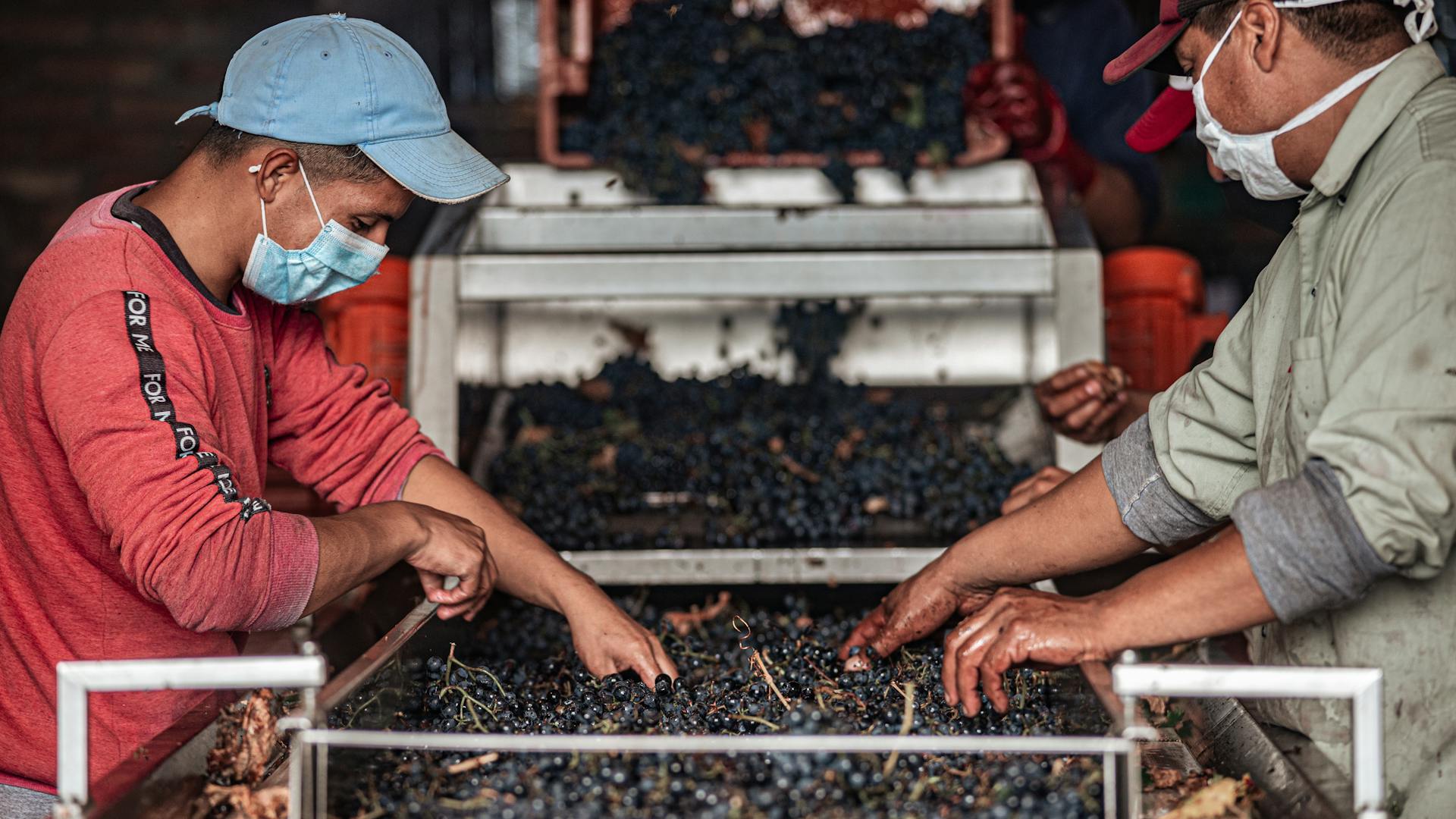
Tracking conveyor belts is a crucial aspect of maintaining a smooth and efficient production line. A well-maintained conveyor belt can significantly reduce downtime and increase productivity.
To track a conveyor belt, it's essential to identify the signs of misalignment, such as uneven wear on the belt's surface. Misalignment can cause the belt to wear down faster, leading to costly repairs.
Regular inspections can help prevent misalignment by detecting issues early on. Conducting a thorough inspection every 1,000 to 3,000 hours of operation is a good rule of thumb.
The type of conveyor belt being used also plays a significant role in tracking. For example, a belt with a high coefficient of friction, like a rubber belt, may require more frequent tracking than a belt with a lower coefficient, like a PVC belt.
Additional reading: Power and Free Conveyor Systems
Theory and Basics
Conveyor belt tracking is the process of aligning and controlling a conveyor belt so that it follows the desired path.
The goal of tracking is to fix any tendency of the belt to run any way other than intended.
Idlers, pulleys, and loading conditions are all adjusted to achieve proper tracking.
Tracking is a process of adjusting these components to correct any deviations.
Components and Parts
A tracking conveyor belt is made up of several key components, each playing a crucial role in its overall performance.
The belt itself is typically made of rubber or PVC, with a textured surface to prevent slipping and ensure smooth movement. The belt's thickness and material can vary depending on the application and load.
The pulleys are usually made of metal and are responsible for rotating the belt. They can be fixed or movable, depending on the design of the conveyor system.
The idlers are the rollers that support the belt and keep it in place. They are usually spaced evenly apart and can be adjusted to accommodate changes in the belt's tension.
The take-up system is used to adjust the belt's tension, ensuring it remains at the optimal level for smooth operation. It's usually located near the end of the conveyor belt.
Installation and Operational Conditions
Installation and Operational Conditions play a significant role in conveyor belt tracking performance. Misalignment of the conveyor structure during installation can lead to persistent tracking issues.
Proper installation is crucial to avoid tracking problems. According to Example 1, misalignment of the conveyor structure during installation can lead to persistent tracking issues.
Operational conditions such as conveyor speed, load point alignment, and environmental factors like temperature and humidity can also impact tracking performance. These conditions can cause the belt to drift off course.
To minimize tracking issues, it's essential to ensure that the conveyor is installed accurately and adjusted to suit specific operational conditions. This is in line with Example 2, which emphasizes the importance of a holistic approach to conveyor belt maintenance.
Here are some common operational conditions that can affect conveyor belt tracking:
By understanding the impact of these operational conditions, you can take proactive steps to minimize tracking issues and ensure your conveyor system runs smoothly.
Troubleshooting and Maintenance
Belt tracks to one side at specific points due to debris, material build-up, or damage. Check these areas and clean or repair as necessary.
A belt that drifts in one direction across the entire system often indicates an issue with tension or roller alignment. Recheck and adjust the tension and ensure all rollers are properly aligned.
Sudden belt misalignment can be caused by a damaged roller or a sudden change in load. Inspect the system for damaged components and ensure the load is evenly distributed.
Edge wear on the belt is often a sign of misaligned rollers or guides. Adjust or replace worn components as necessary.
Belt slippage can be caused by inadequate tension or worn pulley surfaces. Adjust the tension and inspect pulleys for wear.
Frequent re-tracking required can indicate a more systemic issue, such as a fundamentally misaligned conveyor frame or improper belt installation. Regular maintenance and a thorough understanding of conveyor belt dynamics are key to preventing and resolving tracking issues.
To maintain your conveyor belts, check for debris, material build-up, or damage at specific points where the belt tracks to one side. Clean or repair these areas as necessary.
Here are some common conveyor belt tracking problems and their solutions:
Advanced Techniques and Tools
Self-Aligning Rollers can automatically adjust the belt's position based on its movement, ensuring continuous alignment without manual intervention. This is a game-changer for conveyor belt tracking, allowing for real-time adjustments to prevent misalignment.
Belt Tracking Guides are installed along the edges of the conveyor frame to gently steer the cut edge conveyor belt back to its correct path, minimizing the risk of misalignment. They work by providing a physical barrier that keeps the belt on track.
Pneumatic Tensioning Systems automatically adjust the belt's tension in real-time, maintaining consistent tension levels and preventing tracking issues related to tension fluctuations. This is especially important for conveyor belts that are prone to stretching or shrinking.
Laser Alignment Tools use laser technology to offer a high-precision method for aligning rollers and pulleys, ensuring they are perfectly perpendicular to the belt's direction. This level of accuracy is crucial for maintaining optimal conveyor belt performance.
Infrared Inspection involves using infrared cameras to detect uneven temperature distributions along the belt, which can indicate misalignment or other issues affecting tracking. This technique provides valuable insights into belt performance.
Digital Monitoring Systems use advanced sensors and IoT devices to monitor the belt's position and movement, providing real-time data for predictive maintenance and adjustments. This level of monitoring can help prevent costly downtime and improve overall efficiency.
Here are some advanced techniques and tools you can use to improve conveyor belt tracking:
Real-World Examples
In the mining industry, frequent belt misalignments at Goldstone Mining Co. were significantly reduced with the implementation of self-aligning idlers.
Heavy loads and harsh conditions can cause conveyor belt misalignments, but the right solution can make a big difference.
A 50% reduction in downtime and significant increase in production efficiency were achieved by Vista Mining Solutions through the integration of conveyor belt tracking theory.
Self-aligning idlers and enhanced monitoring systems were key to this success.
PureFood Productions reduced product waste by 30% and improved regulatory compliance by implementing belt tracking guides.
Maintaining hygiene standards is crucial in the food processing industry, and belt tracking guides are an effective solution.
SwiftLog Distribution Services decreased package damage and increased throughput with the use of laser alignment tools.
Laser alignment tools can be a game-changer for distribution centers with high package handling volumes.
The implementation of regular cleaning and maintenance protocols, inspired by conveyor belt tracking theory, resulted in a 40% reduction in maintenance costs for EcoRecycle Facilities.
Proactive maintenance can save companies a significant amount of money in the long run.
Here are some real-world examples of conveyor belt tracking issues and resolutions:
Training and Guidance
Side guide rollers can be used to assist in training the belt initially to prevent it from running off the pulleys, but they should not be located so as to bear against the belt edge once the belt is actually on the pulley.
The Benetech Troughing Training Idler is a great option for automatic incremental corrections to even the smallest misalignment on the load-carrying side of the belt, and it gently guides the belt back to the center of the frame to keep the conveyor straight.
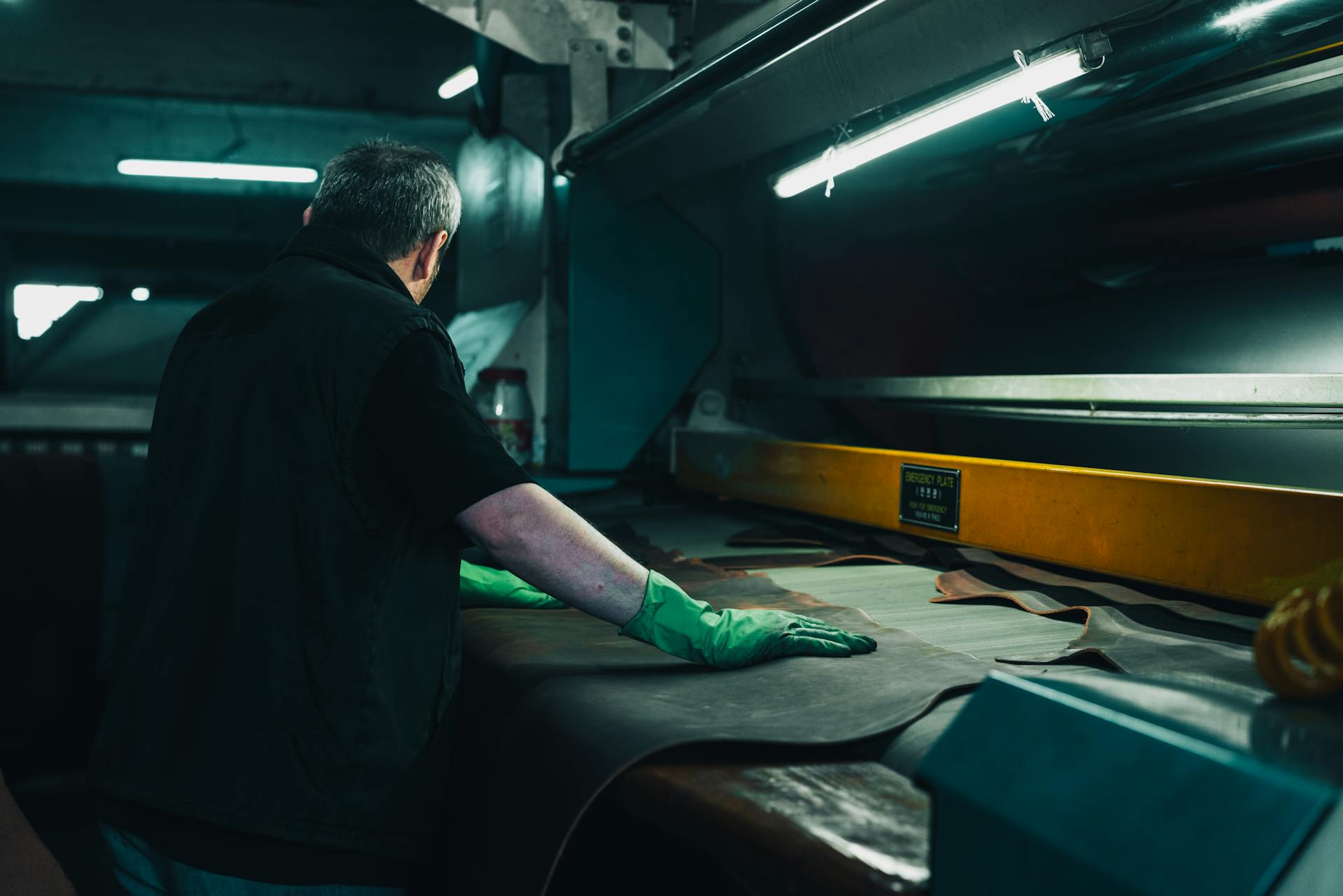
Return idlers, particularly self-aligning return rolls, can provide a constant corrective effect in one direction by shifting their axis with respect to the path of the belt, and some return idlers are made with two rolls forming a 10° to 20° V-trough, which is effective in helping to train the return run.
Training Procedures
Training a conveyor belt to run centrally is a process of adjusting idlers, pulleys, and loading conditions. The basic rule to keep in mind is that the belt moves toward the end of the roll/idler it contacts first.
You can demonstrate this by laying a small dowel rod or round pencil on a flat surface in a skewed orientation, then laying a book across it and gently pushing/rolling it in a line directly away from you. The book will tend to shift to the left or right depending on which end of the dowel rod it contacts first.
For more insights, see: First Class Mail with Tracking
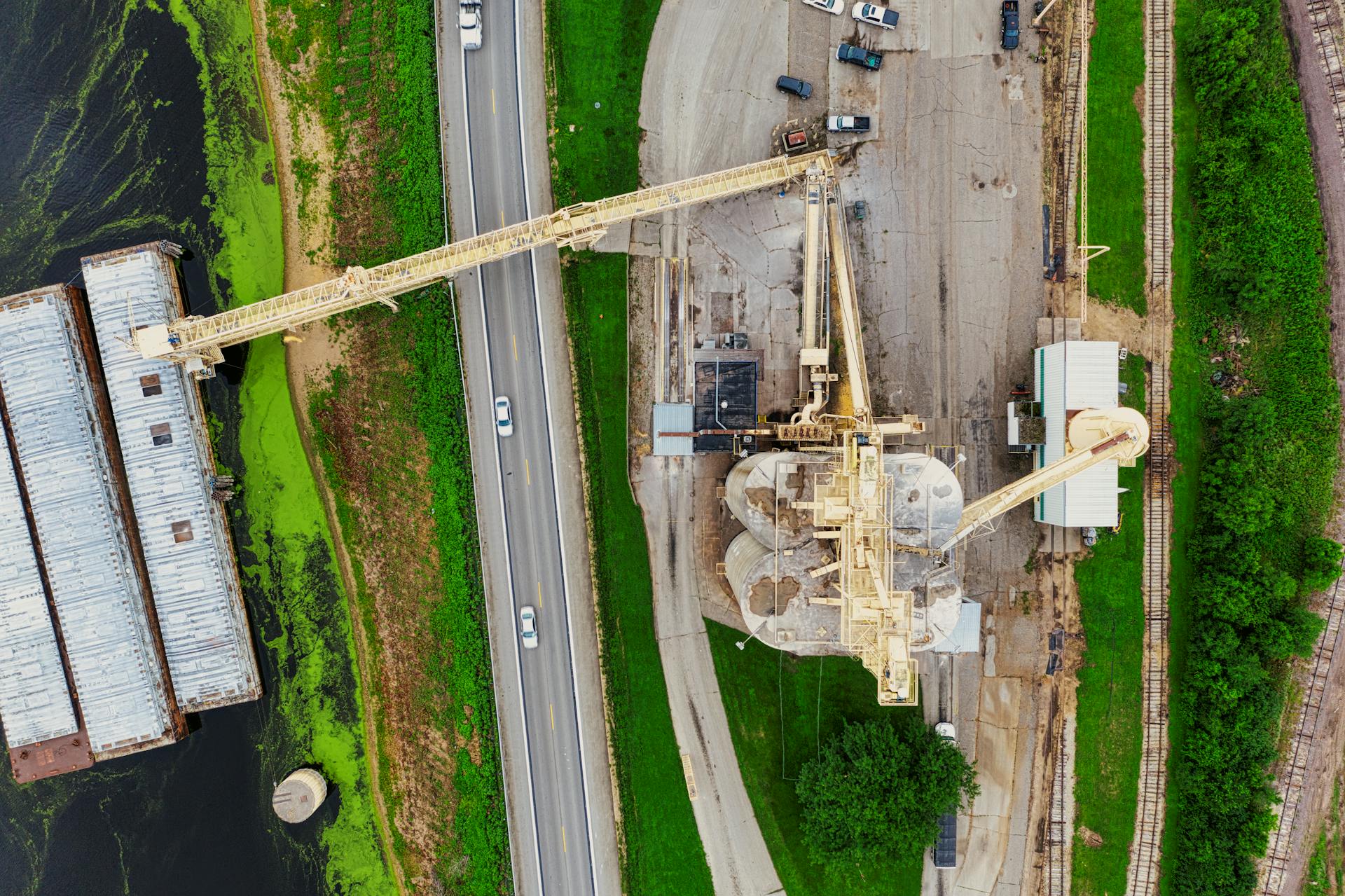
The cause of a belt running off-center can usually be found in the alignment or leveling of the radial stacker or conveyor structures, idlers, or pulleys in that area. If the belt is loaded off-center, the center of gravity of the load tends to find the center of the troughing idlers, leading the belt off on its lightly loaded edge.
Shifting the idler axis with respect to the path of the belt, or "knocking idlers", is an effective way to center a belt where it runs to one side along some portion of the conveyor or radial stacker. This can be done by shifting the idlers over some length of the conveyor, preceding the region of the trouble.
Tilting the troughing idler forward in the direction of belt travel produces a self-aligning effect, but it should be used sparingly, especially on higher angle troughing idlers, as it can encourage accelerated pulley cover wear.
Benetech Troughing Idler Training
The Benetech Troughing Idler is a game-changer when it comes to training your conveyor belt. It provides automatic incremental corrections to even the smallest misalignment on the load-carrying side of the belt.
This idler is different from conventional sidearm roller frames, which can often cause more belt damage. It steers conveyed material with a distinctive pivot and tilt mechanism, and accommodates any inclination angle required.
The Benetech Troughing Idler is designed to work with instant intuition, making it easy to use and understand. It gently guides the belt back to the center of the frame to keep the conveyor straight.
Here are some benefits of using the Benetech Troughing Idler:
- Automatic incremental corrections for even the smallest misalignment
- Reduces belt damage and wear
- Accommodates any inclination angle required
- Works with instant intuition, making it easy to use and understand
The Benetech Troughing Idler is a great option for anyone looking to improve their conveyor belt tracking. It's designed to work with a variety of conveyor systems and can be customized to meet your specific needs.
In addition to the Benetech Troughing Idler, there are other options available for training and guiding your conveyor belt. These include self-aligning rollers and idlers, which can be used to automatically adjust the position of the belt as needed.
Benefits and Selection
When selecting a tracking conveyor belt, consider the material and design. The most suitable material for a tracking conveyor belt is steel-reinforced rubber, which provides excellent durability and resistance to wear.
A well-designed tracking conveyor belt is essential for efficient operation. The design should include a steel-reinforced core and a rubber cover to minimize wear and tear.
The benefits of using a tracking conveyor belt include reduced labor costs, increased productivity, and improved product quality.
Benefits of
Implementing effective conveyor belt tracking can have a significant impact on your production. One of the key benefits is extended equipment lifespan.
By minimizing wear and tear on the belt, you can enjoy longer-lasting equipment. This is especially important for industries where downtime can be costly.
Reduced downtime is another major advantage of conveyor belt tracking. By keeping your belts on track, you can prevent frequent mistracking and the resulting maintenance issues.
Minimized damage and spillage risks are also a major benefit. This not only saves you money but also ensures a safer working environment.
Here are the key benefits of conveyor belt tracking:
- Extended equipment lifespan
- Increased productivity and profitability
- Reduced downtime
- Minimized damage and spillage risks
Selecting Units
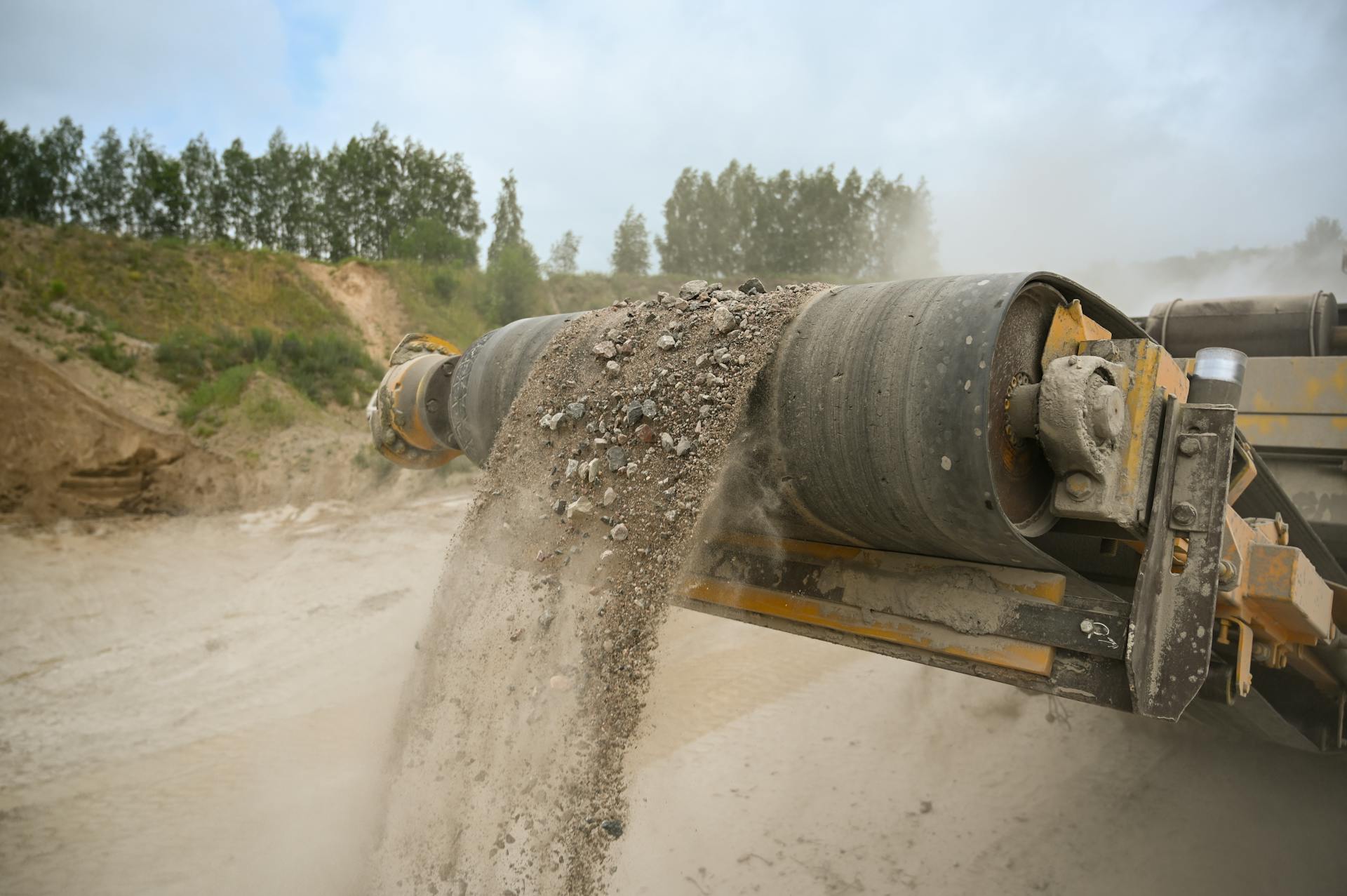
Choosing the right conveyor belt tracking unit is crucial for smooth operations and minimizing downtime.
The choice largely depends on specific operational requirements, including belt type, speed, and material load.
High-speed belts require tracking rollers or frames with advanced adjustment mechanisms to handle rapid changes in belt alignment.
Belt types transporting abrasive or heavy materials need durable tracking components, such as hardened steel or polyurethane, to withstand wear and tear.
Systems equipped with sensors and automatic adjustments can provide real-time corrections, reducing manual intervention and maintenance time.
The installation environment also matters, as tracking units exposed to dusty or moist conditions should resist corrosion and material buildup.
You might enjoy: Eta Track Speed Post Tracking
Featured Images: pexels.com