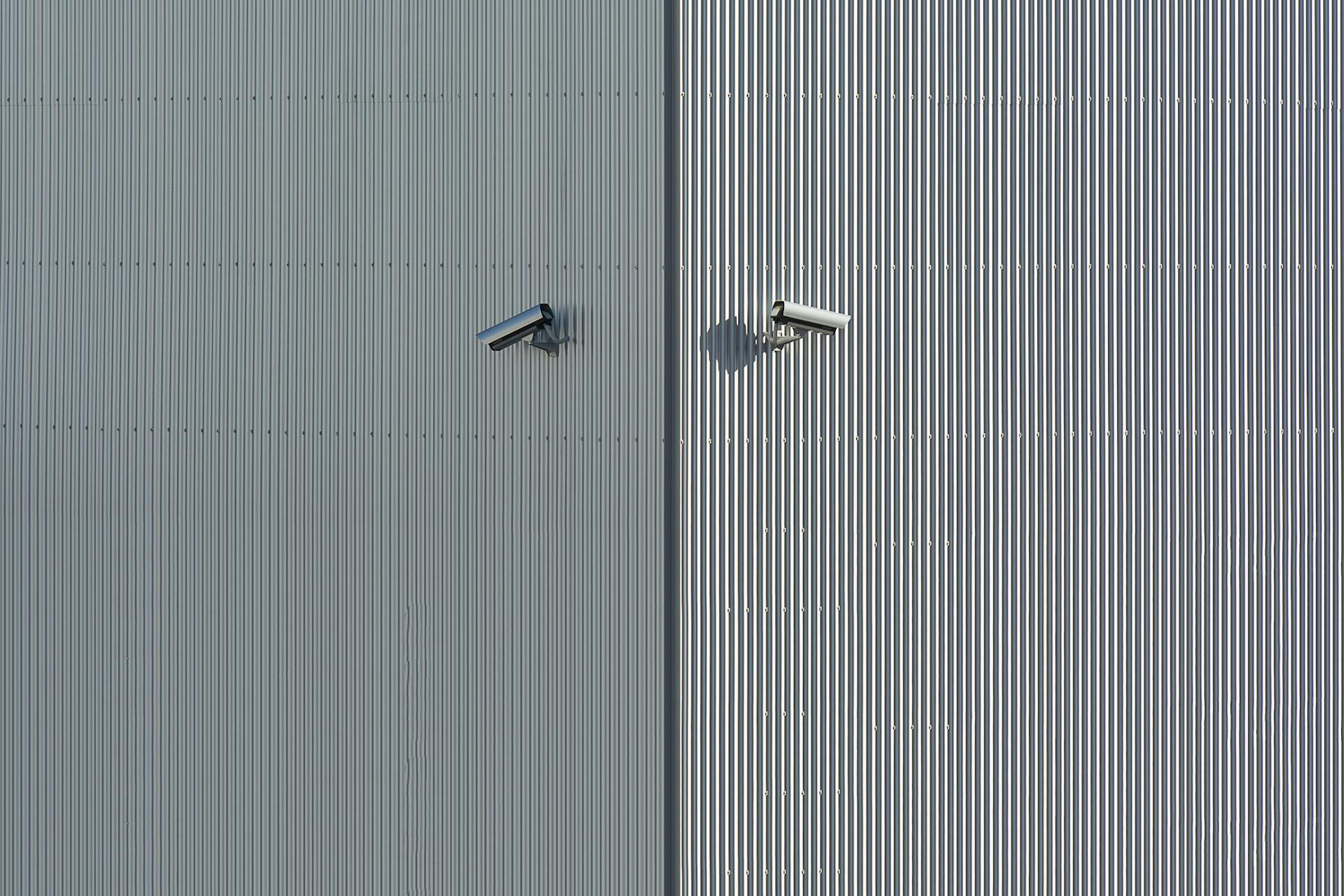
Corrugated fiberboard sheets are a type of material made from paper pulp and a binding agent, which are pressed together to form a strong and lightweight sheet.
They're often used for packaging and shipping fragile items, as they provide excellent protection against shocks and drops.
The manufacturing process involves combining paper pulp and a binding agent, such as starch or glue, and then pressing the mixture into a sheet.
This process can be done using a variety of machines, including corrugators and laminators.
The resulting sheets can be customized to fit specific needs, with different flute sizes and paper types available.
Additional reading: Paper Pulp Molding Machine
What Is Fiberboard?
Fiberboard is a material made from fibrous layers of cardboard.
It's formed by an inner or central rib made from corrugated paper, also called fluting, which is externally covered with two layers of paper.
These two sheets are adhered to the waves of the corrugated paper of the central rib by means of adhesive or cellulose.
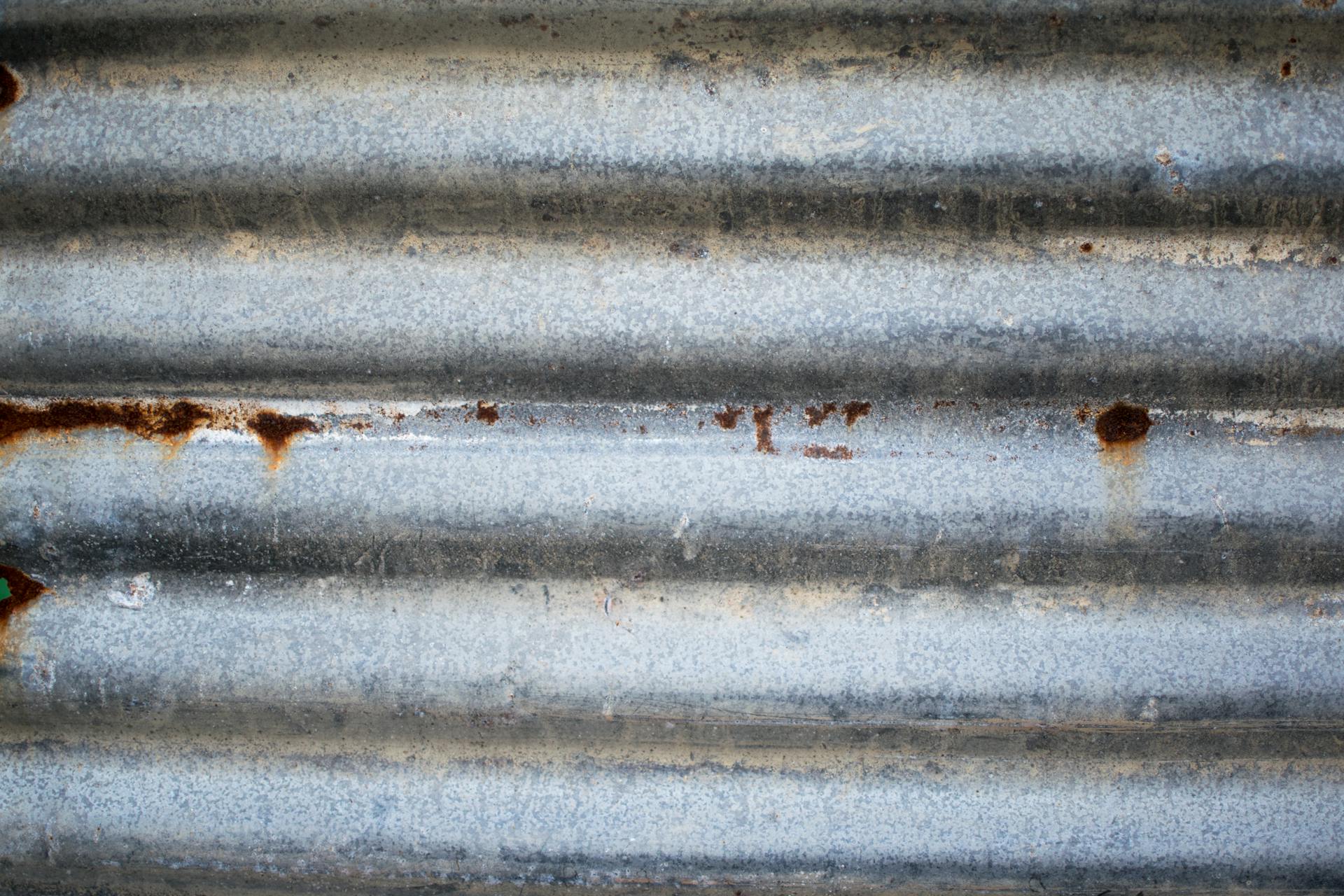
This unique structure gives fiberboard the property of flexibility.
The union of these sheets is what makes fiberboard so versatile.
If the central rib or central corrugated paper suffers crushing or deterioration, the board loses its resistance and correct flexibility.
There are several variants of fiberboard, with 3 to 5 layers of paper and one or two ribs made with corrugated paper.
Properties
Corrugated fiberboard sheets have a range of properties that make them suitable for various applications. Moisture content, for instance, should be between 6.5 to 9.5%.
Moisture levels outside this range can have negative effects on the board. If it's too low, it can cause cracking, while too high a level reduces compression strength.
Edge crush test is a key measurement, reporting force per unit width and predicting box compression strength. The results are typically expressed in KN/m or lb/inch.
Here are some key properties of corrugated fiberboard sheets:
- Moisture content: 6.5 to 9.5%
- Edge crush test: force per unit width, predicting box compression strength (reported in KN/m or lb/inch)
- Burst strength: pressure required to rupture corrugated sheet (reported in KPa or lb/inch2)
- Box Compression strength: direct measurement of performance (reported in kgf or N)
- Flat crush test: measures flutes rigidity (reported in KPa)
- Bending resistance
- Impact resistance
- Cushioning, shock absorption
- Tear resistance
- Grammage: weight per meter square (reported in g/m2)
Purpose
Properties are built to serve a purpose, and understanding that purpose is key to appreciating their value.
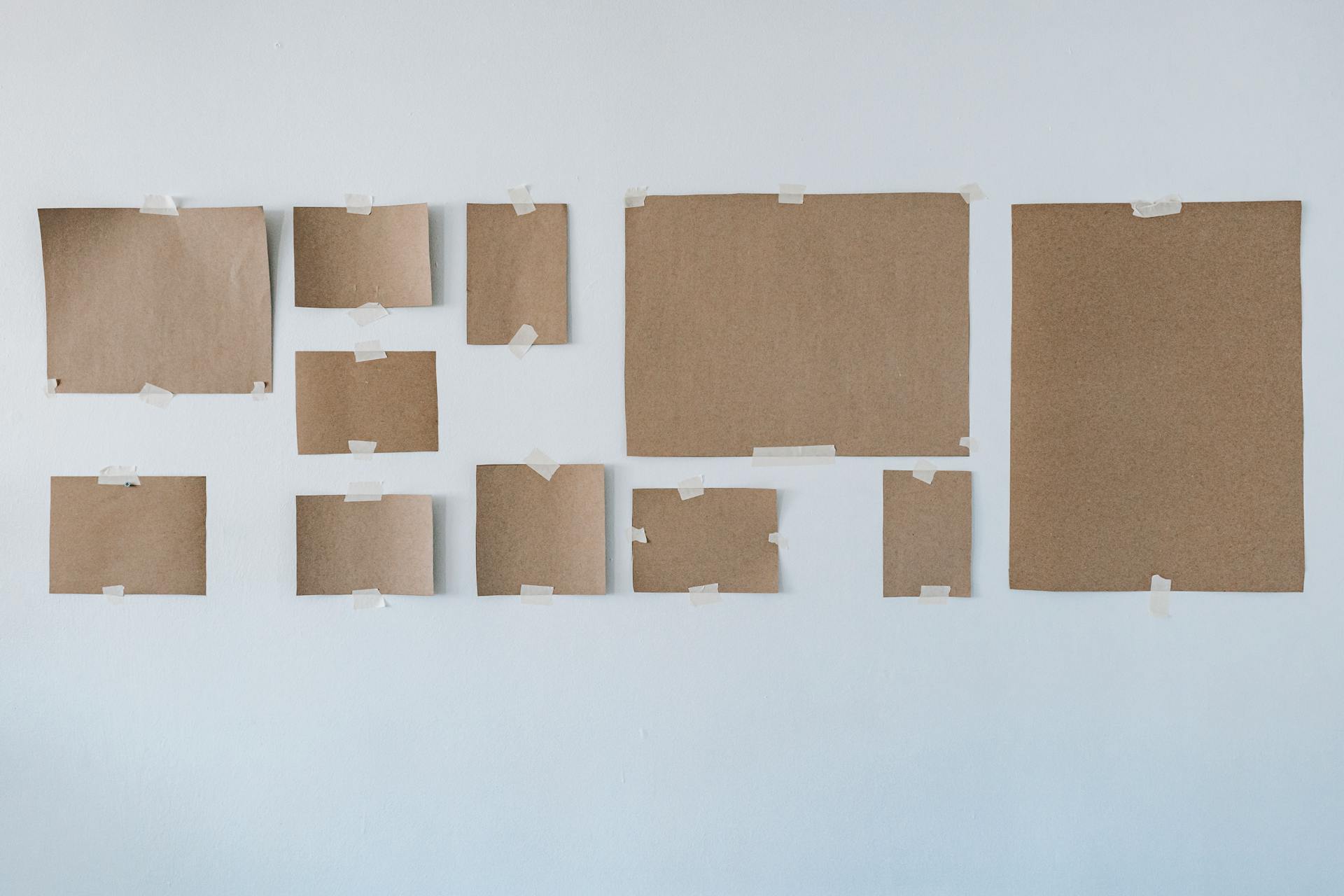
The purpose of a property can vary greatly, from providing a comfortable living space to generating income through rentals.
A property can be a home for a family, offering a sense of security and belonging.
In some cases, properties are used as investment opportunities, generating passive income through rental properties or property management.
Properties can also serve as a business hub, providing a location for commercial activities.
Ultimately, the purpose of a property is to meet the needs of its occupants or users.
Physical
Physical properties of corrugated board are crucial to its performance and durability. Moisture content ranges from 6.5 to 9.5%, and if it's too low, it can cause cracking, while too high a level reduces compression strength.
Edge crush test measures force per unit width and predicts box compression strength, reported in KN/m or lb/inch. This test is a good indicator of a box's ability to withstand external forces.
Burst strength is the pressure required to rupture corrugated sheet, reported in KPa or lb/inch2. A higher burst strength indicates a more robust sheet.
For your interest: Plastic Pp 5
Box compression strength is a direct measurement of a box's performance, reported in kgf or N. This is a critical factor to consider when designing and manufacturing boxes.
Flat crush test measures flutes' rigidity and is reported in KPa. This test helps assess a box's ability to maintain its shape under pressure.
Corrugated board also exhibits bending resistance, impact resistance, cushioning, shock absorption, and tear resistance. These properties are essential for ensuring a box can withstand various environmental conditions and handling stresses.
Here are some key physical properties of corrugated board:
- Moisture content: 6.5-9.5%
- Edge crush test: predicts box compression strength, reported in KN/m or lb/inch
- Burst strength: pressure required to rupture corrugated sheet, reported in KPa or lb/inch2
- Box compression strength: direct measurement of box performance, reported in kgf or N
- Flat crush test: measures flutes' rigidity, reported in KPa
Manufacturing
Corrugated fiberboard sheets are made by layering kraft paper or other paper-based materials in a specific way to create the corrugated flutes.
The manufacturing process involves using a machine to cut the paper into the desired size and shape.
These sheets are often used in packaging and shipping due to their strength and durability.
Process
The manufacturing process involves several key stages.
Design is a crucial part of manufacturing, where engineers create detailed plans and prototypes of the product.
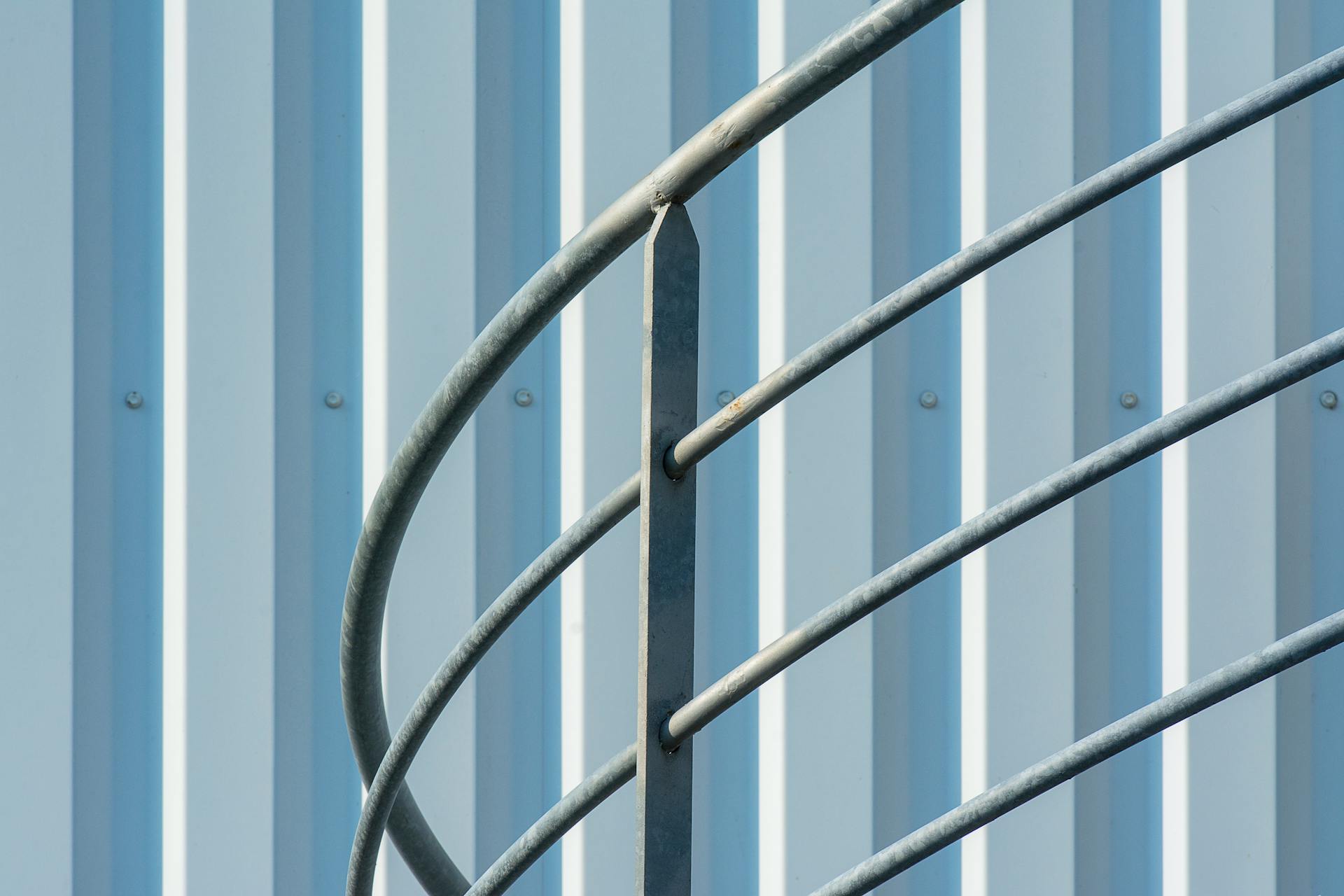
A product's design can be influenced by factors such as cost, functionality, and aesthetics.
Computer-Aided Design (CAD) software is often used to create detailed digital models of the product.
Manufacturers use a variety of materials, including metals, plastics, and textiles, depending on the product's requirements.
Materials are sourced from suppliers and transported to the manufacturing facility.
The manufacturing process can be broadly categorized into three types: batch production, mass production, and job production.
Batch production involves producing a small batch of products, typically with similar characteristics.
Manufacturing facilities often have specific equipment and machinery tailored to the production process.
Quality control measures are in place to ensure products meet the required standards.
Inspection and testing are critical steps in the manufacturing process to identify any defects or issues.
A different take: Foam Packaging Materials
Methods
Manufacturing involves several key methods to produce goods efficiently.
Computer-aided design (CAD) software is used to create detailed digital models of products before production begins.
This approach helps manufacturers identify and fix errors early on, reducing waste and saving time.
3D printing is a popular method for producing complex parts and products with high precision.
It's commonly used in the production of prototypes, custom parts, and even end-use products in industries like aerospace and healthcare.
Robotics and automation play a crucial role in manufacturing, increasing efficiency and reducing labor costs.
Manufacturers can program robots to perform repetitive tasks with high accuracy, freeing up human workers for more complex tasks.
Quality control checks are essential to ensure products meet the required standards before they leave the factory.
Manufacturers use various techniques, including inspection and testing, to identify defects and make necessary corrections.
Types of Fiberboard
When working with corrugated fiberboard sheets, it's essential to understand the different types available. Single-channel corrugated fiberboard with a single cover is ideal for wrapping fragile products before placing them in boxes during the order picking process.
This type of fiberboard consists of a medium and a single liner. You can also get a single-channel corrugated fiberboard with two covers, which is most common in the manufacture of boxes with flaps.
Intriguing read: Single Wall Corrugated Board
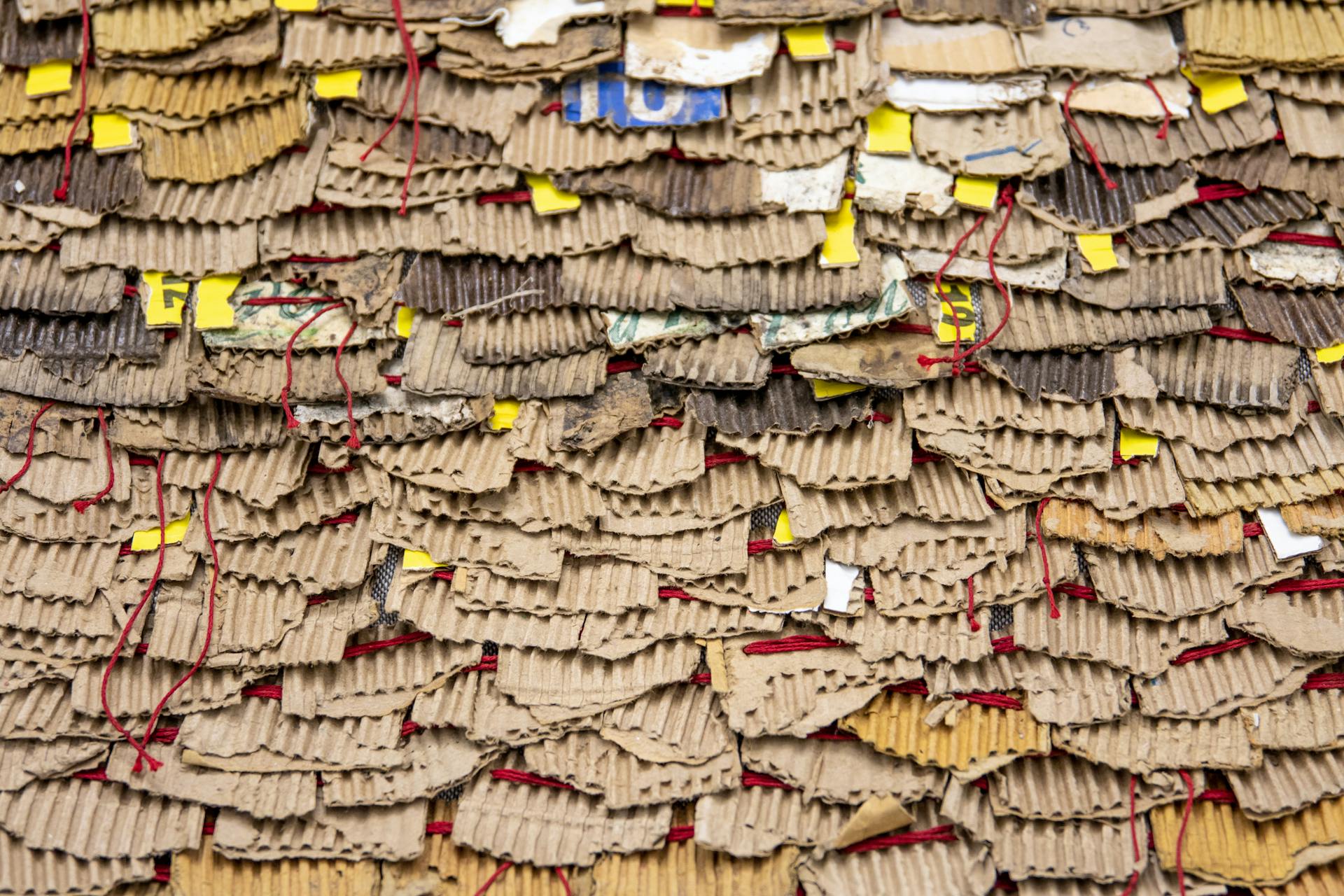
The two types mentioned above are great for everyday use, but if you need extra resistance in your boxes, you can opt for double channel corrugated fiberboard. This type has two flutes separated by a third liner, in addition to the two external ones.
If you're shipping especially heavy merchandise, triple channel corrugated fiberboard is the way to go. It's the result of joining three sheets of corrugated paper and four cardboard sheets.
Here's a quick summary of the types of fiberboard:
- Single-channel corrugated fiberboard with a single cover: ideal for wrapping fragile products
- Single-channel corrugated fiberboard with two covers: most common in box manufacturing
- Double channel corrugated fiberboard: ideal for boxes with extra resistance
- Triple channel corrugated fiberboard: ideal for shipping heavy merchandise
Single-Face Laminate
Single-Face Laminate is a hybrid product that combines the structural benefits of corrugated with the high-graphics print of lithography.
This application, known as Single-Face Laminate (SFL), starts with a traditional fluted medium adhered to a single linerboard.
Specialized equipment is necessary for the material construction of SFL, which can lead to a higher cost for these products.
However, this cost is often offset by the savings over a separate paperboard sleeve and the labor necessary to assemble the completed package.
Readers also liked: Single Face Corrugated Board
Double-Face Laminate
Double-Face Laminate is made by sandwiching a layer of decorative paper between two layers of fiberboard, creating a smooth surface on both sides. This type of laminate is ideal for furniture making and cabinetry.
It's often used for building cabinets and furniture because it provides a strong and durable surface that can withstand wear and tear.
Standards and Classifications
ASTM standards are crucial for ensuring the quality and consistency of corrugated fiberboard sheets. The American Society for Testing and Materials (ASTM) has established several standards for the fabrication, closure, and selection of corrugated fiberboard materials and box construction.
One of the key ASTM standards is D1974, which outlines methods for closing, sealing, and reinforcing fiberboard boxes. This standard is essential for manufacturers who want to ensure that their boxes are properly constructed and can withstand various environmental conditions.
ASTM standards also cover the specification for corrugated and solid fiberboard sheet stock, as outlined in standard D4727. This standard provides guidelines for the selection of corrugated fiberboard materials and box construction based on performance requirements, as described in standard D5639.
Curious to learn more? Check out: Kraft Brown Paper Box
If you're looking to fabricate or close triple-wall corrugated fiberboard containers, you'll need to follow the guidelines outlined in standard D5168. This standard provides a comprehensive guide for the fabrication and closure of these types of containers.
Here's a summary of the key ASTM standards related to corrugated fiberboard sheets:
- D1974: Standard Practice for Methods of Closing, Sealing and Reinforcing Fiberboard Boxes
- D4727: Standard Specification for Corrugated and Solid Fiberboard Sheet Stock (Container Grade) and Cut Shapes
- D5118: Standard Practice for Fabrication of Fiberboard Shipping Boxes
- D5168: Standard Practice for Fabrication and Closure of Triple-Wall Corrugated Fiberboard Containers
- D5639: Standard Practice for Selection of Corrugated Fiberboard Materials and Box Construction Based on Performance Requirements
- D6804: Standard Guide for Hand Hole Design in Corrugated Boxes
ASTM standards are not the only classification system used for corrugated fiberboard sheets. The American National Standards Institute (ANSI) also uses a classification system based on the type of material used. However, the classifications are not explicitly stated in the provided article sections, but we can look at the classifications mentioned in the article sections.
Specifications
Corrugated fiberboard sheets are made from a combination of paper pulp and a binding agent, which creates a strong and durable material.
The sheets can be cut to various sizes, ranging from standard 4x8 feet to custom sizes depending on the application.
They are often used for packaging and shipping due to their light weight and resistance to moisture.
You might like: Corrugated Board Flute Sizes
Chemical
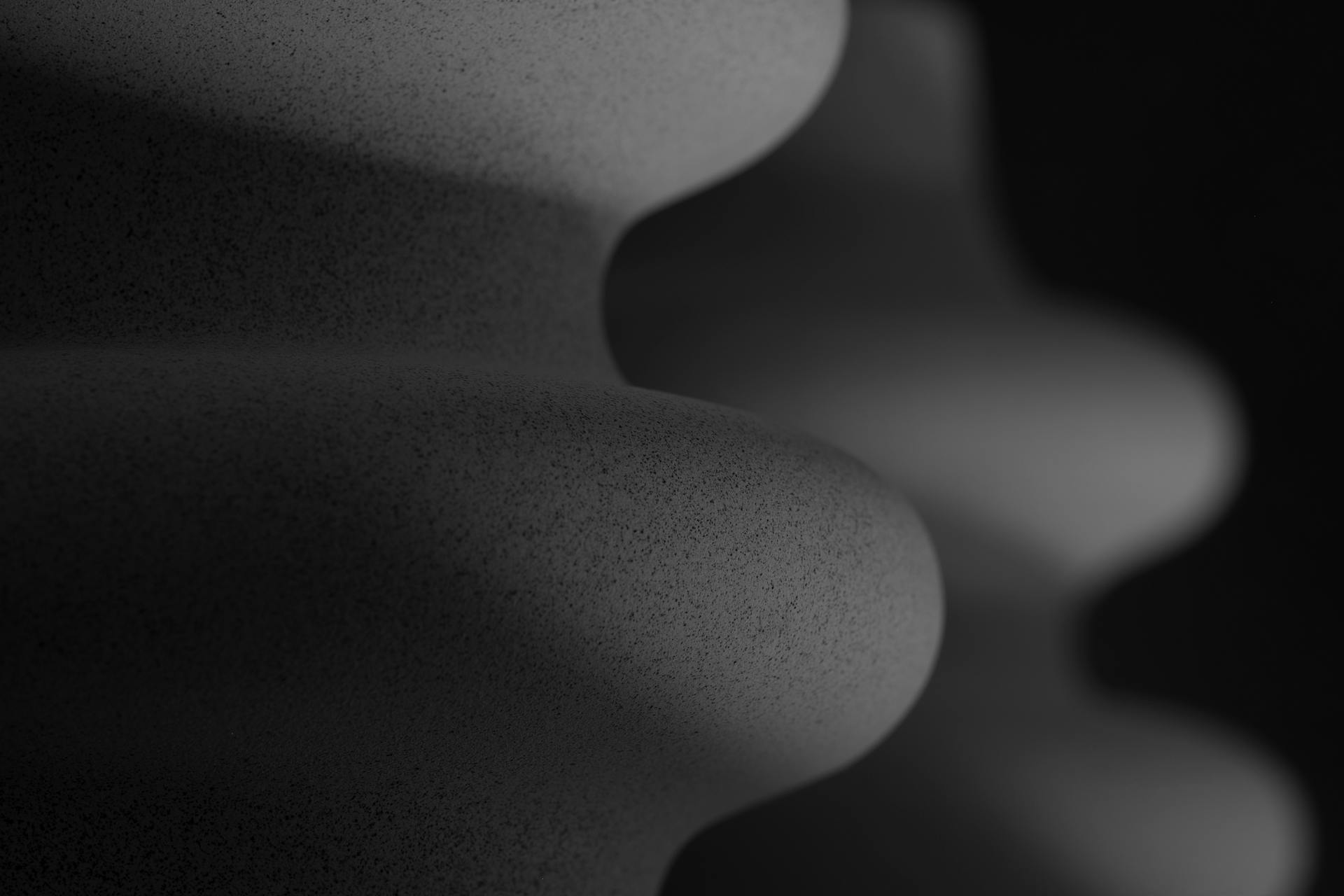
Chemical specifications are crucial in various industries. The concentration of chemicals in a product can be measured in different units, such as percentage, parts per million (ppm), or milligrams per liter (mg/L).
The pH level of a chemical solution is a measure of its acidity or alkalinity. For example, a pH level of 7 is neutral, while a pH level of 0-1 is highly acidic.
Chemicals can be classified into different types based on their properties, such as solubility in water. Some chemicals, like sodium chloride, are highly soluble in water, while others, like oil, are not.
The purity of a chemical can be measured using techniques like chromatography or spectroscopy. These methods can detect even small amounts of impurities in a chemical sample.
In the food industry, chemical specifications are important for ensuring the safety and quality of food products. For example, the concentration of sodium benzoate in food products must be within a certain range to prevent spoilage.
See what others are reading: Plastic Pallet Specifications
48X96 C-Flute 26ECT
The 48X96 C-Flute 26ECT is a versatile and widely used material.
It has a thickness of 0.013 inches (0.33 mm), making it suitable for various applications.
The C-Flute designation refers to its corrugation profile, which features a sinusoidal shape with a wavelength of 0.039 inches (1 mm).
This material is commonly used in point-of-purchase displays, shelf liners, and packaging applications.
Its 26ECT (End-Corrugated Thickness) rating indicates that it has a thickness of 0.013 inches (0.33 mm) at the end of the corrugation.
For more insights, see: 5 Mm Plastic Sheets
Other Sizes
The 24-inch model is a great option for those who want a compact display without sacrificing too much screen real estate.
In terms of resolution, the 24-inch model has a 1080p display, which is perfect for everyday tasks like browsing the web and checking email.
The 27-inch model, on the other hand, offers a 1440p display, making it ideal for graphic designers and video editors who need a higher level of detail.
The 32-inch model is a beast, with a 4K display that's perfect for watching movies or playing games.
For those who want to save space, the 22-inch model is a great option, but it's worth noting that the screen resolution is lower than the other models.
Frequently Asked Questions
What are the disadvantages of corrugated fiberboard?
Corrugated fiberboard is prone to deformation and shape loss under extreme pressure, and its weatherproofing is limited, making it vulnerable to rain and snow.
What is corrugated fiberboard used for?
Corrugated fiberboard is commonly used for shipping and packaging boxes, as well as direct product packaging, such as for electronics and household appliances. Its versatility makes it a popular choice for protecting and transporting goods.
What is the difference between cardboard and corrugated board?
Cardboard is a single-layer material, whereas corrugated board is a multi-layered material with greater strength and durability. This difference makes corrugated board ideal for shipping and packaging.
Sources
- https://en.wikipedia.org/wiki/Corrugated_fiberboard
- https://www.imperialdade.com/catalog/packaging/cardboard-sheets-pads
- https://www.morebusiness.com/3-things-you-must-know-about-corrugated-fiberboard/
- https://patents.google.com/patent/US6794016B2/en
- https://www.document-center.com/standards/show/ASTM-D4727
Featured Images: pexels.com