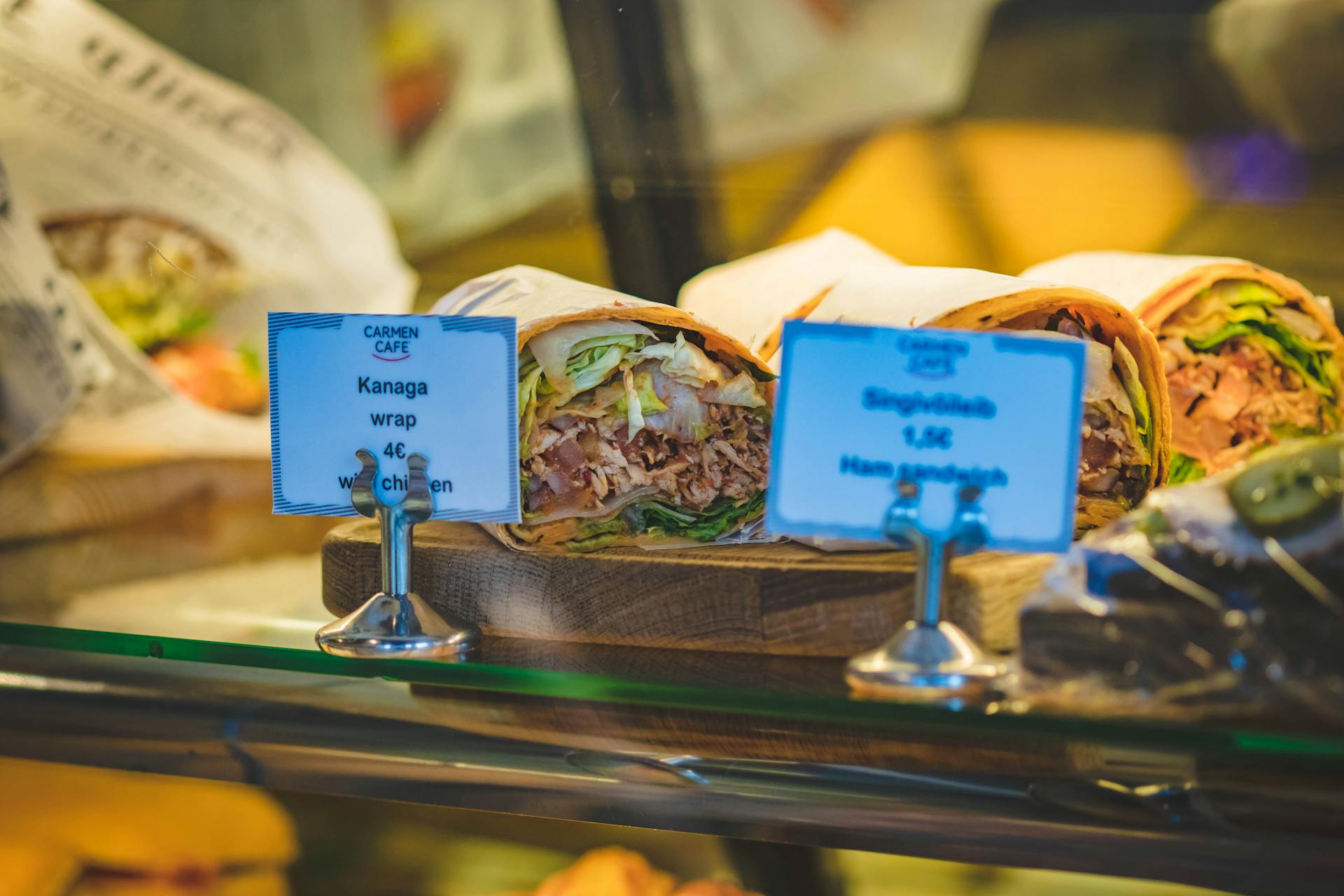
Saran wrap machines come in various types, each designed for specific applications. There are semi-automatic machines that can wrap up to 20 pounds of food per hour.
Some saran wrap machines are specifically designed for wrapping large items like meat or cheese. These machines can wrap items up to 20 inches in diameter.
Semi-automatic machines are a popular choice for small to medium-sized businesses due to their affordability and ease of use. They are often used in delis, butcher shops, and restaurants.
Automatic machines are ideal for high-volume wrapping operations and can wrap up to 50 pounds of food per hour. They are commonly used in large supermarkets and food processing facilities.
Broaden your view: Semi-automatic Stretch Wrap Machine with Scale
Machine Types
There are three main types of cling film wrapping machines: manual, semi-automatic, and fully automatic. Each type has its own unique features and benefits.
A manual cling film wrapping machine requires complete human involvement, with the operator placing the product in a tray and manually wrapping the film around it. This process is slow, with only 50-60 products wrapped per hour.
You might like: Automatic Strapping Machine
Semi-automatic cling film wrapping machines, on the other hand, strike a balance between efficiency and manual labor. They require human operators to place the products on the platform and start the wrapping cycle, but the machine itself wraps the film around the product. This increases productivity to over 150 products per hour.
Fully automatic cling film wrapping machines are the most efficient option, with the machine capable of wrapping, cutting, and sealing the film automatically. They can produce over 200-250 wrapped products per hour, making them ideal for high-speed production lines.
Here are the key features of each machine type:
- Manual: 50-60 products per hour, complete human involvement
- Semi-automatic: 150+ products per hour, human operator assistance
- Fully automatic: 200-250 products per hour, complete machine automation
Types of
There are three main types of cling film wrapping machines: manual, semi-automatic, and fully automatic. Manual machines require a lot of human effort and can only wrap around 50-60 products per hour.
Semi-automatic machines are a great middle ground, allowing operators to place products on the inlet station and then wrapping the film around them. These machines can produce over 150 trays per hour.
Worth a look: Semi-automatic Bag in Box Filling Machines
Fully automatic machines, on the other hand, can wrap, cut, seal, and apply heat automatically, making them perfect for high-speed production lines. They can produce around 200-250 wrapped products per hour.
Here are some key differences between these types of machines:
Ultimately, the choice of machine depends on the specific needs of your business. If you're looking for high-speed production and efficiency, a fully automatic machine might be the way to go.
Tw-550e Food Preserver
The TW-550E Food Preservation Cling Film Wrapping Machine is a versatile tool suitable for wrapping food and non-food products with widths between 0mm to 550mm.
It's widely used in various settings, including supermarkets, hotels, restaurants, family kitchens, and small factories.
This machine is made of high-level stainless steel, making it durable and hard.
It's equipped with world-class components for excellent performance.
The TW-550E can be easily operated, requiring minimal training.
A strong sealing effect is one of its notable features.
Its compact design makes it a great addition to any workspace.
The TW-550E is a reliable choice for preserving food and other products.
It's a great option for producers looking to extend the life of their products and protect them from environmental effects.
Recommended read: Glad Wrap Products
Applications of
Saran wrap machines are widely used in various industries, including food packaging, where they wrap food products like vegetables, fruits, and eatables to protect them from microorganism and bacterial attacks.
Food packaging is the largest user of saran wrap machines globally, with almost every part of the world utilizing them to package food products.
Agricultural products also use saran wrap machines to wrap products that can be easily transported over long distances.
In the cosmetic industry, saran wrap machines are used to wrap chemical and cosmetic products, which are sensitive and require secure packaging.
Chemical products are highly sensitive and wrapping them with a saran wrap machine doubles their strength and life.
Small-scale retail stores use saran wrap machines to wrap items like groceries, vegetables, fruits, snacks, and baked goods for their clients.
In restaurants, saran wrap machines are used to wrap leftovers, pre-cut food items, and prepared dishes to keep them fresh and maintain their flavors.
Bakeries and snack production facilities use saran wrap machines to wrap baked goods like bread, cookies, and pastries.
Meat processing plants use saran wrap machines to wrap fresh meat cuts to preserve their freshness and avoid contamination.
In the pharmaceutical industry, saran wrap machines are used to wrap and package medical and healthcare products, ensuring their sterility and protection from external contaminants.
In logistics and warehousing, saran wrap machines are used to wrap and secure pallets, boxes, and other items for storage and transportation.
The machine applies a layer of saran wrap around the items to create a secure and stable load that protects the products from damage and theft.
In the manufacturing industry, saran wrap machines are used to wrap individual items, components, or finished goods to protect them during storage, handling, and transportation.
For another approach, see: Blister Packaging Machine Pharmaceutical Industry
Working and Structure
A cling film wrapping machine, also known as a saran wrap machine, has a working principle that involves checking external parameters before operation, which includes temperature, pressure, electric supply, vacuum, film length, and more.
The machine is preheated for 5 to 10 minutes to ensure smooth operation, and the product is placed on the cover plate with the film pulled out to cover and wrap it.
The machine then cuts the film to the desired length, and the product is placed on a teflon coated hot plate where it is wrapped and sealed in 3 to 5 minutes.
The structure of a cling film wrapping machine consists of stainless steel to make it durable and long lasting. It has various systems, including a heating system, stretching system, conveying system, induction conveying system, sealing system, and controllers.
The machine has controlling knobs for parameters like temperature, pressure, and conveying speed, as well as a feeding bracket or platform where the product is fed into the system.
The wrapping platform is the main unit where the wrapping is done, and it has an induction system to enter the product automatically and a release conveying system to send the wrapped product back after process completion.
A fresh viewpoint: Avery Labels Printer
Working Principles of
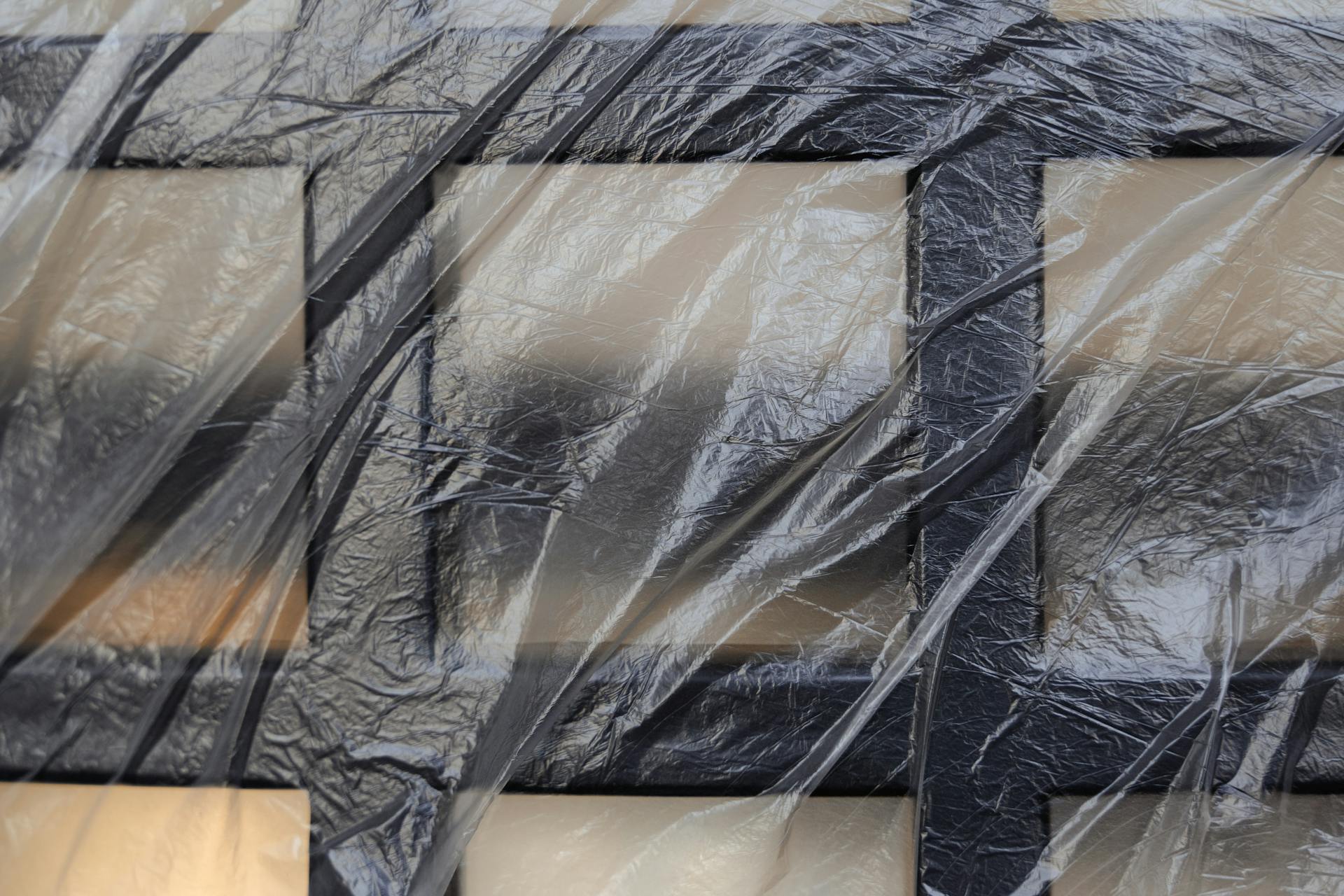
The working principles of a cling film wrapping machine are quite fascinating. They start by checking all the external parameters of the machine, such as temperature, pressure, electric supply, vacuum, film length, and more, before it begins operation.
These parameters are crucial to ensure the machine runs smoothly and efficiently. The thermostats maintain the temperature of the hot plate, depending on the type of wrapping material used.
The film roll is set according to the material being wrapped and the product's size. This ensures a perfect fit for the product.
The machine is then preheated for 5 to 10 minutes to allow it to run smoothly from the first product. This initial heating process is essential for the machine's performance.
Here's a step-by-step overview of the machine's operation:
- Place the product on the cover plate and pull the film out to cover and wrap the product.
- Cut the film to the desired length of the product using the cutoff bar.
- Place the product on the teflon-coated hot plate, where it will be completely wrapped and sealed in 3 to 5 minutes.
- The machine produces an airtight and sealed product with efficiency and precision.
The cling film roller is a crucial component, allowing for the wrapping of products of any size, length, or diameter. This roller ensures a secure and even wrap.
On a similar theme: Lineshaft Roller Conveyor
Describe Structure
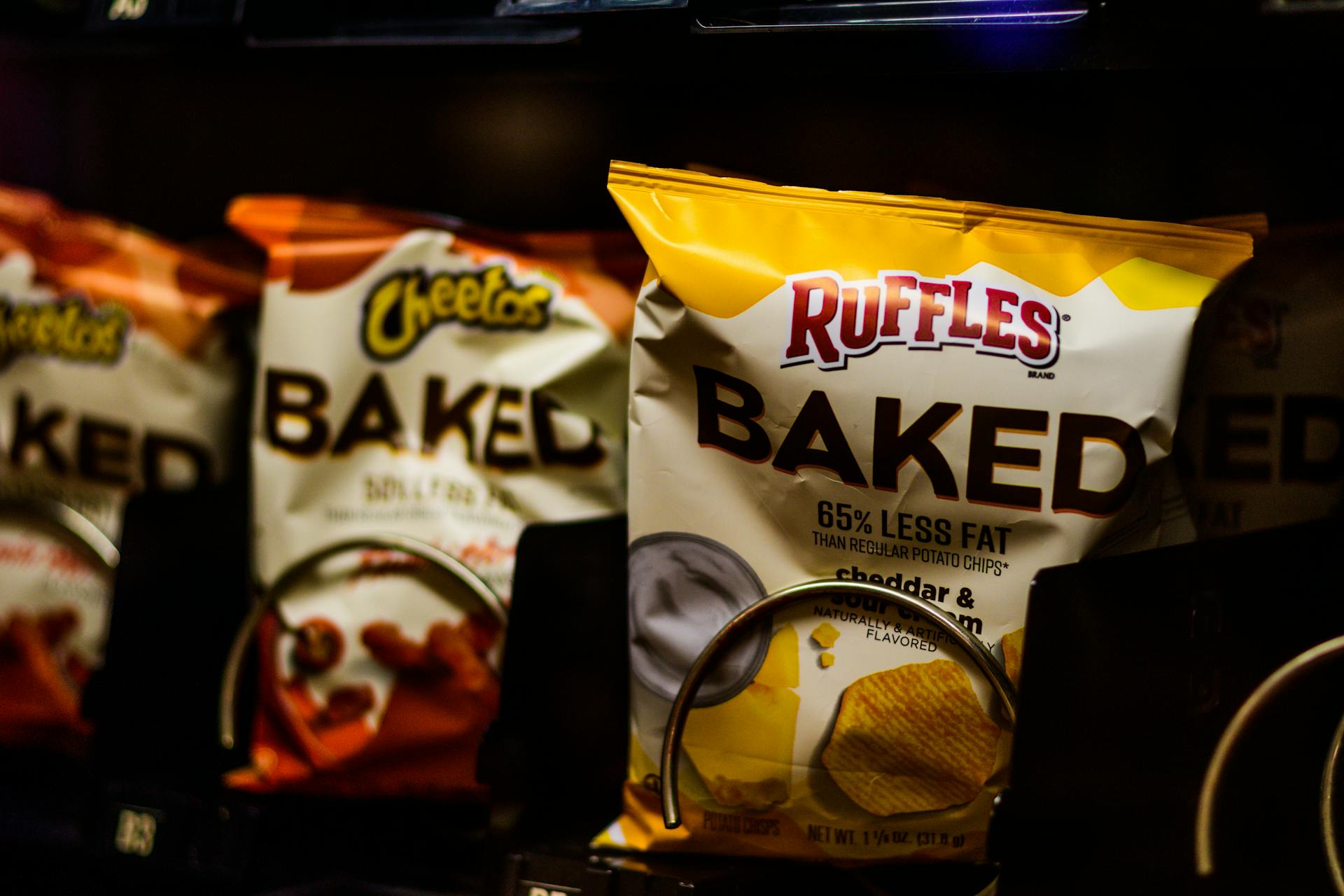
The structure of a cling film wrapping machine is made up of stainless steel to make it durable and long lasting.
The machine is mainly consisting of a heating system, stretching system, conveying system, induction conveying system, sealing system, and some controllers.
The initial power supply is given to the machine through a power supply unit, which activates all the accessories.
Controlling knobs are present to control parameters like temperature, pressure, conveying speed, reset box, roller speed, and release door time.
Constant temperature heating knobs, quick release door knob, film roller positioning knob, and quick release knob are all present to maintain the machine's process.
A feeding bracket or platform is located at the inlet, where the product is fed into the system.
The operation of the conveying system starts as the product is placed on the feeding platform.
An induction conveying system is used to enter the product automatically into the wrapping platform, and a release conveying system sends the wrapped product back after process completion.
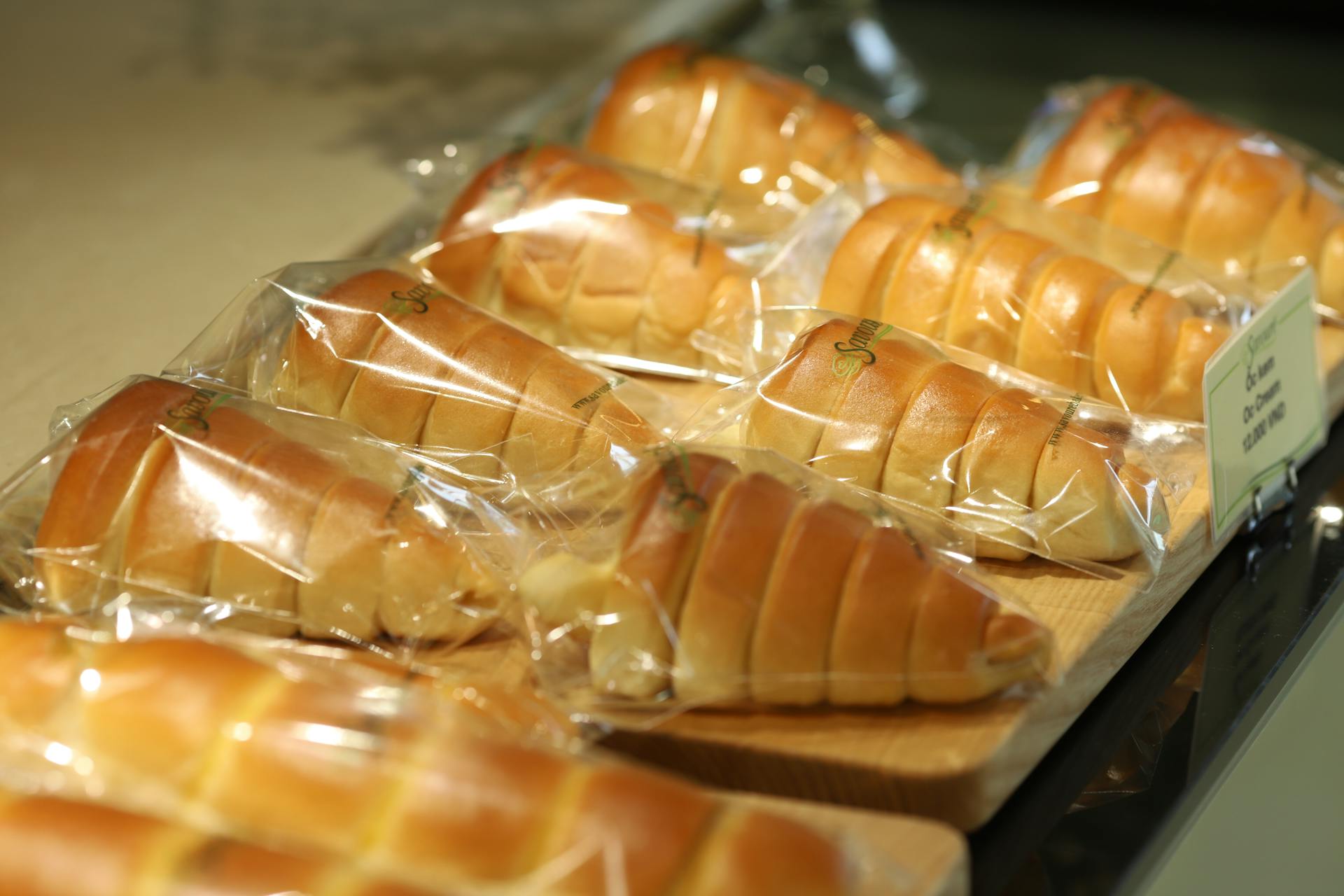
The main unit of the cling film wrapping machine is where the wrapping is done, using a platform that rolls the film around the product and then automatically cuts the film with perfection.
A touchscreen is used to monitor all the activities performed by the machine and to control its functions.
Benefits and Advantages
A cling film wrapping machine is highly efficient in its process, maintaining product life for a longer period.
It can be used for the packaging of multiple shapes and sizes, making it a versatile option.
The machine provides hygienic, sealed, dustproof, and clean packaging of products that increases their life.
The film packaging done by using a cling film wrapping machine resists the entrance of moisture and prevents contamination.
Defect-free packaging is carried out by a cling film wrapping machine.
It reduces film wrinkles to a distinct level and increases the transparency of a product.
Using a cling film wrapping machine makes the product more attractive to customers and reduces the cost created by commonly used plastic wraps.
Replacing the wrap plastic is a simple process with a cling film wrapping machine.
This reduces long changeover times and makes the operation more efficient.
The operation of a cling film wrapping machine is user-friendly, allowing the operator to easily get used to it.
In a short duration, the operator can be fully trained on the machine.
A cling film wrapping machine is ideally used to wrap food and eatables, increasing their life when wrapped with cling film material.
Comparison and Differences
A cling film wrapping machine is a simple type of wrapping machine made up of few important components, including a main frame, film sealing system, heating system, conveying system, and other controlling equipment.
The design of a cling film wrapping machine is made up of stainless steel to prevent rust and increase its life.
A vacuum packaging machine, on the other hand, is made up of SS material and has a simple designed structure, making it easy for operators to handle.
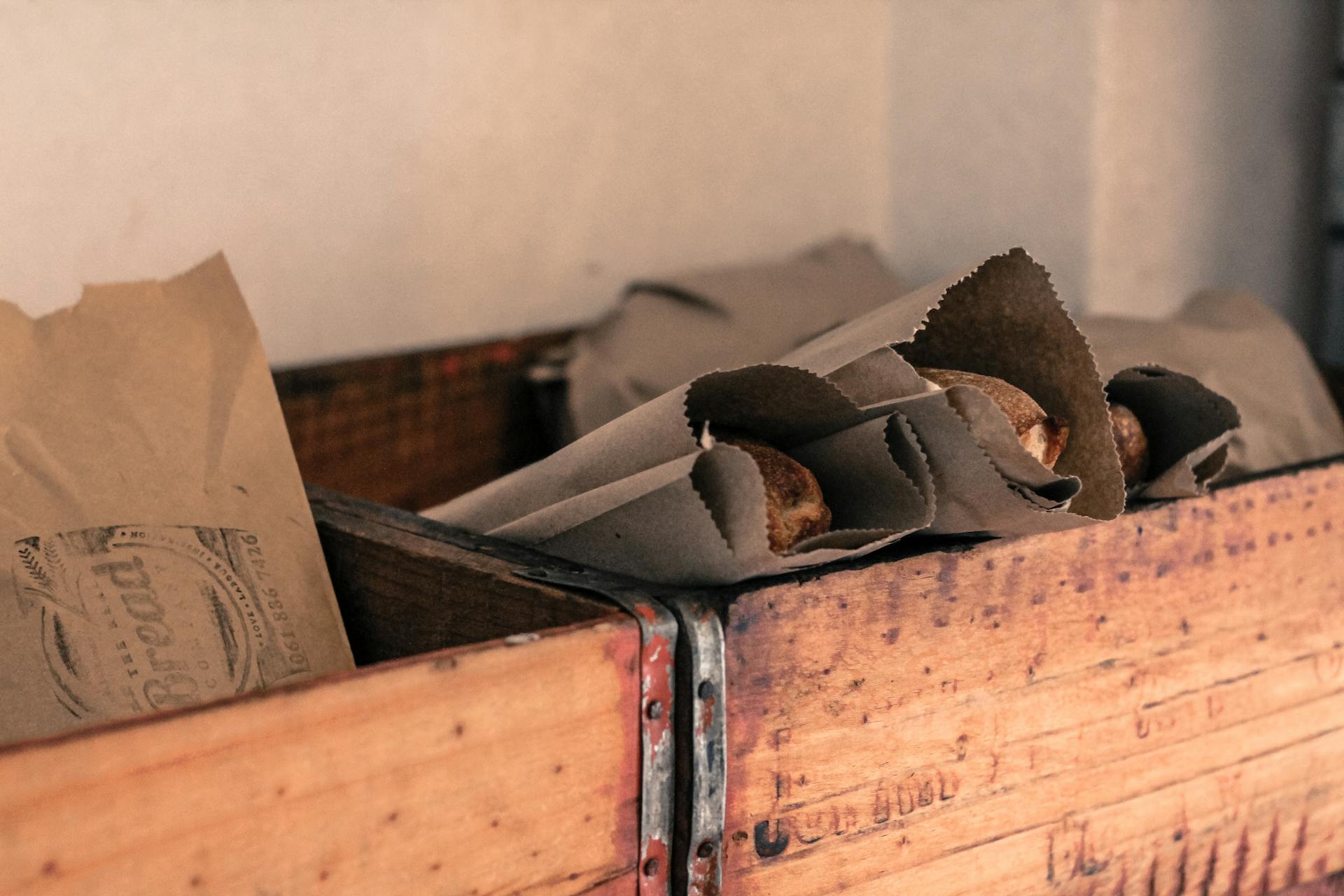
Both single and double chamber vacuum packaging machines have the same basic components, including a vacuum pump, vacuum room, sealer frame, and main frame.
A manual, semi-automatic, and automatic cling film wrapping machine holds the same sealing technique as the product gets wrapped completely within the system.
The end product after getting wrapped is kept on a sealing plate where the product edges are sealed.
Vacuum packaging machines remove atmospheric oxygen from the product through a vacuum pump and then seal the edges.
Cling film wrapping machines are highly versatile and can use a number of packaging materials, including PVC, PET, PP, PR, PVDC, HPDE, and LDPE.
Vacuum packaging machines, on the other hand, ideally use plastic aluminum composite film or plastic composite films for packaging.
Vacuum packaging machines are mostly used for packaging food, electronics parts, cosmetics, medical instruments, and hardware equipment.
The products packaged in vacuum machines are used because oxygen is taken out to increase product life and make it easily transferable from one place to another.
You might enjoy: Vertical Form Fill Sealing Machine
Maintenance and Troubleshooting
Regular maintenance of your saran wrap machine is crucial to ensure it operates efficiently and effectively. Regularly measure the machine's dimensions to ensure there's enough space for proper operation and access for maintenance and repairs.
Machine dimensions should be measured regularly to ensure there is enough space for proper operation and access for maintenance and repairs. Regular cleaning of the machine to avoid any blockage and lubrication of moving parts to reduce friction and wear.
Regularly inspect the machine's operating speed to ensure it's consistent with the setting and also the need of the production line. Monitor the film's diameter to avoid running out of the film during production.
To help you stay on top of maintenance, here's a quick checklist:
- Measure machine dimensions regularly
- Clean the machine regularly to avoid blockages
- Lubricate moving parts to reduce friction and wear
- Inspect operating speed and film diameter regularly
Common Faults
Tears in cling film can cost productivity, safety, and efficiency of a machine, indicating compromised product safety and stability.
Improper load containment is another common issue, causing problems with material not being properly wrapped and resulting in production and material loss.
Selecting the wrong size of film for wrapping can lead to quality, presentation, and material loss issues.
The size of film should be matched to the product length and installed in the machine, and operator training is crucial in this regard.
Wrong thickness of film selection can cause damage to products and consistent tearing, resulting in material and money wastage.
Specification and Maintenance
Regular machine dimension measurements are crucial to ensure there's enough space for proper operation and access for maintenance and repairs.
Machine dimensions should be measured regularly to ensure there's enough space for proper operation and access for maintenance and repairs.
Regular cleaning of the machine to avoid any blockage and lubrication of moving parts to reduce friction and wear is a must.
This helps prevent machine downtime and extends its lifespan.
Regular inspection of the machine's operating speed is essential to ensure it's consistent with the setting and also the need of the production line.
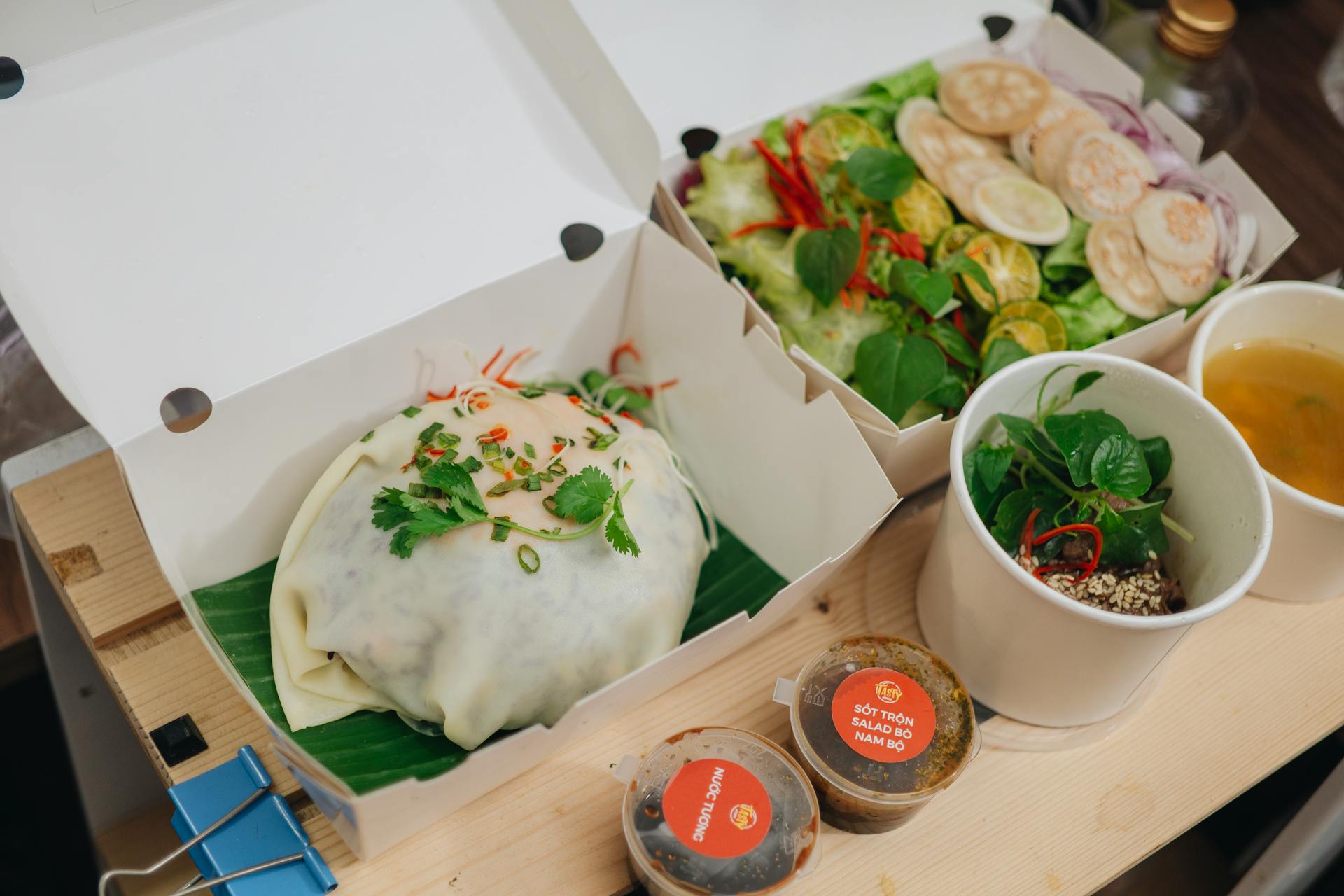
Monitor the film's diameter to avoid running out of the film during production.
Adjust the diameter according to the packaging requirements to minimize waste.
Regular calibration of the temperature sensors and controllers is necessary to ensure the appropriate temperature for sealing and cutting the film.
Check the heating elements for any damage and ensure proper functioning.
Here's a summary of the key maintenance tasks:
- Measure machine dimensions regularly
- Clean the machine regularly
- Lubricate moving parts
- Inspect operating speed
- Monitor film diameter
- Calibrate temperature sensors and controllers
- Check heating elements
Additional Equipment for a Machine
A saran wrap machine requires some additional equipment to function smoothly and efficiently.
Conveyors are often used to feed products into the system and to exit them accordingly, especially in semi-automatic and automatic machines.
Heavy products that can't be carried easily get a helping hand from these conveyors.
Laser inkjets are used to display codes, barcodes, and QR codes on the wrapped products for proper finishing and identification.
A heating plate is sometimes present in manual or semi-automatic saran wrap machines to provide a strong seal to the products.
Choosing and Selecting
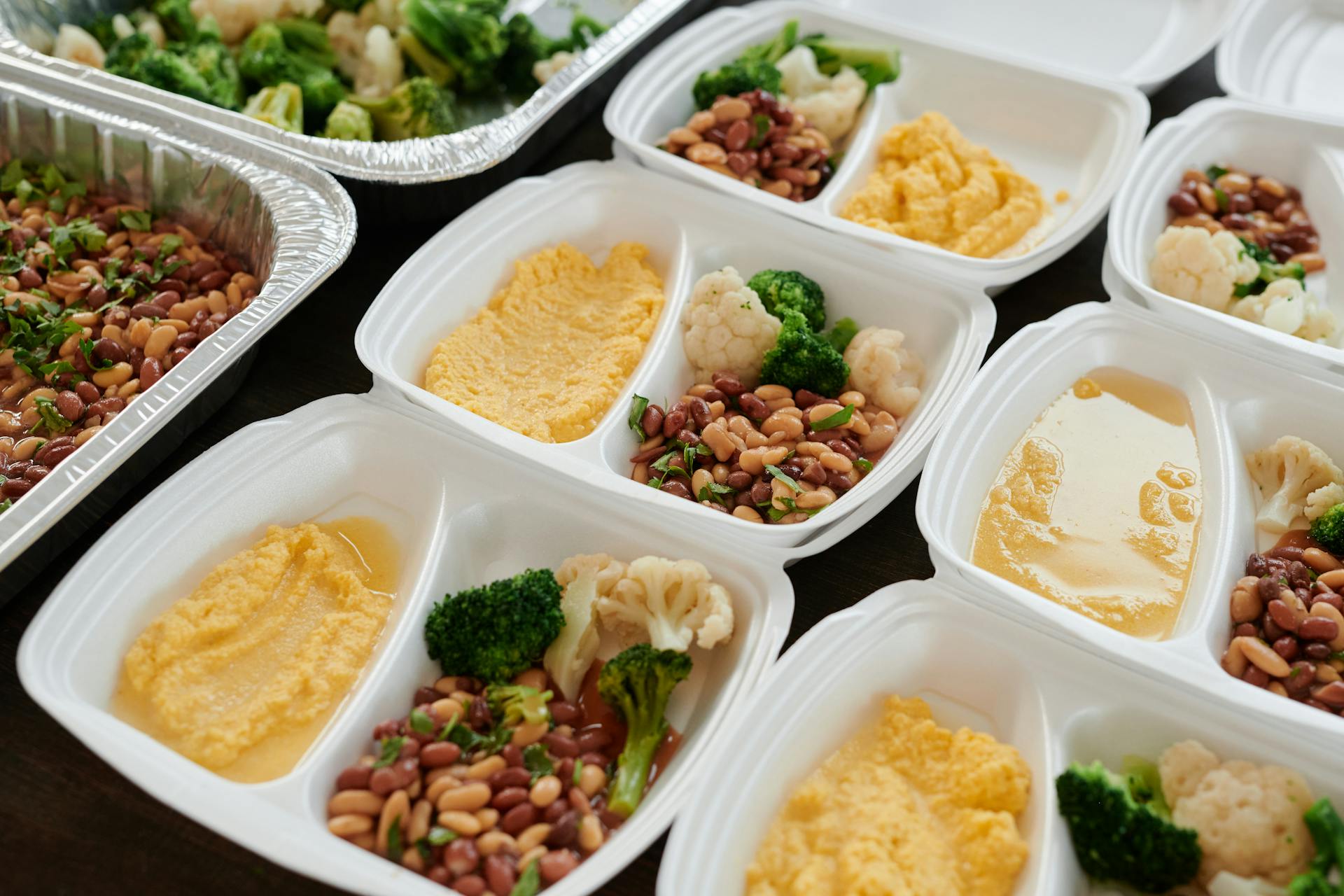
Choosing the right saran wrap machine can be a daunting task, but it's essential to get it right. There are several types of machines available, including manual, semi-automatic, and automatic.
Manual machines are the most basic and affordable option, but they can be time-consuming and labor-intensive. They require you to wrap each piece of food individually, which can be a tedious process.
Semi-automatic machines are a step up from manual machines and can wrap multiple pieces of food at once, but they still require some manual effort. They often have a rotating drum or a conveyor belt that helps to automate the wrapping process.
Automatic machines are the most advanced and efficient option, capable of wrapping large quantities of food quickly and accurately. They often come with features like adjustable speed and automatic film cutting.
When selecting a saran wrap machine, consider the size of your business and the volume of food you need to wrap. If you're a small business, a manual or semi-automatic machine may be sufficient, but if you're a large business or need to wrap large quantities quickly, an automatic machine is the way to go.
Sources
- https://www.webstaurantstore.com/14277/film-and-shrink-wrap-machines.html
- https://www.handleitinc.com/products/fa-50-automatic-orbital-wrap-machine/
- https://scaledepot.com/industrial-scales/stretch-wrap-machines/
- https://www.allpackchina.com/cling-film-wrapping-machine/
- https://www.alibaba.com/showroom/cling-film-wrapping-machine.html
Featured Images: pexels.com