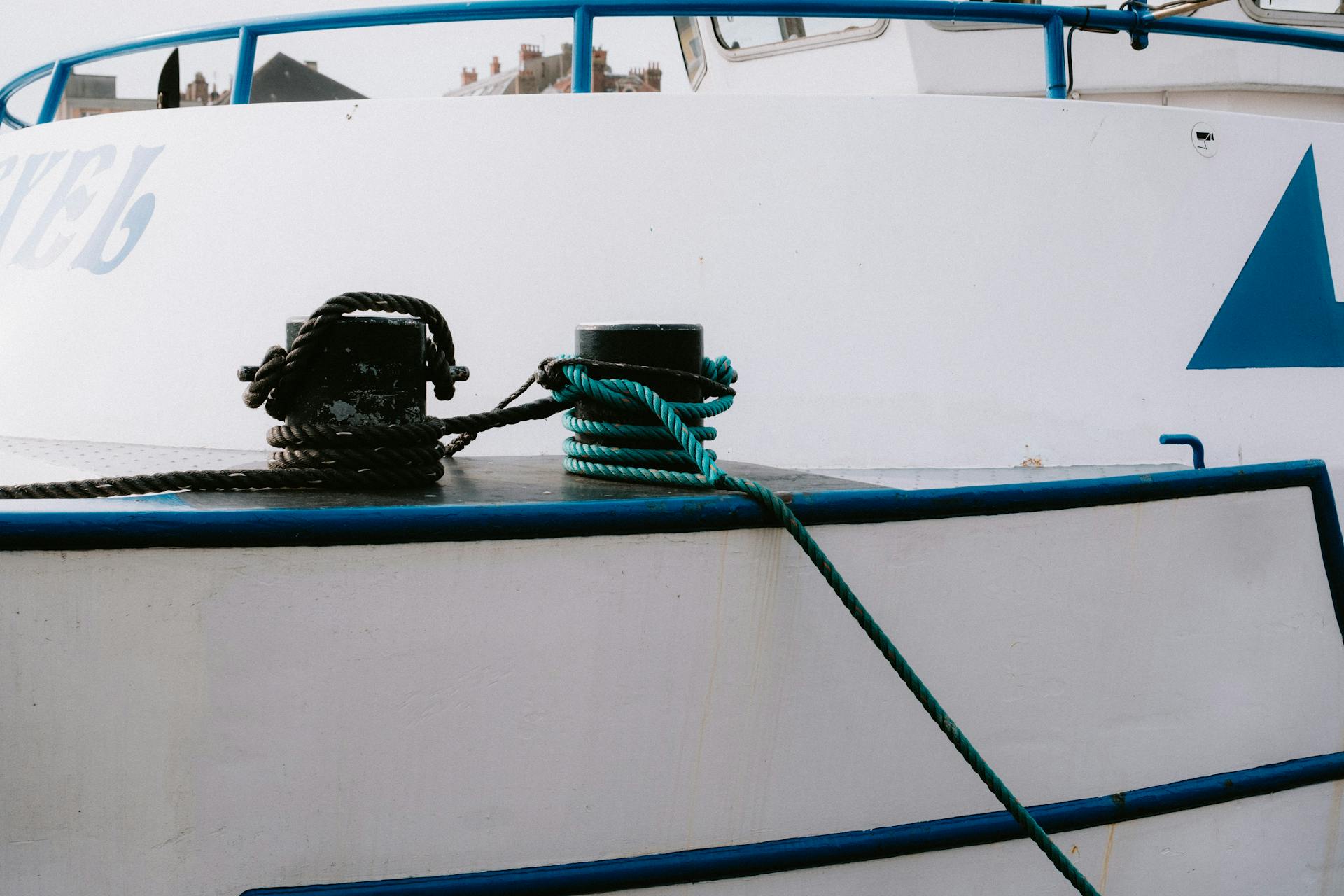
Hydraulic tensioning is a crucial aspect of the marine industry, where it's used to secure and stabilize critical components on ships and offshore platforms.
This method involves using hydraulic systems to apply precise and controlled forces to tensioning rods, which are then attached to the component in need of adjustment.
In the marine industry, hydraulic tensioning is often used to secure anchor chains, mooring ropes, and other critical components that require precise tensioning to ensure safe operation.
Properly tensioned components are essential for preventing equipment failure, reducing downtime, and ensuring the overall safety of the vessel and its crew.
Marine Riser Equipment
Marine riser equipment is a crucial component of offshore drilling rigs. It's what keeps the riser from buckling when the rig moves downward and stretching when it rises.
Crews on these rigs understand how critical this functionality is, and you can see the tensioner system hard at work during a storm near the moon pool of any offshore rig or vessel. These systems use hydraulic accumulators to drive piston displacements in reaction to the heaving of a heavy sea.
The tensioner must manage differential movements between the riser and the rig, as the riser is connected to the wellhead on the seabed. This is done through the use of hydro-pneumatics in a system comprising a hydraulic cylinder, accumulator, and typically wire sheaves.
Accurate measurements of the air/oil compression ratio are critical to the operation of the tensioner system. This means control systems must monitor and replace lost air dynamically.
The position of the piston for a given hydraulic oil pressure is a direct indication of the need for increases to gas volume, which can then be injected by an automatically controlled compressor. These accumulators are constructed using a gas, typically air or nitrogen, and hydraulic fluid to drive displacements up to 12 meters.
Equipment Offerings
Our equipment offerings for the marine industry are designed to meet the unique demands of this sector. We provide a range of hydraulic tensioning systems that can withstand the harsh marine environment.
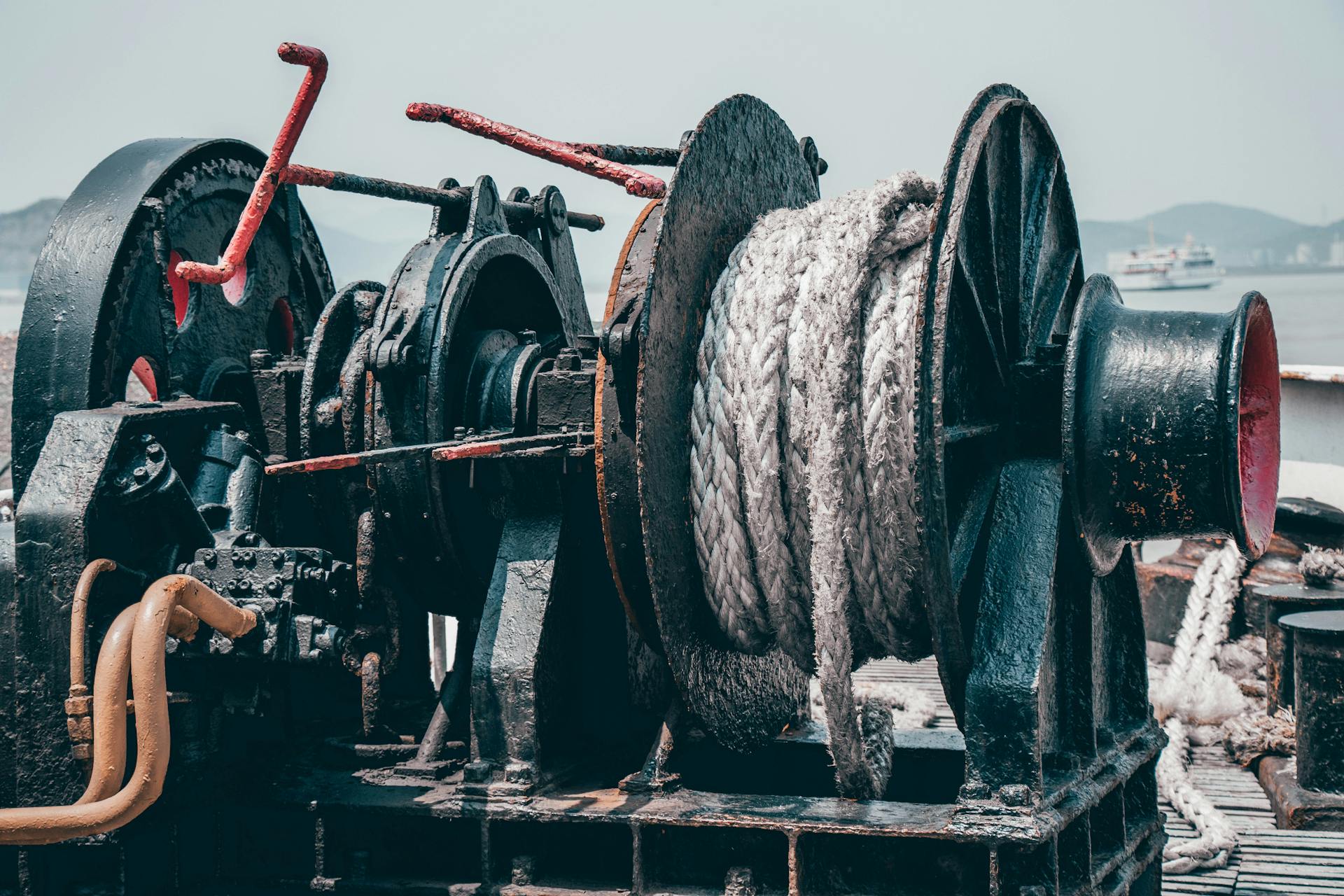
Our most popular product is the HT-1000, a hydraulic tensioner that can apply up to 100 tons of force. This is ideal for use on large vessels where high-tension cables are required.
We also offer a variety of accessories to complement our hydraulic tensioning systems, including cable clamps and tensioning rods. These accessories help to ensure that our systems are installed and maintained correctly.
Our equipment is built to last, with durable materials and robust construction that can withstand the corrosive effects of seawater. This means that our equipment can be relied upon to perform consistently over time.
See what others are reading: ThyssenKrupp Marine Systems
Hydraulic Tensioning Process
Hydraulic tensioning is a crucial process in the marine industry, and it's essential to understand the correct procedure to ensure a safe and efficient installation. The working pressure of the hydraulic power source is typically one pressure value, expressed in B.
To begin the 100% stretching procedure, pressurize the system to 6.9 MPa (1000 psi) and check the hydraulic tensioner installation for proper alignment and locknut engagement. The diver should also inspect the hydraulic hose fittings for leaks and abnormalities.
The stretching process involves using a toggle bar to tighten the nuts in the hydraulic tensioner, ensuring each nut is firmly affixed to the flange surface. The piston stroke may not exceed its maximum stroke, so if necessary, tighten all the bolts and nuts, reset the tensioner head stroke, and continue to pressurize the full B-value.
The stretching procedure requires repeating steps until all nuts can no longer be pivoted, which indicates the tensioning is complete. If the nut can still be pivoted, the process must be repeated until all nuts are secure.
Advantages
The hydraulic tensioning process has several advantages that make it a preferred method for various industries. One of the key benefits is that it eliminates the need to overcome friction, allowing for a more efficient and accurate application of tension.
Direct tension is applied to stretch the bolt, reducing the risk of damage to the connection surface. This is particularly important in industries such as ocean engineering, where precise control is crucial.
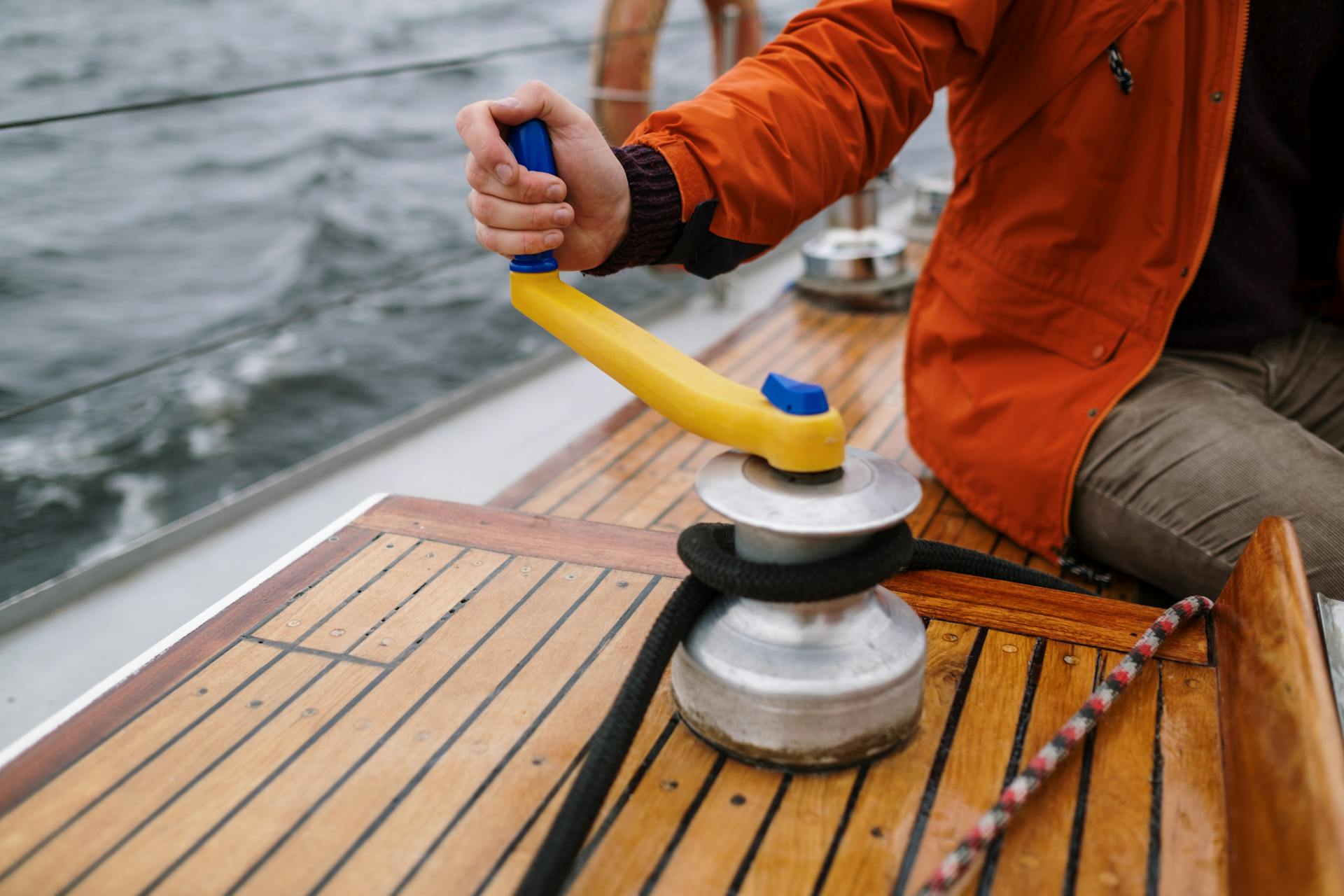
The applied load is accurately controlled, as it is directly proportional to the pressure applied to the hydraulic bolt tensioner. This means that the preload of the connecting parts can be precisely controlled.
The hydraulic tensioner can also synchronize the fastening or removal of multiple bolts, ensuring uniform compression of the gasket. This is especially useful in industries where large-scale equipment installation requires precise control.
In situations where underwater handling of heavy bolts is required, such as in offshore oil projects, the use of strapping to prevent slippage can improve efficiency and solve the problem of underwater handling.
Here are some key benefits of the hydraulic tensioning process:
- Tension is applied directly to stretch the bolt, meaning that no friction needs to be overcome
- Applied load is very accurately controlled, as it is directly proportional to the pressure applied to the hydraulic bolt tensioner
- Loss of load between applied and retained load after tensioning is 20% less than frictional loss associated with torqueing
- Accurate residual load outcomes due to calculable load loss
- Tensioning can be repeated
Determination of Extension Bolt Length Core
To determine the correct length of an extension bolt, you need to consider the space occupied by the hydraulic tensioner. Theoretically, the bolt should extend the length of L = H – B, where H is the hydraulic tensioner body and the total length of the reaction nut, and B is the thickness of the nut.
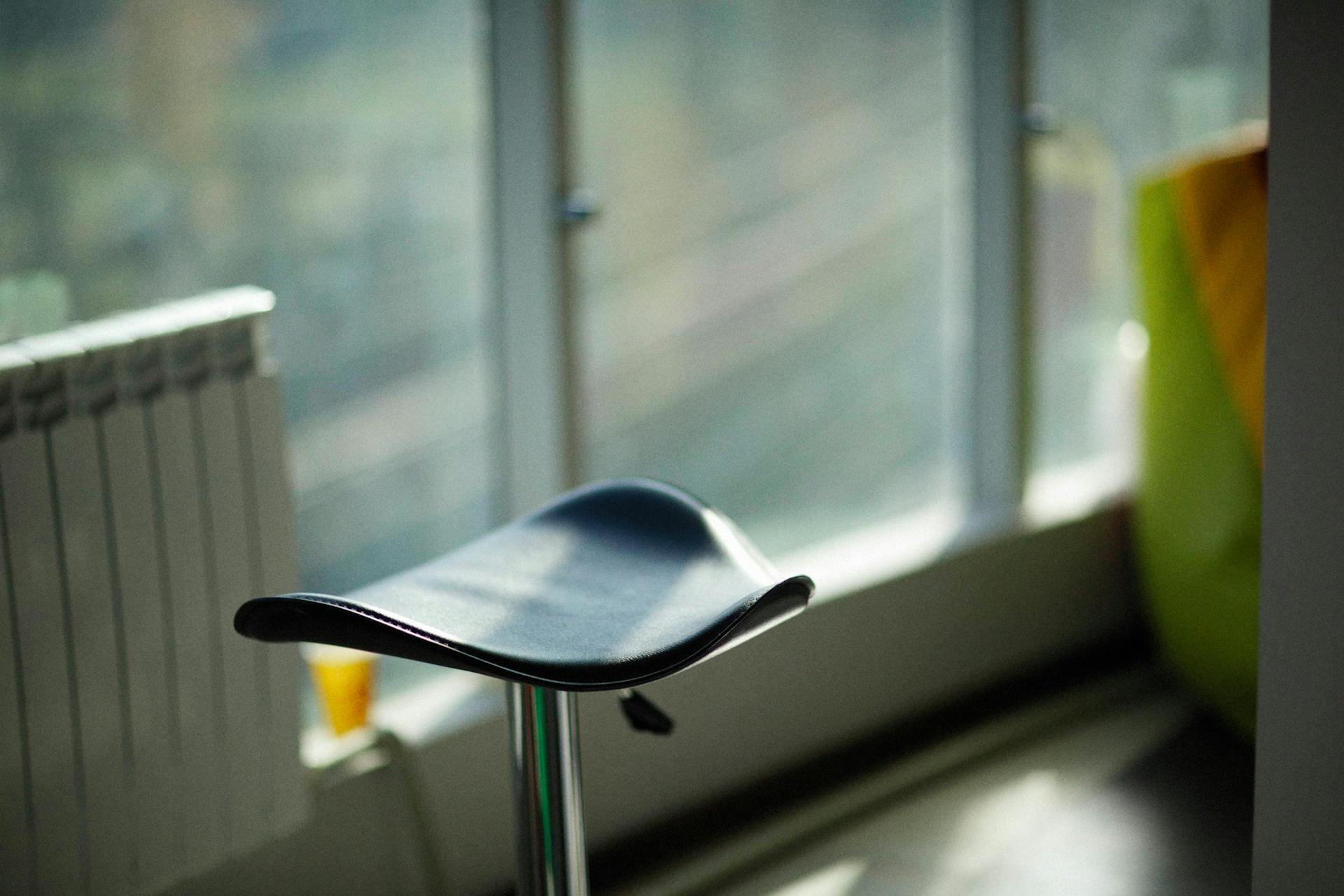
The actual length of the extension bolt should also take into account the length of 2 ~ 3 buckles of thread beyond the reaction nut to ensure operational safety. This is a crucial factor to consider.
In practice, you can approximate the extension length of L by taking the value of H. This is because the distance between the two flanges has not been compressed to the theoretical minimum value before the completion of the actual flange butt.
50% Tensioning Procedure
The 50% tensioning procedure is a bit more complex than the 100% method, but still follows a straightforward process.
To start, the preload pressure of the hydraulic power source is set to two separate values, A and B.
The procedure begins by pressurizing to 6.9 MPa, checking the same requirements as for 100% stretching, and then continuing to pressurize to A.
The diver uses a toggle bar to tighten the nut inside the hydraulic tensioner until it is firmly attached to the flange surface, and then stops the pump to remove pressure and reset the tensioner stroke.
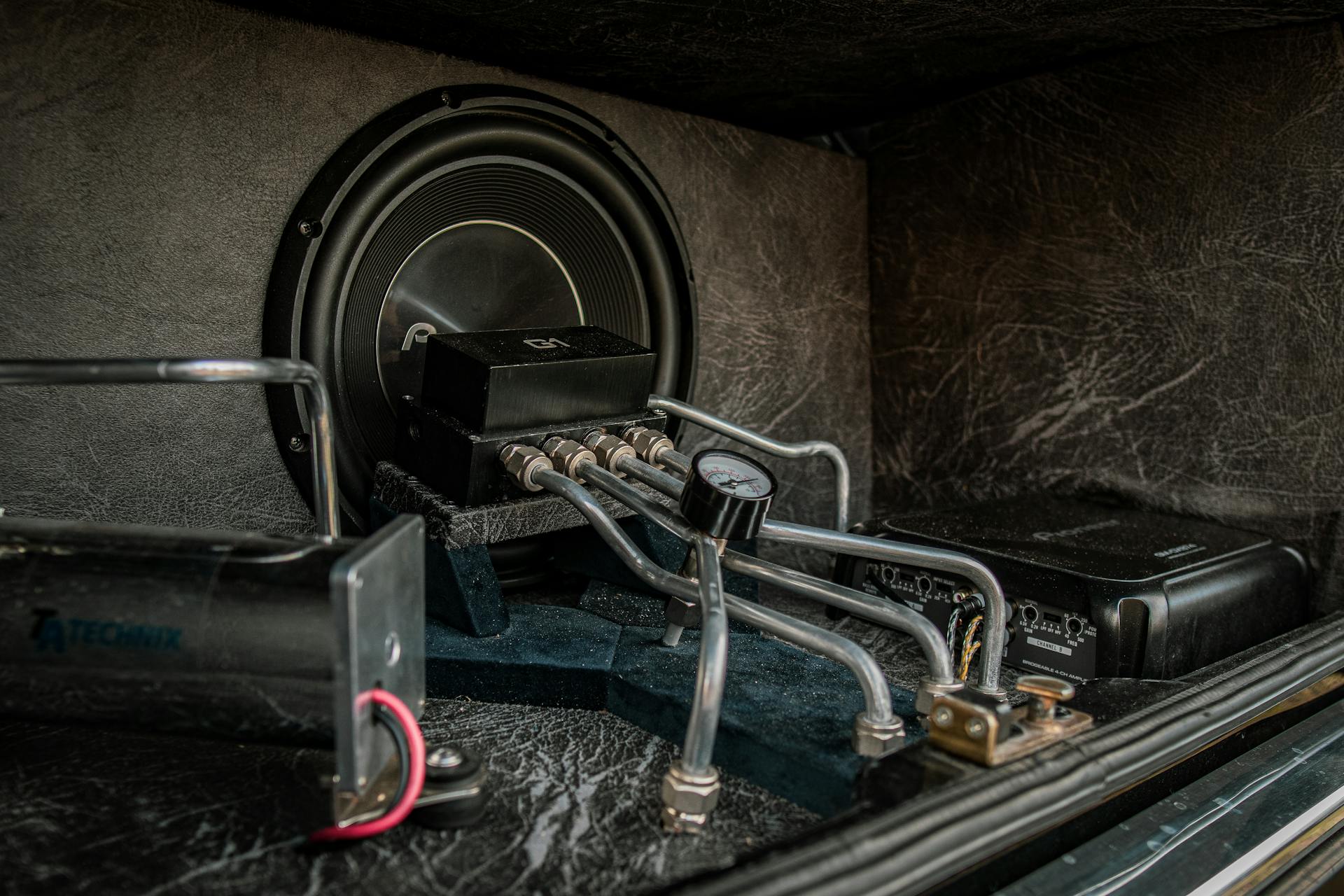
This process is repeated twice.
Next, the tensioner is reversed and reattached to the other 50% of the bolts, and the same steps are followed, pressurizing to 6.9 MPa, checking the requirements, and continuing to pressurize to B.
The diver tightens the inner nut of the hydraulic tensioner until it is securely attached to the flange surface, stops the pump, and resets the tensioner stroke.
This process is also repeated twice.
Finally, the tensioner is reattached to the first set of 50% bolts, and the diver pressurizes to B, tightening the nut until it can no longer be pivoted, and then measures the flange clearances at 3, 6, 9, and 12 o’clock positions.
100% Stretching Procedure
The 100% stretching procedure is a crucial step in the hydraulic tensioning process. It involves simultaneous tensioning of all bolts to achieve uniform and consistent flange gap.
Pressurize to 6.9 MPa (1000 psi) to begin the process. Check the verticality and alignment of the hydraulic tensioner installation to ensure secure engagement of the locknuts.
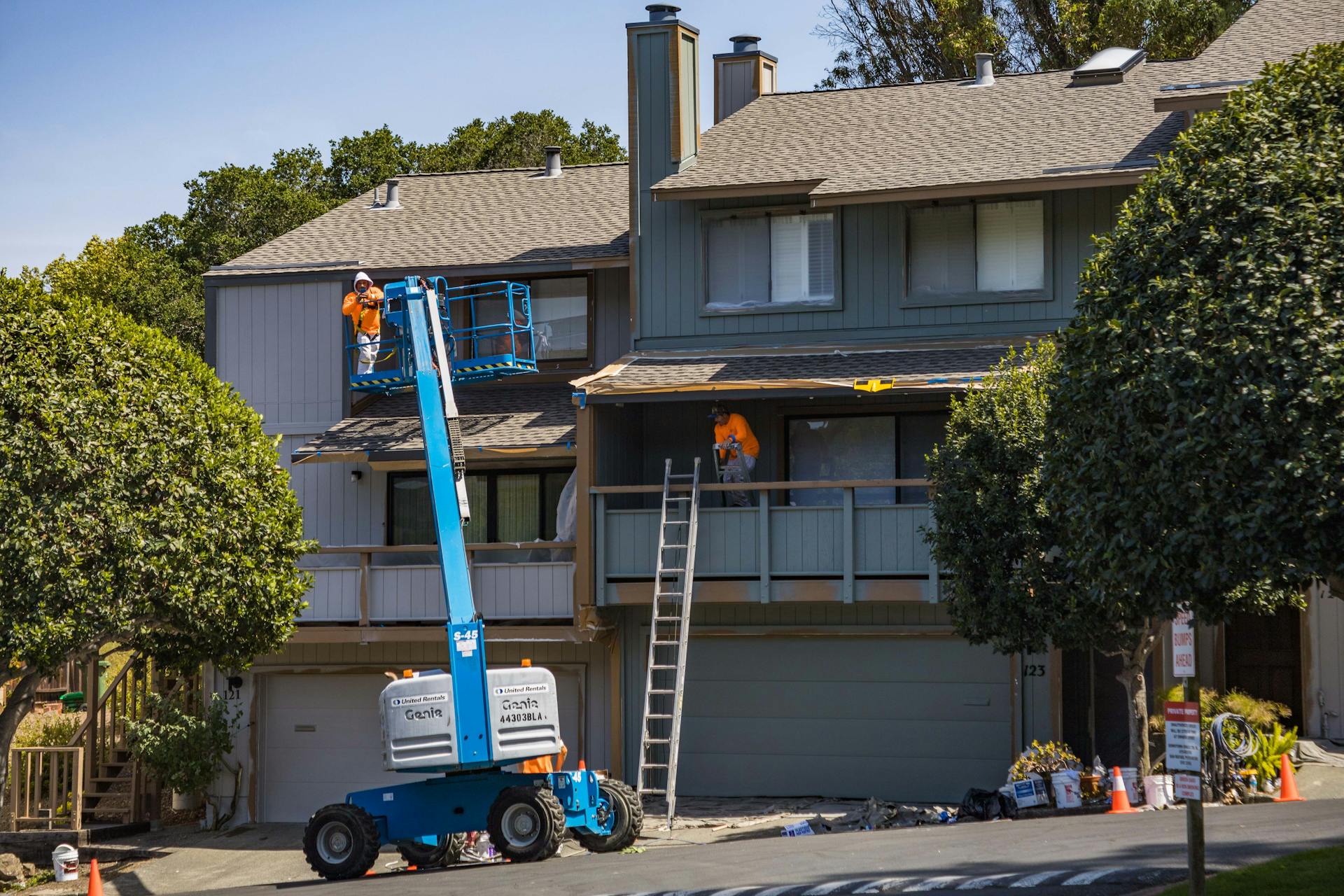
Hydraulic hose fittings should be checked for leaks and other abnormalities before proceeding. If there's a change in the hydraulic tensioner stroke, use a toggle bar to tighten the nut in the tensioner head and reset the tensioner head stroke.
Continue to pressurize to the B value, then use a toggle bar to tighten the nuts in the hydraulic tensioner, firmly affixing each nut to the flange surface. Note that the piston stroke may not exceed its maximum stroke, so tighten all the bolts and nuts if necessary.
Stop the pump unpressurized, reset the tensioner stroke, and repeat the operation twice. This ensures uniform and consistent flange gap.
A final check should be made to ensure the flange gap is uniform and consistent. If necessary, pressurize to the B value and toggle the nut further with the toggle bar until it can no longer be pivoted.
The stretching procedure is as follows: stretch the first set of 50% bolts.
Take a look at this: Electric Marine Head
System Design and Installation
A well-designed system is crucial for efficient hydraulic tensioning in the marine industry.
The system should be designed to withstand the harsh marine environment, with factors such as corrosion resistance and IP67 rating considered.
The installation process should be carried out by trained professionals to ensure the system is properly aligned and secured.
A typical installation process involves mounting the hydraulic tensioner on a fixed or rotating shaft, depending on the application.
System Installation
System Installation is a crucial step in the system design process. It involves physically setting up the hardware components, such as the server, storage devices, and networking equipment.
The installation process typically begins with preparing the physical space, including ensuring adequate power and cooling. This is especially important for servers that generate a lot of heat.
Cable management is also essential during installation to prevent damage to the equipment and ensure easy maintenance. This involves organizing cables and securing them to the floor or walls.
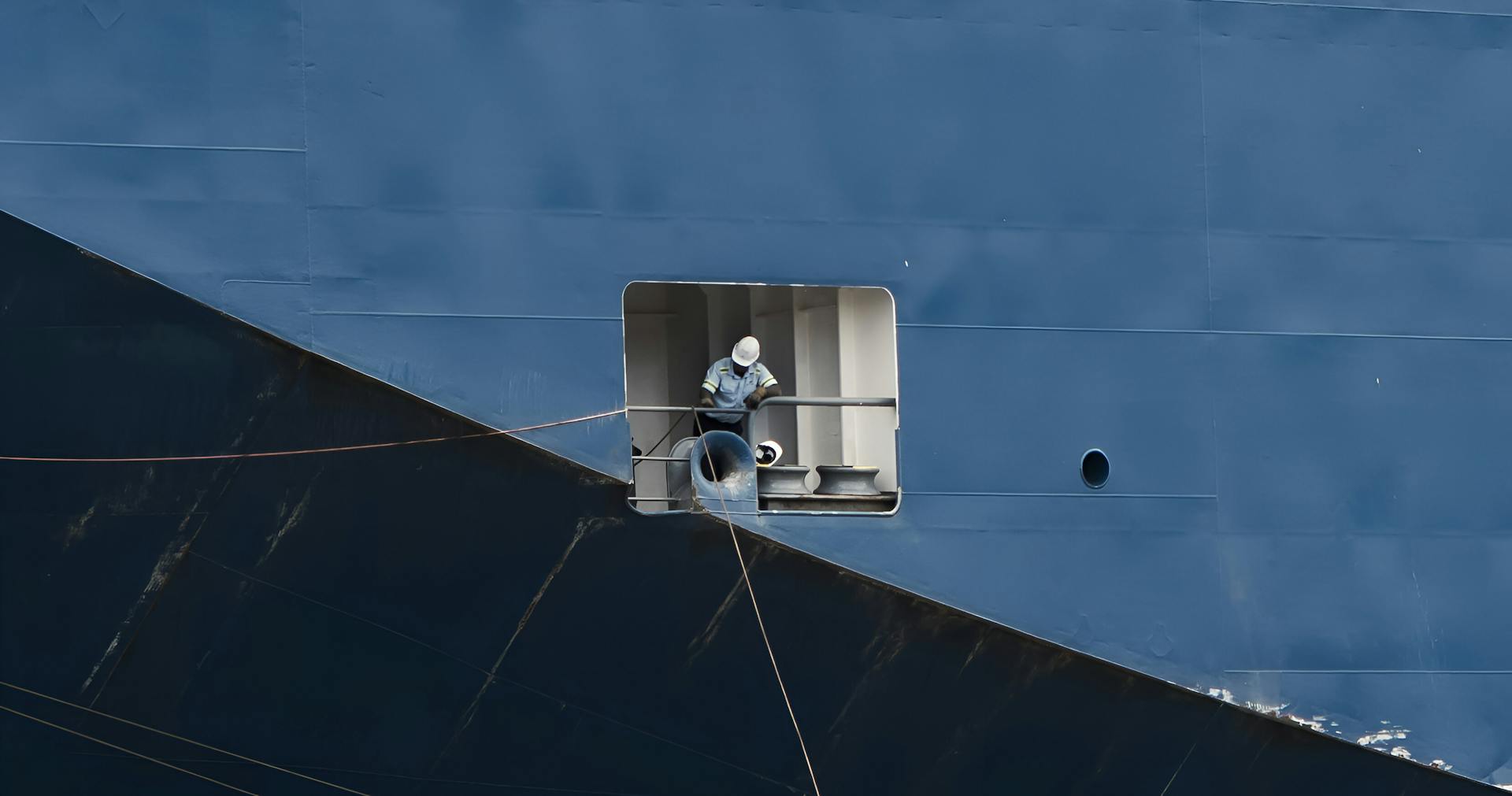
Proper installation of the server and storage devices is critical to ensure data integrity and system performance. This includes configuring the storage arrays and setting up the file system.
Network configuration is also a key aspect of system installation, involving setting up the network interface cards, configuring the network protocols, and establishing connections to other systems.
Topside
The topside tensioners are a reliable and economical option for hydraulic tensioning. They are insert type tools that are proven in the marketplace.
Each base tool can be converted for use on a different bolt size by using a conversion kit, making them a versatile solution.
The Tentec Aero WTF is a purpose-designed range of hydraulic bolt tensioning tools that are safe, reliable, and consistent. They are specifically designed to suit most wind turbine foundation bolting applications.
Rapid tensioning is a key benefit of these tools, allowing for quick and efficient installation.
Subsea Operations
Subsea operations require specialized equipment to ensure safe and efficient installation of subsea structures. The hydraulic tensioner system is a crucial component in this process.
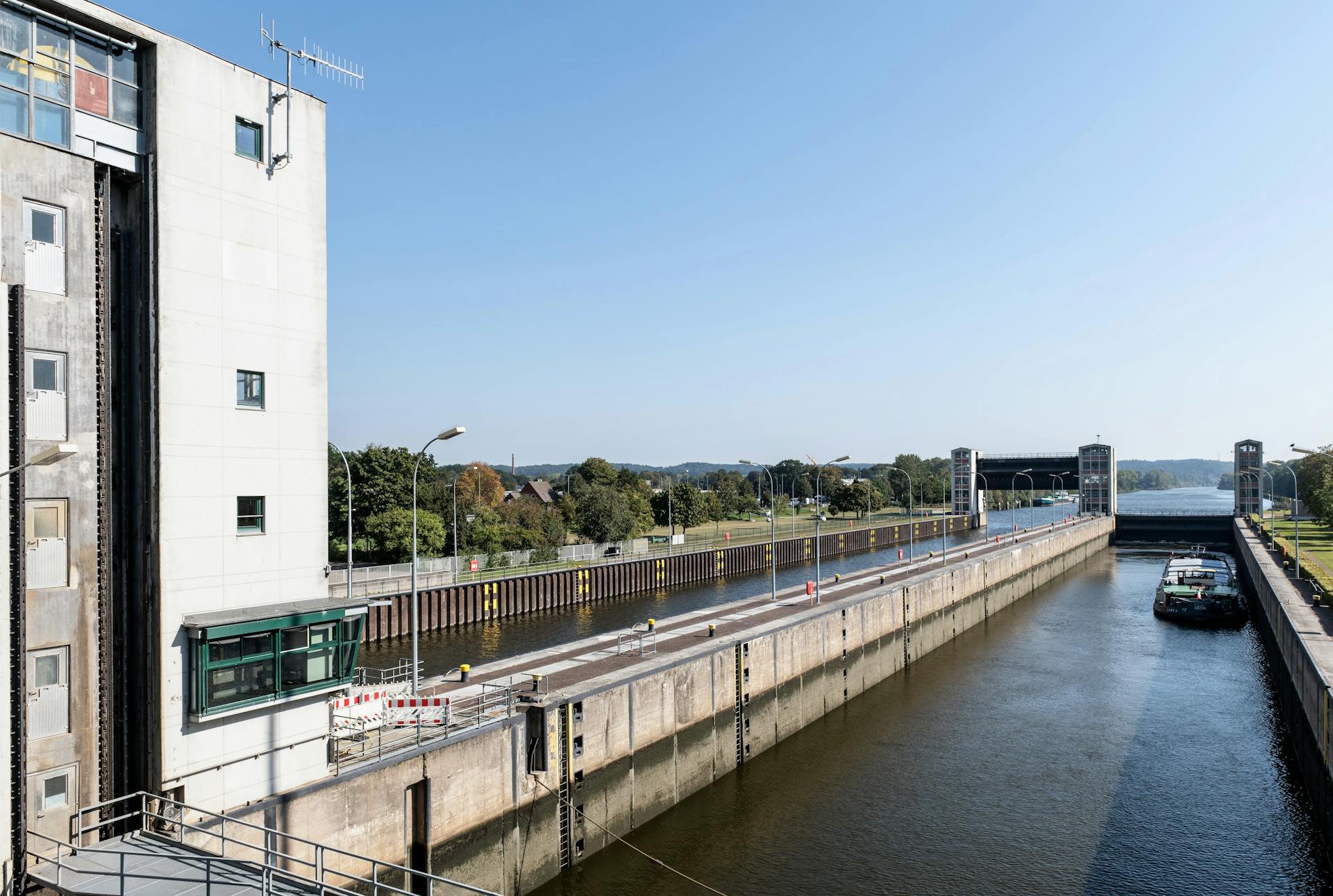
The hydraulic tensioner system is connected to the subsea structure, and the surface operator stretches it according to the calculated preload pressure value of the hydraulic power source. This process varies depending on the installation method.
For 100% tensioning, the surface operator applies the force according to the specified stretching procedure to correctly apply the required residual bolt load. The tensioning procedure for 50% tensioning differs, requiring a different approach.
Subsea tensioners are designed to withstand harsh marine environments, made from high-strength stainless steel that reduces maintenance work after subsea use. This design feature makes the job of the diver easier and quicker.
A subsea tensioner typically consists of a split nut design of reaction nut and integrated bridge with load cell. This design allows for customized solutions, hydraulic nuts, hydraulic tensioning pumps, and tensioners to be used in various subsea applications.
Here's a breakdown of the various components used in subsea tensioners:
Subsea tensioners are designed to operate at various pressure levels, including 19580 psig, 21750 psig, 29000 psig, and 33000 psig.
Safety and Precautions
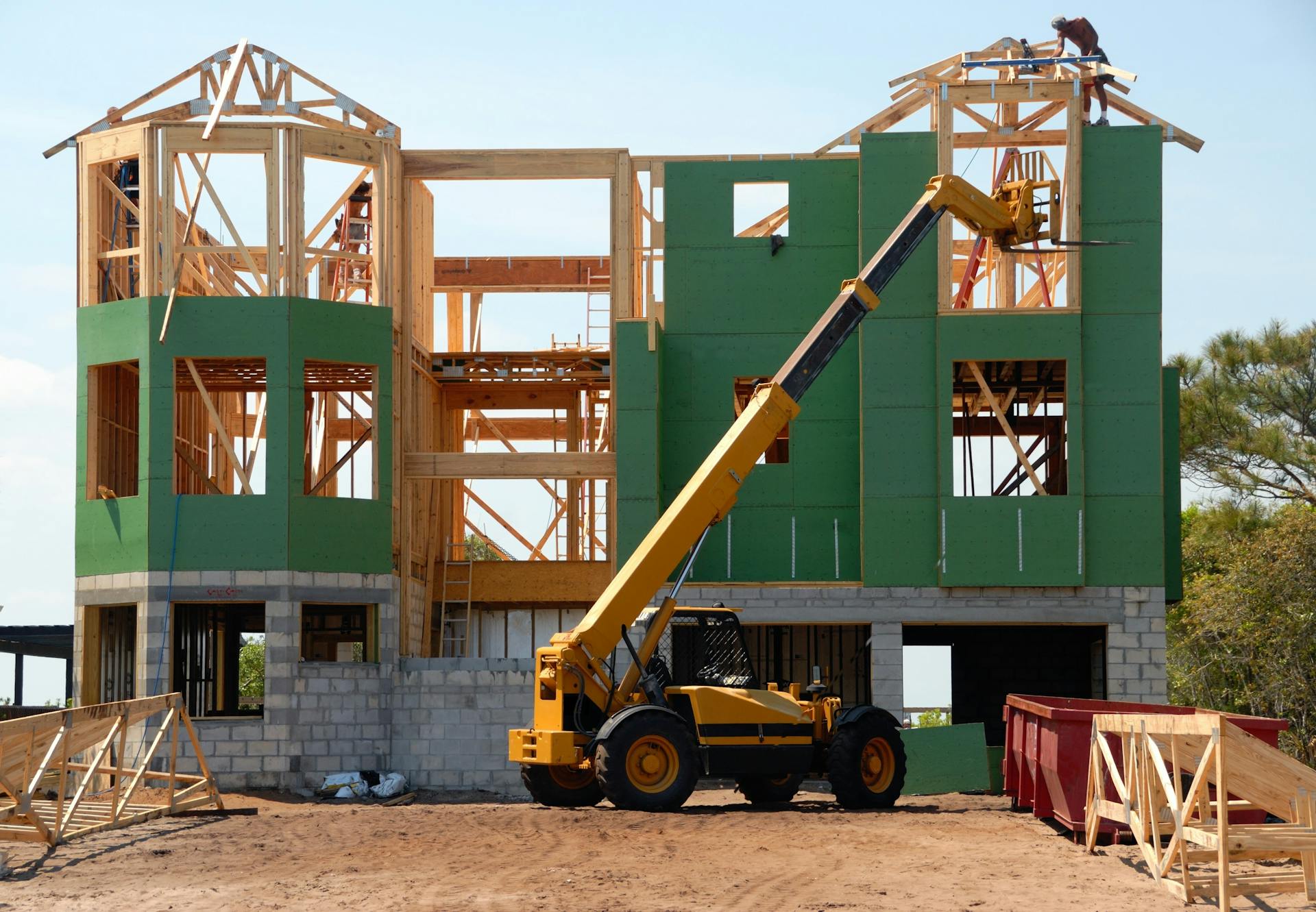
Don't exceed the maximum working pressure of the hydraulic tensioner system under any circumstances.
It's crucial to avoid attempting to disconnect or retighten any part of the hydraulic system while it's under pressure.
When using the tensioner to remove a bolt, be sure to leave a 2-3 mm gap between the sleeve and nut to prevent jamming.
Most underwater hydraulic tensioners have over-travel protection, but if not implemented correctly, piston over-travel can still occur.
Disadvantages
The hydraulic tensioner requires additional bolt length to operate, which can be a challenge in certain situations.
A single hydraulic tensioner is usually only applicable to 2 ~ 3 bolt sizes, making it necessary to have multiple models on hand for projects with varying flange specifications.
This can result in a higher upfront cost and increased complexity in the installation process.
The hydraulic tensioner is relatively unsuitable for low load bolts and shorter bolts (length, diameter ratio of less than 3:1), requiring a larger initial force to be loaded.
Precautions in Underwater Application
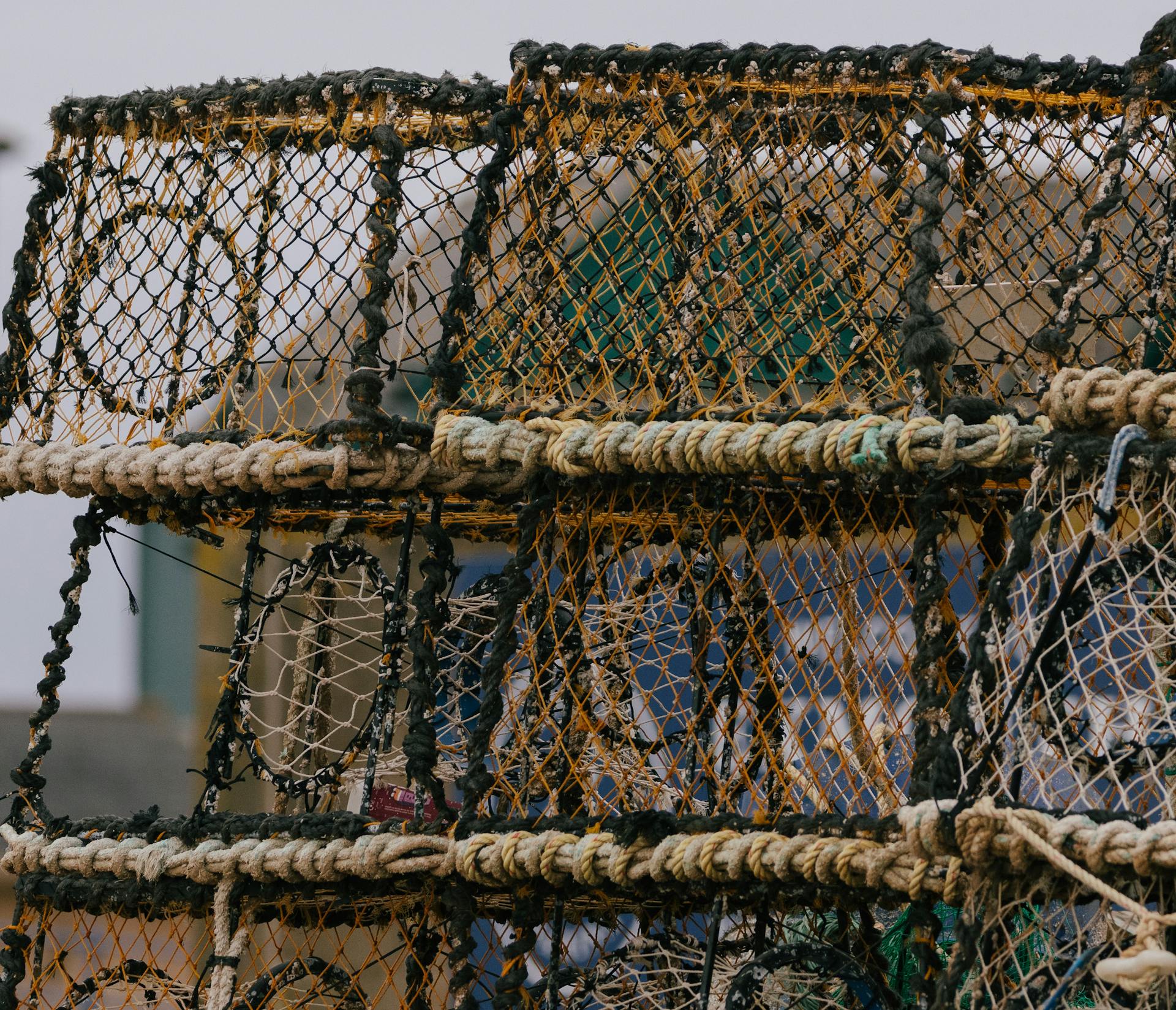
Never exceed the maximum working pressure of the hydraulic tensioner system, as it can lead to serious consequences.
You should not attempt to disconnect or retighten any part of the hydraulic system while it's under pressure.
Loosening the bolt using the tensioner requires a slightly greater pressure than the initial tightening pressure, so be prepared for a slower process.
Leave a gap of 2-3 mm between the sleeve, nut, and screw to prevent jamming.
Most underwater hydraulic tensioners have over-travel protection, but it's still possible to over-travel if you don't follow the operating procedures.
To avoid over-travel, ensure the hexagonal nut with a hole is a standard heavy-duty series, where the nut's height is equal to one times the bolt's diameter.
Before reaching the predetermined hydraulic pressure, don't rotate the nut with a hole downward, or reset the piston and then carry out the stretching operation.
Always fully reset the piston and ensure the reaction nut is firmly in place before stretching.
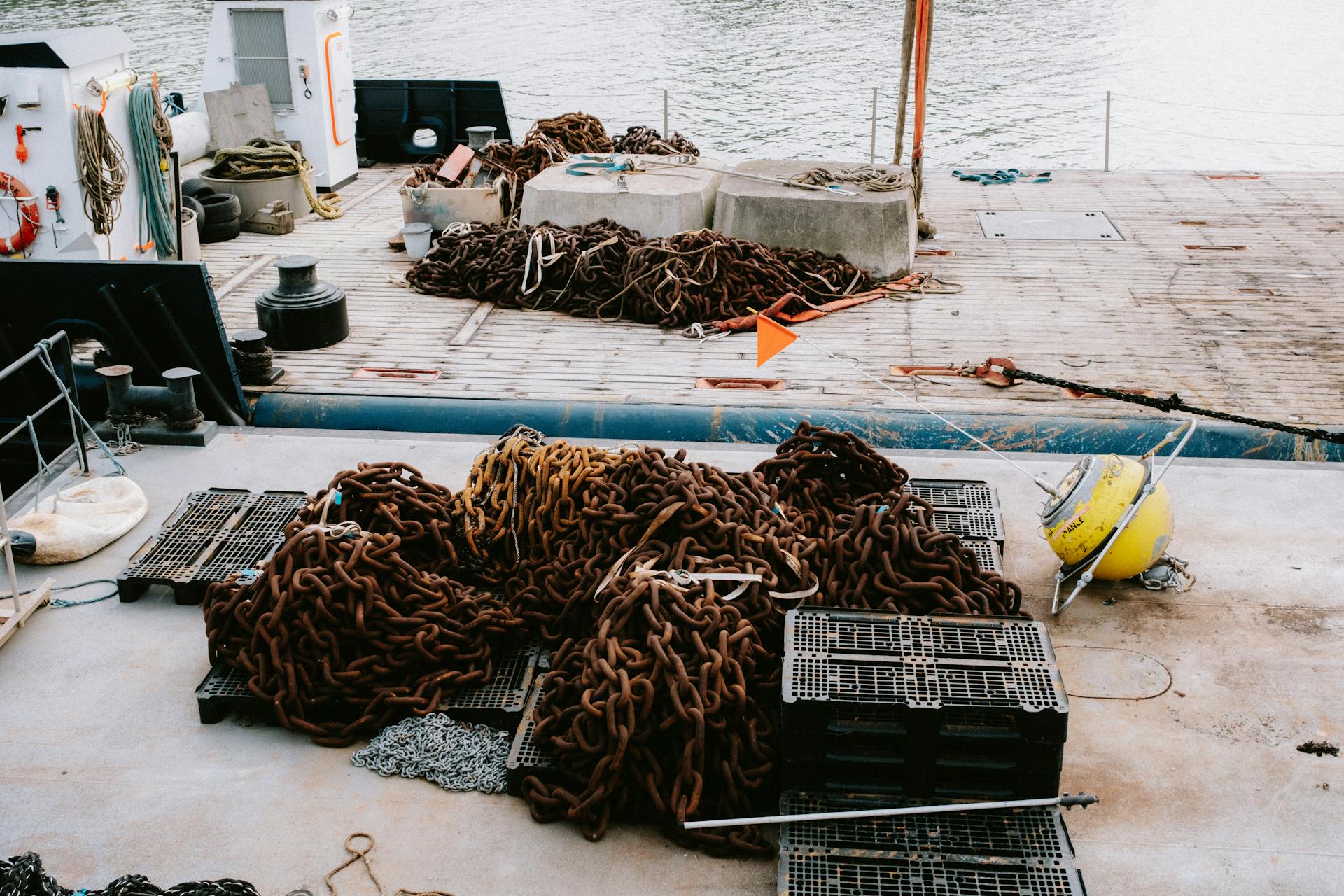
In emergencies, you can use a standard hexagonal nut as a reaction nut, but prepare a washer that covers the entire piston surface and assemble it underneath the nut.
When using extension bolts and tensioners on submarine pipelines, consider the corrosion layer and cement weight layer, as they may affect installation.
Components and Sensors
Components and Sensors play a crucial role in hydraulic tensioning for the marine industry. They need to be able to withstand harsh environments and maintain accuracy over long stroke lengths.
For example, CPI Linear Position Sensors like the SL-1500 can operate with high accuracy to 15 meters of stroke. This is due to their innovative draw wire design.
Hardened operation is a standard feature of CPI sensors, making them immune to pressure and perfect for use on the oil or gas side of the cylinder, or even outside the cylinder.
Their patented LVDT based implementation means the core sensing technology is completely non-contacting and immune to local EMI distortions. This is a game-changer for marine applications where reliability is key.
One notable advantage of CPI sensors is that they are the only hardened sensor in the world that works with telescoping hydraulics. This makes them a valuable component in marine riser tensioner systems.
A fresh viewpoint: Liftgate Hydraulic Cylinder
Installation and Operation
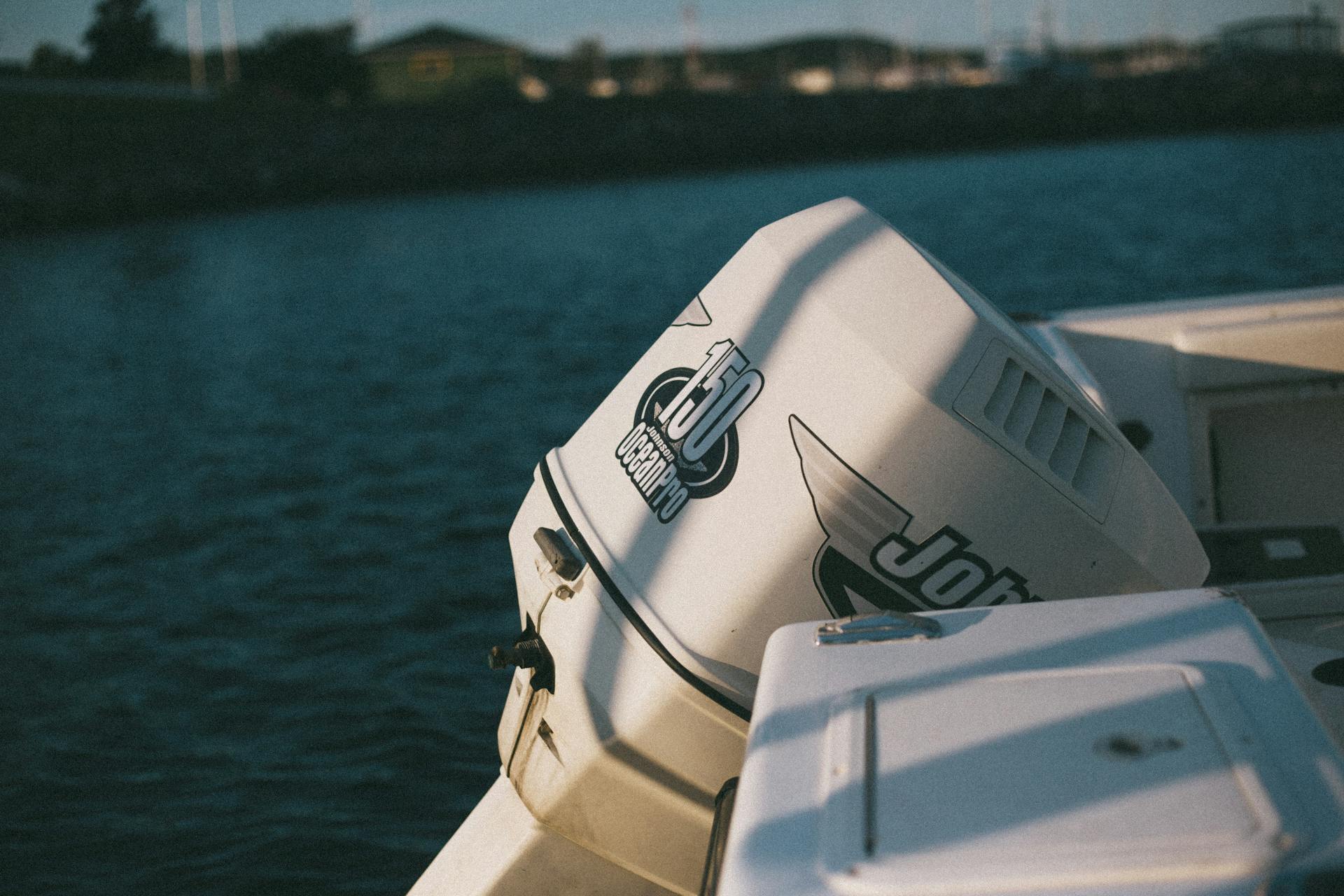
The hydraulic tensioner system requires connection before the stretching process can begin. The surface operator stretches according to the calculated preload pressure value of the hydraulic power source.
To correctly apply the required residual bolt load, the force must be applied according to the specified stretching procedure. This procedure varies depending on how the hydraulic tensioner is installed.
The tensioning procedure for 100% tensioning involves stretching according to the calculated preload pressure value of the hydraulic power source. For 50% tensioning, the process is different and requires a specific stretching procedure.
The force must be applied according to the specified stretching procedure to ensure the required residual bolt load is achieved. This is crucial for the proper functioning of the hydraulic tensioner system.
You might like: Marine Shore Power
Frequently Asked Questions
What is the function of hydraulic tensioner?
The hydraulic tensioner automatically adjusts belt or chain tension as the engine warms up, ensuring optimal tension is maintained. This prevents engine damage by preventing the belt or chain from slipping.
What is advantage of using hydraulic tensioning when installing a nut?
Using a hydraulic tensioning tool eliminates the need for forceful turning and reduces the risk of damage from friction, ensuring a safe and accurate installation process. It provides a quick and easy method for achieving high preloads on large diameter bolts.
What is the advantage of using hydraulic torquing or tensioning equipment?
Hydraulic torquing and tensioning equipment offers higher accuracy due to precise control over applied tension, unlike torque wrenches which rely on friction factors and variables. This results in more reliable and consistent bolt tightening
Sources
- https://www.hannonhydraulics.com/equipment/marine-riser-guideline-tensioners/
- https://torcstark.com/application-of-subsea-hydraulic-tensioners/
- https://www.atlascopco.com/en-us/itba/products/bolt-tightening-solutions/bolt-tensioning
- https://www.nord-lock.com/boltight/technology/
- https://www.cpi-nj.com/marine-riser-and-tensioner-system-hydraulics/
Featured Images: pexels.com