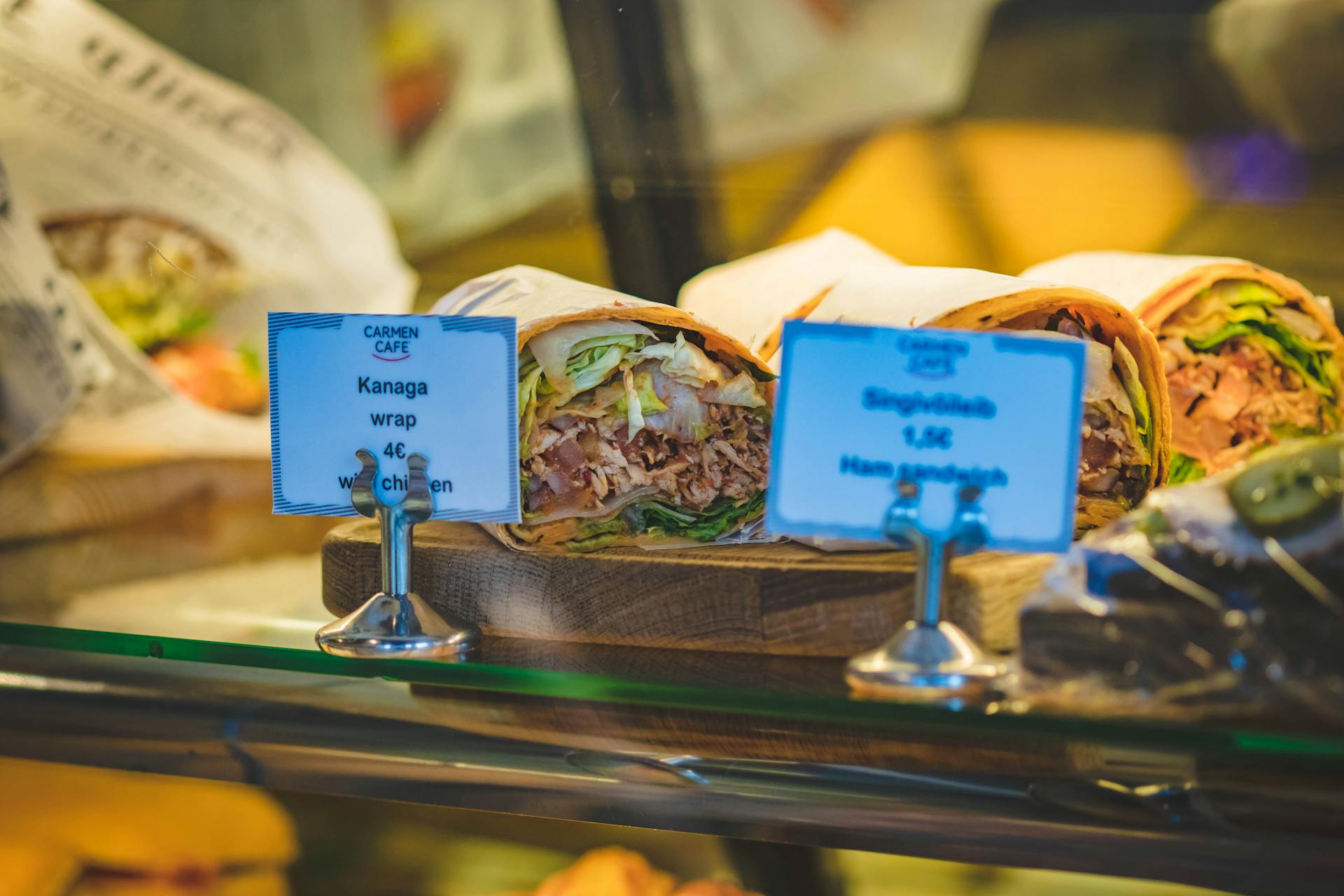
Saran Wrap thickness is a crucial factor to consider when choosing the right product for your needs. There are several thickness options available, ranging from 0.5 mil to 3 mil.
A 0.5 mil thickness is ideal for delicate items and is often used for packaging and wrapping food. This thickness is also great for crafting and DIY projects.
A 1 mil thickness is a good all-purpose option, suitable for wrapping most household items. It's also a popular choice for food storage and wrapping.
For heavy-duty use or wrapping larger items, a 2 mil or 3 mil thickness is recommended. These thicker options provide added durability and protection.
Understanding Saran Wrap
Saran wrap was discovered in 1933 when a lab worker at Dow chemical was having trouble washing out beakers used in developing a dry-cleaning product.
The original plastic wrap that was invented was PVdC, or Polyvinylidene Chloride.
In 1949 Dow Chemical refined the spray and developed saran plastic wrap, which is now commonly made out of PVC, or Polyvinylidene Chloride.
PVC plastic wrap provides a good amount of cling, but it has environmental concerns associated with the chloride it contains.
In 2004 the "Saran" brand changed to using LDPE, or Low-Density Polyethylene, due to these environmental concerns.
Additional reading: Pvc Cling Wrap
Measuring Thickness
Saran wrap thickness can be measured in various ways, with common methods including using a micrometer, caliper, or even a ruler.
A typical sheet of saran wrap is around 0.5 to 0.7 millimeters thick, depending on the type and brand.
The thickness of saran wrap can affect its performance, with thicker sheets being more durable but also more prone to tearing.
Saran wrap thickness can range from 0.2 to 1.5 millimeters, with some specialty products even thinner or thicker.
In practical terms, this means that thicker saran wrap is better suited for heavy-duty applications, while thinner sheets are more suitable for delicate or precise tasks.
Optimizing Film Thickness
Reducing the thickness of stretch wrapping film is a key strategy to lower production costs. From 1975 to 2013, the uniform thickness of stretch wrap film decreased from 30 μm to 20 μm.
By reducing the thickness, the net weight of the stretch film is also greatly reduced. The weight of the stretch film was reduced from 5kg to 3kg.
A unique perspective: Cling Film Wrapper
The original thickness of a roll of ordinary stretch wrapping film was 20mic, but now it's been reduced to 13mic. This change has resulted in a significant decrease in production costs.
Our company's stretch film research is based on the principle of constant quality change, ensuring that the quality of the film is not compromised despite the reduction in thickness. The purpose of Sinyar stretch film is to reduce costs for our customers who use our stretch film.
The reduced thickness of the film also makes it more efficient to use, allowing for easier wrapping and less waste.
For another approach, see: Shrink Film Wrap
Factors Affecting Thickness
The uneven thickness of saran wrap is primarily caused by the blow molding process, which can result in uneven distribution due to high and low die temperatures.
Die temperature plays a crucial role, and adjusting the machine head's temperature can make the mold uniform. The gap between the die openings can also cause inconsistencies, with larger gaps resulting in thinner film and smaller gaps resulting in thicker film.
To achieve uniform thickness, the gap between the die openings needs to be adjusted. Inconsistent air supply around the cooling air ring can also lead to uneven cooling effects and thickness.
Here are the main factors affecting the thickness of saran wrap:
- Uneven die temperatures
- Inconsistent gap between die openings
- Incorrect inflation and traction ratios
- Uneven air supply around the cooling air ring
- Variable traction speed
Factors Affecting Thickness
The uneven thickness of stretch wrapping film is a common problem that can be caused by several factors.
High and low die temperatures during the blow molding process can lead to uneven distribution of the film's thickness.
The gap between the die openings can also be a problem, with some parts having larger gaps and others having smaller gaps, resulting in inconsistent thickness.
Adjusting the die temperature and gap can help to make the mold temperature uniform and ensure consistent thickness everywhere.
The inflation and traction ratios can also impact the film's thickness, making it difficult to control if they are not suitable.
A consistent air supply around the cooling air ring is also important, as an uneven cooling effect can result in uneven thickness.
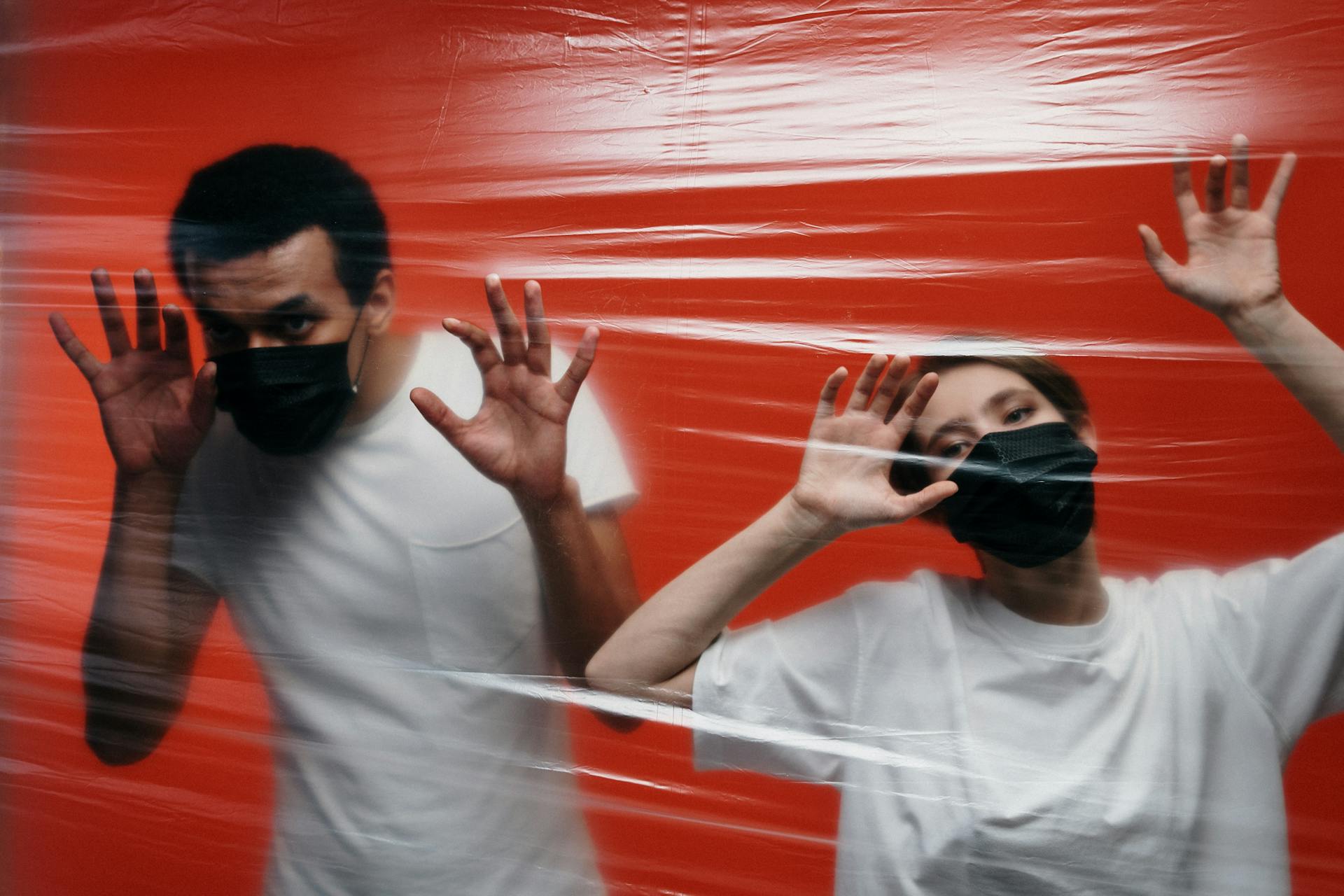
If the traction speed is not constant, it can lead to uneven thickness of the produced stretch wrapping film.
Here are the main factors affecting the thickness of stretch wrapping film:
- High and low die temperatures
- Uneven gap between die openings
- Insuitable inflation and traction ratios
- Uneven air supply around the cooling air ring
- Variable traction speed
Common Issues with Film Thickness
Film thickness can be affected by the type of coating being applied, as seen in the section on "Coating Type and Thickness". For example, epoxy coatings tend to be thicker than polyurethane coatings.
Incorrect application techniques can also lead to issues with film thickness. The section on "Application Methods and Thickness" highlights the importance of proper application to achieve the desired thickness.
Temperature and humidity can also impact film thickness, as mentioned in the section on "Environmental Factors and Thickness". For instance, high temperatures can cause the coating to dry too quickly, resulting in a thinner film.
Inadequate surface preparation can also lead to issues with film thickness. The section on "Surface Preparation and Thickness" emphasizes the importance of a clean and dry surface for optimal coating performance.
Film thickness can also be affected by the amount of coating material used, as seen in the section on "Material Quantity and Thickness". Using too little material can result in a thin film, while using too much can lead to a thick, uneven film.
Sources
- https://uspackagingandwrapping.com/plastic-wrap-101.html
- https://uspackagingandwrapping.com/blog/a-guide-to-stretch-wrap-thickness.html
- https://www.webstaurantstore.com/455/cling-wrap-and-plastic-food-wrap.html
- https://www.aaapolymer.com/choosing-the-right-stretch-wrap-gauge-or-thickness/
- https://www.plasticwraproll.com/do-you-know-the-stretch-film-thickness/
Featured Images: pexels.com