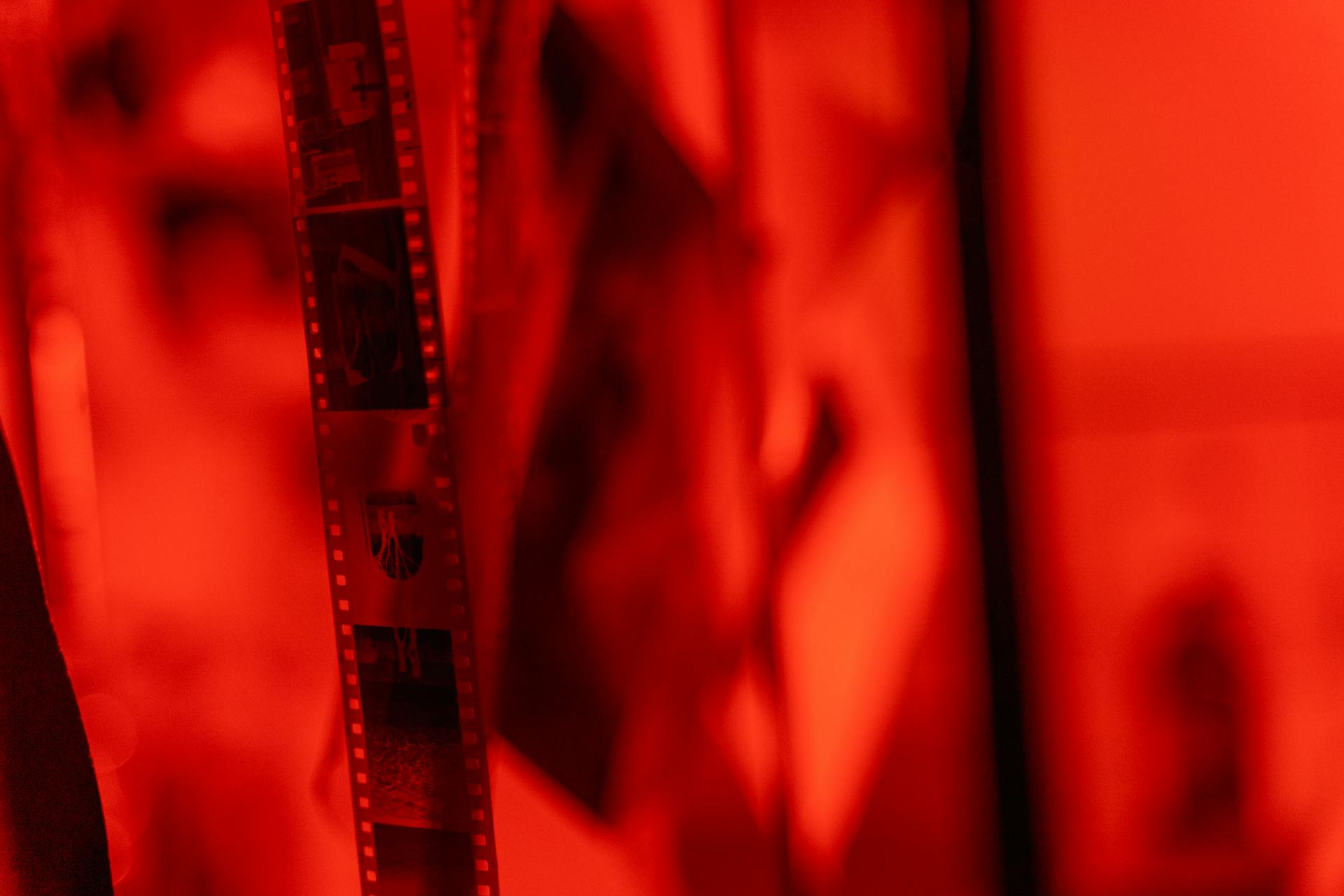
High density polyethylene film is a versatile and widely used material in various industries. It has a high density of around 0.94-0.97 g/cm3.
One of its key properties is its high tensile strength, which can range from 6,000 to 12,000 psi. This makes it suitable for applications that require durability and resistance to stress.
HDPE film is also known for its low permeability to gases and water, making it an excellent choice for packaging and wrapping applications. It can withstand exposure to water and chemicals without degrading.
Its high melting point of around 220-250°F (104-121°C) also makes it a good option for applications that require heat resistance.
Advantages
HDPE film is a versatile material with many advantages. HDPE is resistant to many industrial and live chemicals and can withstand the corrosion of strong oxidising agents, organic solvents and acid-based salts.
One of the most notable benefits of HDPE film is its water resistance. HDPE is waterproof and non-hygroscopic, meaning it doesn't attract water. This makes it an ideal choice for packaging and other applications where moisture is a concern.
HDPE film is also incredibly durable. It's four to five times harder than LDPE-film and very strong and impact-resistant. This means it can withstand rough handling and harsh environments.
In addition to its physical properties, HDPE film is also non-toxic and odorless. This makes it suitable for food packaging and clothing.
Properties and Additives
High density polyethylene film can be customized with various additives to enhance its properties.
Color pigments can be added to the film to change its color. This is a simple way to make the film more visually appealing or to match a specific brand identity.
The addition of carbon fillers to the film can increase its conductivity, making it suitable for applications where electrical properties are crucial.
UV stabilizers are often added to resist sunlight damage and extend the film's lifespan.
Slip/anti-block agents can be added to improve the film's slipping and blocking properties, reducing the risk of film to film sticking.
Anti-static additives can be added to prevent static buildup, which can damage electronic components or cause other issues.
Some HDPE films are coated with silicone or treated with corona to enhance their properties and performance.
If this caught your attention, see: Anti Static Vinyl Record Sleeves
Properties of
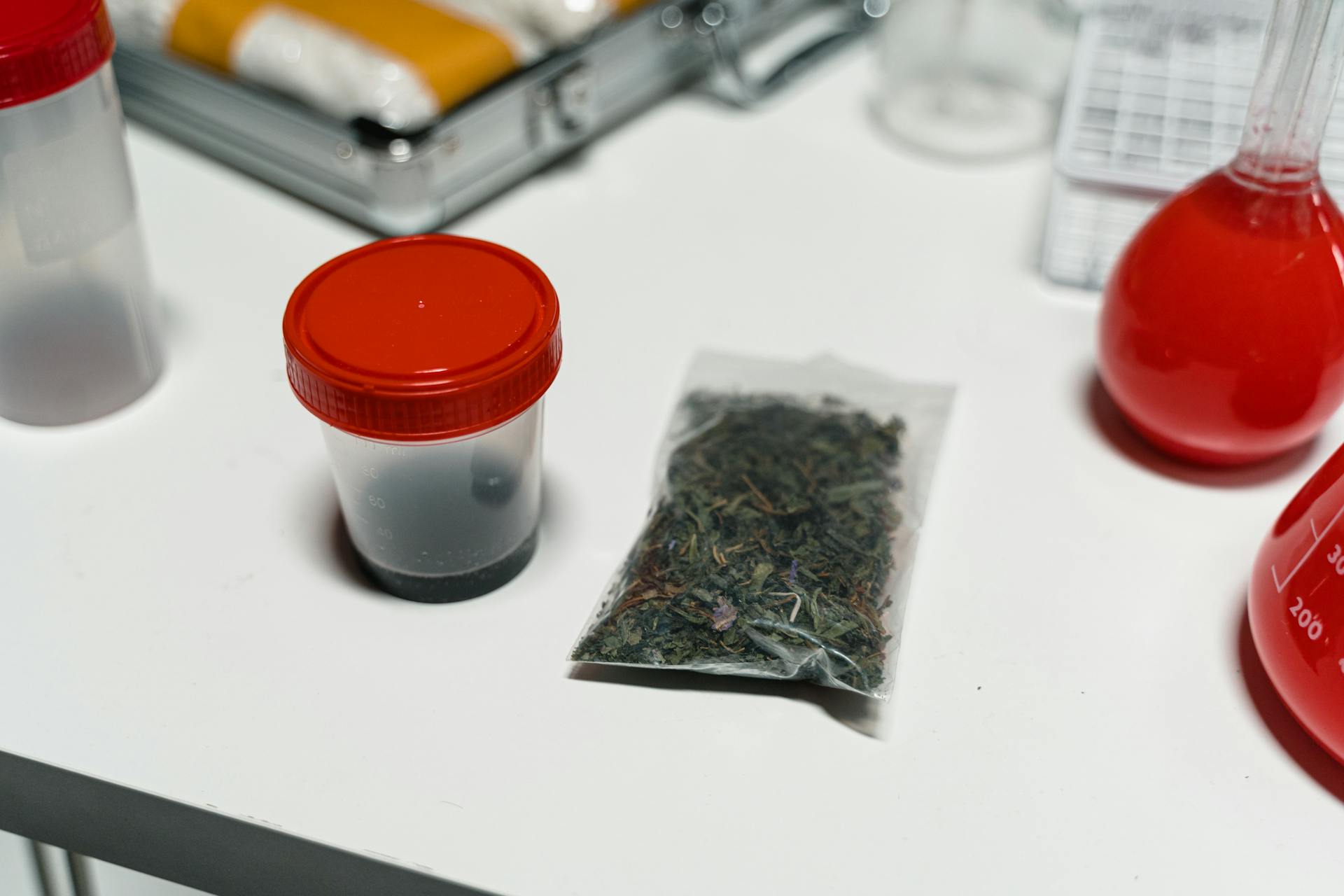
High density polyethylene (HDPE) is a machinable thermoplastic known for its high strength to density ratio. It's incredibly light and durable.
HDPE is high impact, meaning it can withstand a lot of stress without breaking. It also won't splinter or rot, making it a great choice for outdoor use.
HDPE has very high impact strength, abrasion, stain, moisture, and odor resistance. This makes it perfect for use in food processing and other industries where cleanliness is crucial.
HDPE has a low coefficient of friction, which makes it easy to cut, weld, thermoform, and machine. It's also resistant to moisture and water, including saltwater.
HDPE is stronger and stiffer than low density polyethylene (LDPE), but its impact strength is not as good at low temperatures.
Expand your knowledge: High Impact Polystyrene
Plastic Additives & Treatments
Plastic Additives & Treatments can greatly enhance the properties of plastic films. Color Pigments can be added to HDPE film to change its color.
Carbon Fillers can be used to increase the conductivity of the film. This is especially useful in applications where electrical conductivity is required.
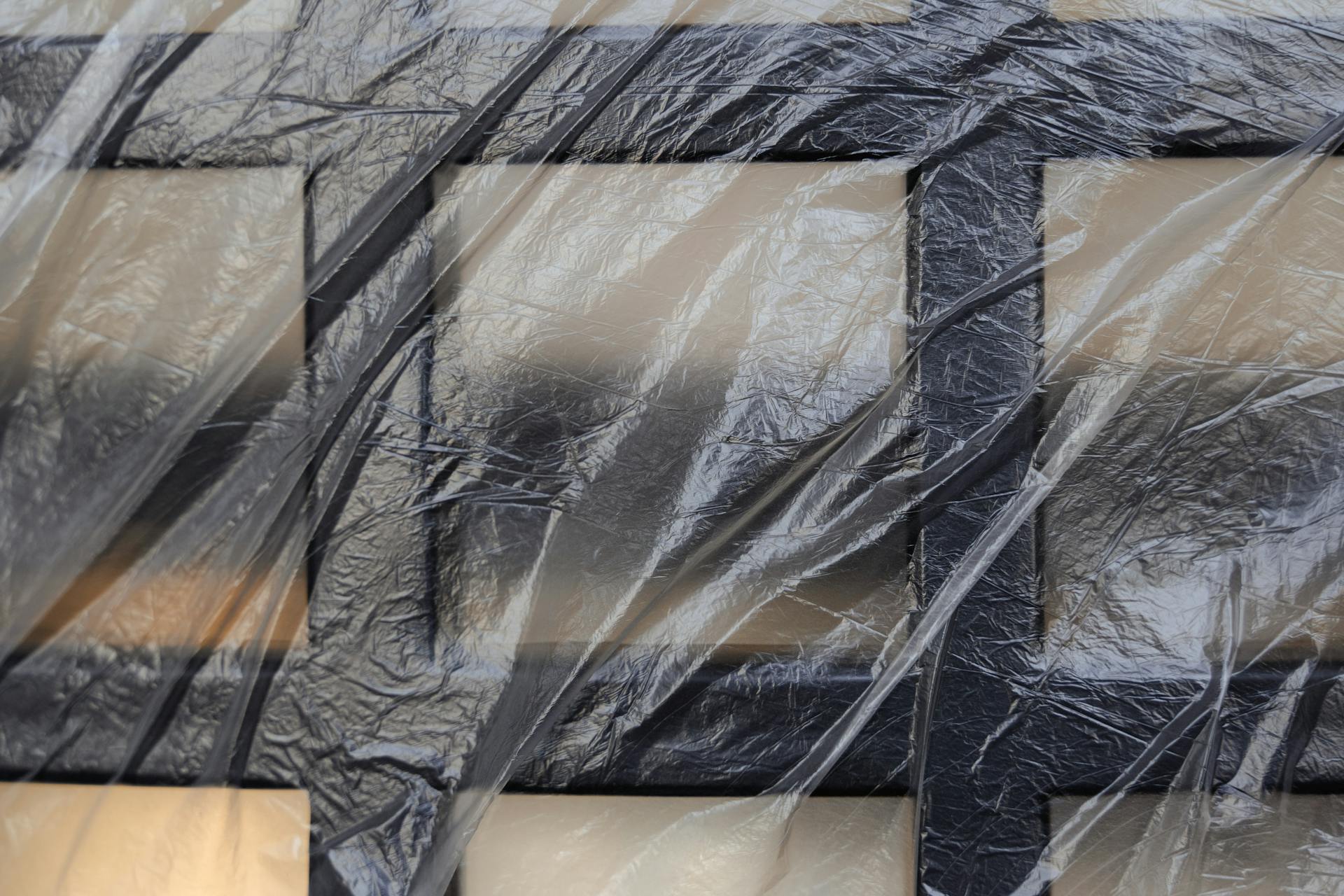
UV Stabilizers are added to resist the effects of sunlight on the film. This helps to prevent degradation over time.
Slip/Anti-block Agents are used to improve the slipping and blocking properties of the film. This is important in applications where the film needs to move smoothly over other surfaces.
Anti-Static agents can be added to resist static buildup on the film. This is useful in applications where static electricity could cause problems.
Some plastic films are also coated with silicone or treated with corona treatment.
Applications and Uses
High-density polyethylene film is a versatile material with a wide range of applications. It's used in the automotive industry, construction sealing strips, and even in medical products.
In the packaging industry, HDPE film is widely used for producing bags, wrappers, and geotextiles for food and non-food products. This is because of its durability and resistance to moisture and chemicals.
HDPE films are also used in agriculture for mulching, which helps in weed control, conserving soil moisture, and regulating temperature. This is a game-changer for outdoor farming practices.
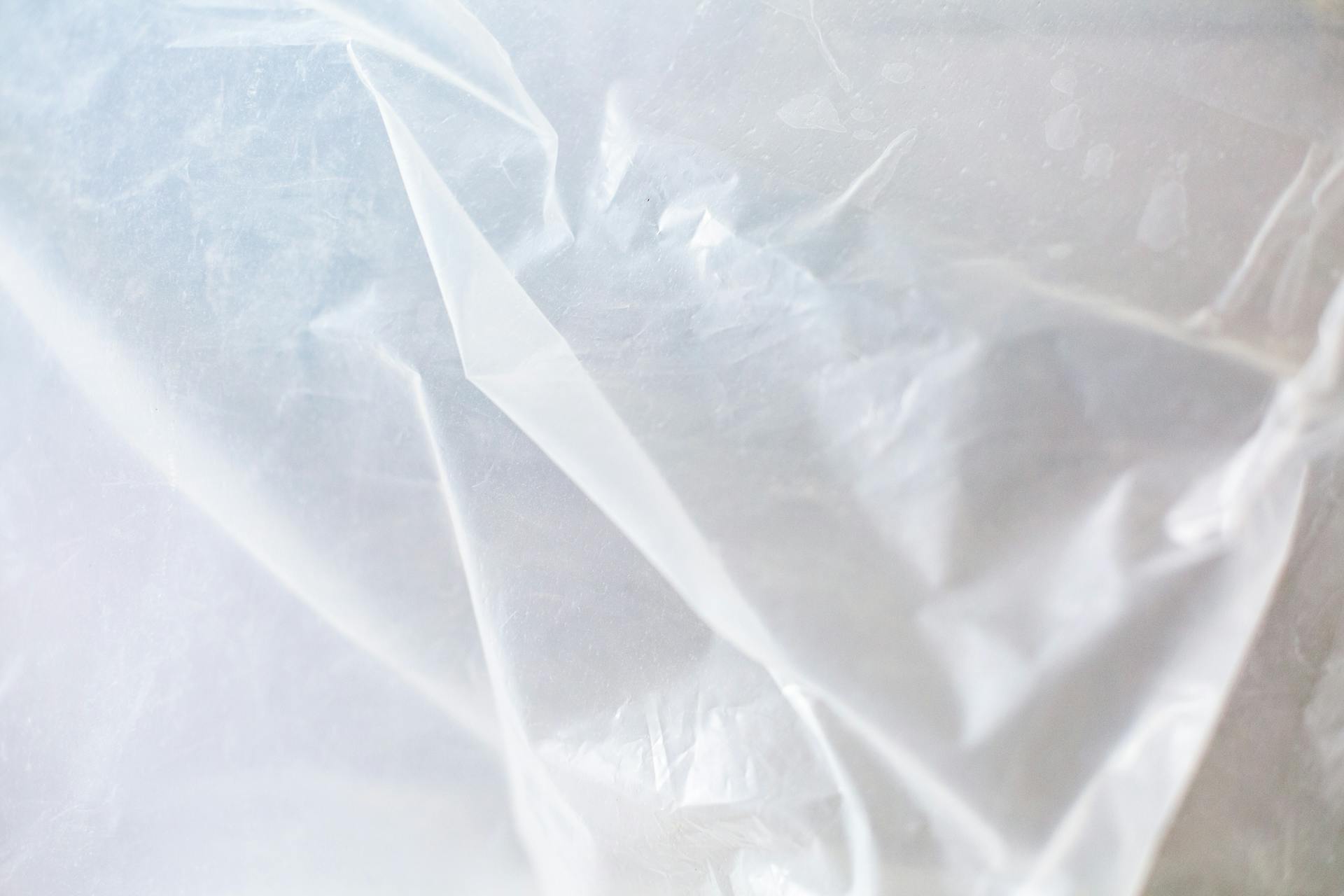
Construction and civil engineering also rely heavily on HDPE film, which acts as a moisture barrier in building elements. It's used in vapor and damp proof membranes to protect structures from mold and mildew formation.
Industrial and manufacturing sectors use HDPE films for surface protection, safeguarding products from scratches, dust, and other environmental damage during storage and transportation.
Here are some of the most common applications of high-density polyethylene film:
HDPE films are also used in the production of plastic sacks for carrying groceries, as their lightweight yet sturdy design allows for safe transportation of various items without tearing or leaking.
Choosing and Working with
Choosing the right thickness of HDPE film can greatly impact its performance. Thicker films provide enhanced durability and are ideal for heavy-duty or long-term exposures, such as agricultural films or industrial packaging.
Film width is also an important consideration, as it affects the scale of the project and ease of handling. Typically, HDPE films come in standardized widths ranging from 1 to 4 meters, with industrial rolls extending much longer.
For large agricultural fields or construction covers, a wider film can reduce the number of joints while achieving a seamless coverage.
Consider reading: Industrial Stretch Wrap
Connecting Pieces
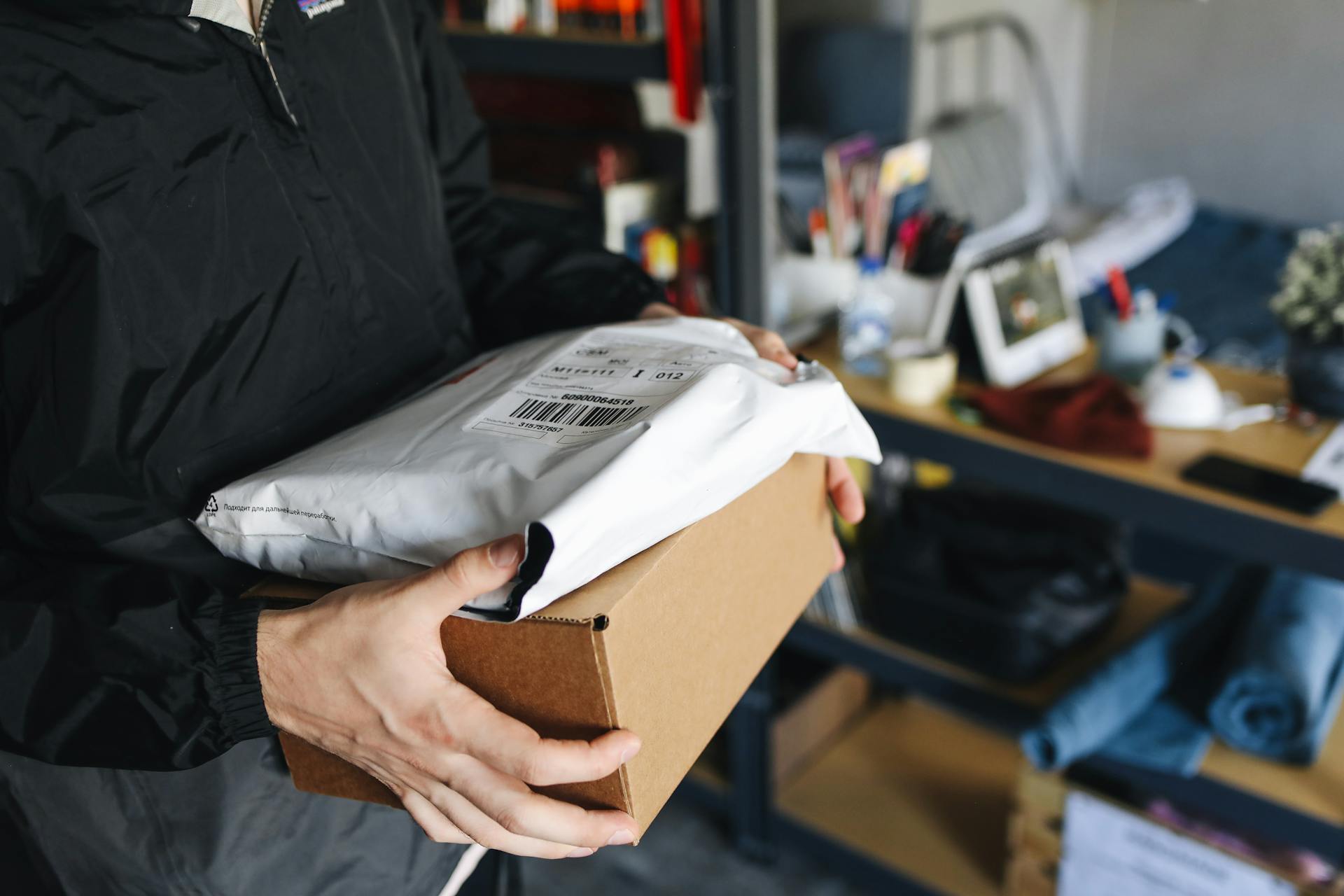
Connecting pieces is a crucial step in your project, and it's great that you're thinking ahead.
You have two main options for connecting multiple pieces of HDPE together. One method is to overlap the HDPE and use our double-sided seam tape to connect the two pieces.
Butt joining is another viable option, which involves connecting the ends of the pieces together using our 17 mil single-sided seam tape. This creates a solid connection that's perfect for a variety of projects.
A unique perspective: Poly Vinyl Chloride Packaging Tape Printing Market
How to Choose
Choosing the right high-density polyethylene (HDPE) film for your project can be a daunting task, but it doesn't have to be. First and foremost, consider the thickness of the film - a thicker film provides enhanced durability, making it ideal for heavy-duty or long-term exposures.
The thickness of the film is crucial, as it influences the rigidity, strength, and impermeability to gases or liquids. Thicker films are perfect for industrial packaging or agricultural films, while thinner films are better suited for day-to-day tasks like grocery bags or food packaging.
A fresh viewpoint: Corrugated Board Thickness
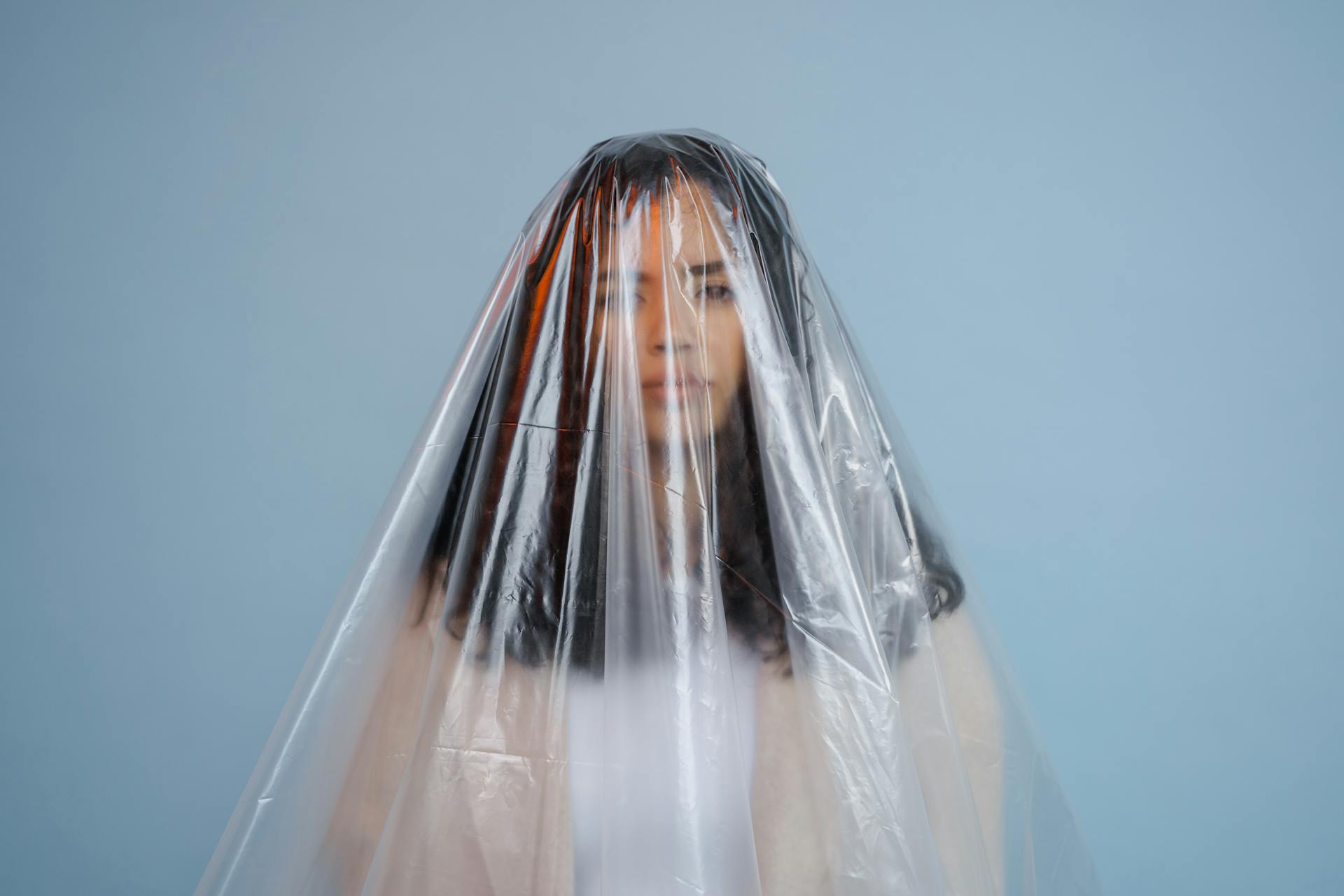
Film width is another important factor to consider. HDPE films typically come in standardized widths ranging from 1 to 4 meters, with industrial rolls extending much longer. For large projects, a wider film can reduce the number of joints and achieve a seamless coverage.
The density of the film also plays a significant role. High-density polyethylene offers superior strength, chemical resistance, and UV protection, making it ideal for outdoor and industrial applications. Low-density polyethylene, on the other hand, provides more flexibility at the expense of strength, making it unsuitable for carry bags or food packaging.
The surface finish of the film is also worth considering. HDPE films can be smooth or embossed, with textured films ideal for construction or industrial uses where a non-slip surface is required. Smooth films, on the other hand, are suitable for packaging purposes where a seamless finish is a requirement.
Here are some key factors to consider when choosing an HDPE film:
- Thickness: Thicker films for heavy-duty or long-term exposures, thinner films for day-to-day tasks
- Film width: Wider films for large projects, narrower films for smaller projects
- Density: High-density polyethylene for outdoor and industrial applications, low-density polyethylene for flexibility
- Surface finish: Textured films for construction or industrial uses, smooth films for packaging purposes
- Tensile strength: Films with longer tensile strength for applications that undergo constant pulling or heavy loads
- Color: Clear films for light penetration, opaque or black films for light exclusion, blue or green films for energy trapping in greenhouses
Types and Features
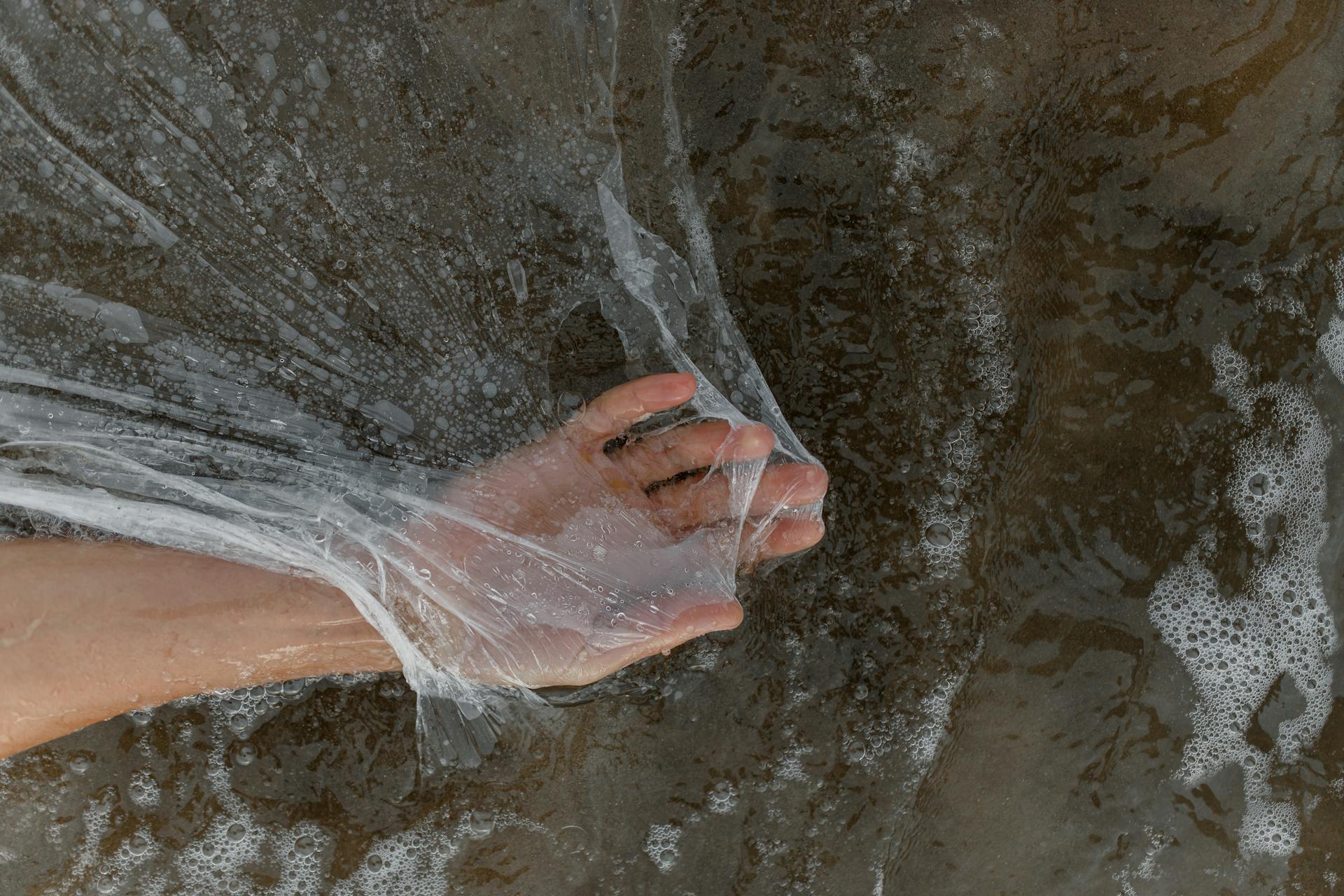
High-density polyethylene film comes in a variety of forms, each with its own unique properties and applications.
Clear HDPE film is known for its clarity and strength, making it ideal for packaging and industrial applications like greenhouse covers and construction moisture barriers.
Colored HDPE film is manufactured by adding pigments to the plastic resin, providing product branding and protection against UV exposure.
Common colors include blue, red, and black, each serving distinct purposes like agricultural uses and industrial settings.
Opaque HDPE films are ideal for applications requiring privacy or light blockage, commonly used in construction sites, security applications, and as packaging materials.
Textured HDPE film provides a better grip or enhances the rigidity of the final product, often used in furniture, partitions, or HDPE film bags.
UV-resistant HDPE film is designed with specific additives that absorb or reflect harmful UV rays, prolonging the life of products exposed to sunlight.
Here's a breakdown of the different types of HDPE film:
- Clear HDPE Film: ideal for packaging and industrial applications
- Colored HDPE Film: provides product branding and UV protection
- Opaque HDPE Film: ideal for applications requiring privacy or light blockage
- Textured HDPE Film: provides a better grip or enhances rigidity
- UV-Resistant HDPE Film: prolongs the life of products exposed to sunlight
Frequently Asked Questions
What is the difference between LDPE and HDPE film?
LDPE film is more flexible and transparent, while HDPE film is more rigid and opaque. The choice between LDPE and HDPE depends on the application, with LDPE suitable for injection molding and HDPE for additive manufacturing.
What are the disadvantages of polyethylene film?
Polyethylene film has poor mechanical properties, including low tensile strength and poor creep resistance. However, it does offer good impact resistance.
Sources
- https://www.kivo.nl/en/knowledge-base/what-is-hdpe-film/
- https://www.profabricsupply.com/products/hdpe-roll-stock-polyethylene-plastic-film
- https://www.cheeverspecialty.com/products/films/hdpe-film
- https://taminkalatak.com/product/high-density-polyethylene-film/
- https://www.alibaba.com/showroom/high-density-polyethylene-hdpe-film.html
Featured Images: pexels.com