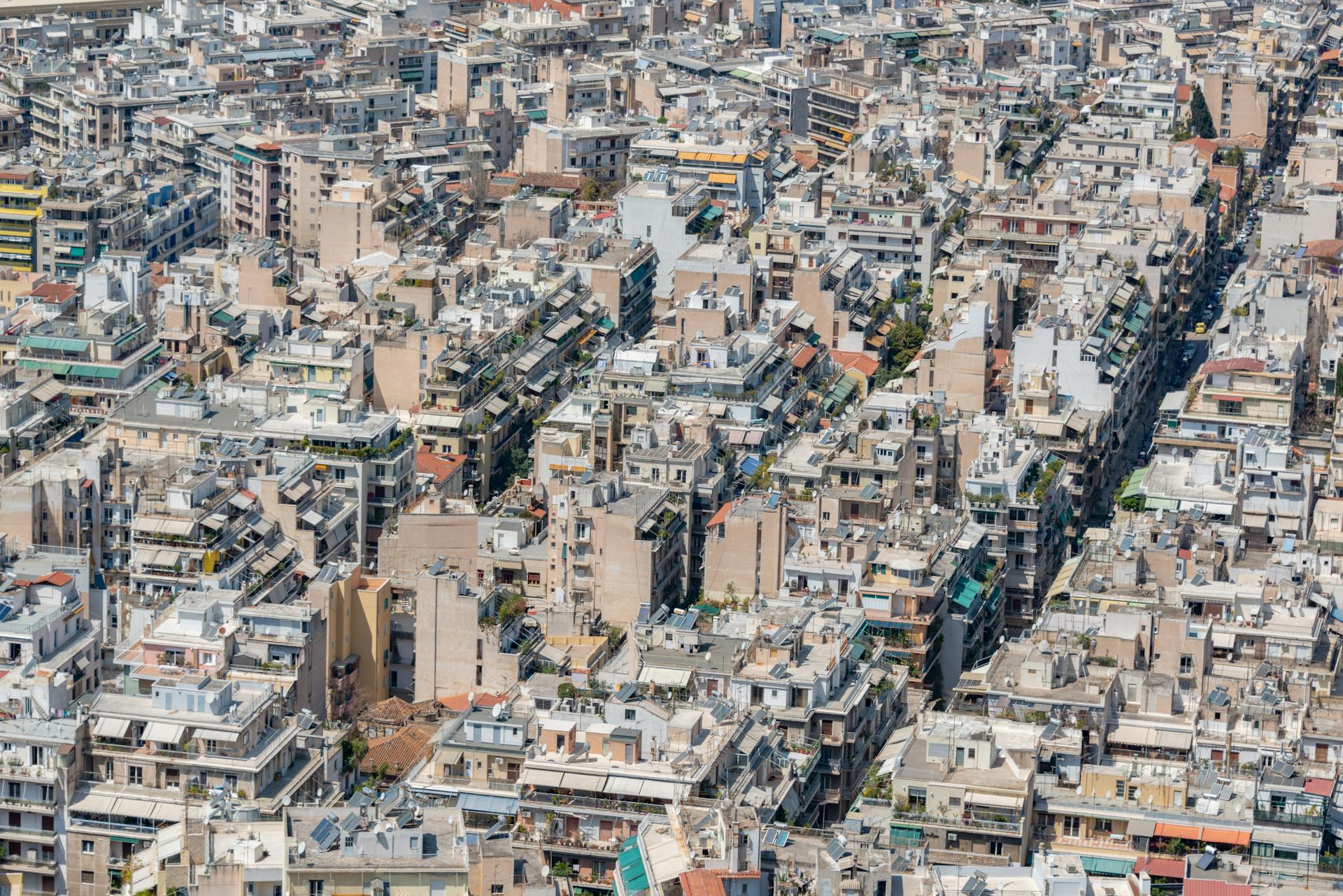
High density packing foam is a game-changer for businesses that ship fragile items, as it provides excellent protection and can be cut to fit specific shapes and sizes.
This type of foam is made from a unique blend of materials that make it incredibly durable and resistant to compression.
High density packing foam is also a cost-effective solution for businesses, as it can be reused multiple times and is often more affordable than other types of packing materials.
By investing in high density packing foam, businesses can reduce their shipping costs and minimize damage to their products, ultimately saving money and increasing customer satisfaction.
On a similar theme: Foam Packaging Materials
Types of Foam
High-density packing foam comes in various types, each selected according to the product's fragility, shipping distance, and the environment within which it is going to be shipped.
Polyurethane foam is one of the most common types of high-density foam, with a density of 1.3 to 1.8 pounds per cubic foot. It's valued for its durability and resilience, and can even compress and return to its original shape with excellent cushioning.
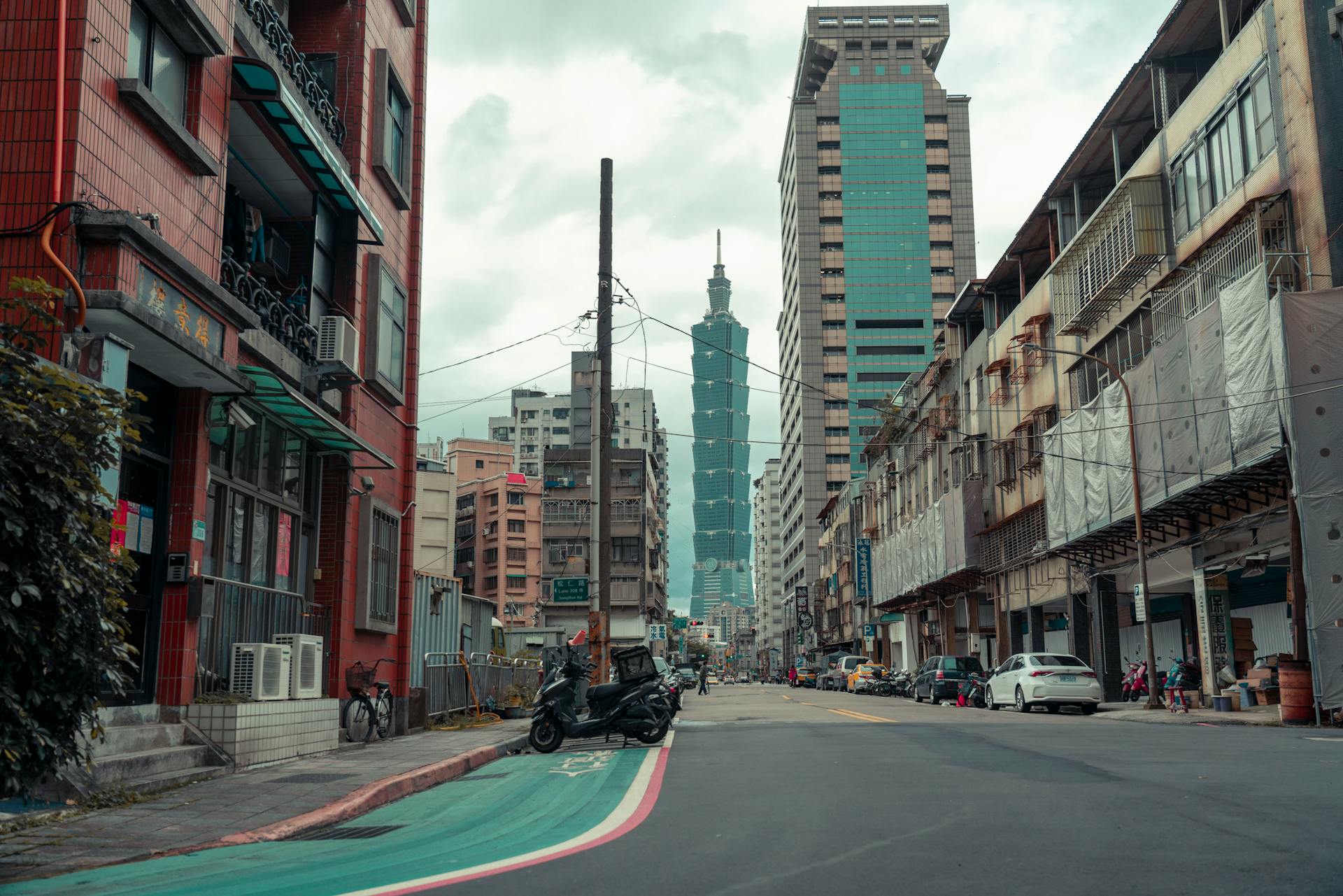
High-density polyethylene foam is renowned for its toughness and chemical resistance, with a density that ranges from 2.0 to 3.0 pounds per cubic foot. This makes it ideal for heavy-duty applications.
Cross-linked polyethylene foam is made by heating and pressurizing polyethylene foam, creating a dense, cross-linked cell structure that enhances its strength and longevity. It retains excellent cushioning properties even under extreme conditions.
Ethylene vinyl acetate (EVA) foam comes with a density of 1.2 to 2.0 pounds per cubic foot, and is widely appreciated for its flexibility and UV resistance properties. This makes it ideal for packaging outdoor gear and items prone to color fading.
Here's a quick rundown of the types of high-density packing foam:
Designs and Customization
High-density packing foam comes in various designs to suit specific items and provide optimal protection. Solid sheets are a cost-effective way to protect flat or rectangular-shaped products, such as plates, pictures, or windows.
Die-cut shapes are preferred for high-value products as they provide the best form of protection and can hold items like electronics securely in place, reducing movement during transit.
See what others are reading: Pu Foam Products
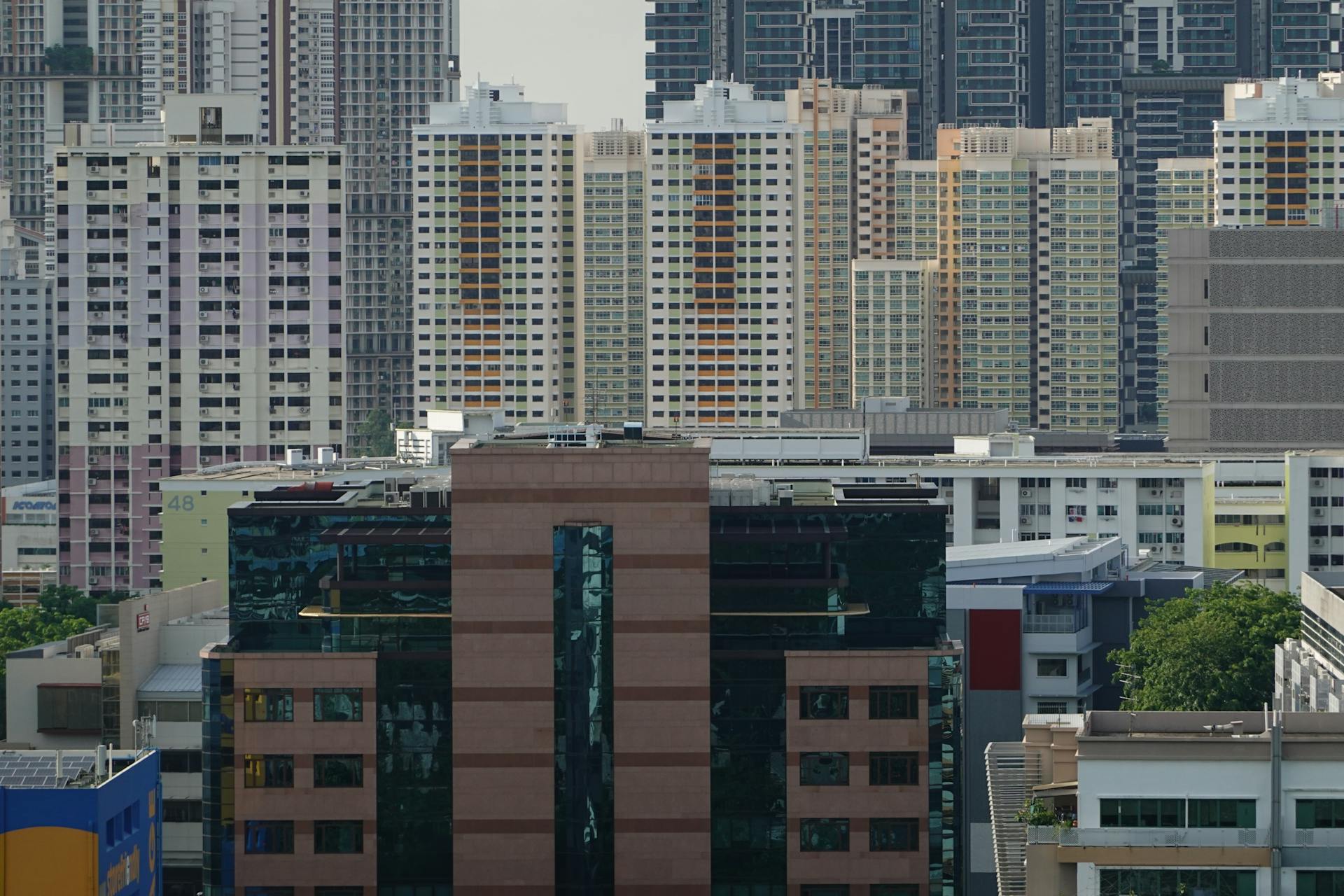
Egg-crate foam has a unique, wavy surface that provides ventilation and extra cushioning beneath fragile items, minimizing shock by distributing impact energy uniformly.
High-density box or crate foam is fitted inside hard cases or crates and provides a rigid form of support for heavy goods, integrating a cushioning effect and being water-resistant.
Anti-static foam helps prevent electrostatic discharge (ESD) from affecting electronic components and is often used in tandem with other types of packing.
High-density packing foam can be customized in various ways, including cut-to-size options, custom inserts, layering options, die-cutting, color and textures, and anti-static properties.
Cut-to-size foam can be cut using a sharp blade or laser cutter to meet precise requirements of packaging a particular product.
Custom inserts can be molded or carved to create custom-shaped inserts that provide exceptional support for fragile items, such as electronics, glassware, and other delicate products.
Layering options allow for increased protection by adding additional layers, which is particularly critical when shipping products that require extra care in handling.
Die-cutting can create unique shapes or patterns in high-density packing foam, making it useful for both functional and aesthetic properties.
Intriguing read: Foam Package Inserts
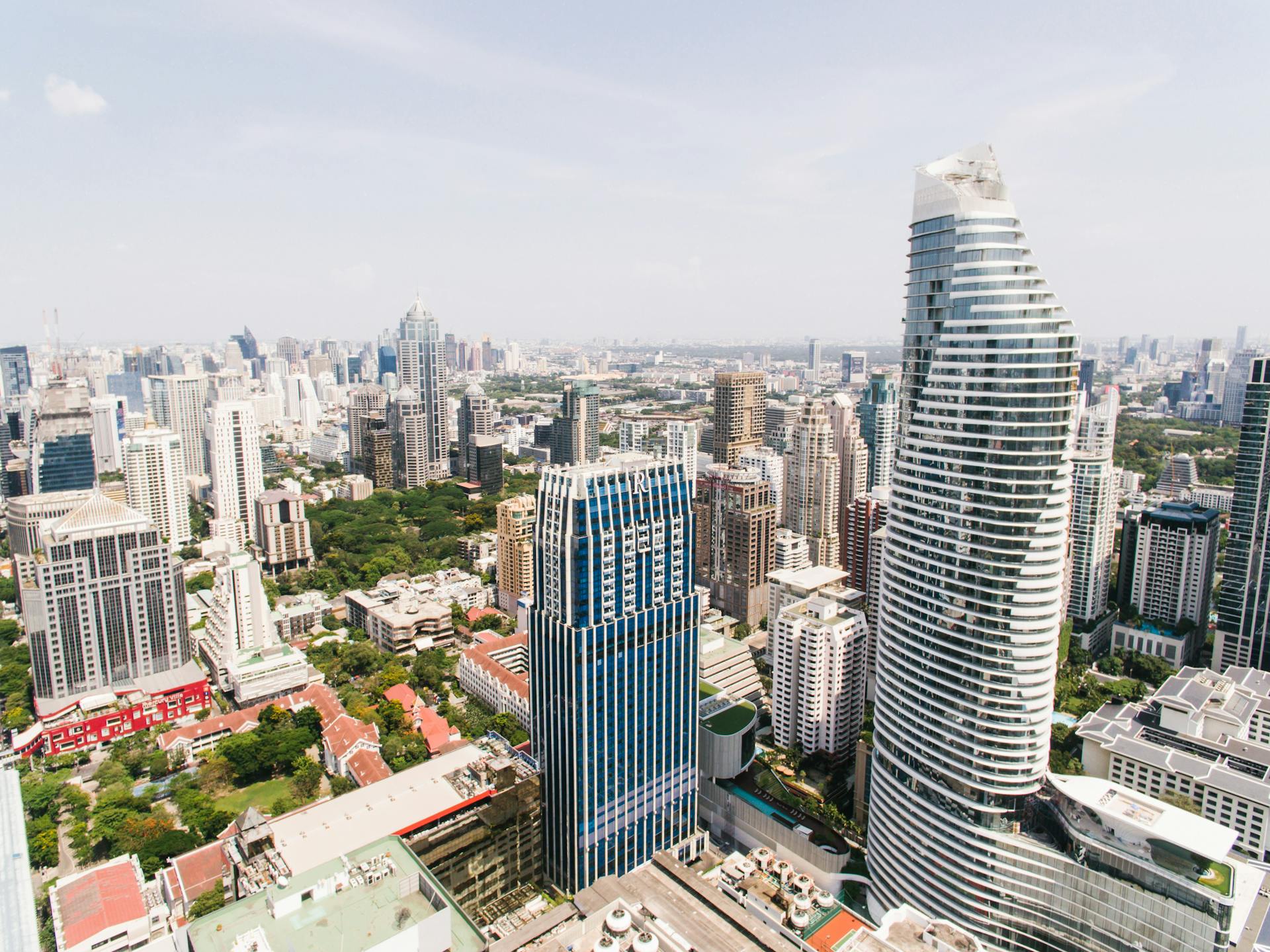
High-density packing foam is typically available in cream or white, but customization options include different colors or textures to improve the product's overall visual appeal or match the company's brand colors.
Various surface textures can enhance grip or improve impact absorption, including smooth, wavy, or "egg crate" textures.
Custom high-density packing foam can be embedded with anti-static properties to eliminate the risk of electrostatic discharge, which damages sensitive components and is required by most wholesalers.
Here are some common designs of high-density packing foam:
Uses and Applications
High-density packing foam has a multitude of uses, making it a versatile and essential material in various industries.
Its primary use is to pack fragile items such as glassware, ceramics, electronics, and other sensitive products, providing superior cushioning that absorbs shocks and vibrations effectively during transit.
High-density foam is also commonly used in warehouses and retail environments, reducing replacement costs and improving customer satisfaction due to receiving undamaged products.
In industrial settings, this type of foam is employed to protect components and machinery during transportation and storage, often customized to fit specific parts or equipment.
It is also used in aerospace and automotive sectors, where precision and reliability are crucial.
This foam can be tailored to create custom packaging solutions that suit specific needs, making it a quick fix whenever gaps have to be filled in the packaging.
Here are some of the key uses of high-density packing foam:
- Shipping fragile items
- Protective packaging in retail
- Industrial applications
- Custom packaging solutions
- Cushioning in storage
- Art and antiques preservation
Uses of
High-density packing foam is a versatile material with a wide range of uses, making it a go-to choice for many industries.
Shipping fragile items is one of the primary uses of high-density packing foam. It provides superior cushioning that absorbs shocks and vibrations effectively during transit, minimizing the risk of breaking or damaging items.
Protecting items from damage during handling and storage is also a key application of high-density foam. It's commonly used in retail settings as protective packaging, safeguarding electronic devices, appliances, and other fragile merchandise.
A unique perspective: Pu Foam Uses
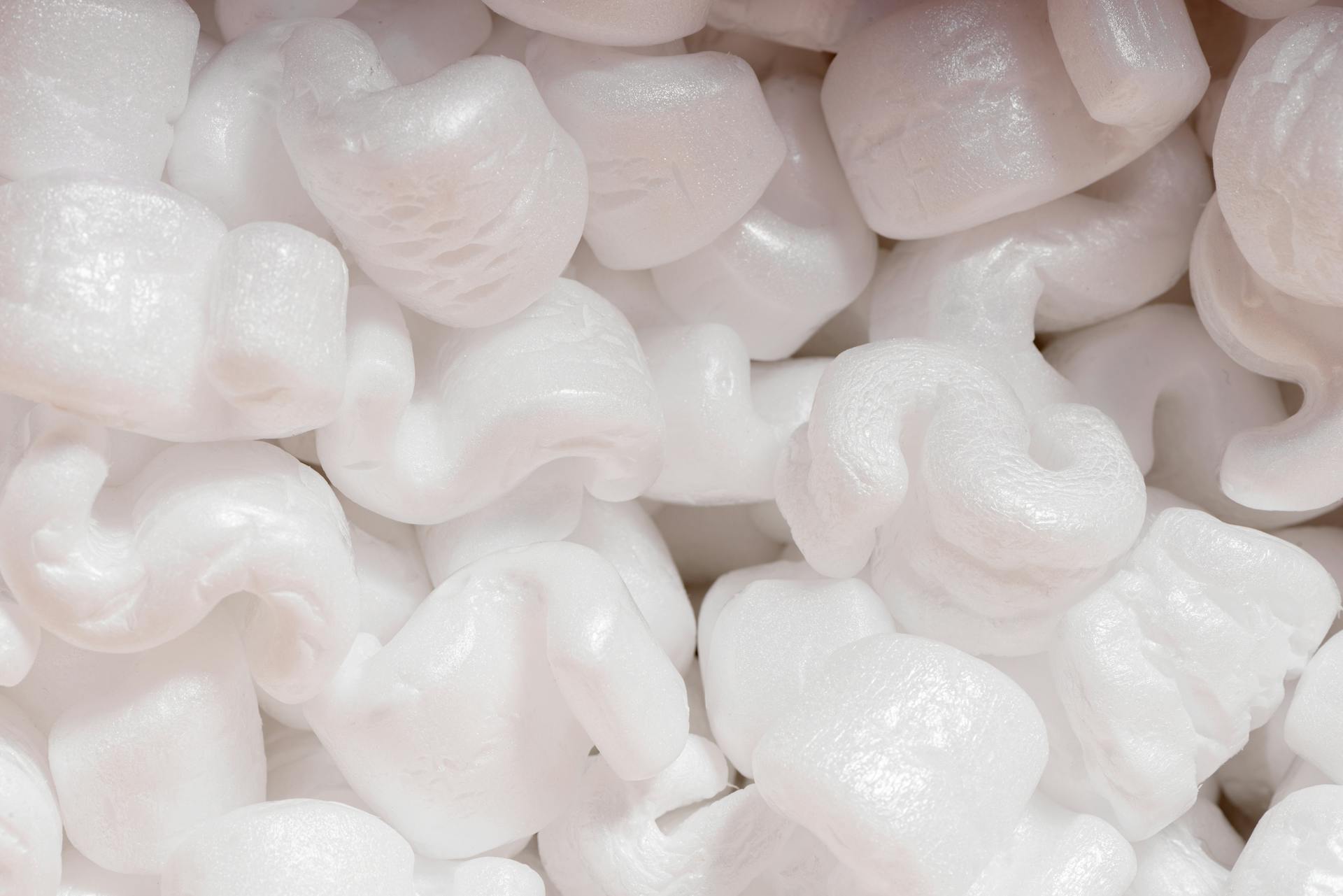
In industrial settings, high-density foam is employed to protect components and machinery during transportation and storage. It's often customized to fit specific parts or equipment, ensuring that heavy items remain stable and secured amid movements.
High-density packing foam can be tailored to create custom packaging solutions that suit specific needs. This versatility makes it a quick fix whenever gaps have to be filled in the packaging.
Here are some of the key uses of high-density packing foam:
- Shipping fragile items
- Protective packaging in retail
- Industrial applications
- Custom packaging solutions
- Cushioning in storage
- Art and antiques preservation
High-density foam provides cushioning and is frequently used in long-term storage solutions, helping to protect items from moisture and dust. It also minimizes the risk of damage due to shifting or settling in warehouses.
Conservation professionals use high-density foam to create custom-fit inserts for cases, keeping valuable items safely cushioned from shocks and impacts. This makes it invaluable for preserving delicate items like artwork, antiques, and musical instruments.
Sample Pack
Trying out different types of foam before investing in a specific type can be a game-changer. Our High Density Foam Sample Pack includes 10 different types of foam, each measured at 5” x 5” x 2".
This sample pack is a great way to get a feel for the different foams, and it's a cost-effective way to test them out.
Key Considerations
Choosing the right high-density packing foam is crucial to ensure your products arrive safely. The level of protection required by the product is the first thing to consider.
Other factors to consider include whether the product will be shipped or stored, its weight, and the duration of transit. The weight and transit time of the product can significantly impact the type of foam needed.
Regular cleaning with mild soap and water is effective in prolonging the lifespan of high-density packing foam. It's also essential to keep the foam away from direct sunlight and extreme temperatures.
Foam vs Low-Density Foam
Foam is a type of material that can be made from a variety of sources, including plastic and natural fibers.
Low-density foam, on the other hand, is a specific type of foam that is designed to be lightweight and flexible.
Foam is often used in applications where a soft, cushioning material is needed, such as in furniture and packaging.
Here's an interesting read: White Foam Packing Material
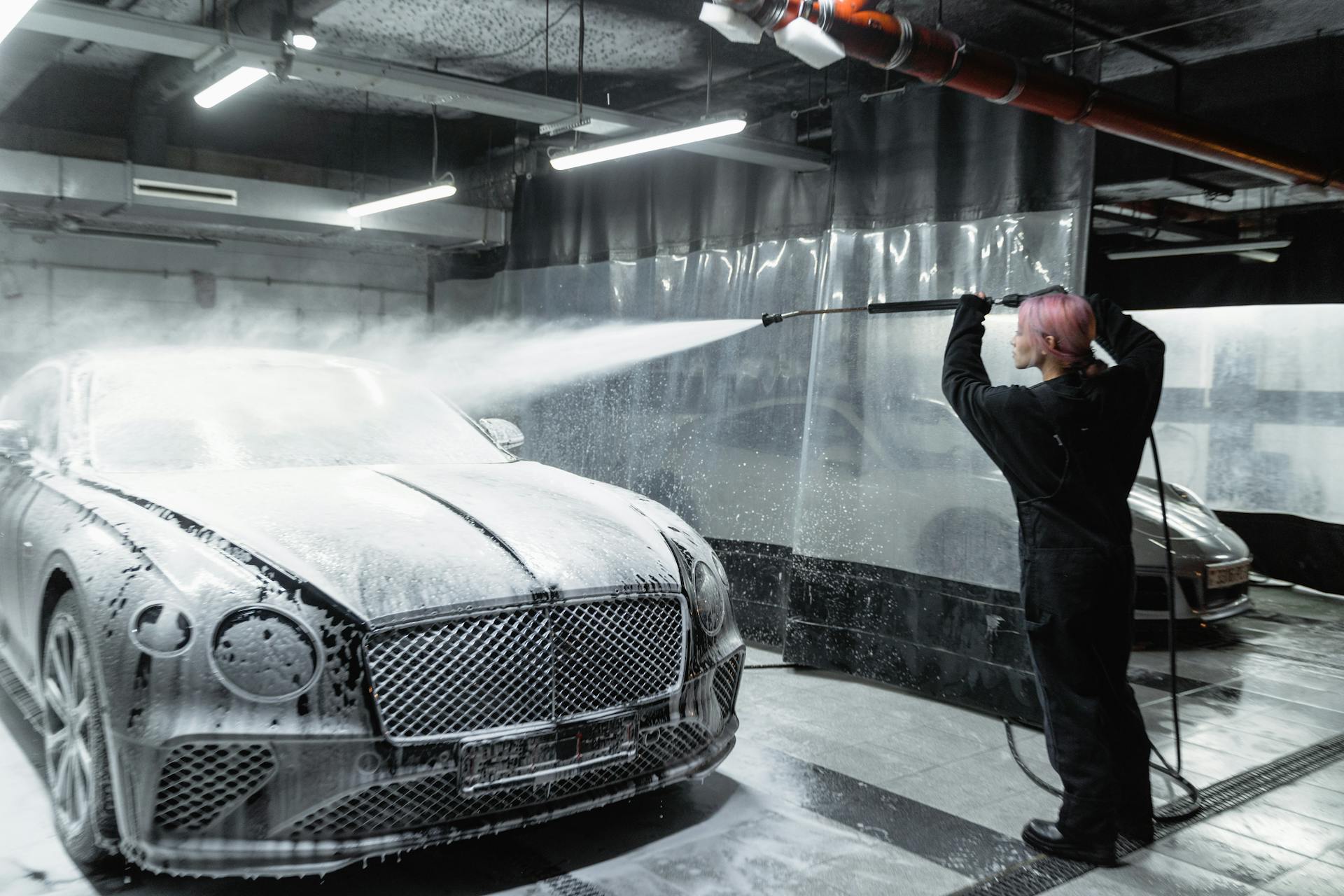
Low-density foam is commonly used in applications where a high level of flexibility is required, such as in athletic equipment and safety gear.
One key consideration when choosing between foam and low-density foam is the level of support and cushioning needed.
Low-density foam is generally more expensive than regular foam, but it offers improved flexibility and durability.
Q2. Key Factors to Consider
Choosing the right high-density packing foam is crucial for protecting your product during transit. The level of protection required by the product is the first thing to consider.
The product's weight and whether it will be shipped or stored are also important factors to think about. This will help you determine the right amount of foam needed.
To maintain high-density packing foam, regular cleaning with mild soap and water is effective in prolonging its lifespan.
Environmental Impact
High-density packing foam has a significant impact on the environment, and it's essential to understand the facts.
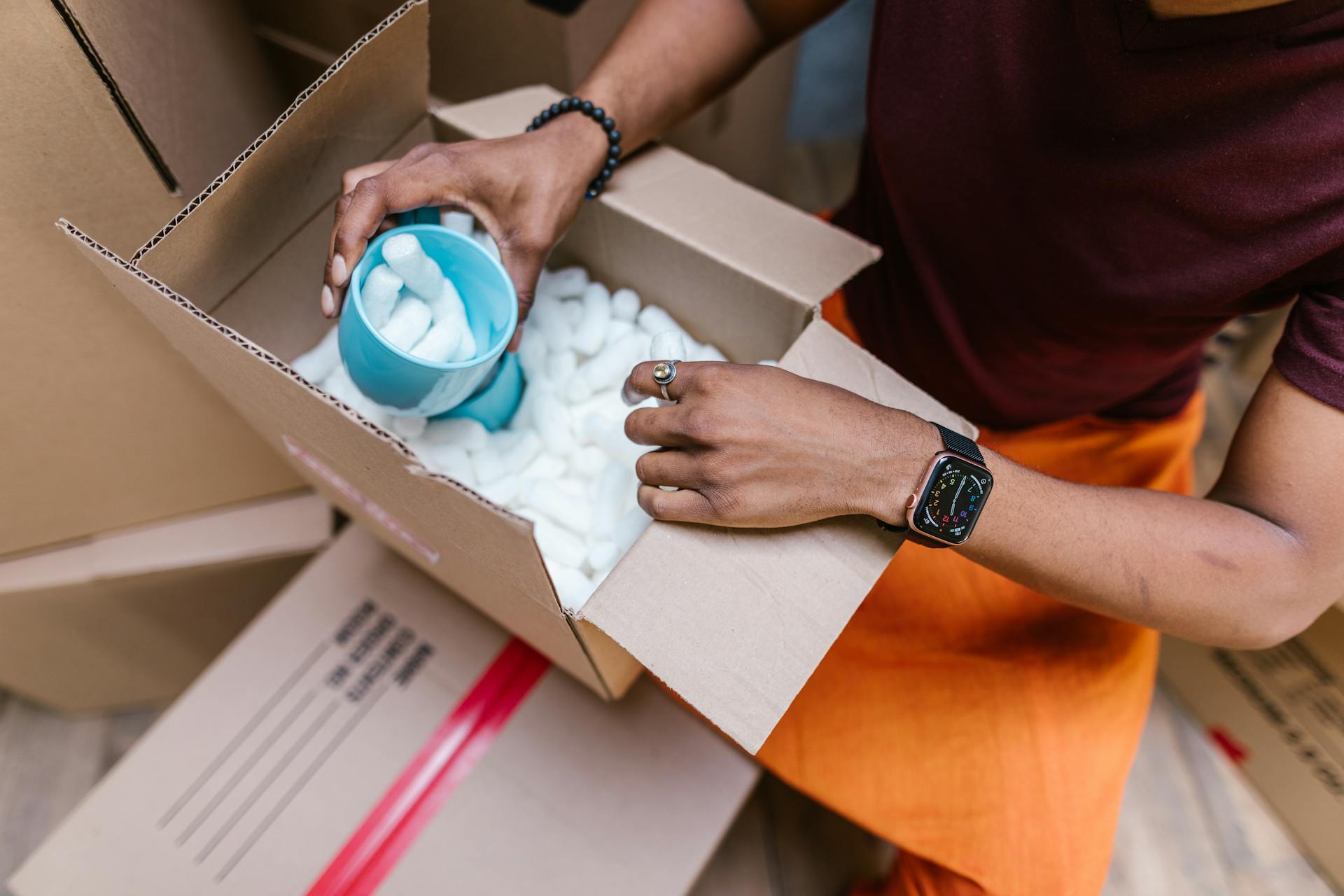
The production of high-density packing foam requires a large amount of petroleum, which is a non-renewable resource.
It's estimated that over 500 million pounds of packing peanuts are used in the US alone each year, with the majority being made from styrofoam.
The non-biodegradable nature of high-density packing foam means it can take hundreds of years to decompose.
The foam can also be broken down into smaller pieces, contributing to microplastic pollution in our oceans.
Packing foam is often disposed of in landfills, where it can take up to 500 years to decompose.
A single cubic foot of high-density packing foam can produce up to 10 pounds of waste.
Frequently Asked Questions
What are the disadvantages of high density foam?
High-density foam has a few drawbacks, including being firm, heavy, and expensive. These limitations may affect its suitability for certain applications or users.
Which foam is best for packaging?
For heavy-duty packaging, Polyethylene foam is recommended due to its shock absorption capabilities. For more cushioned packaging, softer Polyurethane foam options like Charcoal Foam are suitable.
Featured Images: pexels.com