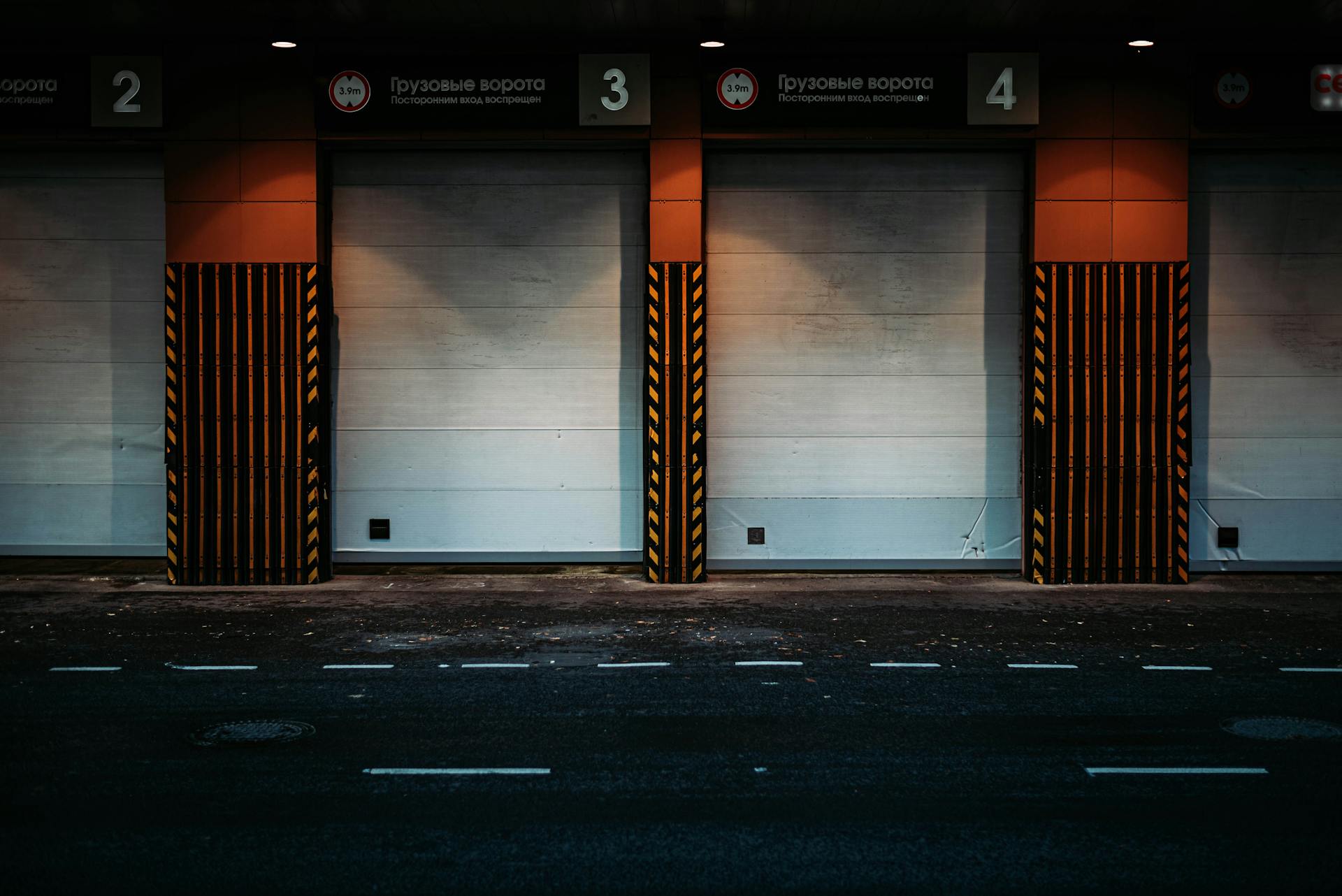
A well-designed loading dock can make a huge difference in your warehouse's efficiency and productivity. A standard loading dock typically consists of a receiving area, a loading area, and a shipping area.
The receiving area is usually located on the opposite side of the dock from the loading area, and it's where incoming shipments are unloaded and inspected. This area should be equipped with a dock leveler, which allows trucks to drive up to the dock and unload their cargo at the same level as the warehouse floor.
The loading area is where products are loaded onto trucks, and it's usually equipped with a dock leveler and a loading dock door. The size of the loading area will depend on the size of the trucks that will be using the dock, as well as the type of products being loaded.
For more insights, see: Loading Dock Warehouse
Truck and Container Specifications
When designing a loading dock, it's essential to consider the types and dimensions of the trucks that will use it. The dimensions of trucks can vary, but it's best to use Figure 21 through Figure 26 for preliminary design.
You might like: Loading Dock Measurements
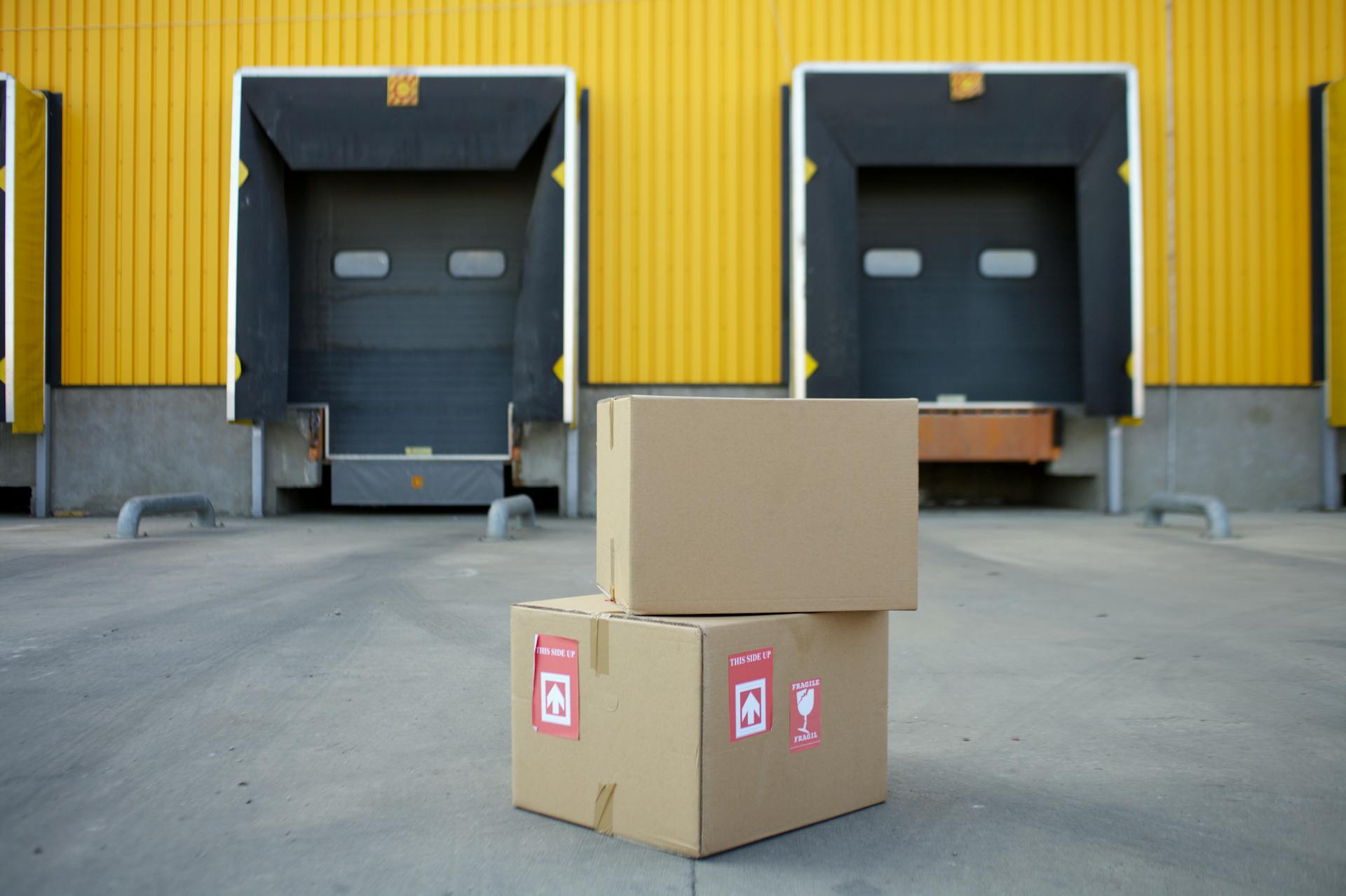
Truck bed heights can be affected by the weight of freight, causing a variance of up to 6 in. in trailer and bed heights. This is something to keep in mind when planning your dock's design.
Air suspension systems can also impact truck dimensions, so it's crucial to obtain actual truck dimensions before making final design decisions. This will help ensure a safe and efficient loading process.
Sea containers can have trailers with heights of up to 62 in., which is significantly higher than low-bed trucks. This height difference can range from 30 to 62 in.
Facilities that service sea containers may also need to accommodate low-bed trucks, so designing docks of various heights or installing equipment like hydraulic truck levelers or elevating docks is a good idea.
A different take: St Katharine Docks
Dock Design and Layout
When designing your loading dock, consider the main elements of a dock design. The apron area is crucial, as it needs to be large enough for trucks to position themselves in front of the bay.
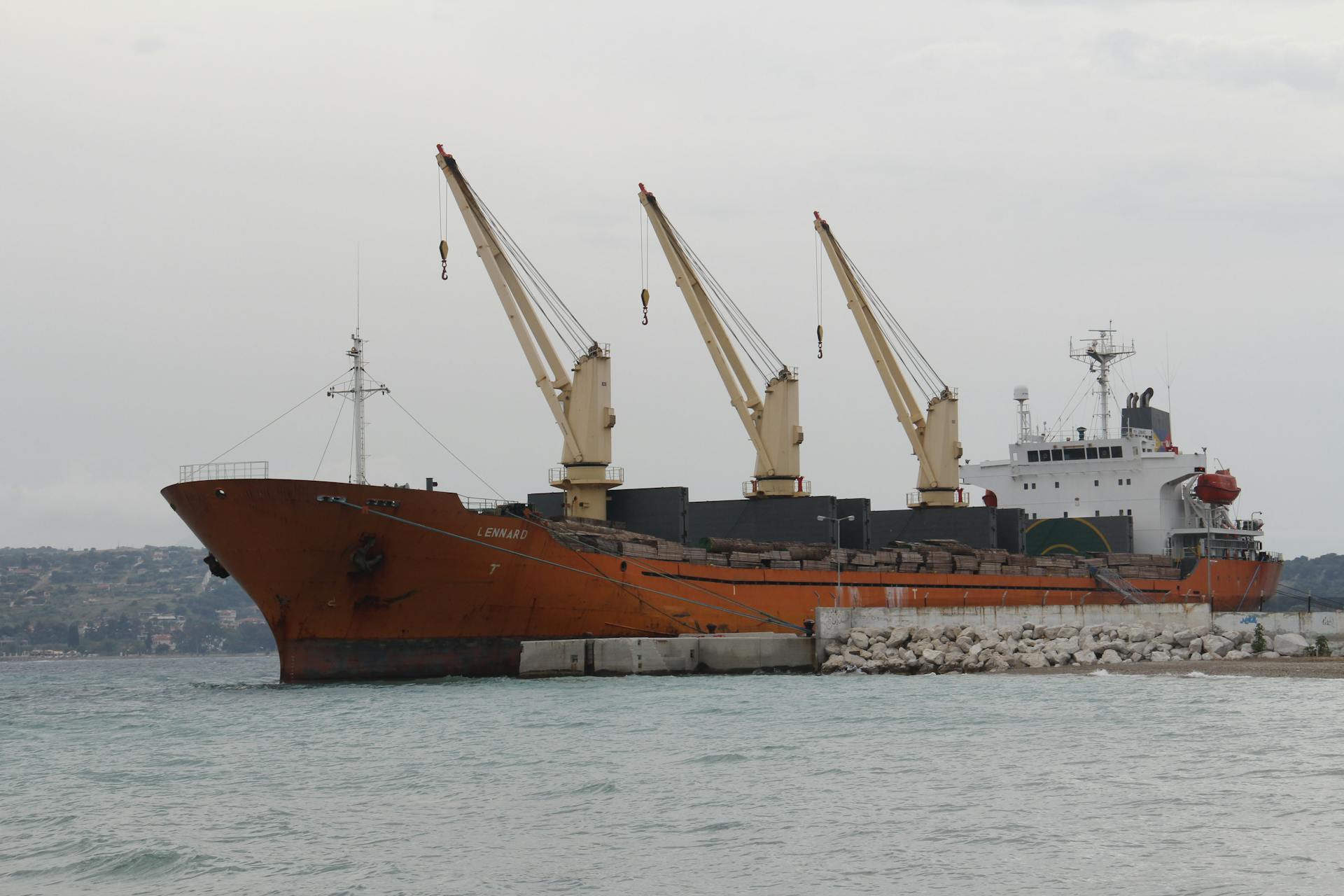
The apron area should be at least 5 to 10 feet longer than the size of the trailer, with a recommended 135 feet of apron space for a standard truck length of 65 feet.
To ensure safe and easy maneuvering, the approach angle of the dock should be taken into account, with proper bumpers installed to factor in the angle of the trucks. This will prevent damage to the building and make parking easier for drivers.
Select Doors
Selecting the right doors for your dock is a crucial decision. A dock door is required for inside/outside loading docks, and the most commonly installed doors are manually operated and are either an overhead sectional door or a roller door. Sectional doors are smoother and quieter than roller doors.
Other advantages of sectional doors include being thicker and stronger than roller doors, and they can be insulated. Common dock door dimensions are 8’0″ in width with 8 ft, 9 ft or 10 ft heights.
For your interest: Loading Dock Door Seals
To determine the door size, you should consider the type of trucks being serviced, the sealing system, and environmental concerns. A good rule of thumb is to keep doors as small as possible, usually narrower than 8 ft, in temperature-controlled docks where energy is lost through doors.
Here are some general guidelines for door sizes:
It's also important to consider the height of the door, as 8 ft high doors can accommodate many loading and unloading operations, but may not be suitable for floor-to-ceiling loading. A 9 ft high door allows for improved floor-to-ceiling loading, and a 10 ft high door services the full range of loading and unloading operations.
On a similar theme: Loading Dock Door Installation
Key Elements
Before building your loading dock, consider the main elements of a dock design. The design should take into account the space needed for trucks to maneuver and for workers to safely load and unload goods.
The driveway leading up to the dock should be designed with a specific grade in mind. It's crucial to keep the grade below 10% to prevent the top portion of the truck from impacting the wall of your building.
A depressed (declined approach) dock is a good option when level docks aren't feasible. This type of dock requires a driveway grade that's kept below 10% for safe operation.
Here's an interesting read: Concrete Loading Dock Design
Apron Space
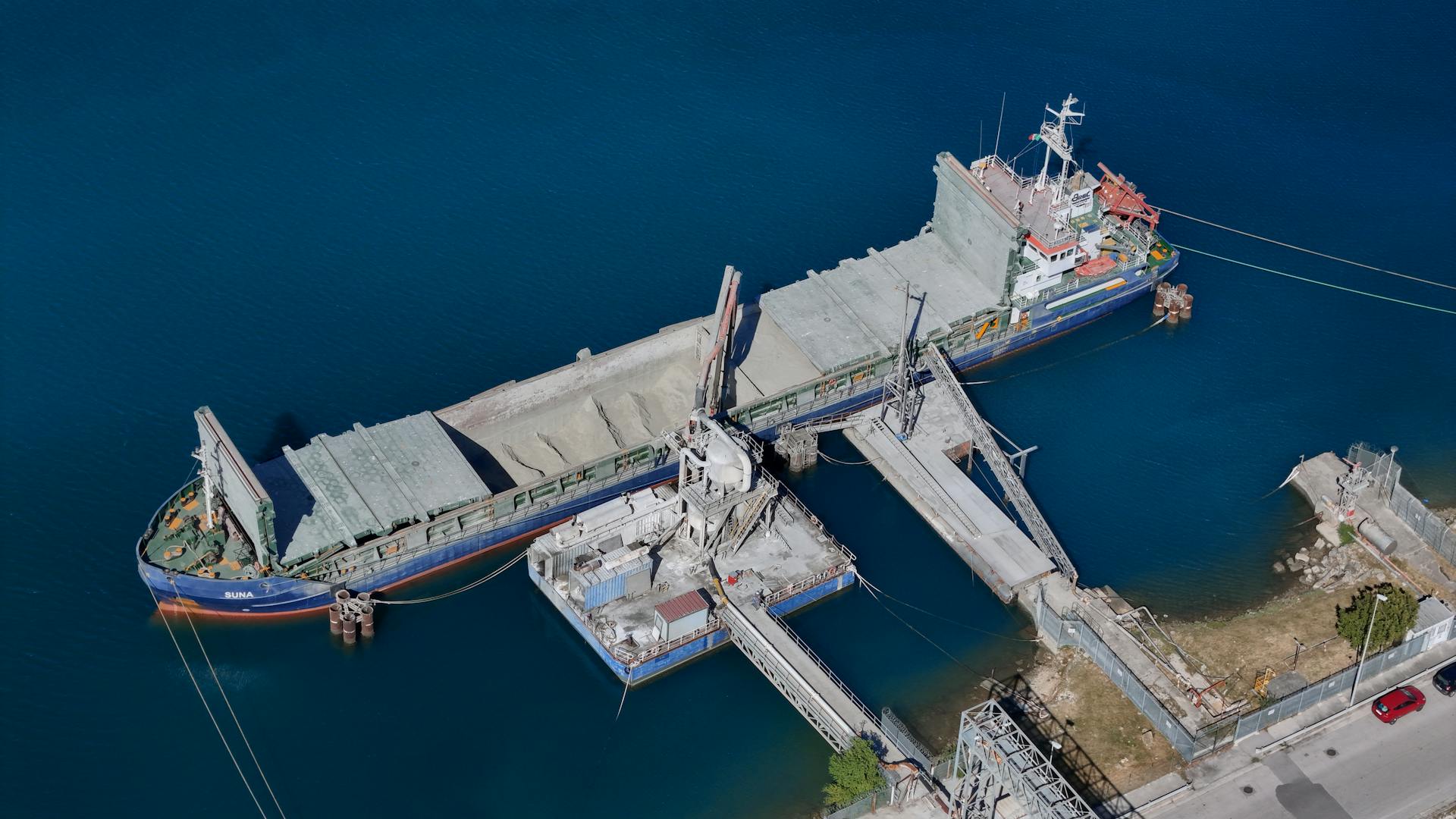
The apron space is a critical component of a loading dock design, requiring careful consideration of standard truck movements to ensure safe and efficient operations. You'll need to identify the average length of the trucks that will be using the dock.
A good rule of thumb is to provide a maneuverability distance of at least 5 to 10 feet, which is more than twice the size of the trailer. This will give drivers ample space to position their vehicles in front of the bay.
If you're working with a standard truck length of 65′, you'll need to allocate at least 135′ of apron space to accommodate safe maneuvering. This will help prevent accidents and ensure a smooth flow of operations.
If this caught your attention, see: Loading Dock Truck Ramps
Roadway Approach
When designing the roadway approach to your facility, it's essential to consider the type of traffic that will be using it. You should use angle, straight-through, or "Y" approaches, depending on the traffic volume.
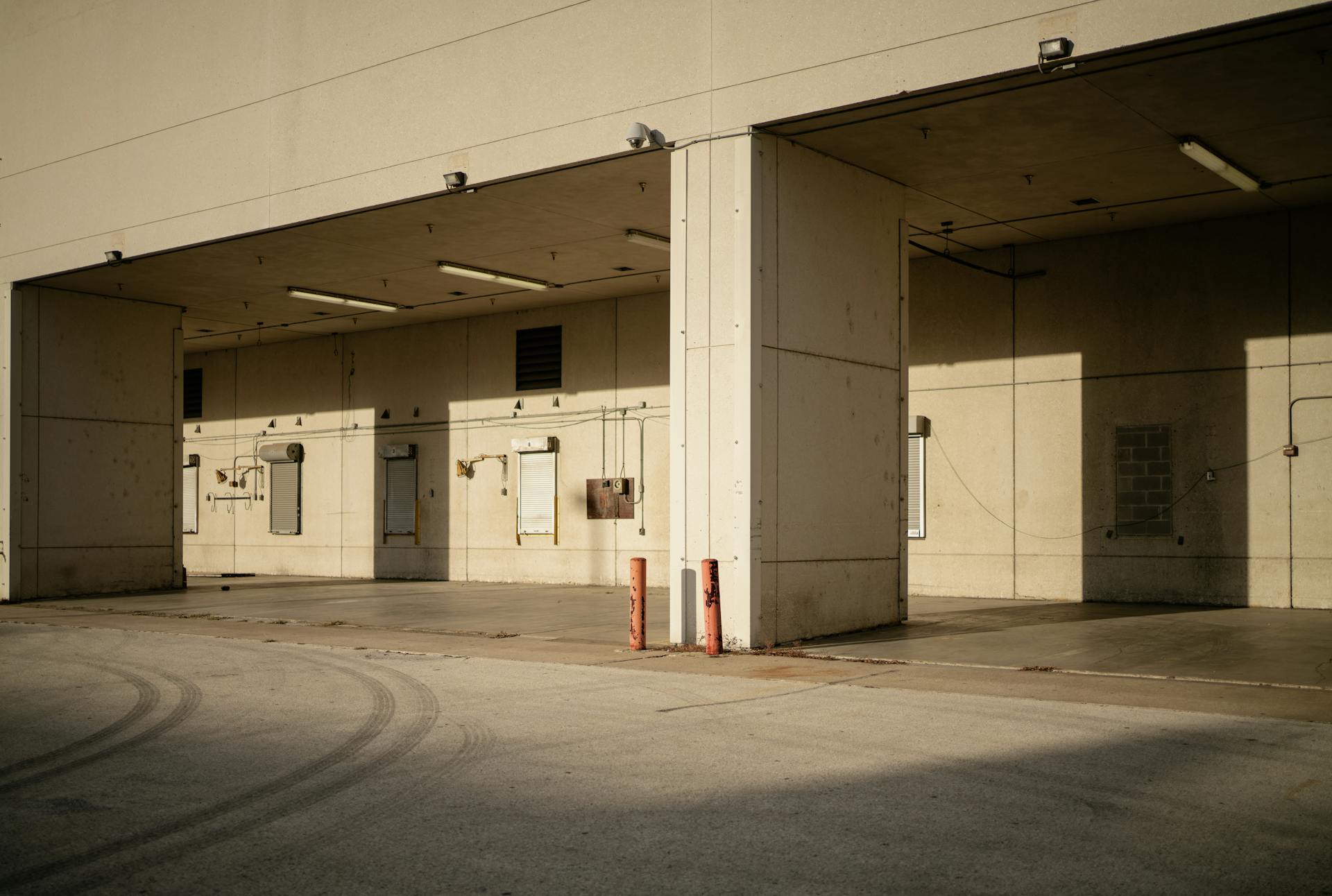
A well-designed roadway approach can make a big difference in the efficiency of your operations. Implementing safety precautions is crucial if pedestrian traffic is involved.
The type of approach you choose will depend on the volume of traffic that needs to access your facility. Angle approaches are often used for high-traffic areas, while straight-through approaches are better suited for lower-traffic areas.
In any case, it's crucial to prioritize safety, especially if pedestrians will be using the approach.
Readers also liked: Loading Dock Safety Barriers
Flush
Flush loading docks are often used by warehouses because of their affordability and efficient design. They feature a face that is flush with the building wall.
A flush design allows for easy access and maneuverability of equipment and personnel. Bumper projection may be necessary if the wall projects beyond the face of the dock.
Dock Construction
The construction process for a loading dock is a crucial step in creating a safe and efficient facility. Excavation and foundation elements come first, requiring the site to be leveled and the foundation laid.

Preparing the site and laying the foundation are essential steps in the construction process. You'll need to install pavement surfaces and ensure proper drainage before completing the construction process.
Building the actual dock platform, including supports and bumpers, is a key part of the construction process. This should be done after the foundation is laid and before constructing the roadway approach and apron space.
Set Bay Widths
Setting the right width for your loading bays is crucial to ensure efficient truck traffic flow. A minimum of 12 ft wide bays is recommended to accommodate trailers that are 8’0″ to 8’6″ wide.
Designing 14 ft wide bays can reduce congestion and provide extra space for trailers to back squarely to the dock. This is especially important if swinging trailer doors will be opening or closing at the dock, which requires a center distance of at least 14 ft.
The maximum trailer size limits are 8’6″ wide x 13’6″ high, but with a special permit, a flatbed may exceed the maximum width.
Expand your knowledge: Wide Load vs Oversize Load
Construction
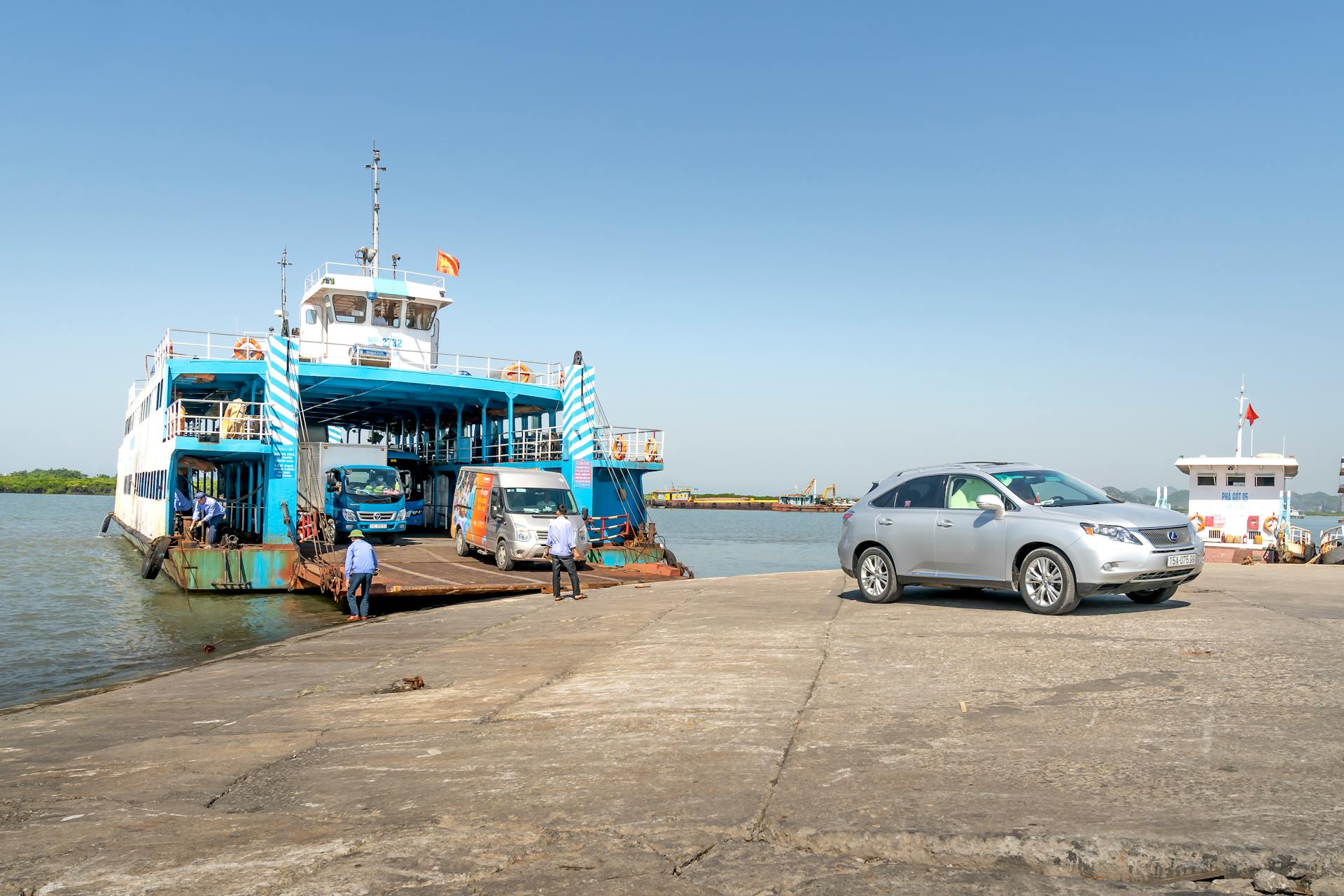
Construction is a crucial step in building a dock, and it starts with excavation and foundation elements. You'll need to prepare the site by leveling it, which is essential for a stable and even dock.
The foundation is the base of the dock, and it's essential to lay it correctly. This involves preparing the site and laying the foundation.
The next step is to build the actual dock platform, including any necessary supports and bumpers. These will help secure the dock and prevent damage.
Constructing the roadway approach and apron space is also crucial. This will allow for safe and efficient loading and unloading of goods.
Finally, you'll need to install pavement surfaces and ensure proper drainage. This will help prevent accidents and maintain the dock's integrity.
Dock Features and Safety
When designing your loading dock, safety features are a must to prevent accidents. A dock leveler can bridge any gaps between the dock and the truck, ensuring a smooth and safe loading process.
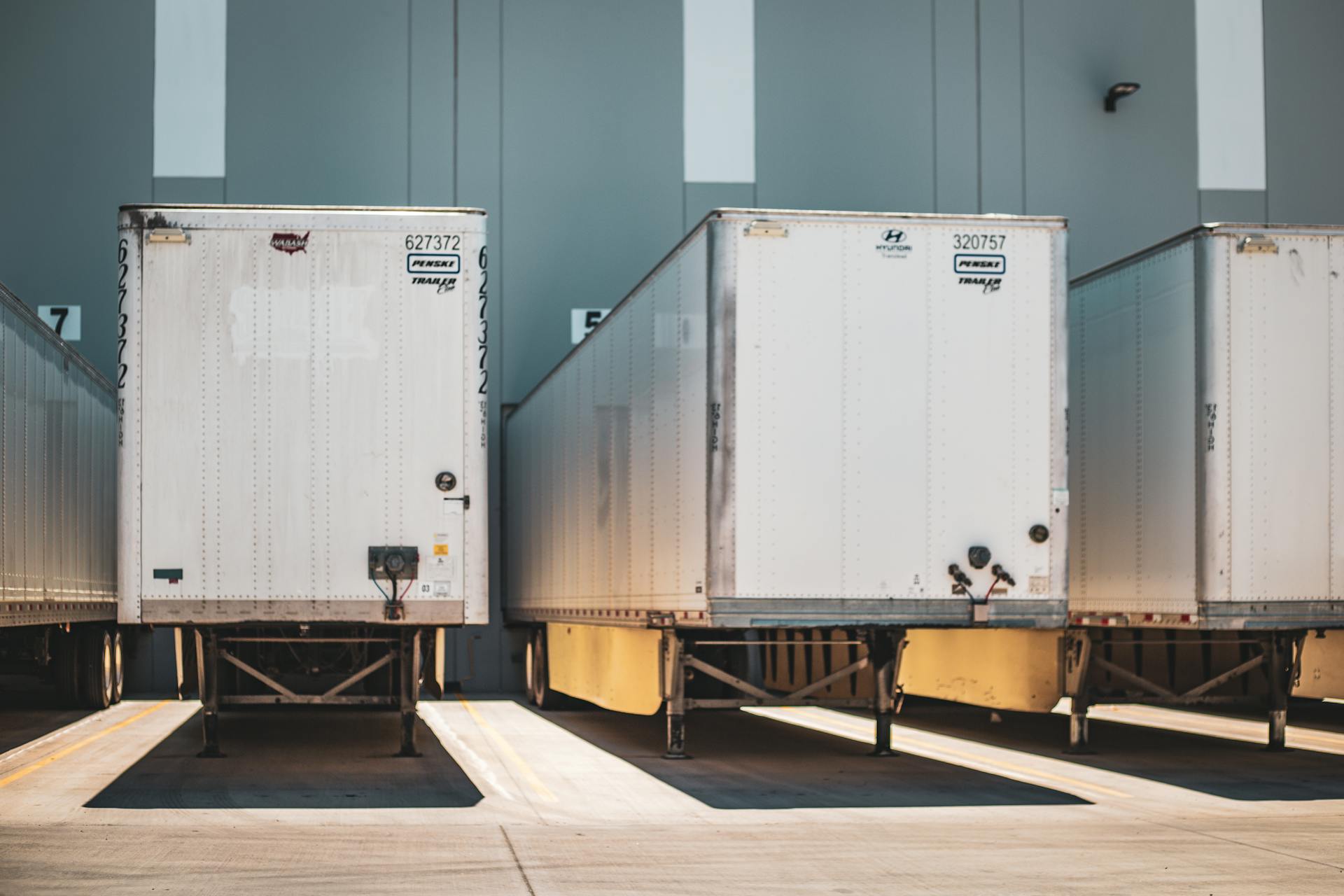
A loading dock should also have rubber or composite dock bumpers to prevent damage to your building. These bumpers can absorb up to 95% of the impact from a trailer or truck.
To enhance accessibility and worker protection, guardrails or barriers around the dock can prevent falls off the edge, particularly in open platform designs. Emergency stop buttons and safety interlocks can also prevent machinery from operating when unsafe conditions are detected.
Some essential safety features include:
- Dock levelers for bridging gaps between the dock and the truck
- Rubber or composite dock bumpers to prevent damage to your building
- Guardrails or barriers around the dock to prevent falls off the edge
- Emergency stop buttons and safety interlocks to prevent machinery from operating when unsafe conditions are detected
- Audible alarms or visual indicators to signal when a dock is in operation or when a door is about to move
Safety Features
Safety features are a must-have for any loading dock. Properly designed safety features can prevent accidents and ensure efficient operations.
Dock levelers are a crucial safety feature that bridges any gaps between the dock and the truck. This helps prevent accidents and damage to the dock and surrounding area.
Rubber or composite dock bumpers are another essential safety feature that prevents damage to your building. They absorb the impact of a trailer or truck, and a high-quality bumper can absorb up to 95% of the impact.
Take a look at this: Loading Dock Safety Lights
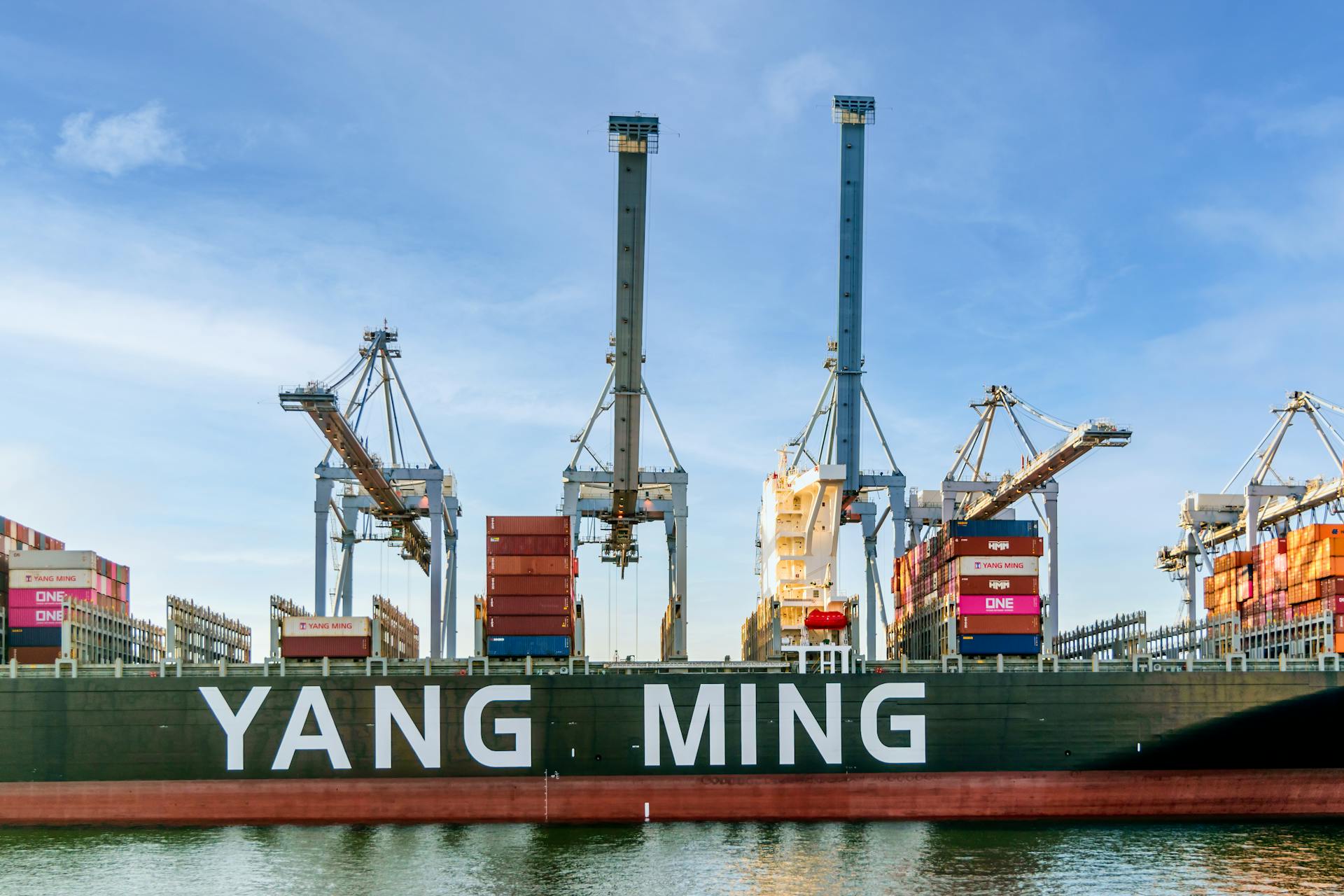
Guardrails or barriers around the dock are also vital for preventing falls off the edge, particularly in open platform designs. This is especially important in areas where workers are present.
Emergency stop buttons and safety interlocks prevent machinery from operating when unsafe conditions are detected. This helps prevent accidents and ensures a safe working environment.
Audible alarms or visual indicators signal when a dock is in operation or when a door is about to move. This helps prevent accidents and ensures that workers are aware of their surroundings.
Here are some key safety features to consider when designing your loading dock:
- Dock levelers for bridging gaps between the dock and the truck
- Rubber or composite dock bumpers to prevent damage to your building
- Guardrails or barriers around the dock to prevent falls off the edge
- Emergency stop buttons and safety interlocks to prevent machinery from operating when unsafe conditions are detected
- Audible alarms or visual indicators to signal when a dock is in operation or when a door is about to move
- Overhead protection, like canopies or awnings to provide extra weather protection
Enclosed
Enclosed docks are a great option for businesses handling sensitive or high-value products, as they provide maximum protection against the elements.
They're often used by companies that need to keep their products safe from the weather and potential damage.
In this design, trucks enter through an overhead door to load and unload goods, which can be a convenient feature for businesses with frequent deliveries.
Enclosed docks are typically the most expensive option because they require more materials, climate control, and security features.
Expand your knowledge: Loading Dock Truck Bumpers
Dock Types and Design
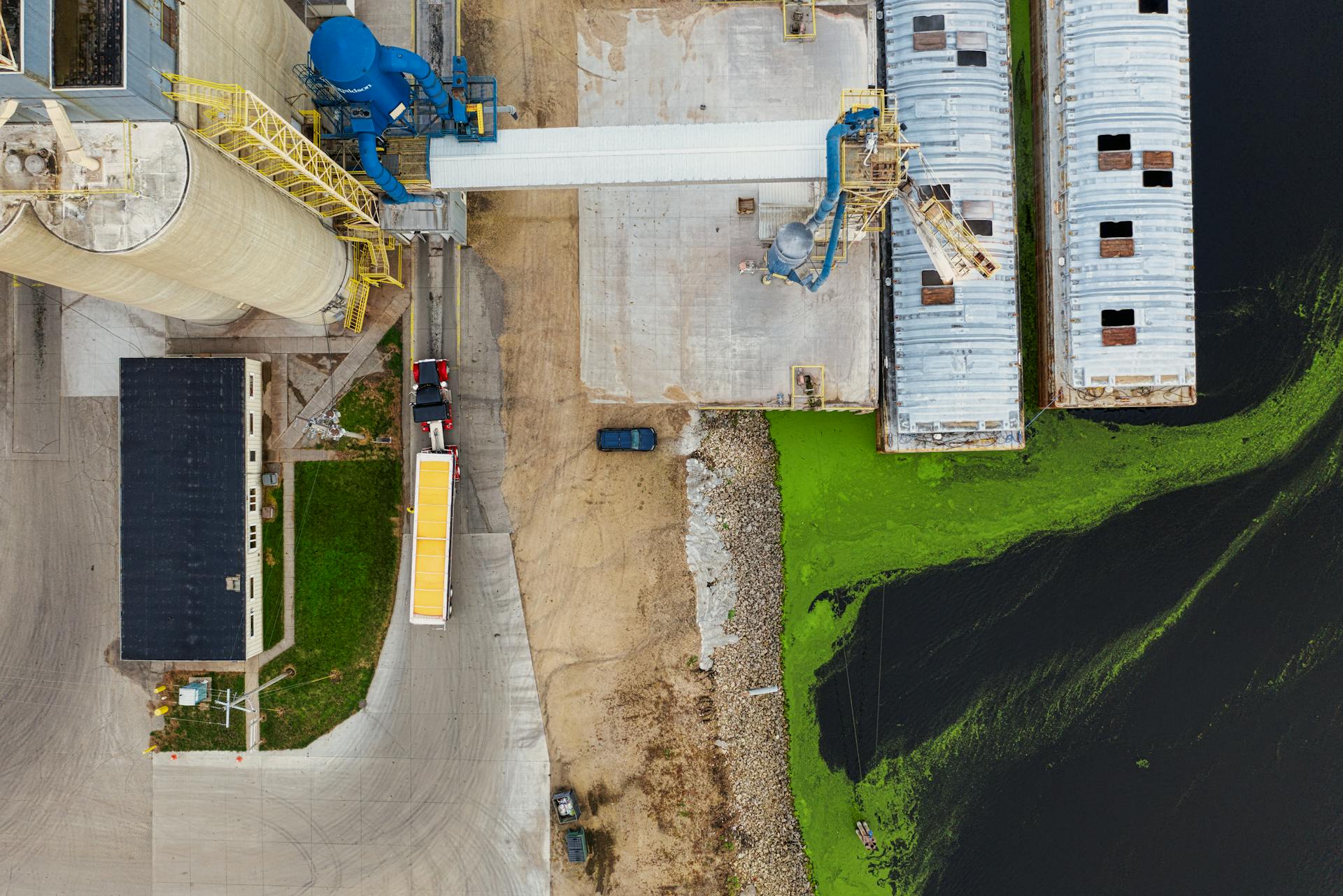
When planning a loading dock, understanding the different types of docks is crucial for efficient operations.
There are many types of loading docks to choose from, including flush loading docks and saw tooth platforms.
Flush loading docks provide a flat surface for loading and unloading, while saw tooth platforms offer a more aggressive surface for secure cargo retention.
Sea Containers
Sea containers can have trailers with heights of up to 62 in, which can pose a challenge for facilities that need to service them.
Facilities that service sea containers often also handle low-bed trucks, with height differences ranging from 30 to 62 in.
Designing docks of various heights can be a solution to accommodate these varying heights.
Typical container sizes vary, and it's worth referencing Table 5 for a comprehensive list.
Types of
There are many types of loading docks you can install in your warehouse. From flush loading docks to saw tooth platforms, the options can be overwhelming.
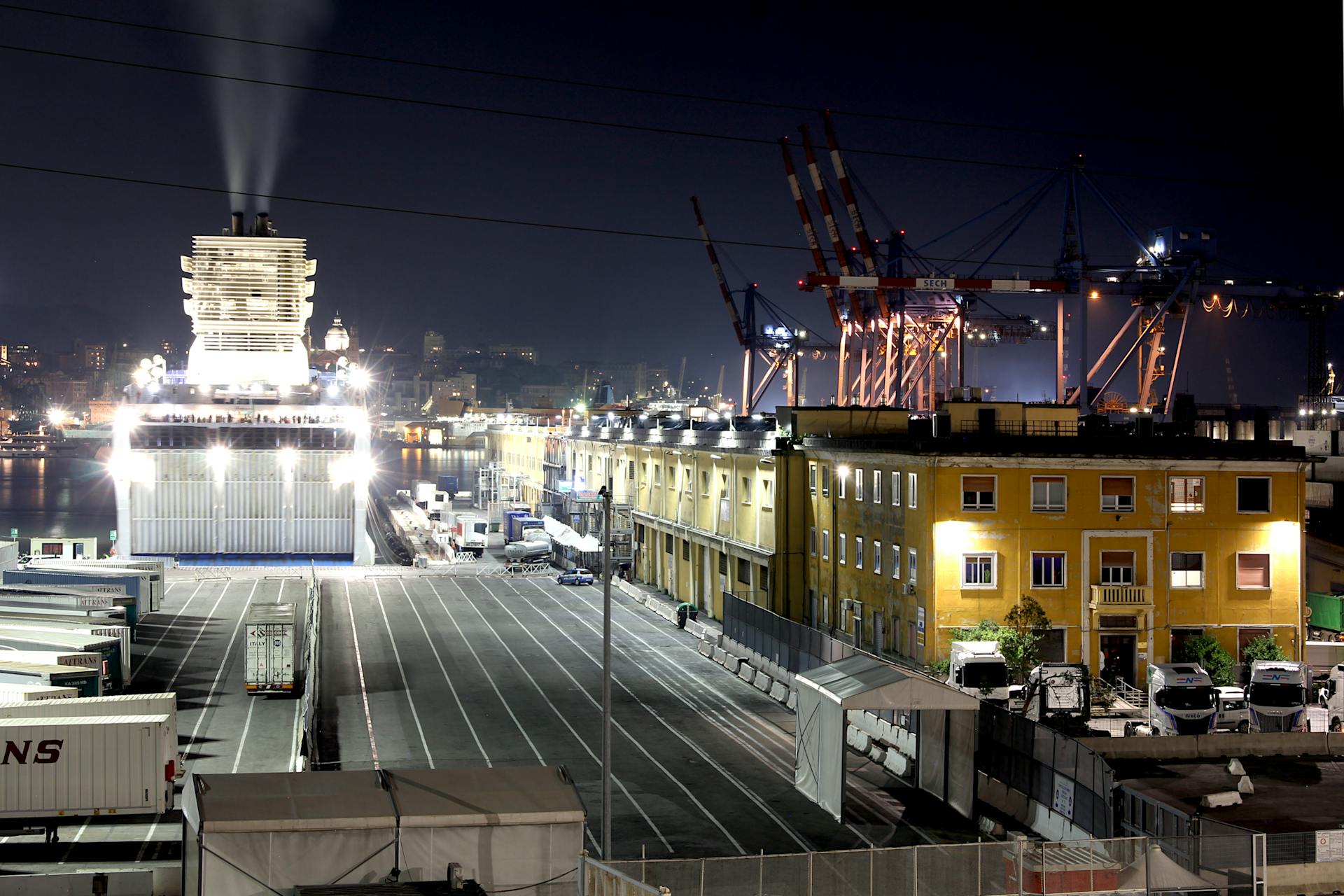
Flush loading docks are a popular choice, providing a smooth surface for easy loading and unloading. They're ideal for warehouses with a lot of foot traffic.
Saw tooth platforms are another type of loading dock that offers a slight incline to help prevent damage to products and equipment. This design is perfect for warehouses with heavy machinery.
There are also different styles of loading bays to consider, each with its own unique features and benefits.
Open
An open loading dock is a common type of dock, but it has some downsides. It's exposed to the weather, which can be a problem.
You can limit the amount of rain and snow that gets in by using a canopy. This can be especially helpful if you live in an area with harsh winters.
If you place a canopy over a dock with a sloped grade, its height must accommodate the sloped trailer's height. This is an important consideration to keep in mind when designing your dock.
Related reading: Loading Dock Canopies
Planning and Compliance
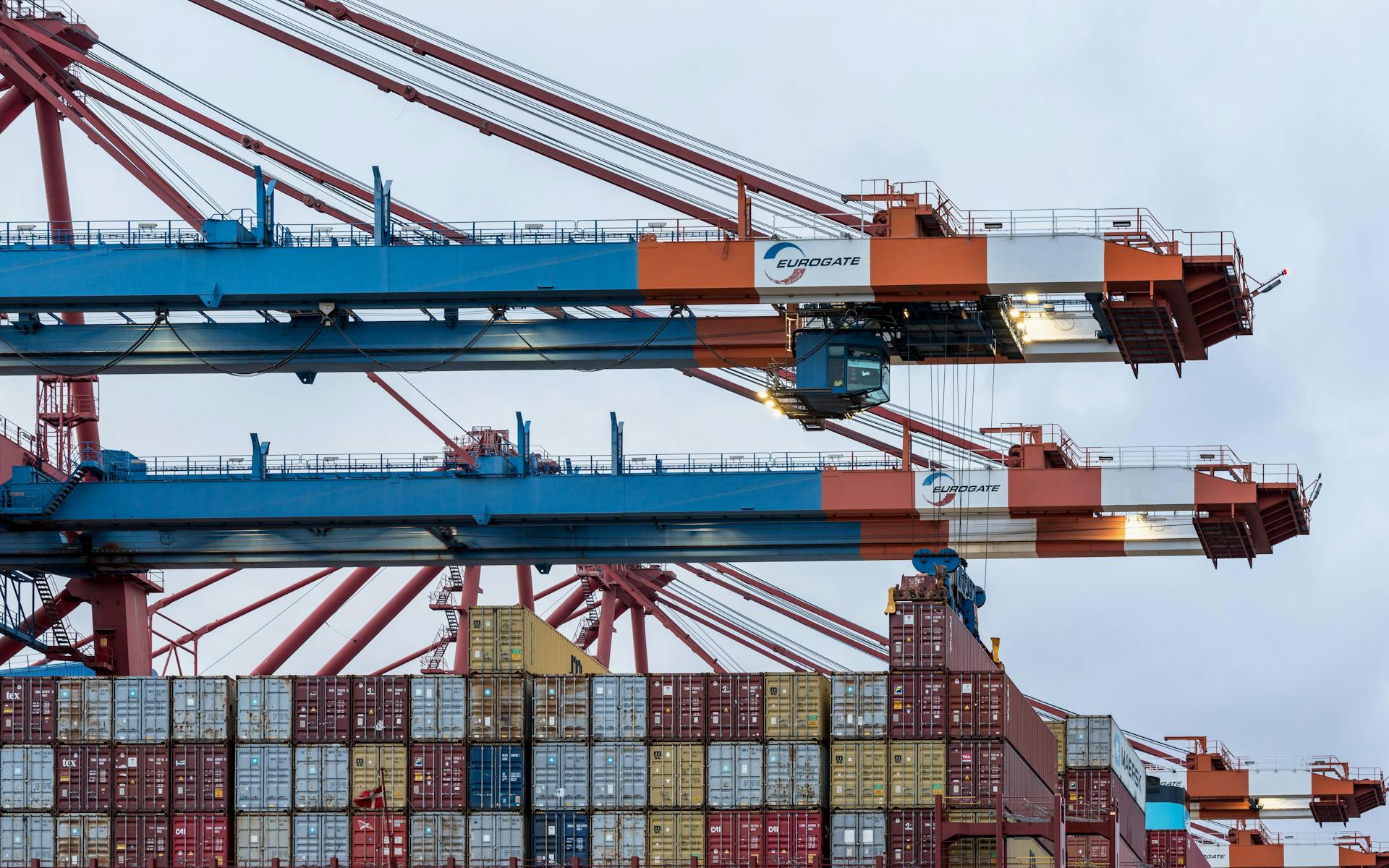
Planning and Compliance is a crucial aspect of designing a loading dock. The most important thing is making sure it's compliant with state and national regulations.
You'll need to consider local codes and traffic engineering standards, as each city and county has its own building code requirements. Failing to meet these standards can result in fines and penalties.
To ensure compliance, think about the traffic patterns you design for your loading dock. Limit two-way traffic to aisles that are wide enough for larger vehicles. This will help you avoid any issues with pallet jacks, forklifts, and other equipment.
Consider the following factors when planning your loading dock:
- The characteristics of your building processes
- Truck configurations
- The number of trucks your facility receives per day
- Dimensions of doors and dock
Set the proper loading bay width and dock height to avoid any potential problems.
Planning
Planning a loading dock is crucial to ensure efficient and safe operations. Efficiency is key to any business, so it's essential to layout the dock area in a logical manner.
The traffic patterns should be clearly laid out for operators, and two-way traffic is only acceptable when aisles are wide enough for vehicles to pass. This means you should plan for one-way and circular traffic patterns, or two-way traffic when only one operator is running.
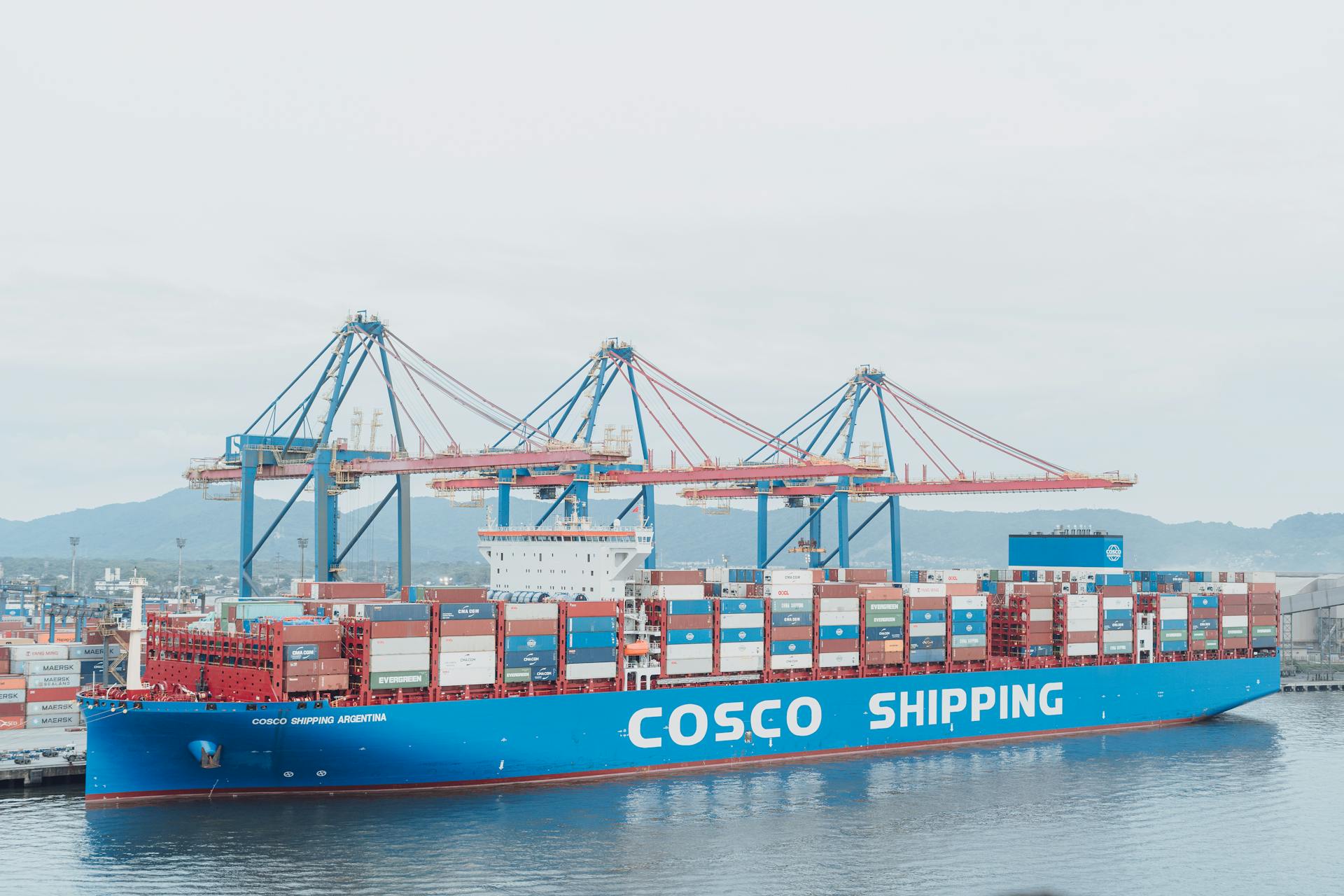
You'll need to consider the characteristics of your building processes, including the number of trucks your facility receives per day. This will help you determine the proper loading bay width and dock height.
To plan for your facility's loading dock, you should also consider truck configurations and the dimensions of doors and dock. This will ensure that your loading dock is compliant with state and national regulations.
Here are some key factors to consider when planning your loading dock:
- Truck configurations
- Number of trucks your facility receives per day
- Dimensions of doors and dock
- Characteristics of your building processes
By considering these factors, you can create a loading dock that is efficient, safe, and compliant with local codes and traffic engineering standards.
Waiting Area
A waiting area is essential for your loading dock, providing a dedicated space for trucks to wait to dock without disrupting standard loading and unloading operations.
This separate area helps maintain a smooth flow of goods and prevents congestion on the dock. Your loading dock should also be outfitted with a waiting area, which is a dedicated space where trucks can wait to dock without interfering with standard loading and unloading operations.
Dock Maintenance and Operations
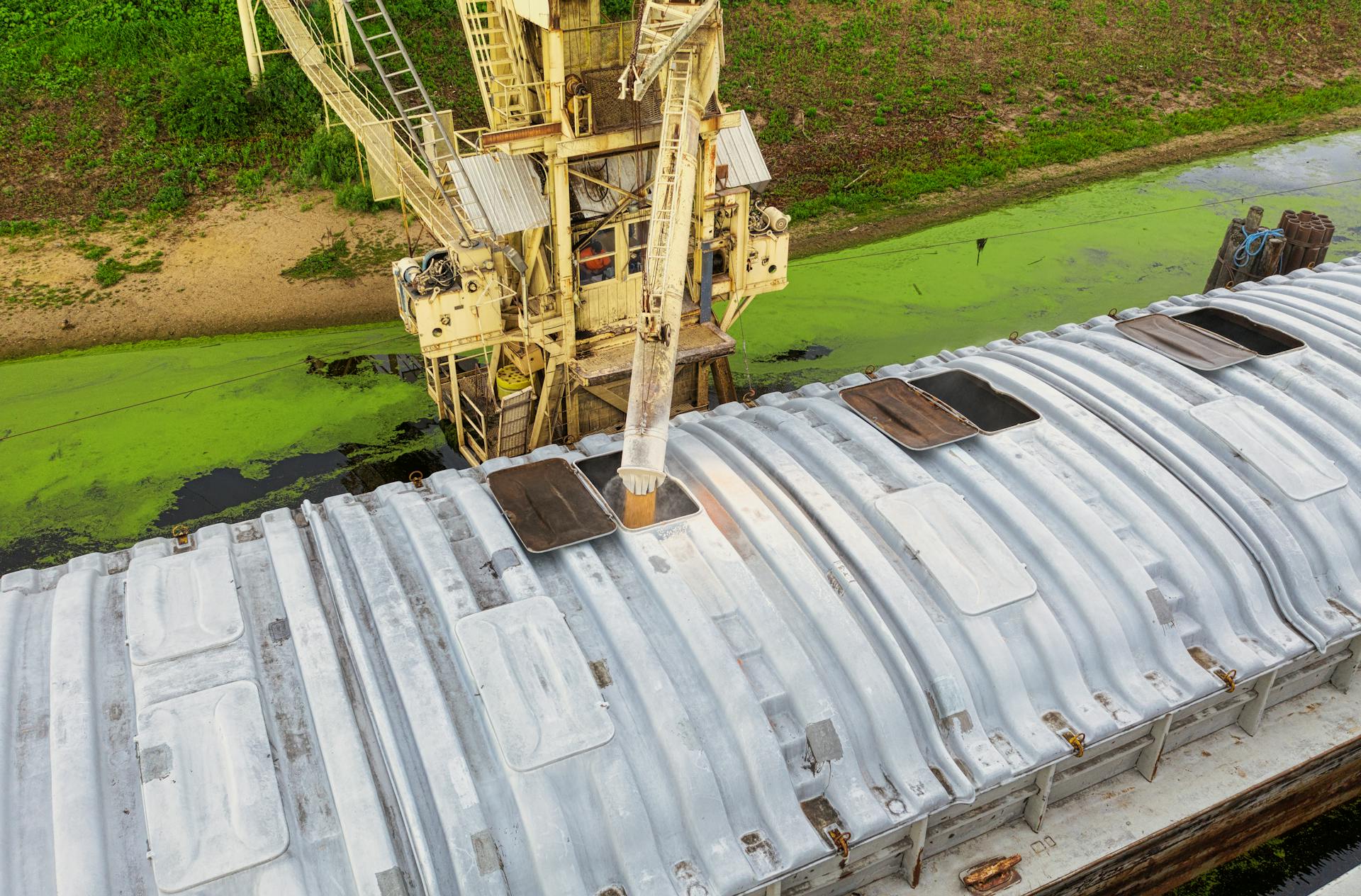
Loading docks require regular upkeep to ensure safe and efficient operations. Open docks generally need less maintenance than enclosed docks.
Cleaning and weatherproofing are essential for open docks to prevent damage from the elements. Regular checks on dock levelers and bumpers are also crucial for flush docks.
Saw-tooth designs require regular inspections to ensure the dock angles are properly aligned and not causing undue strain on vehicles or equipment. Enclosed docks, on the other hand, need to manage the internal environment for temperature and humidity.
Routine inspections are a must for all dock styles, including enclosed docks. Regular maintenance can help prevent costly repairs and ensure a smooth operation.
For more insights, see: Loading Dock Maintenance
Dock Design Parameters
When designing your loading dock, consider the width of the truck bays. Each bay should be at least 12 ft wide to accommodate 8’0″ to 8’6″ wide trailers.
To reduce congestion, design 14 ft wide bays. This will provide enough space for trailers to back squarely to the dock.
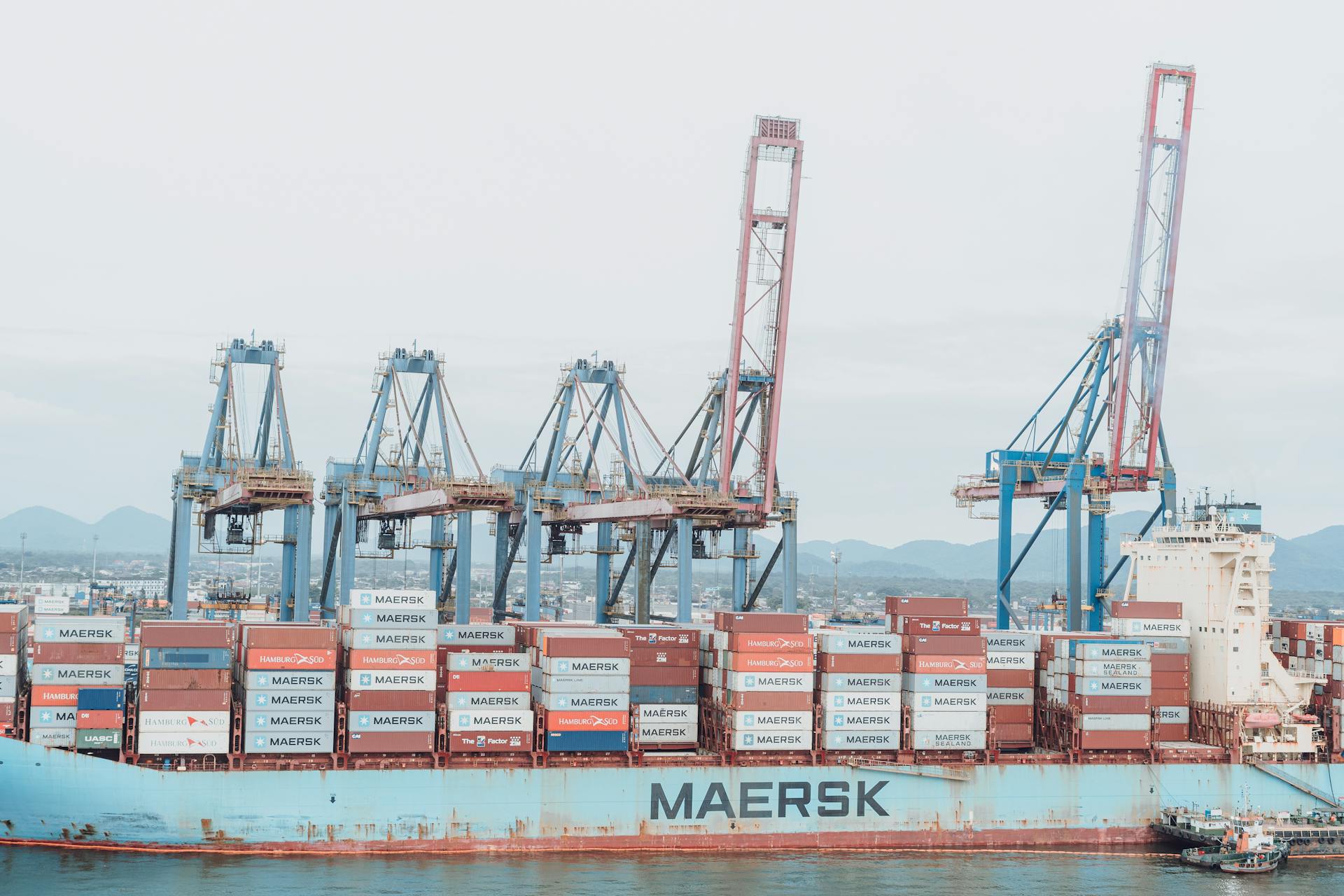
The maximum trailer size limits are 8’6″ wide x 13’6″ high, varying by state. With a special permit, a flatbed may exceed the maximum width.
The approach angle of trucks to the loading dock is also important. Proper bumpers need to be installed to factor in this angle, so trucks can park easily without causing damage to the building.
Set the Height
Setting the dock height is a crucial aspect of dock design. It must match the height of the docking trucks.
The ideal dock height is between 46 and 52 inches, covering most truck bed heights. Most trucks require a dock height within this range.
A steep incline between the dock and the trailer bed can cause insufficient forklift underclearance and increase maintenance demands on the equipment. The incline should not be too steep.
If the driveway is recessed, the dock height should be lower. A recessed parking area may lower the truck bed height by 6 to 10 inches.
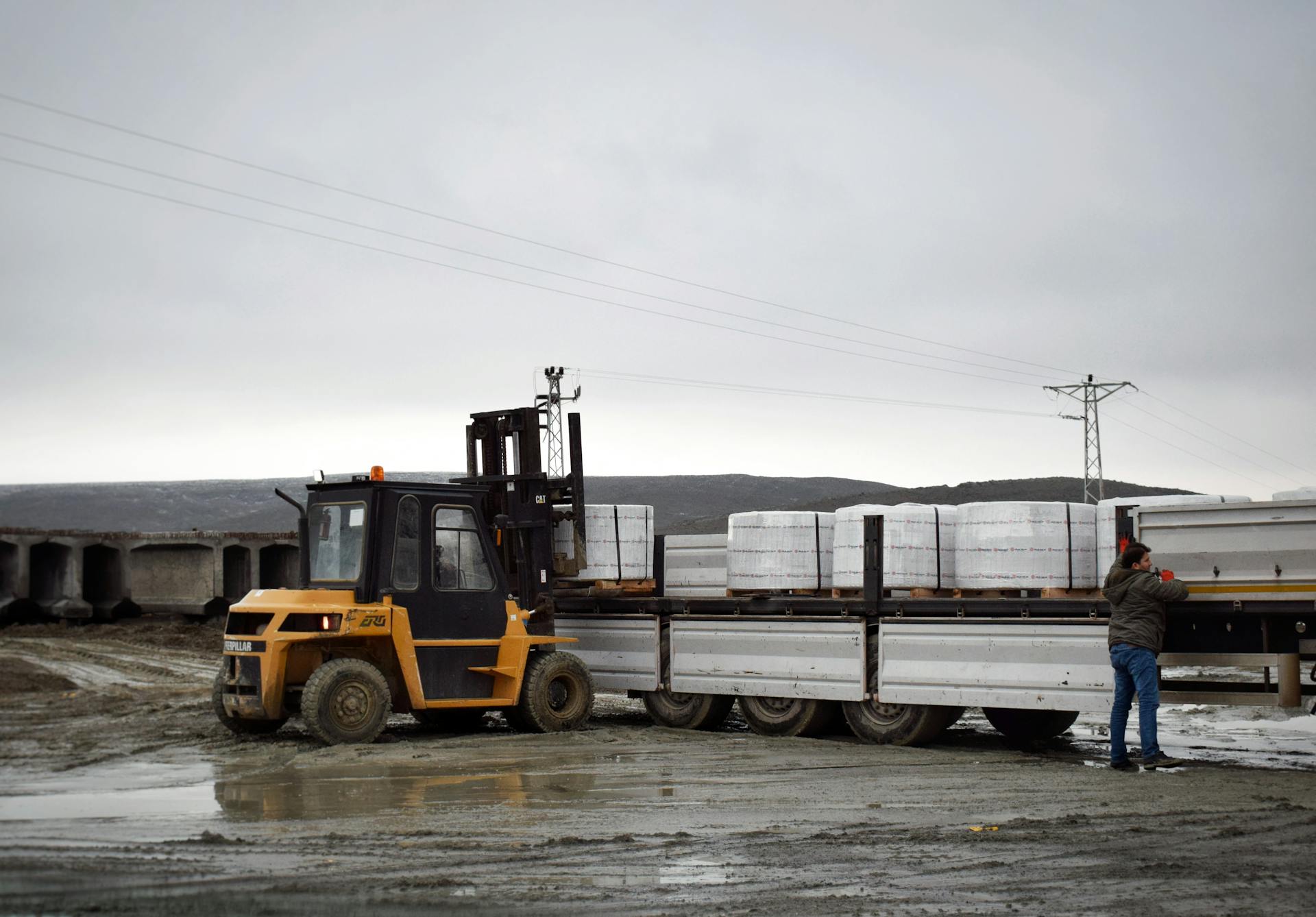
For example, if a driveway approach declines to a level surface in front of the dock, and the truck or trailer has its wheels positioned well forward of the rear of the vehicle, the dock height should be lower. In this case, the dock height should be at least 40 inches.
Design the dock height based on the specific parameters of driveway slope, geometry of the recessed parking area, and bed heights of the expected trucks unique to your building.
Related reading: Truck Loading Dock Height
Approach Angle
The approach angle of trucks arriving at your loading dock is a crucial factor in dock design. It's essential to consider the angle at which trucks will be approaching your dock to prevent damage to your building.
Proper bumpers need to be installed to factor in this angle, as mentioned earlier. This will ensure that trucks can park easily without causing damage.
The angle of approach can vary depending on whether trucks are traveling downward, upward, or on level ground. This means you need to design your bays with flexibility in mind.
Frequently Asked Questions
What are the OSHA requirements for a loading dock?
According to OSHA, loading docks 4 feet or more above adjacent floor or ground level must be guarded by a standard railing or equivalent to prevent employee falls. This safeguard is crucial to ensure a safe working environment.
What are the minimum dimensions for a loading dock?
For a loading dock, each truck bay should be at least 12 ft wide to accommodate trailers, with 14 ft wide bays recommended to reduce congestion. The center distance should be at least 14 ft if trailer doors will be opening or closing at the dock.
How much does it cost to build a loading dock?
The cost of building a loading dock can range from $40,000 to $100,000 or more, depending on the project's size and complexity. Learn more about the factors that influence the cost of a loading dock installation.
What is the maximum slope for a loading dock?
The maximum slope for a loading dock is 10%, with a recommended limit of 3-5% for heavy loads to prevent loads from toppling.
Featured Images: pexels.com