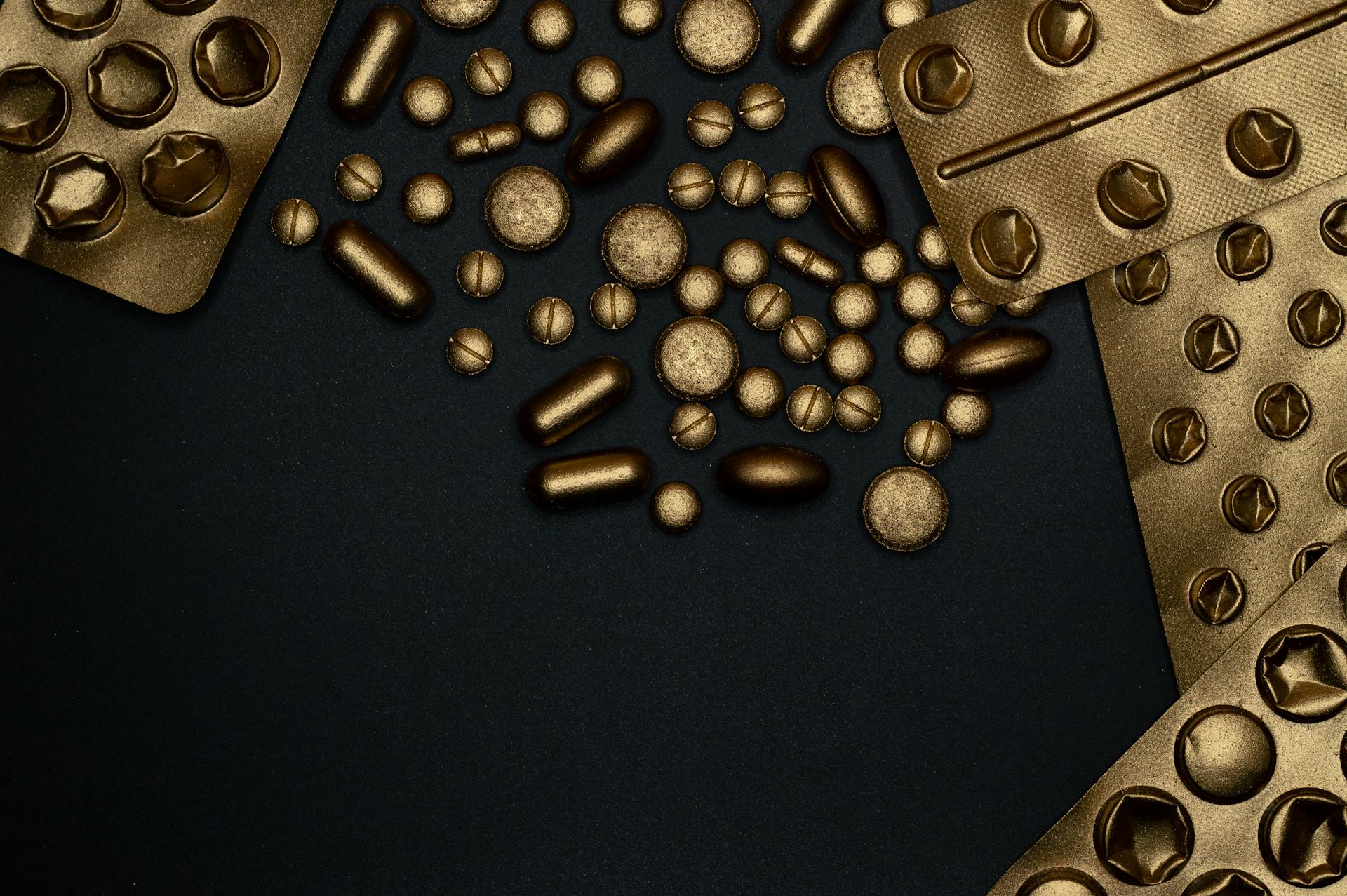
The Unidoses unit dose packaging machine, for example, can package at a speed of 55 packages per minute. It also features a built-in computer and has integration options with various systems, including QSI, Computer Rx, and Pioneer Rx.
Packages Per Minute: 55
Our unit dose packaging machines can produce up to 55 packages per minute, which is a significant boost to productivity in medication packaging workflows. This means you can get more done in less time.
Calibration-free dispensing ensures accurate dosage without manual adjustments, reducing the risk of errors. This is especially important in industries where precision is crucial.
The machines can extract manufacturing date, expiration, and lot number from GS1 barcodes, ensuring accurate tracking and traceability. This is a huge advantage in terms of inventory management and quality control.
Patented pill orientation technology prevents tablet crushing by centering pills within the pouch, away from sealing areas. This is a clever design feature that helps maintain the integrity of the medication.
Cleaning the machine's filling, sealing, and labeling components is a straightforward process that helps maintain the machine's performance over time. Regular maintenance is key to getting the most out of your unit dose packaging machine.
Enhancing Efficiency

Unit dose packaging machines can significantly enhance efficiency and output quality by automating the packaging process, reducing labor costs, and improving overall productivity. These machines are designed to fill and package individual doses accurately and swiftly.
With the ability to package multiple powders simultaneously, unit dose packaging machines can reduce the time and cost of production. This is particularly useful for pharmaceutical companies that need to produce large volumes of different medications quickly and efficiently.
According to Example 3, these machines can efficiently produce up to 55 packages per minute, optimizing productivity in medication packaging workflows. This level of efficiency is essential for businesses prioritizing precision and productivity.
Some of the key benefits of unit dose packaging machines include:
- Ability to fill and package multiple powders simultaneously
- Accuracy and precision in measuring and dispensing powder
- Ease of operation and maintenance
- Minimal downtime
- Integration with pharmacy management systems to enhance workflow and data tracking
By incorporating unit dose packaging machines into their production line, businesses can streamline their packaging process, reduce labor costs, and improve overall productivity.
Efficient Maintenance
Regular maintenance is key to keeping your unit dose packaging machine running smoothly. Follow the manufacturer's guidelines for cleaning, lubrication, and calibration to prevent breakdowns and ensure consistent operation.
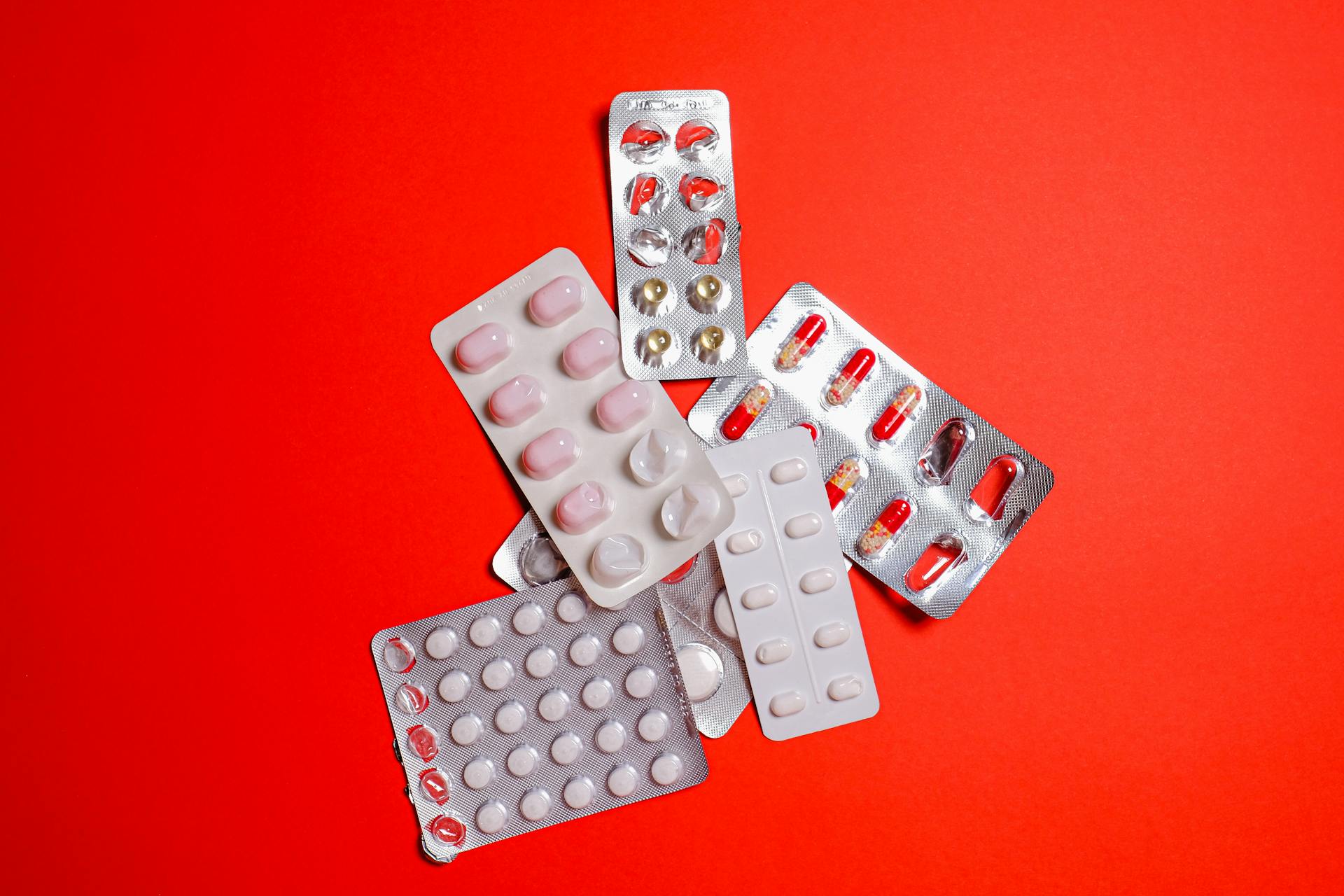
Routine inspections are essential to ensure all mechanical parts are functioning correctly. This helps you catch any potential issues before they become major problems.
Check with the manufacturer for specific maintenance schedules and service contracts for ongoing support. This will help you stay on top of maintenance and minimize downtime.
Training your staff on proper machine handling and maintenance procedures is crucial to minimizing downtime and maximizing productivity. By doing so, you can ensure that everyone knows how to properly care for the machine.
Pharmacy and Compliance
Regulatory compliance is crucial in pharmacies, and a unit dose packaging machine can help with that. It ensures accurate tracking, tamper-proof packaging, and audit readiness.
Integration with pharmacy management systems is a big plus for pharmacies. Our unit dose packaging machines can be integrated with pharmacy management systems to enhance workflow and data tracking.
Having multiple package size options is essential for pharmacies. The Smart Pack Unit Dose Packaging System offers four package size options for versatile medication packaging.
Readers also liked: Cd Packaging Size
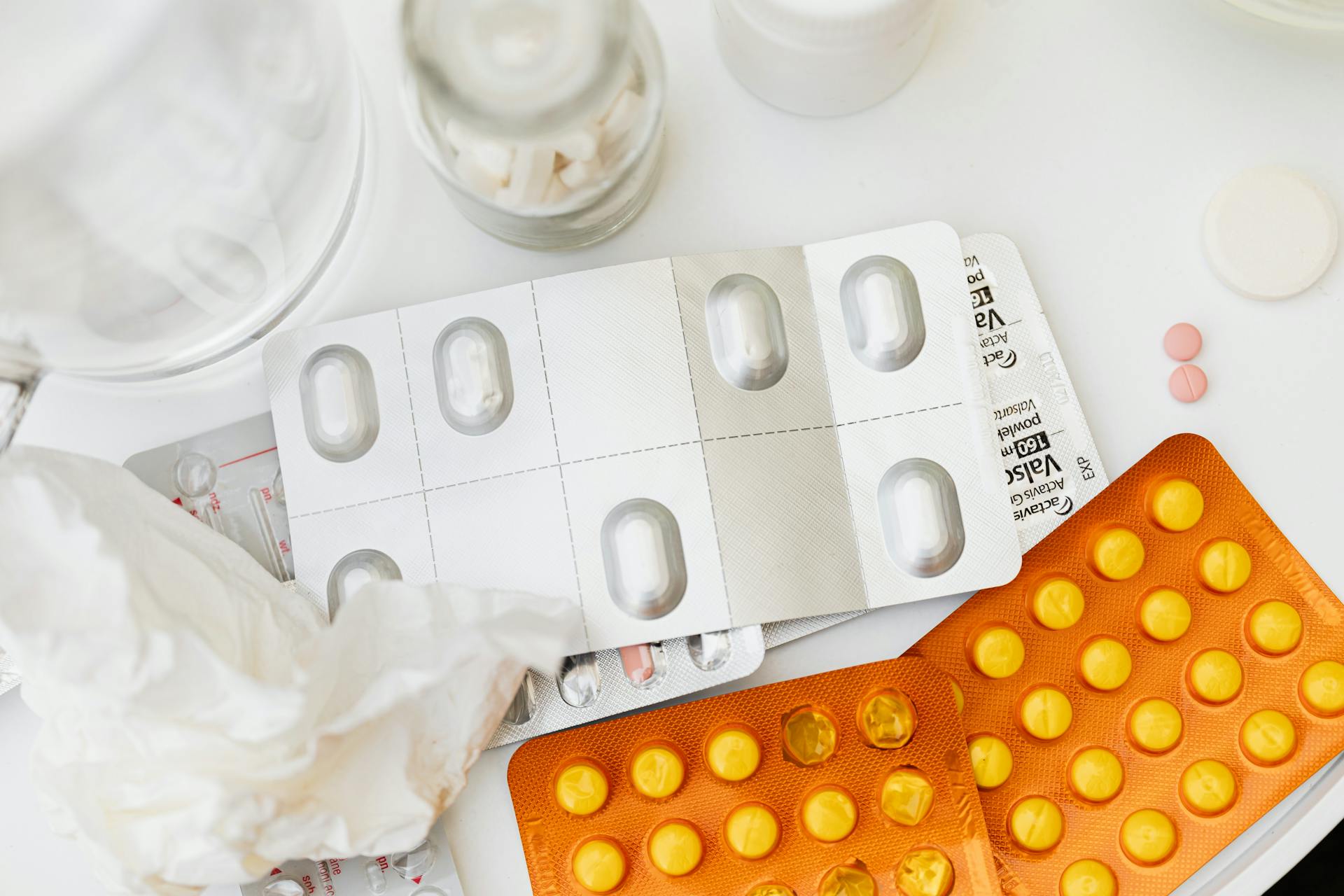
Scannability and accuracy are vital for patient safety. The Smart Pack Unit Dose Packaging System verifies each package's scannability and accuracy, ensuring correct information is encoded.
High-volume pharmacies require a unit dose packaging machine that can keep up. Many unit dose tabletop pouch packaging machines are capable of high throughput, especially those designed for medium to large-scale operations.
Handling narcotic or controlled medications requires precision and security. Automated pouch packaging solutions like Smart Pack streamline dispensing, improve patient safety, and enhance inventory control.
Types and Applications
There are several types of unit dose packaging machines, each designed to cater to specific packaging needs. These machines are tailored to handle various types of medications or products, such as liquid medications or solid tablets.
Automated unit dose packagers are perfect for high-speed packaging, capable of producing up to 60 packages per minute, making them ideal for hospitals and large pharmacies. They reduce manual labor and increase accuracy.

Multi-dose packagers are designed for packaging multiple medications at once, simplifying medication administration for long-term care facilities. Liquid unit dose packagers feature a syringe pump mechanism, ensuring precise dosing for oral liquid medications.
Here's a breakdown of the different types of unit dose packaging machines:
What is a Tabletop Pouch?
A tabletop pouch is a compact, automated system used in pharmacies to package individual doses of medication into single-use pouches. These pouches are designed to be used once and then discarded.
The pouches are filled and sealed by a machine, which also prints labels and barcodes for tracking and identification purposes. This ensures medication accuracy and patient safety.
How Does the Tabletop Pouch Function?
The tabletop pouch function is quite fascinating. It works by filling the pouch with a precise dose of medication, ensuring accuracy and safety.
This precision filling is made possible by the machine's ability to accurately measure and dispense the medication. This is especially important for solid oral medications that require a specific dose.
Consider reading: Pill Bottle Filling Machine
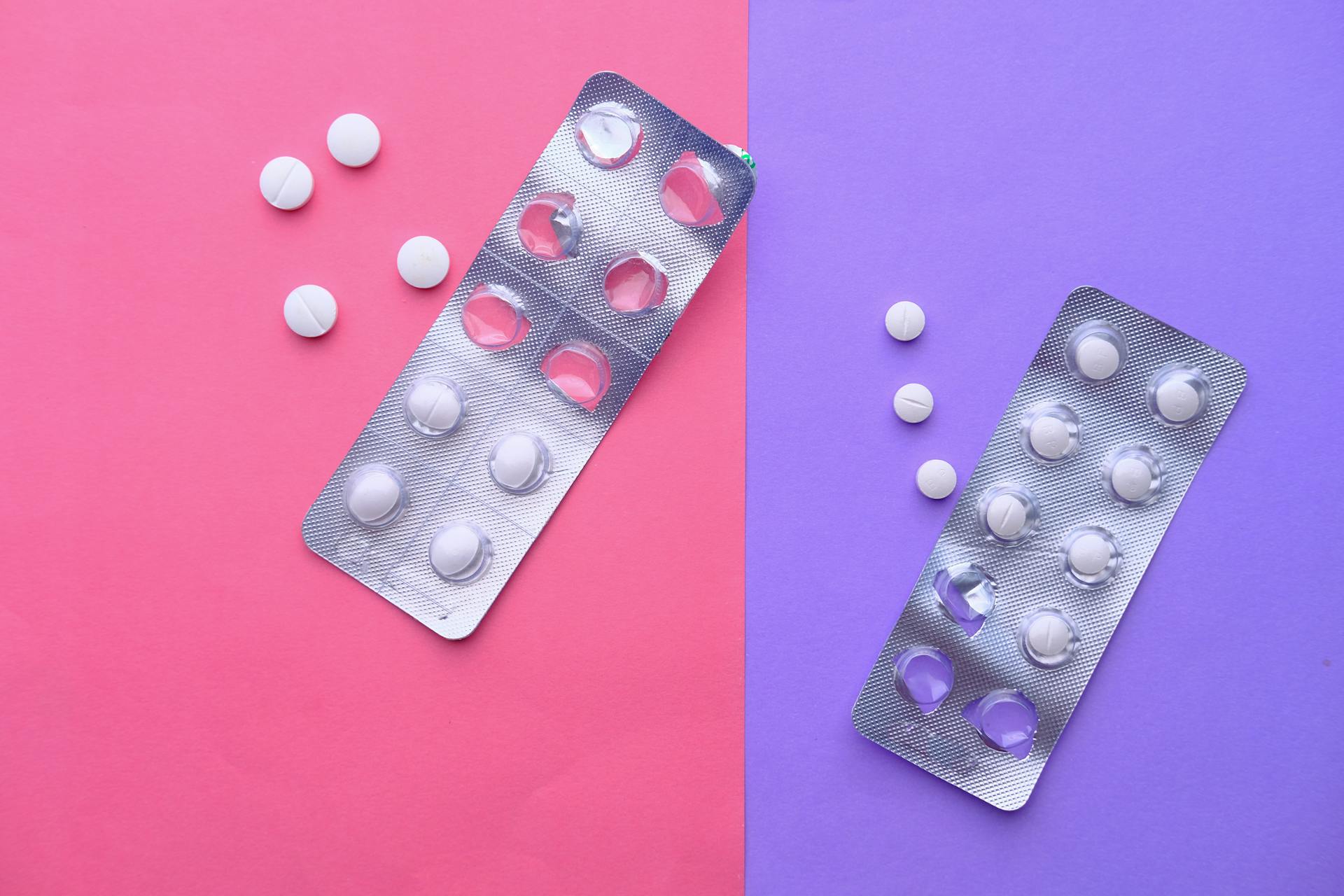
The pouch is then sealed using heat or another sealing method to securely enclose the dose. This sealing process is crucial to prevent the medication from spilling or being contaminated.
Labels are printed directly onto the pouches, including vital information like medication name, dosage instructions, expiration date, and barcodes for easy tracking.
See what others are reading: Chamber Vacuum Sealing Machine
Types of
Unit dose packaging machines come in various types, each designed to cater to specific packaging needs. Liquid unit dose packaging machines are perfect for handling liquid medications or products that require precise measurement and sealing.
There are several types of unit dose packaging machines available, including automated unit dose packagers, multi-dose packagers, liquid unit dose packagers, compliance packaging systems, and tabletop unit dose packagers.
Automated unit dose packagers can package up to 60 packages per minute, making them ideal for hospitals and large pharmacies. They reduce manual labor and increase accuracy, which is a significant advantage.
Multi-dose packagers are designed for packaging multiple medications at once, making them perfect for long-term care facilities. They simplify medication administration and make it easier for caregivers to manage patient medication.
Curious to learn more? Check out: Liquid Packaging Companies

Liquid unit dose packagers use a syringe pump mechanism to ensure precise dosing, making them ideal for oral liquid medications. They are a crucial tool for businesses that need to package liquid solutions with accuracy.
Compliance packaging systems offer customizable packaging, which is a significant advantage for retail pharmacies. They enhance patient adherence by providing packaging that meets specific regulatory requirements.
Tabletop unit dose packagers are compact and space-efficient, making them perfect for small pharmacies and clinics. They are easy to operate and require minimal maintenance, which is a significant advantage for businesses with limited resources.
Here's a breakdown of the different types of unit dose packaging machines:
Technical Details
High-speed packaging capabilities are a must-have for efficient operations. This feature allows you to package a large volume of medications quickly and accurately.
Adjustable dosing options are a key consideration. This feature enables you to customize the packaging for different medications and dosages.
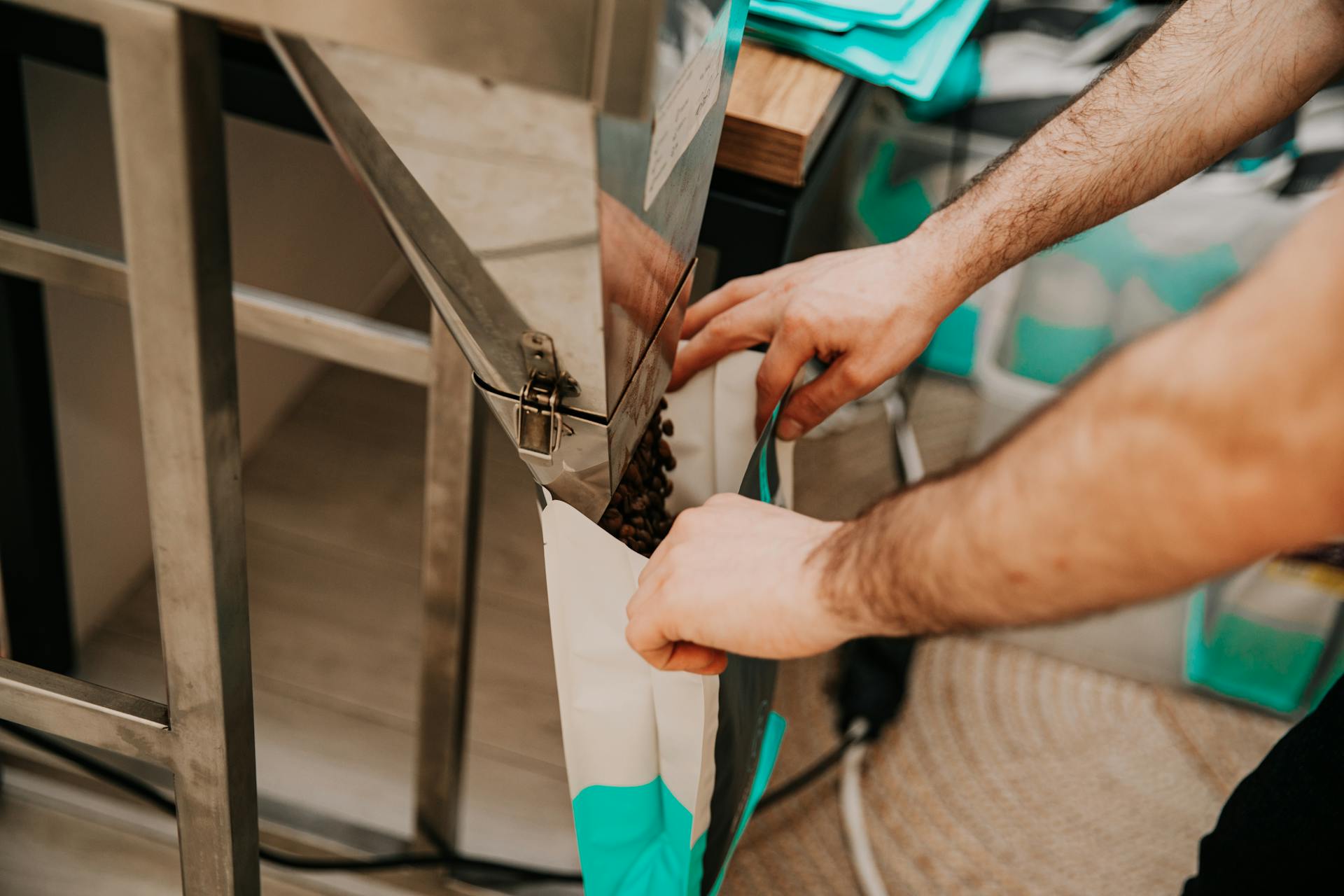
Automatic filling and sealing functions are also essential. These functions help prevent contamination and ensure that your medications are packaged safely and securely.
User-friendly interfaces are crucial for easy operation. A machine with a simple and intuitive interface will save you time and reduce errors.
Easy maintenance requirements are vital for smooth operations. Look for machines with minimal maintenance needs to reduce downtime and increase productivity.
Labeling and barcode printing functionality is a must-have for accurate tracking and identification. This feature helps you keep track of your medications and ensures that they are properly labeled.
Automatic sealing prevents contamination and ensures that your medications are packaged safely. This feature is a critical component of a unit dose packaging machine.
Accuracy and weight control systems are essential for ensuring correct dosages. These systems help you package the right amount of medication every time.
Ease of maintenance and availability of customer support are critical factors to consider. Look for machines with minimal maintenance needs and a reliable support team to ensure smooth operations.
You might like: Automatic Strapping Machine
Purchasing and Implementation
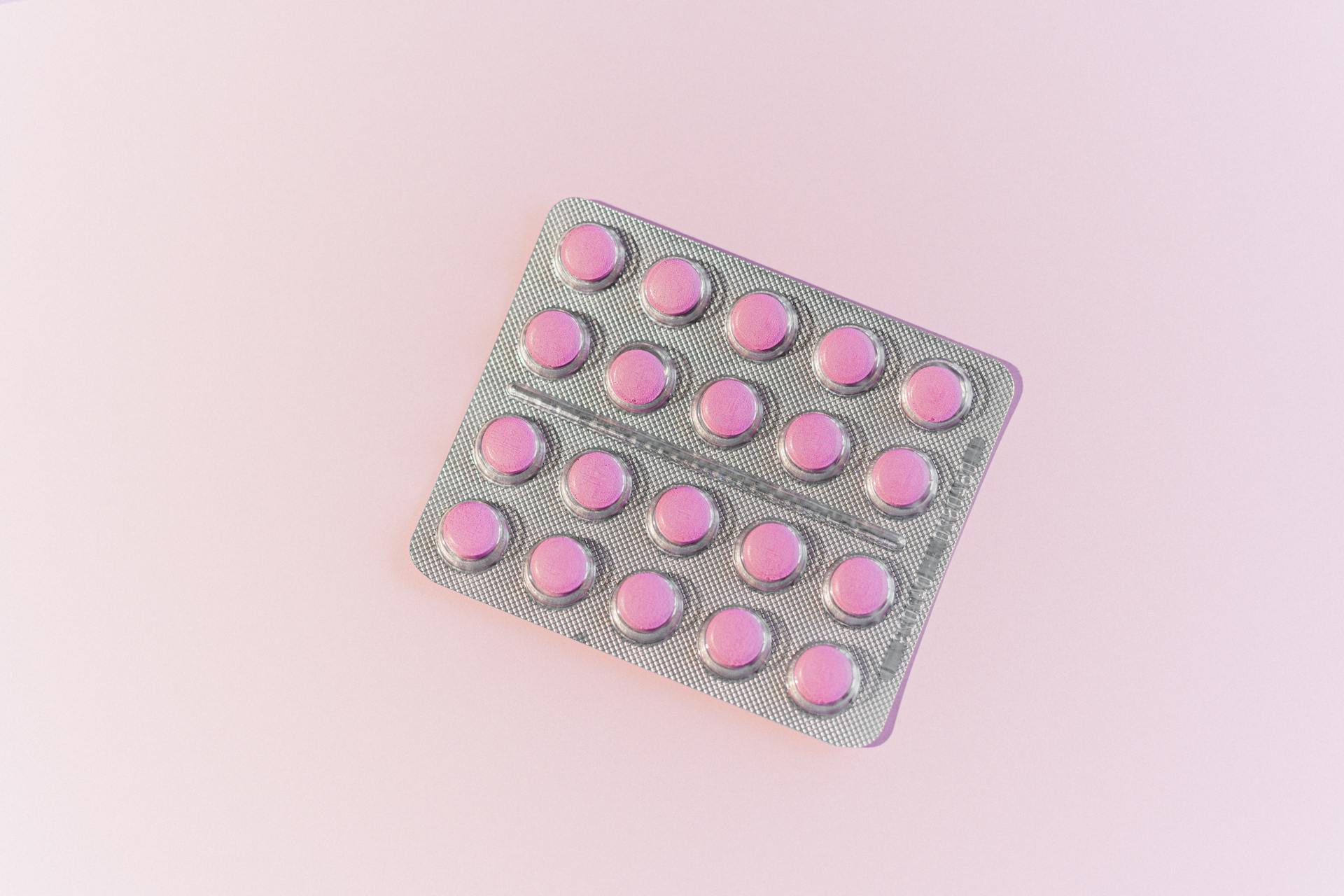
Purchasing and implementation of a unit dose packaging machine requires careful consideration of several factors. The cost of the machine can range from $10,000 to $50,000, depending on the size and features.
Before making a purchase, it's essential to assess your company's specific needs and budget. The machine's size and capacity will also impact your decision, as a larger machine may be more expensive but also more efficient.
A unit dose packaging machine can be purchased outright or leased, with leasing options typically ranging from 2 to 5 years. This can help spread out the cost and improve cash flow.
Core Features for Purchase
When purchasing a Unit Dose Packaging machine, there are several key features to consider. Labeling and barcode printing functionality is a must-have.
Accuracy and weight control systems are also essential to ensure correct dosage. This feature helps prevent errors and ensures patients receive the right medication.
Automatic sealing is crucial to prevent contamination. This feature also helps maintain a clean and sterile environment.
Ease of maintenance and customer support availability are also important considerations. A machine that's easy to maintain and has reliable customer support can save you time and money in the long run.
Here are some specific features to look for in a Unit Dose Packaging machine:
Some Unit Dose Packaging machines offer advanced features like high-speed packaging and automated feeding systems. These features can increase productivity and reduce manual labor.
For example, some machines can produce up to 60 packages per minute, making them ideal for high-volume operations in hospitals and large pharmacies.
Implementation Considerations
When implementing a unit dose packaging system, consider the space requirements of your facility. This will help you choose the right size system for your needs.
You'll want to think about tabletop models for small facilities, or larger systems for high-volume operations. This will ensure you're not wasting space or struggling to meet demand.
Proper ventilation and electrical connections are crucial for the safe operation of your system. Don't overlook these important details.
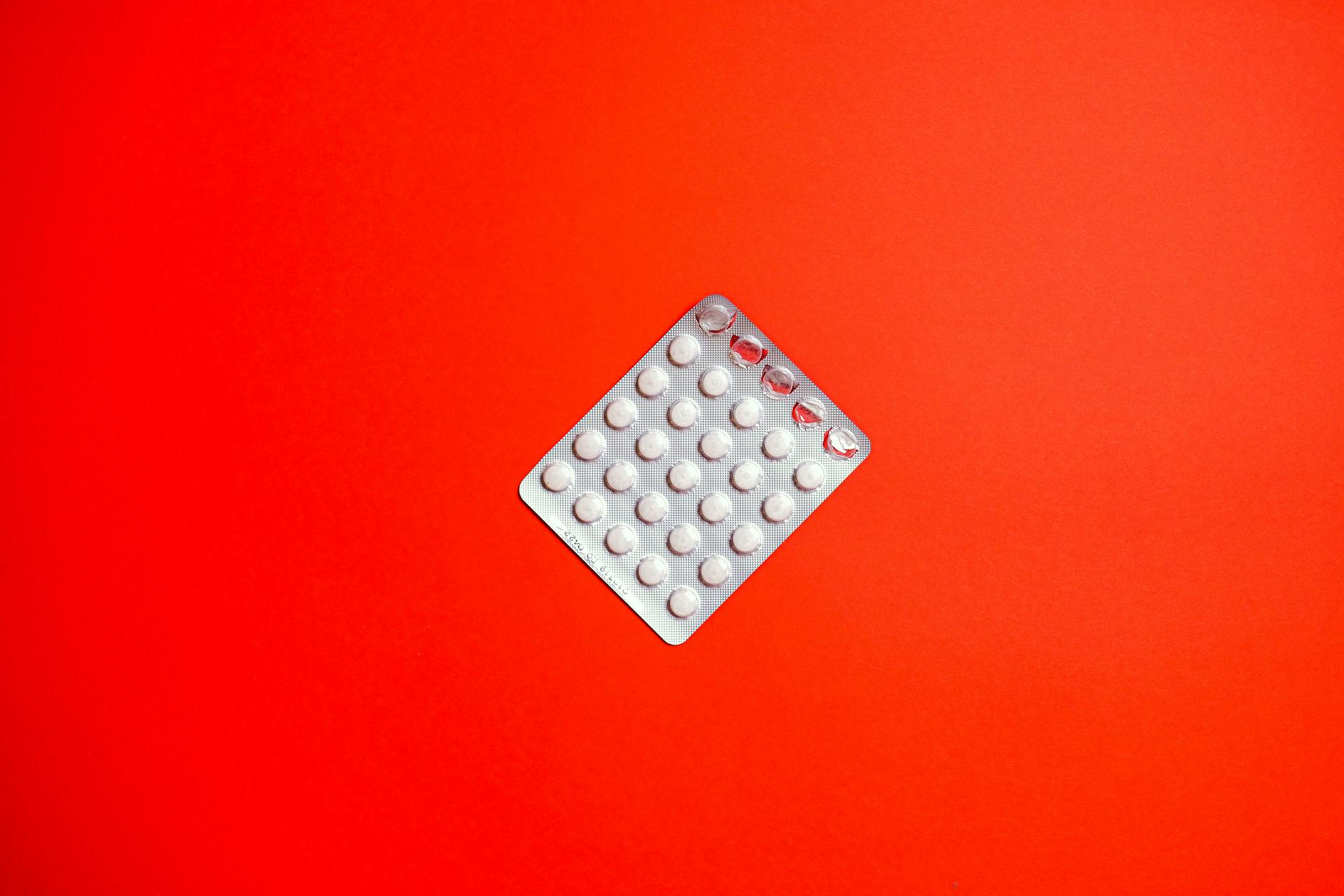
Comprehensive training programs are essential for staff to learn how to use the system effectively. This will save you time and reduce errors in the long run.
User-friendly interfaces and technical support availability are also important considerations. You want to make sure your staff can easily use the system and get help when they need it.
To ensure regulatory compliance, look for FDA-registered materials and USP Class A and B standards. This will give you peace of mind and avoid any potential issues.
DSCSA and JCAHO compliance are also important to consider. These regulations are in place to protect patients and ensure the safe handling of medications.
In addition to these considerations, you'll also want to conduct a cost-benefit analysis. This will help you weigh the initial investment against the long-term savings and calculate your return on investment.
Here's a breakdown of the costs to consider:
Best Practices
When implementing unit dose packaging, it's essential to prioritize quality control. Regular calibration checks are a must to ensure accurate measurements.
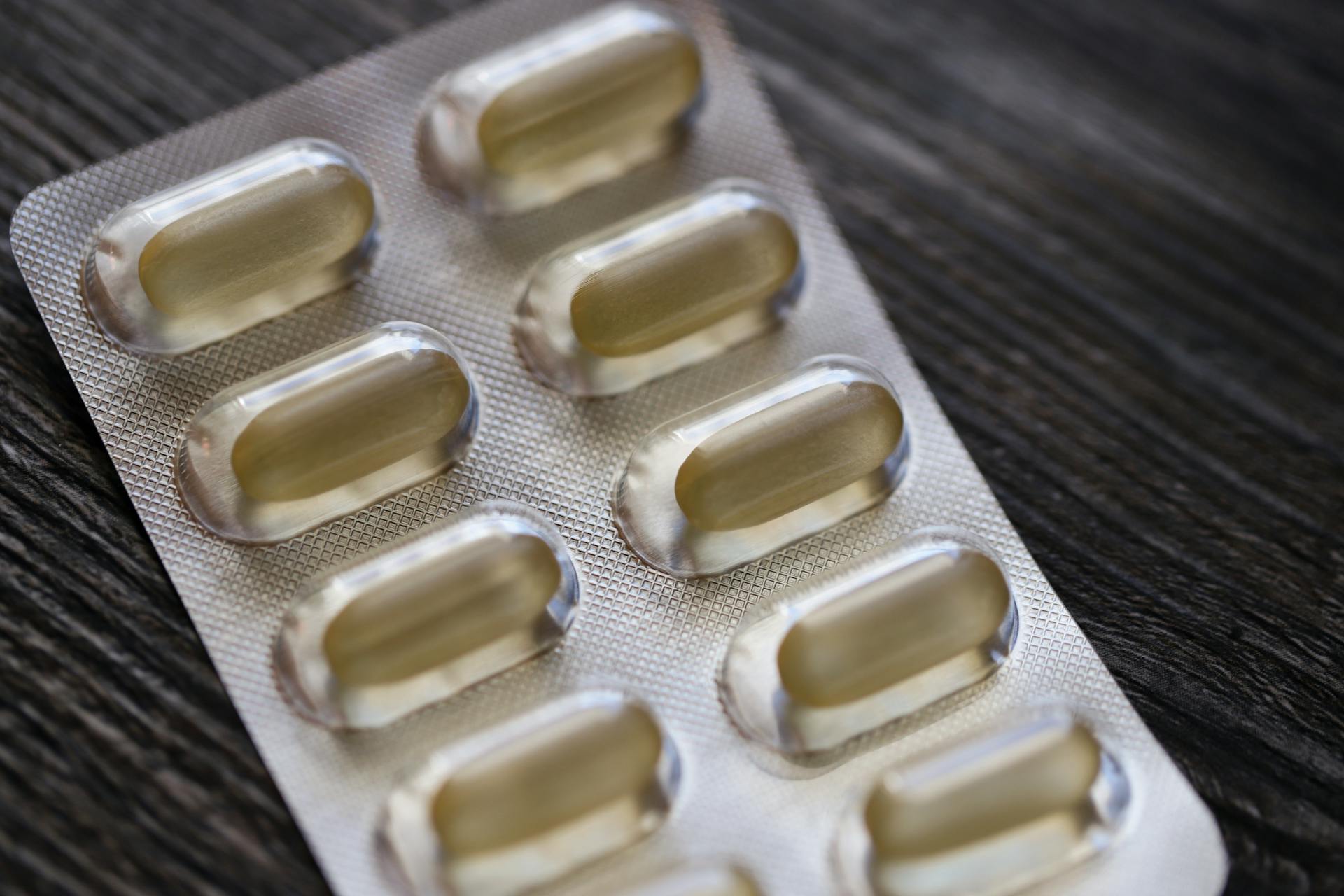
Documentation of all processes is crucial for maintaining transparency and accountability. This includes inventory management, where accurate stock tracking and efficient medication rotation are vital for minimizing waste.
Staff training is also a critical aspect of implementing unit dose packaging. Comprehensive onboarding and regular refresher courses are necessary for ensuring that staff are equipped to handle the new system. Documentation of training is also important for tracking progress and identifying areas for improvement.
Regular cleaning protocols and preventive maintenance are essential for maintaining the system's performance. This includes regular cleaning of equipment and performing preventive maintenance tasks to prevent system downtime.
Here are some key maintenance tasks to keep in mind:
Sources
- https://www.euclidmedicalproducts.com/products/unit-dose-packaging-machines/
- https://www.alibaba.com/showroom/unit-dose-packaging-machine.html
- https://www.maxispharmacyautomation.ca/Smart-Pack
- https://www.sourcifychina.com/unit-dose-packaging-machine/
- https://www.cankeytech.com/unit-dose-packaging-machine/
Featured Images: pexels.com