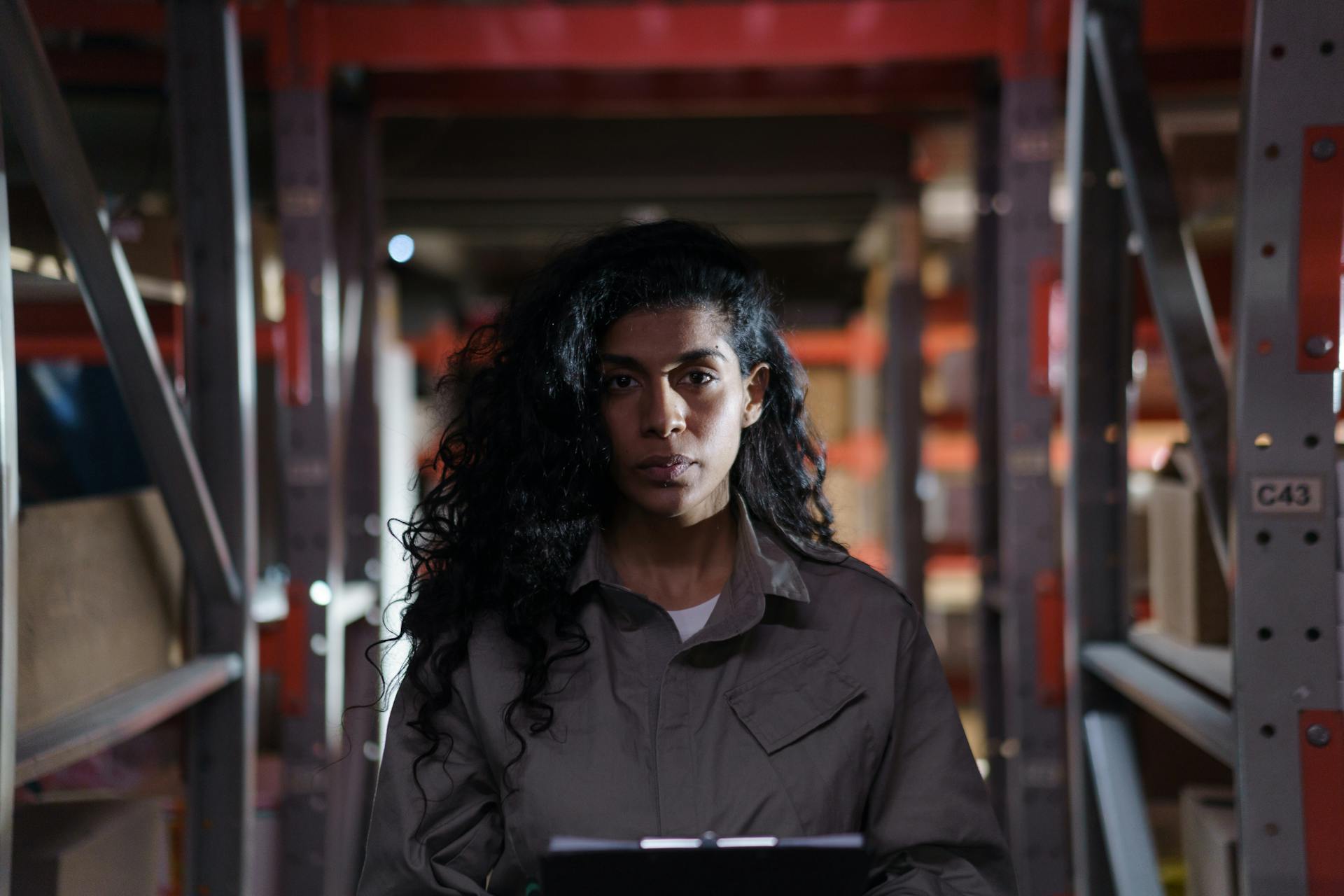
Truck transportation plays a vital role in getting goods from one place to another, ultimately leading to inventory. This process starts with manufacturers shipping products to warehouses for storage.
Manufacturers can't store their products in their factories, so they need to transport them to a separate location for inventory.
The logistics of truck transportation involve planning and coordinating the movement of goods from one place to another.
Explore further: How to Start a Transportation Business with One Truck
Truck Transportation and Inventory
Truck transportation and inventory are closely linked, and understanding this relationship is crucial for businesses that rely on trucks to deliver goods and supplies.
Delivery lead times play a significant role in inventory management, as they determine how long it takes for supplies to arrive after ordering.
Frequent deliveries can lead to higher transportation costs, which can eat into profit margins if not managed properly.
To optimize orders, it's essential to consider the truck's carrying capacity, as overloading can result in wasted space and additional costs.
See what others are reading: What Is the Just in Time Inventory System
A well-managed truck stock can help reduce unnecessary trips back to a central warehouse and minimize the time wasted searching for items.
Here are some key statistics on the benefits of effective truck stock management:
By maximizing truck shipments, businesses can ship the same volume on fewer trucks, resulting in significant cost savings and increased operational efficiency.
Strategies for Balance
Predicting future demand is key to navigating the truck-inventory relationship. Analyze past sales data and consider upcoming promotions or seasonal trends to estimate how much stock you'll need.
Having a buffer of essential items on hand helps avoid stockouts in case of unexpected delays in deliveries. Think of it as an insurance policy for your inventory – a safety net to catch you if a delivery arrives a little later than expected.
Consolidating small orders into larger ones can reduce transportation costs. This might involve working with suppliers or collaborating with other businesses in your area to share truckloads.
Maintaining clear communication with your suppliers is crucial. Knowing their lead times and any potential delays helps you adjust your inventory levels accordingly.
Here are some practical tips to help you balance truck transportation and inventory:
- Use demand forecasting to predict future demand.
- Keep a safety stock of essential items on hand.
- Consolidate small orders into larger ones to reduce transportation costs.
- Maintain clear communication with your suppliers.
Truck Tonnage Index Importance
Operational efficiency is a major benefit of tracking the Truck Tonnage Index, as it helps companies like yours optimize their truck shipments and reduce transportation costs. By shipping the same volume on fewer trucks, companies can utilize up to 98% of a truck's capacity.
Reducing transportation costs is a significant advantage, and a case study showed that a company saved 10.5% on yearly transportation costs, along with an additional 4.6% savings with the establishment of three new warehouses.
A well-managed truck stock is crucial for meeting customer expectations, and the Truck Tonnage Index helps ensure that technicians have the necessary tools and parts to complete repairs in one visit. This reduces the necessity for additional trips to supply stores and significantly enhances inventory efficiency.
Effective truck stock management also leads to customer satisfaction, which is a key factor in fostering long-term customer relationships. By meeting and often exceeding customer expectations, companies can build trust and loyalty with their customers.
Suggestion: Power Only Trucking Companies
Inventory Management Best Practices
Effective inventory management is crucial to minimize stockouts and overstocking. This can be achieved by implementing a first-in-first-out (FIFO) inventory system, where the oldest items are sold or used first.
Proper labeling and tracking of inventory is essential. As mentioned earlier, companies can use barcodes or RFID tags to quickly identify and locate specific items.
Regular inventory audits help identify discrepancies and prevent overstocking. For instance, a company may discover that they have more stock than expected due to incorrect inventory counts.
Accurate forecasting is vital to determine the right amount of stock to hold. Companies can use historical sales data and seasonal trends to make informed decisions about inventory levels.
Automating inventory management processes can streamline operations and reduce errors. By using software to track inventory levels and automate ordering, companies can save time and resources.
See what others are reading: Transportation System Management
Maximizing Efficiency
Operational efficiency is at the heart of truck stock management, streamlining operations and reducing the time wasted on searching for items or making unnecessary trips back to a central warehouse.
Technicians can swiftly locate the tools and parts they require, leading to more jobs completed within a given timeframe. This efficiency is crucial in the service industry where time is of the essence.
Mismanaged truck stock can lead to costly emergency orders or expedited shipping fees, but an effective truck stock management system strikes the right balance, ensuring that resources are utilized optimally.
By maximizing truck shipments, companies can ship the same volume on fewer trucks by utilizing up to 98% of a truck's capacity, thus significantly reducing transportation costs.
A case study highlighted a potential savings of 10.5% on yearly transportation costs along with an additional 4.6% savings with the establishment of three new warehouses, showcasing the substantial cost savings that can be achieved through smart truck stock management strategies.
Here are some key statistics on the benefits of maximizing efficiency in truck stock management:
Truck Stock Management
Delivery lead times are a crucial factor in inventory management. You need to consider how long it takes for supplies to arrive after ordering them, to avoid running out of stock before the next delivery.
A truck's carrying capacity is limited, just like a suitcase. You want to optimize your orders to maximize the space without going over the weight limit.
Transportation costs can add up quickly with frequent deliveries. Finding the right balance between ordering enough and keeping costs in check is vital.
To better understand truck stock management, consider the following key factors:
Frequently Asked Questions
Is transportation included in inventory?
Yes, transportation costs are included in inventory carrying costs. This expense is one of the many factors that contribute to the overall cost of holding unsold goods.
How does transit inventory come about?
Transit inventory comes about when a seller ships products to a customer, but the goods have not yet been received. This occurs during the transportation process, when products are in transit from the seller's location to the customer's location.
Sources
- https://trucksbybenko.com/truck-transportation-inventory/
- https://www.freightwaves.com/news/transportation-caving-under-weight-of-inventory
- https://fastercapital.com/topics/importance-of-the-truck-tonnage-index-for-inventory-management.html
- https://getply.com/blog/truck-stock-management-basics-auditing-bardcoding-and-organization/
- https://www.cogisticstransportation.com/expedited-freight-shipping-its-role-in-supporting-just-in-time-manufacturing/
Featured Images: pexels.com