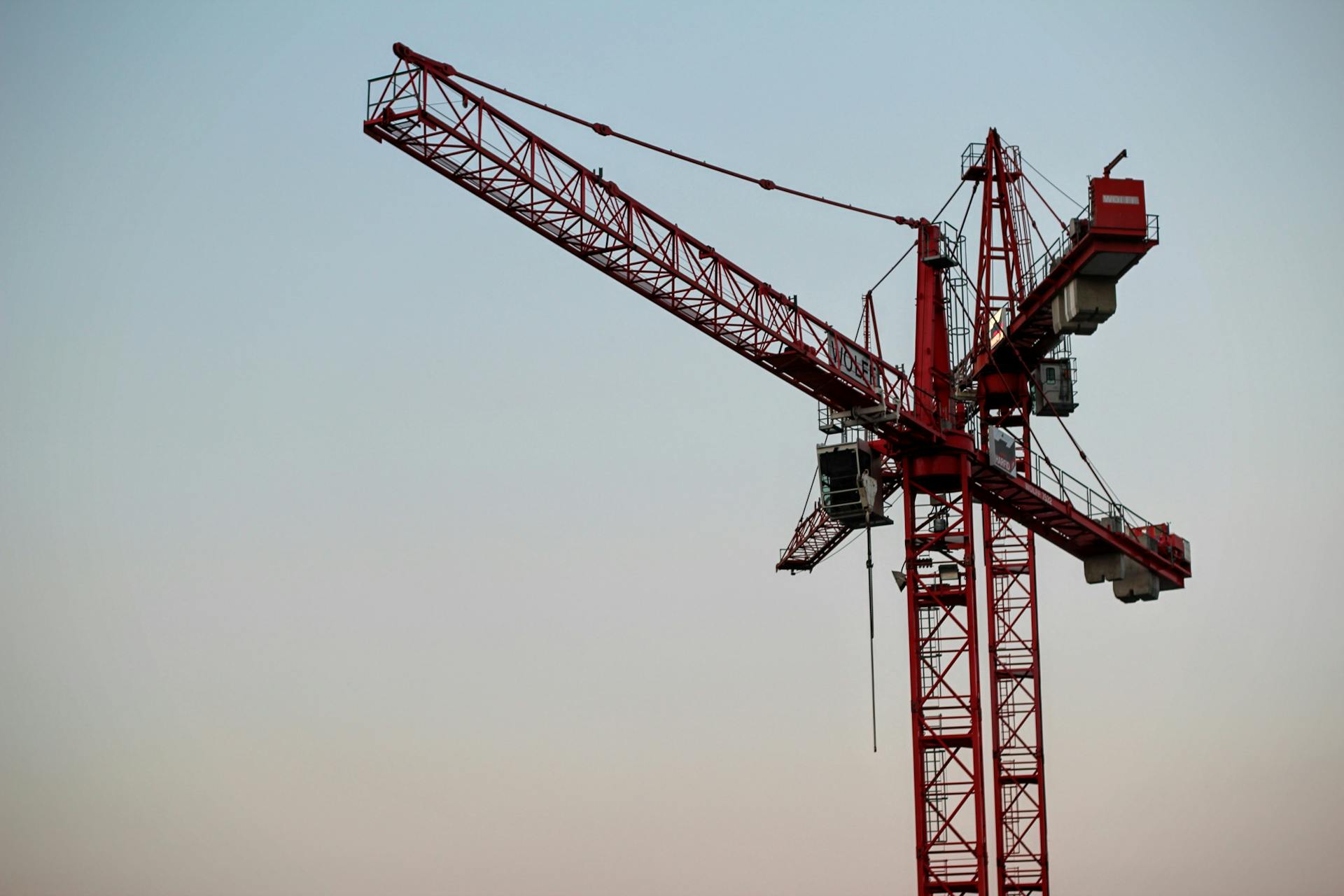
Stretch wrap machines can be prone to issues like worn-out rollers or misaligned film guides, which can cause uneven wrapping and decreased efficiency.
Regular maintenance is key to preventing these problems. This includes cleaning the machine, checking for loose screws, and ensuring proper tension on the film.
If your machine is experiencing issues, start by checking the film tension, as it's often the culprit behind uneven wrapping. Proper film tension is critical for even wrapping and can be adjusted by tightening or loosening the film's take-up arm.
A well-maintained machine can run smoothly for years, but even the best machines require occasional repairs. Common repairs include replacing worn-out rollers or bearings, which can be done with the help of a repair manual or online tutorials.
By following a few simple steps and troubleshooting common issues, you can get your stretch wrap machine up and running in no time.
Broaden your view: Wine Wrapping Paper
Troubleshooting and Maintenance
Troubleshooting your stretch wrap machine can save you a lot of time and money. It's essential to check the power source before attempting to fix the problem.
Before you start troubleshooting, make sure to disconnect the machine from the power source, as recommended in the maintenance checklist for Handle It pallet wrappers. This is a crucial step to avoid any accidents or injuries.
If the problem persists, follow the step-by-step troubleshooting process outlined in the user manual. This process typically involves checking the power, emergency stops, safety switch, and performing a running self-test check. If none of these steps solve the problem, it's time to call a technician.
Regular maintenance is key to preventing damage to your pallet wrapping machine. Make sure to inspect the chain or belt for tension and wear, and replace it immediately if you notice any signs of degradation. It's also a good idea to keep a spare belt or chain in stock to avoid downtime in case of an emergency.
Step-by-Step Troubleshooting
Troubleshooting can be a daunting task, but it doesn't have to be. By following these simple steps, you can save time and money by identifying and fixing the problem yourself.

First, check that the power is on. Yes, it may seem obvious, but you'd be surprised how often this is the culprit.
Next, check that all emergency stops are deactivated. This is an easy fix that can save you a lot of downtime.
The safety switch should also be checked. This is a crucial step before trying to fix the problem or calling a technician.
Performing a running self-test check can also be a good idea. This can be done through the main screen and may be able to determine what the problem is.
If none of these steps solve the problem, it's time to refer to the troubleshooting guide in the manual. This may contain more information specific to your pallet wrapping machine model.
If all else fails, don't hesitate to call a technician. They will be able to inspect the machine and get it up and running in no time.
Maintenance Checklist for Pallet Wrappers
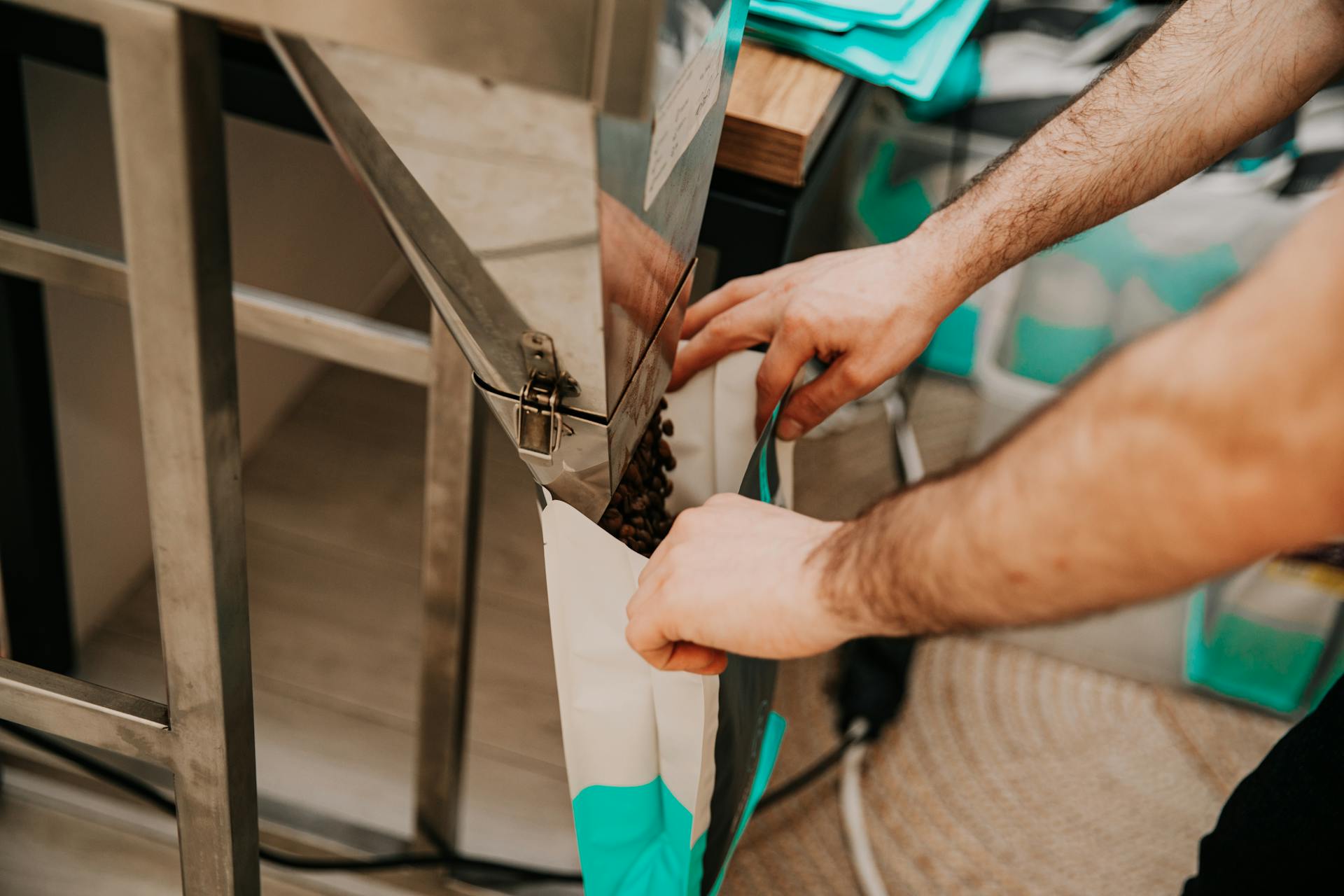
Before performing maintenance on your pallet wrapping machine, it's essential to disconnect it from the power source. This is a crucial safety step to avoid any accidents or injuries.
To ensure you're doing the right maintenance tasks, refer to your machine's user manual or the manufacturer's guidelines. Each machine model has specific requirements, and neglecting these can lead to malfunctions or even damage to the machine.
You can find the recommended maintenance tasks for your Handle It pallet wrapping machine in the user manual or online resources. For example, the maintenance checklist for the SWM-SA-0600 machine includes tasks such as checking the turntable and ensuring it's properly aligned.
Here's a breakdown of the maintenance tasks for different machine models:
Remember, regular maintenance is key to preventing malfunctions and extending the lifespan of your pallet wrapping machine. By following the manufacturer's guidelines and performing the necessary tasks, you can ensure your machine runs smoothly and efficiently.
Repair and Support
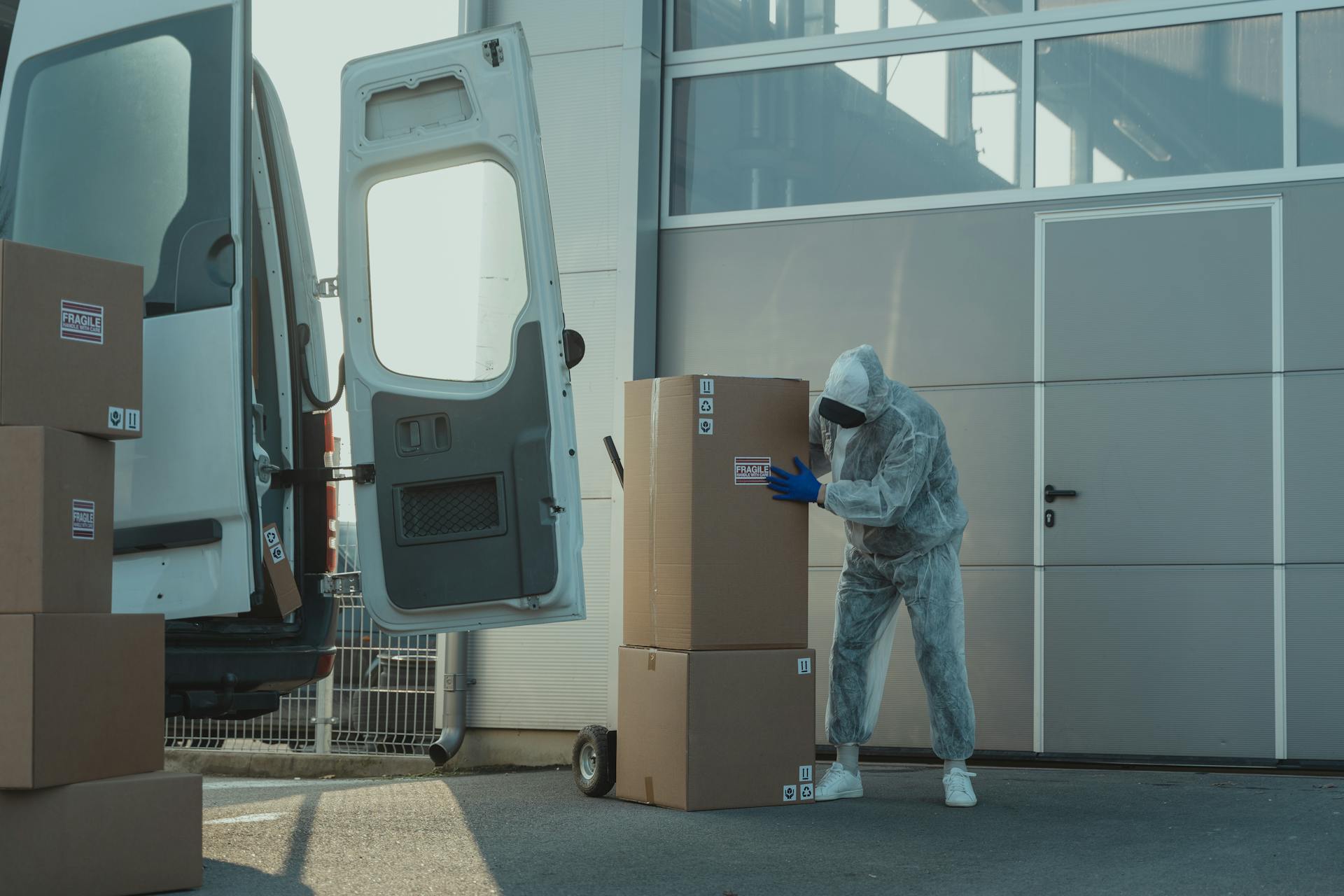
Our comprehensive repair and support services are designed to get your stretch wrap machine up and running as quickly as possible. With a team of certified field service technicians available to arrive at your site within 24 to 48 hours, you can trust that your machine will be in good hands.
We service a wide range of stretch wrapping machines, including fully-automatic, semi-automatic, rotary arm, turntable, high and low profile models from major manufacturers like Lantech, Wulftec, Cousins, and our own brand of TRANSFORMER machines.
Our field technicians are trained to perform routine service, on-demand troubleshooting, and preventative maintenance to help you avoid problems before they occur. They'll also work with you to establish a proactive maintenance routine that keeps your machine in pristine condition.
Comprehensive Support
Comprehensive support is a vital aspect of maintaining your secondary packaging solutions. Our team at Robopac USA offers comprehensive services to support all of your equipment needs.
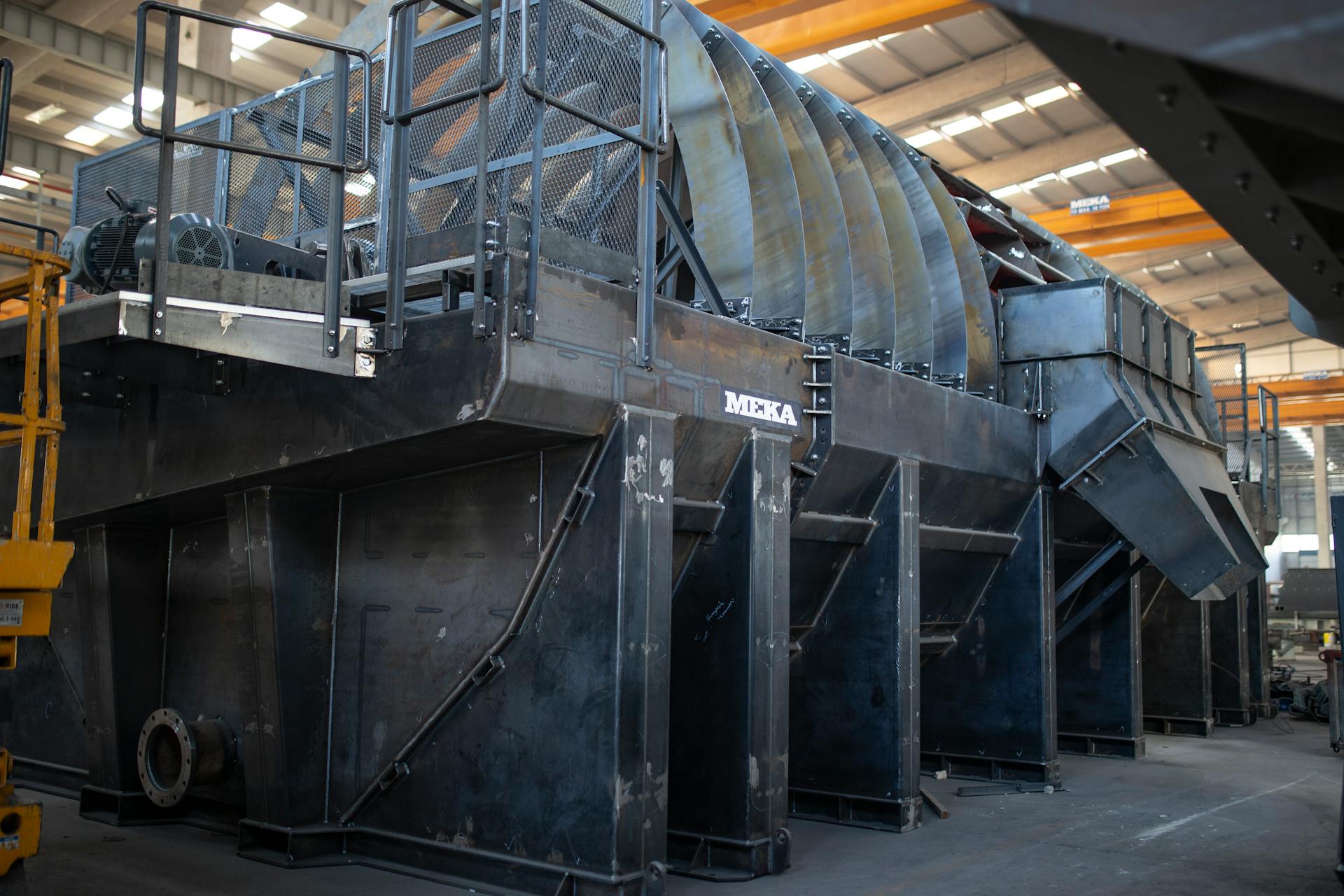
We have a team of certified field service technicians who can arrive at your site within 24 to 48 hours when you need technical support. This ensures that you get the help you need as soon as possible.
Our team works with you to establish a proactive service routine that helps you avoid problems before they occur. This includes machine audits, inspections, troubleshooting, and preventative maintenance.
We offer 24/7/365 live technical support to assist you as soon as you need help. This means you can get in touch with us at any time, day or night, and get the support you need.
Here are the comprehensive field services we offer:
- Machine audits
- Inspections
- Troubleshooting
- Preventative maintenance
Our team is dedicated to keeping your machines in pristine condition so you can continue making the most of your secondary packaging solutions.
Common Problems Requiring Technician
If you're having trouble with your pallet wrapping machine, there are a few common problems that might require a technician's attention. Damage from forklifts can be a major issue, often caused by people rushing and not paying attention.
Forklift collisions can cause extensive damage to the machine. Debris under the turntable is another common problem, which can lead to paper jams when the stretch film gets stuck.
A blown fuse can happen during a power surge, and technicians need to replace fuses properly and safely.
Drive and Lubrication
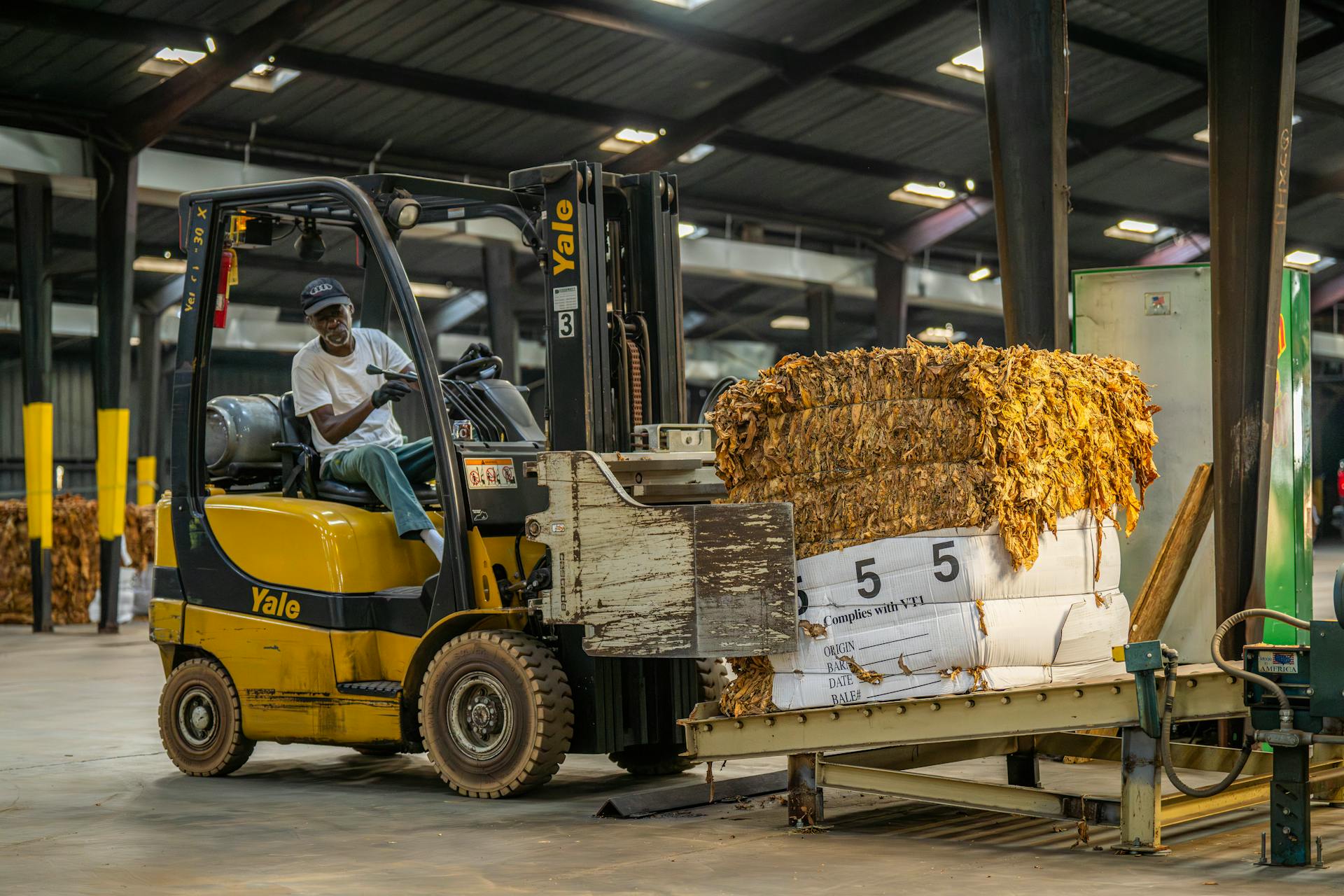
Regular drive system maintenance is crucial to prevent costly repairs and worker injuries. The drive system on your stretch wrapper could utilize belts, chains, or a combination of the two.
It's essential to inspect the chain or belt for tension and wear, as signs of degradation can lead to expensive repairs or severe worker injuries. Immediately tag the machine and order a replacement part if you notice any damage.
Proper lubrication is also vital for smooth operation. Refer to your owner's manual for the exact lubrication points and approved lubricant. Avoid using non-recommended products, as they may not have the correct formulation to ensure consistent performance and long life.
Over-lubricating can cause the grease to splatter and accumulate on other parts, so try to avoid it. If you don't have a spare belt or chain in stock, now is a great time to order a replacement to save time and money in the long run.
Troubleshooting Process
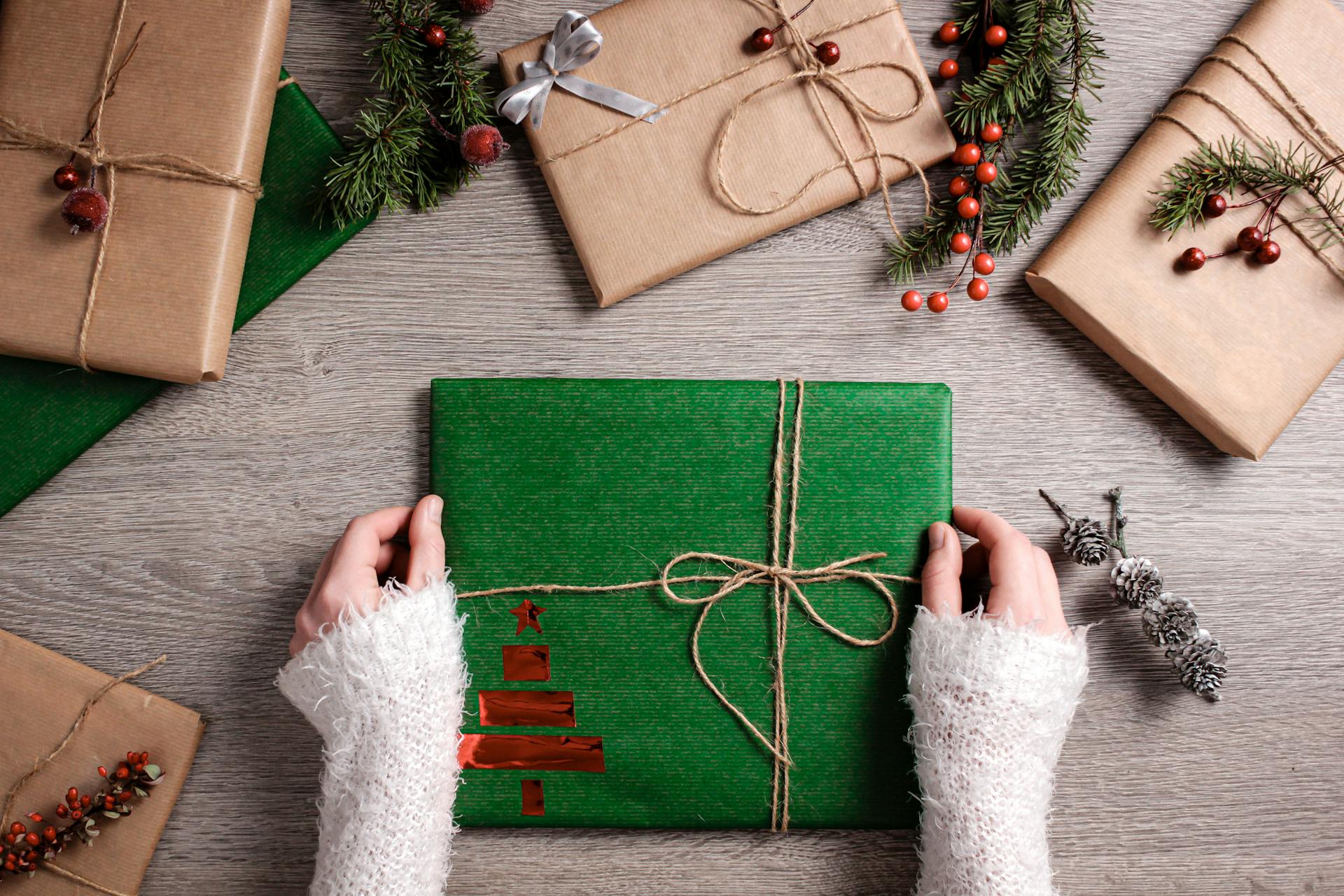
Checking the power is the first step in troubleshooting a non-working pallet wrapping machine. This simple check can save you time and money by ruling out a basic issue.
It's surprising how often a machine fails to turn on because the power was simply switched off or a circuit breaker tripped. Always check this first.
Make sure all emergency stops are deactivated, as this is another easy fix that can save downtime. It's a quick check to make, but it can make a big difference.
The safety switch should also be checked to ensure it's not activated. This is an essential step to take before escalating the problem or calling a technician.
A running self-test check can be performed through the main screen and may be able to determine the problem. This can often be done in a matter of minutes and can save you a lot of hassle.
If none of the above steps solve the problem, refer to the troubleshooting guide in the manual for more specific information about your pallet wrapping machine model.
See what others are reading: Wine Bottle Wrapping Paper
Stretch Wrapper Parts
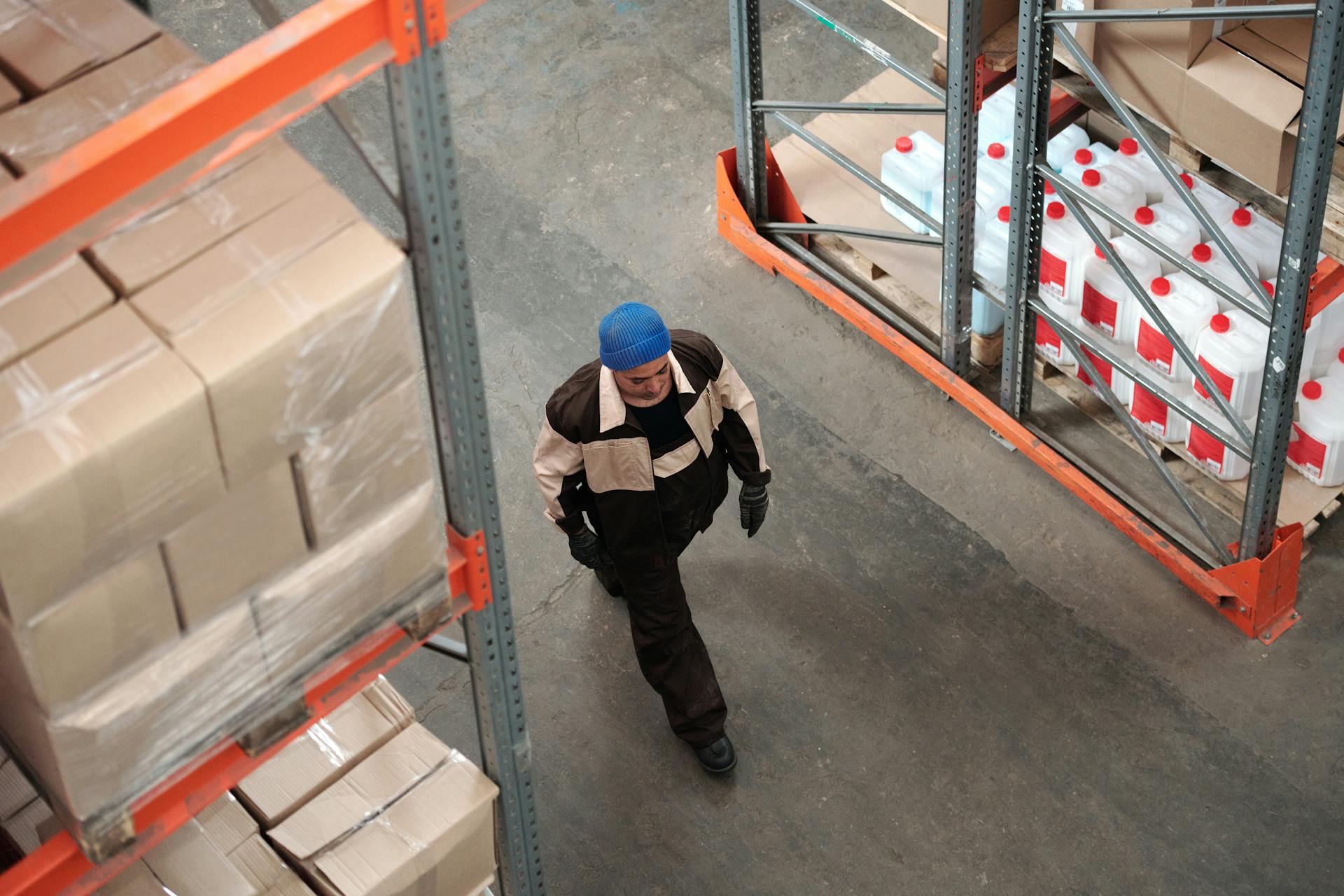
Stretch wrapper parts are essential for keeping your packaging operations running smoothly. You can find a variety of parts and accessories on Rocket Industrial's website.
Rocket Industrial offers bearings, fasteners, rollers, springs, and switches specifically designed for stretch wrapper machines.
These parts can be found in the "Stretch Wrapper Parts" section of Rocket Industrial's website, where you can browse through a list of available items.
Some of the parts available include bearings, fasteners, rollers, and switches, among others.
Here's a breakdown of the types of parts available:
Some parts, like the BER-FG-08-19A-EA, are in stock and available for purchase.
Sources
- https://robopacusa.com/field-service-repair/
- https://gap-co.com/equipment-service/
- https://www.handleitinc.com/news/pallet-wrapper-preventative-maintenance-guide/
- https://www.smartwasp.com/company-news/a-guide-to-troubleshooting-your-pallet-wrapping-machine-388.html
- https://www.rocketindustrial.com/products/parts/stretch-wrapper-parts.html
Featured Images: pexels.com