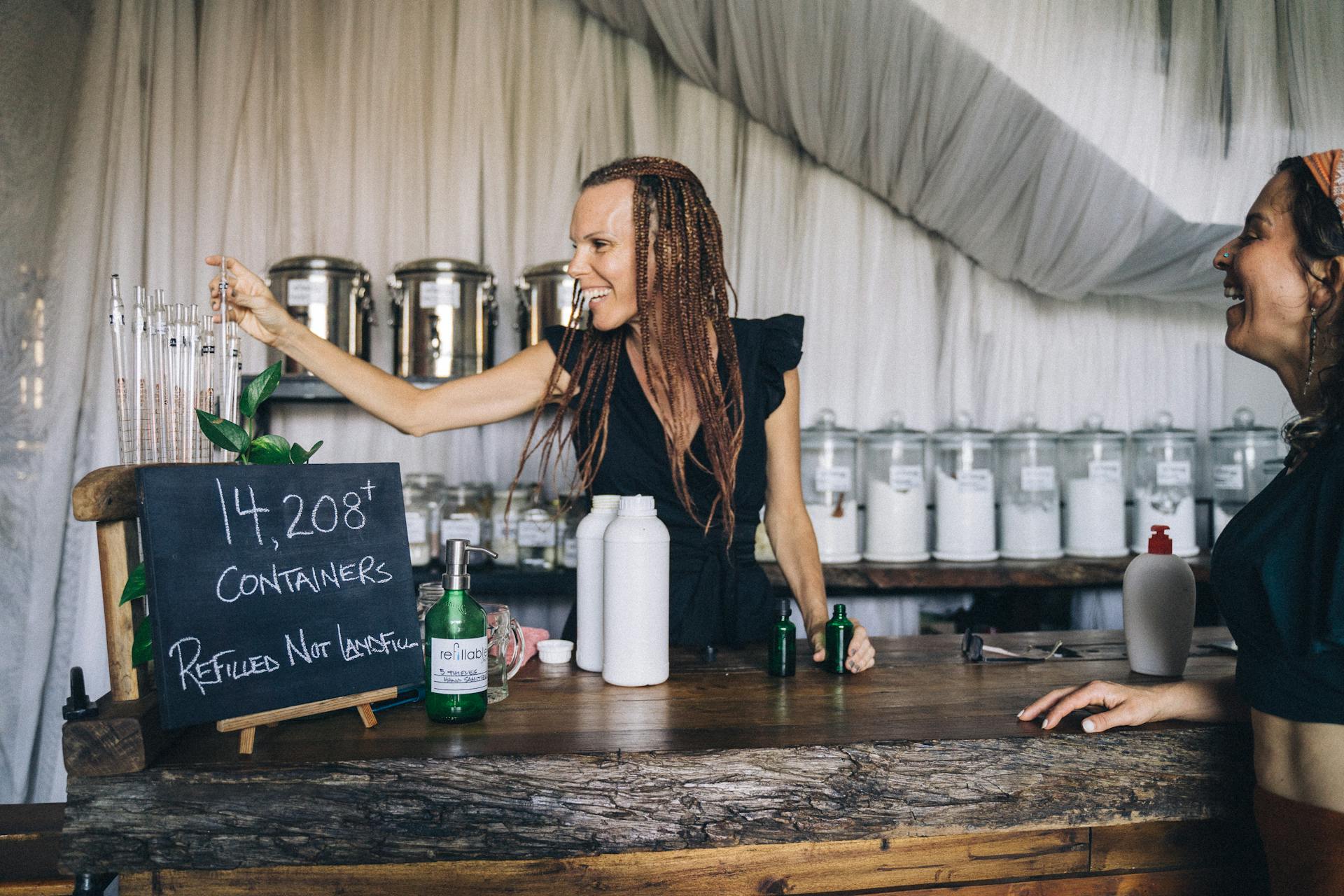
Custom blow moulding is a versatile manufacturing process that allows for the creation of complex shapes and designs. It's used to produce a wide range of products, from plastic containers and bottles to medical devices and automotive parts.
The process involves injecting molten plastic into a mould, which is then sealed and subjected to high pressure to shape the plastic into the desired form. This can be done with a variety of plastics, including polyethylene, polypropylene, and polycarbonate.
Custom blow moulding has many applications, including the production of packaging materials, such as water bottles and shampoo containers. It's also used to create medical devices, like syringes and test tubes.
With the ability to produce complex shapes and designs, custom blow moulding is a great option for companies looking to create unique products that stand out from the competition.
Consider reading: Custom Medical Labels
Our Capabilities
We're proud to offer a wide range of capabilities in custom blow molding. We can work with a variety of plastics, including High Density Polyethylene (HDPE), Polypropylene (PP), and Acrylonitrile-Butadiene-Styrene (ABS).
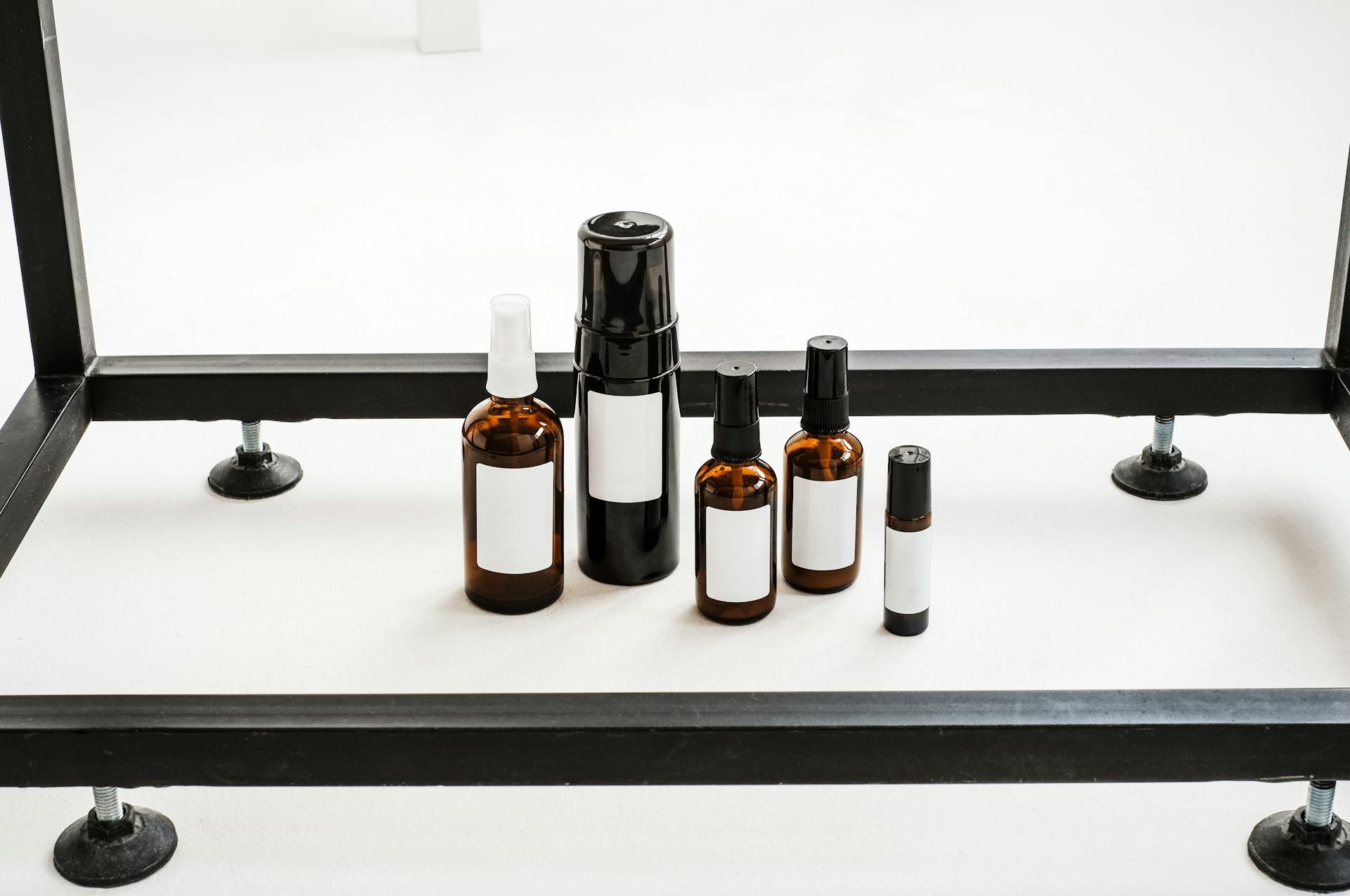
Our blow molding machines can produce parts with a wide range of dimensions, from 6 to 120 inches in length, 1 to 48 inches in width, and ½ to 50 pounds in weight. This flexibility allows us to create complex parts with hollow chambers, making us a great fit for industries like automotive and medical.
Some of the specific types of plastics we can work with include HDPE, HMW-HDPE, talc-filled HDPE, PP, glass-filled PP, and TPR. We also offer secondary services like assembly, labeling, and full product pack-out.
Our equipment list includes a range of Sterling Single and Twin presses, as well as rotary air compressors and material dryers. We're ISO 9001:2015 registered and comply with ISO quality control processes.
We serve a diverse range of industries, including exterior and interior automotive, juvenile furniture, heavy truck, outdoor recreation equipment, and office/medical products. Some of the specific products we can create include containers, water bottles, shampoo and conditioner bottles, milk bottles, automotive ducting, and industrial parts.
Products and Materials
Universal Plastics offers a wide range of products through custom blow molding, including medical devices, waste management containers, automotive components, and large capacity potable water bottles. Their facility spans 120,000 sq. ft. and features blow molding machines that can handle parts of various sizes.
Some common products created with custom blow molding include water bottles, shampoo and conditioner bottles, milk bottles, and automotive ducting. Containers with a hollow chamber, industrial parts, and fuel tanks are also commonly produced.
The materials used in custom blow molding include HDPE, PP, PC, and PETG. HDPE offers excellent impact and chemical resistance, while PP is rigid and has good impact strength. PETG is clear and has excellent impact strength, and PC has very high impact strength and high temperature resistance.
USA-Made Products
Universal Plastics, a leading blow molding supplier, offers custom extrusion blow molding services in the United States. Their 120,000 sq. ft facility in the US houses blow molding machines ranging in size from 1.5 lbs. to 30 lbs.
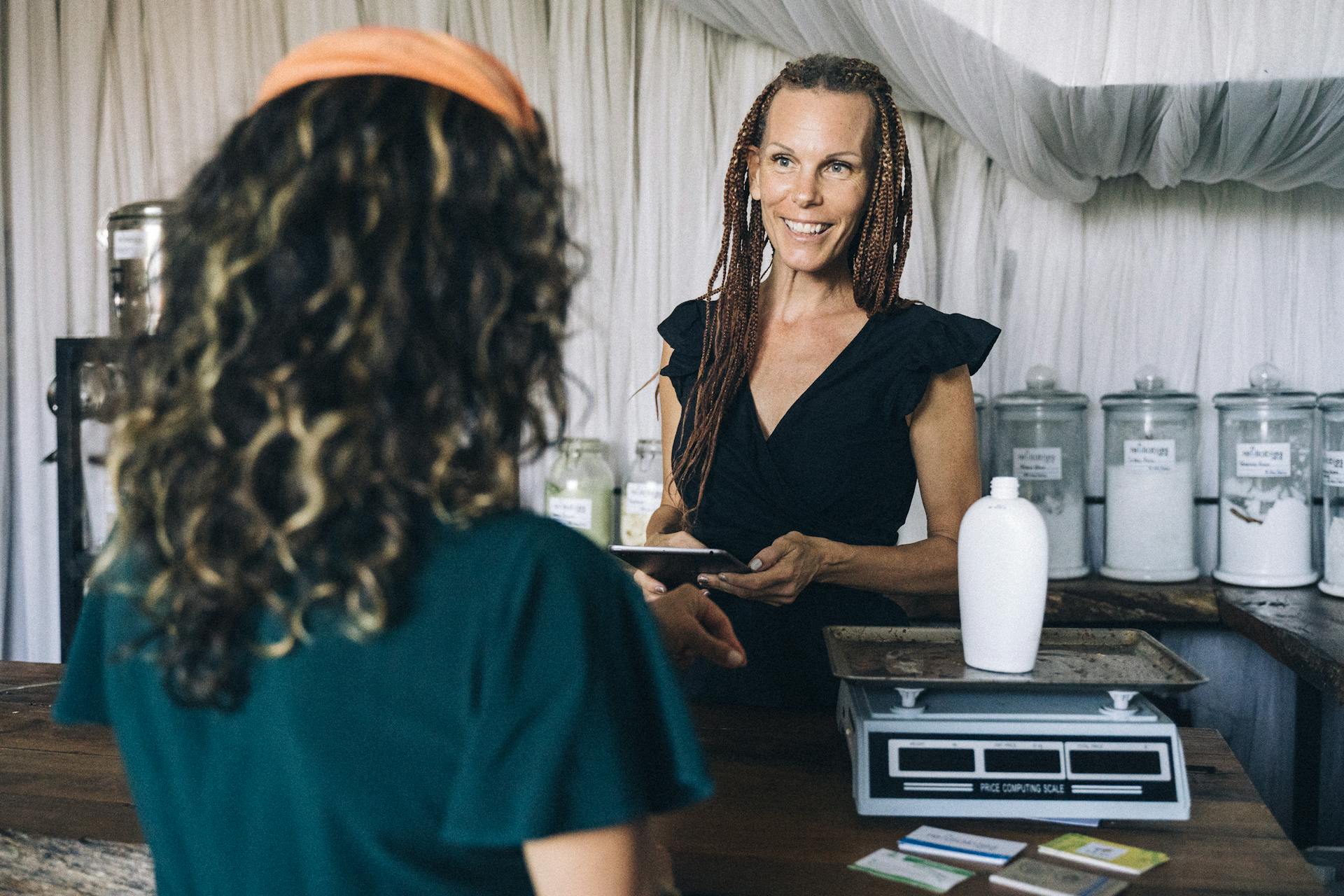
The company's expertise spans various materials, including HDPE, PP, PC, and PETG. They also offer injection molding services with 2 machines in the 225 ton range. Their wide range of machine size capabilities makes them one of the most versatile custom blow molding facilities in the industry.
With a focus on quality and accuracy, Universal Plastics uses state-of-the-art equipment and technology to produce complete products from concept to sale. Their blow molding facility encompasses 120,000 sq. ft, including areas dedicated to manufacturing, assembly, warehousing, and shipping.
Their mold and machine shop capabilities provide customers with a seamless and efficient process from concept to production capability. Universal Plastics has 18 machine cells and continues to add new equipment as customer needs grow and vary.
As a custom plastic products manufacturer, Universal Plastics offers unbiased, process-agnostic advice and multiple production processes for various markets. They are known for outstanding customer service and engineering support, with dedicated staff, operating facilities, and processes at each of their manufacturing sites.
Universal Plastics is ISO9001: 2015 registered, ensuring that their products meet high quality and safety standards. They work collaboratively with customers to improve business processes, skills, and technology to deliver innovative custom plastic product solutions at globally competitive pricing.
Recommended read: Custom Quality Control Stickers
What Products Are Created?
Universal Plastics offers custom extrusion blow molding for a wide range of products, including medical devices, waste management containers, automotive parts, and large capacity potable water bottles.
Their facility spans 120,000 sq. ft. and features blow molding machines that can produce parts ranging from 18 grams to 40 pounds in size.
Custom blow molding technology is used in many modern industrial, medical, and consumer applications, such as containers with a hollow chamber, water bottles, and automotive ducting.
Some interesting custom blow molded parts include hiking backpack frames, toys, kitchen appliances, and hospital beds.
Universal Plastics can produce parts with dimensions as large as 36” by 66” and has expertise in numerous materials, including HDPE, PP, PC, and PETG.
Their injection molding services include 2 machines in the 225 ton range, offering a wide range of machine size capabilities.
Here's an interesting read: Large Custom Stickers for Boxes
What Materials?
When working with blow molding, you'll often use thermoplastic resins. These materials are ideal for the process because they can be melted and reformed multiple times.
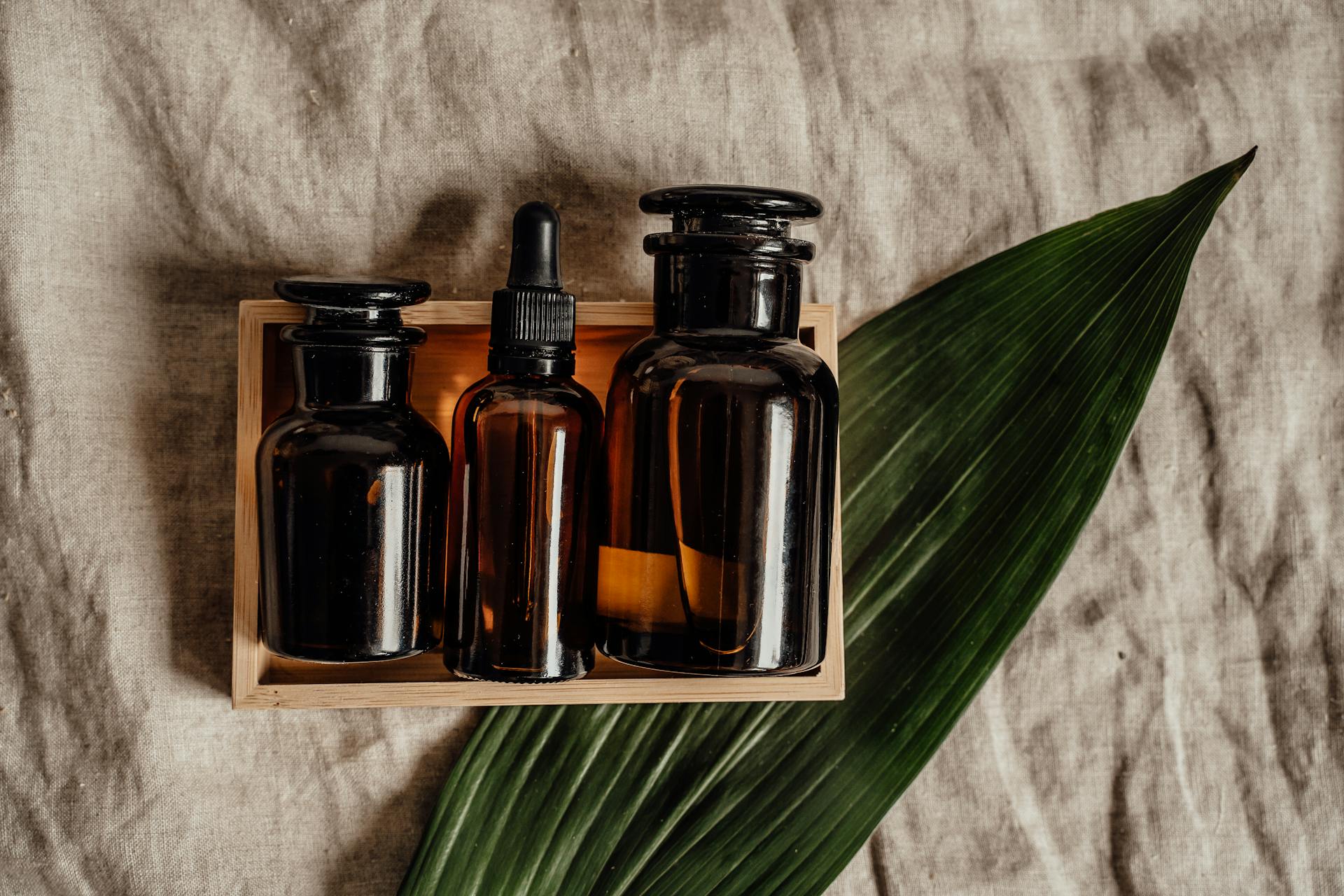
HDPE (High Density Polyethylene) is a popular choice for blow molding due to its excellent impact and chemical resistance. It's also great in cold temperatures, but it's not the most dimensionally stable material.
PP (Polypropylene) is another common option, offering excellent chemical resistance and a rigid structure with good impact strength. It performs well at higher temperatures, but it's not the most stable material in terms of dimensions.
PETG (Polyethylene Terephthalate Glycol) is a clear material with excellent impact strength and forms well. It's a great choice for blow molding applications.
PC (Polycarbonate) is a very high impact strength material that's also clear. It has high temperature resistance, making it a great option for blow molding.
Here's a quick rundown of the materials mentioned:
Applications and Benefits
Custom blow moulding is used in a wide range of applications, from medical containers to lawn and garden care products.
We can manufacture medical sharps collectors, which is a critical need in the medical field. Universal Plastics is registered with the U.S. Food & Drug Administration for this purpose.
In the automotive industry, custom blow moulding can be used to create components such as wheels and industrial cases.
Food containers and pollution control components are also manufactured using this process.
Planters and water bottles are just a few examples of the many lawn and garden care products that can be produced.
In the recreational and leisure industries, custom blow moulding can be used to create playground equipment and furniture components.
We can also manufacture agricultural tanks and storage units, which are essential for various industries.
Our ISO 9001:2015 certification ensures that all products meet the highest quality standards.
How It Works
Our custom blow molding process is quite fascinating. It allows us to produce a wide range of products across hundreds of industries, including automotive manufacturing, storage, transportation, and healthcare.
This process takes only a few seconds per product, which is incredibly efficient. Our blow molding machines can produce thousands of units per hour, making it a highly productive method.
The process starts with a preform or parison being clamped into a mold, where the mold's shape determines the final shape of the product.
Seamless Execution
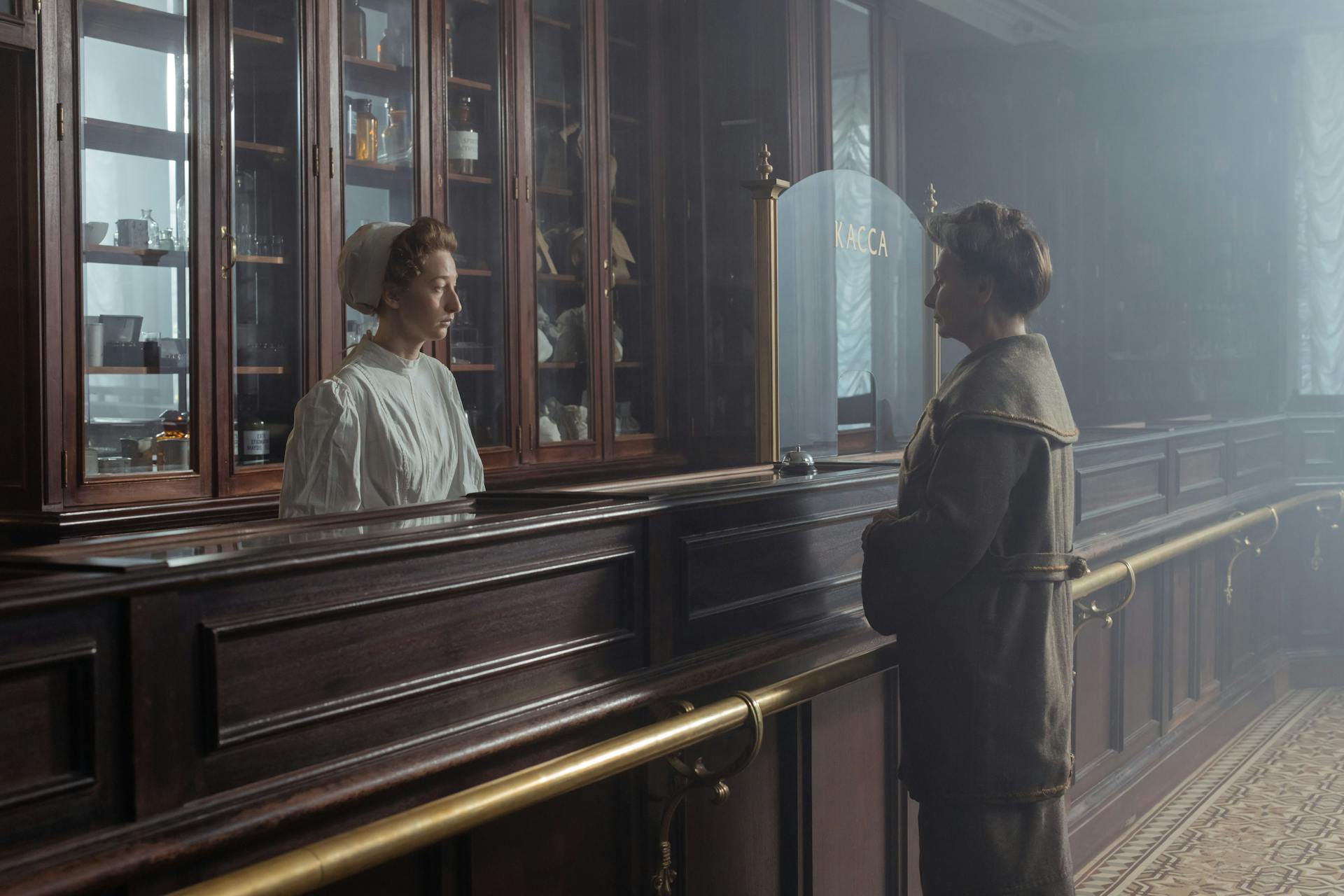
From the initial concept to full-scale production, we ensure a seamless execution of your custom blow molding project.
Our team of professionals works directly with you to understand your vision and needs. We combine your ideas with our technical knowledge, leveraging innovative design and engineering techniques to develop optimal solutions.
Our specialized team of professionals ensures a seamless execution of your project. They work closely with you to understand your unique requirements.
We combine your ideas with our technical knowledge to develop optimal solutions. This collaborative approach results in a project that meets your exact needs.
How Machines Work
Our machines are capable of producing thousands of units per hour, making them incredibly efficient. This is especially impressive considering the blow molding process takes only a few seconds per product.
The preform or parison is clamped into a mold, which determines the ultimate shape of the blow molded plastic. The shape of the mold is crucial in creating the desired product.
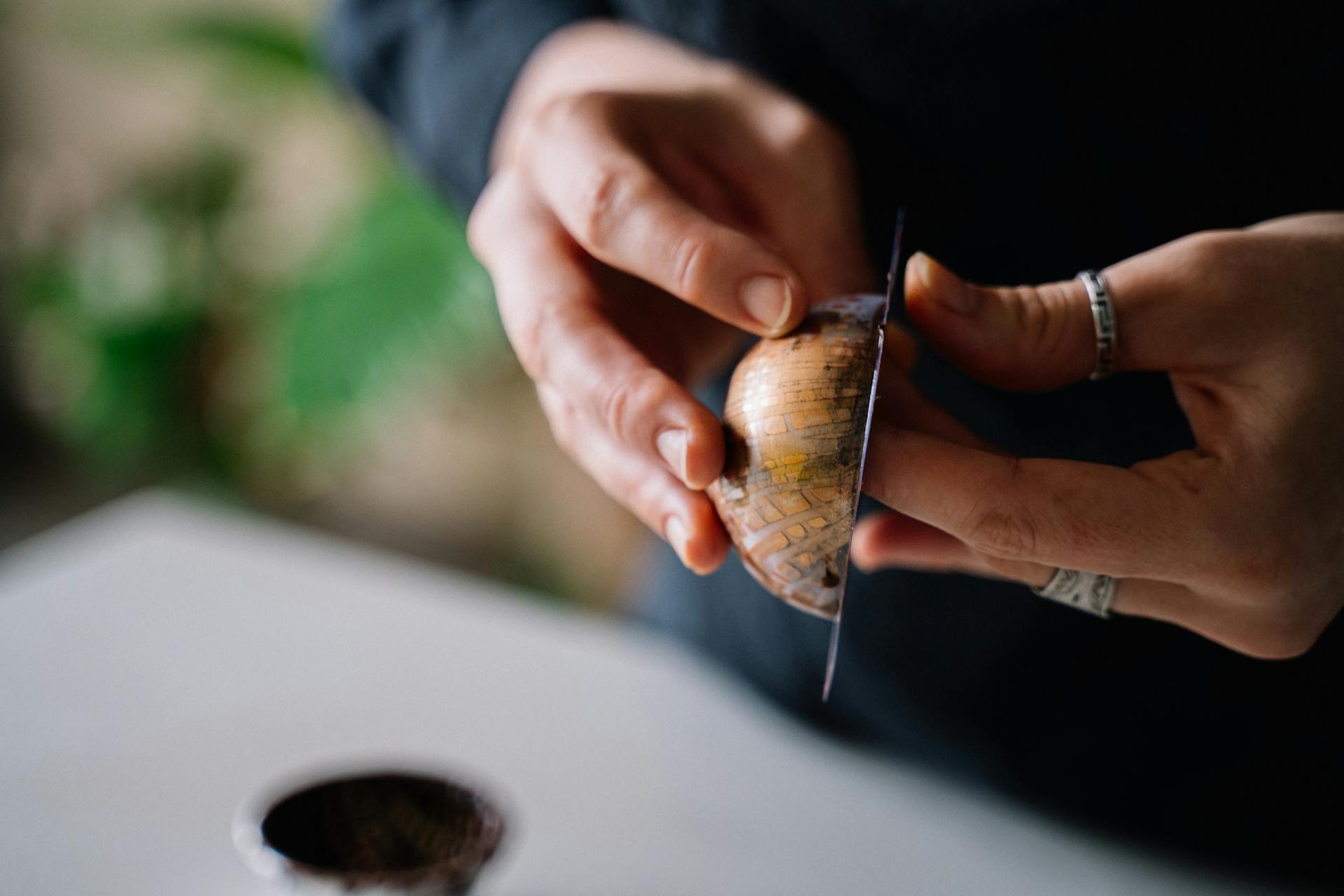
Air pressure is introduced, causing the parison to swell and take the shape of the cavity. This process is what gives blow molded products their unique shape and form.
The end product is cooled, either with water, conduction, or evaporation. Cooling is a critical step in the process, ensuring the plastic hardens properly.
After the plastic has cooled and hardened, the mold is released and the product is ejected. This marks the end of the blow molding process, and the product is now ready for use.
Featured Images: pexels.com