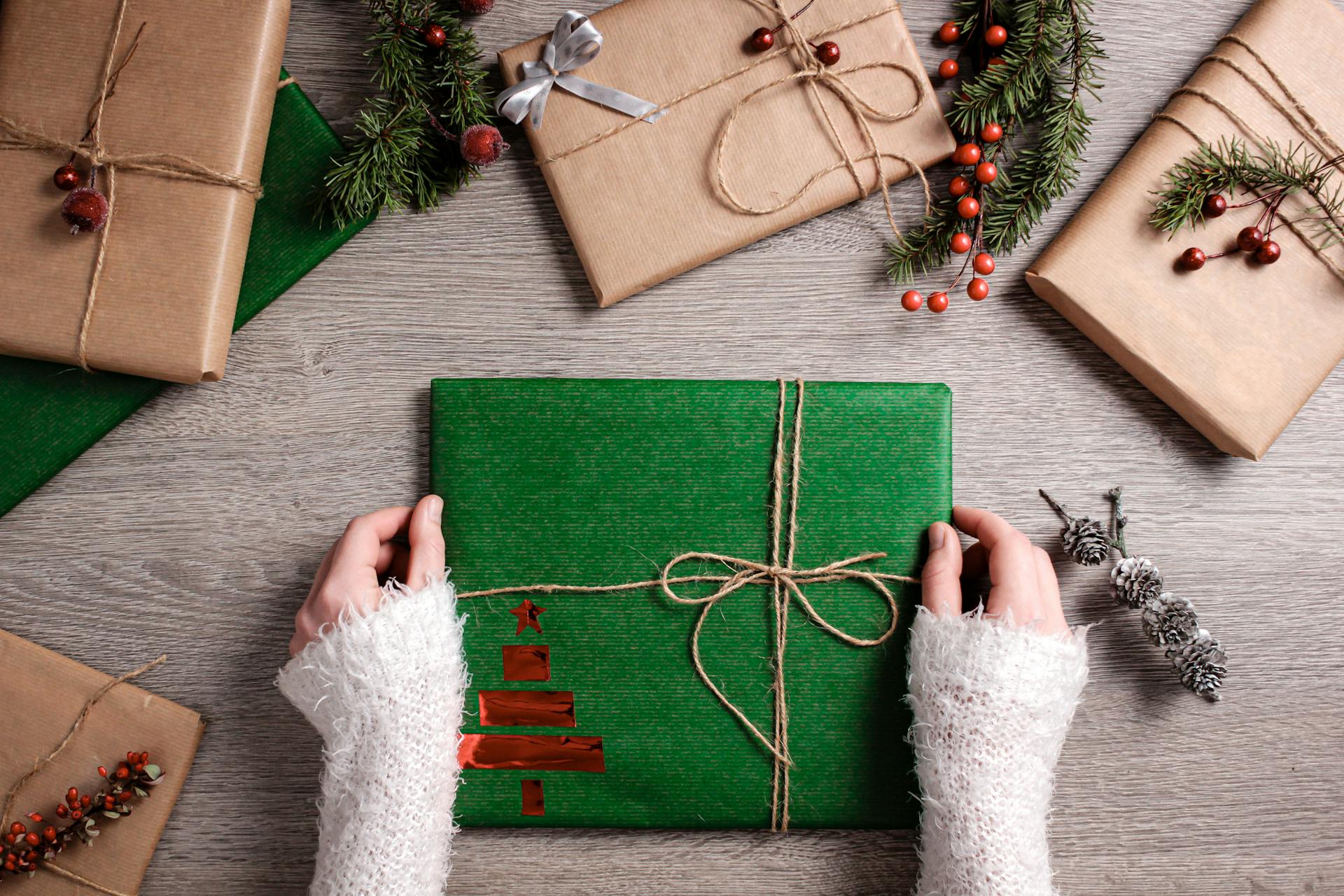
Stretch wrap recycling is an innovative solution that can significantly reduce waste and save businesses money. According to the US Environmental Protection Agency, the average business uses over 100,000 pounds of stretch wrap per year.
By recycling stretch wrap, businesses can divert millions of pounds of waste from landfills annually. In fact, a single stretch wrap recycling program can collect and recycle up to 50 tons of material per month.
Stretch wrap is made from a combination of plastic and resin, making it a valuable resource for recycling. The recycling process involves collecting used stretch wrap, sorting it by type, and processing it into raw materials that can be reused to make new products.
What Is Stretch Wrap Recycling?
Stretch wrap recycling is a process that involves collecting and processing used plastic stretch wrap to create new products.
Used stretch wrap is typically made from a type of plastic called low-density polyethylene (LDPE), which is a common material used in packaging.
Stretch wrap recycling can be done through various methods, including sorting and cleaning the used wrap, then melting it down to create pellets that can be used to make new products.
These pellets can be used to make a range of items, including plastic containers, bags, and even new stretch wrap.
Stretch wrap recycling is a great way to reduce waste and conserve natural resources.
Benefits of Stretch Wrap Recycling
Stretch wrap recycling is a valuable practice that offers several benefits. Stretch wraps manufactured from linear low-density polyethylene (LLDPE) or high-density polyethylene (HDPE) are highly recyclable.
These types of stretch films can be recycled and turned into new products, reducing waste and conserving natural resources. Post-industrial plastics, which are clean and free of contaminants, can net the highest return.
Stretch wrap and shrink wraps are used by warehouses and distribution centers to wrap and secure pallets sent to customers and outlets, known as post-commercial stretch wrap. This process can be a significant source of recyclable materials.
Recycling stretch wrap can help reduce the amount of plastic waste sent to landfills and conserve the raw materials needed to produce new stretch films.
How to Recycle Stretch Wrap
Stretch film can be recycled, and some simple steps can reduce the amount that needs to be recycled.
To quantify film use, cut and weigh the film after it's been properly wrapped around a load, then compress it. This is the benchmark against which future changes should be measured for net impact.
Recyclable stretch films are made from linear low-density polyethylene (LLDPE) or high-density polyethylene (HDPE). These types of films are highly recyclable and can have tremendous value.
Stretch film recycling faces challenges, such as the film being thin and wrapping around recycling equipment, leading to clogging. The cleaning and sorting process can also require special attention due to the film being used with other packaging materials.
Shuliy's plastic recycling machine is designed to overcome the obstacles in stretch film recycling, including a shredder that allows for efficient feeding of the film material into the shredding area.
POLYSTAR has also manufactured efficient recycling machines that can process stretch film, turning it into high-quality, uniform recycled pellets with properties similar to raw materials.
Challenges and Solutions
Plastics recycling rates remain low, with only 5% of plastic waste being recaptured after single use, amounting to $4-6 billion annually.
The New Plastics Economy report highlights the importance of creating a financially viable collection and recycling ecosystem to increase these rates.
Recycling stretch film is particularly challenging due to its use in industrial settings, making it difficult to separate from other waste streams.
Contamination from dirt, adhesive residues, or mixed materials can further complicate the recycling process.
Biodegradable stretch films made from biopolymers derived from renewable resources like cornstarch or PLA offer a promising eco-friendly alternative, as they naturally break down over time.
Advancements in
Advancements in stretch film recycling have made a significant impact on the industry. Several plastic producers are constantly looking for recycled material to incorporate into their production lines.
Collaborative efforts between businesses and recycling companies have led to dedicated collection programs for stretch film. These programs aim to improve collection efficiency and ensure proper separation from other waste streams.
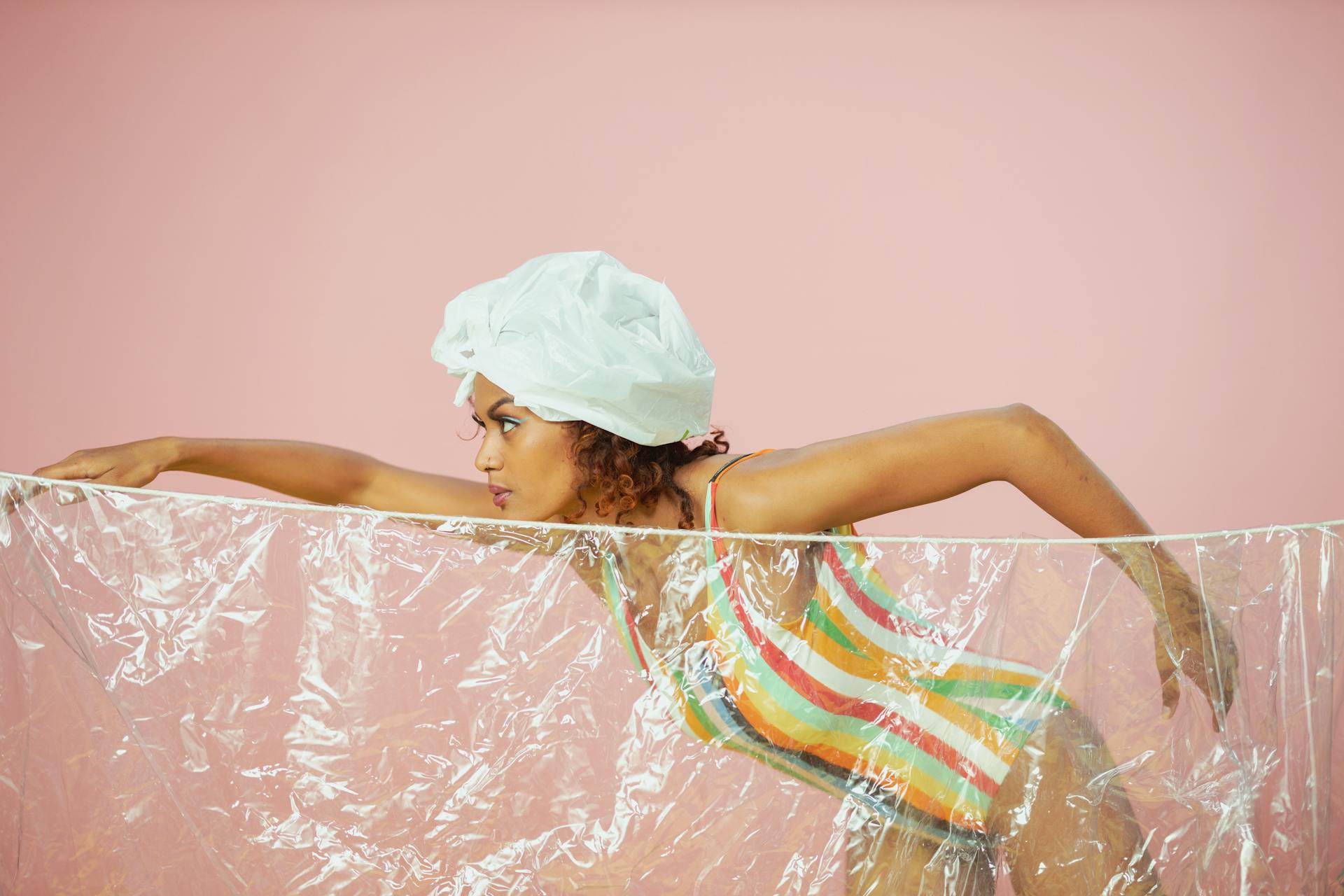
Specialized facilities equipped with advanced machinery can effectively process and recycle stretch film. These facilities employ specific techniques to remove contaminants, shred the film into recyclable pellets, and reintroduce them into the manufacturing process.
Some recycling companies collect waste from other factories, turn it into pellets, and sell it to plastic producers, resulting in a profitable business model. This approach not only reduces costs but also helps create a healthier environment for everyone.
Here are some notable advancements in stretch film recycling:
- Stretch Film Collection Programs: Improves collection efficiency and ensures proper separation from other waste streams.
- Stretch Film Reclamation Facilities: Equipped with advanced machinery to process and recycle stretch film, and reintroduce it into the manufacturing process.
By implementing these advancements, businesses can reduce their trash costs, including the cost of hauling trash to the disposal site or landfill, and tipping fees. The tipping fees in New York can be as high as $102.00 and as low as $49.50.
Recommended Machines
When dealing with stretch film recycling, having the right equipment is crucial. The Plastic Shredder Machine is a vital piece of equipment for reprocessing stretch wrap.

If you're looking to get started, consider investing in a Plastic Shredder Machine. This machine can help break down stretch film into smaller pieces, making it easier to recycle.
Here are some key features to look for in a Plastic Shredder Machine:
Having the right equipment can make all the difference in the stretch film recycling process.
The Challenge of
Recycling stretch film presents unique challenges due to its predominant use in industrial settings, where it is often difficult to separate from other waste streams.
Contamination from dirt, adhesive residues, or mixed materials can complicate the recycling process. This can make it difficult to produce high-quality recycled materials.
Plastics recycling rates in general remain low, with a current 5% rate of recapture after single use. This equates to roughly $4-6 billion annually, highlighting the potential benefits of even small incremental improvements.
The recycling process for stretch film is more complex than other types of plastics, which can make it harder to implement. Companies like Nestle Waters of North America are focused on supporting a high-level shift towards a more sustainable plastics economy.
Biodegradable stretch films, made from biopolymers derived from renewable resources like cornstarch or PLA, have gained traction as an eco-friendly alternative.
Sustainability in Packaging
Manufacturers have a 360-degree motivation to reduce packaging due to cost reduction initiatives, general awareness, social pressure, and supplier scorecards tracked by mass retailers.
The economics of recycling may be even more favorable today, making the compelling CPG case studies, including Pepsi Cola, Target, and Anheuser Busch, even more so.
Source reduction and sustainability in packaging are top concerns for everyone. Driven by these concerns, manufacturers are motivated to reduce packaging.
Post-consumer recycled content is another facet of going green, but it can be complex. The net impact of changes is one example, where increased damage resulting in unsalable product in landfills may outweigh some reduction initiatives.
Stretch film is widely used in industries such as logistics, warehousing, transportation, and retail. Its primary purpose is to secure and protect goods on pallets, providing stability during storage and transit.
Stretch film is made from linear low-density polyethylene (LLDPE) and possesses excellent elongation and cling properties. This makes it ideal for wrapping irregularly shaped or heavy loads.
Embracing a sustainable future requires recycling and developing eco-friendly alternatives for stretch film. Recycling initiatives and the emergence of biodegradable stretch film offer promising pathways toward a more sustainable future.
Businesses and individuals can contribute to this journey by adopting responsible waste management practices, participating in stretch film recycling programs, and exploring the use of biodegradable alternatives when appropriate.
Yuandian, a trusted stretch film manufacturer and exporter, offers a wide range of sustainable stretch film options, including their popular Nano Stretch Film.
Frequently Asked Questions
Can you recycle stretch wrap?
Unfortunately, stretch wrap cannot be recycled through single-stream recycling centers due to a lack of specialized equipment. However, there are alternative recycling options available for stretch wrap, which we'll explore in more detail.
What plastic wrap cannot be recycled?
Plastic wrap that cannot be recycled includes food or cling wrap, prepackaged food bags, and plastic film with paint or excessive glue residue. Check your local recycling guidelines for specific details on what types of plastic wrap are accepted.
Sources
- https://www.lantech.com/can-stretch-wrap-be-recycled/
- https://www.polystarco.com/blog-detail/how-can-plastic-producers-enhance-their-stretch-film-recycling/
- https://www.aaapolymer.com/stretch-film-recycling-faqs/
- https://www.recycle-plant.com/stretch-film-recycling.html
- https://www.hsydpac.com/the-sustainable-future-of-stretch-film-can-it-be-recycled/
Featured Images: pexels.com