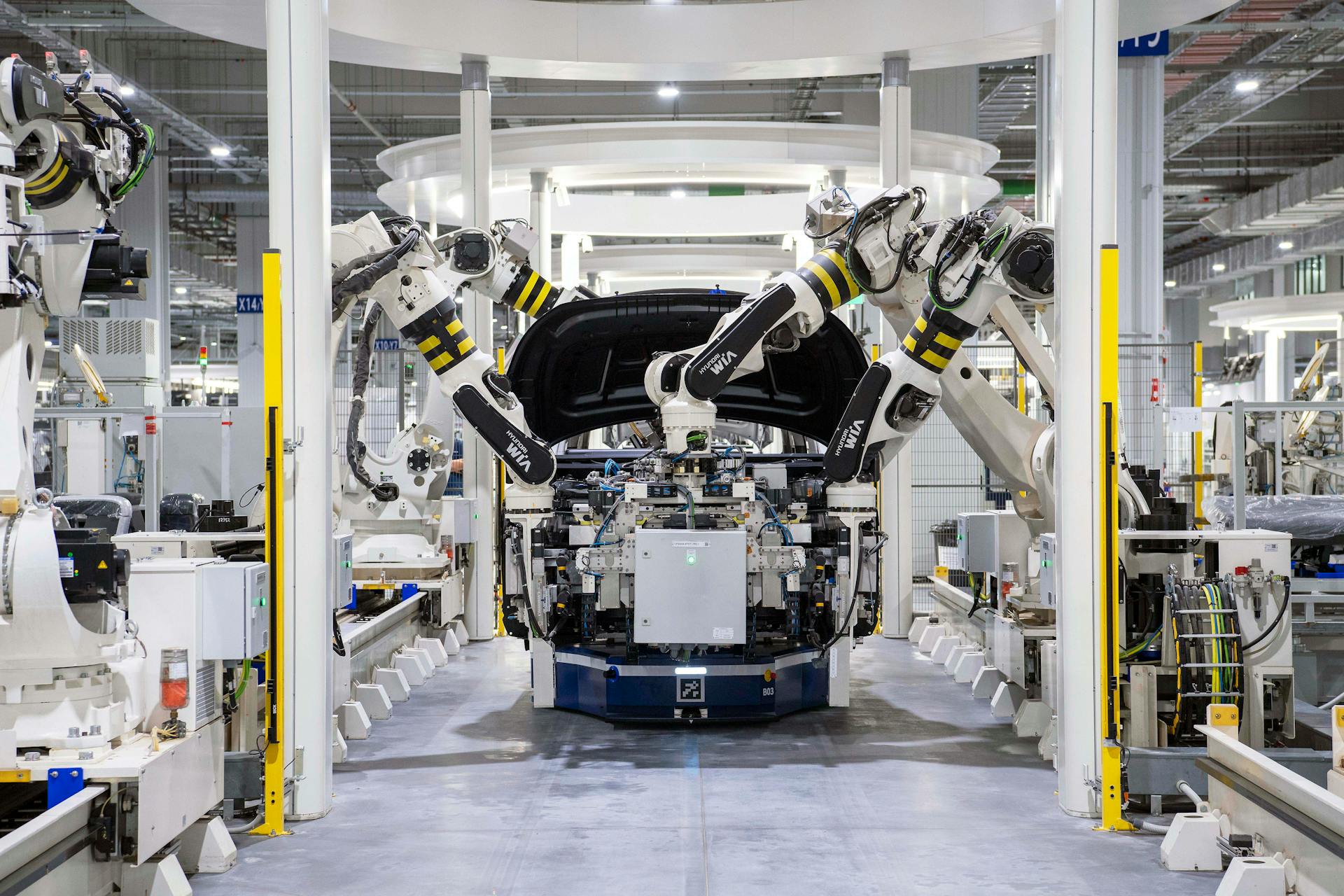
Palletizing bags with robotic precision can significantly increase efficiency and reduce labor costs.
Robotic palletizing systems can handle a wide range of bag sizes and types, from small paper bags to large industrial sacks.
These systems use computer vision and machine learning algorithms to accurately identify and orient bags for efficient stacking.
By automating the palletizing process, companies can reduce the risk of product damage and improve overall product quality.
On a similar theme: B Pallets
Types of Palletizers
Gantry type bag palletizing machines are perfect for small spaces due to their compact dimensions. They can handle both stable and difficult bags, even those that are half empty or contain products that are at the viscosity limit or aerated.
One of the strengths of gantry type bag palletizing machines is their ability to form pallets quickly, with relatively short pallet formation times. This is especially useful in high-speed production environments.
Their precision and repeatability of movements are also noteworthy, allowing for consistent and accurate palletizing.
Palletizer Systems
Palletizer Systems can be customized to meet the unique needs of each customer, incorporating features such as weight-check conveyors to reject bags that don't meet the specified weight.
A key feature of these systems is the ability to add various components, including bag settling conveyors that agitate the bags to disperse contents evenly and consistently, and bag flattening conveyors that squeeze bags flat to create uniform loads.
Some palletizer systems can palletize up to 15 bags or more per minute, making them ideal for high-volume bagging operations. These systems often include a 6-axis palletizing robot arm and mounting base, as well as automatic pallet dispensers and automated pallet wrappers.
Here are some common components found in palletizer systems:
- Weight-check conveyors
- Bag settling conveyors
- Bag flattening conveyors
- Leak detection stations
- Bag kickers
- Stainless steel parts and chain conveyors
- Stretch wrappers
- Poly sheet dispensers
- Hold downs
Single or Dual Stack Robotic Palletizers
Single or Dual Stack Robotic Palletizers are ideal for bagging lines filling 12 bags per minute or less. They use a Fanuc or Kawasaki palletizing robot in a single or dual stacking configuration.
A safety fence surrounds the end of the bagging line, as well as the robot, to ensure the robot is not active in the zone where a forklift operator retrieves a filled pallet. This setup still requires an operator to load empty pallets into the bag stack zone for the palletizing robot arm to stack bags upon.
These systems are relatively simple and can be easily integrated into existing bagging lines. They're perfect for smaller-scale operations or those just starting out with palletizing.
Here are some key features of Single or Dual Stack Robotic Palletizers:
- Recommended for bagging lines filling 12 bags per minute or less
- Use a Fanuc or Kawasaki palletizing robot
- Single or dual stacking configuration
- Operator required to load empty pallets
- Safety fences for robot and bagging line protection
Four-Column System
The four-column bag palletizing system is a robust and versatile machine that allows palletizing even with bags that are not completely full.
It can handle bags of various shapes and types, including valve, open-mouth, paper, raffia, and PE bags, regardless of their degree of filling.
Good stability and geometry to the palletized load is ensured, making it a reliable option for many applications.
This system is suitable for palletizing bags that contain different types of materials.
High-Level Machine
High-Level Bag Palletizing Machines are particularly suitable for high-speeds with stable bags that have well-defined geometry. These machines can achieve high production capacities by performing several operations simultaneously.
Automatic high-level bag palletizing machines are designed to handle high-speed production, making them ideal for companies that need to package large quantities of stable bags quickly.
These machines can operate at speeds of up to 1400 bags per hour, as seen in the Bag in Box Palletizer example. This is a significant increase in productivity compared to manual palletizing methods.
High-level bag palletizing machines are also designed to handle a wide range of bag sizes and weights, making them a versatile solution for companies with varying packaging needs.
Some key features of high-level bag palletizing machines include:
By investing in a high-level bag palletizing machine, companies can significantly increase their productivity and efficiency, making them a valuable addition to any packaging operation.
Palletizer Features
Flexibility is crucial in a palletizer, as it should be able to handle a wide range of bag sizes and weights, up to 50kg or more. This includes different types of bags like paper, plastic, or woven materials.
A good palletizer should be able to stack bags uniformly on the pallet, ensuring stability during transportation. This is essential for products to arrive at their destination in perfect condition.
To ensure ease of use, operators should be able to easily program and operate the system without extensive technical knowledge or training. This feature is a must-have for any business looking to streamline their operations.
Here are the key features to look for in a palletizer:
- Flexibility: Handles bags up to 50kg or more and different types of bags
- Accuracy: Stacks bags uniformly on the pallet
- Speed: Palletizes bags quickly without sacrificing accuracy
- Ease of use: Easy to program and operate
- Safety features: Emergency stop buttons and sensors for obstruction detection
- Reliability: Minimal downtime and low maintenance
- Integration capabilities: Integrates with other equipment like conveyors or stretch wrappers
Key Features
When choosing a palletizer, flexibility is key. A system should be able to handle a wide range of bag sizes and weights, up to 50kg or more, and accommodate different types of bags such as paper, plastic, or woven materials.
Accuracy is crucial to ensure that products arrive at their destination in perfect condition. A palletizer should be able to stack bags uniformly on the pallet while maintaining stability during transportation.
Speed is essential in a fast-paced work environment. A palletizer should be able to palletize bags quickly without sacrificing accuracy.
Ease of use is vital for operators who should be able to easily program and operate the system without extensive technical knowledge or training.
Safety features are a must-have in a robotic system. Look for features such as emergency stop buttons and sensors that detect any obstructions in the workspace.
A reliable palletizer should have minimal downtime and require little maintenance to ensure maximum productivity.
Here are the key features to look for in a palletizer:
- Flexibility: up to 50kg or more and various bag types
- Accuracy: uniform stacking and stability
- Speed: fast palletizing without sacrificing accuracy
- Ease of use: easy programming and operation
- Safety features: emergency stop buttons and obstruction sensors
- Reliability: minimal downtime and low maintenance
- Integration capabilities: integration with other equipment
Functional Description
In a well-designed palletizing system, the functional description is crucial in determining its efficiency and effectiveness. The solution consists of four internal transport lines, including modular and roller conveyors, as well as a vertical conveyor, for product transport.
These lines are distributed on two Okura robot palletizing cells with associated sheet and pallet magazine. The robot tool is a combined gripping and vacuum tool that can handle bags and boxes, as well as sheet loading.
The conveyor where the robot picks up the bag has a built-in tilt function, which ensures that the contents of the bag are distributed. This is a key feature in maintaining the stability and optimal placement of bags on the pallet.
Subsequently, the pallets are transported on the same pallet track for application of top foil and pallet wrapping to protect the pallet during transport. This is a critical step in ensuring the pallet is secure and ready for shipping or storage.
The pallet gets labels affixed on all four sides as the last step before being transported to the storage facility. This adds an extra layer of organization and tracking to the palletizing process.
Here are some key features to consider in a palletizing system:
- Four internal transport lines (modular and roller conveyors, and a vertical conveyor)
- Two Okura robot palletizing cells with associated sheet and pallet magazine
- Combined gripping and vacuum tool for handling bags, boxes, and sheet loading
Images
Click the thumbnails below to view larger images of palletizers and systems in action.
Palletizers come in different forms, including semi-automatic and fully automatic models.
Semi-automatic palletizers require some manual intervention, while fully automatic models can operate independently.
You can view larger images of these palletizers and systems by clicking on the thumbnails provided.
These images showcase the various configurations and layouts of palletizers and systems.
Palletizer Solutions
PAYPER designs and manufactures high-quality, reliable equipment, including palletizing solutions, with a commitment to technological innovation.
The company offers different palletizing technologies, including conventional and robotic solutions.
Conventional palletizers, such as the PPAL palletizer, are speedy and heavy-duty, allowing for high production capacities and creating fully square pallets with high stability. They are particularly suitable for valve bags and FFS bags.
The PPAL palletizer can palletize up to 2,800 bags per hour, making it an ideal solution for high-production facilities.
Robotic palletizers, such as PAYPER's RPAL palletizer, are compact and versatile, taking up very little space and ideal for production areas with a limited footprint.
The RPAL palletizer can handle any type and size of bags, including open-mouth bags, and can be customized with different types of grippers to optimize palletizing tasks.
Here are some key features of robotic palletizers:
- Compact and versatile design
- Can handle any type and size of bags
- Customizable with different grippers
These palletizer solutions offer high-speed palletizing, accuracy, and efficiency, making them ideal for businesses looking to improve their operations.
Choosing the Right Solution
Choosing the right palletizer solution can be a daunting task, but understanding the options can help make the decision easier. There are two main categories of palletizing technologies: conventional and robotic.
PAYPER offers a range of conventional palletizers, including the PPAL palletizer, which is speedy, heavy-duty, and high-productive. This push-type palletizer can palletize 2,800 bags per hour.
The GPAL clamp palletizer is another option, handling any type of bag, but particularly suitable for open-mouth bags. It provides a stable and perfectly stacked pallet.
Robotic palletizers, like PAYPER's RPAL, are a compact and versatile option. They take up little space and can handle any type of bag, including open-mouth bags with overlapping.
Here are some key differences between the PPAL and RPAL palletizers:
Ultimately, the right palletizer solution will depend on your specific needs and production requirements.
Benefits of the New Solution
The new palletizing solution has brought a significant boost to Palsgaard's production efficiency. One of the key benefits is the ease and speed of conversion between different settings. This flexibility is a major advantage.
The new lines are equipped with palletizing robots, which have replaced traditional palletizers. This switch has given Palsgaard greater flexibility in running all products on all lines.
With the new palletizing line, operators can easily switch between different settings for bag handling and box handling. This is made possible by the line's fully automatic nature.
Here are some key benefits of the new solution:
- Easy and fast conversion
- Greater flexibility
- User-friendly operation
Quality Assurance by Concetti
Concetti's quality assurance process is a game-changer for customers.
Each customer gets to visit Concetti's Italian headquarters to test and verify the operation of the bag palletizing systems before they're shipped out.
This pre-installation, or F.A.T., ensures that the contract specifications are fully met, and the plant is assembled in its entirety in Concetti's factory.
The machines are then put into operation with the customer's bags and materials, speeding up subsequent installation and testing at the customer's factory.
Concetti remains committed to its customers throughout the bag palletizing machinery lifecycle.
The company offers a range of digital services, including a customer portal, Check app, and smart glass assistance, to provide direct support and remote assistance.
Additionally, customers can rely on local service centers with experienced technicians who can travel directly to the site upon request.
Concetti also provides an appreciated training service for customer personnel to properly operate the machines.
Here are the various services Concetti offers to its customers:
- Customer Help Care Kit for field and remote assistance
- Customer portal
- Check app
- Smart glass assistance
- Local service centers
- Training service for customer personnel
Sources
- https://www.kaufmanengsys.com/product-type/bag
- https://www.tinsleycompany.com/equipment-systems/palletizing-machines-robots/
- https://www.payper.com/en/bag-palletizing-equipment-choosing-right-solution
- https://www.concetti.com/en-us/news-and-events/1175-bag-palletizing-how-do-concetti-systems-work
- https://sealing-system.com/cases/palletizing-of-bags-and-boxes
Featured Images: pexels.com