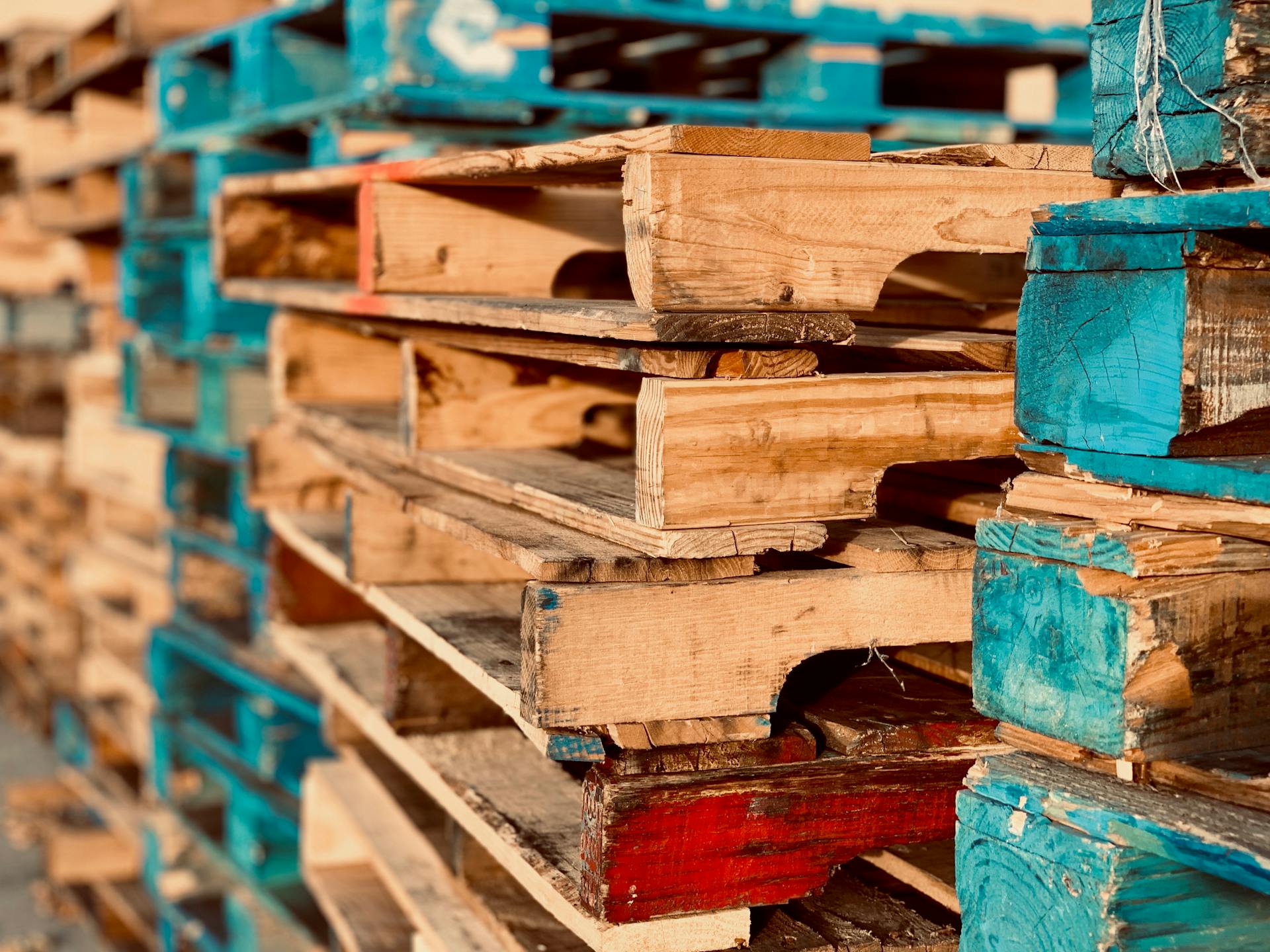
In the world of warehousing and distribution, the choice between a manual and robotic palletizer is a crucial one. Manual palletizers are still widely used in industries where the volume of goods is low, such as in small to medium-sized businesses.
Manual palletizers are relatively inexpensive to purchase and maintain, with a price tag that can be as low as $5,000. They also require minimal training for operators, making them a great option for companies with limited resources.
However, manual palletizers can be time-consuming and labor-intensive, with some operators able to load only 10-20 pallets per hour. In contrast, robotic palletizers can load up to 100 pallets per hour, making them a better option for high-volume industries.
Robotic palletizers are also more efficient and accurate, with a higher level of precision when it comes to palletizing and depalletizing. This is especially important in industries where product damage is a major concern, such as in the food and pharmaceutical sectors.
What is Palletizing?
Palletizing is a crucial task in the supply chain process where products are sorted and placed on pallets for storage or transportation. This task forms the core of the supply chain exercise.
It's an ordering task that requires products to be sorted before being palletized. Palletizing may also involve the use of a robot system to achieve the respective palletizing.
Robotic palletizing uses robots to handle the stacking of products on pallets. These robots come in various shapes and sizes, from robotic arms to more sophisticated systems.
Here are the different types of robotic palletizers:
- Robotic Arms: These are programmable robots equipped with grippers, claws, or suction cups to lift and place products onto pallets.
- Automated Robotic Systems: These systems can include robotic arms working in tandem with conveyors, sensors, and software to efficiently palletize goods without needing constant human intervention.
- Highly Flexible: Unlike conventional systems, robotic palletizers can easily adapt to different product types, shapes, and sizes with just a few adjustments in programming.
Robotic palletizers can efficiently palletize goods without needing constant human intervention. They can easily adapt to different product types, shapes, and sizes with just a few adjustments in programming.
Conventional Palletizing
Conventional palletizing is a traditional method that has been around for years and is still widely used in many industries. It involves manual labor or basic machinery to stack and organize goods onto a pallet.
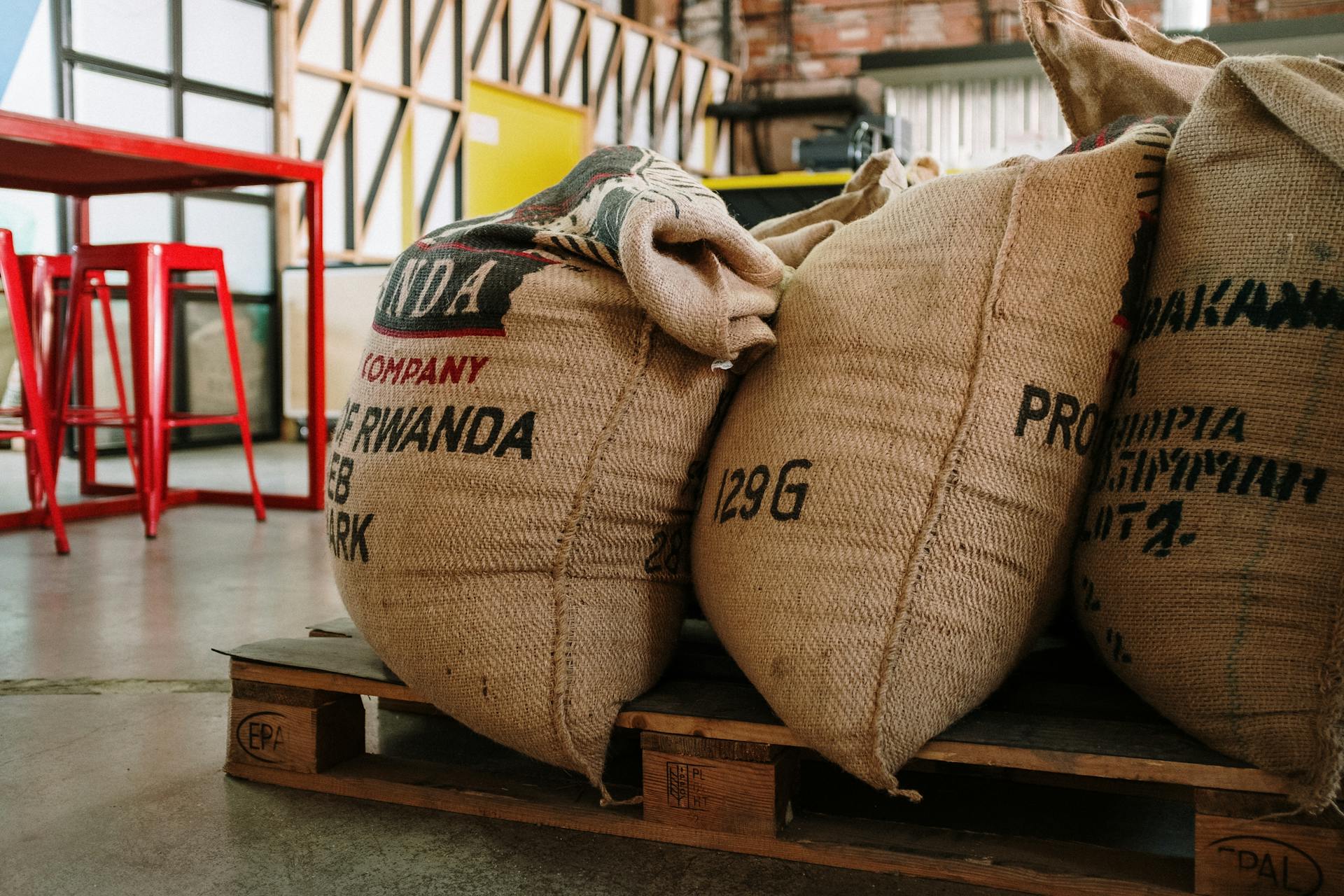
Manual labor is often used for smaller operations or lighter items, but it can be physically demanding and time-consuming. Semi-automatic machines assist workers by automating part of the process, but human intervention is still required to handle the products or control the machine.
Fully automated conventional systems use conveyors, lifts, and other equipment to handle the palletizing process, but they tend to be large, rigid systems that aren’t easily adaptable.
The cost of conventional palletizing is lower in the short term, but it can be higher in the long term due to labor costs. Here are some key differences between conventional and robotic palletizing:
Conventional palletizing can be slower, especially with manual labor, and requires significant human labor or supervision. It can also be inefficient with repetitive tasks, and manual handling increases the risk of injury.
What is Palletizing?
Palletizing is a crucial task in the supply chain exercise where products are sorted and prepared for the next step in processing. It involves placing products on pallets to store or move them from one location to another.
Palletizing can be done manually or with the help of technology, such as robotic systems. These systems can include robotic arms, automated robotic systems, and more sophisticated systems that can sort, pick, and stack items with little human input.
Robotic palletizing is a type of palletizing that uses robots to handle the stacking of products on pallets. These robots are highly flexible and can easily adapt to different product types, shapes, and sizes with just a few adjustments in programming.
Here are the different types of robotic palletizers:
- Robotic Arms: These are programmable robots equipped with grippers, claws, or suction cups to lift and place products onto pallets.
- Automated Robotic Systems: These systems can include robotic arms working in tandem with conveyors, sensors, and software to efficiently palletize goods without needing constant human intervention.
Conventional Palletizing
Conventional palletizing is a traditional method that's been around for years, and it's still widely used in many industries. It involves using manual labor or basic machinery to stack and organize goods onto a pallet.
Manual labor is often used for smaller operations or lighter items, but it can be physically demanding and time-consuming. Semi-automatic machines assist workers by automating part of the process, but human intervention is still required to handle the products or control the machine.
Fully automated conventional systems use conveyors, lifts, and other equipment to handle the palletizing process, but they tend to be large and rigid, making them less adaptable to different products.
Conventional palletizing has a lower initial cost, but higher long-term labor costs. It's also limited in its flexibility, not easily adaptable to different products.
Here are some key differences between conventional and robotic palletizing:
Conventional palletizing can be a viable option for businesses with smaller operations or lighter items, but it may not be the most efficient or cost-effective solution for larger or more complex operations.
Manual vs Robotic Palletizer
Manual palletizing is a traditional method that involves manual labor or basic machinery to stack and organize goods onto a pallet. It's a time-consuming process that can be physically demanding.
Robotic palletizing, on the other hand, uses automated systems to stack and arrange products with precision. Robots can work at all times, boosting productivity by several folds.
A fresh viewpoint: Palletizing for Bags
Here are some key differences between manual and robotic palletizing:
- Speed: Robots are usually faster and more accurate in their operations.
- Accuracy: Robots minimize the possibility of mistakes occurring within the stacks.
- Flexibility: Manual systems have more flexibility in case of a change in the kind of product and pallets.
- Automation: Robots can repeat similar exercises many times with precision, easing the workload.
- Efficiency: Robots can work at all times, boosting productivity by several folds.
- Cost: While robotic systems may be expensive to install, they can reduce labor costs and increase effectiveness in the long run.
In terms of efficiency, robotic palletizing clearly has the upper hand.
Conventional vs
Conventional palletizing is a traditional method that relies on manual labor or machinery to stack products onto pallets. It has a lower initial cost, but higher long-term labor costs.
One of the main advantages of conventional palletizing is its flexibility, but it's limited and not easily adaptable to different products. Conventional palletizing is also slower, especially with manual labor, and requires significant human involvement.
Here's a comparison of conventional and robotic palletizing:
Conventional palletizing can be efficient in certain situations, such as when handling a small number of products or in a well-organized warehouse with minimal space constraints. However, it's essential to consider the long-term labor costs and potential risks of injury associated with manual handling.
Comparing Conventional and
Conventional palletizing has been around for years and is still widely used in many industries. It involves manual labor or basic machinery to stack and organize goods onto a pallet. Workers physically pick up items and place them on pallets, making it a physically demanding and time-consuming process.
Conventional palletizing can be inefficient with repetitive tasks, and manual handling increases the risk of injury. The process requires regular maintenance of machines and higher risk of human error. However, it has a lower initial cost, but higher long-term labor costs.
Robotic palletizing, on the other hand, is a more advanced technology that tends to increase efficiency by replacing repetitive activities with tools and machinery. It's more efficient in terms of speed and accuracy, hence increasing productivity while achieving uniformity.
Here's a comparison of the two methods:
Robotic palletizing systems have developed in the 1980s and 1990s, offering more specialized capabilities, such as loading delicate or flexible products. Today, packaging facilities utilize either conventional or robotic palletizing systems depending on their specific needs.
Advantages of
Robotic palletizing is a game-changer for businesses looking to boost efficiency. With robotic palletizing, tasks take less time and results are more standardized.
One of the biggest advantages of robotic palletizing is its ability to reduce labor costs. This is because robots can work long hours without breaks, allowing for faster completion of tasks.
Robotic palletizing also enhances safety by eliminating the risk of worker injuries. This is because robots take over the dangerous and tedious tasks, freeing up humans from harm's way.
Robots are programmed to work at a uniform speed, making them more accurate than manual labor. This means fewer errors and a more consistent outcome.
Robotic palletizing systems are designed to be user-friendly, with installation taking less than 5-10 minutes. This makes it easy to get started and see results quickly.
Here are some key benefits of robotic palletizing:
Overall, robotic palletizing offers a range of advantages that make it an attractive option for businesses looking to improve efficiency and reduce costs.
Risks and Challenges
Manual palletizing comes with several safety concerns, including accidents and injuries from slips, trips, and falls, especially in cluttered or obstructed environments.
Accidents and injuries can also occur due to strains and sprains from handling heavy or awkward items.
Manual palletizing is a repetitive job that can lead to fatigue and human error, causing mistakes and incidents.
Fatigue can cause workers to make mistakes and compromise safety measures, leading to malaise and decreased productivity.
Repetitive movements, such as bending, lifting, and twisting, can strain muscles and lead to chronic injuries.
These health risks can result in additional healthcare costs and increased workforce absence for small companies.
The labor cost of manual palletizing can become a financial burden, especially with rising inflation and large-scale operations.
Physical burnout from manual palletizing can lead to decreased productivity and frequent errors over time.
Manual palletizing is not error-free, and humans can make mistakes due to lack of attention or other reasons.
These malpractices can damage products during storage or transportation, affecting the overall quality of the palletized products.
Robotics and Automation
Robotics and automation have revolutionized the palletizing industry, offering specialized capabilities that conventional palletizers couldn't match. By the 1980s and 1990s, robotic palletizing systems had developed, enabling precise loading of delicate or flexible products such as bags.
These robotic systems have greatly increased efficiency in packaging facilities, allowing for faster and more accurate palletizing. In the 1970s, inline palletizing emerged, further increasing performance demands on palletizers.
Today, robotic palletizing systems coexist with conventional palletizers, each suited to specific product needs. The choice between the two ultimately depends on the facility's requirements.
Evaluating Small Footprint Automation
NOVA Automation's mobile palletizing cell, the MPC-80 robotic palletizer, is a great example of small footprint automation equipment. It's ready to palletize on delivery and can support payloads up to 80 kg.
The MPC-80 is designed to be easy to set up, requiring only industrial power and compressed air to get started. You can even place it with a forklift, making it a great option for facilities with limited space.
One of the key benefits of small footprint automation is increased efficiency. Robot palletizing can handle repetitive tasks quickly and accurately, reducing the need for manual labor and minimizing the risk of human error.
The MPC-80 comes with NOVA's safety zone scanner, which provides interaction with operators during continuous operations. This feature helps ensure a safe working environment.
Here are some key specifications of the MPC-80:
- Ready to palletize on delivery
- No install required
- Place the palletizing cell with a forklift, add power, connect to compressed air, and you’re all set
- System includes NOVA’s safety zone scanner to provide interaction with operators during continuous operations
- Comes standard with NOVA’s advance control system and pallet builder software
- Available in 30, 50, 80 kg payload robots
- Option to palletize on both sides of the cell for increased efficiency
- Smaller, more mobile footprint than a conventional palletizer
To get the most out of small footprint automation, it's essential to maintain production level rates above six cases per minute. This will ensure that your operations run smoothly and efficiently.
Palletizer Technology Evolution
The first conventional palletizer was developed in the late 1940s as an alternative to manual loading.
Conventional palletizers experienced rapid improvement between 1950 and 1970, with the development of row-forming and inline palletizing.
The demands for palletizer performance greatly increased in the 1970s, requiring automatic palletizing systems to pack products at rapid speeds.
Conventional palletizers remained useful for high-speed and repetitive loading operations, but robotic palletizing systems developed in the 1980s and 1990s offered more specialized capabilities.
Robotic palletizing systems can now load delicate or flexible products, such as bags, with relative precision.
Today, packaging facilities utilize either conventional or robotic palletizing systems depending on their specific needs.
Suggestion: Palletizer Machine
Safety and Efficiency
Robots are designed to minimize the risk of accidents, letting them work in specific safety areas and reducing the chances of worker-robot accidents.
Manual palletizing, on the other hand, poses some risks, but robotic systems can mitigate these risks with features like sensors and emergency stop functions.
Robotic palletizing systems provide consistent performances, unlike human factors, which makes them less prone to errors and operate in a more controlled manner.
Robots can work on heavy, large, or dangerous items, increasing safety levels in workplaces and reducing the risk of accidents.
Most modern robots used for operations have safety precautions such as collision detection, safety barriers, and self-stop functions to ensure the safety of equipment operators.
Enhanced Safety Features
Robotic palletizing systems have enhanced safety features that minimize the risk of accidents. These safety areas allow robots to work without posing a threat to workers.
Robots can operate in a more controlled manner, reducing the likelihood of errors. This is due to consistent performance, unlike human factors that can fluctuate.
Most modern robots used for palletizing operations have safety precautions such as collision detection and safety barriers. These features ensure the safety of equipment operators.
Robots can handle heavy, large, or hazardous items that would be a danger to workers handling shipments. This frees workers from performing these tasks, increasing safety levels in the workplace.
Comparing Efficiency
Comparing Efficiency is a crucial aspect of any production process. Robots are usually faster and more accurate in their operations.
This means they can manage more pallets in a given time, which is a significant advantage. Robots are also less prone to mistakes, especially when it comes to stacking patterns.
Manual systems, on the other hand, have more flexibility when it comes to handling different products and pallets. This flexibility can be beneficial in certain situations.
However, robots' precision and speed often make them the better choice for high-volume production. Robots can maintain accuracy even when handling complex or irregularly shaped products.
Industry Applications
In the food and beverage production industry, robotic palletizing can offer high-speed efficiency and the necessary accuracy for a large volume of products, especially considering the importance of hygiene.
Robotic systems are particularly well-suited for handling heavy parts in automotive manufacturing, providing much-needed precision in demanding palletizing systems.
E-commerce fulfillment requires solutions that can adapt to varying product types and quantities, and robotized systems can offer the flexibility and velocity necessary for such procedures.
Food and beverage production often involves high-speed palletizing, which robotic systems can efficiently handle while maintaining the required accuracy.
Explore further: Pallets Food
Technology Evolution
The technology behind palletizers has come a long way since the 1940s when the first conventional palletizer was developed as an alternative to manual loading. Conventional palletizers experienced rapid improvement between 1950 and 1970, with row-forming and inline palletizing developing during this time.
The demands for palletizer performance increased in the 1970s with the development of inline palletizing, requiring automatic palletizing systems to pack products at rapid speeds. These systems had to be organized and consistent in their packing.
Conventional palletizers remained useful for high-speed and repetitive loading operations, but robotic palletizing systems developed in the 1980s and 1990s offered more specialized capabilities. Robotic palletizing systems could load delicate or flexible products like bags with relative precision.
Today, packaging facilities use either conventional or robotic palletizing systems depending on their specific needs, with one type not necessarily being better than the other. Different solutions are better suited for different products.
Frequently Asked Questions
What is robotic palletizing?
Robotic palletizing is a process where products are efficiently loaded onto pallets using a combination of automated systems and a palletizing robot. This technology streamlines the packaging process, ensuring accurate and rapid pallet loading.
How fast is a Cobot palletizer?
A Cobot palletizer's speed ranges from 200 to 500 cases per hour, depending on the model and application. Discover how our cobot solutions can optimize your palletizing process.
Sources
- https://novaautomation.com/uncategorized/traditional-robots-vs-collaborative-robots-for-palletizing-cases-of-product/
- https://www.afasystemsinc.com/conventional-vs-robotic-palletizing/
- https://www.warsonco-robot.com/manual-vs-robot-palletize/
- https://www.warsonco-robot.com/manual-vs-robotic-palletizer/
- https://www.aetnagroup.com/es/blog/-13
Featured Images: pexels.com